MMF # 3:армированные волокном живые петли, достаточно прочные, чтобы на них стоять
MarkForged Mechanical Features [MMF] - это серия сообщений в блоге, в которых подробно описываются передовые методы проектирования обычных традиционных инженерных деталей и механических элементов для 3D-печати с композитным армированием с помощью принтеров MarkForged.
Плохая вертикальная прочность детали обычна для 3D-принтеров FFF (Fused Filament Fabrication), особенно при натяжении. В этих технологиях 3D-печати связь по вертикальной оси слабее, чем прочность составляющего материала, потому что в каждой части есть сотни слоев, склеенных друг с другом вдоль вертикальной оси, поэтому соединение между каждым слоем ведет себя как шов или трещит при загрузке. Прочность слоя в плоскости выше, чем межслойная адгезия, потому что пластик в каждом слое укладывается в виде непрерывного экструдата и проявляет прочностные свойства самого материала детали. На Mark Two эта направленная разница в прочности (или анизотропии) также возникает с нашим процессом производства непрерывных волокон (CFF) - все композитные волокна, с которыми мы работаем, имеют впечатляющую прочность на разрыв, но потому, что они уложены вдоль плоскостей, параллельных плоскости строительной плиты, эта сила не переносится напрямую на вертикальную ось. Правильный дизайн деталей, напечатанных на 3D-принтере, подразумевает подгонку геометрии компонента таким образом, чтобы он в основном загружался в горизонтальной плоскости, и детали, созданные на принтере Markforged, не являются исключением. Однако с помощью некоторых изящных дизайнерских уловок вы можете обойти эту проблему и создавать промышленные 3D-печатные детали на Mark Two с гораздо более изотропными свойствами.
Если вы раньше работали с нашими материалами, то, возможно, заметили, что наш нейлон может быть довольно гибким сам по себе. Это позволяет создавать подвижные петли или гибкие секции компонентов, которые могут образовывать соединение или шарнир без какой-либо сборки. Узнайте больше о проектировании подвижных петель и изгибных элементов здесь.
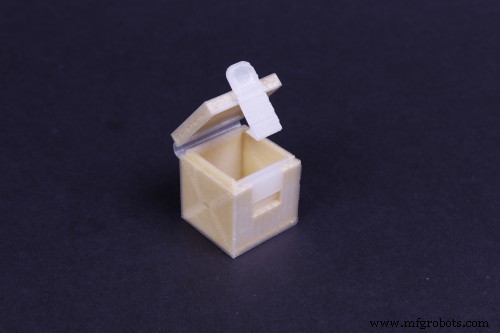
Хотя армирование волокном на принтере Markforged может немного повысить жесткость нейлона, вы можете использовать Kevlar® для создания армированных волокном живых петель. В этих складывающихся трехмерных печатных структурах нейлон обеспечивает гибкость, а волокно обеспечивает прочность соединения. Используя немного армированного волокном оригами, вы можете создавать скелетонированные детали с минимальным количеством поддерживающего материала, которые будут прочными во всех направлениях. Вот пример:
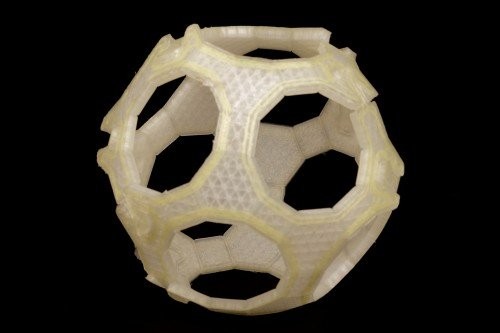
Для печати такой детали потребовалось бы безумное количество времени и вспомогательного материала, и она была бы довольно слабой по вертикальной оси, поэтому я решил напечатать ее следующим образом:
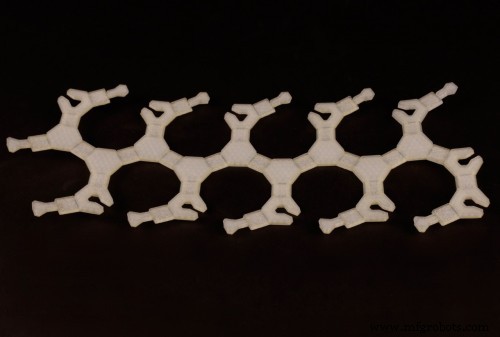
Взглянув на расположение волокон в Эйгере, вы увидите только один слой кевлара с концентрическим рисунком на этом отпечатке. Я выбрал кевлар, потому что, хотя углеродное волокно и стекловолокно прочнее, кевлар является наиболее гибким из материалов, которые мы предлагаем, и сохраняет большую часть своей прочности на разрыв даже при изгибе под острыми углами. Углеродное волокно и стекловолокно намного жестче и ломаются на радиусах изгиба, с которыми кевлар может без проблем справиться. Однослойный кевлар обеспечивает достаточную прочность для этого мяча, чтобы выдержать несколько десятков фунтов, но при этом достаточную гибкость для того, чтобы суставы красиво складывались.
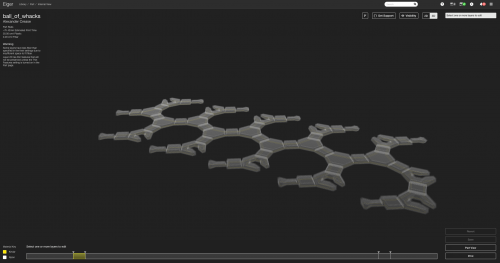
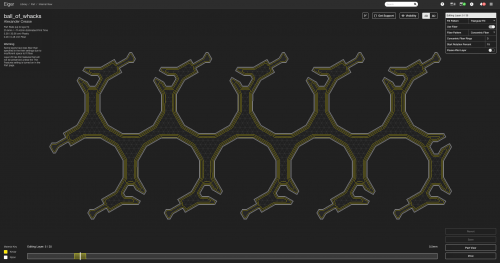
После создания многогранника я повысил ставки, чтобы посмотреть, смогу ли я напечатать на 3D-принтере что-нибудь складное, достаточно прочное, чтобы выдержать вес моего тела. Я решил не усложнять задачу и спроектировал складной куб из кевлара в Autodesk Fusion 360. Мне нужен был способ скрепления граней куба вместе и соединение для соединения граней, которые не были непосредственно примыкающими друг к другу. Я начал с моделирования четырех граней куба, каждую как отдельного компонента, чтобы можно было манипулировать в среде САПР, чтобы смоделировать поведение складывания, которое я хотел для своего сустава. Чтобы обеспечить соединение между каждой гранью, я спроектировал соединение с защелкиванием так, чтобы, когда вы складываете каждую грань в правильную ориентацию, грань защелкивалась на месте, а стыковка с защелкой предотвращала разворачивание или деформацию куба.
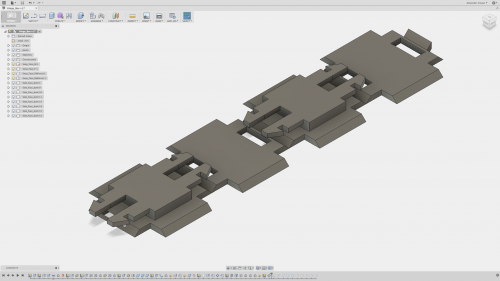
Я также добавил небольшой паз и шип к краям, которые в конечном итоге соединятся, когда крайняя левая грань встретится с крайней правой.
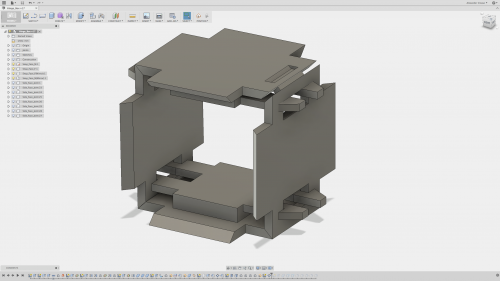
Затем я решил попробовать что-нибудь интересное с оставшимися двумя сторонами коробки - на каждом открытом оставшемся крае я разработал секцию каждой стороны. У каждой секции есть вкладка с поворотной посадкой и вырез для соответствующей вкладки в соседней секции. После того, как коробка сложена, все они могут быть соединены вместе, чтобы образовать оставшиеся две стороны. На изображении ниже я сделал одну из частей прозрачной, чтобы показать фаски, которые я добавил для создания соединения в форме ласточкина хвоста, которое зависит от гибкости материала, который нужно скрутить на место.
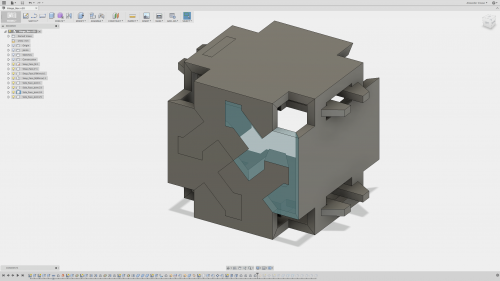
После того, как геометрия каждой грани была высечена в камне, я «развернул» куб в САПР так, чтобы все тела были уложены в той ориентации, в которой я хотел напечатать деталь. На изображении ниже вы заметите, что каждый из компонентов встречаются по краям - они еще не связаны. На данный момент мне все еще нужно было объединить это в единую унифицированную деталь, добавив слои, необходимые для создания живого шарнира.
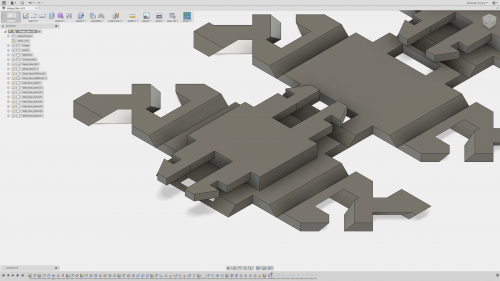
Для этого я захватил профили нижних граней каждого компонента, выдавил их на 0,875 мм и объединил все отдельные тела в одно. Это придает толщину живой петле:толщина 0,875 мм добавляет материала, достаточного для того, чтобы один слой кевлара мог поместиться внутри и создать живую петлю, армированную волокном. Обратите внимание на то, что теперь каждая кромка, на которой встречаются отдельные компоненты, теперь имеет толщину.
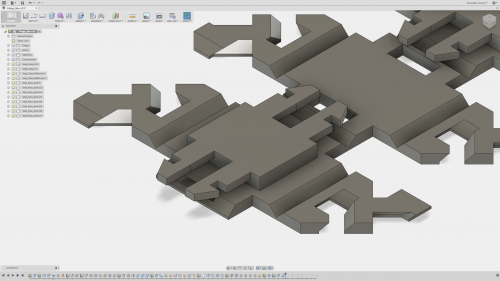
А вот и полный вид детали, готовой к печати:
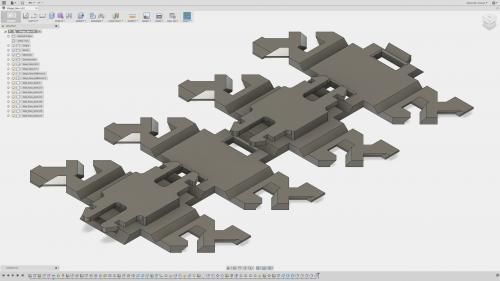
В Эйгере я выложил концентрические кольца волокна на этот первый слой кевлара, чтобы создать и укрепить соединение. Чтобы усилить остальную часть детали, я создал сэндвич-панели, начиная с каждой стороны над первым слоем кевлара. Как мы объясняли в более ранней публикации, сэндвич-панели имеют фундаментальное значение для композитных материалов, поскольку они обеспечивают высокую прочность при небольшом весе. Сэндвич-панели усиливают каждую грань куба, делая их прочными и жесткими компонентами, напечатанными на 3D-принтере - имейте в виду, что каждая грань имеет толщину всего около 3 мм. Я также смог вставить кевлар в шарниры с защелкой, чтобы усилить их мелкие детали, которые мы обсуждали в предыдущем посте. На приведенном ниже GIF-изображении показаны несколько первых слоев, включая слой живой петли, армированный кевларом (слой 5), и нижние слои сэндвич-панели (слои 6-8).
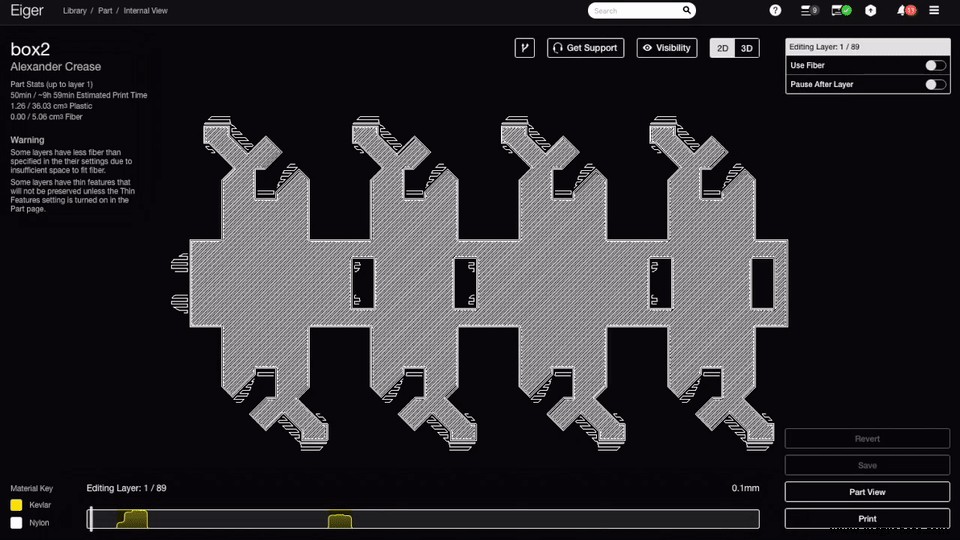
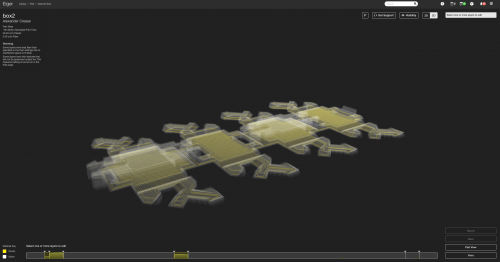
После того, как он напечатан, я собрал все вместе, скрутил стыки боковых панелей и сделал 3D-печатный складной куб с некоторым усилением кевларом!
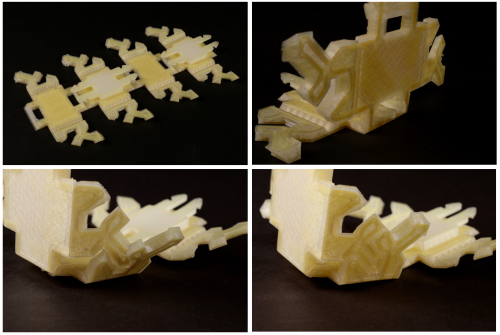
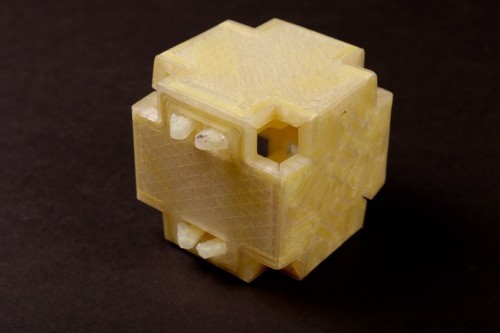
Каждая сторона куба обеспечивает существенное усиление как при растяжении, так и при изгибе, что делает куб в целом очень трудным для сжатия и изометрическим по трем основным осям. Я смог перенести на него все свое тело (около 130 фунтов) без малейшей деформации. Однако я довольно маленький человек, поэтому прошел гораздо более тщательный тест. Я не получил очень хороших результатов, но я предполагал, что он удерживал около 300-400 фунтов, прежде чем потерпеть неудачу. Вот что произошло:
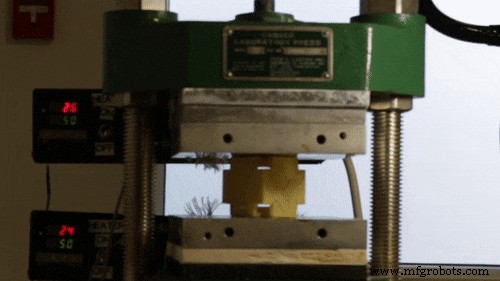
Итак, после нескольких сотен фунтов самым удивительным было то, что деталь на самом деле не сломалась, все суставы просто разлетелись, а весь куб стал плоским, поэтому, немного выпрямив его, можно вернуть его первоначальную форму. Таким образом, создавая складные конструкции с живыми петлями, армированными волокном, вы можете создавать действительно прочные 3D-печатные детали во всех направлениях.
Хотите распечатать это сами? Загрузите файл в формате STL или .mfp!
Хотите испытать силы на себе? Закажите бесплатный образец здесь!
3D печать
- Что такое двустворчатые петли?
- 5 преимуществ выбора алюминиевых петель
- Введение в неразрезные петли
- Преимущества живых петель
- Существующие лазерные технологии достаточно сильны, чтобы привлечь инопланетян на расстоянии 20 000 световых л…
- Мой первый индивидуальный мини-фрезерный станок с ЧПУ — он должен быть достаточно прочным
- Ферро-Титанит® У
- ДИФЕНДЕР 400
- Понимание прочности на сжатие
- Как спроектировать живые шарниры с помощью 3D-печати