HP-RTM для серийного производства экономичных авиационных конструкций из углепластика
Когда около десяти лет назад формование с переносом смолы (RTM) начало переходить на RTM под высоким давлением (HP-RTM), оно было в основном одобрено для автомобильных приложений, сокращая время цикла композитных деталей с часов до менее чем 2 минут. Меньше было сказано о применении этой технологии в аэрокосмических деталях. Авиационная промышленность имеет долгую историю использования традиционных RTM, включая их использование для производства тысяч лопастей вентиляторов из армированного углеродным волокном пластика (CFRP) и защитных кожухов для двигателей коммерческих самолетов. Компания Airbus даже создала прототип 7-метрового цельного многошпонентного закрылка из композитного материала для Airbus A320 с использованием RTM. Но можно ли превратить этот опыт с многочасовыми процессами в полностью автоматизированное формование композитных деталей самолетов за считанные минуты? Некоторые ключевые игроки говорят, что это возможно.
Традиционный RTM, называемый здесь LP-RTM для ясности, обычно использует давление впрыска 10-20 бар. HP-RTM, с другой стороны, использует давление впрыска 30–120 бар.
«Мы начали работать с аэрокосмической обработкой RTM 10 лет назад в рамках финансируемого ЕС проекта по производству каркасов фюзеляжа», - говорит Бернхард Риттеншобер, руководитель отдела исследований и разработок компании Alpex Technologies (Милс, Австрия), поставщика инновационных систем инструментов для серийного производства композитных материалов. производство деталей. «В то время предсказывалось, что многие детали для [Airbus] A350 будут производиться с использованием RTM, но это не сбылось». Однако Alpex продолжала работать над этой технологией и, как поставщик для автомобильной и аэрокосмической отраслей, начала искать пути объединения процессов, используемых в этих двух отраслях. «Идея заключалась в том, чтобы использовать эпоксидную смолу [Hexcel] RTM6, пригодную для применения в аэрокосмической отрасли, но с использованием передовых методов автомобильной оснастки и автоматизированной системы впрыска для сокращения времени цикла», - объясняет Риттеншобер.
Результатом стала исследовательская программа под названием TAKE OFF на 2013-2015 годы, финансируемая правительством Австрии, в которой Alpex участвовала вместе с партнерами Airbus Helicopters (предприятие в Донауворте, Германия), поставщиком оборудования KraussMaffei (Мюнхен, Германия), специалистом по тестированию Aerospace и Advanced Composites. (AAC, Винер-Нойштадт, Австрия) и поставщик смолы Hexcel (Стэмфорд, Коннектикут, США). Программа продемонстрировала, что HP-RTM привела к 30-процентному снижению стоимости дверной коробки A350 и значительному развитию технологий, включая использование двухкомпонентной (2K) полимерной системы, интеллектуальный контроль впрыска и отверждения с помощью датчиков в пресс-форме и возможность еще больше сократить время неполного цикла. Alpex продолжает разработку и видит потенциал этой технологии HP-RTM для решения текущих проблем с производством углепластика.
Поддерживая эту точку зрения, Центр технологий композитов (CTC), дочерняя компания Airbus Operations GmbH, также в течение десяти лет разрабатывает автоматизированную RTM, сначала с LP-RTM, а затем около пяти лет назад перешедшей на HP-RTM. ( CompositesWorld отметил машину KraussMaffei HP-RTM и опытно-конструкторские работы во время экскурсии по ее предприятию в 2016 г.) «HP-RTM устраняет узкие места инъекции и отверждения благодаря высокоскоростному перемешиванию, которое позволяет использовать высокореактивные смолы», - поясняет Ян Шиллер. Руководитель проекта CTC по производственным системам и ведущий контакт по технологиям RTM. «Мы разработали процесс, позволяющий производить детали со сложной геометрией размером 1-2 метра, отвечающие аэрокосмическим требованиям (например, 60 процентов объема волокна и менее 2 процентов пустот) за время цикла 20 минут». Он добавляет, что после визитов и обсуждений с поставщиками Airbus в прошлом году был определен ряд деталей для перехода на HP-RTM, что позволит производить более производительные самолеты A320. «Сейчас мы разрабатываем для них особую обработку и работаем в этом году, чтобы запустить их в серийное производство».
Дверная коробка HP-RTM A350
Разработка Alpex была завершена в рамках австрийской программы TAKE OFF в рамках проекта под названием SPARTA. «Эту роль выбрали Airbus Helicopters, - вспоминает Риттеншобер. «Эта дверная рама - это то, что вы видите, когда заходите в A350 с открытой дверью. Это примерно 2 метра в высоту, 200-250 миллиметров в ширину и 8-10 миллиметров в толщину, со сложной формой и конструктивными особенностями, отвечающими различным требованиям к собранной двери, которая является основной конструкцией ». Дверь A350 состоит из 14 частей, изготовленных Airbus Helicopters в Донауворте, Германия, с использованием LP-RTM. Рама, выбранная для SPARTA, - одна из самых сложных частей двери. «Это хорошая демонстрационная часть, потому что мы можем сравнить HP-RTM напрямую со стандартным аэрокосмическим LP-RTM», - добавляет Риттеншобер.
Компания Alpex разработала и изготовила оснастку LP-RTM, которая в настоящее время используется для производства дверных коробок A350 в Airbus Helicopters. Для разработки и сборки инструментария HP-RTM это применило бы более автомобильный образ мышления. «Наша цель состояла в том, чтобы обеспечить автоматизацию автомобильного типа в производстве деталей из композиционных материалов для авиакосмической промышленности», - говорит Риттеншобер. «Это необходимо, если Airbus собирается строить будущий A320 с большим количеством композитных деталей и из расчета от 60 до 100 самолетов в месяц».
Он продолжает:«Мы исходили из производства пресс-форм для BMW, которая активно пыталась упростить свои детали и процессы, чтобы сократить время цикла, в то время как Airbus исходил из предыдущей сложности в аэрокосмической отрасли. Например, когда мы только начинали, Airbus Helicopters спрашивали, сколько деталей будет у этой формы ». Обратите внимание, что в настоящее время производство дверей LP-RTM включает сложные, состоящие из нескольких частей инструменты. «Мы объяснили, что инструмент HP-RTM будет иметь только одну верхнюю и одну нижнюю формы», - говорит Риттеншобер.
Таким образом, компания Alpex начала с простой конструкции пресс-формы, а затем добавила функции, чтобы сделать процесс обработки более надежным и гибким - например, системы уплотнения, используемые для крупносерийного автомобильного производства. «Кроме того, у нас есть все датчики, встроенные в пресс-форму», - отмечает он.
Преформы и обработка
В преформах, которые в настоящее время используются для дверной коробки A350, используется тканый материал, и для них требуется несколько этапов удаления массы, что приводит к трехдневному производственному циклу. «Вместо этого мы решили использовать ткань без обжима (NCF)», - говорит Риттеншобер. «Это значительно снижает цену и время цикла. В итоге мы также продемонстрировали некоторые детали с ткаными преформами, сертифицированными Hexcel, но мы видим переход в отрасли композитов за пределами авиакосмической отрасли, когда SGL и другие компании перешли от тканых материалов к лентам и более дешевым формам, таким как NCF ».
Когда его спрашивают о точках впрыска и любых проблемах с промывкой волокна, Риттеншобер объясняет, что инструмент HP-RTM имеет только одну точку впрыска, но промывка волокна отсутствует, потому что преформа зажата так, что она фиксируется в форме и очень стабильна. P>
Другой ключевой момент заключается в том, что Alpex решила использовать двухкомпонентную (2K) систему смолы вместо однокомпонентной RTM6, которая в настоящее время используется Airbus Helicopters. Риттеншобер утверждает, что система 2K может быть более реактивной, что лучше подходит для HP-RTM и может снизить затраты, поскольку в ней нет предварительного смешивания и не требуется транспортировка опасных материалов. Однако для этого требуется более высокая температура - 180 ° C. «Это было самым сложным для нас, - говорит Риттеншобер, - потому что мы привыкли обрабатывать при 120 ° C».
KraussMaffei установила в своем легком техническом центре в Мюнхене, Германия, готовую оснастку в своей системе RimStar Compact HP-RTM с автоматическим смешиванием, дозатором и впрыском под высоким давлением (до 80 бар / 1100 фунтов на квадратный дюйм). Затем было изготовлено 20 демонстрационных деталей. Риттеншобер описывает базовый процесс:впрыскивание при 80 ° C, повышение до 120 ° C, выдержка в течение одного часа, повышение до 180 ° и выдержка в течение 90 минут отверждения, снижение (2 ° C / мин) и извлечение из формы. «Впрыск занимает всего 20 секунд, - говорит он, - но полный цикл формования составляет около четырех часов».
Время цикла и стоимость
По-прежнему продолжительный цикл отверждения дверной коробки SPARTA обеспечивается составом и обработкой смолы Hexcel RTM6, одобренной Airbus. «Нам удалось достичь 30-минутных циклов отверждения при 180 ° C с дополнительным последующим отверждением в вакууме для снятия термического напряжения и обеспечения механических свойств», - отмечает Риттеншобер, добавляя, что свойства были довольно хорошими и сравнимыми с LP. -RTM часть.
«Мы показали, что вы можете использовать этот процесс и автоматизировать производство для больших объемов деталей», - говорит Риттеншобер. «Вы можете впрыскивать и отверждать в форме, а затем после отверждения вне пресса». Он признает, что для этого требуются дополнительные наборы инструментов, но только один блок пресса и впрыска. «С помощью этой системы вы можете снизить стоимость детали на 700 евро, что позволит вам легко оплачивать оборудование с производительностью от 500 до 1000 деталей в год, что даже не является очень большим объемом».
Разработка и демонстрация процессов CTC
Помимо инструментов и технологического процесса, дверной проект HP-RTM также включал новаторское использование формата волокна. «Мы начали с тканых тканей, уже прошедших квалификацию Airbus, и были очень успешными», - вспоминает Шиллер. «Затем мы продолжили разработку NCF и более инновационного текстиля». Последнее включало размещение волокон в сухом состоянии и чередование слоев с расправленными слоями жгута для повышения прочности, но последнее представляло проблемы с плотной упаковкой волокон и слоев, что приводило к плохой проницаемости и препятствовало проникновению смолы. «Есть также разработки для решения этой проблемы, такие как NCF со специальными волокнами для улучшения проницаемости», - добавляет он.
Что касается давления для HP-RTM, Шиллер подчеркивает, что решение использовать этот процесс было вызвано больше технологией смешивания из полиуретановой промышленности, чем высокими технологическими давлениями. «Мы используем HP-RTM только для того, чтобы получить хорошее смешивание высокореактивных смол», - объясняет он. «В пресс-форме может быть более высокое давление, но это вторичный эффект от быстрого впрыска. Для автомобильных деталей с 2-минутным временем цикла они должны пропитывать сухую преформу смолой намного быстрее, чем это делаем мы. Наше 15-минутное время отверждения дает больше времени для инфильтрации смолы, что также снижает давление в форме ».
Между тем, тоннаж пресса зависит от размера детали. «Изготовление деталей размером до 2 метров - это хорошо (около 1500 тонн), но детали размером 4-6 метров требуют расчетов с экономической точки зрения, поскольку затраты на прессование становятся очень высокими», - говорит Шиллер. Компания CTC продемонстрировала ребро из углепластика размером 1,5 на 0,5 метра, представляющее любую возможную основную конструкцию аэрокосмической отрасли на выставке JEC World в 2018 году. В конце 2019 года он также получит высокотоннажный пресс.
Двухкомпонентные смолы и контроль качества на основе датчиков
Шиллер отмечает, что во всех предыдущих конструкциях самолетов RTM использовались только системы 1K, смешанные поставщиком, который затем сертифицирует смесь и несет ответственность за соответствие смолы квалификационным требованиям. «Сейчас мы рассматриваем системы 2K, но задача состоит в том, чтобы обеспечить качество микширования», - поясняет он. Предварительно смешанные системы 1K требуют холодной транспортировки и хранения, чтобы предотвратить реакцию до обработки детали. Таким образом, преимущества систем 2K включают устранение этих затрат, а также более высокую реактивность для более быстрой обработки. Однако одна из проблем заключается в том, что обеспечение качества (ОК) перейдет от поставщика смолы к производителю деталей. «Этот QA требует определения соотношения смешивания и качество смешанной смолы. Оба необходимы для квалификации нового материала Airbus. Таким образом, это означает измерения двух компонентов непосредственно перед смешиванием и смолы после смешивания. Сегодня у нас есть только датчики перед смесительной головкой, показывающие, сколько смолы и сколько отвердителя добавлено в смесь. Этого недостаточно для квалификации ».
Тем временем Alpex работает над разработкой встроенной системы контроля качества, чтобы обеспечить проверку 100% правильно смешанной смолы, которая требуется Airbus. «Мы работаем с датчиками Netzsch для литья под давлением с самого начала разработки», - отмечает Риттеншобер. «Теперь, когда Netzsch сотрудничает с Kistler (Винтертур, Швейцария), доступны новые технологии. Мы можем контролировать температуру, давление и отверждение смолы с помощью одного датчика, который мы включаем в форму ».
«Alpex рекомендует использовать датчики в пресс-форме, а поставщики оборудования для смешивания / впрыска говорят, что датчики должны быть в их систем », - говорит Шиллер. «Оба правы». Но он отмечает, что последнее также необходимо улучшить. «В автомобильной HP-RTM соотношение смол в смеси измеряется на протяжении всего процесса, поэтому это среднее значение», - объясняет Шиллер. «Однако мне нужно это измерение в каждой дискретной точке во время процесса, чтобы я знал, что соотношение смеси всегда правильное, даже в течение последней половины секунды во время впрыска. Нам нужно лучшее временное разрешение в измерительных системах ». Шиллер предполагает, что датчики, вероятно, понадобятся перед смесительной головкой, внутри смесительной головки и в форме. «Мы работаем над разработкой QA параллельно с оценкой 2K смол в аэрокосмической сфере, и вместе с поставщиками оборудования мы определили сенсорные системы, которые обещают достаточное разрешение. Они будут утверждены в течение этого года ».
Alpex также испытывает новый гибридный многофункциональный пьезоэлектрический датчик, разработанный Aerospace &Advanced Composites (AAC, Винер-Нойштадт, Австрия). Размещено на В пресс-форме RTM он действует как датчик давления для отслеживания фронта потока смолы в пресс-форме. После того, как преформа пропитана смолой и начнется отверждение, датчик использует изменение спектра импеданса для определения степени отверждения. По завершении отверждения пьезоэлектрические датчики отверждаются на поверхности детали, которая будет использоваться для мониторинга состояния конструкции либо в пассивном режиме в качестве датчиков акустической эмиссии, либо в активном режиме с использованием направленных ультразвуковых волн. Они были продемонстрированы для контроля ударов и повреждений готовых деталей.
Обратите внимание, что эти данные процесса могут быть проанализированы интеллектуальными производственными системами Индустрии 4.0 для определения путей дальнейшего повышения качества и эффективности. Эти данные процесса также могут регистрироваться для цифрового двойника каждой детали.
Будущий потенциал
Риттеншобер говорит, что единственным реальным препятствием для технологии HP-RTM является сертификация:«Мы демонстрируем с Airbus Helicopters, что этот процесс может работать, но кто-то должен его сертифицировать». Шиллер согласен с тем, что всегда сложно найти, кто будет первым, но за последний год он также рассчитал бизнес-модели для многих деталей. «Для 200 деталей в год это не имеет смысла. Однако для деталей на А320, например, он становится привлекательным. Каждый месяц мы видим более высокий целевой показатель по программе A320. Многие из этих деталей были спроектированы в 1980-х годах и производятся вручную, поэтому их можно легко сделать намного более эффективными с помощью HP-RTM ».
Благодаря продемонстрированному CTC времени частичного цикла в 20 минут, HP-RTM также может быть привлекательным для рынка самолетов с электрическим вертикальным взлетом и посадкой (eVTOL), где производственные объемы производства 5000 самолетов в год были предложены производителем аэротакси в качестве верхнего предела. UBER.
По словам Риттеншобера, Alpex продолжит разработку ряда усовершенствований RTM. «Мы считаем, что HP-RTM имеет реальный потенциал, чтобы помочь решить некоторые проблемы с более экономичным промышленным производством авиационных конструкций из углепластика». Шиллер соглашается, отмечая, что для многих целевых приложений A320 существует множество деталей из углепластика в каждой партии. «Таким образом, преимущества более эффективного процесса начинают накапливаться. Если мы сможем запустить первое приложение в производство, то появятся и другие ».
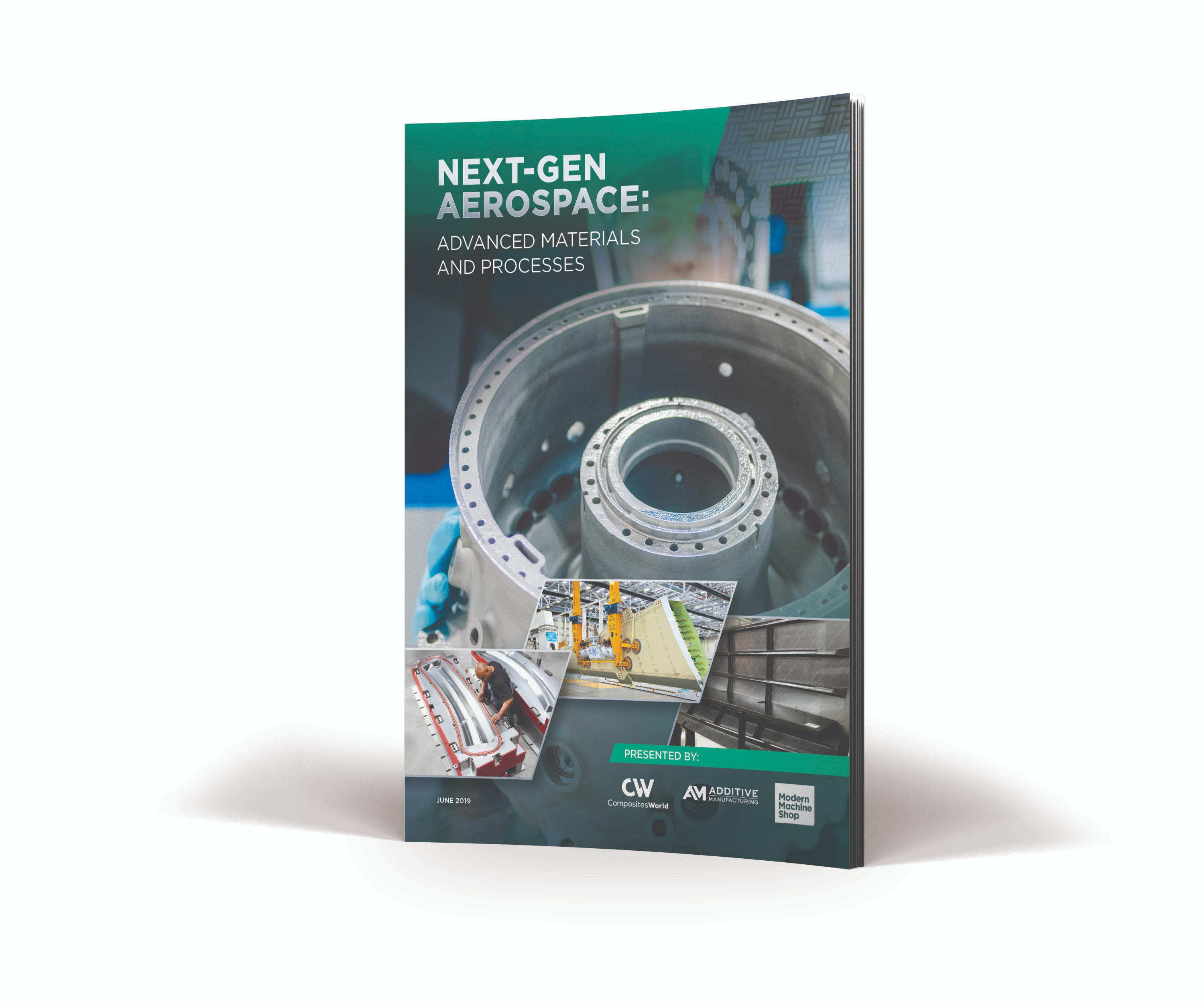
Новое поколение
Аэрокосмическое производство
Поскольку в ближайшие 20 лет отрасль коммерческой авиации вырастет вдвое, удовлетворение спроса на пассажирские и грузовые самолеты потребует новых технологий и беспрецедентных темпов производства.
Узнайте больше о материалах и процессах, которые будут использоваться в самолетах следующего поколения, из коллекции историй от CompositesWorld, Modern Machine Shop и Аддитивное производство , доступно для чтения или скачивания бесплатно . Получите это здесь.
Смола
- Добавки:экономичные красители для проводов и кабелей
- Чистящие составы для производства тонкостенных полиолефиновых упаковок
- Fraunhofer вводит в эксплуатацию автоматизированные производственные ячейки Engel для НИОКР термопластичных компо…
- Проектирование для автоматизированного производства композитных материалов для малосерийных авиационных к…
- Термопластические ленты продолжают демонстрировать потенциал для создания композитных аэроструктур
- Карл Майер запускает линию по производству термопластичных UD-лент
- Расплавление гидроабразивным лазером для повышения эффективности обработки углепластика / CMC
- Broetje-Automation расширяет портфолио AFP для серийного производства композитных материалов
- INEOS Styrolution для создания производственной площадки для термопластичного композита StyLight
- Методы отслеживания литейного производства