Автоматизированное производство аэрокомпозитов:жидкое формование или сварка термопласта?
По мере того как производители оригинального оборудования и поставщики исследуют материалы и процессы, которые позволят создать новое поколение самолетов, демонстрируются два различных подхода. Первый - это жидкое формование преформ из сухого волокна, которое можно увидеть, например, на линии высокопроизводительного литья под давлением смолы (RTM) компании Spirit AeroSystem (Прествик, Шотландия) для спойлеров Airbus A320, а также в программе Wing of Tomorrow (WOT) под руководством Airbus. в котором используется автоматическое размещение не изгибающихся тканей (NCF) и инфузия жидкой смолы с последующим отверждением вне автоклава (OOA) в печи (см. «Высокопроизводительная автоматизированная линия RTM для аэрокосмической промышленности поставляет спойлеры нового поколения» и «Обновление:нижнее крыло скин, Wing of Tomorrow »соответственно.)
Второй - это термопластичные композиты (TPC), представленные, например, в многофункциональном демонстраторе фюзеляжа Clean Sky 2 (MFFD), где жесткие оболочки создаются с использованием автоматизированного размещения волокон - на месте консолидируются для верхней половины и автоклавно для нижней. половина - с последующей сборкой сваркой. Эти программы используют автоматизацию для увеличения производительности и качества при одновременном снижении затрат. Но как они сравниваются?
Институт конструкций и дизайна Немецкого аэрокосмического центра (DLR) управляет Центром технологий производства легких грузов (ZLP) в Аугсбурге. Среди своих многочисленных проектов по производству композитов PROTEC NSR и Fast Lane RPB предоставляют уникальную возможность сравнить, соответственно, отлитую жидким формованием термореактивную заднюю переборку давления (RPB) для двухпроходного Airbus A350 с термопластичным RPB для узкофюзеляжного Airbus. A320. Оба проекта работали с поставщиком этих конструкций первого уровня, Premium Aerotec Group (PAG, Аугсбург, Германия), и продемонстрировали автоматизацию при оценке времени цикла и стоимости.
Жидкая перегородка TS
«Много лет назад мы начали с PAG в проекте AZIMUT по анализу ручных процессов производства композитов», - говорит д-р Ларс Ларсен, руководитель технологий сборки и соединения в ZLP Augsburg. «Наше первое решение автоматизации было для простоев, а затем мы работали над автоматизацией большего количества операций». Основная цель PROTEC NSR заключалась в том, чтобы объединить эти специализированные решения для производства RPB в единый автоматизированный процесс, - объясняет д-р Марчин Малеха, менеджер проекта PROTEC NSR в DLR.
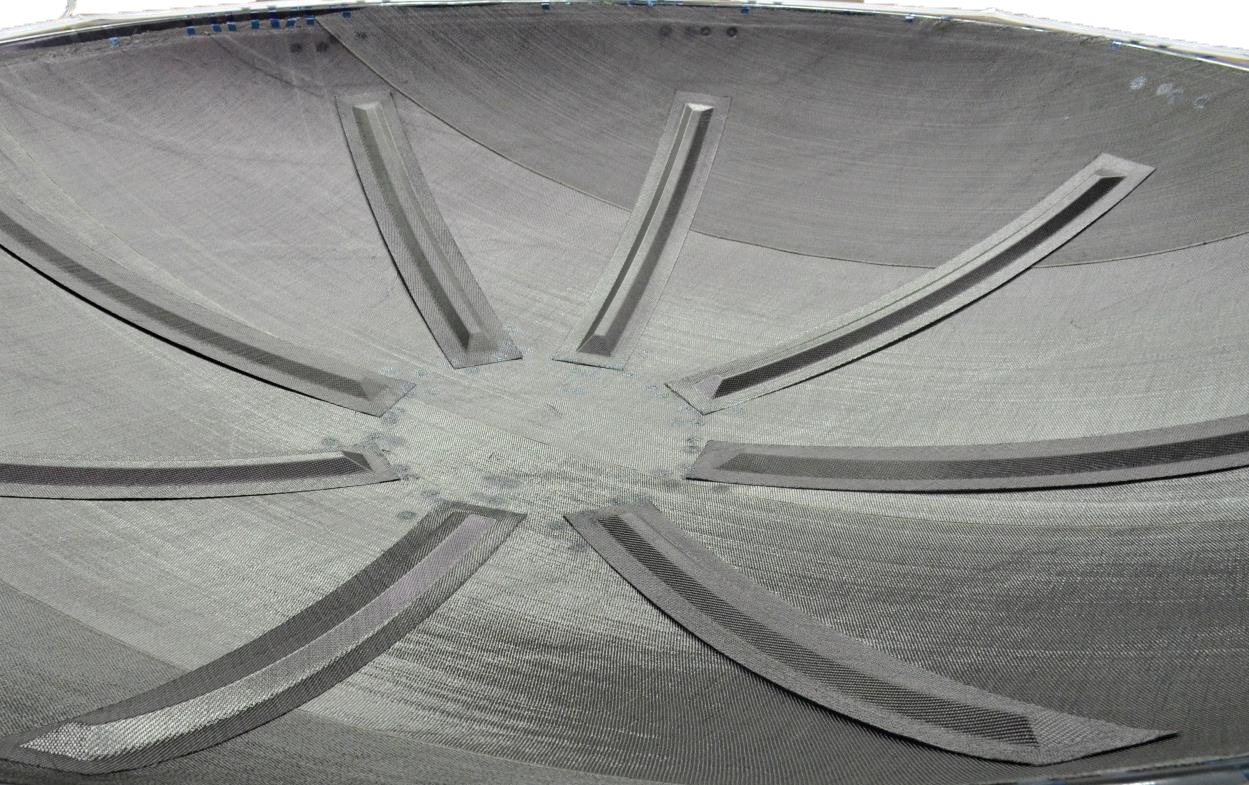
Преформы и захваты. Этапы процесса создания сухой преформы, помещенной в вакуумный мешок, показаны на рис. 1 ниже. Он был пропитан эпоксидной смолой RTM6 с использованием запатентованного Airbus процесса с использованием вакуума (VAP), в котором используется полупроницаемая мембрана для уменьшения пористости. Укладка преформ состояла из двух комплектов по 16 слоев длиной до 5 метров с использованием полной ширины 1,27 метра сатинированной ткани из углеродного волокна с пятью жгутами. Между этими двумя наборами были вставлены 25 арматурных элементов сложной формы размером до 1,5 на 2,5 метра. Сверху разместили восемь стрингеров.
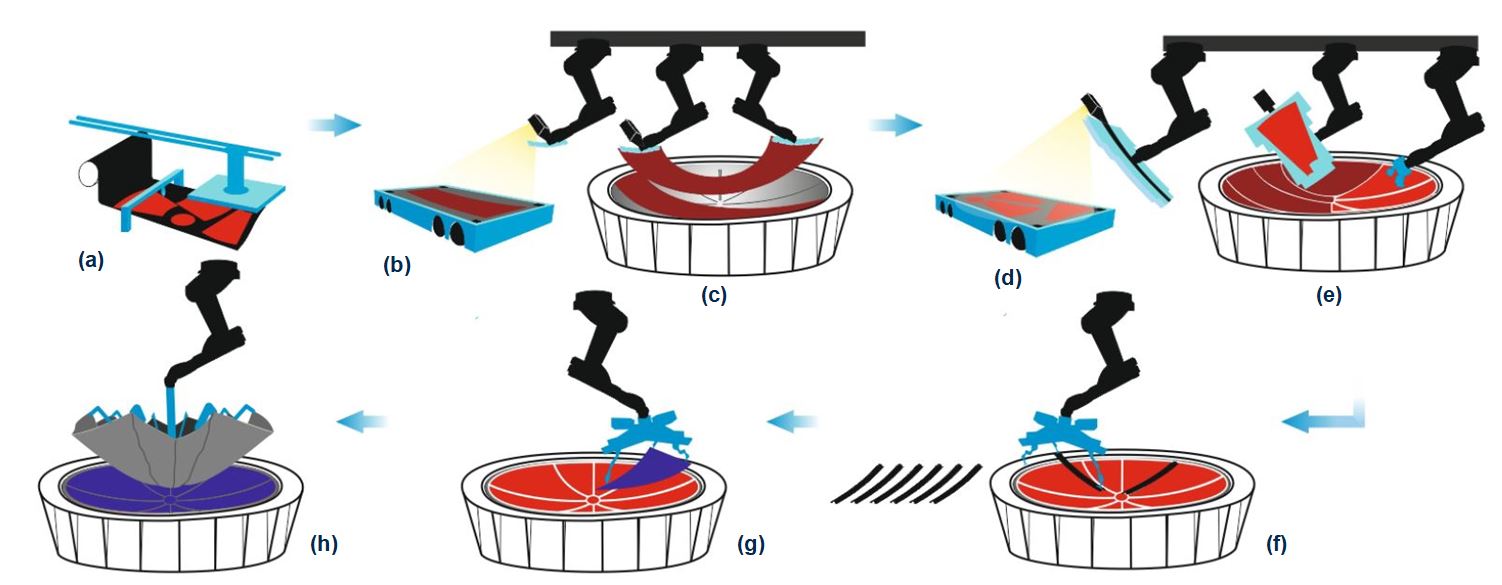
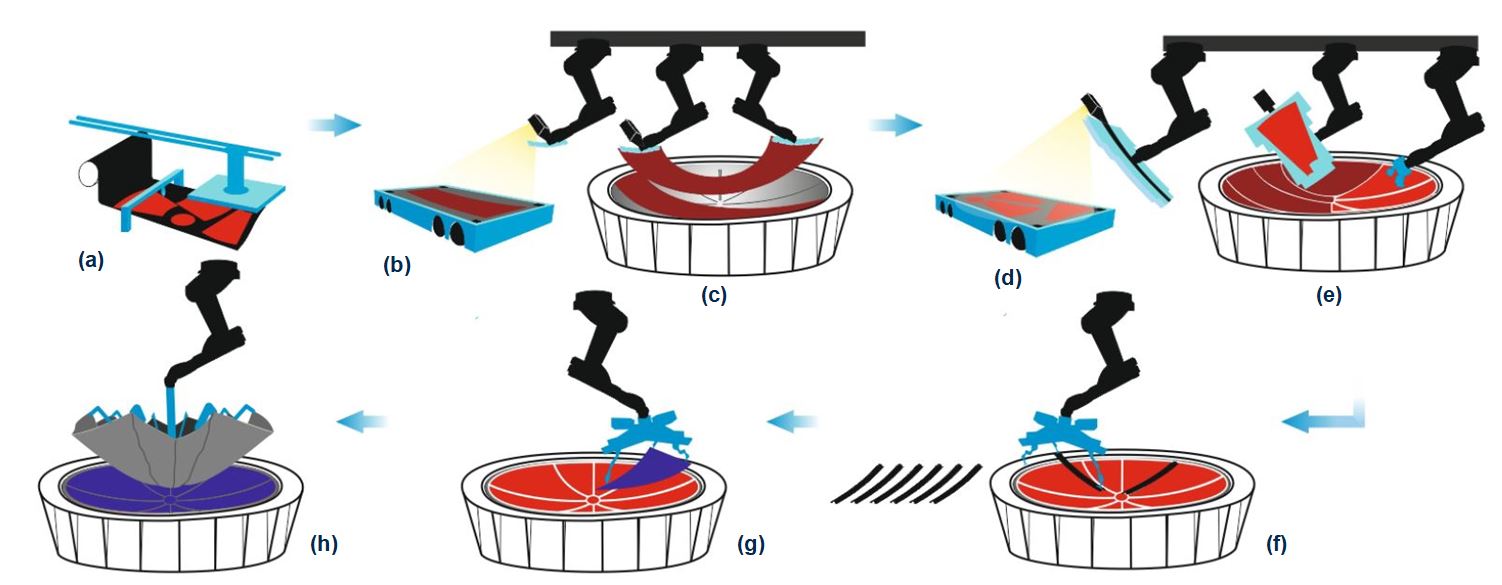
«Разработка инструментов и захватов, которые могли бы обеспечить необходимую точность при драпировке и перемещении, была одной из самых больших проблем», - отмечает Ларсен. Отчасти это произошло из-за сложной смеси слоев, для которой требовалось три различных механизма драпировки:
- Нанесение материала на всю ширину прямо с рулона, который должен соответствовать форме формы.
- Драпировка структурных слоев большого кроя где два робота взаимодействуют, по одному на кромке ткани, чтобы подобрать и создать заданную геометрию формы чтобы обеспечить соответствие без складок перед укладкой.
- Подходит для маленьких фигурных пластин размером до 1,5 на 2,5 метра .
«Для взаимодействующих роботов мы разработали рабочие органы, которые содержат шесть модулей, соединенных сферическими соединениями», - объясняет Ларсен. «Это позволяет рабочему элементу деформироваться подобно змейке в соответствии с заданной геометрией пресс-формы. Интегрированные нагревательные устройства активируют связующее в ткани во время транспортировки и формы, сохраняя свою трехмерную форму и положение после размещения ».
Автоматическая драпировка и размещение
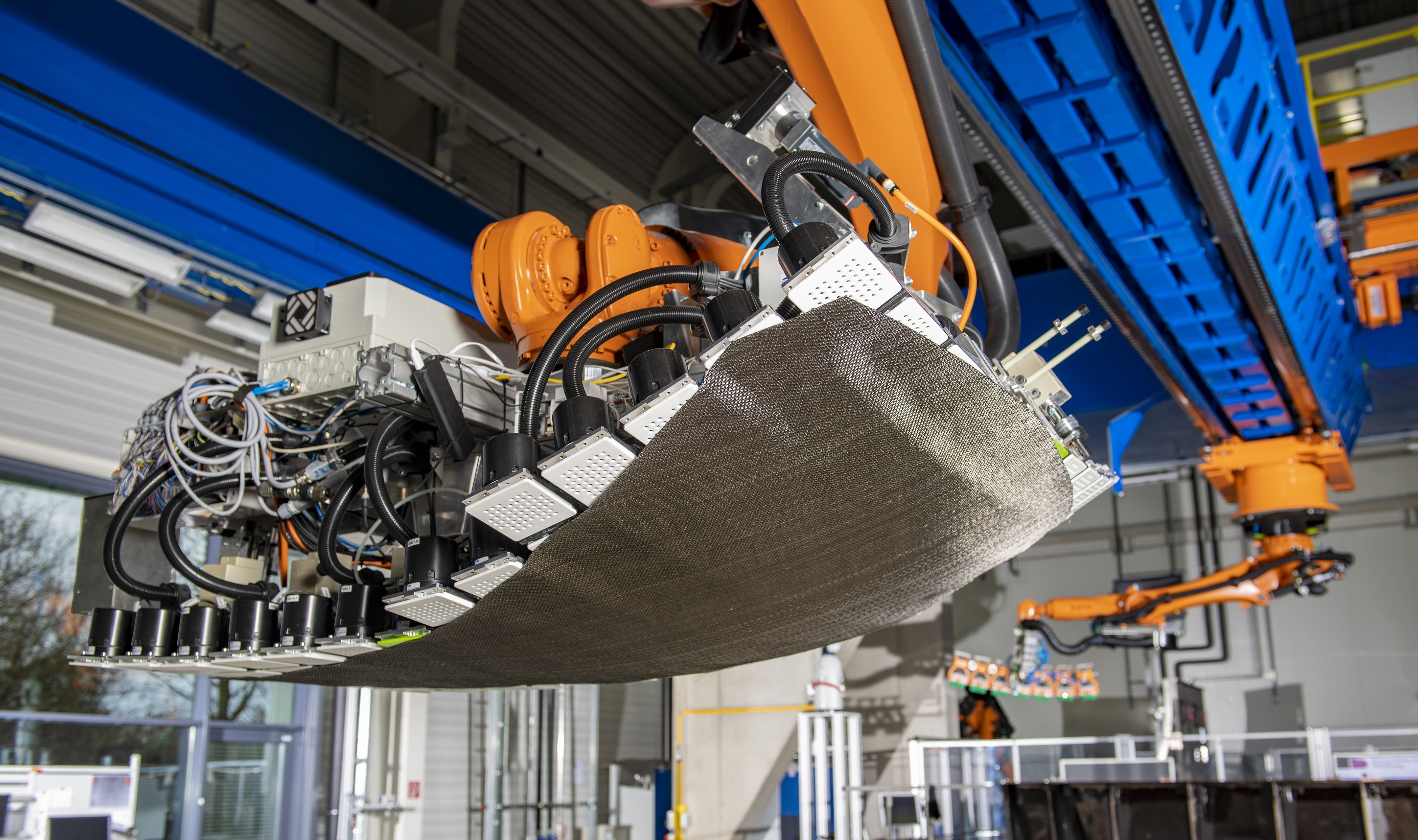
Конечный эффектор оснащен захватом, который использует 127 модулей, оснащенных вакуумным отсосом, для захвата обрезанных слоев ткани, преобразования их в трехмерную форму и последующего нагрева их перед помещением в форму. Фото:Институт конструкций и дизайна Немецкого аэрокосмического центра (DLR)
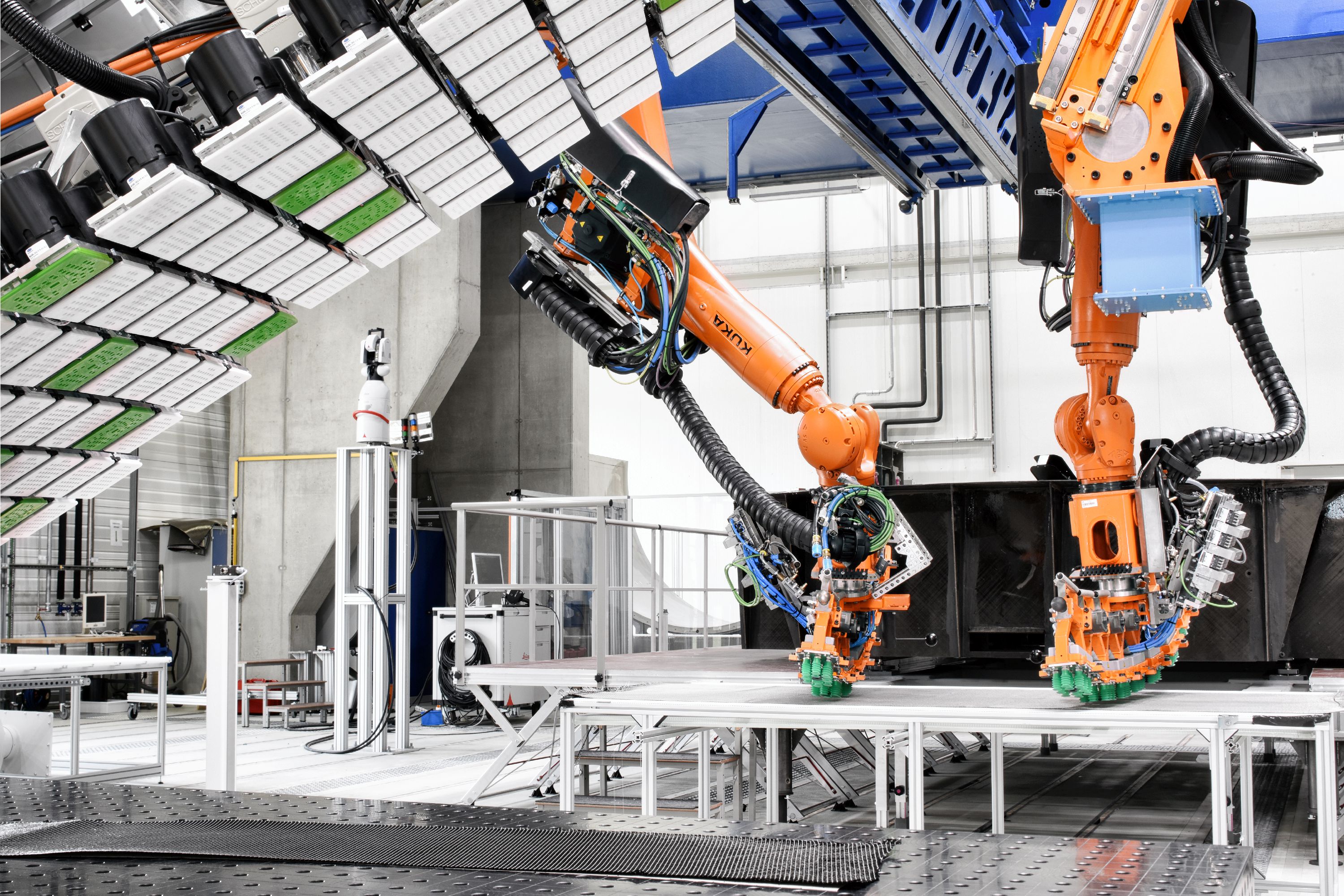
Здесь можно увидеть как захват на 127 модулей (слева), так и взаимодействующих роботов (на заднем плане). Фото:Институт конструкций и дизайна Немецкого аэрокосмического центра (DLR)
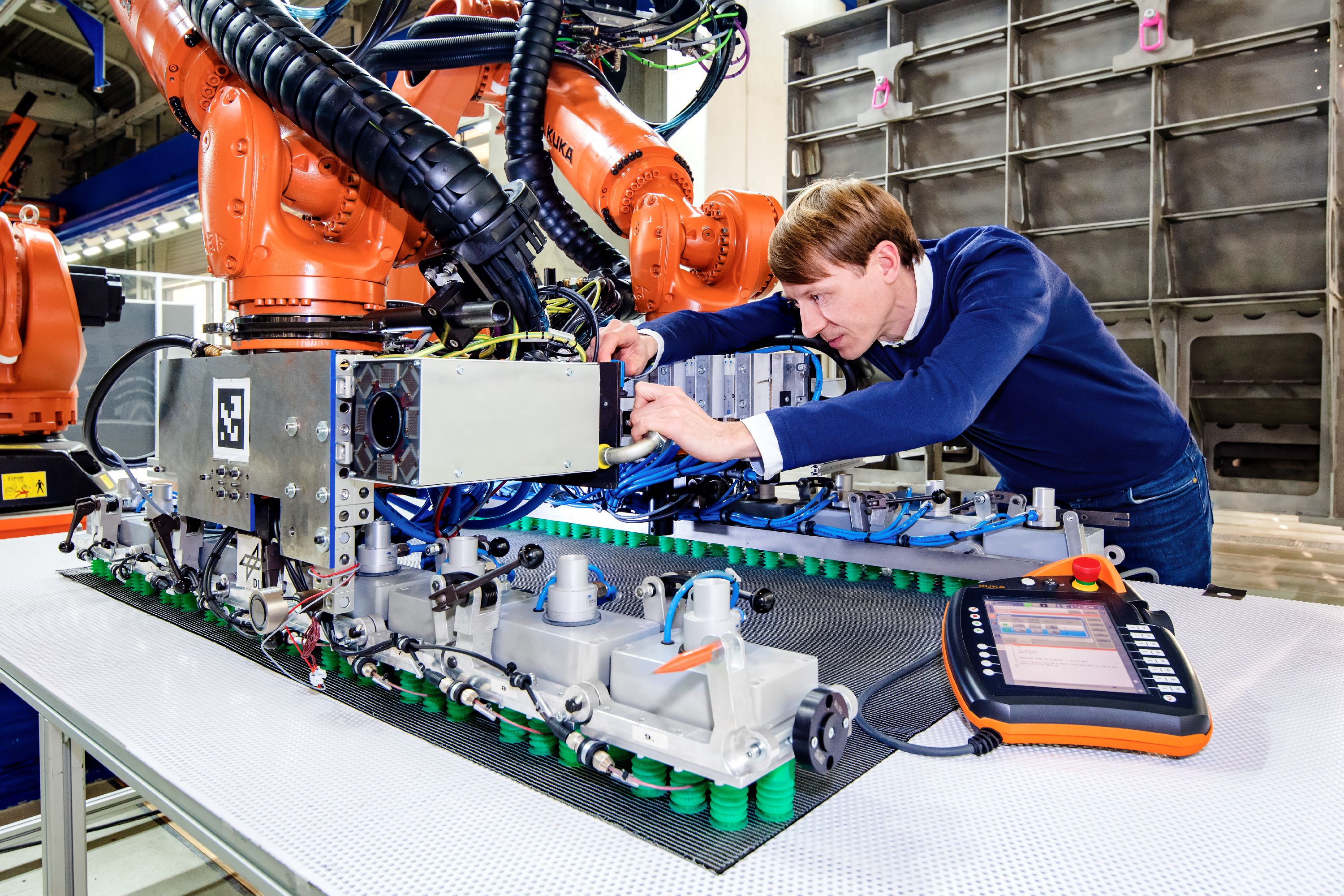
Для сотрудничающих роботов были разработаны рабочие органы, содержащие шесть модулей, соединенных сферическими соединениями. Фото:Институт конструкций и дизайна Немецкого аэрокосмического центра (DLR)

Каждый робот берет край большого слоя ткани. Затем они работают вместе, транспортируя слой, чтобы создать требуемую целевую геометрию перед помещением ткани в форму. Фото:Институт конструкций и дизайна Немецкого аэрокосмического центра (DLR)
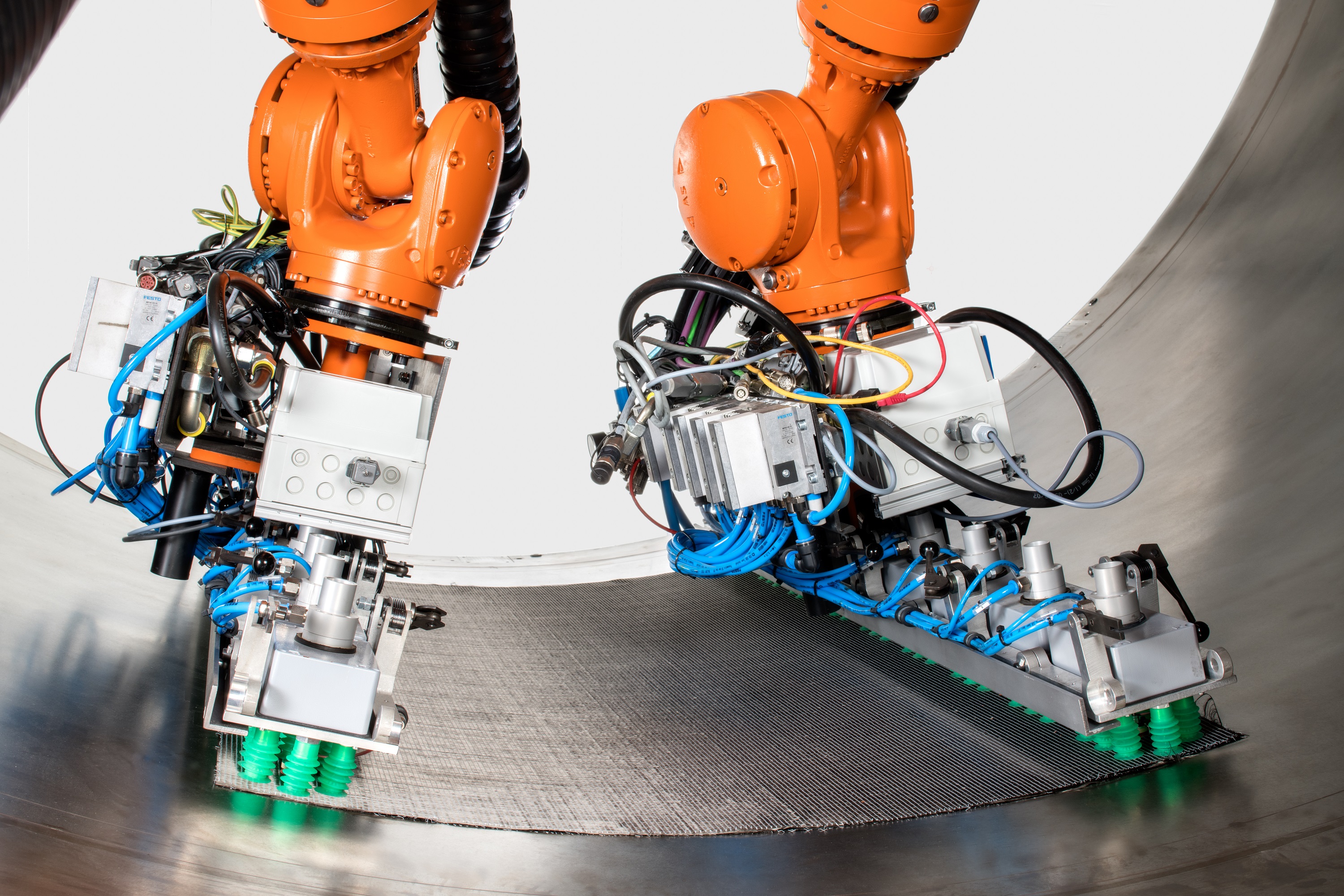
Фото:Институт конструкций и дизайна Немецкого аэрокосмического центра (DLR)
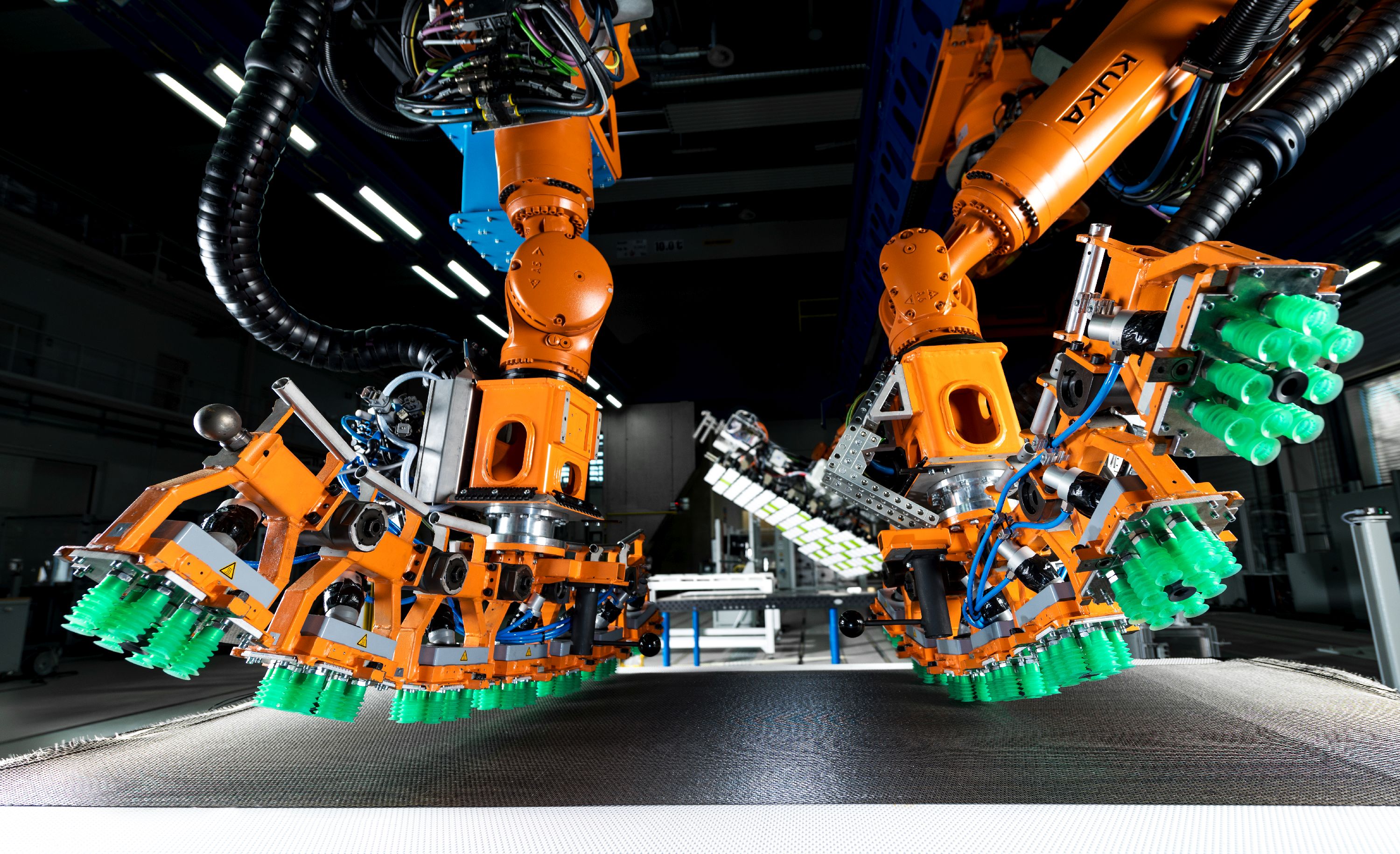
Крупным планом - рабочие органы коллаборативного робота. Фото:Институт конструкций и дизайна Немецкого аэрокосмического центра (DLR)
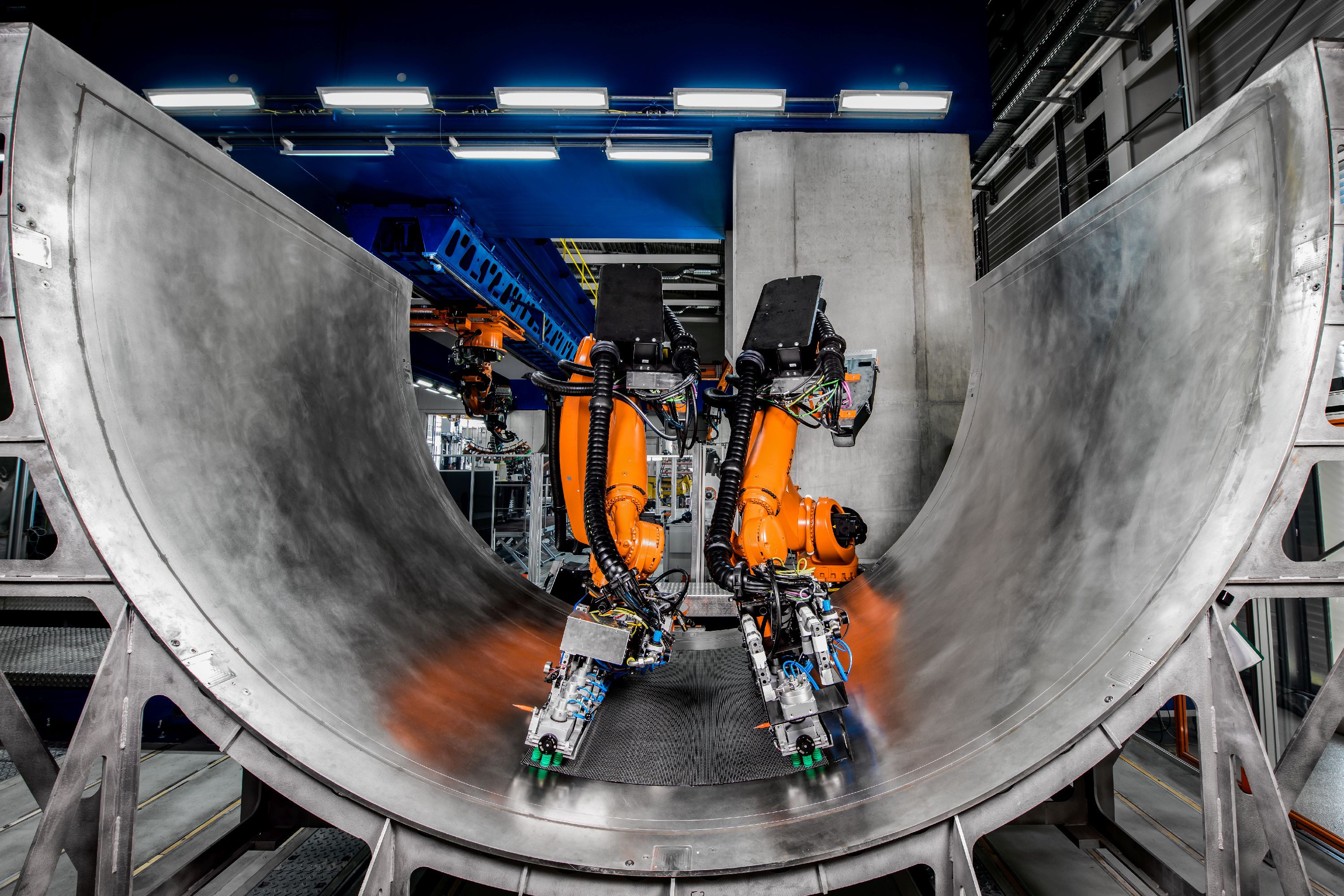
Эта система, которую DLR изначально разработала для задней переборки с повышенным давлением A320, теперь была продемонстрирована и для панели фюзеляжа, и на основе их файлов цифрового дизайна разработана с учетом гибкости для различных крупных авиационных конструкций без повторного обучения роботов. Фото:Институт конструкций и дизайна Немецкого аэрокосмического центра (DLR)
Предыдущий СледующийДля маленьких фигурных слоев до 1,5 на 2,5 метра, был разработан второй тип захвата, который использует 127 модулей, оснащенных вакуумным отсосом для захвата. «Этот захват захватывает материал в 2D-состоянии, а затем изгибает его в соответствии с заданной геометрией», - объясняет Малеха. «Он должен решить, какой из 127 модулей он будет удерживать, а какой позволит сдвинуть, чтобы преобразовать 2D-слой в 3D-форму. Итак, это очень похоже на то, как работают руки, чтобы драпировать. Мы провели множество экспериментов и приобрели опыт, где держать, а где выпускать. Силу можно регулировать в зависимости от того, насколько сильно модули захватывают материал ».
Встроенная проверка. Оптические датчики в модульных захватах контролировали процесс драпировки. После размещения слоя рабочий орган, объединяющий Leica T-Scan (Hexagon Manufacturing, Cobham, UK) и систему измерения угла волокна на основе камеры от Profactor (Steyr, Австрия), проверяет качество. «Сначала мы измерили углы волокон и сравнили их с файлом САПР, - говорит Малеха, - а затем мы измерили края каждой детали и проверили ее положение по сравнению с файлом САПР».
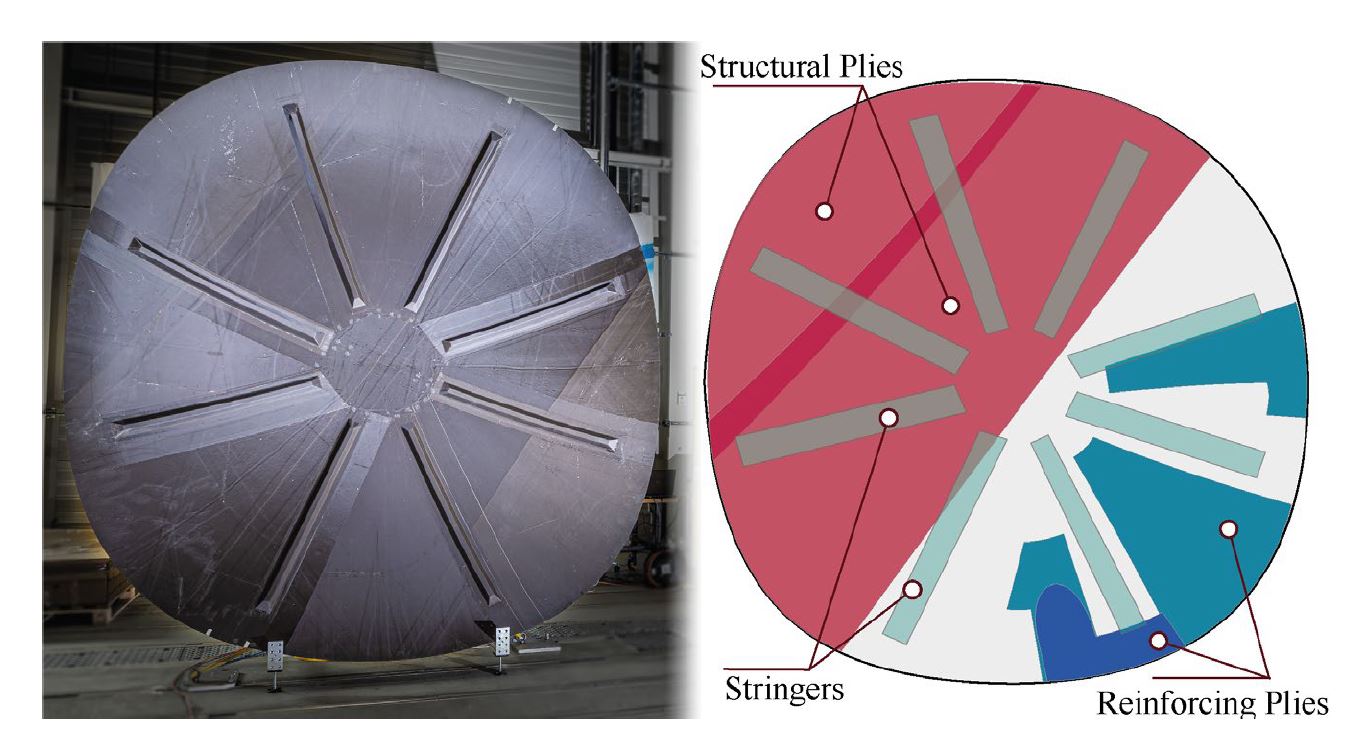
Стрингеры и вакуумная упаковка . После изготовления преформы сверху прикрепляли восемь ребер жесткости (стрингеров). Для этой задачи был разработан Multi Kinematic Gripper, который также использовался для нанесения вспомогательных материалов вакуумного мешка. Этот захват состоит из трех небольших и независимых роботов с 6 степенями свободы (DOF) и жесткой руки, все они установлены на центральном фланце промышленного робота с 6 степенями свободы. Вспомогательные материалы для вакуумной упаковки - отслаивающая пленка, перфорированная разделительная пленка и текучая среда для смолы (вспомогательные материалы со стороны инструмента) - были предварительно нарезаны и предварительно соединены в соответствии с тем местом, где они были размещены. «Их не нужно было задрапировать, их нужно было просто укладывать», - отмечает Малеха. Готовую полупроницаемую мембрану накладывали полуавтоматическим способом с помощью рабочего органа с «зонтичным» механизмом, в то время как размещение липкой ленты и внешнего вакуумного мешка оставалось ручным, но также могло быть автоматизировано.
Время и стоимость цикла. Для Malecha самой большой проблемой было создание модульной системы управления производством (MES) на основе искусственного интеллекта для мониторинга и управления технологической цепочкой. «Нам пришлось создать системы управления данными, которые могли бы объединить совершенно разные процессы, а затем управлять ими через MES через один порт обмена данными», - объясняет он. «Мы можем использовать их по мере необходимости на лету, обеспечивая большую гибкость и более широкое использование по сравнению со строгим производственным порядком».
Технология PROTEC NSR была проверена путем производства полноразмерного демонстратора в январе 2019 года и достижения уровня зрелости 5-6 TRL к середине 2019 года. По сравнению с современным уровнем развития компании PAG, эта автоматизированная технологическая цепочка сокращает время цикла наложения рулонной ткани на 58% и подбора и размещения обрезных слоев на 50%. Производственные затраты на эти операции были сокращены на 11,5% и 31% соответственно.
Термопластический RPB
«Этот проект начался в 2018 году с PAG и Institut für Verbundwerkstoffe (IVW, Кайзерслаутерн, Германия), чтобы показать, что возможно с термопластическими композитами в крупных деталях и первичных конструкциях», - объясняет д-р Стефан Ярка, руководитель проекта Fast Lane RPB и эксперт по сварочные технологии в ZLP Augsburg. «RPB на самом деле не является основным, потому что механические требования не такие высокие, как крыло или фюзеляж, но он показывает, что возможно для больших, плоских, слегка изогнутых конструкций. Всего за четыре месяца мы разработали демонстрационный образец A320 RPB в качестве примера преобразования существующей алюминиевой конструкции в термопластичные композиты ».
В этом демонстраторе использовалась ткань Cetex из углеродного волокна (CF) и органосульфид (PPS) (Toray Advanced Composites, Nijverdal, Нидерланды) и контактная сварка. Резистивный элемент между двумя свариваемыми поверхностями выделяет тепло и остается в сварной конструкции. Компания GKN Fokker (Хоогевен, Нидерланды) десятилетиями использовала эту технику для изготовления дверей шасси самолетов и фиксированных передних кромок. Для этого A320 RPB команда ZLP использовала резистивный элемент CF вместо обычной сетки из нержавеющей стали.
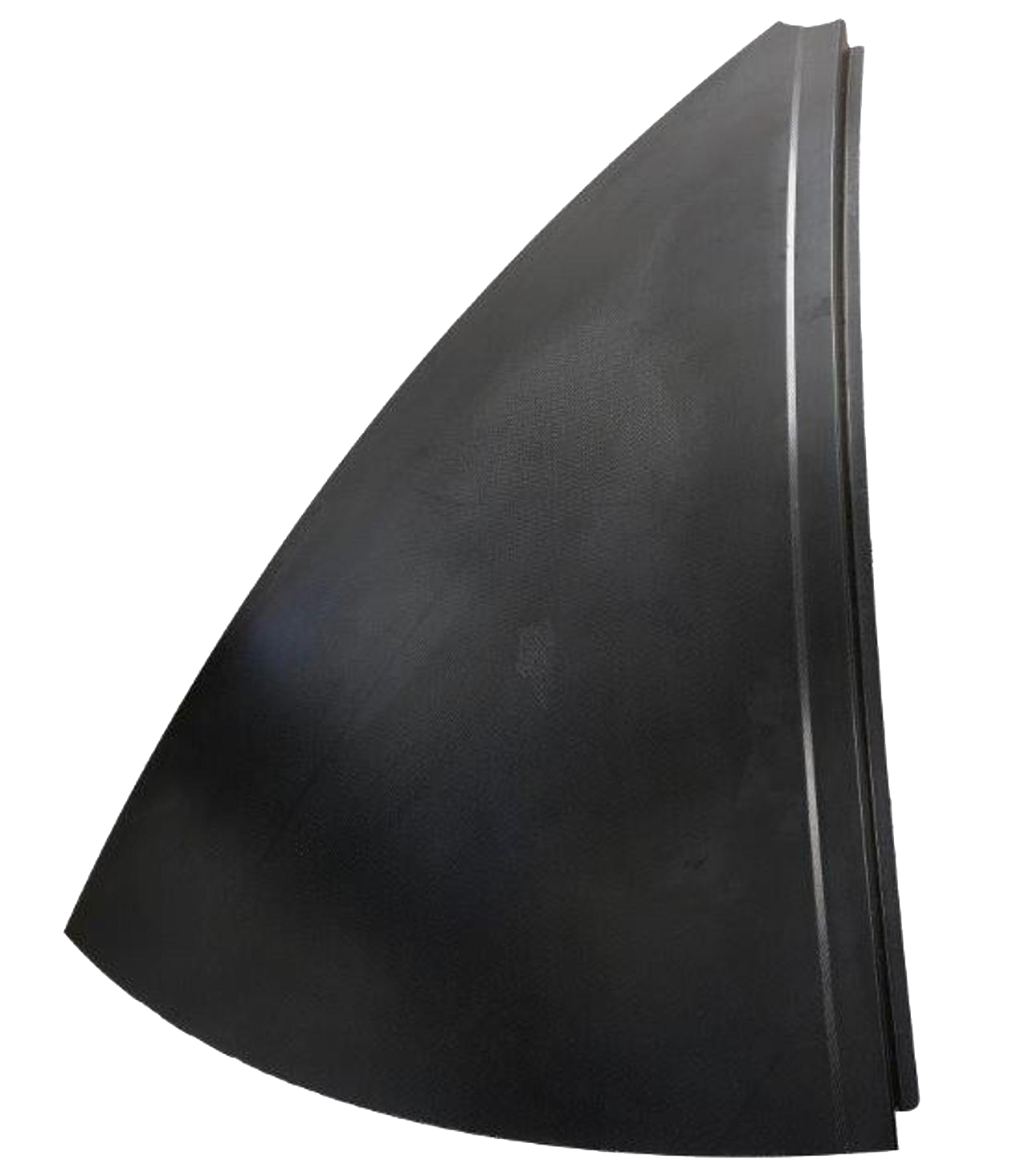
«Термопластический композит RPB должен был быть по той же цене или дешевле, но этот материал намного дороже», - отмечает Ларсен. Таким образом, снижение производственных затрат за счет автоматизации было ключевым моментом, как и использование восьми идентичных лепестковых секций. «Эти секции были необходимы, чтобы сформировать форму детали с двойной кривизной», - объясняет Джарка. «Для термоформования как одной детали потребуется очень большой пресс, что было бы слишком дорого. Таким образом, восемь меньших секций были отформованы прессом на IVW с использованием подобранной металлической оснастки, и мы собрали их с помощью автоматической сварки. Уровень автоматизации штамповки термопластов выше, чем у термореактивных композитов. В основном вы используете подходящую металлическую оснастку, при этом основной проблемой является высокая, но постоянная температура, но это также делает автоматизированный цикл прессования очень быстрым ».
Общие этапы процесса для демонстрационного RPB показаны на рис. 2. «Используемый нами процесс сварки не был новым, - говорит Джарка, - но его нужно было доработать, чтобы соединить 1,5-метровую [и 40-миллиметровую проволоку]. широкие] швы для детали диаметром 3 метра и интегрировать систему контроля качества. Компоненты сначала были зафиксированы в правильном положении с помощью зажимного приспособления, а затем была приложена электрическая энергия для образования расплава пластика в зоне сварного шва ».
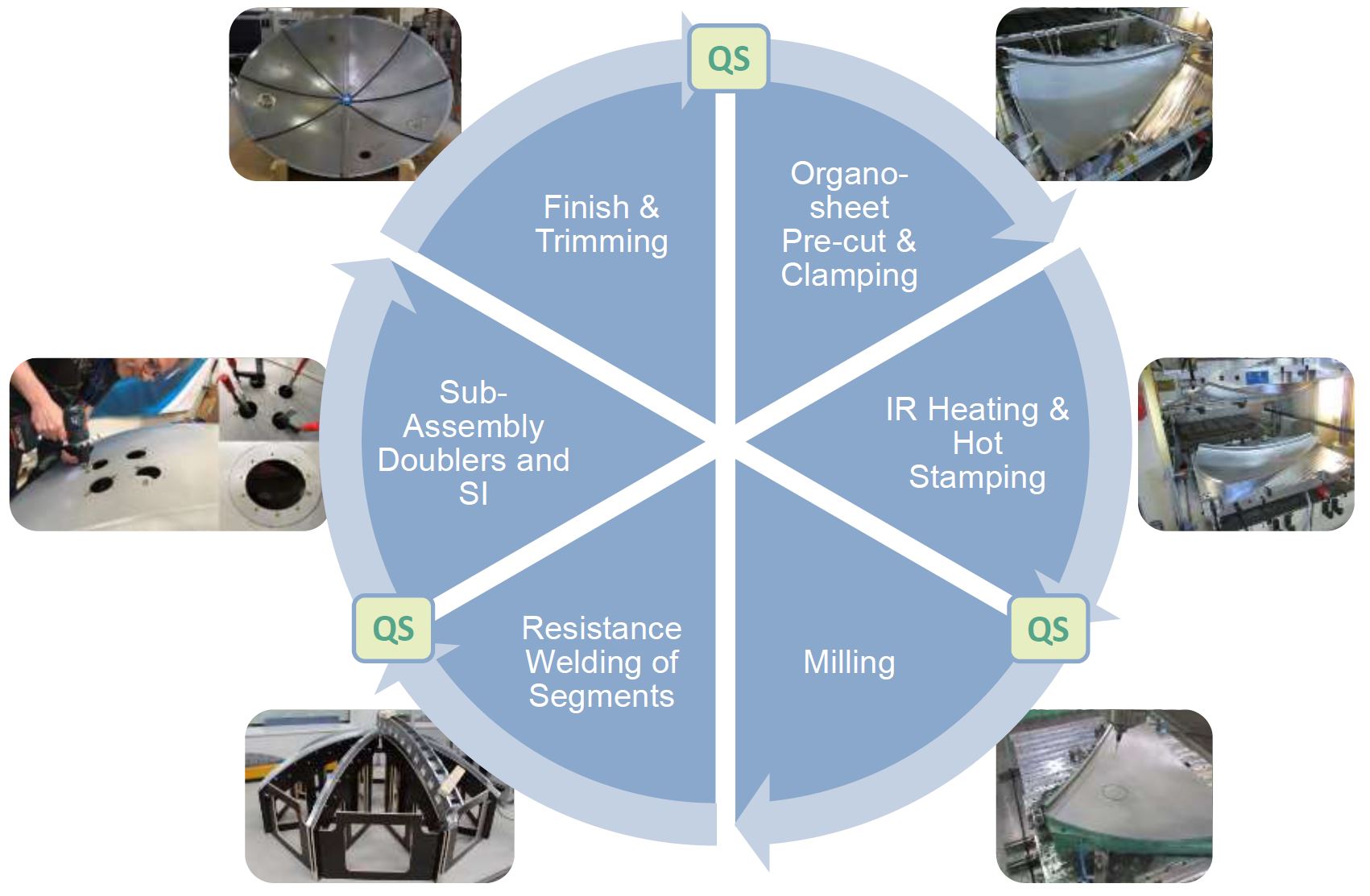
Рис. 2. Этапы процесса изготовления термопласта RPB
Этапы процесса, использованные для производства восьми секций (внизу) штампованного органолиста CF / PPS, которые затем были соединены контактной сваркой с образованием переборки демонстратора A320. Фото:Институт конструкций и дизайна Немецкого аэрокосмического центра (DLR)
Интеграция QA. «Мы пробовали термографию, активируемую как импульсной лампой, так и ультразвуком, но с ее помощью не так просто измерить зону сварки», - объясняет Джарка. «Термография очень быстрая, но с ее помощью нелегко сказать, есть ли у вас хорошее уплотнение». Вместо этого они использовали стандартный испытательный стенд для изготовления нескольких сварных образцов, измерения тока, напряжения и температуры. «Затем мы проверили их с помощью ультразвукового контроля (UT) и установили корреляцию между параметрами процесса и хорошей консолидацией», - говорит Ларсен. «Если у нас хорошие параметры, значит, и у нас есть хорошая роль. Мы также создали имитацию процесса, чтобы сравнить данные, которые мы получаем во время сварки, с установленными нами исходными базовыми показателями ».
Автоматизация и время цикла. «Весь процесс был очень быстрым, в масштабе автомобильных запчастей», - говорит Джарка. «Мы достигли TRL 3 в нашем обзоре 2019 года и с тех пор достигли TRL 4. Мы достигнем TRL 6 к концу 2021 года». Перед пандемией PAG заявила, что запустит производство термопластичного RPB к 2021 году. Хотя будущее сейчас менее ясно, термопластический RPB по-прежнему рассматривается как «фюзеляж завтрашнего дня», снижающий вес с 41 до 35 кг. время сборки на 75% и общая стоимость детали более чем на 10%.
Сравнение композитов TS и TP
«Процессы термопласта настолько быстры, что вы можете быть дешевле, чем алюминий, и даже обеспечить производительность 100 самолетов в месяц», - говорит Джарка. «RPB - хорошее приложение для сварки термопластов, но также и для автоматизации», - говорит Малеха. «Сухое волокно, полученное жидким формованием RPB, дороже автоматизировать».
«Но такая автоматизация интересна, потому что вы можете добиться реальных результатов, автоматизируя лишь некоторые из подпроцессов», - говорит Ларсен. «Например, с автоматизацией вспомогательного оборудования мы могли завершить вакуумную упаковку в мешки примерно за час, что примерно в 10 раз быстрее, чем при ручном процессе». Однако он признает, что стоимость является основным препятствием для реализации такого улучшения. «Стоимость цифровых инструментов, роботов и разработки слишком высока для одной части, такой как RPB. Но если бы мы могли разработать модульный подход, при котором вы могли бы использовать эту систему для многих деталей, тогда эту стоимость можно было бы расширить, сделав ее доступной при расчетах с меньшими затратами времени и трудозатрат ». ZLP действительно добился этого, как объясняется в CW . Выпуск от июля 2020 года:«Композиты 4.0:цифровая трансформация, адаптивное производство, новые парадигмы».
«Пока еще не так много сравнений между термореактивными и термопластичными композитными конструкциями», - говорит Малеха. «Но мы начинаем сравнивать термореактивные и термопластические процессы». Он отмечает, что следующая цель - показать, что линии сварного шва из термопласта обладают свойствами, необходимыми для крыльев и фюзеляжей самолетов. И эти характеристики также должны быть продемонстрированы, например, для больших интегрированных крыльев, отформованных методом жидкостного литья. Это именно то, к чему стремятся программы MFFD и WOT. И мы ждем их результатов, а также результатов многих других проектов Clean Sky 2 и EC, чтобы показать дальнейшие шаги вперед.
Смола
- Блог:литье под давлением жидкого силиконового каучука
- Технология производства термопластичных сотовых панелей EconCore
- Карл Майер запускает линию по производству термопластичных UD-лент
- INEOS Styrolution для создания производственной площадки для термопластичного композита StyLight
- Технология производства Herone получила награду JEC Innovation Award
- Термопластические формованные термореактивные пластмассы, 2-минутный цикл, одна ячейка
- LANXESS расширяет производственные мощности по производству термопластичных композитов, армированных непрерыв…
- Airtech запускает высокотемпературные вакуумные упаковочные материалы для формования термопластов
- Процесс Finex для производства жидкого чугуна
- Автоматизированное производство муфт для бурения нефтяных скважин