Революция парадигмы стоимости композитных материалов, Часть 2:Формирование
Подпрограмма RAPM в рамках программы Tailorable Feedstock and Forming (TFF) DARPA собирала аналитические данные по текущему / прошлому производству, а также эмпирические данные из собственных испытаний формования для нескольких деталей для построения этих кривых. Цель состоит в том, чтобы лучше понять торговое пространство для составных частей и процессов.
Источник всех изображений:The Boeing Co., DARPA.
Программа Tailorable Feedstock and Forming (TFF) была запущена Управлением перспективных исследовательских проектов Министерства обороны США (DARPA, Арлингтон, Вирджиния, США) в 2015 году, чтобы обеспечить быстрое, недорогое и гибкое производство небольших композитных деталей сложной формы для нужд обороны. самолет. Эта 48-месячная программа была направлена на повышение экономической конкурентоспособности композитов с целью использования их снижения веса и устойчивости к коррозии и растрескиванию по сравнению с обработанным алюминием. В первой части этой серии статей CW изучил концепцию TFF и ее подпрограмму Tailorable Universal Feedstock for Forming (TuFF), в рамках которой был разработан коротковолокнистый листовой материал с высокими механическими свойствами и формуемостью, напоминающей металл.
В этой статье акцент смещается с исходного сырья на формование с помощью второй подпрограммы TFF:высокопроизводительного производства RApid (RAPM, произносится как «wrap-em») под руководством The Boeing Co. (Чикаго, Иллинойс, США). Программа началась в июле 2016 года и представила свои результаты в многочисленных публикациях, включая 6 статей и две презентации на SAMPE 2019. Цель RAPM, как объяснили технические специалисты и главные исследователи Boeing Гейл Хан и Том Цоцис, - «революционизировать парадигму затрат для небольшие составные части, позволяющие повсеместно использовать в оборонных приложениях ».
«Мы начали с этого видения достижения аэрокосмических характеристик за счет повышения эффективности автомобилестроения», - говорит Хан. Программа работала с производителями автомобильных композитных материалов и запчастей, включая Solvay Composite Materials (Alpharetta, Джорджия, США) и SGL Composites (Ried and Ort im Innkreis, Австрия), но достижение аэрокосмических свойств не всегда было простым делом. «Хотя низкотемпературные эпоксидные смолы быстрого отверждения легко доступны для автомобильной промышленности, они не соответствуют требованиям аэрокосмической отрасли», - говорит Цоцис. RAPM действительно использовала новые двухкомпонентные эпоксидные смолы быстрого отверждения, предназначенные для частей, пригодных для вливания смол авиационно-космического класса. Однако изначально температура формовочной системы на SGL не могла превышать 130 ° C, что не позволяло достичь 30 минут наработки инструмента.
«Наша цель состояла в том, чтобы обеспечить максимальное время работы с инструментом 30 минут, чтобы можно было использовать высокопроизводительную рабочую ячейку, чтобы снизить затраты на уровне системы и быть конкурентоспособными по сравнению с обработанным алюминием», - говорит Цоцис. «В компании Boeing мы решили, что это удовлетворит все, что мы видели в области оборонных приложений», - добавляет Хан. «Зачем устанавливать его здесь, если с термопластом можно получить от 2 до 6 минут? Потому что термопласты требуют еще более высокой температуры обработки с соответствующими ограничениями инструментов, и наша цель - предоставить нашей цепочке поставок множество вариантов ».
По мере продвижения программы она открывалась для авиакосмических материалов и производителей и даже для экспериментальных систем, таких как Solvay XEP-2750. «Первоначально мы думали, что сможем полностью оценить эту систему, как мы это сделали с CYCOM 5320-1 в нашей работе с программой DARPA« Технология неавтоклавного производства »с 2007 по 2012 год», - говорит Хан. Хотя такая же степень оценки была невозможна, XEP-2750 теперь коммерциализируется Solvay как CYCOM EP-2750 (см. Врезку в Интернете «Новый препрег для компрессионного формования в RAPM . ”) И извлекли пользу из многочисленных испытаний деталей RAPM и извлеченных уроков.
«Все, что мне нужно, - это пара процессов для небольших композитных деталей, которые могут выиграть у алюминия при коммерческом исследовании», - говорит консультант по индустрии композитов и программы TFF Джефф Хендрикс о своих целях в отношении RAPM. Итак, удалось ли RAPM? CW исследует усилия программы по производству сотен деталей, сравнивает более десятка конфигураций деталей для аэрокосмической отрасли с использованием различных материалов и процессов, при этом исследуя методы сокращения времени и затрат.
Структура программы
Работая с ключевыми отраслевыми партнерами, RAPM испытал детали в трех основных направлениях:
- Настой смолы с углеродными композитами HITCO (Гардена, Калифорния, США) и SGL Composites
- Термореактивный препрег формовка с использованием композитных материалов Solvay (Хеанор, Великобритания и Анахайм, Калифорния, США), Fiber Dynamics (Уичито, Канзас, США) и Reinhold Industries (Санта-Фе-Спрингс, Калифорния, США).
- Формование из термопласта с ATC Manufacturing Inc. (Пост-Фолс, Айдахо, США) и TxV Aero (Бристоль, Род-Айленд, США)
Формовочные испытания были выполнены в два этапа:начальный этап «Разработка производства» (рис. 1), за которым следовали последующие этапы «Проблемы и переход» (C&T) (рис. 2) к вызову начальные разработки и переход кандидаты с потенциалом победы над обработанным алюминием.
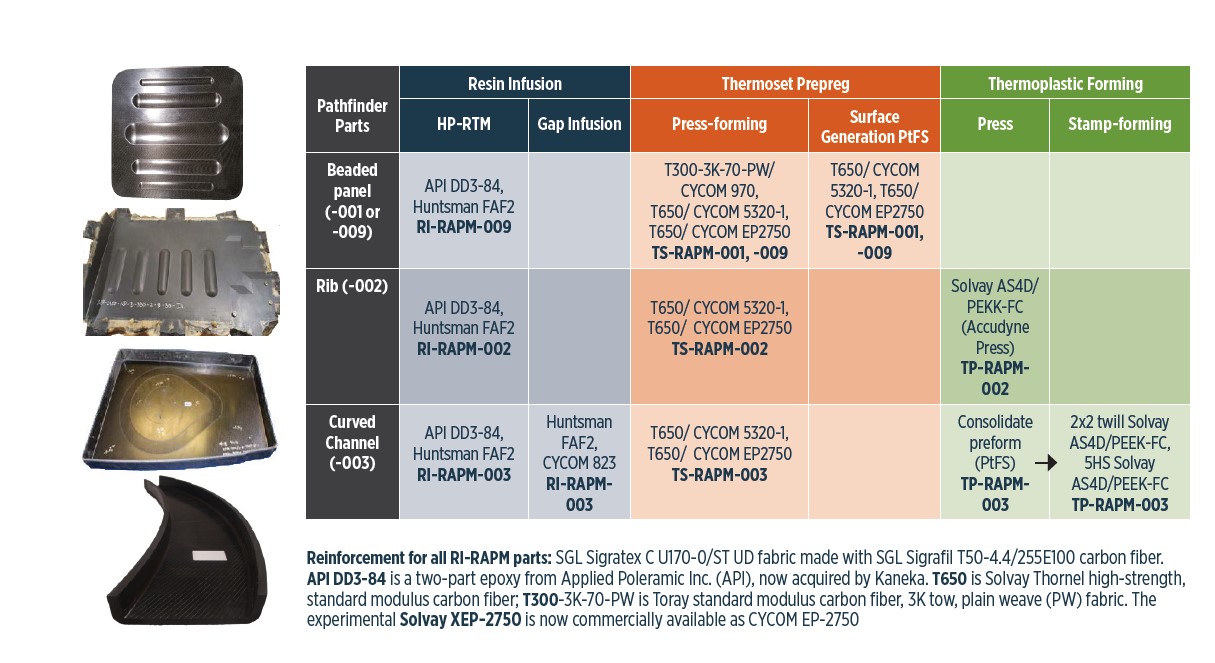
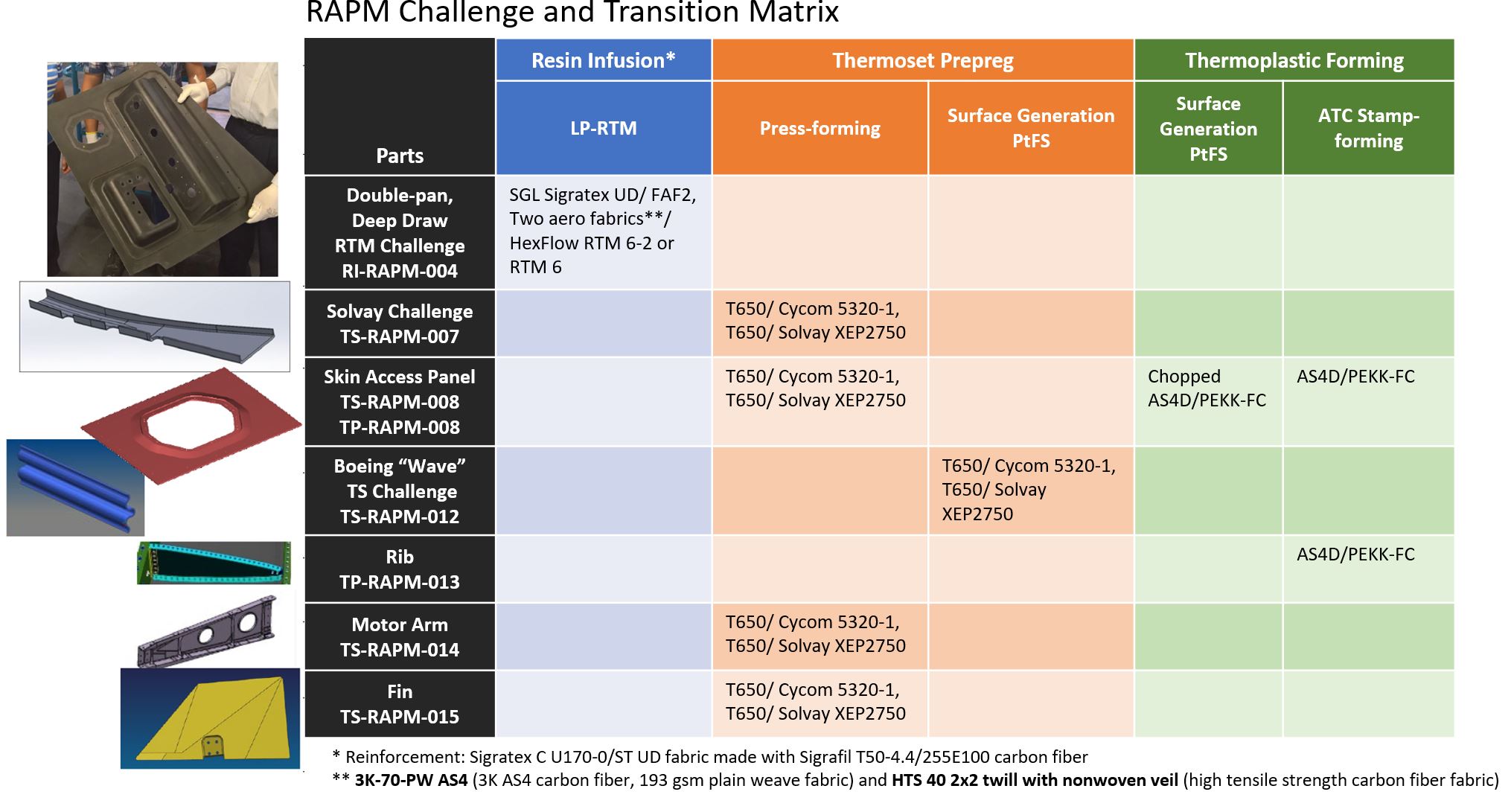
Развитие производства В испытаниях использовались три основные конфигурации деталей:панели с бортиком (было два типа), ребро с выступами (наращивание слоев) и изогнутый С-образный канал. Эти встроенные элементы, общие для аэрокосмических деталей, могут вызвать производственные проблемы:панель с бортиком имела несколько отличий от плоскости, плюс выступы вверх, вниз и вертикальный край; ребристая панель имела подкладку с несколькими краями под углом 90 градусов, а также выступ на одном из краев; а С-образный канал имел разный внутренний и внешний радиус, разную кривизну во фланцах и значительные провалы слоя в стенке.
Целью было разработать руководство по проектированию и производству для каждого из трех гусениц. «На первых испытаниях это не выглядело сексуально, - вспоминает Хан. «Но они помогли определить приемлемые радиусы и геометрию деталей, которые позволили бы производить детали без нежелательного искажения волокон, а также оптимальные комбинации параметров, таких как приложенное натяжение, температура, давление и время на инструменте».
Все три дорожки материала и процесса RAPM включали испытания с использованием системы управления и инструментов для пиксельного нагрева от производства до функциональных спецификаций (PtFS) Surface Generation (Rutland, Великобритания) (см. Врезку онлайн « Разработка RAPM с PtFS »), Расположенный в Boeing R&T в Сент-Луисе, Миссури, США.« Это произошло потому, что мы искали рабочую ячейку, которая могла бы вместить все три типа материалов / процессов в среде с гибкой скоростью », - говорит Хан. «Мы смогли изучить различные подходы к регулированию температуры и затраты». Ячейка Boeing PtFS имеет максимальную температуру 440 ° C, усилие зажима 150 тонн и полезный объем детали 750 на 750 на 100 миллиметров.
Хотя первоначальное видение заключалось в использовании коротковолокнистых листовых материалов TuFF, поскольку они были недоступны на начальном этапе, RAPM продолжил использование суррогатных материалов. Это на самом деле выгодно для индустрии композитов, потому что суррогаты охватывают материалы, которые в большей степени отражают то, что используется и разрабатывается вне этого проекта:автомобильные органо-листы и подготовленные для аэрокосмической промышленности препреги, экспериментальные эпоксидные смолы, полукристаллические термопласты и рубленые составы препрегов. Таким образом, результаты и выводы относятся ко всем производителям композитов, а не только к тем, кто защищает.
Трек 1. Настой смолы / производство RTM
Пробные разработки на этом треке начались с материалов и процессов автомобильного типа. Детали были изготовлены компанией SGL Composites с использованием литьевого формования смолы под высоким давлением (HP-RTM, 300 бар) и стандартного модуля упругости C T50, не изгибающихся тканей из углеродного волокна 50K (SGL Carbon в Ваккерсдорфе, Германия) в трех конфигурациях:RI-RAPM-009 , RI-RAPM-002, RI-RAPM-003 (рис. 1). Они использовались для определения параметров преформы, необходимых для получения высококачественных готовых деталей. Инфузия с разрывом (компрессионная RTM или C-RTM) была также испытана для RI-RAPM-003 компанией Boeing St. Louis с использованием ее системы PtFS.
Вычислительное моделирование потока использовалось для лучшего понимания того, как вводить эти детали, анализа поведения процесса для оптимизации материалов и параметров процесса, а также для оценки сценариев нагнетания.
Подходы к инструментальной оснастке были оценены в отношении того, как и когда прикладывать натяжение к различным типам геометрии преформ, чтобы минимизировать деформацию волокна. Эти изменения конструкции были подтверждены для измененной геометрии С-канала с последующим анализом компьютерной томографии (КТ). Извлеченные уроки были применены на последующем этапе C&T с переходом на RTM низкого давления (LP-RTM) для снижения затрат.
В ходе этих испытаний детали Pathfinder были обнаружены расслоения на нескольких радиусах глубокой вытяжки. Цоцис считает, что это было вызвано сочетанием недостаточного начального отверждения смолы в инструменте - потому что система парового нагрева SGL ограничивала температуру в инструменте до 130 ° C - и термических / механических напряжений вне плоскости во время снятия детали. «Поскольку прочность смолы еще не была достаточно развита, эти аномалии, вероятно, можно было бы устранить с помощью полного отверждения инструмента», - предполагает он. «SGL не смогла удовлетворить оба раза по инструменту и «Аэрокосмические свойства до тех пор, пока к инструменту не будет добавлен нагрев масла (по сравнению только с паром), что обеспечит отверждение при температуре выше 130 ° C», - отмечает Хан. Это было добавлено после производственных испытаний.
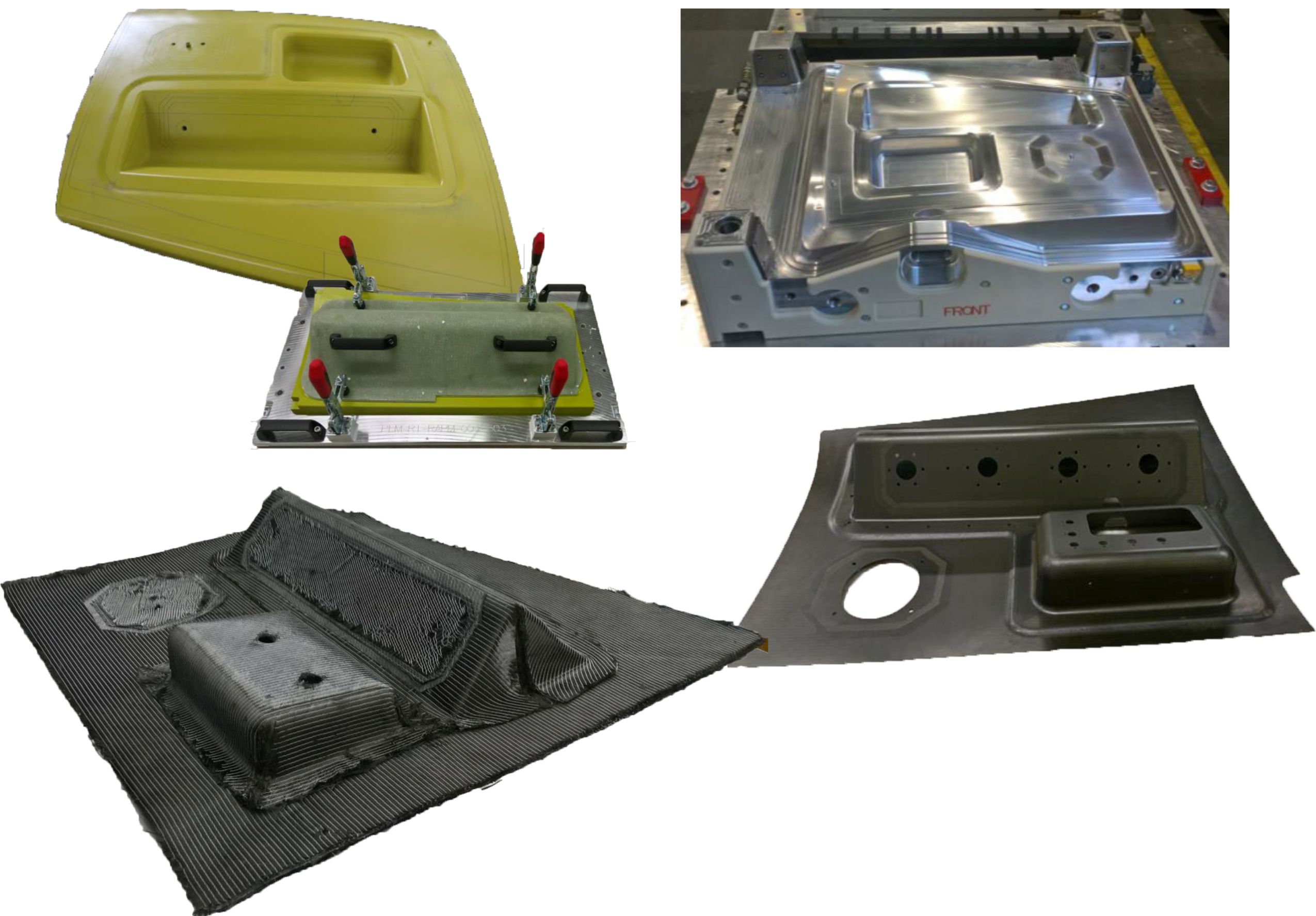
Задание по глубокой вытяжке
Затем результаты испытаний по развитию производства были использованы для разработки испытаний на соответствие требованиям и переходного периода. Также было завершено моделирование детали для сложной вытяжки RI-RAPM-004 (рис. 3), которая имеет две глубокие вытяжки:5-сантиметровую прямоугольную область и 10-сантиметровую область, которая переходит от прямоугольной к V-образной. Вдохновленный сборкой производственного поддона, его сложная геометрия обеспечивала неравномерный путь потока смолы. Хантсман (Базель, Швейцария) выполнил моделирование потока с помощью программного обеспечения PAM RTM (ESI Group, Париж, Франция) для процесса LP-RTM с использованием двухкомпонентной эпоксидной смолы FAF2 (Huntsman, The Woodlands, Техас, США) и SGL Carbon NCF 150 -грамм на квадратный метр двухосного и 190 грамм на квадратный метр однонаправленного армирования.
RI-RAPM-004 содержит одну преформу для обшивки, по одной для каждой секции глубокой вытяжки, а также две зоны наращивания (рис. 3). Для этих элементов преформы использовались различные варианты компоновки, чтобы соответствовать проектной толщине панели (см. « Производство деталей сложной геометрии из RAPM ”).
«Предварительное формование под низким давлением и LP-RTM позволило использовать рентабельные инструменты (по сравнению со сталью):инструмент для преформ с ручными зажимами был изготовлен из материала Raku-Tool на основе полиуретана (RAMPF Tooling Solutions, Grafenberg, Германия); инструмент для отверждения был изготовлен из алюминия 5083.
Первоначальные испытания RI-RAPM-004 показали неожиданную аномалию в потоке около выхода, которая подняла поверхностные слои, вызывая деформацию волокна. Поменяв местами впуск и выпуск, проблема решена. После инфузии и первоначального отверждения в инструменте 130 ° C детали были подвергнуты дополнительному отверждению при 180 ° C в течение 60 минут, а затем обработаны для придания чистой формы. В компанию Boeing было доставлено десять высококачественных деталей для автоматизированной ультразвуковой системы (AUSS) C-сканирования.
Готовые детали для испытаний показали полное уплотнение, отличное выравнивание волокон и хорошее качество. Детали показали температуру стеклования 197 ° C и объемную долю волокна (FVF) 49,5%, типичную для используемого NCF. Количество деталей при укладке сократилось более чем на две трети по сравнению с текущим процессом изготовления препрега, а трудозатраты упали примерно на 90%. RAPM также сделал сложную часть с помощью смол и тканей, пригодных для аэрокосмической промышленности - для проверки адаптируемости разработанных инструментов и процессов - и изготовленных деталей, которые прошли производственные требования для неразрушающего контроля (NDT).
Дорожка 2:формирование препрега TS

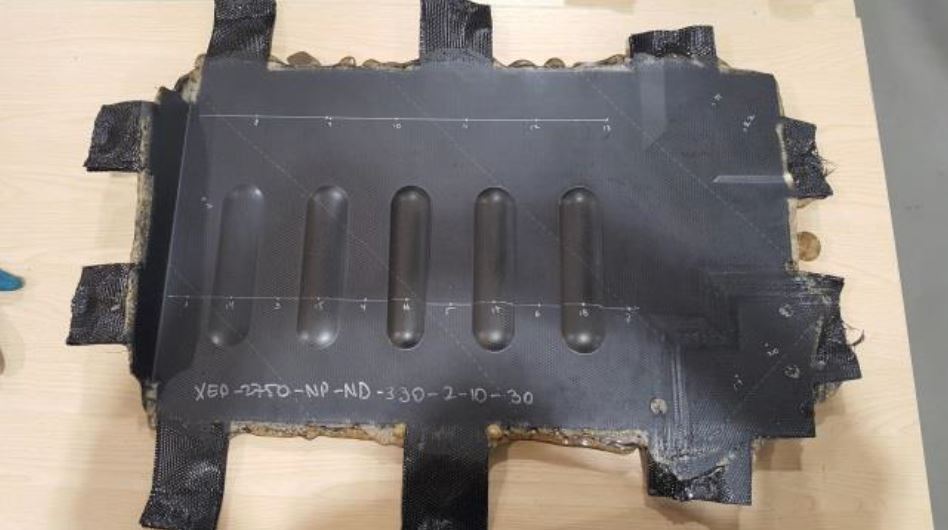
Три опытных детали из термореактивного препрега (TS) были изготовлены в Центре приложений Solvay в Хеаноре, Великобритания, с использованием штамповки пружинной рамы и / или формовки двойной диафрагмы (DDF). Все три детали были изготовлены с использованием эпоксидных препрегов на основе смол Solvay, включая CYCOM 5320-1, CYCOM 970 и аэрокосмическую систему CYCOM EP-2750. «CYCOM 5320-1 - это наш лучший выбор для деталей вне автоклава (OOA), но он также используется в качестве квалифицированной системы для автоклава», - говорит Хан. «CYCOM 970 - это вариант растворителя по сравнению с термоплавким препрегом, а [CYCOM] EP-2750 - наша система для штамповки, потому что она оптимизирована с учетом физики и кинетики процесса, который, как мы показали, дает лучшие детали».
Штамповка пружинной рамы и DDF - это процессы изотермического формования под давлением, в которых термореактивные препреги разрезаются, объединяются и объединяются в двухмерную преформу. Затем преформу предварительно нагревают, перемещают в соответствующие металлические инструменты и формуют в обычном гидравлическом плиточном прессе. Преформа может удерживаться в напряжении с помощью пружинной рамы (рис. 4), что снижает образование складок, вызванное зонами сжатия материала во время формования. В качестве альтернативы DDF помещает преформу между двумя диафрагмами, что устраняет необходимость в очистке формы и ее снятии. Заготовка прикреплена лентой к одной из диафрагм, по существу удерживая ее в напряжении, хотя и не так прямо или адаптируется как с пружинной рамой. В RAPM тип пружины, ее расположение и натяжение были оптимизированы для каждой детали с помощью моделирования, как и пружинная рама. Например, в панели с бортиком TS-RAPM-009 используется рама, которая может приводиться в действие вверх и вниз, чтобы адаптировать формирование заряда параллельно с закрытием пресса.
RAPM минимизировал время наработки детали на инструмент за счет удаления деталей со стабильными размерами после 15-30-минутного начального отверждения и последующего периодического пост-отверждения для увеличения скорости обработки. Семейства деталей также были исследованы с использованием одного набора инструментов - например, С-образного канала с тремя различными углами фланца по длине крыла - для максимального использования ячеек. Другие цели, которыми руководствуется подход RAPM TS, включают:
- Автоматическая подборка и формирование для минимизации ручного труда.
- Аэрокосмические механические характеристики при температуре отверждения 177 ° C.
- Стальная оснастка, рассчитанная на> 1000 деталей на набор инструментов.
Часть задачи "Развитие" до "волны"
Были сформированы экспериментальные детали производства термореактивного препрега, индексируя одну переменную за раз, до тех пор, пока не было достигнуто достаточное качество детали. Были оценены такие переменные, как скорость закрытия пресса, положение закрытия и давление закрытия, с целью консолидации материала в правильной точке на реологической кривой для создания внутреннего гидростатического давления, минимизации утечки смолы и предотвращения слишком большого продвижения отверждения, чтобы избежать трещин. индукция. После того, как параметры формования были установлены, было изготовлено от трех до пяти деталей для проверки повторяемости процесса и затем проверено качество. Панели с бусами показали пористость <0,5% из-за высокого давления консолидации (20,7 бар). Также были изготовлены повторяющиеся высококачественные ребра.
Затем извлеченные уроки были применены к гофрированной «волновой» детали TS-RAPM-012, чтобы продемонстрировать компрессионное формование толстых (номинальная толщина 6,3 мм) ламината UD форм с малым радиусом (12,7 мм) кривизны. Чтобы соответствовать требованиям, в детали использовалась квазиизотропная укладка ленты UD из углеродного волокна с промежуточным модулем (IM7; Hexcel; Стэмфорд, Коннектикут, США). Наружные слои из стекловолокна стиля 108 и углеродного волокна со стандартным модулем упругости Solvay THORNEL T650 в атласной ткани с 8 жгутами защищают волокна UD и предотвращают гальваническую коррозию на той стороне, которая соприкасается с металлической деталью. Использование эпоксидной смолы Solvay CYCOM 5320-1 позволило сократить продолжительность (≤ 30 минут) циклов изотермического отверждения с 2-часовым постотверждением в автономном режиме при 177 ° C.
Деталь для испытания на волну была отлита с использованием рабочей ячейки Boeing PtFS и стальных поверхностей пресс-формы P20 со встроенными вакуумными и полимерными уплотнениями. Полость инструмента была тоньше номинальной толщины ламината, чтобы учесть изменение содержания смолы в материале, поддерживая внутреннее гидростатическое давление для высококачественных деталей.
Были испытаны три параметра процесса, включая холодное формование (предварительное формование слоев без нагрева), предварительное горячее удаление массы и предварительный нагрев преформы. Холодное формование было отвергнуто как трудоемкое и бесполезное. Для предварительного уплотнения ламинаты помещали в вакуумный мешок на пластину с тканевым сапуном из стекловолокна и очищали от массы при полном вакууме в печи при 116 ° C в течение 40 минут. Хотя автоматический инфракрасный предварительный нагрев является стандартным для промышленного производства, в этих испытаниях предварительный нагрев заключался в помещении преформы в горячую форму (179 ° C) и максимально возможном закрытии без касания в течение 3 минут. Затем деталь была отформована под давлением.
8-е испытание из девяти завершенных (№0-8) показало детали самого высокого качества, главным образом, благодаря предварительной консолидации. Образцы, взятые из него, соответствовали толщине (проблема с другими деталями) и качеству ламината с объемом волокна 59-63% и содержанием пустот 0-0,6%.
Дорожка 3:ребро TP и С-образный канал в форме мочевого пузыря
RAPM выбрала ребро TP-RAPM-002 из опытно-промышленных испытаний, чтобы продемонстрировать одноступенчатое прессование от сырья до готовой сложной детали, и изогнутый канал TP-RAPM-003 для двухэтапного подхода. Компания Boeing St. Louis отлила ребро -002 с помощью пресса Accudyne Systems (Делавэр, США) и консолидировала заготовки для С-образного канала -003 с помощью оборудования PtFS. На втором этапе компания ATC Manufacturing штамповала заготовки с каналом C на детали.
Для ребра -002 RAPM использовала ленту UD шириной 12 дюймов, поставляемую Solvay:углеродное волокно 12K AS4D (Hexcel, Стэмфорд, Коннектикут, США), армированное полиэфиркетонкетоном (PEKK). В С-образном канале -003 использовалась ткань от Cramer Fabrics Inc. (Довер, Нью-Хэмпшир, США):углеродное волокно без заданного размера 3K AS4 (Hexcel) в сарже 2x2 с порошковым покрытием из полиэфирэфиркетона (PEEK); поверхностная масса волокна 250 грамм / квадратный метр; содержание смолы составляет 42%.
Проблемы с формованием термопласта
Композиты TP обрабатываются при более высоких температурах, чем термореактивные, например, 390 ° C для PEEK и 375 ° C для PEKK, что создает ряд проблем. Инструментальные материалы, которые могут выдерживать такие высокие температуры процесса, ограничены. Кроме того, большая разница температур между обработкой детали и удалением затрудняет поддержание постоянной температуры инструмента. Решением является нагревание и / или более медленное нарастание и замедление, что увеличивает продолжительность цикла.
Высокие температуры также создают проблему с коэффициентом теплового расширения (КТР). CTE инструментального материала часто отличается от CTE слоистого материала TP, что может вызвать сжатие слоистого материала TP от инструмента, уменьшая прикладываемое давление и предотвращая полное уплотнение. Кроме того, КТР слоистого материала TP постоянен вдоль углеродного волокна, но имеет двилинейную кривую, перпендикулярную волокну. Это приводит к разной усадке в плоскости и вне плоскости по мере того, как ламинат TP нагревается и охлаждается, и это также следует учитывать при проектировании инструментов.
Ламинат TP также может давать усадку от инструмента, поскольку объем смолы уменьшается при переходе от жидкого к твердому. Именно во время этой фазы охлаждения, когда происходит критическая кристаллизация матрицы смолы, требуется точный контроль однородности температуры и давления ламината для обеспечения высококачественных свойств готовой детали.
Другая проблема заключается в том, что инструменты должны быть полностью герметизированы, чтобы удерживать расплавленную жидкость TP во время формования. «Герметизировать инструмент при температуре от 375 ° C до 390 ° C сложно, так как очень мало подходящих прокладок, которые могут выдерживать эту температуру и Давление формования TP составляет от 300 до 500 фунтов на квадратный дюйм или выше », - говорит Хан. «Мы ограничены либо металлическими прокладками, либо подходящей металлической оснасткой для обеспечения уплотняющих свойств. Эластомерная оснастка была бы невероятно полезной, однако все существующие эластомеры будут разрушаться при температурах формования TP ».
Boeing St. Louis требовалось новое оборудование для создания горизонтального давления на вертикальные элементы выступа во время уплотнения в гидравлическом прессе, который приводился в действие только вертикально. Его решением был тонкий алюминиевый баллон (аналогичная система использовалась при формировании TP-RAPM-003, рис. 5). Под давлением инертного газообразного аргона при высоких температурах баллон расширился, чтобы обеспечить равномерное давление на все поверхности детали во время уплотнения.
Верхний и нижний инструменты были изготовлены из нержавеющей стали 410, что соответствовало КТР в плоскости углеродного волокна UD / ламината PEKK. Во время цикла прессования верхний инструмент с алюминиевым баллоном опускался и медленно вдавливал укладку в гнездовую полость нижнего инструмента. Баллон был уменьшен на 30% по сравнению с толщиной конечной детали, чтобы вместить большую часть рыхлой ленточной заготовки в этом одноэтапном процессе. Этот инструмент был установлен в обычном прессе с электронагревательными патронами, подключенными к 12 независимо контролируемым зонам - плюс шесть основных зон плиты пресса - для контроля температуры поверхности инструмента во фланцах и стенке выступа.
Эти испытания формовки позволили получить композитные детали с удовлетворительными результатами NDI. Однако конструкция баллонного инструмента требует доработки, чтобы улучшить формование укладки в узкие внутренние радиусы детали, а также для поддержания равномерной толщины поверхности.
Объединение заготовок из ткани PEEK
Для изогнутого С-образного канала TP-RAPM-003 использованная саржа PEEK 2x2 с порошковым покрытием имела относительно высокий объемный коэффициент. Boeing St. Louis first consolidated the layup, which dropped from 32 to 24 plies along the length of the part, into a flat blank with a tapered cross-section, and then sent the blanks to ATC Manufacturing, which stamped the final part with vertical flanges.
As with the rib, Boeing used a forming bladder and steel top and bottom tools. The bladder was changed to AZ31 magnesium, which better resists rupture versus aluminum. The C-channel tool was designed to operate within the Surface Generation PtFS forming cell to enable more rapid heating and cooling versus the conventional press with cartridge heaters used for the rib.
The C-channel tooling approach was developed to increase flexibility for multiple parts. The layup was placed onto the bottom tool, which was heated to the material’s glass transition temperature (Tg ) to maintain pliability without melting. A volume reducing frame that included a pressure-sealing gasket was placed on top of the bottom tool, leaving a cavity slightly larger than the part layup (Fig. 5). Heat and hydraulic pressure were applied from the top tool through the bladder to the layup. Once at forming temperature, argon gas was applied to the bladder, forcing it down into the frame cavity to apply pressure to the tapered blank. The tool temperature was then increased through the melt phase of the material while maintaining bladder pressure, which prevented material from flowing across the lower tool while in melt phase.
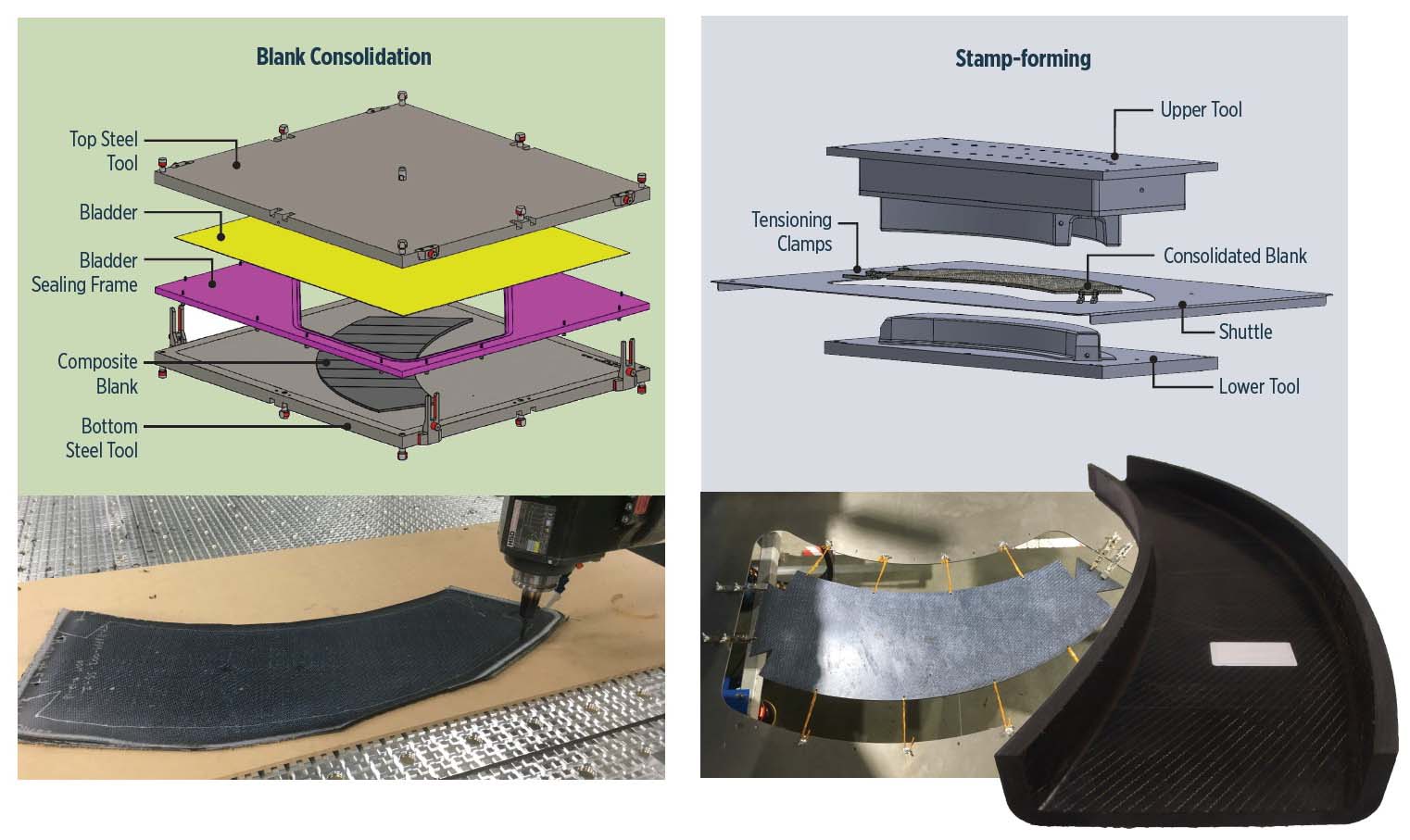
Preforming cycle time comprised 55 minutes for bladder and TP charge to reach process temperature and 30 minutes to cool below the PEEK crystallization temperature. Pressure ranged from 1.4 to 9.7 bar and was maintained manually from a high-pressure tank with a valve. With the recent incorporation of a pressclave system into the PtFS cell, autoclave-like control of vacuum and pressure (±3 psi) in the press mold cavity will be automated in the future.
TP stamp-forming
Consolidated blanks for the -003 C-channel were sent to ATC Manufacturing for stamp-forming, in which the blank is heated sufficiently above melt temperature to ensure polymer flow. It was then transferred to a rapidly closing press to form and cool the part quickly. The forming tool in the press is kept at constant temperature, enabling rapid cycle times by eliminating ramp-up and cool-down. The tool temperature must be between melt temperature and Tg to develop the required level of thermoplastic matrix crystallinity in a short time, yet ensure the part can be removed without deformation. A series of blanks with implanted thermocouples was used to validate the complete thermal cycle for stamp-forming the C-channel.
Forming simulations using Aniform software (Enschede, Netherlands) showed the highly drapable PEEK fabric blank still posed a risk of wrinkling in compression areas, namely the inner (smaller radius) flange. Thus, a tensioning system (Fig. 5) comprising shuttle plate and clips held the blank in tension as the matched metal tools closed to form it. Despite this, the flange face in compression still showed buckling as fiber was pushed inward at the inner radius. “All three RAPM tracks struggled to make this part,” Hahn contends. “Its geometry was extreme, and not so indicative of a real part, but more designed to push what we could achieve in formability.”
The manufacturing development trials led to challenge and transition parts that included multiple versions of the TP-RAPM-008 skin access panel, the TP-RAPM-013 rib with joggles on the flanges and a bladder study using three different geometries of the TP-RAPM-017 panel (Fig. 2). Boeing St. Louis produced all of these except for the TP-RAPM-013 rib, which ATC produced. “Even though this part was made with UD tape, which is typically more challenging to form versus fabric, we were able to form these parts very well,” says Trevor McCrae, R&D director for ATC Manufacturing. Overall, the TP forming trials showed that stamp-forming can produce complex geometries that might not be possible with conventional compression molding.
Learning to cut cost vs. aluminum
RAPM has demonstrated novel forming capability in all three tracks and amassed numerous lessons learned, ranging from how to position pad-ups to prevent slippage during compression molding to guidelines for part geometry to maximize quality and minimize tooling cost. “Understanding the effects of out-of-plane features, radius-to-thickness ratio and distance between geometric details becomes key as you move to small parts,” Hahn observes. “Standardizing features such as radii, curves and flange angles can help mitigate cost drivers, for example, reducing tooling costs, the number of forming trials during development and the need for multiple scans during NDI (nondestructive inspection) by enabling a standard AUSS shoe for a family of parts.”
Another cost driver RAPM highlighted was the time-consuming pre-consolidation step during TS prepreg compression molding. “Low-bulk and higher resin content prepregs widen the process window and increase repeatability for high-quality parts,” Hahn explains. “Solvay has developed a patent-pending ‘transformer film’ which can be applied to lower-impregnation prepregs before compression molding as a method of guaranteeing hydrostatic pressure in the mold cavity during consolidation.”
Although RAPM won’t officially end until fall 2020, followed by additional published results, findings so far for selected parts, which are based on real defense programs, show that composites can compete with machined aluminum (Fig. 6). Though the selected resin infusion and TP parts reduce recurring costs — e.g., materials, machine time, etc. calculated over total parts per family assuming non-recurring infrastructure is in place — the TS-RAPM-012 wave assembly actually shows a 7% increase vs. machined aluminum. However, it does achieve desired weight savings, and at a premium that is actually within the margin mandated by Hendrix:“No one is going to pay 2X for the weight savings composites offer; they must cost within 10 percent of aluminum.” However, he does concede, “There are still non-recurring time and cost issues to figure out, such as tooling and the development required to successfully form the shape.”
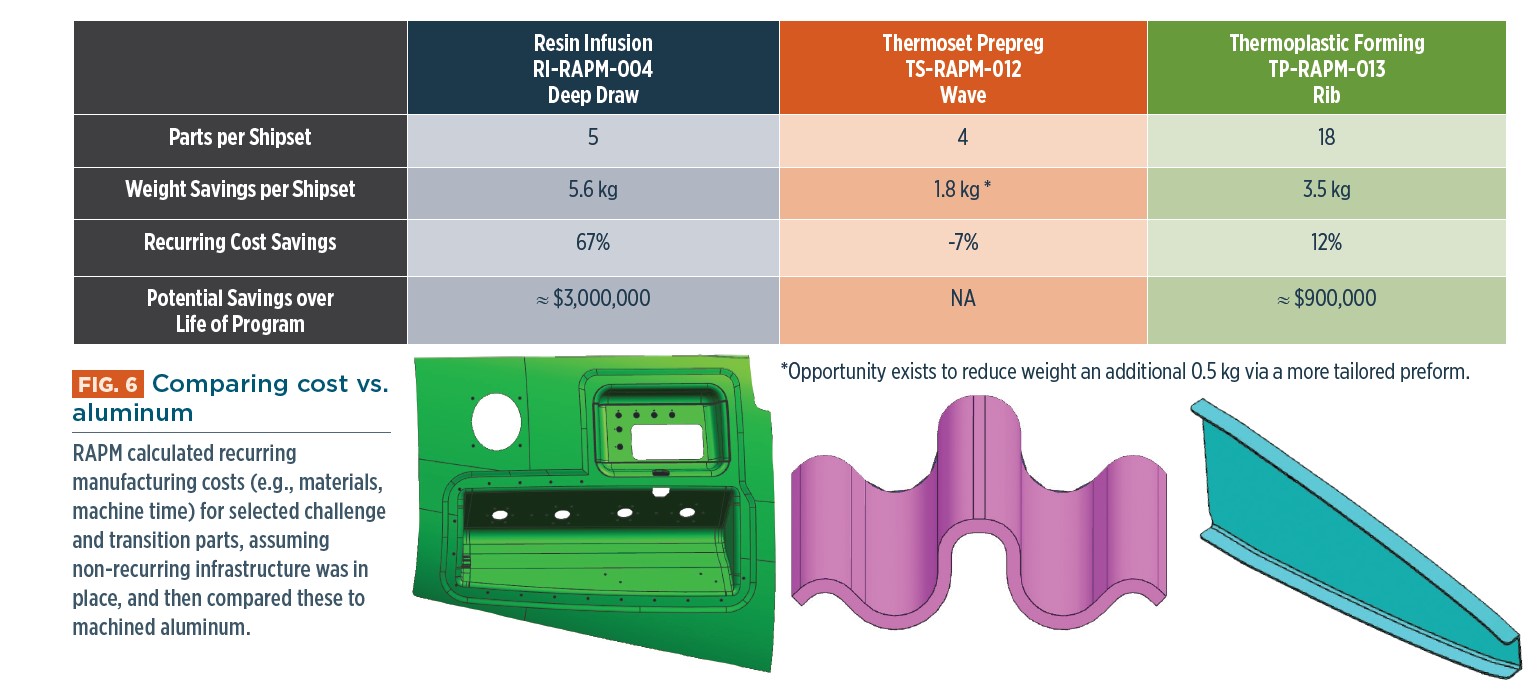
Expanding options
Although resin infusion wins for large parts, says Hahn, TS and TP stamping look pretty good for small parts. “Initial tooling cost for resin infusion is hard to overcome unless the metal parts are very complex, requiring a lot of machining,” she explains.
“Thermoplastics look good for high volume, but a subcontractor for a given program might not be set up to do thermoplastics. However, thermoset stamping might be a very good option, even for low-volume replacement parts. Because defense applications are so wide-ranging, it is important to have more than one material and process in a trade discussion.” Hahn notes that RAPM has opened up new materials and proven aerospace materials can work in automotive-type processes. “We also brought in new manufacturers.”
Hendrix agrees that RAPM’s aerospace and automotive manufacturing exchange was beneficial. Further, he was impressed with Solvay’s and SGL’s ability to form complex shapes without fiber distortion or other defects. “What it takes to make aesthetic auto parts actually has benefits,” he concedes. “You can’t have wrinkles or bad surface finish; they have to be perfect. But it still took multiple trials and significant development for them to form the RAPM parts. I’m not sure defense programs will want to invest in this non-recurring engineering if they’re dealing with small quantities. The economics will be on a case-by-case basis, but tooling and development remain issues we need to address.” Hahn adds, “We are publishing lessons learned, enabling more informed trade studies with expanded options and establishing a reasonably open basis for industry discussion.” CW will continue this discussion with an update once RAPM wraps up later this year.
Смола
- 6 способов снизить стоимость 3D-печати
- Вопрос об обслуживании контракта - Часть I
- Производство композитов:производство композитных материалов
- Экономика 3D-печати
- Прослеживание истории полимерных материалов, часть 13
- Преимущества корпоративной программы поддонов
- ACMA выпускает программу конференции Thermoplastic Composites Conference 2020
- Основной доклад SAMPE 2018 смотрит на будущее композитов
- Стоимость обработки с ЧПУ
- Ценность литья по выплавляемым моделям (часть 2)