Интервью с экспертом:соучредитель Arevo Винер Мондезир о производстве первой в мире рамы велосипеда из углеродного волокна с 3D-печатью
Компания Arevo из Кремниевой долины попала в заголовки газет в 2018 году после того, как представила так называемую первую в мире раму велосипеда из углеродного волокна, напечатанную на 3D-принтере. Вариант использования продемонстрировал уникальные возможности запатентованной технологии композитной 3D-печати Arevo, которая сочетает в себе робототехнику и программное обеспечение для производства легких, индивидуальных композитных деталей.
С тех пор Arevo стала партнером производителя велосипедов Franco Bicycles, чтобы доставить цельные рамы из углеродного волокна с 3D-печатью для нового бренда электронных велосипедов.
На этой неделе мы рады поговорить с Винером Мондезиром, соучредителем и техническим директором Arevo, о запатентованной технологии Arevo, преимуществах композитной 3D-печати и о том, что ждет композитное производство в будущем.
Не могли бы вы рассказать нам немного об Арево?
В Arevo наша цель - обеспечить масштабное производство композитных деталей. Мы делаем это с помощью робототехники, материалов и программного обеспечения.
Если посмотреть на отрасль композитов, производство композитных деталей представляет собой очень большие возможности. Углеродное волокно может быть прочнее некоторых металлов и легким, поэтому оно широко применяется во многих отраслях промышленности.
Но по ряду причин внедрение производства композитов сдерживается, поэтому возможность не используется. Одна из причин этого - неэффективные производственные процессы.
Производство композитов в настоящее время требует больших затрат труда, ресурсов и капиталовложений, а это означает, что оно не масштабируется до больших объемов. Отрасли, которые действительно смогли извлечь выгоду из производства композитов, были теми, которые могли позволить себе экономическое обоснование, например, аэрокосмическая промышленность и высокотехнологичная автомобильная промышленность.
Кроме того, существуют длительные циклы проектирования из-за неадекватного программного обеспечения и неэффективного моделирования. Еще одна причина, о которой часто забывают, - это непонимание композитов в других отраслях.
Arevo решает все эти проблемы. Мы переосмысливаем производство композитов, используя то, что мы называем дигитализацией композитов.
Мы решили решить эту проблему, разработав программное обеспечение, которое устраняет пробелы в знаниях.
Вы начинаете с 3D-модели, а наше программное обеспечение выполняет анализ, определяет оптимальную окончательную ориентацию, необходимое количество материала и выдает инструкции по изготовлению детали с использованием нашей технологии изготовления.
Возьмем для примера паутину. Когда вы смотрите на паутину, это трехмерная структура, в которой есть нужное количество материала для ее целей.
Волокно, или шелк в случае паутины, использует только нужное количество материала и идеально укладывается там, где нужно. Мы черпаем вдохновение в этом, когда придумываем оптимизированный способ 3D-печати композитных деталей.
Итак, наша миссия как компании - обеспечить масштабное производство композитов.
Каковы преимущества композитной 3D-печати?
Композиты из углеродного волокна обладают отличным соотношением прочности и веса, поэтому вы получаете действительно прочный, но легкий материал.
Если вы посмотрите на тенденции в 3D-печати, то увидите, что множество различных техник использует решетчатую структуру для легкого металла, который от природы плотный и тяжелый.
Но если вы начнете с легкого и прочного материала, такого как углеродное волокно, вы получите конечный результат намного быстрее. Таким образом, композиты намного лучше подходят для определенных областей применения, чем изделия с металлической решеткой, которые выглядят великолепно, но не обязательно служат цели.
Сложность с углеродным волокном заключается в том, что оно анизотропно, это означает, что он силен в одном направлении. Вот почему с этим немного сложнее справиться без специальных инструментов.
В Arevo мы разработали набор инструментов для дизайнеров, поэтому вам не нужно иметь докторскую степень для производства композитов из углеродного волокна. Наше программное обеспечение позаботится об этом.
Ваша рама велосипеда, напечатанная на 3D-принтере из углеродного волокна, получила широкую огласку, когда была представлена. Каков был процесс создания рамы велосипеда от проектирования до производства?
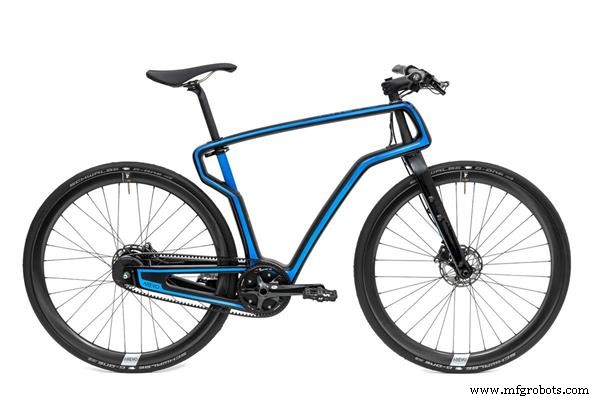
Это конкретное приложение началось как способ продемонстрировать возможности этой технологии.
Рама велосипеда очень доступна, но она имеет очень сложную форму и представляет собой большую конструкцию, которая требует нагрузки, скручивания и способности выдерживать вес. Так что это было идеальное приложение для демонстрации нашей технологии.
Если вы сделаете шаг назад и посмотрите на традиционные композитные велосипеды сегодня, то увидите, что они проходят путь от проектирования до создания прототипа, а затем - до производства. Этот процесс занимает около года.
Кроме того, традиционные велосипеды из композитных материалов производятся вручную. Кадры склеиваются между собой от 20 до 30 частей, и каждый кадр касается до 40 человек. Это очень трудоемкий процесс, и в итоге вы получаете очень дорогой продукт, который не обязательно масштабируется.
Дизайн также очень похож, поэтому вы не можете много настраивать.
Благодаря нашей технологии мы сократили этот процесс с почти года до нескольких дней. Программное обеспечение Arevo использует дизайн САПР и создает изотропный генеративный дизайн на раме, которую придумывает дизайнер. Он также оптимизирует ориентацию и выполняет прогнозный анализ.
Следующий шаг происходит на нашем производственном предприятии. Мы построили производственный объект в Калифорнии, который может производить велосипедные рамы по индивидуальному заказу с использованием нашей робототехники и технологии наплавки.
Когда мы выпустили велосипед, к нам обратились все крупные производители велосипедов, потому что они были заинтересованы в свободе дизайна, предлагаемой технологией.
Когда вы смотрите на конструкцию велосипедной рамы Arevo, она фактически отклоняется от конструкции обычного велосипеда. Например, у него нет сиденья, и он сильно отличается от традиционного велосипеда.
Велосипед Arevo - это цельный велосипед, сделанный из очень прочных углеродных волокон, ориентированных в оптимальной ориентации в трехмерном пространстве. Нам удалось создать цельную конструкцию, которая делает его очень прочным и легким.
Мы можем настроить реальную езду на велосипеде с помощью программных инструментов. Мы можем настроить жесткость в определенных частях велосипеда и при желании сделать езду еще более плавной. С традиционными велосипедами вы, по сути, всегда пытаетесь изготавливать одну и ту же раму снова и снова.
Напечатанная на 3D-принтере рама, с другой стороны, открывает новую бизнес-модель для отрасли, которая привыкла к очень долгому процессу вывода на рынок нового велосипеда. Сегодня в год изготавливается около миллиона композитных рам. И теперь с помощью нашей технологии вы можете предлагать очень индивидуальные рамки по запросу.
Наша цель - продолжать создавать новые приложения, использующие эту возможность.
Является ли индивидуальный подход к производству масштабируемой бизнес-моделью?
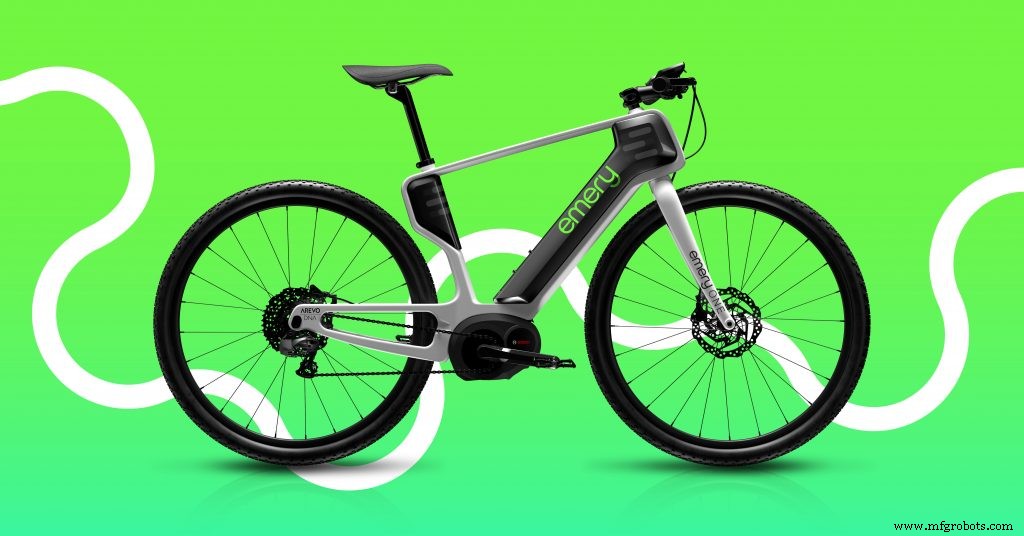
Когда речь идет о велосипедах, индивидуальная настройка очень ценится. Каждый человек уникален. Вы быстрее устаете, когда едете не на велосипеде, который разработан, настроен или отрегулирован для вашей рамы. Так что байк на самом деле является хорошим средством демонстрации ценности индивидуальной настройки.
Существует целая тенденция к микромобильности и возможности передвигаться на очень удобном транспортном средстве. Велосипед представляет это. Во многих странах это основной вид транспорта.
Если вам нужна настройка формы и функций, вы не можете сделать это массовым способом. Но с помощью нашей технологии потребитель может спроектировать раму, а наше программное обеспечение может гарантировать, что спроектированная им рама структурно надежна.
Затем они могут отправить его в наши отделения для 3D-печати, чтобы изготовить велосипед по запросу. Таким образом, процесс от идеи до производства очень упрощен.
Какие еще приложения вы видите в своей технологии?
Сегодня мы сосредоточимся на велосипедах и мобильных приложениях. Это приложения, которые могут использовать преимущества предлагаемого нами ценного предложения, которое заключается в очень легком весе, высоком соотношении прочности и веса и индивидуализированных продуктах.
Если вы посмотрите на отрасли, действительно важно улучшить производительность в спортивном секторе, а также в автомобильной, энергетической и аэрокосмической отраслях.
У нас есть множество различных приложений, над которыми мы работаем, для которых требуются легкие, высокопроизводительные и широкие возможности настройки. И это ключевые области, в которых можно использовать наши технологии.
Как робототехника вписывается в вашу технологию?
Когда вы смотрите на 3D-печать, большая часть 3D-печати основана на слоях, и слои размещаются в плоскостях X и Y. Если посмотреть на свойства деталей, изготовленных с помощью этого процесса, они, как правило, страдают в направлении Z.
Мы используем полностью сочлененный шестиосевой робот для укладки углеродного волокна в направлениях X, Y и Z. Мы устранили проблему прочности по оси Z, которая мешает другим многослойным технологиям, потому что мы можем укладываться в направлении Z. Это одна из уникальных возможностей нашей технологии осаждения. Робототехника играет в этом большую роль.
Второй аспект - это масштаб деталей, которые можно распечатать. Сегодня большинство систем относятся к определенному диапазону сборки, что означает, что вы можете изготавливать детали только определенного размера. Если вы превысите определенный размер, деталь нужно будет разрезать на узлы, чтобы получить более крупную конструкцию.
Наши роботы обеспечивают неограниченные возможности сборки, потому что мы можем разместить наших роботов на портале для изготовления деталей для аэрокосмической отрасли. В то же время тот же робот может сделать велосипед. Радиус действия наших роботов составляет четыре метра в высоту. По сути, он очень масштабируемый с точки зрения предоставления нам такого большого конверта для печати.
Как бы вы описали текущее состояние рынка композитной 3D-печати? Насколько развита эта технология?
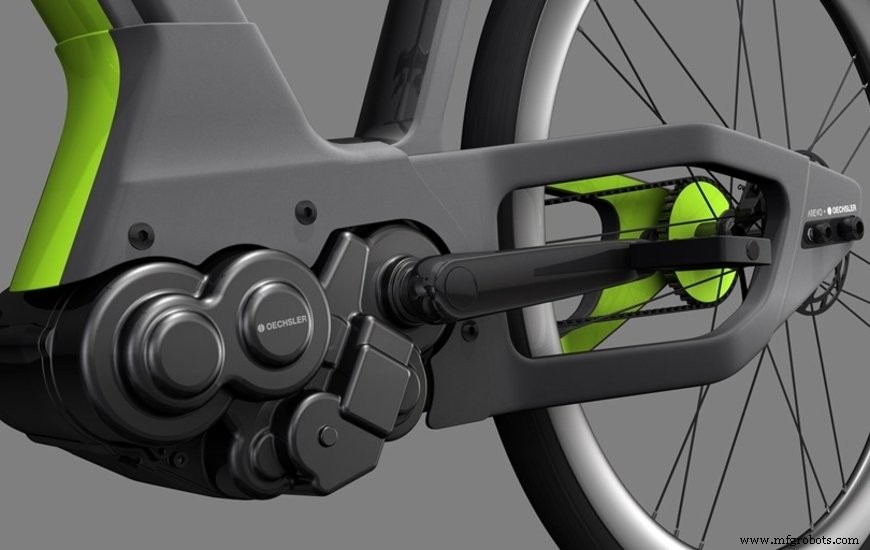
В композитной промышленности уже довольно давно используются добавки. Просто сложность геометрии была очень ограничена тем, что вы могли уместить на пресс-форме, например, детали с очень малой кривизной. Кроме того, слои обычно укладываются вручную, в результате чего получается довольно ограниченная по сложности деталь.
Итак, композитная 3D-печать существует уже давно. Но теперь такие вещи, как автоматизированная робототехника или системы мехатроники, которые автоматизируют размещение волокна, позволяют создавать более сложные геометрические формы.
Есть много компаний, использующих другой подход к автоматизации производства композитов, от различных типов полимерных систем до различных вариантов использования.
И это очень полезно.
В целом, я считаю, что сектор композитной 3D-печати находится в хорошем состоянии, и здесь лидирует Arevo.
С какими проблемами сталкивается отрасль, будь то 3D-печать в целом или композитная 3D-печать в частности?
Я думаю, что самые большие проблемы связаны с отсутствием доступных программных инструментов, чтобы изучить возможности добавления аддитивов. Вы привыкли изучать традиционные технологии производства, а нас научили использовать традиционные методы производства.
Люди часто начинают с деталей, которые были изготовлены традиционным способом, и хотят принудительно подогнать к ним добавку, но это не всегда совпадает.
Но когда вы действительно используете то, что вы можете сделать с добавкой, будь то металл, композит или полимер, с точки зрения уникальности и сложности, вам действительно понадобятся инструменты, которые проведут вас через этот процесс и проинформируют дизайнеров. и инженеры.
Каким вы видите развитие отрасли в следующие пять лет?
Это очень обнадеживает. С момента основания Arevo мы всегда были сосредоточены на производстве деталей.
Когда вы смотрите на отрасль сегодня, действительно приятно видеть, что все говорят о производственных запчастях. Это общая тема.
В будущем я ожидаю, что отрасль также начнет говорить о качестве и масштабируемости. Когда вы начнете производить продукцию, ее производство в больших масштабах и с большей повторяемостью станет ключевым направлением для отрасли.
В настоящее время обеспечение качества деталей и процессов - важная тема для аддитивного производства. Каковы подходы Arevo к этому?
Одним из ключевых достижений Arevo стала технология лазерного напыления.
Кроме того, мы используем алгоритмы машинного обучения, которые могут выполнять проверку на месте. У нас есть набор датчиков, и мы можем проводить инспекцию на месте детали в процессе ее изготовления.
Это позволяет нам получать очень однородный печатный материал с пустотами менее 1%. Вы можете сделать поперечный разрез детали, и когда вы подберете его под микроскопом, вы увидите очень однородный печатный материал.
Это означает очень высокое качество деталей, когда вы работаете с очень требовательными приложениями, такими как аэрокосмическая промышленность. Этот контроль качества на месте в сочетании с нашим мониторингом с обратной связью - это то, что позволяет нам обеспечивать стабильное и предсказуемое качество.
Что ожидает Arevo в следующие 12 месяцев?
В следующие 12 месяцев мы сосредоточимся на производстве. С тех пор, как мы запустили байк, спрос на него больше, чем мы можем удовлетворить. Наша цель на следующий год - продолжить запуск новых приложений, но в основном для увеличения наших мощностей для удовлетворения текущего спроса.
Чтобы узнать больше об Arevo, посетите: https://arevo.com/
3D печать
- Интервью с экспертом:генеральный директор Nanoe Гийом де Калан о будущем керамической 3D-печати
- Интервью с экспертом:президент Ultimaker Джон Кавола о будущем 3D-печати
- Интервью с экспертом:соучредитель Nano Dimension Саймон Фрид о развитии 3D-печати для электроники
- Интервью с экспертом:соучредитель Carbon Филип Дезимоун о переходе к массовому производству с помощью 3D-печати
- Интервью с экспертом:Rush LaSelle от Jabil о будущем аддитивного производства
- Интервью с экспертом:Грег Полсен из Xometry о подъеме бизнес-модели "Производство как услуга"
- Интервью с экспертом:вице-президент VELO3D по технологическому партнерству по расширению возможностей 3D-печати…
- Интервью с экспертом:Джон Барнс, основатель Barnes Group Advisors, о будущем аддитивного производства
- Представляем первый в мире смартфон из углеродного волокна
- Toray создает первое в мире пористое углеродное волокно с наноразмерной сплошной структурой пор