Экскурсия по заводу:Holland Composites, Лелистад, Нидерланды
Покрытие катамаранов, фасадов зданий и др. Holland Composites, расположенная менее чем в часе езды от Амстердама, реализует широкий спектр высокотехнологичных проектов на своей площади 2 площадью 4500 м. средство. Источник, все изображения | Голландские композиты
Расположенный в здании площадью 4500 квадратных метров, менее чем в часе езды от Амстердама, Holland Composites (Лелистад, Нидерланды) ориентирован на четыре рынка:морской / морской, архитектуру, возобновляемые источники энергии и специальные проекты. Holland Composites использует смесь препрегового полимера, армированного углеродным волокном (CFRP), и сотового заполнителя Nomex для высоконагруженных деталей, а также вливание смолы и стекловолокно для строительной индустрии и проектов с низкой рентабельностью. «Мы по-прежнему можем обеспечивать высокую производительность даже с этими более экономичными конструкциями, и мы сохраняем низкие накладные расходы на детали с использованием современных материалов», - говорит Свен Эрик Янссен, со-управляющий партнер Holland Composites вместе с основателем Питерьяном. Dwarshuis. «Это уникально».
Компания также управляет брендом DNA Performance Sailing, производящим многокорпусные катамараны, в том числе 5,5-метровый катамаран F1X, 11-метровый тримаран TF10 и 14-метровый катамаран F4. 12-метровый катамаран G4 больше не производится, «но он демонстрирует наши возможности в области современного строительства яхт из композитных материалов и высокой производительности», - отмечает Янссен. «Эта лодка - гоночный на рапирах двойного назначения и семейный круизер с койками, кухней и головой, но при этом развивает скорость более 35 узлов. Способность преодолевать препятствия весом более 4000 кг и экипаж из шести человек - в этой области все еще нет конкурентов, кроме яхт America’s Cups стоимостью в несколько миллионов долларов ».
Морской, автомобильный и воздушный транспорт
Перед началом экскурсии Янссен рассказывает историю компании и производимых ею композитных конструкций. Holland Composites была основана в 1992 году Янссеном и Даршуисом, которые в то время были студентами Технического университета в Делфте (TU Delft, Нидерланды). Они построили мачты из углеродного волокна для парусных катамаранов Hobie, тендерную 18-метровую яхту с использованием углепластика и сотовых ячеек Nomex в 1993 году и 100-футовую парусную яхту с использованием обработки вливанием смолы в 1994 году. «К тому времени все, что мы строили, было сделано из углеродное волокно с использованием препрега или инфузии », - вспоминает Янссен. Однако, добавляет он, поскольку бизнес был подвержен типичным взлетам и падениям морского рынка и разовым проектам:«Мы стремились диверсифицироваться, но хотели остаться в области передовых композитов, а не стекловолокна [что означает менее продвинутое, более товарное стекловолокно. и полиэфирная смола] ».
Компания начала изучать легкие решения для автомобильного транспорта, выпустив 35 грузовых прицепов с монококовым шасси из композитного стекловолокна и углеродного волокна, которые снизили вес на 3500 кг. «Грузовики перевозили плотные грузы, такие как картофель, и должны были набрать максимальный вес, прежде чем заполнить свой объем», - объясняет Янссен. Holland Composites также производила прицепы-рефрижераторы, добавляет он:«Но мы были слишком рано; рынок еще не был готов - компании еще не могли рассчитать годовую прибыль от перевозки большего количества грузов и экономии на обслуживании композитных прицепов по сравнению с их более высокой начальной стоимостью ».
Примерно в то же время к компании обратился VRR (Роттердам, Нидерланды), поставщик индивидуальных решений для грузовых авиаперевозок. «Они выполняли работу для Airbus, Boeing и авиакомпаний», - вспоминает Янссен. «Мы разработали легкий контейнер с монококом из углеродного / арамидного волокна, который до сих пор не имеет себе равных по легкому весу», - говорит он. Хотя Holland Composites произвела несколько тысяч таких изделий, рынок быстро наполнился недорогими изделиями из стеклопластика.
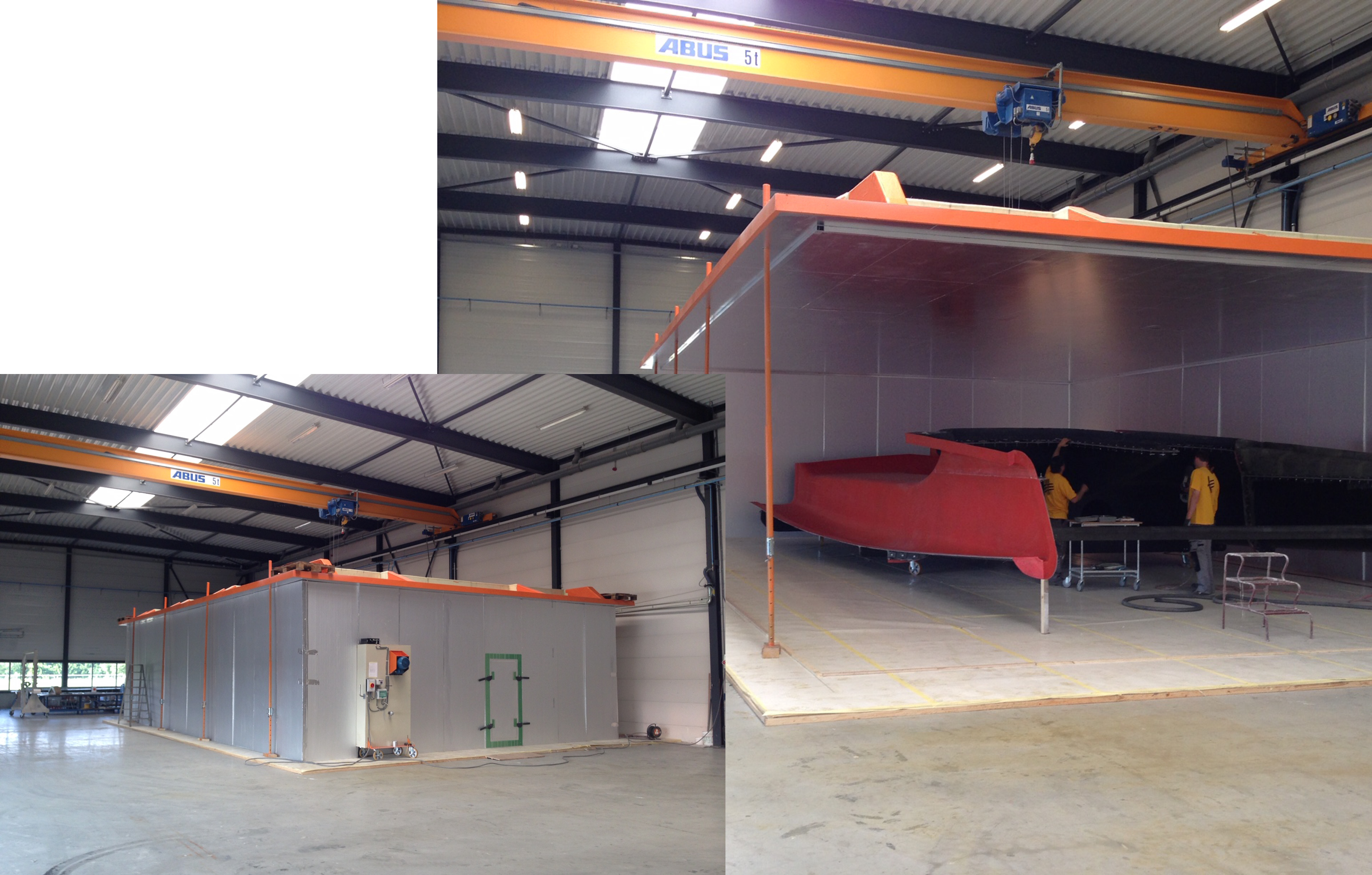
Структуры, отвержденные методом OOA. Крупные углеродные композитные конструкции для многокорпусных парусников марки DNA Performance Sailing сушатся в гибких печах (справа), состоящих из теплоизоляционных панелей с подогревом и циркуляцией воздуха, управляемыми компьютером с внешнего блока (вставка).
Морской пехотинец остается сильной стороной
В 1999 году ВМС Нидерландов обратились к Holland Composites с предложением изготовить купола гидролокатора из стекловолокна для подводных лодок. «Традиционно они строились из двух половин, соединенных вместе, - говорит Янссен, - но шов нарушает поле зрения». Нас попросили собрать их как одно целое. Эти купола гидролокатора большие - 11,5 на 3 на 3 метра и толщина от 45 до 110 миллиметров - и трудны для инфузии, они содержат 5000 кг гибридной смолы на основе сложного винилового эфира и эпоксидной смолы, поставляемой Romar-Voss Composites (Roggel, Нидерланды). Готовая конструкция весит 6500 кг. Они должны быть жесткими и выдерживать ударные нагрузки, поскольку расположены в носовой части корпуса. «Мы также должны соответствовать плотности и прозрачности воды с помощью сонара», - говорит Янссен. «Мы делаем это для кораблей типа эсминцев многих военно-морских сил по всему миру».
На другом конце весового диапазона находятся многокорпусные характеристики, которые не выдерживают испытания ДНК. «Наши небольшие лодки были первыми катамаранами, принявшими участие в соревнованиях, - говорит Янссен. Holland Composites также производит композитные суда на подводных крыльях для рекордных гоночных яхт, таких как MOD70’s Team ARGO и Beau Geste . «У нас есть собственная технология, позволяющая без сбоев изготавливать действительно высоконагруженные детали, а также уникальный однократный метод производства этих высокоэффективных пленок», - добавляет он. «Мы работаем с лучшими моряками в мире, чтобы выйти на новый уровень эффективности фольгирования и произвести все рапиры для лодок олимпийского класса NACMA17».
В легкой рубке из углепластика, которую Holland Composites производит для обслуживающих / вспомогательных судов ветряных электростанций Windcat Workboats (см. «Композитные рубки с меньшим весом»), используется многослойная конструкция из пенопласта из углепластика, наполненная смолой, для обеспечения жесткости и достижения большого открытого пролета без столбов внутри кабины. «Рубка с монококом достаточно легкая, поэтому мы можем надеть на нее хорошие демпферы, чтобы изолировать [ее] от двигателя и волновой вибрации в корпусе», - говорит Янссен. «Windcat известен своей действительно тихой ездой, а лодки пользуются популярностью у крупных производителей ветряных турбин. Все эти ветряные электростанции необходимо обслуживать, поэтому появился новый рынок высокоскоростных катамаранов длиной от 50 до 60 футов ».

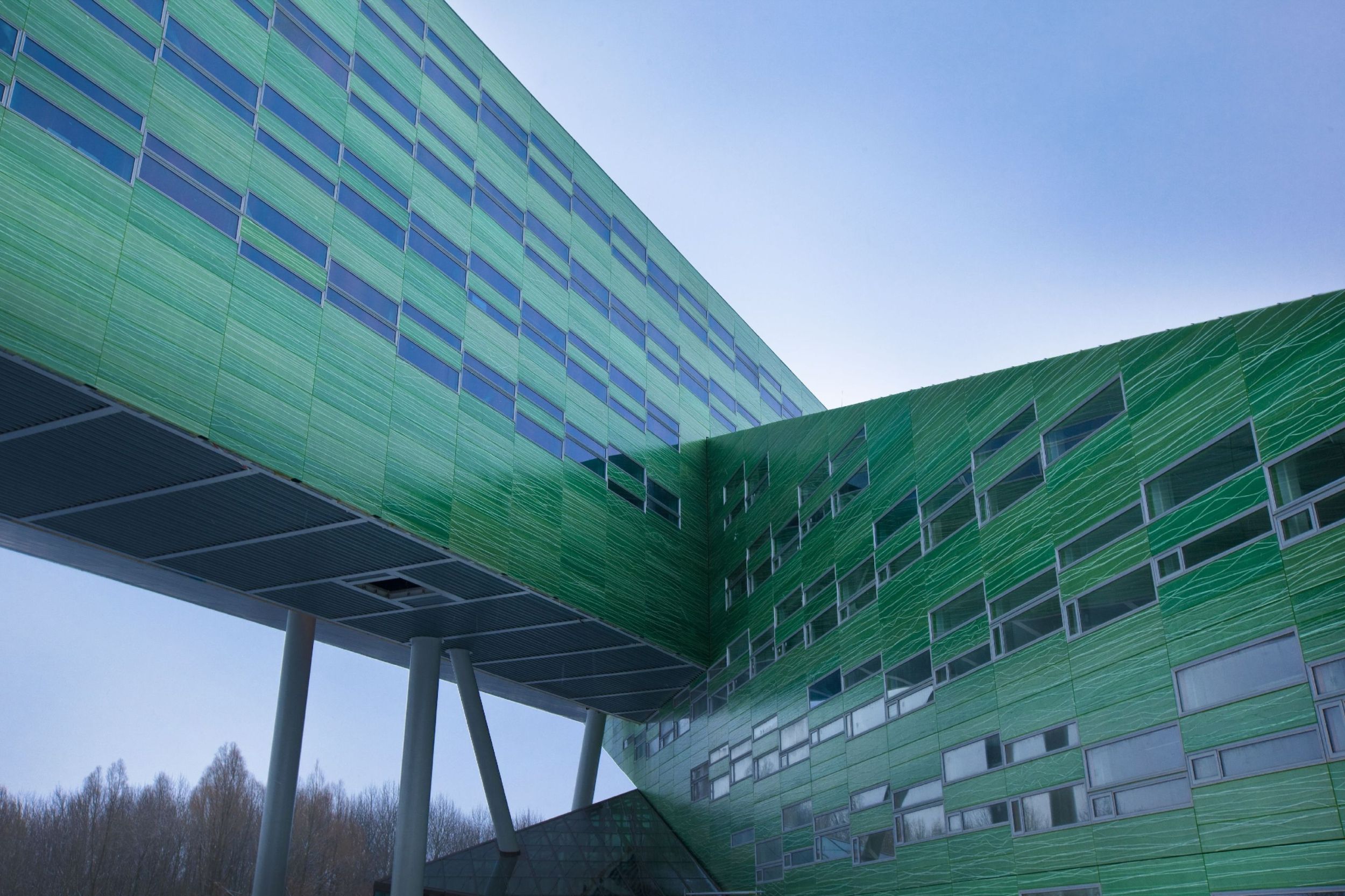
Holland Composites поставила структурный композитный фасад для Университета Гронингена. Здание наук, использующее их систему полупрозрачных панелей RAFICLAD и большие (3,6 на 3,3 метра) размеры панелей, обеспечивает экономию веса и максимальную теплоизоляцию.
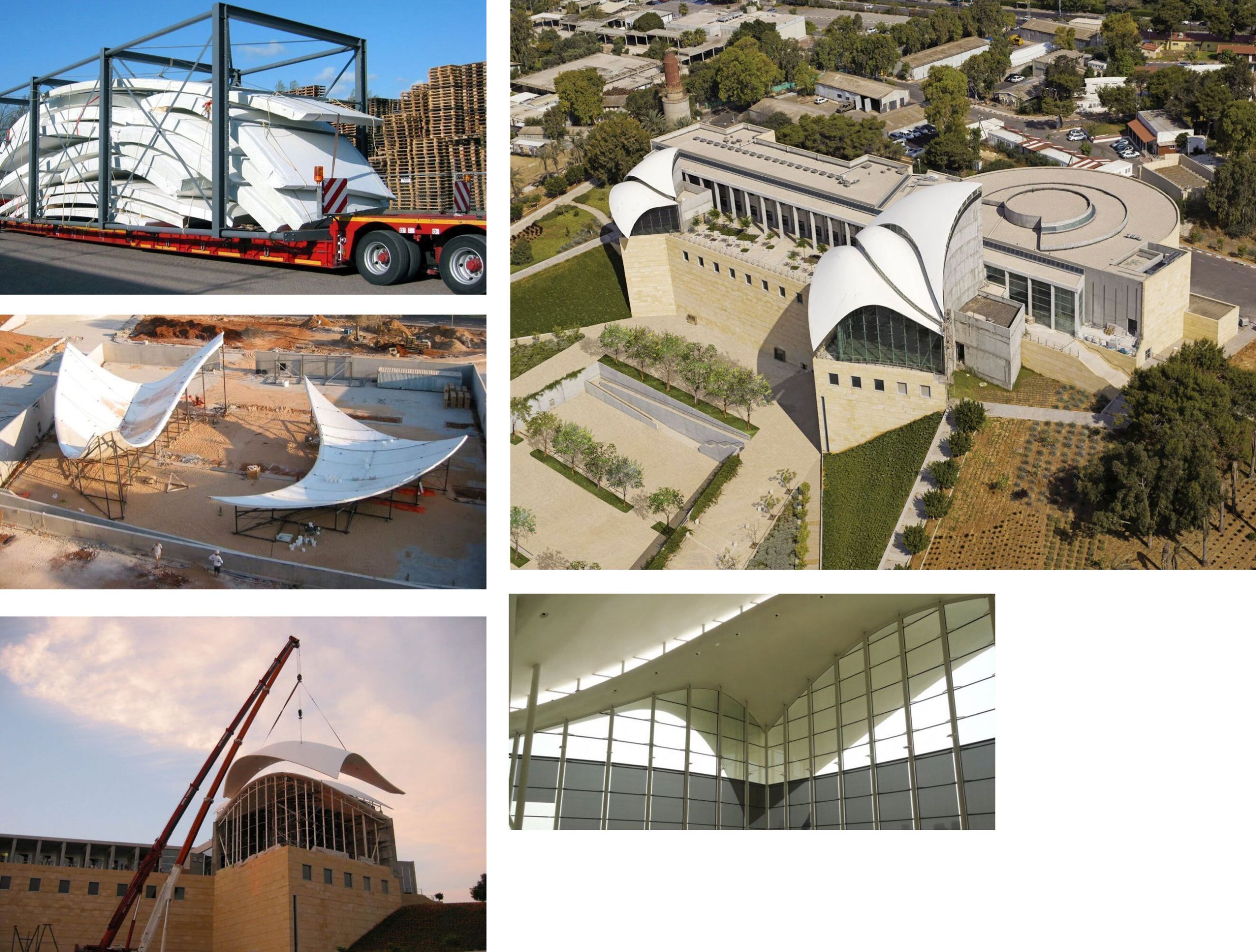
Семьдесят пять композитных секций размером 40 на 60 метров были отправлены в Израиль, склеены вместе и подняты на место для создания крыловидных секций крыши Центра Ицака Рабина в Тель-Авиве.
«Все, что мы делаем, носит структурный характер»
Для Центра Ицака Рабина (Тель-Авив, Израиль) компанию попросили построить крылатые конструкции крыши, которые были бы слишком тяжелыми, если бы они были сделаны из бетона. «Мы снова сделали максимально большие секции, - говорит Янссен. Семьдесят пять секций размером 40 на 60 метров были пропитаны смолой с использованием стекловолокна и винилэфирной смолы на эпоксидной основе, а затем отправлены в Израиль. На месте они были сложены в перевернутом виде в приспособления, чтобы соединить их вместе в «крылья крыла» с максимальным размахом 31 метр. Янссен отмечает, что проект был очень сложным в структурном отношении. «Эти панели имеют толщину от 200 до 300 миллиметров и удерживают вместе стеклянный фасад, включая 11-метровую консольную секцию. Композитный материал может выдерживать все нагрузки, что дает вам возможность спроектировать такие свободно висящие пролеты крыши ».
Башня Fletcher Hotel - еще один такой проект, завершенный в 2012-2013 годах. Он начинался как торговый центр рядом с шоссе, но после того, как было принято решение переоборудовать здание в элитный отель, потребовалось существенное шумоподавление в конструкции. «Бетонный каркас не выдерживал значительных дополнительных нагрузок, поэтому нам пришлось предложить облегченное решение», - говорит Янссен. Компания Holland Composites разработала композитные панели размером 8,5 на 3 метра, к которым можно было прикрепить фасад из листового стекла. «Стекло фактически висит на наших панелях, что помогает выдерживать нагрузку», - отмечает он. «Затем мы прикрепили наши панели к бетонному каркасу. Такое сочетание стекла перед композитными сэндвич-панелями с воздушным зазором между ними создает огромный акустический барьер ». Каждая композитная панель была готова к покраске для внутренних стен с одной стороны и покрыта УФ-стойким покрытием на стеклянной внешней стороне.
«Это был также очень быстрый способ крепления облицовки к зданию круглой формы», - говорит Янссен. «Мы смонтировали фасад целиком за один этап и достигли значения теплоизоляции R из 8, что в два раза превышает рейтинг обычных строительных материалов для экстерьера ». Развивая эту идею, Янссен считает, что энергетическая нейтральность имеет решающее значение для строительства зданий в будущем. «Для обогрева зданий, в которых используется наша структурная композитная облицовка, требуется не так много энергии, поэтому наш подход очень эффективен для достижения нулевой площади основания. BREEAM - это голландский сертификат энергоэффективности, и в первых двух зданиях, получивших этот сертификат, используются наши композиты ».
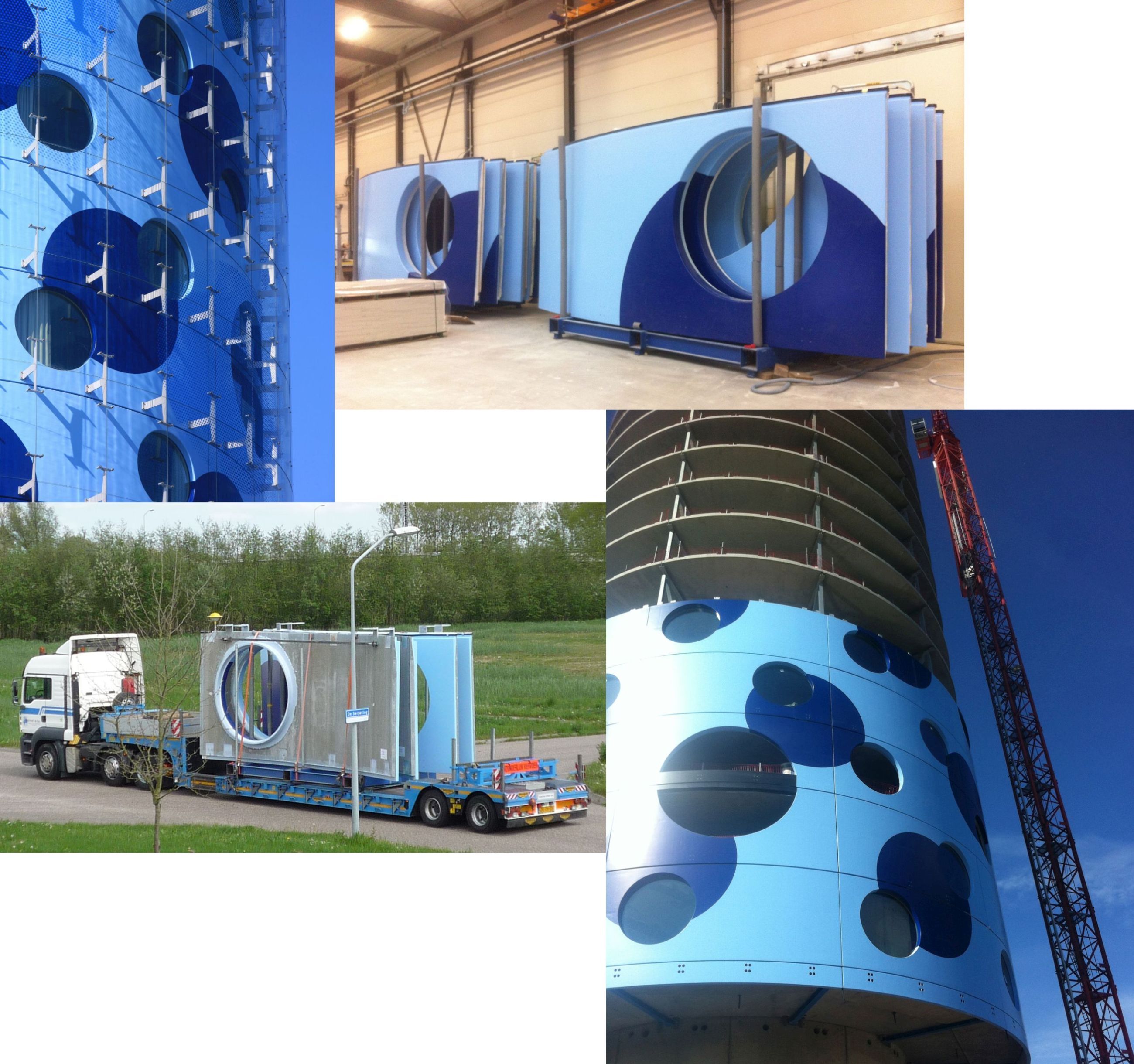
Для отеля Fletcher компания Holland Composites реализовала эстетичный внешний вид с низким уровнем шума, прикрепив изогнутые композитные панели к бетонному каркасу здания, к которому можно было прикрепить стеклянный фасад без чрезмерной статической нагрузки.
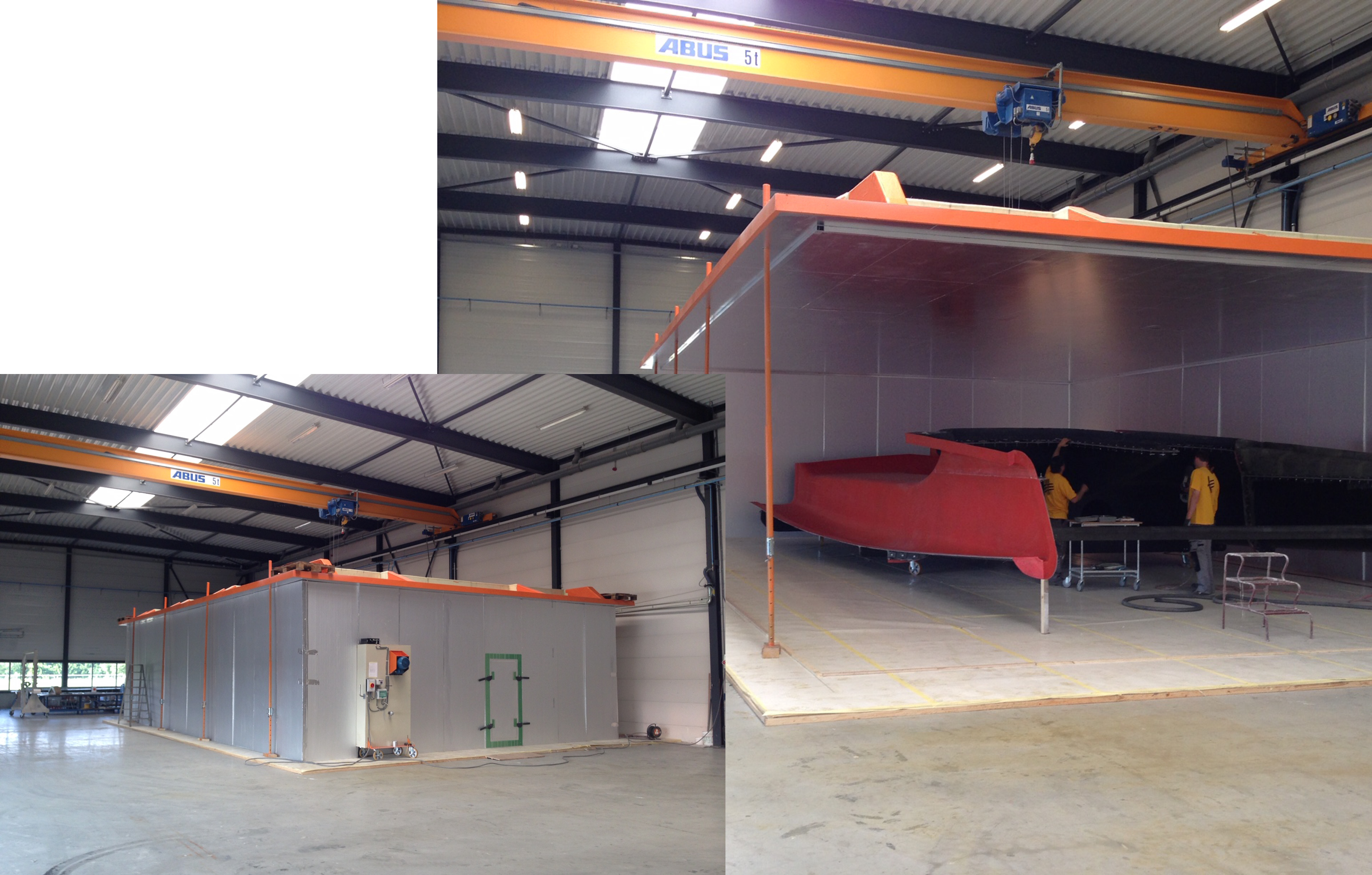
Янссен выделяет Музей современного искусства Stedelijk в центре Амстердама как вершину технических строительных проектов Holland Composites (см. «Большой музей, большие сооружения»). «Это было экстремальное упражнение в управлении тепловым расширением, которое иллюстрирует то, что мы делаем». Компания Holland Composites также первой изобрела сейсмостойкие структурные фасады, которые сейчас требуются в некоторых частях Нидерландов, объясняет Янссен, потому что почва была дестабилизирована из-за гидроразрыва (гидроразрыва). Здание Wiebenga в Гронингене отличается сейсмоустойчивым фасадом, который без повреждений может сдвинуться на 30 сантиметров. «Обычная сталь и бетон не выдерживают такого движения», - добавляет он.
Хотя при строительстве конструкций сложно найти баланс между бесчисленными требованиями, стоимостью и графиком, Янссен отмечает, что самой большой проблемой в настоящее время является огнестойкость. «Неправильное использование композитов принесло композитной промышленности дурную репутацию в этом отношении », - поясняет он. «Сейчас мы используем только огнестойкие материалы в этих строительных проектах и проводим испытания на огнестойкость в соответствии с утвержденными правилами».
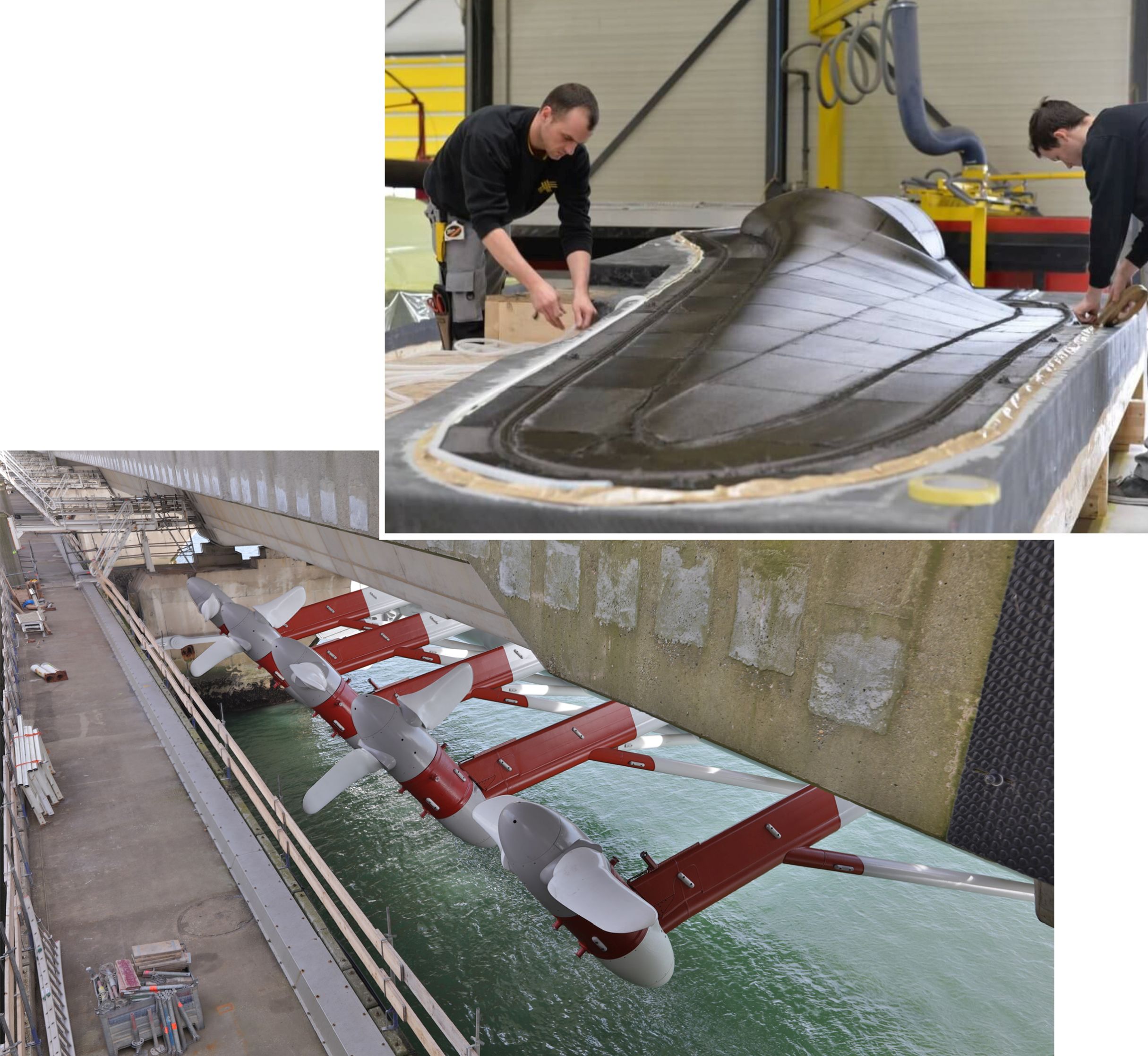
Holland Composites производит лопасти для приливных турбинных генераторов, используя препрег из углеродного волокна, отвержденный в автоклаве, чтобы выдерживать большие нагрузки, оказываемые на эти низкоскоростные конструкции с высоким крутящим моментом.
Оффшорные и возобновляемые источники энергии
Holland Composites также имеет долгосрочные контракты в морской нефтегазовой отрасли. «Композиты здесь не только обладают малым весом и устойчивостью к коррозии, но и легко ремонтируются», - говорит Янссен. «Оффшорные буровые установки и суда не имеют простоев. Однако ремонт металлоконструкций требует сварки и искры, поэтому производство приходится останавливать из-за опасности возникновения пожара. Мы можем исправлять композиты без этого нарушения ». У компании появились новые клиенты, которым нужна такая продукция для различных морских сооружений.
Он также производит лопасти для приливных турбин. По словам Янссена, получение приливной энергии еще ново, но первые проекты уже завершены, и результаты впечатляют. «Приливные турбины - надежный источник энергии, - поясняет он. «По сравнению с ветровыми и солнечными приливами всегда есть приливы, поэтому вы можете надежно прогнозировать выходную мощность, что является ключевым моментом для энергетических компаний». Holland Composites использует препрег из углеродного волокна, отверждаемый в автоклаве, для изготовления этих лезвий, так как нагрузки очень велики. «Лезвия вращаются с низкой скоростью, но с высоким крутящим моментом», - говорит Янссен. «Вы хотите, чтобы скорость ротора передавалась двигателю с максимальной скоростью, поэтому производителям турбин нужны прочные, но эффективные конструкции, которые имеют форму, позволяющую извлекать как можно больше энергии из приливных движений».
Каждая турбина имеет две лопатки длиной 3 метра и толщиной 18 миллиметров. На каждый приливный генератор приходится пять турбин. «Нагрузка на эти лопасти турбины описывается как буксир мощностью 13 600 лошадиных сил, движущийся вперед на полной мощности, - говорит Янссен, - но заказчику также нужны жесткие, легкие и неприхотливые в обслуживании лопасти с хорошей усталостной прочностью для долговечности. Сталь была бы слишком тяжелой, что сделало бы генераторы менее эффективными ». Holland Composites производит только лезвия; Обтекатели, носовой обтекатель и неструктурная облицовка изготавливаются производителями из стеклопластика.
Предприятие, ориентированное на будущее
Экскурсия начинается в зоне для укладки, где есть большой стол для укладки, детали для парусных лодок с характеристиками ДНК и различные пленки из углепластика, готовые к установке. Потолок здесь низкий из-за антресоли для хранения материалов. Он выходит на производственный цех с высокими потолками, где установлен автомат для резки Zünd (Альтштеттен, Швейцария), сразу за пределами зоны укладки. Резак имеет диапазон резки 5,7 на 2,8 на 0,3 метра для обработки препрега, сухого волокна и пеноматериалов толщиной до 25 миллиметров.
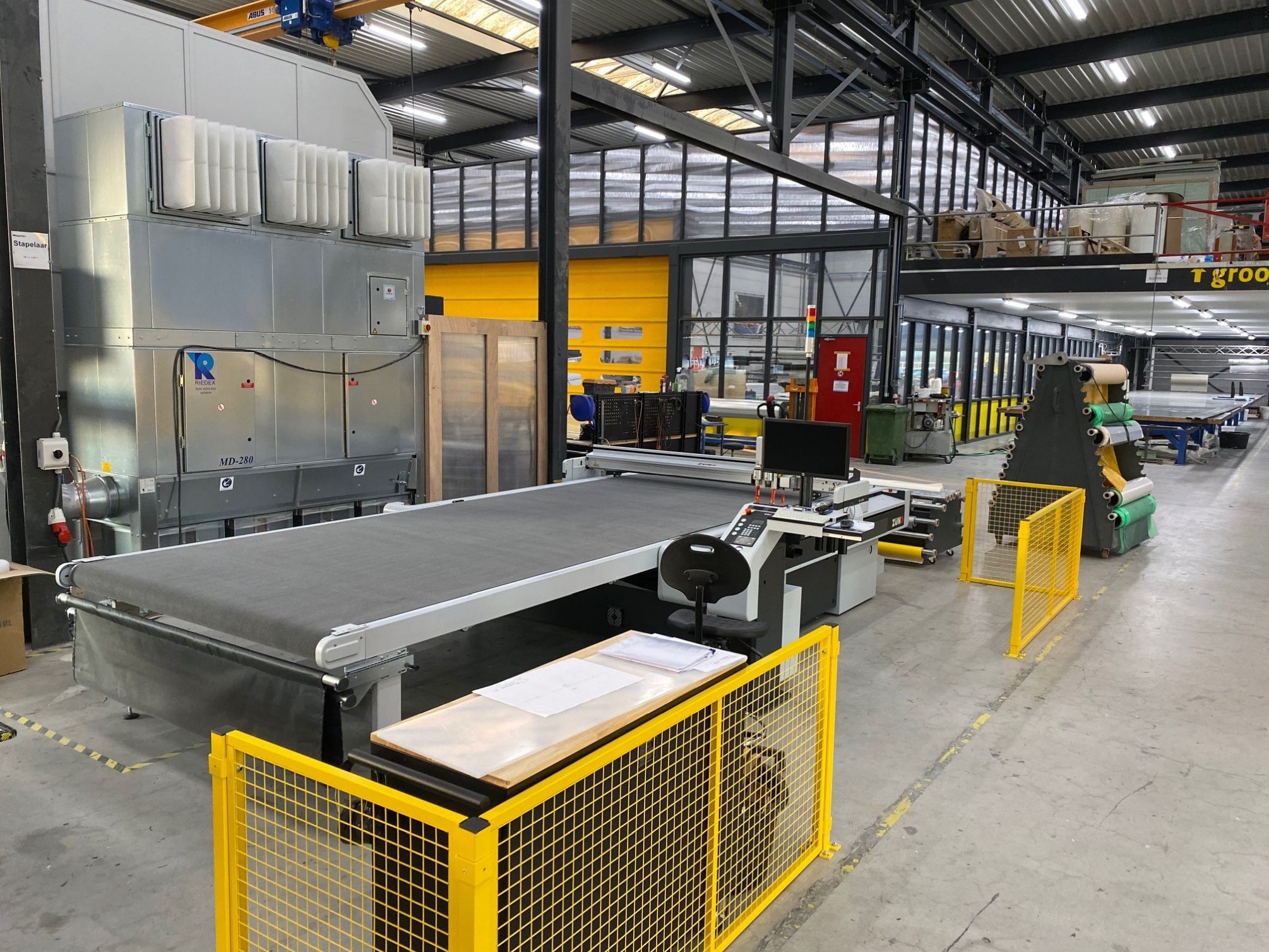
Автоматический резак Zünd на переднем плане подает арматуру и пену в зону укладки, которую можно увидеть сзади справа, с антресолью для хранения материалов выше. Закрытая площадка для инструментов находится за желтой откидной дверцей, которую можно увидеть здесь, за боковой стороной обрабатывающего центра CMS, который находится рядом с режущим столом Zünd.
Повернувшись от резака Zünd, мы идем в застекленную инструментальную комнату, которая примыкает к зоне простоя. Проходя через желтую рулонную дверь, мы видим, что в процессе обработки находятся несколько инструментов, а детали обрабатываются в вакуумных пакетах. «Мы сами изготавливаем формы», - говорит Янссен. «Для деталей из углепластика мы используем углепластик или алюминий в качестве инструмента, а также вентиляционные отверстия для циркуляции воздуха внутри инструментов, что помогает обеспечить равномерное отверждение по всей детали».
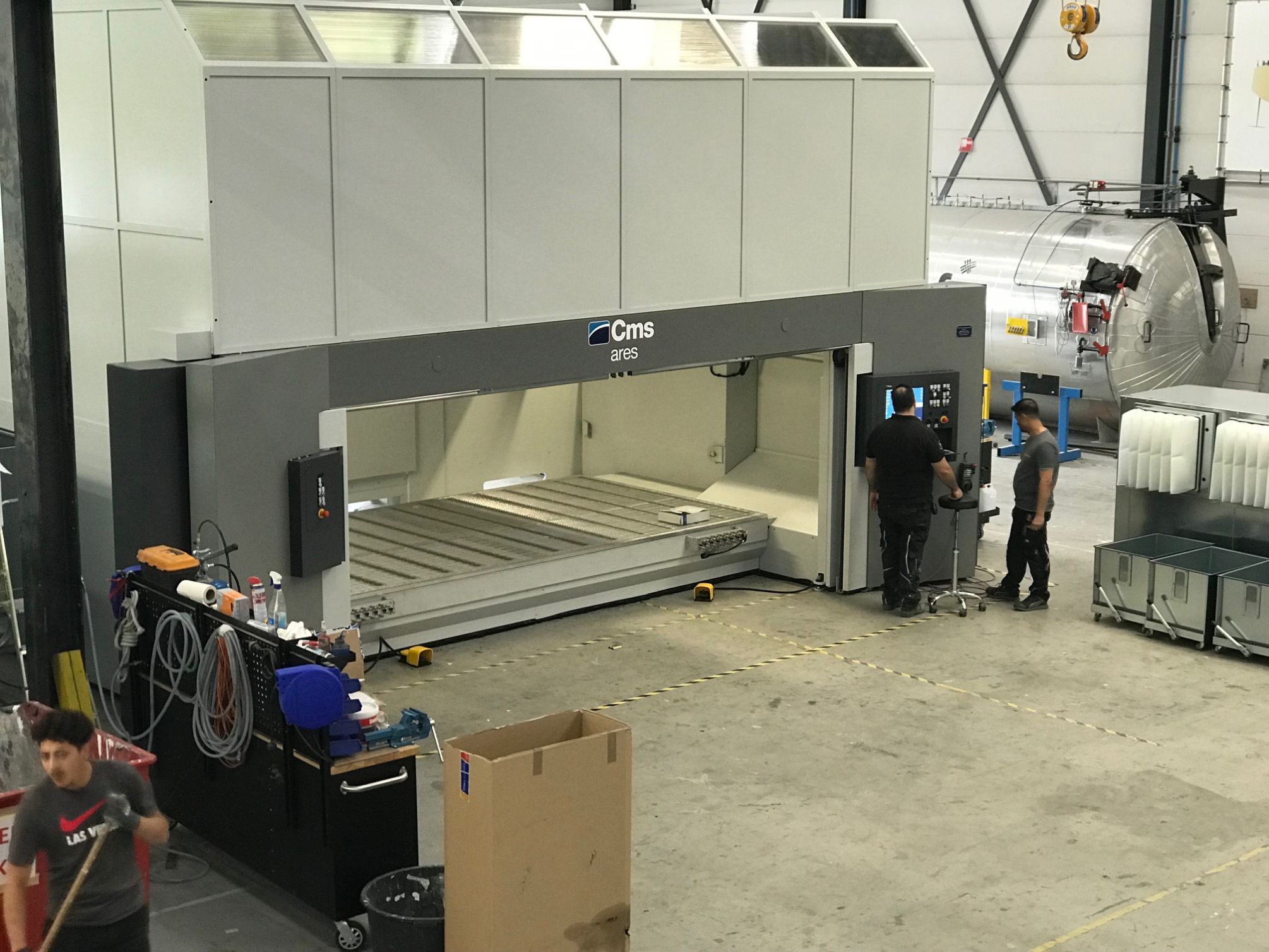
Обрабатывающий центр CMS расположен между столом для резки слева (вне поля зрения) и автоклавом (крайний справа, у стены).
Выйдя из инструментального цеха, мы проходим 5-осевой 5-осевой фрезерный центр с ЧПУ (CMS SpA, Zogno, Италия) размером 5 на 2 на 1,8 метра и видим автоклав размером 6,5 на 2,2 метра (Tankbouw Рутселаар, Нийкерк, Нидерланды). «Обычно мы отверждаем при 125 ° C при давлении 6 бар », - отмечает Янссен.
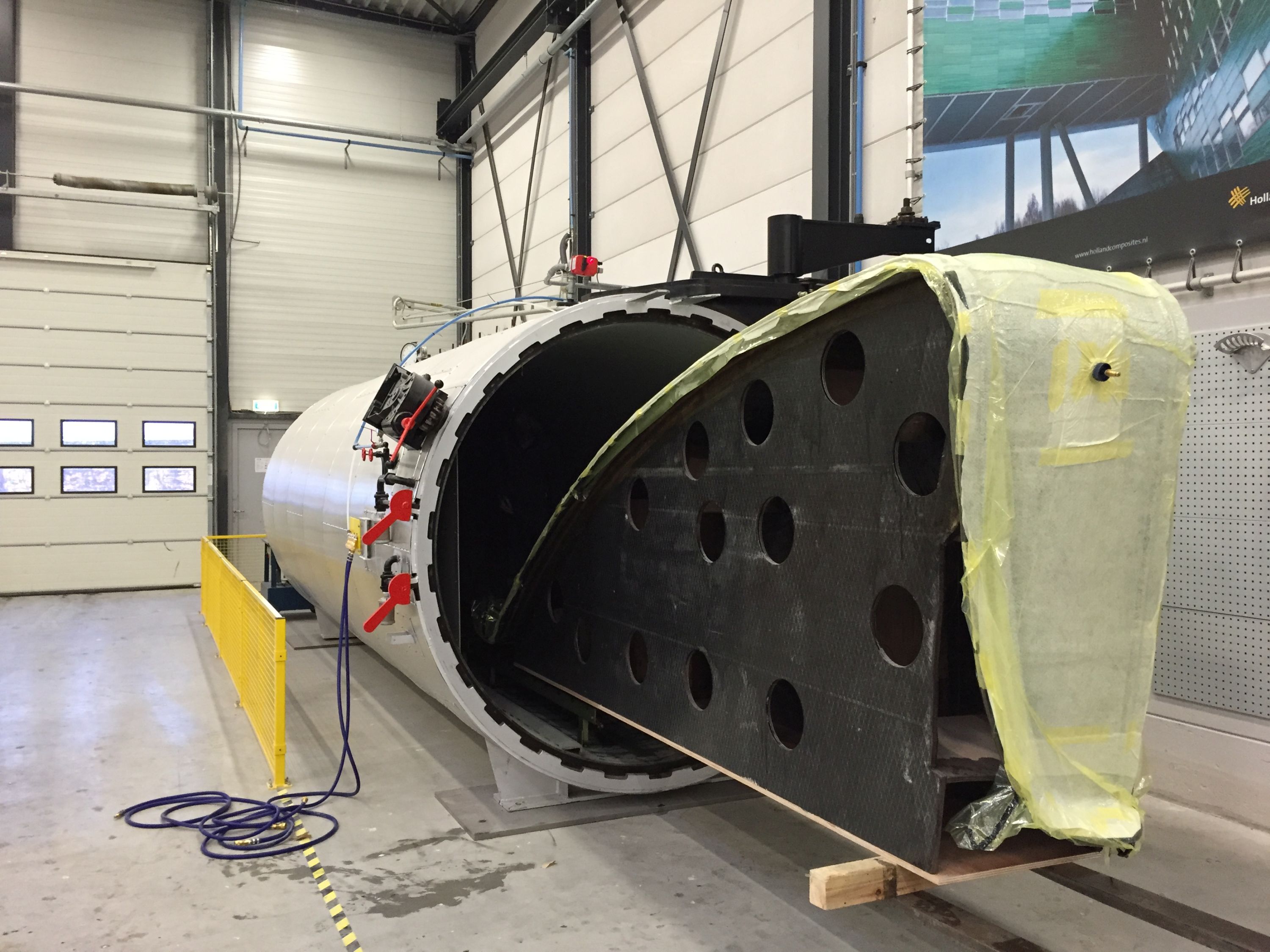
Автоклав также показан ниже с инструментом из углепластика (обратите внимание на отверстия для вентиляции воздуха) и большой пленкой из углепластика, отверждаемой под вакуумным мешком для высокопроизводительной многокорпусной парусной лодки.
Стена рядом с автоклавом разрезает производственную зону на две половины, по всей длине здания вдоль инструментальной комнаты. Мы разворачиваемся и проходим через дверь во вторую половину завода Holland Composites, где есть машина для гидроабразивной резки (диапазон резки 8 на 2 на 0,5 метра), несколько печей размером до 15 на 10. окрасочные камеры размером 19 на 12 на 3,5 метра. «В настоящее время мы производим большие панели для проекта в Катаре и серию рубок из углепластика для лодок Windcat», - говорит Янссен.
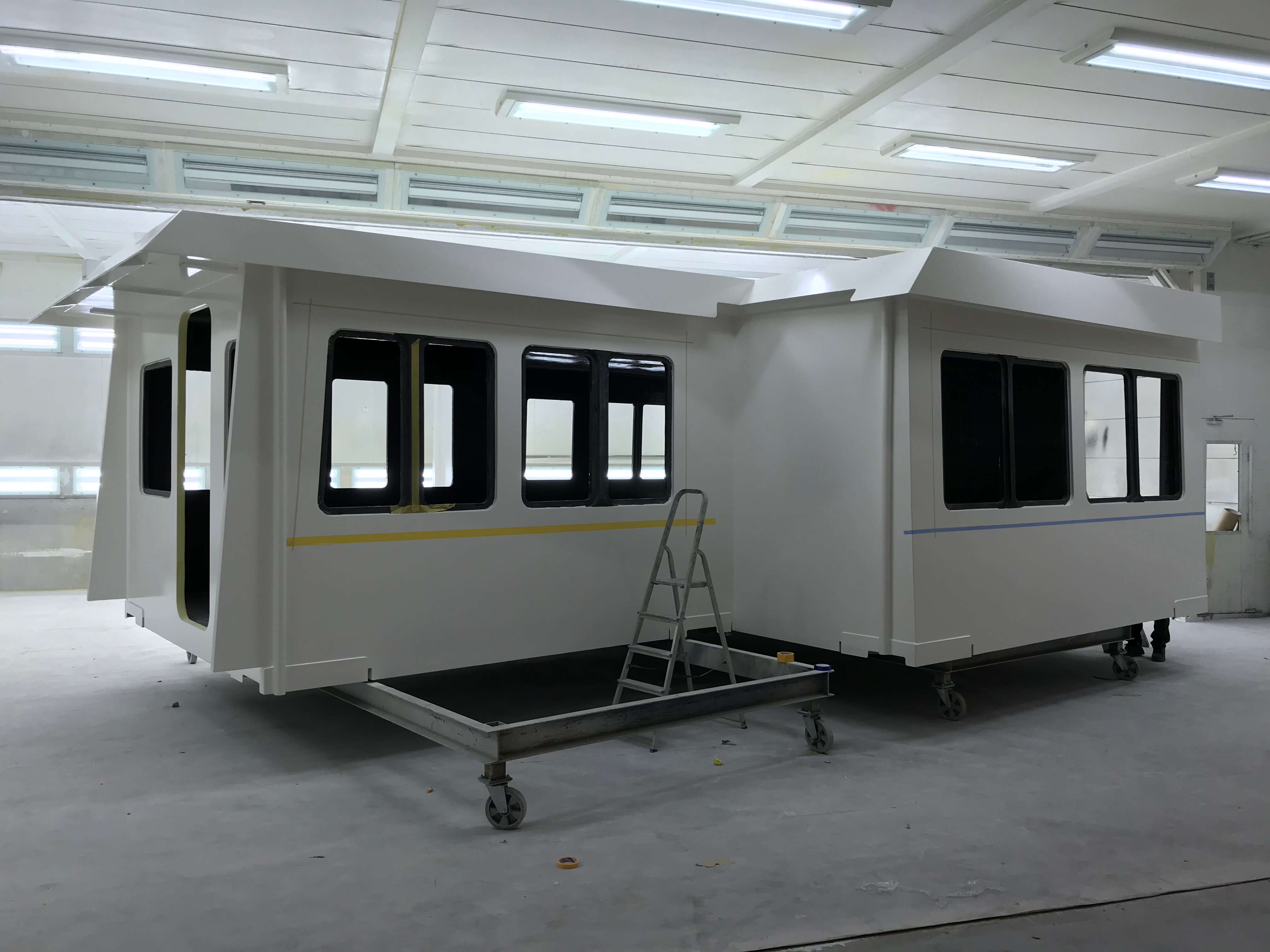
Рубки из углепластика, которые Holland Composites производит для катамаранов Windcat Workboats, окрашиваются в окрасочной кабине размером 19 на 12 на 3,5 метра.
Последняя установка Holland Composites - это принтер Massivit 3D (Лод, Израиль) 1800 Pro с объемом сборки 145 на 111 на 180 сантиметров. «Мы являемся партнерами, внедряющими инновации в 3D-печать форм с использованием трех печатающих головок, где две печатают оболочку сэндвича, а центральное сопло печатает заполнение или решетчатую структуру между ними», - объясняет Янссен. «В будущих разработках мы будем использовать армированный волокном материал, но пока мы можем печатать точные инструменты с минимальным фрезерованием. Мы используем гораздо меньше материала и видим очень короткие сроки изготовления пресс-форм. Теперь у нас есть полная производственная цепочка, с возможностью перехода от проектирования к формам и окрашенным деталям за короткий период времени ».
Он отмечает, что компания все еще изучает, как расширить использование автоматизации для дальнейшего продвижения своих продуктов, но без увеличения затрат. «Все сводится к изобретательности. Нас привлекают очень сложные проблемы, с которыми немногие отваживаются решать, но, как судостроителям, нам всегда приходилось проявлять изобретательность при ограниченных ресурсах. В том, что мы делаем с композитами, мы видим много возможностей в будущем ».
Смола
- Производители посещают United Safety for Plant Tour, обсуждение передового опыта
- CompositesWorld SourceBook 2022
- Устранение проблем термоформования термопластичных композитов
- Развитие аддитивных композитов
- Термопластические композиты:структурный кронштейн бампера
- Композиты как подкрепления авто-тела
- Нидерланды для демонстрации опыта страны в области композитных материалов на JEC World 2019
- TPAC и TPRC разрабатывают процесс переработки термопластичных композитов
- Сварка термопластичных композитов
- Высокопроизводительные композиты в Израиле