Конструкция лопаток гидроэлектрической турбины, приводимой в движение композитами
Термин «гидроэлектроэнергия» часто ассоциируется с огромными операциями, управляемыми специально построенной инфраструктурой, такой как системы плотин и большие турбины с традиционно металлическими лопастями турбины на основе пропеллера. Однако во многих регионах не хватает новых мощностей для крупных мощных гидроэлектростанций. В то же время продолжает расти спрос на более дешевые возобновляемые источники энергии.
Министерство энергетики США (DOE) в своем отчете «Видение гидроэнергетики» за 2018 год, в котором излагается текущее состояние гидроэнергетики в Соединенных Штатах и ее цели на будущее, предсказало рост гидроэнергетического рынка США - от 101 гигаватт (ГВт). энергетической мощности в 2018 году до потенциальной мощности почти 150 ГВт в 2050 году - потребуются новые передовые технологии, которые могут обеспечить больше энергии при меньших затратах.
По словам Даррена Рена, генерального менеджера Kinetic NRG (Голд-Кост, Австралия), одним из потенциальных решений могут быть гидроэлектрические генераторы меньшего размера, улавливающие неиспользованную энергию из водных систем с низким расходом, таких как оросительные каналы и ручьи. Компания Kinetic NRG, основанная в 2016 году покойным основателем Полом Камиллери, является частной компанией по возобновляемым источникам энергии, специализирующейся на разработке новых гидроэнергетических технологий для производства недорогой и надежной электроэнергии.
Первая технология компании называется системой генератора гидрокинетической энергии (HEG), которая имеет диаметр 1,5 метра и мощность до 30 киловатт (кВт) при расходе воды 2,0 метра в секунду. Этот результат делает ее «микро» гидроэнергетической системой в соответствии с классификационными органами, такими как Министерство энергетики США, которое определяет микросистемы как системы с мощностью до 100 кВт. Предназначенный для прямого использования в реках, оросительных каналах или отводах воды из существующих плотин, HEG разработан для гидроэнергетики с низким напором, то есть «напор» или расстояние между линией ватерлинии и турбиной составляет менее 20 метров.
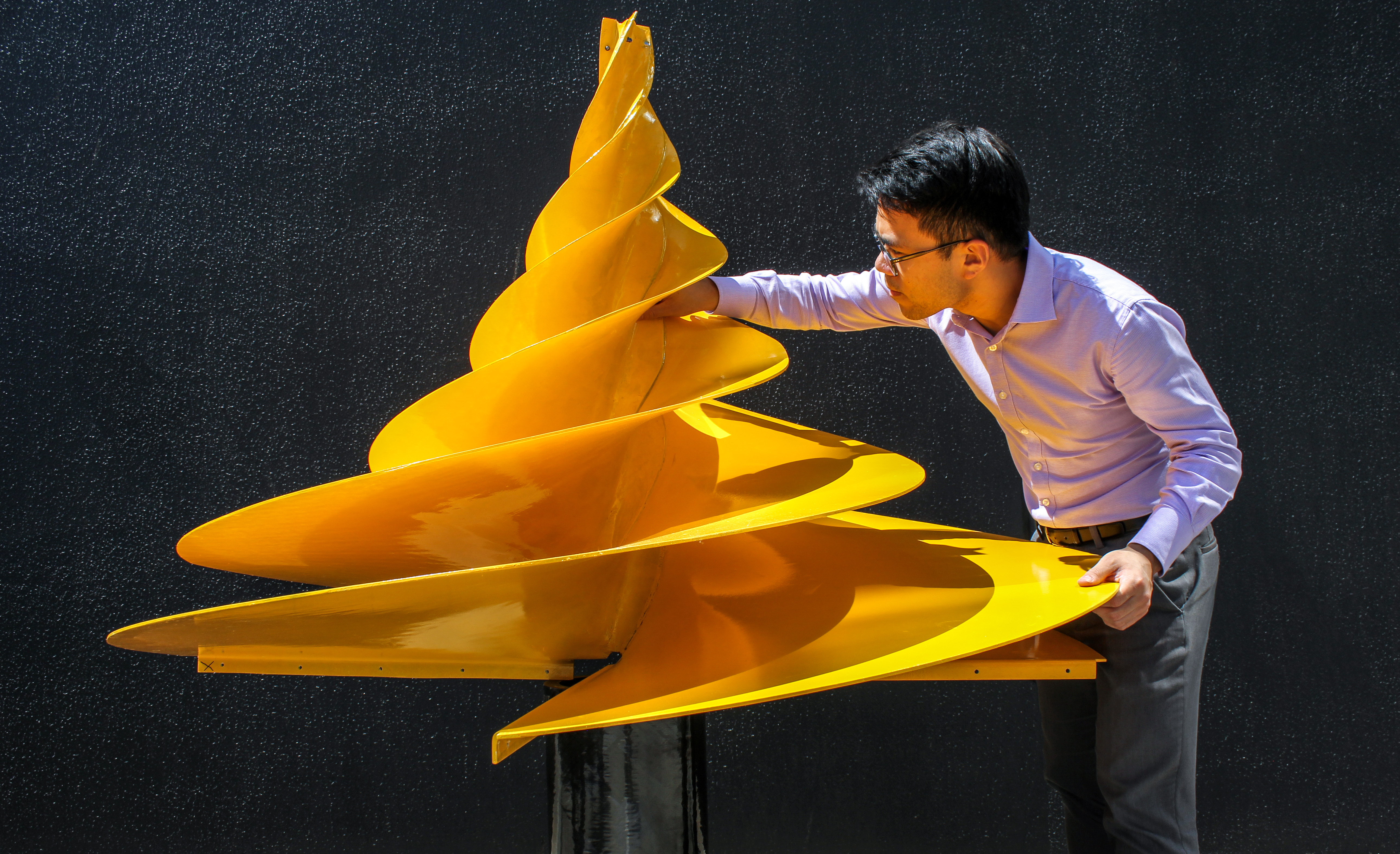
По словам Рена, разработка HEG и его спиральной турбинной лопатки велась около пяти лет. «Это было настоящее путешествие. Дизайн, который у нас сейчас, появился буквально путем проб и ошибок ».
Разработка модульного технологичного лезвия
Первые небольшие модели спиральных лопастей Kinetic NRG были сформированы из металла, но когда пришло время изготовить полномасштабный прототип диаметром 1,5 метра, «мы фактически обнаружили, что не можем этого сделать», - говорит Рен. Идея заключалась в том, чтобы начать с плоского куска металла, а затем сформировать или выковать набор спиралей, исходящих из центра. «Мы просто не могли найти способ получить доступ к определенным точкам детали, чтобы создать необходимую нам силу», - объясняет он.
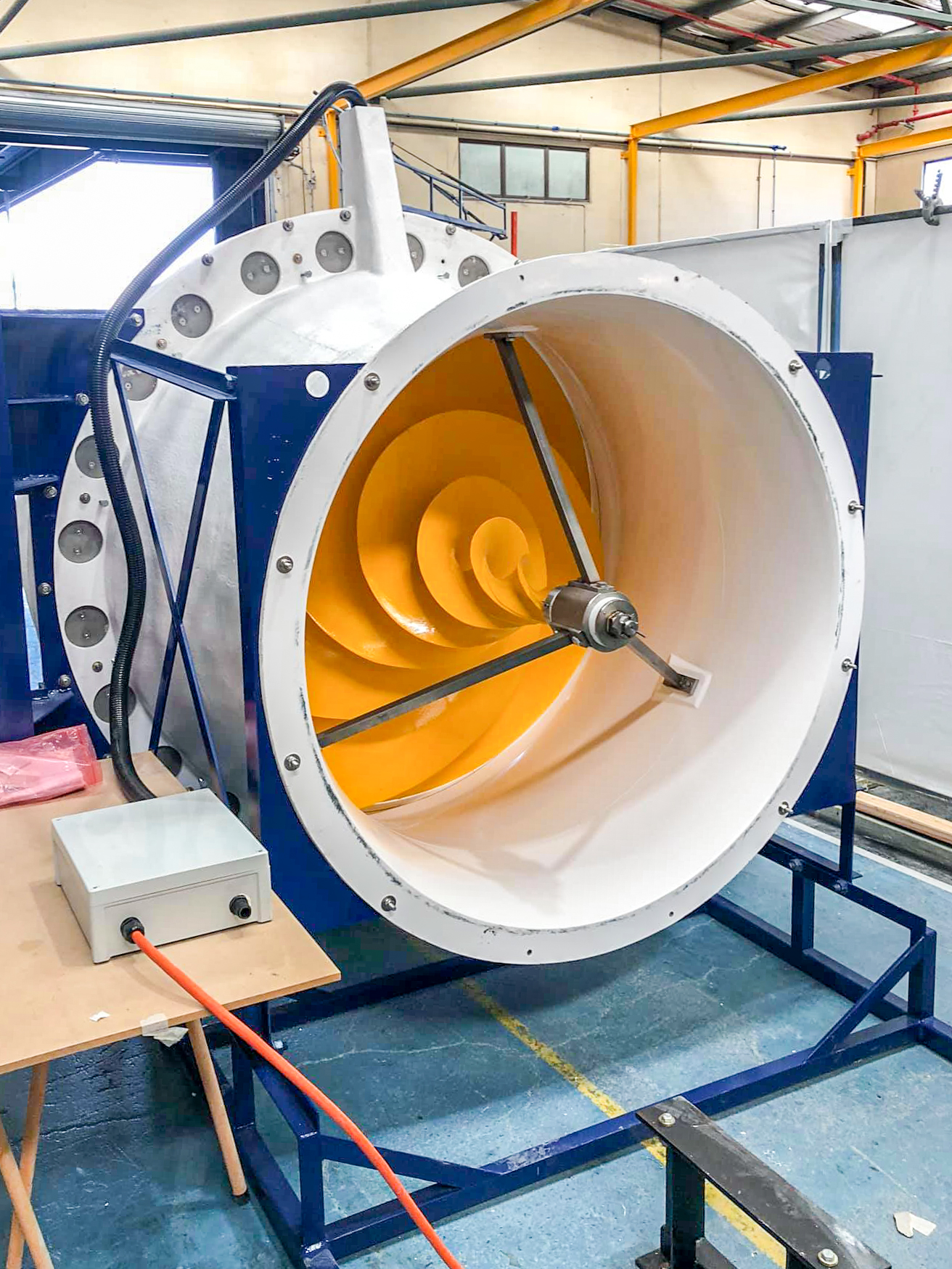
В конечном итоге компания отказалась от металлических изделий, но не от самого дизайна. Рен говорит, что Kinetic NRG сотрудничал с местным университетом, чтобы изучить альтернативные технологии производства и материалы, такие как нейлон или керамику, и начал переговоры с компаниями, занимающимися 3D-печатью, чтобы увидеть, может ли аддитивное производство быть жизнеспособным вариантом. Однако решения, обеспечивающего правильное сочетание технологичности и механических свойств, не нашлось. Наконец, после трехлетнего путешествия, Kinetic NRG была представлена через сеть поставок команде инженерной компании Advanced Composite Structures Australia (ACS-A, Мельбурн), которая специализируется на разработке и производстве небольших объемов дорогостоящих материалов. -добавленные композитные компоненты для различных конечных рынков.
Рен называет то, что произошло дальше, «совпадением мнений», объясняя, что Kinetic NRG работала с Полом Фальзоном, генеральным менеджером ACS-A, и его командой над различными методами производства и проектирования детали с использованием композитных материалов - материалов, которые были известны ACS-A. исходя из опыта, сможет удовлетворить требования к форме, весу и жесткости, необходимые для Kinetic NRG.
Инновационная форма лезвия была ключевой задачей проекта, поскольку механические требования к лезвию, по словам Рена, основывались на стандартах, установленных Министерством энергетики США и Международной электротехнической комиссией. Остальные компоненты системы - передача, управление питанием, связь и т. Д. - представляют собой стандартные готовые продукты, которые, как известно, соответствуют всем необходимым нормам.
По словам Фальзона, ACS-A сначала оценила попытки использования металла в конструкции лезвия, а затем определила, как добиться необходимой формы, допусков по размерам и веса лезвия. Лезвие также должно было выдерживать воздействие водной среды и быть достаточно жестким, чтобы поддерживать стальной вал турбины, к которому он прикреплен. Команда ACS-A начала с оригинальной металлической конструкции и «реконструировала» композитное лезвие из стекловолокна, чтобы оно соответствовало исходной жесткости, говорит Фалзон. Однако при переходе от сварной металлической конструкции к композитному ламинату необходимо было внести некоторые изменения в конструкцию. Как объясняет Фальзон:«Мы сделали шаг назад и спросили:« Хорошо, если мы собираемся в полной мере использовать преимущества композитных материалов, как это выглядит? »»
После нескольких итераций и обсуждений текущая конструкция, которая приняла форму, состоит из четырех идентичных композитных лопастей, которые сцепляются друг с другом, образуя окончательную спиральную форму. «Композитное лезвие на самом деле толще, чем стальная конструкция, но легче из-за меньшей плотности материалов, с которыми мы работаем», - говорит Фалзон. «Толщина также означает, что мы получаем намного большую жесткость на изгиб по сравнению со стальной конструкцией, поэтому в целом вы получаете гораздо более жесткий продукт».
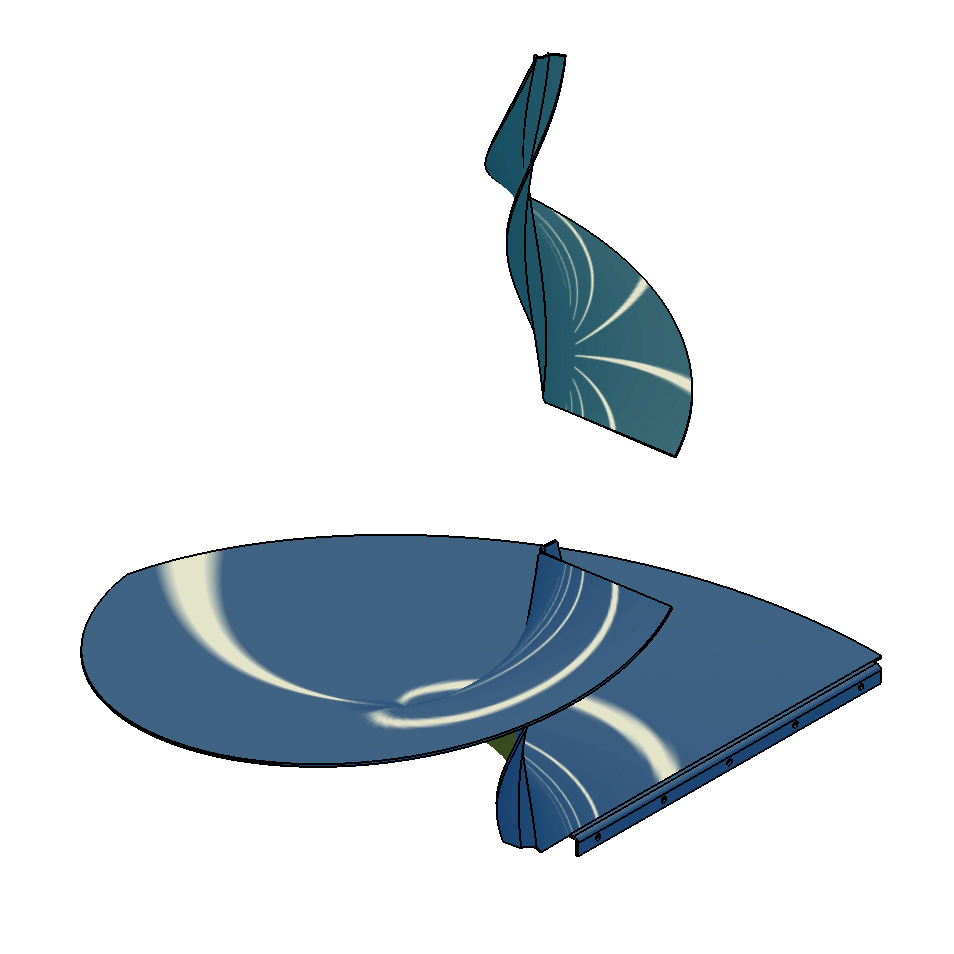
Перевернутая оснастка
По словам Фальзона, разработка формы для инструментов была самой сложной частью процесса. Команда ACS-A оценила форму исходного узла лопасти с помощью программного обеспечения CATIA от Dassault Systèmes (Уолтем, Массачусетс, США). Это привело к разработке поверхностей лезвий и разработке концепций инструментов. «Когда вы смотрите на детали в том виде, в каком они есть сегодня, то на самом деле они сделаны в перевернутом виде. Чтобы создать инструмент, модель лезвия пришлось перевернуть, и это странно, пока вы не увидите реальный инструмент, когда он появится. Это довольно сложно, - говорит Фальзон. Он объясняет, что оснастку пришлось перевернуть, «чтобы обеспечить необходимую чистоту поверхности на стороне лопасти, подверженной воздействию потока воды», и чтобы каждый из изготовленных компонентов лопасти можно было демонтировать как одно целое. Инструменты также должны были быть точными:компоненты блокируемых лопастей должны были точно выровняться в собранном виде друг с другом и с центральным валом турбины. Для прототипа оснастка, поставленная Sykes Australia (Сидней), была изготовлена из недорогой инструментальной пасты, нанесенной на пенопласт и затем обработанной на станке с ЧПУ для придания окончательной формы.
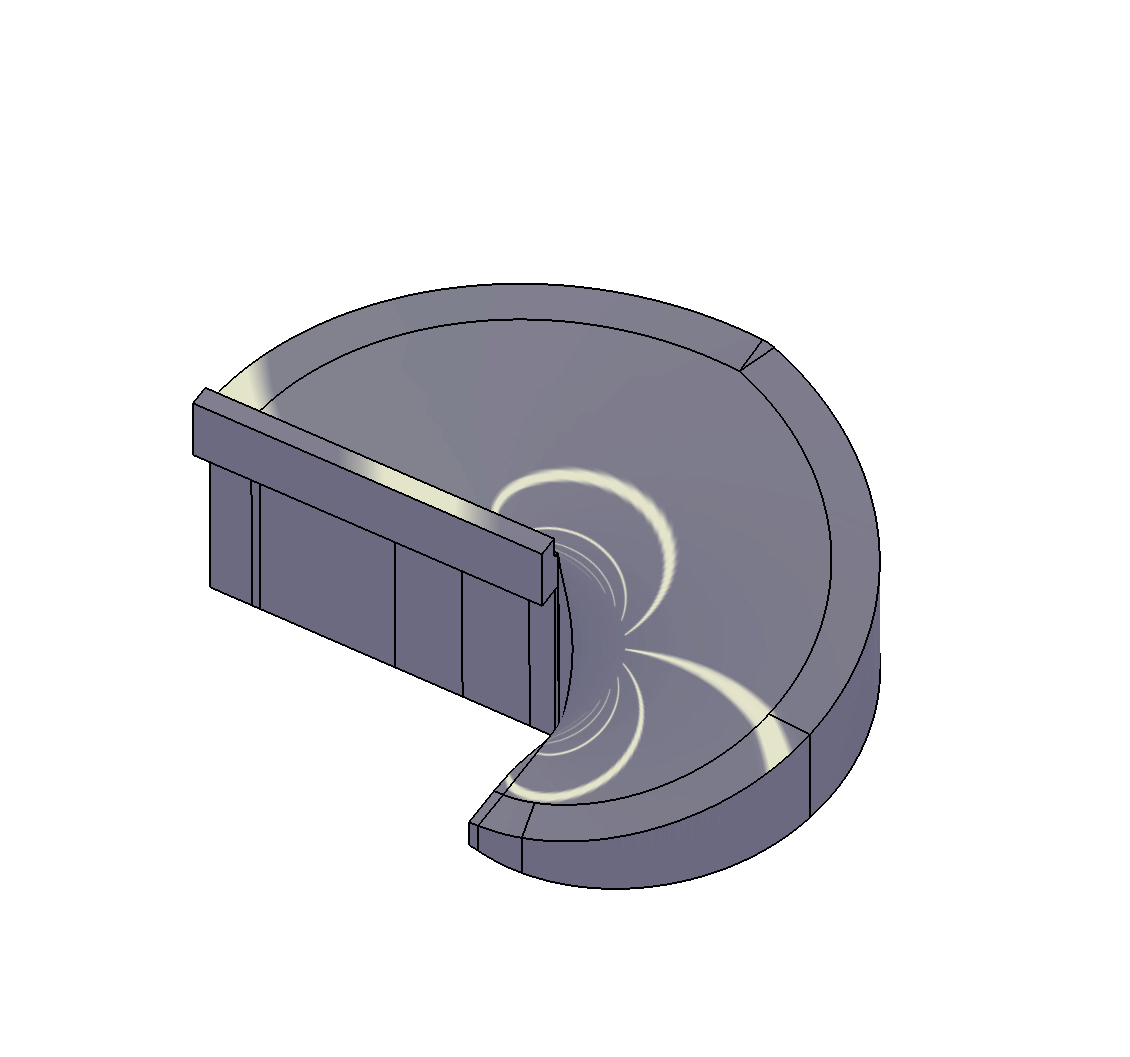
После разработки инструмента текущий полномасштабный прототип лезвия был сконструирован из стекловолоконной неотжимной ткани (NCF) и эпоксидной смолы, изготовлен вручную и отвержден при комнатной температуре с последующим последующим отверждением в печи при повышенной температуре и нанесением. краски морского класса. Фальзон отмечает, что материалы были выбраны таким образом, чтобы удовлетворить как структурные, так и стоимостные требования к детали. Блокируемые подкомпоненты склеены клеем - предпочтительнее механического крепления для лучшего контроля и точности размеров при сборке. «Настоящая уловка, - говорит он, - состоит в том, чтобы убедиться, что лезвия могут блокироваться, но как только мы ламинируем все это и склеиваем вместе, он образует очень жесткий узел, который обеспечивает необходимые структурные и гидродинамические характеристики формы».
Цифровой анализ жесткости конструкции и других механических свойств был выполнен с использованием инструментов от MSC Software (Ньюпорт-Бич, Калифорния, США). «Эта система намного эффективнее, легче и способна выполнять больше работы, чем исходная конструкция», - добавляет Фальзон.
Переход к коммерческому производству
По словам Рена, первоначальная цель производства Kinetic NRG будет составлять 950 единиц в течение трехлетнего периода, а затем увеличится до нескольких тысяч в год. По словам Рена, среди потенциальных клиентов могут быть частные лица и компании, энергетические компании и муниципалитеты - широкий спектр, что подчеркивает универсальность концепции HEG. По его словам, системы могут быть установлены как «мини-гидроэлектростанции» в оросительных каналах или размещены ниже по течению от существующих гидроэлектрических генераторов для выработки энергии из недостаточно используемых стоков, или в качестве дополнительной энергии для удаленных населенных пунктов или предприятий.
В настоящее время полномасштабный прототип ГЭН проходит механические испытания в воде; тем временем крупномасштабные производственные процессы оцениваются для коммерческого производства.
ACS-A планирует продолжить доводку конструкции лопасти по мере необходимости в зависимости от результатов механических испытаний и требований для наиболее экономичного производства. В частности, Фальзон говорит, что ACS-A изучает автоматизированные процессы предварительного формования, «чтобы мы могли получить нужную форму с минимальными затратами ручного труда», с последующим формованием с переносом легкой смолы (L-RTM) или другим высокоскоростным процессом.
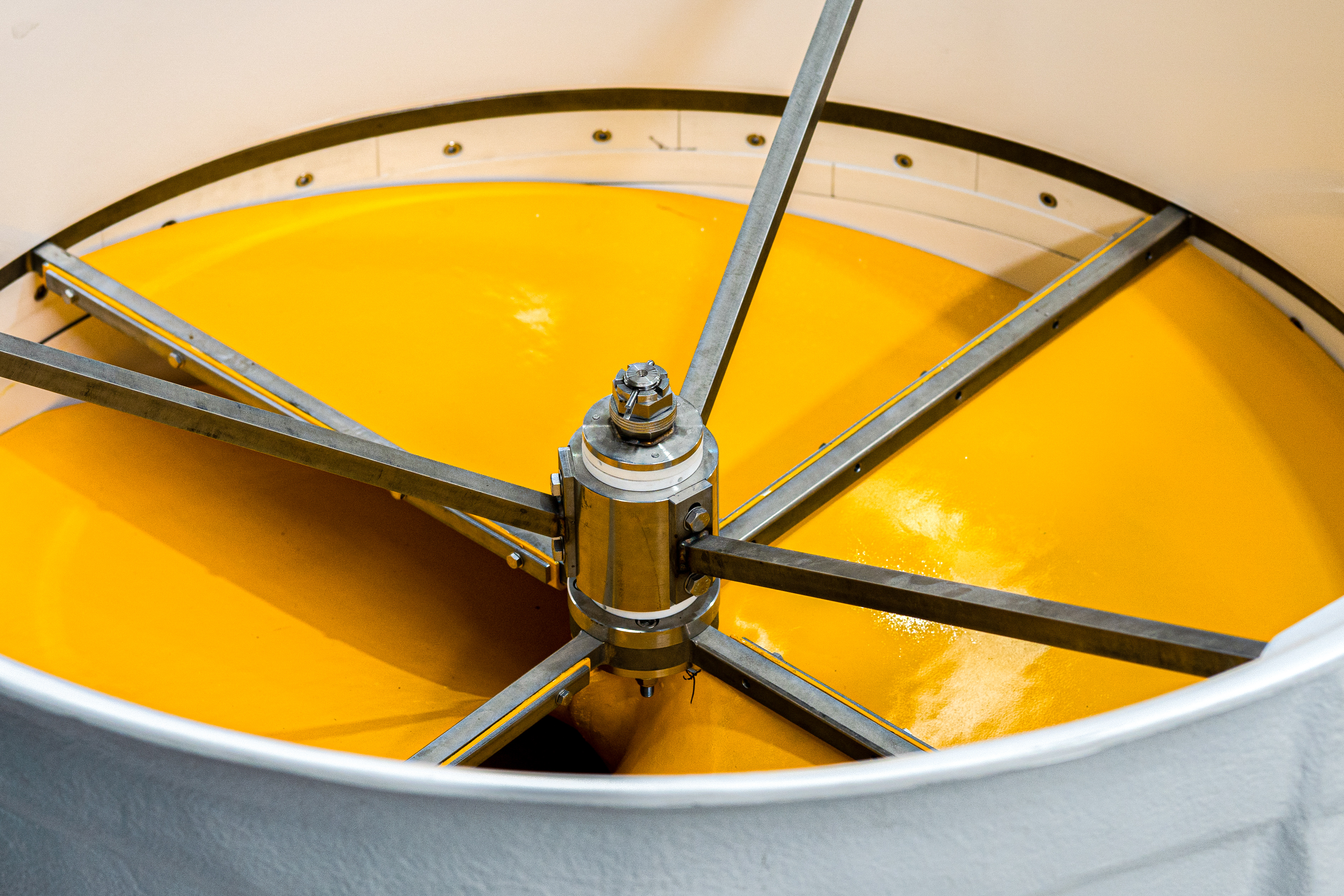
Методы сборки турбины также находятся в стадии оценки, цель, по словам Рена, состоит в том, чтобы подкомпоненты лопаток производились модульно и собирались на месте, чтобы избежать затрат и проблем при отгрузке целых полномасштабных агрегатов, создавая при этом возможности для трудоустройства на местном уровне и снижая затраты на установку. . Чтобы сделать это возможным, ACS-A может потребоваться изменить способ блокировки лезвий и количество подкомпонентов в каждой сборке. «У нас по-прежнему будут полные лопасти в их первоначальной форме, которые по-прежнему будут ключевой частью, - говорит Рен, - но мы можем изменить место перехода, чтобы сделать ту же форму у меньшего количества компонентов для упрощения. монтаж на месте ».
Обе компании также оценивают преобразование металлических компонентов турбины в композиты, чтобы снизить вес всей сборки. «Мы будем использовать стекло там, где это целесообразно, и углеродное волокно, где это необходимо, но в конечном итоге нам нужно достичь определенной цены на технологию, чтобы сделать стоимость производства энергии для системы конкурентоспособной», - говорит Фалзон.
По мере того, как процесс проектирования и производства приближается к оптимизации, следующей проблемой, по словам Рена, будет обеспечение правильных инвестиций и производственных партнерств для масштабирования до коммерческих объемов.
Смола
- Эталонный дизайн смарт-значка Особенности Bluetooth SoC
- Решение проблем проектирования при прецизионном измерении энергии постоянного тока
- Megger жертвует программе энергии ветряных турбин Iowa Lakes
- Соображения и ограничения при проектировании системы передачи энергии
- CompositesWorld SourceBook 2022
- Инициатива CETEC, созданная для коммерциализации технологии переработки полностью композитных лопастей ветря…
- Сплошные композиты, Siemens Energy применяет высокоэффективные материалы для генераторов энергии
- Композиты как подкрепления авто-тела
- Высокопроизводительные композиты в Израиле
- Понимание гидроэнергетики