Тесты обработки крупных деталей Возможности горизонтального станка
Универсальные платформы обеспечивают максимальную эффективность обработки
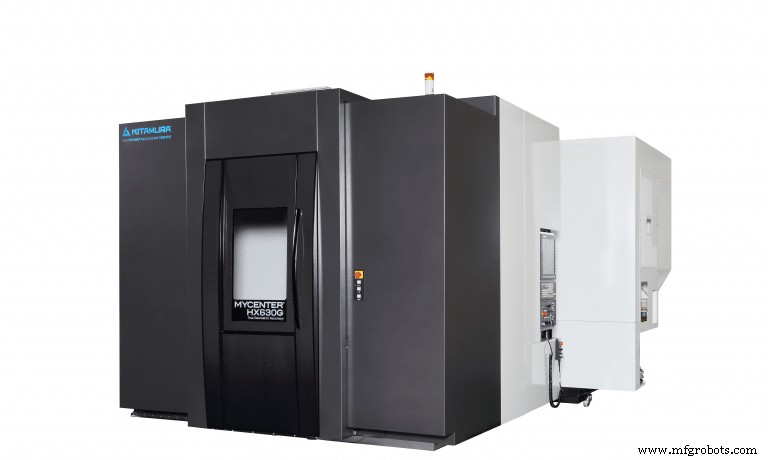
Горизонтальные обрабатывающие центры (HMC) представляют собой универсальные четырехосевые и, все чаще, пятиосевые станочные платформы, которые максимизируют обработку многогранных крупных деталей за счет минимизации обработки деталей. Они используются в таких различных отраслях, как аэрокосмическая, автомобильная, энергетическая и машиностроительная.
Обладая почти универсальными производственными мощностями, HMC предлагают производителям широкий выбор, что делает их менее восприимчивыми к циклическим взлетам и падениям в какой-либо одной отрасли, например, в нефтегазовой. HMC легко автоматизируются. Как правило, они оснащены двумя поддонами для деталей, установленных на надгробии, одной заготовкой, или они могут быть автоматизированы с помощью групп поддонов из шести или более поддонов. Для производства без присмотра доступны линейные гибкие производственные системы (подаваемые от складских запасов и обслуживаемые рельсовыми, надземными портальными роботами или шестиосевыми роботами, установленными на пьедестале). Отдельные крупные детали варьируются от блоков двигателей до буровых долот, корпусов насосов и коллекторов, а также семейств компонентов, устанавливаемых на надгробиях.
Подходящие машины, крупные детали
По словам Сала Сверчека, помощника менеджера по продажам Kitamura USA Inc., Уилинг, Иллинойс, при обработке крупных деталей жесткость станка и его фундаментальная конструкция имеют решающее значение для эффективности, точности и постоянства процесса.
«Станки HMC серии HXiG от Kitamura имеют размер стола от 250 до 1250 мм с четырехступенчатыми шпинделями с зубчатым приводом со скоростью вращения 8 000 или 12 000 об/мин, которые обеспечивают крутящий момент от 430 до 900 футо-фунтов для резки экзотических материалов», — сказал он. «Эти HMC оснащены двойными шарико-винтовыми парами с масляным охлаждением на коробчатых направляющих, которые проходят индукционную закалку и шлифовку в соответствии с запатентованным процессом Kitamura до шероховатости поверхности менее 4 мкм для превосходного сопряжения, точности и долговременной надежности. Мастерство в технике ручного соскабливания обеспечивает постоянную точность ± 0,002 мм полного хода и повторяемость ± 0,001 мм ».
По словам Сверчека, первое соображение, конечно же, заключается в том, чтобы заготовка соответствовала рабочей зоне станка, будь то загрузка одной детали на стол или загрузка нескольких деталей для увеличения производительности. «К ключевым критериям выбора станка относятся производительность станка (включая общий размер станка), мощность шпинделя, жесткость, количество инструментов, выбор размера магазина, а также конусность и размеры инструмента», — сказал он. «Горизонтальные машины Kitamura имеют стандартный двухпозиционный APC [автомат смены поддонов] с возможностью увеличения количества поддонов с помощью групп поддонов в полевых условиях».
Сверчек добавил, что «возможность автоматизации решает одну из задач, стоящих сегодня перед магазинами, а именно трудность в поиске квалифицированных операторов и рабочей силы, способных справиться с механической обработкой без отключения труда».
Горизонтальные обрабатывающие центры обеспечивают столь необходимую гибкость при обработке деталей. «По сравнению с трехосевым обрабатывающим центром полноценные четырехосевые обрабатывающие центры сводят к минимуму обработку деталей, уменьшая количество переворачиваний детали с шести до двух», — сказал Сверчек. «С четвертой осью на обрабатывающем центре оператор может подходить к детали спереди и с обеих сторон, а затем перемещать ее для окончательной обработки».
Кроме того, Kitamura HMC может быть расширен до полной пятиосевой обработки по мере роста бизнеса цеха. Kitamura предлагает собственное ЧПУ Arumatik-Mi, управляемое пиктограммами, которое совместимо с программированием FANUC. Система управления Arumatik-Mi определяет износ инструмента и автоматически регулирует скорость подачи, отслеживая динамическую нагрузку на шпиндель во время обработки. Срок службы инструмента увеличивается, а время цикла значительно сокращается за счет адаптации к изменению условий резания. Дополнительные преимущества включают сокращение времени простоя и предотвращение сбоев оборудования и/или человеческих ошибок.
Станки для крупногабаритных деталей
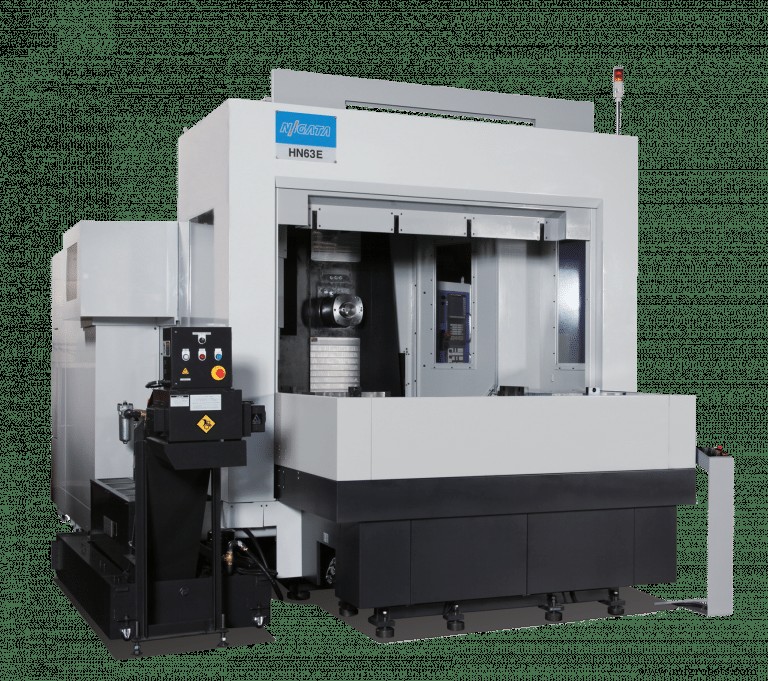
Для обработки крупных деталей компания Methods Machine Tools Inc., Садбери, Массачусетс, предлагает две линии горизонтальных обрабатывающих центров:Niigata и KIWA Japan. «Линия KIWA Japan известна своей высокоскоростной и надежной обработкой, как правило, для мастерских и автомобильных мастерских первого и второго уровня», — сказал Дейл Хедберг, вице-президент по производству. «Линейка продуктов Niigata предназначена для тяжелых условий резания, где требуется низкочастотная обработка и скорость удаления тяжелых металлов».
Ассортимент продукции Niigata включает пятиосевые станки HN50E-5X и HN63E-5X, четырехосевые станки от HN50 до HN1600, от HN800 до HN1600-BAR, а также торцовочные и контурные станки HN800 и HN1000-FC. Платформы станков имеют размер стола от 500 мм до 1600 мм. Размеры конуса шпинделя:CAT-50 BIG Plus, HSK100A, с вариантами вращения шпинделя 6 000, 8 000, 12 000 и 15 000 об/мин.
«Сейчас в отрасли наблюдается тенденция к использованию пятиосевых платформ в горизонтальных обрабатывающих центрах, которые Niigata предлагает в размерах 500 и 630 мм», — сказал Хедберг. «В аэрокосмической и энергетической отраслях Niigata фокусируется на низкочастотной обработке, которая выигрывает от естественных характеристик демпфирования станков. Низкочастотная обработка становится популярной фразой, когда речь идет об обработке титана и инконеля с высоким крутящим моментом для увеличения срока службы инструмента и долговечности шпинделя», — пояснил он.
Способность гасить вибрацию сил резания естественным образом присуща отливкам станка и контактным поверхностям металла по металлу, которые зачищаются вручную для получения шероховатой поверхности. По словам Хедберга, типичные области применения в области энергетики и производства электроэнергии включают фланцы, головки для гидроразрыва и блиски.
При обработке крупных деталей с помощью HMC диаметральная точность перемещения по каждой оси и жесткость особенно важны для достижения точности и повторяемости. Хедберг сказал:«Прелесть пятиосевой обработки заключается в том, что вам не нужно сложное приспособление или специальное приспособление, если только вы не обрабатываете уникальную деталь, для которой может потребоваться приспособление оконного типа или какой-то особый метод зажима».П>
HMC, ориентированные на приложения
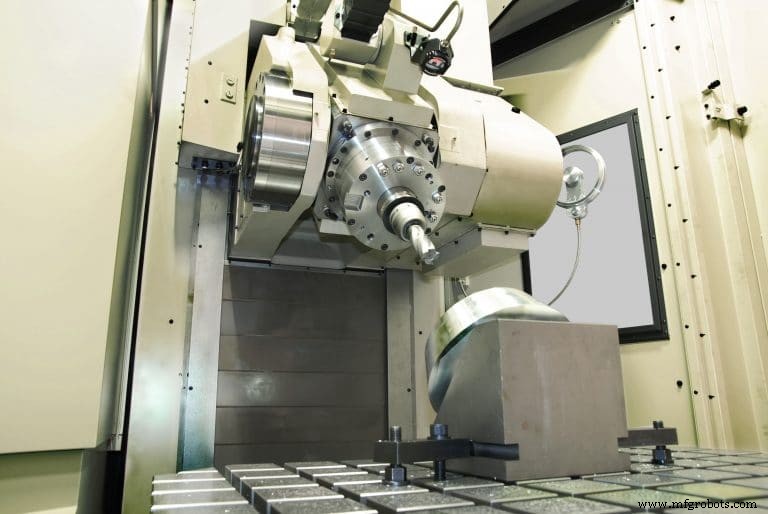
По словам президента Робба Хадсона, компания Mitsui Seiki USA Inc., Франклин Лейкс, штат Нью-Джерси, изучает спрос клиентов на разработку новых горизонтальных обрабатывающих центров, в частности на текущие модели, наиболее востребованные для обработки крупных деталей. «Сегодня спрос на крупные детали определенно исходит от аэрокосмической отрасли, которая в настоящее время является основным драйвером, как в семействе деталей для реактивных двигателей, так и в конструктивных компонентах. Другие целевые рынки включают пресс-формы и штампы, космос, оборону и промышленные газовые турбины», — сказал он.
«Наши горизонтальные обрабатывающие центры с поддонами длиной 1 м и более и конфигурациями сопутствующих столов, которые могут выдерживать вес от 1000 до 10 000 фунтов [453–4 535 кг], считаются нашими станками для крупных деталей. Важно отметить, что все наши машины в этом типоразмере были разработаны благодаря усилиям клиентов. Мы не создавали машины, а затем искали рынки сбыта. Все они основаны на требованиях заказчика к конкретному приложению».
Все станки Mitsui Seiki, предназначенные для производства крупных деталей, имеют одни и те же основные технические характеристики. Хадсон сказал:«Я думаю, что есть две категории:большие детали, которые также требуют удаления большого количества материала, и детали, которые просто неудобны и требуют более легкой резки. Mitsui Seiki работает в секторе крупногабаритных деталей, требующих тяжелой резки прочных материалов. Таким образом, наши станки имеют большую массу, жесткость, большие коробчатые направляющие, шарико-винтовые пары большого диаметра для достаточной тяги, надежный осевой крутящий момент и специальные серводвигатели для перемещения детали в рабочей зоне и обеспечения необходимых сил резания». /Р>
По словам Хадсона, все эти функции, а также контроль и точность конструкции необходимы для обеспечения надлежащей производительности приложения. Он добавил, что приспособление является важным элементом в производстве крупных деталей и часто бывает столь же прочным и весомым, как и обрабатываемая деталь.
Автоматизация стала проще
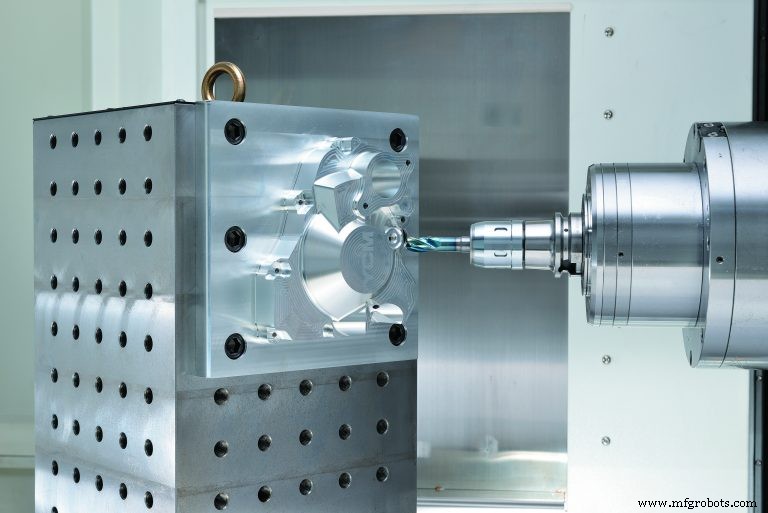
По словам Мэла Гэя, регионального менеджера по продажам YCM Technology (USA) Inc., Карсон, Калифорния, автоматизация машин любого типа сложна, но HMC проще автоматизировать из-за объема их производства.
«Скорость возврата вложенных долларов всегда является главной задачей при покупке HMC», — сказал он. «Популярные размеры — 500/630 мм с минимальной вместимостью 60–120 инструментов для небольших мастерских и 240 инструментов и выше для крупных заводов. Большие возможности инструментов позволяют выполнять более сложные работы с минимальным временем настройки, особенно в конфигурации с несколькими ячейками».
На выставке IMTS компания YCM представила БТР NH500A 6, предназначенный для таких отраслей, как автомобилестроение, которые производят большие объемы деталей. NH500A оснащен шпинделем мощностью 30 л.с., 20 000 об/мин и поддоном размером 500 x 500 мм.
«Производительность начинается с очень жесткого Т-образного основания с ребрами конструкции, — сказал Гей. «YCM сочетает в себе этот фундамент с цельной литой передней бабкой шпинделя и конструкцией колонны с двойными стенками. Шпиндель с прямым приводом оснащен прецизионными керамическими шарикоподшипниками, что обеспечивает более высокую динамику резания и более высокие скорости шпинделя».
По словам Гэя, высокоточные направляющие роликового типа на всех осях обеспечивают высокую скорость 2362 дюймов в минуту (60 м/мин) и подачу при резке до 1575 дюймов в минуту (40 м/мин). Система прецизионной индексации поддонов вмещает APC с шестью поддонами для высокой пропускной способности одного компонента или семейства деталей.
«Все эти функции позволяют использовать новейшие технологии режущего инструмента, улучшать обработку деталей и снижать общую стоимость владения», — сказал он.
Большая часть HMC построена в Америке
DMG Mori, Хоффман Эстейтс, Иллинойс, производит четыре модели горизонтальных обрабатывающих центров на своем заводе в Дейвисе, Калифорния. NHX 4000 и NHX 5000 — это машины третьего поколения с конусом 40 и паллетами 400 и 500 мм; NHX 5500 и NHX 6300 — это машины второго поколения с конусом 50 и паллетами 500 и 630 мм.
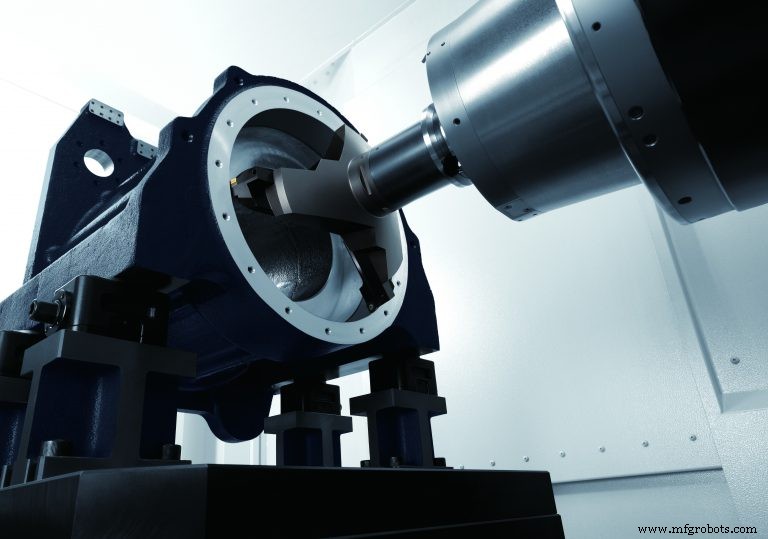
«Наши горизонтальные станки рассчитаны как на тяжелую резку, так и на высокую точность требований наших клиентов в энергетике, аэрокосмической промышленности, промышленном оборудовании и контрактном производстве, — сказал Джон Макдональд, исполнительный вице-президент по развитию и управлению продуктами.
Типичные детали включают большие клапаны и детали турбин для энергетической промышленности; картеры двигателя, дифференциала и трансмиссии в промышленном оборудовании; и конструктивные элементы в аэрокосмической отрасли. Материалы варьируются от титана или нержавеющей стали до чугуна или алюминия — все зависит от области применения.
«Наши клиенты достигают высокой производительности за счет автоматизации, используя системы пулов поддонов для производства с большим количеством номенклатуры или с помощью специальной роботизированной загрузки, используя нашу встроенную гидравлическую систему крепления через стол, которая входит в стандартную комплектацию наших горизонтальных обрабатывающих центров», — сказал Макдональд. «Обработка крупных деталей и тяжелое резание зависят от оптимизированной конструкции станка. Все наши горизонтальные станки имеют полностью оптимизированную структуру конечных элементов, в том числе прочную трехточечную опорную конструкцию из чугуна, шпиндель powerMASTER (станки с конусом 50) и роликовые линейные направляющие. Линейные шкалы входят в стандартную комплектацию всех наших машин, что позволяет нашим клиентам поддерживать высочайшую точность на протяжении всего срока службы машины».
Стандартный шпиндель powerMASTER с конусом 50 имеет скорость 12 000 об/мин, а опциональная высокоскоростная версия — 16 000 об/мин. NHX 6300 также оснащен дополнительным шпинделем с высоким крутящим моментом на 8000 об/мин для тяжелой обработки труднообрабатываемых металлов, таких как экзотические материалы и тяжелый чугун.
Интерфейс управления CELOS от DMG Mori предлагает ряд приложений для оптимизации процесса. В соответствии с инициативами Industry 4.0, интерфейс управления CELOS упрощает и ускоряет все этапы обработки деталей, от идеи до готового продукта, от изготовления отдельных деталей до серийного массового производства.
По словам DMG Mori, приложения CELOS обеспечивают последовательное управление, документирование и визуализацию данных о заданиях, процессах и машинах, а также связывают мастерские и структуры компании более высокого уровня, создавая тем самым основу для последовательного оцифрованного и безбумажного производства. Эту функциональность можно получить даже с офисного компьютера с CELOS PC-версии.
«Мы также предлагаем технологические циклы, которые позволяют нашим клиентам легко реализовать сложные процессы обработки», — сказал Макдональд. «Например, Machine Vibration Control (MVC) позволяет оператору находить стабильные подачи и скорости резания во время тяжелой обработки. С другой стороны, Machine Protection Control (MPC) обеспечивает мониторинг вибрации шпинделя, контроль нагрузки на инструмент и обнаружение столкновений для предотвращения или уменьшения повреждений. Собирая и анализируя эти данные, интерфейс управления CELOS помогает
производителям максимизировать производительность, добиться еще большей точности и увеличить количество часов работы шпинделей в день», — сказал Макдональд.
Возможности строительства
По словам Эррола Баррелла, специалиста по обрабатывающим центрам Okuma America Corp., Шарлотта, Северная Каролина, горизонтальные обрабатывающие центры Okuma, такие как MA-600HII, являются популярным выбором для автомобильной, пресс-форм, энергетической и аэрокосмической промышленности.
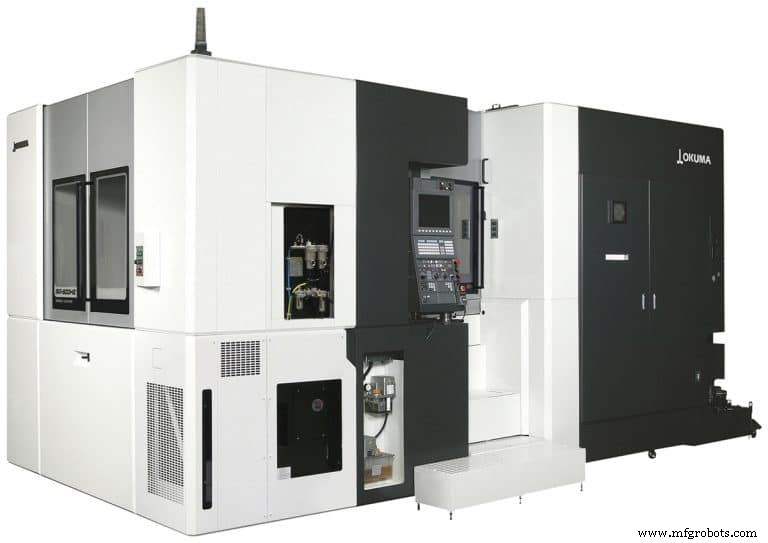
«Они обеспечивают точность и стабильность при обработке крупных деталей благодаря их стабильной термостойкости», — сказал он. «Машины испытываются на предмет их теплового профиля, и данные о возможной тепловой деформации передаются обратно в систему управления в режиме реального времени для любой необходимой компенсации с помощью программного обеспечения Okuma TAS (термостабилизатор оси)».
MA-600HII — это станок с конусом 50, шпинделем с частотой вращения 6000 об/мин и стандартным магазином на 40 инструментов, который можно увеличить до 60 и даже до 285 или 400 инструментов, поэтому он идеально подходит для мастерских или производственного производства. . MB-8000H — это практически та же платформа с 800-мм столом, а следующий размер — MB-10000H с конструкцией «коробка в коробке», а не колонной.
По словам Баррелла, станки Okuma очищаются вручную на каждой сопрягаемой поверхности для повышения точности и производительности в течение более длительного периода времени, снижения затрат и максимальной прибыльности.
Типичные компоненты нефтяных месторождений, такие как корпуса насосов, выигрывают от уникальной возможности Okuma Turn-Cut. «Что касается корпусов насосов, наша функция Turn-Cut позволяет точить фланец на горизонтальных обрабатывающих центрах Okuma», — сказал Баррелл. Turn-Cut — это опция программирования, доступная на Okuma HMC, которая позволяет станку создавать отверстия и диаметры, включающие круглые и/или угловые элементы. Это позволяет пользователям обрабатывать большие несбалансированные детали на той же платформе, на которой выполняются стандартные функции обработки с ЧПУ. Turn-Cut избавляет от необходимости приобретать специальные станки, инструменты, приспособления или дополнительные компоненты.
Turn-Cut не влияет на производительность или долговечность машин. По словам Окумы, когда требуется тяжелое фрезерование, Okuma HMC, оснащенный Turn-Cut, по-прежнему может работать как никогда. Самое главное, Turn-Cut позволяет выполнять обработку без необходимости использования дополнительного станка для токарной обработки. Такие детали, как клапаны, трубы или детали коллекторного типа, идеально подходят для точечной резки.
На выставке IMTS компания Okuma продемонстрировала автоматизированную систему вертикального поддона Tower Pallet. Он имеет двенадцать поддонов размером 20 x 20 дюймов (500 x 500 мм), каждый с максимальной грузоподъемностью 1100 фунтов (500 кг) на двух уровнях. По словам компании, интегрированная система APC обеспечивает быструю загрузку/разгрузку благодаря системе поворота с серводвигателем для работы без освещения.
Полная четвертая ось, автоматизация
Корпорация Mazak, Флоренция, Кентукки, предлагает полную линейку HMC в дополнение к своим большим вертикальным обрабатывающим центрам мостового типа, пятиосным вертикальным станкам с токарной обработкой (INTEGREX) и пятиосевому станку VARIAXIS с цапфой, в зависимости от продукта. специалист Джаред Лейк.
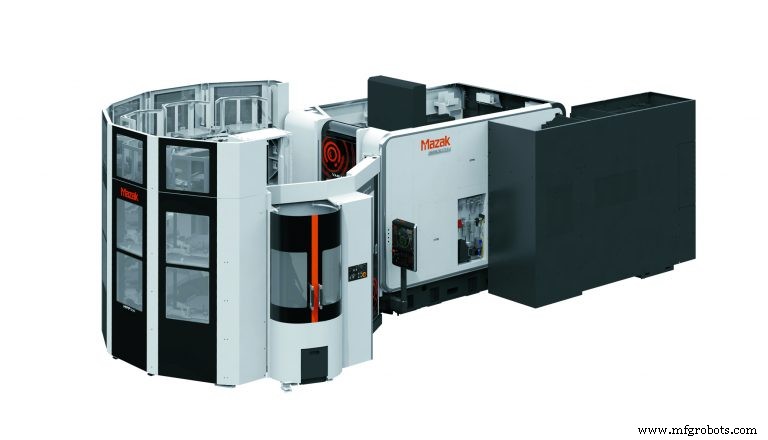
«Обработка крупногабаритных деталей шпинделями с конусом 50 выполняется на станках со столами/поддонами от 800 до 1600 мм, в том числе на нашем HMC серии Quill со столами от 1250 до 1600 мм, а также на нашем HCN-6800 со столом 630 мм для большие блоки двигателей для автомобильных и энергетических компонентов».
Линейка с конусом 50 включает три дополнительные модели серии (HCN-8800, HCN-10800 и HCN-12800) со стандартными 10 000 об/мин и дополнительными 8000 об/мин и 6000 об/мин шпинделями мощностью 50 л.с. для обработки титана, нержавеющей стали с более высоким крутящим моментом. и другие экзотические металлы. По словам Лейка, для обработки крупных алюминиевых конструкционных деталей в аэрокосмической и полупроводниковой промышленности доступен шпиндель со скоростью вращения 16 000 об/мин.
По его словам, Mazak предлагает полноценные четырехосевые HMC, на долю которых приходится около 60% всех HMC, продаваемых компанией. Четырехосевые HMC со стандартным позиционированием 0,0001° позволяют поворачивать двух- или четырехстороннее приспособление для сверления сложных углов, индексировать на 90° и поворачивать назад. Полный четырехосевой режим позволяет создавать контуры и может использоваться для сокращения времени цикла, что упрощает обработку, особенно для сложных деталей.
Доступная автоматизация включает систему Mazak PALLETECH, которая может вместить большое количество машин в конфигурации FMS и рельсового робота, а также новую систему автоматизации Mazak Multi-Pallet Pool (MPP) для одной машины для станков шириной 400 и 500 мм. «Мы автоматизировали HMC с помощью шестиосевых роботов FANUC на рельсах, которые будут размещать детали на разных станциях для лазерной маркировки, промывки и удаления заусенцев», — сказал Лейк.
Mazak HCN-5000 HMC теперь доступен с системой MPP компании, базовым решением автоматизации в компактном корпусе. По словам Лейка, магазины, в которых недостаточно места для размещения обычного линейного горизонтального накопителя поддонов, теперь могут автоматизировать производство для непрерывного производства.
MPP предлагает удобство более крупной системы Mazak PALLETECH, занимая до 30% меньше места. По его словам, серводвигатели на каждой оси, а также двухуровневое расположение поддонов, при котором каждый поддон находится на одинаковом расстоянии от центра накопителя, обеспечивают быструю и стабильную загрузку/разгрузку.
Разработанный для расширения по мере роста производственных потребностей, производители могут переконфигурировать стандартный накопитель системы на 10 поддонов для размещения 16 поддонов для увеличения производительности. Имея в виду, что HCN-5000 может работать с крупными и тяжелыми деталями, Mazak сделала этот последний MPP самой большой версией с точки зрения производительности по размерам деталей. Система вмещает поддоны площадью 500 кв. мм, на которых размещаются заготовки диаметром до 800 мм и высотой 1000 мм.
Система управления автоматикой
- Видео горизонтального обрабатывающего центра
- Различные типы станков с ЧПУ
- Разнообразие автоматизации станков на выставке
- Уроки высокопроизводительной обработки:не забывайте о держателях инструментов
- Niagara Gear расширяет собственные возможности обработки
- Заказы на станки сократились в сентябре
- Fuji представляет многозадачную машину
- Методы станков для приобретения станков Коха
- Что такое горизонтально-сверлильный станок?
- Понимание процесса обработки и станка