Развитие термопластичных композитов и RTM для Clean Sky 2 в Испании
Технологический центр EURECAT в Каталонии (Технологический центр EURECAT в Каталонии, Барселона, Испания) - это частная некоммерческая научно-исследовательская организация с 11 объектами, 650 сотрудниками и годовым доходом 50 миллионов евро. «Это второй по величине научно-исследовательский центр в Испании», - объясняет Анхель Лагранья Эрнандес, программный директор по рынку аэронавтики и космоса компании EURECAT. Он объясняет, что часть доходов EURECAT поступает от правительства Каталонии, а оставшаяся половина должна поступать от частных компаний - в основном малых и средних предприятий (МСП) - в то время как другая половина может быть публичной, например, финансируемой Европейским союзом. Программа "Чистое небо 2". «Сейчас у нас есть 18 проектов Clean Sky, - отмечает Лаграна, - которые мы были награждены исключительно на основе конкурсных заявок в ответ на призывы к подаче заявок».
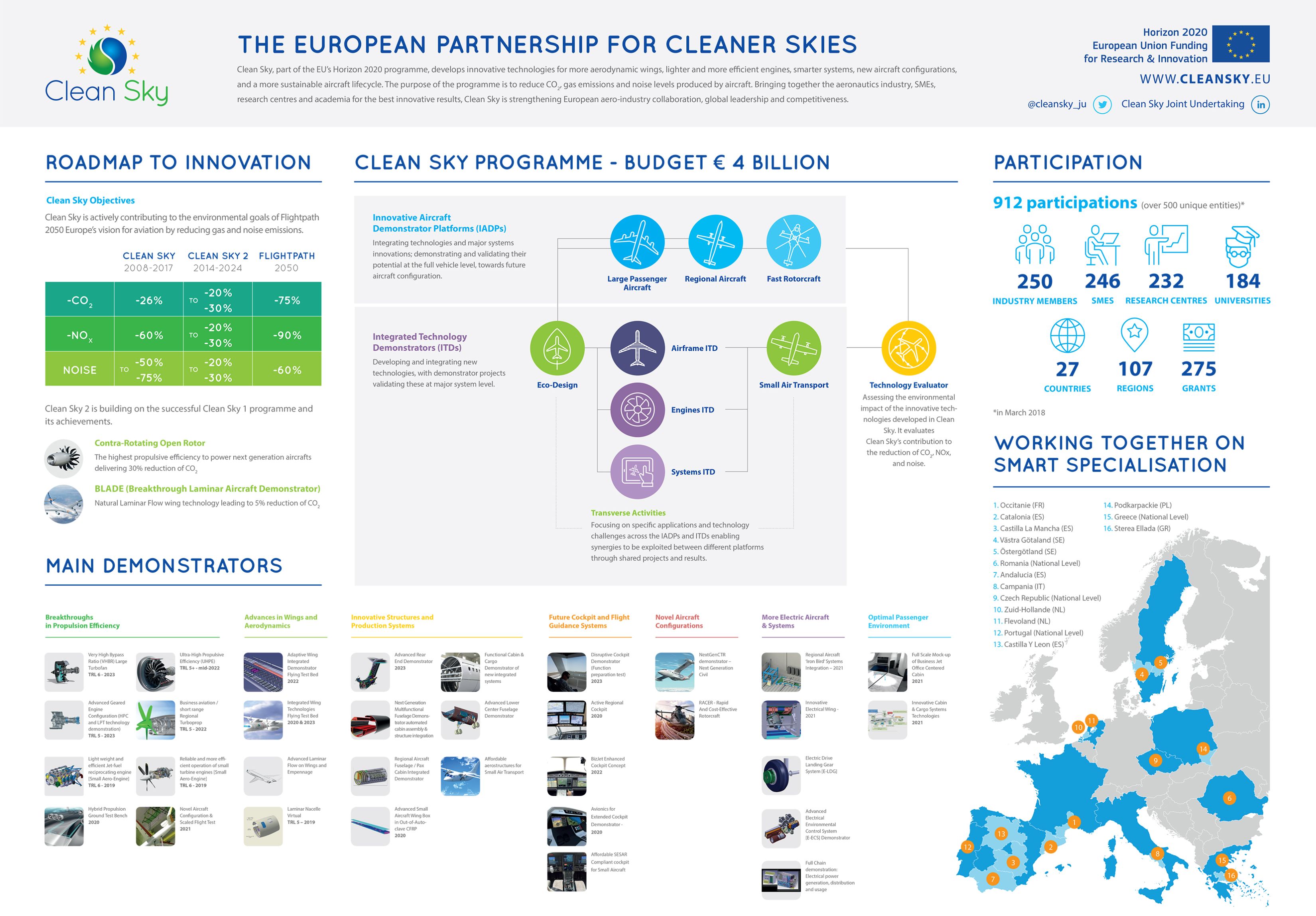
Примеры того, как композитные материалы используются в многочисленных целях и запланированных демонстраторах технологий Clean Sky 2, включают:
- Многофункциональный демонстратор фюзеляжа нового поколения - использование термопластов для более чистого неба.
- Циркулярная экономика:обретает форму композитный фюзеляж для региональных самолетов.
- Использование опыта в автоспорте для FastCan от Clean Sky
«EURECAT - это очень поперечная система, которая работает не только в аэрокосмической, но и в автомобильной, железнодорожной и других отраслях», - говорит Лагранья. «Он также активно занимается ИТ, например, анализом данных, блокчейном и т. Д. Composites 4.0 - одно из его стратегических направлений». Что касается композитов, он отмечает, что EURECAT в основном работает вне автоклавных технологий (OOA). «Мы специализируемся на термопластах и жидкостном компрессионном формовании, включая мониторинг процесса в режиме реального времени, включая мониторинг температуры стеклования (Tg) смолы во время обработки». (Продолжайте читать раздел COFRARE в конце этого блога, чтобы узнать больше об этом мониторинге Tg.)
Самые последние проекты EURECAT, связанные с композитами в Clean Sky 2, включают:
- КИЛБЕМАН продемонстрировать килевая балка из термопластичного композитного материала (этот проект получил финансирование от совместного предприятия Clean Sky 2 в рамках исследовательской и инновационной программы Европейского союза Horizon в соответствии с GAP № 785435 KEELBEMAN) ;
- WINFRAME 4.0 построить оконные рамы из термопластичного композита (TPC) для демонстратора Green Regional Aircraft (GRA) в Clean Sky (2008-2017 гг.) и распространить на IADP (Innovative Aircraft Demonstrator Platform) в Clean Sky 2 (2014-2024);
(Этот проект получил финансирование от совместного предприятия Clean Sky 2 в рамках исследовательской и инновационной программы Европейского союза Horizon в рамках GAP № 821323 WINFRAME 4.0.) - COFRARE 2020 для термореактивных каркасов фюзеляжа, изготовленных методом литья под давлением (RTM) с использованием поперечных стяжек TPC.
(Этот проект получил финансирование от совместного предприятия Clean Sky 2 в рамках исследовательской и инновационной программы Европейского Союза Horizon в рамках GAP № 821261 COFRARE 2020.)
Килевая балка из термопластичного композитного материала
Чистое небо 2 - JTI-CS2-2017-CFP06-LPA-02-20. Срок реализации проекта:с марта 2018 г. по декабрь 2019 г.
Целью проекта KEELBEMAN является разработка ориентированной на производство конструкции килевой балки для самолета типа A320, которая обеспечивает высокие темпы производства самолетов, но по доступной цене за счет использования термопластичных композитов. Помимо EURECAT в качестве координатора проекта, в число партнеров входят:
- Airbus (Тулуза, Франция) в качестве руководителя темы.
- CETMA (Европейский исследовательский центр технологий дизайна и материалов, Бриндизи, Италия)
- Инженерная группа CT (CT Ingenieros, Мадрид, Испания), фирма с многочисленными офисами по всему миру, имеющая многолетний контракт с Airbus на разработку самолетов, таких как исследования фюзеляжа, крыльев и задней части через свой офис в Гамбурге, Германия; исследование задней части (Испания); исследования конструкций, связанных с фюзеляжем и силовой установкой (Тулуза, Франция), и разработка крыла (Бристоль, Великобритания)
- Софитек (Севилья, Испания), специалист по производству и сборке авиационных конструкций, обладающий опытом и производственными мощностями в композитах.
CT Engineering Group предоставила полное моделирование геометрии килевой балки через свой офис в Тулузе, а Sofitec разработала метод контроля неразрушающего контроля (NDT). «Это очень сложно с такой закрытой структурой, - отмечает Лагранья.
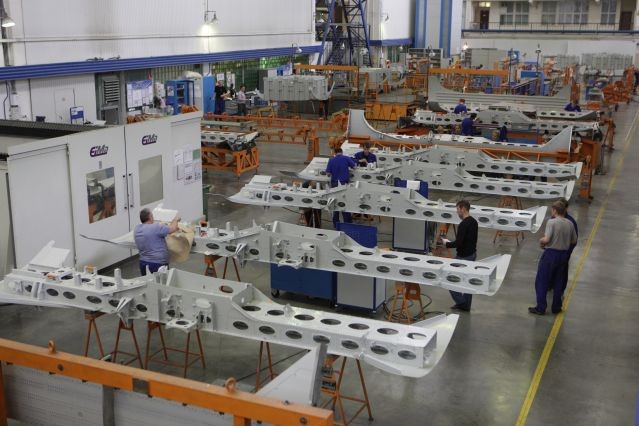
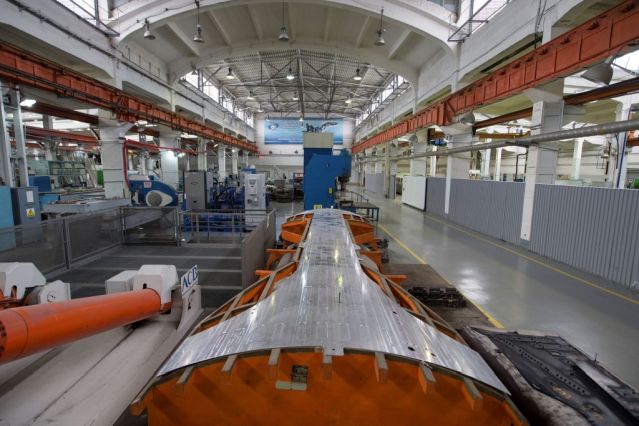
На фотографии показана килевая балка А320, изготовленная из металла корпорацией «Иркут» (Москва, Россия). Сообщается, что в 2004 году «Иркут» заключил контракт с Airbus на поставку компонентов, включая отсек передней стойки шасси, килевую балку и гусеницу закрылков, которые устанавливаются в среднем на каждый третий самолет семейства А320. ИСТОЧНИК | Иркут
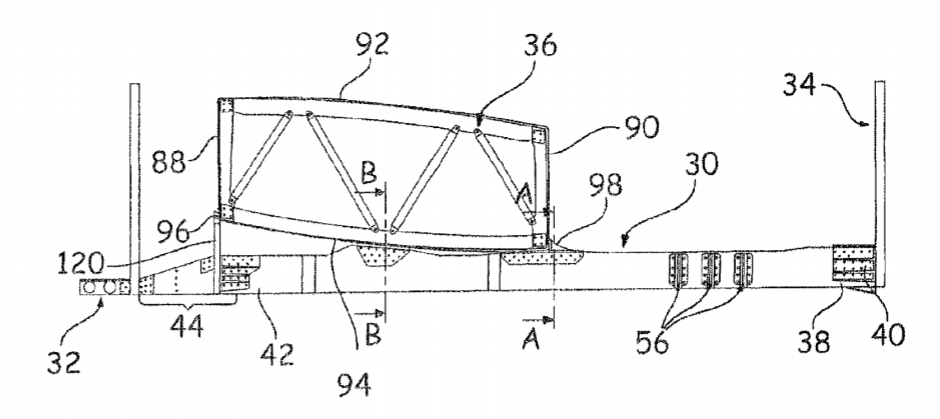
Разработка конструкции килевой балки
«Сегодня большинство килевых балок самолетов делают из металла, за исключением Airbus.
А350, который представляет собой монолитный композит из углеродного волокна », - говорит Лагранья. «Это требует большого количества заклепок и значительного времени для сборки». Он объясняет, что килевая балка является важной структурой фюзеляжа:«Были случаи, когда килевая балка ломалась во время посадки, в результате чего весь фюзеляж трескался и ломался.
Согласно статье Стива Вильгельма 2011 года, килевая балка A350 на 70% состоит из композитных материалов, длина 54 фута (16,5 метра), вместе с 10 000 крепежных деталей, весит 1,2 тонны и составляет основу самолета. Вильгельм отмечает, что конкурентоспособный самолет Boeing 787 «не зависит от такой прочной конструкции киля, потому что большая часть прочности корпуса обеспечивается за счет композитных стволов, скрепленных вместе встык». Затем в статье цитируется Мишель Мерлузо, управляющий партнер аэрокосмической консалтинговой компании G2 Solutions LLC (Киркланд, Вашингтон, США), который описывает конструкцию Airbus как «более традиционную» и «менее рискованную», но отмечает, что балка киля «важна для структурная целостность этого самолета ».
Компания Airbus впервые применила композитную килевую балку для A340 в 2001 году. Но, как описано выше, большое количество необходимых заклепок работает против экономии веса, возможной за счет использования композитов. Таким образом, ключевая цель проекта KEELBEMAN - минимизировать количество крепежных элементов за счет использования термопластичных композитных компонентов, которые свариваются вместе.
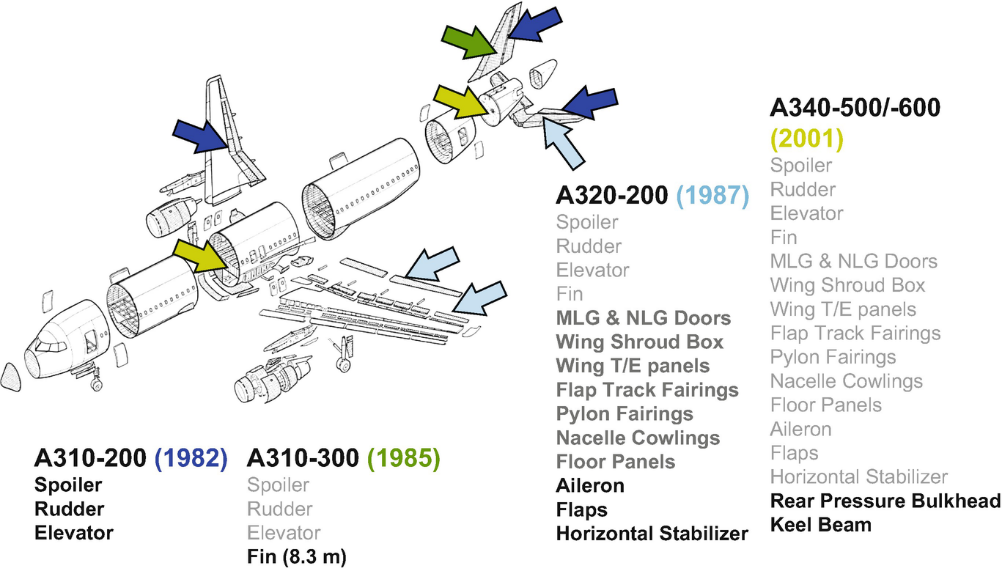
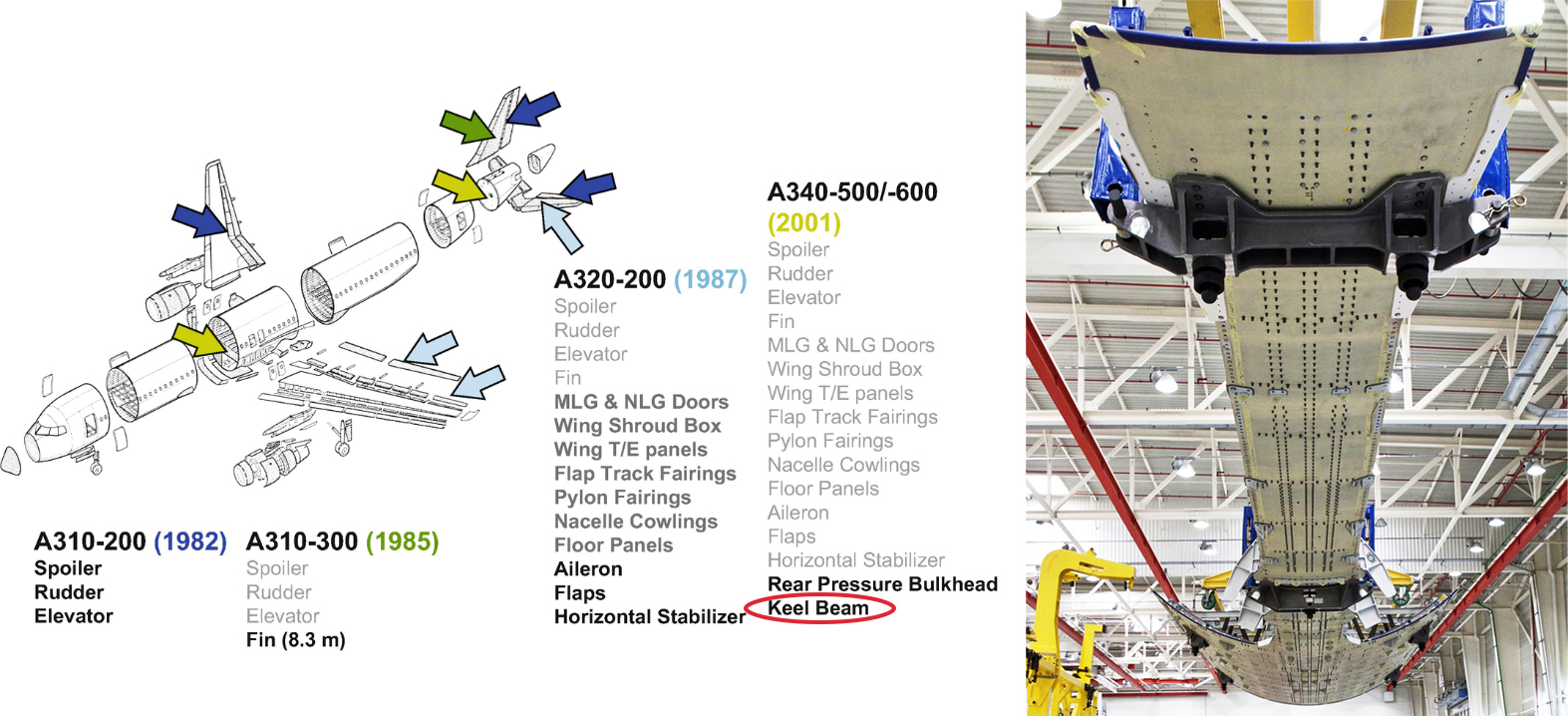
Килевая балка TPC
«Разработка килевой балки из термопластичного композита с использованием сварки для сборки является частью разработки Airbus самолета будущего, который включает такие программы, как Wing of Tomorrow и Fuselage of Tomorrow», - говорит Лагранья. «В рамках KEELBEMAN мы изготовили демонстрационную секцию килевой балки со стрингерами размером 250 мм на 500 мм на 1 метр и продемонстрировали возможность сварки этой конструкции с максимальной степенью автоматизации».
Лаграна отмечает, что демонстрационные стеновые панели и стрингеры были изготовлены с использованием однонаправленной (UD) ленты из углеродного волокна / полиэфиркетонекетона (PEKK) в процессе непрерывного компрессионного формования (CCM), разработанном CETMA (см. «Компрессионное формование для аэрокосмической промышленности» и «PEEK vs. PEKK по сравнению с ПАЭК и непрерывным компрессионным формованием »). «Есть также ребра для поперечных ребер жесткости, которые были изготовлены с использованием традиционного неизотермического формования прессованием компанией EURECAT», - добавляет Лагранья.
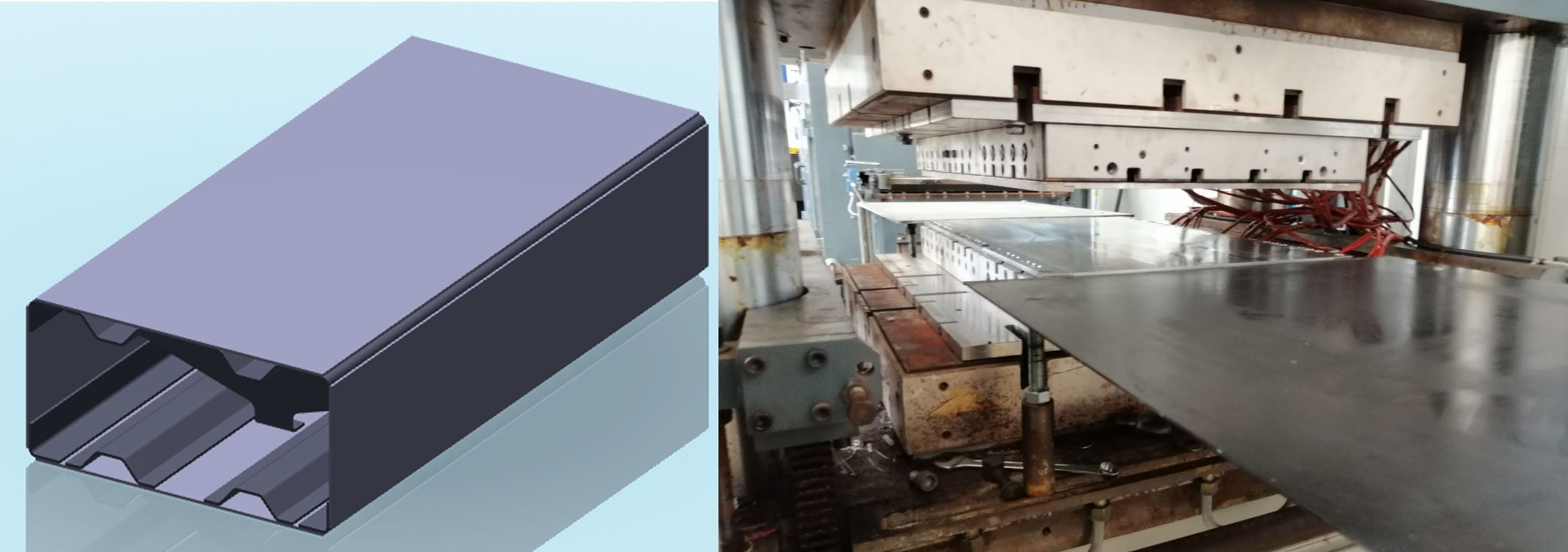
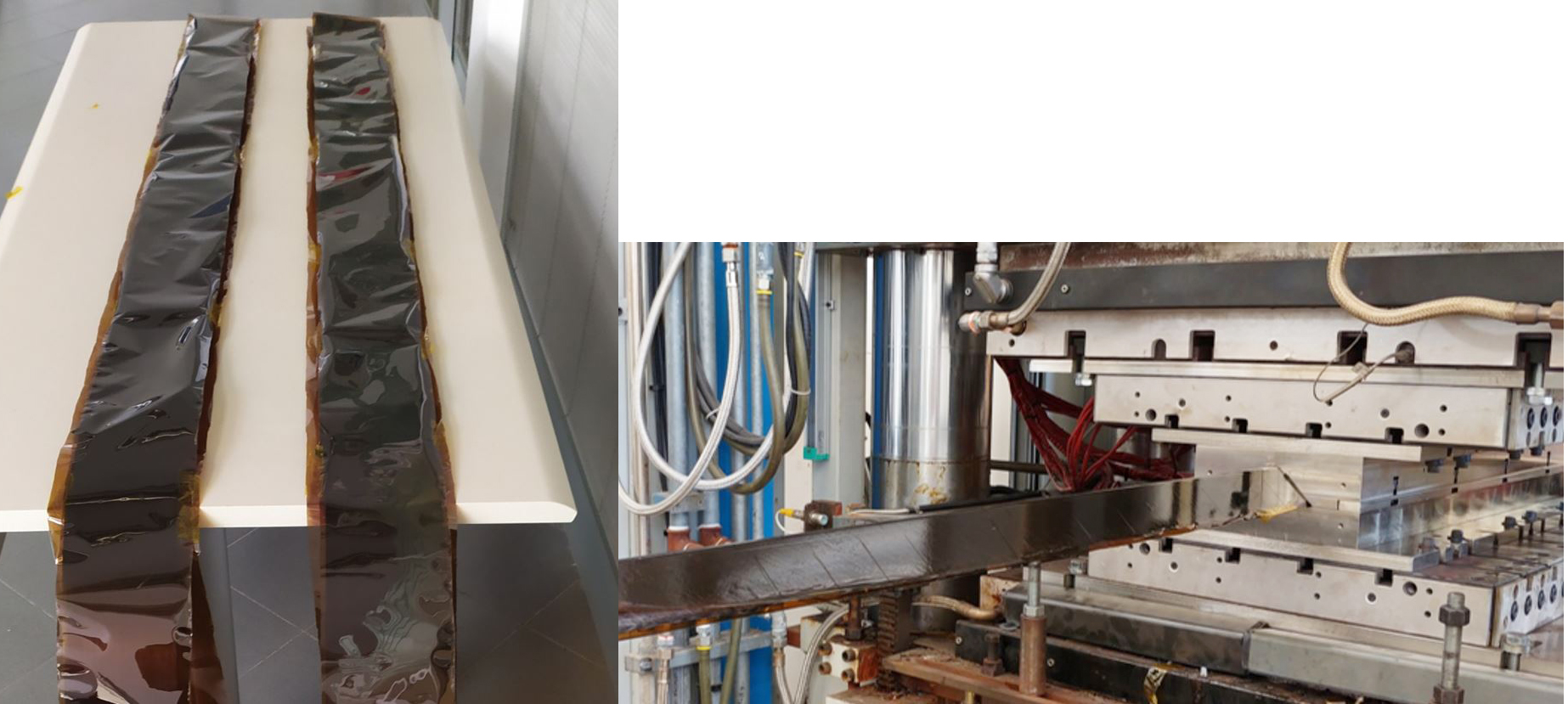
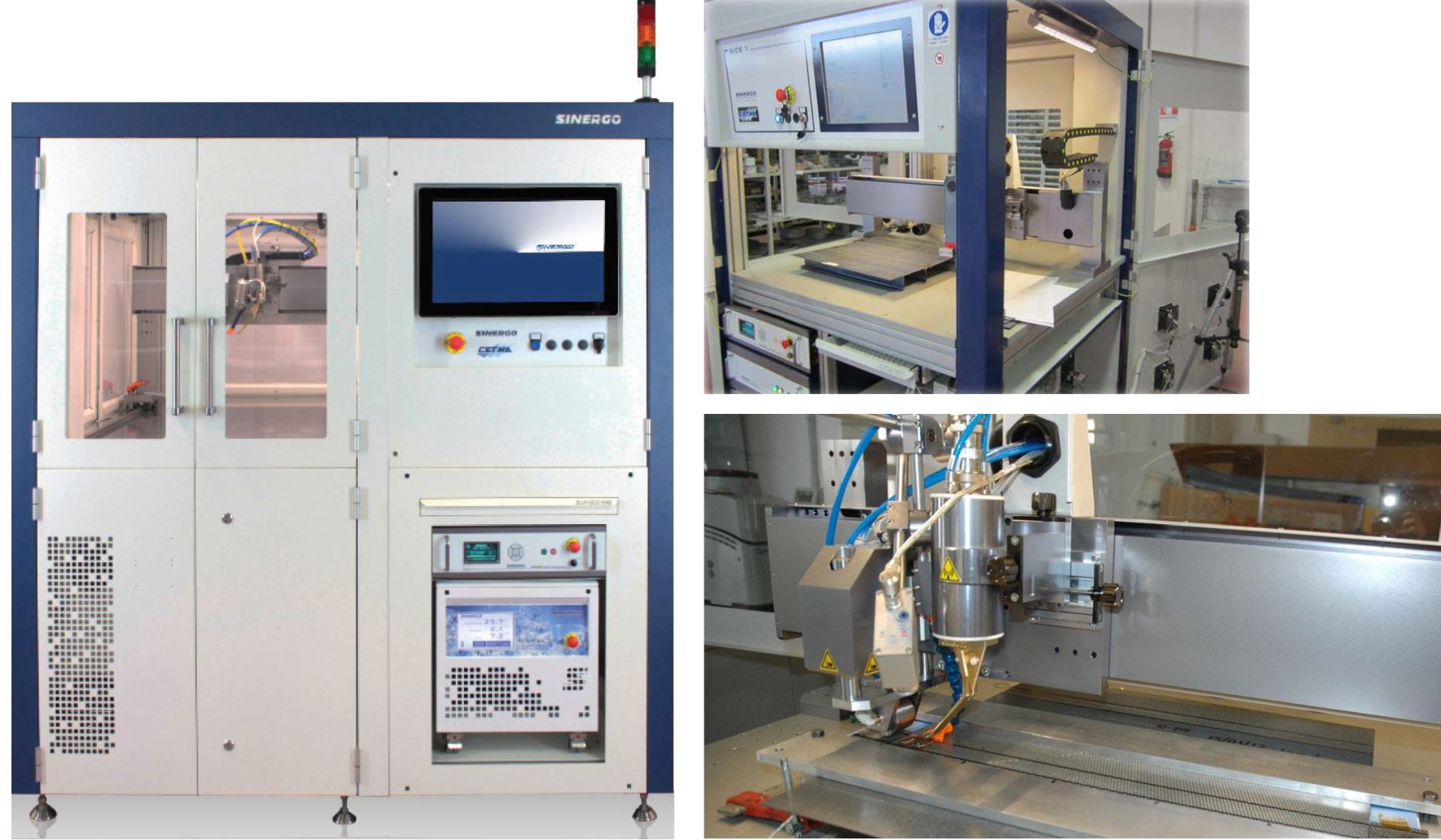
Индукционная сварка как ключ к успеху
Лаграна отмечает, что CETMA сыграла ключевую роль не только в производстве деталей для KEELBEMAN, но и в сборке демонстратора с использованием его запатентованной машины и технологии индукционной сварки. Эта сварка была первоначально разработана в рамках проекта ECO FAIRS первой программы Clean Sky (2011-2014), наряду с изотермическим и неизотермическим прессованием конструкций TPC, показанных выше. На ECO FAIRS CETMA использовала все эти технологии для производства прототипа демонстратора на основе существующей верхней панели (усиленная стрингерами обшивка) хвостовой части вертолета Agusta Westland, а также демонстрационного демонстратора изогнутого спонсонного обтекателя. Хотя они были изготовлены с использованием углеродного волокна CETEX (предоставленного TenCate, теперь Toray Advanced Composites) T300 3K 5HS с двусторонней пленкой PPS (полифениленсульфид), CETMA также зарекомендовала себя индукционной сваркой с композитами PEEK и PEI.
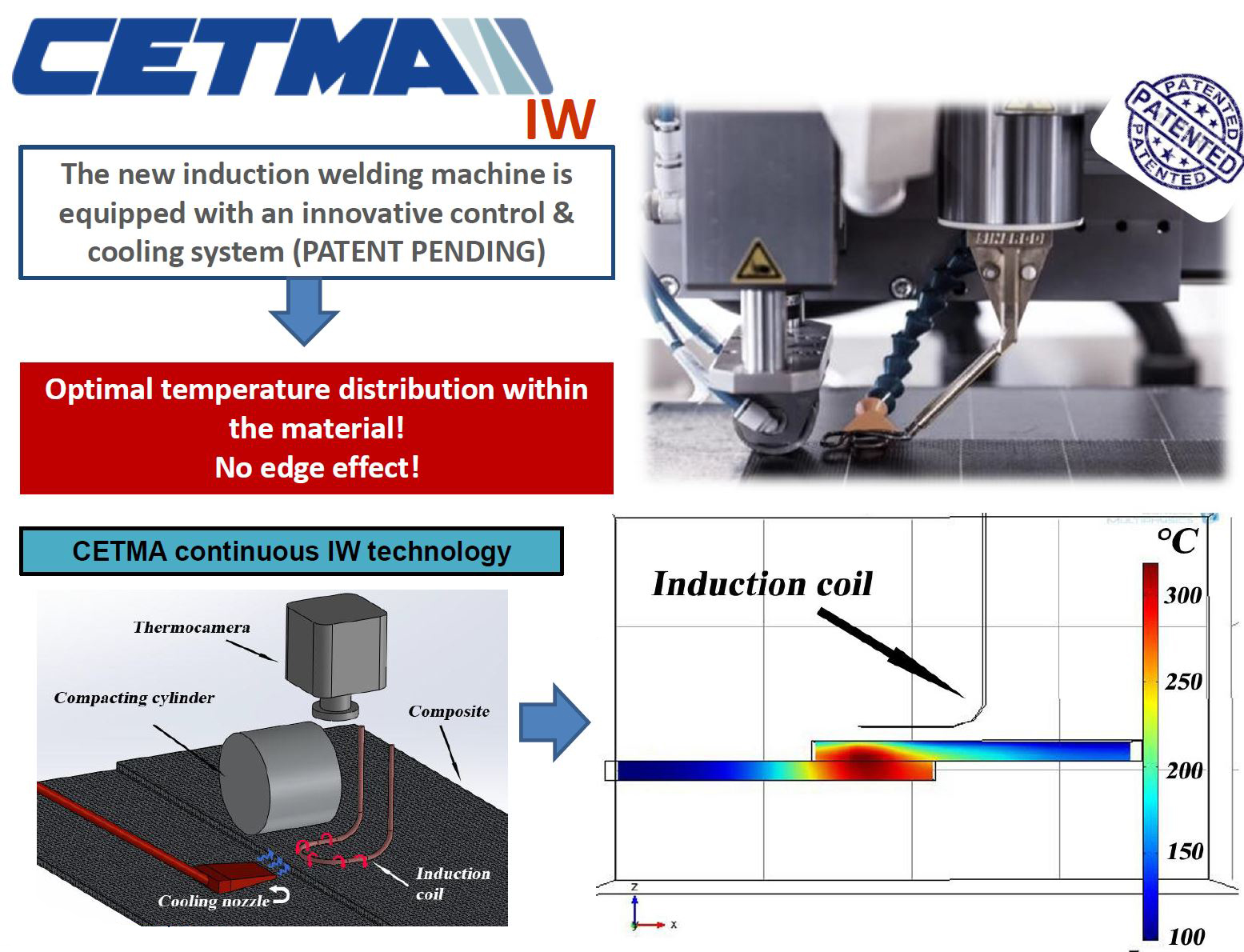
Компания CETMA выбрала индукционную сварку (IW) как наиболее перспективный из методов сварки термопластических композитов и вместе со специалистом по сварке и электронике SINERGO srl (Вальдоббьадене, Тревизо, Италия) разработала новый аппарат для индукционной сварки. Портальная машина SICE 1 WIDE, предлагаемая SINERGO (см. Изображение ниже) может непрерывно сваривать детали аэрокосмического качества размером до 1 на 1 метр. Он включает в себя надежную систему управления для обеспечения оптимального распределения температуры в свариваемых материалах. Машина оснащена охлаждаемым цилиндром для приложения давления уплотнения и системой воздушного охлаждения для отвода тепла там, где это необходимо, например, на краях, где поток индуцированных электрических вихревых токов ограничен, что приводит к высокой плотности тока и перегреву. . Также возможно установить головку для индукционной сварки CETMA на 6-осевой роботизированный манипулятор для сварки геометрически сложных форм.
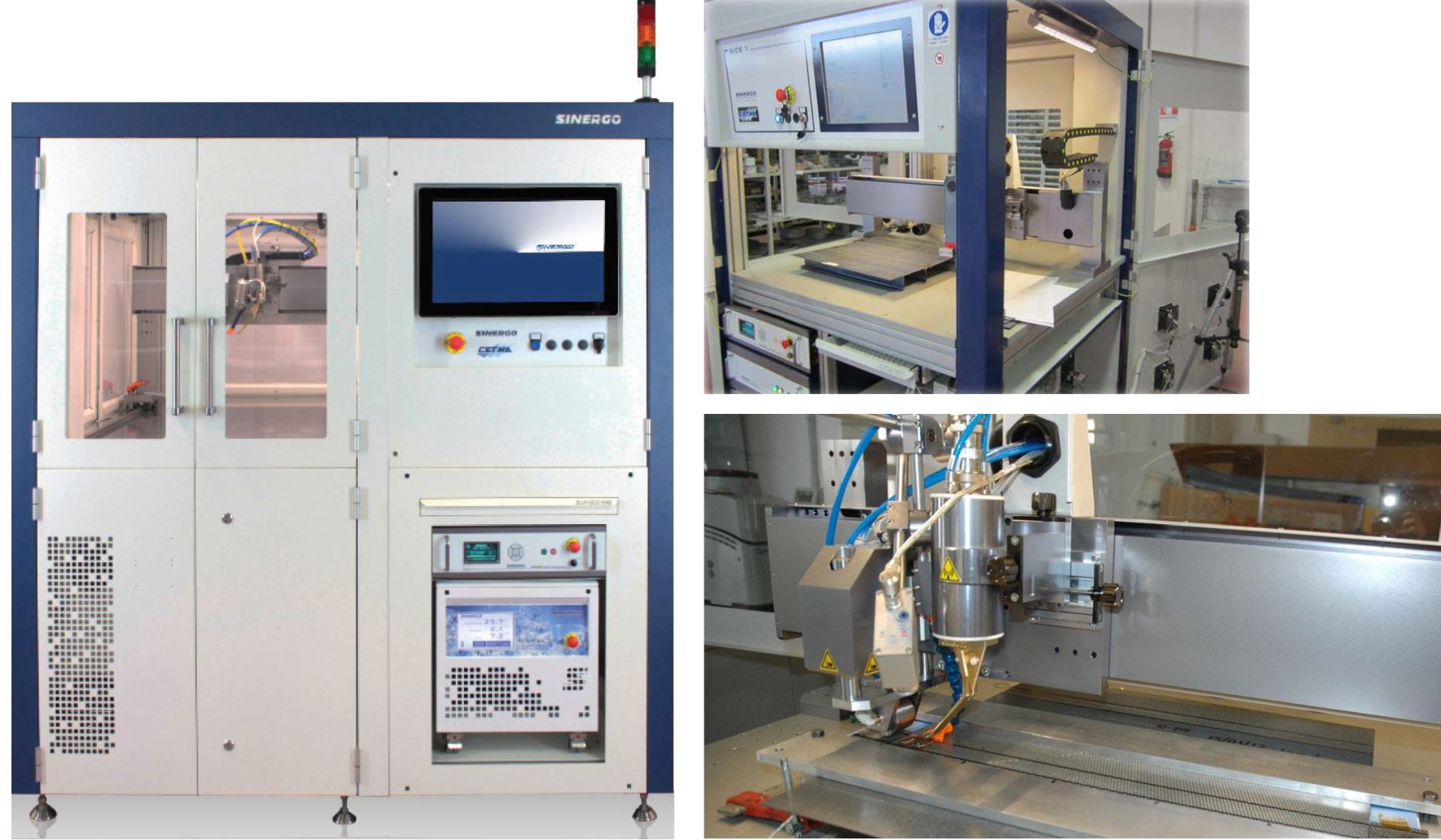
CETMA также разработала возможность оптимизации процесса индукционной сварки с помощью инструментов моделирования, выполнения численного анализа с использованием программного обеспечения для моделирования конечных элементов (FEM) COMSOL Multiphysics (COMSOL Inc., Берлингтон, Массачусетс, США). Он проверил эти модели с помощью большого количества физических испытаний. CETMA подтвердила свои оптимизированные технологические параметры испытаниями в один нахлест на сварных образцах, в которых значения прочности на сдвиг были очень близки к максимальным значениям, указанным в литературе. Примечательно, что они также были намного выше максимальных значений при использовании структурных клеев, сообщает CETMA.
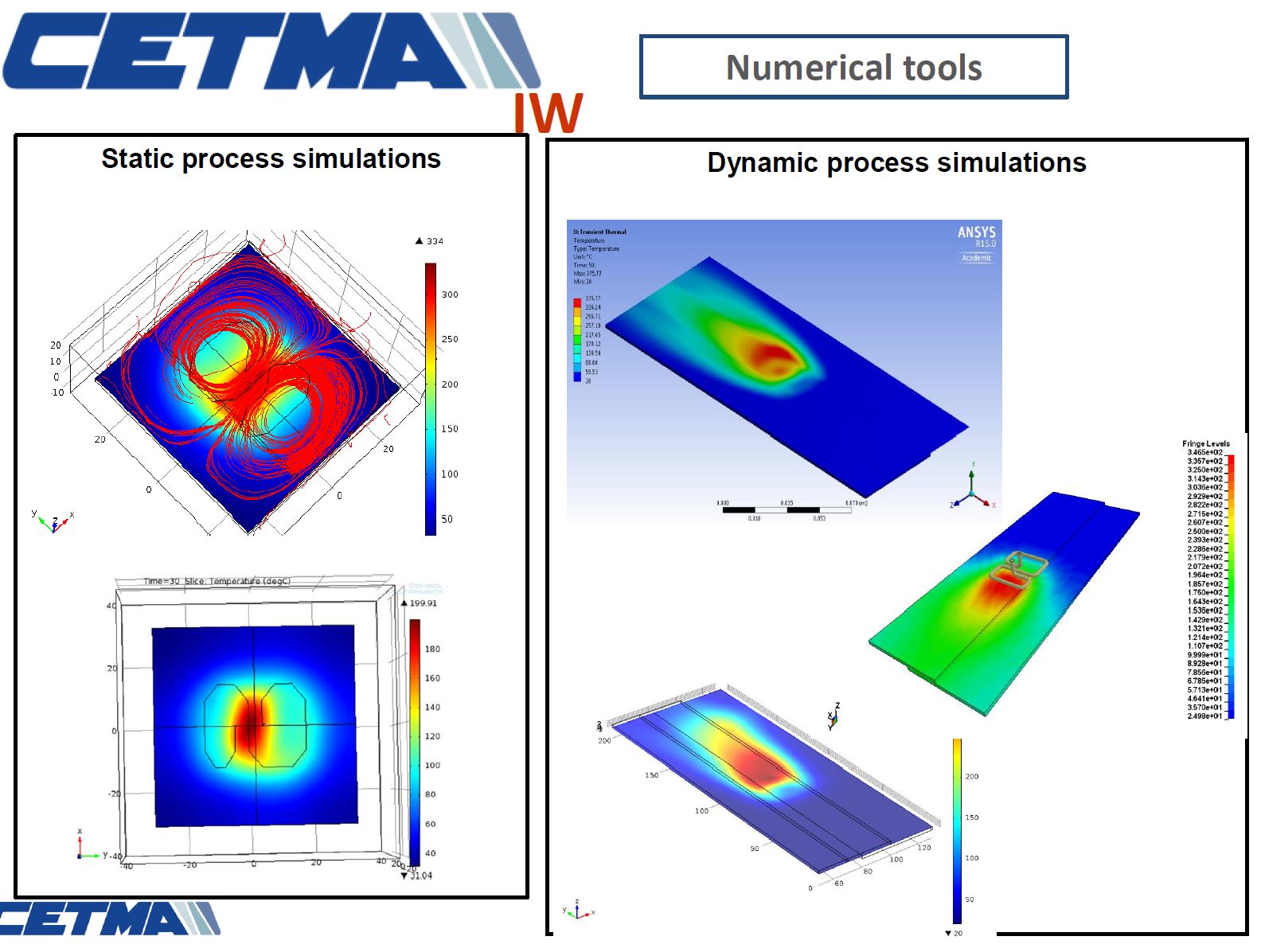
CETMA доказала свою способность к сварке самых разных материалов, включая тканое и углеродное волокно UD, а также PEEK, PEI, PEKK, PP, PA6, PA12 и даже сварку CF / эпоксидной смолы с использованием гибридного термопластичного PVB (поливинилбутираля). слой для перехода от термореактивной подложки к термопластической поверхности для сварки. (Большая часть деталей этого раздела была взята из презентации компетенций CETMA и Заключительный отчет CORDIS для ЭКО ЯРМАРКИ.) CETMA подала заявку на европейский патент в 2014 году, а изобретатели Сильвио Паппада и Андреа Саломи получили патент EP2801472A1 в 2016 году. CETMA опубликовала множество статей и презентаций по этой технологии, в том числе:
- «Моделирование методом конечных элементов для поддержки разработки внеавтоклавных технологий», A&D, 11–12 октября 2012 г.
- «Моделирование методом конечных элементов для поддержки непрерывной индукционной сварки композитов ПФС-углерод», SEICO 13, 11-13 марта 2013 г. «Париж».
- «Разработка новой машины для индукционной сварки термопластичных композитов в аэрокосмическом секторе», XXII конференция Итальянской ассоциации аэронавтики и астронавтики, Неаполь, 9–12 сентября 2013 г.
- «Индукционная сварка в аэрокосмическом секторе», TPRC, Европейский консорциум термопластичных композитов, веб-конференция, декабрь 2013 г.
- «Полномасштабные испытания термопластических компонентов для аэрокосмической отрасли», SEICO 14, 10-11 марта 2014 г., «Париж».
- «Новое оборудование для индукционной сварки для аэрокосмической отрасли», журнал JEC, № 87, март 2014 г., стр. 89-91.
Статус KEELBEMAN и дальнейший путь
Airbus посетил CETMA в декабре, чтобы увидеть заключительную сварку 1-метровой демонстрационной секции, а команда KEELBEMAN также провела окончательный анализ уровня технологической готовности (TRL). «Мы получаем хорошие результаты и развиваем технологию с TRL 3 до TRL 4», - говорит Лагранья. Следующие шаги могут включать дальнейшую разработку TRL 6 и производство полномасштабной килевой балки, которая будет установлена на одном из демонстраторов Clean Sky 2, например, полноразмерный нижний центральный фюзеляж WP 2.3.2, но это еще не было сделано. решил.
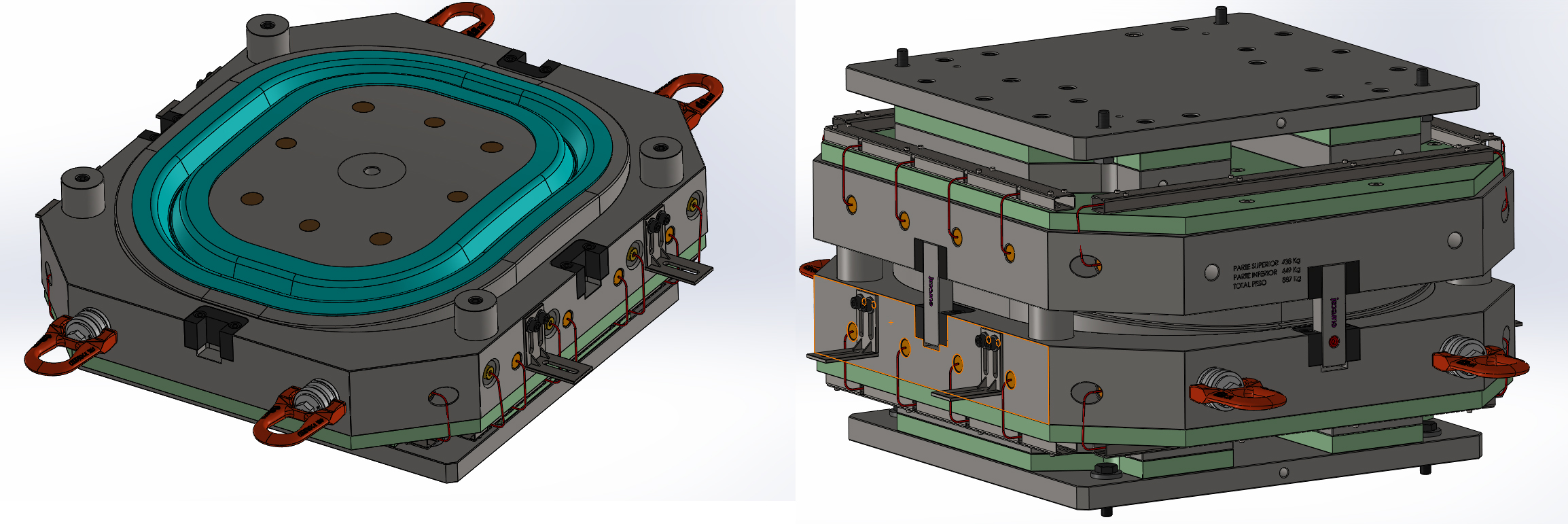
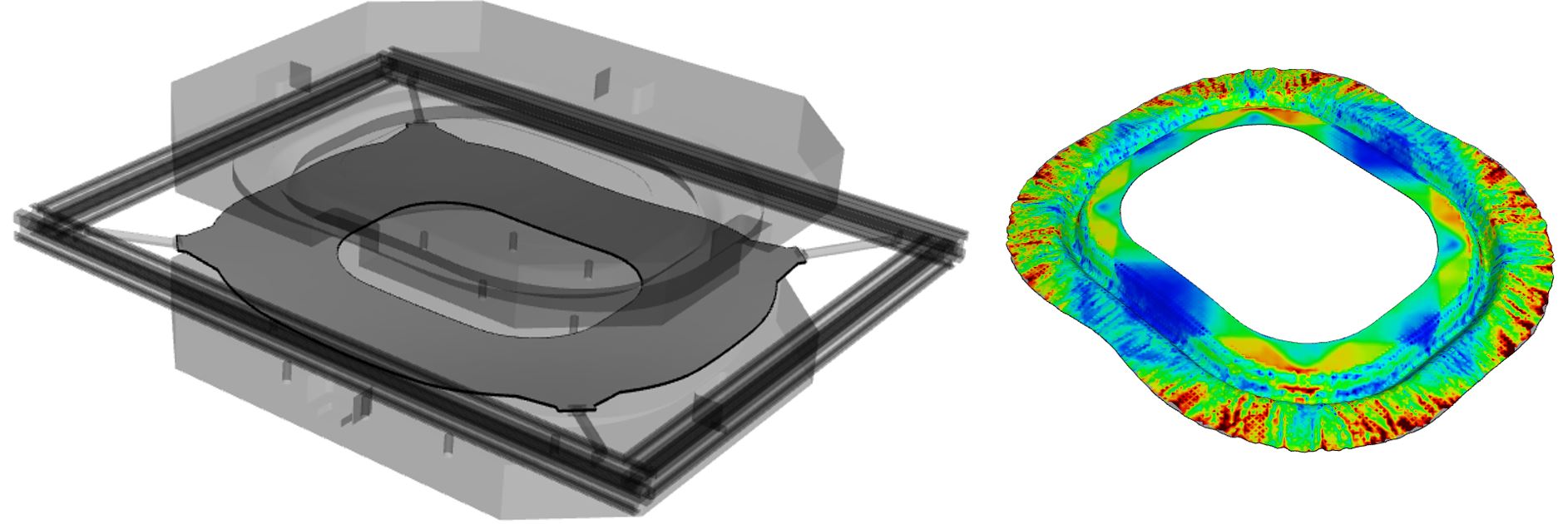
Проект WINFRAME 4.0 для оконных рам TPC
Еще одна программа из термопластичных композитов (TPC) для EURECAT - это WINFRAME 4.0 с целью разработки и производства 24 оконных рам для интегрированного наземного демонстратора фюзеляжа / кабины регионального самолета (см. Объяснение разработок Clean Sky 2 для региональных самолетов и Full -масштабный демонстратор инновационного фюзеляжа и пассажирской кабины ниже). Партнерами WINFRAME 4.0 являются:
- Многонациональная аэрокосмическая компания Леонардо (Рим, Италия) в качестве руководителя темы.
- EURECAT
- Sofitec.
«Используемый нами метод позволяет производить одну оконную раму каждые 10 минут», - говорит Лаграна. Этапы производства включают в себя:нагревание заготовок из ламината TPC в печи, перевод в форму, закрытие формы в прессе, применение тепла и давления в течение 10-20 минут и демонтаж готовой детали (деталей). «Такой подход не только позволяет достичь более коротких циклов, чем жидкое формование, но и позволяет получить гораздо более дешевую оснастку», - добавляет он. «Этот процесс хорошо известен в автомобильной промышленности, это компрессионное формование в высокоавтоматизированной конфигурации, которое повышает качество детали, но в аэрокосмической отрасли используются другие материалы, в данном случае армированный углеродным волокном PPS и углеродное волокно от Toray. Advanced Composites (ранее TenCate). К концу этого проекта мы достигнем TRL 6 для этих технологий », - говорит Лаграна.
Проект COFRARE:С-образные рамы RTM и стяжки из термопласта
Проект COFRARE 2020 является расширением первоначального проекта COFRARE 2.0:
Чистое небо 2 - JTI-CS2-2015-CFP02-AIR-02-16. «Разработка технологии производства композитных каркасов с высокой производительностью и низкой стоимостью» Срок реализации проекта:с 2016 по 2018 годы.
Целью проекта Clean Sky 2 COFRARE 2.0 было разработать конкурентоспособный и осуществимый процесс производства композитных рам из углеродного волокна, которые будут использоваться в фюзеляже из композитных панелей для региональных самолетов. Включены партнеры:
- Базирующаяся в Неаполе компания Tier 1, занимающаяся поставкой аэрокосмической продукции и инжиниринговая / индустриальная компания DEMA (Design Manufacturing SpA, Сомма Везувиана, Италия)
- EURECAT
- LGAI Technological Center S.A., подразделение Applus + Laboratories в Барселоне, Испания, провела тестирование.
Целью проекта COFRARE 2020 следующего поколения является производство полномасштабных композитных каркасов и поперечных стяжек, которые будут использоваться в интегрированном наземном демонстраторе фюзеляжа / кабины Clean Sky 2. Этот демонстрационный ролик организован в рамках проекта IADP (платформа для демонстрации инновационных самолетов) компании Clean Sky 2 и подробно описан в разделе 5.2.2 документа Совместной технической программы за март 2015 года:
« Региональные самолеты - ключевой элемент Clean Sky через специальный ITD (Integrated Technology Demonstrator) - Зеленые региональные самолеты (GRA) , обеспечивая необходимые строительные блоки для системы воздушного транспорта, которая уважает окружающую среду, обеспечивает безопасную и бесперебойную мобильность и укрепляет промышленное лидерство в Европе. В чистом небе 2 , … Цели демонстрации региональных авиалайнеров IADP намного сложнее, полнее и труднее, чем цели нынешней Clean Sky Проект GRA , который был вынужден работать в рамках бюджета и временных ограничений. … »
Совместная техническая программа на 2015 год предусматривает разработку региональных самолетов, включающих два летающих испытательных стенда и пять крупных интегрированных наземных демонстраторов. Последний включает полномасштабный инновационный демонстратор фюзеляжа и пассажирской кабины :«Фюзеляж станет полномасштабной демонстрацией технологий для композитных материалов, конструкций и производства направлена на [достижение] снижения веса и затрат, а также на минимизацию воздействия на окружающую среду за счет экологического проектирования и оптимизации энергопотребления на протяжении всего жизненного цикла (в направлении нулевого воздействия) ».
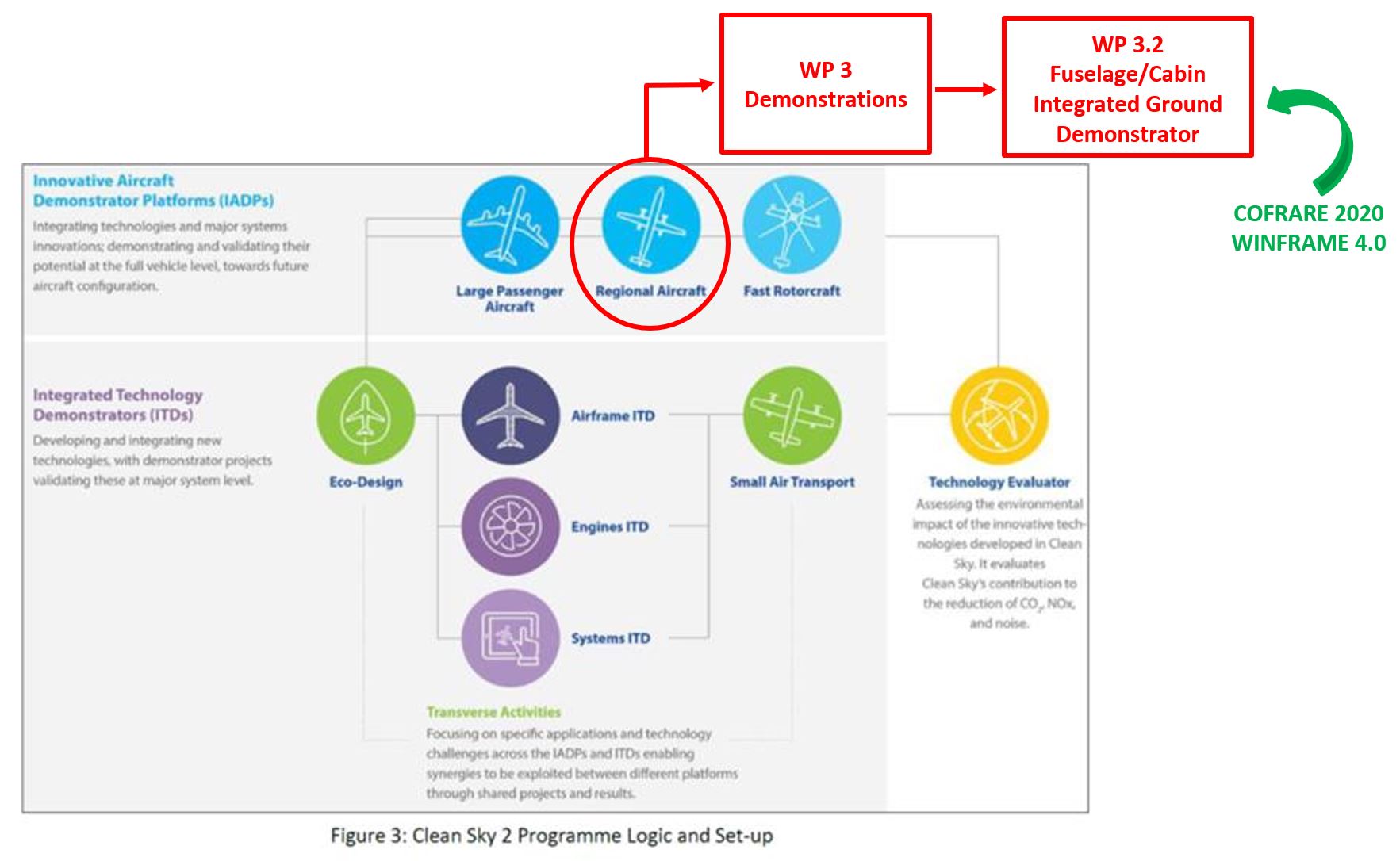
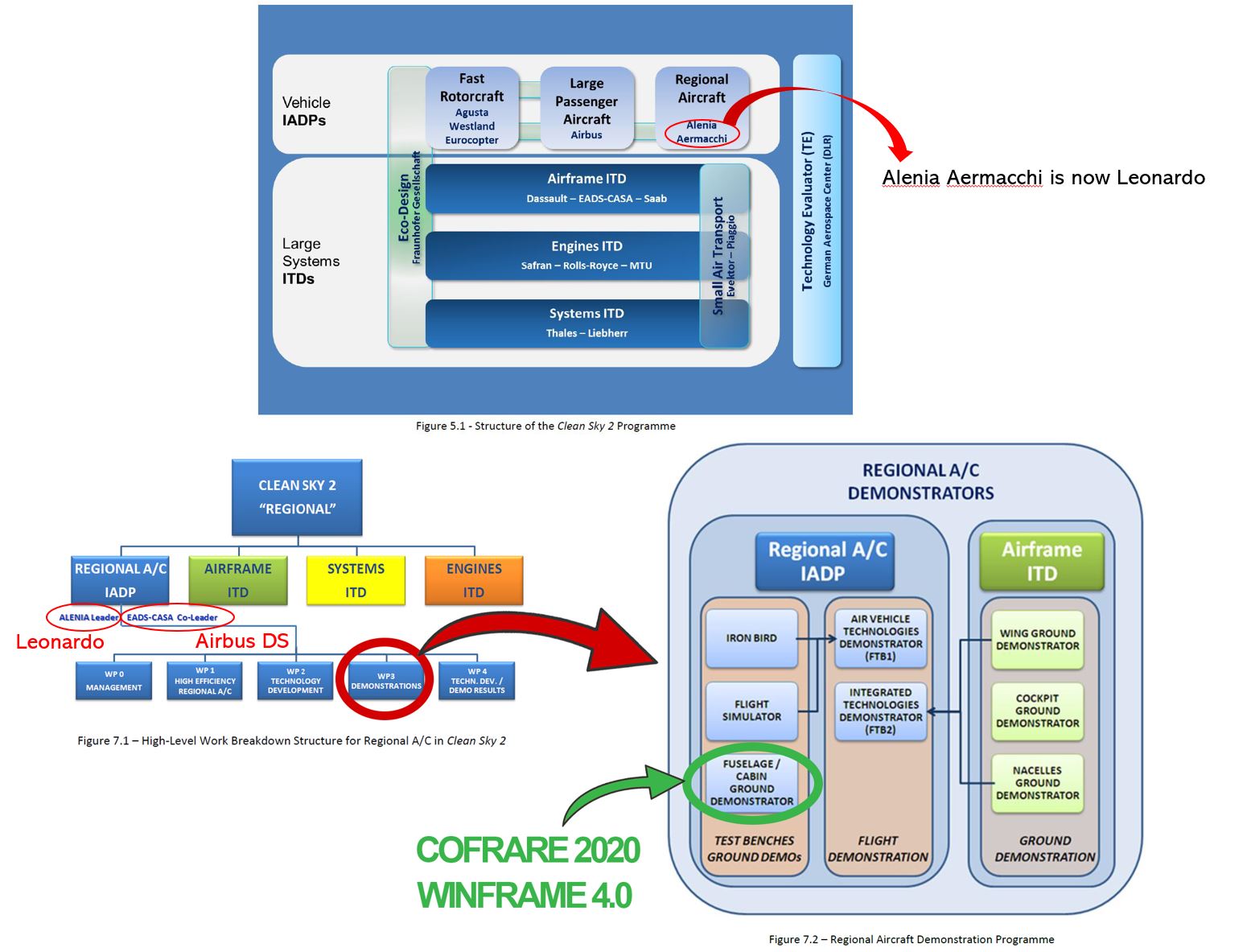
Партнерами проекта COFRARE 2020 являются:
- Леонардо как руководитель темы
- EURECAT
- ДЕМА
- Производство узлов и агрегатов самолетов A. Абете (Нола / Марильяно, Италия).
«В COFRARE 2020 мы производим каркасы фюзеляжа с использованием RTM (литье с переносом полимера), которые будут интегрированы в демонстрационный образец фюзеляжа», - поясняет Лагранья. «Мы используем технологию Ziplus от Shikibo (Осака, Япония), которая производит преформы, которые хорошо подходят для впрыска со смолой». Shikibo Ltd. является частью Composite Alliance Corp. (Даллас, Техас, США) и предлагает различные технологии предварительного формования тканей.
Одним из интересных аспектов этой программы является использование датчиков Synthesites (Уккле, Бельгия) для мониторинга в реальном времени поступления смолы, температуры, давления, Tg и отверждения. «Датчики расположены в определенных областях композитной детали и инструмента RTM, чтобы оптимизировать стратегию впрыска смолы», - отмечает Лаграна. Инжекция осуществляется с помощью высокоавтоматизированной системы, поставляемой ISOJET (Корба, Франция), которая также является частью Composite Alliance Corp. Датчики Synthesites являются диэлектрическими датчиками, но в отличие от большинства диэлектрических анализов (DEA), которые основаны на переменном токе (AC) , Synthesites использует постоянный ток (DC). «Наши сенсоры хорошо работают с материалами с высоким удельным сопротивлением, такими как смолы, и, поскольку мы прикладываем одно напряжение, нам не нужно анализировать несколько частот, но мы достигаем высокой точности даже в конце отверждения», - объясняет директор Synthesites д-р. Никос Пантелелис.
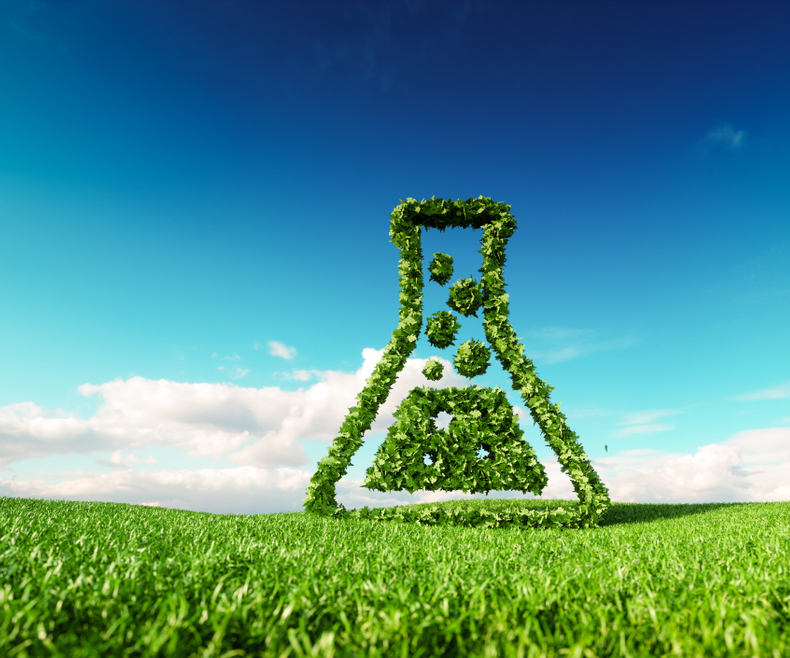
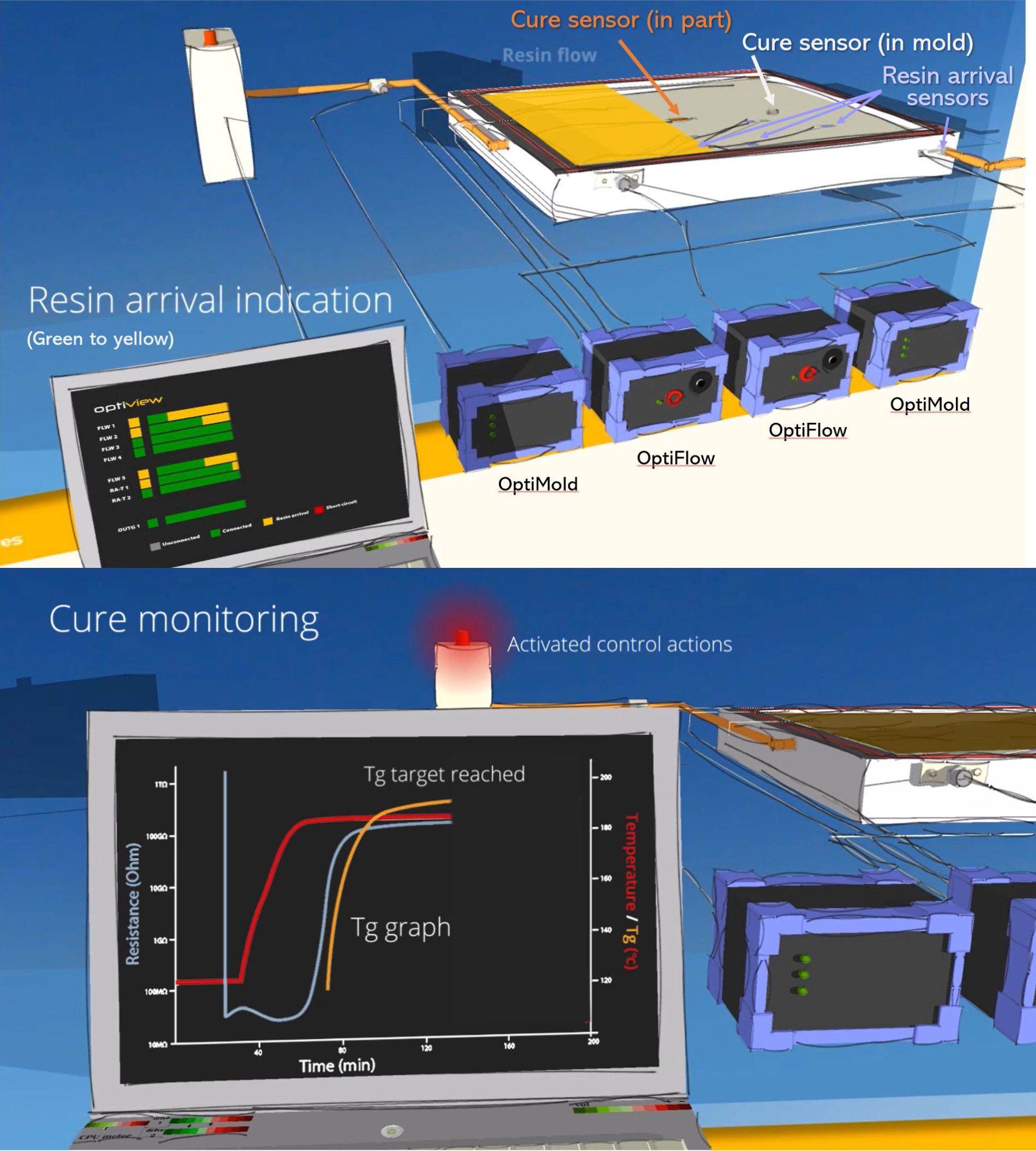
«Мы познакомились с Synthesites на конференции SAMPE в 2011 году», - вспоминает Лаграна. «Они говорили о датчиках для сокращения цикла отверждения. Мы изучаем, как автоматизировать преформы для каркасов фюзеляжа и даже использовать более быструю обработку с помощью HP-RTM (RTM высокого давления), но все же время обработки у вас составляет 3-4 часа. Однако с Synthesites мы сократили цикл отверждения на 50 процентов, контролируя Tg. Сейчас мы проверяем свойства. Эти датчики могут работать при высоком давлении, но в процессе RTM мы используем давление всего 8 бар ».
Диэлектрические датчики постоянного тока Synthesites, система контроля потока жидкой смолы OptiFlow и система контроля отверждения OptiMold были продемонстрированы в производстве различными производителями ветряных лопастей. Они также используются Bombardier Aerospace (Белфаст, Великобритания) для производства формованного крыла из жидкого композита для самолетов Airbus 220 серии C. Немецкий аэрокосмический центр (DLR, Stade, Германия) продемонстрировал сокращение цикла отверждения до 50% для обоих препрег в автоклаве и RTM, в то время как Национальный центр композитов (NCC, Бристоль, Великобритания) продемонстрировал, что даже для высокореактивных смол расчеты Tg в реальном времени, сделанные на основе сенсорных измерений температуры и удельного сопротивления смолы, являются такими же точными, как Tg, измеренные для отвержденных панелей. с помощью дифференциальной сканирующей калориметрии (ДСК).
Соединение рам с помощью поперечных стяжек TPC
Еще одна ключевая часть COFRARE 2020 - это более крупносерийный метод производства для производства сотен поперечных стяжек и кронштейнов, необходимых для соединения С-образных рам фюзеляжа RTM с композитными панелями фюзеляжа. «Мы разрабатываем 255 различных геометрических форм для кронштейнов из термопластичного композита, изготовленных методом компрессионного формования», - говорит Лаграна. (Обратите внимание:у GKN Fokker есть несколько проектов Clean Sky 2, в которых он будет производить кронштейны TPC для многофункционального демонстратора фюзеляжа в IADP большого пассажирского самолета; эта работа в COFRARE 2020 предназначена для небольших региональных самолетов.) Ниже показан основной метод с использованием подходящих стальных инструментов и горячего пресса. «Стоимость таких инструментов для компрессионного формования составляет всего 2000 евро, что очень доступно по сравнению с инструментами RTM», - добавляет он. «Штамповка также обеспечивает очень короткое время цикла».
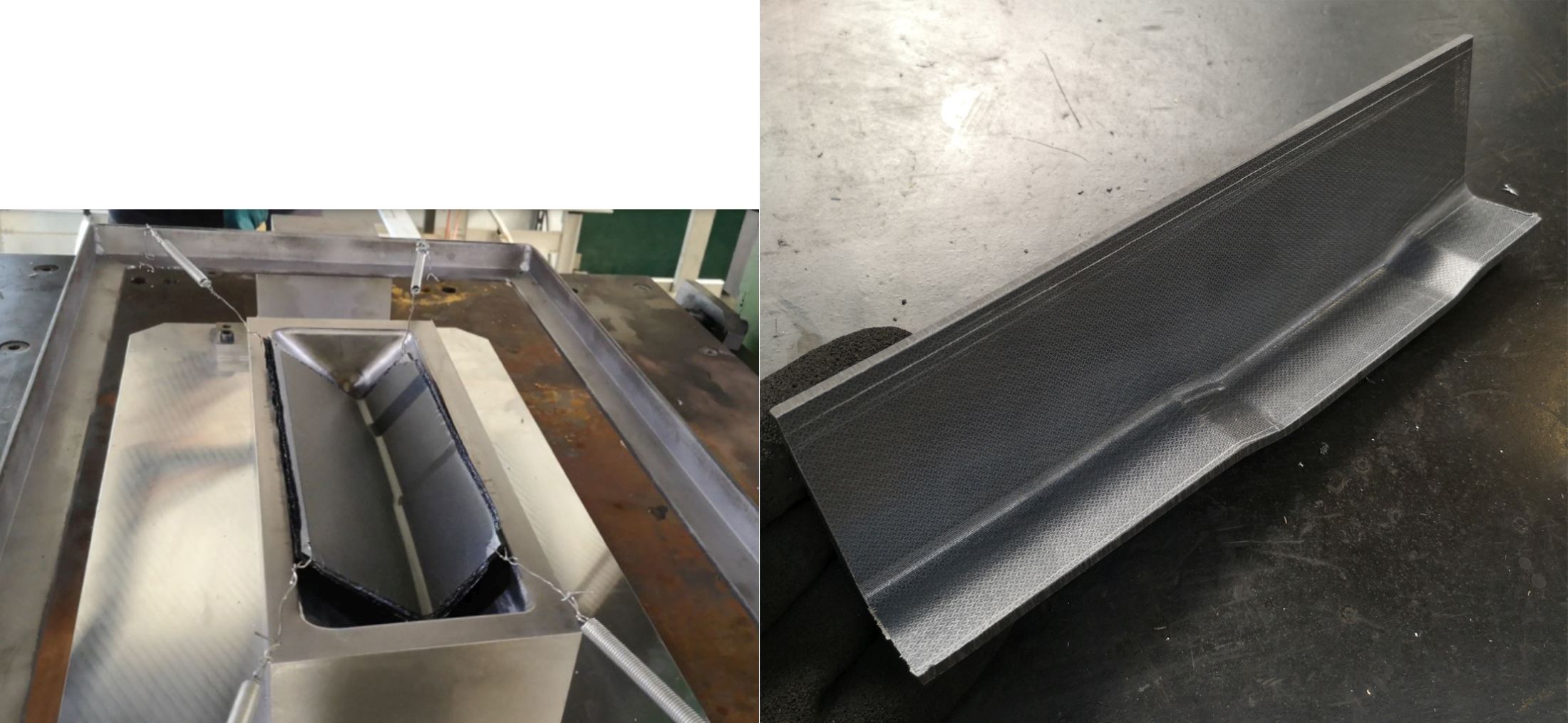
«EURECAT инвестирует в то, чтобы оставаться в авангарде развития технологий композитов», - говорит Лагранья. «Мы считаем, что необходимость в чистой окружающей среде резко увеличит использование композитов во всех видах транспорта, и что доступность и производительность будут идти вместе. Вот почему мы фокусируемся на автоматизированных технологиях вне автоклавов, чтобы предложить нашим клиентам ».
Следите за обновлениями в моем предстоящем блоге о проектах Clean Sky 2 STUNNING и MECATESTERS, в котором будет обсуждаться разработка сварных кронштейнов TPC для многофункционального демонстратора фюзеляжа и полная характеристика PAEK для этого проекта. Я также буду вести блог о синтетических материалах более подробно, а также о других разработках CETMA в области композитов. 2020 год будет очень интересным для композитов!
Смола
- Сэндвич с термопластическими сотами для повторного формования в более тонкие легкие композиты
- Настройка ультразвуковых датчиков для оптимизации и контроля процесса композитов
- Перерабатываемые, ремонтируемые и перерабатываемые эпоксидные смолы для композитов
- Объединение диэлектрических измерений переменного и постоянного тока для мониторинга отверждения композит…
- Солвей и Леонардо открывают совместную исследовательскую лабораторию термопластичных композитов
- Двери из термопласта впервые для автомобильных композитов
- LANXESS расширяет производственные мощности по производству термопластичных композитов, армированных непрерыв…
- TPAC и TPRC разрабатывают процесс переработки термопластичных композитов
- Сварка термопластичных композитов
- Консорциум термопластичных композитов нацелен на крупносерийное производство для автомобильной и аэрокосм…