Гибридный широкоформатный аддитивный инструмент:более легкие, быстрые и менее дорогие формы для больших деталей
На протяжении более трех десятилетий коммерческая авиация все чаще использует композитные материалы. Фактически, более половины критических структурных компонентов на некоторых моделях крупных коммерческих самолетов сегодня являются композитами. По мере того, как использование этих материалов увеличивалось как с точки зрения объема, так и с точки зрения размеров деталей, становилось все труднее создавать инструменты - особенно доступные инструменты - для более быстрого прототипирования и производства этих деталей. Например, каждое крыло A350 XWB от Airbus SE (Лейден, Нидерланды) имеет длину 32 метра и ширину 6 метров и представляет собой одни из крупнейших когда-либо созданных композитных авиационных конструкций.
«Сейчас на рынке присутствуют такие прорывные производственные технологии, что мы можем ожидать больших шагов в эволюции инструментов, которые помогут нам решить проблемы, с которыми мы сталкиваемся при разработке компонентов самолетов из композитных материалов», - отмечает М. Пилар Муньос Лопес, инженер по производству композитных материалов в компании. Завод Airbus в Ильескасе, Испания:«Для нас крайне важно изучить эти технологии, возможности и ограничения, чтобы подготовиться к будущему».
Учитывая, что инструментальная оснастка представляет собой значительную часть общих затрат на программу для деталей конструкции самолета, и учитывая увеличивающийся размер этих деталей, необходимы новые варианты инструментов с более низкими затратами и сокращением времени выполнения заказа. Интересное исследование гибридной, широкоформатной, аддитивно производимой оснастки (LFAM) для прототипов и мелкосерийных деталей аэроструктуры было недавно завершено Airbus, Northrop Grumman Aeronautics Systems - бизнес-подразделением Aerospace Structures (Клирфилд, Юта, США) и Университетом. Дейтонского научно-исследовательского института (UDRI, Дейтон, Огайо, США) с обнадеживающими результатами.
Решение проблем с тепловым расширением
Большинство аэроструктур из углепластика (углепластика) изготавливается из препрега с эпоксидной матрицей. Для формования таких деталей инструмент должен выдерживать температуру отверждения в печи или автоклаве до 180 ° C / 356 ° F. Кроме того, учитывая очень низкий коэффициент (линейного) теплового расширения углепластика (CLTE или CTE), очень важно максимально точно согласовать CLTE инструмента и формовочного материала при комнатной и повышенных температурах. Это гарантирует, что формы сохранят размеры, чтобы полученные детали также соответствовали требованиям к размерам. Чтобы избежать деформации или напряжения в конечных конструкциях, также важно избегать использования инструментального материала, который остывает быстрее, чем материал детали. Как следствие, наиболее распространенные инструменты, используемые для формования больших аэроструктур из углепластика, изготавливаются либо из самого углепластика, либо из инвара, железного сплава никеля и железа, известного своим низким CLTE. Оба являются дорогостоящими и могут потребовать значительного времени выполнения заказа. Кроме того, инвар сложно и требует много времени для обработки и транспортировки. Хотя стальные или алюминиевые инструменты могут снизить затраты, их относительно более высокие значения CLTE ограничивают их использование во многих областях, особенно при формовании больших или длинных деталей.
Во многих исследованиях государственного и частного секторов оценивались инструменты, изготовленные аддитивным способом, напечатанные на термопластических материалах, и был сделан вывод о том, что они потенциально предлагают преимущества, включая более низкие затраты и более короткие сроки изготовления термореактивных ламинатных композитов. К сожалению, инструменты LFAM на полимерной основе имеют такие проблемы, как пористость инструмента, которая может привести к значительным потерям вакуума при температурах / давлениях отверждения. Решение этой проблемы требует дополнительной доработки инструмента и покрытия поверхности. Еще более серьезной проблемой являются сильно анизотропные значения CLTE из-за выравнивания наполнителя исходного материала в плоскости во время экструзии / печати, что может привести к различиям в расширении / сжатии в 5-10 раз больше по оси Z, чем по осям печати X и Y. Это затрудняет получение деталей с точными размерами, воспроизводимостью и воспроизводимостью, особенно когда детали большие, имеют высокое соотношение сторон и / или имеют сложные поверхности.
«Все, кто интересуется аддитивным инструментарием, сталкиваются с одними и теми же проблемами пористости и неконтролируемого теплового расширения, имея несколько эффективных способов решения этих проблем», - объясняет Скотт Хуэльскэмп, руководитель группы UDRI, занимающийся разработкой передовых производственных процессов, Отдел конструкционных материалов. «Есть много людей, которые хотят использовать инструменты AM, но они ждут, что кто-то решит эти проблемы».
Учитывая потенциал AM в сокращении стоимости инструментов и времени выполнения заказов, отрасль сосредоточила значительные усилия на решении проблем расширения за счет изучения новых материалов для печати, модификаций оборудования принтера и новаторских подходов к моделированию. Например, некоторые группы разработали «величину компенсации» для разработки инструментов AM для устранения различий в CLTE. Однако Хуэльскэмп отмечает, что при определении какой значение компенсации использовать сложно и подвержено ошибкам. Кроме того, такие подходы оказались неэффективными для инструментов с охватывающей полостью и инструментов с захватывающими элементами по всей их длине, которые создают условия штамповки, способные повредить детали во время термоциклирования в инструменте.
«Нет никакого компенсационного фактора, который решит такую проблему», - добавляет он. «На сегодняшний день ни одно исследование инструментов AM не полностью удовлетворило потребность в низких, изотропных значениях CTE при повышенной температуре. Без этой особенности размеры и геометрия инструментов всегда будут ограничены, а более крупные инструменты будут страдать от более высоких погрешностей размеров при температурах отверждения ».
В попытке опробовать новые подходы к решению проблем, связанных с инструментами LFAM, несколько компаний-членов предприняли 18-месячный проект под эгидой Института инноваций в области производства передовых композитов (IACMI, Ноксвилл, штат Теннеси, США) и при поддержке США. Министерство энергетики и занятости Огайо (Колумбус, Огайо). Команда, возглавляемая UDRI, включала Airbus и Northrop Grumman. Эти организации ранее сотрудничали в других исследованиях как внутри, так и за пределами IACMI, и поэтому были знакомы с возможностями друг друга.
Подход «грубой силы»
UDRI уже имеет значительный опыт работы с инструментами AM и является активным членом America Makes (Янгстаун, Огайо, США), консорциума AM США. Кроме того, институт проводил исследования для ВВС США с использованием структур AM с металлической опорой и работал с Cincinnati Inc. (Харрисон, Огайо, США), производителем принтеров Big Area Additive Manufacturing (BAAM), над чистыми инструментами AM.
«Мы также работали с пользовательскими компаундерами над новым сырьем для 3D-принтеров, но ничто из того, что мы делали, похоже, не продвигалось вперед, и мы не знали, что кто-то другой добился большего успеха, чем мы», - вспоминает Хуэльскэмп. «Именно тогда у нас возникла идея подойти к проблеме иначе. Если бы мы не могли изменить поведение материалов AM или предсказать это поведение напрямую , тогда, возможно, мы могли бы заставить их вести себя так, как мы хотели косвенно . » Принимая то, что Хуэльскэмп называет подходом «грубой силы», UDRI предложил гибридное исследование LFAM, которое позволит создать инструменты для аэроструктуры с применением обычных Обшивка лица из углепластика в термопластичный композит Ядра AM
Цели проекта были просты:найти менее затратный и быстрый метод изготовления больших инструментов для аэроструктур. Команда искала вариант, который снизил бы затраты на 50% и произвел по крайней мере 10 приемлемых прототипов или деталей небольшого объема для последующего тестирования
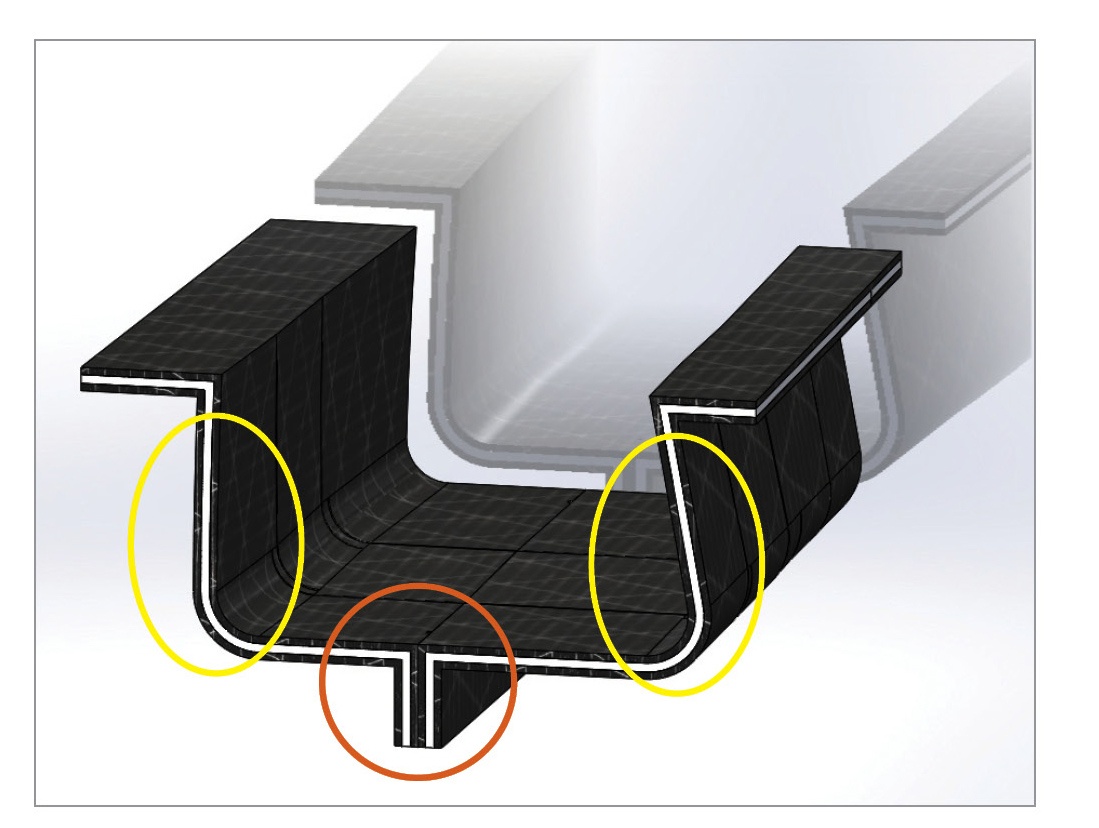
Команда решила использовать многослойную конструкцию для производства одностороннего инструмента для части стандартного лонжерона крыла с использованием данных по инструментам от Airbus. За исключением изготовления оснастки для формования только части полномасштабного С-образного лонжерона - из-за нехватки места на предприятии UDRI - никаких серьезных изменений конструкции не было внесено.
Инструмент с внутренней резьбой был разработан для обеспечения того, чтобы критическая геометрия детали формировалась с использованием поверхностей с твердым инструментом. Этот инструмент для крышки лонжерона имел небольшой угол внутрь, что создавало отрицательную тягу и условие фиксации штампа, поскольку он был цельным. Это побудило исследователей изменить конструкцию на разъемный инструмент, который был герметизирован с помощью прокладки / шнура. Чтобы снизить риск, команда начала с инструмента подшкалы 0,6 метра / 2,0 фута, чтобы подтвердить концепцию. После того, как процесс разработки инструмента и детали прототипа, изготовленные на этом инструменте, были протестированы и признаны работоспособными, команда построила инструмент большего размера 3,3 метра / 11 футов длиной для формования большей части лонжерона для испытаний прототипа.>
Поскольку инструмент из углепластика имеет такое низкое значение CLTE, легче, чем инвар, и инструмент предназначен для изготовления прототипов / деталей небольшого объема, команда решила использовать лицевые оболочки из углепластика, чтобы ограничить ядро AM. Обшивки были изготовлены из эпоксидного препрега для инструментов Hextool M81 от Hexcel (Corp., Стэмфорд, Коннектикут, США).
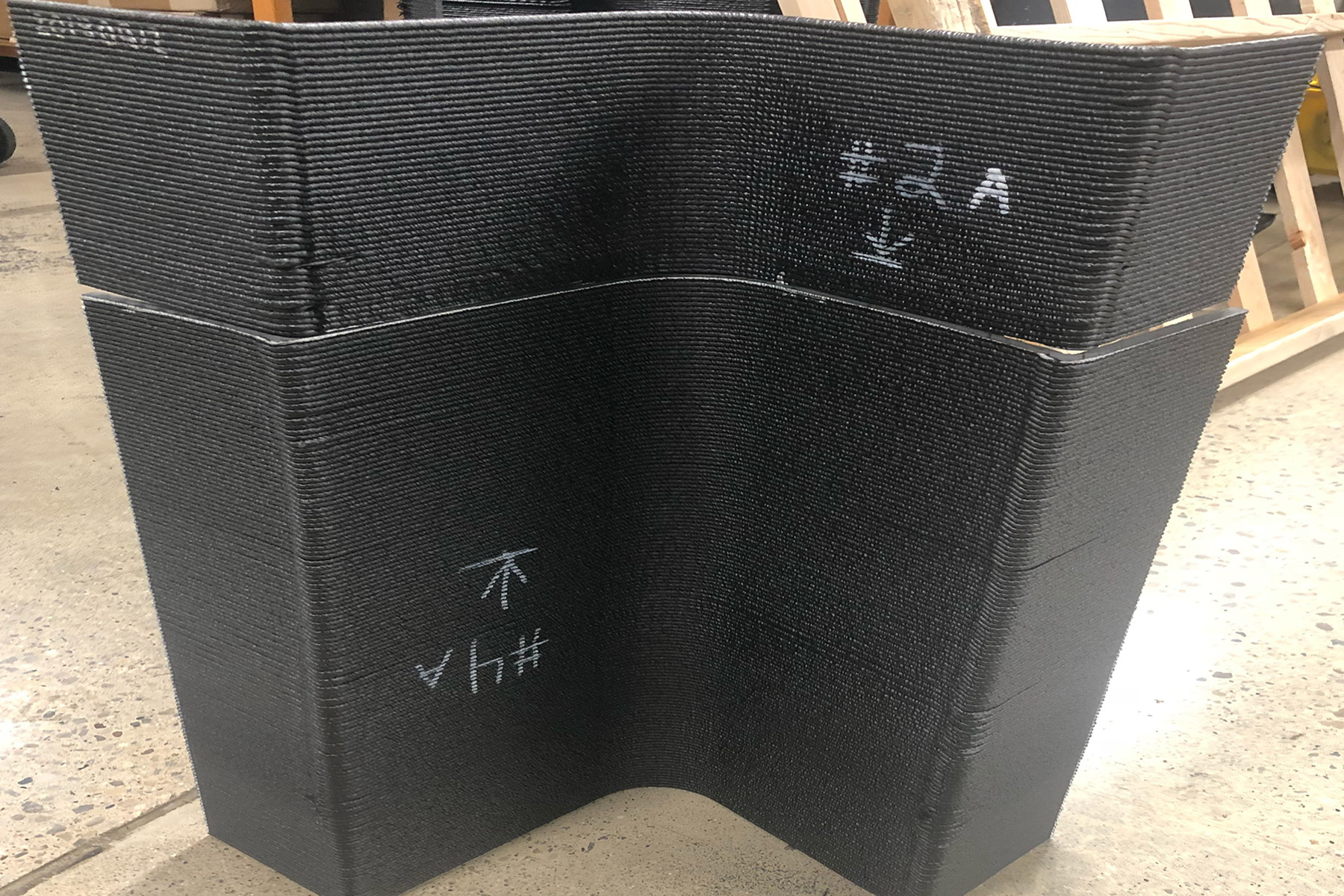
На верхнем изображении показана одна часть правой половины субшкалы, напечатанного BAAM, с красными линиями, обозначающими линии разреза после печати. На нижнем изображении показана правая половина инструмента после соединения секций. Фото:Исследовательский институт Дейтонского университета.
Формат материала представлял собой мат из рубленого углеродного волокна, пропитанного усиленной эпоксидной смолой Hexcel 8552, плотностью 2000 грамм на квадратный метр / 59 унций на квадратный ярд. Этот материал часто используется для изготовления композитной оснастки из-за его почти изотропных свойств, которые позволяют производить обработку после пресс-формы без перемещения инструмента, которое в противном случае могло бы быть вызвано релаксацией остаточных напряжений.
Учитывая, что ядро будет напечатано на принтере Cincinnati Inc. BAAM 1000 в компании Additive Engineering Solutions (Акрон, Огайо, США), и учитывая, что UDRI и Cincinnati имеют значительный опыт работы с высокотемпературным термопластичным полиэфиримидом (PEI), они выбрали 20% короткий PEI, армированный углеродным волокном (Thermocomp EX004EXAR1 Ultem) от SABIC, (Эр-Рияд, Саудовская Аравия), для печати сердцевины почти чистой формы. (Наличие углеродных волокон стабилизирует полимер во время печати и предотвращает его оседание; в готовой структуре волокна уменьшают CLTE в направлении печати.) Чтобы снизить затраты, сердцевина функционировала как мастер инструмента, а кожа лица была ламинирована напрямую к сердцевине без клея, но с некоторыми модификациями поверхности сердцевины, которая защищена интеллектуальной собственностью (IP), разработанной в ходе проекта. Такой подход оказался эффективным, без расслоения даже после нескольких термических циклов.
Конденсированное производство
При традиционном изготовлении оснастки из углепластика для аэроструктуры сначала создается недорогая мастер-модель. Обычно это включает склеивание блоков инструментальной доски в печи или автоклаве, а затем механическую обработку монолитной конструкции до желаемой геометрии детали. Затем инструментальный материал складывается, упаковывается в мешки и отверждается на эталоне в автоклаве. После извлечения из формы и очистки к инструменту приклеивается несущая конструкция, и поверхность инструмента снова обрабатывается для обеспечения хорошего геометрического допуска и качества поверхности.
Используя гибридные инструменты AM, команда разработала сжатый производственный процесс, чтобы сократить время выполнения заказа и снизить затраты. Сначала был напечатан сердечник почти чистой формы (мастер инструмента) (из короткого углеродного волокна / PEI). Затем инструментальный препрег из углепластика был нанесен непосредственно на обе стороны сердечника (с горячим удалением массы между первым, четвертым и седьмым слоями в соответствии с рекомендациями поставщика). Затем вся конструкция была помещена в вакуумный мешок и отверждена в автоклаве.
Краткий производственный процесс субшкалы C-образного лонжерона.
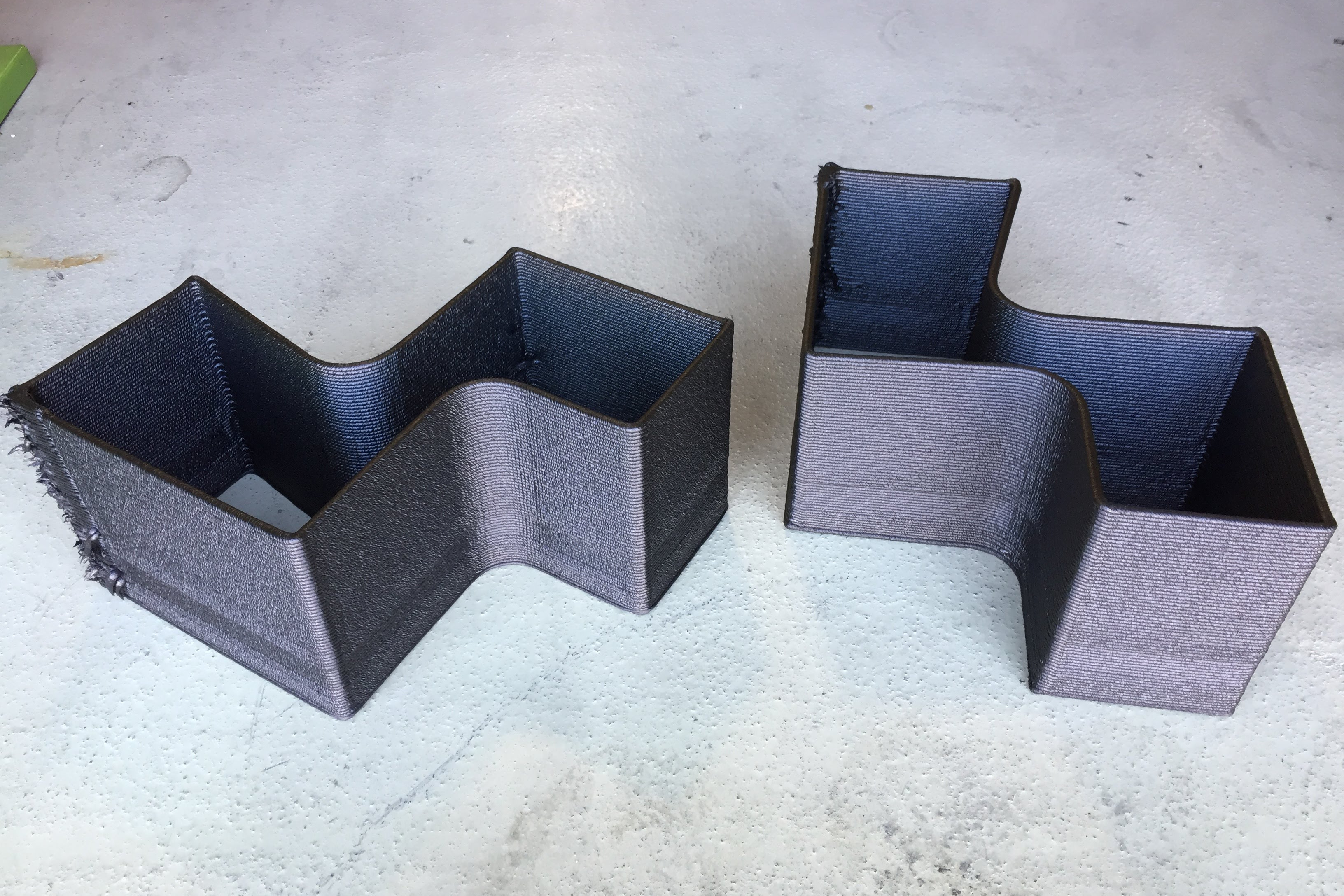
Шаг 2:Разрежьте отпечаток BAAM посередине, на левую и правую половины.
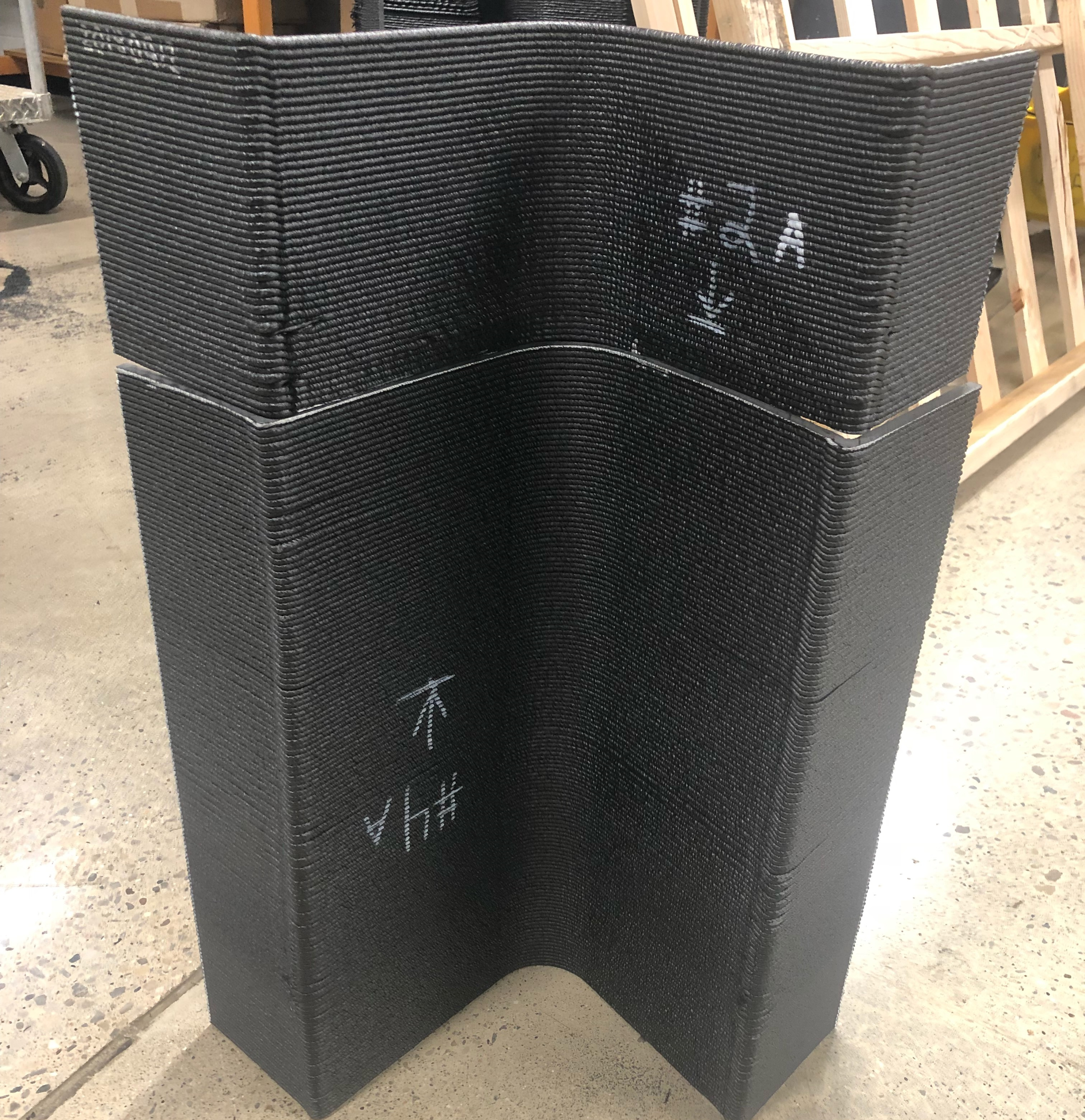
Шаг 3:приклейте печать BAAM до нужной длины и дайте ей застыть.
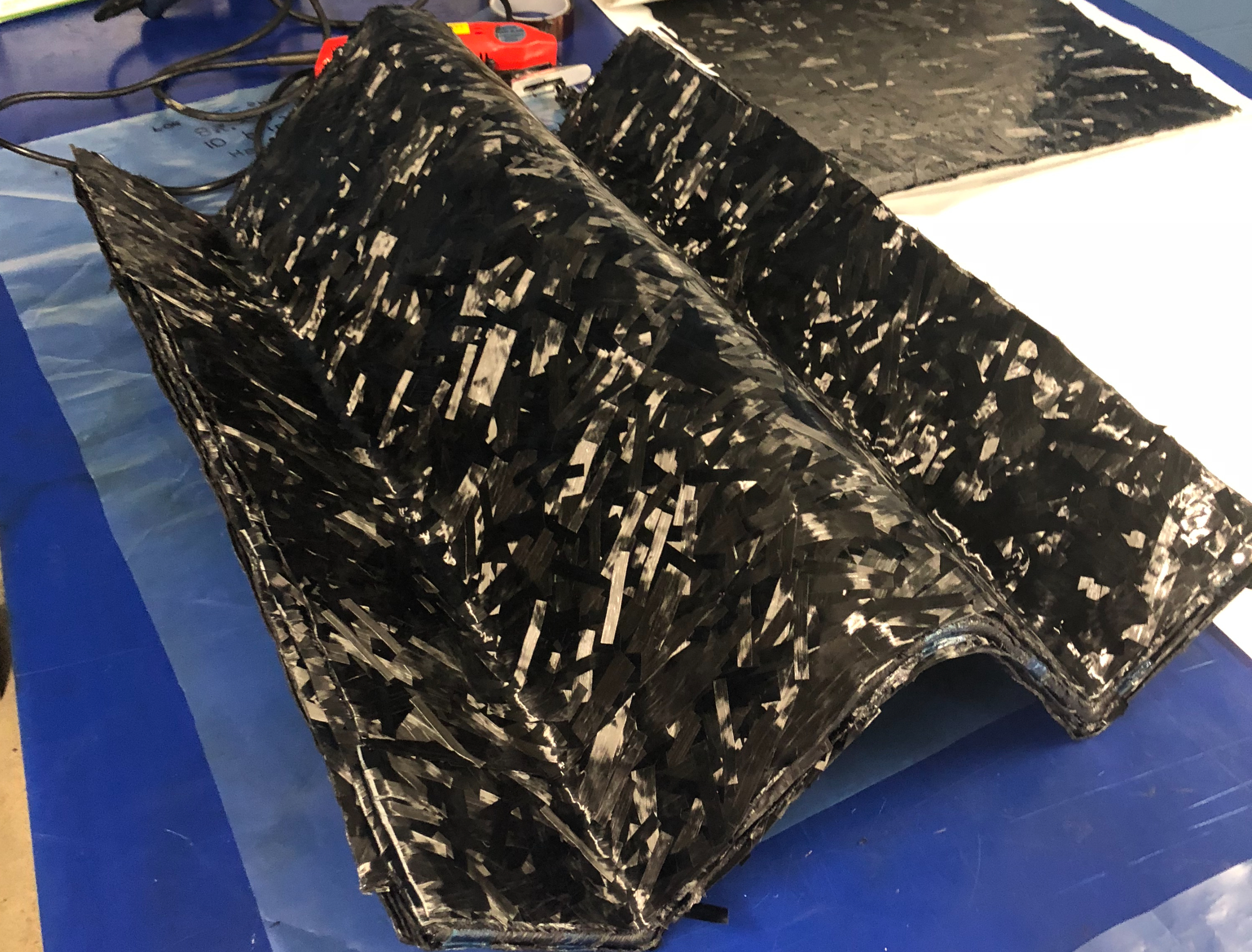
Шаг 4:Ламинируйте инструментальный препрег с обеих сторон сердечника горячим способом в соответствии с инструкциями производителя.
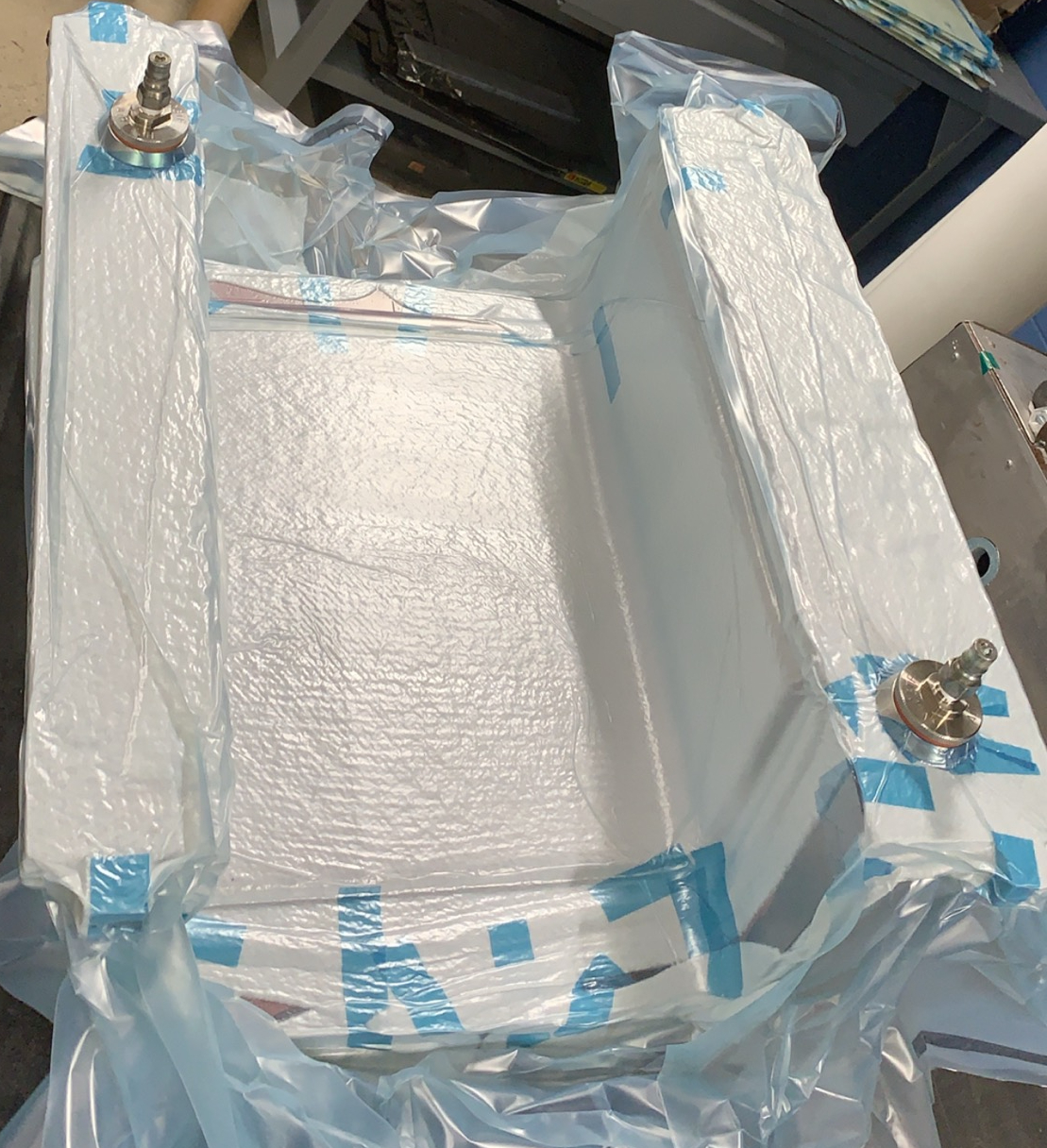
Шаг 5:Вакуумный мешок и отверждение в автоклаве.
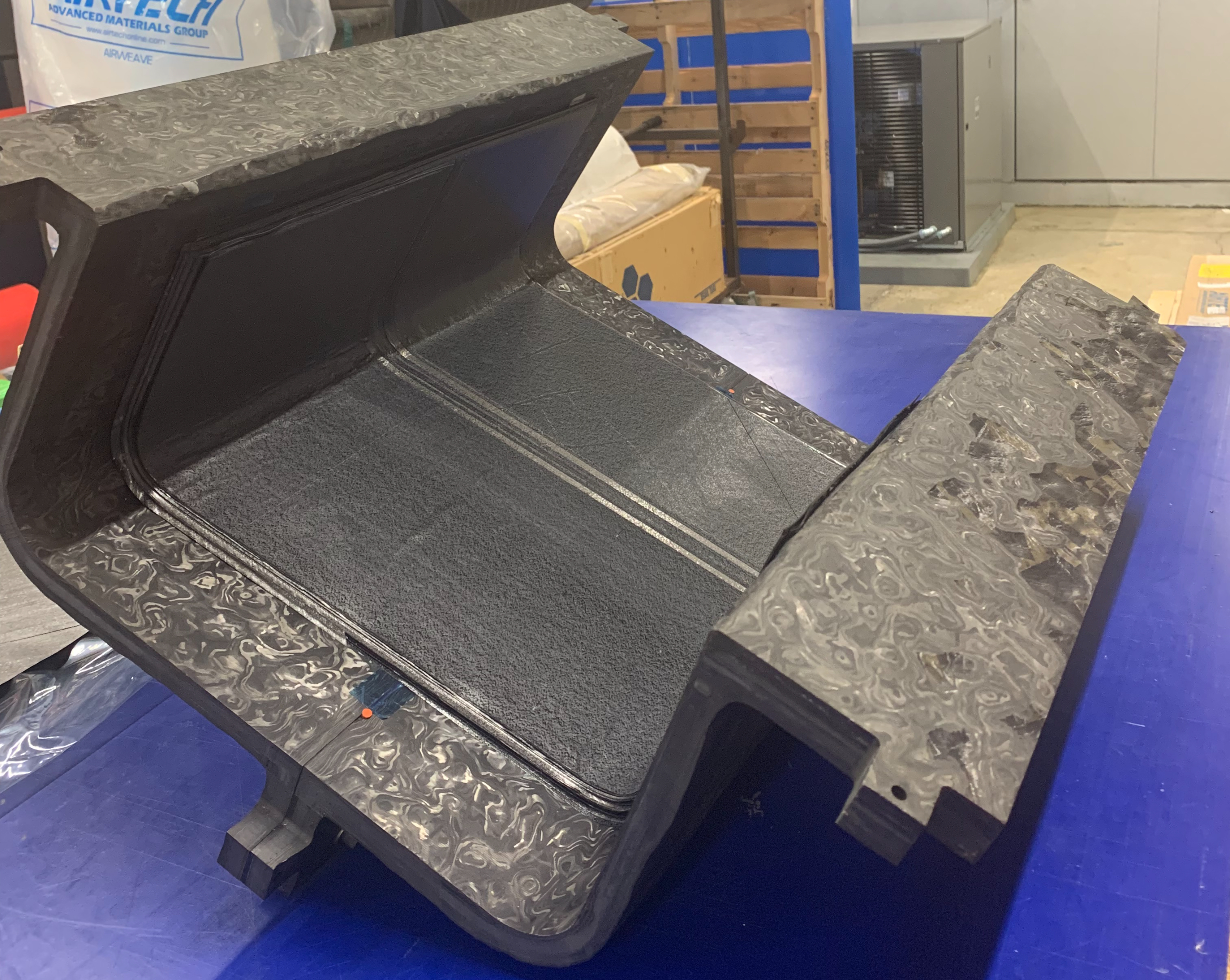
Шаг 6:Инструмент машинного отверждения для получения окончательных размеров и отделки поверхности.
Предыдущий СледующийВо время отверждения ламината была достигнута хорошая адгезия между сердцевиной PEI и эпоксидной оболочкой, поэтому клей не требовался. Покрытия из углепластика не только непористые и более долговечные, чем сердечник AM, они также физически ограничивают движение сердечника во время скачков температуры из-за их гораздо более низких значений CLTE. Только однократное отверждение и одна операция обработки - основные расходы при традиционном инструментальное производство - нужны были для получения окончательных размеров и чистоты поверхности. Кроме того, не требовалось подкладки из-за многослойной конструкции и формы инструмента, которые включали возвратные фланцы в верхней части формы для обеспечения поперечной жесткости и болтовое соединение в центре формы для обеспечения жесткости по вертикали, что исключает операцию соединения. P>
Первоначальные проблемы
Исследователи столкнулись с несколькими управляемыми проблемами, связанными с новым процессом.
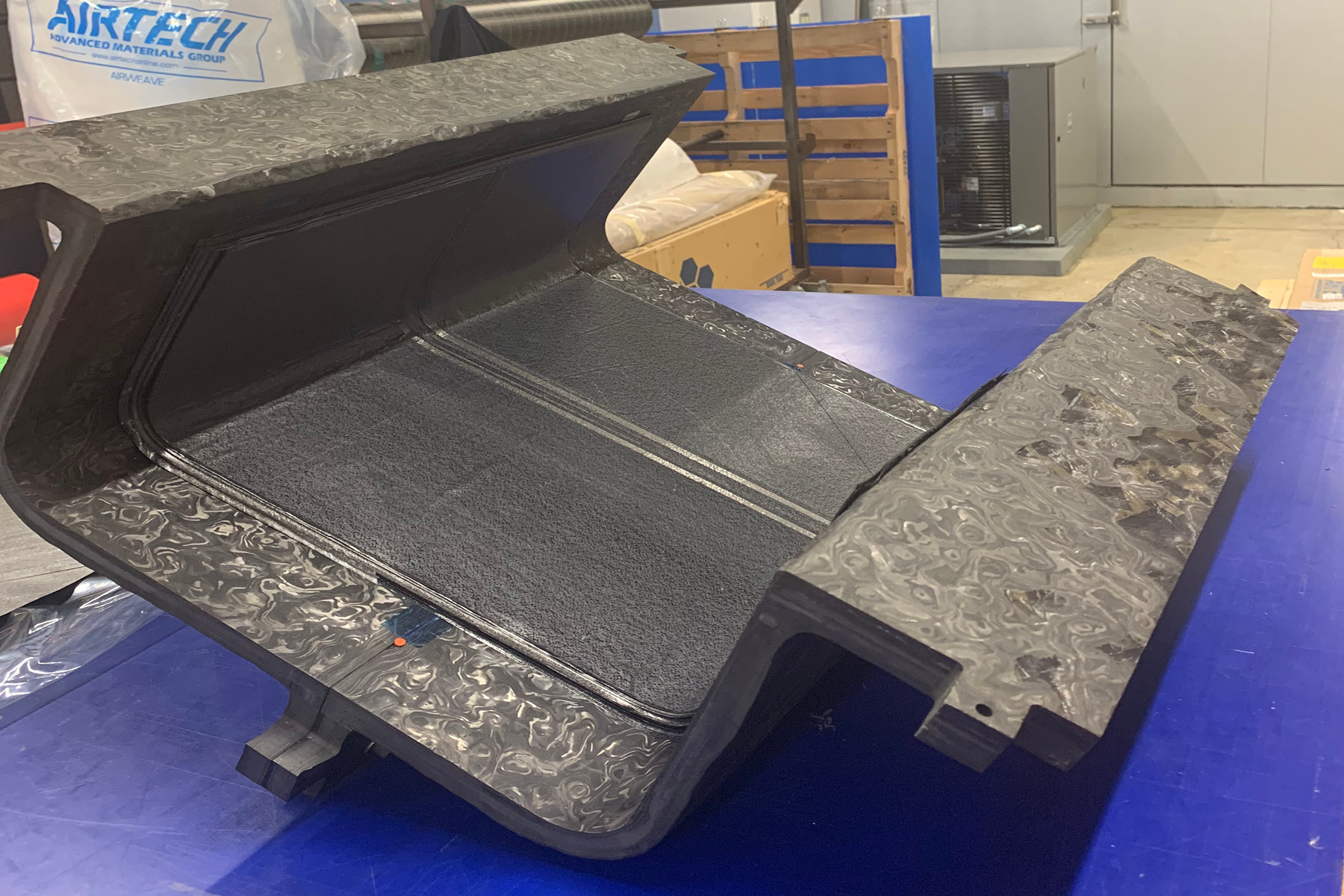
Для простоты изготовления на BAAM предпочтительным направлением изготовления сердечника была печать поперечного сечения в виде вертикальной сборки. Для инструмента диаметром 0,6 метра это не было проблемой; однако для более крупного инструмента на 3,3 метра было больше, чем BAAM 1000 мог печатать вертикально. Из-за ограниченного пространства для печати по оси Z в принтере исследователи решили уменьшить вдвое оба инструмента субшкалы по длине, а затем снова разделить их на левую и правую части (чтобы решить проблемы с подрезкой лонжерона и упростить демонтаж).
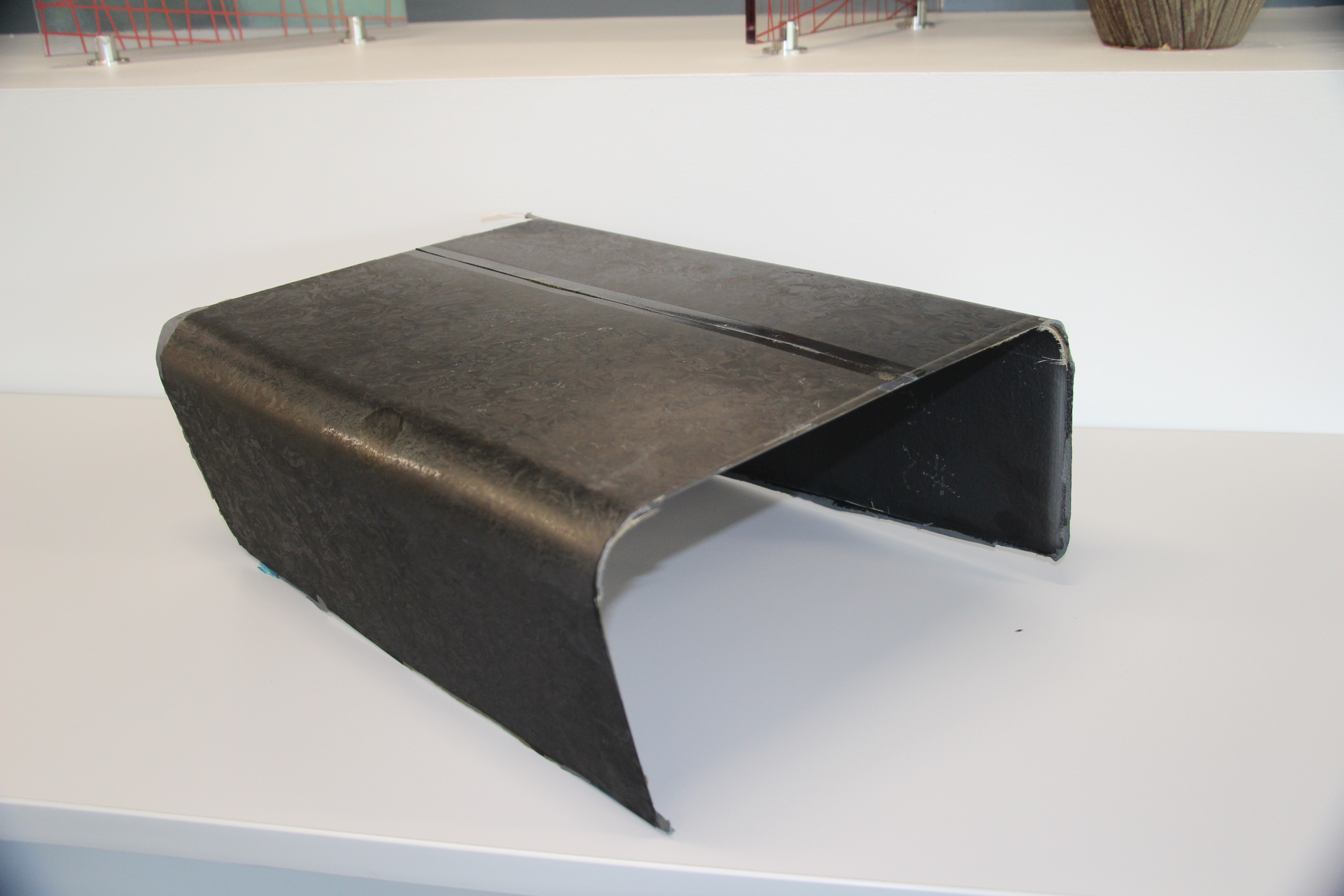
Чтобы повысить эффективность печати, части инструментов печатались вплотную друг к другу, а затем разрезались на правые и левые части. Для достижения длины 3,3 метра две правые секции были склеены вместе, а затем две левые секции с помощью эпоксидного клея Loctite EA9394 от Henkel Corp. (Роки-Хилл, Коннектикут, США). Команда оставила ядро AM без обработки, чувствуя, что это имеет решающее значение для достижения низких затрат на инструмент и сокращения времени выполнения заказа, а также для создания механической блокировки между сердечником AM и оболочкой из углепластика с каждой стороны. Задняя сторона каждой половины инструмента была покрыта пятью слоями препрега, а передняя сторона была покрыта девятью слоями, чтобы обеспечить дополнительный материал, который можно было удалить во время обработки после отверждения.
Предварительные результаты
В дополнение к контролю CLTE сердцевины AM препрег обеспечивал поверхность без ямок, которая сохраняла целостность вакуума без необходимости использования герметика / покрытия. Этот подход оказался настолько успешным, что позволил использовать конструкцию, состоящую из нескольких частей, герметизированную прокладкой, что, по мнению исследователей, ранее не было продемонстрировано в инструментах AM, используемых при высоких температурах. Кроме того, значительно уменьшилась масса инструмента; инструмент подшкалы составлял одну треть веса, рассчитанного для сопоставимого инварного дизайна. Более легкие инструменты из углепластика не только легче обрабатывать и хранить на стеллажах, но и требуют более коротких циклов нагрева / охлаждения в автоклаве. На инструменте для формования полноразмерного С-образного лонжерона это преимущество в весе может иметь значение между превышением или превышением предельных значений веса портала / крана в некоторых производственных помещениях.
Важно отметить, что стоимость 0,6-метрового гибридного инструмента была рассчитана во время производства с использованием стандартных отраслевых расценок на оплату труда и составила 24 136 долларов США с примерно 50/50 разделением между затратами на обработку и затратами на печать / ламинирование. Напротив, идентичный инварный инструмент был оценен в 46 775 долларов США - почти 50% экономии. Затраты на инструмент длиной 3,3 метра не являются полными, но ожидается, что они дадут примерно 30% экономии в расчете на единицу длины, так как затраты на материалы / печать растут линейно, но затраты на обработку имеют экономию на масштабе, которая снижает их влияние. Гибридный подход позволил создать инструменты, которые отвечали эксплуатационным требованиям Airbus и Northrop Grumman и считаются жизнеспособной альтернативой Invar для быстрого прототипирования или малоиспользуемого инструментария. Исследование срока службы инструмента не входило в данное исследование, но, вероятно, оно значительно расширится за пределы продемонстрированных 12 циклов.
Программа была продлена с 18 до 30 месяцев, но все еще есть области, требующие дополнительных исследований, например, понимание того, насколько окончательная геометрия сердечника после печати отличается от предсказанной в моделях CAE. Команда также хочет повысить точность прогнозирования, чтобы в критических областях было добавлено достаточное количество слоев, чтобы гарантировать отсутствие сквозных отверстий во время обработки. Тем не менее, команда сочла это успешным проектом с большими возможностями для будущих инструментов LFAM.
«Northrop Grumman с нетерпением ожидает создания демонстрационной части 3-метрового лонжерона с использованием гибридного инструмента длиной 3,3 метра, созданного UDRI, и нашего собственного процесса автоматизированного формования ребер жесткости (ASF) для оценки долговечности и стабильности размеров инструмента», - добавляет Верн Бенсон, технический специалист Northrop Grumman.
Смола
- Evonik, Evolve Additive Solutions для разработки материалов для 3D-печати для процесса STEP
- Henkel предлагает платформу материалов для аддитивного производства
- Essentium и Lehvoss сотрудничают в разработке материалов для аддитивного производства
- Новый термостабилизированный нейлон 6 для гибридных и электрических силовых агрегатов
- Trelleborg объявляет о новом дистрибьюторе инструментальных материалов
- UAMMI, Impossible Objects создают составные части для ВВС США
- Партнер Victrex и Bond для 3D-печати деталей из PAEK
- AeroLas исследует новую технологию прядения термопластичной гибридной пряжи
- Советы по формам для 3D-печати
- Минимизация времени обработки больших деталей