Процесс осаждения и свойства композиционных покрытий Ni-P-Al2O3 на магниевом сплаве, нанесенных методом химического восстановления,
Аннотация
Для повышения коррозионной стойкости и износостойкости никель-фосфорного (Ni-P) покрытия на магниевом (Mg) сплаве. Ni-P-Al 2 О 3 Покрытия получали на сплаве Mg из ванны композиционного покрытия. Оптимальный Al 2 О 3 Концентрация определялась свойствами гальванической ванны и покрытий. Эволюция морфологии роста Ni-P-Al 2 О 3 Композитные покрытия в разное время наблюдали с помощью сканирующего электронного микроскопа (SEM). Результаты показывают, что нано-Al 2 О 3 частицы могут замедлить реакцию замещения Mg и Ni 2+ на ранней стадии процесса осаждения, но это почти не влияет на скорость процесса автокаталитического восстановления Ni-P. Антикоррозийные испытания и испытания покрытий на микротвердость показывают, что Ni-P-Al 2 О 3 композитные покрытия демонстрируют лучшие характеристики по сравнению с покрытием Ni-P из-за более подходящего расстояния между кристаллическими плоскостями и размера зерна Ni-P-Al 2 О 3 покрытия. Испытание на тепловой удар показывает, что Al 2 О 3 частицы не влияют на адгезию покрытий. Кроме того, срок службы ванны для нанесения композитного покрытия составляет 4,2 оборота металла, что предполагает ее потенциальное применение в области магниевых сплавов.
Фон
Сплавы магния (Mg) привлекли к себе большое внимание и стали предметом научных исследований из-за низкой плотности, высокой удельной прочности и отличной обрабатываемости [1, 2]. Поэтому сплавы Mg обычно используются в аэрокосмической, электронной и автомобильной областях [3, 4]. Однако применение сплавов Mg ограничено из-за нежелательных дефектов антикоррозионной защиты и износостойкости [5, 6]. Таким образом, для Mg-сплавов были разработаны поверхностные антикоррозионные и антифрикционные методы, такие как микродуговая оксидная пленка, химическое конверсионное покрытие, термическое напыление, физическое осаждение из паровой фазы, гальваническое и химическое покрытие [7,8,9, 10,11,12,13].
Покрытие никель-фосфором (Ni-P) методом химического восстановления является одной из наиболее эффективных технологий обработки поверхности Mg-сплавов, поскольку оно имеет превосходные комплексные преимущества в отношении низкой стоимости, эффективности, коррозионной стойкости и износостойкости [14, 15]. Следовательно, покрытие Ni-P, нанесенное химическим способом, играет важную роль в области защиты от коррозии сплавов Mg. Для дальнейшего улучшения характеристик покрытия Ni-P наночастицы, например SiC, ZrO 2 , TiO 2 , SiO 2 , и Al 2 О 3 и т. д. обычно добавляют в ванну для химического нанесения покрытия для получения композиционных покрытий из наночастиц Ni-P [16,17,18,19,20]. Согласно предыдущим исследованиям [20,21,22,23], характеристики покрытия Ni-P эффективно улучшаются за счет наночастиц. Хотя композитные покрытия из наночастиц Ni-P обладают относительно высокими характеристиками по сравнению с покрытием Ni-P, необходимо отметить три проблемы. Во-первых, наночастицы легко объединяются и образуют активный центр в ванне для химического нанесения покрытия, что снижает стабильность раствора для нанесения покрытия. Во-вторых, технологические параметры ванны для нанесения композиционного покрытия обычно определяют содержание и распределение наночастиц в покрытиях, а также являются ключевыми факторами для улучшения свойств покрытий. В-третьих, процесс соосаждения наночастиц с Ni-P является еще одним фактором, влияющим на свойства покрытия. Следовательно, эти факторы заслуживают внимания. Нано-Al 2 О 3 частицы представляют собой дешевый абразив, обладающий высокой твердостью и хорошей химической стабильностью [24, 25]. Его можно хорошо диспергировать в ванне для химического никелирования. Следовательно, Ni-P-Al 2 О 3 Композитные покрытия обычно используются в качестве антикоррозионных и противоизносных покрытий для защиты стальной или медной основы. Тем не менее, лишь несколько отчетов были посвящены химическому процессу Ni-P-Al 2 О 3 нанесение покрытия на подложку из магниевого сплава [20, 22, 26]. Более того, изучение процесса роста Ni-P-Al 2 О 3 покрытие на сплавах Mg и стабильность ванны композитного покрытия довольно редки. Поэтому более подробная информация о производительности ванны композита и процессе совместного осаждения Ni-P-Al 2 О 3 необходимо изучить.
В настоящей работе для дальнейшего улучшения свойств покрытия Ni-P на подложке из сплава Mg мы использовали сульфат никеля и систему молочной кислоты в качестве основной соли и комплексообразователя, соответственно, в ванне для нанесения покрытия. Между тем, нано-Al 2 О 3 порошок добавляли в ванну для электроосаждения Ni-P. Чтобы получить подходящую ванну для химического нанесения композиционного покрытия для сплава AZ91D Mg, технологические параметры этой ванны оценивали по скорости осаждения и свойствам покрытия. Кроме того, были проведены периодические циклические испытания для оценки срока службы и стабильности ванны для нанесения покрытия при оптимальных условиях процесса. Изучить действие нано-Al 2 О 3 частиц на процесс роста покрытий, поведение осаждения и фазовая структура покрытия Ni-P обсуждались. Кроме того, свойства, включая коррозионную стойкость, микротвердость и адгезию покрытий, были проанализированы на основе морфологии и структуры. Результаты показали, что свойства Ni-P-Al 2 О 3 Композитные покрытия были предпочтительнее покрытия Ni-P, а ванна для химического нанесения композитного покрытия имела хорошую стабильность в течение срока службы. Таким образом, наши результаты в этой работе являются полезными справочными материалами при нанесении композиционных покрытий из наночастиц Ni-P на сплав Mg.
Методы
Подготовка композитных покрытий
В данной работе в качестве экспериментального материала использовался литой под давлением сплав Mg AZ91D размером 2 см × 1 см × 0,5 см, содержащий химический состав в мас.%:8,5 Al, 0,34 Zn, 0,1 Si, 0,03 Cu, 0,002 Ni. , 0,005 Fe и 0,02 другие и остальное Mg. Подложка AZ91D была последовательно отполирована краской № Бумага SiC 500 и 1000, промытая деионизированной водой и погружена в щелочной раствор на 5 мин при 65 ° C с последующим травлением кислотой в растворе хромовой кислоты (CrO 3 200 г / л) в течение 60 с. После этого подложку из сплава Mg погружали в раствор плавиковой кислоты с концентрацией 380 мл / л для активационной обработки примерно на 10 мин. Субстрат Mg очищали деионизированной водой на каждом этапе. Основной состав ванны и рабочие условия химического никелирования магниевого сплава были проиллюстрированы следующим образом:35 г / л NiSO 4 ⋅6H 2 O, 35 г / л молочной кислоты, 30 г / л Na 2 H 2 ЗП 2 ⋅H 2 O, 10 г / л NH 4 ВЧ 2 , Стабилизатор 3 мг / л, pH 4,5 ~ 7,0 и температура 70 ~ 90 ° C. Ванну для химического нанесения покрытия держали в стеклянном стакане, который помещали в водяную баню, управляемую термостатом. Для обеспечения силы перемешивания использовали электрическую мешалку с цифровым дисплеем. Средний размер частиц нано-Al 2 О 3 частиц составляет около 50 нм. Нано-Al 2 О 3 частицы были должным образом диспергированы в ванне в условиях ультразвуковой волны перед химическим нанесением покрытия.
Испытания скорости осаждения и стабильности гальванических ванн
Изучить действие нано-Al 2 О 3 частиц от скорости осаждения ванны для химического никелирования, скорость осаждения выражается в формуле. (1).
$$ v =\ frac {\ Delta w \ times {10} ^ 4} {\ rho St} $$ (1)где v , ρ , S , t , и △ w представляют скорость осаждения (мкм / ч), плотность покрытия Ni-P (~ 7,9 г / см 3 ), площадь поверхности Mg-подложки (см 2 ), время осаждения (ч) и вес покрытия (г) соответственно. Кроме того, содержание нано-Al 2 О 3 Количество частиц в покрытии оценивали взвешиванием на электронных весах (AR2140, Ohaus). Чтобы оценить стабильность ванны для химического нанесения покрытия, для оценки срока службы и стабильности ванны использовались периодические циклические испытания (или переворачивание металла, MTO). Здесь 1 МТО определил, что масса осаждения Ni эквивалентна начальной концентрации Ni 2+ в ванной. На примере 1 л гальванической ванны из ванны получается около 7,8 г Ni \ (\ left ({C} _ {{\ mathrm {Ni}} ^ {2 +}} =7,8 \ kern0.5em \ mathrm {g} / \ mathrm {L} \ right) \) относительно 1 МТО. Кроме того, свежий раствор смеси (\ ({\ mathrm {Ni}} ^ {2 +}:{\ mathrm {H}} _ 2 {\ mathrm {PO}} _ 2 ^ {2 -} =1:3 \) в мольном соотношении) добавляли в ванну для нанесения покрытия, когда ванна имела низкую скорость осаждения. Испытание на стабильность заканчивали до разложения ванны для нанесения покрытия. Таким образом, выражение MTO может быть представлено как уравнение. (2).
$$ \ mathrm {MTO} =M / m $$ (2)M и м представляют совокупную массу осаждения Ni и концентрацию Ni 2+ в гальванической ванне соответственно.
Характеристики материалов
Морфологию поверхности покрытия наблюдали с помощью сканирующей электронной микроскопии (SEM, Hitachi S-4800). Структуру покрытия исследовали на рентгеновском дифрактометре (XRD, D / Max-2200, Япония) с CuK α излучение ( γ =0,154 нм).
Электрохимические измерения
Тест потенциодинамической поляризации проводили на электрохимическом анализаторе (CHI800, Chenhua, China). Электрохимический эксперимент проводился в водном растворе NaCl с концентрацией 3,5 мас.% С использованием классической трехэлектродной конфигурации, состоящей из рабочего электрода (образец, 1 см 2 ), противоэлектрод (платина) и эталон (насыщенный каломельный электрод). Во время эксперимента с потенциодинамической разверткой образец сначала погружали в раствор электролита на 30 минут для стабилизации потенциала холостого хода ( E 0 ). График Тафеля был преобразован из записанных данных, и плотность тока коррозии ( i corr ) определялась экстраполяцией прямолинейного участка анодной и катодной линий Тафеля. Скорость развертки эксперимента составляла 5 мВ / с и проводилась при 25 ° C. Микротвердость магниевого сплава с различными композиционными покрытиями оценивалась с помощью измерителя микротвердости HXD-1000 с индентором Викера при нагрузке 100 г и продолжительности службы 15 с. Для оценки адгезии покрытий было проведено испытание на термический удар [23]. Это описывалось следующим образом:в воздушной атмосфере Mg-подложка с покрытием Ni-P или Ni-P-Al 2 О 3 покрытие помещали в высокотемпературную коробчатую печь сопротивления и нагревали до 250 ± 10 ° C со скоростью нагрева 20 ° C мин -1 . затем закаливают в холодной воде. Этот процесс повторялся 20 раз.
Результаты и обсуждение
На рисунке 1 показано влияние концентрации нано-Al 2 . О 3 частицы, скорость перемешивания, pH и температура от скорости осаждения, а также Al 2 О 3 состав композиционных покрытий. Как видно на рис. 1а, скорость осаждения немного уменьшается с увеличением Al 2 . О 3 концентрация частиц от 0 до 15 г / л. С другой стороны, Al 2 О 3 содержание композиционных покрытий постепенно увеличивается, в то время как концентрация Al 2 О 3 частиц увеличивается от 0 до 10 г / л. Однако вместо этого она уменьшается, когда концентрация Al 2 О 3 частицы выше 10 г / л. Это изменение связано с агрегацией частиц при высоких концентрациях, что ослабляет поведение Ni-P при совместном осаждении с Al 2 О 3 . На рис. 1b, когда скорость перемешивания установлена на 300 ~ 400 об / мин, скорость осаждения и Al 2 О 3 содержание композиционных покрытий составляет 18 мкм / ч и 3,6% соответственно. Результаты показывают, что дисперсность Al 2 О 3 частицы в гальванической ванне лучше всего подходят для этого диапазона скорости перемешивания. Что касается ванны для нанесения кислотного композитного покрытия, влияние значения pH на скорость осаждения и Al 2 О 3 Содержание покрытий показано на рис. 1в. Максимальная скорость осаждения составляет до 18,5 мкм / ч, когда значение pH находится в диапазоне 6,0 ~ 6,5, тогда как Al 2 О 3 содержание покрытий практически увеличивается с увеличением значения pH. Рисунок 1d показывает, что как скорость осаждения, так и Al 2 О 3 содержание композитных покрытий увеличивается с температурой, так как активность ионов и частиц улучшается, а скорость реакции ванны композита также увеличивается при высокой температуре. Однако стабильность гальванической ванны и пористость покрытий ухудшаются при высокой температуре (> 85 ° C) [13, 22]. На основании результатов анализа определены предварительные технологические параметры и режим работы ванны композита для магниевого сплава, то есть 35 г / л NiSO 4 ⋅6H 2 O, 35 г / л молочной кислоты, 30 г / л Na 2 H 2 ЗП 2 ⋅H 2 O, 10 г / л NH 4 ВЧ 2 , 10 г / л нано-Al 2 О 3 частицы, стабилизатор 3 мг / л, pH =6,0 ~ 6,5, T =85 ° C, скорость перемешивания 350 об / мин.
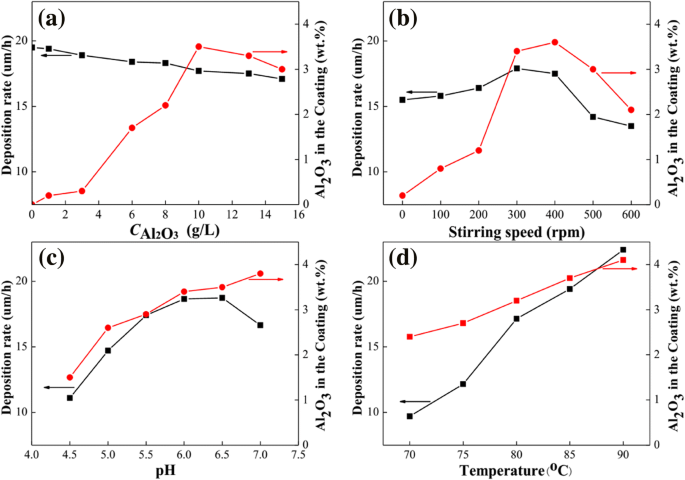
Влияние параметров процесса на скорость осаждения и Al 2 О 3 содержание покрытий
Для исследования процесса осаждения Ni-P-Al 2 О 3 покрытий, изменение изображений морфологии поверхности магниевого сплава в зависимости от времени реакции осаждения показано на рис. 2. Для сравнительного анализа на рис. 2a – c показан процесс нанесения покрытия Ni-P, а на рис. 2d – f - -процесс нанесения Ni-P-Al 2 О 3 (3,6 мас.%) Композиционные покрытия. Рисунок 2а представляет собой морфологическое изображение погружения подложки из Mg в ванну для нанесения покрытия на 0,5 мин, при этом большое количество частиц кубической структуры распределено по ее поверхности. Эти кубические частицы подтверждены как MgF 2 , который в основном формируется в процессе активации HF, что согласуется с литературными данными [23, 27]. Однако морфология изображения на рис. 2d заметно отличается от рис. 2а. Основное отличие показывает, что MgF 2 частиц на рис. 2г меньше, чем на рис. 2а. Кроме того, многие нано-Al 2 О 3 частицы наблюдаются на поверхности Mg-подложки. Изменение морфологии происходит от Al 2 О 3 частицы, которые непрерывно воздействуют на поверхность магниевого сплава при высокой температуре и перемешивании. Когда время нанесения покрытия Ni-P химическим способом составляет до 5 мин, как показано на рис. 2b, частицы Ni постепенно растут, а затем покрывают всю поверхность магниевого сплава. Но для химического нанесения композитного покрытия (см. Рис. 2e) более крупные частицы Ni и нано-Al 2 О 3 частицы наблюдаются на поверхности магниевого сплава, а Ni-P-Al 2 О 3 покрытия не покрывают полностью Mg подложку в течение 5 мин. Это указывает на то, что скорость роста Ni-P-Al 2 О 3 покрытия в ванне композита ниже, чем у покрытия Ni-P в ванне без Al 2 О 3 частицы. Это доказательство, подтверждающее причину низкой скорости осаждения в ванне для нанесения гальванического покрытия. Когда время химического осаждения составляет 30 мин, морфология покрытия Ni-P и Ni-P-Al 2 О 3 покрытий показано на рис. 2в, е соответственно. Что касается покрытия Ni-P, поверхность имеет плотную узловую структуру со средним размером 3 мкм. Но на рис. 2е средний размер узлов Ni-P-Al 2 О 3 композитное покрытие явно меньше, чем покрытие Ni-P. Более того, ясно видно, что нано-Al 2 О 3 частицы внедряются в покрытие Ni-P. Важно отметить, что с точки зрения поверхностного распределения Al 2 О 3 частиц, распределение Al 2 О 3 частиц на рис. 2е значительно меньше, чем на рис. 2в, д. Этот результат показывает, что осаждение Ni-P является преобладающим, в то время как осаждение Al 2 О 3 частицы становятся подчиненными после времени реакции осаждения 5 мин. Подобные выводы также можно сделать из относительного содержания Al 2 О 3 частиц в покрытиях (рис. 1). Другими словами, эффект Al 2 О 3 частицы в процессе осаждения в основном присутствуют на начальной стадии химического никелирования.
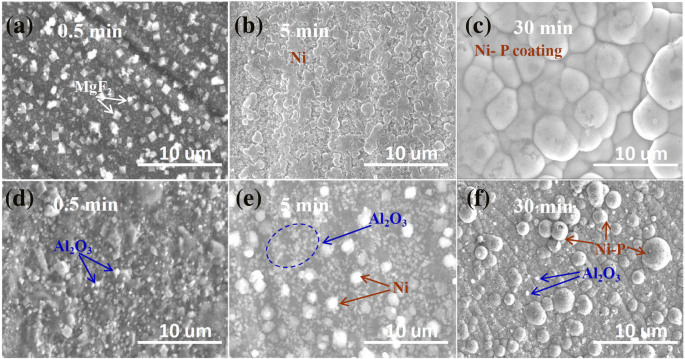
Морфология поверхности покрытия Ni-P (вверху, a - c ) и Ni-P-Al 2 О 3 композитные покрытия (низ, d - е ) при разном времени осаждения
Чтобы изучить влияние нано-Al 2 О 3 частиц на структуре покрытия Ni-P, дифрактограммах сплава AZ91D Mg, покрытии Ni-P и Ni-P-Al 2 О 3 Составные покрытия проанализированы на рис. 3. Как видно на рис. 3, угол дифракции кристаллических плоскостей магниевого сплава в основном концентрируется в диапазоне 30 ° ~ 70 °, например, α (10 \ (\ overline {1} \) 0) 32,2 °, α (0002) 34,2 °, β (10 \ (\ overline {1} \) 1) 36,8 ° и т. Д. Что касается сплава Mg с покрытием Ni-P, на дифракционной картине покрытия Ni-P наблюдается уширение пика и дифракция высокой интенсивности при 44,7 °, что можно отнести к кристаллической плоскости (111) гранецентрированной кубической (ГЦК) фазы никеля (табл. 1) [28]. Более того, наличие такого широкого пика указывает на образование покрытия Ni-P со смешанной аморфной кристаллической структурой. После покрытия Ni-P-Al 2 О 3 (3,6 мас.%) Композиционных покрытий, три новых дифракционных пика, очевидно, могут быть обнаружены при 25,6 °, 43,5 ° и 73,2 °. Эти пики относятся к характерным дифракционным пикам Al 2 О 3 по сравнению с карточкой PDF нет. 88-0826. Следовательно, Ni-P-Al 2 О 3 Композитные покрытия наносятся на поверхность сплава Mg. Кроме того, дифракционный пик кристаллической плоскости (111) Ni смещается до 45,2 ° (см. Таблицу 1) в Ni-P-Al 2 О 3 композитные покрытия, предполагающие нано-Al 2 О 3 частицы оказывают определенное влияние на расстояние между кристаллическими плоскостями (111) Ni. Согласно формуле Брэгга, nλ =2 д грех θ ( нет =1, 2, 3, ..., λ = 0,154 нм, d и θ представляют собой межплоскостное расстояние и угол дифракции соответственно), расстояние между кристаллическими плоскостями (111) Ni уменьшается примерно на 3% на Al 2 О 3 частицы. Кроме того, как дифракционные пики (111) Ni в покрытии Ni-P, так и Ni-P-Al 2 О 3 композитные покрытия аппроксимированы функцией Гаусса соответственно. Результат показывает, что полная ширина на полувысоте (FWHM) этого дифракционного пика в Ni-P-Al 2 О 3 композитное покрытие шире, чем покрытие Ni-P (таблица 1). Согласно формуле Шеррера, D = Kγ / B cos θ ( Д , К , B представляют собой кристаллическое зерно, постоянную Шеррера и FWHM соответственно), кристаллическое зерно Ni-P-Al 2 О 3 композитные покрытия уменьшаются примерно на 8% Al 2 О 3 частиц по сравнению с покрытием Ni-P. Это означает, что нано-Al 2 О 3 частицы уменьшают размер кристаллического зерна Ni, что согласуется с наблюдаемым результатом SEM выше.
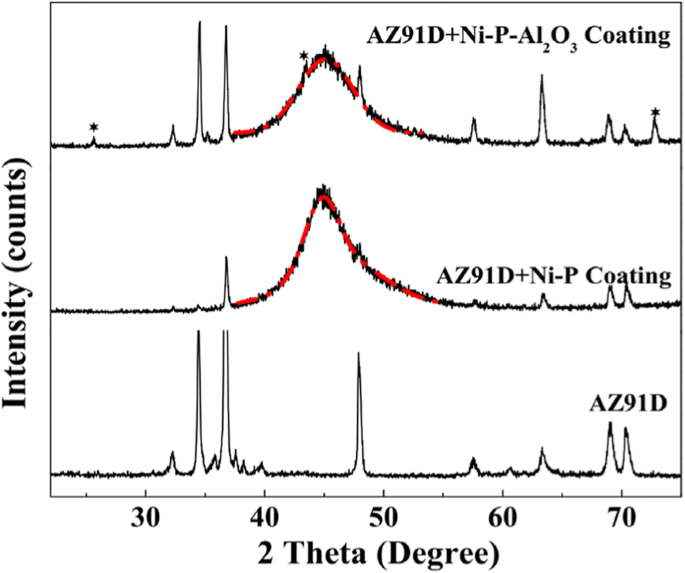
Рентгенограммы подложки AZ91D, покрытия Ni-P и Ni-P-Al 2 О 3 (3,6 мас.%) Композитные покрытия
На Рисунке 4 и в Таблице 2 показаны поляризационные кривые и антикоррозионные параметры подложки из сплава AZ91D Mg, покрытия Ni-P и Ni-P-Al 2 . О 3 композитные покрытия в водном растворе 3.5 мас.% NaCl при комнатной температуре соответственно. Катодная реакция на поляризационных кривых соответствует выделению водорода, а анодные поляризационные кривые являются наиболее важными характеристическими реакционными процессами коррозионной стойкости [29]. Для подложки из сплава AZ91D Mg наблюдается контролируемый активацией анодный процесс, когда приложенный потенциал увеличивается в анодной области. Кроме того, он серьезно растворяется в растворе электролита, и его потенциал коррозии ( E corr ) читается при - 1,47 В. Но для E corr покрытия Ni-P, он показывает значительный положительный сдвиг до -0,51 В по сравнению с подложкой из сплава Mg (-1,47 В), а плотность тока коррозии ( i corr ) очевидно уменьшается с 1,4 × 10 −4 А / см 2 подложки до 3,1 × 10 −6 А / см 2 покрытия Ni-P (см. таблицу 2). Что касается Ni-P-Al 2 О 3 (1,7 ~ 4,2 мас.%) Композитные покрытия, здесь Al 2 О 3 содержание покрытий определяется взвешиванием. Как видно из таблицы 2, все E corr положительного сдвига композитного покрытия и i corr композитных покрытий уменьшается по сравнению с покрытием Ni-P, что позволяет предположить, что Ni-P-Al 2 О 3 Покрытия обладают более высокими показателями коррозионной стойкости. Здесь покрытие Ni-P с 3,6 мас.% Al 2 О 3 показывает самый высокий E corr (- 0,35 В) и самый низкий i corr (4,5 × 10 −7 А / см 2 ). Однако E corr и я corr из Ni-P-Al 2 О 3 (4,2 мас.%) Изменяются на - 0,41 В и 1,0 × 10 −6 А / см 2 , соответственно. Возможно, что Al 2 О 3 частицы увеличивают пористость покрытия Ni-P и снижают эффективность композитных покрытий. Следовательно, Al 2 О 3 содержание композиционных покрытий оказывает важное влияние на коррозионную стойкость композиционных покрытий. Это также связано со структурой, включая расстояние между кристаллическими плоскостями и размер зерен покрытий (рис. 3).
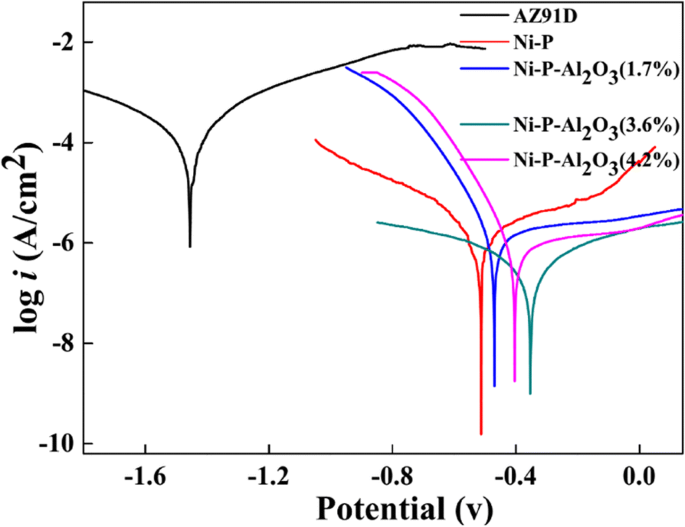
Поляризационные кривые подложки AZ91D, покрытия Ni-P и Ni-P-Al 2 О 3 композитные покрытия
Для проверки микротвердости покрытий средняя толщина всех покрытий была определена как 18 мкм, что было оценено по скорости осаждения и времени осаждения. Результаты испытаний на микротвердость подложки из сплава Mg и покрытий с различным Al 2 О 3 содержание показано на рис. 5. Как видно на рис. 5, микротвердость чистого сплава AZ91D Mg составляет всего около 120 HV, тогда как микротвердость подложки из сплава Mg, покрытой покрытием Ni-P, составляет до 520 HV. Это выше, чем у подложки, примерно на 400 HV, что указывает на то, что покрытие Ni-P может эффективно улучшить твердость покрытия подложки. В результате износостойкость подложки из сплава Mg повышается за счет покрытия Ni-P. Кроме того, Ni-P-Al 2 О 3 композитные покрытия демонстрируют значительную тенденцию к увеличению микротвердости при содержании Al 2 О 3 в покрытии увеличивается от 0 до 3,6 мас.%. Следовательно, Ni-P-Al 2 О 3 (3,6%) композитные покрытия показывают наивысшее значение твердости при 638 HV. Причина в нано-Al 2 О 3 частицы, оптимизирующие фазовую структуру (см. рис. 3) сплава Ni-P и повышающие микротвердость покрытий. Однако содержание Al 2 О 3 в композиционных покрытиях достигает 4,2 мас.%, а микротвердость покрытий снижается до 576 HV. Это означает, что более высокое содержание наночастиц может повлиять на кристаллическую структуру Ni-P, что приведет к неблагоприятным характеристикам композитных покрытий.
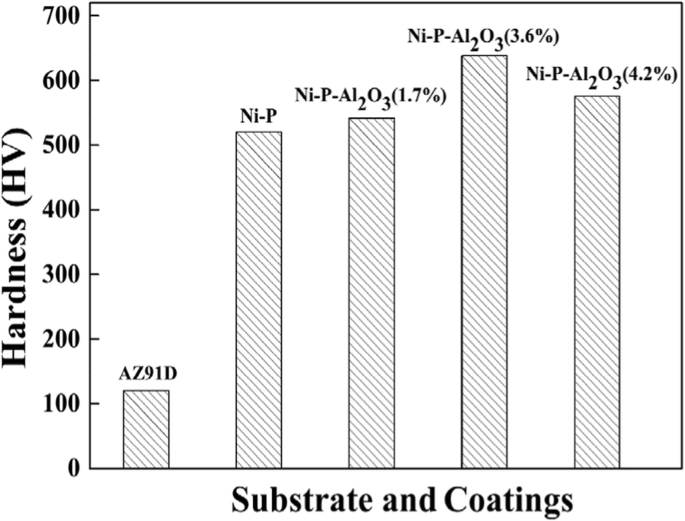
Твердость подложки AZ91D, покрытия Ni-P и Ni-P-Al 2 О 3 композитные покрытия
Адгезия между покрытиями и подложкой из сплава Mg осуществлялась испытанием на термический удар согласно разделу экспериментов. Путем 20 циклов испытаний, как покрытие Ni-P, так и Ni-P-Al 2 О 3 композитные покрытия хорошо сцепляются с подложкой из сплава Mg. Дефекты, такие как трещины, пузыри и сколы, не наблюдались во время процесса испытания, что указывает на то, что Ni-P или Ni-P-Al 2 О 3 Покрытия имели хорошую адгезию к подложке из сплава Mg, чтобы противостоять термическому удару. Кроме того, изображения морфологии поперечного сечения между покрытиями и подложкой из сплава Mg также наблюдались с помощью SEM. Как видно на рис. 6, это дополнительно демонстрирует отсутствие видимых дефектов между покрытиями и подложкой при испытании на тепловой удар. Важно отметить, что испытание на тепловой удар и наблюдение поперечного сечения показывают, что нано-Al 2 О 3 частицы не влияют на адгезию композитных покрытий.
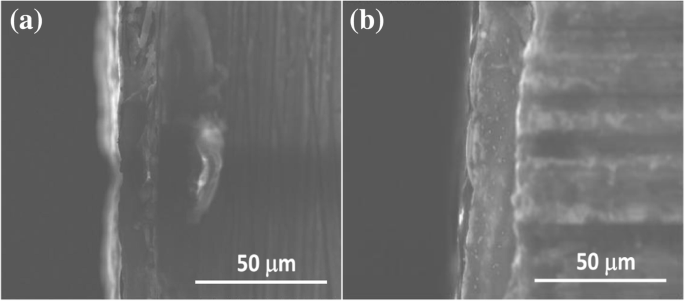
Морфологические изображения поперечного сечения покрытия Ni-P ( a ) и Ni-P-Al 2 О 3 (3,6 мас.%) Композитные покрытия ( b )
В настоящей работе гальванические ванны объемом 1 л без нано-Al и с ним 2 О 3 были приготовлены частицы (10 г / л) соответственно. Здесь исходное содержание источника никеля в ванне для гальваники было рассчитано как 7,8 г, а грузоподъемность ванны была установлена на уровне 0,5 дм 2 . / L. В соответствии с правилами испытания периодического цикла (см. Экспериментальный раздел), сначала была оценена MTO ванны для химического восстановления Ni-P, и было получено около 48,2 г сплава Ni-P. При этом 90% -ное содержание никеля в покрытии Ni-P было определено с помощью анализа EDS (см. Рис. 7). Следовательно, содержание никеля в покрытии можно рассчитать как 43,4 г. То есть MTO электролитической ванны без Al 2 О 3 частиц составляет 5,6 с помощью уравнения. (2). Что касается химического восстановления Ni-P-Al 2 О 3 композитная гальваническая ванна, всего 38,8 г Ni-P-Al 2 О 3 покрытия наносились из ванны композита. Аналогичным образом 86,45% Ni, 9,84% P, 1,96% Al и 1,75% O были определены с помощью EDS-анализа (рис. 7). Следовательно, содержание никеля в композиционных покрытиях можно рассчитать как 33,5 г, а MTO ванны композита составляет 4,2. По результатам испытаний с периодическим циклом, рабочий цикл ванны для нанесения композитного покрытия на 1,4 МТО меньше, чем у ванны для нанесения покрытия методом химического восстановления Ni-P. Это означает, что нано-Al 2 О 3 частицы сокращают срок службы ванны для химического нанесения покрытия. Тем не менее, Ni-P-Al 2 О 3 композитное покрытие по-прежнему имеет потенциальное применение в области магниевых сплавов.
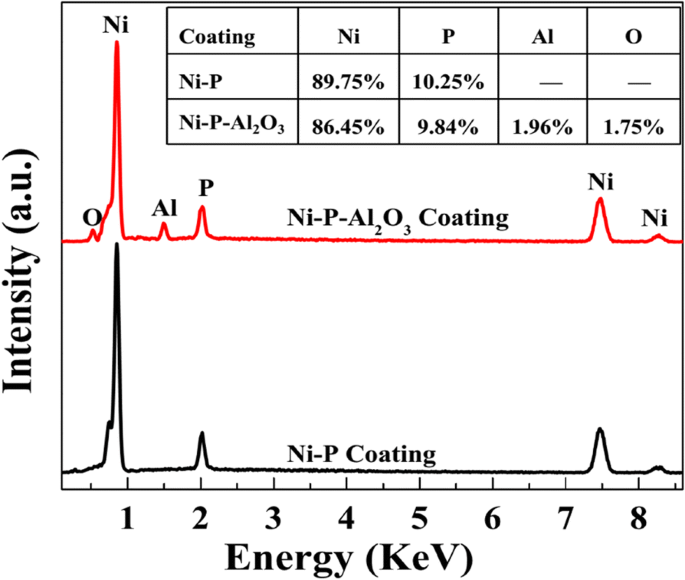
Спектры ЭДС покрытия Ni-P и Ni-P-Al 2 О 3 композитные покрытия
Выводы
Таким образом, мы получили ванну для химического нанесения композитного покрытия и рабочие условия для совместного осаждения Ni-P-Al 2 О 3 покрытия на магниевом сплаве, т.е. 35 г / л NiSO 4 ⋅6H 2 O, 35 г / л молочной кислоты, 30 г / л Na 2 H 2 ЗП 2 ⋅H 2 O, 10 г / л NH 4 ВЧ 2 , 10 г / л нано-Al 2 О 3 частицы, стабилизатор 3 мг / л, pH =6,0 ~ 6,5, T =85 ° C, и скорость перемешивания 350 об / мин. Морфологические характеристики и анализ фазовой структуры композитных покрытий показали, что нано-Al 2 О 3 частицы оказали важное влияние на процесс роста и фазовые структуры (расстояние между кристаллическими плоскостями и размер зерен) покрытий. 3,6 мас.% Al 2 О 3 содержание эффективно улучшило микротвердость и коррозионную стойкость покрытия Ni-P. Кроме того, тест на адгезию показал, что почти не было разницы между покрытием Ni-P и Ni-P-Al 2 . О 3 покрытие. Испытания на срок службы показали, что MTO ванны для химического нанесения композитного покрытия составляет около 4. Короче говоря, Ni-P-Al 2 О 3 композитное покрытие - важная технология для расширения области применения магниевого сплава.
Сокращения
- E 0 :
-
Потенциал холостого хода
- я corr :
-
Плотность тока коррозии
- Mg:
-
Магний
- MTO:
-
Оборот металла
- Ni-P:
-
Никель фосфор
- SEM:
-
Сканирующая электронная микроскопия
- XRD:
-
Рентгеновская дифракция
Наноматериалы
- Свойства и применение противовеса из вольфрамового сплава
- Свойства и использование шаров из вольфрамового сплава
- Свойства и применение медно-вольфрамового сплава
- Применение и свойства вольфрамово-никелевого сплава железа
- Что такое кобальтовый сплав и каковы его свойства?
- Свойства алюминия и характеристики сплава
- Получение и магнитные свойства легированных кобальтом наночастиц шпинели FeMn2O4
- Наножидкости TiO2 - Часть 1:Приготовление и свойства
- Свойства и применение медно-никелевого сплава
- ВДМ® Сплав 40 В