Медицинское производство становится умнее
Цифровое и автоматизированное производство делает успехи в мире медицинского производства, о чем свидетельствуют недавние системы, запущенные в производственные линии во время пандемии COVID-19.
Учитывая строгие стандарты, регулирующие производство медицинского оборудования, среда Индустрии 4.0, ориентированная на данные, создана специально для контрактных производителей, стремящихся соответствовать спецификациям, но при этом справляющихся с острой нехваткой квалифицированных операторов.
Как всегда, материалы становятся все более сложными, а детали становятся все меньше, имеют более сложную геометрию и более жесткие требования к допускам.
В широком смысле тенденции в области здравоохранения — старение населения, стремление к удаленной диагностике и терапии вне дорогостоящей больничной среды, более персонализированные методы лечения — стимулируют разработку медицинского оборудования. А в условиях продолжающейся неопределенности, связанной с пандемией, и связанных с этим разрушенных цепочек поставок обеспечение большей прозрачности работы поставщиков и продавцов является приоритетом № 1.
Наряду с оцифровкой здравоохранения возникает необходимость защиты всех собираемых данных. С этой целью действуют такие инициативы, как новый Центр кибербезопасности медицинских устройств Университета Миннесоты, о котором было объявлено 9 сентября. Пять крупных игроков в отрасли здравоохранения объединились для совместной работы в новом центре:Boston Scientific, Smiths Medical, Optum, Medtronic и Abbot. Лаборатории. Их цель — устранить уязвимости программного обеспечения в медицинских устройствах, которые потенциально могут быть использованы для причинения вреда пациентам или нарушения работы медицинских учреждений.
Высокотехнологичное будущее здравоохранения также означает больше роботизированной диагностики и процедур, следовательно, потребность в большем количестве медицинских инструментов и деталей, предназначенных для использования с этими системами. Например, компания XACT Robotics в Хингеме, штат Массачусетс, разработчик роботизированной системы XACT ACE, объявила 30 августа, что успешно завершила набор пациентов в первое в США исследование по оценке XACT ACE для использования в чрескожных процедурах на легких. Это включает биопсию для подтверждения наличия рака. Роботизированная система без помощи рук может обнаруживать рак раньше и менее инвазивно.
Между тем, по прогнозам iData Research, к 2025 году ежегодно будет выполняться 3 миллиона роботизированных хирургических процедур. Роботизированные руки на таком оборудовании, как хирургическая система да Винчи, потребуют большого количества миниатюрных инструментов, которые врачи контролируют для выполнения этих минимально инвазивных операций. При роботизированных операциях используются меньшие разрезы, что приводит к меньшей кровопотере и рубцеванию, сокращению времени пребывания в больнице и более быстрому выздоровлению.
ИИ на основе данных также выйдет на первый план в улучшении результатов лечения пациентов. Ярким индикатором этого пути является приобретение компанией Stryker компании Gauss Surgical из Менло-Парка, Калифорния. Компания Gauss разработала Triton, платформу с искусственным интеллектом для мониторинга кровопотери во время операции.
Аддитивное производство также продолжит расширять свою критическую роль в производстве имплантатов, инструментов и хирургических учебных моделей для конкретных пациентов. Например, итальянская компания Tsunami Medical поражает отрасль тем, что использует лазерные и электронно-лучевые системы 3D-печати GE Additive для производства ряда очень сложных спинальных имплантатов.
Мелкие детали, проблемы с сортировкой
По мере того, как материалы для изготовления медицинских устройств развиваются, а детали становятся меньше, машины швейцарского типа серии L компании Marubeni Citizen-Cincom (MCC), Аллендейл, штат Нью-Джерси, отвечают на вызов.
«У Medical есть материалы, о которых вы раньше не слышали», — пошутил президент и главный операционный директор Брайан Сач. Прочные материалы можно использовать для изготовления простых деталей или более сложных компонентов, требующих использования множества инструментов для создания различных элементов.
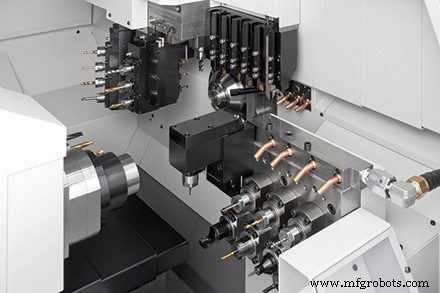
«Наши станки серии L представляют собой станки с контршпинделем, и их существенным преимуществом для медицинского производства является их модульность, — пояснил Сайш. «В любой момент доступно несколько инструментов, поэтому мы можем просто выдвинуть один и поставить три на одно место».
Для работы с меньшими диаметрами, типичными для современных медицинских сверл и фрез, MCC предлагает ускорители до 4-кратного ускорения. «Наши приводные инструменты развивают скорость до 6 000 или 9 000 об/мин в зависимости от модели, но мы можем вставлять другой держатель инструмента, и теперь мы развиваем скорость до 36 000 об/мин. Когда этого недостаточно, мы можем модернизировать наши электрические шпиндели, которые могут развивать скорость до 80 000 об/мин».
В качестве примера, отметил Саш, клиент может сверлить восьмитысячное отверстие, «поэтому вам нужна некоторая скорость для этого — или использовать концевую фрезу с 16-тысячным сечением или, может быть, даже концевую фрезу с восьмитысячным сечением, чтобы наклонить где-нибудь угол. . С нашими электрическими шпинделями со скоростью вращения 80 000 об/мин мы можем скользить в эти карманы. И этот же инструмент можно использовать в качестве торцевого, поперечного или обратного инструмента, так что он очень модульный». Компания MCC заключила партнерское соглашение с продавцом высокоскоростных шпинделей NSK для создания этих собственных шпинделей.
Около двух лет назад компания MCC расширила функциональность оси B своих станков, представив версию ATC (автоматическая смена инструмента) своего станка L20. «Теперь у нас есть возможность использовать 13 инструментов на оси B», — сказал Так, тогда как обычно ось B имеет только четыре инструмента — и это «довольно горячая вещь для медицинского рынка», учитывая узкие углы сегодняшних деталей.П>
Еще одна инновация MCC, представленная примерно в 2016 году, — резка с помощью низкочастотной вибрации (LFV). В этом процессе станок «колеблется по траектории резания по оси Z или X, двигаясь вперед и назад с очень высокой скоростью, чтобы делать небольшие воздушные пропилы и ломать стружку во время обработки», — сказал Так. «Медицинская сфера любит технологию LFV, и большинство клиентов, которые используют ее впервые, говорят:«Я никогда больше не куплю машину без нее». С LFV «вы на 100 процентов сломаете чипы; нет промежуточного. Как только вы запустите процесс, это гарантировано. Вы по-прежнему должны знать свои режущие инструменты, а режущие инструменты все равно могут выйти из строя, но проблема наматывания стружки исчезнет».
Клиенты MCC варьируются от OEM-производителей с 300 или 400 машинами до небольших производителей с 10 машинами. И эти клиенты «изготавливают самые разные детали», от обычных костных винтов и кейджей для хирургии позвоночника до различных хирургических инструментов, таких как костные развертки, необходимые для операций на бедре и колене. Есть крошечные костные винты диаметром примерно 4 мм с отверстиями для швов. «Для вырезания разных форм нужны девять разных инструментов», — сказал Сайч. «В этом маленьком костном винте много особенностей — это не просто винт с головкой».
После того, как эти крошечные детали изготовлены, сортировка становится главной проблемой. MCC производит оборудование для автоматизации, адаптированное к поставленной задаче.
«Эти детали настолько малы, что когда они падают в ведро, там может быть 300 штук. Если вы попытаетесь выбрать последний, чтобы попытаться его измерить, какой из них был? У нас может быть устройство с разными лотками для подсчета», — сказал Сайч.
Клиент может положить 100 деталей на один лоток, затем, когда лоток переместится, положить одну деталь на следующий лоток, 100 деталей на следующий лоток, одну на следующий лоток и так далее. Если есть 10 лотков, он может работать без присмотра восемь часов или всю ночь. Измеряя детали через определенные промежутки времени, клиенты могут определить, хорошие или плохие предыдущие детали, благодаря сборным лоткам.
Преимущество шести осей
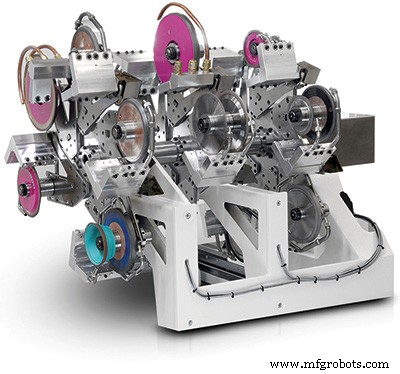
По словам президента Эрика Шварценбаха, устойчивый спрос на станки для заточки режущего инструмента компании Rollomatic USA Inc., Манделейн, Иллинойс, является ярким показателем устойчивости производства медицинского оборудования.
Среди множества инструментов, которые OEM-производители и контрактные производители используют для изготовления станков Rollomatic, есть различные ортопедические режущие инструменты, такие как рашпили, костные сверла, перфораторы черепа и артроскопические боры. На протяжении всей пандемии «наши клиенты инвестировали, как и раньше — ни больше, ни меньше», несмотря на отсрочку ортопедических или плановых операций. "Бизнеса было достаточно, чтобы эти компании продолжали работать и удовлетворяли потребность в реинвестировании".
В последние пару лет, отметил он, растет спрос на различные инструменты для роботизированных операций. Но эти устройства представляют собой особую проблему.
«Дрель, которую хирург использует с наконечником для сверления кости, отличается от того, что выдает робот», — пояснил он. «Роботы используют более длинные сверла, чем хирурги. Природа изготовления длинного сверла сложнее, чем короткого. Сначала заготовки хирургического инструмента обрабатываются в мягком состоянии на токарном станке швейцарского типа с последующей закалкой. Эти процессы по своей сути вызывают коробление этих заготовок, и чем они длиннее, тем больше они изгибаются. И когда они согнуты, у нас возникают проблемы с надежной загрузкой, шлифовкой и разгрузкой. Когда мы обучаем клиентов нашему станку и настройке, мы должны быть очень осторожны, чтобы научить их более глубоко и убедиться, что они понимают особенности, позволяющие обойти изогнутую заготовку. Изогнутые заготовки часто выпрямляются производителем, но даже в этом случае они никогда не бывают идеальными, хотя они и не обязаны быть идеальными. Машина способна обрабатывать небольшие искажения».
Чем более роботизированной становится отрасль, «тем больше внимания должно уделяться точке сверления. В то время как хирург всегда может просверлить кость, потому что он может смотреть, видеть, регулировать руку и давление, чтобы острие не ушло, робот этого не делает. Таким образом, эти точки должны быть разработаны, чтобы быть более эгоцентричными. Мы помогаем производителям медицинского оборудования научить их тому, как выглядит точка самоцентрирования».
Шварценбах также отметил больше вариантов из нержавеющей стали 17-4 для ортопедических фрез. «Материал стал мягче и менее затвердевшим, что является для нас проблемой с точки зрения поиска подходящих шлифовальных кругов для их шлифовки. Как известно, чем мягче материал, тем труднее его шлифовать». Чтобы удовлетворить эту потребность, Rollomatic сотрудничает с производителями колес в Швейцарии и США, чтобы закупить колеса, подходящие для более мягких материалов.
«Чем мягче материал, тем больше заусенцев он оставляет, — объяснил Шварценбах, — поэтому удаление заусенцев представляет собой проблему. Наши клиенты обычно используют нейлоновые щетки для удаления заусенцев после шлифовки, особенно при работе с более мягкими материалами. Но ни колесо, ни процесс никогда не бывают совершенными; всегда будет немного рыхлого заусенца, который необходимо удалить каким-либо методом. Для удаления этих заусенцев мы используем нейлоновые или иногда пропитанные керамические или абразивные щетки».
Еще одной областью роста являются быстроразъемные захваты для медицинских инструментов, продолжил он. Эти инструменты могут быть вставлены хирургом в наконечник или закреплены на роботизированной руке. Такие захваты «стали намного сложнее, чем мы когда-либо видели. Для большинства из них мы используем кофемолку».
По словам Шварценбаха, возможности Rollomatic с шестью осями меняют правила игры для производителей медицинских товаров, которым нужна большая гибкость для программирования и более простая настройка колес.
«Вам не нужно использовать сложные колеса; вы можете использовать колеса более простой формы, особенно на точках сверления», — сказал он. «Вы можете изготовить точку сверления проще, чем на пятикоординатном станке. И не забывайте:угол сверления теперь составляет от 50 до 60 градусов включительно. Они очень крутые, в отличие от твердосплавного сверла по металлу под углом 120 или 130 градусов. Наши шестиосевые станки действительно помогают обтачивать точки сверления гораздо легче, чем мучиться с настройкой пятиосевого станка».
Он добавил, что система быстрой смены колес Rollomatic предлагает еще больше преимуществ. «Мы продаем намного больше станков для смены колес. Базовое устройство смены колес имеет шесть станций, поэтому вы можете установить шесть пакетов колес для повышения гибкости, что подходит для более коротких партий. Более короткие партии требуют большей гибкости с частой заменой. Станки для замены колес очень хороши для этого». В то время как около 80 процентов машин, которые Rollomatic продает для медицинской промышленности, сохраняют стандартные шпиндели с парой колес спереди и сзади, некоторые производители «начинают использовать нашу новую технологию».
Роль силового тестирования
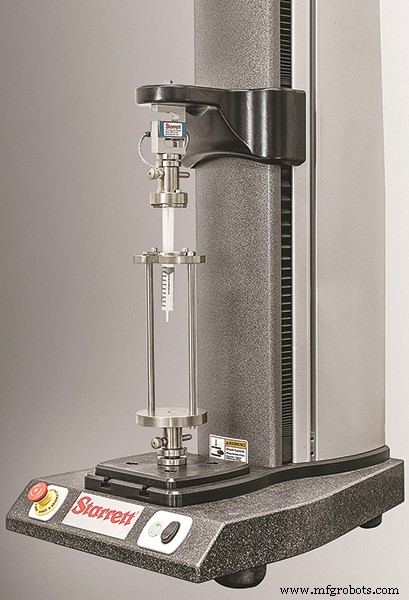
От подготовки к производству до изготовления детали оборудование для силовых испытаний и его встроенное программное обеспечение выполняют важные функции для медицинских изделий, часто с целью обеспечения комфорта пациента.
Например, контуры и покрытие иглы можно проверить на то, насколько легко они входят в кожу, а клей можно оценить на то, насколько хорошо они прилегают к коже или насколько легко они удаляются.
Перед производством «вы можете создать тесты, чтобы убедиться, что ваше оборудование работает должным образом, прежде чем использовать его в производстве», — объяснил Джейкоб Моралес, инженер технической поддержки The L.S. Starrett Co., Атол, Массачусетс. Что касается бинтов, то «вы можете протестировать клей, прежде чем использовать его на своей производственной линии», в партиях, варьирующихся, например, от одного образца на 100 до одного на 10 000 образцов. «После обработки вы можете снова запустить эти тесты, чтобы обеспечить согласованность».
Такие тесты особенно важны при производстве в соответствии со стандартами ASTM и ISO, а также для подготовки документации, важной для прослеживаемости, добавил Эрик Перкинс, технический менеджер Starrett по испытаниям сил и материалов. Программное обеспечение Starrett позволяет тестировать как силу, так и свойства материала, и просто щелкнув нужный значок, программное обеспечение может запустить соответствующий тест. Измерение силы охватывает сценарии «годен/не годен», включая тестирование на пиковую нагрузку, среднюю нагрузку, тестирование на сжатие и многое другое. Шприцы — яркий пример, требующий одноосного приложения силы, — могут быть протестированы с образцами веществ для определения силы впрыска для контролируемой скорости впрыска.
Хотя эти тесты предоставляют информацию об образце, они не всегда возвращают данные, относящиеся к материалу, составляющему образец. Испытания материалов идут дальше, используя свойства материалов, например, для испытаний на удлинение и напряжение-деформацию.
По словам Моралеса, программное обеспечение Starrett можно интегрировать в производственный процесс. <о:р>о:р>
«Если у вас есть силовая система для тестирования образца, вы можете запрограммировать ее на систему ввода-вывода, чтобы тест выполнялся постоянно. Производственное оборудование перемещает образец к машине и посылает сигнал; машина отвечает запуском теста и выдает выходной сигнал на основе результатов теста. Остальное производственное оборудование может отреагировать соответствующим образом. Если вы получите результат, выходящий за пределы допуска, сигнал может предупредить оператора».
Эта гибкость означает, что «вы можете подключить силовую систему к ПЛК и интегрировать ее в производственную среду, чтобы исключить потенциальную ошибку ввода данных, связанную с человеческим фактором», — сказал Перкинс. «Пользователи могут автоматически тестировать продукт каждый раз, когда он ставится в очередь».
От базового программного обеспечения Starrett L1 force до более продвинутых вариантов L2, L2Plus и L3 «мы даем клиентам возможность проводить испытания в точности в соответствии с требованиями любого производственного стандарта», — сказал Перкинс. А поскольку программное обеспечение Starrett совместимо на разных платформах, добавление оптических систем и систем технического зрения создает чрезвычайно широкое метрологическое решение. <о:р>о:р>
Однако этот уровень настройки не ограничивается программным обеспечением. Starrett работает с производителями над созданием полностью автоматизированных систем.
«Мы используем роботов для вставки деталей в нашу систему силовых испытаний», — сказал Перкинс. «Мы используем пневматические захваты для захвата деталей». С постоянно работающей тестовой платформой в сочетании с этим уровнем автоматизации «наша система сообщит, хорошая у вас деталь или нет, затем робот выполнит любую требуемую программу и поместит эти детали в указанную корзину».
Общее представление GE
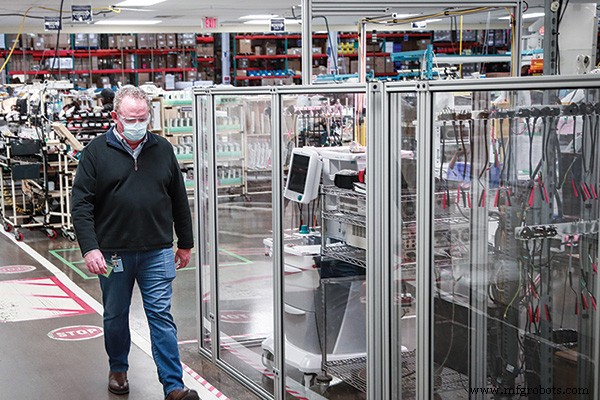
Улучшение рабочих процессов в больницах и поддержание устойчивости цепочки поставок были главными задачами GE Healthcare во время пандемии.
«Мы наблюдаем рост запросов на дополнительную автоматизацию — не только с типичной точки зрения производительности, но и с точки зрения использования автоматизации, чтобы мы могли поддерживать производство в разных местах», — сказал Джимми Бичем, исполнительный главный инженер по передовому производству в GE Healthcare в Милуоки. «Это проще, чем обучать новую или возобновляемую рабочую силу. Речь идет не обязательно о рабочей силе, но о безопасности цепочки поставок, где автоматизация имеет смысл. Если мне нужно перевести производство из одного региона в другой, гораздо проще, если процесс уже автоматизирован».
Он добавил, что основной частью этой философии является защита от ошибок. «Мы обучали операторов и составляли письменные процедуры, — объяснил Бичем. «Сейчас мы рассматриваем возможность использования других технологий, которые оцифровывают то, что должны делать операторы, и взаимодействуют с ними. Допустим, у вас есть станция крутящего момента, на которой вы затягиваете болты, затем идет сложная сборка, а затем кобот. Мы смотрим на технологии, которые соединяют все это в цифровом виде, которые работают синхронно с оператором, поэтому они взаимодействуют с этим человеком и не требуют, чтобы оператор все это запоминал. Это дает нам большую гибкость, когда мы производим один и тот же продукт в трех регионах по всему миру. Теперь у нас есть один процесс управления. Мы не полагаемся на то, что операторы запомнят бумажные процедуры, когда им нужно циклически выполнять несколько сложных частей операции».
Это жизненно важно для GE Healthcare, которая производит множество умного диагностического оборудования. Аддитивное производство — важная часть уравнения, и GE Healthcare также усовершенствовала свои процессы в этом отношении.
«Когда мы только начинали, вероятно, от 80 до 90 процентов нашего времени уходило на исследования и разработки, пытаясь понять, как работают добавки, как разрабатывать материалы и параметры для удовлетворения наших технических требований», — сказал он. «Сейчас мы достигли примерно 80-процентной готовности, когда мы переходим к производству, а остальные 20 процентов нашего времени посвящены разработке новых материалов для новых поступающих воронок. У нас есть производственное предприятие в Монтеррее, Мексика, и у нас есть довольно активная воронка вещей, идущих туда. Затем у нас есть другие дополнительные приложения, которые мы запускаем в момент использования».
В конечном счете, хотя пандемия оказалась сложной задачей, GE Healthcare выдержала бурю.
«Нашей большой проблемой было снабжение, безопасное размещение людей на заводе, — сказал Бичем. «В некоторых случаях, например, с вентиляторами, мы во многом полагались на автоматизацию, чтобы удовлетворить беспрецедентный спрос. Мы привлекли много людей для выполнения этой работы, но нам все еще нужно было найти творческие способы производства того объема продукции, в котором отчаянно нуждались наши клиенты. И мы узнали, что можем производить вещи по-другому; это вдохновило еще больше идей».
<о:р>о:р>
Система управления автоматикой
- Оценка воздействия Индустрии 4.0 на производство
- Развенчаны 8 мифов о металлургическом производстве
- Технологии для более эффективного производства медицинских компонентов, представленные на выставке MD&M West 201…
- 6 способов IIoT сделать производство более эффективным
- Stratasys:повышение экологичности с помощью 3D-печати
- ОТЧЕТ:2016 год станет «переломным моментом» для производственных технологий
- Умение британского производства:ожидания на 2018 год
- Преодоление разрыва в навыках в автомобилестроении
- Stora Enso:будущее производства стало умнее
- Построение устойчивой цепочки производственных поставок