Индивидуальный процесс создает композитную педаль тормоза каждую минуту
Tier 1 Boge Rubber &Plastics Group (Дамме, Германия) производит, по ее словам, самые легкие, наименее дорогие и прочные полностью композитные педали тормоза в мире и первые в серийном производстве. Как подробно описано в январском FOD (см. «Термопластическая композитная конструкция заменяет металлы на педалях тормоза, критически важных для безопасности»), поставщик в настоящее время производит четверть миллиона педалей тормоза в год для четырех платформ автомобилей, производимых немецкими автопроизводителями, и система может производить до 1 миллион педалей ежегодно. Это важно, потому что педали являются конструктивными, они должны соответствовать тем же строгим требованиям к характеристикам, что и старая сталь и алюминий, а в конструкции используются три различных типа термопластичных композитов, армированных стекловолокном.
Три материала повышают эффективность волокна
Чтобы педали были легкими, тонкими, рентабельными и соответствовали сложным спецификациям производителей оригинального оборудования, Boge использует сплошной органо-лист из стекловолокна в качестве структуры оболочки, чтобы выдерживать основные нагрузки детали, которые могут достигать 3000 ньютонов. Заготовки из органолиста поставляются предварительно нарезанными по размеру, с полностью уплотненными двумя или тремя слоями поставщиком Lanxess Deutschland GmbH (Кельн, Германия). Чтобы усилить основные пути нагрузки на заготовке из органолиста, Boge добавляет полосы однонаправленных (UD) лент из стекловолокна (поставляемых Celanese Corp., Ирвинг, Техас, США) в ориентации и компоновки на основе результатов моделирования методом конечных элементов. Для этого компания Boge использует модифицированное программное обеспечение и карты материалов, разработанные компанией совместно со своими поставщиками на основе кривых напряжения / деформации, измеренных для каждого материала в условиях температуры и влажности, указанных OEM-заказчиками. Чтобы добавить функциональную геометрию, Boge использует формованные смеси из рубленого стекловолокна (от нескольких поставщиков) для создания структурных ребер и элементов крепления.
Все материалы содержат матрицы из предварительно окрашенного черного полиамида 6 (PA6), прочного полимера, широко используемого в автомобильной промышленности. Если этого требуют OEM-спецификации, Boge также имеет возможность использовать более высокотемпературную и менее гигроскопичную матрицу PA6 / 6 в компаунде для формования, поскольку оба полимера достаточно похожи, чтобы связываться друг с другом. Используя три различных типа композитов со стеклянным армированием в трех различных формах, Boge может размещать волокно именно там, где это необходимо, для удовлетворения требований к характеристикам, избегая при этом излишней инженерии. Эффект от этого гибридно-композитного подхода состоит в том, что он снижает расход материала, номинальную толщину стенки, время цикла и общую стоимость детали.
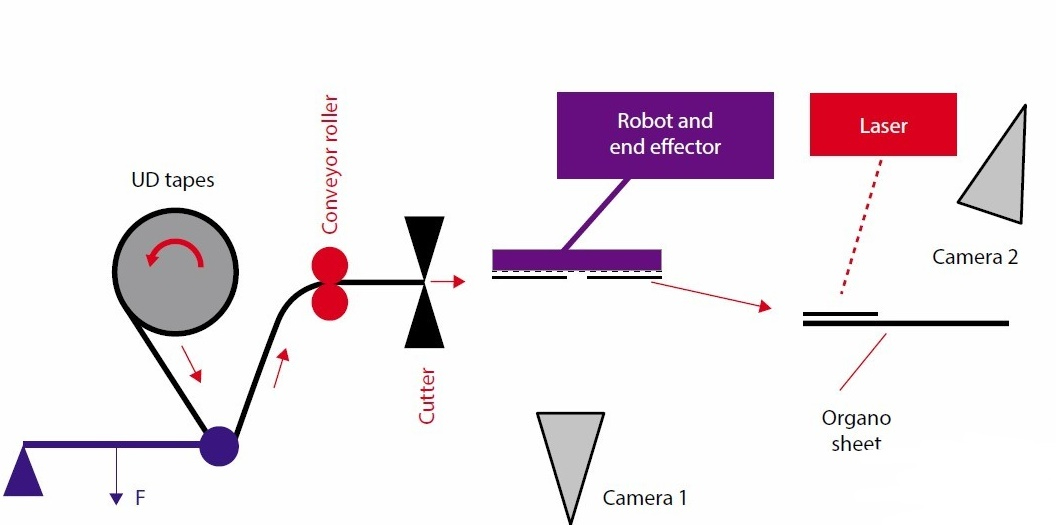
Этапы процесса и критерии оборудования
Партнерство с разработчиком автоматизации / сборочной линии M.A.i. GmbH &Co. KG (Кронах, Германия), Boge разработала трехэтапный производственный процесс, который является быстрым, эффективным и позволяет производить детали проверенного качества по доступной цене. При проектировании процесса и оборудования у команды был ряд требований. Во-первых, чтобы снизить затраты на детали, компаниям необходимо было поддерживать общее эффективное время цикла на уровне ~ 1 минуты. Достижение этого потребует автоматизации, чтобы материалы могли беспрепятственно перемещаться по производственной ячейке.
Во-вторых, хотя заготовки из органолиста поставляются предварительно уложенными, полностью консолидированными и предварительно нарезанными по размеру (контурными), требования к различным конструкциям педалей означали, что команде требовалась гибкость, чтобы разрезать, ориентировать и размещать полосы ленты разной длины в разных местах и направлениях для усиления основные пути нагрузки органо-оболочки. Опять же, чтобы снизить затраты, был разработан индивидуальный процесс укладки ленты, обеспечивающий высокий уровень гибкости и контроля, а также скорость.
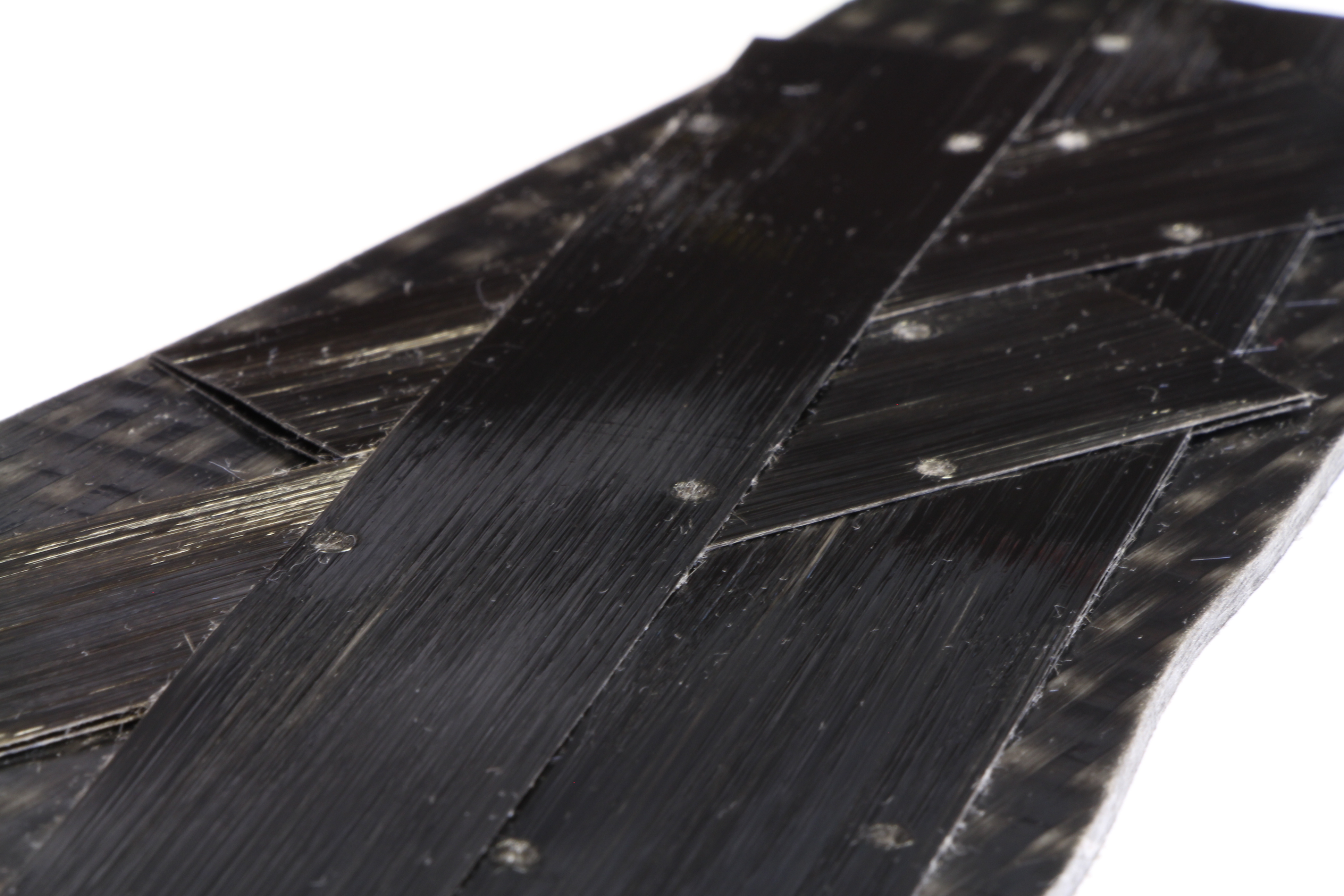
В начале процесса производственная ячейка вмещает две стопки предварительно нарезанных заготовки органолиста в кассетах и четыре шпателя лент UD одновременно. Сначала робот берет контурную заготовку из органолиста и перемещает ее на рабочую поверхность. Одновременно выдается лента UD и отрезается до необходимой длины. Затем полосы помещаются на вакуумную ленту, которая удерживает их на месте по мере продвижения конвейера. Затем робот с вращающимся устройством захвата и размещения (концевой эффектор) отрывает по одной полосе от вакуумной ленты, и камера проверяет каждую полосу на качество, размер и положение. Когда все четыре части подобраны, робот перемещается в рабочее пространство и начинает размещать по одной полоске на заготовке органолиста в месте и положении, определенном с помощью коррекции положения на основе изображения. При позиционировании каждой полосы предотвращается ее смещение за счет множества точечных сварных швов, созданных лазером. Тем временем на вакуумной ленте нарезается больше лент, и процесс повторяется до тех пор, пока все ленты, необходимые для данной конструкции педали тормоза, не будут сложены в стопку и прикреплены в правильном положении на органолите.
Система, которая производит эту специально подобранную оптоволоконную заготовку, на 100% контролируется численно, при этом каждый аспект операции полностью программируется для максимальной гибкости. На каждом этапе камеры или другие датчики, подключенные к системе онлайн-контроля качества (QC), обнаруживают все края и положения лент ленты и оболочки органолиста и сравнивают геометрические данные для этих материалов с известными параметрами, чтобы гарантировать, что каждый материал пригоден. расположен там, где он должен быть.
Чтобы поддерживать высокую скорость производства, заготовка из специально разработанного волокна затем перемещается в инфракрасную печь для нагрева обоих материалов непосредственно перед нанесением / предварительным формованием / уплотнением лент на органолист. Специальный пакет антиоксидантов в системах из ленты и органолиста предотвращает термическое повреждение. Затем горячая заготовка быстро перемещается в полость для формования / предварительного формования, где используется высокое давление для придания заготовке U-образной формы, обеспечивая при этом высококачественную поверхность. Система контроля качества снова контролирует качество уплотнения и предварительного формования по времени, температуре и давлению.
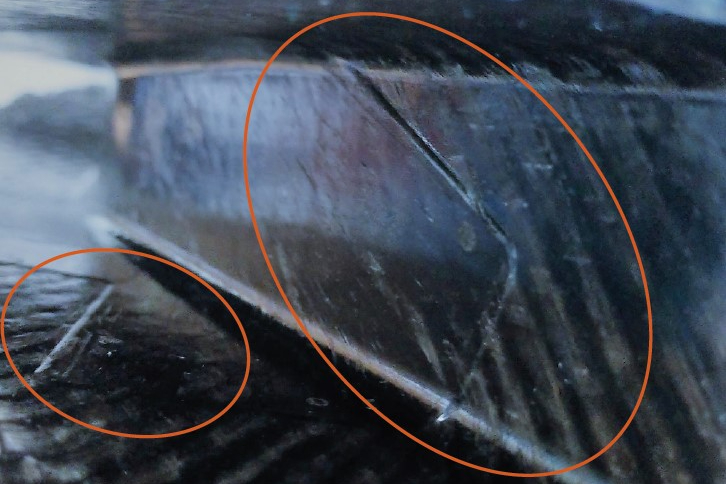
Наконец, еще теплый и драпированный материал перемещают в форму для литья под давлением, где на него формуют смесь из короткого стекла и полиамида для создания дополнительной геометрии, такой как сложная ребристая структура на нижней стороне. После извлечения из формы выполняется быстрая автоматическая обрезка и визуальный осмотр. Никакой краски или другой отделки поверхности не требуется. Окончательный размер педали составляет примерно 350 x 90 x 60 миллиметров. Перед тем, как покинуть производственный цех, к каждой педали прикрепляется уникальный QR-код, чтобы связать его с данными о производстве и материалах для этой педали в системе качества. После сборки выполняется функциональное испытание педали в ее кронштейне и окончательная роботизированная проверка. Предполагая, что устройство прошло успешно, на готовую педаль тормоза в сборе наносится еще один QR-код, чтобы обеспечить полную прослеживаемость каждой педали и дополнительных компонентов до их отправки производителю.
Поскольку педали тормоза являются критически важными деталями и должны соответствовать высоким требованиям производителей оборудования, а также требованиям качества, компания Boge и ее партнеры встроили несколько отказоустойчивых механизмов в систему контроля качества, совместимую с Индустрией 4.0, чтобы быстро и точно проверять соответствие спецификациям на каждом этапе. процесс. Данные контроля качества сохраняются, и каждая педаль получает уникальный идентификационный номер в виде QR-кода, чтобы гарантировать 100% отслеживаемость материала, смен и условий процесса, участвующих в производстве этой детали.
Цельнокомпозитные педали тормоза, которые производит Boge, примерно вдвое легче металлических педалей. Они также улучшают тактильные ощущения от вождения для потребителей, полностью пригодны для вторичной переработки в конце срока службы и соответствуют или превышают требования к прочности для существующих сталей.
Смола
- Самые популярные методы изготовления композитов
- Криогенное удаление заусенцев и удаление заусенцев
- Первая полностью пластиковая педаль тормоза для спортивного электромобиля с аккумулятором
- Solvay увеличивает емкость термопластичного композитного материала
- Колесо из термопласта выходит на неровную дорогу
- Представлен композит для архитектурной облицовки
- Создание лучших композитных велосипедов в Арканзасе
- Как работает процесс CMC
- 4 важные вещи, которые должен знать каждый оператор листогибочного пресса
- 4 вещи, которые каждый оператор листогибочного пресса должен знать во сне