Состояние переработанного углеродного волокна
Случай с переработанным углеродным волокном - сложный. Отрасль строится на надежде на решение проблем, а именно на желании не допускать попадания отходов углеродного волокна на свалки и заполнить потенциальный разрыв между спросом и предложением углеродного волокна. Обычно считается, что около 30% произведенного углеродного волокна попадает в отходы. Между тем, поскольку ценный материал попадает на свалки, большинство аналитиков сходятся во мнении, что годовой спрос на этот материал может превысить текущие годовые производственные мощности в течение следующих нескольких лет. Согласно оценкам, представленным Бреттом Шнайдером, президентом отдела глобальных волокон Hexcel, средний прогнозируемый мировой спрос на углеродное волокно составляет около 65 000-85 000 метрических тонн в год, а мировая производственная мощность (которая превышает фактическую) составляет около 150 000 метрических тонн. (Стэмфорд, Коннектикут, США) и Дэн Пихлер, управляющий директор CarbConsult GmbH (Хофхайм-ам-Таунус, Германия) на конференции по углеродному волокну в декабре 2018 года. По сообщению CW Автор статьи Аманда Джейкоб, в марте некоторые аналитики подсчитали, что к 2022 году спрос на углеродное волокно может превысить предложение примерно на 24 000 метрических тонн (см. «Укрепление доверия к переработанному углеродному волокну»).
И хотя коммерческие поставщики переработанного углеродного волокна (rCF) указывают на переработанный и переработанный материал как на потенциальное решение этого разрыва в спросе и предложении, отрасль rCF имеет свои собственные проблемы. Хотя технология переработки композитов из углеродного волокна существует уже несколько лет и позволяет получать продукт с механическими свойствами, очень близкими к свойствам первичного материала, промышленность по переработке композитов является относительно молодой и все еще находится на ранних стадиях развития рынков для материалов. он производится из вторичного сырья. По мере роста уверенности в качестве волокна, производимого переработчиками, на первый план выходят вопросы о стоимости и доступности. Возможно, самая большая проблема для отрасли - это забота о безопасности цепочки поставок.
«Технологии на самом деле существуют, и они существуют довольно давно, но цепочка поставок еще не проверена», - говорит Эндрю Макси, генеральный директор Vartega (Голден, Колорадо, США). «Без правильных частей, собранных вместе, у вас может быть лучшая технология в мире, но у вас не будет материала, который нужно перерабатывать, и у вас не будет никаких продуктов для его использования».
Коммерческие поставщики часто смотрят на аэрокосмическую промышленность как на источник производственного лома и отработанного материала для использования в качестве вторичного сырья, хотя количество отходов, создаваемых аэрокосмической промышленностью, велико с точки зрения того, что отправляется на свалку, многие производители оригинального оборудования и производители неохотно полагались на него как на стабильный источник поставок для крупносерийной линейки продуктов.
С другой стороны, некоторый прогресс налицо. В декабре 2018 года Boeing объявила, что будет поставлять компании ELG Carbon Fiber Ltd. (Козли, Великобритания) специалисту по переработке углеродного волокна отвержденные и неотвержденные отходы углеродного волокна для вторичной переработки для использования во вторичных продуктах для производства других композитов. Соглашение является первым официальным соглашением о поставках материалов между переработчиком углеродного волокна и крупным OEM-производителем самолетов и, похоже, является хорошим предзнаменованием для отрасли.
Речь идет не только об окружающей среде
Аргумент в пользу использования rCF выходит за рамки устойчивости. Снижение стоимости также является преимуществом. Например, rCF из углеродного волокна ELG стоит примерно на 40% меньше, чем первичное углеродное волокно промышленного качества. Другие коммерческие поставщики заявляют, что их материал на 20-40% дешевле, чем углеродное волокно. Кроме того, для многих приложений необходимы прерывистые форматы волокна, что предполагает возможность, когда rCF может предложить более экологичную и экономичную альтернативу первичному материалу.
«Везде, где промышленность использует прерывистое или рубленое углеродное волокно, переработанное [волокно] должно быть в первую очередь, - говорит Макси. «Мы тратим все эти деньги, чтобы производить первичное углеродное волокно в непрерывном формате… почему мы тогда берем его и измельчаем, чтобы превратить в термопласт? Если у нас уже есть прерывистый формат в этих обрезках, это, на мой взгляд, лучший материал для тех формовочных смесей, которые вы все равно собираетесь нарезать ».
Кроме того, было показано, что качество производимого rCF в некоторых случаях не уступает качеству первичного волокна. ELG Carbon Fiber, которая восстанавливает углеродные волокна с помощью пиролиза, утверждает, что его волокно обычно сохраняет не менее 90% своей прочности на разрыв без изменения модуля. Vartega использует процесс химической переработки и утверждает, что его волокно демонстрирует те же механические свойства, что и первичное углеродное волокно. Компания Shocker Composites (Вичита, Канзас, США) использует поточный процесс сольволиза для восстановления волокна и заявляет о высоком качестве без видимого повреждения волокон.
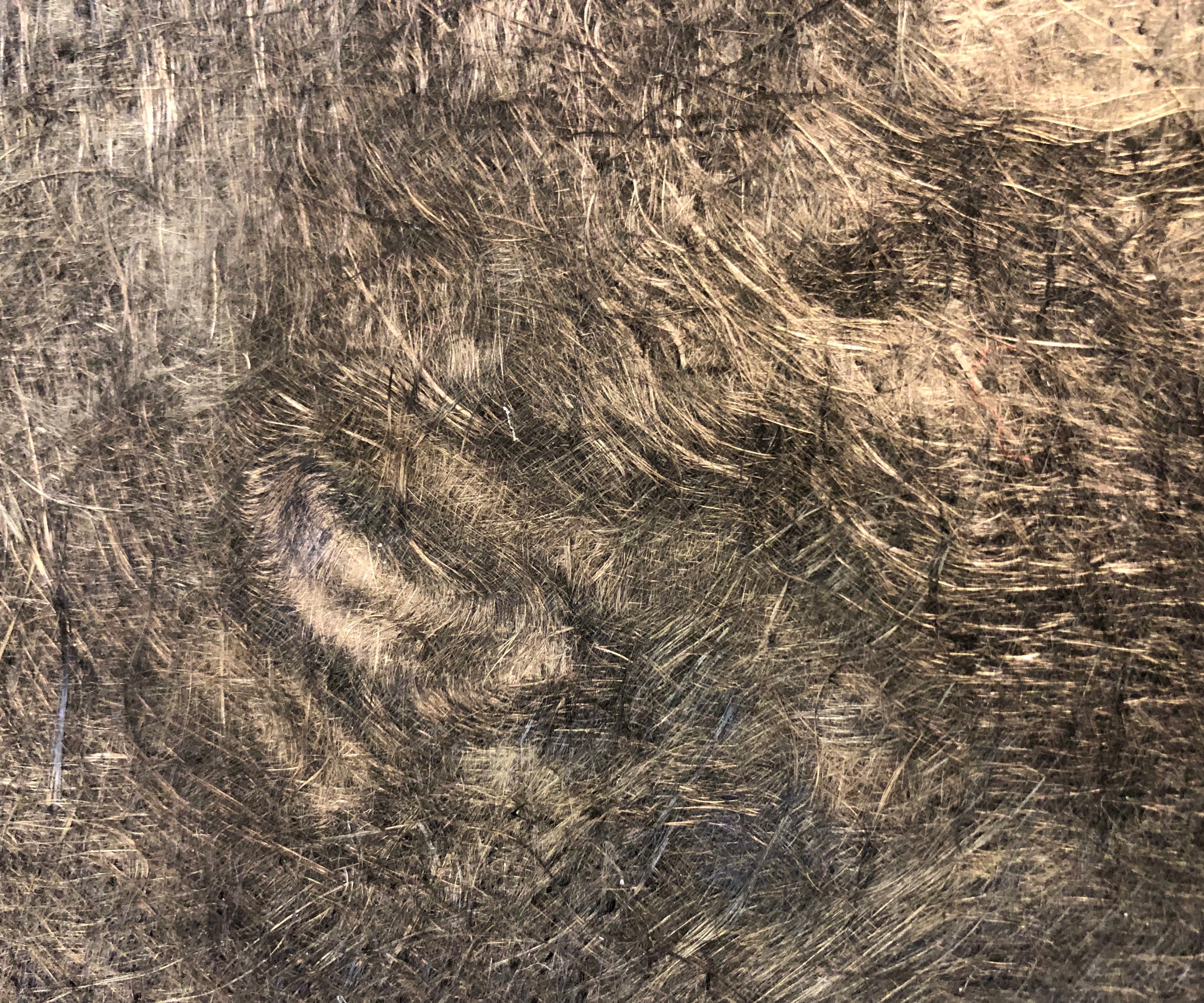
Коврик из нетканого материала из переработанного углеродного волокна от ELG Carbon Fiber.
CW фото | Скотт Фрэнсис
По словам Вамсидхара Патоллы, доктора философии Университета Уичито. Студент и основатель Shocker Composites, задача состоит в том, чтобы снизить стоимость до уровня, сопоставимого с ценами на другие материалы, такие как алюминий. «Технологичность должна соответствовать масштабам крупносерийного производства», - говорит он. Процесс Shocker Composites предлагает это преимущество, потому что это встроенный процесс, а не пакетный процесс. (Подробнее читайте в статье «Экологичная вторичная переработка углеродного волокна».)
Учитывая недавние улучшения за последние несколько лет в переработке rCF и качестве волокна, коммерческие поставщики начали переключать свое внимание с вторичного использования rCF на продукты с более низкими характеристиками и больше на поиск подходящих приложений, которые извлекают выгоду из свойств материала.
«Мы никогда не будем полностью заменять первичное волокно, особенно в аэрокосмической отрасли, где есть высокие требования к прочности и жесткости, но люди приходят к мысли, что переработанное волокно - это не просто переработанное волокно со слабым потенциалом», - говорит Бенджамин Эндрюс, технический специалист. сервисный инженер компании ELG Carbon Fiber. «У него есть свои преимущества, которые превосходят первичное волокно в некоторых областях применения. Драпируемость и качество поверхности лучше, чем у первичного волокна… это не просто материал многоразового использования; у этого материала есть свои преимущества ».
Что там с автомобилем?
Когда дело доходит до рынков, автомобильная промышленность, похоже, обладает наибольшим потенциалом для использования rCF. Благодаря способности материала сочетать легкий вес с хорошей обработкой поверхности, он идеально подходит для кузовных панелей, не говоря уже о различных компонентах интерьера. Коммерческие поставщики rCF долгое время смотрели на отрасль, затаив дыхание, надеясь на широкое распространение, но переломный момент еще не наступил. Время и стоимость обработки продолжают оставаться камнями преткновения для отрасли.
Марк Маухар, генеральный директор Carbon Conversions (Лейк-Сити, Южная Каролина, США), утверждает, что эти опасения являются своего рода оправданием с учетом достигнутого прогресса, и он считает, что главным препятствием для внедрения на любой рынок на самом деле является неприятие риска. .
«Никто не хочет быть первым, кто внедрит новую материальную экосистему», - говорит он. Он также подчеркивает, что широкомасштабное внедрение rCF в автомобильной промышленности не обязательно даже желательно, указывая на то, что принятие использования на дюжине основных автомобильных платформ может быстро поглотить глобальные поставки rCF. По его словам, подход должен заключаться в нацеливании на нишевые программы, что, в свою очередь, сделает цепочку поставок более устойчивой с точки зрения бизнеса.
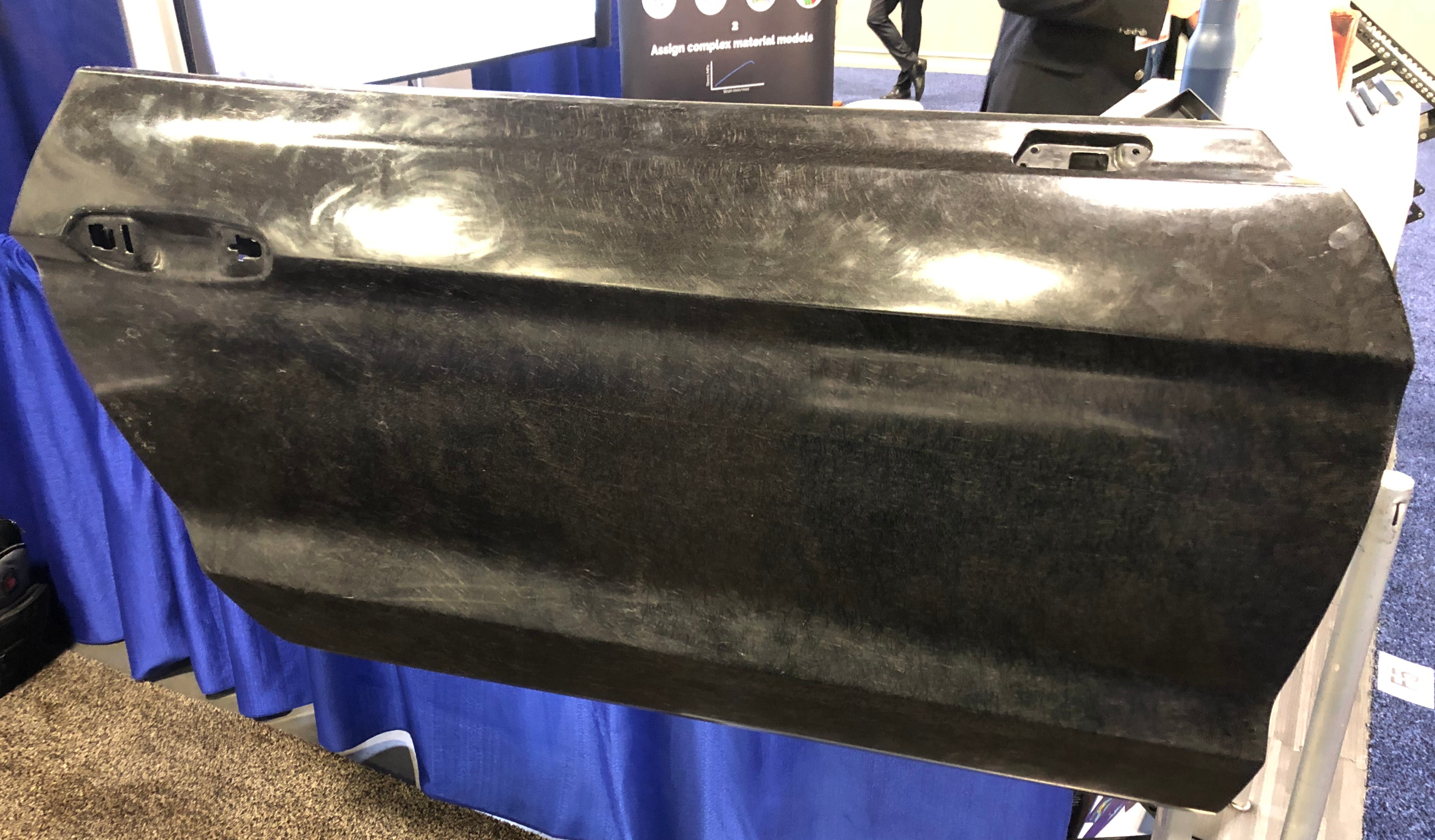
Автомобильная дверная панель из препрега, изготовленного из переработанного Evo MCF компании Carbon Conversions.
CW фото | Скотт Фрэнсис
«Это окупается, если вы будете умно подходить к выбору места в автомобиле», - говорит он. «Выбор конкретных деталей для конкретных моделей автомобилей имеет смысл».
Маухар надеется, что автомобилестроение станет первым крупным рынком, потребляющим приличную долю доступного переработанного углеродного волокна. «В следующие 24 месяца мы начнем видеть там какое-то движение», - прогнозирует он.
Композиты, как правило, постепенно проникают в автомобильную промышленность в виде таких деталей, как аккумуляторные ящики, сосуды под давлением, листовые рессоры и даже системы подъемных ворот. Для rCF имеет смысл следовать по той же траектории.
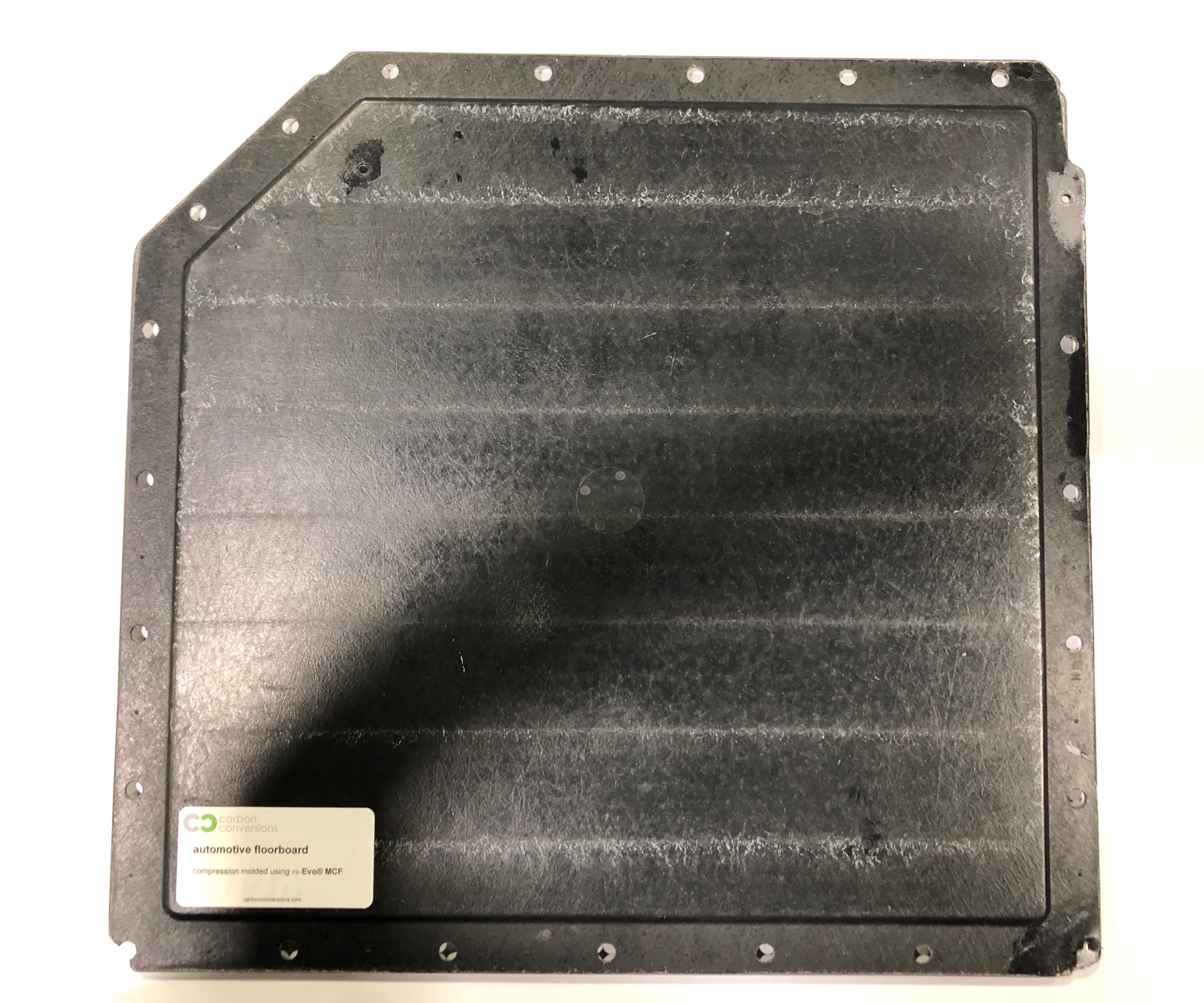
В этой прессованной автомобильной половой доске используется нетканый мат Evo MCF, изготовленный компанией Carbon Conversions.
CW фото | Скотт Фрэнсис
Одним из интересных примеров такого нишевого подхода является компания ProDrive Composites (Милтон-Кейнс, Великобритания), производитель современных легких композитных материалов для различных областей применения - от автомобилей и автоспорта до авиакосмической и оборонной промышленности. Компания сотрудничает с Центром перспективных производственных исследований Университета Шеффилда (AMRC, Шеффилд, Великобритания) и ELG Carbon Fiber над своим процессом P2T (от первичного до третичного), новым процессом, в котором для производства перерабатываемых композитных компонентов используется реактивная термопластичная смола. Пластичный мономер реагирует с катализатором в присутствии переработанных волокон с получением отвержденного ламината на выходе из автоклава.
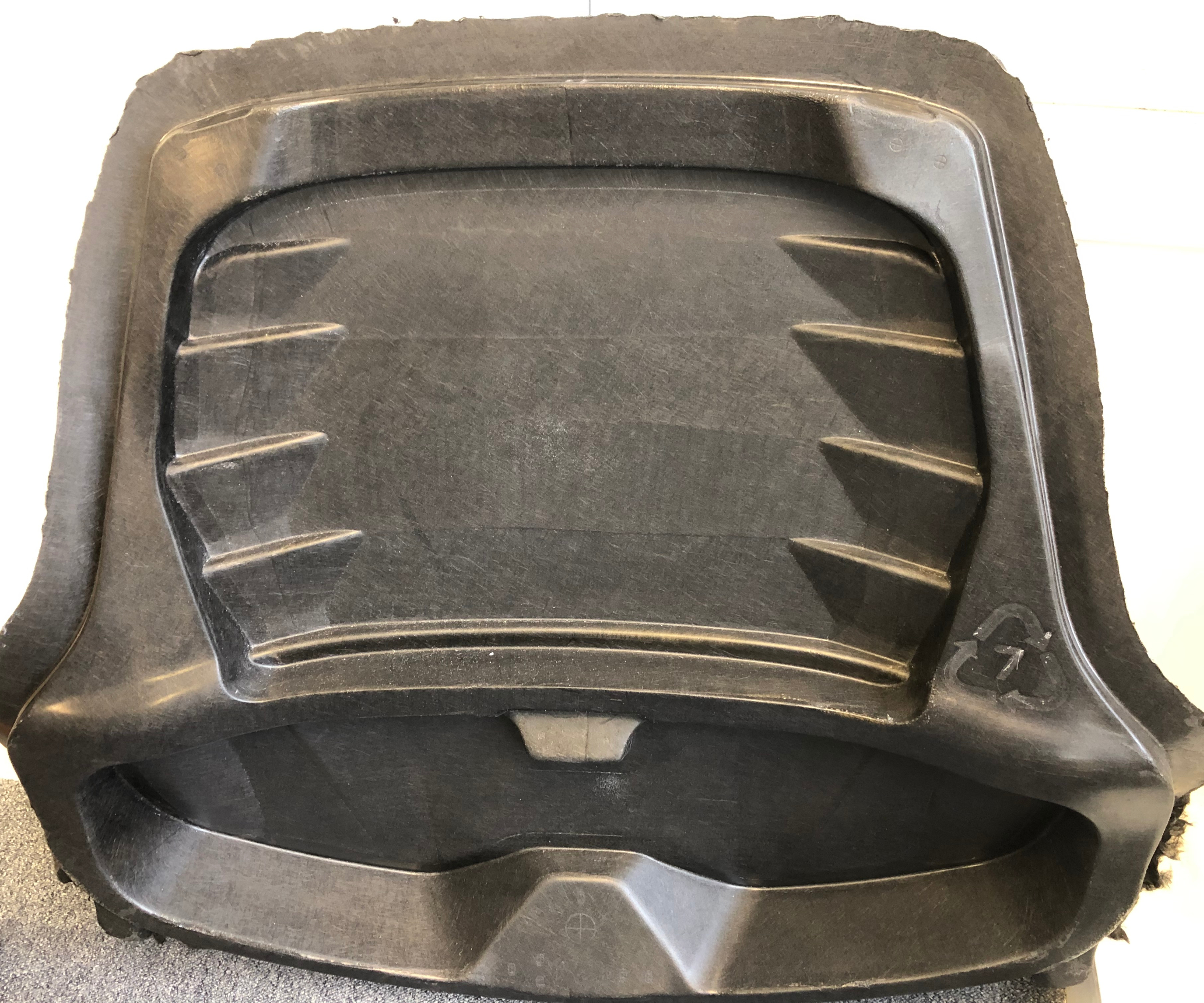
Пример третичной детали, произведенной с использованием процесса P2T ProDrive.
CW фото | Скотт Фрэнсис
«[Мы] продемонстрировали, что перерабатываемые композитные панели могут производиться со скоростью и стоимостью, подходящими для многих отраслей промышленности», - говорит Джон МакКвиллиам, главный инженер ProDrive Composites.
Компания заявляет, что P2T позволяет использовать композитный материал три или более раз. По окончании срока службы первичной детали волокна и, возможно, смола могут быть переработаны, обеспечивая сырьем для вторичной термопластичной детали, такой как панель корпуса. Когда срок службы этой детали истечет, ее можно будет нарезать и превратить в новые части. (Подробнее читайте в статье «Процесс P2T, предназначенный для вторичной переработки».)
Тем временем Вартега возглавляет проект Института инноваций в производстве передовых композитов (IACMI, Ноксвилл, Теннесси, США), ориентированный на автомобильную промышленность. Двухлетнее техническое сотрудничество направлено на решение проблем создания согласованных переработанных термопластов, армированных углеродным волокном, для использования в легковесных транспортных средствах. Макси говорит, что проект продвигается к созданию надежного набора данных, который предлагает полную характеристику материалов, от интерфейса волокна до свойств готовой детали.
Конечно, при рассмотрении автомобильной промышленности лучше всего делать ставку на связанные с ней развивающиеся технологии. Электромобили, автономные транспортные средства и возможности подключения в автомобилях открывают новые возможности для запчастей и приложений, в которых композиты, вероятно, будут играть большую роль.
Макси предлагает свою оценку того, куда движется автомобильная промышленность:«За последние пару лет в автомобильной промышленности многое произошло, и акцент сместится с экономии топлива на другие приоритеты в зависимости от того, какие правила и какие [президентская] администрация говорит », - говорит он. «[Мы] не наблюдаем серьезных откатов в области облегчения веса, но, возможно, мотивация для этого изменится. Я думаю, что в отрасли вы увидите упор на облегчение мобильных приложений ».
Может ли авиастроение замкнуть круг?
В аэрокосмической отрасли образуется больше всего отходов из углеродного волокна, а коммерческие поставщики rCF часто обращаются к аэрокосмической отрасли как к источнику вторичной переработки. Избыточный материал, обычно неотвержденный термореактивный композитный препрег, собирают, а смолу удаляют с помощью тепла (пиролиз) или химического растворителя (сольволиз), чтобы получить волокно, которое измельчается, рубится или гранулируется.
По мере того, как промышленность движется к более широкому использованию термопластичных композитов (ТПК), этот материал открывает новые возможности для вторичной переработки. Поскольку термопластичные полимеры можно переплавлять и изменять форму, у авиакосмической промышленности есть больше возможностей реабсорбировать часть собственного лома для вторичных применений, потенциально повторно используя как волокно, так и матрицу. Томас де Брюйн, научный сотрудник Центра применения термопластичных композитов (TPAC, Энсхеде, Нидерланды) - центра исследований и разработок термопластичных композитов, работающего вместе с Центром исследований термопластов (TPRC, Энсхеде, Нидерланды) на уровне прикладных исследований - указывает на усилия в отрасли производятся для внутренней переработки материала.
«С точки зрения осуществимости, для термопластичных композитов более целесообразно использовать собственный подход», - говорит он.
По словам де Брёйна, производители самолетов с большей вероятностью будут утилизировать внутреннюю переработку, чем обратятся к коммерческому поставщику rCF. Основная причина этого - отслеживаемость. Подбирать типы полимеров для конкретного применения становится намного сложнее, когда запасы материала перемещаются из дома.
Йохан Меузелаар, специалист по инженерным нагрузкам в GKN Fokker (Хоогевен, Нидерланды), считает, что ответ - попытаться найти как можно больше приложений в вашей собственной производственной среде. «Если я посмотрю на тип термопластичных компонентов, которые мы производим из первичного материала, в них есть много деталей, которые мы могли бы переработать», - говорит он. «[Мы] определенно могли бы использовать значительное количество отходов, которые мы производим».
«У нас уже есть оборудование», - добавляет Гийом Винсент, инженер по термопластическим композитам TPRC. Он объясняет, что внутренняя переработка вписывается в обычные технологические цепочки и что большая часть оборудования уже установлена, что делает ее наиболее доступным способом. «[Это] вписывается в нашу деятельность в нормальной производственной среде».
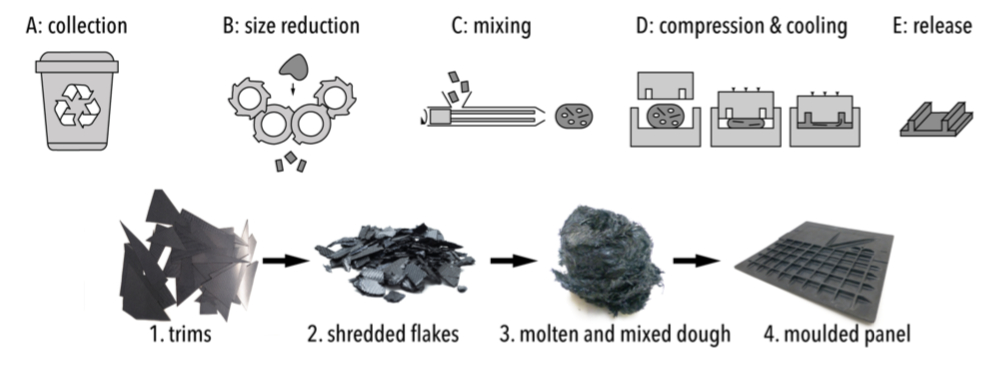
Источник | TPRC, TPAC
Де Брёйн, Винсент и Меузелаар участвуют в проекте TPC-Cycle, которым управляют TPAC и TPRC. Проект направлен на повторное использование отходов производства термопластичных композитов для аэрокосмической и крупносерийной промышленности. Цель состоит в том, чтобы сохранить высокие механические свойства термопластичных композитов и снизить общее воздействие на окружающую среду при доступной цене. TPC-Cycle имеет короткое время цикла и, как говорят, позволяет изготавливать изделия сложной формы.
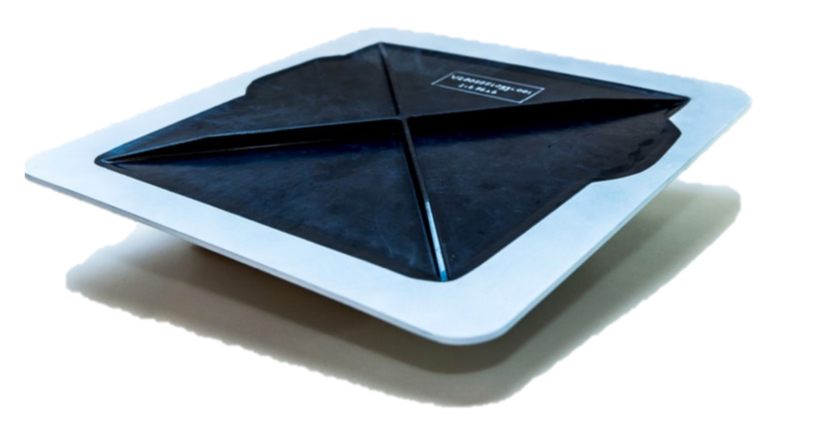
Демонстрационная панель доступа для винтокрылых аппаратов, разработанная с использованием процесса TPC-Cycle.
Источник | TPRC, TPAC, GKN Fokker
Несколько промышленных партнеров, включая GKN Fokker, Toray Advanced Composites (Морган Хилл, Калифорния, США; Нейвердал, Нидерланды), Cato Composite Innovations (Реден, Нидерланды), Dutch Thermoplastic Components (Алмере, Нидерланды) и Nido RecyclingTechniek (Нейвердал, Нидерланды) , участвуют в проекте TPC-Cycle, представляя различные сегменты цепочки создания стоимости от материалов, производства, дизайна и применения.
По словам де Брейна, в настоящее время в рамках проекта TPC-Cycle изучается возможность завершения анализа затрат и анализа жизненного цикла, чтобы доказать, что этот процесс является экономически выгодным.
Кроме того, такие программы, как совместное предприятие Clean Sky 2 (которое финансируется программой ЕС Horizon 2020) поощряют НИОКР, которые направлены на то, чтобы замкнуть цикл для аэрокосмического лома. Производители оригинального оборудования рассматривают возможность использования переработанных заводских отходов для изготовления деталей интерьера, съемных панелей, небольших компонентов и даже зажимов планера и системных кронштейнов.
Д-р Бас Вельдман, менеджер программы GKN Fokker по нижней части термопластичного многофункционального демонстратора фюзеляжа, поддерживает эту концепцию, объявив конкурс предложений по программе Clean Sky 2 на зажимы и кронштейны. Важным элементом при разработке демонстратора является снижение воздействия на окружающую среду за счет использования заводских отходов для таких продуктов, как зажимы для рам и кронштейны. Демонстрация также призвана заменить крепежи сваркой, тем самым сэкономив материалы, энергию и деньги, а также уменьшив вес.
По словам Меузелаара, GKN Fokker изучает, как технология переработки может стать частью концепции будущего предприятия. Он говорит, что в концепции потенциально будет использоваться много термопластичных композитов, которые, в свою очередь, могут привести к образованию большого количества отходов, которые можно будет использовать для переработанных кронштейнов, фитингов и неструктурных деталей.
«Причина, по которой стоит обратить внимание на фюзеляж из термопласта, - это стоимость, и мы думаем, что это экономичный метод производства, который также включает переработку», - говорит он.
Меузелаар говорит, что цель на высоком уровне состоит в том, чтобы делать более доступные и экологически безопасные продукты в аэрокосмической отрасли. Хотя предпринимаются шаги в направлении серийного производства термопластов, это также приведет к отходам (как, к сожалению, в случае композитов в целом). Но он считает, что отходы могут быть коммерчески жизнеспособными, и говорит, что смешивание / компрессионное формование с низким усилием сдвига TPC из переработанного углеродного волокна предлагает свободу дизайна, которой не дает традиционное ламинирование непрерывными волокнами. «Вы получаете множество дополнительных опций для изготовления очень интересных неструктурных деталей, таких как панели, небольшие обтекатели или системные кронштейны, которые обычно в аэрокосмической отрасли имеют тенденцию быть чрезмерно сконструированными с точки зрения используемых материалов, используемых сплавов [и] используемых производственных систем», он объясняет.
Он считает, что возможность заключается в основном в неструктурных деталях среднего размера и средней сложности, которые по-прежнему составляют значительную часть общей стоимости более крупных компонентов.
«В ближайшем будущем мы не будем делать крылья из переработанного термопласта», - говорит Меузелаар. «Но внутри крыла есть детали, которые имеют экономический смысл».
Все это говорит о том, что еще очень далеко предсказать влияние термопластичных композитов на отрасль вторичной переработки.
«Процент отходов снизится, вероятно, из-за новых методов производства, таких как укладка ленты или специально подобранные заготовки, которые, вероятно, производят меньше отходов, чем текущие типичные процессы раскроя и штамповки, которые мы наблюдаем», - говорит де Брюйн. «Но в целом я думаю, что будут больше термопластичных отходов в ближайшие годы и десятилетия ».
И хотя интерес к переработке собственными силами растет, всегда будут оставаться отходы, которые нельзя использовать, и производители не захотят или не смогут перерабатывать их самостоятельно. В таких случаях эти материалы могут быть возвращены поставщиком материалов. Время покажет, что более широкое использование термопластичных композитов может означать для цепочки поставок. (Узнайте больше о проекте TPC-Cycle и инициативе Clean Sky 2 в разделе «Переработанные термопластичные композиты для производства».)
Аддитивное производство
Аддитивное производство - еще одна область, в которой есть потенциал для rCF. Например, компания Shocker Composites объединила свое переработанное углеродное волокно в армированную на 20-40% нить из АБС-пластика и продемонстрировала свое успешное использование в процессе 3D-печати Big Area Additive Manufacturing (BAAM) компании Cincinnati Inc. (Харрисон, Огайо, США).
Кроме того, Vartega заявляет, что использует свою технологию рециркуляции углеродного волокна и опыт разработки материалов, чтобы продвигать полимерное сырье для производства добавок для плавления порошковых материалов. Компания недавно получила грант Национального научного фонда (NSF, Александрия, Вирджиния, США) на исследования в области инноваций малого бизнеса (SBIR) на проведение исследований и разработок (НИОКР) в этой области.
Вартега утверждает, что также разрабатывает процесс, который позволит армировать термопластические порошки углеродным волокном, обеспечивая при этом создание функциональных деталей в инфракрасных аддитивных системах. Сообщается, что этот прогресс позволит производителям цифровых технологий реализовать весь потенциал новых аппаратных платформ на основе порошка для производства деталей, которые по своим характеристикам аналогичны материалам, полученным литьем под давлением, при средних объемах производства.
«Предлагая полимерные порошки, армированные углеродным волокном, производители в таких секторах, как БПЛА [беспилотные летательные аппараты] и медицинские протезы, осознают преимущества быстрой, сложной и индивидуальной 3D-печати, гарантируя при этом, что выбранный ими материал будет демонстрировать структурную целостность, необходимую для их продукт », - говорит Элис Хэвилл, главный операционный директор Vartega.
Другие приложения
Между тем, продолжают появляться другие рынки и области применения, в которых переработанное углеродное волокно может сыграть свою роль.
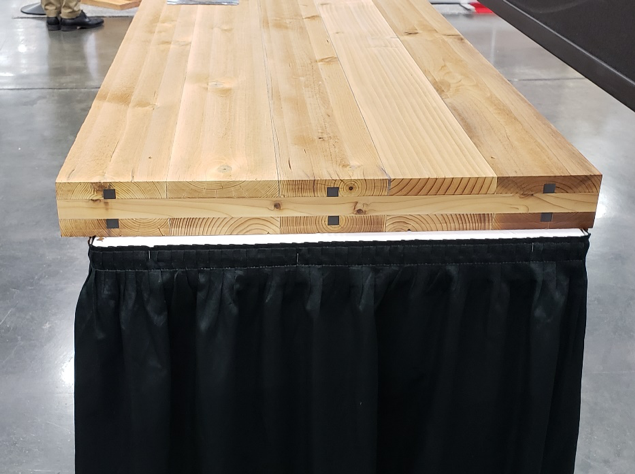
Этот строительный кросс-клееный брус (CLT) сочетает в себе термически модифицированный пиломатериал с переработанным углеродным волокном, полученным в Центре технологий вторичной переработки композитов.
Источник | Центр технологий вторичной переработки композитов
The Composite Recycling Technology Center (CRTC, Port Angels, Wash., U.S.) has been exploring use of recycled carbon fiber in a variety of products, from park benches to high-performance sporting goods to composite tubing. The company works with reclaimed uncured prepreg material from Toray Composite Materials America (Tacoma, Wash., U.S.) as well as rCF from ELG Carbon Fibre.
Dave Walter, CEO of the CRTC, points to the construction industry as an area of potential growth. The company recently developed a construction grade cross-laminated timber (CLT) under a patent-pending process that combines thermally modified lumber with recycled carbon fiber. The thermal modification process cooks off the sugars and lignin, providing rot and termite resistance, and then carbon fiber strips are integrated for strength.
The CRTC also uses recycled carbon fiber to create panels bonded with wood veneer. These panels showcase the beauty of wood with a strong, light and flexible substrate for various interior and exterior applications, as shown in the picture below from a 2019 installation at the Benaroya Hall in Seattle.
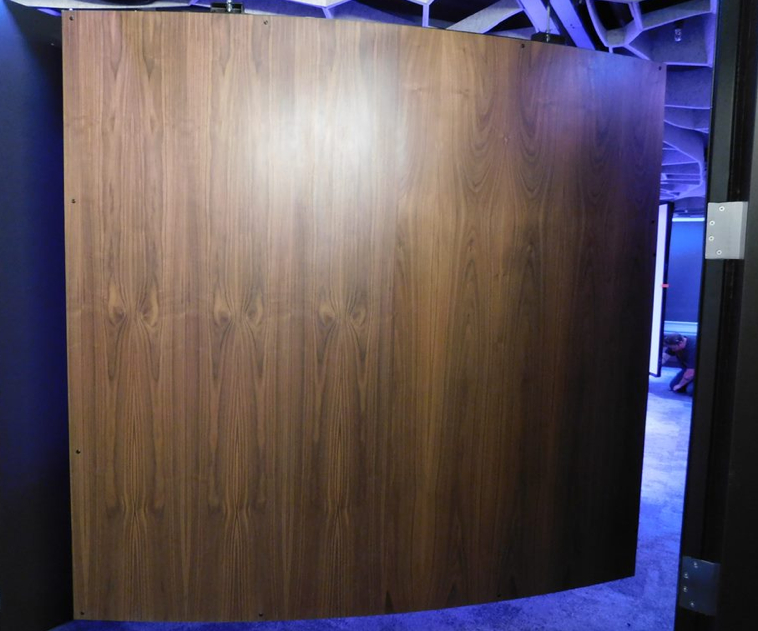
Octave 9 Raisbeck Music Center – Benaroya Hall (Seattle, Wash., U.S.)
Photo | The Composite Recycling Technology Center
A mind change for the industry?
Big changes often happen incrementally, and the relatively young recycled carbon fiber industry continues to slowly push forward. While downcycling of rCF continues, perceptions about the material are beginning to change. Quality of fiber has been proven and processes continue to evolve. Awareness of the necessity to recycle carbon fiber is high and more players are getting involved.
“The ELG and Boeing announcement was a really big deal; it helps everyone move the ball forward [and] to accelerate the supply chain connections,” says Maxey.
“We’re here to enable and connect the dots,” he adds, summing up the industry. “We have this enabling technology that sits in the middle of the supply chain, but its really about connecting that stranded asset in the waste stream to an unmet demand downstream.”
The biggest change, according to Mark Mauhar of Carbon Conversions, is that suppliers now want to be part of the solution. “Prior to two years ago we’d get multiple calls a week from suppliers about getting rid of scrap, but no interest in using the material,” he says. “Now, people are starting to walk the walk. Only recently, we are finally starting to see potential customers of reclaimed carbon fiber spend significant resources in cutting molding tools, building prototypes and mock-ups, solving process issues — all activities that are well down the line in terms of commercial adoption.”
Perhaps what it really boils down to is patience. Detlef Drafz, CEO at ELG Carbon Fibre, points out that it’s helpful to examine the recycling history for other legacy materials.
“For over 50 years, ELG has recycled raw materials for the stainless steel industry. With metal, it’s accepted that you use the scrap even in vacuum furnaces for turbine blades … it’s accepted that recycled metal is a raw material, which properly processed can just be used. That wasn’t common in the aerospace application 25 years ago; however, we established a supply chain in order to give the guarantees that the material performs. We do the same here,” he says.
Смола
- Углеродное волокно
- Как в медицинской промышленности используется углеродное волокно
- Преимущества углеродного волокна в аэрокосмической промышленности
- Стекловолокно и углеродное волокно:в чем разница?
- Пять основных видов использования углеродного волокна в спорте
- Стоимость углеродного волокна:почему качество того стоит
- Самые продаваемые преимущества багажа из углеродного волокна
- Инновации из углеродного волокна в медицинской промышленности
- Можно ли переработать углеродное волокно?
- Представляем первый в мире смартфон из углеродного волокна