Влияние подповерхностных дефектов, вызванных механической обработкой, на эволюцию дислокаций и механические свойства материалов посредством наноиндентирования
Аннотация
Подповерхностные дефекты оказывают значительное влияние на точность и характеристики наноструктур. В этой статье выполняется молекулярно-динамическое моделирование наноиндентирования для исследования влияния подповерхностных дефектов, вызванных механической обработкой, на эволюцию дислокаций и механические свойства материалов, в которых модель образца с подповерхностными дефектами создается с помощью нанорезки в соответствии с реальностью. Обсуждается механизм образования подповерхностных дефектов и механизм взаимодействия машинных дефектов с эволюцией дислокаций. Рассчитаны твердость и модуль упругости монокристаллических образцов меди. Результаты моделирования показывают, что существуют стабильные остатки дефектной структуры под поверхностью детали, такие как атомные кластеры, тетраэдрические дефекты упаковки и ступенчатые дислокации стержня. Вторичная обработка наноиндентирования может восстановить внутренние дефекты заготовки, но подповерхностные повреждения в зоне вторичной обработки усугубляются. Твердость образцов на наноиндентировании увеличивается с введением подповерхностных дефектов, что приводит к формированию эффекта наклепа. Наличие подповерхностных дефектов может ослабить способность материала противостоять упругой деформации, в которой важную роль играет взаимная эволюция дислокаций и подповерхностных дефектов.
Фон
Сверхточное изготовление в нанометровом масштабе широко считается эффективным методом получения нанокомпонентов с субмикронной точностью размеров и качеством поверхности в нанометровом масштабе [1]. Некоторые устойчивые подповерхностные дефекты остаются внутри детали после изготовления [2,3,4,5]. Подповерхностные дефекты не только влияют на точность обработки и качество поверхности, но и критически влияют на механические свойства и срок службы нанокомпонентов. Многие исследования подповерхностных дефектов проводились методом молекулярной динамики (МД), в основном сосредотачиваясь на формировании и развитии подповерхностных дефектов s [6, 7], толщине слоя подповерхностных дефектов (SSD) [8, 9] и влияние подповерхностных дефектов на целостность поверхности [10, 11]. Однако влияние подповерхностных дефектов на механические свойства материалов заготовок изучено меньше. Механические свойства наноструктур имеют решающее значение для их эксплуатационных характеристик и срока службы. Таким образом, влияние подповерхностных дефектов на механические свойства материалов стало ключевой проблемой, требующей исследования.
Было проведено множество исследований для определения слоя SSD с помощью молекулярно-динамического моделирования процесса нанорезки. Нараянан [12] изучил образование тетраэдрических дефектов упаковки (SFT) в монокристалле золота и представил механизм SFT, вызванный деформацией. Инамура [13] исследовал стружкообразование и деформацию проскальзывания материала во время процесса нанорезки и указал, что стружкообразование в основном вызывается деформацией сдвига-проскальзывания. Пей [14] изучил влияние параметров резания на эволюцию дислокаций и принудительное резание во время процесса наноразрезки и обнаружил, что, когда размер заготовки превышает 40 нм, размерный эффект не является значительным. Дай [15] и Лю [16] применили методы МД-моделирования и эксперимента, соответственно, для изучения влияния структуры алмазного инструмента и размерного эффекта на развитие подповерхностных дефектов детали. Предыдущие исследования показали, что после нанорезки в заготовке существуют устойчивые подповерхностные дефекты. Параметры резания и параметры геометрии инструмента имеют большое влияние на толщину и эволюцию подповерхностного поврежденного слоя и даже на точность обработки. Однако механические свойства материалов заготовок невозможно рассчитать, анализируя соответствующие данные, полученные с помощью нанорезки.
Нано-вдавливание - эффективный метод для характеристики механических свойств, таких как твердость и модуль упругости [17]. Было проведено множество исследований наноиндентирования для оценки механических свойств с помощью экспериментальных и теоретических моделей. Циммерман [18] проанализировал эмиссию дислокаций в процессе наноиндентирования по вектору скольжения. Ruestes [19] исследовал наноиндентирование монокристалла Fe с помощью МД-моделирования и обнаружил, что образование дислокаций в подповерхностном слое необходимо для удаления материала из зоны вдавливания. Хуанг [20] выполнил МД-моделирование наноиндентирования на монокристаллической алмазной матрице и обнаружил, что деформация алмазного материала при вдавливании определяется зарождением и распространением дислокационных петель 〈110〉 {111}. Шарма [21] искусственно построил модель твердых частиц в медной матрице и проанализировал влияние твердых частиц на развитие подповерхностных дефектов в процессе обработки. Пэн [22] исследовал механизмы упрочнения графеновых покрытий на подложке Cu за счет наноиндентирования, которое возникает в результате эффекта гомогенизации напряжений, создаваемого границей раздела. Из приведенного выше анализа можно увидеть, что предыдущие исследования влияния подповерхностных дефектов в основном основывались на идеальных кристаллических материалах или искусственном построении гипотетических дефектов, которые далеки от реальных подповерхностных дефектов. Следовательно, построение модели детали с подповерхностными дефектами в реалистичном режиме важно для анализа влияния подповерхностных дефектов на механические свойства детали.
В данной работе метод наноразрезки был использован для получения модели детали с подповерхностными дефектами, соответствующей практическим характеристикам. На этой основе было проведено моделирование наноиндентирования для изучения влияния подповерхностных дефектов на механические свойства монокристаллической меди. Во-первых, будет обсужден механизм образования и эволюции подповерхностных дефектов в процессе наноразрезки, а также проанализированы типичные дефектные структуры подповерхностного слоя заготовки после наноразрезки. Во-вторых, будет проанализирован механизм взаимодействия между подповерхностными дефектами, вызванными механической обработкой, и зарождением дислокаций во время индентирования. В-третьих, на основе данных «нагрузка-смещение», полученных с помощью наноиндентирования, будут рассчитаны твердость и модуль упругости образцов монокристаллической меди. Наконец, будут подведены некоторые новые выводы.
Методы
Имитационная модель
Чтобы исследовать влияние подповерхностных дефектов на механические свойства материалов при нанообработке, необходимо построить модель образца с подповерхностными дефектами. В данном исследовании это реализовано с помощью МД моделирования процесса нанорезки. Прежде всего, создается имитационная модель МД и выполняется моделирование процесса нанорезки. Затем образец и режущий инструмент расслабились на достаточное время во время моделирования МД . Наконец, некоторые стабильные дефекты остались в подповерхностном слое заготовки. Принципиальная схема трехмерных моделей МД показана на рис. 1, в котором модель нанорезания показана на рис. 1а, а модель наноиндентирования с подповерхностными дефектами показана на рис. 1б. На рис. 1 материалы заготовки и образца - монокристаллическая медь, а инструмент и индентор - алмазные материалы. Алмазный инструмент с дуговым лезвием используется в процессе нанорезки, а радиус кромки инструмента составляет 3 нм. Индентор имеет форму полусферы в процессе наноиндентирования, диаметр - 6 нм. Заготовка и образец разделены на три части:слой Ньютона, температурный слой и пограничный слой соответственно. Чтобы уменьшить размерный эффект и граничный эффект, периодическое граничное условие (PBC) принимается в направлении [010] системы моделирования. Чтобы избежать первоначального взаимодействия между инструментом и заготовкой, режущий инструмент помещают на 3 нм вверху справа от заготовки, а индентор помещают на 6 нм выше образца. Подробные параметры моделирования показаны в таблице 1.
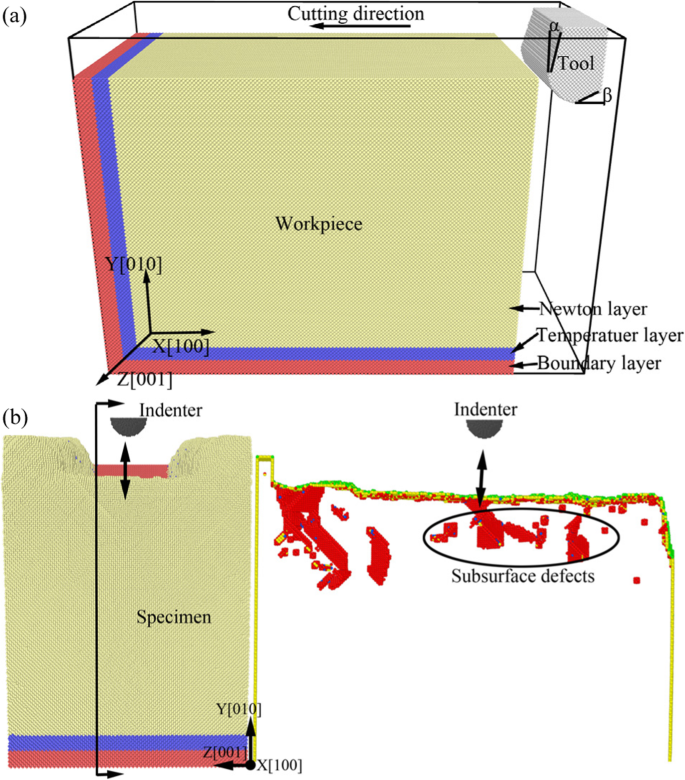
Принципиальная схема имитационных трехмерных моделей монокристалла меди для нанорезки и наноиндентирования. а Модель для процесса нанорезки. б Модель процесса наноиндентирования с подповерхностными дефектами
Межатомные потенциальные функции
В этом исследовании трехмерное моделирование МД было выполнено с помощью крупномасштабного атомно-молекулярного массово-параллельного симулятора (LAMMPS). Параллельные вычисления реализованы с помощью библиотеки интерфейсов передачи сообщений. В моделировании используются потенциал Морзе, потенциал метода встроенного атома (EAM) и потенциал Терсоффа, которые вызываются из программного пакета LAMMPS. Взаимодействие между атомами Cu в заготовке и атомами C в инструменте рассчитывается с помощью потенциала Морзе, который показан в формуле. 1 [23].
$$ u \ left ({r} _ {ij} \ right) =D \ left [\ exp \ left (-2 \ alpha \ left ({r} _ {ij} - {r} _0 \ right) \ right) ) -2 \ exp \ left (- \ alpha \ left ({r} _ {ij} - {r} _0 \ right) \ right) \ right] $$ (1)где r 0 , α , и D соответственно - межатомные расстояния, модуль упругости и энергия связи. Значение показано в таблице 2.
Межатомная функция между атомами Cu в заготовке описывается потенциалом EAM, который показан в уравнениях. 2, 3 [24, 25].
$$ E =\ sum \ limits_i ^ N \ left [F \ left ({\ rho} _i \ right) + \ sum \ limits_ {j> i} ^ Nu \ left ({r} _ {ij} \ right) \ right] $$ (2) $$ {\ rho} _i =\ sum \ limits_jf \ left ({r} _ {ij} \ right) $$ (3)Взаимодействие между атомами углерода в алмазном инструменте рассчитывается с помощью потенциала Терсоффа, который показан в уравнениях. 4, 5 [26].
$$ E =\ frac {1} {2} \ sum \ limits_ {i \ ne j} {V} _ {ij} $$ (4) $$ {V} _ {ij} ={f} _c \ left ({r} _ {ij} \ right) \ left [{V} _R ^ {\ hbox {'}} \ left ({r} _ {ij} \ right) + {b} _ {ij} {V} _A \ left ({r} _ {ij} \ right) \ right] $$ (5)где f c ( г ij ) - функция усечения между атомами, V А ( г ij ) - двойственный потенциал члена поглощения, V R ( г ij ) - член двойственного потенциала отталкивания, а r ij атомное расстояние между атомом i и атом j .
Методы анализа дефектов
При нанорезке монокристаллической меди деформации и дислокации зарождаются на поверхности детали. В этой статье параметр центросимметрии (CSP) вводится для анализа зарождения дислокаций и эволюции дефектов в заготовке. Для материалов кубической формы с центром в центре (FCC) значение CSP может быть рассчитано по формуле. 6 [27].
$$ CSP =\ sum \ limits_ {i =1} ^ 6 {\ left | {R} _i + {R} _ {i + 6} \ right |} ^ 2 $$ (6)где R я - соседние атомы одинаковой длины и R я + 6 - противоположное направление соседних атомов. Значения CSP для кристалла ГЦК, частичной дислокации, дефекта упаковки и поверхностных атомов равны 0, 2,1, 8,3 и 24,9 соответственно [27].
Метод CSP может идентифицировать атомные смещения, но не может распознать локальное состояние атомной кристаллической структуры заготовки. Поэтому для выявления локального дефекта кристаллической структуры вводится анализ общего соседа (CNA). В исходном методе CNA, предложенном Ханикаттом и Андерсеном [28], различные структуры представлены диаграммами. В настоящее время существует пять типов паттернов CNA в OVITO [29], где локальные кристаллические структуры идентифицируются как кубический гранеццентр (FCC), плотноупакованный гексагональный (HCP), объемно-центрированный кубический (BCC), икосоэдрический (ICO), и неизвестно соответственно. В этой статье также представлен алгоритм извлечения дислокации (DXA) [30] для анализа эволюции дислокационного дефекта. С помощью DXA различные кристаллические структуры в заготовке будут отмечены разными цветами, а дислокационные дефекты в заготовке будут представлены линиями разных цветов.
Результаты и обсуждение
Развитие подповерхностных дефектов в процессе нанорезки
В процессе нанорезки под действием экструзии и сдвига режущего инструмента на заготовку материал поверхности заготовки с толщиной глубины резания удаляется, и образуется новая обработанная поверхность с определенной точностью размеров и качеством поверхности. Сложная упруго-пластическая деформация, включающая деформацию напряжения и тепловую деформацию, происходит на поверхности и под поверхностью детали, сопровождаясь преобразованием энергии и концентрацией напряжений. Таким образом, формируется слой подповерхностных повреждений, и стружка удаляется. На рис. 2 показаны мгновенные изображения развития подповерхностных дефектов и удаления материала в процессе нанорезки монокристаллической меди. На рис. 2 атомы окрашены в соответствии со значением результатов анализа CSP и CNA. На рис. 2а и с желтые, зеленые, красные и синие атомы представляют собой поверхностные атомы, атомы поверхностных дефектов, подповерхностные дефектные атомы и атомы ГЦК. Из рис.2 видно, что в процессе нанорезки на поверхности детали формируется множество типичных дефектных структур, таких как точечные дефекты, вакансионные дефекты, дефекты упаковки, кластерные дефекты, призматические дислокации и петли винтовых дислокаций.
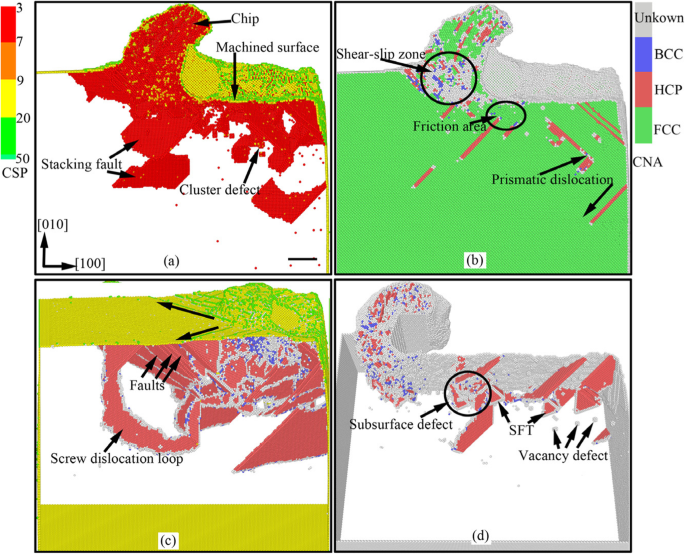
Мгновенные изображения эволюции подповерхностных дефектов в процессе нанорезки монокристалла меди (цвет онлайн, шкала 5 нм). Расстояния реза a , b , c , и d соответственно 18 нм, 18 нм, 6 нм и 32 нм
Из-за сжимающего и режущего эффекта режущего инструмента для атомов перед передней поверхностью создается деформация сдвига-проскальзывания, а в заготовке во время процесса нанорезки формируется первичная зона сдвига-проскальзывания, как показано на рис. . 2b. Некоторые из этих атомов скользят вверх по передней поверхности, и режущая стружка формируется, как показано на рис. 2а. Некоторые из них перемещаются вниз, и обработанная поверхность образуется под действием трения сжатия боковой поверхности инструмента, как показано на рис. 2b. Другие перемещаются внутрь, и образуются подповерхностные дефекты, такие как дефекты упаковки, кластерные дефекты и призматические дислокации, показанные на рис. 2a и b.
Из-за трения и выдавливания боковой поверхности инструмента происходит накопление энергии для атомов вблизи боковой поверхности, и атомы превращаются в атомы с высокой энергией. Когда атомная энергия превышает определенный уровень, энергия, переносимая энергичными атомами, высвобождается, и дислокация формируется под действием энергичных атомов. Следовательно, в зоне трения по боковой поверхности образуется большое количество дислокаций, как показано на рис. 2d. При формировании обработанной поверхности дислокации зарождаются, расширяются и аннигилируют под поверхностью. Наконец, дефектные структуры, такие как дефекты упаковки, SFT и вакансионные дефекты, остаются в подповерхностном слое, как показано на рис. 2d. Дефекты упаковки зарождаются в зоне сдвига-проскальзывания под режущим инструментом, затем распространяются на заготовку и, наконец, уничтожаются на свободной поверхности заготовки. В итоге линия дислокации формируется на поверхности детали. Линия дислокации продолжается вдоль \ (\ left [\ overline {1} 0 \ overline {1} \ right] \), \ (\ left [\ overline {1} 01 \ right] \) и [101] направления. Петля винтовой дислокации, расположенная на краю зоны сдвигового скольжения, состоит из нескольких дефектов упаковки и серии винтовых дислокаций. Винтовая дислокация формируется при движении сжимающего напряженного состояния в зоне сдвига-скольжения [11].
В процессе нанорезки дислокации зарождаются и расширяются под действием режущего инструмента. Сопровождая агрегацию и высвобождение энергии, сила резания колеблется с увеличением расстояния резания, что показано на рис. 3 в трех измерениях. На рис. 3 черные, красные и синие кривые соответственно представляют собой силу подачи (Fx), обратную силу (Fy) и тангенциальную силу (Fz). Из рис. 3 видно, что процесс резания разделен на два периода:начальный этап резания и этап стабильного резания. На начальном этапе резания сила подачи и обратная сила быстро увеличиваются, прямолинейно. Максимальное значение усилия подачи достигает более 1100 нН, но только что достигается обратная сила около 600 нН. Когда острие инструмента полностью врезается в заготовку, образуется обработанная поверхность, показанная в виде первого небольшого графика, обозначенного как Обработанная поверхность на рис. 3. Затем процесс нанорезки переводится на этап стабильной резки. На стабильной стадии резания все три силы колеблются в своих положениях равновесия. Средняя сила подачи составляет около 1000 нН, а средняя обратная сила составляет всего около 500 нН. Из рис. 3 видно, что сила подачи быстро уменьшается на расстоянии резания 20 нм. Это связано с тем, что накопление энергии достигает определенного уровня, который представляет собой критическую энергию деформации решетки, показанную вторым маленьким графиком на рис. 3. Между тем, на режущий инструмент действует большое сопротивление, в результате чего усилие резания становится меньше. пиковое значение. Затем энергия высвобождается, что приводит к эмиссии дислокаций, и сила резания уменьшается, что показано на третьем маленьком графике на фиг. 3. Следовательно, сила резания колеблется во время стабильной стадии резания. Зарождение, распространение и аннигиляция дислокаций привели к колебаниям силы резания и, в конечном итоге, к подповерхностному дефекту, существующему в заготовке.
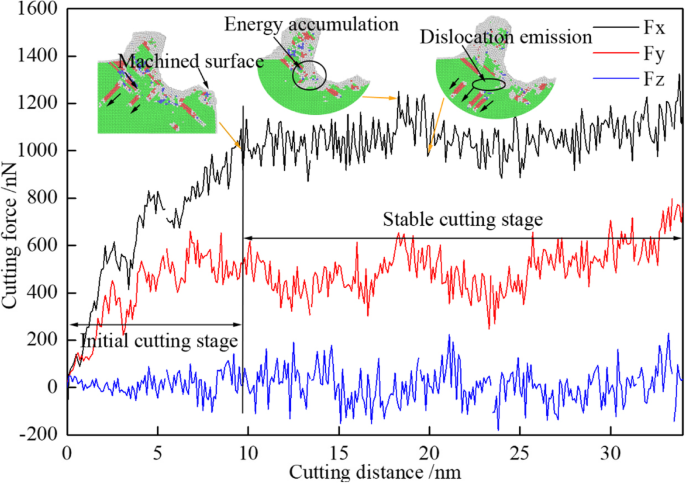
Кривая изменения силы резания в зависимости от расстояния резания (цвет онлайн). Черная, красная и синяя кривые соответственно - это сила подачи (Fx), обратная сила (Fy) и тангенциальная сила (Fz)
Чтобы детально изучить эволюцию и проявление дислокационных дефектов под поверхностью заготовки во время процесса нанорезки, с помощью метода CNA детально анализируется распределение дислокаций и его изменение в зависимости от расстояния резания. Развитие подповерхностных дефектов детали на определенной области показано на рис. 4, на котором расстояния резания на рис. 4a, b, c, d, e и f соответственно составляют 8 нм, 10 нм, 12 нм, 20 нм. , 24 нм и 32 нм. Из рис. 4а видно, что большое количество дислокационных дефектов зарождается в зоне сдвига-проскальзывания под действием экструзионного сдвига режущего инструмента во время предварительной стадии процесса резания. В частности, V-образная дислокация и разлом образуются под действием атомного напряжения и энергии в зоне сдвига-проскальзывания, показанной на рис. 4b. В последующем процессе обработки зона сдвига-проскальзывания продвигается вперед, а режущий инструмент продолжает двигаться. За счет уменьшения энергии деформации разлом постепенно аннигилирует. Во время движения режущего инструмента вперед зона трения по боковой поверхности смещается вблизи разлома. И шероховатость обработанной поверхности образуется под действием выдавливания и трения боковой поверхности. Затем дефект продолжает аннигилировать и постепенно отрывается от поверхности детали, как показано на рис. 4d. Наконец, неисправность трансформируется в кластерный дефект, который устойчиво существует в глубине заготовки. Точно так же сформированная V-образная дислокация постепенно превращается в SFT в результате взаимодействия двух дефектов упаковки и дислокационного замка. Эти стабильные дефекты вместе составляют подповерхностный деформированный слой, как показано на Рис. 4e и Рис. 4f.
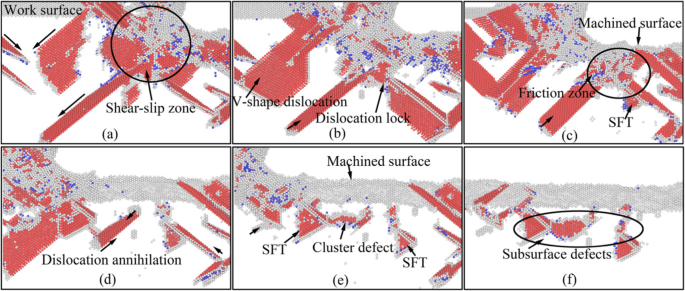
Развитие подповерхностных дефектов детали (цвет онлайн). Расстояния реза a , b , c , d , e , и f соответственно 8 нм, 10 нм, 12 нм, 20 нм, 24 нм и 32 нм
Как известно, произойдет снятие остаточного напряжения и восстановление внутренних дефектов . на заготовке после обработки старением. В реальном нанопроизводстве некоторые из подповерхностных дефектов, образовавшихся во время обработки, будут исчезать после процесса механической обработки. Чтобы смоделировать состояние заготовки после обработки старением, на режущей системе в течение длительного времени выполняется релаксация молекулярной динамики. Диаграмма распределения остаточного дефекта в подповерхности детали после длительной МД релаксации представлена на рис. 5, на котором атомы окрашены в соответствии с результатами анализа методами CSP и CNA. Из рис. 5 видно, что первичные дислокации аннигилируют после релаксации. Вакансионные дефекты, дефекты упаковки, атомный кластер, призматическая дислокация, винтовая дислокация, SFT и ступенчатая дислокация существуют на поверхности детали, как показано на рис. 5. Согласно приведенному выше анализу, эти дефекты, которые образуются при индукция сложных внутренних напряжений и взаимодействие дислокационных дефектов будут влиять на точность размеров и качество поверхности заготовки после нанообработки.
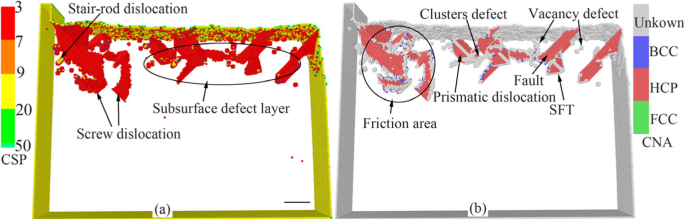
Распределение остаточных дефектов на поверхности детали после нанометровой резки (цветной онлайн, шкала 5 нм). а Желтый, зеленый, красный и синий атомы - это поверхностные атомы, атомы поверхностных дефектов, подповерхностные дефектные атомы и атомы ГЦК. б Зеленый, красный, серый и синий атомы - это FCC, HCP, неизвестная и BCC структура
Испытание на наноиндентирование на медном образце с дефектами под поверхностью, вызванными механической обработкой
Подповерхностные остаточные дефекты, вызванные механической обработкой, определяют механические свойства поверхности, особенно твердость и модуль Юнга. Поэтому исследование зарождения и взаимодействия дислокаций во время наноиндентирования представляется крайне необходимым. Чтобы исследовать влияние подповерхностных дефектов, вызванных механической обработкой, на механические свойства монокристаллической меди, процесс наноиндентирования на образце после нанорезки был применен на практике с теми же параметрами, что и моделирование нанорезки. Результат моделирования представлен на рис. 6, 7, 8, 9 и 10. Мгновенное атомное изображение распределения подповерхностных дефектов в исходном состоянии наноиндентирования показано на рис. 6. Из рисунка видно, что имеется несколько SFT, V-образный дислокация, некоторые призматические дислокации и некоторые кластерные дефекты ниже индентора. Эти подповерхностные дефекты могут влиять на зарождение дислокаций и расширение заготовки во время процесса наноиндентирования. Затем меняются механические свойства материала заготовки.
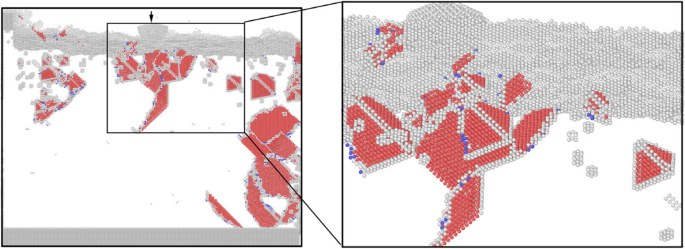
Распределение подповерхностных дефектов заготовки в исходном состоянии вдавливания (цвет онлайн). Красный, серый и синий атомы представляют собой HCP, неизвестную структуру и структуру BCC
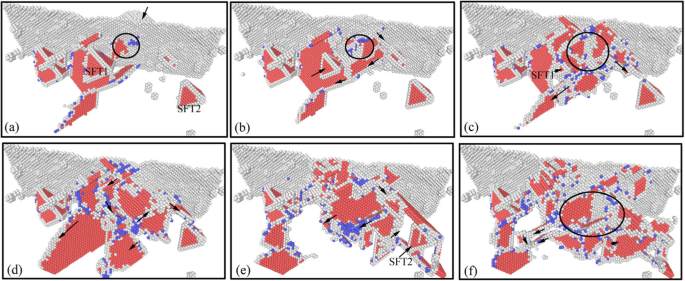
Эволюция подповерхностных дислокационных дефектов в процессе нагружения наноиндентирования (цветной онлайн). Соответствующая глубина отступа a - е равны 0 нм, 0,5 нм, 1 нм, 2 нм, 3 нм и 4 нм соответственно
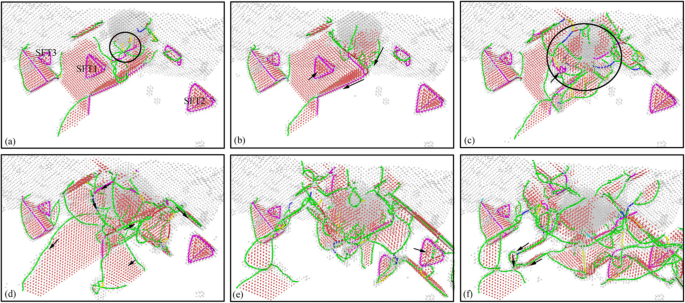
Распределение подповерхностных дислокаций в процессе нагружения наноиндентирования (цветной онлайн). Соответствующая глубина отступа a - е равны 0 нм, 0,5 нм, 1 нм, 2 нм, 3 нм и 4 нм соответственно. Цветовая схема:темно-синий для идеальных дислокаций, зеленый для дислокаций Шокли, розовый для дислокаций Лестничного стержня, желтый для дислокаций Хирта, голубой для дислокаций Франка и красный для неидентифицированных дислокаций.
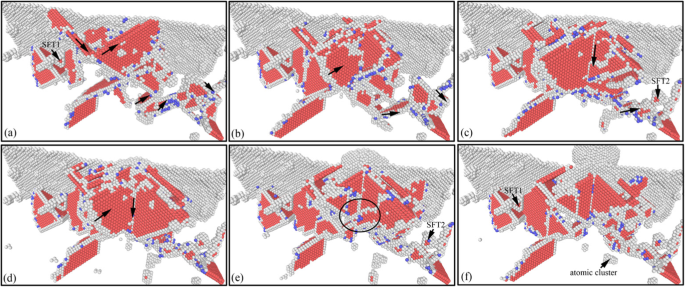
Эволюция подповерхностных дефектов в процессе разгрузки наноиндентирования (цвет онлайн). Соответствующая глубина отступа a –F - 4 нм, 3 нм, 2 нм, 1 нм, 0 нм и - 1 нм соответственно
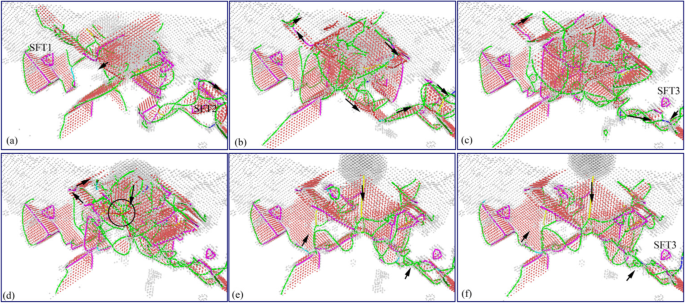
Распределение подповерхностных дислокаций в процессе разгрузки наноиндентирования (цветной онлайн). Соответствующая глубина отступа a - е равны 4 нм, 3 нм, 2 нм, 1 нм, 0 нм и -1 нм соответственно. Цветовая схема:темно-синий для идеальных дислокаций, зеленый для дислокаций Шокли, розовый для дислокаций Лестничного стержня, желтый для дислокаций Хирта, голубой для дислокаций Франка и красный для неидентифицированных дислокаций.
Изображение атомной эволюции подповерхностных дислокаций в процессе нагружения наноинденторами показано на рис. 7. Из рис. 7а видно, что первоначальное зарождение дислокации происходит на поверхности образца, когда индентор контактирует с поверхностью образца. образец. При давлении индентора вниз зародышевые дислокации постепенно расширяются. Между тем, под действием напряжения, оказываемого индентором, большое количество дислокаций зарождались и перемещались по системе скольжения, как показано на рис. 7b. При взаимодействии между вновь образованными дислокациями и исходными подповерхностными дефектами некоторые простые дефекты постепенно исчезают, а V-образные дислокации продолжают развиваться и постепенно аннигилировать. SFT под индентором постепенно уменьшается, как показано на рис. 7c. По мере продвижения процесса индентирования масштаб новых зародышевых дислокационных дефектов увеличивается, а V-образная дислокация и SFT1 под индентором постепенно исчезают. Одновременно с этим дислокационные дефекты, образующиеся во время индентирования, постепенно превращаются в призматическую дислокационную петлю, в которой дефекты упаковки постепенно исчезают, как показано на рис. 7d. Вновь образованная призматическая дислокационная петля продолжает расширяться до SFT2 в правом нижнем углу индентора. Благодаря своей стабильной структуре SFT2 остается недеформированной во время расширения призматической дислокационной петли, как показано на рис. 7e. По мере надавливания индентора вниз призматическая дислокационная петля продолжает расширяться вниз, а масштаб дислокационных дефектов в приповерхностной области постепенно увеличивается. Структура SFT2 стабильно существует на поверхности образца и не изменяется во время движения и интерференции дислокационных дефектов, как показано на рис. 7 f.
Чтобы более четко показать эволюцию и распределение подповерхностных дефектов в процессе индентирования, для анализа образца после индентирования используется метод DXA. Изображение распределения подповерхностных дислокаций в каждый момент времени, соответствующее рис. 7, получено с помощью DXA-анализа, как показано на рис. 8. Дислокации окрашены в соответствии со следующей схемой:темно-синий для идеальных дислокаций, зеленый для дислокаций Шокли, розовый для ступенчатых стержней. дислокации, желтый для дислокаций Хирта, голубой для дислокаций Франка и красный для неидентифицированных дислокаций.
Из рис. 8 видно, что подповерхность детали в основном состоит из дислокации Шокли и дислокации ступенчатого стержня в исходном состоянии вдавливания. SFT, существующий в недрах, представляет собой правильную тетраэдрическую структуру, состоящую из шести ступенчато-стержневых дислокаций. Когда индентор контактирует с заготовкой, зарождение дислокации на поверхности заготовки представляет собой желтые дислокации Хирша, как показано на рис. 8а. При нажатии индентора происходит зарождение большого количества дислокаций, которые перемещаются по системе скольжения. Желтые дислокации Хирша постепенно сменяются зелеными дислокациями Шокли, как показано на рис. 8b. При взаимодействии между вновь образованными дислокациями и исходной SFT1 некоторые простые дислокации исчезают постепенно, как показано на рис. 8c. Масштаб подповерхностных дислокаций увеличивается с опусканием индентора, и вновь образованные дислокации представляют собой в основном зеленые дислокации Шекли. Взаимодействие между дислокациями Шокли и SFT1 приводит к постепенному уменьшению размера SFT1 и, в конечном итоге, к исчезновению SFT1, как показано на рис. 8d. С увеличением масштаба дефектов количество и типы дислокаций в подповерхностной части образца увеличиваются. Есть красные дислокации неизвестного типа, сформированные под поверхностью, и несколько дислокаций Шокли составили петлю призменной дислокации, как показано на рис. 8e. При взаимодействии дислокации Шокли и дислокации ступенчатого стержня SFT2 и SFT3 вдали от области вдавливания наконец не исчезли из-за более слабого выдавливания индентора, как показано на рис. 8f.
Изображение эволюции подповерхностной дислокации в процессе разгрузки наноиндентации показано на рис. 9. На рис. 10 показано изображение распределения подповерхностной дислокации, соответствующее рис. 9. Из двух графиков видно, что масштаб подповерхностных дефектов увеличивается. сначала, а затем постепенно уменьшается по мере продвижения индентора вверх. Это вызвано комплексной функцией между непрерывным высвобождением энергии деформации материала и силой адгезии, оказываемой индентором на образец. На начальной стадии процесса разгрузки восходящая адсорбционная сила воздействия индентора на образец незначительна. Развитие подповерхностных дефектов в основном обусловлено энергией деформации материала, что приводит к увеличению масштабов подповерхностных дефектов. И основными типами дислокаций в стадии являются зеленая дислокация Шокли и розовая лестничная дислокация, как показано на рис. 9а, б и 10а, б. Взаимодействие между SFT2 и дислокацией Шокли поблизости заставляет розовую ступенчатую дислокацию стержня превращаться в зеленую дислокацию Шекли в области, удаленной от действия индентора. Между тем, SFT2 преобразуется в меньший дефект, которым является SFT3, как показано на фиг. 9c и 10c. При непрерывном подъеме индентора эффект связывания и адсорбции, оказываемый индентором на образец, постепенно увеличивается. Accompany with the deformation energy release, the size and types of dislocations in subsurface increase. And more perfect dislocations, Hirh dislocations, and unknown dislocations are formed, as shown in Figs. 9d and 10d. In later stage of unloading process, the material deformation energy is basically released, and the evolution of subsurface defects is dominated by the adsorption from the indenter. Therefore, the subsurface defects are annihilated rapidly, and the scale of subsurface defects decreases rapidly. And a typical Hirsch dislocation is formed in the direction of the indenter upward, which is shown in Figs. 9e, f and 10e, f. Finally, the scale of subsurface defects decreases considerably, and some typical subsurface defects, such as SFT and atomic clusters, are gradually disappeared. From the above analysis, it can be seen that secondary processing (nano-indentation) can restore the typical internal defects formed in nano-cutting, and the subsurface damage becomes more serious in the secondary processing area. These characteristics of subsurface defects will affect the mechanical properties of materials. Hence, it is necessary to study the effect of subsurface defects on the mechanical properties of material.
Mechanical properties of materials can be calculated by load-displacement curve, such as hardness, elastic modulus, and yield strength. In this study, hardness and Young’s modulus of single crystal copper were investigated. The variation of load on the indenter was monitored during the nano-indentation process, and the load-displacement curve of the nano-indentation process was drawn, as shown in Fig. 11. The max indentation depth of the red and black curves respectively is 2 nm and 3 nm, in which both loading and unloading processes are included. The upward direction of load is defined as positive direction, so the load-displacement curves are all above the zero line in the process of loading, while the load on the indenter changes from positive to negative during unloading. The elasticity restore of deformed matrix material exerts an upward force on the indenter. Therefore, in order to keep the indenter raising in uniform speed, a downward force (positive) is required. With the gradual recovery of deformation, the force gradually decreases until it disappears. Then the force applied on the indenter becomes negative, and the absolute value of the force first increases and then decreases. From the graph, it can be seen that the specimen is in the stage of elastic deformation during loading process, and the load increases in proportion to the displacement. When the displacement of the indenter is 1 nm, the load on the indenter is fluctuated dramatically, as indicated by the arrow on the left side of Fig. 11. This is because that the indenter is pressed down to the SFT1 shown in Fig. 7, which results in the greater impediment to the indenter. When the indenter displacement is in the range of 2 to 3 nm, the fluctuation amplitude of the load increases. This is because the indenter is pressed down to the SSD layer, and the impediment of the indenter to the subsurface defect in the specimen is more significant, so the fluctuation amplitude of the load increases significantly.
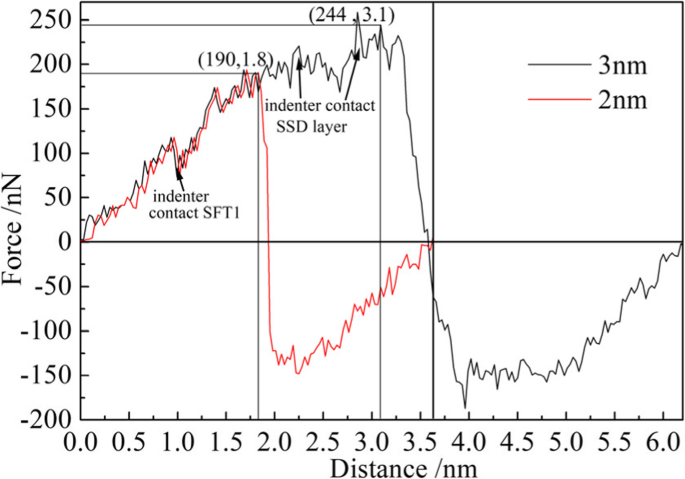
Load-displacement curve of nano-indentation on the machining-induced specimen (color online). The maximum indentation depth of the black curve and the red curve respectively is 3 nm and 2 nm
According to Oliver-Pharr Method [31], nano-indentation hardness can be defined as indentation load divided by the contact area between indenter and specimen, which is calculated by Eq. 7.
$$ H={F}_{\mathrm{max}}/{A}_c $$ (7)In which, F макс is the peak value of the load. А c is projected contact area for indenter and specimen, which can be obtained by
$$ {A}_c=\pi {r}^2 $$ (8)где r is contact radius for indenter. Because the indenter is hemispherical in shape, r is approximately equal to indentation depth.
The elastic deformation of single crystal copper material is caused by the load exerted from indenter. Based on the previous load-displacement curve, Young’s modulus (E ) of single crystal copper can be calculated by Eq. 9.
$$ E=\frac{\sigma }{\varepsilon }=\frac{F/S}{DL/L}=\frac{F/\pi {r}^2}{DL/L} $$ (9)где F is applied load, S is contact area, r is projection radius of indenter, DL is material deformation along loading direction, which is equal to indentation depth, and L is the total length of material along loading direction. In this study, L is equal to 30 nm.
According to the Oliver-Pharr method and load-displacement data, nano-indentation hardness and Young’s elastic modulus of single crystal copper materials with subsurface defects can be calculated based on Eqs. 7, 8, 9. Table 3 shows the applied load acting on the specimens by indenter with different indentation depths.
The nano-indentation hardness of single crystal copper can be calculated by Eqs. 7 and 8 combining the data in Table 3. When the maximum depth is 2 nm, F макс =190.67 nN and from Fig. 11 r =2.75 nm. The calculated value of nano-indentation hardness H2 is 8.029 GPa. When the maximum depth is 3 nm, F макс =244.66 nN and r =3 nm. The calculated value of nano-indentation hardness H3 is 8.675 GPa, which is slightly larger than it obtained at indentation depth of 2 nm. It is because the indenter is pressed down to the subsurface defects area at indentation depth of 3 nm, and the deformation resistance of the subsurface defects increases. Therefore, the hardness of the single crystal copper increased. It can be concluded from the result that the subsurface defects make the machined surface much harder, which is work-hardening phenomenon.
The Young’s modulus E of single crystal copper can be calculated by Eq. 9 combining the data in the Table 3. The calculation results are shown in Table 4. It can be noted that the Young’s modulus becomes distinctly higher when the indentation depth is smaller than 1.5 nm. In the initial stage of nano-indentation, the indenter does not contact the defects residual area in subsurface. However, the work-hardening effect makes the specimen material not easily be occurred elastic deformation; therefore, the Young’s modulus of single crystal copper is larger in the initial stage of indentation. The value of Young’s modulus is 119.4 GPa when indentation depth is 2 nm, which is almost the same with Zhang’s research (120.4 GPa) [14]. With the increase of indentation depth, the Young’s elastic modulus of single crystal copper specimens decreases gradually, and the ability of materials to resist elastic deformation is weakened. It is due to the permanent elastic deformation is derived from the dislocation motion and its interaction with subsurface defects. It has been revealed that the nano-cutting-induced subsurface defects will affect the physical and mechanical properties of single crystal copper materials, which is also applicable to other FCC materials. The existence of subsurface defects will enhance the hardness of machined surface and weaken the ability of material to resist elastic deformation, in which the mutual evolution between dislocations and subsurface defects plays an important role. Therefore, it is very important to predict the thickness of subsurface deformation layer and study the surface properties for nano-fabrication.
Выводы
The subsurface defects stable exist in workpiece after nano-cutting can affect the mechanical properties, which is critical to the service performance and life of nano-structures. The previous studies are mainly based on perfect crystal materials or artificial constructing hypothetical defects, which is far from the actual subsurface defects. In this paper, molecular dynamics simulation of nano-cutting is performed to construct the specimen model with subsurface defects. Based on the built MD model, nano-indentation simulation is carried out to study the influence of machining-induced subsurface defects on the physical and mechanical properties of single crystal copper materials. The interaction mechanism between dislocation and complex defects during nano-indentation is studied. The nano-indentation hardness and Young’s elastic modulus of single crystal copper materials are calculated. Based on the above analysis, some interesting conclusions can be drawn as follows.
- 1.
The dislocation nucleation and expansion in workpiece subsurface are driven by the extrusion and shearing action of cutting tool during the nano-cutting process, which results in the fluctuation of cutting force. After nano-cutting, there are stable defect structure residues in the subsurface of workpiece, such as vacancy defects, stacking faults, atomic clusters, SFT, and stair-rod dislocations, which together constitute the subsurface defect layer of workpiece.
- 2.
The existence of subsurface defects affects the nucleation and expansion of dislocations during nano-indentation process. Some stable defects directly below the indenter, such as V-shaped dislocation and SFT1, are annihilated after indentation. And SFT2 far from the indentation region is transformed into a smaller one. Secondary processing of nano-indentation can restore typical internal defects of the workpiece, but the subsurface defects in the secondary processing area are aggravated.
- 3.
The nano-indentation hardness of specimens increases with the introduction of subsurface defects, which results in the formation of work-hardening effect. The Young’s modulus of single crystal copper is larger in the initial stage of indentation and gradually decreases with the increase of indentation depth. The existence of subsurface defects can weaken the ability of material to resist elastic deformation, in which the mutual evolution between dislocations and subsurface defects plays an important role.
Доступность данных и материалов
The conclusions made in this manuscript are based on the data which are all presented and shown in this paper.
Сокращения
- MD:
-
Molecular dynamics
- SSD:
-
Subsurface defects
- SFT:
-
Stacking fault tetrahedral
- PBC:
-
Periodic boundary condition
- LAMMPS:
-
Large-scale atomic/molecular massively parallel simulator
- EAM:
-
Embedded-atom method
- CSP:
-
Centro-symmetry parameter
- FCC:
-
Face center cubic
- CNA:
-
Common neighbor analysis
- HCP:
-
Close-packed hexagonal
- BCC:
-
Body centered cubic
- ICO:
-
Icosohedral
- DXA:
-
Dislocation extract algorithm
Наноматериалы
- Эволюция рынка материалов для 3D-печати:тенденции и возможности в 2019 году
- Эволюция SLS:новые технологии, материалы и приложения
- Как инженеры оценивают пластмассовые материалы и прочность материалов?
- Гибридный композит на основе наноструктурированного диоксида кремния / золота и целлюлозы с амино-POSS, получе…
- Влияние контактной неравновесной плазмы на структурные и магнитные свойства шпинелей Mn Х Fe3 - X О4
- Парамагнитные свойства фуллереновых наноматериалов и их полимерных композитов:эффект резкого откачивания
- Свойства инженерных материалов:общие, физические и механические
- Список 14 различных механических свойств материалов
- Свойства стальных материалов и инструментов, используемых для пуансонов
- Различные типы механических свойств материалов