Коррозионно-стойкие смолы подходят для оборудования нефтехимических заводов из стеклопластика
Композитные материалы известны своей долговечностью в высококоррозионных средах, но для достижения оптимальных характеристик важно выбирать подходящую смолу для каждого применения. Нефтехимический комплекс Petrokemya, дочерняя компания SABIC (Эр-Рияд, Саудовская Аравия), в Джубайле, Саудовская Аравия, производит различные химические исходные вещества, такие как этилен, стирол, хлор, сырой промышленный этанол и многое другое. Для производственного процесса комплекс требовал установки для сжигания с несколькими крупными компонентами и трубами, которые должны выдерживать соляную кислоту без коррозии.
Проектирование и изготовление охлаждающего бака, скруббера, выхлопного бака и связанных с ним сосудов и трубопроводов было поручено группе, в которую входил производитель коррозионно-стойкого оборудования Оллеарис (Мартореллес, Испания), подрядчик China Tianchen Engineering Corp. (TCC, Тяньцзинь, Китай) ) и инженерной фирмой John Zink Hamworthy Combustion (Талса, Оклахома, США). Эти компоненты должны были выдерживать контакт с соляной кислотой, соответствовать ряду конструктивных требований и быть экономически эффективным решением.
Композиты, армированные стекловолокном, были выбраны как материал, способный противостоять высококоррозионным химическим веществам, при этом предлагая более экономичное решение, чем специализированные металлические сплавы. Все основные компоненты были изготовлены из армированного волокном пластика (FRP), за небольшими исключениями, включая подъемные и прижимные проушины (нержавеющая сталь), распылительные форсунки (термопластические или металлические) и набивку скруббера.
Чтобы обеспечить наиболее экономичное решение при соблюдении требований к производительности, Оллеарис обратился к трем смолам Atlac компании AOC (Коллиервилл, Теннесси, США). «Мы выбрали типы смол, используя Руководство AOC по химической стойкости, а также опыт группы технической поддержки AOC с учетом перекачиваемых жидкостей и расчетных температур, указанных клиентом. Было необходимо убедиться, что предлагаемые смолы будут хорошо работать в [требуемых] условиях », - объясняет Адриано Уренья, технический менеджер Ollearis.
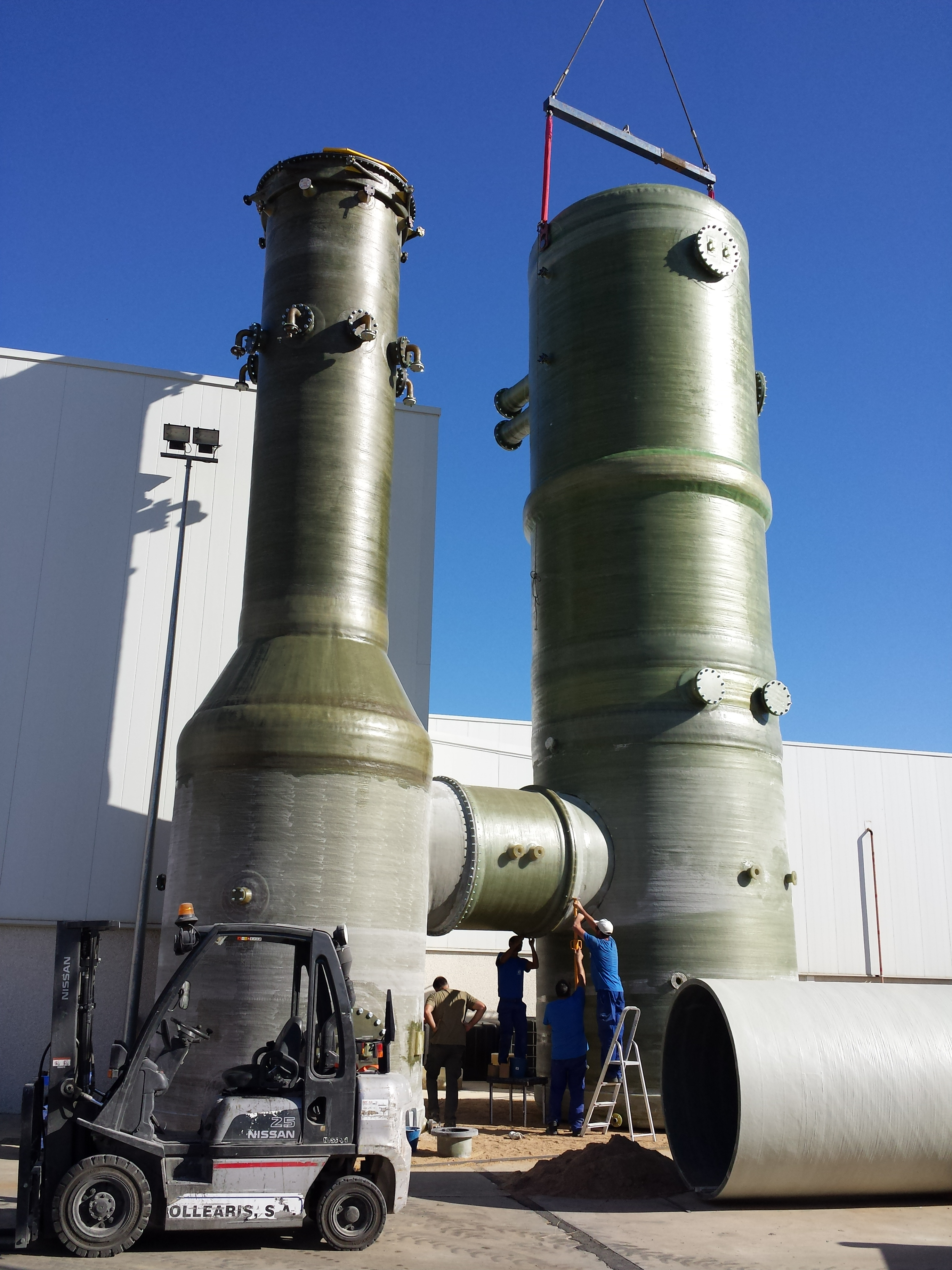
Оллеарис выбрал эпоксидно-новолачную смолу Atlac 590 для закалочного резервуара, который является первым этапом процесса очистки газа. Высота резервуара составляет 11,8 метра, а внутренний диаметр - 3 метра. Проблема заключается в том, что во время работы выхлопной газ из блока сгорания попадает в этот охлаждающий резервуар с температурой примерно 300 ° C, а затем очень быстро охлаждается водой, распыляемой из форсунок рядом с входным отверстием для газа. Atlac 590 был выбран для обеспечения устойчивости к раствору соляной кислоты и сохранения прочности при требуемых повышенных температурах.
Для скруббера высотой 14,10 метра, выхлопной трубы высотой 39,7 метра, из которой выпускается очищенный газ, и канала длиной 1,45 метра, соединяющего скруббер и охлаждающую емкость, была выбрана эпоксидная винилэфирная смола на основе бисфенола А Atlac 430. . Говорят, что это универсальный стандартный продукт, подходящий для сравнительно менее сложных температурных условий для этих компонентов - расчетные температуры скруббера и выхлопной трубы достигают 85 ° C. Скруббер подвергается воздействию раствора соляной кислоты, поступающего из охлаждающего резервуара, а также раствора гидроксида натрия, присутствующего в промывной воде, который используется для нейтрализации кислоты. Выхлопная труба также подвергается воздействию воздуха, содержащего небольшое количество соляной кислоты и влажного хлора.
Для системы трубопроводов, установленных вокруг скруббера и закалочного резервуара, был выбран ненасыщенный бисфенол А из полиэфира Atlac 383 из-за его химической стойкости к кислотам и щелочам при более низкой стоимости, чем у стандартных винилэфирных смол.
Закалочный резервуар, скруббер и цилиндрические части стопки были изготовлены с помощью гибридного производственного процесса, в котором намотка мокрого волокна сочеталась с одновременным нанесением внешнего слоя двунаправленных тканых материалов. Эта комбинация позволила получить детали с лучшими механическими свойствами как в направлении обруча (от намотки нити), так и в осевом направлении (от тканей, которые совпадают с осью детали). Добавление тканого материала также снизило массовую долю стекловолокна на деталь с 70% для полностью намотанной части до 55%. Это увеличивает количество коррозионно-стойкой смолы на деталь. Остальные компоненты были изготовлены вручную.
Решение проблем дизайна
При разработке оборудования для этого проекта Оллеарис столкнулся с несколькими проблемами. Одна из проблем возникла из-за необходимости нанести на внутреннюю поверхность закалочного резервуара пропитанный смолой слой, препятствующий коррозии, что создавало риск образования трещин - или растрескиваний - из-за теплового удара во время работы. Команда улучшила устойчивость компонента к тепловому удару, усилив антикоррозионный барьер с помощью поверхностной вуали из углеродного волокна.
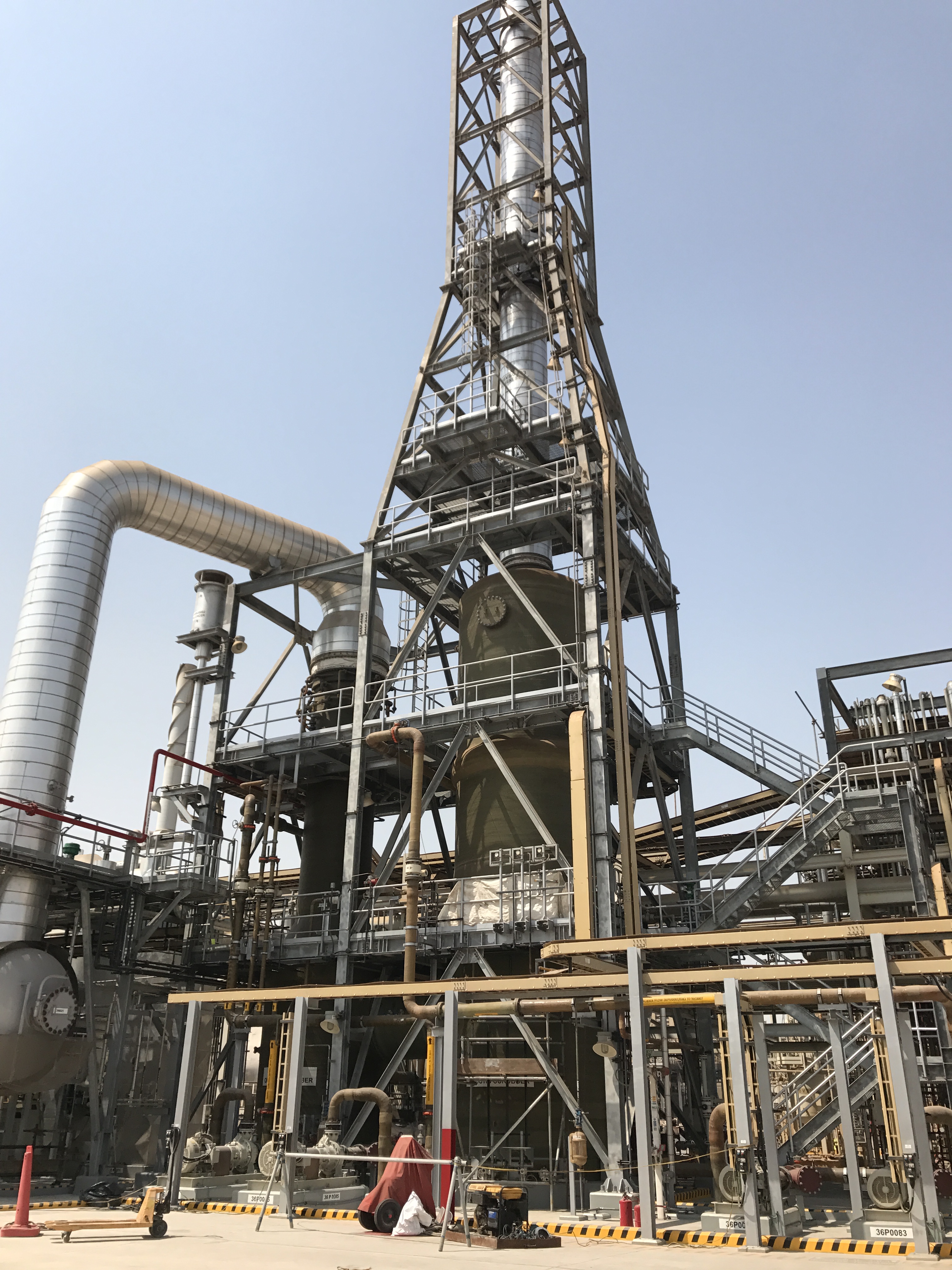
Вторая проблема заключалась в том, что Оллеарису нужно было найти способ выдержать вес набивки внутри скруббера - набивка - это материал, который удаляет газы из воздуха, проходящего через скруббер. Чтобы решить эту проблему, Оллеарис установил композитную решетку под насадкой, поддерживаемую композитным выступом и двумя композитными балками. Выступ и балки имеют полое прямоугольное сечение, выступ заполнен пенополиуретаном. Выступ был изготовлен непосредственно в цилиндрическом скруббере с намотанной нитью как одно целое; склеивание после изготовления могло бы создать риск отслоения из-за нагрузок от веса упаковки. Балки поддерживаются композитными форсунками специальной конструкции, прикрепленными к корпусу скруббера.
Третья проблема проектирования возникла из-за того, что охлаждающий резервуар и скруббер работают под вакуумом, но имеют плоское дно - плоские композитные панели плохо выдерживают давление и вакуум и, как правило, должны быть очень толстыми, чтобы выдерживать такие нагрузки, что делает их производство дорогостоящим. Для достижения целей проекта Оллеарис разработал менее затратное решение, используя многослойную конструкцию, включающую сердцевину из пропитанной смолой трехмерной стекловолоконной ткани, покрытой слоями композитной оболочки, чтобы снизить стоимость и вес твердой композитной детали.
Для этого проекта композитные компоненты были спроектированы и доставлены в 2016 году, а окончательная установка завершена в 2017 году.
Смола
- CRC предлагает руководство по подготовке вашего растения к сезону ураганов
- Как предотвратить дорогостоящие простои из-за отключения электроэнергии на нефтехимических предприятиях
- Время безотказной работы является ключом к производству на заводе American Gypsum
- Дрю Тройер:Общая эффективность оборудования
- Дрю Тройер:Цепочка создания стоимости оборудования, часть 3
- Дрю Тройер:Цепочка создания стоимости оборудования, часть 2
- Дрю Тройер:Цепочка создания стоимости оборудования, часть 1
- Руководство для начинающих по армированным волокном пластикам (FRP)
- Цены на объемные смолы в основном равны или ниже
- Повышение цен на смолы большого объема