Формирование горячего драпирования
Эта онлайн-боковая панель к мартовской статье 2021 года «Продвижение крыла, наполненного OOA» направлена на то, чтобы собрать воедино то, что CW написал о формировании горячей драпировки на протяжении многих лет в одном месте и, надеюсь, предоставил полезный ресурс. Ниже приведены выдержки из нескольких статей - с 2010 по 2020 годы - с фотографиями, которые помогают продемонстрировать, как горячее формование драпировки помогает автоматизировать производство композитов.
2010, GKN Aerospace, лонжероны A400M
Из: «Композитные лонжероны крыла несут огромные турбовинтовые двигатели»
Фил Грейнджер, технический директор и главный технолог GKN Aerospace, объясняет, что сборка такой крупной детали вручную, как это делалось на ранних лонжеронах A400M, происходит медленно, обычно со скоростью сборки 0,75 кг / час (1,5 фунта / час). Однако во время серийного производства деталь будет складываться ровно с использованием автоматической укладки ленты (ATL) с последующим формированием горячего драпирования . в форму C-образного сечения. На этом этапе можно будет достичь скорости укладки 25 кг / час (50 фунтов / час). Грейнджер подчеркивает, что это достижимые средние значения за смену для реальных деталей.
Чтобы автоматизировать этот процесс, GKN Aerospace инвестировала в большой ATL с 20-метровой станиной, производимой MTorres (Наварра, Испания). ATL может укладывать сложные преформы в их разработанные формы из однонаправленного препрега с использованием ленты 977-2 из углеродного волокна / упрочненной эпоксидной смолы, поставляемой Cytec Engineered Materials Ltd. (теперь Solvay, Wrexham, UK). Чтобы сформировать кесарево сечение, преформа будет перемещена из слоя ленты в горячее формовочное устройство . предоставлено производителем оборудования Aeroform Ltd. (Пул, Дорсет, Великобритания). Чтобы облегчить создание вакуума, укладка будет зажата между двумя диафрагмами, сделанными из полиимидной пленки Kapton, поставляемой DuPont Electronic Technologies (Серклвилль, Огайо). Пространство между пленками будет вакуумировано, а затем будет применен инфракрасный нагрев сверху части для повышения температуры до 60 ° C / 140 ° F в течение одного часа. Это гарантирует, что даже материал в центре самого толстого участка у корневого конца равномерно нагревается до той же температуры. Затем будет мягко приложено давление, чтобы сформировать ламинат, ограниченный двумя диафрагмами над легким инструментом, который точно представляет внутреннюю поверхность лонжерона. Этот процесс C-образования достигается очень медленно в течение 20 минут. (После формирования каптоновые пленки выбрасываются.)
2014, FACC, закрылки A321
Источник:«FACC AG:электростанция по производству аэрокомпозитов»
На заводе 3 производится большое количество закрылков, обтекателей и поверхностей управления полетом. Здесь также эффективность автоматизированной укладки ленты (ATL) и горячего формирования драпировки . эксплуатируются. Последний применяет тепло и давление к плоским преформам ATL с помощью сердечника и гибкой формовочной площадки для получения трехмерных форм (см. Рис. 7). Один пример находится в стадии разработки A321 производство лоскутов, в котором используется передовая автоматизированная рабочая ячейка, разработанная по индивидуальному заказу компанией Fill (Гуртен, Австрия).
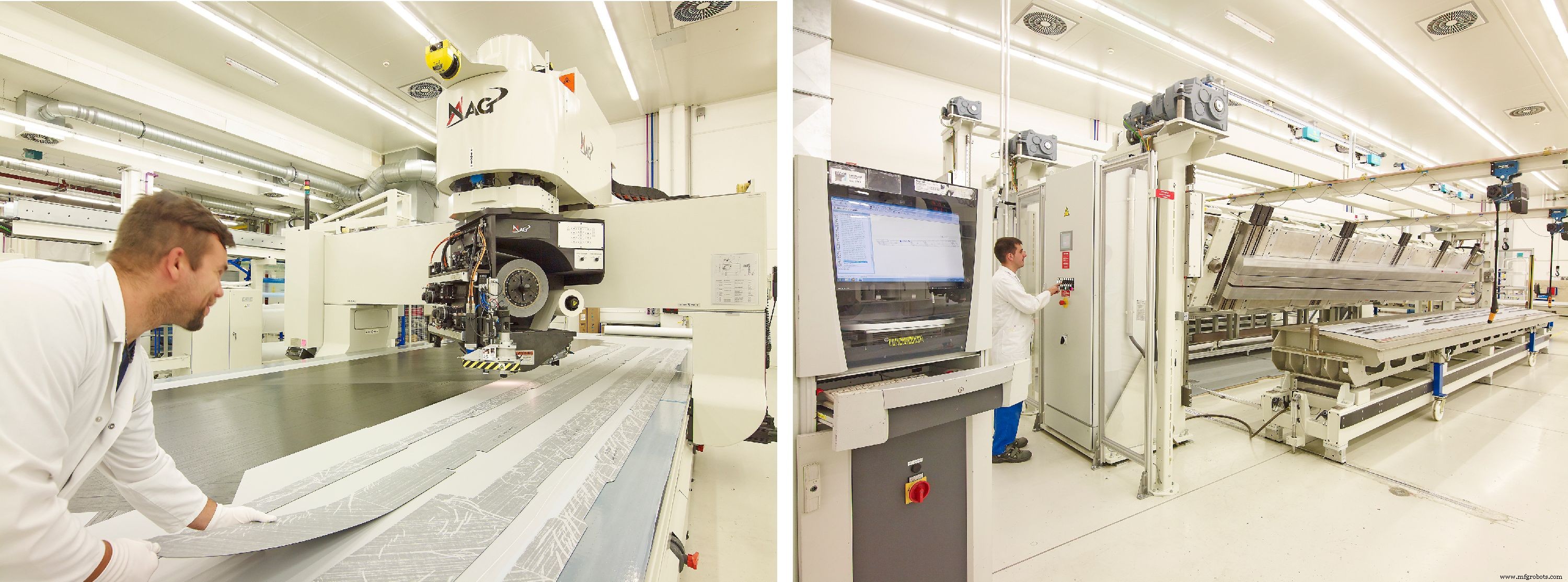
2018 г., розлив, автоматическое формование
Источник:«Автоматическое преформование, часть 7:заполнение Gesellschaft»
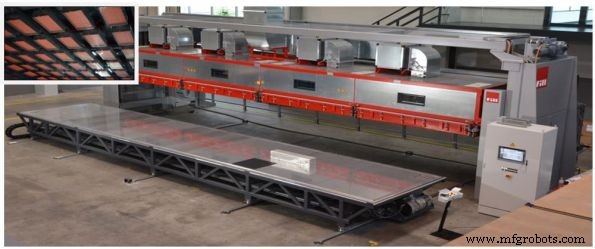
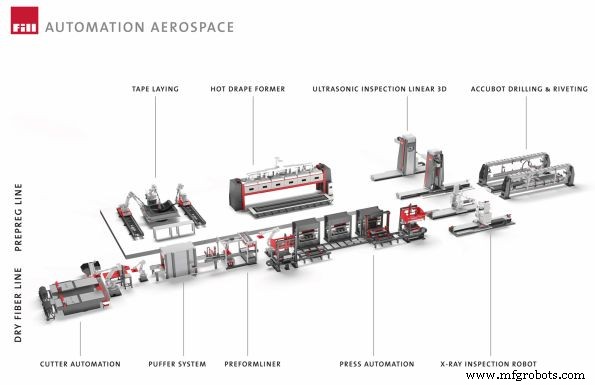
В недавних туристических статьях, которые мы с Сарой Блэк писали о высокоэффективных композитах в Израиле, мы отметили, что большинство компаний использовали горячее формование драпировки . . Фактически, в Elbit Cyclone наш гид Джонатан Хулати заявил:«Я не знаю, как вы делаете этот тип высокопроизводительного производства деталей из препрега без горячего формования», имея в виду балки и стойки для сборок Boeing 787. Горячие драпировщики (HDF) также незаменимы в компаниях FBM и Israel Aerospace Industries.
Fill уже много лет поставляет системы HDF, в том числе несколько единиц, производимых на заводе FACC. В основном это системы вакуумного формования, оснащенные инфракрасными или другими типами нагревательных элементов и многоразовой мембраной из силиконовой резины для нагрева и сжатия - удаления массы - слоев препрега на их инструментах перед отверждением. HDF становится ключевым элементом всей линии производства аэрокомпозитов, показанной ниже.
2018, FBM, 787 частей
Из:«Слияние предпринимательских металлоцентричных фирм делает ставку на композиты»
CW сначала приводят в чистое помещение, где рабочие собирают различные детали. Сегодня на нескольких станциях, каждая из которых оснащена компьютеризированным компьютерным экраном с функцией помощи при укладке, в центре внимания находятся детали для Boeing 787. Простые для понимания сенсорные экраны четко показывают углы укладки для каждого слоя и их расположение. быть размещенным на каждом инструменте. «Гильотинный» станок от Century Design (Сан-Диего, Калифорния, США) с вращающимся столом диаметром 2 м и лезвием ножа в центре позволяет быстро разрезать наклонные слои угольно-эпоксидного препрега. Инструменты для дверных рамок 787 представляют собой фасонные стальные оправки, обычно длиннее ширины, от нескольких сантиметров до ~ 2 м в длину, которые используются для изготовления сотен рам, скоб и зажимов. Автоматизированный планшетный раскройный стол от Assyst-Bullmer Inc. (Уэйкфилд, Великобритания) используется специалистами по укладке для резки до 50 сложенных слоев за одну операцию.
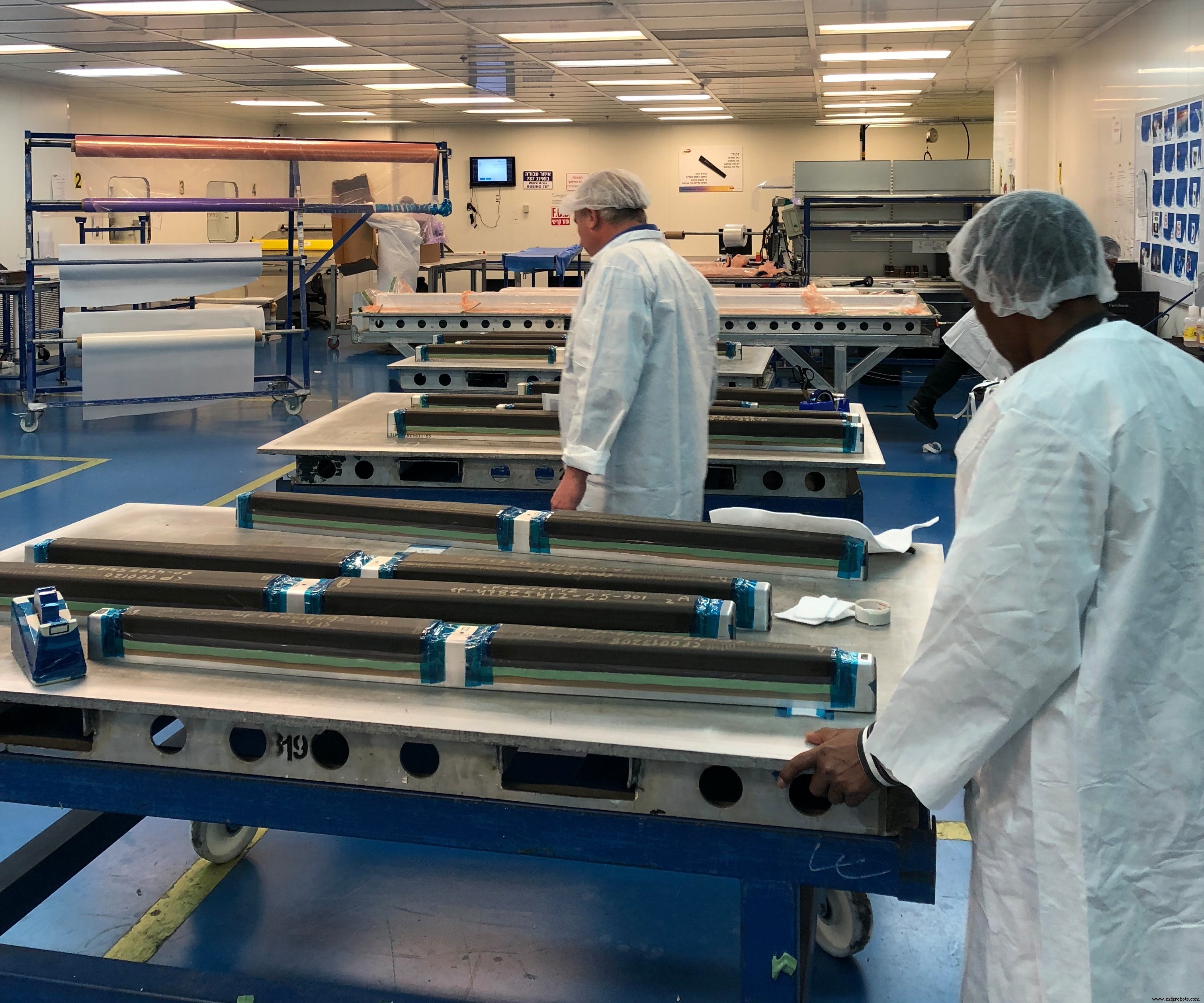
Резка мелких деталей, комплектация и укладка в чистом помещении FBM для самых разных мелких деталей, автоклавированных. Фото: CW , Сара Блэк.
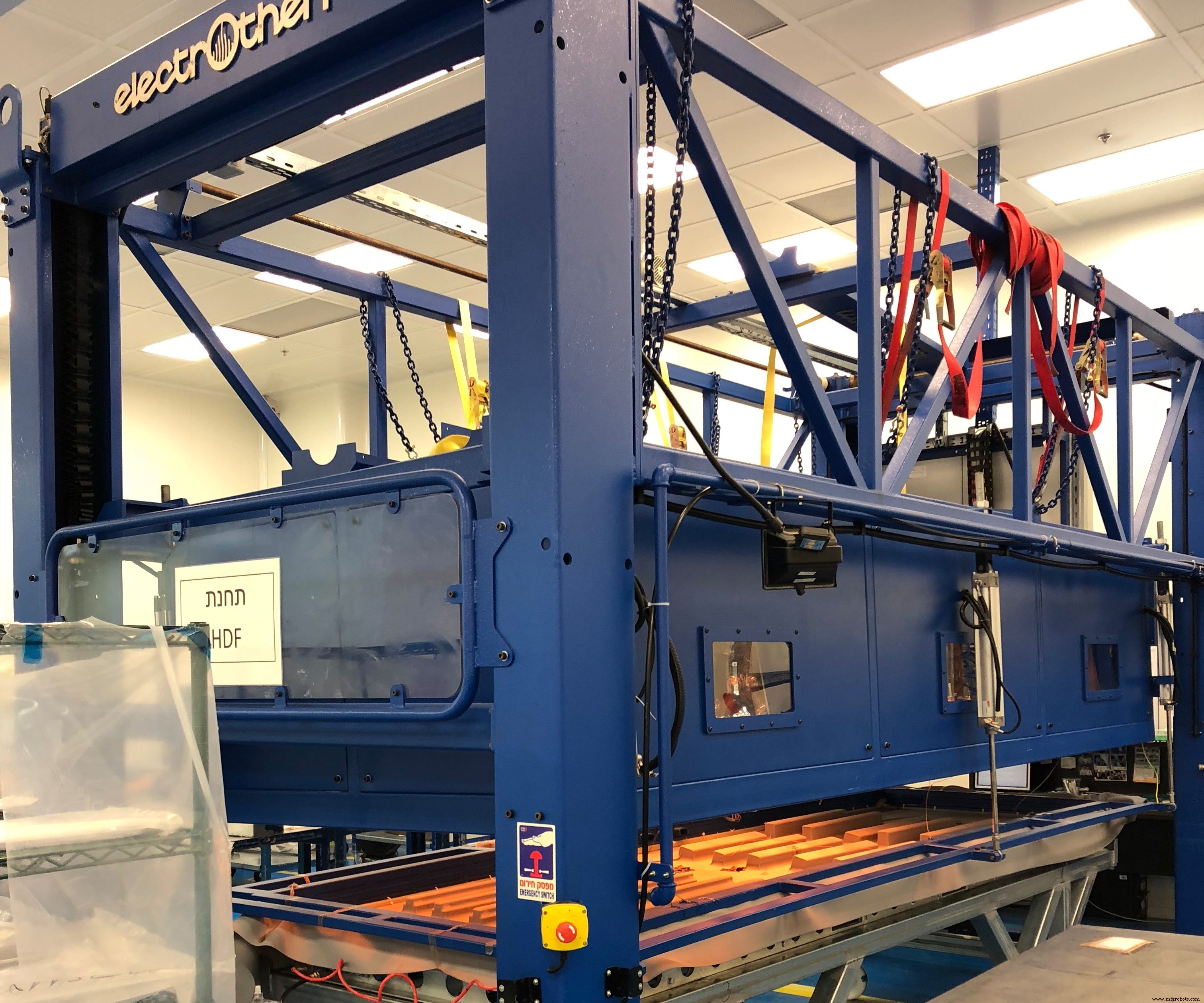
Машина для горячего формования полотна FBM, поставленная израильской компанией Electrotherm Industry, удаляет промежуточные этапы удаления массы, формируя до 50 однонаправленных слоев за один цикл, и ей приписывают ускорение процесса укладки FBM перед отверждением. Фотография: CW , Сара Блэк.
В чистом помещении преобладает горячая формовочная ткань (HDF) . . Изготовленная ElectroTherm Industry (Мигдаль Ха-Эмек, Израиль), статическая машина (компания также производит передвижные версии на тележках) представляет собой индивидуальную вакуумно-формовочную систему, оснащенную инфракрасными нагревательными элементами и мембраной из силиконовой резины для нагрева и сжатия композита. отложений на инструментах перед отверждением. HDF По словам Поликера, можно формировать до 50 слоев, уложенных друг на друга, без промежуточных этапов удаления массы:«Мы стремились устранить сложность процесса, поэтому формируем укладки за один раз». После того, как препрег нагреется и затвердеет в HDF , перед упаковкой в мешки по всей укладке помещается герметик. Изготовлен из композитного углеродного волокна, покрытие имеет шероховатую поверхность. Poliker не раскрывает подробностей о патентованном материале, но заявляет, что он выдерживает температуру отверждения в автоклаве 177 ° C:«Он имитирует инструмент с подобранной головкой». Он добавляет, что инструменты оправки ремонтируются на заводе по мере необходимости. Упаковки и расходные материалы поставляются Airtech International (Хантингтон-Бич, Калифорния, США).
2018, Elbit Cyclone, 787 деталей
Из:«Обслуживание мира композитов в Израиле и США»
Справа рабочие в чистом помещении для деталей Boeing 787 собирают препрег для множества деталей, от небольших зажимов и стоек до сложных J-, двутавровых и C-образных балок, а также многосекционных дверей передней стойки шасси. Препрег разрезается с помощью автоматического резака для ткани Assyst Bullmer (Уэйкфилд, Великобритания) и гильотинного станка для резки толстых стопок под любым углом. Морозильная камера для препрега находится рядом с чистым помещением. Хулати отмечает, что иногда стопки препрега разрезаются, комплектуются и кладутся обратно в морозильную камеру. Лазерные проекционные системы Aligned Vision (Челмсфорд, Массачусетс, США), расположенные по всему чистому помещению, помогают раскладывать руки.
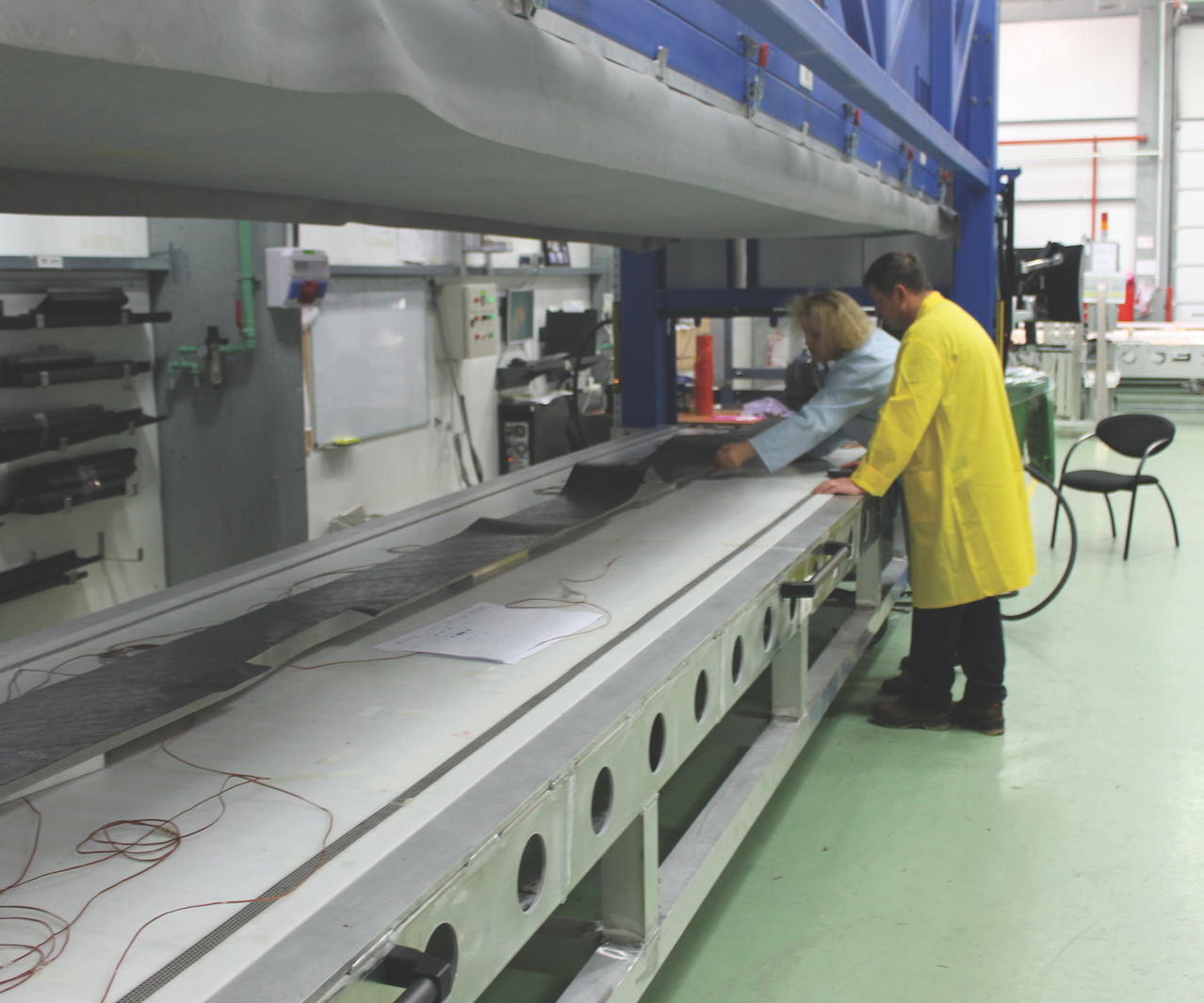
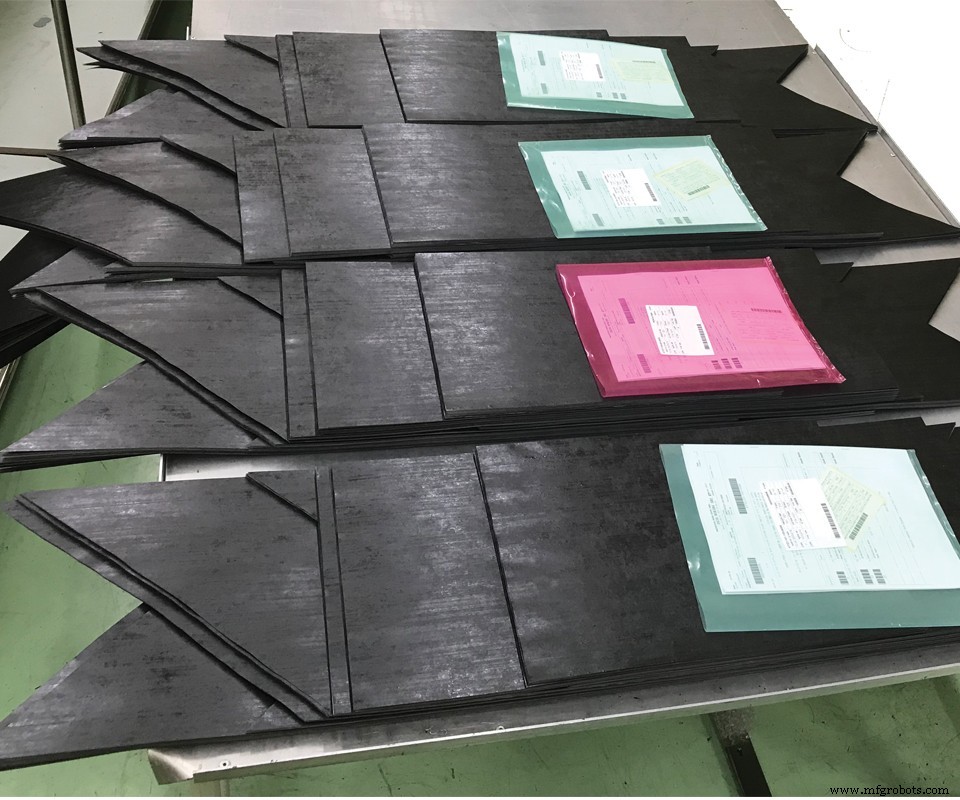
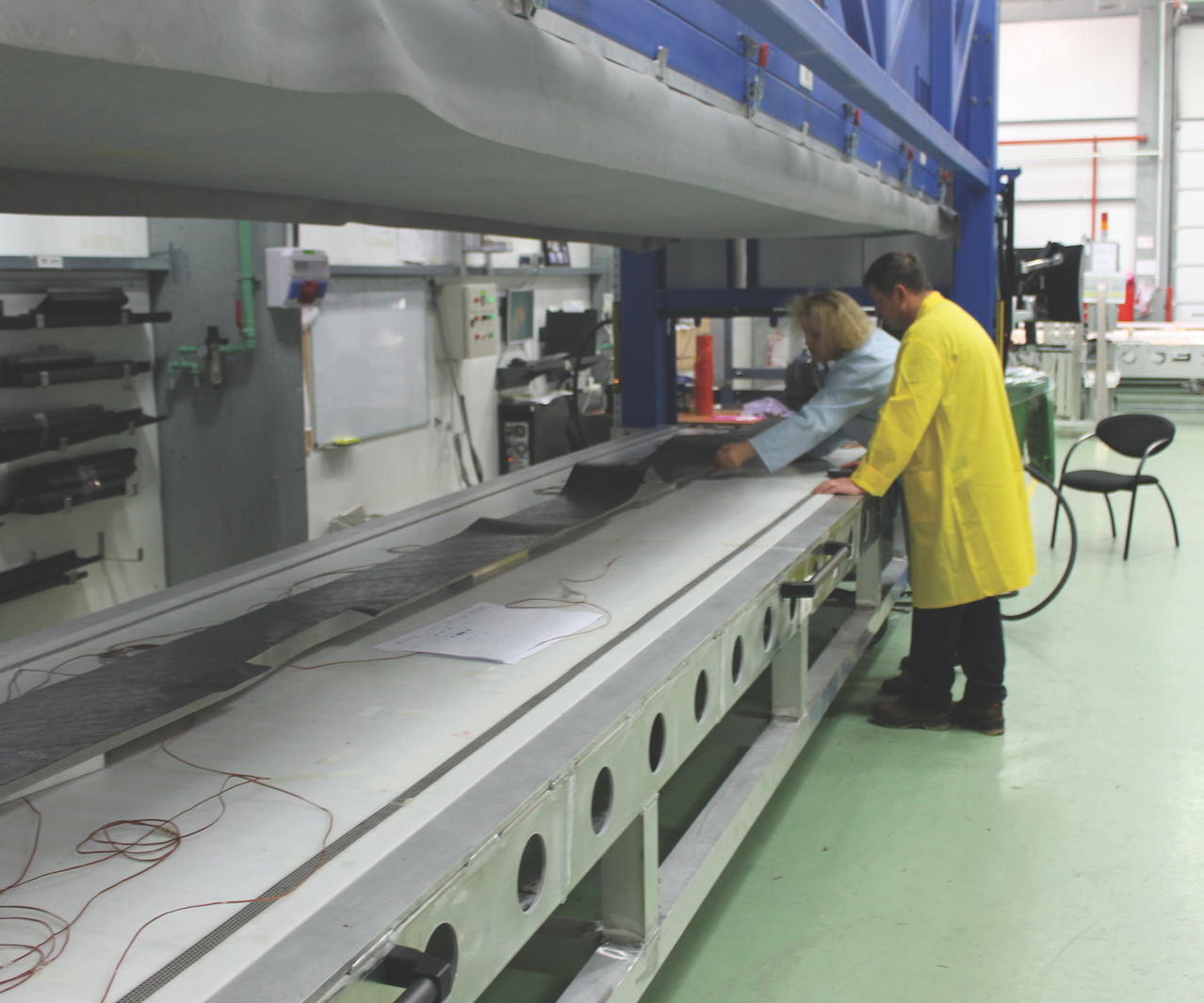
Детали балок перекрытия из армированного углеродным волокном пластика (углепластика) укладываются на металлические оправки с наружной резьбой. Hulaty подробно описывает упрощенный процесс:«Сначала мы складываем стопки препрега, а затем накладываем их на оправку. Это экономит массу времени по сравнению с нанесением на инструмент по частям. Затем укладки покрываются герметиком из углепластика нашей собственной конструкции, что помогает обеспечить 100% повторяемость деталей ».
формирование горячей драпировки Машина расположена вдоль задней стены чистого помещения, что позволяет удалять большое количество деталей за цикл. «Я не знаю, как сделать этот тип высокопроизводительного производства деталей из препрега без горячего формования драпировки», - говорит Хулати, говоря о таких деталях, как балки и стойки. И все же он признает, что ни этот шаг, ни автоклав не являются узким местом. «Узким местом является обработка в конце, после отверждения», - утверждает он, объясняя, что для длинных деталей балок перекрытия быстрее сложить простой штабель и обработать его после отверждения. «Автоклав - не проблема, потому что мы можем складывать много деталей для отверждения за один раз», - добавляет он. «Таким образом, мы действительно получаем хорошую производительность на цикл отверждения».
2018, IAI, авиастроения
Из:«Краеугольный камень воздушной обороны Израиля готов к более широкому охвату мира»
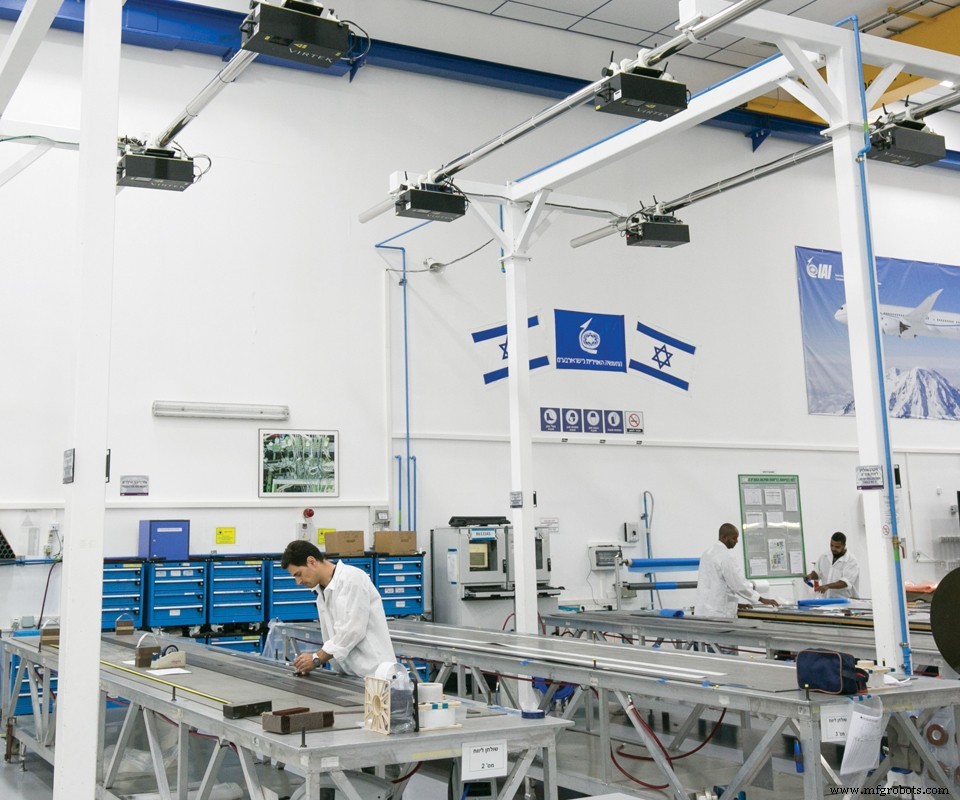
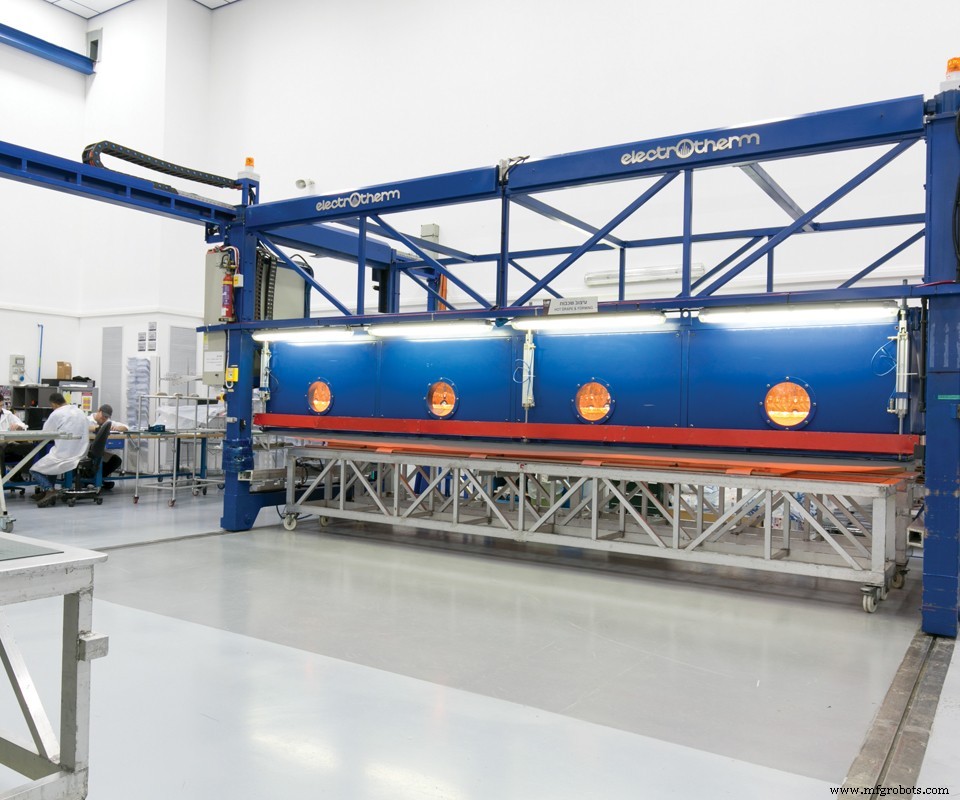
Компания IAI использует машину для горячего формования полотна для массового удаления массы из толстых слоев препрега, устраняя необходимость в традиционных промежуточных этапах удаления массы. Фото:Israel Aerospace Industries
Производство композитных материалов IAI включает изготовление деталей и сборок для бизнес-джетов и коммерческих самолетов, беспилотных летательных аппаратов (БПЛА) и военных самолетов. Производимые детали включают вертикальные и горизонтальные стабилизаторы, рули направления, конструкции крыла, гондолы двигателей, балки пола, обрамления дверей, структурные переборки, нервюры и ребра жесткости, поверхности управления, обтекатели и обтекатели. Среди производственных возможностей компании - ручная укладка препрега и автоматическая укладка ленты (ATL), горячее формование . отверждение в автоклаве и вне автоклава (OOA), включая процессы жидкого формования, такие как инфузия смолы и литье с переносом смолы (RTM), а также сложное соединение и сборку. Компания также разрабатывает и производит собственное оборудование, имеет все основные сертификаты качества в аэрокосмической отрасли и композитных материалах и обеспечивает контроль качества посредством комплексных неразрушающих испытаний и инспекций.
- Производственные мощности IAI значительны:10 автоклавов, семь из которых принадлежат подразделению Aero-assembly Div. и варьируются в размерах от 4,5 м в длину и 2 м в диаметре до самых больших 14 м в длину и 4,7 м в диаметре.
- Накладки препрега удаляются перед отверждением с помощью горячего формирования драпировки . машина (6,9 на 2,7 на 3,1 м) от Electrotherm Industry (Мигдаль Ха-Эмек, Израиль).
2020, Strata, A350-900 внутренние закрылки
Источник:«Strata поставляет 100 комплектов бортовых закрылков для A350-900»
Разработанный для увеличения общей подъемной способности крыла самолета, IBF [внутренний закрылок] устанавливается на задней кромке крыла для увеличения поверхности крыла во время взлета и посадки и повышения устойчивости во время полета. Strata заявляет, что планирует полностью автоматизировать производственный процесс IBF, используя горячее формование (HDF) . и роботизированные машины для автоматической укладки ленты (ATL) с компьютерным управлением, которые в начале этого года прошли сертификацию первой части (FPQ), а также проверки конструкции и качества FAI.
Компания заявляет, что в рамках этого процесса машина HDF выполняет предварительную формовку компонентов из углеродного волокна для деталей самолетов, что позволяет ускорить производство высококачественных композитных деталей, а его система нагрева инфракрасным излучением быстро и равномерно размягчает углеродное волокно для получения точных деталей, которые, как утверждается, не деформируются. Кроме того, две машины ATL компании Strata укладывают материалы однонаправленного препрега на планшет перед их перемещением в пресс-форму для дальнейшей обработки. Согласно Strata, его рабочая зона размером 2,5 метра на 10 метров позволяет автоматизировать обработку больших слоев композитных материалов, устраняя необходимость в отдельном ультразвуковом станке для резки и сокращая время обработки.
2020, Techni-Modul, нервюра и стрингер крыла
Из:«Компрессионная установка для производства будущих авиастроек»
«Для нас OPTICOMS также была связана с автоматизацией, - говорит Шевалле. Techni-Modul Engineering поставила не только систему впрыска C-RTM для проекта OPTICOMS, но также робота для захвата и размещения и горячее формование (HDF) машина, интегрированная в полностью автоматизированную производственную ячейку. … «Мы автоматизировали классическую ручную укладку слоев с помощью роботизированного захвата и складывания», - говорит Шевалле. «Робот захватывает слои из автоматического резака и передает их на инструмент для нагрева преформ . который находится на столе уплотнения [Этапы 1 и 6] ». Применяются отслаивающий слой (синяя пленка на шаге 6), сапун (белый материал на шаге 6) и шарнирная многоразовая вакуумная мембрана (светло-голубая слева на шагах 2 и 6), затем вакуум и нагревание для предварительной формы и удаления воздуха из текстильный стек ( горячее формование, HDF ) при плавлении тонкой термопластической вуали для создания спрессованной преформы.
нервюр и стрингер OPTICOMS
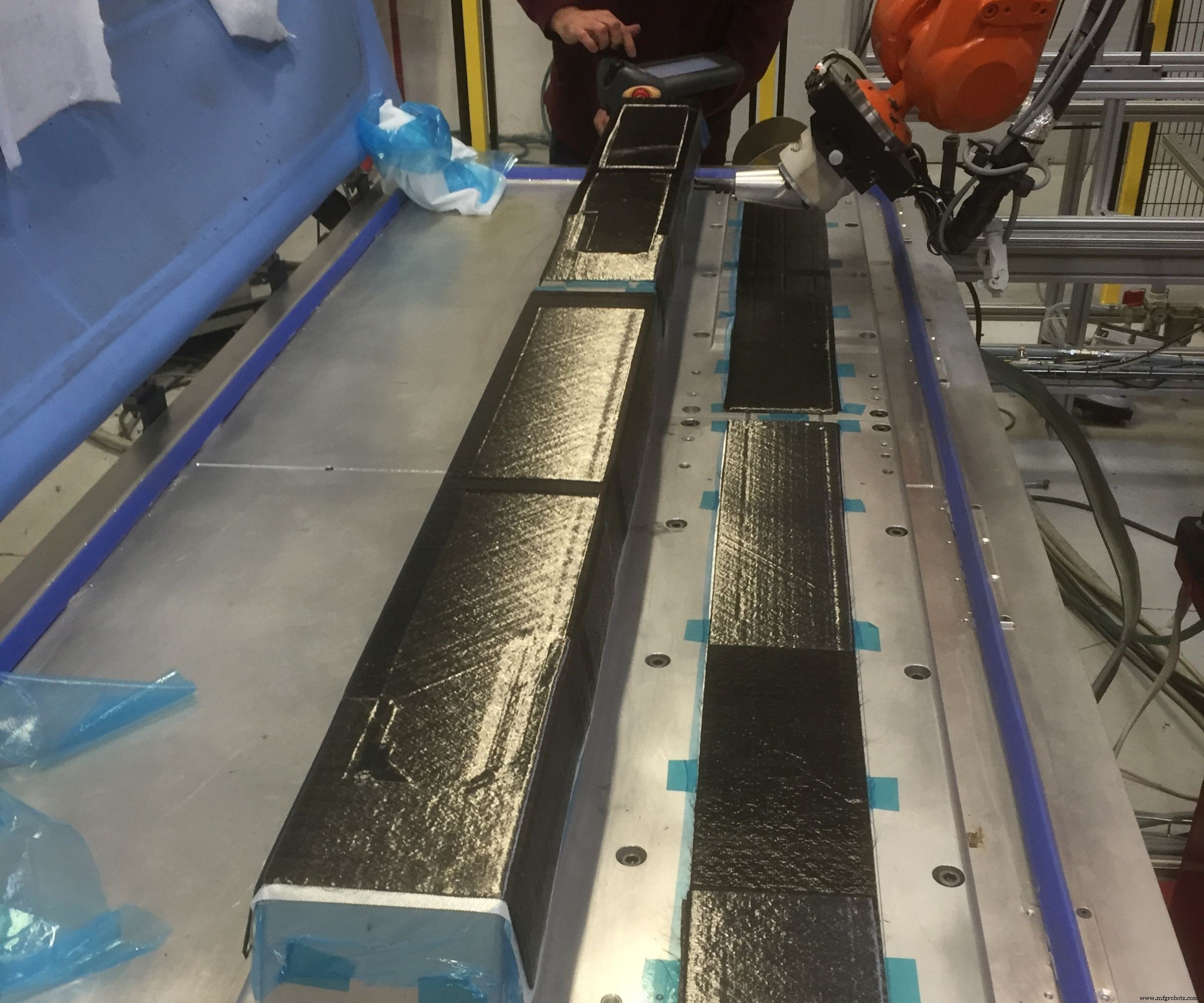
Этап 2. Инструменты для предварительного формования располагаются на столе для уплотнения с шарнирной многоразовой вакуумной мембраной (синяя слева), используемой для завершения нагрева с подогревом через каждые 5-8 слоев во время укладки. Фото:все изображения:Tecni-Modul Engineering.
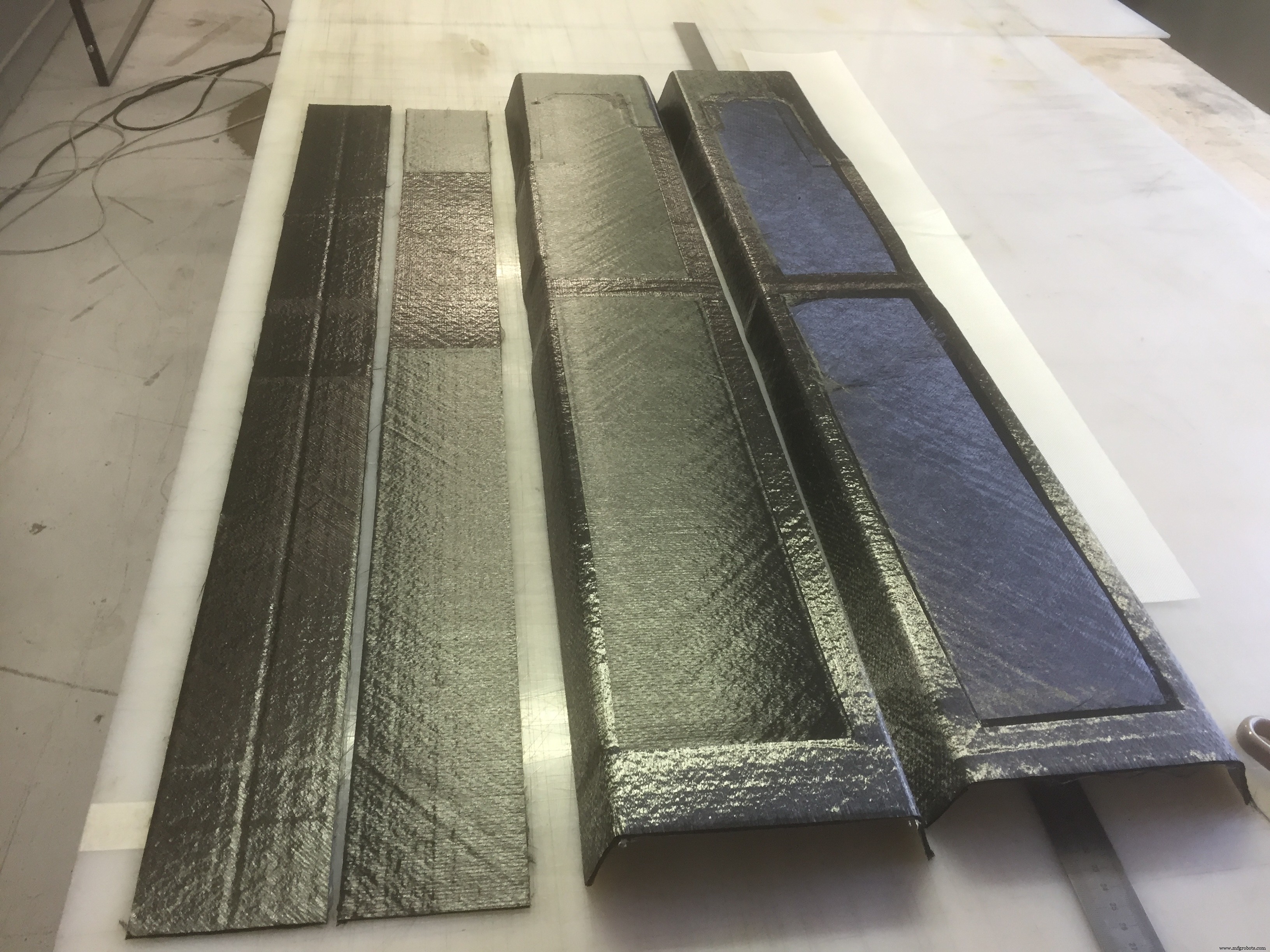
Этап 3. Каждый цикл предварительной формовки стрингера производит одну заготовку C-образной балки (две составляют стенку двутавровой балки) и одну заготовку с плоским фланцем. Здесь показаны два комплекта, необходимые для каждого стрингера двутавровой балки.
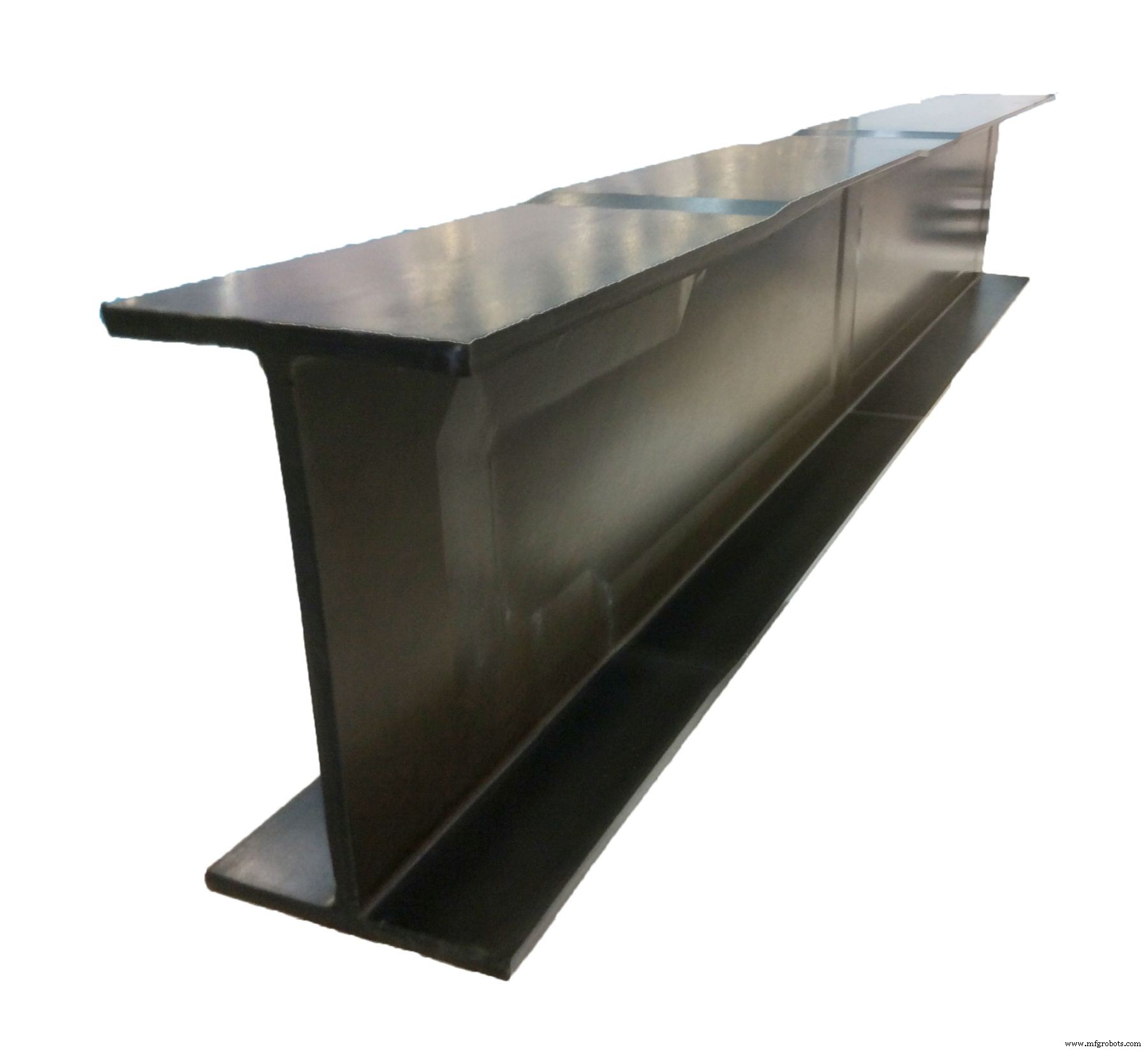
Шаг 5. Стрингер двутавровой балки, изготовленный из преформ HDF и RTM для проекта Clean Sky 2 OPTICOMS.
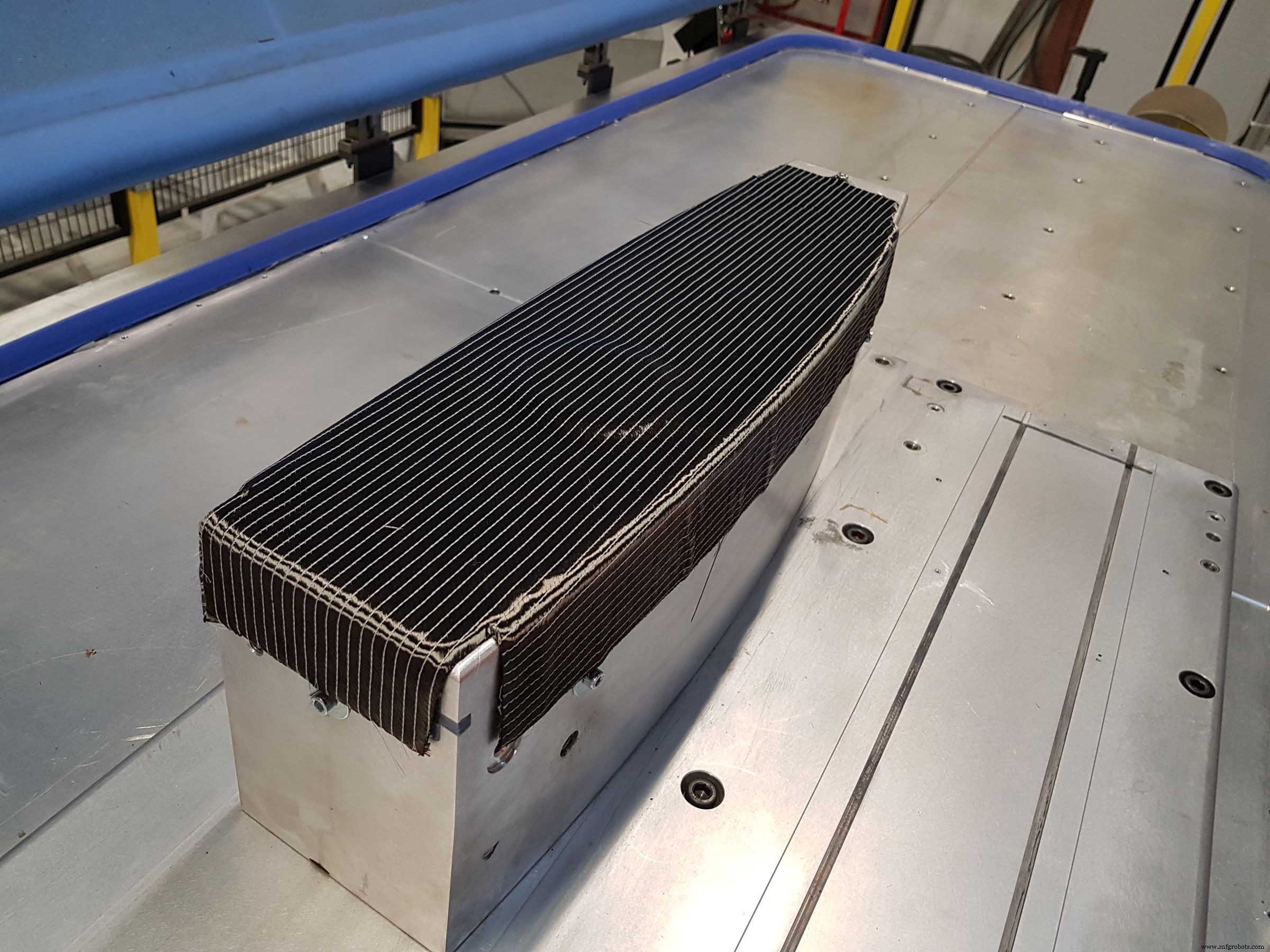
Шаг 6. Робот размещает слои обрезки на нагретом инструменте для изготовления преформ. Каждые 5-8 слоев выполняется разгрузка с подогревом для уплотнения преформы.
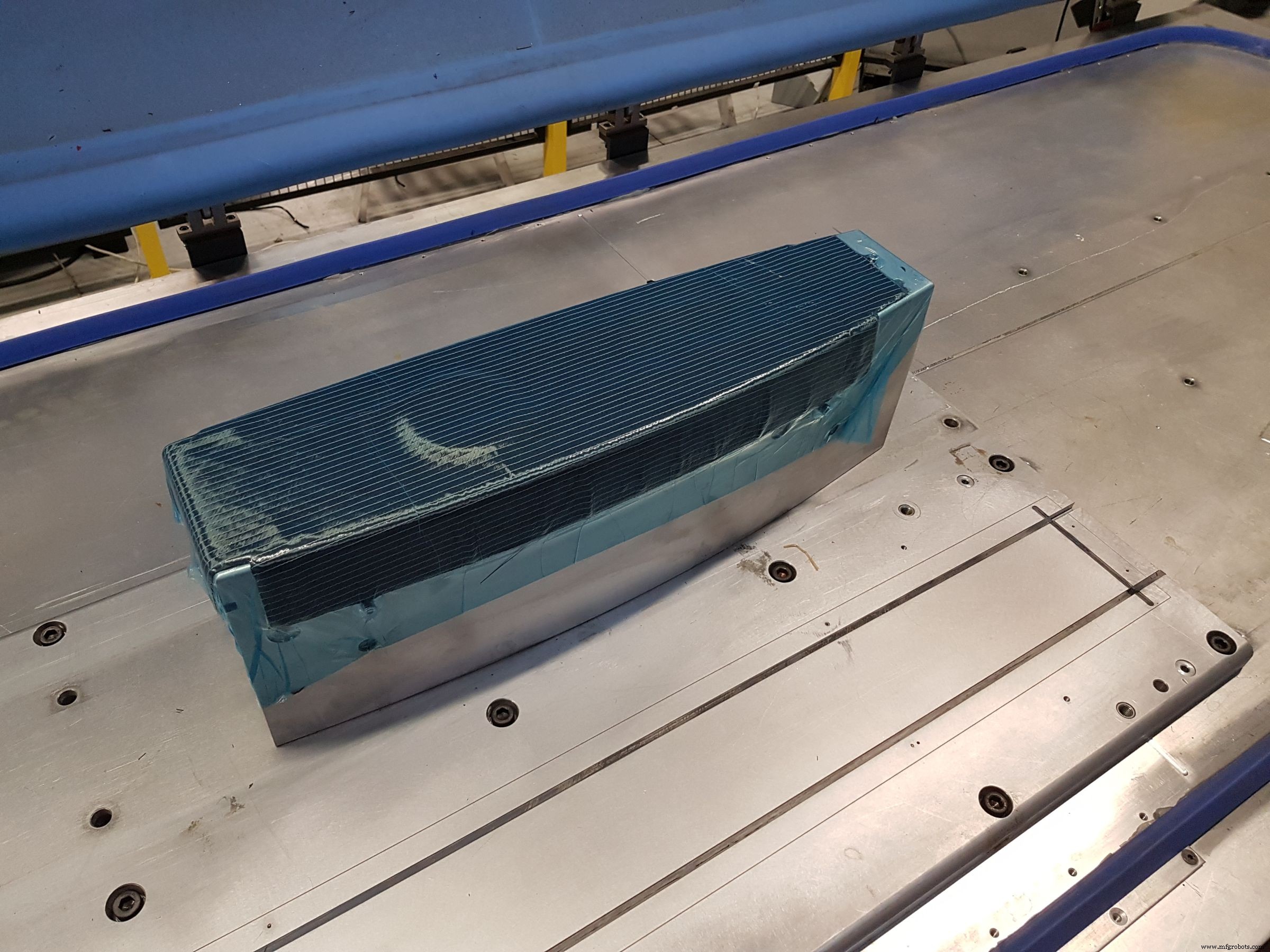
Перед удалением массы наносится синяя антиадгезионная пленка.
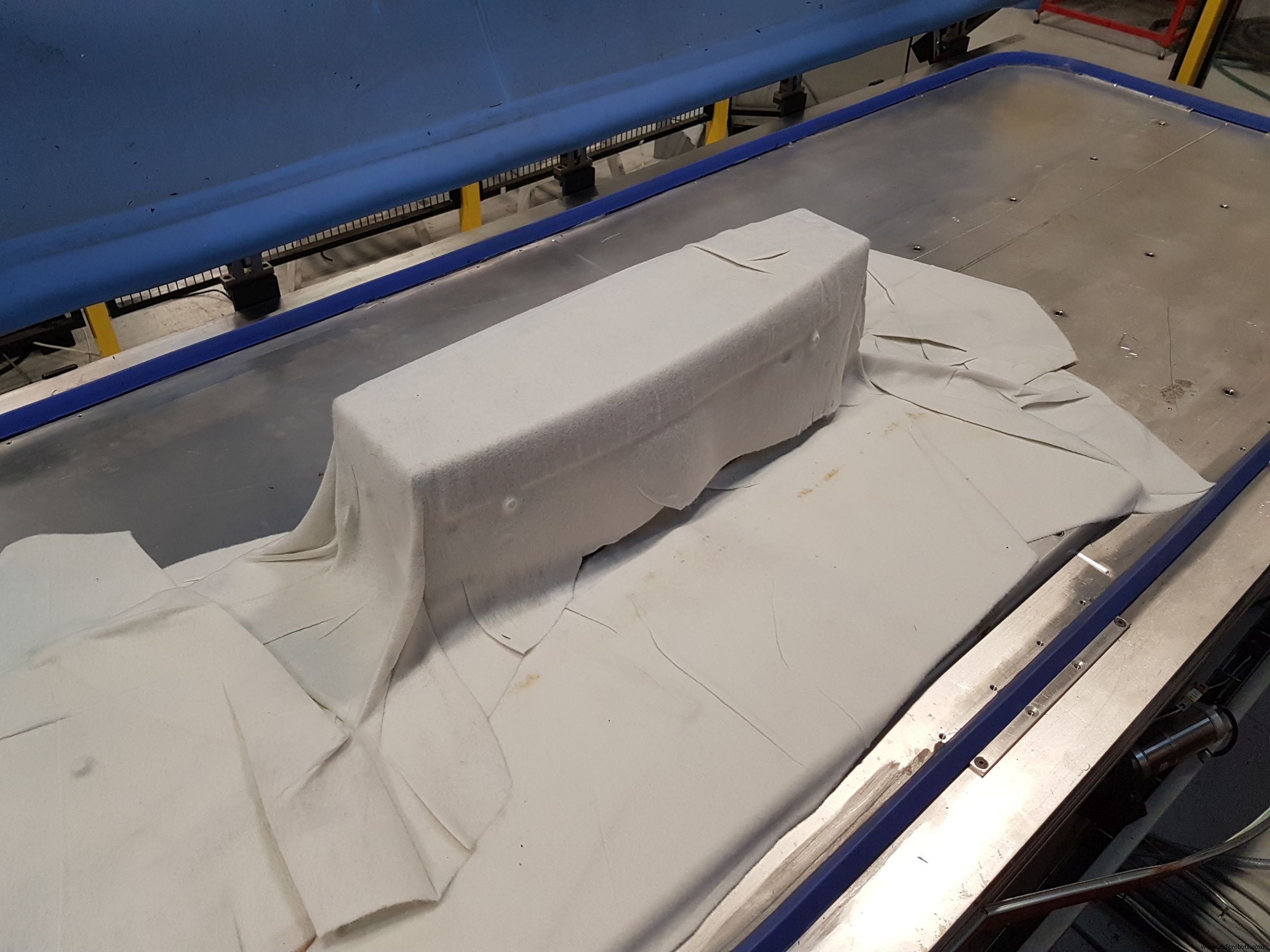
Сапун используется для удаления воздуха через преформу.
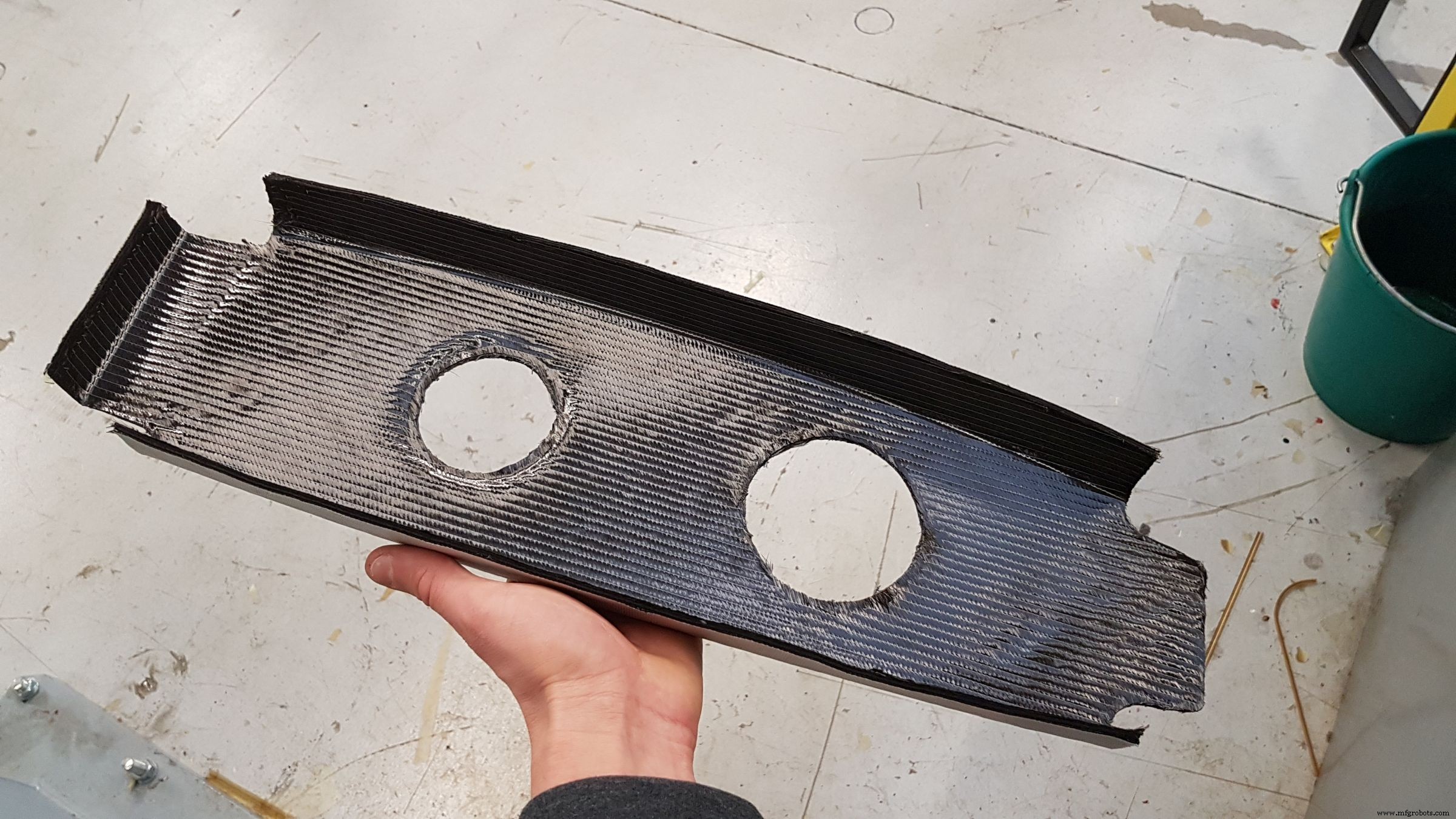
После окончательной обработки заготовка на инструменте охлаждается и вырезы обрезаются.
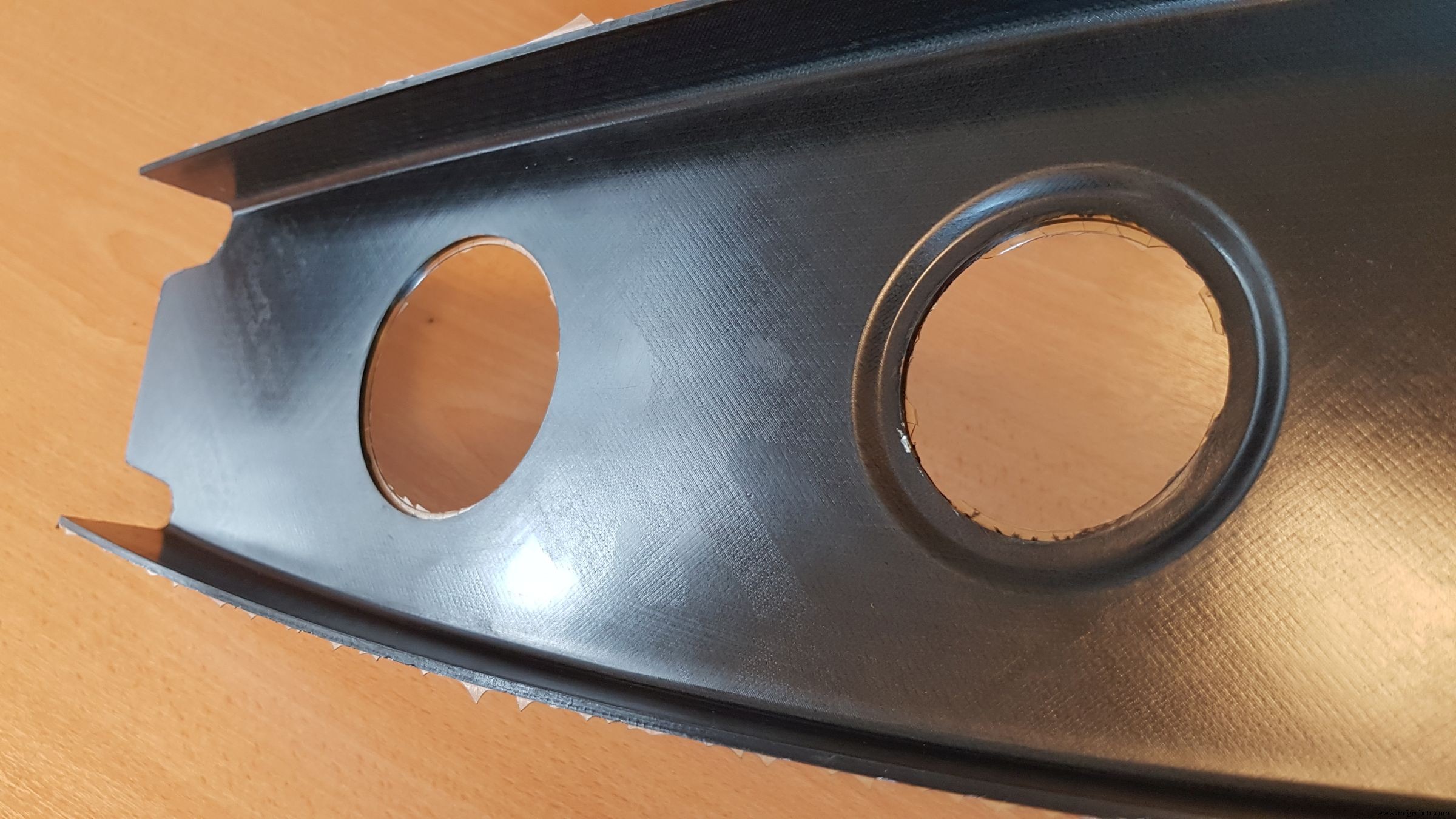
Этап 10. Заготовку ребра формуют с использованием RTM и эпоксидной смолы.
Предыдущий Следующий«Сколько слоев вы можете уплотнить за один раз, зависит от материалов и формы детали», - объясняет Шевалле. «Для деталей с малой кривизной, таких как крылья, можно уплотнять каждые 50 слоев. Ребро OPTICOMS, однако, имеет углы 90 градусов, а тестовая двутавровая балка имеет Т-образную форму, поэтому вы должны быть осторожны, чтобы не образовывать складки на слоях во время предварительной формовки ». Он добавляет, что такие сложные формы могут потребовать уплотнения через каждые 5-8 слоев, но все же могут быть частью крупномасштабного промышленного процесса:штабелирование слоев , 2-минутное уплотнение HDF , повторно открыть и снова штабелировать с последующими повторными циклами уплотнения с окончательным охлаждением преформы на инструменте перед перемещением в пресс-форму RTM.
волокно