Диэлектрические датчики постоянного тока для производства промышленных композитов
Поскольку производители стремятся одновременно снизить стоимость и увеличить скорость производства композитных деталей, возможность видеть внутренние процессы формования в режиме реального времени и контролировать поток смолы, вязкость, температуру, давление и Tg / состояние отверждения становится отличительным признаком. Synthesites (Uccle, Бельгия) развил эту способность. Основываясь на результатах, представленных Немецким аэрокосмическим центром (DLR, Stade) и Национальным центром композитов (NCC, Бристоль, Великобритания), эта технология может сократить время цикла до 50%, с решениями отверждения на основе Tg и степени отверждения на смолу и деталь по сравнению с консервативными периодами времени, основанными на типовых исследованиях материалов. Фактически, это прогресс в направлении производства Composites 4.0 с использованием данных с датчиков для управления процессами и оборудованием, а также для улучшения моделирования и проектирования.
Впервые я сообщил о Synthesites в рамках проекта OPTO-Light (см. «Термопластичные формованные термореактивные пластмассы , 2-х минутный цикл, одна ячейка »). Фактически, возможность соединения термопластов с термореактивными пластиками в OPTO-Light без Поверхности, подвергнутые лазерной абляции, стали возможны благодаря использованию датчиков давления, температуры, удельного сопротивления постоянному току (DCR) и диэлектрического анализа (DEA) прямо в форме. Датчики DCR были поставлены Synthesites, а датчики для DEA - Netzsch (Зельб, Германия). Оба являются диэлектрическими датчиками, которые измеряют электрические свойства смолы. Я расскажу об истории и различиях этих технологий ниже.
Технология, разработанная Synthesites с рядом коммерческих клиентов, впечатляет, включая промышленное производство ветряных лопастей и пропитанных смолой крыльев для самолетов серии C, теперь Airbus 220. Она также была продемонстрирована для ряда материалов и процессов, включая автоклав. -отвержденный препрег, инфузия смолы и формование смолы под высоким давлением (HP-RTM).

- Первоначальное снижение удельного сопротивления отражает снижение вязкости смолы во время подъема до ≈120 ° C.
- Во время выдержки при 120 ° C удельное сопротивление увеличивается по мере увеличения вязкости смолы из-за реакции смолы и потери летучих веществ.
- Удельное сопротивление снова уменьшается и достигает минимума при нагревании смолы до 177 ° C.
- Затем сопротивление быстро увеличивается по мере того, как быстро протекает реакция отверждения.
- Увеличение удельного сопротивления замедляется по мере замедления реакции отверждения, приближаясь к нулевому значению через 300 минут, когда реакция отверждения приближается к завершению.
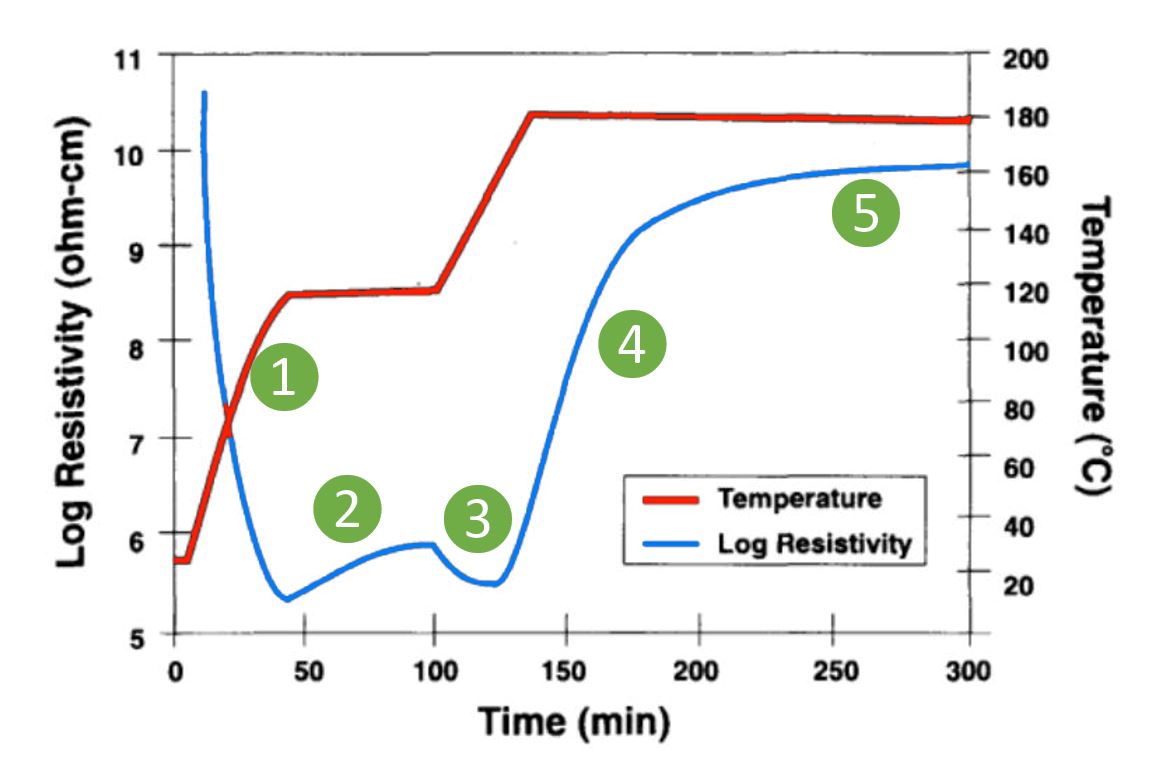
ИСТОЧНИК | Неразрушающая характеризация материалов VIII под редакцией Роберта Э. Грина, с. 385.
Ионная проводимость обратно пропорциональна вязкости смолы до гелеобразования и жесткости после гелеобразования (высокая подвижность ионов, низкая вязкость смолы и низкая жесткость). Обратное значение ионной проводимости, удельное сопротивление, таким образом, напрямую связано с изменениями вязкости / жесткости матричной смолы.
Было показано, что увеличение удельного сопротивления коррелирует с увеличением Tg. Это основа для определения удельного сопротивления постоянному току (DCR), которое представляет собой просто DEA с использованием постоянного тока (DC), и изначально дано описание процесса, разработанного Synthesites.
Как объяснялось выше, этот метод использования постоянного напряжения для DEA основан на корреляциях между удельным сопротивлением и состоянием отверждения. Об этом сообщил в 1962 году Р. В. Варфилд в статье «Свойства сшитых полимеров, подтвержденные измерениями удельного электрического сопротивления», Makromoleculare Chemistry, Vol. 58. (Ссылки, используемые в этом разделе, см. Внизу.)
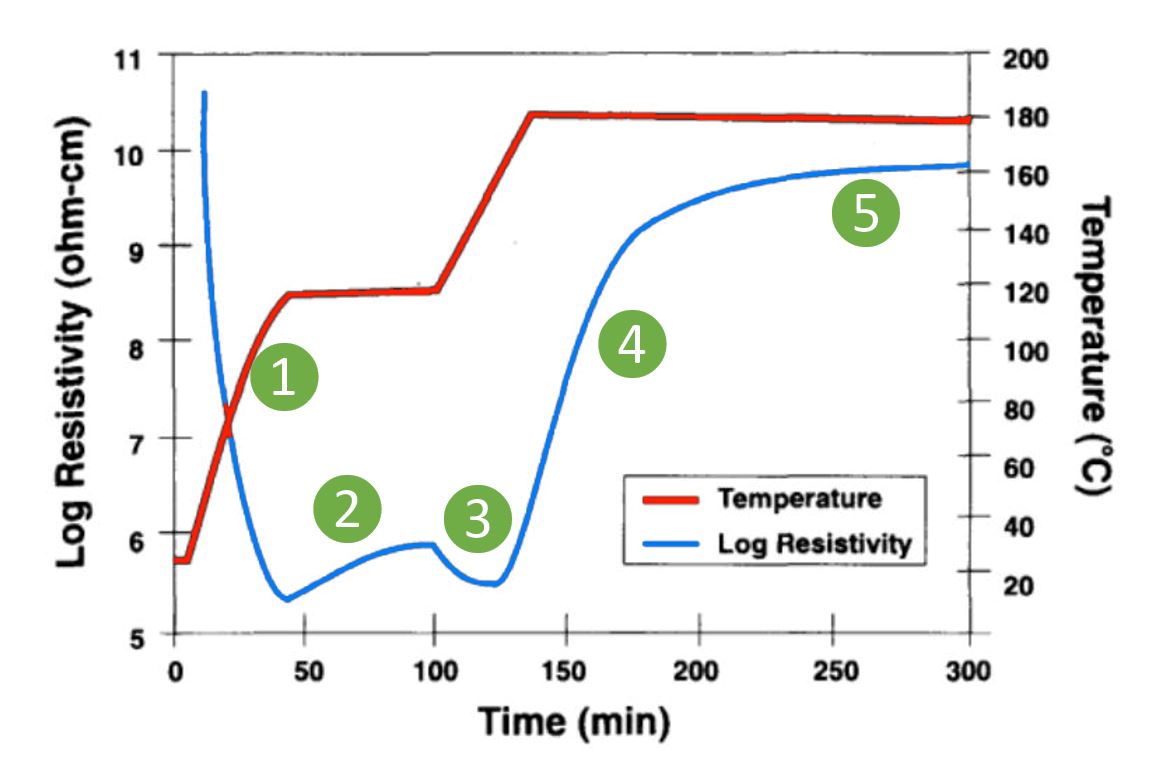
История датчиков DEA и переменного тока в сравнении с датчиками постоянного тока
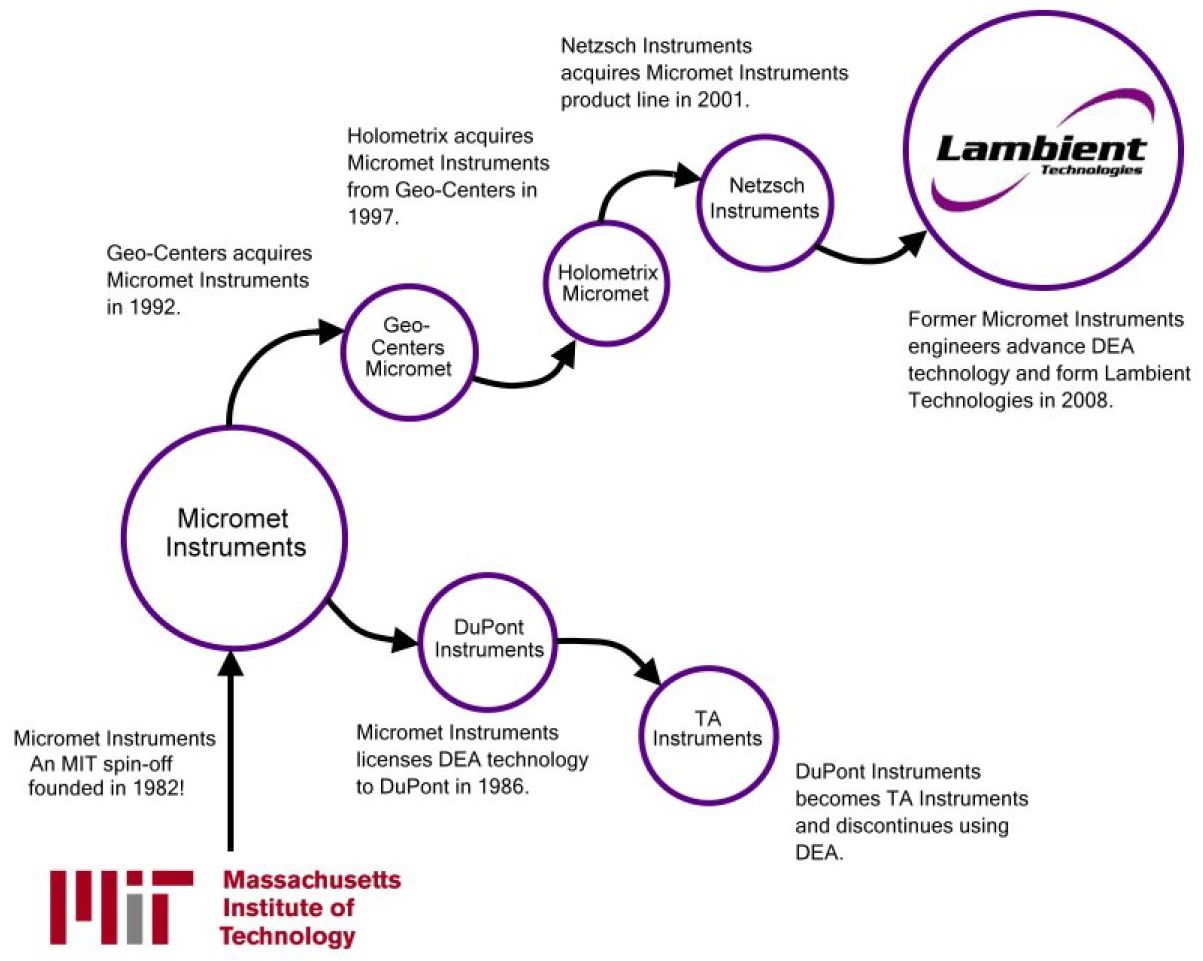
«Идея мониторинга излечения довольно старая, - объясняет доктор Никос Пантелелис, директор Synthesites. «В 80-х годах прошлого века метод измерения диэлектрической проницаемости считался более зрелым, чем другие методы, такие как оптические волокна. MIT (Массачусетский технологический институт) работал над этим и пытался внедрить его в производство. Эту технологию Netzsch купила и использует сегодня ».
Компания Synthesites была основана в 2008 году. «Мы разработали нашу технологию с нуля, используя электрические датчики постоянного, а не переменного тока», - рассказывает Пантелелис. «Для нас недостатком использования обычных диэлектрических датчиков переменного тока является необходимость возбуждать смолу в диапазоне частот, а затем измерять отклик импеданса для различных сигналов. Не только сложно обработать все эти данные, но и по мере того, как смола превращается из жидкой в твердую, вам необходимо сосредоточиться на разных частотах сигнала, чтобы получить правильную информацию ».
Пантелелис говорит, что датчики постоянного тока Synthesites могут измерять очень низкую проводимость и высокое удельное сопротивление, «что необходимо для измерения трансформации смол во время отверждения». Он утверждает, что использование обычного DEA только на одной частоте для упрощения не дает точных данных. «У нас нет нескольких частот, мы просто подаем постоянное напряжение. Обратной стороной является то, что этот подход очень узок, что означает, что он хорошо работает для очень специфических приложений, таких как отверждение смол, но не для всего. Однако, сравнивая производительность нашего оборудования с обычным DEA, мы можем измерить весь диапазон отверждения даже при более низких температурах. Компаниям, поставляющим инструменты и услуги помимо композитов, не нравится наш подход, потому что он имеет ограниченные параметры для настройки ».
Это не проблема для Synthesites, потому что они специально нацелены на композиты. «Наш подход хорошо работает с широким спектром композитных смол и процессов, включая термореактивные пластмассы, RTM, препрег и даже реактивные термопласты, такие как Elium». (Elium - это термопласт с низкой вязкостью от Arkema (Коломб, Франция), который можно обрабатывать с помощью настаивания смолы.)
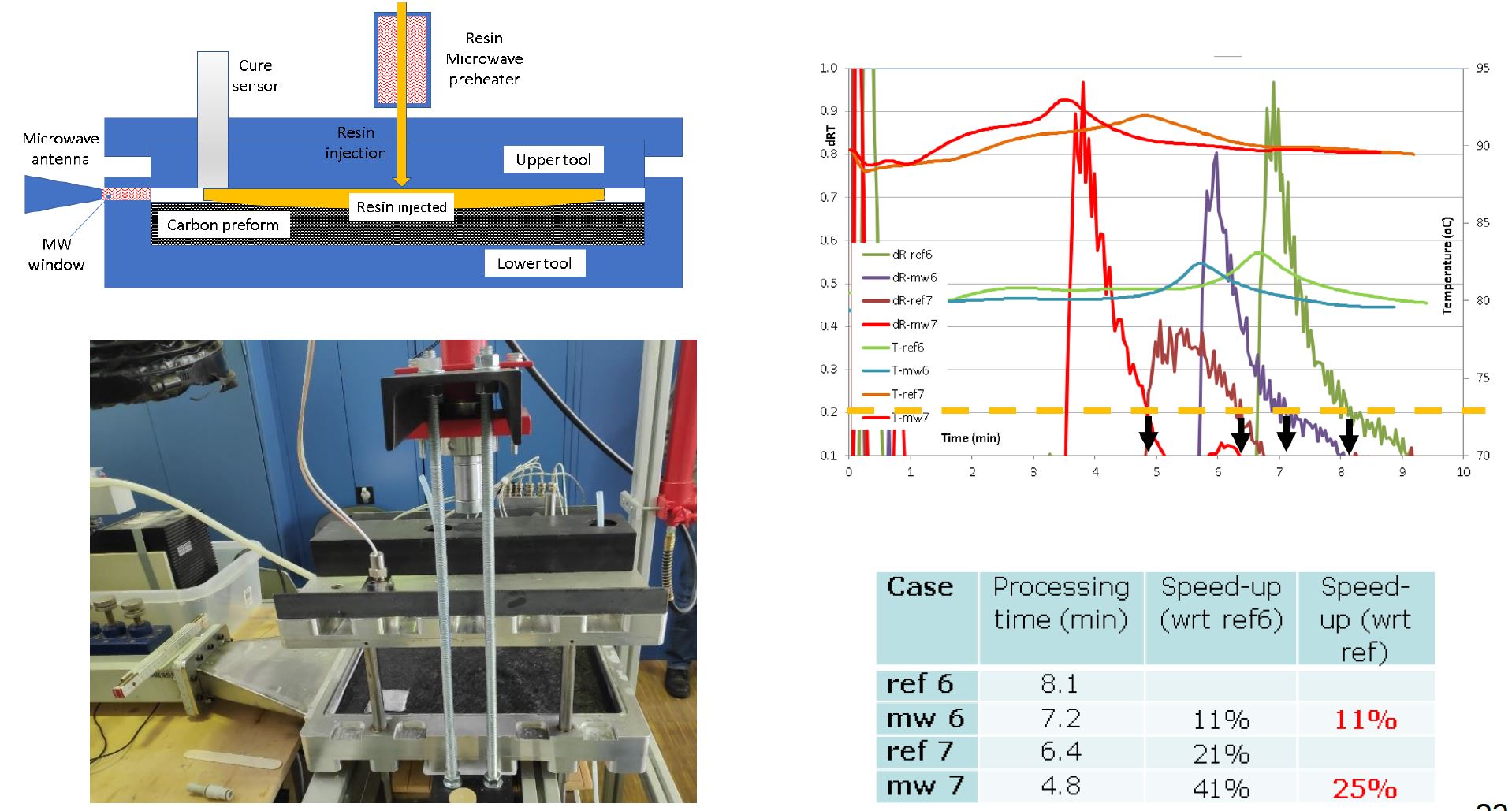
Если DEA с использованием постоянного тока был известен в 1960-х годах, то почему датчики переменного тока были предпочтены в 1980-х и продвигались вперед? «Тридцать лет назад технология DEA с использованием датчиков постоянного тока не была так развита», - отмечает Пантелелис. «Но мы усовершенствовали наш подход, чтобы обеспечить очень плавные и точные измерения для промышленного производства. Мы продемонстрировали и продолжаем развивать наши системы с такими клиентами, как GE Aviation (Бейтсвилл и Эллисвилл, штат Миссисипи, США) и Bombardier, которые обрабатывают большие детали с помощью формования жидкой пластмассы. Наши системы также используются каждый день в производстве ветряных лопастей и продемонстрировали возможность промышленного производства ламинатов препрегов автоклавного отверждения ».
Управление процессом
Пантелелис объясняет, как датчики постоянного тока Synthesites являются лишь частью интегрированной системы для мониторинга обработки и отверждения композитов. «Мы непосредственно измеряем сопротивление и температуру, и исходя из этого рассчитываем в режиме онлайн вязкость, степень гелеобразования и степень отверждения. Мы используем прочные датчики в форме, а также датчики ворот и линейные датчики для входов, выходов и линий подачи смолы, а также одноразовые датчики на деталях. Вы используете датчики только там, где они вам нужны ».
Датчики температуры представляют собой платиновые резистивные датчики температуры (RTD), которые обеспечивают гораздо более высокую точность (в пределах 0,1 ° C), чем термопары, а также стабильность в течение многих лет по сравнению с дрейфом измерения, возможным с помощью термопар. RTD являются стандартным оборудованием во многих промышленных приложениях. Датчики заслонки (см. Схему управления процессом ниже) являются двоичными, сообщая поток смолы как включенный, так и выключенный, хотя есть вторая версия, которая также может сообщать вязкость. Компания Synthesites разработала датчики для использования с углеродным волокном без риска гальванической коррозии, датчики, которые можно использовать через вакуумный мешок, и датчики формы в форме, соответствующие геометрии формы.
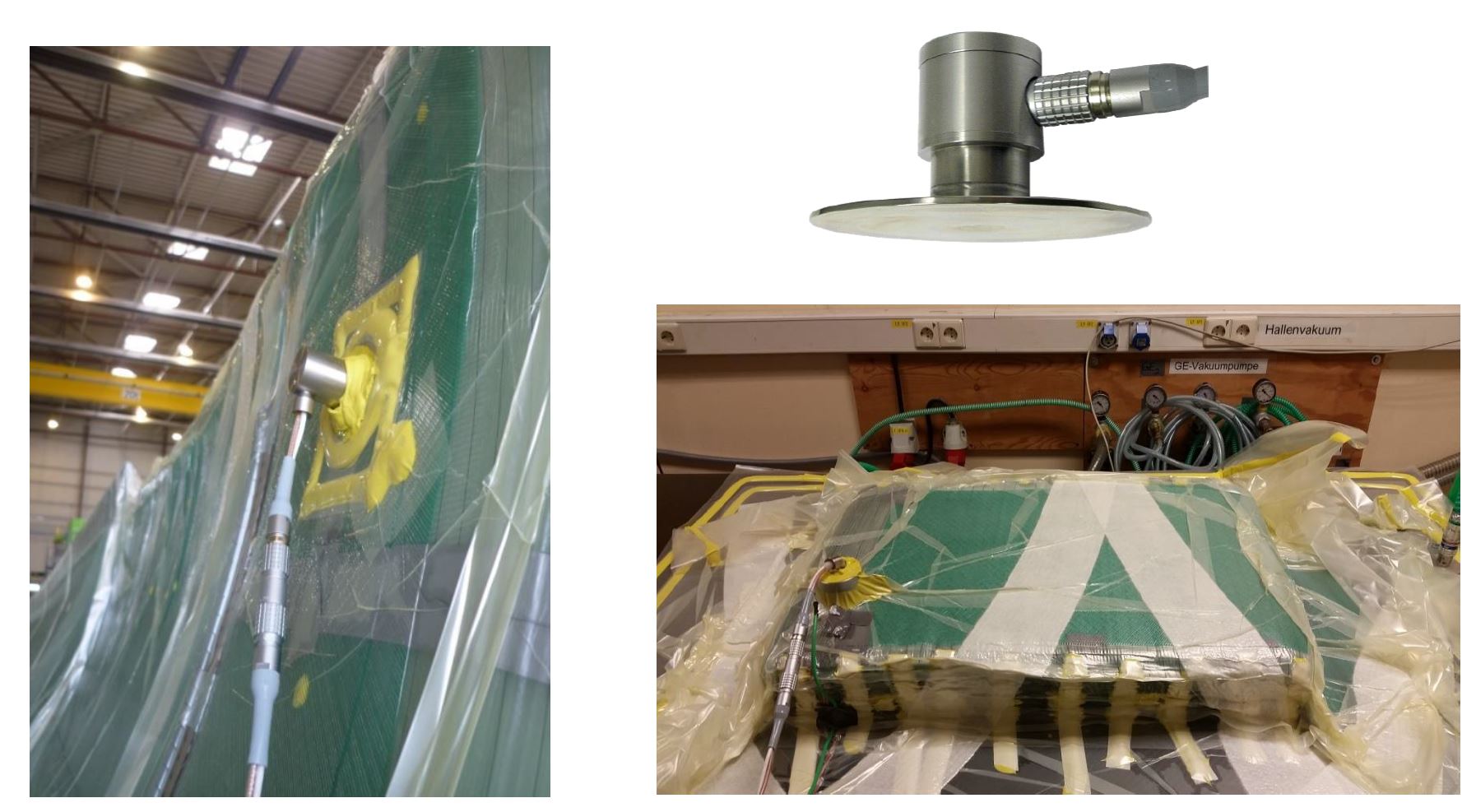
Следующие компоненты - это блоки сбора данных OPTIFLOW и OPTIMOLD. OPTIFLOW обеспечивает мониторинг поступления смолы и температуры в режиме реального времени на месте для формования жидких композитов. Он проверяет и регистрирует поток смолы и может выявлять производственные отклонения во время инфильтрации смолы. OPTIMOLD использует измерения температуры и сопротивления смолы для проведения расчетов и мониторинга состояния смолы, включая соотношение смеси, химическое старение, вязкость, Tg и степень отверждения. Его можно использовать в процессах формования препрега и жидкого формования.
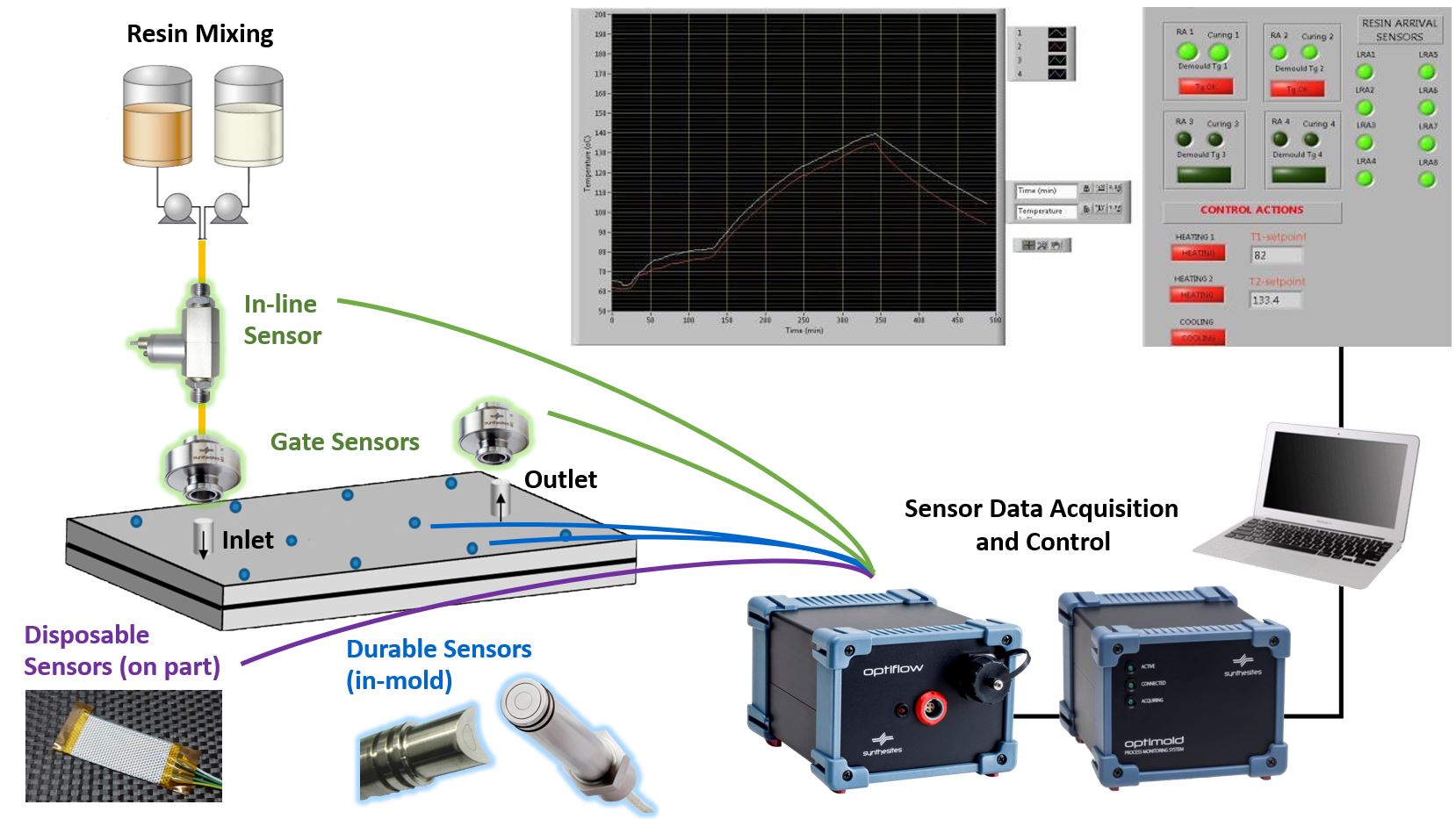
Установки OPTIFLOW и OPTIMOLD управляются программным обеспечением OPTIVIEW. «Это программное обеспечение обеспечивает сбор и хранение данных и предоставляется бесплатно вместе с нашим оборудованием», - поясняет Пантелелис. «Мы также предлагаем программное обеспечение Online Resin State (ORS), более продвинутый вариант, который клиенты могут приобрести дополнительно. Он собирает входные данные, выполняет онлайн-вычисления и отправляет выходные данные для интеллектуального управления процессами ».
Системы OPTIFLOW и OPTIMOLD постоянно проверяют, подключены ли датчики, а показания находятся в пределах допустимого диапазона. «Когда вы полагаетесь на эти датчики для управления технологическим процессом, крайне важно, чтобы система подала сигнал тревоги, если датчик не работает или если его показания выходят за установленные пределы», - говорит Пантелелис. Обе системы также имеют релейные выходы для управления технологическим оборудованием. Например, клапаны линии подачи могут быть открыты или закрыты в зависимости от данных о поступлении смолы, а оборудование для нагрева / охлаждения может управляться в зависимости от вязкости смолы. «Вы можете передавать данные с датчиков давления в OPTIMOLD, - отмечает Пантелелис, - и таким образом контролировать давление в форме на основе данных вязкости».
Измерения и типовые кривые данных
На приведенных ниже снимках экрана показаны измерения OPTIMOLD в ходе испытаний RTM на сжатие под высоким давлением (HP-CRTM) в NCC (Бристоль, Великобритания). Первый набор, основанный на простом испытании при 115 ° C, показывает, как измерения электрического сопротивления и температуры смолы в реальном времени преобразуются в расчетную вязкость и Tg с помощью программного обеспечения ORS.
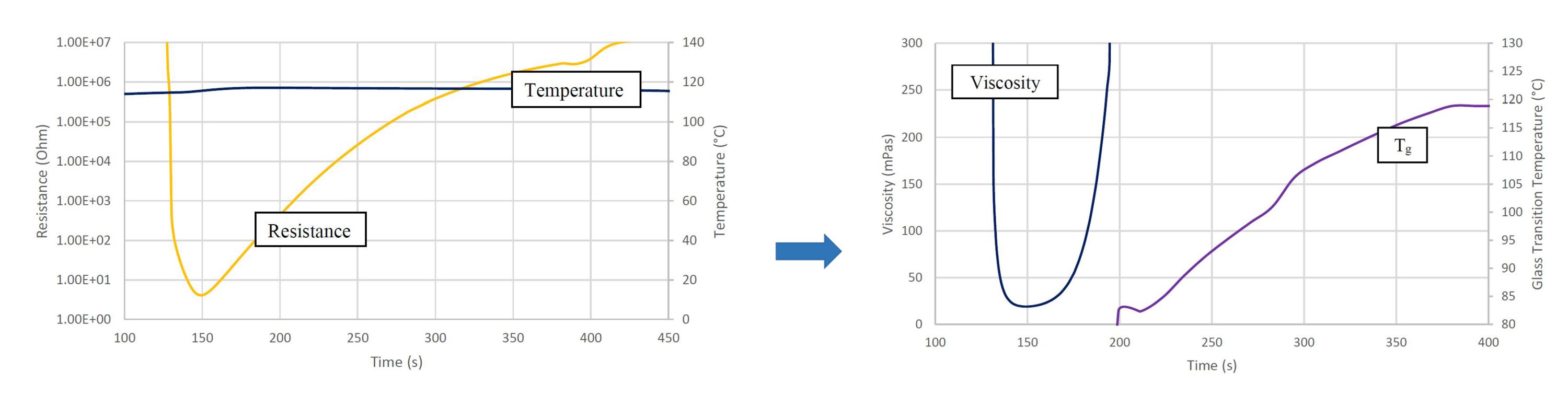
На графиках ниже электрическое сопротивление и температура (верхние графики) были записаны под углом 110 ° (слева) и 120 ° C (справа). Ниже значений сопротивления (R) и температуры (T) находятся графики, показывающие расчетную вязкость и Tg при 110 ° C (слева) и 120 ° C (справа) . Эти измерения были получены от двух датчиков OPTIMOLD, расположенных в верхней половине формы (Sn.1 и Sn.2, нижнее фото ), а давление в полости регистрировалось двумя датчиками давления Kistler 6162A (Sn.3 и Sn.4).
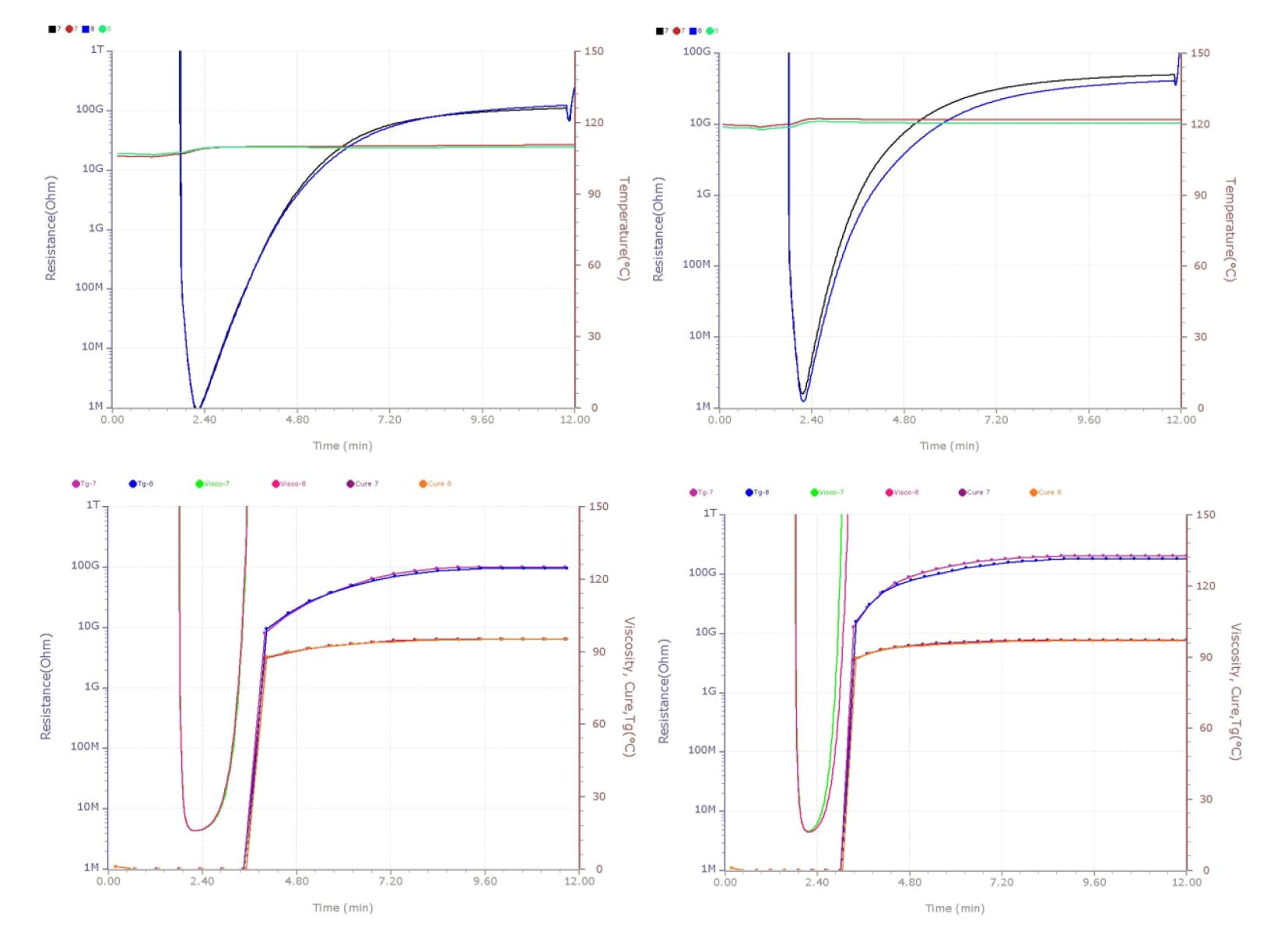
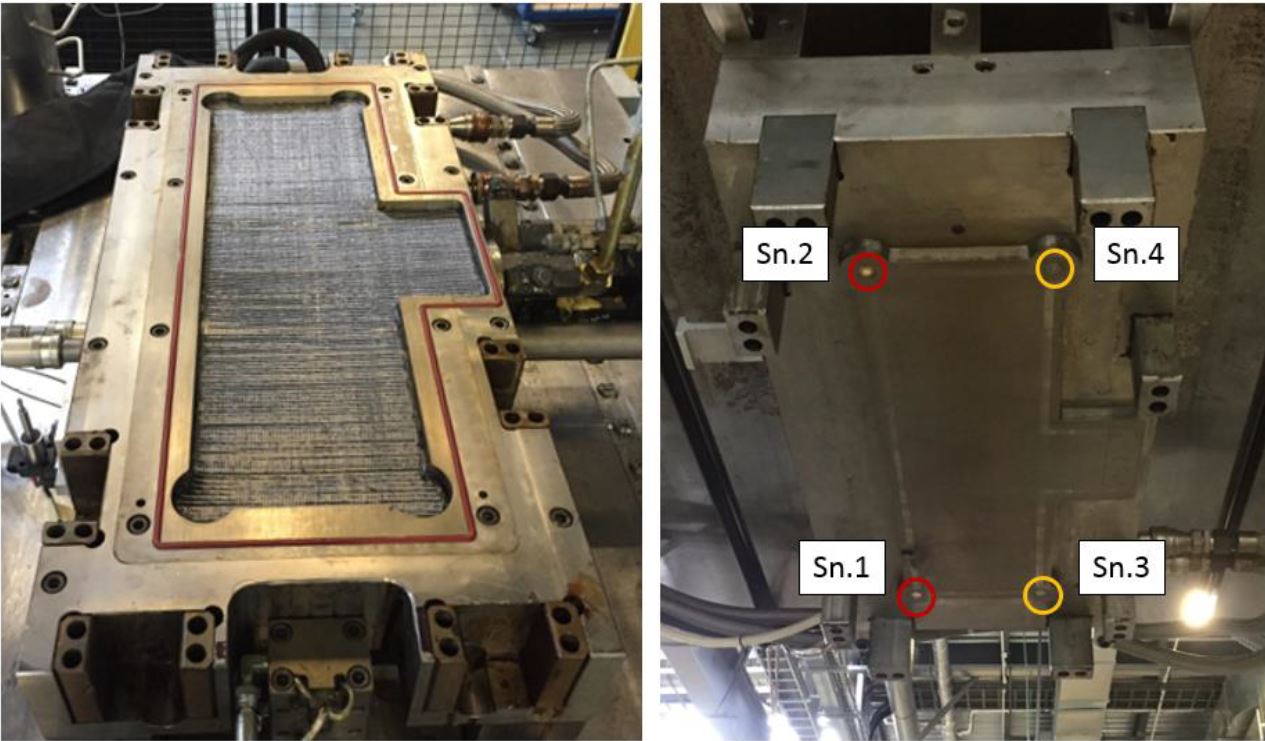
Все данные, зарегистрированные датчиками в форме, а также прессом и оборудованием для литья под давлением, могут быть сопоставлены в один файл журнала, что позволяет получить подробное изображение производственного процесса для каждого созданного компонента.
Сокращение времени отверждения
«У нас есть возможность снизить время отверждения более чем на 30%, потому что производитель может видеть Tg в реальном времени, чтобы они могли решить, когда остановить цикл отверждения», - объясняет Пантелелис. «Им не нужно ждать завершения более длинного, чем необходимо, цикла наследия. Например, унаследованный цикл для RTM6 составляет 2 часа при 180 ° C для полного отверждения. Мы видели, что при определенных геометрических формах это может сокращаться до 70 минут ».
Итак, цель - остановить процесс после завершения лечения? «Речь идет не о полном отверждении, а о достижении уровня отверждения, необходимого для каждого компонента», - говорит Пантелелис. «Полное излечение занимает слишком много времени. Ключ в том, чтобы увидеть, когда будет достигнуто достаточное излечение. Производители ветряных лопастей имеют целевую Tg. Когда они достигнут этого, они могут начать охлаждаться. Поэтому необходим датчик, который может давать очень точные измерения Tg в режиме реального времени ».
Компания Synthesites завершила демонстрационный проект с Hutchinson (Париж, Франция) по производству лопасти автомобильной подвески, сделанной из стекловолокна / эпоксидной смолы и RTM для проекта ECOMISE, финансируемого ЕС (Обеспечение производства COmposite нового поколения с помощью структурной оценки и корректировки процессов на месте, 2013 г. -2016). Целью этого проекта была оптимизация цикла RTM на основе мониторинга процессов в реальном времени:
- Первая рампа нагрева будет запущена после завершения инфильтрации смолы на основе датчиков.
- Вторая рампа нагрева будет активирована после завершения отверждения на основе расчета Tg.
- Охлаждение запускается после завершения постотверждения на основе расчета Tg.
Система Synthesites состояла из двух (2) литьевых датчики для отверждения (CS1, CS2), один (1) в форме датчик потока и температуры смолы (датчик потока 1) и восемь (8) одноразовых датчики расхода / температуры смолы - четыре (4) встроены в тестируемую часть и четыре (4) прикреплены к поверхности инструмента.
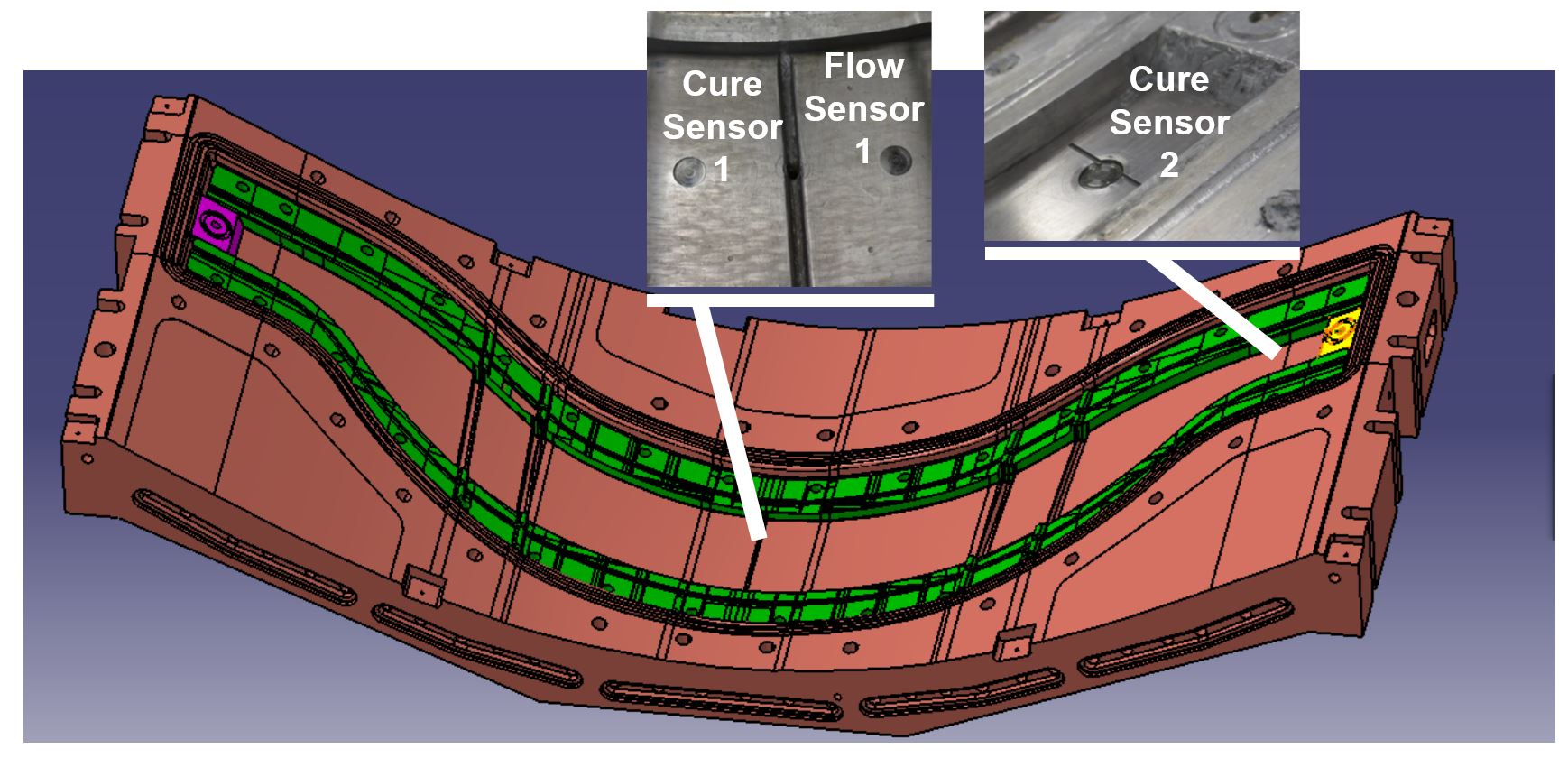
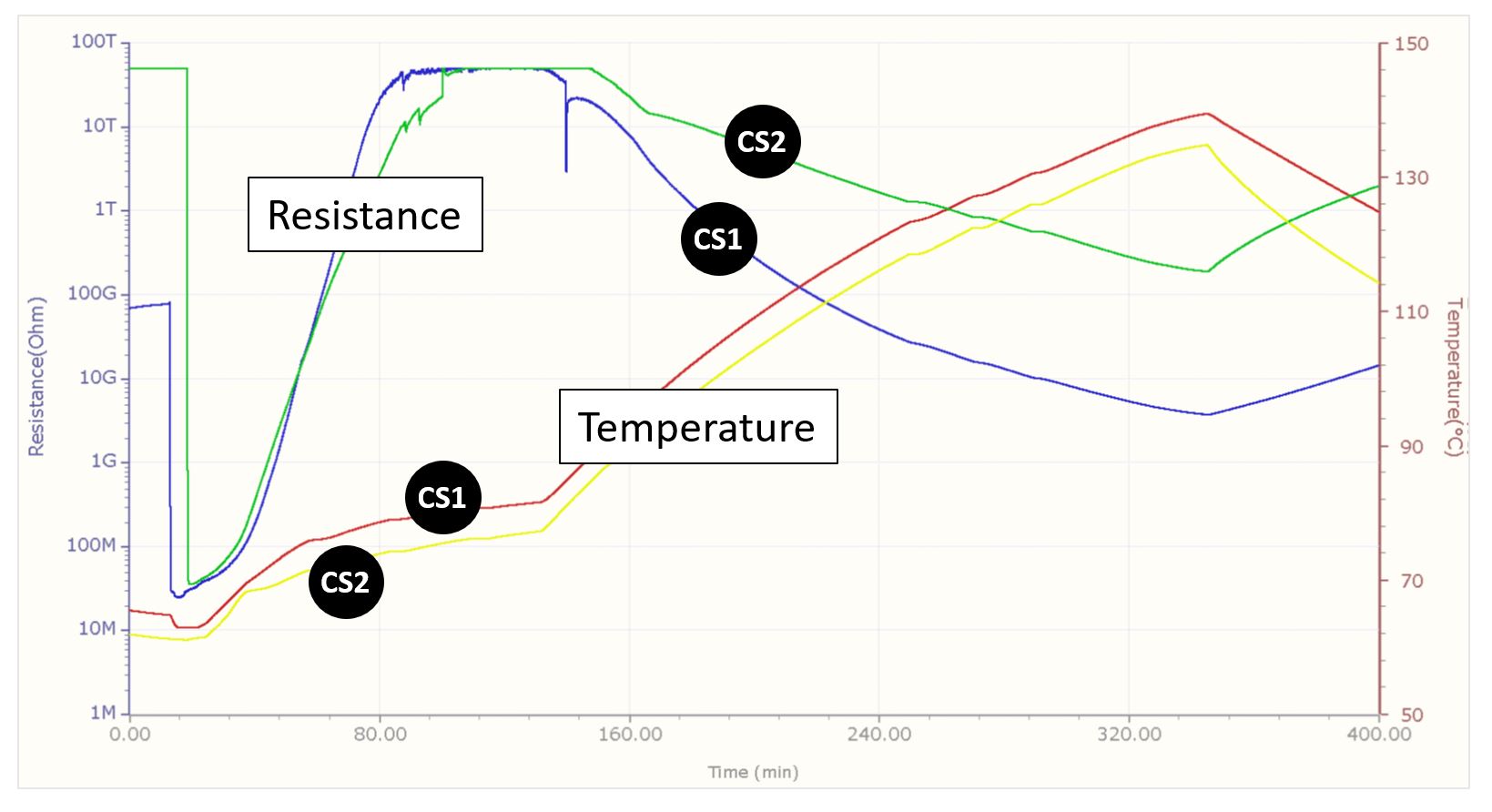
«Устройства OPTIMOLD и OPTIFLOW можно соединить вместе через Ethernet, так что все датчики могут быть записаны за один сеанс Optiview», - объясняет Пантелелис. «Таким образом, CS1 и CS2 были подключены к двум блокам OPTIMOLD, датчик потока 1 в форме и восемь одноразовых датчиков потока были подключены к трем блокам OPTIFLOW».
Эта система датчиков, устройств сбора данных OPTIMOLD / OPTIFLOW и программное обеспечение OPPTIVIEW / ORS затем применялась во время испытаний формования RTM для определения целей для различных стадий процесса, включая впрыск / инфильтрацию смолы и две мишени Tg. «Это была толстая деталь, сделанная из однонаправленного волокна и эпоксидной смолы Huntsman», - говорит Пантелелис. «В этом случае мы использовали проточные проволочные датчики для проверки потока в этих слоях UD, которые обычно плотно упакованы и могут создавать проблемы во время инфильтрации смолы».
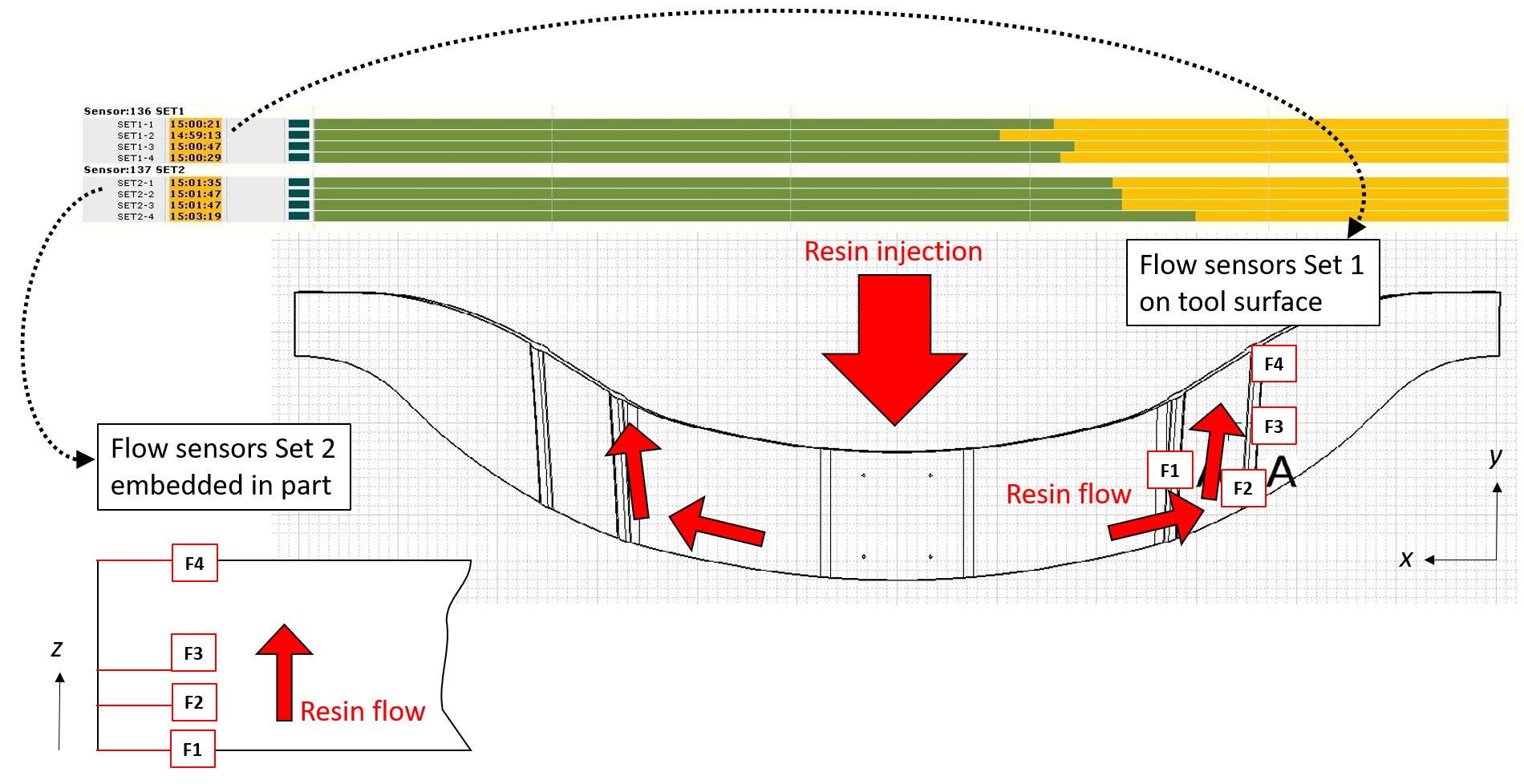
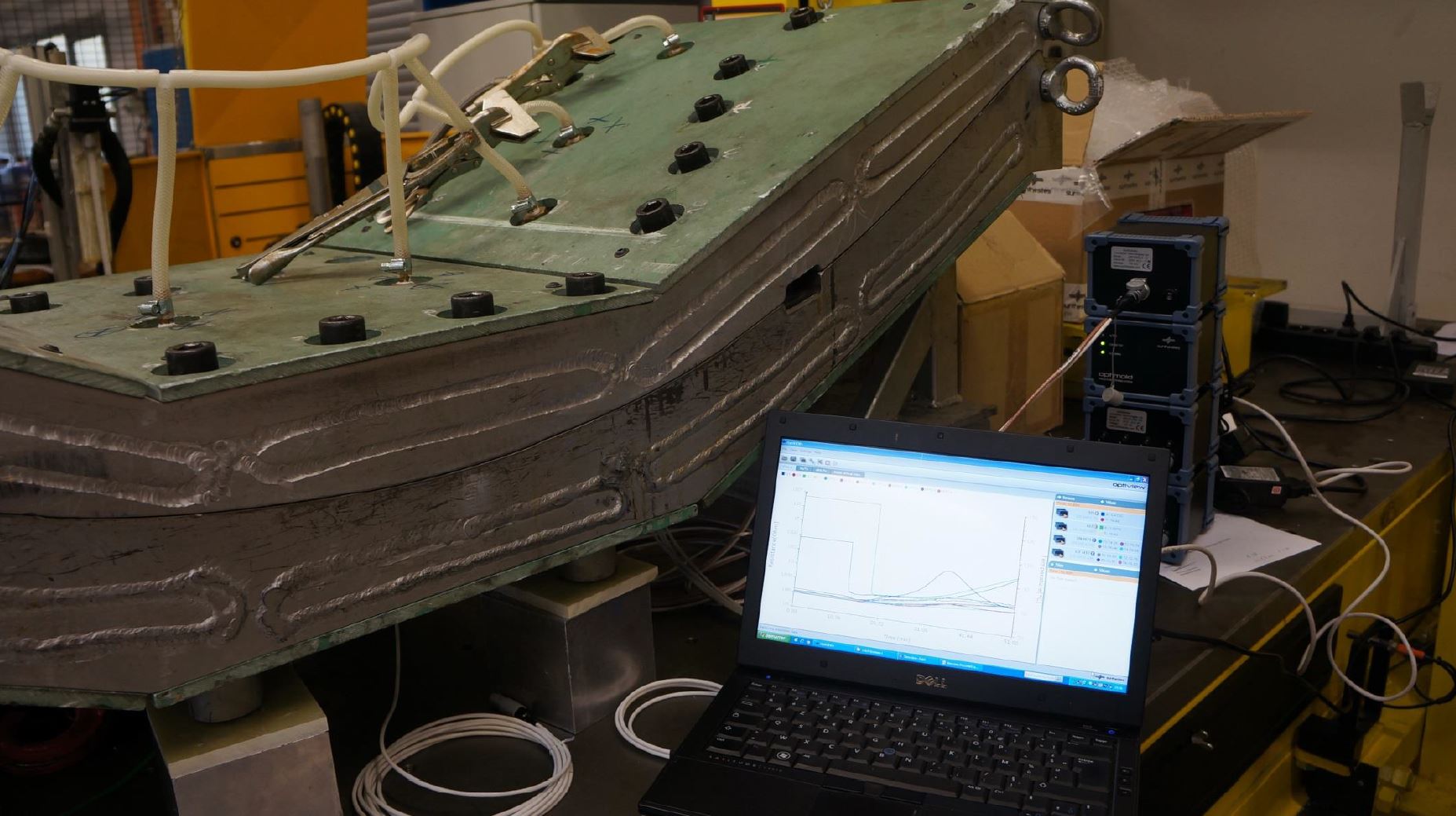
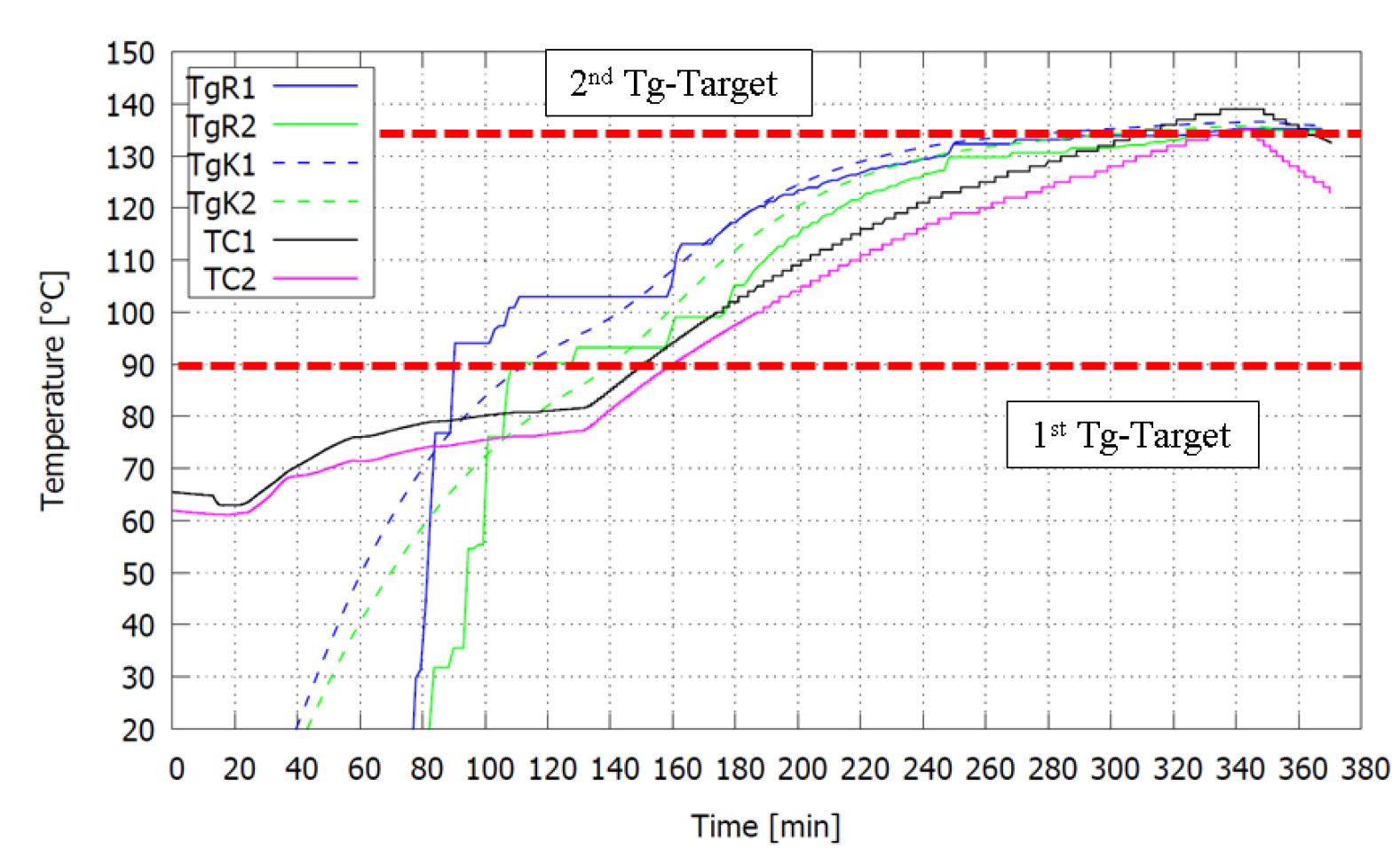
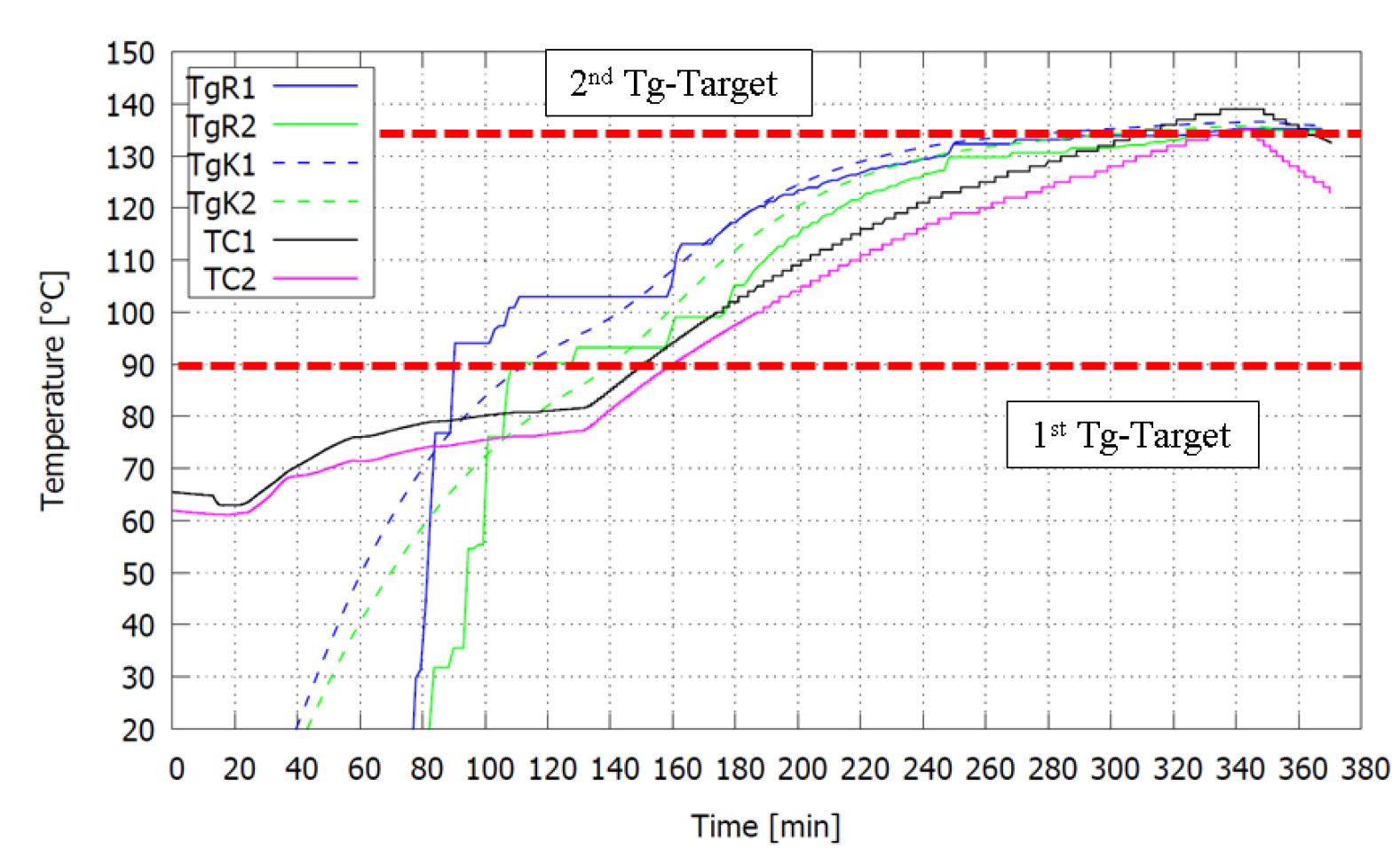
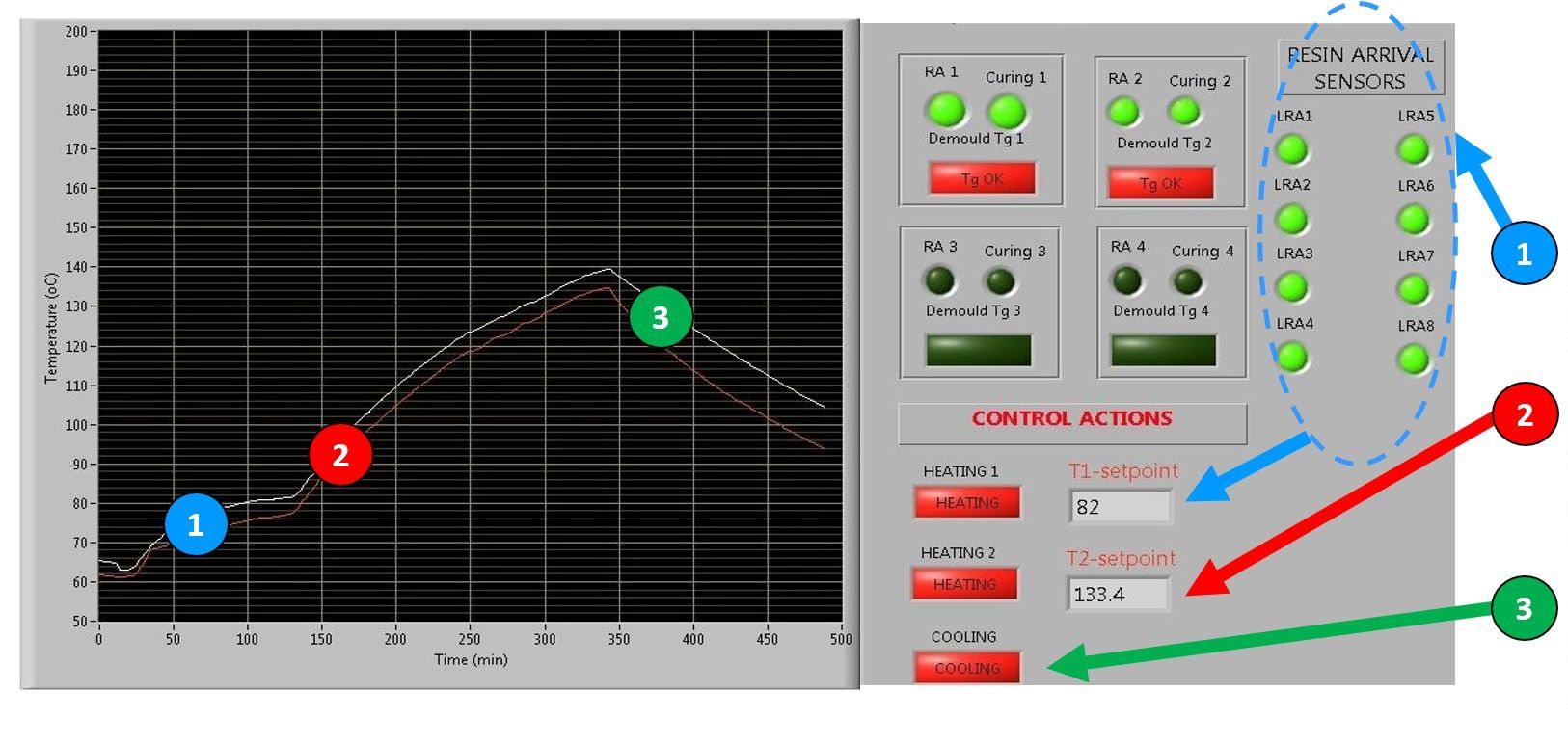
Используя эту систему управления технологическим процессом, проект ECOMISE в Hutchinson смог сократить цикл отверждения более чем на 30%.
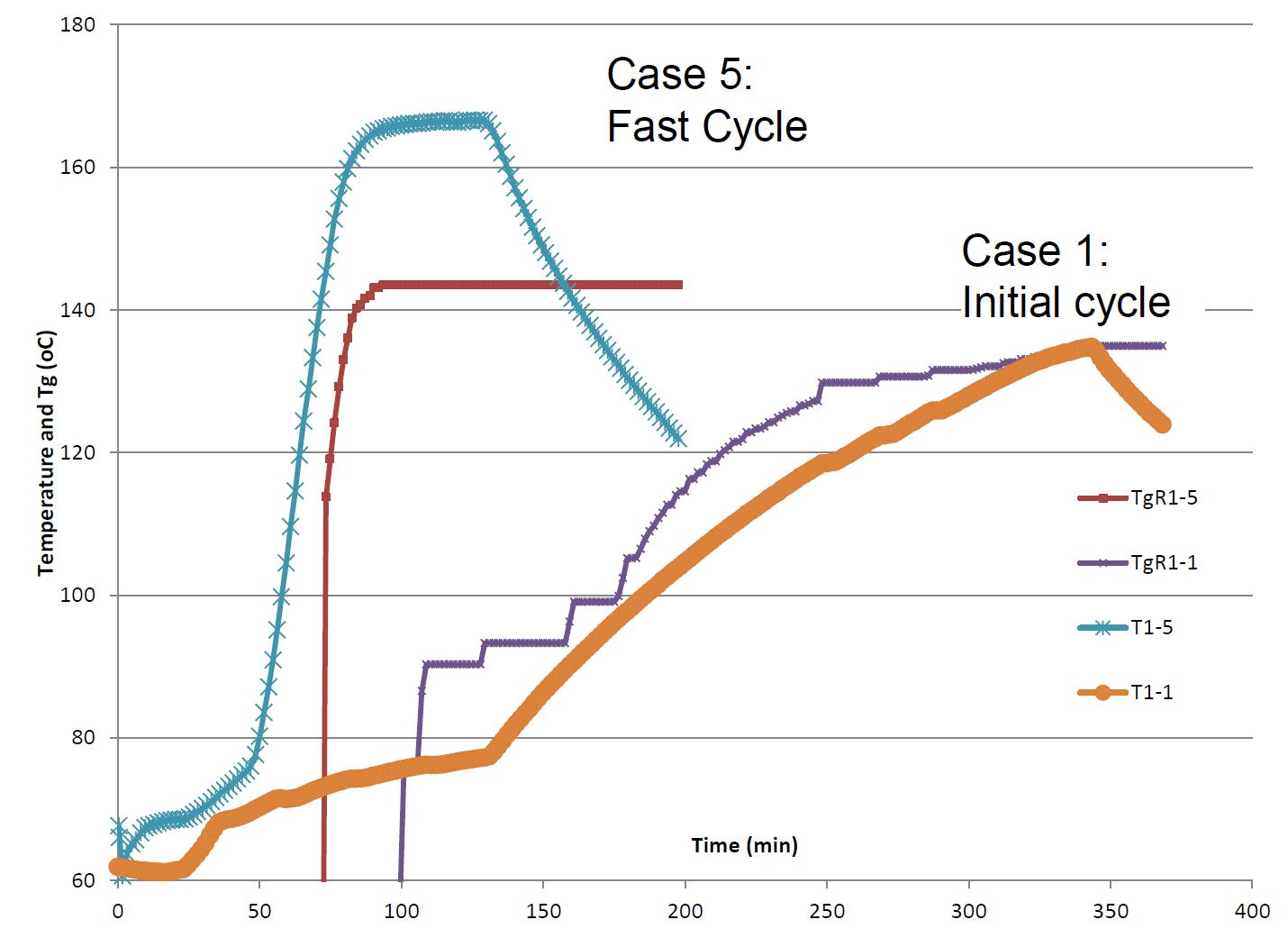
Калибровка
Для онлайн-мониторинга Tg требуется калибровка. Поскольку измерения собираются с датчиков с помощью устройств OPTIMOLD, программное обеспечение ORS переводит их в вязкость и Tg на основе калибровки для этой конкретной смолы. «Эта калибровка выполняется перед обработкой, чтобы обеспечить корреляции, которые программа ORS будет использовать для своих расчетов», - объясняет Пантелелис. «Мы калибруем, помещая смолу в реометр и измеряя температуру и вязкость. Затем, применяя соответствующие формулы, вы рассчитываете соответствующее сопротивление и Tg. Мы разрабатываем калибровку смол для наших клиентов на основе их стандартов и изучаем различные циклы отверждения смол. Эти данные калибровки затем используются программным обеспечением ORS при обработке этой смолы ».

Точность расчетов Tg программного обеспечения ORS в реальном времени была продемонстрирована в ходе испытаний производителем ветряных лопастей Carbon Rotec Composite Technology (Лемвердер, Германия). Tg, рассчитанный в режиме онлайн с помощью программного обеспечения ORS, сравнивали с Tg, измеренным сразу после извлечения из формы, с помощью дифференциального сканирующего калориметра (DSC). Для изотермической обработки средняя разница составила 1,61 ° C, а для неизотермической обработки - 2,15 ° C.
«Эта точность неоднократно демонстрировалась в частных проектах с другими заказчиками», - говорит Пантелелис.
Успехи для промышленного производства
Управление процессом на основе датчиков и данных действительно является большим шагом на пути к полностью автоматизированному и интеллектуальному производству композитов 4.0. Хотя он был продемонстрирован на ECOMISE, а также на NCC в Бристоле, он еще не используется в повседневном производстве. «Идея использования датчиков для определения Tg и последующего охлаждения действительно зародилась в производстве ветряных лопастей, - сообщает Пантелелис, - но она еще не полностью автоматизирована. Система подает сигнал при достижении целевой Tg, а затем оператор останавливает цикл отверждения. Автоматизация проста и будет завершена после того, как производитель подтвердит точность системы на пилотной стадии ».
«Для достижения этой цели мы разработали новую рабочую станцию, чтобы позволить производственному оператору контролировать автоматизированный процесс, который не требует участия с его стороны», - продолжает он. «При производстве лопастей ветряных турбин использование одной рабочей станции во время отверждения смолы и клея может сократить время цикла как минимум на 2-3 часа без ущерба для качества».
Хотя Bombardier Belfast, теперь Spirit AeroSystems, действительно использует оборудование Synthesites при производстве своего композитного крыла с пропиткой смолой для C-Series, теперь Airbus A220, управление процессом не автоматизировано. Однако Synthesites также работали с Bombardier в ECOMISE, и эта разработка продолжается. Одним из ключевых достижений стали датчики, которые проходят через стенку автоклава. Как объяснялось в моем блоге 2013 года «Композитное крыло серии C»:
Bombardier выполняет инъекцию после того, как образец был помещен в автоклав длиной 21,3 м и диаметром 5,6 м, что позволяет поддерживать температуру и давление на уровне, необходимом для снижения вязкости и смачивания - Cytec 890 - это вводится при 80˚C. . . После завершения впрыска смолы в автоклав во время уплотнения прикладывается положительное давление, в результате чего элементы инструмента закрываются, уплотняют влажный ламинат и выталкивают излишки смолы обратно из впускного отверстия для смолы в специально спроектированный отвал смолы.
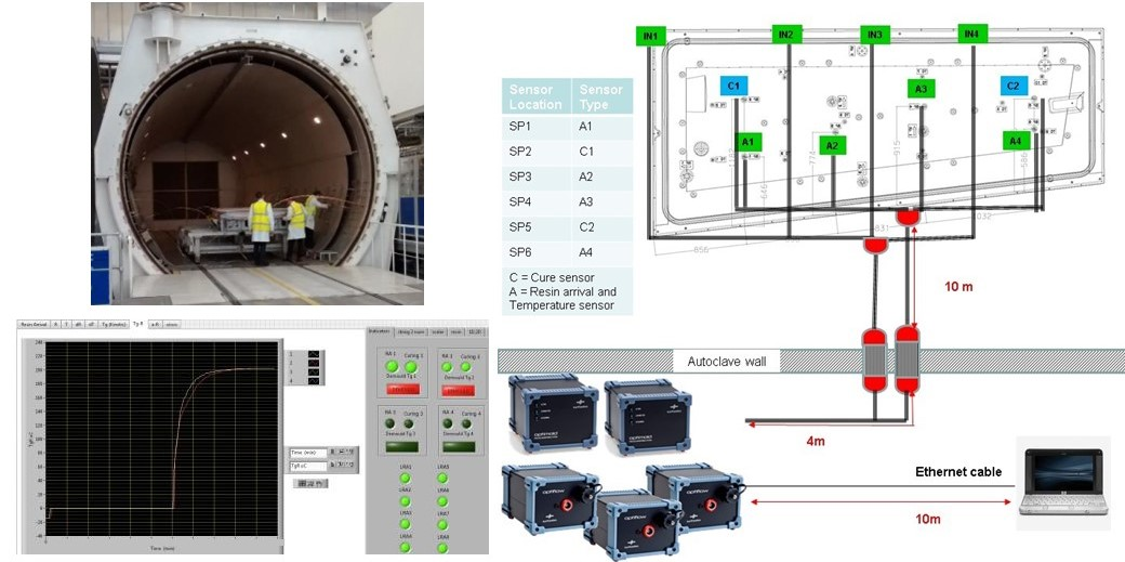
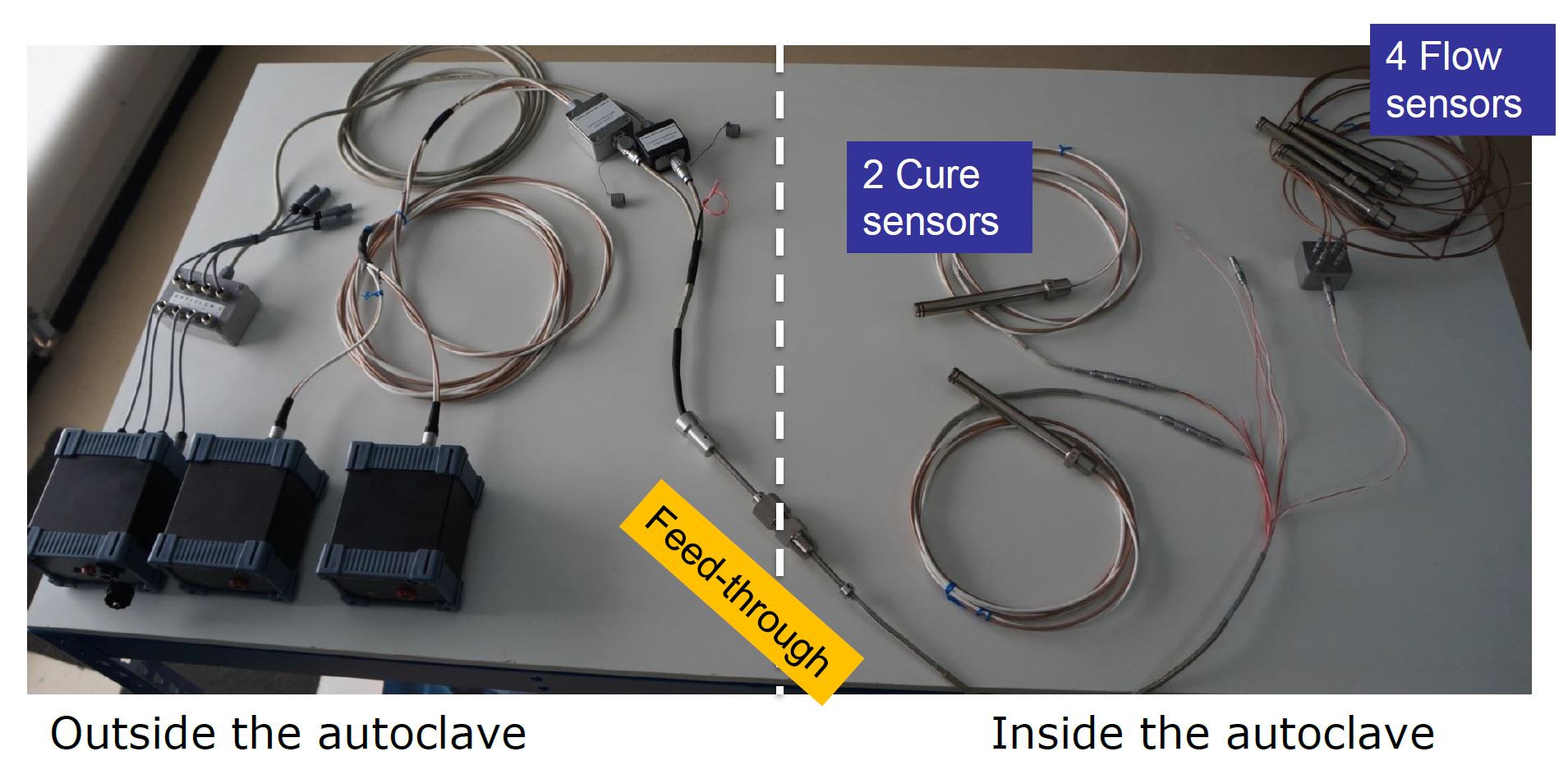
«Как и большинство производителей в коммерческой авиакосмической отрасли, он заинтересован в обеспечении качества и увеличении скорости», - объясняет Пантелелис. Приведенный ниже макет и результаты ECOMISE предназначены для демонстрации, а не для коммерческой части. В нем использовались два блока OPTIMOLD с двумя датчиками отверждения в форме и три блока OPTIFLOW с четырьмя датчиками потока в форме и четырьмя встроенными датчиками на вакуумных линиях. «OPTIFLOW может контролировать до четырех датчиков поступления смолы и четырех датчиков температуры / сопротивления», - отмечает Пантелелис. «Цели демонстрации были полностью достигнуты. Мы доказали, что датчики, проводка и системы могут без проблем работать в самых сложных аэрокосмических условиях. Интересно, что измерения поступления смолы показали большие различия по сравнению с моделированием потока. Кроме того, онлайн-мониторинг Tg показал, что цикл лечения для этого конкретного демонстратора мог быть значительно короче ».
«Сейчас мы разрабатываем систему мониторинга линий склеивания, - говорит Пантелелис, - в первую очередь для производства лопастей ветряных турбин, но в конечном итоге для любого процесса склеивания. Хотя в настоящее время мы очень заняты отраслью ветряных турбин, которая пытается снизить затраты, мы наблюдаем все больший интерес со стороны аэрокосмического сектора по мере того, как он движется к формованию жидких композитов для массового производства. Производители хотят получить больше информации о том, что именно происходит во время формования, и о том, как они могут стабилизировать и оптимизировать свои процессы ».
Проекты Ecomise и Recotrans получали финансирование от программ исследований и инноваций Европейского Союза FP7 и Horizon 2020 в соответствии с Соглашением о гранте № NMP2-SL-2013-608667 и 768737, соответственно.
Ссылки на раздел « Диэлектрический анализ (DEA), переменный и постоянный ток» включают:
- «Мониторинг УФ-отверждения в реальном времени» от VINCENTZ, опубликованный в European Coatings Journal, выпуск 11/2003, стр. 7.
- «Системы онлайн-мониторинга процессов - эталонное и тестовое исследование» Райнхольда Мейера 1 , Свен Заремба 1 , Флориан Спрингл 1 , Клаус Дрекслер 1 , Фабрис Гейл 2 и Кристиан Веймер 2 - 1 Институт углеродных композитов, ТУ Мюнхен, Гархинг, Германия. 2 Eurocopter Deutschland GmbH, Донаувёрт. Поточный процесс в композитных материалах - FPCM 11, 9–12 июля 2012 г., Окленд, Новая Зеландия.
- Неразрушающая характеризация материалов VIII под редакцией Роберта Э. Грина, Протоколы 8 th Intl. Симпозиум по неразрушающему контролю материалов, 16-20 июня 1997 г., Боулдер, Колорадо, США, опубликовано Springer Science &Business Media, стр. 384-385.
Еще одна полезная ссылка - это «Справочник по диэлектрическому анализу и мониторингу отверждения» Хуана Л. Ли, опубликованный Lambient Technologies.
Смола
- Датчики и процессоры объединяются для промышленного применения
- BASF и Toray в соглашении о поставке для производства лент CFRT для автомобильного и промышленного применения
- Сверхлегкие композиты TPE для обуви
- Композиты Solvay, выбранные для гоночного катамарана
- Hexion представляет двухкомпонентный эпоксидный раствор для производства аэрокосмических композитов
- LANXESS расширяет производственные мощности по производству термопластичных композитов, армированных непрерыв…
- Консорциум термопластичных композитов нацелен на крупносерийное производство для автомобильной и аэрокосм…
- Ультратонкие безбатарейные датчики деформации для промышленных роботов-манипуляторов
- Интеллектуальные датчики:преимущества и недостатки для промышленного оборудования
- Каковы инновации для промышленного обслуживания?