Демонстрация многофункционального фюзеляжа (MFFD)
Сниженные выбросы топлива и потребление энергии, а также способность производить узкофюзеляжные коммерческие самолеты со скоростью не менее 60 в месяц являются движущей силой развития технологий европейского партнерства Clean Sky 2 для самолетов следующего поколения, которые поднимутся в небо в 2035 году и в последующий период. . Легкие композитные материалы и более быстрые и экологически безопасные производственные процессы делают эти цели реальностью, особенно для проекта Многофункциональный демонстратор фюзеляжа (MFFD).
Основным результатом этого проекта, которым руководит Airbus (Гамбург, Германия) с партнерами из академических кругов и авиационной промышленности, является 8-метровый узкофюзеляжный узкофюзеляжный образец ствола фюзеляжа коммерческого самолета из термопласта длиной 8 метров, который будет производить 2022. MFFD - одна из трех полноразмерных секций фюзеляжа, производимых на платформе для демонстрации инновационных самолетов (IADP) компании Clean Sky 2.
Цели проекта MFFD, начатого в 2014 году, включают:
- Обеспечить производительность 60–100 самолетов в месяц.
- Уменьшить вес фюзеляжа на 1000 кг.
- Сократите текущие расходы на 20%.
Для достижения этих целей завершаются десятки отдельных проектов и рабочих пакетов, в ходе которых производятся две основные конструкции:верхняя оболочка фюзеляжа и нижняя оболочка фюзеляжа, которые будут сварены вместе, чтобы сформировать окончательный демонстрационный образец. Фактически, соединение без пыли (без креплений и отверстий) с помощью сварки является одним из основных компонентов программы. Обе половинки изготавливаются из термопластического препрега из легкоплавкого полиарилэфиркетона (PAEK) Toray Cetex TC1225 из углеродного волокна от Toray Advanced Composites (Морган Хилл, Калифорния, США). По словам доктора технических наук. Ларс Ларсен, руководитель отдела технологий соединения и сборки Немецкого аэрокосмического центра (DLR; Аугсбург, Германия), обе половины протестируют использование различных производственных технологий.
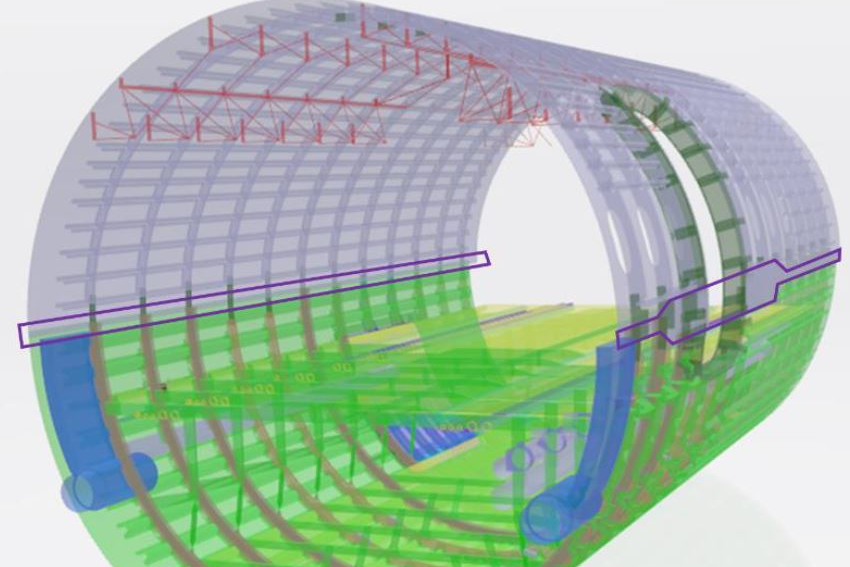
Нижняя часть фюзеляжа MFFD производится в рамках проекта STUNNING (УМНАЯ МНОГОФУНКЦИОНАЛЬНАЯ И ИНТЕГРИРОВАННАЯ ФЮЗЕЛЛЯ ИЗ ТЕРМОПЛАСТИКА), в основе которого находится множество проектов (таких как MECATESTERS, ориентированные на индукционную сварку). Нижняя секция будет включать нижнюю оболочку фюзеляжа со сварными стрингерами и шпангоутами, конструкцию кабины и грузового пола, а также соответствующие элементы интерьера и системы.
STUNNING возглавляет GKN Fokker (Папендрехт, Нидерланды) с ключевыми партнерами Diehl Aviation (Лаупхайм, Германия), Нидерландский аэрокосмический центр (NLR; Амстердам, Нидерланды) и Делфтский технологический университет (TU Delft; Делфт, Нидерланды). Проект направлен на дальнейшее совершенствование автоматизированных процессов сборки, технологий производства и сварки термопластов, комплексное проектирование и развитие производства, а также усовершенствованные архитектуры электрических систем.
«Наше влияние на промышленность двоякое:уровень автоматизации, который мы применяем при сборке демонстратора, и разработка экологически безопасных способов производства деталей», - говорит д-р Бас Вельдман, менеджер программы GKN Fokker.
Согласно статье Велдмана, опубликованной в феврале 2020 года, модульная сборка нижней части фюзеляжа является ключом к достижению цели сокращения времени производства. Для изготовления основной обшивки фюзеляжа большие заготовки из углеродного волокна / термопластического препрега укладываются с помощью автоматической машины для укладки ленты (ATL) с ультразвуковым или лазерным нагревом, но не консолидируются на месте. Детали укладываются с помощью автоматической машины для укладки волокон (AFP). Затем роботы помещают преформы в пресс-форму для внутреннего уплотнения, и после упаковки оболочка уплотняется в автоклаве. По словам Вельдмана, исследуются также и внеавтоклавные процессы. Стрингеры и рамы будут приварены к обшивке.
«Первоначально планировалось, что все детали будут изготовлены в этом году», - говорит Велдман, но из-за задержек, связанных с коронавирусом, «теперь он также переходит в следующий год. Но у нас есть довольно много деталей, которые уже завершены », в том числе многие из более мелких штампованных деталей, таких как зажимы, стойки и кронштейны, которые будут использоваться для крепления сидений самолетов и других компонентов. Подчеркивая экологичность производства, Велдман добавляет, что некоторые зажимы производятся из повторно используемых обрезков других частей демонстратора в рамках проекта Clean Sky 2 под названием ECO-CLIP.
С начала 2020 года в консорциум, производящий верхнюю часть корпуса длиной 8 метров, входят Airbus, Premium Aerotec (Аугсбург, Германия), которая является лидером в области промышленного и структурного проектирования; DLR, отвечающий за укладку обшивки и разработку сварочных технологий; и Aernnova (Витория-Гастейс, Испания), производящая стрингеры.
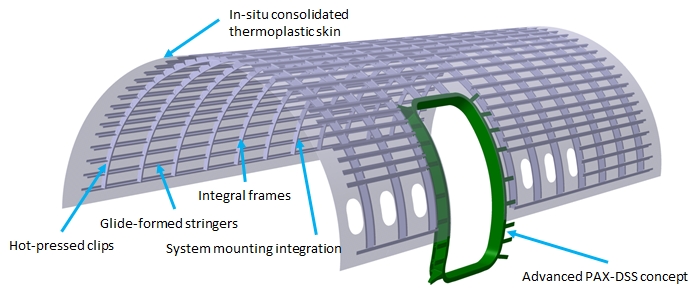
По словам Ларсена, для перехода авиакосмической промышленности на более дорогие термопластические материалы «мы должны показать, что можем снизить затраты во время производства». Консорциум верхней половины разрабатывает новую технологию продвинутого размещения волокон (AFP), в частности, консолидацию на месте для укладки углеродного волокна / оболочки PAEK, а также индустриализацию непрерывной ультразвуковой сварки и контактной сварки для интеграции стрингеров, рам и другие компоненты, повышающие безопасность и снижающие стоимость. DLR сначала создает преддемонстрационную испытательную оболочку длиной 1 метр для проверки технологий до того, как будет построен полномасштабный демонстратор, и планирует изготовить оболочку для преддемонстрационной оболочки к концу 2020 года. Интеграция стрингеры запланированы на начало 2021 года.
Ожидается, что полномасштабные версии обеих половин будут завершены к концу 2021 года. После завершения они будут вварены в финальный демонстрационный образец в Институте производственных технологий и передовых материалов им. Фраунгофера IFAM (Штаде, Германия).
Смола
- Выходя за рамки основ:машинное обучение и AM
- Преимущества составной конструкции самолетов для самолетов всех размеров
- Почему автоматизация - единственный путь вперед для производства
- 5 Роботизированные приложения в аэрокосмической промышленности
- Производственный ландшафт:оглядываясь назад и глядя в будущее
- Три преимущества переноса управления расходами в облако
- Первая секция фюзеляжа из композитных материалов для первого коммерческого реактивного самолета из компози…
- Обслуживание мира композитов в Израиле и США
- Что такое прямое напряжение диода?
- Производство азота в аэрокосмической промышленности