Аддитивное производство делает большие морские конструкции более универсальными
Возможность быстро создавать различные итерации деталей - без необходимости разрабатывать или покупать дорогостоящие специальные инструменты - вот почему аддитивное производство (AM) так часто используется при прототипировании деталей. Однако по мере того, как материалы и технологии печати продолжают совершенствоваться, все больше компаний могут расширять скорость и универсальность AM до деталей конечного использования, особенно для краткосрочных или одноразовых приложений, где возможность быстро создавать новые дизайны является преимуществом. .
Недавно две компании продемонстрировали, что композитные технологии AM могут быть полезными решениями для настройки крупных морских сооружений, таких как автономные подводные аппараты (АНПА) и моторные лодки.
Широкоформатная 3D-печать для настраиваемого производства АПА
Автономные подводные аппараты - это тип беспилотных роботизированных транспортных средств, способных перемещаться под водой без физического подключения к лодке или дистанционного управления со стороны человека-оператора, и часто они оснащены камерами или датчиками для различных случаев использования в оборонных целях, при исследованиях океана или в морских исследованиях. Как правило, внешние корпуса АНПА состоят из одного большого металлического сосуда под давлением или построены из термоформованного пластика или композитов. Однако оба варианта требуют разработки и покупки специального инструментария, который может быть дорогостоящим и ограничивает количество настроек, которые могут быть выполнены для клиентов AUV. Производитель АНПА Dive Technologies (Куинси, Массачусетс, США) обнаружил, что композитная 3D-печать снимает многие ограничения традиционного производства.
В 2018 году соучредители Dive Technologies Билл Лебо, Джерри Сгоббо и Сэм Руссо решили создать свою собственную компанию для разработки и запуска нового, более производительного АПА, отвечающего требованиям клиентов в отношении долговечности и большой грузоподъемности.
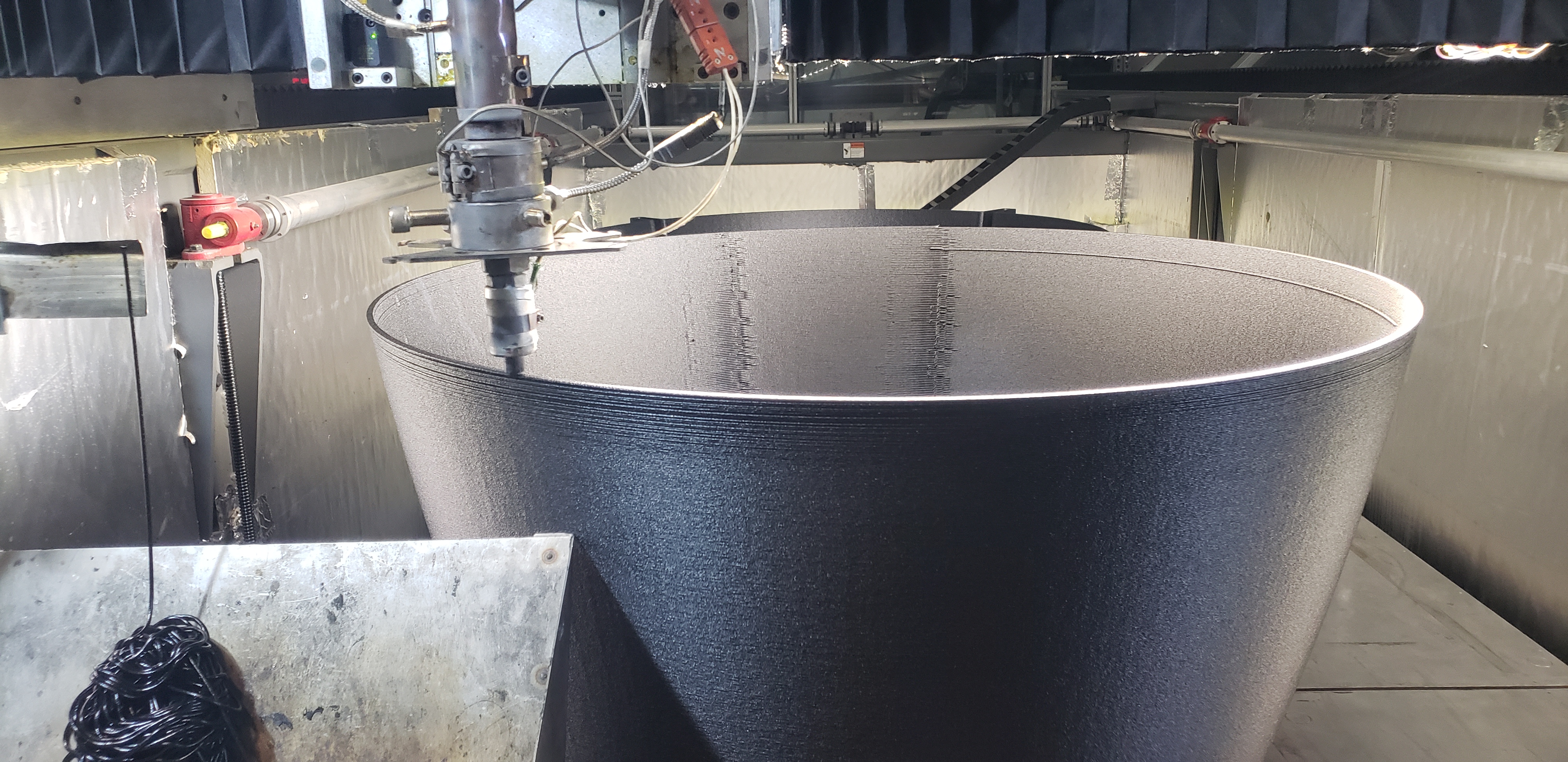
Они и их команда разработали DIVE-LD, коммерческий АПА длиной 19 футов и диаметром 4 фута, способный погружаться на глубину 6000 метров и преодолевать расстояние до 500 миль, неся полезную нагрузку до 1 кубического метра. Первоначально команда предполагала, что в окончательной конструкции автомобиля будет использоваться термоформованный пластик для внешнего корпуса. Чтобы изучить и протестировать дизайн, Dive Technologies поговорила с Национальной лабораторией Ок-Ридж (ORNL, Ок-Ридж, штат Теннеси, США) об использовании 3D-печати для быстрого прототипирования. Через ORNL команда Dive была представлена специалистам по аддитивному производству (LFAM), специалистам по аддитивным инженерным решениям (AES, Акрон, Огайо, США), и начала работать с командой AES над производственным процессом для форм корпуса АПА.
Однако в ходе работы над прототипами, напечатанными на 3D-принтере, Dive Technologies осознала, что LFAM может быстро производить готовые компоненты, а не только прототипы. Компоненты прототипа, напечатанные на 3D-принтере, не только лучше, чем ожидалось, соответствовали требованиям к деталям, но и внедрение AM для серийных автомобилей также снизило бы затраты на инструменты, позволило Dive производить конечные продукты быстрее, чем при использовании традиционных методов, и обеспечило бы новый, более высокий уровень быстрой настройки для клиентов.
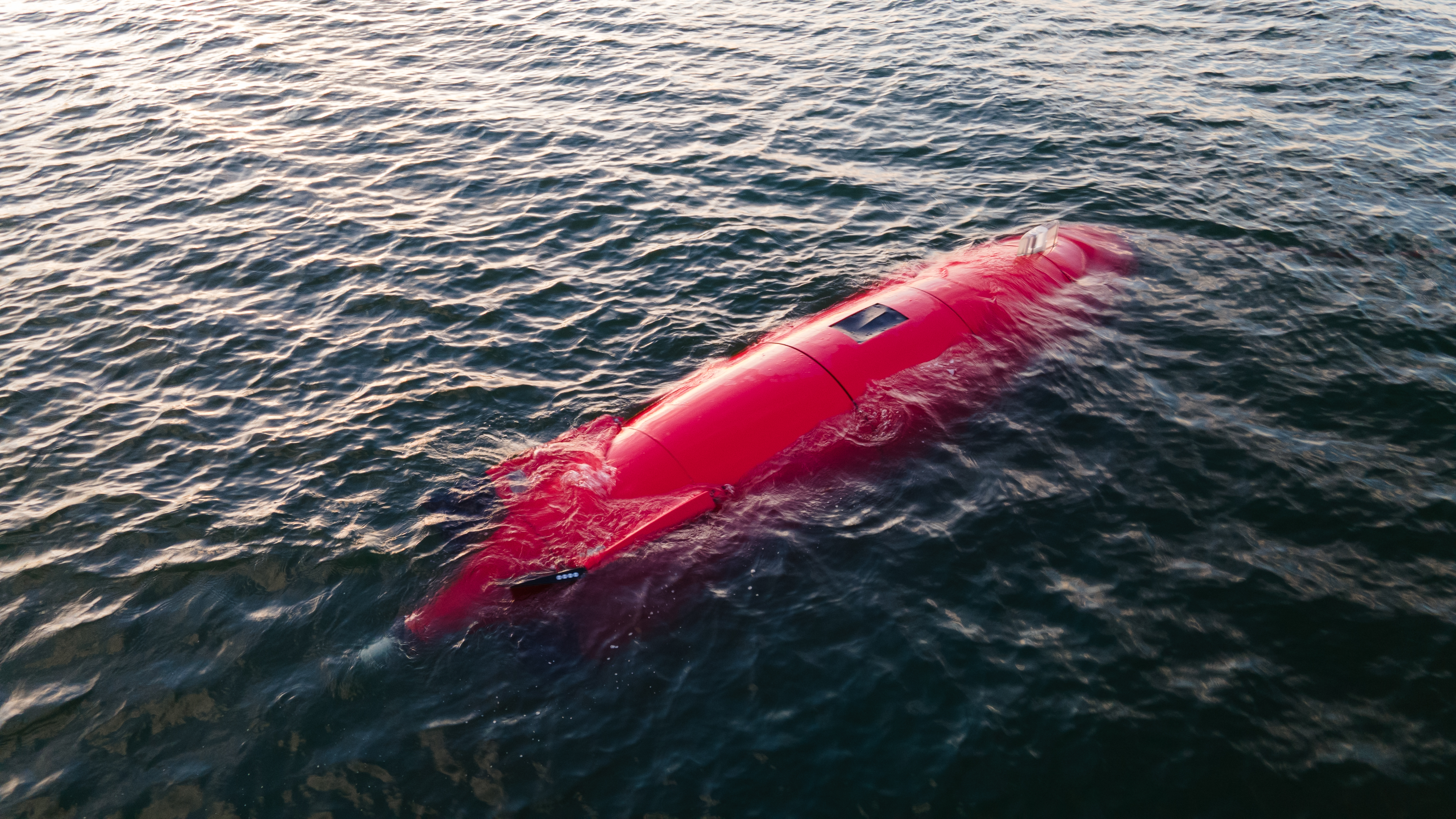
Внешний корпус DIVE-LD состоит из девяти трубчатых обтекателей, напечатанных на одном из четырех 3D-принтеров Big Area Additive Manufacturing (BAAM) компании AES (Цинциннати, Огайо, США). Эти обтекатели напечатаны из АБС-пластика с наполнителем из рубленого волокна, поставляемого Sabic (Эр-Рияд, Саудовская Аравия). По словам соучредителя и вице-президента AES Эндрю Бадера, AES может напечатать все детали для всего корпуса менее чем за два дня. После доставки в Dive обтекатели, напечатанные на 3D-принтере, механически закрепляются с помощью четырех крепежных элементов на каждый обтекатель и покрываются для получения гладкой гидродинамической внешней поверхности. После успешного первоначального тестирования в 2020 году компания Dive этой весной строит первые автомобили для клиентов и доставит первый заказ в июне 2021 года.
По словам Руссо, AM стала основной частью ценностного предложения Dive Technologies в отношении будущих автомобилей и продуктов. Партнерство с Dive также является большим шагом для AES и композитной 3D-печати. Бадер добавляет:«Обычно, когда люди думают о 3D-печати, они думают о прототипах, приспособлениях и инструментах, так что это показывает, на что еще способна 3D-печать».
Чтобы узнать больше о Dive Technologies и AES, прочтите «Широкоформатная 3D-печать позволяет быстро и без инструментов производить АПА».
Сплошное волокно AM и автоматизация для универсальной конструкции моторных лодок
С момента патентования процесса производства непрерывного волокна (CFM) в 2015 году компания Moi Composites (Милан, Италия) изучила ряд применений своей технологии CFM для 3D-печати на основе осаждения непрерывных волокон. Отличительными чертами CFM являются программное обеспечение для индивидуального проектирования Moi Composites, использование роботизированных манипуляторов, УФ-отверждение и «гибридное» производство - более традиционное ламинирование композитных материалов поверх структурного сердечника, напечатанного на 3D-принтере. Недавно компания продемонстрировала свою технологию CFM как решение для более экономичного, быстрого и инновационного проектирования морских конструкций на демонстрационной моторной лодке под названием MAMBO.
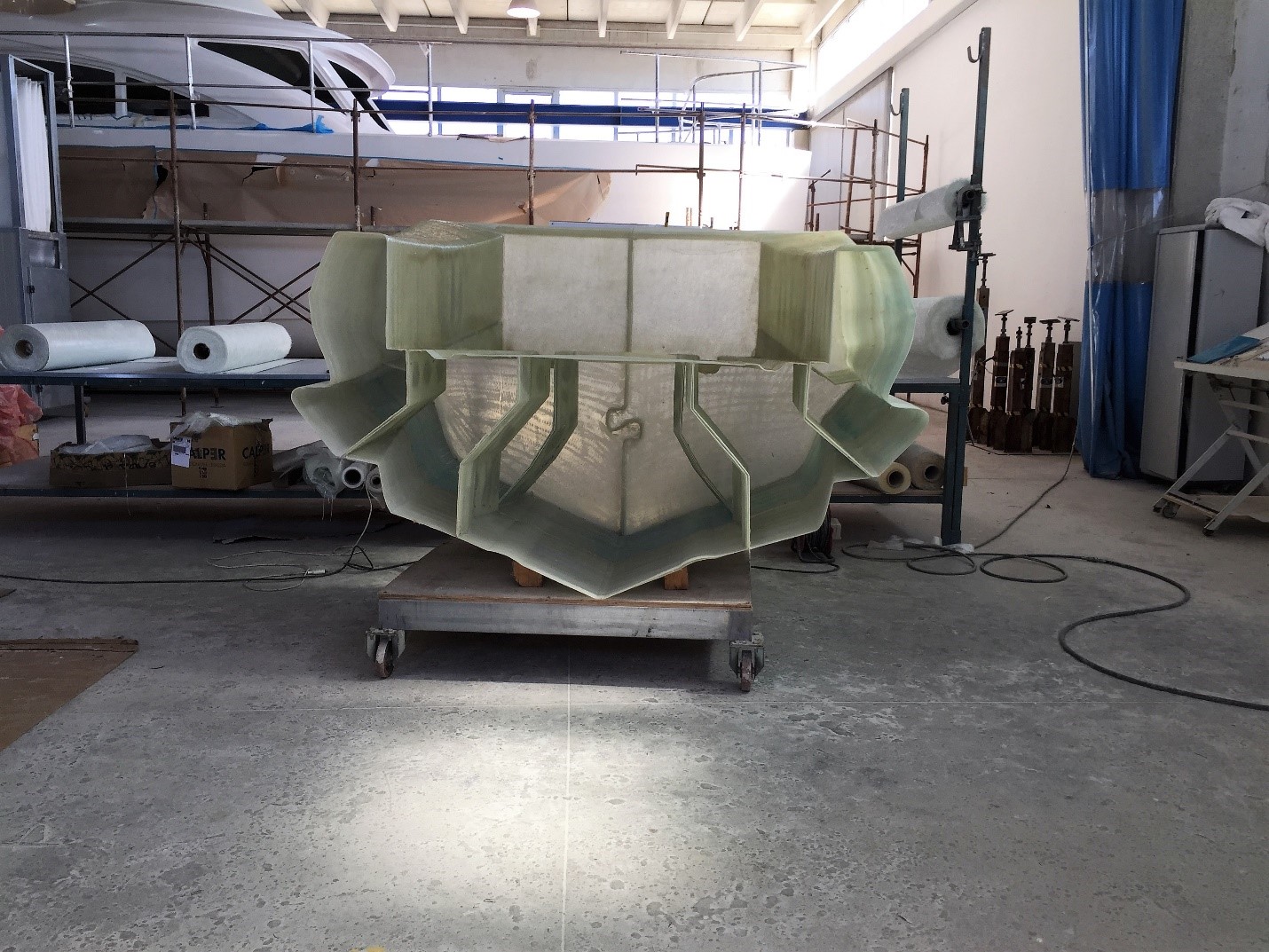
По словам Габриэле Натале, соучредителя Moi Composites, он и его соучредитель Микеле Тониццо посетили выставку лодок в Генуе в 2017 году и поняли, что затраты на инструменты и традиционные процессы вливания стекловолокна, используемые для корпусов многих лодок, ограничивают способность конструкторов лодок исследовать новые и более сложные конструкции. Признавая, что их технология трехмерной печати из непрерывного волокна без формования может быть подходящим решением, Натале говорит:«С этого момента мы начали разрабатывать план и начали встречаться с партнерами в морской отрасли».
Получившаяся лодка MAMBO имеет длину 6,5 метра и ширину 2,5 метра, сухой вес около 800 кг, оснащена системой навигации, пробковым полом, белыми кожаными сиденьями и двигателем мощностью 115 лошадиных сил. Компания Moi Composites работала со студией морского дизайна MICAD (Лечче, Италия) над концепцией структурного дизайна лодки, которая объединяет органические формы в ее структурные элементы, вдохновленные знаменитым катамараном Arcidiavolo Сонни Леви. Autodesk (Сан-Рафаэль, Калифорния, США) Fusion 360 CAD и программное обеспечение для аддитивного производства NETFABB использовались при проектировании и гидродинамическом анализе компонентов.
Корпус и палуба лодки, напечатанные из однонаправленного E-стекла, поставляемого Owens Corning (Толедо, Огайо, США), и винилэфирной смолы, были спроектированы так, чтобы изготавливаться из 50 отдельных секций различных размеров. Половина секций была напечатана на предприятии Moi Composites в Милане, а другая половина - на предприятии Advanced Manufacturing Facility (ACF) партнера Autodesk в Бирмингеме, на обоих использовались технология 3D-печати CFM компании Moi Composites и двойные роботы Kuka (Аугсбург, Германия). удобства. По словам Доминика Мюллера, менеджера по исследованиям в группе аддитивного производства в Autodesk, система CFM в технологическом центре Autodesk позволила быстро распечатать лодку, а также позволила Autodesk лучше узнать технологию, которую Мой управлял удаленно с помощью программного обеспечения Autodesk. . Общее время печати всех компонентов составило около двух месяцев.
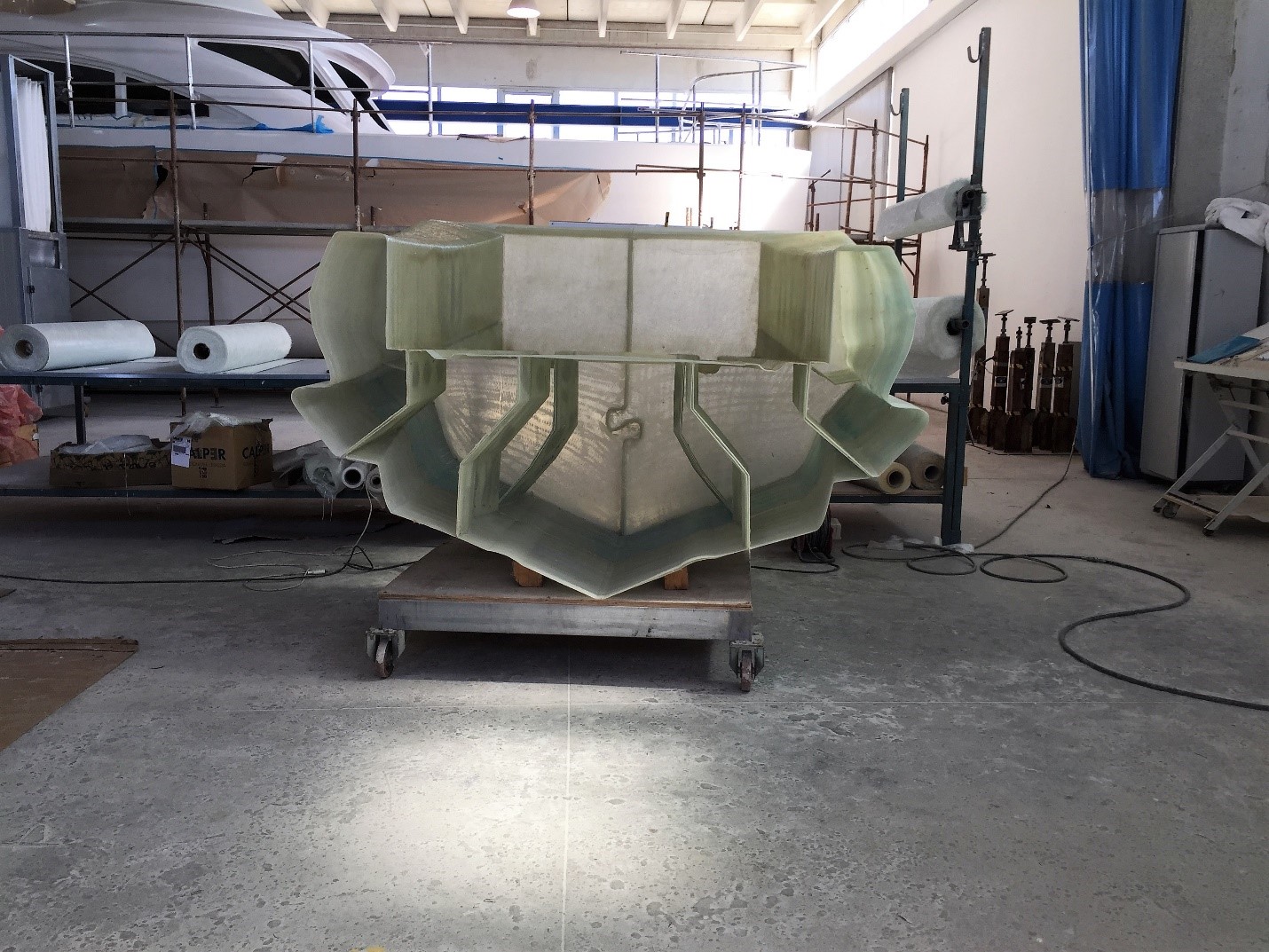
Отпечатанные детали были отправлены на верфь Catmarine в Миджано, Италия, где они были собраны вместе и склеены. В гибридном производственном процессе, аналогичном тому, который Moi использовал для изготовления протезов и других деталей, весь корпус был затем ламинирован вручную с дополнительным слоем стекловолокна / полиэстера, заполненным пенопластом, который, по словам Натале, варьируется по толщине в зависимости от конструкции. После того, как корпус и палуба были полностью собраны, отшлифованы и покрыты гелем, партнеры Moi Composites оснастили лодку двигательными, навигационными и другими системами для завершения лодки.
Первоначальные ходовые испытания и испытания на остойчивость были проведены осенью 2020 года, когда MAMBO разогнался до 26 узлов; Компания Moi Composites планирует продолжить ходовые испытания летом 2021 года, работая над сертификацией лодки.

«Аддитивное производство, цифровизация и автоматизация могут ускорить создание новых концепций и футуристических проектов, потому что для каждой лодки, которую вы хотите спроектировать, вам нужно создать новую форму. Используя эту технологию, вы можете легко изменить свою 3D-модель и снова распечатать ее. Это идеально подходит для коротких или одноразовых лодок », - говорит Натале.
Чтобы узнать больше о MAMBO, прочтите «MAMBO тестирует воду для 3D-печати больших морских сооружений».
Смола
- 5 общих процессов аддитивного производства
- Аддитивное производство против субтрактивного производства
- Преимущества аддитивного производства
- Обзор рабочих процессов аддитивного производства
- Henkel предлагает платформу материалов для аддитивного производства
- NCAMP выпускает первую квалификационную программу аддитивного производства
- Альянс устойчивого производства термопластов и аддитивных технологий создается в Колорадо
- 5 технологий, разрушающих производство
- Аддитивное производство в электронике
- Аддитивное производство в аэрокосмической отрасли