Автоматическое соединение гибридных металло-термопластичных композитных конструкций
Включение гибридного присоединения в промышленных масштабах
FlexHyJoin демонстрирует процесс массового производства термопластичного композитного элемента жесткости крыши со сварными металлическими кронштейнами для сборки в металлический корпус в белом цвете, как в случае использования проекта Fiat Panda городской автомобиль. Источник | IVW
Гибридные металлокомпозитные конструкции по-прежнему представляют интерес для автомобильной и аэрокосмической промышленности, предлагая уменьшенный вес и улучшенные характеристики за счет размещения «нужного материала в нужном месте». Термопластические композиты (ТПК) привлекательны для таких многоматериальных структур из-за их быстрой обработки, включая возможность сварки и термоформования. Однако до сих пор для соединения композитов с металлами в основном использовались механические крепежные детали, которые требовали сверления отверстий, повреждающих несущие волокна. Также использовалось клеевое соединение, но некоторые термопласты трудно соединить таким образом; Кроме того, клеи добавляют материал и вес. Например, BMW i3 , в котором используется шасси из армированного углеродным волокном пластика (CFRP) и пластиковые панели кузова, используется 16 кг клея, что частично снижает потенциал композитных материалов по снижению веса.
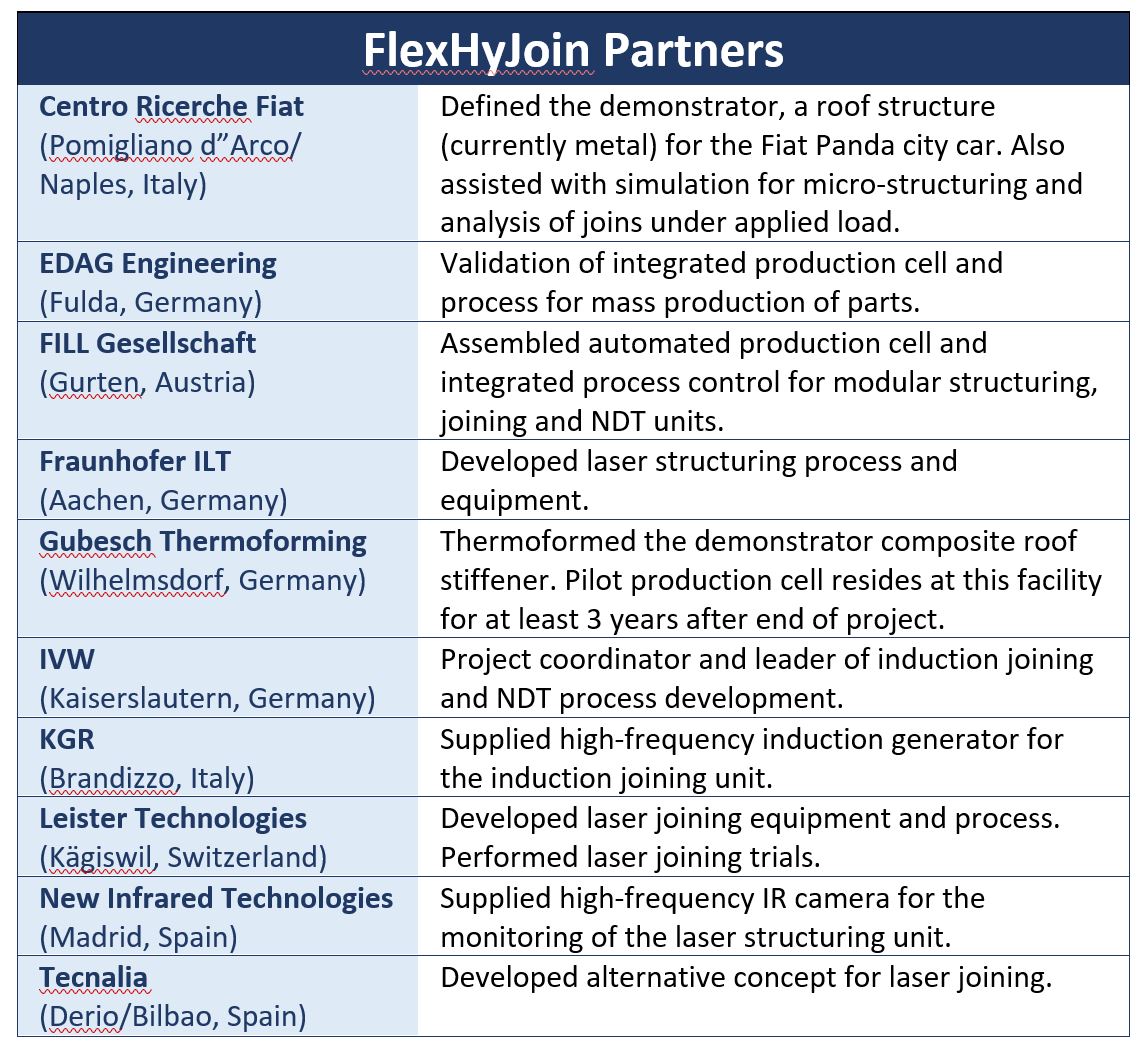
FlexHyJoin - это проект, финансируемый программой исследований и инноваций Европейского Союза Horizon 2020, проводимой с октября 2015 года по декабрь 2018 года и направленной на решение проблем, связанных с соединением TPC и металлических деталей. При координации со стороны Institut für Verbundwerkstoffe (IVW) - некоммерческого исследовательского учреждения земли Рейнланд-Пфальц и Технического университета Кайзерслаутерна, Германия - FlexHyJoin объединила 10 партнеров со всей Европы для разработки автоматизированного процесса, позволяющего создавать автомобильную крышу TPC. конструкция должна быть собрана в металлический корпус в белом цвете (BIW). Стратегия заключалась в создании высокопрочного соединения с нейтральным весом - без клея и креплений - путем предварительной обработки металлических кронштейнов лазером и их прикрепления к ребру жесткости кровли с помощью индукционного и лазерного соединения. Это было достигнуто в единой автоматизированной производственной ячейке со встроенным контролем процесса и встроенным неразрушающим контролем (NDT).
Гибридный демонстратор за 140 секунд
Партнер проекта Centro Ricerche Fiat (Помильяно д'Арко / Неаполь, Италия) предоставил спецификации для демонстрационной части - элемента жесткости крыши для Fiat Panda городской автомобиль, который на данный момент изготавливается из стали. Для FlexHyJoin деталь была термоформована из термопластичного композита (рис. 1) в компании Gubesch Thermoforming (Вильгельмсдорф, Германия) с использованием тканого органоида Tepex Dynalite 102 из стекловолокна / полиамида 6 (PA6) толщиной 1,5 миллиметра, поставляемого Bond-Laminates (Brilon, Германия). Чтобы присоединить этот элемент жесткости крыши TPC к Panda Стальной BIW, набор боковых скоб (левый и правый), изготовленных из стали DC04 толщиной 0,7 миллиметра, были присоединены к концам лазером. Центральный кронштейн, сделанный из того же материала, был прикреплен с помощью индукционного соединения. FlexHyJoin показал, что оба метода соединения могут использоваться для производства промышленных гибридных конструкций.
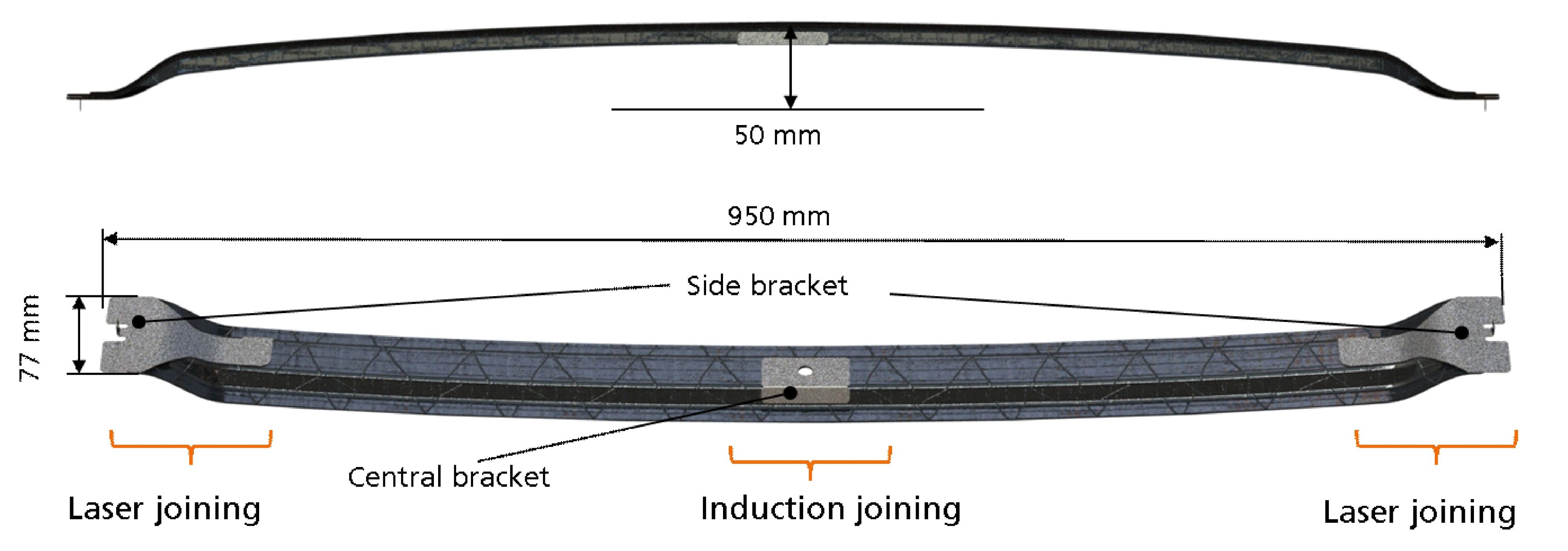
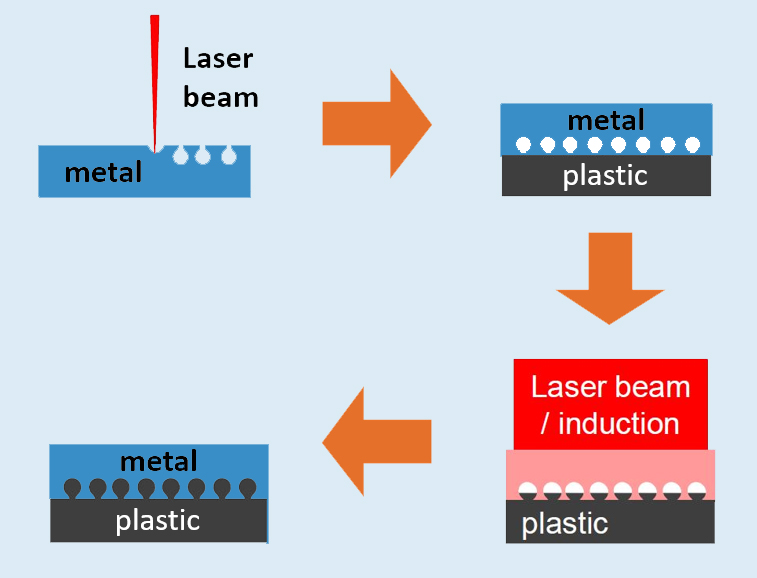
Рис. 1 Структурирование поверхности для гибридного соединения
FlexHyJoin демонстрирует лазерное и индукционное соединение стальных кронштейнов с штампованным элементом жесткости крыши из GF / PA6 ( вверх ). Эти гибридные соединения основаны на обработке поверхности металлических скоб для создания поднутрений, которые заполняются расплавленным пластиком на этапах процесса соединения ( снизу ).
Источник | IVW
Простое расплавление матрицы PA6 на стальные кронштейны не приведет к образованию соединения, обладающего достаточной прочностью, чтобы соответствовать требованиям конструкции. Таким образом, перед сваркой требовалась лазерная обработка поверхности. «Поверхность кронштейнов была структурирована с помощью лазера для создания поднутрений», - объясняет Йоханнес Фойтофер, руководитель проекта в Fill Gesellschaft (Гуртен, Австрия), которому было поручено собрать и интегрировать автоматизированную производственную ячейку. «Обработанные брекеты накладываются на композитную деталь. Затем во время соединения прикладываются тепло и давление, в результате чего матрица PA6 из композита перетекает в индуцированные лазером поднутрения [см. Рис. 1] ». Процесс структурирования был разработан еще одним партнером, Институтом лазерных технологий Фраунгофера (ILT, Ахен, Германия), и в результате получилось соединение металл-композит, сочетающее в себе адгезию материала и механическую фиксацию.
Затем соединенные детали переносятся на станцию неразрушающего контроля, где они сканируются на предмет дефектов с помощью термографии. «Галогенные прожекторы используются для модулированного нагрева композитной поверхности», - объясняет Виталий Попов, научный сотрудник IVW и руководитель разработки FlexHyJoin NDT и управления технологическим процессом. «Это приводит к колебаниям температурного поля внутри композитной конструкции. Мы анализируем тепловую реакцию поверхности с течением времени и выявляем дефекты в стыках ». Полностью автоматизированное тестирование каждого изготовленного компонента проводится в производственной ячейке. Проверка процесса проводилась примерно на 400 стыках.
Автоматизированная производственная ячейка FlexHyJoin, в текущей конфигурации, выполняет лазерное структурирование, соединение и неразрушающий контроль параллельно с длительностью цикла 81, 98-108 и 100 секунд соответственно, не включая время на роботизированную передачу деталей между станциями. Voithofer говорит, что время цикла на готовую гибридную деталь составляет примерно 140 секунд.
Рис. 2 Обеспечение гибридного объединения в промышленных масштабах
Пилотная производственная ячейка FlexHyJoin оснащена тремя модульными станциями для структурирования поверхности, соединения и неразрушающего контроля. Робот-манипулятор ячейки переносит компоненты из загрузочного ящика на каждую из этих станций, помещая готовые гибридные детали в соседний ящик. Источник | IVW и заливка
Лазерное структурирование
В процессе лазерного структурирования создаются линии с геометрией поднутрения на соединительной поверхности металлических скоб. Для FlexHyJoin поднутрения составляли 75 микрометров в ширину и 215 микрометров в глубину. Эти измерения, а также количество линий и общий рисунок линий могут быть адаптированы и, в идеале, согласованы с требованиями по времени выполнения части и цикла.
«Положение, а также количество микроструктур на соединяемой поверхности можно адаптировать к нагрузке в компоненте», - объясняет Стефан Вайдманн, научный сотрудник IVW и руководитель группы разработчиков индукционного соединительного устройства FlexHyJoin. «Расстояние между микроструктурами может быть уменьшено в высоконагруженных областях соединяемой поверхности и увеличено в менее нагруженных областях, чтобы обеспечить эффективный процесс микроструктурирования».
Структурирование достигается путем абляции поверхности металлического кронштейна с помощью мощного одномодового волоконного лазера, поставляемого IPG Photonics (Бурбах, Германия). Этот лазер YLR-1000-WC имеет максимальную мощность 1000 Вт при длине волны излучения 1070 нанометров. «Мы использовали одномодовый волоконный лазер для процесса микроструктурирования из-за его высокой фокусируемости, поддерживающей размер пятна примерно 40 микрометров», - объясняет Кристоф Энгельманн, руководитель группы по обработке полимеров в Fraunhofer ILT.
Лазер находится в оптической головке, установленной на манипуляторе ABB 1200. «Внутри оптической головки у нас есть два гальванометрических зеркала для отклонения луча в рабочем поле размером 240 на 240 мм», - поясняет Энгельманн. «Кроме того, есть одна подвижная линза для отслеживания высоты по оси Z (сдвиг по оси Z). Мы использовали робот только для того, чтобы расположить сканирующую головку над металлическими компонентами, а затем луч отклоняется зеркалами, и положение по оси Z для каждой отдельной линии микроструктуры адаптируется с помощью устройства сдвига по оси Z. Таким образом, во время обработки голова не движется. Таким образом, мы можем обрабатывать детали 2,5D, оставаясь в одном и том же положении по оси z для каждой отдельной линии, но имея возможность регулировать между линиями ».
«По соображениям безопасности блоки структурирования и соединения закрыты», - поясняет Фойтхофер, обращая внимание на черные шкафы в экспериментальной производственной ячейке (рис. 2). Таким образом, автоматические ворота / двери остаются опущенными во время лазерных операций, открываясь для удаления готовых деталей и установки новых.
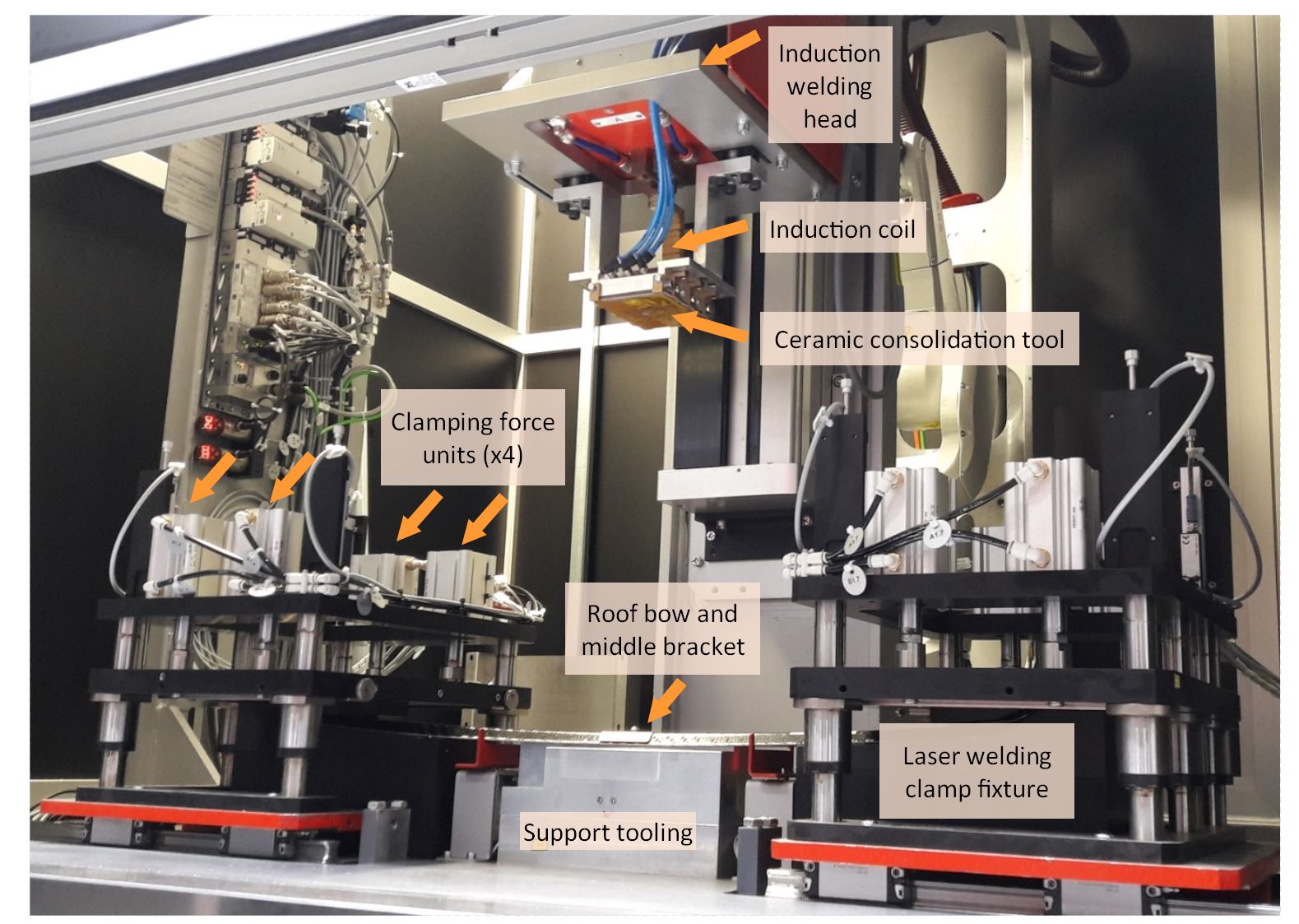
Рис. 3 Индукционная и лазерная сварочная ячейка
В соединительной ячейке индукционное соединение используется для прикрепления среднего кронштейна, в то время как лазерное соединение используется для соединения боковых кронштейнов на каждом конце композитной дуги крыши. Источник | IVW и заливка
Индукционная и лазерная сварка
К ячейке структурирования примыкает ячейка соединения, которая включает две отдельные операции:индукционное соединение центральной скобы и лазерное соединение левой и правой боковых скоб. «Для больших деталей средней сложности, таких как центральный кронштейн, индукционное соединение является более подходящим методом соединения», - говорит Вайдманн. «Инструмент для упрочнения керамики с индуктором оказывает давление на область соединения и проницаем для электромагнитного поля, что приводит к эффективному подаче энергии в металлический кронштейн для нагрева. Это удобно для плоских форм, но более сложно для сложных форм, таких как геометрия боковых скоб. Таким образом, для них было более эффективно использовать лазерное соединение ». Вайдманн добавляет:«Индукционная сварка лучше всего подходит для больших деталей средней сложности, тогда как лазерная сварка больше подходит для деталей высокой сложности».
Просверленное отверстие в композитном элементе жесткости крыши совмещает его с опорными приспособлениями, форма которого соответствует кривизне термоформованного элемента жесткости. Вырезанное лазером отверстие в центральном кронштейне позволяет разместить его на элементе жесткости крыши, а боковые кронштейны выровнены по форме, соответствующей концам элемента жесткости крыши.
«Центральная скоба была соединена с помощью прерывистой индукционная стыковка. «Это, по сути, квазистатическое соединение прессованием, - говорит Вайдманн, - что просто означает, что это статический процесс, обеспечивающий площадное соединение в одном месте, но есть движение в направлении оси z, потому что толщина композита слегка изменяется из-за к давлению уплотнения, приложенному во время (индукционного) соединения ».
Блок индукционного соединения содержит высокочастотный генератор KGR (Brandizzo, Италия) для подачи переменного электрического поля на индукционную катушку. Головка перемещается с помощью электродвигателя и шпинделя (рис. 3), так что инструмент для упрочнения керамики прижимается к металлическому кронштейну. Индукционная катушка в инструменте уплотнения нагревает металл, в результате чего композитная матрица плавится и образуется соединение. «Давление применяется при нагревании и охлаждении», - отмечает Вайдманн.
Лазерная сварка боковых скоб начинается одновременно с индукционной сваркой. Два зажимных устройства, расположенные по обе стороны от опорного инструмента, могут прикладывать зажимное усилие в 4000 Ньютонов к боковым кронштейнам. «Зажим необходим для минимизации зазора между композитными и металлическими компонентами», - поясняет Фойтхофер. «Это предотвращает образование пустот в стыке». После приложения усилия зажима лазерная головка перемещается в нужное положение. Он оснащен диодным лазером LineBeam, поставляемым Leister Technologies (Кегисвиль, Швейцария). Йоханнес Экштадт из Leister объясняет, что максимальная выходная мощность этого лазера составляет 600 Вт при длине волны излучения 980 нанометров. Луч формируется оптическими линзами по линии 27 мм на 1 мм и фокусируется на металлическом кронштейне. Лазерная головка установлена на манипуляторе робота, что позволяет ей перемещаться по фигурной поверхности кронштейна. «Мы устанавливаем разные скорости для каждой области кронштейнов, чтобы достичь однородной температуры соединения и снизить термическое напряжение для достижения наилучших результатов соединения», - говорит Экштадт.
Как правило, для лазерного соединения можно использовать соединение с пропусканием или теплопроводностью. Для соединения с лазерным пропусканием соединяемый композит должен быть прозрачным для выбранной длины волны лазера. Затем лазер проходит через композит, ударяется о металлическую поверхность кронштейна и нагревает ее. Однако этот метод не использовался в демонстраторе FlexHyJoin, поскольку многослойный органолист элемента жесткости крыши не был прозрачным для лазера. Вместо этого был использован альтернативный метод теплопроводного соединения. Это просто применяет лазер непосредственно к металлической поверхности, которая проводит тепло через металлический основной материал к композиту, расплавляя матрицу PA6 при 220-300ºC и создавая соединение. «Благодаря высокой теплопроводности стальных кронштейнов тепловое излучение лазера быстро распространяется, эффективно соединяя боковые кронштейны», - говорит Фойтофер.
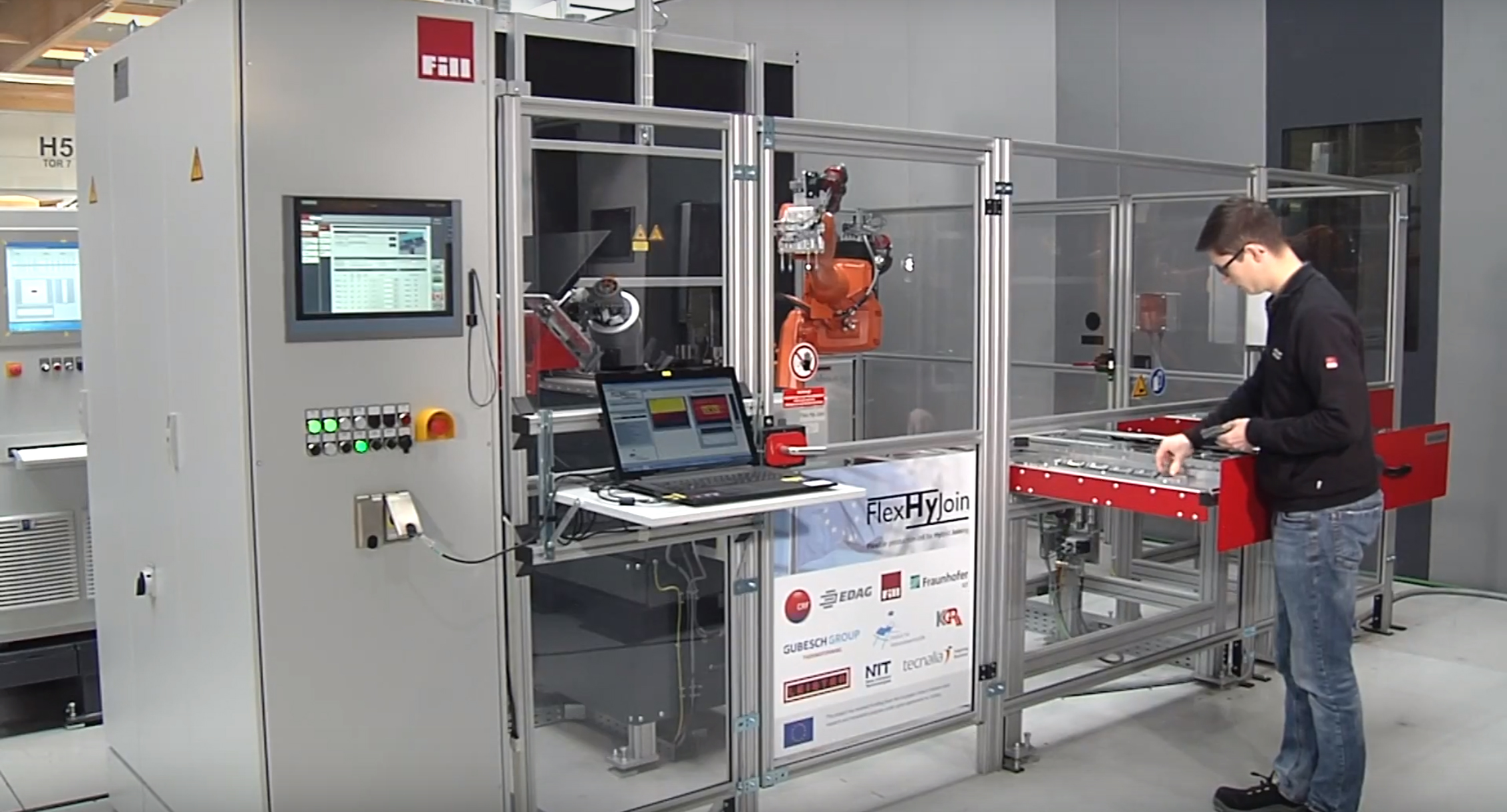
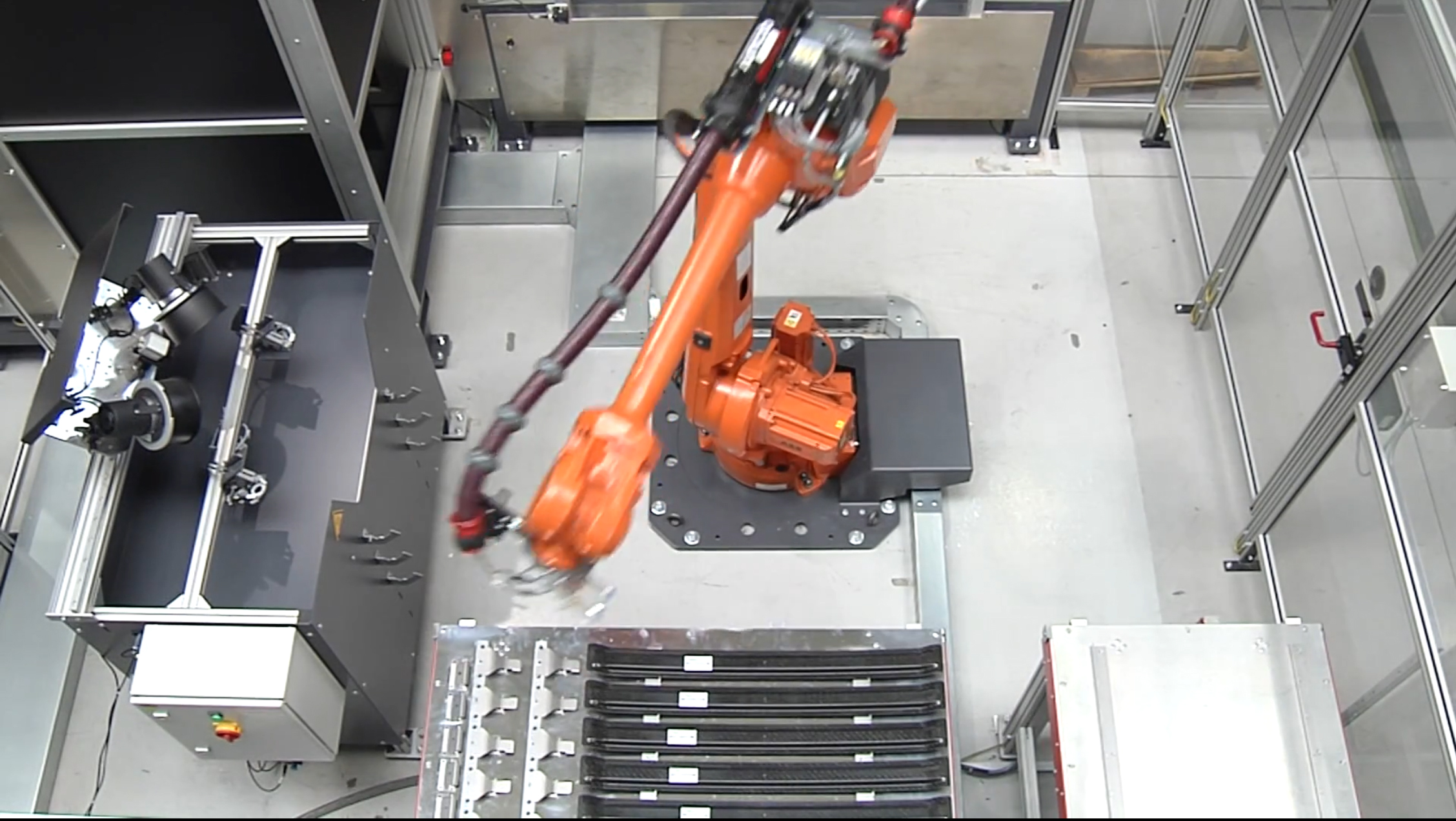
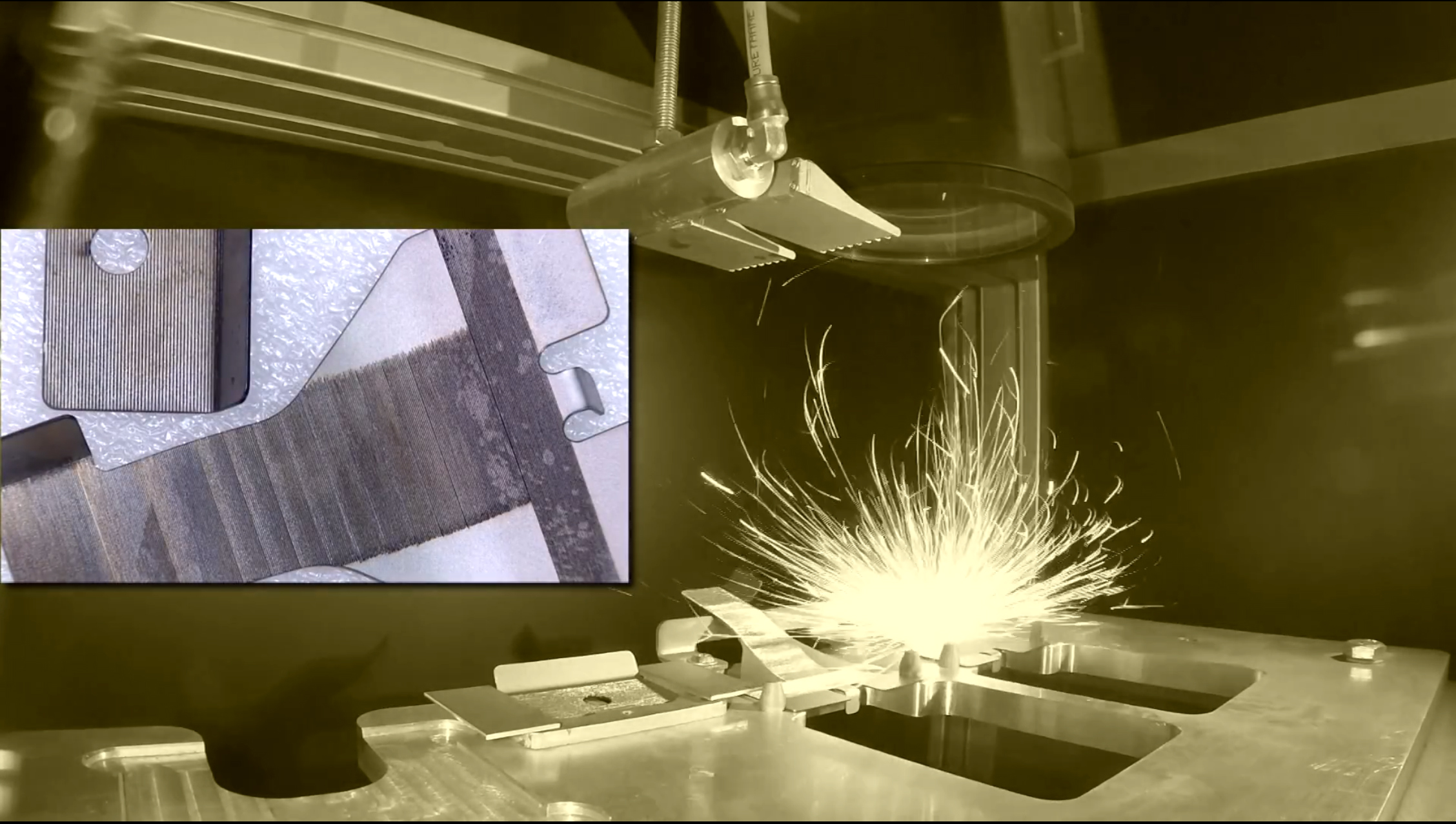
Шаг 3. Внутри структурирующей ячейки мощный волоконный лазер создает поднутрения на поверхности кронштейна, который необходимо соединить в композитном элементе жесткости крыши.
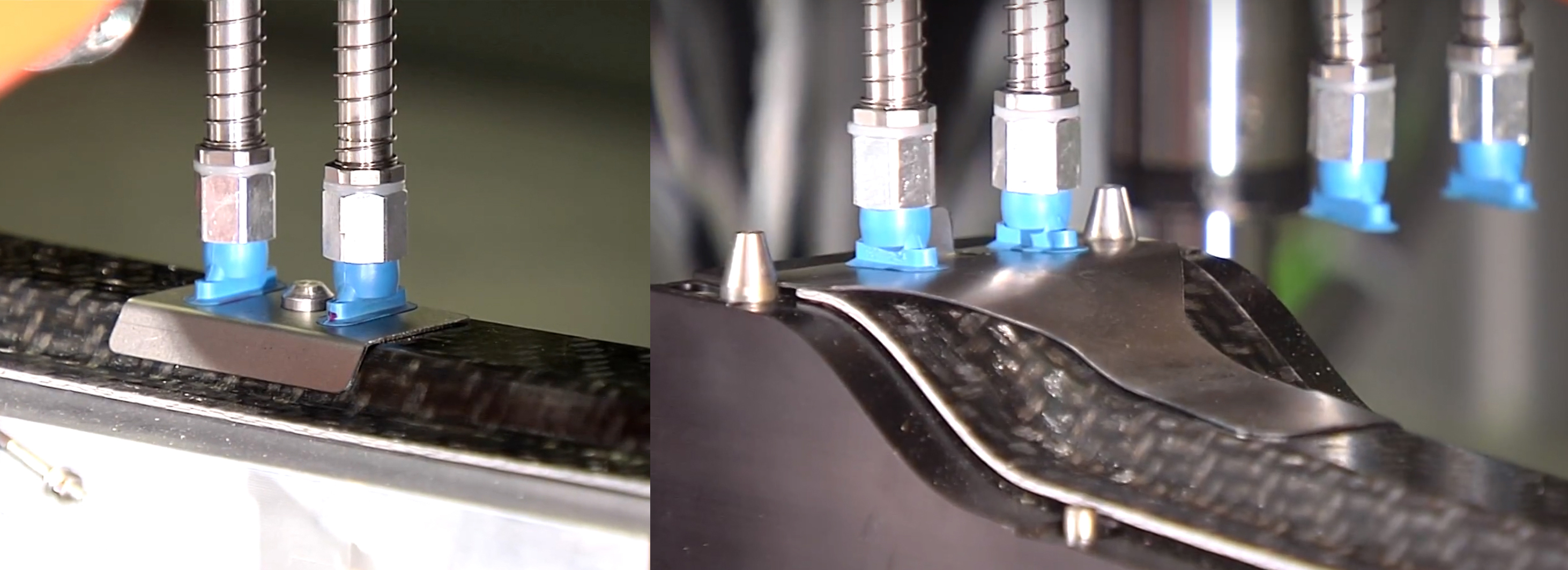
Шаг 5. Робот возвращается в ячейку структурирования, берет обработанные кронштейны и помещает их структурированной стороной вниз на изгиб крыши TPC.
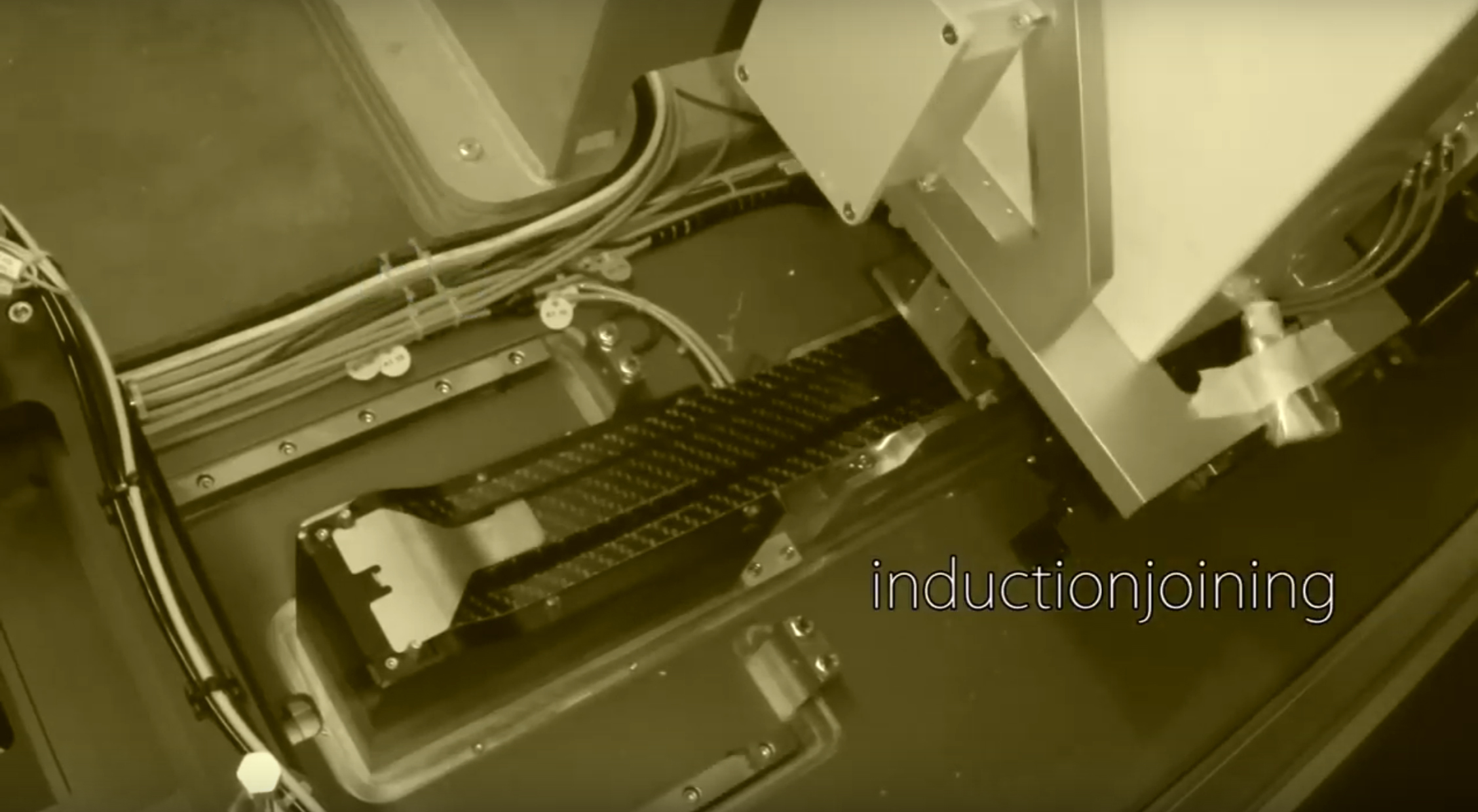
Шаг 6. Затем робот размещает зажимные устройства на трех кронштейнах. Узел индукционного соединения опускается на центральный кронштейн. Индукционная катушка нагревает металлический кронштейн, плавя матрицу PA6 из композита.
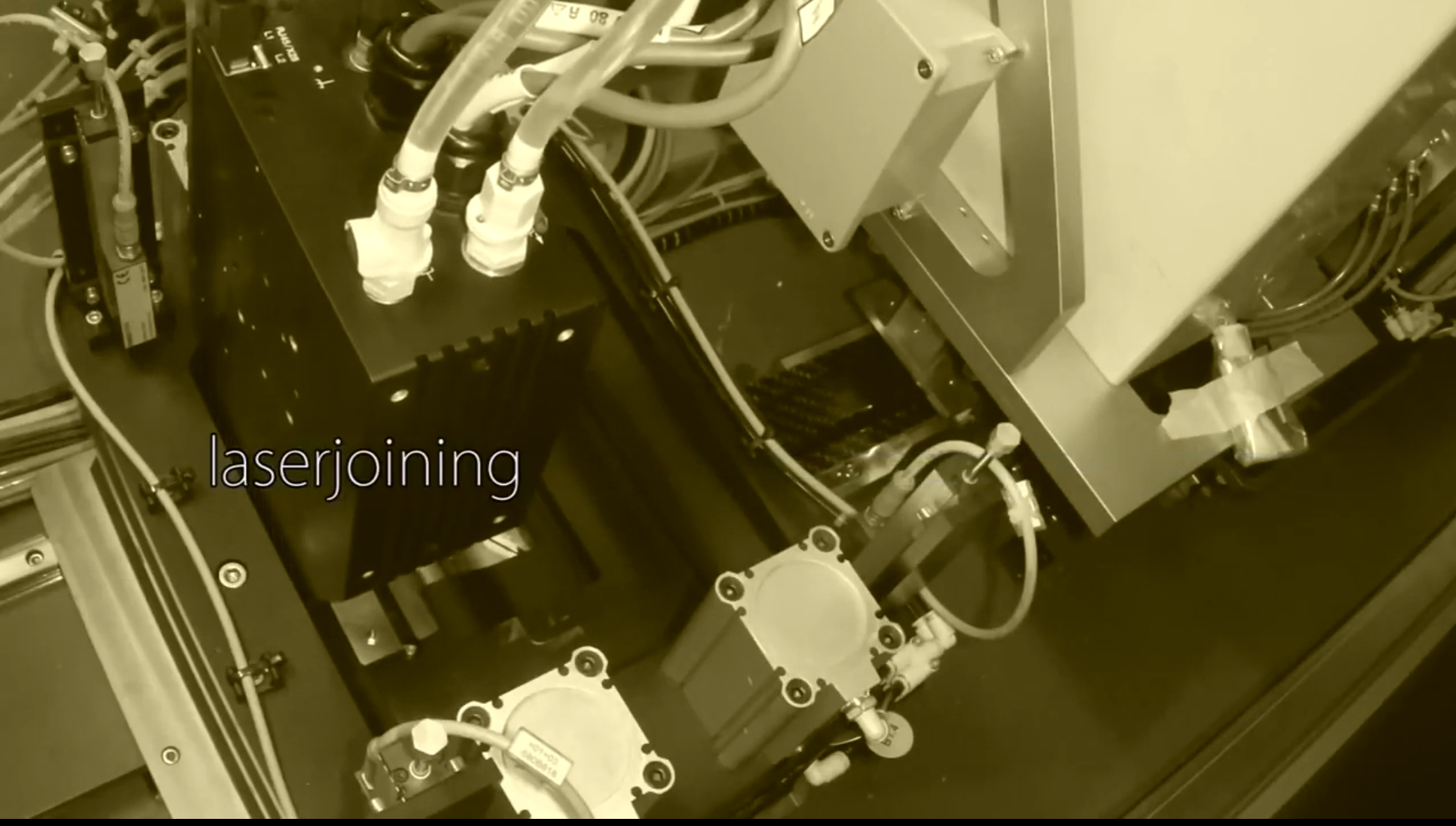
Шаг 7. По завершении индукционного соединения узел лазерного соединения опускается, чтобы соединить левый, а затем правый кронштейны. Лазер нагревает металл, заставляя нижележащую матрицу PA6 плавиться в канавках, создавая высокопрочное соединение.
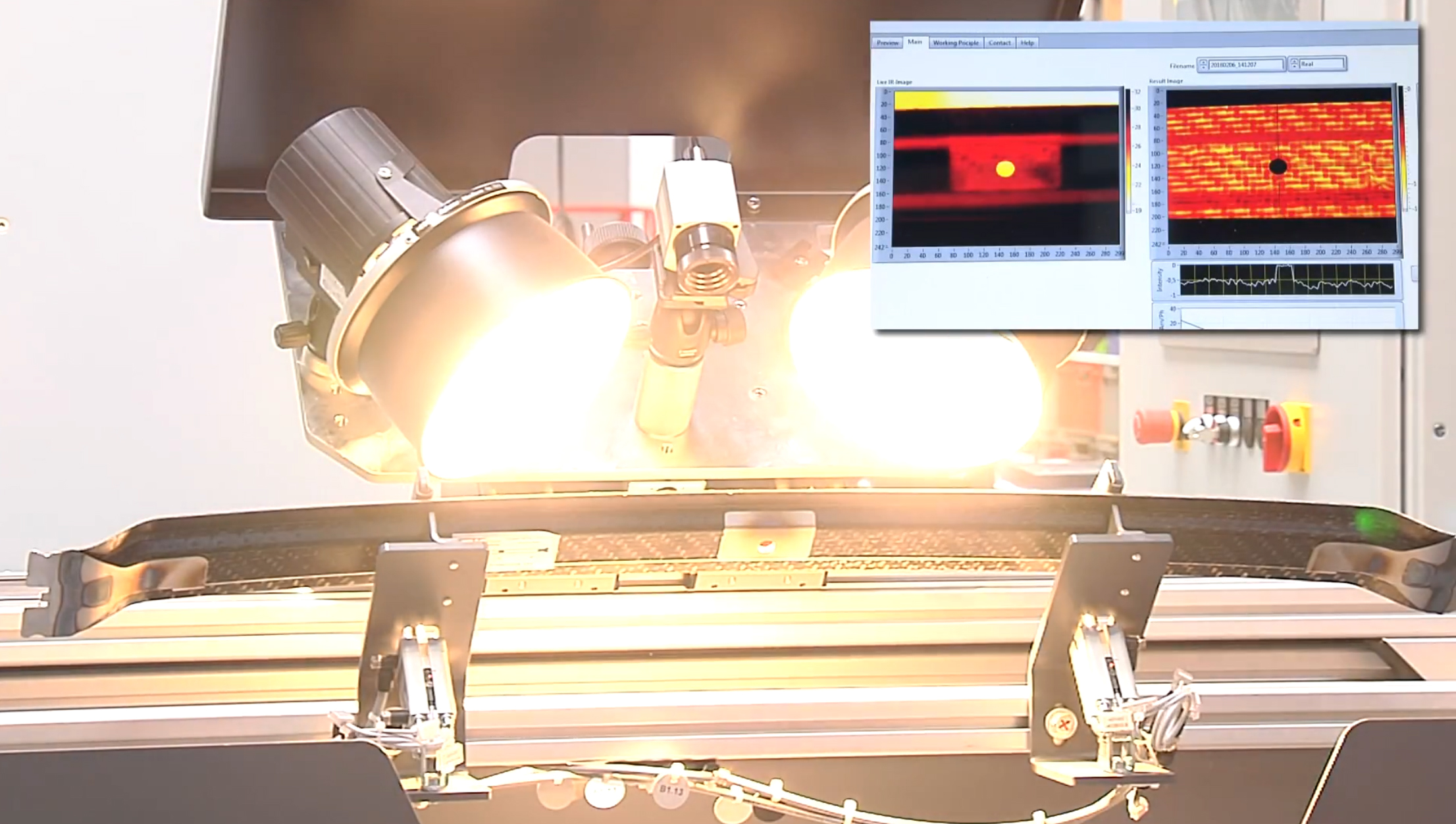
Присоединение к контролю процесса
Основным методом управления обоими процессами соединения является измерение температуры и времени в сравнении с набором оптимизированных параметров, которые были определены в ходе испытаний. «Поэтому мы изготовили соединительные образцы для испытаний с различными параметрами и провели механические испытания для каждого набора параметров с использованием специальных испытательных установок. Для бокового кронштейна была разработана комбинация испытания на сдвиг и испытания на отслаивание, а для центрального кронштейна мы использовали испытание на нагрузку давлением, сравнимое с испытанием на сдвиг внахлестку, но вы нажимаете вместо тяги, чтобы получить сдвигающую нагрузку. в зоне стыковки », - говорит Попов. Схема этих специальных испытаний была разработана совместно с EDAG Engineering GmbH (EDAG, Фульда, Германия), которая также провела анализ результатов испытаний. После этой процедуры был определен лучший набор параметров для процессов соединения, который затем использовался в опытной производственной ячейке.
«Процесс индукционного соединения был откалиброван заранее», - говорит Вайдманн. «Мы знаем, что достигаем температуры соединения примерно через 30 секунд, но мы также измеряем температуру на месте из соображений безопасности, чтобы избежать перегрева». Пирометр, который дистанционно измеряет излучение поверхности, использовался для измерения известной горячей точки в зоне индукционного соединения. «Но он не может обеспечить точные измерения лазерного соединения из-за высокого уровня излучаемого света и тепла на месте», - объясняет он. Однако контактные датчики можно использовать на композитной стороне участков лазерного соединения, хотя они не были применимы для процесса индукционного соединения, потому что они обычно сделаны из металла и могут нагреваться за счет индукции и искажать измерения.
«Обогреваемые области для всех соединений также покрываются прессовым инструментом и зажимными приспособлениями», - отмечает Вайдманн. «Таким образом, мы подтвердили изменение толщины компонента из-за давления и нагрева до и после соединения в качестве метода обеспечения качества». Это изменение толщины измеряется датчиком расстояния, встроенным в инструмент для позиционирования элемента жесткости крыши (также показанный на рис. 3). «Когда мы сжимаем детали вместе, датчик расстояния перемещается», - объясняет он. «Когда мы прикладываем тепло и давление соединения, расплавленный матричный полимер течет в полости лазерного структурирования и немного выдавливается из зоны соединения, пока соединение не остынет. Это приводит к изменению толщины, которое регистрируется датчиком расстояния ». Weidmann и команда IVW связали это расстояние с качеством детали. «Изменение толщины - другими словами, уплотнение - более 0,1 миллиметра означает хорошее качество стыка», - отмечает Вайдманн.
Встроенный NDT
Компания IVW разработала еще один метод обеспечения качества - поточную термографию. «Для обеспечения качества главной целью было увидеть недвижимость в зоне стыковки», - поясняет Попов. «Но это было очень сложно, поэтому мы выполнили термографию на композитной стороне стыков после того, как деталь была завершена».
IVW выбрала метод активной термографии под названием Lock-In Thermography, потому что он предлагает лучшее соотношение сигнал / шум, чем другие активные методы (например, импульсно-фазовая термография), а также может выявлять более глубокие дефекты. «Основная идея состоит в том, чтобы нагреть композит, который затем отводится в зону соединения и обратно на поверхность», - говорит Попов. «При синхронной термографии компонент возбуждается с определенной частотой в течение нескольких периоды. Затем мы анализируем этот ответ с течением времени. Если у вас есть области между композитной поверхностью и областью соединения, которые неоднородны из-за пустоты или дефекта, это будет отражено в тепловом отклике ».
Температурный отклик фиксируется в виде изображения. Точки, из которых состоят эти изображения, представляют собой пиксели, сокращение от элементов изображения. Каждый пиксель также является точкой измерения. Таким образом, анализируется температурный сигнал для каждого пикселя по всей области контроля. «В результате вы получаете информацию об амплитуде и фазе для каждого пикселя, а затем программное обеспечение снова преобразует ее в изображение, которое можно визуально исследовать», - добавляет он. Но он также предоставил большие наборы измерений для 126 протестированных деталей. «Мы сопоставили эти результаты неразрушающего контроля с результатами механических испытаний, проведенных EDAG», - говорит Попов. Его команда также проверила зону соединения после снятия скобок - то есть разрушающим тестом. «Таким образом, мы сопоставили три набора результатов испытаний и теперь можем определить области склеивания с низкой и высокой прочностью на основе визуального анализа результатов термографии», - говорит он.
Интегрированная ячейка для массового производства
По словам Вайдманна, одним из величайших достижений FlexHyJoin является интеграция всех технологических подразделений, каждое из которых разработано разными партнерами по проекту, в автоматизированную оптимизированную производственную линию. Компания Voithofer, занимающаяся интеграцией оборудования в Fill, объясняет, что «в каждом поставленном нам комплекте оборудования использовался другой контроллер. Мне пришлось разработать главный ПЛК для управления всеми различными технологическими установками ». Сюда входили кожухи для лазеров и робот-манипулятор ячейки, которые были поставлены Fill. «Также было очень сложно заставить все эти этапы процесса работать вместе, потому что они занимают разное количество времени», - добавляет он.
Компания Voithofer начала с разработки архитектуры для каждой технологической установки и каждого робота, продумывая, как их расположить для наилучшего потока. «Наша концепция заключалась в том, чтобы сохранить три станции - структурирование, соединение и неразрушающий контроль - модульными, в трех отдельных корпусах», - говорит он. «Таким образом, мы могли извлекать отдельные единицы и использовать их на выставках или других демонстрационных проектах, а затем возвращать их. Итак, рабочая ячейка является модульной, но интегрированной ».
Многолетний опыт Фила в области системной интеграции такого типа для серийного производства композитов помог достичь того, что Попов считает величайшим достижением FlexHyJoin:перейти от лабораторных к промышленным масштабам. «Мы первый консорциум, реализовавший подобный процесс, который подходит для массового производства композитов, соединенных с металлом», - говорит он. «Этот процесс можно использовать для многих автомобильных деталей, таких как стойки стабилизатора, бамперы и двери», - отмечает Фойтхофер. «Есть много составных частей, которые соединяются с металлическими частями в легком BIW».
Адаптация для разных отраслей
Однако необходимо внести несколько изменений, прежде чем ячейка будет запущена в серийное производство. «Мы больше не будем держать лазерное структурирование и соединение в отдельных корпусах, а объединим их в один», - говорит Фойтофер. «Это избавит от необходимости открывать и закрывать двери шкафа между этими процессами, сокращая время цикла». Он также соединил бы все станции линейно на конвейерной ленте. Таким образом, линия будет работать непрерывно, с частями, которые собираются и помещаются обратно на конвейер для каждой станции перед выходом из ячейки, готовой для сборки в BIW. Это еще больше сократит время цикла. Кроме того, расширенные выдвижные ящики, способные загружать сотни деталей, позволят линии работать в течение всей смены без необходимости пополнения запасов.
Хотя эта экспериментальная производственная ячейка была предназначена для автомобильной промышленности, Попов отмечает, что ее можно легко адаптировать для аэрокосмической, спортивной / потребительской техники и промышленных приложений. «Фактически, это было одним из основных правил, - говорит Вайдманн, - что он должен иметь возможность соединять различные геометрические формы и детали. Единственными изменениями должны быть инструмент для уплотнения индукционного соединения, зажимные приспособления для лазерного соединения и вспомогательный инструмент. Основные части камеры должны остаться прежними ». Он отмечает, что компания IVW также продемонстрировала гибридное соединение титана и стали с тканевыми композитами из углеродного волокна и полифениленсульфида (PPS), а в настоящее время разрабатывает демонстрационные образцы полиэфирэфиркетона (PEEK) и полиэфиркетонекетона (PEKK). «Для этого просто требуется адаптировать процессы соединения для более высоких температур и пересмотреть оптимальные параметры процесса», - говорит Вайдманн. «Ячейка открыта для различных материалов, включая алюминий и медь, а также других термопластичных композитных матричных систем, таких как полипропилен и полиэтилен».
«Партнеры по проекту хорошо поработали вместе и рады продолжить разработку», - отмечает он. «Мы думаем, что этот тип производства очень многообещающий, и тот ответ, который мы получили от промышленности, показывает, что есть множество компаний, которые также видят это обещание».
Смола
- Solvay увеличивает емкость термопластичного композитного материала
- Синтез и исследование оптических характеристик гибридных сферических структур Ti0.91O2 / CdS
- Поверхностный импеданс гибридных структур метаповерхностей / графена
- Fraunhofer вводит в эксплуатацию автоматизированные производственные ячейки Engel для НИОКР термопластичных компо…
- Важность выбора смолы
- Институт конструкций и дизайна DLR увеличивает зрелость термопластичных композитных конструкций фюзеляжа
- Простые в использовании комплекты позволяют ремонтировать композитные конструкции в полевых условиях
- Консорциум нацелен на решения для термопластичных композитных конструкций из углеродного волокна
- Представлен композит для архитектурной облицовки
- Композит + металл:гибридная технология полого профиля