Строительство музея будущего
Музей будущего, который в настоящее время строится в Дубае, Объединенные Арабские Эмираты (ОАЭ), является одним из самых сложных когда-либо построенных сооружений. Семь этажей этого 78-метрового здания заключено в торообразную оболочку, которая возвышается на трехэтажном подиуме. Внешний фасад тора состоит из 1024 огнестойких композитных панелей. Каждая панель, облицованная нержавеющей сталью, имеет уникальную трехмерную форму и украшена литой арабской каллиграфией. Плавный шрифт формирует стихи, описывающие видение будущего Дубая Его Высочеством шейхом Мохаммедом бин Рашидом Аль Мактумом, вице-президентом и премьер-министром ОАЭ и правителем Эмирата Дубай. Они также служат окнами здания, пропуская дневной свет через внутреннее пространство без колонн и создавая драматический эффект ночью за счет 14 километров встроенного светодиодного освещения.
Задуманный шейхом Мохаммедом как инкубатор инноваций и изобретений, Музей будущего считается одним из самых современных зданий в мире, местом, где люди могут испытать и исследовать новые технологии. Это также символ архитектуры, которая раздвигает границы с помощью цифрового дизайна и использования более эффективных материалов. Параметрический дизайн был использован для разработки стальной диагробы - каркаса из 2400 диагонально пересекающихся стальных элементов, к которому прикреплены композитные бетонные плиты перекрытия и 17000 квадратных метров композитной облицовки, причем последняя с использованием 1 миллиона квадратных метров многоосного стекла и армированного углеродным волокном. эпоксидный препрег.
Дубайская фирма Affan Innovative Structures предоставила композитный дизайн для панелей, а также изготовление и поддержку для установки. «Такой проект реализуется впервые, - говорит генеральный директор компании д-р Амер Аффан. «И также впервые композитные панели были использованы для интеграции нескольких функций здания с помощью таких сложных форм».
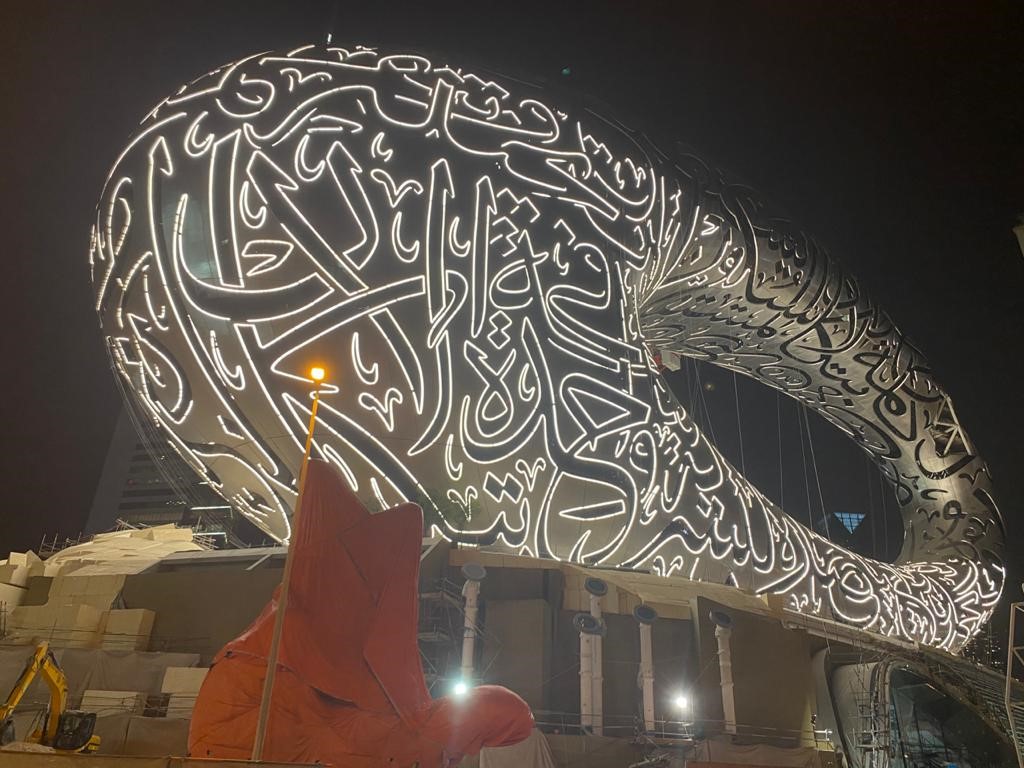
Главный архитектор Шон Килла объясняет, что такие сложные экстерьеры обычно представляют собой экраны от дождя, а позади здания находится система гидроизоляции. «Это упрощает дело, потому что при создании этих очень трехмерных форм проще», - отмечает он. «Однако в этом здании оболочка обеспечивает гидроизоляцию, герметичность, структуру и освещение». Аффан признает, что для такого грандиозного проекта его компания невелика по размеру, «но мы использовали наши технические знания для достижения чего-то уникального и показали, как будут строиться здания в будущем».
Возможность создания сложных цифровых дизайнов
Изначально с Affan Innovative Structures обратилась команда инженеров Музея будущего. «Было не так много компаний, которые могли бы выполнить работы, необходимые для внешней облицовки», - отмечает Аффан. «Единственный другой конкурент предложил обычную навесную стену с панелями из алюминия или нержавеющей стали снаружи». Навесные стены, обычно используемые в дополнение к каркасу из конструкционной стали, тонкие и сделаны из алюминиевых рам, которые поддерживают стеклянные, металлические и / или тонкие каменные внешние панели (см. «Оболочка здания:модульные фасады из стеклопластика»). Команда инженеров отклонила это предложение как слишком сложное и неспособное обеспечить такой же внешний вид, как это было возможно при использовании интегрированного многофункционального фасада из композитных панелей. Таким образом, последний, предложенный Affan Innovative Structures, был выбран для проекта. «У нас также есть уникальная технология, которая позволяет нам изготавливать большие панели, - добавляет Аффан, - до 3 метров в ширину и 9 метров в высоту, изогнутые в обоих направлениях, что означает меньшее количество стыков».
Affan Innovative Structures идеально подошли для этого проекта. Основанная в 2004 году доктором Аффаном, компания предоставляет комплексные решения «под ключ» - от концептуального проектирования до монтажа и обслуживания зданий, - решая самые сложные технические задачи. Резюме компании включает в себя сложный геометрический алюминиевый экран / облицовку стадиона King Abdullah Sports City (Джидда, Саудовская Аравия), композитный навес у входа и 64 стеклянных и стальных окна с замысловатым узором в крыше торгового центра Yas Mall (Абу-Даби, ОАЭ). , наружная композитная крыша для больницы Сидра (Доха, Катар) и многих других сложных проектов. Эта возможность для сложных стальных, стеклянных и композитных сборок была бы именно тем, что было необходимо для многофункционального композитного экстерьера Музея будущего.
«Внутри каждой композитной панели есть система плоских стеклянных [панелей] с арабским шрифтом», - поясняет Аффан. «Стекло почти утоплено внутри панелей на глубину до 200 миллиметров». Это углубление изменяется не только сверху здания, с меньшим углублением для предотвращения захвата воды, к низу, где вертикальные и поднутренные панели могут быть глубоко утоплены, не задерживая воду, но также и внутри каждой панели, наклоняясь и уменьшаясь для получения постепенного, естественного край для сценария. «Расположение и края углубления также менялись в зависимости от расположения стекла внутри панели, потому что стекло было плоским, а панели были изогнутыми», - отмечает Аффан. «Это было возможно только с цифровым дизайном и обработкой с ЧПУ». Такая точность также потребовалась бы для обеспечения того, чтобы сценарий, который менялся от одной панели к другой, выровнялся точно по мере установки панелей, чтобы буквы и слова правильно текли по внешней стороне здания.
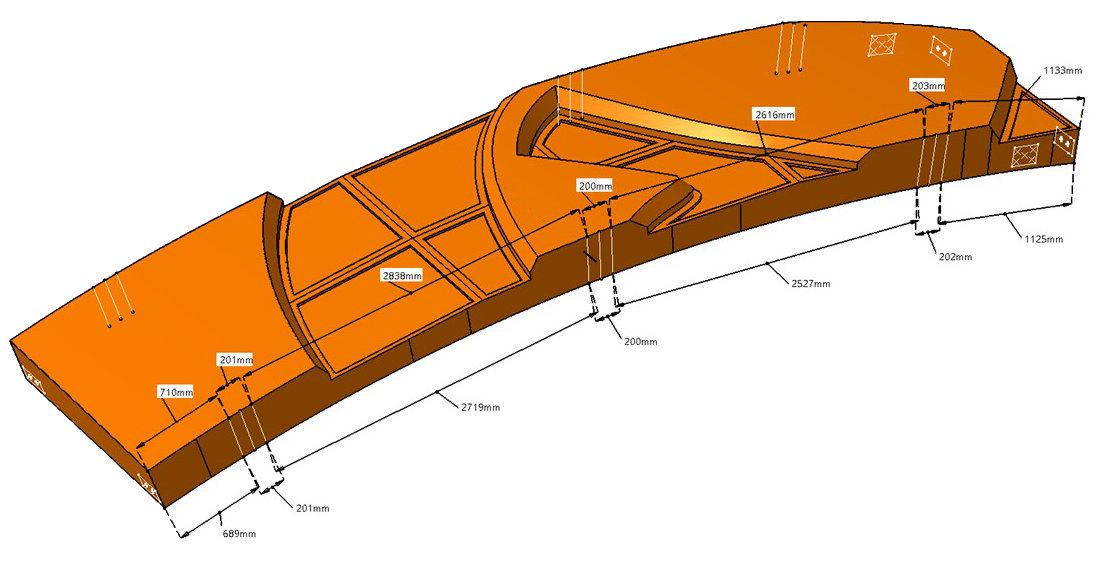
Для Аффана единственным решением было встроить арабский шрифт и углубления в каждую композитную панель. «Усиление будет помещаться в формы, точно обработанные на станке с ЧПУ», - объясняет он. К счастью, программное обеспечение CATIA (Dassault Systèmes, Велизи-Виллакублей, Франция), которое Affan Innovative Solutions использует для управления своими станками с ЧПУ, также является программой 3D CAD, используемой в аэрокосмической промышленности для проектирования сложных самолетов и композитных конструкций. Кроме того, команда Аффана из 28 инженеров также хорошо разбирается в программном обеспечении Tekla BIM, Rhino 3D (Robert McNeel &Assoc., Сиэтл, Вашингтон, США) и AutoCAD от Autodesk. «Мы сделали все чертежи в CATIA, а также разработали дизайн ламината, что дало нам возможность выполнять такую сложную обработку», - говорит Аффан.
Однако конструкция была нетривиальной и должна была выдерживать множество структурных и ветровых нагрузок. Например, внутренняя часть тора создала эффект аэродинамической трубы, объясняет Аффан. Эти панели должны выдерживать нагрузку до 450 кг / м 2 . (92 фунт / фут 2 ) ветровой нагрузки. (Обратите внимание, что в Международном строительном кодексе указаны ветровые нагрузки 71 фунт / фут 2 для районов с высоким риском ураганов в Уэст-Палм-Бич, Флорида, США). Композитные панели для Музея будущего также разработаны с учетом минимального веса. «В панелях используется от 9 до 13 слоев, которые различаются в зависимости от местоположения и нагрузки», - говорит Аффан. Он добавляет, что Центр композитных технологий (Штаде, Германия), дочерняя компания Airbus и давний партнер через торговую организацию CFK Valley ev (Штаде, Германия), «предоставил стороннюю проверку конструкции, прогиба и жесткости нашего ламината. расчеты ».
Еще одна сложность и новшество заключается в том, что панели также имеют собственную систему крепления. «По краям 24 слоя образуют кассетную геометрию крепления для соединения со зданием», - объясняет Аффан. Кассетная система - это метод крепления внешней облицовки, первоначально разработанный для установок типа дождевых экранов. Хотя типы и геометрия различаются, кассеты обычно обеспечивают плоскую водонепроницаемую внешнюю поверхность, которая крепится сзади к несущему каркасу здания. Для фасадных панелей Музея будущего не требовалось отдельных деталей для формирования краев кассет, а вместо этого они были обработаны в каждой форме и, таким образом, интегрированы в каждую композитную панель.
Производство материалов, форм и панелей
Несмотря на то, что на 10 000 квадратных метров производственного пространства композита Affan Innovative Structures есть 16 машин для вливания смолы и восемь столов для вливания смолы со стеклянной столешницей и стальной поверхностью размером 3 на 20 метров, компания решила использовать препрег. Почему? «Для достижения необходимых характеристик огнестойкости требуется много добавок, поэтому смола становится густой и не течет при вливании», - объясняет Аффан. В данном случае добавкой был тригидрат алюминия (ATH, см. «Устойчивость к возгоранию без веса»). Он продолжает:«Таким образом, мы работали с Notus Composites [Рас-Аль-Хайма, ОАЭ], чтобы разработать FR эпоксидный препрег. В основном мы использовали стекловолокно, а также углеродное волокно в некоторых секциях, где были проблемы с прогибом ». Утвержденный гражданской защитой Дубая препрег Notus Composites EPFR-609 в сочетании с поверхностной пленкой NE11-FR соответствует требованиям NFPA 285, EN13051-1 и ASTM E1098 и E84 класса A (см. «Огнестойкие препреги позволяют ... . »И« Лучшая и дешевая проверка строительных материалов из стеклопластика »).
Поскольку внешние металлические поверхности в Дубае летом могут достигать температуры 80 ° C (176 ° F), Аффан объясняет, что «мы отверждали препрег при 120 ° C, чтобы обеспечить достаточную температуру T g . (температура стеклования), чтобы противостоять отклонению головки. Таким образом, формы были изготовлены из пенополиуретана, который мог выдерживать такую высокую температуру, что является более дорогостоящим. Мы пробовали три или четыре разных пенки, но только одну мог выдерживать температуру плюс вакуумное давление, и в то же время был достаточно мягким, чтобы легко и быстро обрабатывать станки с ЧПУ.
Обработка каждой формы с ЧПУ занимала от 12 до 72 часов, и для каждой из 1024 композитных панелей требовалась собственная форма . Все четыре 5-осевых станка с ЧПУ Affan Innovative Structures (Zogno, Италия) - самые большие, размером 33 метра в длину, 13 метров в высоту и 2,5 метра в высоту - были необходимы для удовлетворения высоких требований музея. «Если одна [машина] не работала на техническое обслуживание, другие работали параллельно», - объясняет Аффан.
Слои препрега вырезали и комплектовали, используя (Bulmer , Mehrstetten, Германия) автоматический резак. «Мы не использовали сердцевину в панелях, потому что, в отличие от сегодняшнего дня, в то время не было пенопласта, отвечающего требованиям огнестойкости», - говорит Аффан. Даже с такой автоматизацией персонал компании из 250 сотрудников, общее количество которых достигло к 2015 году, также было необходимо для производства продукции, в среднем четыре панели в день. Команды из шести рабочих, каждая с руководителем и сбалансированным набором навыков, необходимых для эффективной работы, собрали группы. «Обычно над проектом работают две или три команды, - отмечает Аффан, - но для соблюдения этого производственного графика у нас было 20 команд, работающих одновременно».
Этапы производства
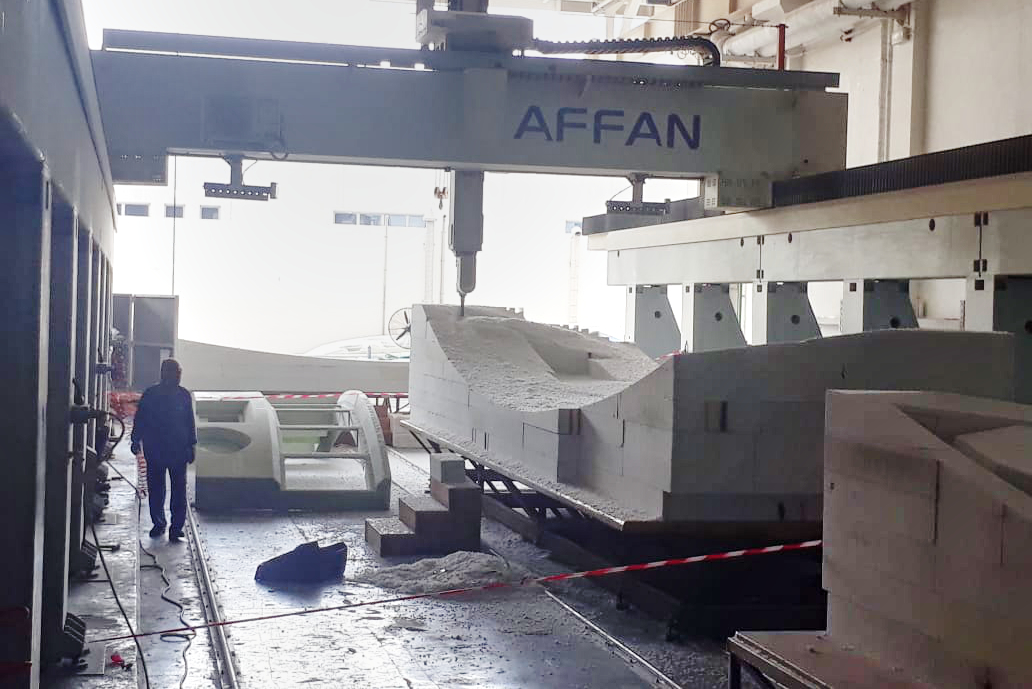
Шаг 1:Пенополиуретан формуют в прецизионные формы. Источник для всех изображений этапов производства | Инновационные решения Affan
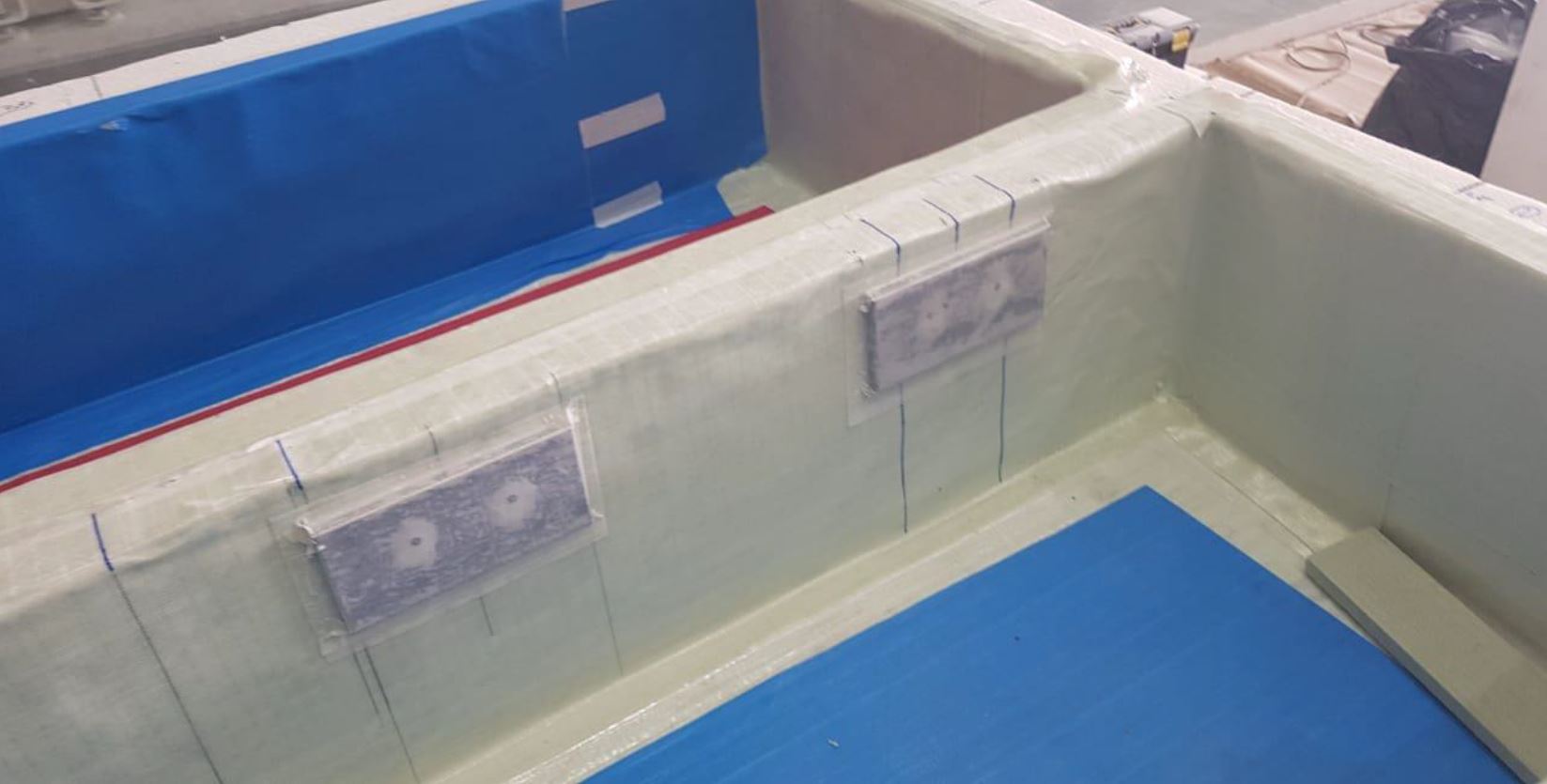
Шаг 2 Стекловолокно / эпоксидный препрег вручную укладывают в формы.
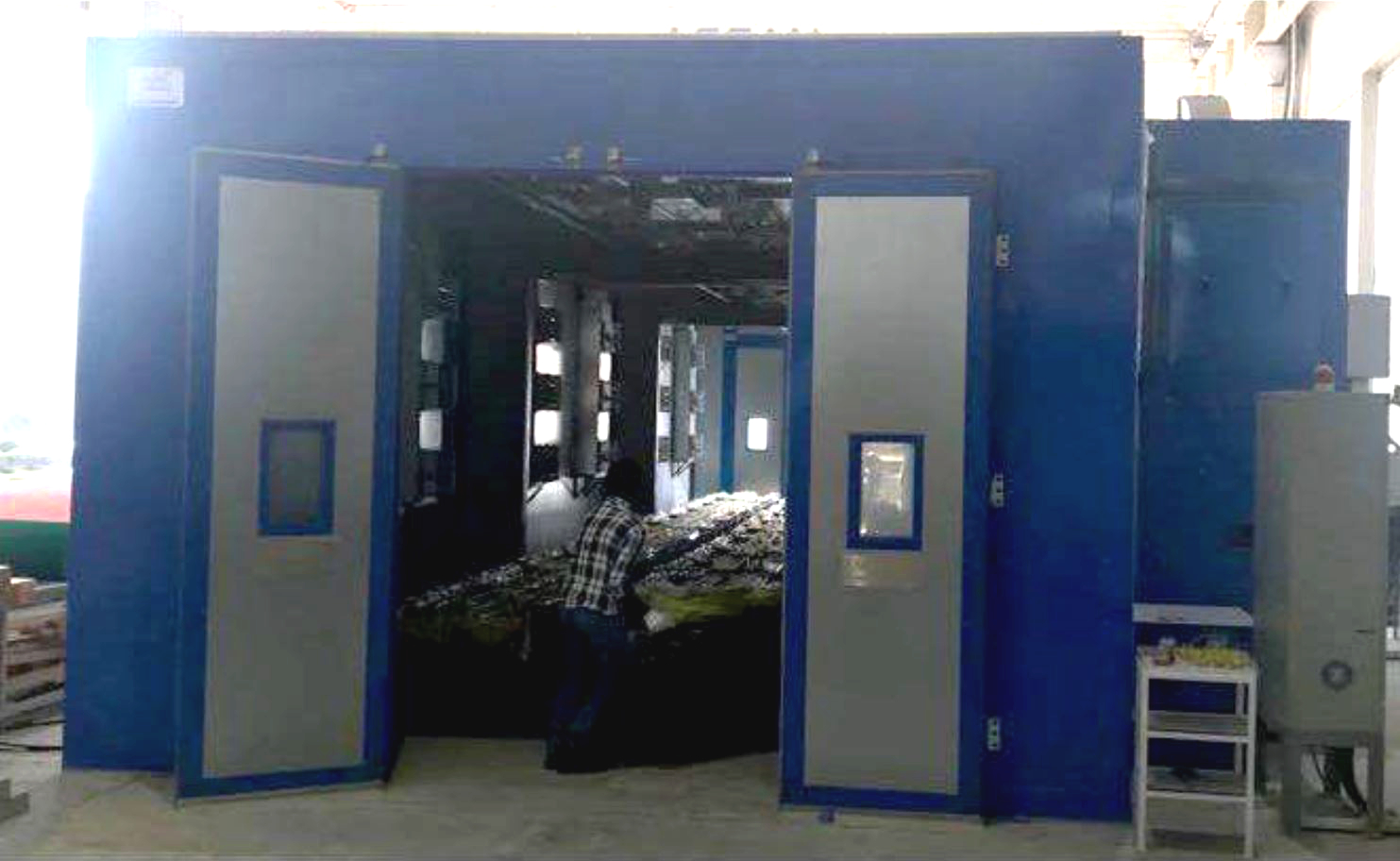
Шаг 3 Слои препрега упаковываются в вакуумный мешок и сушатся в печи в течение 6 часов при 120 ° C.
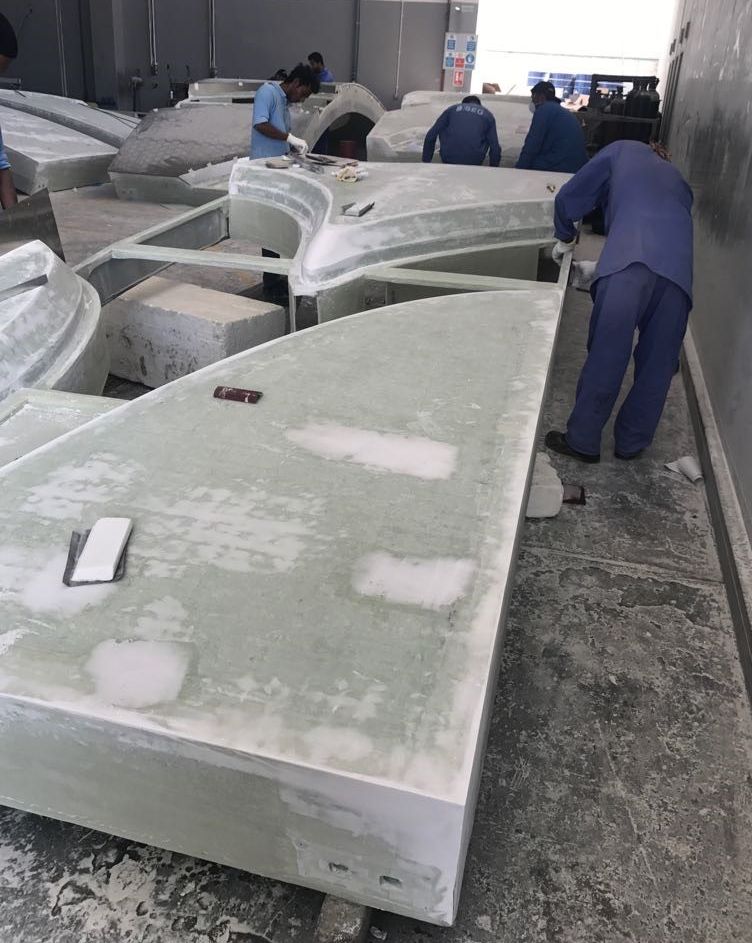
Шаг 4 Сформованные панели подготавливаются для приклеивания отделки из нержавеющей стали.
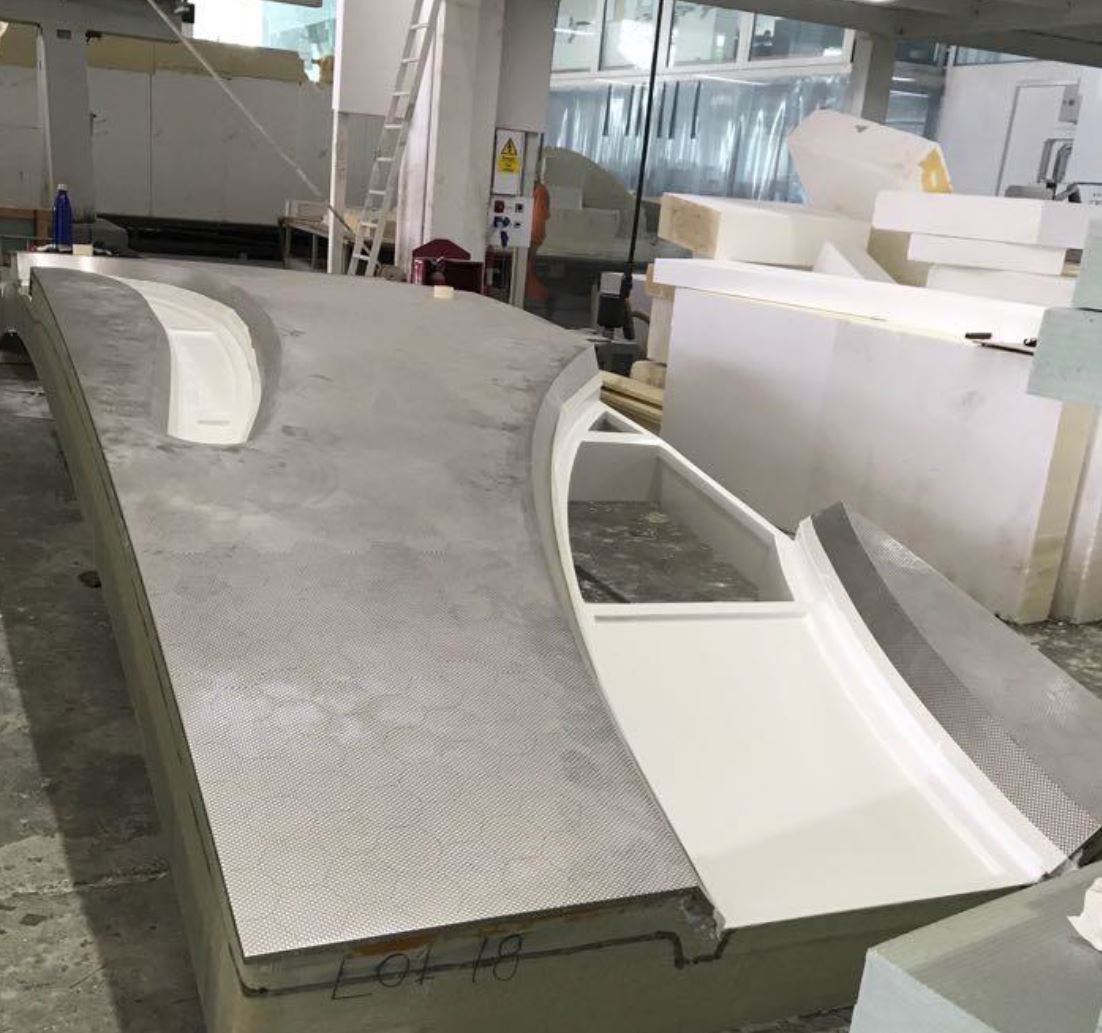
Шаг 5 Шестигранники из нержавеющей стали приклеиваются и механически крепятся к панелям из стеклопластика.
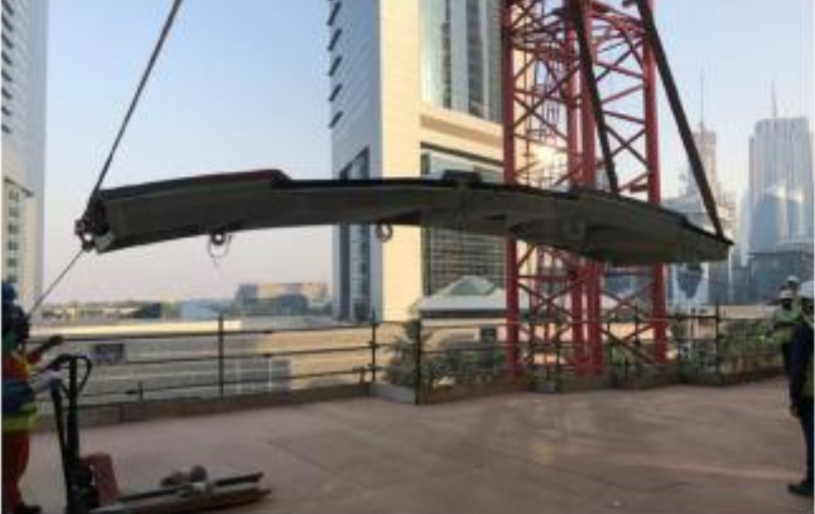
Шаг 6 Готовые панели поднимают для установки.
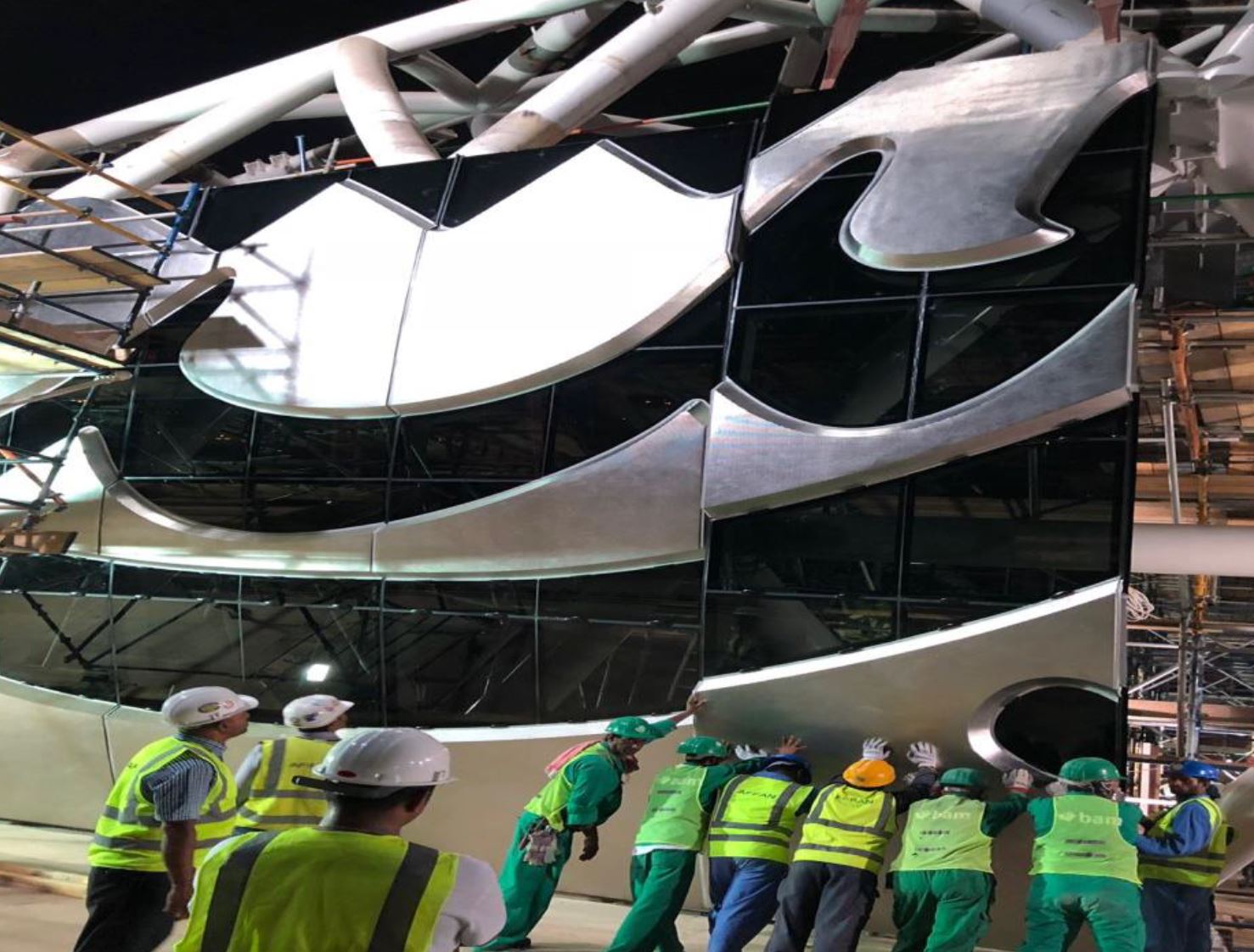
Шаг 7 Каждая панель регулируется с помощью уникального трехмерного «универсального шарнира».
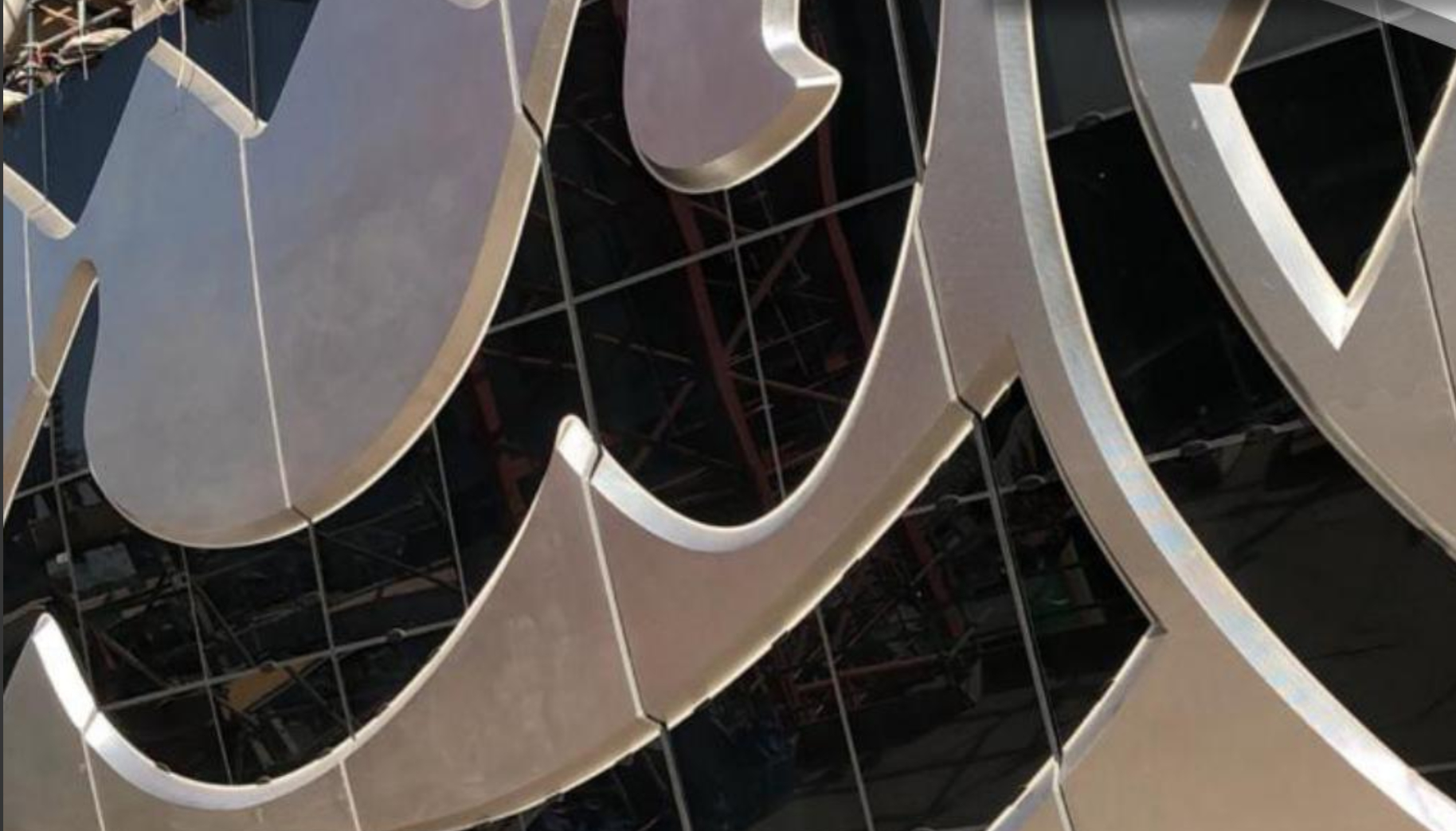
Шаг 8 Каждая панель регулируется с помощью уникального трехмерного «универсального шарнира», чтобы добиться плавного выравнивания внешнего фасада.
Предыдущий СледующийУкладки укладывались вручную, упаковывались в вакуумные пакеты и сушились в течение 6 часов в печах размером 20 метров в длину, 8 метров в ширину и 3 метра в высоту. «У каждого станка с ЧПУ была своя печь», - говорит Аффан. «Мы не собирали вместе много панелей за цикл отверждения. Вместо этого, когда каждая панель была готова, мы немедленно вылечили ее, чтобы поддерживать как можно более высокий производственный поток. Затем мы демонтировали панели и использовали 3D-сканер, чтобы убедиться, что готовая панель соответствует файлу CATIA. Согласно нашей системе тотального контроля качества, нам приходилось сверяться с цифровыми файлами на каждом этапе процесса ».
Готовые панели затем получили внешнюю отделку из нержавеющей стали. «Нержавеющая сталь приклеивается к каждой панели, а затем прикрепляется с помощью механических креплений, что само по себе является искусством», - говорит Аффан. «Металл был разрезан на маленькие шестиугольники, чтобы драпировать поверх 3D-панелей. Гексагональная сетка менялась от части к части в зависимости от величины кривизны. Несмотря на то, что у нас есть опыт и уверенность в склеивании, не может быть риска разрушения единственного шестиугольника в течение всего срока службы здания. Таким образом, необходимо было прикрепить каждый шестигранник, а для одной панели требовалось от 200 до 300 насадок ». Готовые панели были отправлены на место для установки.
Беспроблемная установка с помощью НАСА
Монтаж фактически завершила строительная компания BAM International (Гауда, Нидерланды). «Мы предоставили только супервизоров для установки, чтобы помочь с обращением с панелями», - отмечает Аффан. «Способ подъема каждого из них является ключевым. Панели были спроектированы так, чтобы быть достаточно прочными для каждого конкретного положения в здании. Однако их необходимо поднимать определенным образом, используя как минимум две точки подъема, точно так же, как подвесные кассеты при более традиционных методах строительства ».
Была еще одна проблема, для решения которой Аффан имел уникальную квалификацию. «Чтобы каждая панель располагалась на стальной конструкции и при этом образовывала гладкую поверхность, нам нужна была возможность регулировать панель по глубине, ориентации и кривизне в 3D - другими словами, своего рода универсальный шарнир с тремя степенями свободы. . В 1985 году я работал студентом НАСА в Калифорнии над демпфированием конструкций космической станции. Ключ был в том, чтобы иметь возможность перемещать каждую конструкцию и регулировать ее при стыковке шаттла, чтобы быстро гасить вибрацию, что-то вроде шумоподавления. Я использовал ту же технологию для крепления и регулировки панелей во время установки ».
Кроме того, поскольку панели также обеспечивали водонепроницаемость здания, между ними не могло быть зазоров. «Панели не могли примыкать напрямую, иначе они могли треснуть», - говорит Аффан, объясняя это из-за высокой временной нагрузки в 1,5 тонны на консольную 6 th пол выставочной площади, стальная конструкция действительно движется. «Мы сохранили точно расположенный зазор между панелями, и он был заполнен специальной прокладкой». Эта прокладка, достаточно мягкая, чтобы расширяться, но при этом достаточно жесткая, чтобы выдерживать нагрузку, обеспечивала герметичность, сохраняя эстетичный внешний вид здания.
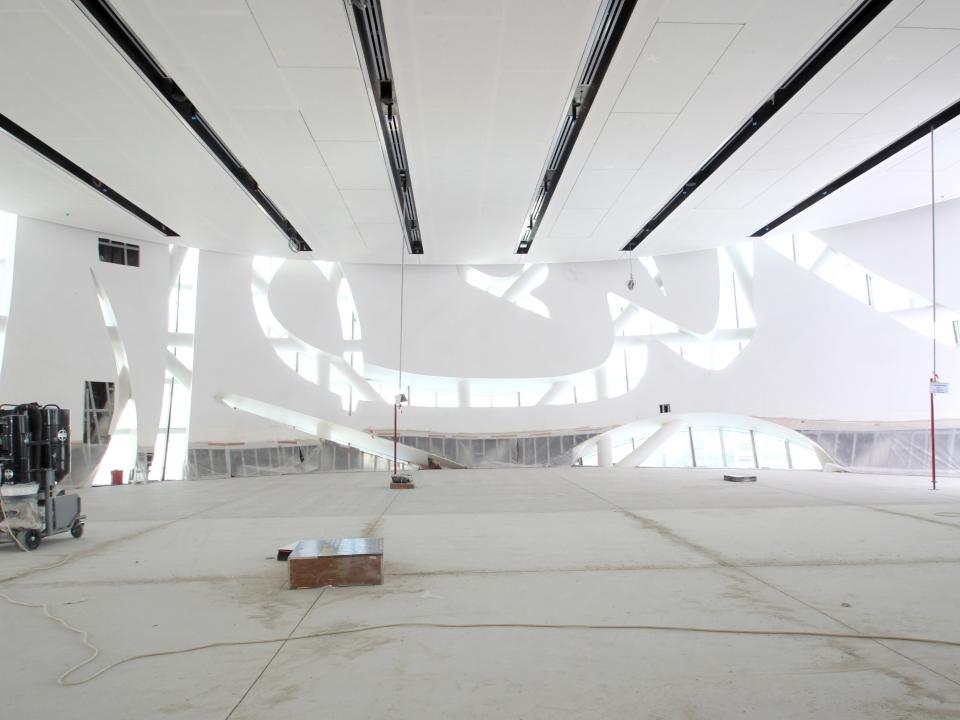
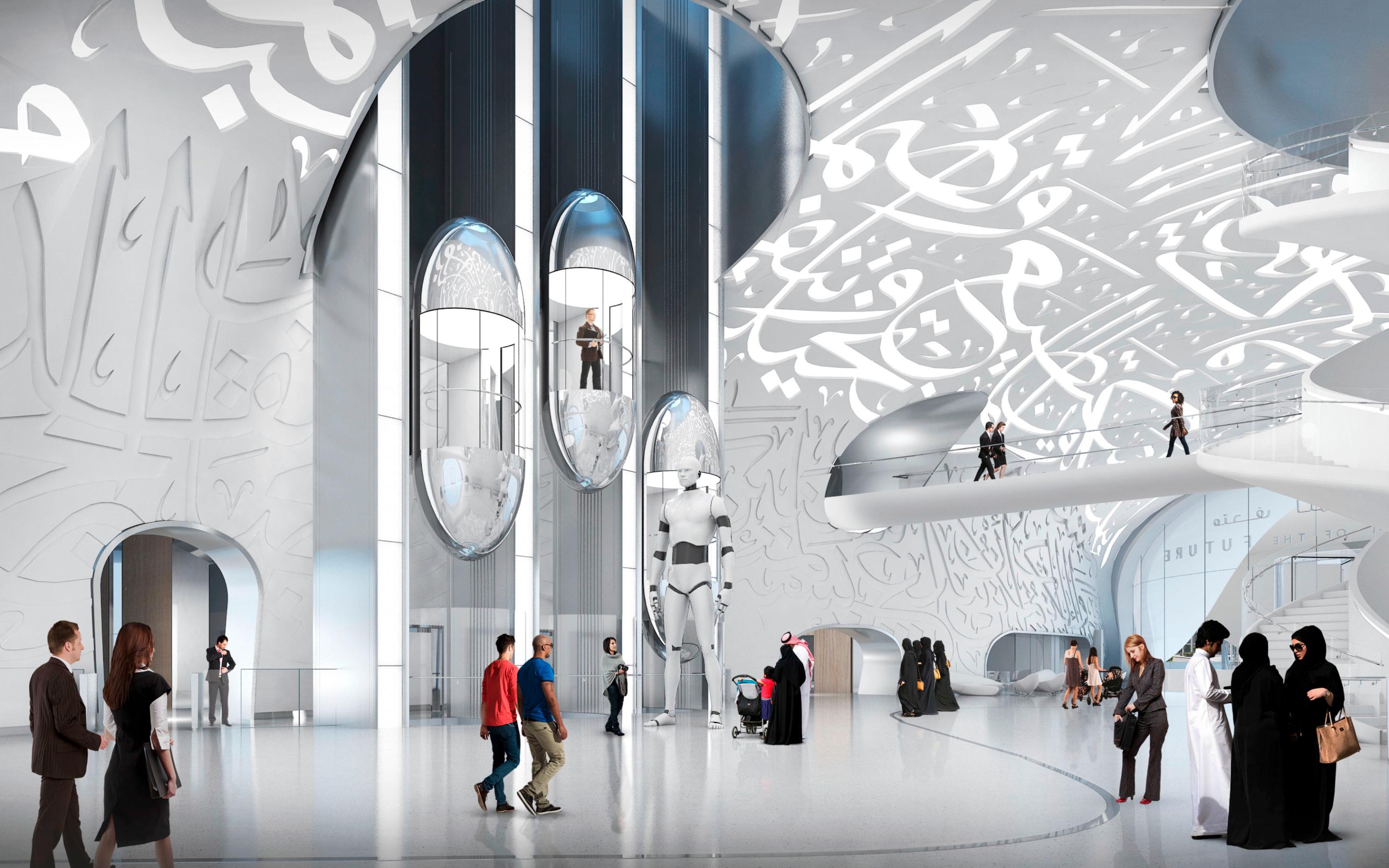
Такие решения являются преимуществом, отмечает Аффан. «Поскольку мы выросли из структур, мы можем комбинировать многие материалы. Это очень важно. Композиты - это лишь один из используемых нами материалов. Это был не просто составной проект ». Результаты говорят сами за себя. «Установка прошла хорошо; никаких проблем не было », - говорит Аффан, который отмечает, что не было никакого способа проверить, подходит ли панель, кроме как убедиться, что она соответствует цифровому файлу. «У нас еще не было панели, которая не подходила бы, имела неправильную форму или слово с орфографической ошибкой», - засвидетельствовал руководитель проекта Buro Happold Баули в статье BBC Элизабет Бейнс.
Модульное строительство будущего
«Мы вместе управляли всем процессом», - добавляет Аффан. «Командная работа внутри самой компании также была ключевой; группы дизайна и компоновки должны были согласовываться друг с другом. Мы никогда не делали такой большой работы, и это было проблемой, но мы любим проблемы ».
К сожалению, COVID-19 взял свое. «Мы закончили эту работу незадолго до закрытия пандемии», - говорит он. «Сейчас у нас осталось менее 30 человек. Это ужасно. Но это коснулось всех, а не только нас ». И все же Аффан видит надежду на будущее и на ту роль, которую композиты будут играть в достижении устойчивости и инноваций, в которых нуждается мир в строительстве. «Люди хотят пробовать новые идеи, особенно в Дубае и странах Персидского залива. Он демонстрирует будущее архитектуры и строительства ».
Он подчеркивает, что это будущее будет для тех, кто сможет использовать модульные системы строительства, «и COVID-19 фактически ускоряет это. Компании будут встраивать модули и отправлять их на сайт. Это будет развиваться, потому что неэффективность перемещается за пределы предприятия на завод, повышая контроль и качество. На месте вы должны координировать всех людей. Это пустая трата времени на ожидание других субподрядчиков. Вы также зависите от погоды и перерывов в работе. Изготовление на фабрике устраняет все это. Поскольку они прочные, легкие и достаточно долговечные, чтобы их можно было легко транспортировать и устанавливать, композиты позволяют использовать этот тип модульной конструкции, и вы можете создавать любые формы, какие захотите ».
Аффан отмечает, что модульная конструкция использовалась на круизных лайнерах в течение многих лет, где каждая каюта предварительно сделана, укомплектована системами отопления / кондиционирования, электрическими и водопроводными системами, а затем собрана в стальной каркас корабля, как блоки LEGO. «Представьте, сколько времени вы сэкономите, если каждый модуль уже оборудован. Сейчас мы рассматриваем проект по возведению таким образом высотного здания из композитных материалов », - говорит он. «Если у вас есть FR-смолы, вам не нужны детали, которые раньше были металлическими». Ссылаясь на отель Marriott, построенный таким образом и завершенный в прошлом году в Нью-Йорке, Аффан добавляет:«Это здание было сделано из стали и дерева, но мы можем построить его из композитных материалов».
Смола
- Облачная безопасность - это будущее кибербезопасности
- Будущее программного обеспечения для нарезки фрагментов
- Периферийные вычисления:архитектура будущего
- Визуализация будущего обслуживания завода
- Будущее центров обработки данных
- Создание более эффективных цепочек поставок на будущее
- Умная автоматизация зданий и будущее застройки в городах
- Создание будущего опыта сотрудников с помощью интеллектуальной автоматизации
- Как Tech Mahindra строит завод будущего
- Будущее 3D-печати в производстве