Системы линейных поддонов:прямой путь к прибыльности?
Усовершенствованное программное обеспечение существенно повышает эффективность систем линейных поддонов
Адам Хансел, директор по системам и продажам, DMG Mori (Hoffman Estates, IL) прекрасно резюмирует это:«Зайдите в любой магазин. Спросите их, хотят ли они автоматизировать. Ответ положительный. 100%». Но какая автоматизация? И какие машины и процессы? Для самых разных компаний логичным ответом является линейная система поддонов, объединяющая несколько металлорежущих станков и, возможно, дополнительные операции. С другой стороны, "логичный" не всегда означает "легкий" или "беспроблемный".
Не путайте FMS с системами пула поддонов
Базовая система линейных поддонов, также известная как гибкая производственная система (FMS), автоматизирует загрузку и разгрузку одного или нескольких обрабатывающих центров заготовками из центрального хранилища. Заготовки перемещаются по прямому рельсу, который перевозит транспортное средство с дополнительными осями движения, которые позволяют ему перемещать заготовку в машину и на ее стол, а затем снова выводить после завершения. Операторы устанавливают задания на центральной станции, а не на отдельных машинах, а центральный компьютер контролирует распределение и выполнение работы.
В наиболее распространенной конфигурации заготовки крепятся болтами к приспособлениям, которые, в свою очередь, крепятся болтами к однородным поддонам. Это максимизирует гибкость системы, поскольку любое задание может быть передано на любую машину в любое время, если машина сконфигурирована для этого стандартного поддона. Еще одной ключевой особенностью систем линейных поддонов является возможность их расширения после первоначальной установки за счет включения дополнительных станков, дополнительных складских помещений и даже операций, не связанных с механической обработкой, таких как проверка. Некоторые системы имеют 10 и более обрабатывающих центров и десятки полок для поддонов, расположенных на трех уровнях.
Таким образом, линейная система поддонов отличается от системы пула поддонов, последнюю из которых можно рассматривать как «неразумное расширение машины», как говорит Боб Бальдиззи, специалист по системам и большим машинам, Doosan Machine Tools America (Pine Brook, Нью-Джерси) объяснил. «В системе пула поддонов система управляется дополнительным программным обеспечением на самой машине. Обычно вы ограничены тем, что сообщаете программному обеспечению, какая программа связана с каким поддоном в пуле, и в какой последовательности вы хотите, чтобы эти поддоны проходили через машину. Вот и все. Плана производства нет. Нет управления данными. Нет отчетности. Это просто более крупное расширение системы паллет для машины». Системы пулов поддонов обычно представляют собой круговые конструкции, хотя они могут быть и линейными, что может внести путаницу.
«Системы пула поддонов, которые я видел, обычно имеют одну и ту же деталь на всех пяти или шести поддонах», — сказал Дэвид Суика, президент Fastems LLC (Западный Честер, Огайо). «Если вы хотите заменить детали, вам, как правило, придется изменить инструменты внутри станка, программу обработки деталей и любые смещения, необходимые для каждой детали. Пулы поддонов подходят для серии одной и той же детали. Но если вы хотите производить именно то, что вам нужно, и в количествах, которые вы можете продать, линейная система поддонов, как правило, лучше».
Использование шпинделя более 90%
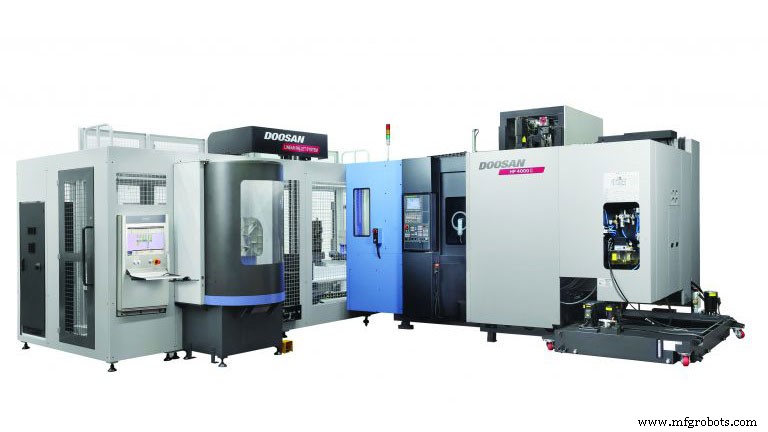
Ситуации бывают разными, но кажется, что ни один механический цех не достигает использования шпинделя более 50–60% без FMS, в то время как любой, кто использует его правильно, увидит показатели 90% или более. А в некоторых случаях разница еще больше. Гензель сказал, что «использование шпинделя, вероятно, составляет 30% или меньше в большинстве случаев, если у них есть несколько машин с ручной подачей. Просто невозможно выполнять смену деталей, приспособлений и эффективно планировать большое количество ресурсов в буфере обмена». Как объяснила Суика:«Большая часть времени простоя станка вызвана людьми… ожиданием инструмента… выяснением программы… ручным вводом коррекции инструмента. Потратив этот час на настройку, вы уже никогда не вернете его в работу».
Это указывает на самое большое и значительное улучшение линейных паллетных систем за последние несколько лет:программное обеспечение. В той или иной степени все поставщики FMS предлагают программное обеспечение для планирования пропускной способности, позволяющее максимально увеличить пропускную способность системы. Гензель описал типичный сценарий:«Допустим, у вас есть несколько станков, 180 инструментов в каждом магазине, 24 приспособления и определенные рабочие места, которые должны выполняться для выполнения ваших контрактов. Вы устанавливаете такие параметры, как приоритет заданий и количество, которое вам нужно в определенное время. Или скажем, вы строите машину. Вы не стали бы производить две оси и три колеса. Вам понадобятся четыре колеса. Таким образом, вы можете указать программному обеспечению производить размеры партии. В любом случае программное обеспечение автоматически рассчитывает, как правильно использовать ваши ресурсы, чтобы получить необходимое вам производство. Если вы правильно спланируете и подготовите приспособления и инструменты, а затем позволите программному обеспечению сделать всю работу за вас, производительность 90–95% вполне достижима».
Хорошо подходит для работы в магазинах… и не только
Кому выгодна ФМС? Любой, от небольшой ремонтной мастерской до предприятия, производящего 100 000 или более деталей в некоторых ситуациях. Джон Эйнбергер (John Einberger), менеджер по продуктам Makino Inc. (Мейсон, Огайо), сказал:«Лучшее место для этой технологии — это тот, у кого есть множество продуктов для запуска в несколько случайном порядке с относительно короткими производственными циклами. Выполняя наладку вне обрабатывающего центра, вы увеличиваете загрузку шпинделя.
«Но есть также заявки на более высокие объемы производства среди людей, у которых есть сезонное производство», — продолжил он. «Например, скажем, они производят 80 000 чего-то в год, но делают это только в течение трех месяцев, а затем запускают вариант или что-то другое в течение следующих четырех месяцев. Индустрия силовых агрегатов для транспортных средств для отдыха соответствует такой схеме производства. В межсезонье они производят то, что им нужно в сезон, например, моторы для лодок при продаже снегоходов и моторы для снегоходов при продаже лодок. Наша FMS оказалась очень полезным инструментом для клиентов в таких ситуациях с большими объемами».
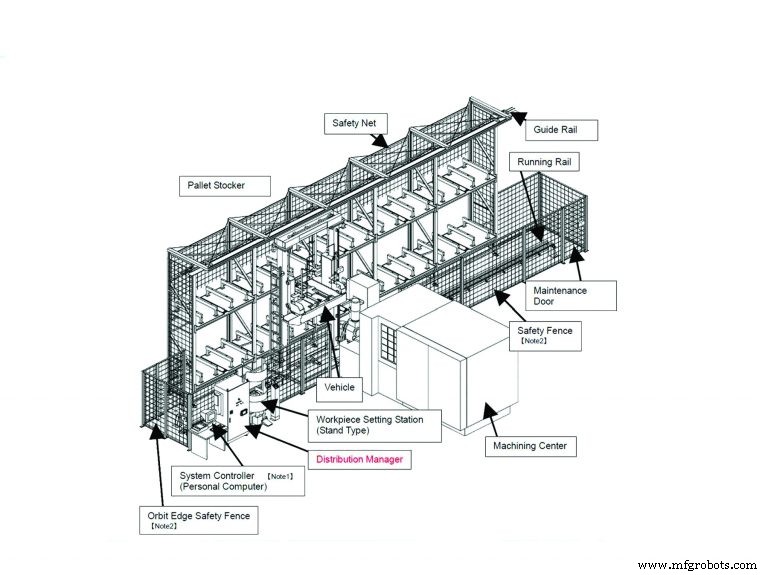
Гензель добавил, что «люди, которые используют всего пять или шесть разных номеров деталей, довольно часто помещают их на линейную систему поддонов. Это потому, что в такой системе много избыточности. Горизонтальные станки обычно имеют большие инструментальные магазины, которые позволяют размещать в магазине избыточные инструменты для работы в более длительные смены. Если инструмент сломается или износится, вы можете просто перейти к следующему». С другой стороны, сотрудники Liebherr (Салин, Мичиган) отметили, что ячейки для обработки поддонов наиболее рентабельны, когда общее время цикла для всех деталей на данном поддоне превышает пять минут. В противном случае вы потеряете время, ожидая, пока транспортное средство поменяет поддон.
Чтобы дать вам некоторое представление о том, насколько популярными стали эти системы, Айнбергер сказал, что за последние 20 лет только в Северной Америке компания Makino установила 575 своих систем линейных поддонов.
Не только для горизонталей
Традиционно системы линейных поддонов обычно соединяли горизонтальные обрабатывающие центры, потому что «горизонтальный станок почти всегда поставляется с устройством смены поддонов», — объясняет Бальдиззи из Doosan. «У вас всегда есть второй поддон в зоне погрузочной станции, которую — в автономном режиме — оператор использует для загрузки и выгрузки деталей во время работы машины. Это преимущество FMS, поскольку кран может выполнять погрузку и разгрузку с погрузочной станции, не прерывая цикл обработки. Типичный вертикальный обрабатывающий центр не имеет этого, как и большинство пятиосевых станков, хотя производители, такие как Doosan, теперь оснащают пятиосевые станки устройствами смены паллет, которые можно подключить к FMS».
Помимо смешивания типов обрабатывающих центров, в FMS также можно интегрировать другие функции. Вы также можете интегрировать станки от разных производителей, хотя в этом случае вам, возможно, лучше работать с «независимой» компанией по автоматизации, такой как Fastems:«У нас может быть станок марки X для черновой обработки, станок марки Y для жестких допусков. приложение, Zoller с автоматической записью коррекции на инструмент, КИМ, промывочная станция и система удаления заусенцев — все это полностью интегрировано», — сказал Суйка. «Наше программное обеспечение может даже автоматически управлять коррекцией инструмента и данными контроля».
Некоторые из этих вариантов требуют робота на одной или нескольких станциях или замены традиционного транспортного средства FMS роботом на рельсах. Эйнбергер сказал, что Макино предлагает последний гибрид «как ответ на некоторые требования, прежде всего в области аэрокосмической конструкции. Некоторые из этих клиентов хотят автоматически загружать детали в станок с помощью робота на рельсе, потому что они хотят иметь возможность начать с загрузки детали на плоскую поверхность, а затем взять дополнительное приспособление и загрузить его в горизонтальный обрабатывающий центр.
«Этот подход также очень удобен для многооперационных деталей, где первая операция может быть четырехосевой операцией, а вторая операция — пятиосевой операцией в одном и том же обрабатывающем центре», — продолжил он. «Таким образом, первый поддон на обрабатывающем центре будет четырехосным надгробием, которое принимает деталь на опорной плите, а второй поддон на том же обрабатывающем центре будет на столе с пятой осью, который принимает ту же деталь на той же опорной плите для последующая пятиосевая операция. Робот на рельсовых системах заполняет пробел между FMS для обработки поддонов и дискретным роботом для обработки деталей».
С другой стороны, Бальдиззи предупредил, что получение одного вида гибкости приводит к потере другого. «Мы начинаем видеть потребность в адаптации к различным поддонам, например, выполнение некоторых функций на горизонтальном, а других — на пятиосевом станке с возможностью поворота, что требует другого поддона. Плюс в том, что все эти машины, необходимые для выполнения операции, можно поставить на ФМС. Минус в том, что вы теряете часть гибкости FMS, потому что программное обеспечение должно следить за тем, чтобы этот поддон работал только на этой конкретной машине в это конкретное время. В то время как если у вас есть несколько одинаковых станков на FMS, работа, закрепленная болтами на поддоне, может быть отправлена куда угодно, когда угодно и как угодно».
Затраты и проблемы
По словам Айнбергера, стоимость первоначальной FMS, включая рельсовую систему, транспортное средство, рабочую станцию и стойки для хранения поддонов, составляет примерно две трети стоимости данного обрабатывающего центра без учета приспособлений. Так что, учитывая обещание удвоить пропускную способность, это хорошая окупаемость. Но Гензель сказал, что «хотя людям действительно нравится идея иметь много поддонов, они иногда недооценивают стоимость крепления. Поэтому, когда они принимают решение о том, какие машины купить, реальная стоимость крепления иногда не учитывается, что может помешать им использовать систему в полной мере. Например, вы получаете преимущество от работы без света или отказа от третьей смены, только если вы можете загрузить достаточно работы, чтобы машина работала в течение восьми или более часов».
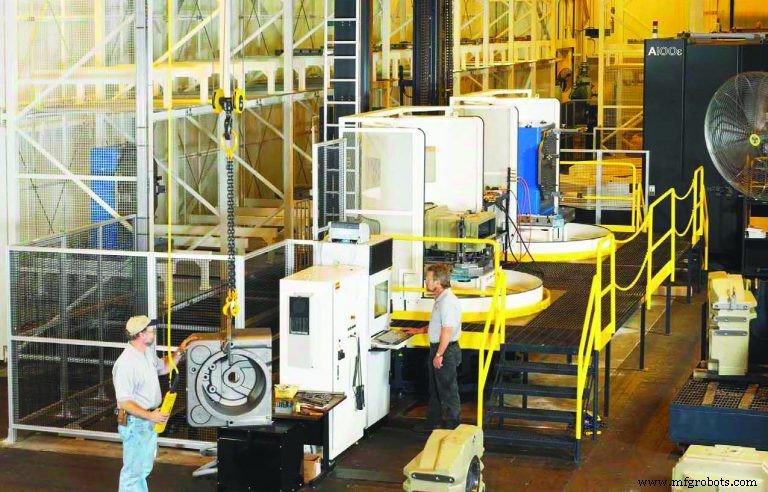
Тем не менее, все согласны с тем, что самая большая проблема с FMS — это функционирование. Как говорит Suica:«Это то же самое, что и ваш компьютер:мусор на входе равен мусору на выходе. Если у вас есть хорошие программы, смещения инструмента известны; если у вас есть свое расписание, это работает очень хорошо. Самое главное для большинства компаний — это дисциплина, необходимая для того, чтобы убедиться, что они готовы. Это ничем не отличается от дисциплины, которую каждая компания вводит в свой бухгалтерский отдел. Вы сопоставляете счета, проверяете их правильность, убеждаетесь, что платите налог. Это непросто, но точно выстроено и завершено. Вы можете сделать то же самое на производстве и интегрировать его, и вы можете удалить человеческий фактор, который вызывает ошибку».
Suica также предупредил, что «большинство линейных поддонов и роботизированных систем, как правило, представляют собой островки автоматизации. Они знают то, что знают, и они не связаны ни с чем внутри вашей операции. У вас может быть пакет ERP [планирование ресурсов предприятия], который отслеживает ваши заказы, потребление сырья и так далее. Вы потратили много денег на инструменты, определение смещения инструмента и системы измерения. Но поток информации между всеми этими системами по-прежнему остается ручным». Это относительное отсутствие интеграции не позволяет компаниям добиться значительной экономии рабочей силы.
Суика сказал, что нередко бывает так, что восемь или девять машин работают всего с несколькими людьми, если вы полностью интегрируете эти системы. «Сейчас мы работаем над системой, состоящей из восьми машин, которыми будут управлять три человека, один из которых просто выполняет проверку, потому что они не хотят автоматизировать это. Она будет работать в две смены, поэтому на этой линии будет шесть человек, а сейчас 14 человек. Но для этого вам нужен высокий уровень системной интеграции, иначе вам все равно понадобится куча людей, которые будут указывать автоматизации, что делать. Интеграция и программное обеспечение являются ключевыми». Так же как и обучение и поддержка, поэтому DMG Mori, Makino и другие компании имеют специальные группы и средства автоматизации.
Однако программное обеспечение не решает всего. Бальдиззи отметил, что механическая надежность имеет первостепенное значение:«Если вы подключите станок — или, что более важно, несколько станков — к FMS, и он выйдет из строя, использование шпинделя этих станков упадет до нуля. Помните, что место, где раньше стоял оператор для загрузки горизонтального обрабатывающего центра, теперь заключено в FMS. Кнопки исчезли. Вероятность того, что вы сможете эффективно загружать и выгружать детали в эту машину вручную, очень мала. Так что загляните под капот, чтобы убедиться, что FMS механически способна обеспечить 90% времени безотказной работы».
Для высококачественных строителей это включает в себя подачу трехфазного высоковольтного питания через шину над транспортным средством, как третий рельс метро, без движущихся частей, кроме точки контакта. «Менее надежные системы привязывают транспортное средство к ряду кабелей в кабельной трассе, которая следует за транспортным средством, когда оно движется вперед и назад. Это вызывает точки усталости, поскольку тросы постоянно изгибаются», — сказал Бальдиззи. «Во-вторых, мы используем оптические глазки, заключенные в туннель, для передачи данных, которая должна происходить между сервоприводами, двигателями, системой управления и т. д., что устраняет необходимость в этих кабелях.
«Я также хотел бы проверить, есть ли в FMS каналы для охлаждающей жидкости, воздуховоды и трубопроводы, чтобы убедиться, что любая охлаждающая жидкость, которая остается на поддонах после их помещения на хранение, извлекается и возвращается либо в баки охлаждающей жидкости машины, либо в центральный репозиторий, вместо того, чтобы беспорядок на вашем этаже», — заключил Бальдиззи.
Система управления автоматикой
- Швейная машина
- Infineon запускает монолитно интегрированный линейный датчик Холла для систем ASIL D
- Timken приобретает производителя решений для автоматизации Intelligent Machine Solutions
- ZF представляет новую кабину SHI
- Как работают системы SCADA?
- Встроенные системы и системная интеграция
- Возможности повышения энергоэффективности насосных систем
- Устройства смены паллет рассчитаны на большие объемы и жесткие допуски
- Практические подходы к автоматизации
- Демистификация машинного обучения