7 сложных проектов, достигнутых с помощью 3D-печати
Используя гибкость дизайна, обеспечиваемую 3D-печатью, инженеры могут воплотить в жизнь даже самые смелые идеи.
3D-печать - это технология, позволяющая создавать формы и детали, недостижимые с помощью традиционных методов производства. Чтобы продемонстрировать мощь этой технологии, мы исследуем 7 примеров впечатляющих дизайнов, которые были созданы только с помощью 3D-печати.
1. Титановый тормозной суппорт Bugatti, напечатанный на 3D-принтере
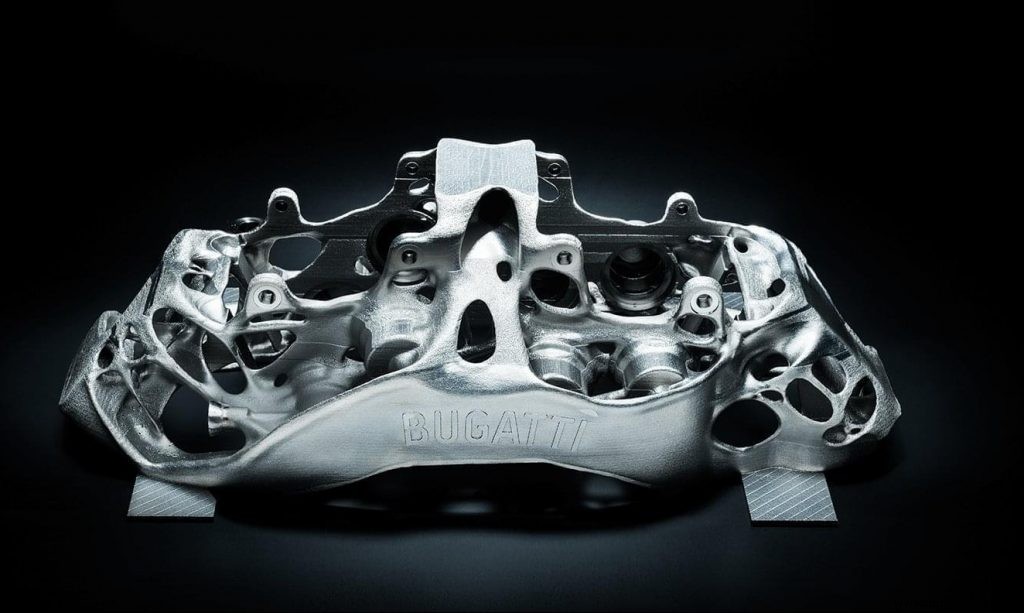
Применение:автомобилестроение
Преимущества:легкий вес, большая прочность
Французский автопроизводитель Bugatti воспользовался возможностью 3D-печати для своего последнего суперкара Chiron, выпустив, как говорят, самый мощный тормозной суппорт в мире - 3D-печать из титана.
Хотя тормозной суппорт работает так же, как обычный суппорт, сочетание 3D-печати и титана означает, что он намного прочнее и примерно на 40% легче, чем алюминиевая деталь, которая используется в настоящее время.
Используя процесс 3D-печати металла под названием Selective Laser Melting, команда Bugatti смогла поэкспериментировать с различными геометрическими формами и толщиной стенок, недостижимыми с помощью традиционных технологий производства.
Результат:тормозной суппорт сложной формы с толщиной стенок от 1 до 4 мм.
В конце 2018 года компания Bugatti успешно провела испытания суппорта при высоких нагрузках и Сейчас компания готовится запустить компонент в производство.
Однако Bugatti - не единственная компания, которая произвела революцию в конструкции тормозных суппортов. Британская автомобильная технологическая компания Carbon Performance также использует 3D-печать для «создания экологически безопасных дизайнов» автомобильных деталей, напечатанных на 3D-принтере, в том числе суппортов.
Для этого Carbon Performance использует свою новую программную платформу на базе искусственного интеллекта. Платформа помогает разрабатывать компоненты, которые могут, например, улучшить топливную экономичность автомобиля.
Используя свое программное обеспечение для проектирования и 3D-печать, Carbon Performance может производить тормозные суппорты, которые являются более прочными и экологически безопасными, отчасти благодаря их меньшему весу. Возможность создавать легкие металлические детали с помощью 3D-печати означает, что требуется меньше материала, а производственный процесс приводит к меньшим отходам материала, чем при субтрактивном производстве.
Создание легких дизайнов - одно из ключевых преимуществ 3D-печати. По мере того, как тенденция к использованию электрических и более эффективных транспортных средств продолжает расти, мы увидим, что все больше автопроизводителей исследуют 3D-печать в своих усилиях по созданию более эффективных и легких компонентов автомобилей.
2. Кронштейн сиденья, разработанный General Motor
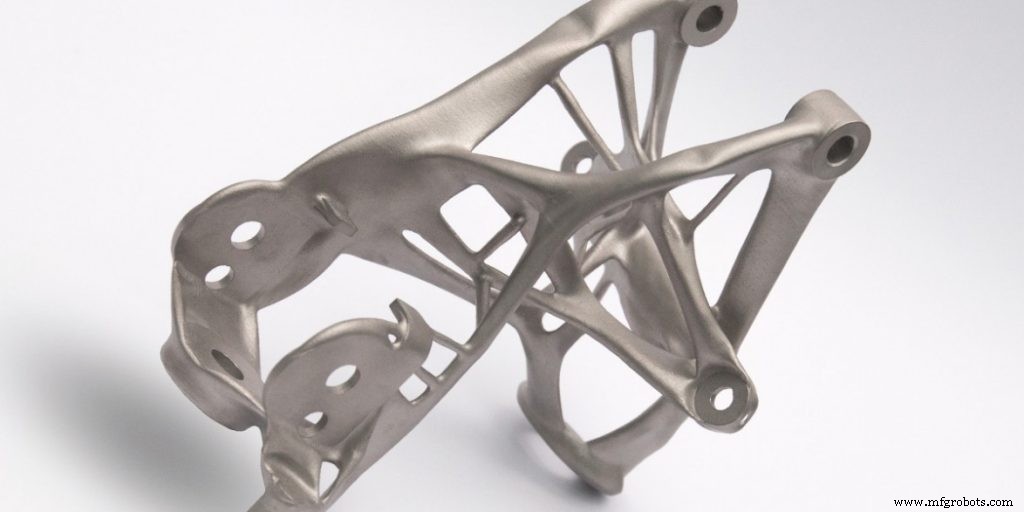
Применение:автомобилестроение
Преимущество:значительная экономия веса
General Motors (GM) недавно создала напечатанную на 3D-принтере версию существующего кронштейна сиденья с помощью инструментов генеративного проектирования.
Программное обеспечение генеративного проектирования использует передовые алгоритмы для автоматического создания нескольких дизайнов варианты, основанные на конкретных параметрах, таких как вес, материал, размер, прочность и методы изготовления. Последующие дизайны имеют сложные органические формы, которые часто можно воплотить в жизнь только с помощью 3D-печати.
Именно так и было с кронштейном сиденья GM. С помощью программного обеспечения для генеративного проектирования Autodesk Fusion 360 было выполнено 150 итераций дизайна. Затем GM выбрала дизайн, который предлагал лучший компромисс между весом, производительностью и технологичностью.
Окончательный дизайн почти не напоминает оригинальный кронштейн. Напечатанный на 3D-принтере из металла, новый кронштейн сиденья на 40% легче и на 20% прочнее оригинала. Он также был изготовлен как единый компонент, в отличие от оригинальной детали, которая должна быть собрана из 8 отдельных частей.
Возможность 3D-печати создавать сложные детали быстрее и с большей гибкостью делает эту технологию естественным выбором для производства переработанных компонентов. Преимущество, показанное в этом примере, - это объединение деталей - возможность печатать несколько деталей как один компонент, тем самым сокращая время и затраты на сборку.
Хотя сиденье GM остается образцом, компания видит огромный потенциал в сочетании 3D-печати и программного обеспечения для генеративного дизайна. Обе технологии, безусловно, будут играть ключевую роль в будущем автомобилестроения, поскольку будут способствовать более быстрому проектированию и разработке продукции, а также производству сложных автомобильных запчастей.
3. Топологически оптимизированный тазобедренный имплант Альтаира
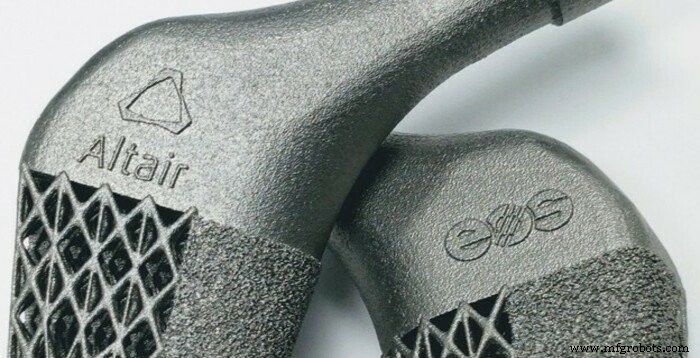
Применение:Медицинское
Преимущество:оптимизация материалов
Оптимизация топологии - это метод генеративного проектирования, который позволяет дизайнерам применять передовые алгоритмы для оптимизации геометрии детали. Используя эту технологию, можно оптимизировать распределение материала детали, чтобы удалить из конструкции любой ненужный материал.
Одной из компаний, использующих оптимизацию топологии, является ИТ-компания Altair, которая объединила 3D-печать с оптимизацией топологии для создания улучшенный имплант тазобедренного стержня.
3D-печать предлагает ряд преимуществ для имплантатов бедра, включая возможность настройки имплантата с учетом конкретных нагрузок, которые он должен выдерживать. Программное обеспечение для оптимизации топологии облегчает это, позволяя инженерам учитывать различные нагрузки, которые имплантат бедра может столкнуться в течение своего жизненного цикла.
Путем ввода таких параметров, как загружения и проектные ограничения, программа оптимизирует распределение материалов в пределах определенного объема. В результате этого процесса создается конструкция, показывающая, где можно удалить материал, чтобы создать наиболее эффективный имплантат бедра.
Команда Altair использовала этот подход для определения твердых и полуплотных областей имплантата перед заполнением полуплотных областей решетчатыми структурами, чтобы сделать имплантат легче.
По сравнению с неповрежденной бедренной или бедренной костью с уже имеющимся имплантатом, команда обнаружила, что новый дизайн помогает увеличить предел выносливости примерно до 10 миллионов циклов. Это означает, что бедренный имплантат выдержал бег трусцой из Лос-Анджелеса в Нью-Йорк и обратно - дважды.
Новый дизайн также помогает снизить защиту от напряжений на 57%. Экранирование напряжения относится к снижению плотности кости, вызванному помещением титанового имплантата внутрь пациента, и в конечном итоге может привести к переломам и вывиху. По этой причине создание имплантата как можно ближе к исходной костной ткани является ключом к снижению защиты от напряжения и устранению этих нежелательных эффектов.
Использование 3D-печати в качестве производственной технологии - единственный способ воплотить такие конструкции в жизнь. Он не только делает возможными сложные формы, такие как решетки, но также позволяет производить их более экономично, чем традиционные методы.
На сегодняшний день топологически оптимизированные имплантаты, напечатанные на 3D-принтере, только начинают находить применение в реальных условиях. Регулирующим органам здравоохранения потребуется некоторое время, чтобы разработать новые методы стандартизации для этих новых конструкций имплантатов. Однако в будущем становится ясно, что 3D-печать станет ключевой технологией для создания более подходящих, долговечных и эффективных имплантатов бедра для конкретного пациента.
4. Пешеходный мост MX3D, напечатанный на 3D-принтере
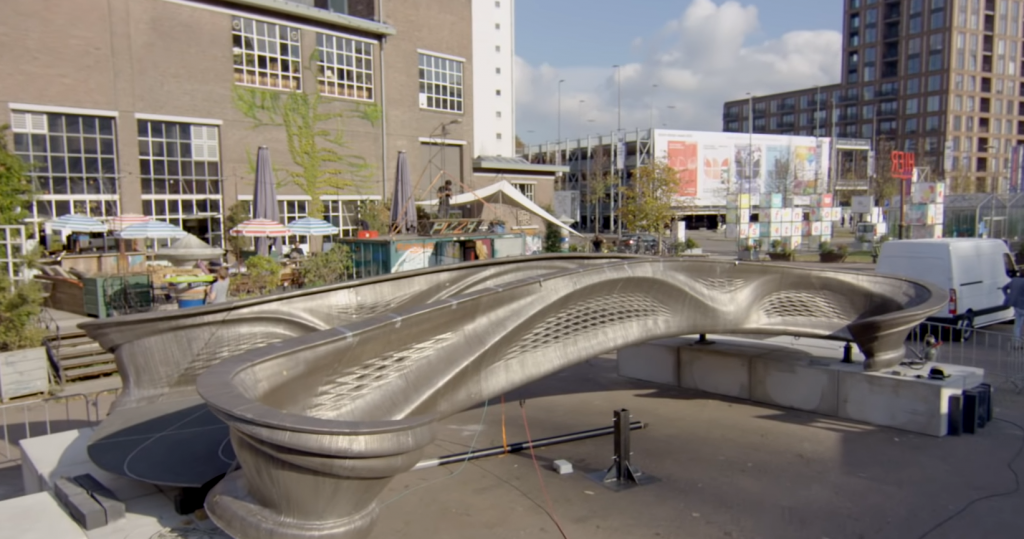
Применение:строительство
Преимущество:инновационный дизайн
Представленный на Голландской неделе дизайна в 2018 году пешеходный мост из нержавеющей стали MX3D, напечатанный на 3D-принтере, является одним из самых захватывающих дизайнерских проектов в сфере 3D-печати.
Установив сварочные аппараты на роботизированные манипуляторы, команда MX3D смогла напечатать на 3D-принтере мост длиной 12 метров, придав ему уникальный внешний вид и форму. Например, конструкция моста органична и похожа на ткань, с множеством изгибов и замысловатых деталей. Поверхность моста оставлена не сглаженной, поэтому слои наплавленной стали видны, что придает мосту грубую и необычную отделку.
Интересно, что 3D-печать была не единственной передовой технологией, используемой для этот проект. Чтобы обеспечить безопасность и оптимальную производительность моста, стальная конструкция, напечатанная на 3D-принтере, оснащена сетью датчиков для отслеживания состояния моста, регистрации количества людей, идущих по нему, и измерения таких параметров, как разброс веса и качество воздуха.
На реализацию всего проекта ушло почти четыре года, и теперь готовый мост должен быть установлен в Амстердаме в конце этого года.
5. GE Research разрабатывает теплообменник на основе биопрепаратов
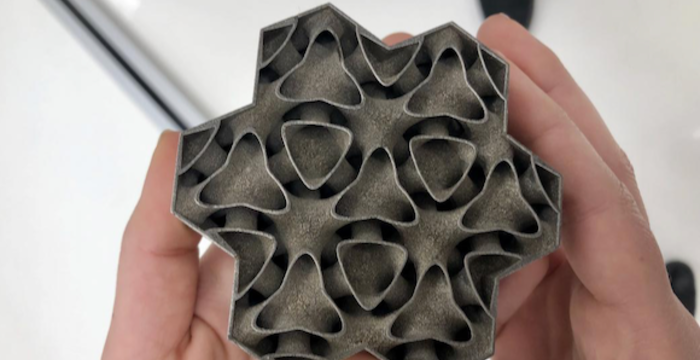
Применение:Энергетика
Преимущество:повышенная производительность
GE Research разрабатывает сверхэффективный теплообменник с низким уровнем выбросов для энергетического оборудования, такого как газовые турбины. Удивительно, но для этого команда разработала инновационный дизайн, вдохновленный человеческими легкими.
Легкие человека - один из самых эффективных и компактных теплообменников. Орган выполняет свою функцию теплообмена с сетью капилляров, которые разделяют поток крови на небольшие потоки. Эта сеть нагревает более прохладный воздух, который мы вдыхаем, а также регулирует температуру тела.
Теплообменник GE работает аналогичным образом, но при гораздо более высоких температурах и давлениях. Компонент имеет тройную сеть каналов, принимающих горячий воздух, выходящий из газовой турбины. Эта сеть переплетается с другой сетью каналов, заполненных более холодной рабочей жидкостью, движущейся в противоположном направлении. Горячий воздух и холодная жидкость не смешиваются друг с другом, но их непосредственная близость позволяет горячему воздуху охлаждаться, улучшая тепловой КПД газовой турбины.
Важно отметить, что 3D-печать была единственной технологией, способной создавать такой сложный дизайн.
После завершения процесса разработки GE сможет напечатать на 3D-принтере теплообменник, который будет экономично работать при температуре на 250 ° C (450 ° F) выше, чем у современных теплообменников. Благодаря значительно повышенной рабочей температуре компонент, напечатанный на 3D-принтере, представляет собой новое поколение высокоэффективных теплообменников.
6. Легкий кронштейн на крышу BMW
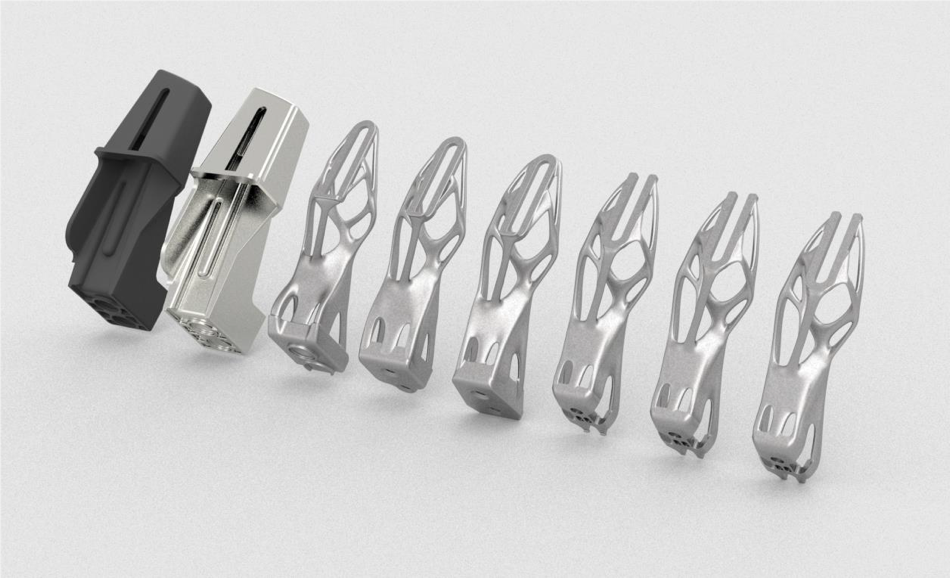
Применение:автомобилестроение
Преимущество:снижение веса
В 2018 году BMW выпустила свой культовый автомобиль i8 Roadster с отмеченным наградами металлическим кронштейном для крыши, напечатанным на 3D-принтере.
Кронштейн для крыши - небольшой компонент, который помогает складывать и раскладывать верхнюю часть автомобиля, потребовалась новая конструкция, чтобы максимизировать производительность механизма складывания крыши. Для достижения этой цели инженеры BMW обратились к программному обеспечению для оптимизации топологии.
С помощью этого программного обеспечения инженеры смогли ввести такие параметры, как вес, размер компонента и нагрузка, которую он будет принимать. Затем программа создала проект, который оптимизировал распределение материала детали.
Дизайн, созданный командой инженеров, невозможно было отлить. Команда обнаружила, что единственный способ реализовать этот дизайн - это 3D-печать металлом.
Благодаря технологии селективной лазерной плавки (SLM) инженеры создали металлический кронштейн для крыши, который в 10 раз жестче и на 44% легче, чем традиционный вариант.
Деталь, которая сейчас производится небольшими сериями, демонстрирует огромный потенциал облегчения конструкции транспортных средств в сочетании с мощью методов оптимизации топологии.
7. KW Micro Power и VELO3D совместно разрабатывают компонент микротурбины
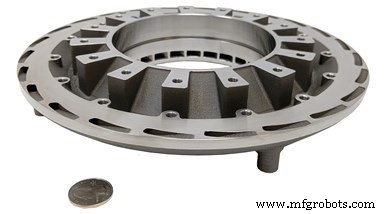
Применение:Энергетика
Преимущество:сложные внутренние функции
В течение нескольких лет инженерная компания KW Micro Power работала над конструкцией микротурбинного генератора, но столкнулась с трудностями при внедрении этой конструкции в производство. Ключевой задачей было производство одного из компонентов устройства.
Речь идет о титановом диске со сложными внутренними каналами, которые помогают более эффективно управлять выхлопными газами. При 3D-печати на металле этому компоненту требуются опорные конструкции для предотвращения провисания или деформации во время процесса печати.
Однако сложность внутренних характеристик компонента не позволила удалить опоры после производства.
Чтобы решить эту проблему, компания сотрудничала с VELO3D, производителем 3D-принтеров, который разработал собственную технологию 3D-печати из металла Intelligent Fusion. Эта технология позволяет 3D-принтеру VELO3D Sapphire печатать детали с минимальными опорными конструкциями и уменьшенными остаточными напряжениями, которые часто являются причиной деформации.
Это достигается за счет запатентованного бесконтактного устройства для повторного нанесения покрытия, которое используется для доставки свежего слоя порошка, который необходимо расплавить и сплавить с помощью лазера. При 3D-печати на порошковой основе металлом, когда порошок укладывается поверх другого слоя, устройство для повторного нанесения покрытия может сместить деталь, если она не закреплена на рабочей пластине.
В сапфировой системе VELO3D лезвие для повторного нанесения покрытия не контактирует с порошковым слоем. После того, как порошок нанесен, на верхнюю часть порошка применяется скребок и вакуумный процесс, чтобы убедиться, что он абсолютно ровный.
Поскольку средство для повторного нанесения покрытия не контактирует с предыдущим слоем порошка, деталь не нуждается в какой-либо опоре, чтобы закрепить ее на металлической рабочей плите. Между тем, моделирование и система управления с обратной связью, питающая принтер, позволяют печатать сложные внутренние функции без опор.
Чтобы использовать всю мощь 3D-принтера Sapphire, команда VELO3D помогла KW Micro Power еще больше улучшить конструкцию компонента генератора. Готовая деталь на 37% легче оригинальной конструкции и, как говорят, работает лучше благодаря уменьшенным напряжениям. Но что еще более важно, конструкция, ранее считавшаяся непроизводимой, стала возможной благодаря новому поколению технологий 3D-печати металлом.
Воплощение самых сложных идей
3D-печать предлагает потрясающую гибкость дизайна, позволяя дизайнерам и инженерам экспериментировать с новыми формами и функциями, включая топологически оптимизированные формы, решетчатые структуры и легкие конструкции.
Благодаря такому количеству возможностей, открываемых 3D-печатью, эта технология позволяет производителям производить инновационные продукты с оптимизированным индивидуальным дизайном, что было бы невозможно при традиционном производстве.
Однако, чтобы раскрыть этот потенциал, очень важно следовать принципам проектирования, уникальным для аддитивного производства. Только вооружившись пониманием возможностей и ограничений 3D-печати, компании смогут использовать эту технологию для реализации своих самых творческих идей.
3D печать
- Введение в 3D-печать из пластика
- Интервью с экспертом:доктором Альваро Гоянесом из FabRx
- 3D-печать силиконом - время пришло?
- Начало работы с керамической 3D-печатью
- Руководство по 3D-печати с помощью HP Multi Jet Fusion
- Краткое руководство по 3D-печати с использованием струйной печати под переплет
- Печать предохранителя 1 с предохранителем 1
- KUHMUTE изменяет мобильность с помощью 3D-печати SLS
- Высокоскоростная 3D-печать с AION500MK3
- Композитные материалы для 3D-печати с непрерывным волокном