Переосмысление систем управления для многоскважинных площадок
Требования к данным и управлению вызывают потребность в модульной, масштабируемой архитектуре управления.
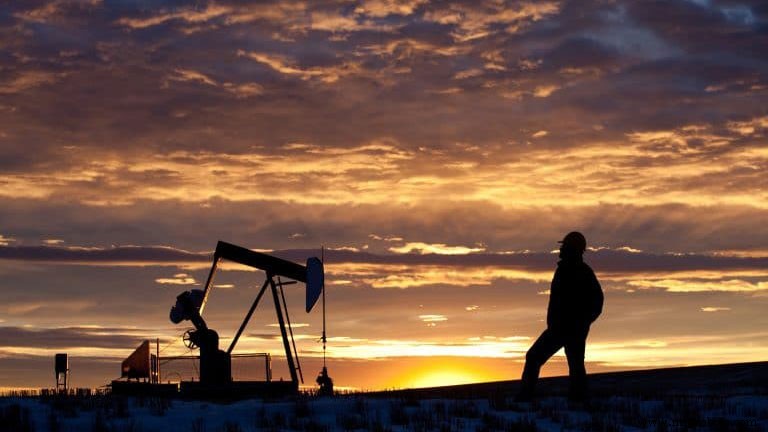
Благодаря достижениям в области бурения нефтегазовые операции перешли от простых кустовых площадок с одной скважиной к более сложным многоскважинным площадкам.
Сегодня многие производители используют технологии гидроразрыва пласта и бокового бурения для размещения 10 и более скважин на одной кустовой площадке. Некоторые операторы даже доводят свою деятельность до 52 скважин на одной кустовой площадке.
Эти усовершенствования не только увеличили добычу скважин, но и создали совершенно новые производственные возможности в нетрадиционных районах. Они также позволили производителям нефти и газа сократить свои операционные затраты.
Однако, несмотря на все преимущества многоскважинных площадок, их существенное увеличение размера и области применения создало новую проблему. Более высокая плотность нескольких скважин на одной площадке увеличивает количество оборудования, необходимого на площадке, и приводит к гораздо большим требованиям к данным и контролю.
Традиционные архитектуры управления, которые использовались десятилетиями, доведены до предела своих возможностей и могут просто перестать быть устойчивыми. Вместо этого необходимы более совершенные системы управления для работы с масштабируемой архитектурой, необходимой для современных кустовых площадок.
В результате как операторы, так и производители оборудования, которые их поддерживают, теперь должны изменить, если не радикально, свой подход к системам управления для этих многоскважинных площадок.
Эволюция технологии RTU
Компании, занимающиеся разведкой и добычей нефти и газа, десятилетиями полагались на технологию удаленных терминалов (RTU) для управления буровой площадкой. Первоначально стоимость внедрения RTU и проблемы с их программированием ограничивали устройства простым сбором данных и управлением.
Однако со временем в RTU появилось больше функций, включая ввод-вывод, связь и программирование IEC-61131. Эти возможности позволили операторам нефтегазовой отрасли отслеживать больше точек данных, регистрировать историю и аварийные сигналы, а также добавлять в RTU более сложные вычисления. Производители оборудования и инженерные фирмы также приступили к разработке специальных приложений для управления механизированной добычей на устье скважины с использованием собственных микропроцессорных контроллеров.
В конце концов, практически каждый производитель механизированной добычи разработал свой собственный RTU для контроля и оптимизации соответствующих решений. Инженерные фирмы также разработали свои собственные методы с немного отличающимися приложениями RTU, в то время как производители контрольно-измерительных приборов представили новые инструменты для измерения практически любой требуемой точки процесса.
Однако в последнее время возросшие требования, связанные с операциями на многоскважинной площадке, стали превышать возможности технологии RTU.
Устройства доведены до предела
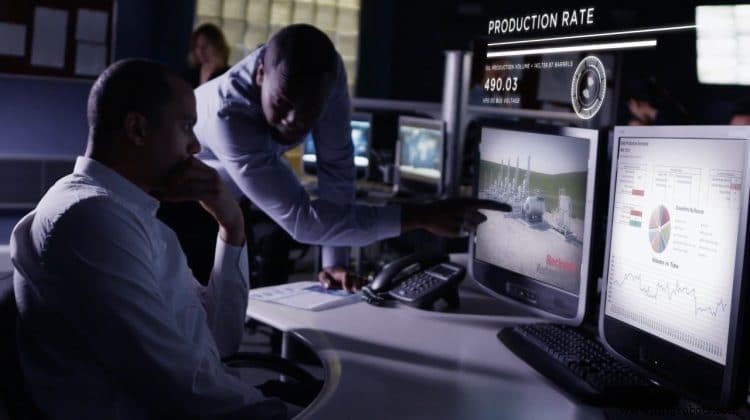
Каждая скважина на многоскважинной площадке требует механизированной добычи, измерения расхода, управления оборудованием и измерения уровня. Это создает больше запросов на ввод-вывод и управление, чем может обработать один RTU. В результате производители нефти и газа вынуждены приобретать дополнительные RTU и распределять управление приложениями и площадками по нескольким установкам.
Производители нефти и газа успешно внедрили несколько контроллеров RTU на кустовую площадку, но они сталкиваются с некоторыми общими проблемами с этими архитектурами. Вот некоторые из этих проблем:
- Управление изменениями нескольких конфигураций или программ на каждой кустовой площадке.
- Управление связью множества удаленных терминалов на месте (например, одноранговая связь).
- Связь SCADA с оборудованием нескольких поставщиков.
- Ненадежное выполнение пользовательских программ в RTU.
Окончательный спрос на устройства RTU возникает, когда требуется гораздо более масштабное управление многоскважинной площадкой. Это может включать в себя работу с 10 или даже несколькими десятками скважин на одной кустовой площадке. Более высокая плотность скважин на площадке также увеличивает потребность в оборудовании на площадке. Например, многие из этих кустовых площадок имеют собственный сепаратор.
Также становится более экономичным устанавливать компримирование трубопроводов, установки улавливания паров (ВРУ) и башни ВРУ из-за большого количества природного газа, добываемого на площадке. На этих кустовых площадках также часто можно увидеть сдаваемые в аренду автоматические узлы коммерческого учета (LACT), машины для перекачки воды и машины для впрыска химикатов.
Кроме того, многие производители нефти и газа вкладывают средства в электрические здания, известные как электрические дома. В этих зданиях размещаются главные распределительные сети, центры управления двигателями (MCC), сетевые коммутаторы и источники бесперебойного питания (UPS), и они часто контролируются окружающей средой.
Все эти увеличения — в оборудовании, полевых приборах и приложениях — только усугубляют общие проблемы с архитектурами RTU.
Они также создают новые проблемы в сфере обслуживания и поддержки. Использование нескольких RTU привело к созданию множества конфигураций приложений и программ для их обслуживания. Это также вынуждает операторов нефтегазовой отрасли работать с несколькими поставщиками.
Кроме того, наличие нескольких устройств от разных поставщиков также требует от сотрудников дополнительной подготовки и опыта для их поддержки. В то время как некоторые производители полностью укомплектованы достаточно обученным персоналом для обслуживания систем управления скважиной, многие этого не делают. Эти производители должны полагаться на поддержку производителя или контрактную инженерную поддержку для обслуживания своих систем управления.
Переход к модульным масштабируемым системам управления
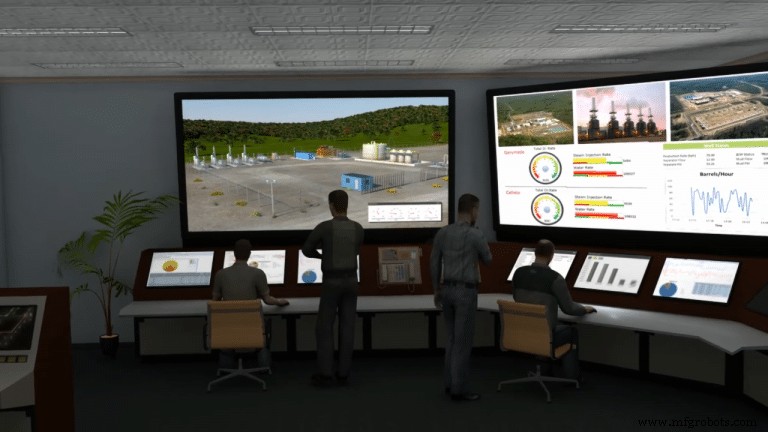
RTU десятилетиями выполняли свою роль в удовлетворении простых требований к управлению, простом взаимодействии полевых устройств и простой связи. Но их уже недостаточно в сегодняшних более сложных операционных средах.
Многие производители нефти и газа, которые столкнулись с общими проблемами RTU, нашли жизнеспособное альтернативное решение в виде модульного и масштабируемого программируемого логического контроллера (ПЛК). Технология ПЛК годами доводилась до совершенства в средах управления промышленными процессами, которые столь же суровы, как добыча нефти и газа.
ПЛК предлагают ряд преимуществ по сравнению с RTU:
- Модульность: Некоторые RTU поддерживают модульное оборудование. Но сбалансировать требования модуля с требованиями приложений и управления в RTU намного сложнее, чем в ПЛК. Кроме того, сторонние модули для удаленных терминалов обычно недоступны, поскольку удаленные терминалы не являются открытой архитектурой, в отличие от ПЛК. полевые приборы. Поддержка связи для многих различных типов сетей также поддерживается благодаря модульной конфигурации.
- Масштабируемость: Это важно при рассмотрении того, как собирается многолуночная прокладка. Одна скважина часто устанавливается на многоскважинной площадке, и лишь спустя месяцы или даже годы вводятся в эксплуатацию дополнительные скважины и оборудование.
В таких случаях производители оборудования хотят иметь возможность создавать блоки оборудования за пределами площадки, а затем просто подключать их и настраивать на кустовой площадке. Они хотят сократить потребность в рытье траншей, протягивании проводов, заделке проводов, монтаже панелей и приборов в полевых условиях, чтобы сократить расходы. В этом случае требуется масштабируемость как в программном, так и в аппаратном обеспечении, и именно это предлагает технология ПЛК. - Простота программирования: Исторически ПЛК рассматривались как чистый холст для автоматизации и управления. Только инженерные фирмы или опытные программисты знали, как начать с нуля и разработать систему управления, необходимую для ПЛК.
Однако современные ПЛК имеют библиотеки предварительно разработанного и задокументированного кода, который можно быстро добавить практически в кратчайшие сроки. мода перетаскивания. Некоторые поставщики ПЛК также имеют предварительно разработанные библиотеки для разведки и добычи нефти и газа, которые можно настроить на месте. Производителям нефти и газа нужно только включить и настроить необходимые данные из ЧМИ для запуска ПЛК или добавить оборудование в существующую систему.
Это может устранить необходимость в ком-то, например, в скважине технический специалист со специальными знаниями, чтобы знать среду программирования и писать новый код при добавлении оборудования.
Более того, изменения в программе и конфигурации могут быть сделаны онлайн в ПЛК без остановки процесса. RTU традиционно не могут принимать такие изменения без отключения и загрузки. Это является важным отличием современной многоскважинной площадки, поскольку отключение системы управления приводит к потере добычи. - Функции удаленного ввода-вывода: У удаленных терминалов традиционно нет собственных функций удаленного ввода-вывода, но у ПЛК они есть. Это может снизить затраты на установку. Кроме того, когда на объект добавляются блоки оборудования, они могут поставляться с предварительно смонтированными и подключенными устройствами ввода-вывода и инструментами. Для запуска этих модулей достаточно просто подключить кабель Ethernet к коммутатору и настроить ввод-вывод в контроллере.
Улучшение управления жизненным циклом
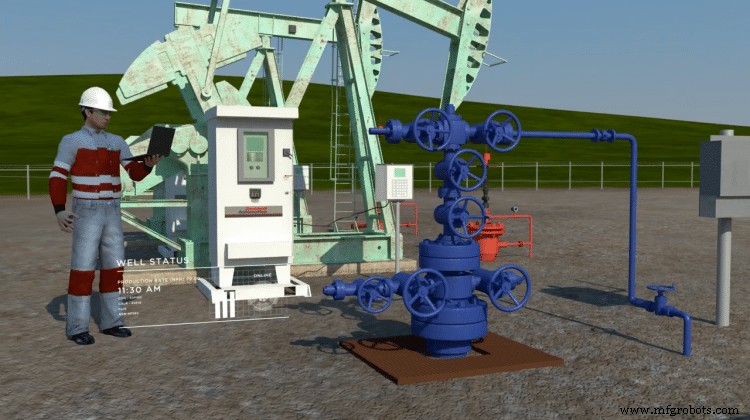
Управление жизненным циклом кустовой площадки может стать серьезной головной болью для эксплуатационных групп. Скважины могут находиться в различных состояниях потока, включая естественное течение, погружной насос с электронным управлением (ЭЦН), винтовой насос с винтовой подачей (ШВН) и штанговый насос. А тип потока и жизненный цикл могут сильно различаться.
Несколько RTU часто используются только для управления различными жизненными циклами скважины. Замена RTU означает замену коммуникационных драйверов в системе SCADA, поскольку физическое RTU на скважине — это аппаратное обеспечение нового поставщика. А настройка RTU для управления приложением и установка этого оборудования в системе часто является кропотливым процессом.
Кустовая площадка на базе ПЛК может существенно упростить эту задачу, обеспечив эффективность и оптимизацию, о которых операторы даже не подозревали.
Используя модульную и масштабируемую аппаратную архитектуру ввода-вывода, которую предоставляет ПЛК, операторы могут устанавливать модули ввода-вывода прямо там, где расположены контрольно-измерительные приборы, и отправлять эти данные в ПЛК. И независимо от того, какой подход к проектированию ввода-вывода использует производитель нефти или газа, аппаратное обеспечение в системе управления останется неизменным, для связи с системой SCADA будут использоваться одни и те же драйверы, а система будет оставаться в сети и контролировать все приложения, как и раньше. обновления сделаны. Все это время остается поддерживать только одну программу ПЛК.
Существует также вопрос поддержки приложений поставщика. Как уже упоминалось, многие поставщики создают свои собственные приложения для различных производственных нужд, и каждый поставщик обычно использует свой тип RTU. В результате поставщики обычно могут поддерживать только несколько конкретных приложений, а не все из них.
Поддержка поставщиков ПЛК для многоскважинных площадок растет с каждым днем. Сюда входит поддержка приложений для управления оборудованием, механизированной добычи и измерения расхода. Автоматизация оборудования легко осуществляется с помощью богатой среды программирования и широкого спектра модулей ввода-вывода и связи. Измерение расхода также поддерживается измерением расхода, совместимым с AGA и API, поддержкой калибровки и отчетами о коммерческом учете в системы SCADA. Приложения для механизированной добычи, хотя и не так распространены в ПЛК, также быстро разрабатываются для поддержки всех типов механизированной добычи.
Наконец, многие производители нефти и газа выразили недовольство тем, что приложения RTU являются «черным ящиком». Это означает, что система разработана с определенными входными данными, которые предназначены только для управления определенными выходными данными.
Подход «черного ящика» препятствует гибкости, поскольку не позволяет производителям нефти и газа изменять способ функционирования системы. В результате им либо приходится менять поставщиков для удовлетворения своих потребностей, либо просто жить с имеющейся у них технологией, зная, что она работает не так эффективно, как им нужно.
С другой стороны, систему на основе ПЛК можно модифицировать в полевых условиях с помощью обычных промышленных инструментов (IEC-61131), что обеспечивает гораздо большую гибкость.
Принятие новых норм
ПЛК долгое время рассматривался как решение, больше подходящее для производственных предприятий, чем для управления кустовыми площадками. Но сегодняшние кустовые площадки — это, по сути, небольшие заводы. У них есть здания с экологическим контролем, коммунальные услуги или мощность генератора, а также гораздо более высокие требования к данным и контролю.
Это делает их идеально подходящими для ПЛК. Система управления многоскважинной площадкой, использующая модульные и масштабируемые возможности ПЛК, может сократить затраты и время установки, увеличить время безотказной работы и упростить управление жизненным циклом.
Зак Мунк (Zack Munk) – менеджер по развитию нефтегазового бизнеса Rockwell Automation на суше.
Система управления автоматикой
- Создание гибких производственных систем для Industrie 4.0
- ASM Assembly Systems использует робота Rethink Robotics Sawyer для контроля качества
- Рекомендации по панелям управления AFD
- Преимущества встроенных технологий для модульного проектирования
- Простые решения для старых систем автоматизации
- Предприятия устанавливают сроки для интеллектуальных систем
- 10 лучших рабочих процессов для производителей
- Локальные и глобальные системы управления производством
- Преимущества использования VIA в пэдах
- Marposs представляет модульную систему управления BLÚ LT для станков