PEEK или PEKK в будущих аэроструктурах TPC?
Что лучше для уплотнения на месте (ISC) лент из термопластичного композита (TPC), разрабатываемых для производства первичных конструкций самолетов, полиэфирэфиркетона (PEEK) или полиэфиркетонекетона (PEKK)? На этой боковой панели представлены дебаты PEEK и PEKK, которые являются частью более широкой дискуссии о том, является ли ISC действительно одностадийным процессом вне автоклава (OOA) может удовлетворить поставленные цели по стоимости и производительности для будущего производства самолетов - это 60-70 самолетов в месяц для узкофюзеляжного реактивного лайнера A320 neo. Альтернативный вариант - использовать два шага :укладка термопластичных композитных лент с помощью автоматизированного размещения волокон (AFP) с последующим закреплением в автоклаве или нагретом прессе. Дополнительные сведения см. В разделах «Укрепление аэроструктур из термопластичного композита на месте, часть 1» и «Часть 2» (также см. Недавнюю тематическую статью Джеффа Слоана о термопластичных лентах).
И PEEK, и PEKK являются членами более широкого семейства полиарилэфиркетонов (PAEK), часто называемых поликетонами . . «PEKK очень похож на PEEK, и его поведение при кристаллизации аналогично, но его температура обработки составляет 375 ° C по сравнению с 385 ° C для PEEK», - говорит Анри де Врис, старший научный сотрудник отдела композитных материалов из отдела структурных технологий в Нидерландский аэрокосмический центр (NLR, Амстердам). Подразделение Fokker компании NLR и GKN Aerospace (Реддич, Великобритания) (Папендрехт и Хоогевен, Нидерланды) впервые внедрило множество технологий TPC в программах TAPAS 1 и TAPAS 2, включая торсионную коробку с размахом 12 м и совсем недавно - 6 м длиной и толщиной 28 мм CF / Верхний лонжерон пилона двигателя ПЭКК изготовлен из AFP, но упрочнен в автоклаве. (См. «Демонстрации термопластичных композитов - дорожная карта ЕС для будущих планеров»).
Де Фрис видит PEKK . как более удобный для AFP, поскольку окно процесса шире . Для PEEK температура должна быть 385–390 ° C, поэтому обработка при 360 ° C не идеальна. Однако с ПЭКК обработка неплохая даже при 355 ° C. Таким образом, ваша нижняя граница не только ниже, но и у вас есть немного больше времени до схватывания материала, поэтому общее время, в течение которого он находится в расплаве, будет немного больше, а значит, лучшее уплотнение . »
Де Фрис добавляет, что PEKK интересен для штамповки, более быстрого варианта консолидации на втором этапе по сравнению с вакуумной упаковкой в мешки и циклической обработкой в автоклаве. «Старые марки PEKK (DS) были слишком медленными для штамповки, но новые марки (FC) лучше и дешевле, чем PEEK ».
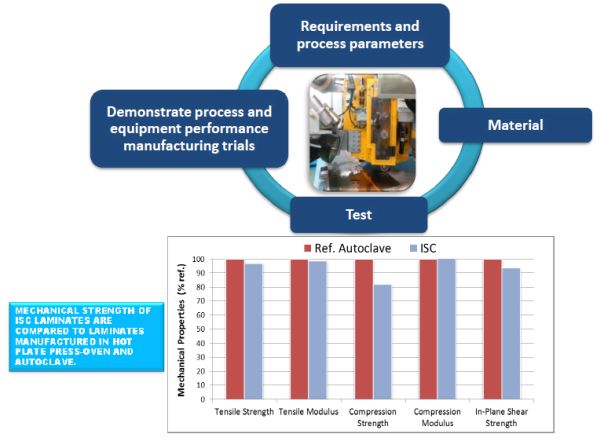
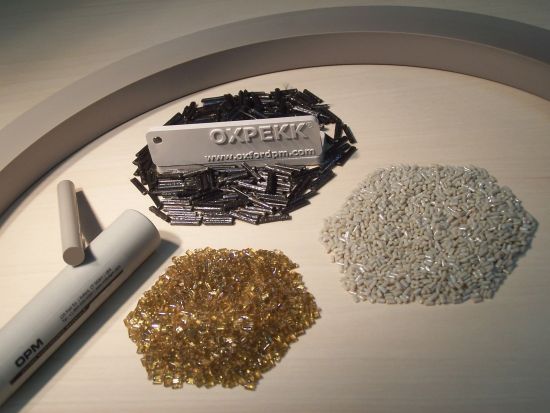
«Oxford Performance Materials (OPM) работает с PEKK с 2000 года, - говорит ДеФелис, - разрабатывая как материалы, так и технологии их применения. Все продукты PEKK, представленные сегодня на рынке, производятся с использованием метода DuPont . . » Он объясняет, что в основном все поликетоны были разработаны одновременно, в ответ на потребность в улучшении характеристик пожаротушения, дыма и токсичности (FST) в салонах самолетов, которым угрожают новые правила FAA в 1990-х годах . . Однако правила так и не были реализованы, и первоначальный рынок для PEEK и PEKK испарился. Таким образом, ICI выделила PEEK на Victrex, а DuPont продала PEKK компании Fiberite, которую приобрела Cytec, которая, в свою очередь, была приобретена Solvay. ДеФелис говорит, что Arkema стала партнером OPM с целью получения опыта в отношении PEKK и в конечном итоге разработала продукт PEKK, разработанный DuPont. В результате этого партнерства Arkema стала вторым источником для PEKK . в индустрии композитов.
«Hexcel также инвестировал в OPM», - говорит ДеФеличе. (Здесь мы сделаем небольшое отступление, чтобы объяснить приобретение Hexcel подразделения OPM по производству аддитивов в аэрокосмической и оборонной промышленности. «Мы разработали технологию аддитивного производства с использованием селективного лазерного плавления (SLM) с PEKK, армированным углеродным волокном, которое сертифицировано в Boeing, Northrop Grumman и других. для приложений AEROSPACE. Это было привлекательно для Hexcel, который уже был значительный акционер OPM ». Так, в декабре 2017 года Hexcel приобрела аэрокосмический и оборонный бизнес OPM (Южный Виндзор, Коннектикут, США). OPM, однако, сохраняет свой бизнес 3D-печати PEKK за пределами аэрокосмической и оборонной промышленности и продолжает развивать свои основные технологии в области материаловедения.
«Не все PEKK одинаковы», - утверждает ДеФеличе. «Solvay и Arkema практикуют метод DuPont, в котором используется высокотемпературный синтез (HTS) . , поэтому он работает немного быстрее, что снижает стоимость. Однако у него есть и недостатки ». Он объясняет, что изначально были проблемы со стабильностью расплава и чистотой полимера PEKK, что затрудняло производство деталей для DuPont. Со временем метод DuPont улучшился, как и полимер, и детали стали более воспроизводимыми. Например, помимо вышеупомянутых технологий аддитивного производства, OPM разработала литье под давлением, а также применение пленок с PEKK.
«Но мы всегда видели, что PEKK можно изготавливать по-другому и улучшать», - говорит ДеФеличе. «Теперь, если вы вернетесь к первоначальным игрокам, на самом деле был третий, и это был Raychem , который был продан BASF, который просто отказался от ПАЭК. Но технология Raychem была предназначена для низкотемпературного синтеза (НТС) . . Это сильно отличается от HTS ». Он отмечает, что вместо производства полимерных хлопьев который затем необходимо отшлифовать. перед смешиванием с растворителем и т. д. для препрега и 3D-печати эта запатентованная технология LTS позволяет производить порошок сферической формы что можно контролировать. Поскольку LTS - это «холодный» процесс, он также гораздо более контролируем с точки зрения молекулярной массы и молекулярной структуры готового полимера. Однако процесс идет медленнее, поэтому немного дороже. «Но также можно перейти непосредственно к порошку, без этапа измельчения . , - говорит ДеФеличе. «Так что это помогает компенсировать более медленную обработку».
Этот новый продукт, OXPEKK-LTS , предлагает лучшее из обоих миров:управляемый процесс, при котором производится продукт из сферического полимерного порошка. «При шлифовании получаются неровные« камешки »полимера, которые сложно уложить равномерно . при покрытии и пропитке ленты », - поясняет ДеФелис. «Круглая форма OXPEKK-LTS обеспечивает большую точность во время изготовления ленты. Итак, теперь мы можем улучшить ленту и включить настоящую обработку OOA за счет консолидации на месте, чему мешает текущая точность размеров ленты ».
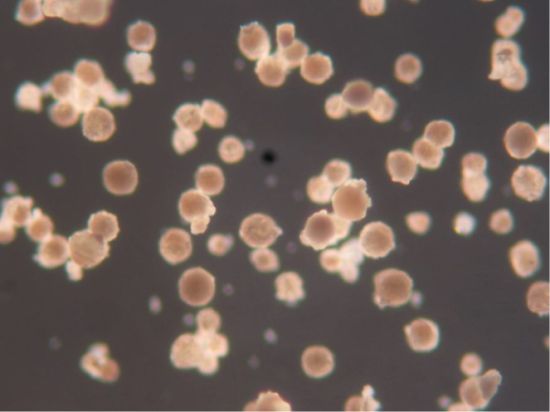
Сферические частицы в OXPEKK-LTS позволяют получить более однородную термопластичную ленту,
который помогает в достижении одностадийных, внеавтоклавных (OOA) консолидированных на месте основных композитных структур летательных аппаратов. ИСТОЧНИК:Oxford Performance Materials.
Так можно ли производить лучшую ленту и при этом соответствовать цене PEEK? «Стоимость, которую Airbus и их поставщики обсуждают для композитных первичных структур, намного сложнее, чем просто стоимость полимерного сырья», - возражает ДеФелис. «Сырье, безусловно, составляет часть общей стоимости компонентов, но процесс изготовления и производительность являются ключевыми элементами затрат. Во-первых, прочность на сжатие у ПЭКК намного выше . чем PEEK, что является существенным преимуществом. Вы можете значительно снизить утомляемость производительность в композитной структуре, что, в свою очередь, означает, что вы можете создавать более легкие конструкции которые не требуют столько материала. Другими словами, мы обеспечиваем более высокое соотношение прочности к весу . . Но мы также включаем ISC, поэтому теперь эти более легкие конструкции производятся за один этап . а не два ».
Но OPM не останавливается на достигнутом. ДеФелис утверждает, что все углеродное волокно, используемое в поликетон предварительная запись для аэрокосмических приложений используется без калибровки . Это является ключевым моментом, поскольку калибровка волокна позволяет ему проходить все этапы обработки с предсказуемостью, уменьшением повреждений и повторяемостью. «Никто в аэрокосмической отрасли не использует углеродное волокно с проклейкой для первичной структуры термопласта PAEK, потому что все известные размеры отрицательно влияют на механические свойства , - поясняет он.
Небольшая заметка здесь. Маттиас Шуберт, технический специалист Teijin Carbon в Европе, не согласен. «Мы использовали специальный размер для PAEK термопластов уже много лет », - поясняет он. «Это было необходимо, потому что стандартные размеры имеют некоторую дегазацию из-за химического состава эпоксида, который ухудшается при температурах обработки PAEK. Наша проклейка на самом деле увеличивает адгезию смолы , что примерно на 20% больше по сравнению с углеродными волокнами большого размера . » Он отмечает, что это было измерено испытаниями на поперечный 4-точечный изгиб и может быть связано с контролируемой инициализацией кристаллических структур на границе раздела волокно-смола. (Обратите внимание, что такое изменение размеров объясняется Жан-Филиппом Канартом из Teijin Carbon America в блоге «PEEK против PEKK против PAEK».)
«С OXPEKK LTS у нас также есть запатентованная химия растворить ПЭКК и использовать его в качестве калибратора что ускоряет обработку и повысить производительность ленты . » - говорит ДеФеличе. Это простирается до консолидации на месте. «Таким образом, сейчас появляется чрезвычайно сильное экономическое обоснование для крупных первичных структур, построенных с использованием этой технологии».
А как насчет более толстых лент? NLR заявила, что хотела бы иметь ленту толщиной 0,25 дюйма, что дополнительно поможет обеспечить производительность 60-70 самолетов в месяц. « Скорость противодействует верности в процессе и производительность в окончательной конструкции », - говорит ДеФелис. «Так что всегда есть баланс между этими противоположными факторами. Физика круглых полимерных частиц в препреггировании хорошо зарекомендовал себя. Мы считаем, что предлагаем контроль над этими частицами, который затем дает больше рычагов для достижения необходимого баланса . для производства больших первичных структур OOA, отвечающих требованиям по стоимости и производительности. У нас есть очень мощные инструменты, позволяющие реализовать эту технологию там, где ее хотят видеть Airbus и другие компании ».
Послужной список OPM, открывающий новые пути, вселяет в компанию уверенность. «Ни у кого не было квалифицированной 3D-печати с использованием PEKK и углеродного волокна для космических кораблей с полным допуском на основе B, - говорит ДеФелис, - и никто другой не разработал имплантаты черепа, позвоночника и ортопедические имплантаты с разрешением FDA, сертифицированной биосовместимостью и производительностью. Мы уверены, что сможем предложить решения из термопластичных композитов ПЭКК для самолетов ».
OXPEKK LTS будет представлен в целях разработки к концу этого года. Продукт поступит в продажу в начале 2019 года.
Смола
- Будущее Live TV
- Будущее за… Индустрия 4.0
- Будущее за… Сотрудничество
- Медицинские имплантаты PEEK
- ПЭЭК высокой вязкости для литья под давлением и экструзии
- Будущие ограничения и закрытия:больше HDPE, больше PCR
- Пойдет ли ИИ на пользу HR в будущем?
- Будущее центров обработки данных
- Энергетическое будущее на месте
- Построение будущего во Флориде