Влияние условий образования наноматериала Pd / SnO2 на свойства датчиков водорода
Аннотация
Сенсоры на основе оксидов металлов созданы с использованием наноразмерного диоксида олова, полученного золь-гель методом. Газочувствительные слои сенсоров пропитаны PdCl 2 растворы различной концентрации для повышения чувствительности предлагаемых сенсоров. Исследовано влияние различных температурных режимов формирования сенсора на его свойства. Установлено, что уменьшение продолжительности высокотемпературной обработки сенсора предотвращает укрупнение частиц газочувствительных материалов. Было показано, что сенсоры на основе материалов с меньшим размером частиц показали более высокий отклик сенсора на 40 ppm H 2 . . Полученные результаты объяснены существенным влиянием длины общих границ между материальными частицами диоксида олова и палладия на газочувствительные свойства сенсоров. Полученные сенсоры обладали быстрым откликом и временем восстановления, а также продемонстрировали стабильные характеристики при длительной эксплуатации.
Фон
В настоящее время водород широко используется для химического синтеза в промышленности и как экологически чистый источник энергии [1,2,3]. Водород - взрывоопасный газ, поэтому контроль H 2 содержание в местах его использования, транспортировки и хранения. Для реализации такого контроля могут быть перспективны газоаналитические приборы на основе металлооксидных сенсоров [4,5,6].
Хорошо известно, что наноразмерные материалы обладают некоторыми уникальными физико-химическими свойствами:оптоэлектронными [7], магнитными [8] и каталитическими [9]. SnO 2 является перспективным материалом для создания металлооксидных сенсоров благодаря своей химической инертности, термической стабильности и способности хемосорбировать кислород. Вот почему наноматериалы на основе диоксида олова очень интересны для изучения в качестве газочувствительных слоев сенсоров для измерения H 2 в воздухе. Повышение чувствительности сенсора к водороду может быть достигнуто за счет добавления в газочувствительный слой сенсоров каталитически активных добавок, включая Pd, который является одним из наиболее активных катализаторов в реакции окисления водорода [6, 10].
Состав сенсорного материала, метод его приготовления и условия образования материала могут влиять на размер частиц [11,12,13] и, следовательно, на газочувствительные свойства материала.
Морфология материала сенсорно-чувствительного слоя, включая размер частиц и их распределение, имеет большое значение для создания высокоэффективных металлооксидных сенсоров [14,15,16]. Известно, что уменьшение размера частиц материала чувствительного слоя сенсора должно увеличивать отклик сенсора [17]. В то же время известно, что для создания датчиков необходимо их высокотемпературное спекание. Однако высокотемпературное спекание приводит к увеличению размера частиц наноматериала. Поэтому условия процесса высокотемпературного спекания сенсора должны предотвращать укрупнение частиц и обеспечивать одновременно как механическую прочность сенсоров, так и их проводимость за счет образования контактов между наночастицами материала газочувствительного материала. слой [18].
Оптимальная температура спекания сенсора, которая должна удовлетворять перечисленным выше условиям, может быть достигнута необходимыми значениями температуры и продолжительностью определенных этапов высокотемпературного спекания сенсоров. Условия формирования сенсорного наноматериала также должны обеспечивать полное завершение кристаллизации и стабилизацию его наночастиц.
Целью данной работы является изучение влияния условий образования Pd / SnO 2 наноматериалы с различным содержанием палладия от свойств полупроводниковых сенсоров к водороду.
Методы
Синтез наноразмерного диоксида олова
Синтез наноразмерного SnO 2 материалов проводился золь-гель методом. Образец SnCl 4 · 5H 2 O ( м =1,5 г) растворяли в 15 мл этиленгликоля. Полученный раствор упаривали при 110–120 ° C. После испарения этиленгликоля образовывался темно-коричневый гель. Полученный гель сушили при 150 ° C с образованием ксерогеля. Ксерогель измельчали и помещали на керамическую пластину. Для получения наноразмерного SnO 2 Термическое разложение ксерогеля проводили на воздухе в высокотемпературной печи Gero (Германия). Наноразмерный SnO 2 , карбоксиметилцеллюлоза и PdCl 2 были использованы для получения газочувствительных материалов.
Подготовка адсорбционных полупроводниковых датчиков
Адсорбционно-полупроводниковые сенсоры были изготовлены путем нанесения пасты из газочувствительного материала на керамическую пластину сенсора, имеющую измерительные электрические контакты и нагреватель [19]. Паста была приготовлена путем смешивания синтезированного SnO 2 наноматериал и водный раствор (3 мас.%) карбоксиметилцеллюлозы. Определенный объем пасты (3 мкл) помещали на керамическую пластину сенсора с помощью шприца Гамильтона 85 RN SYR (5 мкл), чтобы обеспечить такую же толщину сенсорного слоя. Согласно данным SEM, толщина слоя сенсора составляла около 70 мкм (дополнительный файл 1:Рисунок S1, раздел вспомогательной информации). Сенсоры сушили при 90 ° C в течение 1 ч на воздухе. Введение палладия в газочувствительные слои сенсоров осуществлялось пропиткой их раствором хлорида палладия определенных концентраций (CPdCl 2 =0,05 × 10 −2 –0,15 М). После пропитки сенсоры сушили и спекали в высокотемпературной печи в двух различных температурных режимах, включая ступенчатый нагрев сенсоров (рис. 1а, б). Датчики и газочувствительные материалы, полученные в режимах температурного нагрева 1 или 2, получили название S 1 . или S 2 соответственно.
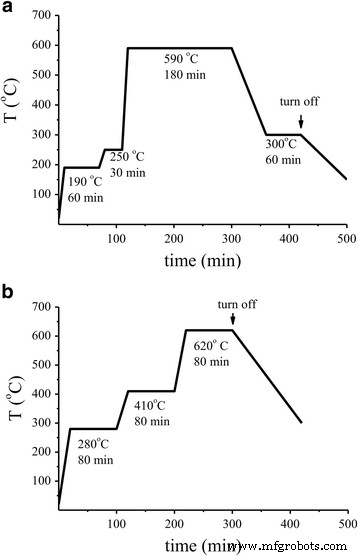
Схемы температурного нагрева датчиков на основе SnO 2 . а Режим 1. b Режим 2
Методы измерения
Для измерения величины сигнала датчика датчики помещались в камеры и подключались к специальному электрическому стенду [20]. Измерения проводились с использованием анализируемого газового потока со скоростью 400 мл / мин. Необходимая температура датчика обеспечивалась определенным значением напряжения на нагревателе датчика. Измерение температуры сенсора производилось пирометром Optris Laser Sight (Optris, Германия). Стабилизация сенсоров осуществлялась старением при 400 ° C в течение 1 недели на воздухе с периодической обработкой сенсоров водородно-воздушной смесью с 1000 ppm H 2 . перед измерением газочувствительных свойств.
Отношение значения электрического сопротивления датчика в воздухе ( R 0 ) до значения его электрического сопротивления в присутствии 40 ppm H 2 ( R H2 ) был выбран в качестве меры отклика датчика. Время отклика датчика ( t 0,9 ) оценивается как время, необходимое датчику для достижения 90% значения равновесного сигнала при замене воздуха анализируемым газом. Время восстановления ( τ 0,1 ) был оценен как время, необходимое для того, чтобы датчик вернулся на 10% выше начального сигнала в воздухе, когда анализируемый газ заменяется воздухом.
Характеристики сенсоров исследованы на водородно-воздушных смесях с различной концентрацией H 2 . . Смеси воздуха с H 2 , CO, CH 4 , и H 2 и CO или H 2 и CH 4 были использованы для оценки селективности полученных сенсоров. Все анализируемые газовые смеси были приготовлены и испытаны в Украинском центре сертификации и метрологии.
Стабильность ответов на 40 ppm H 2 для датчиков S 2 (С-67 и С-69) в течение 6 месяцев эксплуатации изучались.
Определение удельной поверхности сенсорного материала проводилось методом Брунауэра-Эммета-Теллера (БЭТ).
Содержание палладия в материалах сенсора определяли атомно-абсорбционным методом на спектрофотометре AAS1N Carl Zeiss (Йена, Германия) с пламенным распылителем. Распыление палладия производилось в пламени ацетилен-воздух (2350 ° C).
Исследование фазового состава проводилось на дифрактометре Bruker D &Advance (излучение Cu Kα ). Идентификация фазы образца проводилась путем сравнения полученных результатов с опубликованными кристаллографическими данными.
Изучение морфологии сенсорных материалов методом ПЭМ проводили на просвечивающем электронном микроскопе SELMI PEM-125 K с ускоряющим напряжением 100 кВ. Анализ размера частиц на основе изображений ПЭМ проводили с использованием программы Kappa Image Base. Для получения информации о гранулометрическом составе полученных наноматериалов было учтено около 300 частиц на ПЭМ-изображении.
Образцы полученных наноматериалов исследовали методом FESEM на автоэмиссионном сканирующем электронном микроскопе JEOL JSM-6700F (JEOL Ltd., Япония) и методом HRTEM на просвечивающем электронном микроскопе JEM-2100F (JEOL Ltd., Япония).
Толщина сенсорного слоя оценивалась с помощью сканирующего электронного микроскопа JEOL JSM-6060LA (JEOL Ltd., Япония) с рабочим напряжением 30 кВ.
Результаты и обсуждение
Синтезированные наноматериалы на основе SnO 2 [21] со средним размером частиц 8 нм были использованы для создания сенсоров и исследования влияния различных температурных режимов нагрева сенсорной заготовки на газочувствительные свойства.
Ранее было установлено [19, 22, 23], что формирование газочувствительного слоя сенсоров, изготовленных в режиме температурного нагрева 1 с конечной температурой в диапазоне 590–620 ° С в течение 180 мин, приводило к образуют частицы размером от 5 до 30 нм (средний размер 17 нм). ПЭМ изображение сенсорного наноматериала S 1 полученная с использованием температурного режима нагрева 1 с конечной температурой 590 ° C, представлена на рис. 2а. Ответ ( R 0 / R H2 ) датчика по материалу равнялась 6,7. Повышение чувствительности сенсора может быть обеспечено за счет использования материалов с меньшим размером частиц. Такие частицы, возможно, могут быть получены в режиме температурного нагрева с меньшей продолжительностью при конечной температуре спекания сенсора. Было обнаружено, что уменьшение продолжительности нагрева сенсора с 180 до 80 мин при конечной температуре режима нагрева 1 (590 ° C) привело к формированию очень малых значений откликов сенсора на 40 ppm H 2 ( R 0 / R H2 ~ 2) и высокие значения электрических сопротивлений датчиков в воздухе (> 500 МОм) для большинства созданных датчиков. Эти условия спекания сенсора, вероятно, не привели к образованию достаточного количества контактов между частицами материала для прохождения электрического тока через сенсор.
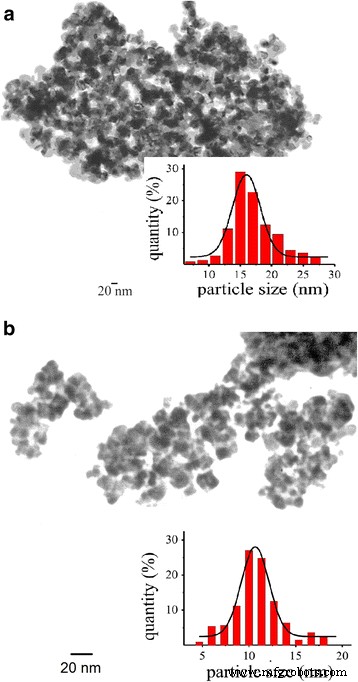
ПЭМ-изображения газочувствительных наноматериалов a S 1 и b S 2
Для обеспечения формирования проводимости сенсора и его механической прочности продолжительность нагрева сенсора уменьшена до 80 мин с одновременным увеличением конечной температуры спекания сенсора до 620 ° С. Кроме того, время нагрева сенсора в этом температурном режиме увеличено до 80 мин в низкотемпературных областях спекания, а именно при 280 и 410 ° С, что соответствует температурам разложения КМЦ и хлорида палладия [24,25 , 26]. Эти изменения в низкотемпературных областях формирования сенсора вызваны необходимостью формирования большего количества контактов в материале сенсора. Увеличение размера частиц материала в низкотемпературных областях, конечно, не должно быть таким интенсивным, как должно быть при 620 ° C. Схема более мягкого температурного нагрева в режиме 2 спекания датчика представлена на рис. 1б.
Анализ ПЭМ-микрофотографий полученных сенсорных материалов S 2 (Рис. 2b) показали, что эти материалы включают частицы, которые были меньше, чем частицы материала датчика S 1 (Рис. 2а):средний размер частиц диоксида олова для обоих исследуемых температурных режимов нагрева 1 и 2 составил 17 и 11 нм соответственно. Такое уменьшение размера частиц сенсорного материала S 2 способствовал увеличению значения удельной поверхности диоксида олова до 47 м 2 / г вместо 39 м 2 / g, который был найден для материала сенсора S 1 .
Было показано, что содержание палладия в Pd / SnO 2 наноматериалы, полученные пропиткой наноразмерного SnO 2 растворами PdCl 2 увеличивается при увеличении концентрации хлорида палладия. В частности, при концентрации PdCl 2 раствор был изменен с 0,05 моль / л на 15 × 10 -2 моль / л, содержание добавок палладия в наноматериалах изменено с 0,001 до 0,193 мас.%.
Согласно данным РФА, немодифицированный диоксид олова и Pd / SnO 2 наноматериалы с различным содержанием палладия, полученные в обоих температурных режимах, имеют структуру касситерита с идентичными параметрами решетки a =0,4738 нм, b = c =0,3187 нм [21].
Изображение полученного сенсорного материала с помощью FESEM (рис. 3а) демонстрирует зерна SnO 2 наноматериал и частицы Pd (показаны стрелками на рис. 3а). Четкие границы между частицами сенсорного наноматериала можно увидеть на изображениях ПЭМВР (рис. 3b, c).
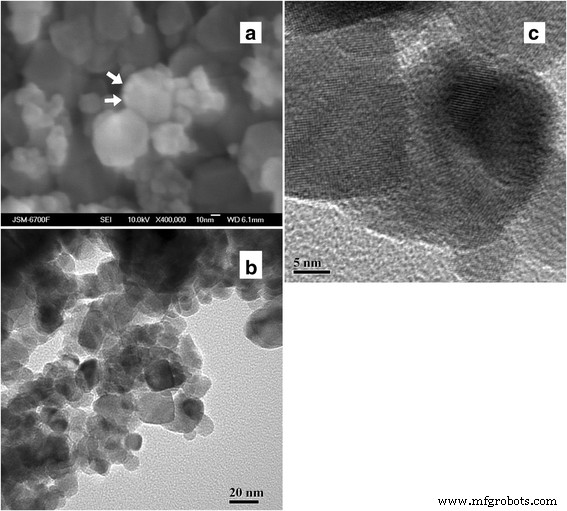
а ФЕСЭМ и б , c Изображения HRTEM сенсора Pd / SnO 2 наноматериал
Было показано (рис. 4а, б), что зависимость значений электросопротивления в воздухе Pd-содержащих сенсоров от содержания палладия при различных температурах сенсора имеет сложный характер с минимумом при малых содержаниях палладия и широким максимумом при значительно более высоких значениях Pd. содержание для обоих различных температурных режимов нагрева датчиков.
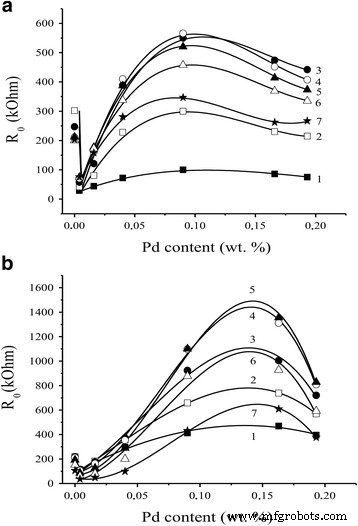
Зависимость R 0 значения датчиков а S 1 и b S 2 на основе Pd / SnO 2 от содержания палладия при разных температурах сенсоров: 1 410 ° С, 2 382 ° С, 3 355 ° С, 4 327 ° С, 5 295 ° С, 6 261 ° C и 7 225 ° С
Для объяснения полученных результатов следует отметить, что значения сопротивления R 0 и отклик сенсора при добавлении металлов (или оксидов) в материал газочувствительного слоя обеспечивался образованием общих границ между частицами активной добавки и диоксида олова [19, 27, 28]. При нагревании сенсора на воздухе эти границы участвуют в хемосорбции кислорода с локализацией электронов из зоны проводимости полупроводника. Такая хемосорбция влияет на значения электрического сопротивления датчика. В присутствии анализируемого газа на поверхности полупроводника протекает гетерогенная каталитическая реакция окисления газа хемосорбированным кислородом. Электроны, локализованные на хемосорбированном кислороде, возвращаются в зону проводимости полупроводника, и происходит уменьшение электрического сопротивления сенсора. В этом случае постоянное количество кислорода на поверхности датчика, которое возникает в результате состояния динамического равновесия реакции окисления, будет определять значение сопротивления датчика. Изменение значения сопротивления датчика при замене воздуха анализируемым газом определяет величину отклика датчика. При одинаковых условиях (один и тот же газ определенной концентрации и одинаковая температура датчика) величина электрического сопротивления датчика в воздухе и его изменение в присутствии анализируемого газа (реакция датчика) будет зависеть от длины границы между частицами палладия и диоксида олова. Содержание палладия в материале сенсора будет влиять на значение длины границы и, таким образом, будет определять свойства сенсора.
Как видно из рис. 4а, б, введение палладия (до 0,05% Pd) влияет на значение датчика R 0 Таким же образом независимо от режима нагрева датчика температуры спекания. Наблюдаемое первоначальное уменьшение значения электрического сопротивления сенсора может происходить в результате наличия металлического палладия, который образуется на поверхности сенсора согласно полученным данным РФЭС [19]. Дальнейшее увеличение содержания палладия приводит к небольшому увеличению значений сопротивлений датчиков S 1 и S 2 из-за низкой хемосорбции кислорода на границе очень небольшой длины между SnO 2 и частицы палладия. Следует отметить, что аналогичные значения сопротивлений датчиков S 1 и S 2 Такие низкие содержания палладия указывают на отсутствие значительного влияния палладия на свойства сенсоров, которые определяются собственными свойствами диоксида олова в этих условиях. Было установлено, что величина электрического сопротивления SnO 2 практически не зависела от температуры спекания сенсора в диапазоне температур 590–620 ° C, как это было обнаружено в [19,22 ,, 21–23].
Изменение температурного режима нагрева создания датчиков S 1 и S 2 существенно влияет на величину их сопротивления при увеличении содержания палладия (> 0,05% Pd) (рис. 4а, б). Действительно, сопротивление датчиков S 2 имеют гораздо большие значения, чем у датчиков S 1 в условиях того же содержания палладия в интервале концентраций 0,05–0,2% Pd. Это согласуется с предположением о стабилизирующей роли палладия [29], который предотвращает увеличение размеров частиц наноматериала, и режим мягкого температурного нагрева 2 спекания сенсора способствует этому процессу. Длина границ между частицами палладия и диоксида олова в этих мягких температурных условиях будет больше для материала S 2 . , и, следовательно, из-за большого количества хемосорбированного на границах кислорода значения сопротивления для датчиков S 2 должны быть больше, чем у датчиков S 1 . Это подтверждается экспериментом (рис. 4а, б). Образование более мелких частиц для Pd-содержащих наноматериалов, полученных в мягких температурных условиях режима нагрева 2, также было подтверждено методом ПЭМ (рис. 2b).
Наконец, при очень высоком содержании палладия может начаться процесс агрегации частиц Pd, который приведет к уменьшению длины общих границ, что приведет к уменьшению значений электрического сопротивления датчиков (рис. 4b).
В целом изменение откликов датчиков на водород коррелирует с изменением их электрического сопротивления (рис. 4а, б и 5а, б):увеличение значений электрического сопротивления датчиков приводит к увеличению значения реакции их сенсоров на H 2 . Отклики датчиков S 2 до 40 ppm водорода выше, чем отклики датчиков S 1 (Рис. 5). Как видно (рис. 5), уменьшение отклика сенсора на H 2 наблюдается при наибольшем содержании добавок Pd по сравнению с датчиком S 2 . Вероятно, это может быть связано с агрегацией кластеров палладия, которые в значительной степени покрывают поверхность полупроводника, и поверхность диоксида олова становится недоступной для водорода. Поэтому в эксперименте наблюдается уменьшение чувствительности сенсора.

Зависимость реакции сенсора на 40 ppm H 2 для датчиков а S 1 и b S 2 на основе Pd / SnO 2 от содержания палладия при разных температурах сенсоров: 1 410 ° С, 2 382 ° С, 3 355 ° С, 4 327 ° С, 5 295 ° С, 6 261 ° C и 7 225 ° С
Установлено, что положения максимальных значений электрических сопротивлений сенсора (рис. 4а, б) и откликов сенсора (рис. 5а, б) для сенсора S 2 по сравнению с датчиком S 1 смещены в область повышенного содержания палладия. Это может быть результатом наличия относительно большего содержания палладия на поверхности сенсора в неагрегированном состоянии для материала SnO 2 с меньшим размером их частиц. Такое состояние материала будет способствовать увеличению значения электрического сопротивления датчика в воздухе и реакции датчика на водород.
Для наиболее чувствительного сенсора S 2 на основе 0,09% Pd / SnO 2 наноматериал, исследованы другие сенсорные свойства. Было обнаружено, что этот сенсор чувствителен к водороду в широком диапазоне его концентраций при различных температурах работы сенсора (рис. 6). Зависимость проводимости датчиков от H 2 концентрация практически линейна в испытанном диапазоне H 2 концентрация (2–1000 частей на миллион H 2 ) при разных температурах сенсора (327 и 382 ° C) (рис. 6). Нелинейность проводимости сенсора в широком диапазоне H 2 Концентрация при 261 ° C, вероятно, связана с различной энергетической связью хемосорбированного кислорода на поверхности сенсора. Было обнаружено, что предел обнаружения H 2 измерение для наиболее чувствительного датчика равно 2 ppm в воздухе. Изменение проводимости сенсора, достигающее 44–52% для такой низкой концентрации водорода, зависит от температуры сенсора. Следует отметить, что реакция на 2 ppm H 2 ( R 0 / R H2 =2,1 при 261 ° C) для созданного сенсора выше, чем отклик на тот же H 2 концентрация ( R 0 / R H2 =1,3 при 265 ° C) для сенсора на основе наноразмерного SnO 2 изучен в [30].
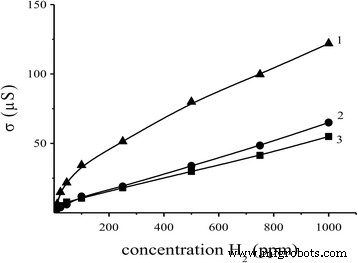
Зависимость проводимости датчика S 2 на основе 0,09% Pd / SnO 2 наноматериал от концентрации водорода при различных температурах сенсора: 1 261 ° С, 2 327 ° С, 3 382 ° С
Было показано, что датчик на базе S 2 материал (0,09% Pd / SnO 2 ) обладают быстрым откликом ( t 0,9 =3 с) и восстановления ( τ 0,1 =12 с) время при 261 ° C (рис.7). Следует отметить, что созданные сенсоры также имеют высокий отклик сенсора ( R 0 / R H2 =19,5) до микроконцентрации (40 частей на миллион H 2 ) водорода. Это намного лучше по сравнению с соответствующими характеристиками датчика на основе Pd / SnO 2 наноматериал, изученный в [31], где чувствительность сенсора к 50 ppm H 2 равно R 0 / R H2 =15,9, а время отклика и восстановления равняется t 0,9 =120 с и τ 0,1 =15 мин.
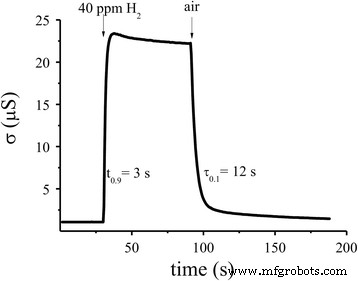
Изменение проводимости в зависимости от времени для оптимального сенсора, легированного Pd (0,09% Pd / SnO 2 ) при температуре сенсора 261 ° C
Результаты исследования селективности по H 2 для датчиков S 2 содержащий 0,09 мас.% Pd ( T =261 ° C) в присутствии CO и CH 4 показаны на рис. 8. Сравнение реакции сенсора на H 2 , Канал 4 , или CO той же концентрации (500 ppm) показывает, что реакция сенсора на H 2 намного выше, чем для CH 4 или CO. Вот почему наличие CH 4 или CO с концентрацией 500 ppm в анализируемой газовой смеси с 500 ppm H 2 практически не влияет на измерение водорода (рис. 8). Такое влияние отсутствует и при измерении микроконцентрации H 2 . (20 ppm) в случае его смеси с 500 ppm CH 4 или CO. Такое поведение датчиков можно объяснить разными значениями оптимальной температуры датчика, необходимой для обеспечения максимального значения отклика датчика для каждого из исследуемых газов. Оптимальная температура датчика для измерения H 2 намного ниже (261 ° C), чем для CH 4 (382 ° C) и CO (327 ° C). Низкая температура сенсора для измерения H 2 объясняется более высокой активностью H 2 по сравнению с CH 4 и активность CO в реакции окисления на поверхности сенсора. Практическое отсутствие помех от канала 4 и CO для реакции сенсора на H 2 (Рис. 8) в изученных условиях также можно объяснить преобладающей реакцией окисления водорода, протекающей на поверхности из-за более высокой реакционной способности H 2 по сравнению с CO и CH 4 .
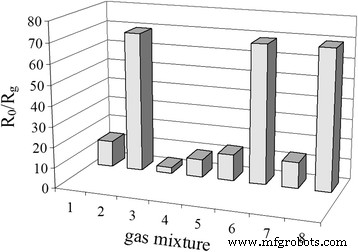
Отклик датчика S 2 содержащий 0,09 мас.% Pd ( T =261 ° C) при воздействии анализируемой газовой смеси воздуха с 1 20 частей на миллион H 2 , 2 500 частей на миллион H 2 , 3 500 частей на миллион CH 4 , 4 500 частей на миллион CO, 5 20 частей на миллион H 2 + 500 частей на миллион CH 4 , 6 500 частей на миллион H 2 + 500 частей на миллион CH 4 , 7 20 частей на миллион H 2 + 500 частей на миллион CO и 8 500 частей на миллион H 2 + 500 чнм CO
Стабильность отклика датчика длительной работы для двух датчиков S 2 на основе 0,09% Pd / SnO 2 наноматериал в течение 6 месяцев. Выяснилось, что датчики S 2 не потеряли своих сенсорных откликов и не имели направленного дрейфа сенсорного отклика через 6 месяцев работы сенсора (рис. 9). Этот результат показывает возможность применения созданных датчиков на практике.
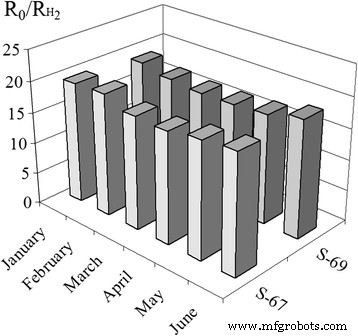
Реакция на 40 частей на миллион H 2 датчиков S 2 (S-67 и S-69) на основе 0,09% Pd / SnO 2 наноматериал за 6 месяцев эксплуатации при температуре сенсора 261 ° C
Выводы
Изменение условий высокотемпературной обработки сенсоров на основе Pd / SnO 2 привело к формированию более мелких частиц наноматериала газочувствительного слоя сенсора, что позволило достичь значительного значения отклика сенсора ( R 0 / R H2 =19,5) до микроконцентрации водорода (40 ppm) при температуре сенсора 261 ° C. Созданные сенсоры позволяют измерять водород в широком диапазоне его концентраций (2–1089 ppm H 2 ), имеют нижний предел H 2 обнаружения и демонстрируют быстрое время отклика и восстановления. Созданные сенсоры стабильны при длительной эксплуатации.
Наноматериалы
- Работа виртуального датчика и его приложения
- Работа датчика занятости и его приложения
- Работа дверного датчика и его применение
- Основы цифровых магнитных датчиков
- Понимание датчиков
- Индуктивный бесконтактный датчик положения
- Датчики исключают искрообразование в водородных транспортных средствах
- Носимые датчики обнаруживают утечку газа
- Датчики устраняют риск искрения в водородных транспортных средствах
- Лабораторный датчик расхода и температуры