Термопластичная композитная конструкция заменяет металлы на педалях тормоза, критичных для безопасности
В 1990-х годах автомобильная промышленность переоборудовала педали акселератора из металла в термопласты из короткого стекла, изготовленные методом литья под давлением. Однако педали тормоза, являющиеся критически важными для безопасности компонентами с высокими требованиями к жесткости, прочности и скручивающим нагрузкам, потребовали гораздо больше времени для преобразования. Поставщик автомобилей первого уровня Boge Rubber &Plastics Group (Дамме, Германия) заявляет, что он является первым поставщиком, который отвечает требованиям производителей оригинального оборудования и целевым показателям затрат на педали тормоза из термопластичных композитов. Уникальный дизайн, три различных материала и индивидуальный производственный процесс позволяют компании производить более прочные и жесткие педали, имеющие меньший вес и меньшую стоимость.
Поиск важной ниши
Boge - разработчик и производитель продуктов для гашения вибрации и монтажа трансмиссии / шасси, а также легких пластиковых модулей и педальных коробок (включая комбинации педалей тормоза, сцепления и акселератора) для автомобильной промышленности. С 2008 года она производит автомобильные компоненты из органолиста из непрерывного волокна с компаундом для формовки короткого стекла. В 2018 году она добавила в смесь однонаправленные (UD) термопластические ленты. Благодаря постоянным инновациям в процессах время цикла и затраты были сокращены, а бизнес увеличился.
«В 2015 году мой босс пришел ко мне и сказал:« Эти изменения, которые вы внесли, хороши, Дэниел, но было бы хорошо, если бы вы могли найти более крупный рынок с объемами производства, которые действительно имеют значение », - вспоминает доктор Инг. . Даниэль Хэффелин, старший менеджер / руководитель группы облегченных работ в Boge Global Innovation Center. Команда инженеров Boge приняла вызов и подумала, как повысить эффективность оптоволокна, чтобы сократить расходы и расширить бизнес.
«Органолист - отличный продукт, но его нужно использовать правильно, только там, где это необходимо», - поясняет Хеффелин. «Мы уже сделали наш производственный процесс очень экономичным, поэтому мы не выиграем, пытаясь еще больше сократить время цикла. Мы пришли к выводу, что лучший способ снизить затраты - это уменьшить количество используемых нами бесконечных волокон за счет более эффективного использования этого волокна ».
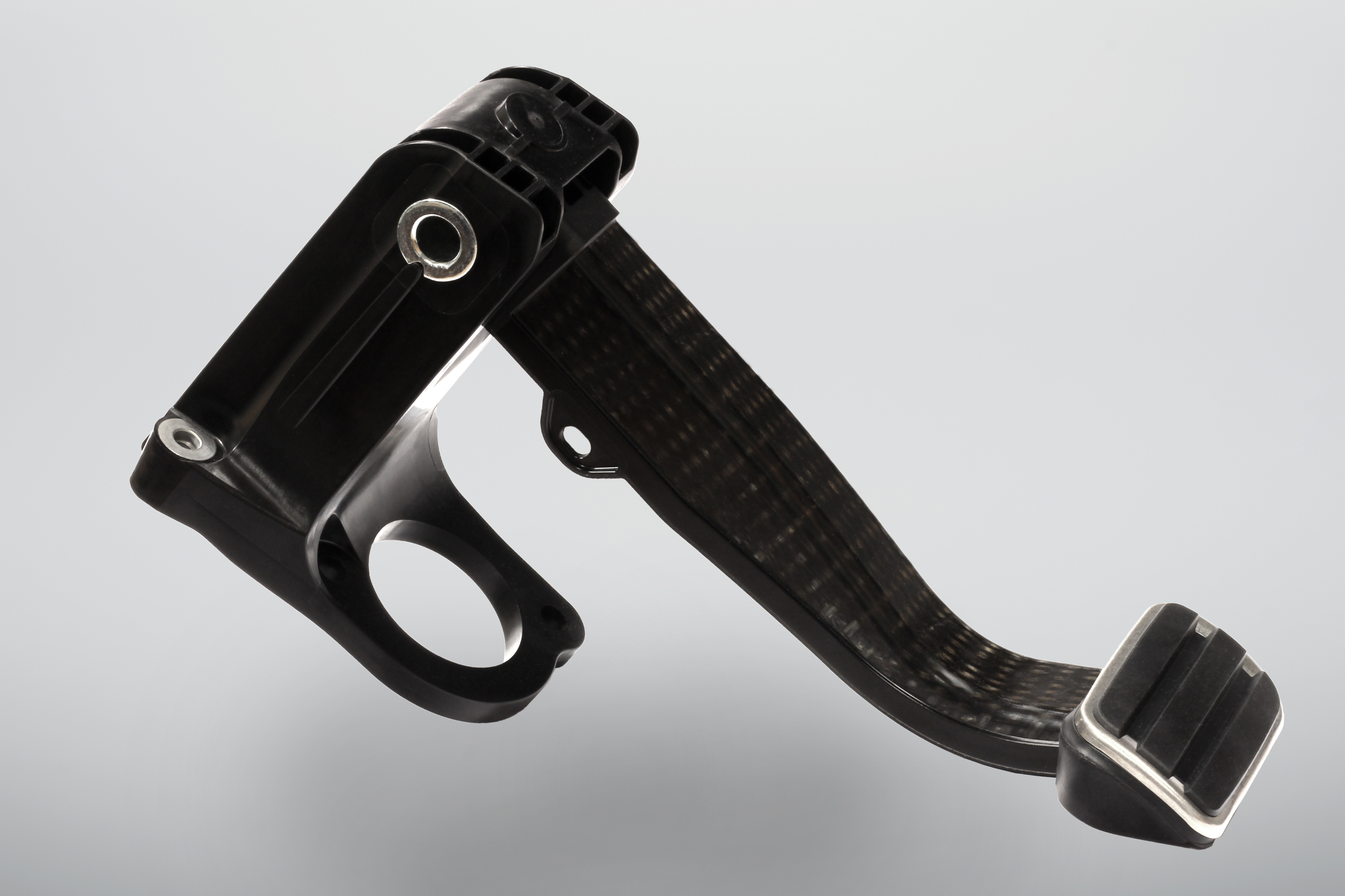
Просто сделать педали меньше или тоньше также не сработает, потому что существуют практические ограничения на размер и форму педали тормоза, не говоря уже о сложных технических характеристиках из-за того, что она критична для безопасности. Что имело наибольший смысл, так это поиск способов лучшего контроля ориентации волокон для оптимизации локальных свойств в тех областях детали, на которые приходятся самые высокие пиковые нагрузки, что дает возможность уменьшить толщину стенок в менее критических областях.
«Мы искали способ локально« направлять »волокна, чтобы мы могли размещать их именно там, где они нам были нужны для сохранения жесткости и прочности», - добавляет д-р Торстен Бремер, генеральный директор Boge Rubber &Plastics Group. «В принципе, мы знали, что это возможно, потому что мы уже рассматривали подъемные машины, используемые в спортивных товарах и медицине, но они были слишком дорогими. Тогда мы решили, что нам нужен новый процесс ».
«Мы уже работали с немецким производителем оригинального оборудования, чтобы найти способы изготавливать полностью композитные педали тормоза, которые отвечали бы их требованиям к характеристикам и стоимости», - вспоминает Буркхард Тиманн, исполнительный вице-президент Boge Plastics &Rubber Group, руководитель линейки продуктов - Пластмассы. «Мы сказали нашему клиенту:« Мы разработаем новый процесс с использованием лент UD и органолиста ». Они сказали нам:« Если вы сможете еще больше снизить массу и стоимость, мы это сделаем ». Это было нашей отправной точкой. В 2015 году мы пообещали поставить полностью композитную педаль тормоза, которая будет дешевле, легче и может производиться в больших количествах. На проработку деталей и поставку наших первых продуктов потребовалось три года ».
Волоконное рулевое управление
Композитные педали тормоза должны соответствовать тем же характеристикам, что и педали из традиционной стали или алюминия. Это включает в себя особые требования к режиму отказа с нагрузками до 3000 ньютонов и прогибом, подобным стали, при максимальной нагрузке. Учитывая эти требования и ограниченное доступное пространство для упаковки, основная конструкция корпуса педали, которая выдерживает максимальные нагрузки, требует непрерывного армирования волокном. Поэтому команда решила использовать органолист для формирования основы педали. Затем ленты UD будут использоваться для локального увеличения жесткости / прочности и усиления внутренних стенок во время пиковых напряжений в области детали, которая впоследствии будет изгибаться в U-образный канал во время предварительного формования. А в тех областях, где требовалась функциональная геометрия, такая как ребра, использовалась смесь для формования колотого стекла. Команда считает, что этот гибридный подход повысит эффективность волокна при одновременном сокращении расхода материала, средней толщины стенок и времени цикла.

Команда начала интенсивную работу по моделированию для оптимизации расположения волокон во время производства. Основой для работы Боге стала немецкая исследовательская программа SoWeMa (разработка программного обеспечения, инструментов и машин для полностью автоматической и закрытой легкой производственной цепочки) на 2011–2014 годы.
«Исследование SoWeMa охватило многие вопросы, которые мы зададим через год нашему собственному предприятию», - объясняет Хеффелин. «Поскольку проектирование является частью основного ноу-хау Boge, мы начали с основ программы SoWeMa и создали собственные возможности моделирования методом конечных элементов для анизотропных структур наложения».
Одной из основных задач была оптимизация комбинированной топологии для укладки лент и структуры ребер. «Мы создали цикл итераций, чтобы оптимизировать размещение лент и соответствующим образом адаптировать структуру ребер, поскольку оба связаны друг с другом из-за жесткости и прочности детали», - продолжает К. Зибе, инженер FEA, Центр инноваций CRRC. «Поскольку комбинация материалов из UD-лент, органолиста и коротковолокнистых материалов уникальна и их применение привязано к определенному диапазону влажности и температуры, мы создали наши собственные карты материалов, чтобы более точно охарактеризовать поведение этих материалов во время физических испытаний. ”
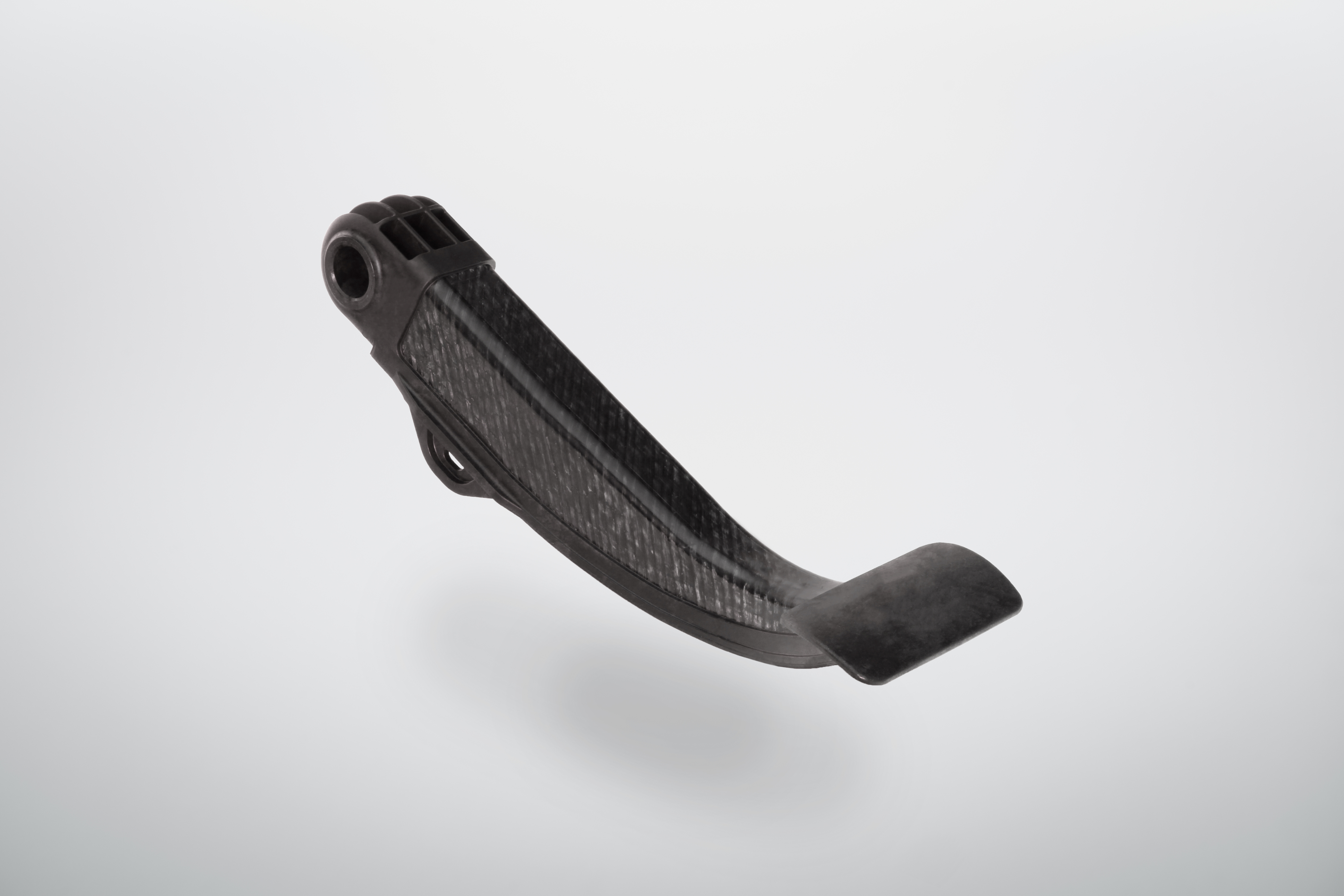
Боге определил структуру слоев и архитектуру волокон для каждого материала на основе результатов моделирования и заданной конструкции педали. Lanxess Deutschland GmbH (Кельн, Германия) поставляет органолист с объемными долями волокон (FVF) 45-50%. Ленты из термопласта UD с содержанием FVF 55-60% были поставлены Celanese Corp. (Ирвинг, Техас, США). Компаунды для инъекций короткого стекла для данного применения с содержанием волокна 40-60% (FWF) поставлялись из нескольких источников. Все материалы черные и имеют матрицу полиамид 6 или 6/6 (PA6, PA6 / 6). В соответствии с требованиями заказчика, PA6 является смолой по умолчанию для всех трех типов композитов. Однако, в зависимости от уровней влажности и температуры во время производства, а также от ограниченного пространства и геометрии педали, Boge также может использовать PA6 / 6 для формовочной смолы, поскольку эти два полимера достаточно похожи, чтобы обеспечить хорошее сцепление.
Трехэтапное производство
Параллельно с дизайном команда работала над трехступенчатым производственным процессом. На первом этапе создается заготовка из специально подобранного волокна с использованием предварительно нарезанного и предварительно уплотненного органолиста в качестве стабильной основы, на которую можно стратегически закрепить полосы UD-ленты, выровненные по траекториям нагрузки, чтобы укрепить структуру оболочки детали. На втором этапе заготовка перемещается и последовательно нагревается, уплотняется и формируется / драпируется. На третьем этапе на него заливают стеклопакет, чтобы создать ребристую структуру.
Для сокращения времени цикла в этой системе использовались роботизированные манипуляторы. Ключевой технологической особенностью, которую команда хотела включить, была гибкость, позволяющая размещать ленты любой длины, в любой ориентации и в любом положении на одной стороне оболочки органолиста и прикреплять эти ленты к оболочке лазером, чтобы они не сдвигались. на последующих этапах.
Другое решение, которое приняла команда, заключалось в том, чтобы предварительно уплотнять изготовленную по индивидуальному заказу заготовку не сразу после простоя, а непосредственно перед драпировкой / предварительным формованием и повторным формованием. Команда пришла к выводу, что материал в любом случае придется повторно нагревать во время драпировки / предварительной формовки, а для обеспечения рентабельности они должны поддерживать общее время цикла около 1 минуты. Следовательно, Boge нагревает и уплотняет заготовку непосредственно перед драпировкой / предварительным формованием, используя быстрое повышение температуры в сочетании с высоким давлением для создания прочной механической связи между лентой и органо-листом. Нагрев прекращается, и температура детали начинает падать по мере того, как еще горячая консолидированная заготовка перемещается в полость для обкладывания обкладыванием, прежде чем она снова перемещается и формуется с ребрами и другими функциональными элементами во второй полости. Между всеми тремя материалами достигаются прочные механические связи с подтвержденным проникновением полимерной цепи. Обработка после формования не требуется.
Чтобы удовлетворить требования к качеству этих критически важных для безопасности деталей, команда также разработала быструю, точную и совместимую с Индустрией 4.0 систему, в которой используются датчики обзора, силы, времени, давления и температуры, которые проверяют материал на каждом этапе производственного процесса. Затем система сохраняет эти данные и связывает их с уникальным идентификационным номером каждой педали. Это обеспечивает 100% отслеживаемость всех материалов, смен и настроек процесса.
Достижения на сегодняшний день
Индивидуальный, полностью автоматизированный и контролируемый по качеству процесс Boge сделал шаг от прототипа к крупносерийному производству в 2018 году. Производя новую педаль примерно каждую минуту, текущая производственная ячейка может производить до 1 миллиона деталей в год. В полностью композитных педалях используется на 33% меньше органолиста, чем в более ранних моделях, а номинальная толщина стенок снизилась с 3 до 2 миллиметров. Педали также на 50-55% легче, но соответствуют или превосходят требования к прочности для стали. Более легкие педали улучшают тактильные ощущения от вождения для потребителей и вся система на 100% подлежит вторичной переработке по окончании срока службы. В настоящее время композитные педали стоят столько же, сколько и алюминий, и немного дороже стали. Другие автомобильные и спортивные приложения находятся в разработке.
Что нас ждет в будущем по мере того, как автопроизводители переводят ресурсы на электрификацию автопарка? «По мере того, как электропривод [электромеханические приводные системы] и электрификация трансмиссии становятся все более распространенными, педали газа могут исчезнуть, но педали тормоза останутся», - размышляет Хеффелин. «Однако мы, вероятно, увидим большую интеграцию электроники, включая датчики, в педали тормоза. Это существенно увеличит сложность деталей, сделав композиты еще более конкурентоспособны, чем металлы ».
Использование материалов, этапы процесса и критерии оборудования более подробно описаны в CW В следующей статье за январь 2021 года:«По индивидуальному заказу композитная педаль тормоза производится каждую минуту».
Смола
- Нейлоновый композит, армированный длинным волокном, заменяет алюминиевый корпус двигателя
- Армированный непрерывным волокном термопластический композит, полностью сделанный из природных ресурсов
- Solvay увеличивает емкость термопластичного композитного материала
- Oribi Composites, партнер Packard Performance по внедорожным колесам из термопластичного композитного материала Powersports
- Консорциум нацелен на решения для термопластичных композитных конструкций из углеродного волокна
- INEOS Styrolution для создания производственной площадки для термопластичного композита StyLight
- Xenia представляет термопластичные композитные компаунды CF / PP
- Труба из термопластичного композитного материала на подъеме в глубоком море
- NIARs NCAMP, квалифицирующий термопластический композит TenCate
- TenCate празднует сборку консорциума термопластичных композитов в Бразилии