Магнитная 3D-печать:новое поколение индивидуальных композитов
Fortify (Бостон, Массачусетс, США) была основана в 2016 году на основе исследования композитной 3D-печати, проведенного Джошем Мартином (генеральным директором Fortify) и Рэндаллом Эрбом, директором лаборатории DAPS в Северо-Восточном университете в Бостоне. (Эрб также является соучредителем компаний Boston Materials и Fortify.) Их цель состояла в том, чтобы обеспечить быстрое производство композитов с оптимизированной микроструктурой. В запатентованной технологии Fluxprint, которую они разработали, используются магнитные поля и цифровая обработка света (DLP) - но с использованием высоконаполненных полимерных систем - для создания индивидуальных микроструктур в 3D-печатных композитных деталях с высоким разрешением.
Fluxprint против DLP
И DLP, и стереолитография (SLA) в настоящее время рассматриваются как технологии 3D-печати, обеспечивающие высочайшую сложность и точность деталей. Оба основаны на использовании света - обычно ультрафиолета (УФ) - для отверждения светочувствительной смолы, которая обычно содержит эпоксидные или акриловые и метакриловые мономеры. Свет направляется в цифровом виде, чтобы освещать смолу в резервуаре системы, создавая формы или узоры для каждого слоя. Производственная платформа перемещается после каждого слоя, что позволяет напечатать следующий слой и перейти к готовой твердой детали.
Проекторы DLP и SLA относятся к началу 3D-печати в 1980-х годах. DLP-принтеры, как правило, больше, потому что в них находится настоящий световой проектор. В большинстве машин SLA и DLP используются термореактивные полимеры, но EnvisionTEC производит принтер, который также может использовать термопласты. В обоих традиционно использовались чистые полимеры без армирования.
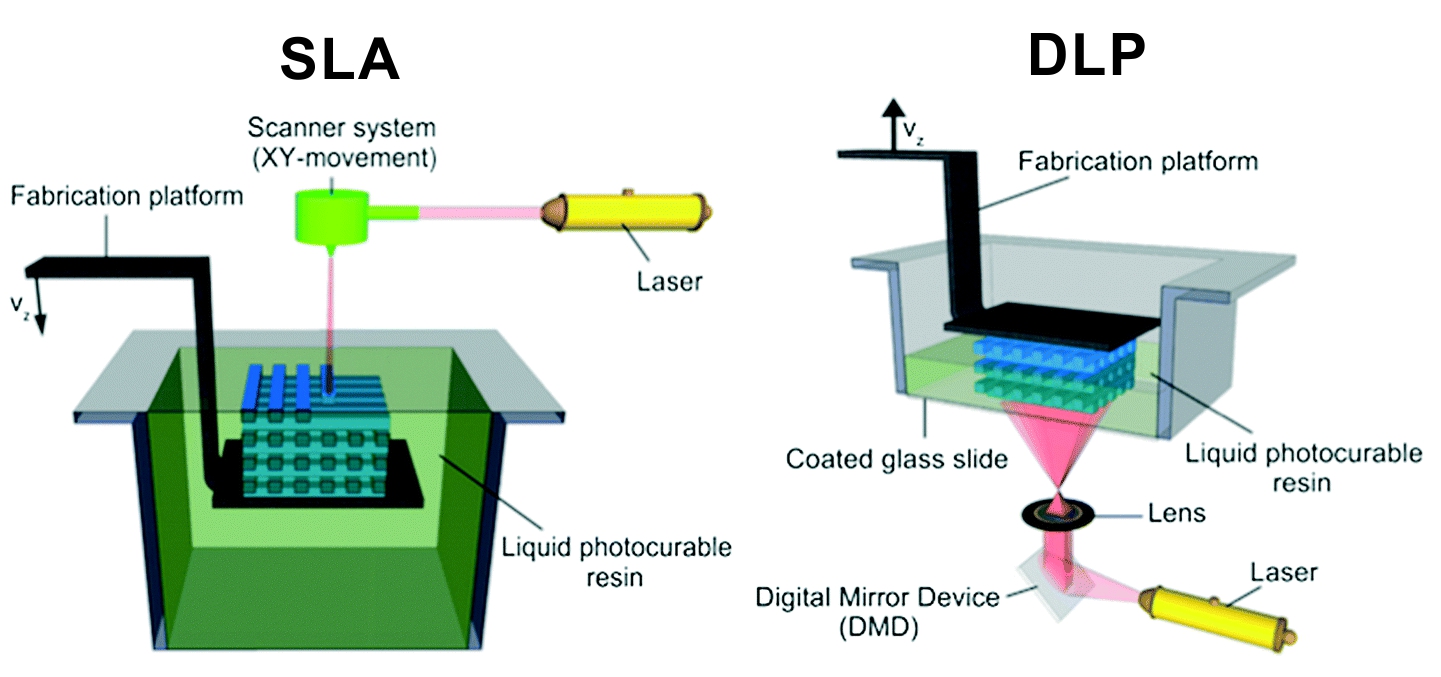
«Платформы DLP обладают достаточной производительностью и качеством, - говорит генеральный директор Fortify Джош Мартин, - но механические свойства всегда были проблемой. Наш основной тезис заключается в том, что ступенчатое изменение характеристик не может быть достигнуто только с помощью химии полимеров. Однако использование уникальных свойств композитов в аддитивной индустрии высокого разрешения изменит правила игры ».
Он объясняет, что Fortify специализируется на УФ-отверждении высоконаполненных технических смол с использованием уникальных добавок и контролем ориентации этих улучшающих свойства добавок в отпечатке. Наполнители включают стеклянные, углеродные и керамические волокна, а также частицы. Технические смолы включают акрилатные и метакрилатные (ПММА) или эпоксидные или катионные смолы, которые, как объясняет Мартин, являются более традиционными для индустрии покрытий. Ведущие производители смол по всему миру (BASF, DSM, Dupont и другие) вкладывают значительные средства в улучшение свойств своих добавочных материалов. Fortify может выбрать лучшее из этих достижений, чтобы добавить технологию армирования.
Контроль ориентации волокна достигается с помощью магнитного поля. Когда Fortify 3D печатает деталь с использованием технологии Fluxprint, волокна выравниваются по вокселю с помощью магнита, чтобы соответствовать требованиям к нагрузке детали. (См. Процесс в действии на видео выше.) Для немагнитных армирующих материалов, таких как керамические и стеклянные частицы и волокна, используются запатентованные методы магнитной маркировки, чтобы покрыть наполнители таким образом, чтобы они были чувствительны к магнетизму и совместимы с смола.
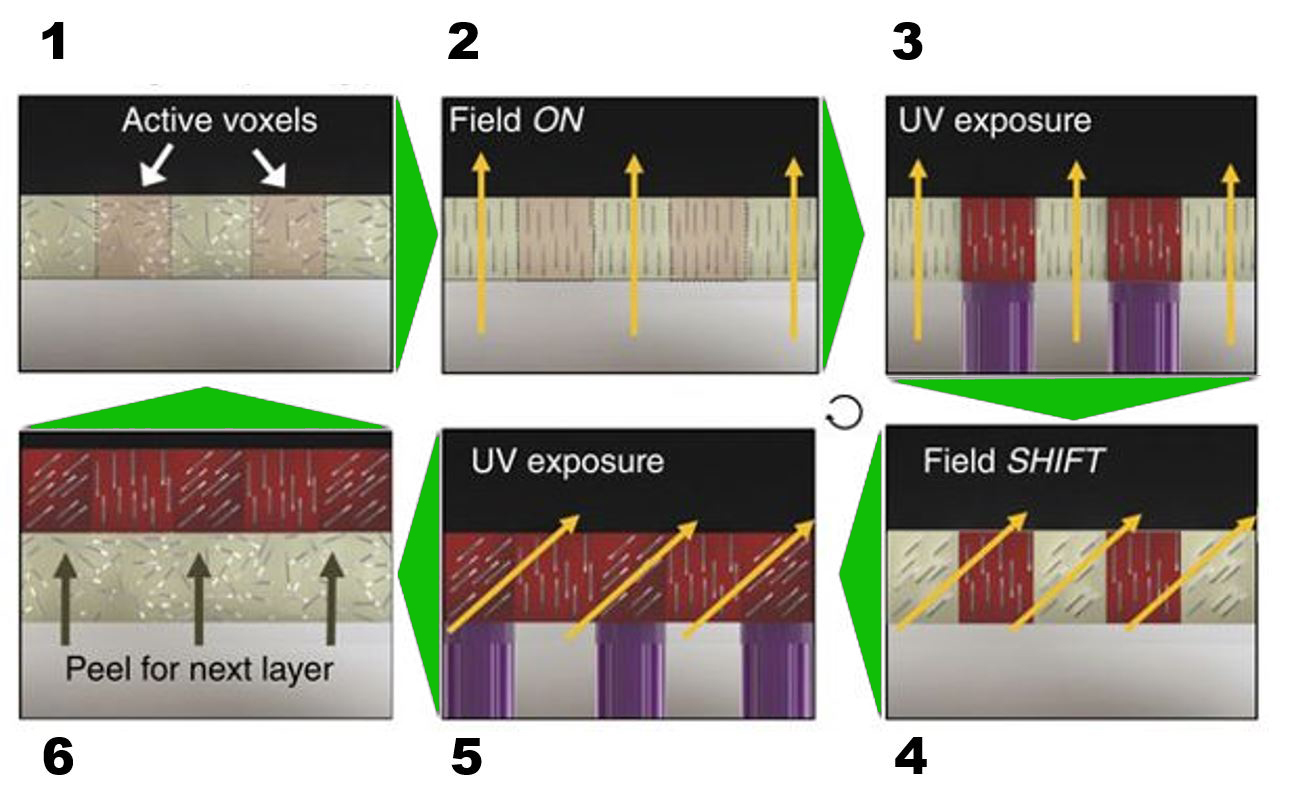
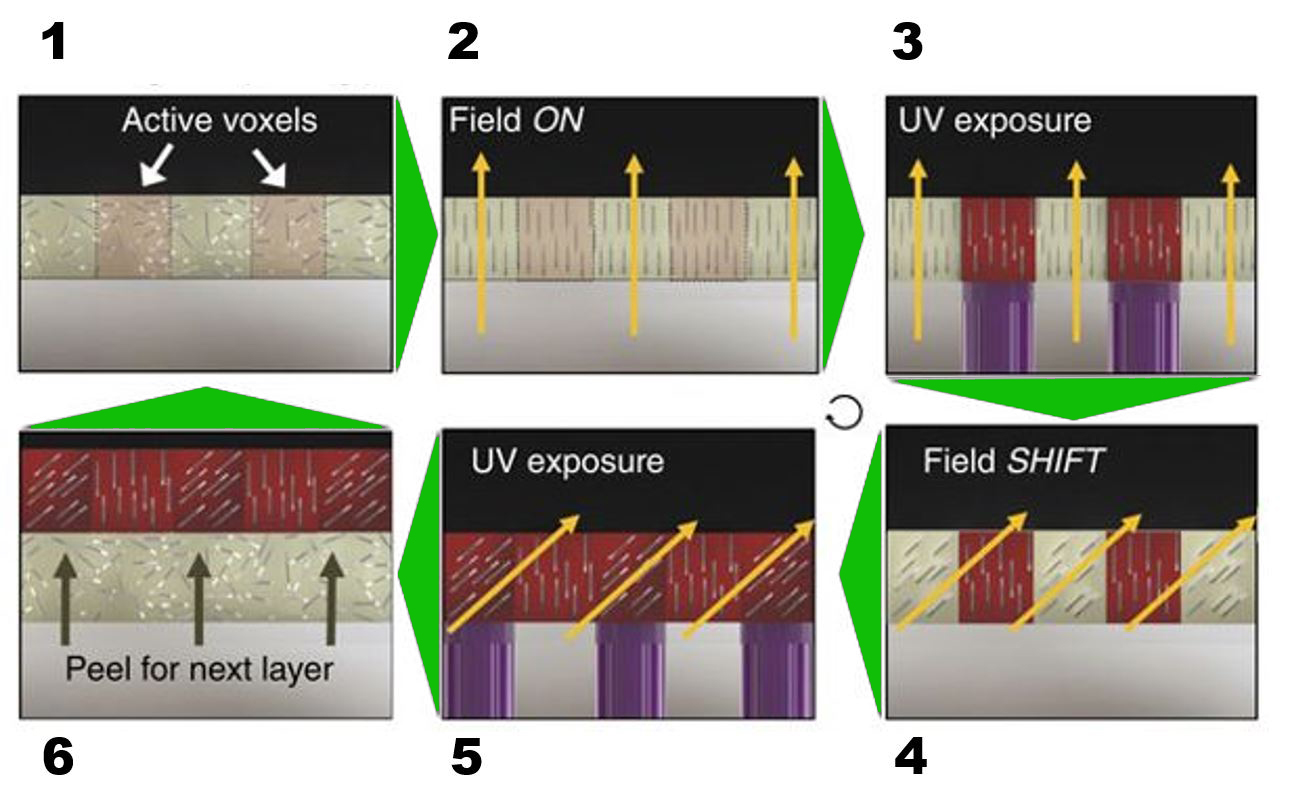
Процесс Fluxprint показан на изображении выше и описан следующим образом:
- Слой загружаемого материала подается в зону строительства с произвольно выровненной арматурой.
- Магнитное поле применяется для выравнивания арматуры.
- Активные воксели подвергаются воздействию ультрафиолетового излучения, фиксируя ориентацию усиления в этих вокселях (теперь показаны красным).
- Магнитное поле смещается, чтобы задать новую ориентацию арматуры.
- Повторите этап УФ-экспозиции, чтобы зафиксировать ориентацию для следующего набора вокселов (при необходимости повторите).
- Формирующая пластина регулируется для подачи неотвержденной матрицы исходного материала для следующего слоя печати.
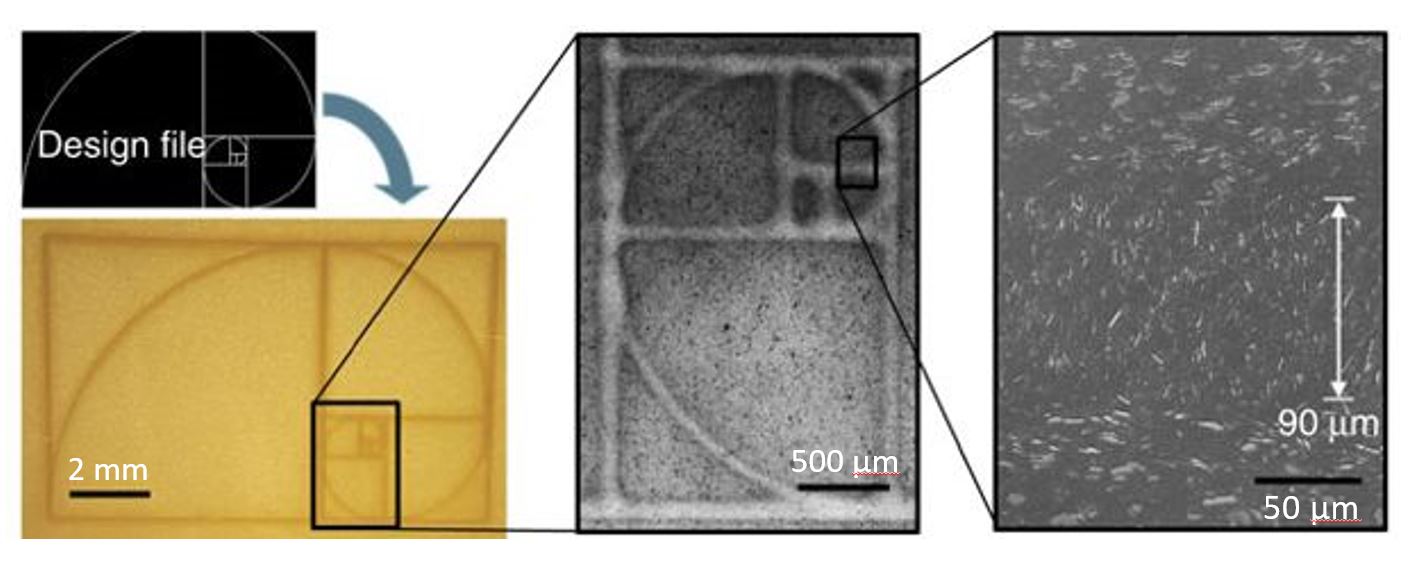
Технология Fluxprint позволяет управлять ориентацией волокна на уровне вокселей в процессе печати. Источник | Джошуа Дж. Мартин, Брэд Э. Фьоре и Рэндалл М. Эрб, Nature Communications «Разработка архитектур композитного армирования, созданного на основе биодобавок, с помощью трехмерной магнитной печати». том 6, Номер статьи:8641 (2015).
Почему воксель за вокселем?
«Каждая геометрия имеет уникальные состояния деформации и напряжения», - объясняет Мартин. «Большинство композитов изготавливаются вручную, чтобы учесть это. Мы оцифровываем процесс. Например, если вы можете правильно укрепить раму БПЛА, вы можете использовать меньше материала. От этого выиграет любое приложение, работающее против гравитации ».
Воксельная печать также имеет высокое разрешение. «На сегодняшний день это процесс производства композитных материалов с самым высоким разрешением», - говорит Мартин, отмечая, что моделирование методом наплавленного осаждения (FDM), при котором неармированная или фрезерованная пластиковая нить, армированная волокном, расплавляется и осаждается на печатный стол, имеет разрешение в сотни единиц. микрометров, в то время как Fluxprint's находится в пределах десятков микрометров. «Итак, это улучшение на порядок, которое выходит за рамки того, что воспринимается невооруженным глазом. Такое разрешение очень важно для большого количества деталей конечного использования ».
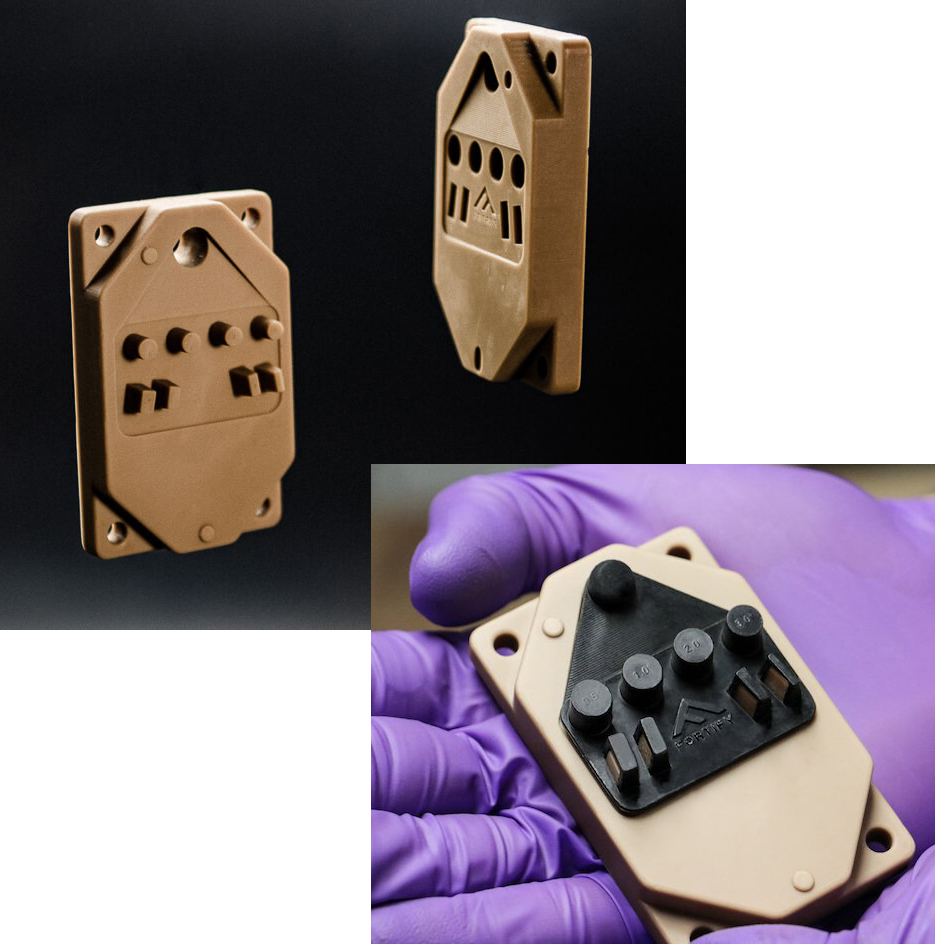
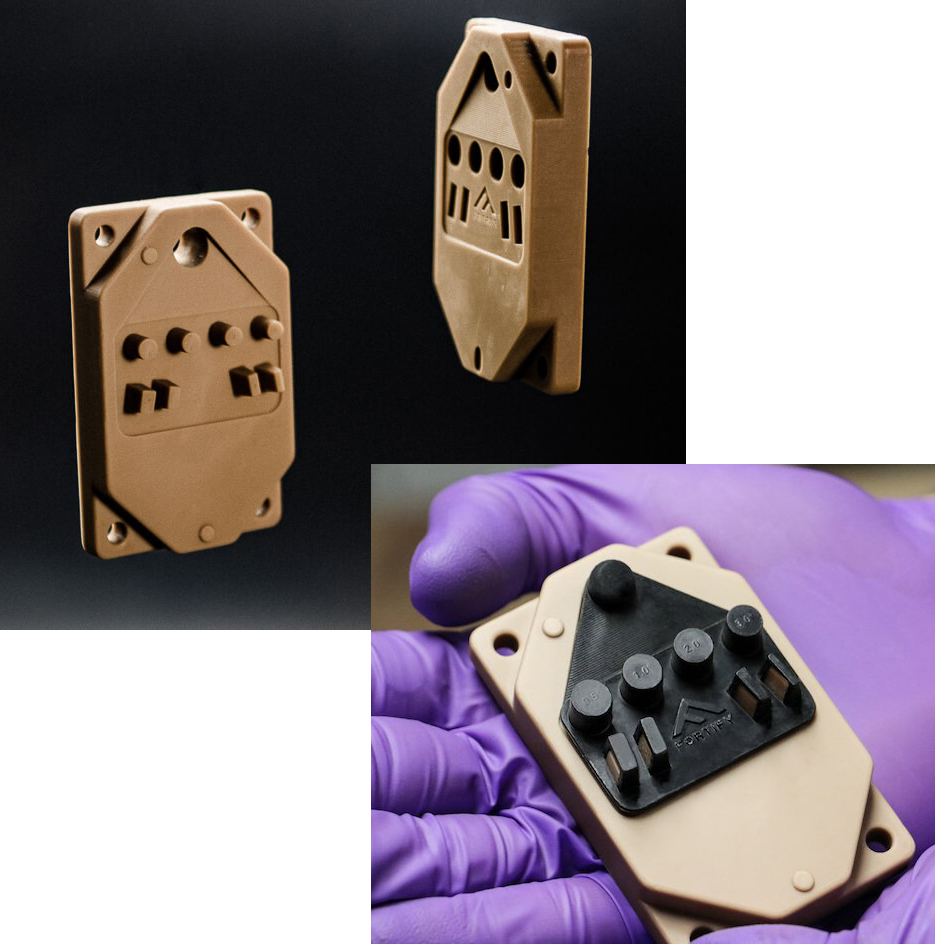
Технология магнитной 3D-печати Fluxprint от Fortify позволяет ориентировать волокна для усиления выступов штифтов на инструментах для литья под давлением. Источник | Укрепите.
«Мы предлагаем инструменты для литья под давлением, которые значительно дешевле, чем металл, обрабатываемый традиционной обработкой, они могут быть доставлены в кратчайшие сроки и обладают функциями, недоступными при использовании традиционных методов обработки», - продолжает Мартин. «Один заказчик будет перебирать 12 различных конструкций в год, изготовленных из алюминия. Мы значительно сократили их время вывода на рынок, выпустив более десятка дизайнов за несколько месяцев. Теперь они могут перейти от дизайна к деталям на полке за несколько недель ». Еще одно преимущество - это возможность усиливать проекции, называемые «колышками». Эти экструзии с высоким соотношением сторон часто вытягиваются. Армирование предотвращает это, сохраняя при этом жесткие допуски.
Узнайте больше о преимуществах Fortify в инструментах для литья под давлением в дочернем журнале CW Additive Manufacturing.
Открытые материалы, новые разработки
Fortify придерживается подхода открытых материалов. «Мы не хотим ограничивать возможности наших клиентов для роста и исследований с помощью аддитивов», - объясняет вице-президент Fortify по приложениям Карло Делос Рейес. «Мы гарантируем нашим клиентам гибкость и использование лучших доступных материалов за счет открытых инноваций».
«Мы сотрудничаем с крупными производителями полимеров и разрабатываем химический состав добавок», - говорит Мартин. Он отмечает, что у каждого наполнителя есть свои плюсы и минусы в отношении износостойкости, характеристик при температуре и т. Д. «Для волокон длина колеблется от нескольких мкм до нескольких мм, в зависимости от области применения. Там, где нам нужно разрешение поверхности, мы используем больший процент добавок меньшей длины. Там, где мы можем позволить себе более шероховатую поверхность, но хотим, например, оптимизировать предел прочности на разрыв, мы используем добавки для более длинных волокон ».
Одна из стратегий Fortify состоит в том, чтобы сотрудничать с лидерами отрасли и поставщиками, чтобы использовать их опыт и способствовать взаимному обмену идеями. Fortify недавно объявила о партнерстве с DSM Additive Manufacturing (Хук ван Холланд, Нидерланды и Элгин, Иллинойс, США) для разработки высокоэффективных композитных материалов, которые будут использоваться в системах печати Fortify для достижения улучшенных механических и температурных характеристик. «Они расширят нашу палитру смол, - говорит Мартин, - и мы рады работать с ними над разработкой новейших смол».
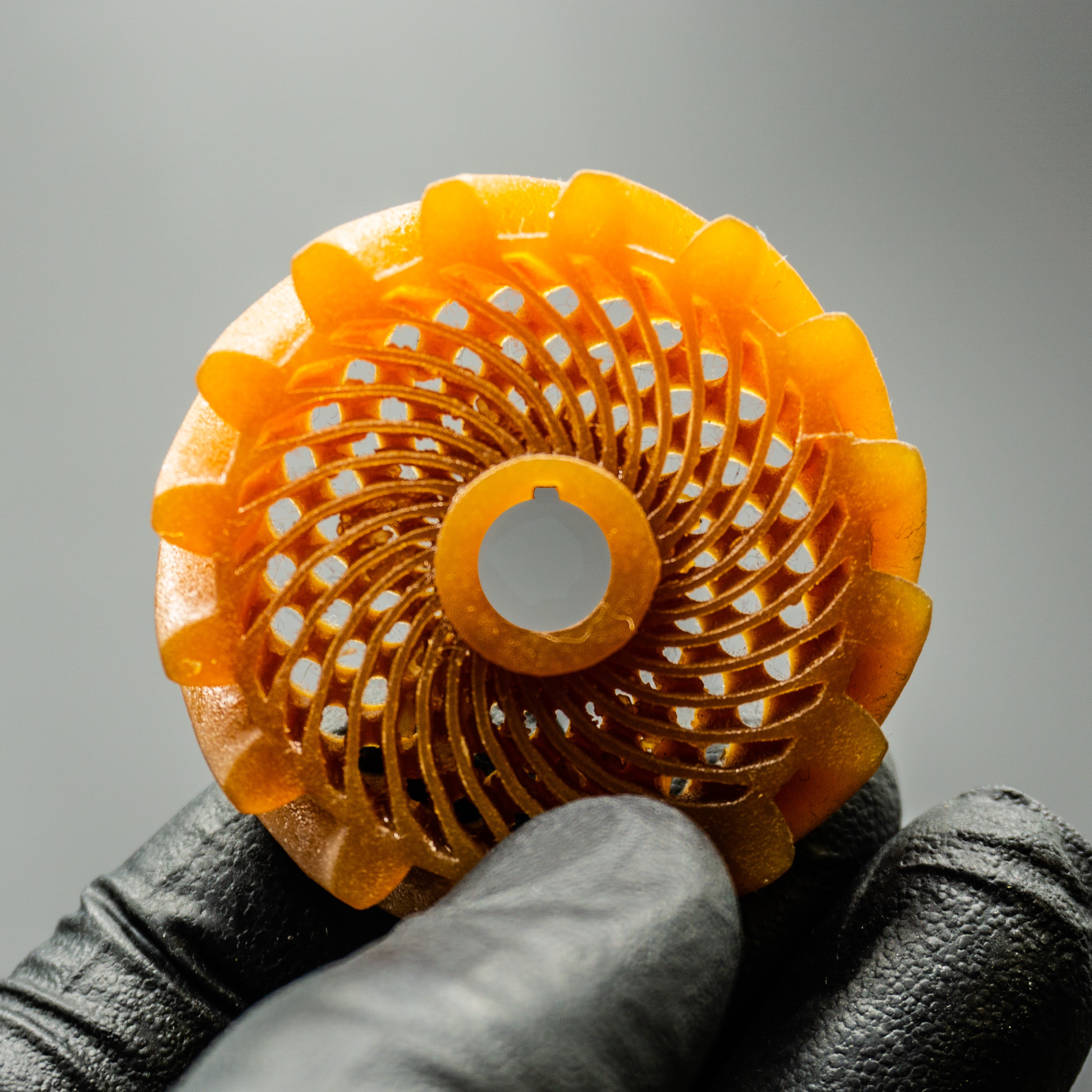
Композитная деталь, армированная стекловолокном, изготовлена с использованием Fluxprint. ИСТОЧНИК | Укрепите.
Армирование в направлении Z и приложения
Fluxprint все еще печатает по слоям. Итак, можно ли добиться армирования в z-направлении? «Если вы печатаете волокна длиной 2 миллиметра, вы не можете размещать их в направлении оси z», - говорит Мартин. «Но вы могли бы стать короче волокна в z-ориентацию. Мы рассматриваем несколько масштабов длины и мы видим, что это будет развиваться в будущем для оптимизации передачи нагрузки ».
Fortify уже производит детали для БПЛА, в том числе пропеллеры, и видит гораздо больше таких применений в аэрокосмической отрасли. «У нас небольшая производственная площадка, поэтому мы сосредотачиваемся на приложениях, в которых мы можем легко справиться с небольшими объемами производства», - говорит Мартин. «Это зрелая экосистема, но мы предлагаем новый уровень механических свойств при высоких температурах и допусках». Он ссылается на возможность улучшить температуру теплового отклонения детали . и объясняет, что в автомобилях есть десятки деталей, находящихся под капотом, которые должны обеспечивать прочность и жесткость при воздействии температур 160 ° C. «Такие детали со сложной геометрией хорошо поддаются 3D-печати с помощью нашей технологии. По сравнению с текущим методом формования и обработки деталей из PEI (полиэфиримида) мы предлагаем более высокую производительность, более короткое время выполнения заказа и высокий потенциал снижения затрат . . »
Оснастка также является актуальным рынком, включая матрицы, приспособления и приспособления для литья под давлением. «Опять же, наши детали жестче, прочнее и обладают более высокой термостойкостью, сохраняя точность размеров при эксплуатации», - говорит Мартин. «Но их настоящая ценность заключается в не требующие значительной постобработки, например, при использовании электроэрозионных станков, и все же они соответствуют качеству приспособлений, изготовленных этими традиционными методами, включая фрезерование с ЧПУ ».
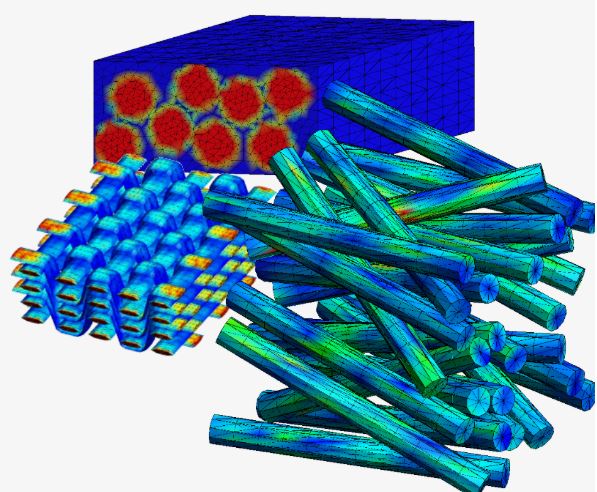
Источник | МультиМеханика
Продвижение следующего поколения многомасштабных многофункциональных композитов
Fortify сотрудничает с MultiMechanics (Омаха, Небраска, США), разработчиком многомасштабного моделирования и программного обеспечения для моделирования сложных материалов. Это партнерство интересно по ряду причин. Во-первых, Fortify будет использовать флагманский продукт MultiMechanics, MultiMech, для прогнозирования характеристик деталей . и оптимизировать их дизайн и ориентацию волокон перед печатью. Таким образом, MultiMech будет обеспечивать обратную связь для итеративного проектирования с обратной связью , позволяя пользователям быстрее адаптировать и оптимизировать композитные детали Fluxprinted. Fortify и MultiMechanics также планируют интегрировать MultiMech в INFORM от Fortify . ПО для генеративного дизайна и управления печатью. Таким образом, от проектирования до виртуального тестирования и печати - все функции будут контролироваться в едином цифровом потоке.
Что касается второго пункта, важно понимать, что MultiMechanics предлагает через свое программное обеспечение MultiMech:
- Многомасштабный анализ методом конечных элементов , включая моделирование практически неограниченного количества масштабов (например, нано, микро, слой, ламинат, деталь).
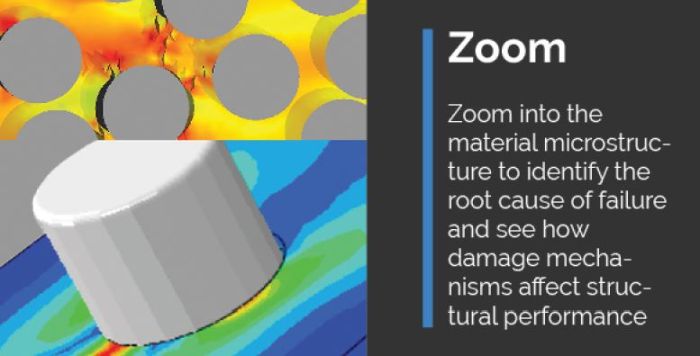
- Автоматическое создание сложных трехмерных микроструктур конечных элементов, а также моделирование микроструктуры практически любых материалов, включая непрерывные и рубленые волокна, частицы, пустоты, пену, ткани и т. д.
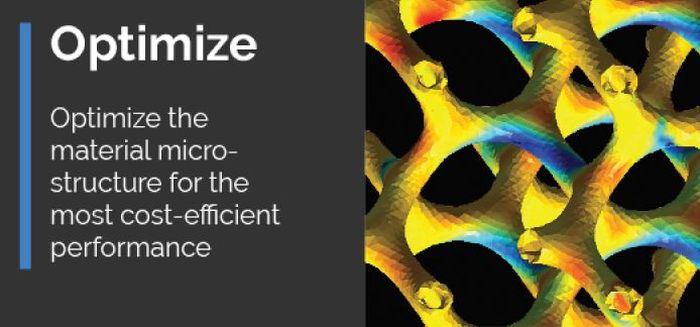
- Моделируйте эффекты микромасштабных компонентов, включая взаимодействия , объемные доли, распределение и ориентация, плюс импорт p вариация, вызванная процессом из программ (например, Moldex3D, Moldflow).
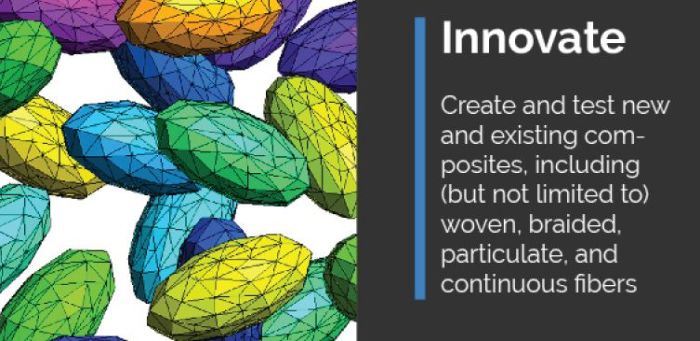
- Проанализировать, как производственные вариации влияют на характеристики деталей . и выполните da моделирование мага включая многомасштабный переход микротрещин в макротрещины.
Это восходит к тому, почему Мартин и Эрб вообще основали Fortify. В своей статье 2015 года «Проектирование архитектур композитного армирования, созданного методом биоинспирации, с помощью 3D-магнитной печати», они заявляют:
Мартин и Эрб обсуждают природные композиты, в которых используются прерывистые волокна и армирующие частицы, организованные в многомасштабную сложную архитектуру . для достижения превосходных свойств по сравнению с их составляющими. Пример, приведенный Цюньфэном Ченгом в журнале Materials Today за 2017 год. Изделие - перламутр в раковинах морского ушка. Вязкость разрушения перламутра, состоящего из 95 об.% Неорганического арагонита и 5 об.% Органического протеина, составляет в 3000 раз больше чем у арагонита. Ченг отмечает, что это демонстрирует «эффект усиления» механических свойств, который выходит далеко за за рамки правил смесей в традиционных композитах . .
В 2018 г. Advanced Materials В статье «Аддитивное производство как метод проектирования и оптимизации биоинспирированных структур» авторы Одри Веласко-Хоган, Цзюнь Сюй и Марк А. Мейерс утверждают, что иерархическая структура таких материалов, как перламутр, кость, бамбук и раковины ракообразных, дает возможность их впечатляющего сочетания прочности, модуля, легкости, прочности и сопротивления усталости. Составляющие их частицы / волокна и матрица организованы по-разному на каждом уровне . (например, нано-, микро-, мезо-, макро-), изменяя свойства на каждом уровне (например, многомасштабный композит). В сочетании с эффективными интерфейсами между уровнями эта иерархическая структура работает синергетически, чтобы уменьшить распространение трещин и повысить ударную вязкость . при сохранении твердости - то, чего еще не удалось достичь в керамике после почти столетних попыток.
Будущее композитов и ИНФОРМ
Это будущее композитов:создание иерархических композитов с уникальными свойствами разработан для точных применений. И он уже быстро продвигается. Например, Институт конструкций и дизайна Немецкого аэрокосмического центра (DLR) в Штутгарте также стал партнером компании MultiMechanics . чтобы понять, как изменение температуры влияет на микроструктуру и поведение материала композитов с керамической матрицей (CMC) . Этот анализ считается решающим для будущего производства компонентов CMC DLR, в том числе сопел для ракет и систем тепловой защиты для возвращающихся кораблей. «Наша работа в MultiMechanics в течение последних десяти лет была посвящена точному соединению микроструктурного поведения передовых материалов на общую производительность детали и ее производство », - говорит д-р Флавио Соуза, президент и технический директор MultiMechanics. «MultiMech позволяет нам моделировать микроструктурные трещины и определять, как они повлияют на композитную деталь в целом», - заявляет Нерадж Джайн, руководитель группы отдела керамических композитов и конструкций DLR. «Эффективная интеграция MultiMech с другими нашими инструментами FEA, такими как Abaqus и ANSYS, увеличивает нашу продуктивность и приближает нас к нашей цели по оптимизации материалов CMC виртуально . »
После того, как эти композиты были виртуально оптимизированы, они затем печатаются с помощью MultiMech, встроенного в программное обеспечение Fortify INFORM, которое уже ориентировано на органические, оптимизированные по нагрузке архитектуры через свою основу генеративного проектирования . (Обратите внимание, что бизнес-подразделение Solvay по композитным материалам также инвестировало средства в технологии MultiMechanics и 3D-печати.)
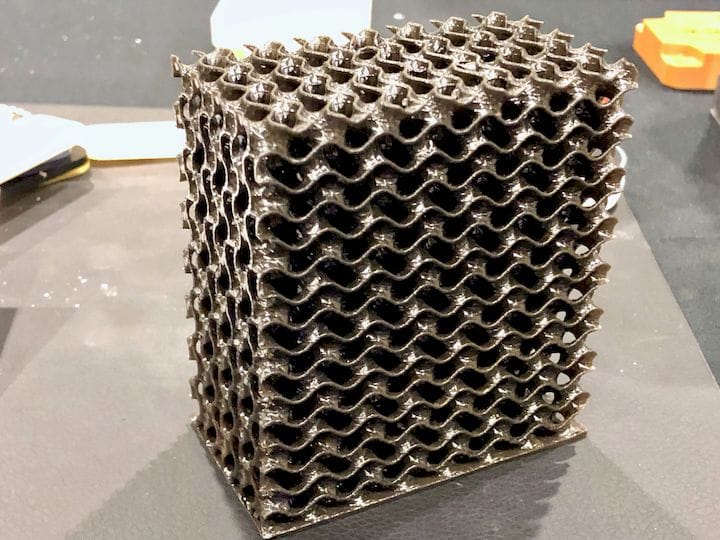
Решетка, армированная волокном, дизайн предоставлен nTopology. Источник | Укрепите.
«ИНФОРМ использует продвинутые алгоритмы для оптимизации ориентации волокон для каждой детали », - объясняет Мартин. «Там, где традиционно рабочий процесс 3D-печати начинается с STL, чтобы разрезать дизайн, наш начинается с FEA . (модель с напряжением и деформацией), а затем решает, на какие воксели разделить эту смоделированную конструкцию и как сориентировать волокна. Мы выполняем итерации, выравнивая волокна с векторами поля напряжения / деформации, а затем моделируем, как будет вести себя этот отпечаток, и используем эти данные для уточнения и оптимизации конструкции, достигая генеративного микроструктурного дизайна . »
Только начало
Обратите внимание, что эти будущие композиты включают в себя ряд материалов. Лаборатория военно-морских исследований (NRL, Арлингтон, Вирджиния, США) разрабатывает КМЦ с использованием керамической матрицы с вторичным керамическим армированием с помощью наночастиц и / или нитей. Эти КМЦ могут также использовать армирование непрерывным волокном. Другими словами, разные компоненты и архитектуры могут использоваться на каждом уровне для повышения прочности и требуемых специальных электрических и тепловых свойств (например, в гиперзвуке, подробнее читайте в моей статье о нанокомпозитах от июля 2019 года).
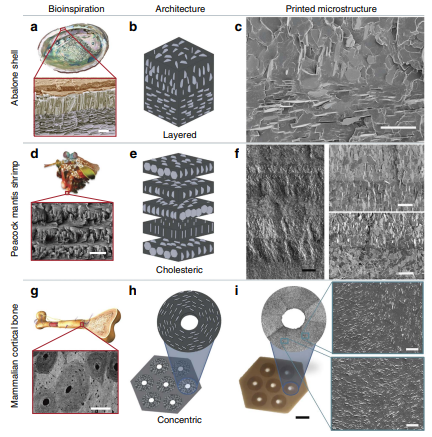
ИСТОЧНИК | Рисунок 3, «Проектирование архитектур биоинспирированного композитного армирования с помощью трехмерной магнитной печати» Джошуа Дж. Мартин, Брэд Э. Фьоре и Рэндалл М. Эрб, Nature Communications, том 6 (2015).
Иерархические композиты также печатаются и тестируются с использованием усиленных эпоксидных красок и термопластичных полимерных матриц. Это, пожалуй, самый большой плюс для Fortify как стартапа. Компания не просто готовится к созданию композитов будущего, она уже занимается их проектированием и производством. И хотя то, что уже достигнуто, впечатляет - это только начало.
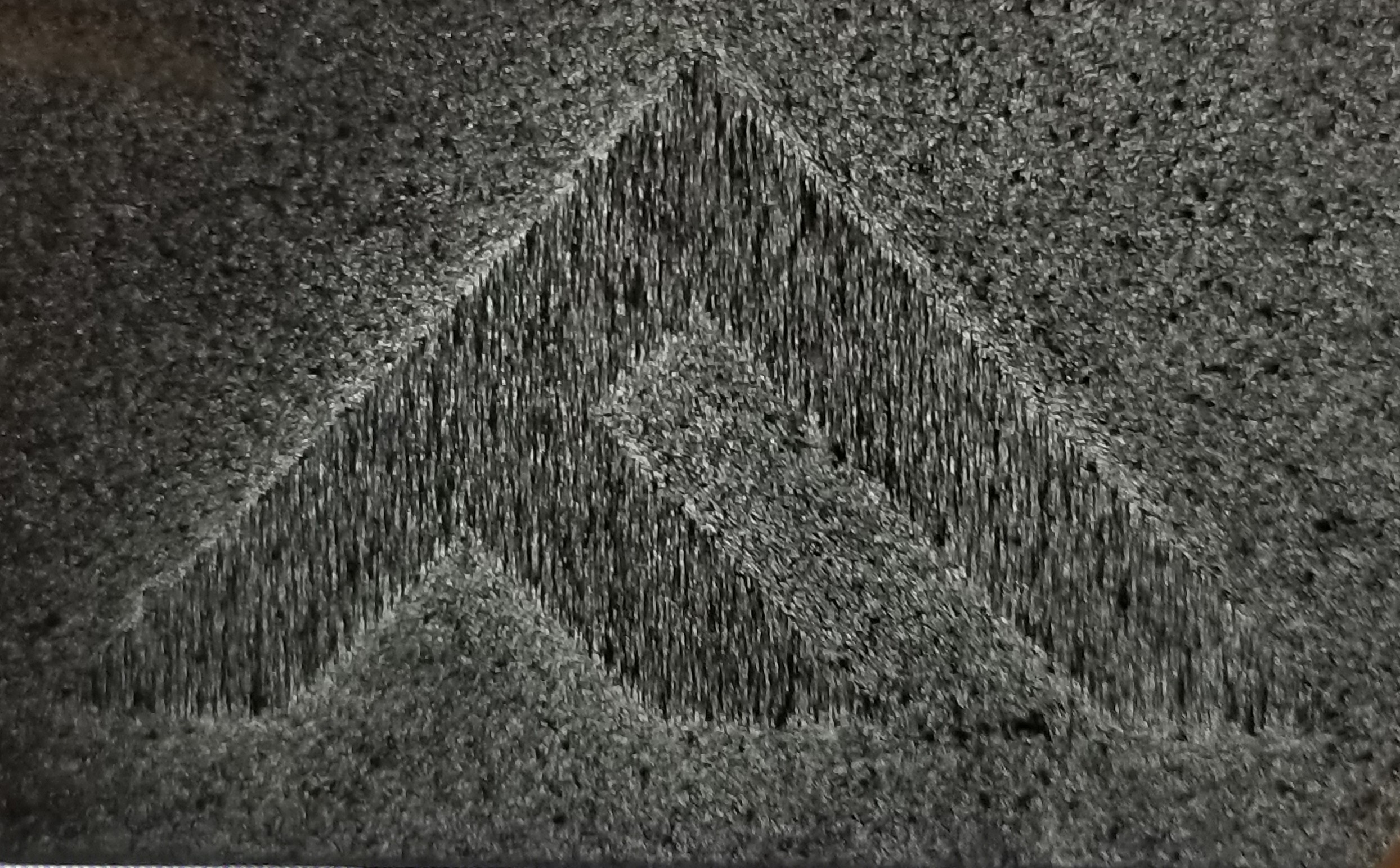
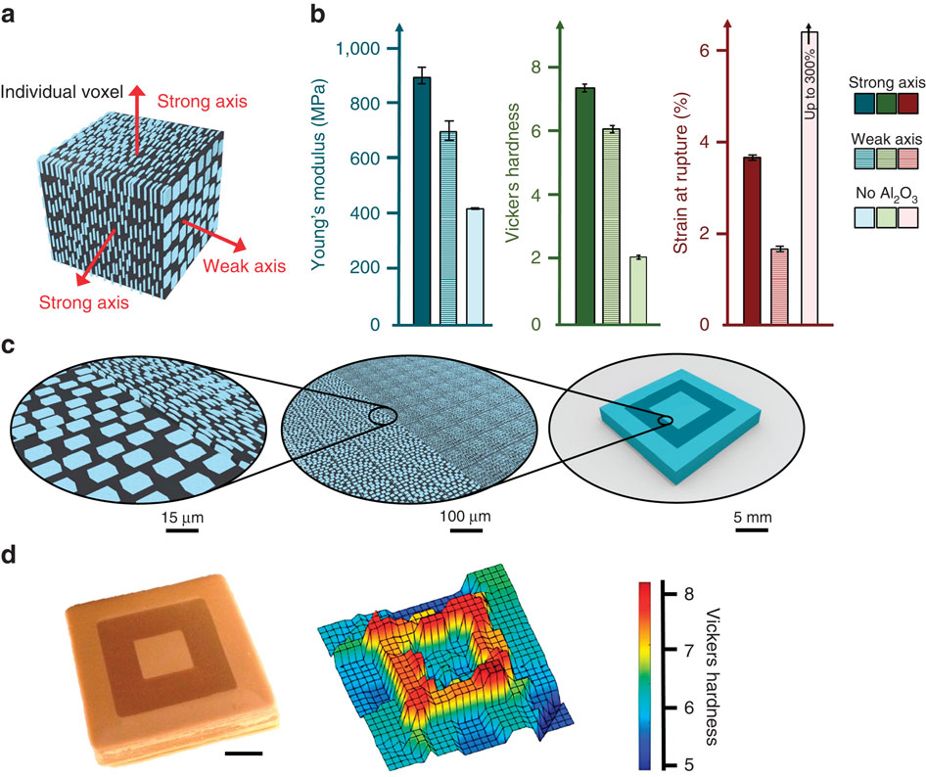
Смола
- 3 основных шага 3D-печати
- Может ли трехмерная печать из нескольких материалов стать следующим шагом для AM?
- Азбука 3D-печати
- Эволюция 3D-печати
- Общественные колледжи:обучение производителей нового поколения
- День производства 2017:обучение следующего поколения рабочих
- Композитные материалы для 3D-печати с непрерывным волокном
- Материал для следующего поколения интеллектуальных датчиков
- Ультратонкий терагерцовый источник прокладывает путь к следующему поколению коммуникационных технологий
- COVID-19:спрос на умные фабрики следующего поколения