Каркас из углепластика прототипов WMG для демонстрационного автомобиля с очень легким рельсовым транспортом (VLR)
Revolution VLR - это консорциум в Великобритании, возглавляемый Transport Design International Ltd (TDI, Стратфорд-на-Эйвоне), который в 2013 году получил финансирование на разработку рельсовой тележки с автономным приводом и встроенной гибридной силовой установкой. TDI считает, что разработка более легких «легкорельсовых» транспортных средств, то есть очень легкорельсового транспорта (VLR), имеет решающее значение для создания экологичного общественного транспорта следующего поколения. На втором этапе проекта VLR полный демонстрационный автомобиль с дизельными аккумуляторами длиной 18 метров будет доступен для испытаний в 2020 году.
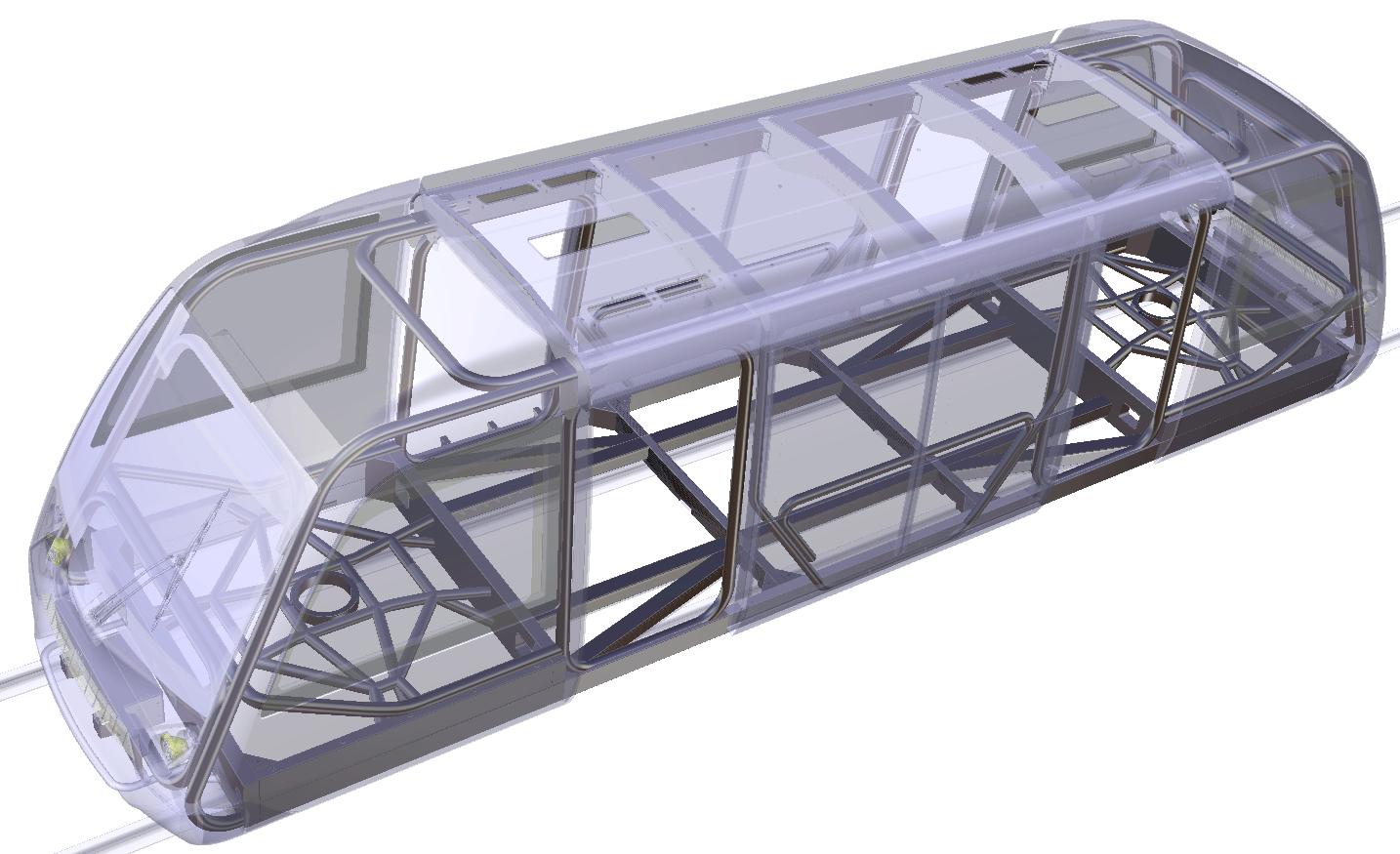
Демонстрационный образец Very Light Rail (VLR) представляет собой тележку длиной 18 метров со встроенной гибридной силовой установкой с дизельным аккумулятором и легким шасси из композитных труб с оплеткой. ИСТОЧНИК | Уорикский университет.
WMG из Уорикского университета, первый член Revolution VLR, разработала раму из армированного углеродным волокном пластика (CFRP) для этого демонстрационного автомобиля VLR. WMG является давним сторонником композитов с такими инициативами, как Национальный центр автомобильных инноваций, Центр инженерии материалов и Международный институт производства нанокомпозитов. Партнерами WMG по проекту «BRAINSTORM VLR» являются TDI, британская правительственная компания Innovate UK (которая финансирует композиты), разработчик легких структурных композитных компонентов Far Composites и Composite Braiding. Каркас изготовлен из ряда плетеных труб из термопластичного композитного материала, которые легко собираются с помощью клеевого соединения и простой сварки.
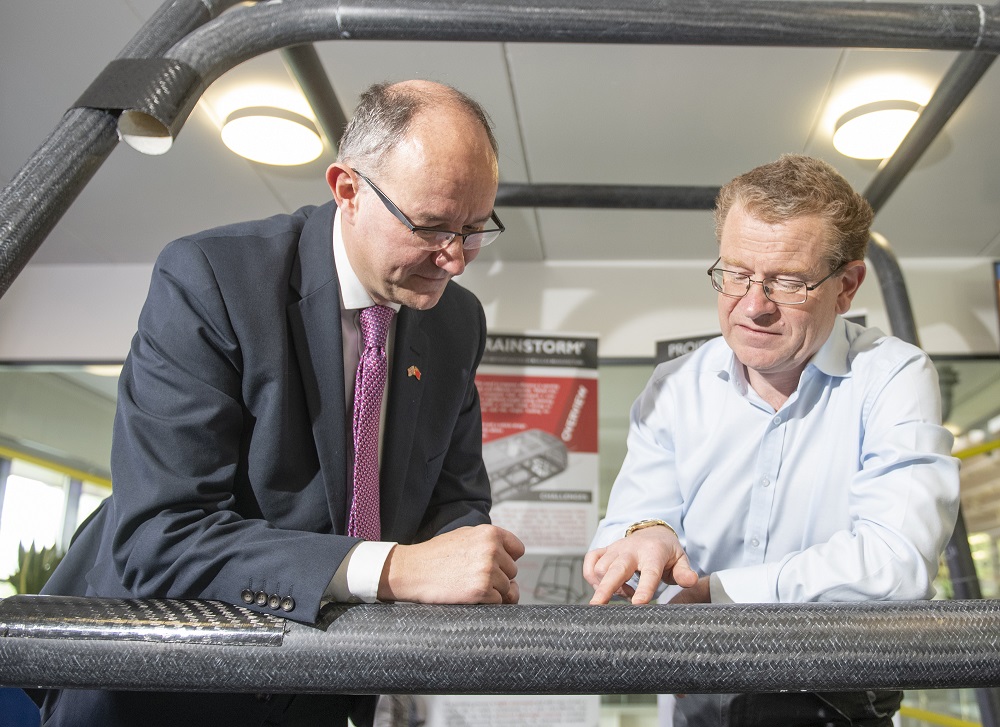
В прототипе / демонстрационном автомобиле VLR будет использоваться шасси с пространственной рамой, изготовленное из плетеных труб из термопластичного композитного материала, армированного углеродным волокном, которые легко собираются с помощью клеевого соединения и простой сварки. ИСТОЧНИК | Уорикский университет.
Наружный диаметр трубы остается неизменным, с различными требованиями к нагрузке и креплению за счет изменения толщины стенок. Это снижает затраты на инструмент и означает, что соединения могут быть стандартизированы. Плетение обеспечивает высокоавтоматизированный производственный процесс (скорость только армирования может превышать 1 милю в день), а также индивидуальный набор материалов, включая другие волокна (например, стекло, арамид, термопласт) и термопластичные матричные материалы из недорогого полипропилена. до высококачественного полиэфирэфиркетона (PEEK). Тем временем WMG продемонстрировала полный цикл формования, который можно сократить до менее чем пяти минут, что подчеркивает потенциал этого доступного процесса для приложений с большими объемами.
По словам Дэвида Гудвина, технического менеджера Far-UK, термопласты также подходят для вторичной переработки. «С композитами вы можете сэкономить много веса, что, очевидно, привлекательно для эксплуатации [железнодорожного] вагона, - начинает он, - но с традиционными композитами в конце срока службы вагон просто помещают на свалку, которая не идеален. Эта [конструкция] позволяет утилизировать кузов автомобиля, когда он в конечном итоге выходит из строя, или, в качестве альтернативы, если он подвергается удару, и его часть необходимо отремонтировать и заменить ».
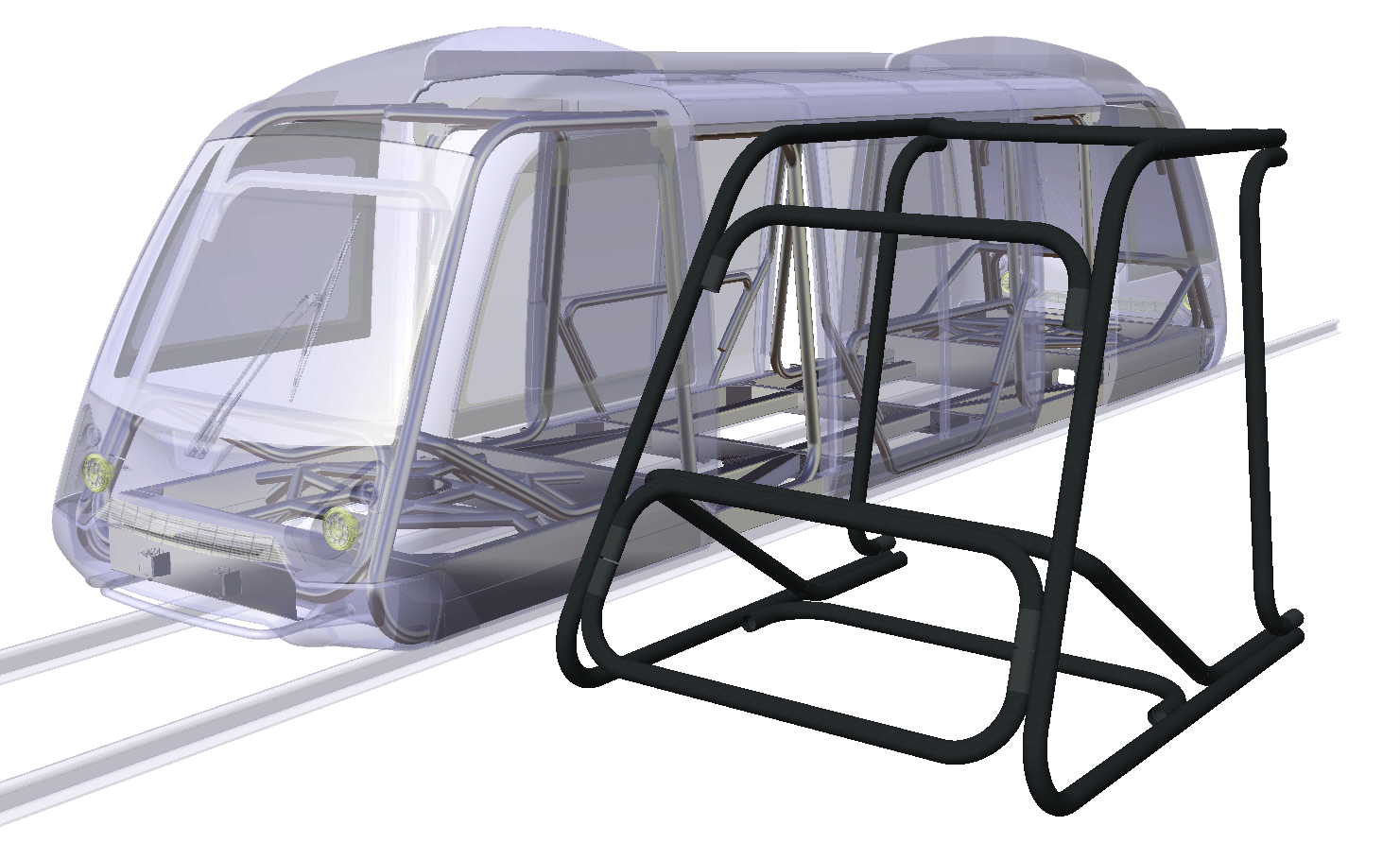
Уорикский университет
Конструкция трубчатого шасси с пространственной рамой также помогает в этом подходе, позволяя просто удалить любые поврежденные трубы и заменить их новыми или отремонтированными. «Наше партнерство в области исследований BRAINSTORM VLR позволило добиться значительной экономии веса, что позволило службам VLR разместить больше пассажиров, снизив при этом энергию, необходимую для движения транспортного средства, и весовую нагрузку, которую он будет оказывать на рельсы и дорожное покрытие», - поясняет д-р Даррен Хьюз. доцент кафедры материалов и производства Университета Уорика WMG. «Эта технология также гарантирует, что транспортное средство будет прочным для долгого срока службы, легко ремонтируемым в случае аварии и достаточно прочным, чтобы защитить пассажиров на борту».
«Проект BRAINSTORM кажется настоящим шагом вперед для команды Far Composites», - говорит директор и генеральный менеджер Far-UK Линдон Сандерс. «Возможность использовать отраслевой опыт TDI для оттачивания принципа нового типа конструкции кузова для транспортных средств - это здорово. Добавьте к этому совместную работу с Composites Braiding и WMG, чтобы превратить это мышление в физический демонстратор, чтобы показать, как это будет на практике, было действительно мощным. Теперь это больше, чем хорошая идея, это открывает глаза игрокам отрасли, которые могут это увидеть, потрогать и даже взять в руки ».
Смола
- Сверхлегкие композиты TPE для обуви
- Проектирование для автоматизированного производства композитных материалов для малосерийных авиационных к…
- Перерабатываемые, ремонтируемые и перерабатываемые эпоксидные смолы для композитов
- Объединение диэлектрических измерений переменного и постоянного тока для мониторинга отверждения композит…
- Марсоход Perseverance делает один шаг к композитам на Марсе
- RS Electric Boats выбирает Norco для изготовления композитов
- Высокотемпературная термопара PEEKSense для отверждения композитов PEEK
- Композиты Solvay, выбранные для гоночного катамарана
- Двери из термопласта впервые для автомобильных композитов
- Ashland сотрудничает с Velox для распространения композитов во Франции