Fraunhofer IPT разрабатывает термопластичные композиты для хранения водорода, лопаток двигателей и т. д.
Разработка Fraunhofer IPT включает (по часовой стрелке сверху слева) лопасти вентилятора из термопластичного композита авиационного двигателя, гибридные композитно-металлические конструкции с использованием лазерного структурирования и AFP, мониторинг состояния конструкции (SHM) композитов и системы обработки термопластичных композитных лент, такие как системы PrePro 2D и PrePro3D. коммерциализирована Conbility. Фото:Fraunhofer IPT
В декабре 2020 года я опубликовал статью о том, как Институт производственных технологий им. Фраунгофера (IPT, Ахен, Германия) разрабатывает полностью автоматизированную укладку и формовку ленты для лопастей вентиляторов авиационных двигателей из термопластичного углеродного волокна, армированного полимером (CFRP). Оказывается, консолидация термопластической композитной ленты на месте (ISC) - это тема, которую Fraunhofer IPT хорошо знает, поскольку она использовала эту технологию с самого начала вместе с пионерами ISC Accudyne Systems Inc. (Ньюарк, Делавэр, США) и Automated Dynamics, теперь Trelleborg Sealing Solutions Albany (TSS Albany, Никсаюна, Нью-Йорк, США). [Подробнее об этих пионерах ISC см. «Консолидация термопластичных аэроструктур на месте, часть 1 и часть 2».] «IPT активно участвует в намотке ленты с помощью лазера (LATW) с 1988 года и остается одной из наших основных тем. », - поясняет д-р Хеннинг Янссен, главный инженер и руководитель отдела армированных волокном пластиков и технологии лазерных систем Fraunhofer IPT. Он отмечает, что технология LATW сильно изменилась, особенно за последние 10-15 лет. В этом блоге содержится более подробная информация о разработке LATW и термопластических композитов в целом, разработанной Fraunhofer IPT, а также о том, как институт видит развитие технологии в будущем.
Эволюция лазерной намотки ленты
«Когда мы начинали 30 лет назад, лазерная технология не была готова к высокоскоростной обработке термопластичных композитов», - говорит Янссен. «Вы можете себе представить, что, особенно на стороне управления, у вас была только аналоговая камера. Теперь у нас есть гораздо более совершенные технологии. Например, когда мы разработали компактную лазерную намоточную головку в 2008 году, в результате чего была основана компания AFPT Germany (Дёрт, Германия), нам пришлось использовать камеру размером 16 x 16 пикселей, которая обеспечивала частоту кадров всего восемь кадров в секунду. Теперь у нас легко разрешение 640 x 480 пикселей и обработка 50 или более кадров в секунду ». Он объясняет, что это важно, «потому что с разработанной нами лазерной намоткой ленты одним из основных преимуществ является то, что вы можете изучить процесс, а также изменить мощность обработки за миллисекунды. Это дает вам хорошее преимущество, например, при обходе сложной геометрии, такой как купол сосудов высокого давления, где скорость наматывания замедляется, и вам необходимо снизить мощность нагрева лазером. Затем вы должны перенастроить, когда обмотка восстановит скорость вдоль цилиндра резервуара. Это было невозможно 15 лет назад, потому что лазер, системы управления и тепловизионные технологии были не готовы или были слишком дорогими, а также не такими мощными, как те, что есть сегодня.
Янссен продолжает:«Итак, в области цифровых технологий многое изменилось. Теперь, например, мы поставляем что-то вроде цифрового двойника, в котором вы можете отобразить всю информацию вашего датчика на сосуде под давлением, чтобы вы могли сравнить произведенную деталь с цифровой конструкцией, чтобы оценить качество детали и спрогнозировать производительность. Использование виртуальных датчиков процесса и моделей также позволяет нам прогнозировать прочность ламината на основе истории его обработки ». Это важно, потому что LATW с использованием термопластичной ленты использует быстрый нагрев и охлаждение, когда свойства материала и детали определяются во время самого процесса наматывания из-за отсутствия этапа термической постобработки, отмечает он. Поэтому очень важно иметь возможность быстро управлять процессом.
По словам Янссена, также произошли изменения в материалах. «Двадцать лет назад было доступно ограниченное количество термопластичных композитных ленточных материалов, таких как APC-2 от Cytec, ныне Solvay (Альфаретта, Джорджия, США)», - объясняет он. «Но сейчас гораздо больше материалов подходят для промышленного применения, и у вас также есть много товарных материалов, таких как полипропилен (PP), армированный углеродным волокном, а также стекловолокном, а также, например, полиамид шесть (PA6), который довольно часто используется в автомобильной промышленности. Также теперь есть приложения для LATW, которые больше ориентированы на массовое производство. Например, в электродвигателях стремятся к удерживающим втулкам и другим деталям. Это простые кольца или трубки из термопластического композита, но в объемах от 10 000 до 50 000 в год ».
ambliFIBRE, трубы для нефти и газа
Часть цифрового управления в LATW, которую Янссен описывает выше, была разработана в проекте ambliFIBRE (2015-2018). «В этом проекте было много партнеров, - говорит он, - но одним из них была Baker Hughes (Ньюкасл, Англия и Хьюстон, Техас, США), и мы использовали наше оборудование LATW для производства их неметаллических труб». Обратите внимание, что вскоре после завершения работы ambliFIBRE в 2018 году Baker Hughes объявила о создании совместного предприятия с Saudi Aramco (Эр-Рияд, Саудовская Аравия) для расширения использования неметаллических труб, включая возможное использование пластика, армированного углеродным волокном (CFRP).
В настоящее время Baker Hughes стремится ускорить внедрение неметаллических материалов в энергетическом секторе, и есть другие компании, использующие лазерную технологию для изготовления труб, например Magma (Портсмут, Великобритания). (См. «Термопластическая труба на подъеме в глубоком море» и «Magma Global поставляет композитный стояк высокого давления…)
«Также довольно часто используется лазерная намотка ленты для стояков и выкидных трубопроводов из термопластического композита», - говорит Янссен. «Хотя это еще не является общепринятым в других отраслях». Он добавляет, что в последнее время большое внимание LATW уделяется резервуарам для хранения водорода, но эта технология уже имеет гораздо более широкое применение.
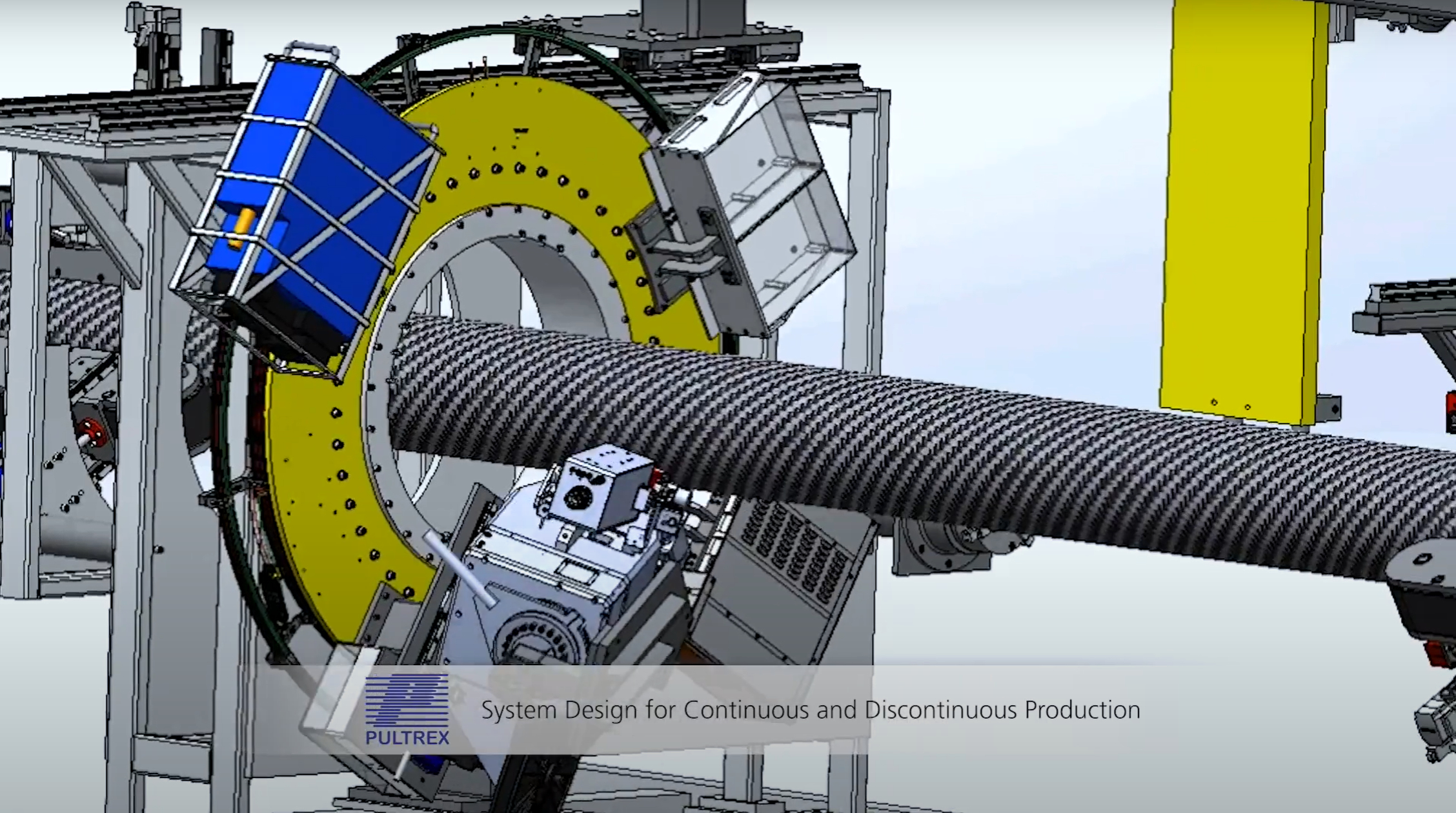
В рамках проекта ambliFIBRE компания Fraunhofer IPT разработала цифровые модели управления технологическим процессом для прерывистой (например, резервуары) и непрерывной намотки ленты, например, для производства труб длиной несколько километров. Фото:видео Фраунгофера IPT для проекта ambliFIBRE
«И то, что мы в Fraunhofer IPT предлагаем для этих приложений, является ключевым, - говорит Янссен. «Очевидно, что у нас в институте нет полномасштабной производственной линии для непрерывного производства труб, но мы предлагаем нашим клиентам испытания материалов и аттестацию продукции. Например, существует пирамида тестирования, основанная на DNV-GL F114, которая начинается с квалификации и тестирования полимера и волокон, а затем расширяется до микроструктуры или мезоструктуры композитного ламината. Поэтому мы проводим много испытаний на уровне купонов, а затем масштабируем их до меньших и типичных труб, например, потому что намотка дает вам другие свойства, чем прессование или автоматическая укладка ленты (ATL) ».
Кроме того, он отмечает:«Поскольку у вас разные нагрузки в вашем материале, многие из этих композитных материалов испытываются на трубах меньшего размера, например, от 2-3 дюймов до нескольких метров в длину. Итак, мы проводим это тестирование, а затем применяем наше понимание процесса для реальной длины детали, например, 2-3 километра. И это очень интересно, потому что время обработки при такой продолжительности может составлять пару дней, и вы должны учитывать усадку, а также другие факторы, такие как изменения температуры окружающего воздуха, которые могут иметь большое влияние ».
LATW в резервуарах для хранения водорода
Янссен говорит, что Fraunhofer IPT работает с нефтегазовыми компаниями с 2000 года. «А потом, восемь лет назад, мы выяснили, что это почти та же технология, которая нужна вам для водородных резервуаров», - вспоминает он. «И теперь у нас есть большая инициатива по производству водорода здесь, в IPT, а также по композитам из углеродного волокна в топливных элементах. Мы создаем завод стоимостью 80 миллионов евро для автоматизированного производства топливных элементов, а также инвестируем в новый, довольно большой завод по намотке, чтобы мы могли производить детали длиной до 7 метров и диаметром 2,5 метра, которые мы также будем использовать. для больших сосудов под давлением ».
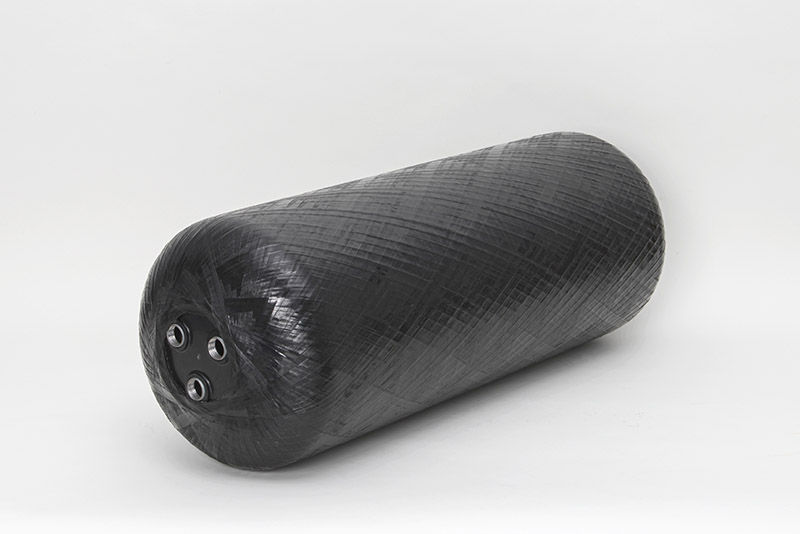
По словам Янссена, LATW с использованием термопластичных композитных лент еще не является современным продуктом для производства сосудов под давлением, «потому что химический состав термопластов, а также их обработка и долговечность все еще исследуются. Но мы твердо убеждены в важности низкой проницаемости, прочности и пригодности для вторичной переработки термопластов ». Он также видит потенциал для термопластов в сосудах высокого давления Типа V, которые являются полностью композитными, но не используют отдельную термопластичную футеровку. «Они могут стать будущим решением для некоторых мобильных систем хранения водорода, таких как электрические грузовики на топливных элементах».
«Мы также видим, что обычный термореактивный Намотка нити ограничена минимальным углом намотки », - говорит Янссен. «Например, вам нужно обойти купола спиральными слоями с углом волокна не менее 10 °. Таким образом, вы не можете поместить арматуру под углом 0 ° в обычный резервуар для намотки нити ». Однако он утверждает, что «в классическом LATW поступающий термопластический препрег непосредственно приваривается к подложке, поэтому вы можете двигаться в любом направлении, в каком захотите, что дает вам гораздо больше свободы дизайна. В настоящее время мы реализуем проекты с партнерами из автомобильной промышленности по разработке резервуаров высокого давления из термопласта для хранения водорода, которые являются безопасными, энергоэффективными и легко перерабатываются ».
Лопасти вентилятора из термопластичного композита
«Фраунгофер IPT имеет большой опыт работы в турбомашиностроении», - говорит Янссен. «Здесь, в Аахене, Международный центр производства турбомашин или ICTM, предконкурентное сообщество, в котором мы работаем с производителями двигателей и их поставщиками совместно в предконкурентных проектах НИОКР, направленных на развитие и совершенствование производственных технологий ».
Он отмечает, что в последние 20 лет основное внимание уделялось механической обработке титановых или никелевых сплавов для передовых изделий секции сжатия и турбин, таких как интегрированный диск с лопастями (блиск). Находясь в холодной секции, детали из композитных материалов, такие как лопасти вентиляторов из углеродного волокна, были разработаны GE в 1990-х годах и сейчас используются в GE90 и GEnx. «Однако сейчас композиты с керамической матрицей (КМК) рассматриваются как материалы следующего поколения для горячей части реактивных двигателей, - говорит Янссен, - позволяя более высокие температуры при меньшем весе для большей эффективности».
«Производство деталей из композитных материалов по сравнению с металлическими сильно отличается», - продолжает он. «В металле вы начинаете с большого количества материала и получаете деталь путем субтрактивной обработки, в основном механической обработки, так что конструкция не так зависит от производства. В композитах все наоборот, они всегда требуют какого-то порождающего процесса. Итак, мы решили, что рассмотрим новые стратегии лопастей вентиляторов с точки зрения производства ».
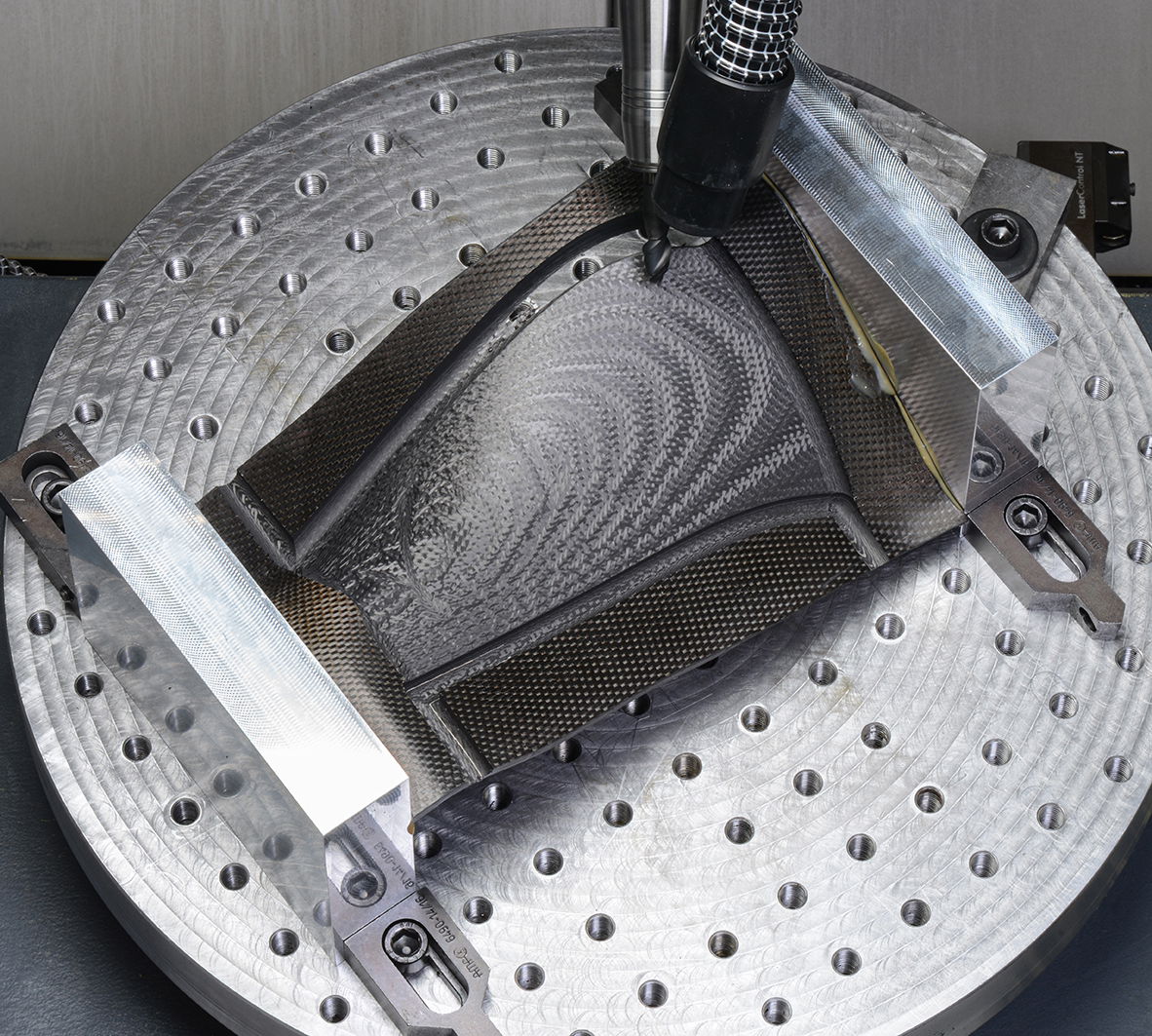
Он также отмечает совместное предприятие Clean Sky 2, в котором Фраунгофер возглавляет деятельность по экодизайну. Fraunhofer IPT уделяет особое внимание экологическому проектированию двигателей, которое включает оценку жизненного цикла и оценку воздействия на окружающую среду. «Вот почему мы начали рассматривать термопластичные композиты», - объясняет он. «Пока что мы находимся на очень низком уровне TRL [уровень технологической готовности]. На данный момент разработка связана с производством и опробованием различных технологических маршрутов, таких как укладка почти чистой формы и немного термоформования, что больше похоже на этап калибровки, а затем чистовая обработка с точки зрения механической обработки. Так что впереди еще довольно много работы ».
Тем временем Fraunhofer IPT расширяет свой опыт обработки металлических компонентов авиационных двигателей до композитов, используя свою цифровую технологию для контроля и оценки параметров обработки на каждой лопасти. Но разве цель композитов не в том, чтобы перейти от такого субтрактивного производства к более аддитивному производству с меньшими отходами? «Да, но для некоторых технологических процессов требуется обработка с соблюдением допусков на размеры», - говорит Янссен. «То, над чем мы сейчас работаем, очень близко к чистой форме».
Он отмечает, что разрабатываемая в настоящее время конструкция представляет собой термопластический ламинат толщиной 0,75 дюйма в основании и всего 2 миллиметра на конце. «Кроме того, существуют различные стратегии проектирования, которые мы обсуждаем вместе с инженерами-проектировщиками. Кроме того, есть ли у вас автоклав или ступень пресса для таких очень нагруженных деталей? Это также будет иметь значение для внутренних напряжений, потому что мы знаем, что это лезвие немного скручивается во время вращения. И, конечно же, ключевым вопросом является столкновение с птицами ». Для последнего Janssen рассматривает повышенную вязкость термопластов как фактор, способствующий развитию, указывая на то, что композиты PPS (полифениленсульфид) используются в передних кромках крыльев именно по этой причине.
Будущие применения термопластичных композитов
Я спросил о возможности использования термопластичных композитов в гондолах двигателей , что, возможно, могло бы помочь решить четыре недавних инцидента, связанных с отключением отвала, когда, как сообщалось в ходе Aviation Week в марте 2021 г. статья:
«… повреждение, вызванное попаданием осколков лопасти в секции обшивки двигателя или гондолы, вызвало серию событий, в результате которых были сломаны большие части конструкции, в том числе части воздухозаборников двигателя и кожухи вентилятора. прочь." Во всех четырех авариях был поврежден фюзеляж самолета, а во время полета Southwest Flight 1380 в апреле 2018 года одно из окон было выбито, что привело к гибели пассажиров.
«Промышленность проявляет некоторый интерес к использованию термопластичных композитов в моторных отсеках, - говорит Янссен, - однако это долгосрочная разработка». Одним из вопросов для такого развития является сертификация авиационными властями, еще одна область, в которой работает Fraunhofer IPT. «Сейчас мы обсуждаем с органами по сертификации, как помочь сократить усилия по сертификации, доказав в цифровой форме, что новые производственные процессы соответствуют текущим и развивающимся стандартам. Итак, это новый образ мышления. В производстве 21 века доступно так много данных, что речь идет не только о сертификации одного процесса или одной конструкции путем тестирования, а затем это замораживается ». Другими словами, сегодняшний акцент на Индустрии 4.0 и Композитах 4.0 заключается в том, что датчики и программное обеспечение с поддержкой ИИ будут непрерывно собирать данные и разрабатывать интеллектуальные средства, которые затем будут непрерывно оптимизировать производство и, в свою очередь, отправлять эти сведения обратно в цифровом потоке для улучшения дизайна. Это действительно сильно отличается от сегодняшнего производства.
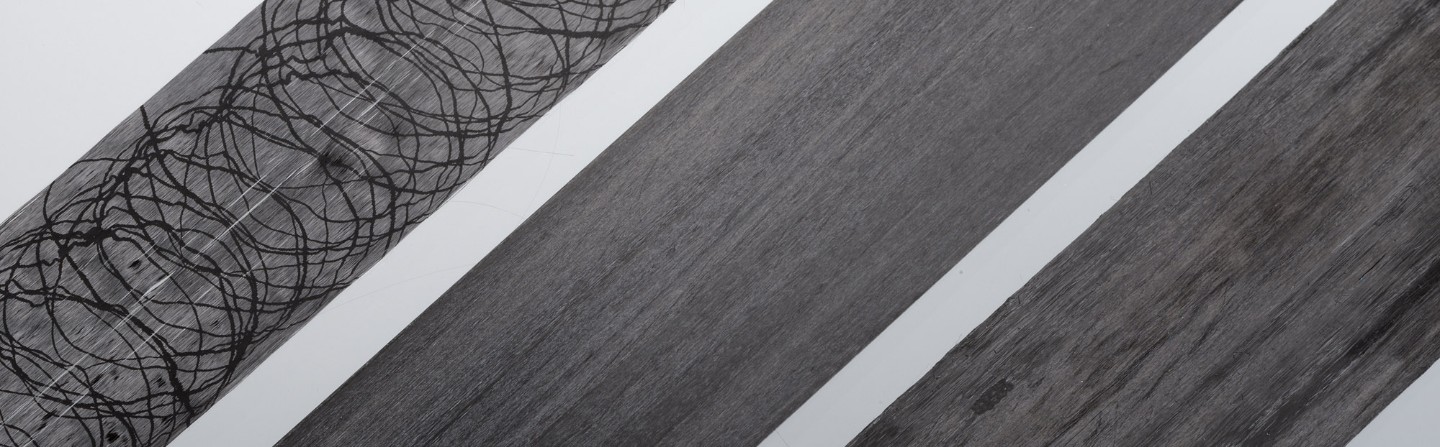
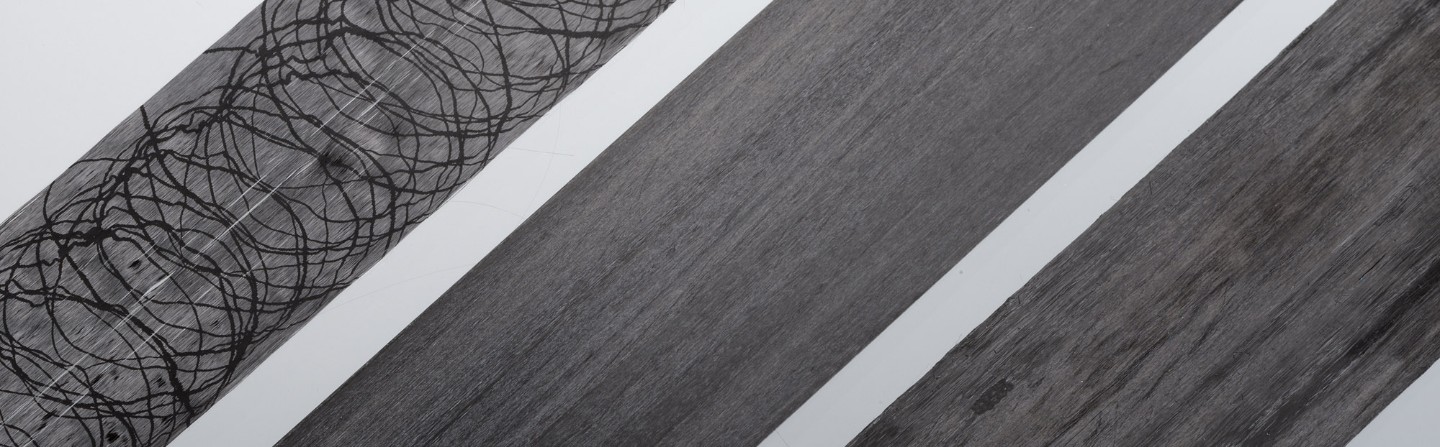
По словам Янссена, работа Fraunhofer IPT в отношении сертификации «может помочь в реализации новых технологий, таких как термопластичные композиты для деталей двигателя, - то есть, если будут учтены все аспекты, включая технологию, дизайн и управление рисками». Он утверждает, что термопластические композиты обладают огромным потенциалом для решения ключевых проблем в разнообразии промышленных секторов и отмечает, что Fraunhofer IPT работает над преодолением сложности обработки термопластичных композитов - например, используя новые доступные цифровые методы производства. «Кроме того, потенциал термопластичных композитов может быть полностью использован только после того, как будет рассмотрен полный жизненный цикл, включая повторное использование и переработку», - говорит Янссен. «Таким образом, Fraunhofer IPT также работает над механической переработкой термопластичных композитов. Мы видим, что можно будет получить ценный переработанный материал, учитывая как данные, полученные во время производства, так и данные, полученные в течение всего жизненного цикла композитных компонентов ».
Смола
- Covestro увеличивает инвестиции в термопластические композиты
- Лучший лазерный гравер 2021 года для лезвий и рукояток ножей
- Проект RECONTRAS проверяет использование микроволн и лазерной сварки для получения перерабатываемых композитов
- OTOMcomposite разрабатывает программное обеспечение для производства Composites 4.0 с использованием лазерной укладки и…
- Устранение проблем термоформования термопластичных композитов
- Термопластические композиты:структурный кронштейн бампера
- TPAC и TPRC разрабатывают процесс переработки термопластичных композитов
- Сварка термопластичных композитов
- Консорциум термопластичных композитов нацелен на крупносерийное производство для автомобильной и аэрокосм…
- Компания RTP разрабатывает легкие и прочные термопластические компаунды