Перезагрузка задней стенки:универсальная, буксировка на липкую ленту к детали из углепластика
В начале нынешнего продвижения композитов из углеродного волокна в автомобилестроение производитель BMW Group (Мюнхен, Германия), казалось, стоял особняком. Начальные работы по ускорению трансфертного формования смолы (RTM) для производства его M Крыша спортивной модели привела к созданию полной цепочки поставок деталей из углепластика (CFRP) для его i3 и i8 транспортных средств, а затем к совершенно новым производственным и сборочным элементам для корпуса в белом цвете с углеродным сердечником из различных материалов (BIW) на его 7-й серии .
BMW посвятила себя i3 в 2009 году с большой помпой, но в том же году Audi AG (Ингольштадт, Германия) открыла технический центр, посвященный армированным волокнами пластмассам. В 2011 году Audi объявила о партнерстве с Voith Composites (Гархинг, Германия) для разработки и производства деталей из углепластика в больших объемах. В следующем году было объявлено о разработке стальной центральной стойки, армированной углепластиком, изготовленной с использованием литьевого формования полимера (RTM), и партнерство с SOGEFI (Гуйанкур, Франция) по коммерциализации композитных спиральных пружин подвески. В 2012 году Audi также выступила партнером-основателем передового кластера MAI Carbon, в который вошли BMW, Voith Composites, SGL Group (Висбаден, Германия) и другие.
В частности, собственное повествование Audi о разработке CFRP начинается с первого поколения R8 . спортивный автомобиль, выпущенный в 2006 году. Он имел крышки отсеков для складного верха, а также боковые ножки, изготовленные методом литья под давлением (RTM). Компания перешла от эстетичного внешнего вида и небольших конструкций к модульной спортивной системе (MSS) в Audi R8 e-tron . . Хотя основная конструкция этого электрического суперкара состояла из экструдированных алюминиевых балок, соединенных алюминиевым литьем, все панели и заполнители были выполнены из углепластика, включая вставку багажника с гофрированными противоударными конструкциями, которые позволили заднему модулю поглощать в пять раз больше энергии, чем металлический каркас. .
Основа MSS - его задняя стенка , который превратился из первоначальной концепции в 2011 году в модуль, который в настоящее время производится для неэлектрического R8 компанией SGL Technologies (ранее BENTELER-SGL, Орт-им-Иннкрайс, Австрия; см. «Обзор завода:BENTELER SGL»). Но Audi уже планировала свой следующий шаг:итерация задней стенки для использования в его более объемном A8 роскошный седан с компанией Voith Composites в качестве производственного партнера.
Voith Composites - это 10-летняя дочерняя компания многонациональной компании Voith GmbH &Co. KGaA, основанной в 1867 году. Сейчас в головной компании работает 19 000 сотрудников, ее годовой доход составляет 4,2 миллиарда евро (5,2 миллиарда долларов США) и предоставляет производственное оборудование и технологии. четыре подразделения:Voith Digital Solutions, Voith Hydro, Voith Paper и Voith Turbo. Компания Voith Composites прошла путь от производства рулонов из углепластика, используемых в производстве бумаги, до производства автомобильных и промышленных приводных и карданных валов из углепластика и плоских ламинатов.
В 2011 году компания Voith Composites начала работу над высокоавтоматизированной технологической цепочкой углепластика, направленной на производство A8 Задняя стена. В его основе лежал аппликатор Voith Roving Applicator (VRA), который в одну линию распределяет жгут из углеродного волокна 35K из Zoltek (Сент-Луис, Миссури, США) на переплетенную однонаправленную (UD) ленту, которая затем разрезается и укладывается в стопку. сформировать заготовку на заказ. В 2017 году установка VRA была отмечена наградой JEC за инновации. Она также создала прочную основу для последующих операций по предварительному формованию и формованию. На выставке JEC World 2018 компании Voith Composites и Audi снова были отмечены высшими наградами в автомобильной категории за завершенную производственную линию Digital 4.0 на основе VRA, используемую для производства Audi A8 модуль задней стенки. Работая с поставщиком смолы Dow Automotive (Оберн-Хиллз, Мичиган, США) и Zoltek, эти партнеры не только разработали материалы, процессы и интегрированные поточные системы контроля, необходимые для производства высокопроизводительных деталей из углепластика в больших объемах, но и создали полную набор основных инструментов автоматизированного проектирования / производства (CAD / CAM) и моделирования, которые уже применяются для разработки будущих деталей.
Эволюция дизайна на основе эффективности
«Мы начали работать с Audi на раннем этапе», - говорит д-р Яромир Уфер, руководитель отдела развития компании Voith Composites. Первым приоритетом была разработка нового A8 конструкция задней стенки, которая будет определять способ изготовления детали.
«Когда мы начинали проектирование этого производства, мы не могли найти готовые [программные] продукты, в которых было бы все необходимое», - объясняет Уфер. «Поэтому мы объединили инструменты проектирования, такие как ABAQUS, но создали собственные карты материалов и разработали собственные методы моделирования». Audi уже определила уменьшенный вес BIW и повышенную жесткость на кручение в качестве ключевых целей для R8 . дизайн задней стенки (см. «Стенка сиденья Audi R8:прелюдия к производству»). Для A8 модуля была предложена целостная конструкция для уменьшения многокомпонентной MSS монтаж на единую профильную панель из углепластика с небольшим количеством приклепанных и заклепок. Эта конструкция привела к разработке высокоанизотропного ламината с локализованными путями нагрузки, что позволяет готовой детали обеспечивать 33% жесткости на кручение приводной ячейки при 50% веса по сравнению со сборкой из трех-пяти сварных алюминиевых деталей.
«Композитная преформа для Audi A8 Панель задней стенки варьируется от 6-слойной до 19-ти слойной основы, где добавляется местное армирование - например, там, где есть вырезы или точечные нагрузки, такие как крепления удерживающих устройств детской коляски », - поясняет Уфер (рис. 2).
Аппликатор ровинга Voith
Уфер отмечает, что разработка этой конструкции и VRA шла в тандеме. «Только благодаря свободе дизайна, которую предлагает VRA, новый A8 возможна задняя стенка ». Также важным было то, что поставщик волокна Zoltek взял на себя семилетнее ценовое обязательство по программе.
Процесс VRA начинается со шпулярника из углеродного волокна PX 35 от Zoltek. Несколько бобин с жгутом 50K подают в каждую линию VRA и распределяют для получения лент шириной 50 мм. Затем наносится связующее на основе эпоксидной смолы, которое позже вступит в реакцию с эпоксидной матричной смолой быстрого отверждения Dow VORAFORCE во время литья композитной детали с переносом смолы (RTM). Небольшое количество инфракрасного (ИК) тепла применяется для расплавления связующего, достаточного для скрепления ленты на последующих этапах консолидации, разрезания и укладки (этап 1).
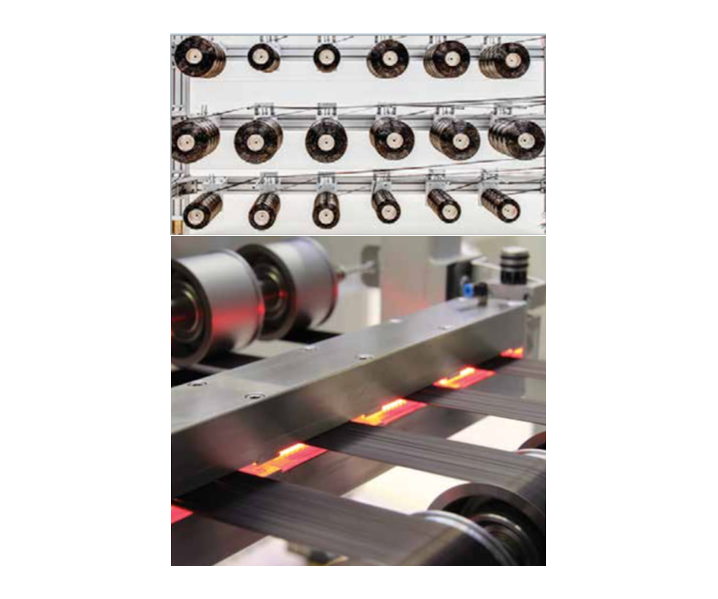
Шаг 1:сильный> Жгут углеродного волокна Zoltek 50K подается в ровинг-аппликатор Voith (VRA), где он сначала распределяется, затем покрывается связующим на основе эпоксидной смолы, а затем нагревается инфракрасным излучением для частичного расплавления связующего.
«Это непрерывный процесс, который полностью автоматизирован, - говорит Уфер. «Если по каким-то причинам необходимо остановить линию, оборудование среагирует автоматически. Например, инфракрасный обогреватель немедленно выключается и убирается, чтобы предотвратить повреждение ленты от перегрева. В оборудовании есть сотни таких деталей, и цифровое управление позволяет использовать эту технологию ».
Шаг 2: Затем лента-жгут уплотняется по мере того, как она проходит через несколько роликов под натяжением.
После нанесения связующего достигается уплотнение ленты, поскольку она проходит через несколько роликов под натяжением (шаг 2). Уфер объясняет, что это также создает буфер для строки. «У нас есть устройство, которое прерывает непрерывный поток волокна, обеспечивая переход к импульсному формату механизма отрезания и размещения ленты». Этот портальный механизм нарезает ленты на нужную длину и укладывает их под заданными углами от 0 до 360 ° на поворотный стол (Шаг 3). Каждая индивидуальная пачка, состоящая из 6-19 слоев ленты, имеет толщину от 1,5 до 3,7 мм соответственно.
Шаг 3: Затем VRA разрезает ленту и помещает до четырех частей одновременно на поворотный стол, изменяя длину ленты и угол ориентации в стопке ламината (например, 45 ° / 90 ° / 30 °).
Компания Voith установила четыре линии VRA (см. Начальную фотографию), и хотя каждая применяет до четырех лент шириной 50 мм за раз, отмечает Уфер, «у линий есть модульный подход, поэтому они могут наносить 10 или более лент за один раз». время. Это зависит от размера детали и производительности ».
Автоматизация включает контроль качества. Сканы лент и преформ сравниваются с алгоритмом отбраковки. «100% сканирование ленты VRA обеспечивает правильное распределение волокон по всей производственной линии», - поясняет Уфер. «Мы также используем термографию и лазерные датчики для проверки преформ в специально отведенных местах». Затем VRA может реагировать на любые обнаруженные проблемы. «Если одна лента неправильная, - отмечает он, - VRA отрежет недостающую длину и произведет другую, чтобы заменить ее». QR-код помещается на готовую преформу для отслеживания. (QR-коды предпочтительнее меток радиочастотной идентификации (RFID), потому что они, как сообщается, лучше выдерживают процесс впрыска смолы.)
Формовка, формование и сборка
Пакет 2D выходит из VRA и перемещается в секцию формования, формования и сборки производственной линии. Первый пресс, в который он помещается, поставлен специалистом по автоматизации композитных материалов FILL (Гуртен, Австрия), использует тепло и давление для придания двухмерной ленточной упаковке трехмерной преформы (этап 4). Уфер объясняет, что, поскольку преформа различается по толщине и форме, пресс может регулировать прикладываемое давление, когда штамп формирует отдельные области преформы, зажатой в формующем инструменте. ALPEX Technologies (Mils bei Hall, Австрия) изготовила формы RTM из согласованной стали на основе конструкции, предоставленной Voith Composites. «Мы виртуально разработали инструменты и процесс прессования, - говорит Уфер. «Хотя никакого реального испытательного цикла не потребовалось, мы проверили и проверили имитационные модели на других формах и деталях перед обработкой A8 инструменты для производства задней стенки. Это моделирование процесса формования воплотилось в реальном производстве и помогло ускорить оптимизацию ».
Шаг 4 :Пачка лент перемещается в пресс, где из нее формируется окончательная трехмерная форма детали.
Пресс выдерживается в течение нескольких секунд для реакции порошкового связующего и установления формы, в результате чего получается стабильная преформа, которая может противостоять смыванию волокна во время впрыска смолы. «Частицы связующего также служат для разделения волокон для улучшения текучести смолы во время RTM», - отмечает Уфер. «Это полезно, потому что в преформе нет сшивания, чтобы способствовать течению смолы, поэтому эти частицы связующего действуют как каналы микротока».
Затем формованная преформа перемещается роботом в ячейку с ЧПУ EiMa Maschinenbau GmbH (Фриккенхаузен, Германия), где ультразвуковой нож обрезает внешний конечный контур. Затем он автоматически помещается в пресс RTM (этап 5), поставляемый ENGEL (Швертберг, Австрия). Все роботы в линии поставляются компанией KUKA Robotics (Аугсбург, Германия).
Шаг 5: Формованная преформа помещается в пресс с усилием 350 кН и формуется с использованием ультра-RTM.
Процесс RTM, использованный для формования A8 задняя стенка такая же, как у Audi Lightweight Center, разработанная для предыдущего R8 задняя стенка, именуемая ультра-RTM. Это позволяет формовать крупные детали с использованием быстрого впрыска, но при низком давлении. По сравнению с 140 барами, типичными для HP-RTM, давление впрыска смолы в форму во время ультра-RTM Audi A8 задняя стенка <15 бар, даже меньше, чем у R8 . В результате вместо усилия пресса в 2500 кН требуется всего 350 кН. Следовательно, для производства высококачественных деталей с большим объемом волокна можно использовать более компактный и менее дорогой пресс.
Эпоксидная смола VORAFORCE 5300, трехкомпонентная система, включающая смазку для форм, отверждается за 90–120 секунд при 120 ° C и имеет технологическую вязкость 20 сП. Для A8 Задняя стенка, в преформу впрыскивается 1,3 кг смолы, после чего происходит 120-секундное отверждение.
Отвержденная деталь извлекается из формы с помощью роботов и загружается в закрытую фрезерную ячейку с ЧПУ для обработки вырезов. Затем отфрезерованную деталь помещают в автоматическую стиральную машину, чтобы счистить остаточную пыль углепластика.
Вымытую заднюю стенку переносят в сборочную ячейку, оборудованную двумя роботами. Первый робот помещает отформованную деталь в автоматизированную клепальную машину, которая фиксирует силу, приложенную во время установки заклепки. Это часть производственного интеллекта, встроенного в общий процесс, и добавляется к записи цифровой обработки каждой детали (т. Е. Цифровой поток). Затем деталь перемещается в зону склеивания, и второй робот подготавливает зоны к склеиванию, используя автоматическую очистку растворителем. Затем тот же робот наносит быстротвердеющий двухкомпонентный полиуретановый структурный клей Dow BETAFORCE 9050M (шаг 6), который совместим с трехкомпонентной эпоксидной смолой. Затем деталь помещается в печь на короткий цикл отверждения клея.
Шаг 6: Полиуретановый клей BETAFORCE наносится с помощью роботов на склеенные детали, а затем отверждается за короткий цикл печи.
Эта производственная линия поддерживает 5-минутный цикл для готовой детали, а текущая потребность в деталях может быть удовлетворена в одну или две 8-часовые смены. Устройство для трехмерного лазерного сканирования периодически используется для проверки трехмерной формы и размеров детали. Готовые детали затем готовятся к отправке на Audi A8 . Линия окончательной сборки в Некерсальме, Германия, примерно в 3 часах езды по дороге (этап 7).
Шаг 7: Готовая деталь затем готовится к отправке на линию окончательной сборки Audi A8.
Прямое размещение волокна =гибкость в будущем
При всех сделанных инвестициях удивительно узнать, что компания Voith Composites не была уверена в этом бизнесе, но на самом деле компания завершила разработку, а затем участвовала в конкурсном тендере, чтобы выиграть производство. «Мы смогли удовлетворить целевую стоимость деталей, установленную Audi, а также выполнить требования к качеству и характеристикам деталей», - говорит Уфер. Это был большой подвиг, учитывая, что за программу претендовало немало компаний.
Компания Voith Composites запатентовала несколько частей своего технологического процесса. «VRA продемонстрировала индустриализацию с использованием прямого размещения волокон [DFP] лент, что сокращает количество брака, а также количество используемых материалов за счет высоко оптимизированной укладки», - говорит Уфер. Здесь также используются самые экономичные материалы - необработанное тяжелое жгутовое волокно и порошковое связующее. Его процесс второго поколения заменяет порошковое связующее прямым нанесением смолы, устраняя необходимость в дополнительных этапах процесса. Однако компания разработала другие процессы DFP, в том числе Preformer Voith Longfiber Preformer и Voith Prepreg Winding.
«Мы устанавливаем новые стандарты для деталей из углеродного волокна для массового серийного производства автомобилей», - говорит управляющий директор Voith Composites д-р Ларс Хербек. «Созданная нами умная фабрика выводит автоматизированное производство компонентов из углепластика на новый уровень эффективности и гибкости, включая практически любую форму, а также размеры отдельных партий». Это действительно то, куда движется отрасль.
Смола
- Почему материал PEEK находится на вершине своего класса
- Пластик, армированный углеродным волокном (CFRP)
- K 2019:материалы имеют значение на выставке
- Arkema запускает программу Start-Up Connect
- Polykemi инвестирует в собственный завод по производству компаундов в США
- Polykemi будет производить комплексное производство на трех континентах
- Термопластичная однонаправленная лента на основе углеродного волокна на основе PPS
- Проблемы лазерной намотки ленты из термопластичных композитов
- Разделенное углеродное волокно увеличивает производительность SMC
- Модуль углепластика снижает вес конструкции ракеты