Леонардо и CETMA:создание композитных материалов для снижения затрат и снижения воздействия на окружающую среду
Этот блог основан на моем интервью со Стефано Корвалья, инженером по материалам, руководителем отдела исследований и разработок и менеджером по интеллектуальной собственности подразделения Leonardo Aerostructures (Гротталье, Помильяно, Фоджа, производственные мощности Нола, юг Италии) и доктором Сильвио Паппада, инженером-исследователем и руководителем программ с Леонардо в CETMA (Бриндизи, Италия).
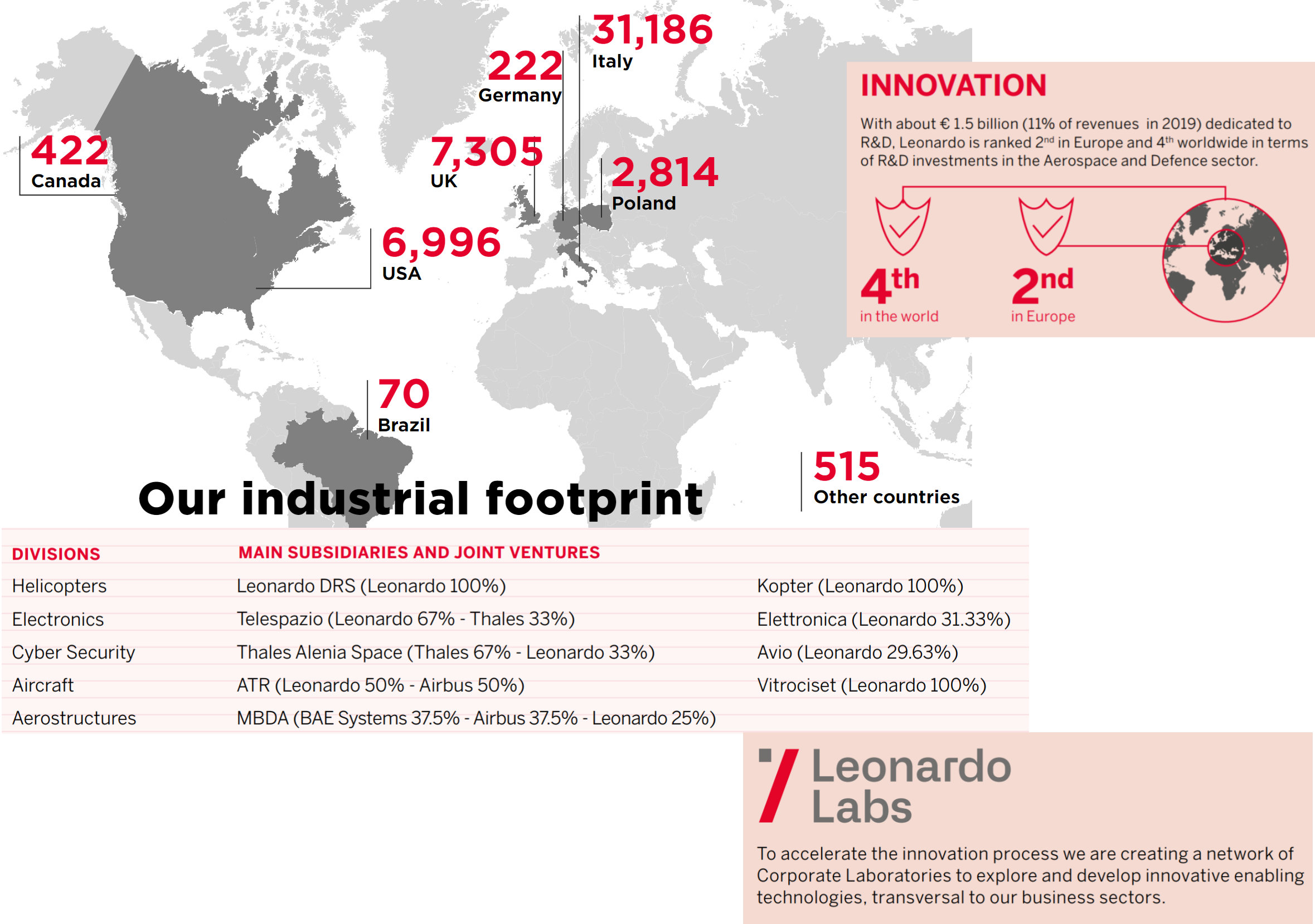
Леонардо (Рим, Италия) - один из крупнейших мировых игроков в аэрокосмической отрасли, обороне и безопасности с доходом 13,8 миллиарда евро и более чем 40 000 сотрудников по всему миру. Компания предоставляет комплексные решения в глобальном масштабе для воздушных, наземных, морских, космических, кибербезопасных и беспилотных систем. Имея около 1,5 млрд евро (11% выручки в 2019 году), выделенных на исследования и разработки, Леонардо занимает 2-е место в Европе и 4-е место в мире по инвестициям в исследования в аэрокосмическом и оборонном секторе.
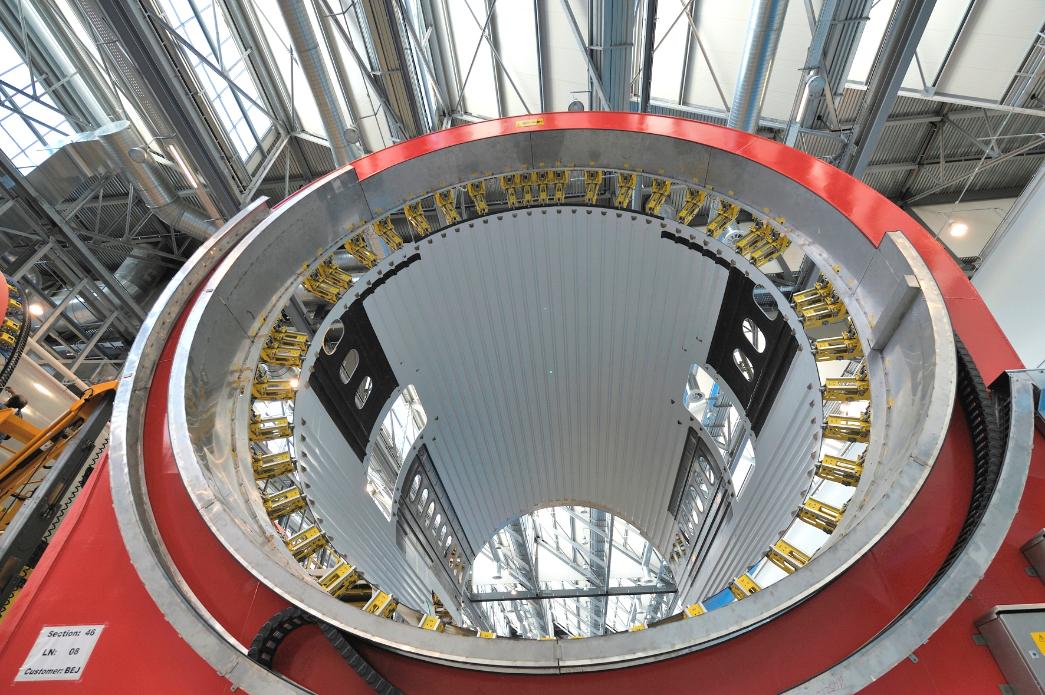
Через свое подразделение «Аэроструктуры» Леонардо обеспечивает изготовление и сборку крупных структурных компонентов, включая фюзеляжи и оперение, из композитных материалов и традиционных материалов для основных мировых программ гражданской авиации.
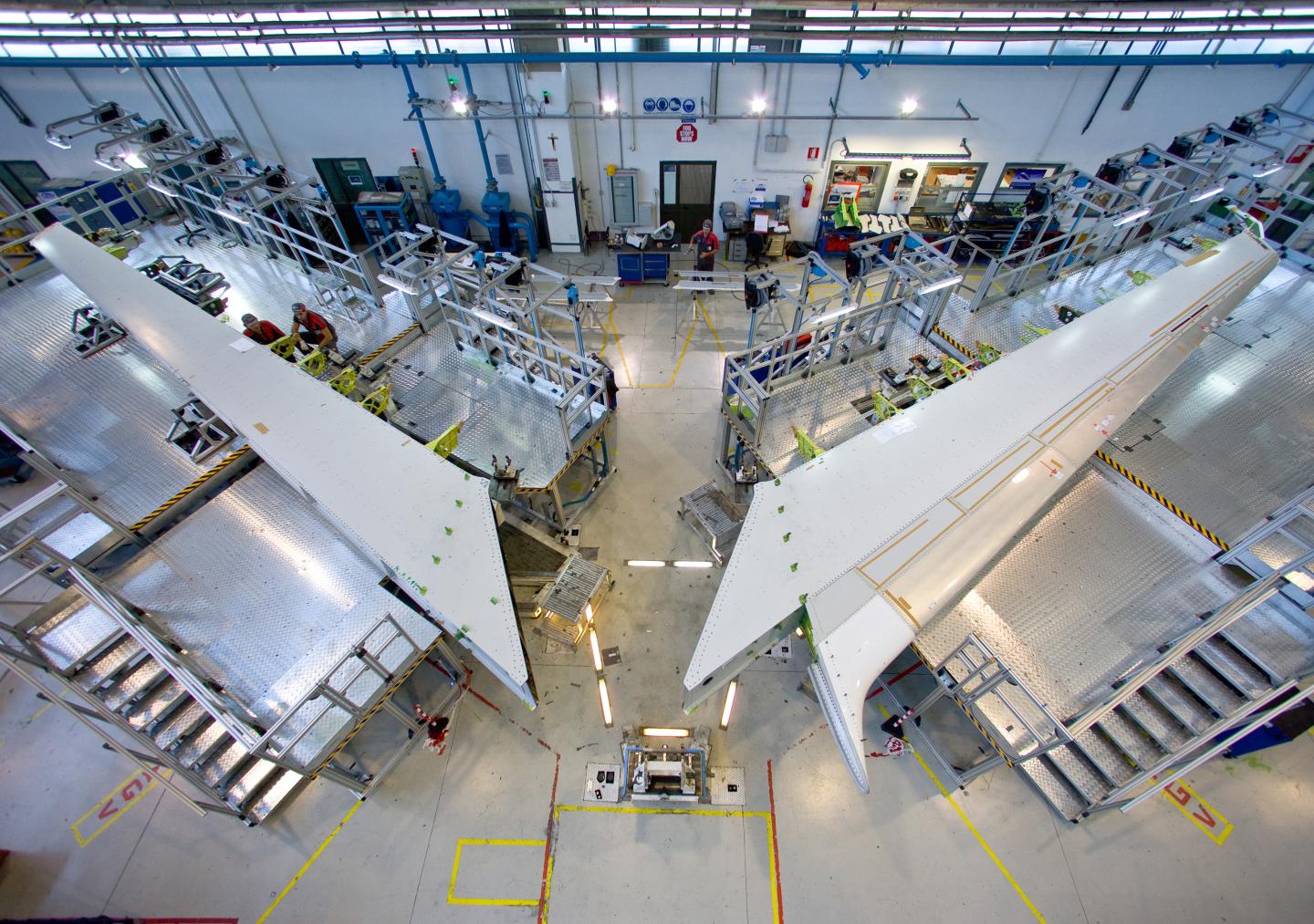
В области композитных материалов подразделение Leonardo Aerostructures производит «неразъемные стволы» для центральных секций 44 и 46 фюзеляжа Boeing 787 на своем заводе в Гротталье, а также горизонтальные стабилизаторы на своем заводе в Фоджи - всего около 14% от планера 787. Производство других композитных конструкций включает в себя на заводе в Фоджиа изготовление и сборку оперения для коммерческих самолетов ATR и Airbus A220. Foggia также производит композитные детали для Boeing 767 и для военных программ, включая Joint Strike Fighter F-35, истребитель Eurofighter Typhoon, военный транспорт C-27J и Falco Xplorer, последний член семейства беспилотных самолетов Falco производства Леонардо.
Работа с CETMA
«Мы ведем много работ с CETMA, например, в области термопластичных композитов и литьевого формования полимеров (RTM)», - говорит Корвалья. «Наша цель - подготовить научно-исследовательские и опытно-конструкторские работы к производству в кратчайшие сроки. В нашем отделе (НИОКР и управление интеллектуальной собственностью) мы также ищем прорывные технологии с более низким TRL [уровень технологической готовности - т. Е. Более низкий TRL является более зарождающимся и дальше от производства], но мы стремимся быть более конкурентоспособными и помогать нашим клиентам по всему миру. . »
«С самого начала нашей совместной работы, - добавляет Паппада, - мы всегда стремились сохранить низкие затраты и воздействие на окружающую среду. Мы обнаружили, что термопластичные композиты (ТПК) обеспечивают меньшее количество материалов по сравнению с термореактивными пластинами ».
Корвалья отмечает, что «вместе с командой Сильвио мы разработали эти технологии и построили несколько автоматизированных прототипов ячеек, чтобы оценить их в процессе производства».
Непрерывное компрессионное формование (CCM)
«CCM - хороший пример нашей совместной работы», - говорит Паппада. «Леонардо определил некоторые компоненты, изготовленные из термореактивных композитов, и вместе мы исследовали технологию, чтобы предоставить их в TPC, глядя на то, где находится большое количество деталей в самолете, например, стыковые конструкции и стойки с простой геометрией».
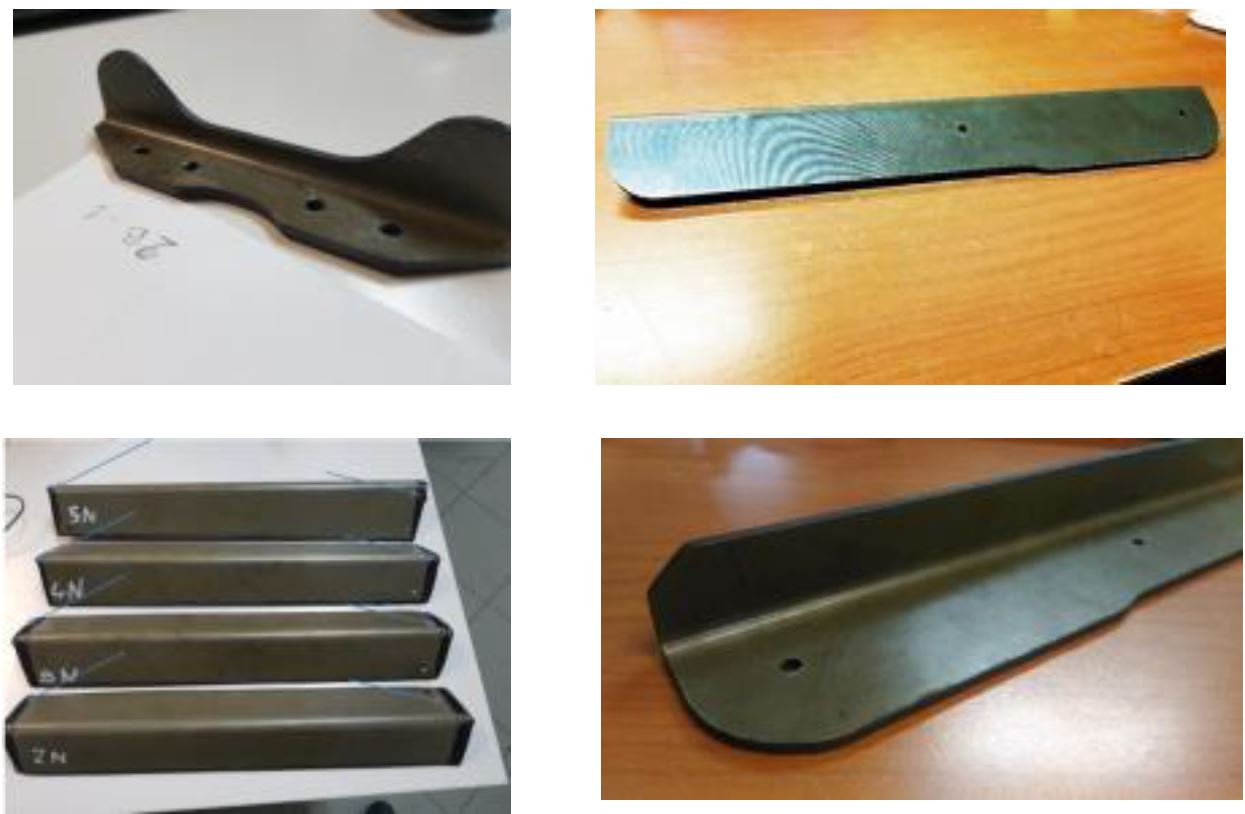
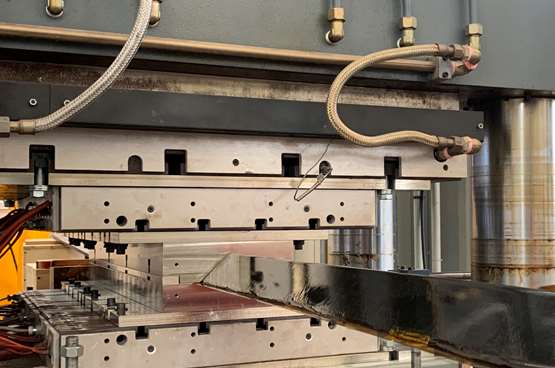
«Нам была нужна новая производственная технология, отличающаяся низкой стоимостью и высокой производительностью», - продолжает он. Он отмечает, что в прошлом отдельные компоненты TPC производились с большим количеством отходов. «Итак, мы производим сетку формы на основе неизотермического прессования, но с некоторыми нововведениями (патенты поданы) для уменьшения количества брака. Для этого мы разработали полностью автоматизированную ячейку, которую затем построила для нас итальянская компания ».
Эта ячейка способна производить компоненты, разработанные Леонардо, по словам Паппады, «из расчета один компонент каждые 5 минут, работая 24 часа в сутки». Однако затем его команде пришлось разобраться с производством преформы. «Вначале нам требовался процесс плоского ламинирования, поскольку на тот момент это было узким местом», - объясняет он. «Итак, наш процесс начинается с заготовки (плоский ламинат), которую нагревают в инфракрасной (ИК) печи, а затем помещают в пресс для формования. Плоские ламинаты обычно производятся на больших прессах и требуют 4-5 часов цикла. Мы решили исследовать новый метод, позволяющий быстрее производить плоский ламинат. Таким образом, при поддержке инженеров Леонардо мы разработали высокопроизводительную линию CCM в CETMA. Мы сократили время цикла для детали размером 1 метр на 1 метр до 15 минут. Важно отметить, что это непрерывный процесс, поэтому мы можем производить продукцию неограниченной длины ».
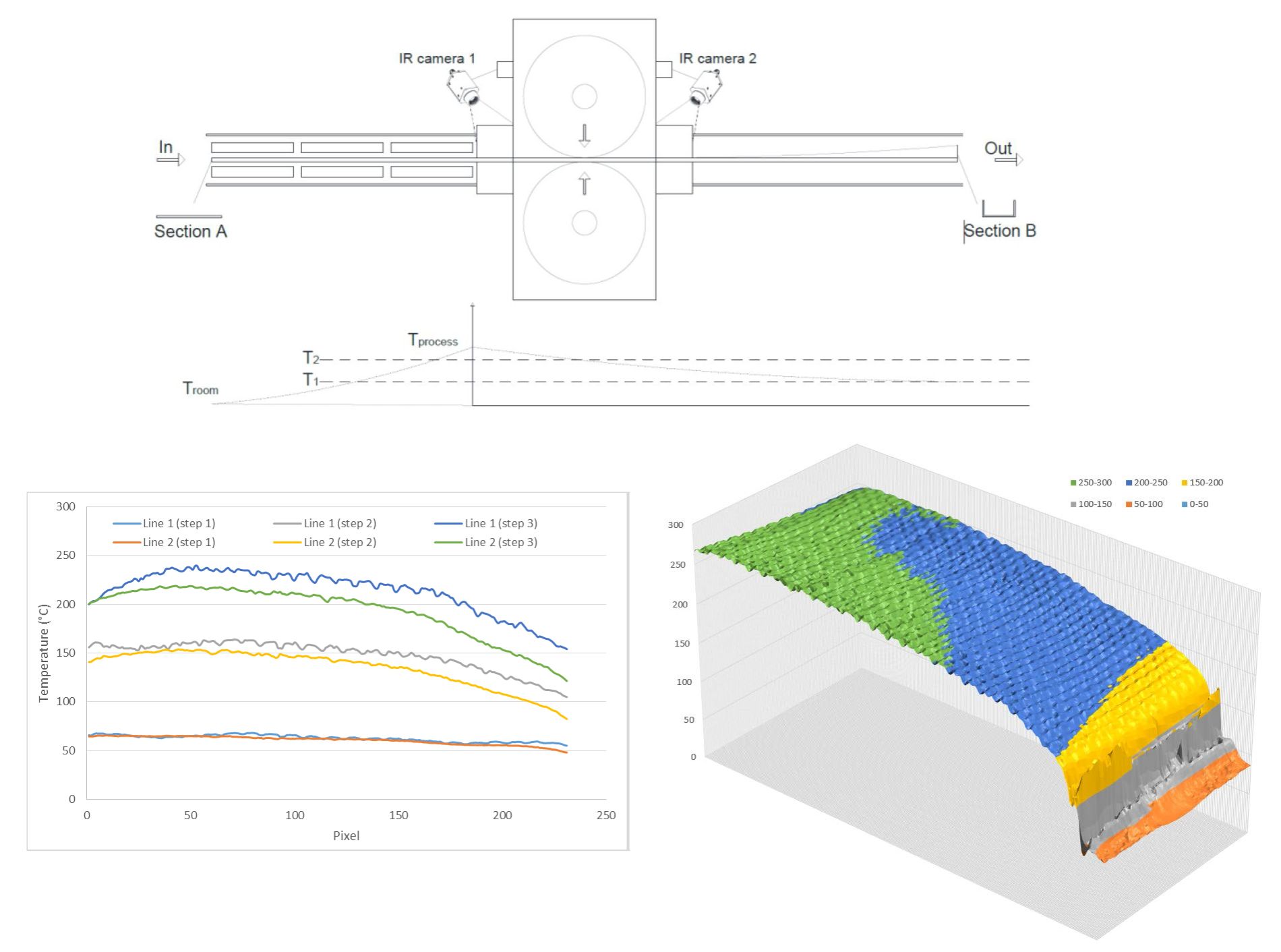
Но чем это новое по сравнению с CCM, используемым более десяти лет компанией Xperion, ныне XELIS (Маркдорф, Германия)? «Мы разработали аналитические и численные модели, позволяющие прогнозировать такие дефекты, как пустоты», - говорит Паппада. «Мы сделали это в сотрудничестве с Леонардо и Университетом Саленто (Лечче, Италия), чтобы понять параметры и их влияние на качество. Мы использовали эти модели для разработки нового CCM, в котором мы можем иметь очень большую толщину, но при этом высокое качество. Благодаря этим моделям мы можем оптимизировать температуру и давление, а также способы их применения. Есть много технологических аспектов, которые вы можете разработать для равномерного распределения температуры и давления; однако нам нужно было понять, как они влияют на механические характеристики и рост дефектов в композитных конструкциях ».
Паппада продолжает:«Наши технологии более гибкие. Кроме того, CCM был разработан 20 лет назад, но информации о нем нет, потому что несколько компаний, которые его использовали, не делились знаниями и ноу-хау. Итак, нам пришлось начать с нуля, просто обладая знаниями в области композитов и обработки ».
«Сейчас мы работаем в рамках внутренних программ и вместе с нашими клиентами над поиском деталей для этих новых технологий», - говорит Корвалья. «Эти детали могут быть переработаны и повторно аттестованы для запуска производства». Почему? «Наша цель - сделать самолет как можно более легким, но при этом конкурентоспособным по цене. Итак, мы также должны оптимизировать толщину. Но мы можем обнаружить, что деталь может стать еще легче или идентифицировать несколько деталей схожей формы, что может дать значительную экономию средств ».
До сих пор, повторяет он, эта технология была в руках немногих. «Но мы разработали альтернативные технологии, чтобы сделать эти процессы еще более автоматизированными, добавив более совершенное штампование. Мы кладем плоский ламинат и вынимаем деталь, готовую к работе. Мы находимся на этапе модернизации деталей и разработки плоских и фигурных МНЛЗ ».
«Теперь у нас в CETMA есть очень гибкая линия CCM, - говорит Паппада, - где мы можем применять различное давление по мере необходимости для получения сложных форм. Линия, которую мы будем развивать вместе с Леонардо, будет больше ориентирована на компоненты, соответствующие ее конкретным потребностям. Мы думаем, что у нас могут быть разные линии CCM для плоских панелей и L-образных стрингеров по сравнению с более сложными формами. Таким образом, мы можем снизить стоимость оборудования по сравнению с большими прессами, которые в настоящее время используются для производства деталей TPC сложной геометрии ».
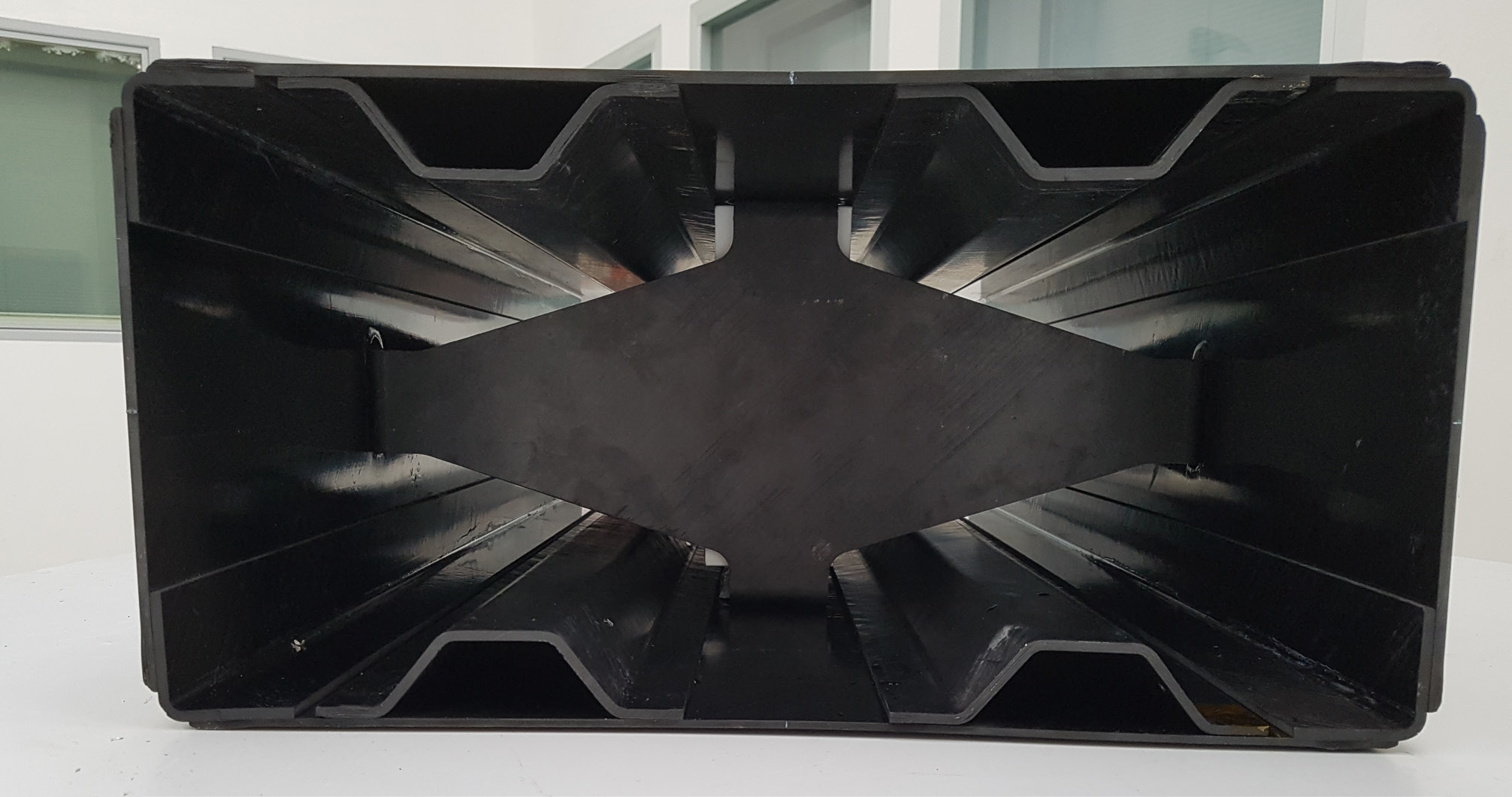
Индукционная сварка для закрепления на месте
«Индукционная сварка очень интересна для композитов, потому что можно очень хорошо настраивать и контролировать температуру, очень быстро нагревать и очень точно контролировать», - отмечает Паппада. «Вместе с Leonardo мы разработали индукционную сварку для соединения компонентов TPC. Но теперь мы думаем использовать индукционную сварку для консолидации на месте (ISC) лент TPC. Для этого мы разработали новую ленту из углеродного волокна, которую можно очень быстро нагреть с помощью индукционной сварки на специальном аппарате. В ленте используются те же матричные материалы, что и в коммерческих лентах, но с другой архитектурой, которая улучшает электромагнитный нагрев. Мы оптимизируем механические характеристики, но также думаем о процессе, пытаясь соответствовать различным потребностям, например, как рентабельно производить процесс с помощью автоматизации ».
Он указывает, что ISC очень трудно достичь с лентой TPC при хорошей производительности. «Чтобы использовать его в промышленном производстве, необходимо быстрее нагревать и охлаждать, а также контролировать давление. Поэтому мы решили использовать индукционную сварку, чтобы нагреть только небольшую область, где мы уплотняем материал, но оставим остальную часть ламината холодным ». По словам Паппады, индукционная сварка, используемая для сборки, имеет более высокий TRL. «
Использование индукционного нагрева для консолидации на месте кажется очень разрушительным - то, что никакие другие OEM-производители или поставщики не делают открыто на данный момент. «Да, возможно, это прорывная технология», - говорит Корвалья. «Мы запатентовали машину и материалы. Мы стремимся к чему-то, что может быть сопоставимо с термореактивными композитами. Многие пробовали AFP (автоматическое размещение оптоволокна) с TPC, но им пришлось сделать дополнительный шаг для консолидации. Это большое ограничение с точки зрения геометрии, стоимости, времени цикла и размера деталей. Мы действительно можем изменить способ производства деталей для авиации ».
SQRTM
Помимо термопластов Леонардо продолжает изучать технологии RTM. «Это еще одна область, в которой мы работали с CETMA и запатентовали новые разработки, основанные на более старой технологии, в данном случае SQRTM. Трансферное формование с аналогичным качеством (SQRTM) изначально было разработано компанией Radius Engineering (Солт-Лейк-Сити, Юта, США). «Очень важно иметь метод без использования автоклава (OOA), который позволяет нам использовать уже прошедший квалификацию материал», - говорит Корвалья. «Это также позволяет нам использовать препреги с хорошо известными свойствами и качеством. Мы разработали, продемонстрировали и запатентовали оконную раму самолета с использованием этой технологии ».
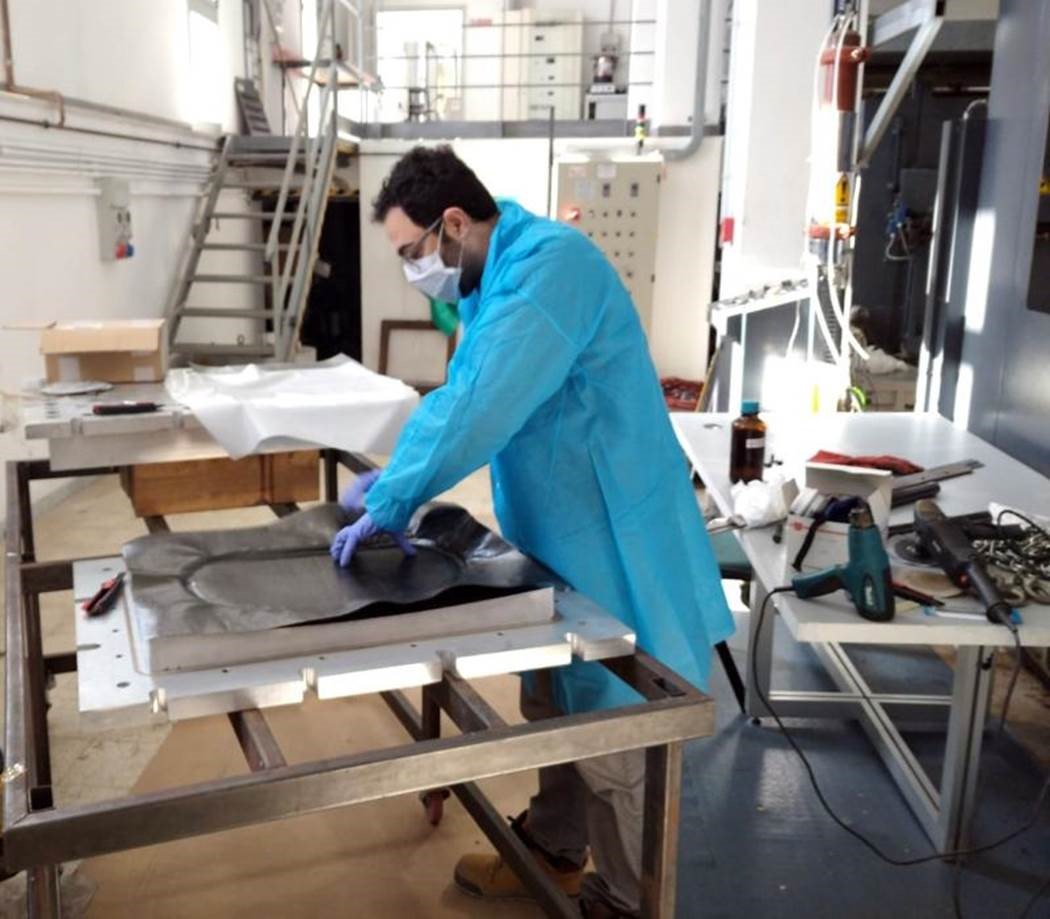
«Это тоже более старая технология, но если вы зайдете в Интернет, вы не сможете найти информацию об этой технике», - отмечает Паппада. «Важно то, что мы снова используем аналитические модели для прогнозирования и оптимизации параметров процесса. С помощью этой технологии мы можем получить хорошее распределение смолы - без сухих участков или скоплений смолы - и почти нулевое содержание пустот. Мы можем производить высокие структурные характеристики, потому что мы можем контролировать содержание волокон, и эту технологию можно использовать для производства сложных форм. Мы используем те же материалы, которые подходят для автоклавного отверждения, но вместо этого в методе OOA, но вы также можете использовать быстро отверждаемые смолы, чтобы сократить время цикла до минут ».
«Даже с использованием текущего препрега мы сократили время отверждения», - отмечает Корвалья. «Например, по сравнению с обычным циклом автоклава, длившимся 8-10 часов, мы можем достичь 3-4 часов с SQRTM для такой детали, как оконная рама. Тепло и давление прикладываются непосредственно к детали, и масса для нагрева меньше. Кроме того, нагрев жидкой смолы по сравнению с воздухом в автоклаве происходит быстрее, а качество деталей является превосходным, что является преимуществом, особенно для изделий сложной формы. Здесь нет переделок, почти нулевые пустоты и отличное качество поверхности, потому что это контролирует инструмент, а не вакуумный мешок ».
Дальновидное будущее, основанное на технологиях
Леонардо создает инновации в большом и разнообразном наборе технологий. В связи с быстрым развитием технологий, он рассматривает инвестиции в НИОКР с высоким риском (низкий TRL) как решающие для разработки новых технологий, необходимых для будущих продуктов, которые выходят за рамки постепенного (краткосрочного) развития, которое оно уже поддерживает в текущих продуктах. Такое сочетание краткосрочных и долгосрочных стратегий объединено в генеральном плане исследований и разработок Леонардо на 2030 год, представляющем собой единое видение устойчивой и конкурентоспособной компании.
В рамках этого плана он запускает Leonardo Labs, международную сеть корпоративных научно-исследовательских лабораторий, занимающихся передовыми исследованиями и технологическими инновациями. В 2020 году компания продолжит открытие первых шести лабораторий Леонардо в Милане, Турине, Генуе, Риме, Неаполе и Таранто и набирает 68 исследователей (научных сотрудников Леонардо) с навыками в следующих областях:36 должностей в области искусственного интеллекта и автономные интеллектуальные системы, 15 - в аналитике больших данных, 6 - в высокопроизводительных вычислениях, 4 - в электрификации авиационных платформ, 5 - в материалах и конструкциях и 2 - в квантовых технологиях. Leonardo Labs будет играть роль форпостов инноваций и генераторов будущих технологий Леонардо.
Примечательно, что технологии, которые Леонардо коммерциализирует в самолетах, могут также найти применение в его наземных и морских подразделениях. Следите за новостями о Леонардо и его потенциальном влиянии на композиты.
Смола
- Сверхлегкие композиты TPE для обуви
- Вспененный полипропилен для повышения устойчивости и затрат
- Графен и полимерные композиты для суперконденсаторов:обзор
- Настройка ультразвуковых датчиков для оптимизации и контроля процесса композитов
- OTOMcomposite разрабатывает программное обеспечение для производства Composites 4.0 с использованием лазерной укладки и…
- Перерабатываемые, ремонтируемые и перерабатываемые эпоксидные смолы для композитов
- Композиты Solvay, выбранные для гоночного катамарана
- Консорциум термопластичных композитов нацелен на крупносерийное производство для автомобильной и аэрокосм…
- Воздействие производства полупроводников и электроники на окружающую среду
- Носимый датчик газа для мониторинга здоровья и окружающей среды