Более высокий уровень контроля качества станков
Контроль качества станков находится на пороге глубоких изменений. По словам Штеффена Хейлера, менеджера по продукции и инженера по применению AfM Technology в Аалене, Германия, скоро будет выпущен стандарт ISO (ISO 230-13), определяющий процесс калибровки станка таким образом, чтобы его зондовые измерения могут быть приняты отделом качества.
Это не означает, что станок всегда будет таким же точным, как обычная КИМ. Но отделы производства и контроля качества будут говорить на одном языке, а машинные измерения можно будет использовать для контроля качества. Это, в свою очередь, дает преимущества в лучшем управлении процессом и более низкой стоимости качества.
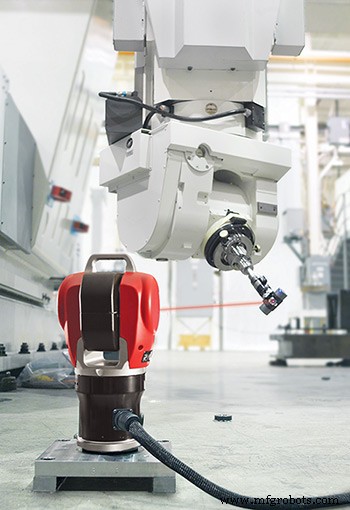
Компенсация объемной погрешности (VEC), возможно, является наиболее важным фактором, позволяющим станку выполнять приемлемый контроль качества. Но даже если вы по-прежнему используете автономное оборудование для окончательной проверки (что, как правило, и происходит), новейшие методы VEC предлагают наилучший путь к обеспечению высокой точности при производстве сложных деталей.
Например, Арт Киетлински, операционный менеджер Automated Precision Inc. (API) из Роквилля, штат Мэриленд, сказал, что компенсационный пакет компании повысит объемную точность многоосевого станка в четыре-пять раз, а иногда даже большее улучшение. «Обычно мы можем увидеть машину с максимальной объемной погрешностью на кончике инструмента, скажем, от 0,3 до 0,5 миллиметра до калибровки. А затем после калибровки мы можем быть около 0,075. На пятиосевом станке мы рассматриваем и устраняем все 43 возможные ошибки». [Объяснение 43 возможных отклонений станка см. в документе «Поддержание качества оборудования с помощью расширенной калибровки и оптимизации», «Технология производства», июнь 2019 г.]
API делает это, комбинируя лазерный трекер с тем, что они называют своей активной целью, объяснил Рон Хикс, вице-президент по управлению продуктами и маркетингу. «Активная мишень — это небольшой моторизованный отражатель, установленный на шпинделе. Это позволяет лазерному трекеру точно измерять положение кончика инструмента станка из одного положения инструмента». Это важно, отметил Хикс, потому что процесс VEC перемещает шпиндель в режиме реального времени по всем осям станка в процессе измерения. Это было бы невозможно со стандартным рефлектором лазерного трекера, потому что луч будет прерываться в разных точках по всему объему машины. Хикс добавил, что «в отличие от обычных лазерных процессов, нашу систему не нужно выравнивать по основным осям станка. Это дает существенные преимущества с точки зрения скорости и точности… Мы смогли компенсировать расходы двух машин за один день».
Система API измеряет «все возможные положения машины», добавил Китлински, поэтому в большом объеме машины (например, 10 м) она может отображать до 250 точек. Оттуда проприетарное программное обеспечение генерирует коэффициенты для полиномов, которые вычисляют необходимые исправления ошибок для каждой оси. Как объяснил Китлински, это сложная математика, потому что «ошибки не обязательно линейны. Вы можете получить полином второго или третьего порядка, для которого нужно найти решение».
По словам Хикс, завод Northrop Grumman в Палмдейле, штат Калифорния, является одной из нескольких историй успеха. На заводе используются большие пятиосевые портальные станки для выполнения всей отделки и сверления отверстий для всего фюзеляжа F-35, и каждый год проводятся посещения API для выполнения VEC на каждой машине. Тем временем, по словам Китлински, Lockheed Martin и Israel Aerospace обрабатывают секции крыла на горизонтальных участках, которые также обслуживает API.
Есть ограничения. Недавний визит в компанию из Мичигана, производящую высококачественные инструменты, прототипы и компоненты для мелкосерийного производства, вызывает предостережение.
Знакомство с ограничениями
Китлински рассказал, что компания из Мичигана пригласила API для демонстрации своего оборудования на пятиосевом станке, который уже прошел VEC на основе карты ошибок 21, «что является нормой для большинства станков и КИМ». Как объяснил Китлински, «все эти калибровки предполагают, что машина имеет твердое тело, а это означает, что все угловые ошибки будут одинаковыми на всем протяжении перемещения этой оси по объему. Так, например, независимо от того, где я проведу ось X через объем, если бы мне нужно было измерить погрешности тангажа, рыскания и крена, я бы получил одни и те же угловые данные. Но это не всегда так на этих больших машинах». По его словам, обычно это происходит из-за того, что рельсы не параллельны. Это создает нагрузку на машину и ее приводную систему, что приводит к «росту токов нагрузки и ряду других проблем».
Итак, первое, что проверил Китлински, — это прямолинейность линейных осей, на что у лазерного трекера уходит меньше часа. Он добавил, что обычно существует прямая связь между прямолинейностью и другими геометрическими ошибками, такими как ошибки тангажа, рыскания, крена и прямоугольности, «потому что вы даже не можете оценить прямоугольность, если вы не прямолинейны». В этом случае он обнаружил ошибки до 200–250 микрон (0,010 дюйма). API выполнила полную центровку машины, «даже разорвав мост и выровняв его механически. Затем мы применили карту коррекции 21 ошибки. В этот момент… угловые ошибки были одинаковыми для всей машины, и мы смогли улучшить машину в десять раз по сравнению с предыдущей калибровкой».
Во многом это связано с улучшенной механической центровкой, подчеркнул Китлински. «Чем лучше вы механически выровняете машину, тем лучше результаты калибровки». И наоборот, «вы не можете взять машину, которая не отрегулирована механически, и попытаться все исправить с помощью программного обеспечения».
Исправление ошибок в процессе
В только что обсуждавшихся пределах VEC может значительно улучшить геометрические неточности машины. А как быть с «неточностями обработки», дополнительными погрешностями, возникающими при обработке из-за эксплуатационных напряжений, термической нестабильности и других факторов? Билл Маланче, главный операционный директор Mitsui Seiki (США), Франклин Лейкс, штат Нью-Джерси, перечислил основные причины неточности:«потеря движения, перегрев и дизайн. Потеря движения работает во многих аспектах, но ее можно суммировать с помощью геометрического выравнивания и подгонки». Поскольку VEC устраняет другие факторы, температурная нестабильность становится, возможно, основным источником ошибок в процессе. И чем крупнее станок, тем больше различий можно увидеть в фактическом и номинальном положении инструмента.
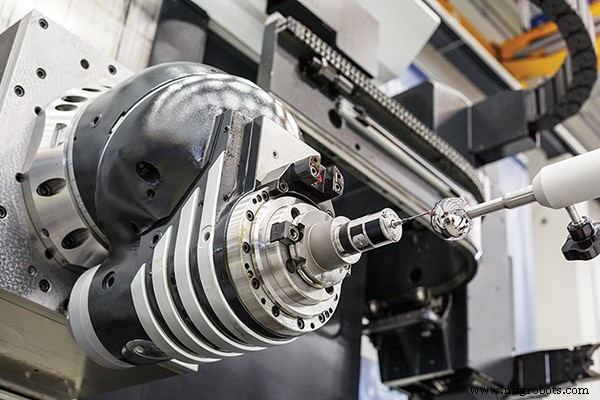
Один из подходов к решению этой проблемы состоит в том, чтобы использовать внутренний датчик машины, чтобы рассчитать это отклонение, а затем компенсировать его. Дуг Шульте, менеджер по развитию бизнеса компании Select Machining Technologies, Виндзор, Коннектикут, сказал, что их станки Soraluce «испытывают квалификационную сферу по ряду предустановленных точек. Это происходит для многих положений головы и оси. Затем программное обеспечение сравнивает измеренные точки с кинематической моделью станка и выполняет любую компенсацию, необходимую для обеспечения соответствия центральной точки инструмента геометрии станка». Соралус называет эту функцию динамической калибровкой головки (DHC), а Шульте сказал, что это обычная функция для пятиосевых станков. [Производственный инжиниринг описал версию Окумы в статье за июнь 2019 г.]
Машины Soraluce обычно оснащены несколькими двухосевыми головками, и DHC занимает от 25 до 30 минут для всего цикла измерения. Он предназначен для периодической компенсации перед обработкой, как и VEC. Но у Soraluce есть дополнительная функция под названием Accura Heads, которая нацелена на возможные ошибки в процессе, и на это уходит всего одна или две минуты. По словам Шульте, в этом варианте используются те же датчик и измерительная сфера, но они выполняются внутри программы обработки.
«Если вы собираетесь обрабатывать элемент детали, которая находится под определенным углом, и этот угол очень важен, вы можете использовать процедуру Accura Heads, чтобы проверить угол и положение вершины инструмента для этой конкретной ориентации. Затем он сделает это смещение для этого одного инструмента. Вы выполняете этот тестовый цикл непосредственно перед выполнением этой операции».
Шульте также указал, что для более жестких допусков в определенных конструкциях станков пользователь должен установить сферу ближе к области, где он собирается резать, в зависимости от размера станка. «Soraluce построила машины с продольным ходом более 60 метров», — добавил он. Можно легко себе представить, что внешнее влияние может привести к такому сильному отклонению между фактическим и номинальным позиционированием.
Подтверждение обработки/контроля качества
Принимая «компенсированную машину» как данность, операторы могут рассмотреть возможность использования датчика станка для выполнения функций контроля качества. Новый стандарт ISO 230-13 определит требования и сделает это со ссылкой на ISO 10360, который является стандартом для КИМ. Ключевой характеристикой, по которой оцениваются КИМ, является значение максимально допустимой погрешности (MPE). Приемочное испытание будет измерять семь ориентаций (четыре диагонали тела плюс по одной вдоль X, Y и Z) либо с помощью ступенчатого датчика, либо с помощью лазера в сочетании с измерительной сферой. Для прохождения теста максимальное отклонение (E0) не должно превышать MPE.
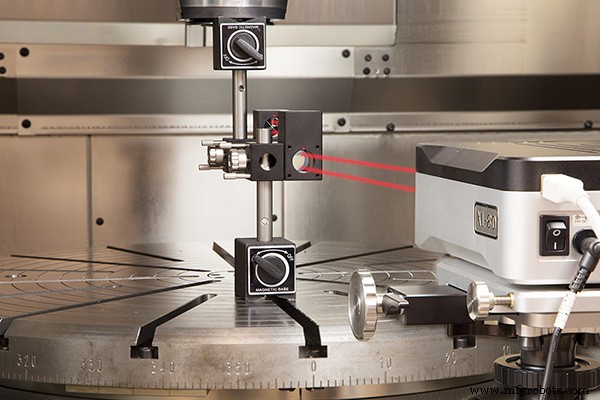
Как объяснил Хейлер, новый стандарт ISO так же четко определяет процедуру приемочных испытаний и необходимые значения для станков, но это новая концепция для машиностроителей. «В настоящее время ни один станкостроитель не знает размер своего MPE. Им предстоит изучить процедуру определения такого значения, а затем выяснить, что это такое. Это одна из услуг, которые мы предоставляем OEM-производителям». Как только строитель определил это значение для данного станка — и оно проверено на месте, как и при установке КИМ, — пользователь может провести окончательную проверку детали на станке, никогда не устанавливая ее на КИМ, и доставить деталь. клиенту с отчетом, подтверждающим точность измерений.
Является ли MPE станка приемлемым для конечного пользователя, это другой вопрос. Но представляется вероятным, что машины с более высокой точностью удовлетворят удовлетворительный контроль качества, по крайней мере, для некоторых применений. Это особенно верно для очень больших деталей, отмечает Беат Рис, менеджер по шлифовальным изделиям Mitsui Seiki. «Вы платите большие деньги за большую КИМ, особенно если хотите добиться сверхвысокой точности. Цифры астрономические. Кажется, никто не может предложить экономичное решение».
Есть еще кое-что, — сказал Рис. Одного знания MPE КИМ или станка недостаточно для соответствия стандартам аэрокосмической или автомобильной промышленности. Это потому, что они также «требуют значения неопределенности рядом с каждым измерением или проверкой деталей». Таким образом, в то время как многие люди думают о MPE как о «точности» машины, цифра не отражает вариации измерений и дополнительные неточности, которые происходят в реальном мире. Например, пояснил Райс, «колебания температуры в магазине могут привести к разным измерениям. Таким образом, если MPE КИМ составляет 1,9 плюс L/250 микрон, расчетная погрешность может составить 3 микрона на метр. Если вы измеряете более одного метра, значение MPE предполагает, что вы имеете точность в пределах 5,9 микрон. Но если вы добавите значение погрешности, вы увидите, что на самом деле вы измеряете с точностью до плюс-минус 8,9 микрон».
Расщепление микрона
Одна мастерская, которая очень серьезно относится к измерениям, — это точно названная Precision Grinding Solutions (PGS) в Хамдене, штат Коннектикут. Владелец Курт Рид считает важным, чтобы они четко понимали свой контроль качества, включая измерения погрешности, потому что они шлифуют вращающиеся детали реактивного двигателя. для крупных OEM-производителей, таких как Pratt &Whitney, а также поставщиков аэрокосмической отрасли 1-го и 2-го уровня. У PGS даже есть контракт на калибровку приборов для нескольких предприятий Pratt.
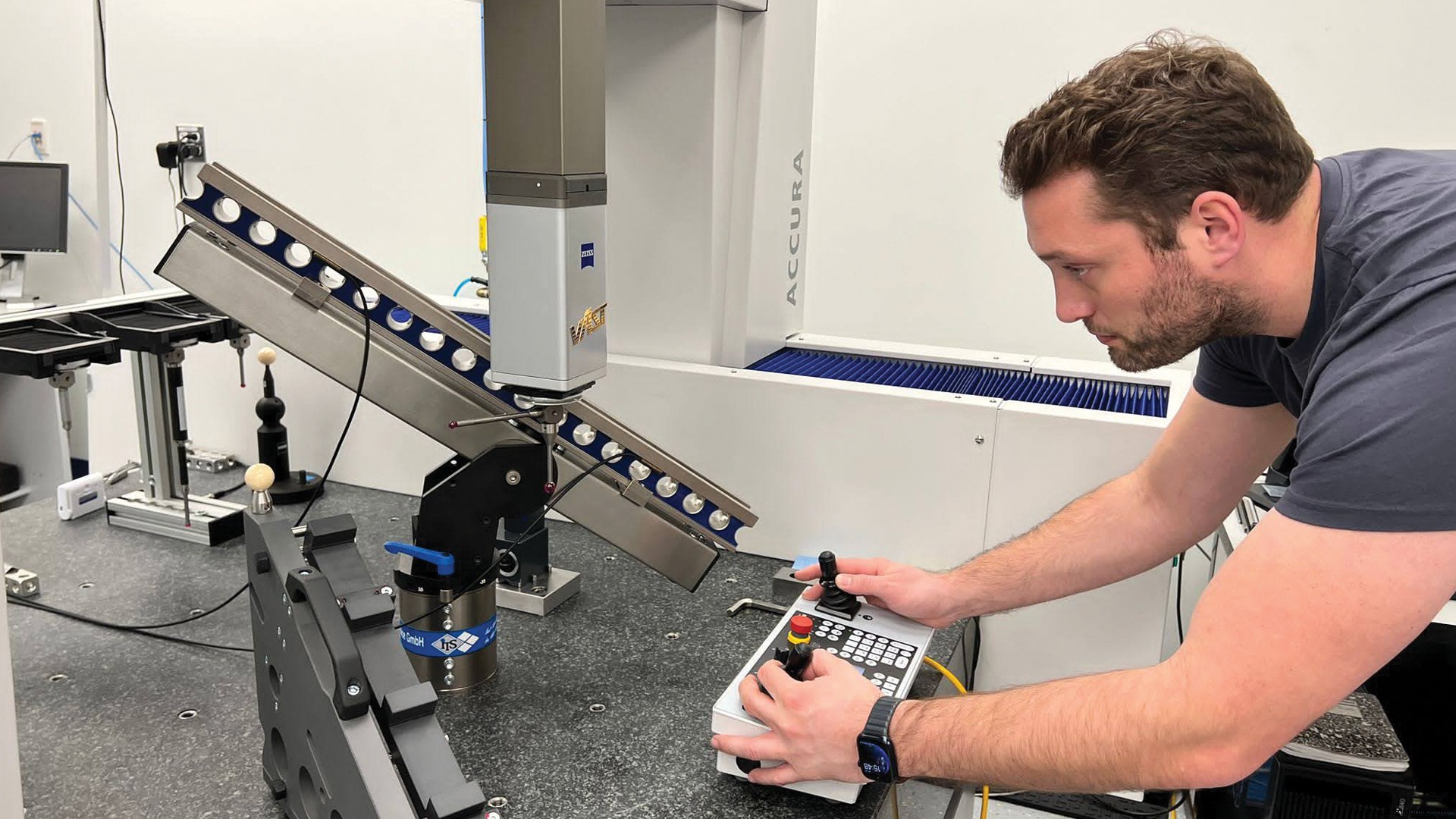
PGS имеет КИМ Zeiss PRISMO ultra, которую Рид называет машиной «эталонного класса». КИМ может похвастаться E0, равным 0,5 + L/500 мкм, и PGS определяет баланс неопределенности «одним из старомодных способов. Вы берете известный артефакт, скажем, один из датчиков Пратта, в калибровке которого мы участвовали, и измеряете важную функцию примерно 50 раз. Затем вы изучаете этот разброс данных, учитываете такие факторы, как изменения температуры в помещении, подставляете все это в долговременную формулу и получаете показатель неопределенности».
Теперь PGS внедряет новый метод, позволяющий еще лучше справляться с погрешностью измерения:Virtual CMM (VCMM). Рид объяснил, что VCMM — это подключаемый модуль для исполнительного пакета программного обеспечения Zeiss Calypso, который «позволяет вам вставлять в отчеты еще один столбец, показывающий неопределенность каждого отдельного измерения, которое вы выполняете». Кроме того, он также фиксирует все другие ошибки, которые не учитываются при калибровке лазера, добавил Рид.
PGS работает с AfM над сбором данных, необходимых для этой работы, которая, по словам Рида, выходит за рамки отслеживания колебаний температуры и вибраций. «Например, учитывается, используете ли вы длинный стилус с тонким или коротким стержнем. На что похожа подпись машины? Когда вы измеряете машину, какова фактическая геометрия, весы, направляющие… Как все это выглядит?» AfM определит все это, проведя серию специальных измерений с набором артефактов, включающих в себя различные мячи и ступеньки. Затем файлы ошибок будут запускаться в фоновом режиме для определения неопределенности.
Подводя итог, сказал Рид, «VCMM — это гораздо более современный и всесторонний способ изучения неопределенности для всей системы и лаборатории. Это не просто основано на одном артефакте. Он проверяет все измерения, которые проводит AfM, и оценивает весь измерительный объем КИМ, а не только одну локальную область, где вы тестировали прибор».
После завершения, как прокомментировал Рид, в новых отчетах качество изображения ухудшится, «потому что оно работает лучше, функция за функцией. Если вы включите эту функцию, вы увидите неопределенность каждой отдельной функции, выполняемой в каждой программе. Так что, если вы измерите что-то, что было бы «с точностью до микрона», и добавите погрешность, возможно, это будет 1,15 микрона. Но он дает реальное, правдивое исследование неопределенности всей системы».
Система Рида уже превосходна. У PGS есть первоклассная КИМ, а ее лаборатория стабильна к температуре с точностью до одной трети градуса по Фаренгейту. Но они сделали и другие инвестиции, чтобы ограничить неопределенность:«Мы купили программное обеспечение AfM и измерительные артефакты, чтобы лучше контролировать точность машины. . Мы также купили 700-миллиметровую ступенчатую кромку, идентичную той, что используется в сервисе Zeiss. Наша цель — всегда знать, где находится машина».
PGS больше не будет полагаться исключительно на ежегодные калибровки OEM, поскольку они представляют собой лишь моментальный снимок. Рид сказал, что эти визиты стоят значительных денег и до сих пор заставляют задуматься о том, как работает машина в течение всего года. «Если OEM-производитель возвращается через год, а калибровка «как найдено» не соответствует спецификации, это ставит под сомнение каждый продукт, который вы принимали вместе с машиной. Мы больше не готовы идти на такой риск. Мы стараемся проводить еженедельные или даже ежедневные проверки наших КИМ».
Техническое обслуживание и ремонт оборудования
- Взаимодействие с углами:как обрабатывать углы
- 10 ключевых шагов к выбору машинного прогностического инструмента
- Операции на токарных станках и режущие инструменты токарных станков
- Заказы на станки сократились в сентябре
- Fuji представляет многозадачную машину
- Методы станков для приобретения станков Коха
- Фрезерная мощность токарно-фрезерного центра
- Токарный центр и технология станков
- 3 метода изготовления 5-осевого станка с ЧПУ
- Понимание процесса обработки и станка