3D-печать пресс-форм из углепластика для RTM флаперонов, экзоскелетов и многого другого
Фото предоставлено Мюнхенским кафедрой углеродных композитов (LCC) и QPoint Composite.
Кафедра углеродных композитов (Lehrstuhl für Carbon Composites или LCC) была основана в 2009 году на факультете машиностроения Мюнхенского технического университета (TUM, Мюнхен, Германия) при финансовой поддержке SGL Carbon (Висбаден, Германия). Его миссия заключается в проведении исследований и разработок в области материалов, процессов и приложений из армированного углеродным волокном полимера (CFRP), включая проекты по моделированию и испытаниям. «Кафедра» в немецкой университетской системе - это наименьшая единица, состоящая из профессора и его команды. Команду LCC возглавляет профессор д-р Инг. Клаусом Дрекслером и в настоящее время работает 30 штатных исследователей. Хотя финансирование SGL подошло к концу в 2016 году, LCC продолжила свое лидерство в области исследований и разработок композитов, включая создание пресс-формы для нижней половины многофункционального демонстратора фюзеляжа (MFFD), см. Боковую панель ниже, а теперь также включает в себя 3D-печать / добавку. производство.
Этот блог начался, когда CEAD (Делфт, Нидерланды) сообщил мне, что LCC купила одну из своих систем гибких роботов AM на основе экструдера для 3D-печати с использованием манипулятора. Мое последующее интервью с исследователем LCC Патриком Консулом, однако, выявило кладезь проектов, включая COMBO3D в рамках Clean Sky 2, по 3D-печати термопластической композитной формы RTM для производства термореактивного композитного флаперона самолета и EMOTION для производства инструмента. для формования нижней части термопластичного композитного многофункционального демонстратора фюзеляжа (MFFD) Clean Sky 2, а также в качестве вспомогательного частичного инструмента для демонстрации того, как тот же фюзеляж может быть изготовлен путем прямой консолидации на месте (вне автоклава). Мне показалось интересным обсуждение того, как TUM достигла этой точки и куда она направляется.
Форма нижней половины MMFD
См. Мой блог в феврале 2020 года:«Сварка LM PAEK для многофункционального демонстратора фюзеляжа». Эта врезка взята из доклада Баса Вельдмана, руководителя программы MFFD в GKN Fokker (Хоогевен, Нидерланды) за февраль 2020 года, «Разработка многофункционального демонстратора фюзеляжа».
Оболочка нижней половины MFFD состоит из термопластической обшивки, усиленной сварными стрингерами, зажимами и шпангоутами. Продемонстрированный производственный процесс состоит из трех основных этапов:
- Лента препрега для большой кожи демонстранта укладывается на плоский наклонный стол с помощью существующей лазерной машины AFP NLR.
- Слои с присосками роботизированно транспортируются в пресс-форму для внутреннего уплотнения и укладываются в нее без нагрева.
- После вакуумной упаковки кожица уплотняется в автоклаве.
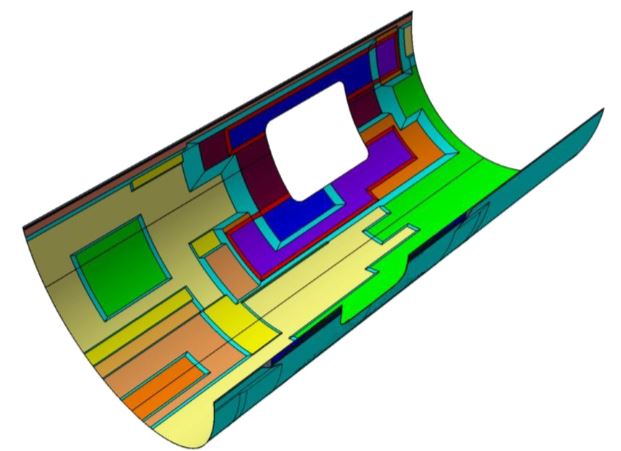
Использование охватывающей пресс-формы для уплотнения обеспечивает гораздо более простую (плоскую) поверхность, чем охватываемый инструмент, при этом напрямую регулируются аэродинамические ограничения на качество внешней поверхности оболочки.
Проект MFFD также требует работы вне автоклава . процессы, подлежащие исследованию - начиная с демонстрации большого многофункционального фюзеляжа - в последующем демонстраторе меньшего размера. В частности, in-situ термопластический композит производство, при котором уплотнение достигается во время укладки, будет рассмотрено, поскольку оно может полностью исключить этап автоклавирования и, следовательно, свести производство к одноэтапной процедуре.
Усовершенствованная пресс-форма для термопластичного фюзеляжа в автоклаве и вне его. Консолидация или EMOTION (https://cordis.europa.eu/project/id/864474) - это проект Clean Sky 2 по производству нижней части корпуса MFFD. «Это звучит просто, - говорит Патрик Консул, координатор проекта, Технический университет Мюнхена, - но на самом деле это довольно сложно, так как его нужно нагреть до 400 ° C. Это намного выше температурного диапазона, в котором Invar36 не имеет значительного КТР [коэффициента теплового расширения] ». Инвар обычно используется для формования композитных материалов из-за его низкого расширения во время высокотемпературных циклов отверждения. Однако КТР инвара увеличивается с температурой. «Задача, - отмечает Консул, - будет заключаться в том, чтобы контролировать тепловое расширение во время нагрева и охлаждения формы размером 8 на 4 метра и обшивки фюзеляжа во время отверждения».
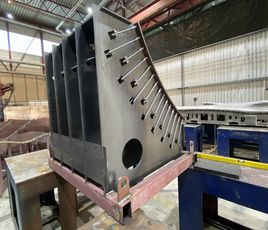
Прогресс в аддитивном производстве
«Нас 8-9 человек работают над аддитивным производством в LCC», - говорит Консул. Он начинает историю этой работы с покупки LCC машины для укладки термопластической композитной ленты с лазерной поддержкой у AFPT (Дёрт, Германия) в 2012 году. Позже она добавила машину Coriolis Composites (Квевен, Франция), чтобы обеспечить автоматическое размещение волокон (AFP). ) термореактивных препрегов. Первые настольные принтеры на основе филамента были приобретены в 2017 году. «Я также присоединился в 2017 году, чтобы помогать в разработке новых приложений и исследовательских проектов, включая написание предложений, например, для Clean Sky 2». Он объясняет, что проекты Clean Sky 2 награждаются на основе предложений, представленных руководителям тем в ответ на публично опубликованные объявления о приеме заявок (CFP). LCC удалось реализовать свои предложения по проектам CFP08 COMBO3D и CFP09 EMOTION. Оба обсуждаются ниже.
«У нас есть еще несколько проектов, некоторые из которых касаются 3D-печати с непрерывным армированием волокон», - говорит Консул. «Другие используют встроенную в лазер печатающую головку для предварительного нагрева композитной подложки для печати на уже консолидированных деталях из углепластика или для увеличения прочности на межслойный сдвиг (ILSS) между напечатанными слоями. Другой проект исследует инструментальные приложения, например, для тех случаев, когда у вас небольшое количество специализированных составных деталей ».
«Эти проекты постоянно поддерживаются численным моделированием с целью прогнозирования поведения деталей, изготовленных аддитивом, во время и после процесса печати», - продолжает он. «LCC также участвует в проекте с Имперским колледжем Лондона, который направлен на производство экзоскелетов с использованием 3D-печати углепластика. В другом проекте исследуются решетчатые структуры с целью оптимизации свойств 3D-печатных деталей в отношении жесткости, прочности или поглощения энергии ».
Развитие принтеров

«Мы начали с использования простого 3D-принтера на основе FDM (моделирование методом наплавленного осаждения) от Apium (Карлсруэ, Германия) для печати специализированных испытательных приспособлений, требующих высокой жесткости», - поясняет Консул. «Принтер был 3 метра в длину и 1 метр в ширину с большим расходом материала для сокращения времени печати. Хотя в нем нельзя было использовать непрерывное волокно, он был хорошо разработан для печати с использованием PEEK, PEKK и PEEK, армированного рубленым углеродным волокном. В нем использовался не только нагретый слой, но и подогреваемая пластина вокруг печатающей головки, которая помогала обеспечивать однородное распределение температуры на отпечатках, уменьшая термическое напряжение и обеспечивая кристаллизацию ».
«Некоторое время у нас также был принтер Markforged (Кембридж, Массачусетс, США), а затем мы получили Anisoprint [Эш-сюр-Альзетт, Люксембург]», - говорит Консул. Хотя принтер Markforged действительно позволял использовать FDM с непрерывным волокном, команда LCC решила не оставлять его. «Проблема, с которой мы столкнулись, заключалась в том, что система была очень закрытой», - объясняет Консул. «Программное обеспечение для слайсеров от Markforged было слишком сложно использовать для исследований, потому что оно сильно ограничивало наши возможности. Мы могли только напечатать слой непрерывного волокнистого материала, а затем слой армированного короткими волокнами термопластичного волокна сверху. Слайсер, генерирующий код, не принимает от нас G-код. Таким образом, не было возможности указать машине печатать так, как мы хотели, с непрерывным волокном в каждом слое и т. Д. »
Отвечая на вопрос об этом, Markforged объясняет, что его системы никогда не предназначались для использования в исследовательских целях, а вместо этого разрабатывались так, чтобы быть простыми и надежными для широкого использования при изготовлении деталей, с использованием волоконно-оптического пути на основе правил и требующих небольших усилий и времени для настройки слайсера. . Его Программное обеспечение Eiger действительно позволяет пользователям настраивать слои индивидуально, и Markforged приветствует отзывы и уделяет приоритетное внимание улучшению взаимодействия с пользователем для своих клиентов.
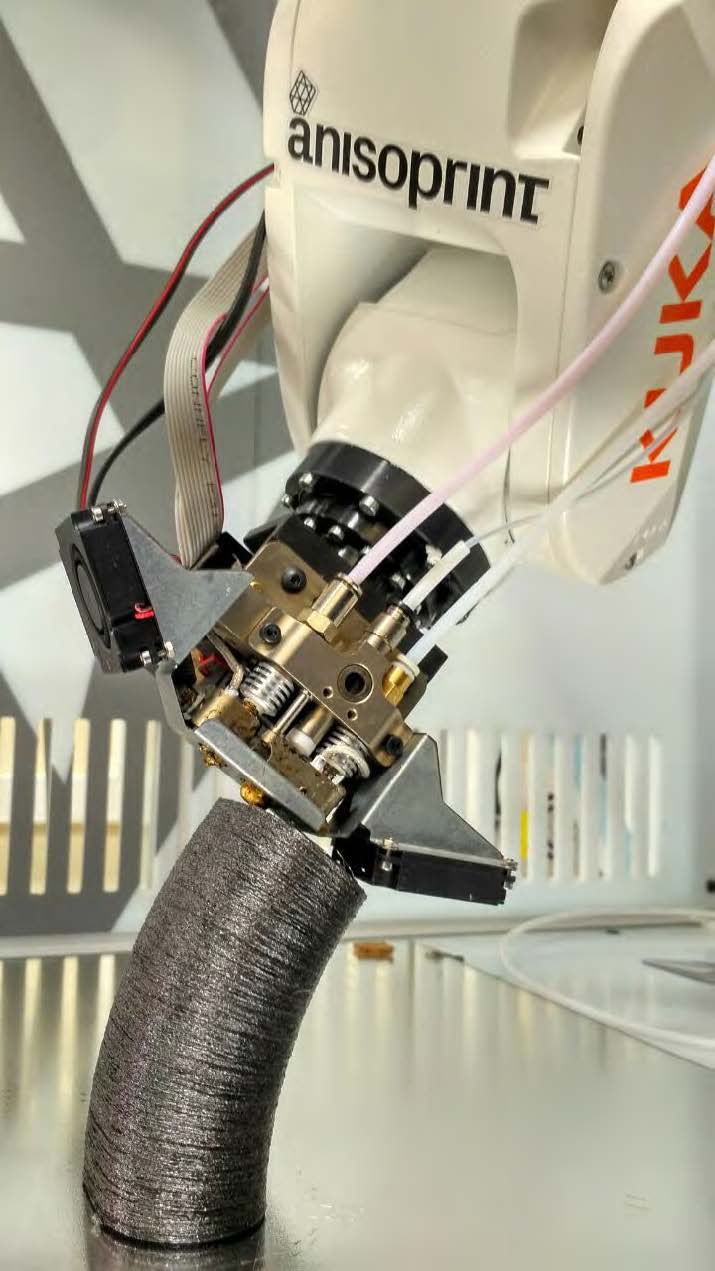
«Anisoprint, который использует полностью открытый слайсер G-кода, дал нам больше доступа к процессу», - говорит Консул. «Он также может печатать непрерывное углеродное волокно, причем не только в двухмерных слоях, но и вне плоскости, в трехмерных кривых. У нас есть печатающая головка Anisoprint для небольшого робота Kuka, способная производить детали размером 1 метр на 1 метр, что больше, чем у большинства настольных компьютеров, но мало для роботизированной системы ".
Но как насчет двойной матрицы Anisoprint термореактивные термопластические (ТС-ТП) материалы? Как объяснялось в моем блоге на Anisoprint в 2019 г., «… сначала он пропитывает арматуру из непрерывных волокон термореактивным веществом . полимер, а затем экструдирует его в расплавленную термопластичную нить во время печати ». Консул отвечает, что адгезия между нитью TS и TP очень хорошая. «В наших первых испытаниях мы могли получить больший объем волокна по сравнению с принтером Markforged, но это произошло потому, что мы могли изменить G-код. Печатающая головка Anisoprint проталкивает нить TS в TP, а затем укладывает ее. Мы планируем использовать этот принтер для деталей экзоскелета. Это простой способ интегрировать более прочные волокна ".
Принтеры для экструдированных гранул
Следующим шагом стал крупномасштабный принтер, сначала с коротким волокном TP, а затем с непрерывным волокном TP. «Сначала мы разработали экструдер, установленный на роботе, а затем наш интерес к машине CEAD быстро последовал. Мы надеемся интегрировать непрерывное волокно в обе эти системы в следующем году ».
Но зачем вам понадобилась машина CEAD, если у вас уже был экструдер на руке робота? «Первоначальный экструдер был бета-версией экструдера гранул Dyze Pulsar, который выдает максимум около 2 кг / час и примерно 1 кг / час с PAEK, но он борется с более чем 20% -ной загрузкой углеродного волокна», - говорит Консул. «Однако средняя производительность ниже, потому что робот часто ускоряется и замедляется во время печати. Для COMBO3D начальные мелкие половинки пресс-формы уже требовали не менее 36 килограммов, поэтому нам потребовалось около 48 часов, чтобы напечатать одну половину. Нам также нужно было, чтобы кто-то всегда был с ним, потому что ошибки, такие как блокировка линии подачи материала или деформация детали, могли произойти в любое время ».
Поскольку конечный демонстрационный образец COMBO3D примерно в 10 раз больше, чем исходные мелкие детали, печать его с использованием этой первой системы экструдера была невозможна, говорит Консул. «Кроме того, некоторые из материалов, которые поставлял нам Victrex, имели более высокую вязкость, и этот первый экструдер не мог обеспечить достаточный крутящий момент для экструзии этих полимеров. С принтером CEAD максимальная производительность составляет около 12,5 кг / час, а после нескольких часов испытаний мы получили стабильную среднюю производительность около 5-6 кг / час. Это позволило нам напечатать небольшую половину пресс-формы менее чем за 8 часов и позволяет нам использовать более высокое содержание волокон для уменьшения коробления, что в целом упрощает контроль процесса ».
«Таким образом, хотя Pulsar уже позволил нам использовать гранулы, добиться высокой производительности материала и воспользоваться преимуществами степеней свободы робота, - продолжает он, - принтер CEAD расширяет наши возможности в сторону более крупных деталей, с более высоким содержанием волокна и более широким спектром полимеров. . Pulsar устраняет разрыв между нашими филаментными принтерами и CEAD не только по производительности, но и по размеру сопла и получаемым деталям отпечатков ».
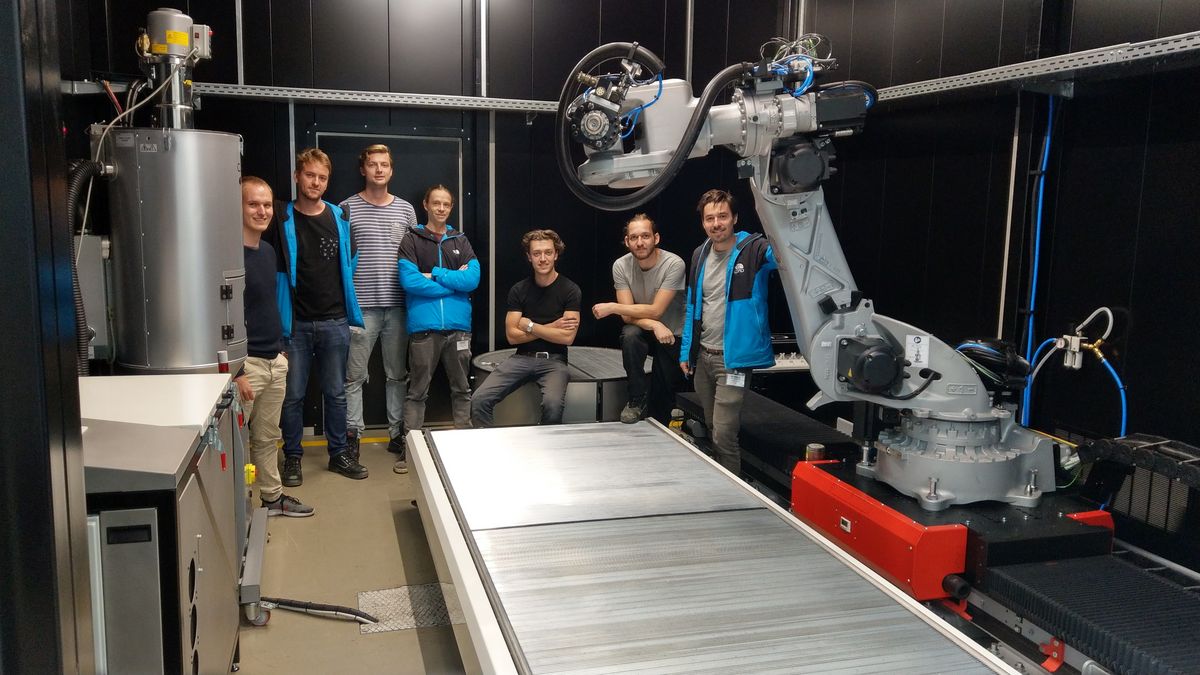
Технические данные CEAD AM Flexbot:
- Технические данные AM Flexbot:
- Экструзионные отпечатки на основе гранул со скоростью до 12,5 кг / час (неармированные и армированные короткими волокнами)
- Обработка материалов до 450 ° C
- Объем сборки 3000 x 1200 x 1700 миллиметров
- Установите пластину на вращающийся или плоский стол (с подогревом).
- Переделка с помощью фрезерной головки.
COMBO3D
Цель этого проекта Clean Sky 2 - напечатать на 3D-принтере пресс-форму для изготовления демонстрационного композитного флаперона (1,5 на 3 метра) для большого пассажирского самолета, входящего в рабочий пакет A-3.1:многопрофильное крыло для высоких и низких скоростей. Цель использования аддитивного производства - сократить время изготовления инструмента. Проект стартовал в январе 2019 года и завершится в марте 2021 года. В число партнеров входят Alpex Technologies (Милс бей Холл, Австрия), специалист по легким металлам Leichtmetallkompetenzzentrum Ranshofen (Раншофен, Австрия) и Victrex (Thornton Cleveleys, Великобритания), поставщик высокоэффективного термопласта. полиарилэфиркетон (ПАЭК).
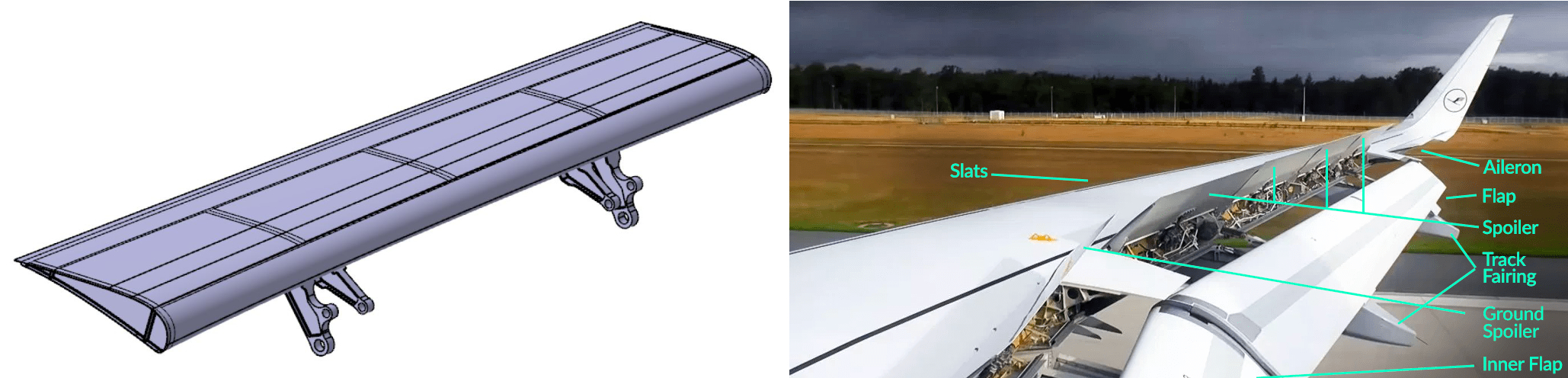
Другой ключевой частью проекта является демонстрация того, что этот флаперон из углеродного волокна / эпоксидной смолы можно изготавливать с помощью литьевого формования смолы (RTM) вместо препрега, отверждаемого в автоклаве. Деталь RTM отверждается при той же температуре 180 ° C, что и детали автоклава. Для обеспечения термостойкости инструмент будет напечатан из короткого армированного углеродным волокном PAEK, температура плавления которого составляет 305 ° C.
Чтобы сократить цикл отверждения, в 3D-печатную форму встроен активный контроль температуры. «Мы должны иметь возможность нагревать и охлаждать форму быстрее, чем автоклав», - отмечает Консул. «Мы будем использовать сетку из электрических нагревательных элементов на 3 миллиметра ниже поверхности формы, а также интегрировать печатные каналы для нагретого масла или воздуха на 6 миллиметрах ниже поверхности формы. Таким образом, мы можем очень быстро нагреть поверхность формы, а также использовать каналы для нагрева по всему объему инструмента. Мы стремимся к скорости нагрева и охлаждения на 50% быстрее, чем автоклав, и уверены, что сможем достичь скорости как минимум на 30% быстрее ».
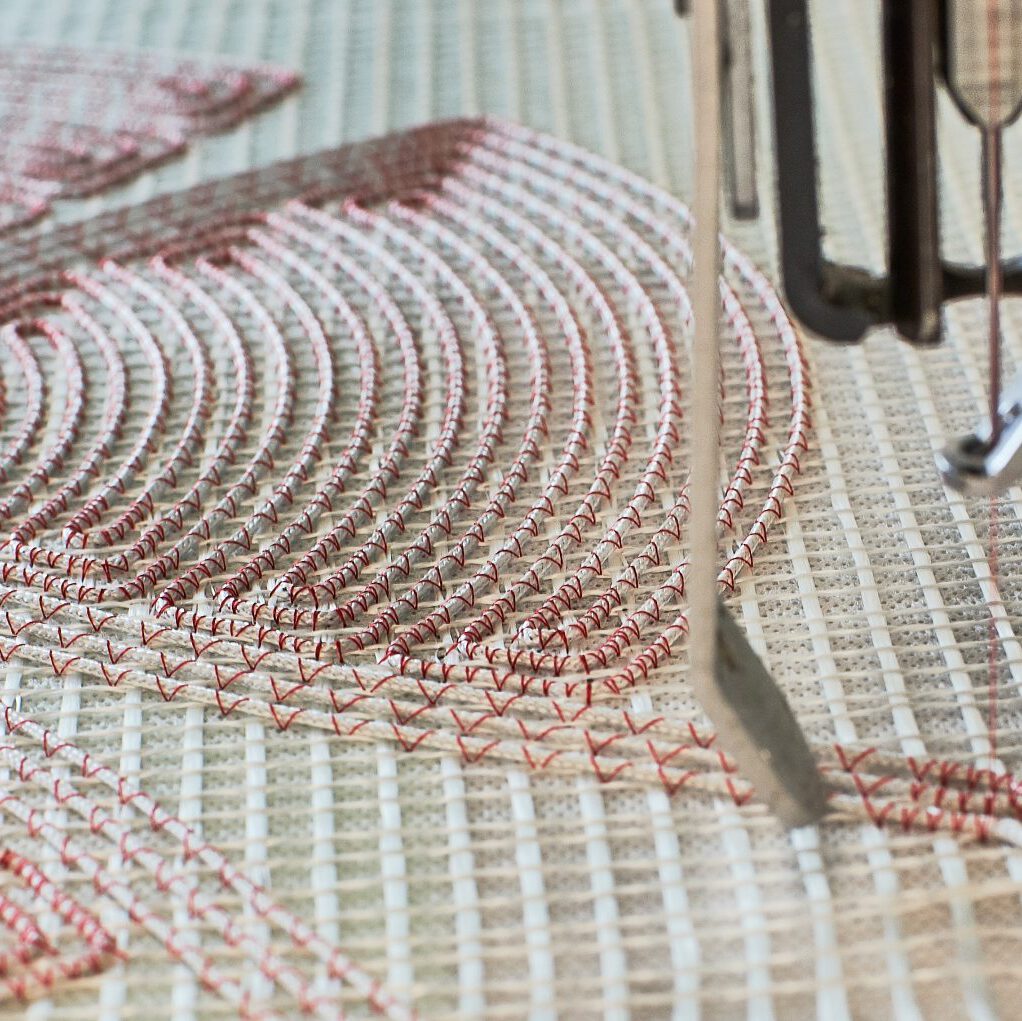
Какие нагревательные элементы будут интегрированы в 3D-печать? «Мы использовали специальное размещение волокон (TFP) углеродных ровингов на стекловолоконной ткани в качестве нагревательных элементов для реализации различных зон нагрева в пресс-форме из углепластика для лопасти винта вертолета», - поясняет Консул. «Это было для проекта Clean Sky 1, который мы завершили, работая с QPoint Composite (Дрезден, Германия). Мы будем работать с аналогичной концепцией на пресс-форме COMBO3D ».
Вся разработка печатного инструмента поддерживается моделированием. Конструкция инструмента будет оптимизирована за счет реализации системы нагрева и охлаждения в тепловом моделировании. Также будет смоделирован производственный процесс, поддерживающий процесс печати за счет получения информации о распределении температуры во время печати и соотнесения ее с планированием траектории.
Установка машины CEAD и ход проекта
«Система CEAD была доставлена очень быстро - от заказа до установки ушло всего 6 месяцев», - говорит Консул. «К этому времени мы завершили испытания материалов, спроектировали инструментальную пластину и начали печатать мелкие детали. Мы волновались, что на то, чтобы процесс работал с CEAD AM Flexbot, потребуется много времени, но в первых испытаниях он работал хорошо ».
Пластинчатая оснастка? «Это небольшая форма, в которой уже интегрированы охлаждающие каналы и нагревательные элементы для производства углепластиковых пластин для тестирования купонов», - объясняет он. «Это испытание было призвано гарантировать, что качество нашей 3D-печатной формы из углепластика RTM будет сопоставимо с качеством нынешнего углепластика, который Saab производит с их автоклавным процессом».
К сожалению, проект был прерван из-за COVID-19, «но сейчас все идет хорошо, и мы догоняем», - говорит Консул. А как насчет использования PAEK для 3D-печатной формы? «Единственная проблема в настоящее время заключается в том, что Tg [температура стеклования] для PAEK составляет 130–140 ° C, что ниже, чем при отверждении 180 ° C для демонстрационной части», - отмечает Консул. «Итак, нам все еще нужно посмотреть, сколько циклов мы можем завершить при температуре отверждения, прежде чем произойдет ползучесть или повреждена поверхность».
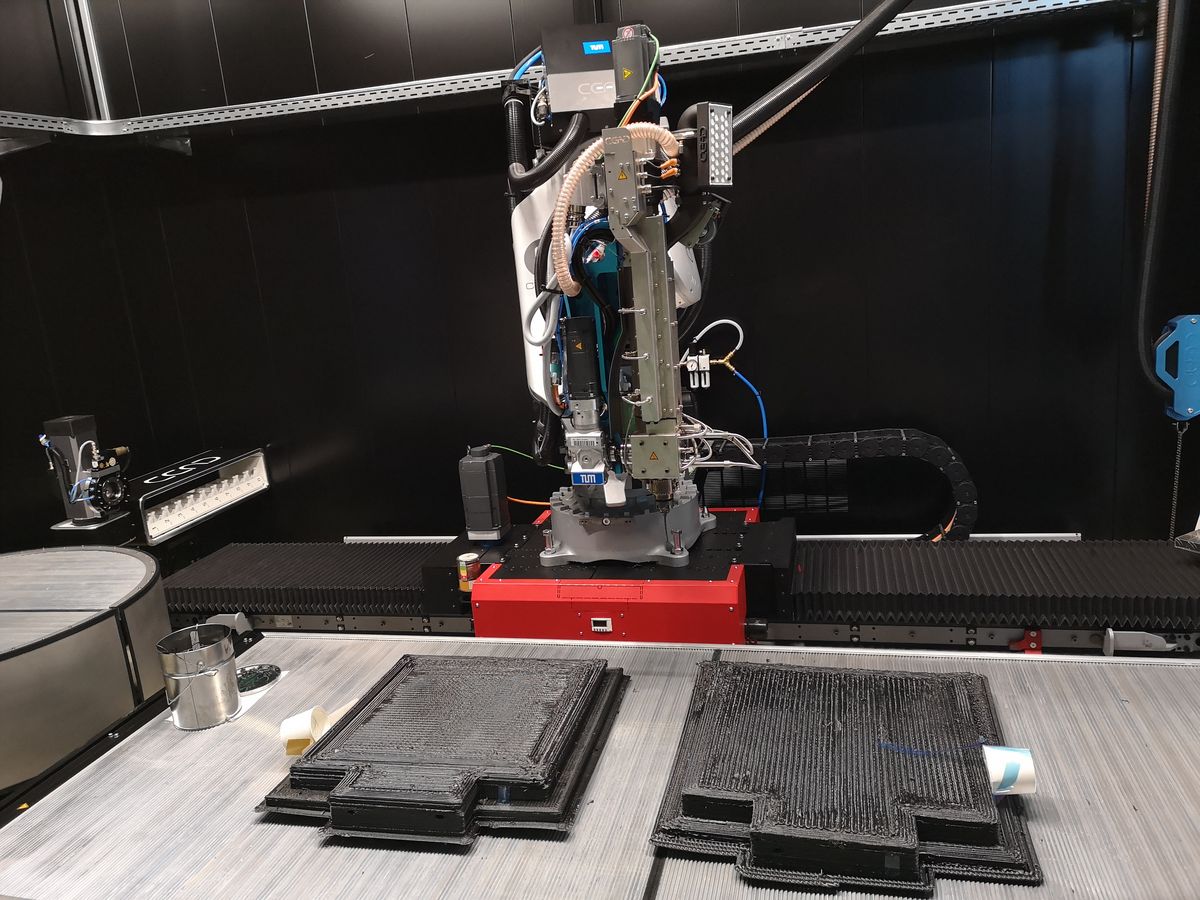
Машина CEAD в других проектах?
«Мы подаем заявку на проект в области аэрокосмической оснастки, который начнется в следующем году с GKN Aerospace Deutschland (Мюнхен) с использованием машины CEAD и полиэфирсульфона (PESU)», - говорит Консул. [Примечание:GKN в Германии производит композитные подкрылки для самолетов A330 и A350, а также элероны для семейства бизнес-джетов Bombardier Global.] «CEAD будет частью этой компании, ответственной за разработку машин для производства непрерывных углеродных волокон. Мы также планируем использовать машину CEAD внутри компании для изготовления прототипов пресс-форм для RTM, которые в противном случае были бы переданы на субподряд. Это дает нам преимущество в ускорении работы ».
Консул отмечает, что у PESU Tg выше, чем у PAEK. «Он также аморфный, а не полукристаллический, поэтому на нем должно быть легче печатать, хотя сопротивление ползучести может быть проблемой. Мы пытаемся избегать PEI (полиэфиримида). Раньше мы рассматривали вопрос приклеивания PEI к эпоксидной смоле. RTM6 [эпоксидная смола для RTM] растворяет PEI, что обеспечивает хорошую адгезию между ними. Это именно то, чего вы не хотите в 3D-печатных формах, которые должны отделять детали, а не прилипать к ним ».
Будущие промышленные (и летающие) композитные материалы для 3D-печати
Обсуждая некоторые другие проекты, которые LCC реализует в области аддитивного производства, я спрашиваю Консула, что удерживало углепластик в экзоскелетах? «Поскольку экзоскелеты должны быть адаптированы для каждого пользователя, их части специализированы, поэтому объем не велик», - отвечает он. «Наш проект нацелен на производство компонентов экзоскелета нижних конечностей для конкретного пациента, чтобы сделать экзоскелет для конкретного пациента менее чем за 24 часа. Эти экзоскелеты будут поддерживать реабилитацию пациентов, перенесших инсульт, на основе их биофизических профилей и уникальных потребностей в медицинской реабилитации ». (См. Статью CW «Экзоскелет C-FREX зависит от углепластика…»)
«Люди считают, что с помощью 3D-печати можно напечатать любую деталь, но сначала нужно иметь опыт работы с 3D-печатью и композитами. Например, часто возникают проблемы со сцеплением слоев и анизотропией, которые необходимо понимать. Композитные детали, напечатанные на 3D-принтере, не будут иметь такой же дизайн, как те, которые в настоящее время изготавливаются из пластика и металла ».
Он отмечает, что есть еще проблемы, которые необходимо преодолеть при использовании композитных материалов, напечатанных на 3D-принтере, для производства высокопроизводительных деталей самолетов, например:как вы проектируете эти детали для аддитивного производства? Как вы идентифицируете детали, в которых аддитивное производство увеличивает стоимость? «Инструменты для аэрокосмической промышленности - это основная область применения, которой сейчас занимается наша команда, - говорит Консул. «3D-печать формы хорошо подходит. Эти формы должны выдерживать все те же условия отверждения, что и детали, но меньше риска, связанного с формами по сравнению с летающими частями. Хорошим примером являются ребра жесткости для крыльев, где имеется большое количество различных частей, но не так много циклов на одну деталь. Итак, это хороший способ накопить опыт работы с этой технологией. Пробовать детали конструкции, которые полетят, пока рано. Мы будем стремиться к этому в долгосрочной перспективе, но инструменты печати позволят нам сделать процесс 3D-печати достаточно стабильным с высокими характеристиками, а также развить способность точно прогнозировать эти детали и процессы в моделировании ».
Смола
- Почему 3D-печать и программное обеспечение имеют решающее значение для цифровой трансформации
- Решения для 3D-печати для нефтегазовых компаний
- DSM и Nedcam для разработки новых приложений для 3D-печати большого размера
- Суперконцентраты красителей на основе ацеталей для автомобилей и др. на основе носителей с низким уровнем вы…
- Автоматизация для IML и форм для штабелирования
- Партнер Victrex и Bond для 3D-печати деталей из PAEK
- Советы по формам для 3D-печати
- Советы по обработке титана на станках с ЧПУ:аэрокосмическая отрасль и не только
- Formlabs поможет сделать 3D-печать более доступной для малого и среднего бизнеса
- SIGRABOND® Chemical CFRP для компонентов и сборок