Композиты ускоряют изготовление бетонных фасадов
Каждое построенное сегодня многоэтажное здание требует фасада. Произведено от французского слова фасад . , которое, в свою очередь, произошло от итальянского facciata , это означает «лицо». Короче говоря, фасад - это внешняя структура, обращенная к публике, которая придает зданию его характер, цвет и форму. Для архитекторов фасад во многом задает тон остальной части здания и многое говорит об архитектурном замысле дизайнера.
Функционален и фасад. Он обеспечивает структуру, которая окружает окна и двери, защищает здание от погодных условий и ударов и влияет на энергоэффективность здания. Фасад может быть построен из различных материалов, включая композит, камень, сталь, стекло или бетон. Бетон в фасаде, благодаря своей пластичности, можно использовать для придания зданию больших размеров и визуально эффектного внешнего вида, особенно если бетонные формы различны.
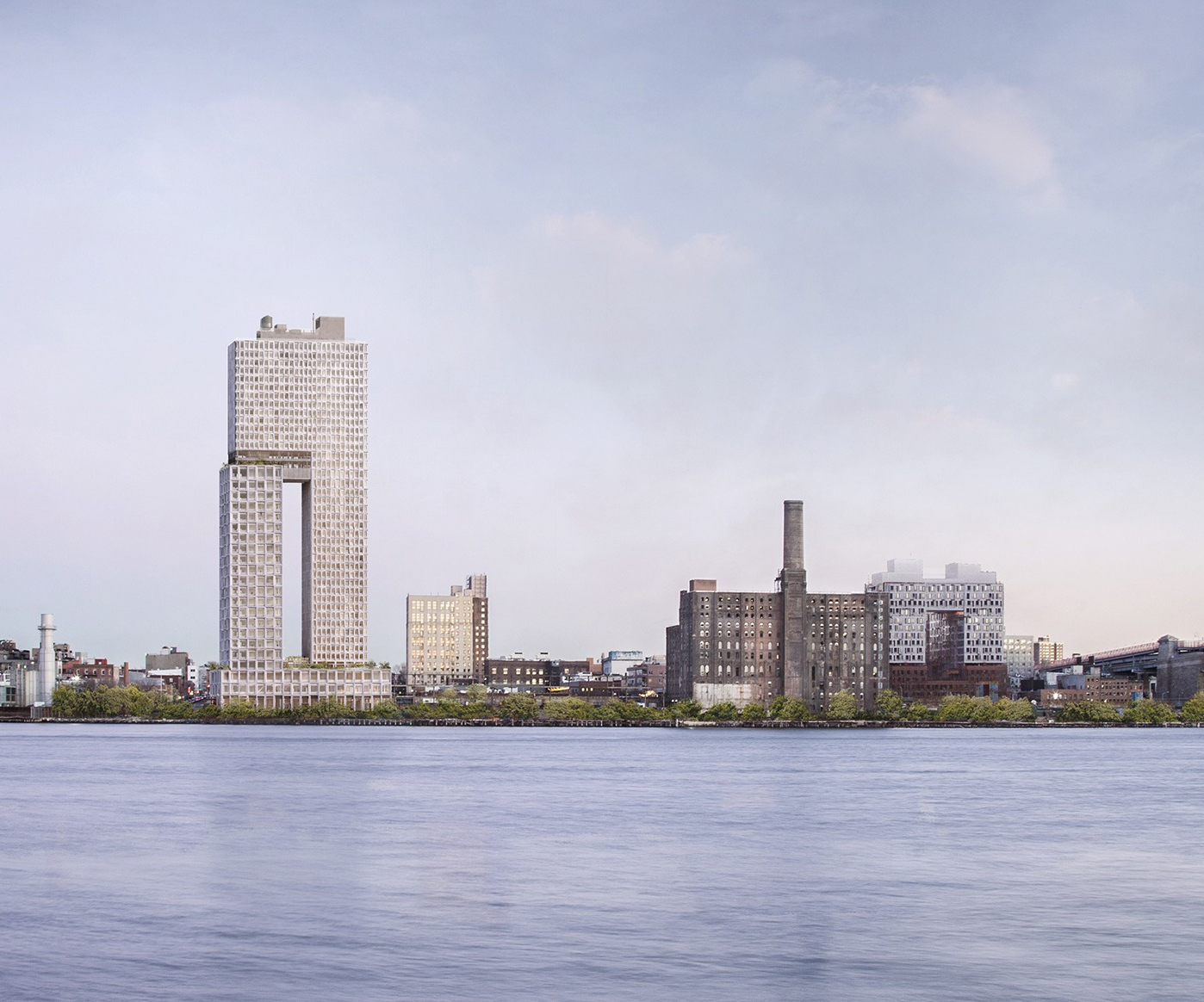
Сахар - король
Так было в Domino Park, проекте реконструкции площадью 11 акров вдоль набережной Вильямсбурга в Бруклине, штат Нью-Йорк, США. В центре Domino Park находится 138-летний завод по переработке сахара Domino, который был закрыт в 2004 году и в настоящее время ремонтируется. как офисные, так и торговые помещения. Часть Domino Park включает в себя несколько новых зданий, в том числе 45-этажный One South First и объединенный 10 Grand. Для этих зданий архитектор COOKFOX (Нью-Йорк, штат Нью-Йорк) решил использовать бетонный фасад с несколькими углами поверхности, несколькими формами оконных рам и различной шириной оконных рам, чтобы издалека слабо передавать ощущение кристалличности сахара в сохранение истории сайта.
Компания Gate Precast Co. (Джексонвилл, Флорида, США) выиграла контракт на строительство бетонного фасада - по сути, серии оконных рам - для проекта One South First. Компания, как это типично для бетонного фасада, изготовит рамы на собственном предприятии, а затем отправит готовые рамы на место работы, где они будут подняты на место для установки с помощью крана. Если бы Gate решила следовать традиции, она бы построила деревянные формы, с помощью которых можно было бы придать форму всем бетонным каркасам. Гейт, однако, решил не следовать традиции.
Чтобы понять это, вернемся в 2017 год, когда компания Gate объединилась с Институтом сборного и предварительно напряженного бетона (PCI, Чикаго, Иллинойс, США) и Национальной лабораторией Ок-Ридж (ORNL, Ок-Ридж, штат Теннеси, США) для проведения предварительной оценки использование широкоформатного аддитивного производства для создания композитных форм для внутризаводского формования сборного железобетона. Эта оценка была проведена с использованием машины BAAM (Big Area Additive Manufacturing) в ORNL. BAAM - это широкоформатная машина для аддитивного производства с рабочей зоной площадью 25 квадратных метров, разработанная совместно ORNL и Cincinnati Inc. (Харрисон, Огайо, США) Gate, которая занимается изготовлением композитных форм для фасада One South First. Всего для проекта потребовалось 80 форм, 37 из которых будут напечатаны. Остальные 43 будут деревянными. К моменту принятия этого решения сроки поставки пресс-форм были жесткими.
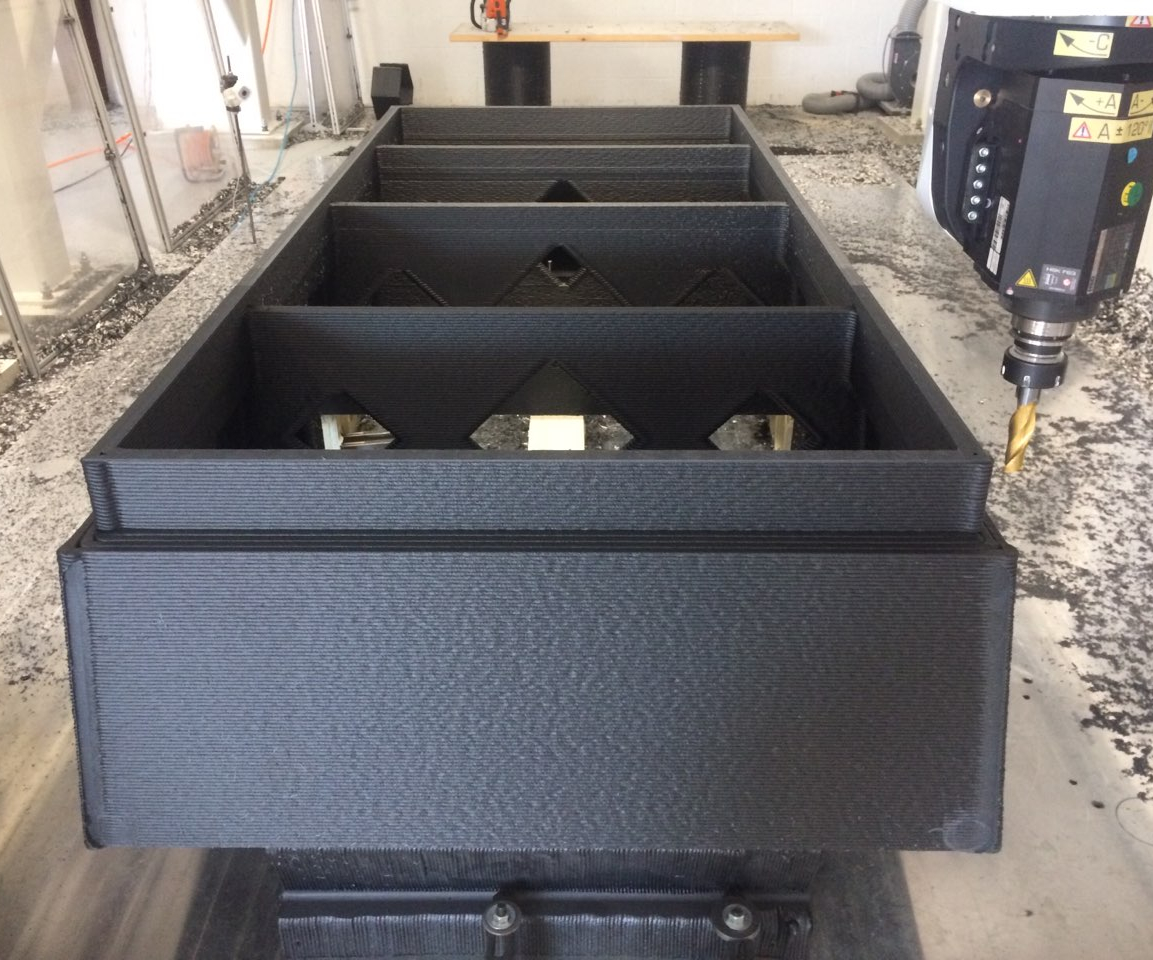
В 2016 году компания Additive Engineering Solutions (AES, Акрон, Огайо) приобрела свой первый станок BAAM у Cincinnati Inc. По этой причине ORNL и Gate Precast обратились за помощью к AES. Эндрю Бадер, вице-президент и соучредитель AES, говорит, что его компания и ORNL разделили рабочий пакет, и AES произвела 18 из 37 форм. Бейдер говорит, что каждая форма для оконных рам имеет ширину около 5-6 футов, высоту 9-10 футов, глубину 16 дюймов и весит около 500 фунтов.
Бадер говорит, что внутренняя геометрия форм, поскольку они предназначены для изготовления рам, окружающих прямоугольные окна, была относительно простой. Однако конструкция внешних поверхностей рам, как уже отмечалось, была более сложной, с различными глубинами и углами, встроенными в каждую форму. Одна печатная форма заменила деревянную форму, состоящую из множества индивидуально вырезанных частей, скрепленных вместе. «Геометрия была простой, но сложной, - говорит Бадер. «Для проекта требовалось несколько уникальных дизайнов рамы, в зависимости от расположения рамы».
Для части своего производства AES выбрала компаунд LNP THERMOCOMP AM, высокомодульный материал с низкой деформацией на основе АБС с 20% армирования рубленым углеродным волокном, поставляемый SABIC (Хьюстон, Техас, США). Бадер говорит, что на изготовление каждой монолитной формы на станке BAAM требовалось 8-10 часов, после чего следовало 4-8 часов механической обработки и чистовой обработки на станке с ЧПУ Quintax (Стоу, Огайо, США). Он сообщает, что формы были отшлифованы до необходимых размеров, но не запломбированы.
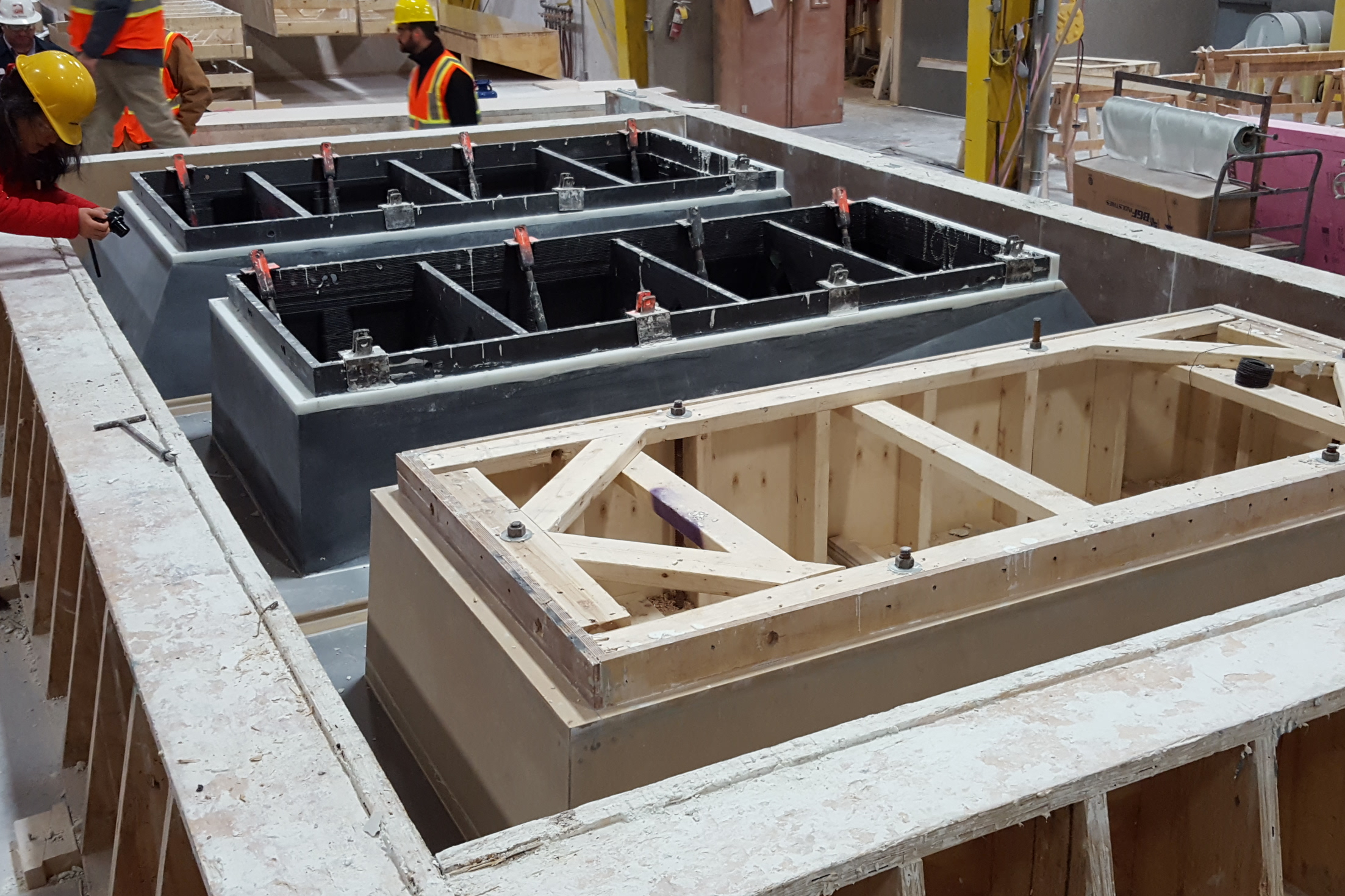
Изготовление оконных рам
Формы были доставлены на предприятие Gate’s Winchester, штат Кентукки, США, где они использовались вместе с 43 традиционными формами для дерева, которые компания Gate построила для этого проекта. Деревянные формы были собраны вручную сотрудниками Gate, затем были нанесены мат из стекловолокна и смоляное покрытие, а на них распылено формовочное масло, чтобы облегчить снятие формованного бетонного каркаса. Формовочное масло также распылялось на композитные формы для облегчения отсоединения.
Чтобы выполнить заливку бетона, несколько форм были размещены на деревянном литейном столе длиной 40-50 футов. Формы были объединены для производства одинарной, двойной или тройной рамы. Стальная арматура была размещена внутри каждой формы, и вокруг нее был залит бетон. Затем литейный стол подвергали вибрации для уплотнения бетона. После 14-20 часов отверждения оконные рамы были сняты, промыты кислотой и отполированы. Затем были установлены окна, и вся упаковка была доставлена грузовиком на строительную площадку в Бруклине.
Бадер говорит, что композитные формы AES, работающие вместе с традиционными формами для дерева, быстро показали свои преимущества. Во-первых, по его словам, деревянная опалубка позволяет заливать бетон только 15-20 раз, прежде чем ее нужно будет вывести из эксплуатации, отремонтировать или заменить. Формы AES, напротив, позволяли заливать 200 бетонных смесей с минимальным ремонтом или простоями. По словам Бадера, 200 заливок ознаменовали конец проекта, не окончание срока службы пресс-формы. «На этом они остановились», - говорит он. «Если за нашими формами ухаживать должным образом, мы думаем, что их можно использовать сотни и сотни раз».
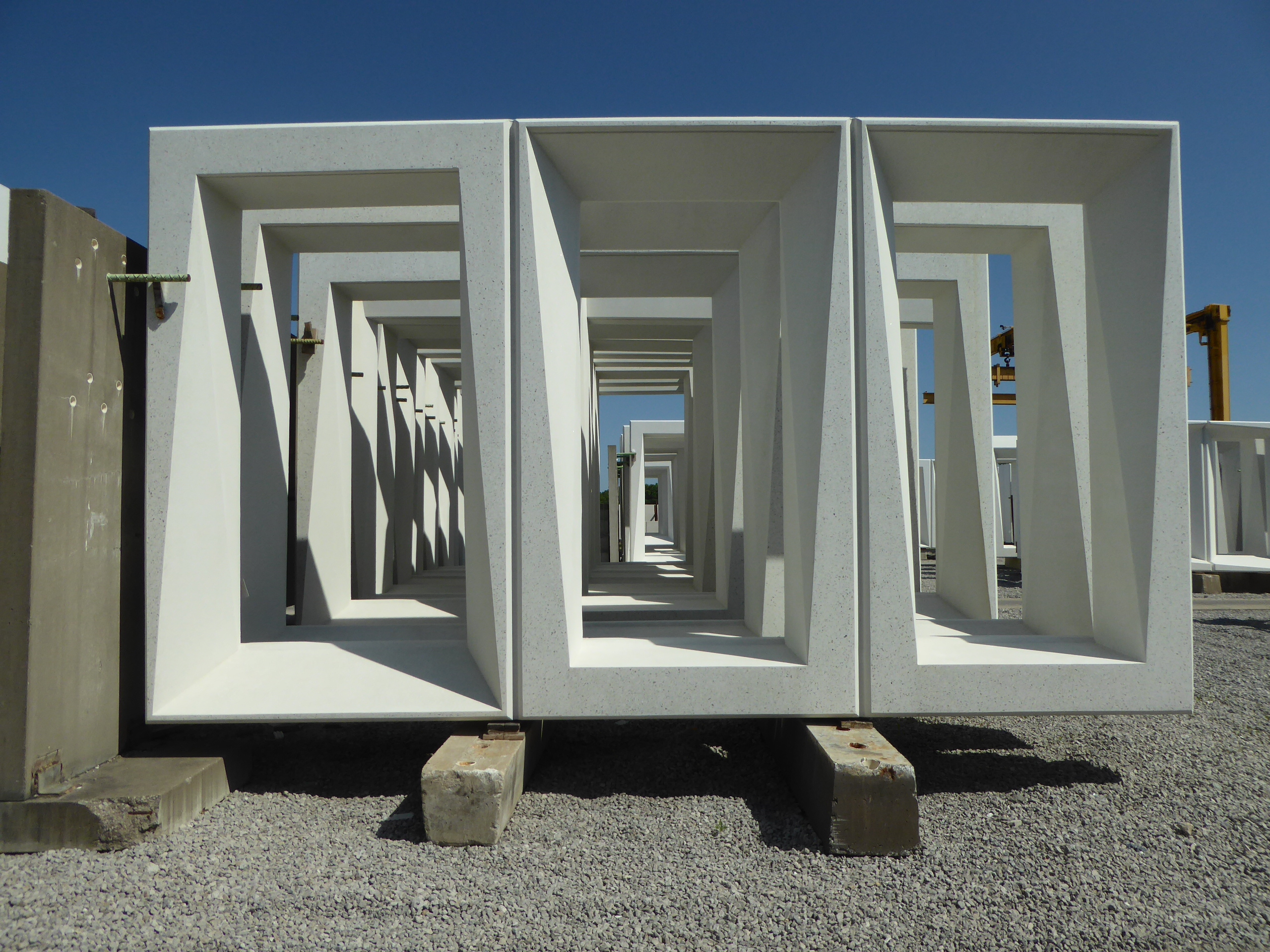
Кроме того, для использования 150 заливок или более, Gate рассчитывает, что потребуется до 10 форм для дерева, чтобы обеспечить производительность одной формы AES. Кроме того, учитывая, что на изготовление формы для дерева у Gate требуется 40 человеко-часов, без 37 композитных форм компания не выполнила бы требования графика проекта One South First.
Бадер признает, что композитная форма AES стоит в четыре раза дороже деревянной формы, но по крайней мере в 10 раз долговечнее. «Способ изготовления сборных железобетонных изделий оставался относительно неизменным на протяжении десятилетий», - утверждает Бадер. «Внезапно, однажды мы делаем 3D-формы весом 500 фунтов, и все были в шоке». При этом он признает, что аддитивное производство таких форм наиболее экономически выгодно в приложениях, где бетонные формы имеют сложную геометрию или часто повторяются - одна и та же форма много раз.
AES, сообщает Бадер, теперь владеет и эксплуатирует четыре станка BAAM и может производить детали высотой до 8 футов. Гораздо более крупные детали были построены путем соединения нескольких частей.
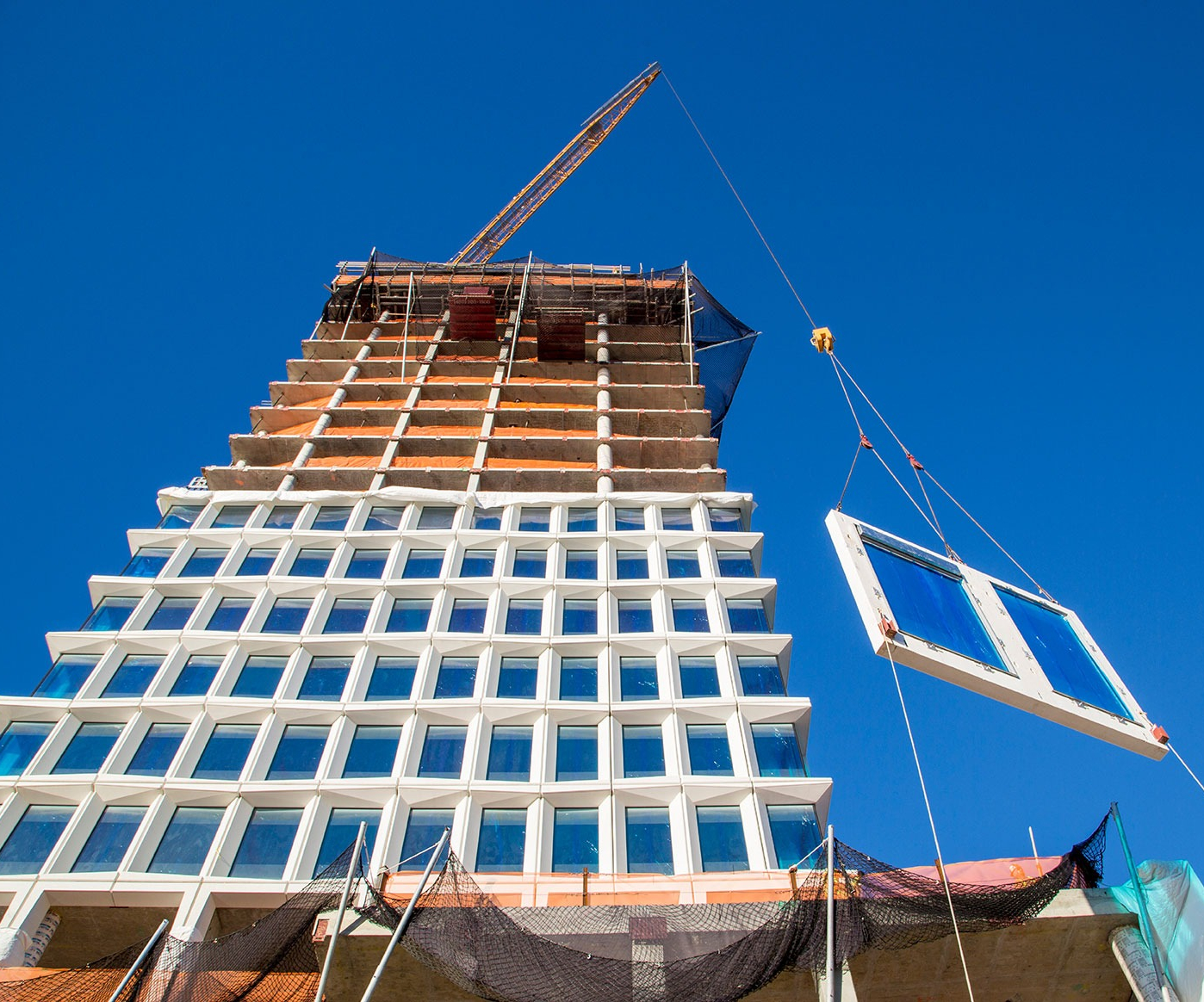
Смола
- Спидометр
- Бетон
- CompositesWorld SourceBook 2022
- Устранение проблем термоформования термопластичных композитов
- Развитие аддитивных композитов
- Термопластические композиты:структурный кронштейн бампера
- Композиты ATL вносят вклад в проект восстановления конкретной опоры
- RS Electric Boats выбирает Norco для изготовления композитов
- Сварка термопластичных композитов
- Высокопроизводительные композиты в Израиле