Устранение барьеров для облегчения судов с помощью композитов
Композиты из полимеров, армированных стекловолокном и углеродным волокном (GFRP и CFRP), использовались для строительства морских судов на протяжении десятилетий, включая многочисленные 40-60-метровые минные охотники и даже более крупные суда, в том числе 72-метровый корвет Visby Class ВМС Швеции и 75-метровая парусная яхта Mirabella V . 141-метровая моторная яхта Swift 141 (переименован в Яс ) представляет собой голландский стальной фрегат, реконструированный с использованием стеклопластика и углепластика в подпалубных подошвах и трехпалубной надстройке (см. «От фрегата до роскошной гигаяхты»), включая соединение палубы из композитного материала и стали.
И все же композиты в судостроении используются редко. Это в основном связано с правилами безопасности жизни на море (SOLAS), изданными Международной морской организацией (IMO, Лондон, Великобритания), которые требовали, чтобы коммерческие суда были построены из стали до тех пор, пока MSC / Circ. 1002 было выдано в 2002 году, разрешая альтернативные конструкции.
«Постановление требует проведения анализа рисков, показывающего, что альтернативный дизайн и конструкция эквивалентны стали», - объясняет Стефан Пабоф, глава отдела композитных материалов классификационного общества Bureau Veritas (BV, Нант, Франция). «Этот процесс долгий, дорогостоящий, и окончательное решение может быть отрицательным». Таким образом, хотя композиты предлагают много преимуществ для судостроения, проблемы пожарной безопасности и нормы создают препятствия для их использования.
Тем временем судовладельцы, операторы и строители ищут решения для повышения устойчивости, включая более легкий вес для снижения расхода топлива, выбросов парниковых газов и осадки судов - последнее для мелких внутренних водных путей. Также привлекательной является присущая композитам коррозионная стойкость, что сокращает потребность в техническом обслуживании.
В 2017 году ИМО выпустила MSC.1 / Circ., Новый набор руководящих принципов по использованию композитов FRP на коммерческих судах. По мере приближения оценки ИМО этих руководящих принципов в 2021 году происходит невероятная активность. Два европейских консорциума, FIBRESHIP и RAMSSES, при поддержке европейской сети для облегченных приложений в море (E-LASS), состоящей из 378 участников, возглавляют эту волну демонстрационных проектов, которые включают композитные палубы, рули, корпуса, модульные кабины и надстройки, патч ремонт сталей и сварных соединений композитов с сталью. Вместе они стремятся преодолеть препятствия для строительства легких композитных судов, не только демонстрируя огнестойкость и характеристики конструкции больших конструкций и судов в целом, но также разрабатывая новые маршруты для сертификации и методов производства, новые технологии соединения и инструменты проектирования. Они также обмениваются информацией через постоянные семинары, хранилища знаний и базы данных материалов / проектов. Для морских композитов может открыться новый рынок, но какие решения для этого потребуются?
ФИБРЕШКА и РАМССЕС
FIBRESHIP и RAMSSES были запущены в июне 2017 года при финансовой поддержке программы Horizon 2020 Европейского Союза. FIBRESHIP состоит из 18 членов и будет работать до мая 2020 года, в то время как RAMSSES будет состоять из 36 членов и закончится в мае 2021 года. Оба включают компании из всей цепочки поставок, охватывающей центры исследований и разработок, университеты, поставщиков материалов и технологий, производителей запчастей, судостроительные и инженерные фирмы, верфи, судовладельцы и классификационные общества. Последние несут ответственность за разработку конкретных правил для постройки отдельных кораблей на основе общих рекомендаций ИМО. Они уполномочены государствами флага (каждое судно носит флаг страны) проверять постройку судов и обеспечивать соблюдение этих правил. «Важно, чтобы все заинтересованные стороны и конечные пользователи были вовлечены», - говорит Альфонсо Хурадо, руководитель отдела исследований и разработок Tecnicas y Servicios de Ingeniería (TSI, Мадрид, Испания) и координатор проекта FIBRESHIP.
«Основная цель FIBRESHIP - развитие возможностей проектирования и производства больших морских судов (более 50 метров в длину) с меньшим весом», - продолжает Хурадо. «Это также основная мотивация для моей компании». TSI проектирует композитную конструкцию рыболовно-исследовательского судна (FRV) общей длиной 85 метров (LOA), которое будет служить в качестве демонстрации и на данный момент обеспечивает снижение веса конструкции почти на 70% по сравнению со стальным эталонным судном. «Это потрясающе - это реальная возможность помочь судоходному сектору», - говорит он. 20-тонная секция этого FRV размером 11 на 11 на 8,6 метра (см. Начальное изображение) была построена партнерской верфью iXblue в Ла-Сиота, Франция, и выставлена на втором открытом семинаре FIBRESHIP в июне 2019 года (см. Публикацию новостей с видео изготовляемого демонстратора).
Хурадо объясняет, что FRV - это первый из трех универсальных композитных корпусов, разрабатываемых FIBRESHIP. Следующие два - это контейнеровозы длиной 260 метров и ROPAX длиной 204 метра, последний сочетает в себе грузоподъемность буксируемого судна с пассажирскими средствами парома. «FRV был выбран в качестве демонстратора, потому что он меньше по размеру и имеет более традиционную морскую конструкцию и, следовательно, наиболее целесообразен для строительства в ближайшем будущем», - говорит он. «Судовладельцы также проявили реальный интерес к такому судну». Между тем, у RAMSSES 13 незавершенных демонстраций, 10 из которых включают композиты, а также разрабатывается полностью композитное судно.
Хурадо отмечает, что компании, участвующие в этих проектах, видят потенциал в таких новаторских конструкциях и новых легких продуктах, которые обеспечат конкурентное преимущество их предприятиям, а также судоходной отрасли каждой страны. Но добиться прогресса одними лишь крупными демонстрантами не удастся. «У нас также должна быть поддержка со стороны регулирующих органов», - добавляет он. «Первый шаг - привлечь ИМО и адаптировать текущие правила СОЛАС к новым требованиям и требованиям судоходной отрасли. Без этого мы не сможем двигаться дальше, потому что страховые компании не будут гарантировать судам, армированным волокном, композитным материалам, если они не соответствуют минимальным требованиям и, например, сертификату безопасности ».
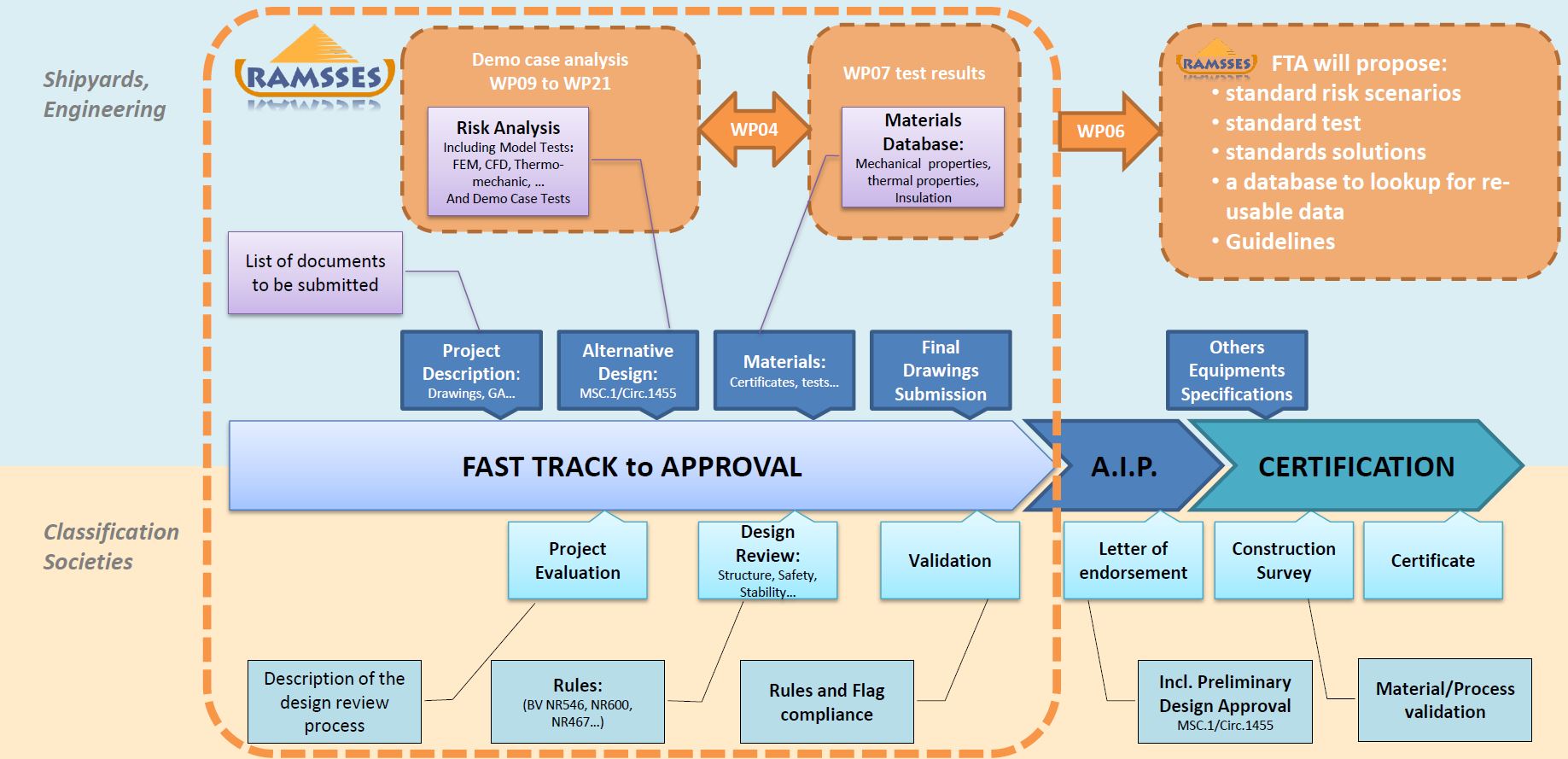
Предлагаемый подход Fast Track to Approval (FTA) для сертификации композитных материалов на коммерческих судах, разрабатываемый в рамках проекта RAMSSES, представленный на семинаре E-LASS в июне 2019 года (Виго, Испания). Источник | РАМССЕС и Стефан Пабёф, Bureau Veritas
«FIBRESHIP придерживается долгосрочного подхода, разрабатывая новые правила, в то время как RAMSSES разрабатывает краткосрочный подход, используя существующие правила и методы», - объясняет Пабоф из BV, которая является единственным партнером классификационного общества в RAMSSES и одним из трех в FIBRESHIP наряду с Lloyd's Register (Лондон, Великобритания) и RINA (Генуя, Италия). «В RAMSSES мы разрабатываем процедуру Fast Track to Approval (FTA), основанную на повторном использовании данных проекта для стандартизации тестов и предоставления рекомендаций по проектированию и утверждению». Эта процедура должна быть простой и удобной для чтения верфям, военно-морским архитекторам и поставщикам. Ускорение по сравнению с текущим процессом будет обеспечено за счет поддержки, разрабатываемой в демонстрационных проектах RAMSSES, включая:
- база данных предварительно утвержденных решений и результатов испытаний материалов, чтобы избежать повторных испытаний,
- сценарии риска пожара, охватывающие ряд аналогичных приложений, чтобы ограничить количество и степень оценки риска, и
- инструменты анализа и моделирования, включая числовые или статистические модели, которые в будущем могут заменить физические испытания.
«В FIBRESHIP мы работаем с Lloyd’s Register и RINA над разработкой набора предписывающих правил специально для больших судов, построенных из композитов», - продолжает Пабоф. «Для структурных характеристик мы определяем новые коэффициенты безопасности для местных и глобальных нагрузок». RAMSSES и FIBRESHIP также предлагают заменить существующие уровни огнестойкости, такие как A60, B30 и B15, новым условным обозначением REIxx, где R обозначает огнестойкость (несущая способность при пожаре), E обозначает целостность (предотвращение распространения дыма и пламени). ) и я определяю противопожарную изоляцию. «Цель состоит в том, чтобы лучше согласовать рейтинги огнестойкости конструкций с используемыми композитными материалами», - объясняет Пабоф.
Кроме того, эти два проекта также связаны с оценкой рисков, связанных с распространением пламени, образованием дыма и риском возникновения пожара в пространстве происхождения, а также на глобальном уровне безопасности судов. «Что касается пожарных характеристик, мы разрабатываем подход локальной эквивалентности, который касается пожарной безопасности на местном уровне, исходя из огнестойкости переборок и других структурных элементов в каждом пространстве судна», - говорит Пабоф. «Второй подход, глобальная эквивалентность, касается пожара на уровне судна с учетом всех систем (активная и пассивная противопожарная защита, обнаружение, эвакуация и т. Д.), Которые влияют на пожарную безопасность судна в целом, а не только каждой из них. разделенное пространство ».
«Более широкое внедрение композитов в судостроение будет происходить постепенно», - говорит он. «Он начнется с небольших деталей, таких как палубы и надстройки, или оборудования, такого как валопроводы и гребные винты, а затем перейдет к строительству целых судов, которые сначала будут в основном судами специального назначения, такими как суда для исследований и сейсмических испытаний, а также высокоскоростные суда. патрульный катер ».

Рис. 1 80-метровое композитное судно RAMSSES
Damen Shipyard (DSNS) разрабатывает полностью составное морское патрульное судно в рамках проекта RAMSSES. Полномасштабный демонстрационный образец корпуса корпуса размером 6 на 6 на 3 метра будет построен в 2020 году с использованием вливания смолы в сотрудничестве с InfraCore Company (ICC) и Airborne International (AIR). Источник | Верфь Damen и РАМССЕС
Демонстраторы цельнокомпозитных судов
В дополнение к 85-метровому FRV, демонстрируемому FIBRESHIP, в RAMSSES разрабатывается морское патрульное судно длиной 80 метров, которое станет первым полностью составным кораблем СОЛАС. Эта работа, проводимая под руководством Damen Shipyard Group (Gorinchem, Нидерланды), развивает результаты ее проекта Bluenose, начатого в 2014 году. В рамках рабочего пакета RAMSSES 17 компания Damen ведет демонстрацию полной конструкции размером 6 на 6 на 3 метра. «Масштабная композитная часть корпуса этого судна, сделанная с использованием вакуумной инфузии», - объясняет Маттиас Краузе, инженер-исследователь Центра морских технологий (CMT, Гамбург, Германия) и со-координатор проекта RAMSSES совместно с CETENA (Генуя, Италия). «Evonik разработала новую смолу для этой секции корпуса демонстратора и изготовила 6-метровую оснастку. Damen также работает с Airborne International (Гаага, Нидерланды), поставщиком авиастроительной отрасли, который также построил большие инфузионные конструкции ». Evonik (Эссен, Германия) объяснил свою роль в улучшении ударопрочности и усталостных характеристик корпуса, наполненного стекловолокном / винилэфиром.
Еще одним партнером в этом демонстраторе является компания InfraCore Co. (Роттердам, Нидерланды), которая разрабатывает новые приложения для технологии InfraCore, используемой дочерней компанией FiberCore Europe (Роттердам) в более чем 1000 композитных мостов и шлюзовых ворот по всему миру. «Изначально мы присоединились к Damen в этом проекте, чтобы построить вертолетную площадку грузоподъемностью от 12 до 14 тонн», - объясняет менеджер по эксплуатации InfraCore Лоран Морель. «Сейчас мы работаем с ними над созданием палубы, переборок и конструкции корпуса. Мы будем использовать как горизонтальную, так и вертикальную инфузию, чтобы создать секцию корпуса за один раз. Пока мы достигли высоты 9,8 метра ». После завершения этот демонстрационный образец будет протестирован на конструктивные и противопожарные характеристики, а результаты и извлеченные уроки будут учтены в новых модулях FTA RAMSSES.
Легкие колоды
Композитные материалы уже были продемонстрированы на первом самоходном автовозе с использованием композитной грузовой платформы, разработанном и построенном Uljanik Group (Пула, Хорватия) в рамках рабочего пакета 14 RAMSSES (см. «Низкий вес на высоком морей »), а также легкую солнечную палубу для речного круизного лайнера длиной 110 метров (см.« Композитная палуба снижает осадку речного судна ») и композитную твин-деку для 200-метрового грузового танкера. «Твин-дек - это съемная платформа, которую можно установить, чтобы разделить грузовой отсек для перевозки различных типов грузов», - объясняет Арнт Фроде Бревик, менеджер компании Compocean (Sandvika, Норвегия), поставщика композитных решений, созданных на основе добычи нефти и газа. промышленность.
«В течение нескольких лет мы работали с Oshima Shipbuilding (Нагасаки, Япония) и DNV GL над разработкой легкой твин-палубы с целью снижения веса на 50% по сравнению со сталью», - говорит Бревик. В результате был создан прототип стеклопластика размером 9 на 2 метра, который был испытан на ударные и максимальные нагрузки, а затем выставлен на выставке NOR-Shipping 2017.
В настоящее время Compocean расширила эту разработку до нового проекта с Oshima, DNV GL и судовладельцем Masterbulk Pte Ltd. (Сингапур) по созданию полномасштабного прототипа композитной твин-платформы размером 27 на 12 метров, которая будет установлена в следующем году и протестирован до конца 2021 года.
«Осима стремился оптимизировать товары, чтобы сократить расходы на топливо и погрузочно-разгрузочные работы», - говорит Бревик. «Несмотря на то, что на каждом корабле не так много подростковых палуб, с этого легко начать при внедрении новых материалов, потому что они не являются частью основной конструкции корабля». Конструкция основана на стекловолоконной пластине, пропитанной полиэфирной смолой, с элементами жесткости под ней. «Мы используем сочетание ± 45 градусов, 0 градусов и 0 градусов / 90 градусов для всех частей, но в разных соотношениях. Конструкция палубы также должна иметь множество точек крепления для фиксации груза ». Пластина будет прикреплена к элементам жесткости шляпки с помощью структурного клея, а болтовые соединения будут использоваться в сочетании с системой крепления. Стальной концевой кронштейн на болтах соединит композит со стальной конструкцией корабля. «В будущем мы также будем развивать дизайн с чисто клеевыми соединениями», - добавляет Бревик.

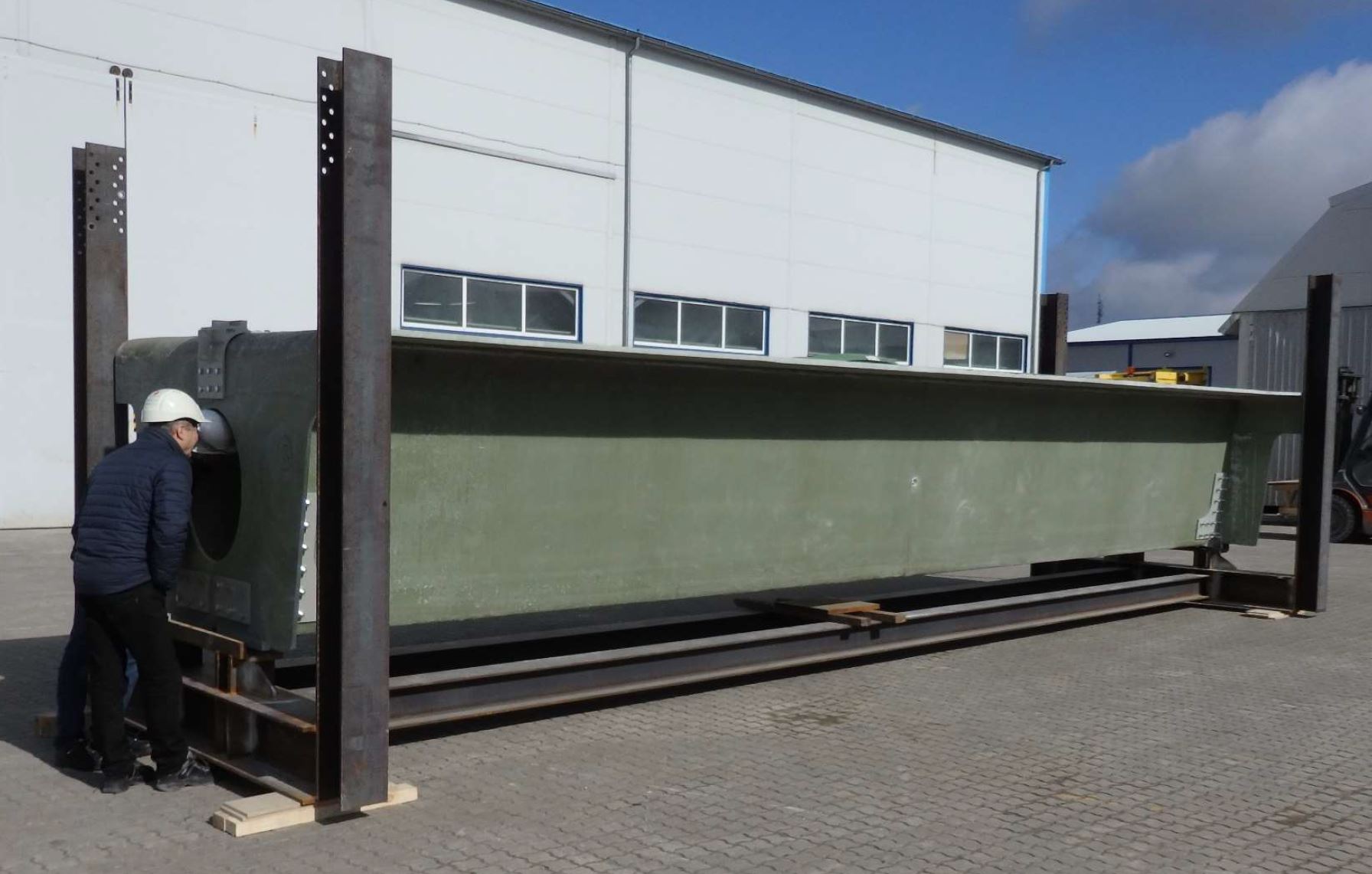
Рис. 2 композитных анимационных ролика
Новый 65-тысячный грузовой контейнеровоз Oshima Shipbuilding с открытым люком будет использовать прототип композитной твин-палубы Compocean, которая экономит 50% веса по сравнению со сталью и будет состоять из нескольких усиленных арматурных элементов жесткости (вставка), прикрепленных к верхней пластине FRP с помощью болтовых соединений от композит к стальной конструкции корабля. Источник | Compocean и DNV GL
Получив окончательное одобрение DNV GL на полномасштабную конструкцию твин-дек, Compocean изготовила формы и приступила к производственным испытаниям. «Полномасштабная композитная палуба будет построена партнером в Малайзии, который доставит ее на судно на барже», - говорит Бревик. Следующим шагом является стремление к гораздо большему снижению веса, например, композитные люки поверх грузовых отверстий (плоские пластины поверх зеленых «ящиков» на изображении корабля выше). «На этом типе авианосца семь больших люковых крышек», - отмечает он. «Чтобы получить их одобрение DNV GL, придется столкнуться с некоторыми новыми проблемами, но успех с подростковой декой поможет».
Легкая надстройка, модульные кабины
RAMSSES имеет шесть рабочих пакетов, ориентированных на композитные надстройки и компоненты, используемые над главной палубой, большинство из которых с демонстрационными материалами и результатами испытаний, которые будут представлены в 2020 году. Рабочий пакет 16, возглавляемый Naval Group (Париж, Франция), демонстрирует легкий композитный модуль надстройки соединен со стальной палубой. Береговой демонстратор представляет собой стандартный блок для морского патрульного судна. «Судостроение из металлических материалов основано на строительстве из блоков для сокращения времени и затрат», - объясняет Хурадо. «Создание таких блоков с использованием композитов связано с проблемами, связанными с необходимостью использования больших форм, а также с технологиями соединения и требованиями безопасности соединений. Компания Fibreship изучила это и разработала некоторые рекомендации по соединению блоков на основе композитов, включая последовательность сборки ». В RAMSSES Naval Group исследовала три типа сэндвич-структур, включая сердцевину из GF / полиэстера / бальзы, сердцевину из FR из эпоксидной смолы / ПЭТ и сердцевину из пенопласта, армированного волокном GF / полиэстер / 3D. Компания также разрабатывает систему мониторинга состояния конструкций (SHM) внутри соединительных и композитных панелей.
Рабочий пакет 18 под руководством Chantiers de l’Atlantique (Сен-Назер, Франция) разрабатывает модульное решение для пассажирских кабин. «Обычно они поставляются без пола, потому что они приварены к стальной палубе корабля», - говорит Краузе. «Идея состоит в том, чтобы сделать их из композитных материалов, предварительно оборудованных всеми вспомогательными системами, такими как отопление, воздух, электричество и т. Д. Включая композитный пол, их можно было бы вставить в стальной каркас (например, ящик), а не приваривать к стене. твердая стальная дека, что значительно снижает вес ». Хотя в рамках проекта проводится оценка композитных материалов для сокращения времени производства и сборки стен, потолков и ванных комнат, поскольку замена стального настила позволит сэкономить примерно 125 килограммов на квадратный метр, композитные полы являются основным направлением деятельности. Компания Hutchinson (Париж, Франция) предложила использовать композитную пену ZALTEX, армированную минеральным волокном, которая выдерживает температуру от -190 ° C до 1000 ° C.
Рабочий пакет 13, возглавляемый судостроительной компанией Meyer Werft (Папенбург, Германия), также направлен на повышение эффективности процессов сборки, но с упором на переборки. . Цель состоит в том, чтобы построить два демонстратора - один на берегу, один на море (морские испытания), где композитные стены будут соединены со стальными каркасными конструкциями, а затем подвергнуты 80 механическим испытаниям. Партнер проекта InfraCore провел анализ для определения требований к тепло- и шумоизоляции, собственной частоте (вибрации), деформации и максимальной ширине и высоте для композитных стен. «Нас попросили разработать многофункциональные внутренние и внешние стены», - объясняет Морел из InfraCore. «Чтобы сэкономить время, деньги и вес, мы должны объединить изоляцию и хорошую внутреннюю отделку с легкой структурной панелью. На каждом круизном лайнере таких стен до 6800 квадратных метров. У нас есть возможность разместить их на борту круизного лайнера в середине 2020 года, и это может быть первая одобренная СОЛАС композитная стена на круизном лайнере во всем мире ».
В рабочем пакете 10 Podcomp (Öjebyn, Швеция) разрабатывает альтернативную внутреннюю / внешнюю панель с использованием биопродукции . композиты, которые должны быть огнестойкими и иметь конкурентоспособную цену. Были исследованы три концепции сэндвичей на основе препрега GF / полифурфуриловый спирт (PFA) от Composites Evolution (Честерфилд, Великобритания) и различных материалов сердцевины. Только одна концепция прошла испытания коническим калориметром и другие испытания на огнестойкость, проведенные шведскими научно-исследовательскими институтами RISE (Бурос). Сейчас его оптимизируют по весу и стоимости.
После опробования алюминия и сварки трением с перемешиванием, Baltic Workboats (Насва, Эстония) теперь продвигается вперед с композитными материалами для разработки предварительно смонтированных усиленных панелей для рубки / надстройки алюминиевых рабочих лодок (рабочий пакет 15). Будет продемонстрирован дизайн панели, соединение с другими панелями и остальной конструкцией рубки, процедуры структурного анализа и изоляционные решения, а также методы установки на борту.
Другое решение для легкой надстройки разрабатывается BaltiCo (Хоэн-Луцков, Германия), производителем судового оборудования, у которого есть новый стартап по строительству готовых лодок с использованием размещенного роботом углеродного волокна, обернутого вокруг ферменной конструкции. «Вы строите каркас конструкции, которую хотите создать, размещая поперечную структуру или ребра из стеклопластика примерно через каждые полметра, а затем робот наматывает вокруг него углеродное волокно», - объясняет Краузе. Наша цель - создать сверхлегкую модульную систему, использующую высокоавтоматизированный процесс. Демонстрация будет включать производство и сборку двух самонесущих модулей корпуса и палубы в легкий катамаран на солнечной энергии, не соответствующий требованиям СОЛАС.
Сварные соединения FRP-сталь
«Мы верим, что будущее судостроения заключается в объединении композитов FRP, стали и других материалов в гибридные конструкции», - говорит д-р Ларс Молтер, 10-летний ветеран CMT. «Мы рассмотрели склеивание, но не существует стандартизированной конструкции стыка, которую можно было бы использовать на всех судах, и нет общих правил о том, как применять склеивание на судах СОЛАС. Кроме того, вы должны контролировать окружающую среду и процесс связи ». Он отмечает, что это сложно из-за сварки и резки, которые обычно преобладают в строительстве верфей. «Мы спросили DNV GL, что они одобрили бы для соединений из разнородных материалов», - говорит Молтер. «Они сказали, что первичная структура обычно требует механического крепления; чистое соединение было бы нелегко сертифицировать без дублирующих крепежных элементов ».
Молтер и CMT ответили финансируемым Германией проектом FAUSST (Стандарт волокна и стали), в ходе которого была разработана гибридная трикотажная ткань, в которой 100% стекловолокно переходит в 100% стальное волокно. Последний приваривается к стальному соединителю (например, плоской пластине, прямоугольному профилю и т. Д.), Который затем легко вваривается в стальную конструкцию корабля (рис. 3). Конец стекловолокна соединяется с композитной структурой с помощью вливания смолы. «Эта конструкция соединения обеспечивает 100% неразрушающий контроль, потому что вы можете использовать УЗИ (ультразвук) или рентгеновское излучение на сварном шве», - говорит Молтер. Компания FAUSST провела механические, экологические и усталостные испытания этого типа соединения, а также получила принципиальное одобрение классификационных обществ, но еще многое предстоит сделать, чтобы превратить эту технологию в коммерческий продукт. Таким образом, Молтер покинул CMT и в 2018 году основал компанию HYCONNECT GmbH (Гамбург, Германия).
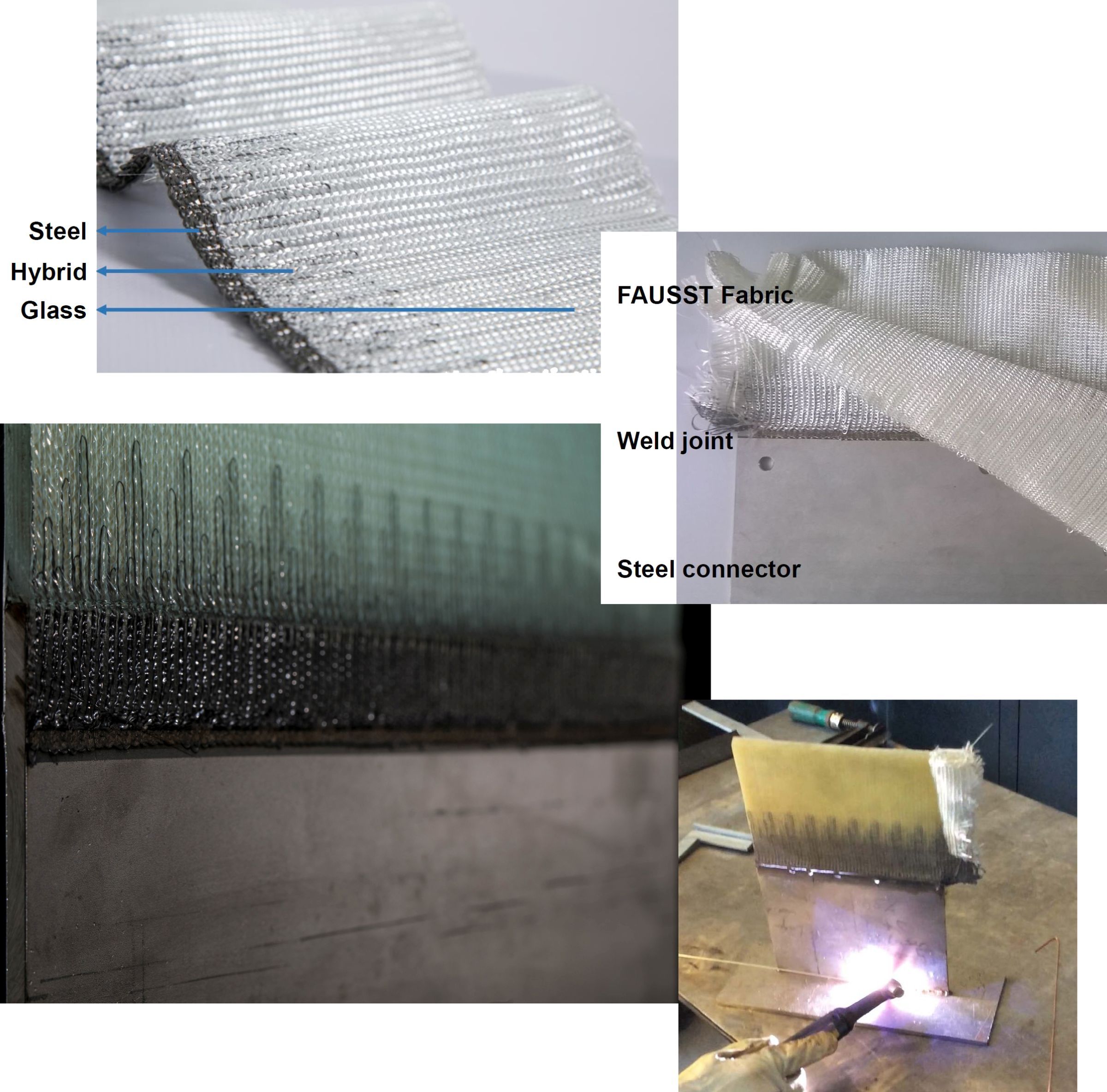
Рис. 3 сварное соединение HYCONNECT из стали и стеклопластика
Гибридная ткань из стали и стекловолокна FAUSST (вверху слева) приварен прессом к стальной пластине или другому соединителю (вверху справа) и затем может быть интегрирован в композитную структуру с помощью вливания смолы (внизу слева) . Такие гибридные композитные конструкции затем легко ввариваются в стальной каркас корабля (справа внизу) .
Источник | HYCONNECT
«Мы встречались с верфями DNV GL и BV и разрабатываем продукт, который может быть сертифицирован», - говорит Молтер. «Вы просто заказываете композитные детали с этой системой соединения, а затем можете приваривать их к своему кораблю. Это наше видение. Мы проектируем соединение композит-сталь, а затем поставляем изделие, ткань которого приварена к стальному соединителю (пластине, профилю и т. Д.) ».
Он объясняет, что конструкция соединения и ткань будут сертифицированы по ступенчатой системе:«При применении большего количества слоев ткани FAUSST происходит линейное увеличение несущей способности». Например, основным продуктом может быть четыре слоя FAUSST с приваренной к нему полосой длиной 1 метр, рассчитанной на определенную растягивающую и изгибающую нагрузку. Тогда будут некоторые продукты, доступные слева (например, всего два-три слоя для более низкой номинальной нагрузки) и справа (например, всего шесть слоев для более высокой номинальной нагрузки). “We are still finalizing these details, but the goal is a standardized and easy-to-use system,” notes Molter.
HYCONNECT has adapted the fabric technology to handle the difference in stiffness and coefficient of thermal expansion (CTE) between steel and composites; the use of knitted fibers for mechanical interlocking with unidirectional fibers for carrying load through the joint; and the technique required for high-quality press welding of the steel fibers to the steel connector (see "Connecting composites to steel”). “This solution is based on continuous testing,” says Molter. “Because FAUSST consists of standardized ready-made sub-products, it can be supplied quickly, within days.” Prototypes are currently being produced for selected customers, and HYCONNECT will begin full production in 2020.
Composite rudders
Ship rudders are also being developed as FRP-steel hybrids. As part of RAMSSES work package 12, Becker Marine Systems (BMS, Hamburg, Germany) is demonstrating a lightweight composite flap for a steel rudder designed for large container ships. Such rudders typically weigh more than 200 tons, says Jörg Mehldau, head of R&D at BMS. “By adding a hinged aft flap, you can significantly reduce the rudder area.” BMS pioneered this flap rudder, which dramatically reduces ship turning radius and improves course-keeping and maneuverability, enabling berthing without tugboat assistance. A composite flap not only reduces weight but also enables more functional shapes as well as more hydrodynamically- and load-optimized designs.
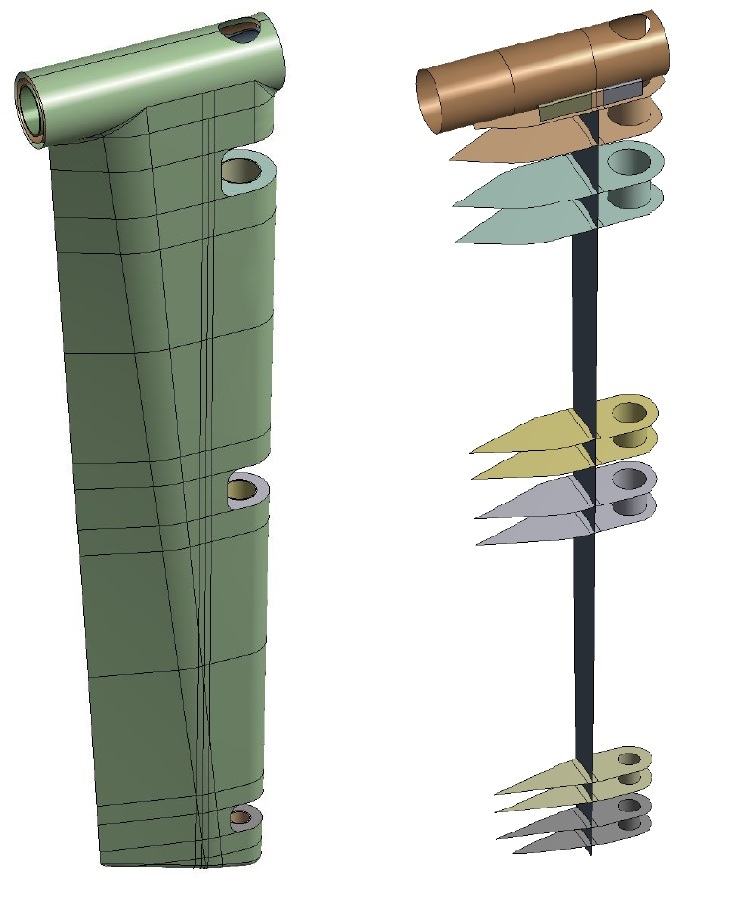
Рис. 4 Composite rudder flap
Becker Marine Systems is working with InfraCore to develop a lightweight, resin-infused rudder flap for the largest container ships. Measuring 11.8 meters long and 0.9 meter wide with a 2.9 meter chord, the full-scale flap must withstand 100 tons/m
2
of load. A 2-meter high demo will be tested 2Q 2020. Source| Becker Marine Systems
“The composite flap we are developing was inspired by the aviation industry,” notes Mehldau. For RAMSSES, the full-scale test case is aimed at one of the largest container ships (≈400 meters long), a flap measuring 11.8 longmeters and 0.9 meters wide with a chord of 2.9 meters (see Fig. 4). “We calculated the forces on this rudder and flap using formulas based on DNV GL rules for this ship’s type, weight and maximum speed,” says Mehldau. BMS then conducted preliminary design and engineering analysis, as well as trade studies for manufacturability and cost. “We first favored filament winding but it was too expensive,” he notes. “For each new ship hull, the rudder is a single design.” Thus, resin infusion was chosen, as was an alternative design from InfraCore. “It was the best for production flexibility, cost and structural performance combined,” Mehldau explains.
“To me, this was a natural fit for InfraCore because the composite lock gates we have built are very similar,” says Morel. He notes container ship rudders must withstand loads of roughly 100 tons per square meter with a surface area of 150 square meters. This matches well with InfraCore’s infusion-based technology used in bridge decks spanning up to 142 meters. Instead of bonding a high-density structural core to faceskins, InfraCore uses a low-density foam core only as a permanent formwork for multiple Z-shaped, two-flanged web structures. These are overlapped, faced with multiaxial fabrics and co-infused to form a robust construction. InfraCore will build a 1:6 scale demonstrator, using glass fiber and polyester resin materials already certified by DNV GL to keep costs low.
Morel notes that the reduced-weight InfraCore composite flap is cost-competitive, “because steel ship rudders are quite complicated to manufacture.” Mehldau agrees, “together with less maintenance and operational cost advantages, we see a successful business case.” The 2-meter -high demonstrator will be finished by 2Q 2020, followed by testing.
“We will test this using a lab test bench and air cushions, which can apply up to 8 bar of pressure equal to at least 80 Mpa of load,” says Mehldau. “We will measure strains and deflections to verify our simulations and perform a break load test.” A lab-scale demonstrator will also be tested via sea trials on a research ship in the Elbe River by CETENA (Genoa, Italy) which serves as project coordinator for RAMSSES along with CMT.
Forward momentum
“The outlook for composites in ships is good because many of the marine sector stakeholders have shown interest in FIBRESHIP, RAMSSES and other projects,” says Jurado. “The largest challenges are the need for new regulations, fire safety aspects, bonding techniques and reduction of shipbuilding costs.” For the latter, he cites automated manufacturing in shipyards as a key issue as well as mold construction and composite materials sourcing and storage. “Composites are already growing in ships,” says Krause at CMT, “but we started this work 20 years ago, so it is a slow process. However, we now have this critical mass and the industry is more connected via E-LASS.”
Jörg Bünker, head of R&D, application service for SAERTEX LEO FR products at SAERTEX (Saerbeck, Germany), agrees:“The drivers to reduce weight are strengthening. Within the next five to seven years, more composite materials will be sold into ships. This is the right time for more projects because IMO needs to see this interest and effort from the industry. Suppliers must show new solutions and shipyards must show where composites can be used, but no one can do it alone.”
Смола
- Корабль в бутылке
- Переработка:армированные непрерывным волокном термопластические композиты с переработанным поликарбонато…
- Как мобильные технологии устраняют препятствия для путешествий
- Композитные материалы TxV Aero соответствуют стандартам AS9100
- Mikrosam автоматизирует термопластические композиты с помощью безинструментальной системы размещения нескольк…
- Hexcel сотрудничает с Lavoisier Composites, Arkema
- Непрерывное производство волокна (CFM) с использованием композитов moi
- Саммит по облегчению:нацеливание на композитные возможности автоматической трансмиссии
- Ashland сотрудничает с Velox для распространения композитов во Франции
- Композитные материалы для 3D-печати с непрерывным волокном