Задний лонжерон VBO вне автоклава, ребра из термопласта нацелены на Wing of Tomorrow
Airbus (Тулуза, Франция) активно работает с производителями аэрокомпозитов над разработкой внеавтоклавных конструкций (OOA) для программы Wing of Tomorrow (WOT). Эти конструкции будут доставлены Airbus в 2021 году и будут собраны в демонстрационное крыло, которое будет испытано и оценено для потенциального использования в узкофюзеляжных самолетах следующего поколения. Когда такая программа может быть объявлена, неизвестно и является предметом множества спекуляций, но вся цепочка поставок аэрокомпозитов позиционирует себя как часть авиастроения следующего поколения, будь то Airbus или Boeing, или и то, и другое.
CW уже сообщал о некоторых из этих мероприятий WOT в статьях об обшивке нижней части крыла, производимой Spirit AeroSystems (Вичита, Канада, США), и термопластических нервюрах, производимых GKN Aerospace (Хогевен, Нидерланды). К усилиям WOT присоединился производитель самолетов и поставщик авиационных конструкций Daher (Париж, Франция), который разработал, изготовил и поставил задний лонжерон OOA и пять нервюр из термопласта для этой программы.
«Daher гордится своим участием в этой программе WOT. Эта разработка подтверждает позицию Daher как одного из мировых лидеров в области технологий термопластов и интегрированных функциональных структур из термореактивных материалов, а также как надежного партнера для производителей самолетов и уровня 1 для сложных деталей », - говорит Доминик Байи, вице-президент по исследованиям и разработкам Daher. / P>
Высокопроизводительный лонжерон
Демонстрационный образец WOT, как и крыло любого коммерческого самолета, имеет несколько лонжеронных конструкций. Задний лонжерон, разработанный Daher для WOT, находится за пределами танка, а второй из двух лонжеронов, непосредственно примыкающих к фюзеляжу, расположен прямо над шасси. Он имеет длину более двух метров и толщину 10 миллиметров и должен соответствовать значительным требованиям к прочности и жесткости - «несколько тонн, приложенных к элементам, и несколько десятков тонн для сдвига и тяги в направлении размаха», - говорит Байи, - учитывая его близость к к фюзеляжу и к системе шасси.
Кроме того, говорит Александр Конде, главный инженер Daher, который работал над лонжероном, Airbus искал разработку высокоавтоматизированного производственного процесса, который позволил бы компании снизить вес самолета и с минимальными затратами обеспечить производство самолетов в 60-100 единиц. в месяц. Дахер предложил конструкцию, способную заменить 15 металлических компонентов и креплений, которые были оригинальными для базовой конструкции композитного лонжерона. «Идея заключалась в том, чтобы интегрировать большинство функций, чтобы добиться рентабельности и снижения веса», - говорит Конде.
Полученная в результате конструкция лонжерона является побочным продуктом термореактивного лонжерона только с вакуумным мешком OOA (VBO), разработанного Daher в 2018 году для бизнес-джета Dassault Aviation (Париж, Франция). Бейли говорит, что лонжерон Dassault был изготовлен из препрега на основе эпоксидной смолы M56, отвержденного OOA VBO компании Hexcel (Стэмфорд, Коннектикут, США). Впоследствии, когда Дахер стал участвовать в программе Airbus WOT, компания решила адаптировать конструкцию, процессы и обоснование лонжеронов Dassault и применить их к новой структуре Airbus WOT, выбрав отверждаемую эпоксидную смолу OOA Hexcel M56 350 ° F, предварительно подготовленную в Углеродное волокно Hexcel AS4 и углеродное волокно IM7 UD
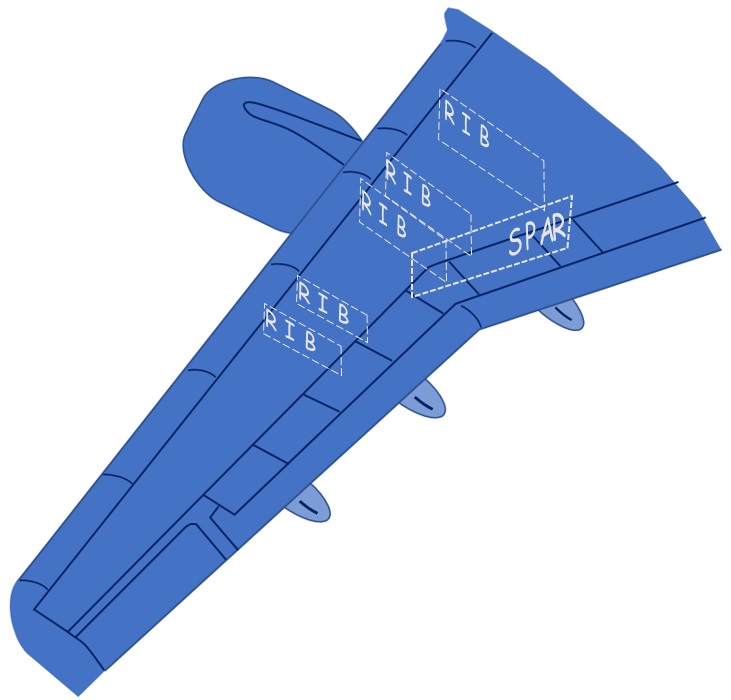
Производственный процесс, используемый для изготовления лонжерона, представляет собой автоматическое размещение волокон (AFP) с использованием системы Coriolis Composites (Queven, Франция), в которой материал наносится на охватываемую форму. Отверждение происходит под вакуумным мешком в духовке. Полученная деталь, по словам Конде, имеет пористость 0,1%.
Конде говорит, что препрег был выбран вместо формования из жидкой смолы по той же причине, по которой препрег стал основным продуктом аэрокосмического производства за последние 30 лет:он обеспечивает постоянный и надежный объем смолы / волокна, что позволяет изготавливать детали с постоянными и надежными размерами. и масса. «Используя это новое поколение смолы OOA только в вакууме, вы получаете идеальную устойчивость по содержанию волокон в толщине композита после отверждения», - говорит Конде. «Кроме того, вес детали очень стабилен, потому что вы не выталкиваете смолу за пределы волокна».
Дахер говорит, что это был первый партнер, поставивший в конце 2020 года компонент WOT - один лонжерон для Airbus в Бристоле, Великобритания - для интеграции в первый демонстрационный образец WOT; компания поставляет еще два. Помимо этого демонстрационного этапа, Daher также думает об индустриализации производства лонжеронов и работает над анализом проектирования производственной системы (MSD), который оценивает и моделирует операции, производственные мощности, оборудование и потребности в персонале для полноценного производства узкофюзеляжного оборудования следующего поколения. самолет.
Несколько ребер, несколько размеров
Усилия в Daher по развитию ребер поскольку программа WOT была более сложной и требовательной. Компания разработала пять нервюр различных размеров и размеров внутри крыла; другие ребра представляют собой комбинацию алюминиевых и композитных конструкций, включая ребро из термопластичного композитного материала, разработанное GKN Aerospace.
В предыдущем проекте с Dassault Aviation компания Daher продемонстрировала свою способность конструировать и производить относительно небольшие ребра из термопластичных композитов, объясняет Байи. Благодаря WOT у компании появилась возможность расширить свои навыки в области разработки более крупных (длиной ~ 2 метра) ребер с большей нагрузкой.
Кроме того, согласно целям WOT, Daher нацеливается на уровень технологической готовности (TRL) 6 к концу 2023 года. «В конце программы WOT, когда мы доказали, что мы находимся на уровне TRL 6 для больших ребер, между этими с помощью двух программ [WOT и Dassault Aviation], мы продемонстрируем, что можем покрыть всю нервюрную часть крыла - в этом и заключается идея », - говорит Байи.
«Мы воспользовались этой программой, чтобы изучить различные способы производства деталей и сравнить их механическое поведение, а также посмотреть, как они влияют на производство. Параллельно с этим мы работаем над моделированием, чтобы предсказать поведение компонентов, например, эффект пружинения или штамповки. Цель состоит в том, чтобы сократить количество испытаний во время разработки и, следовательно, сократить единовременные расходы », - говорит Конде.
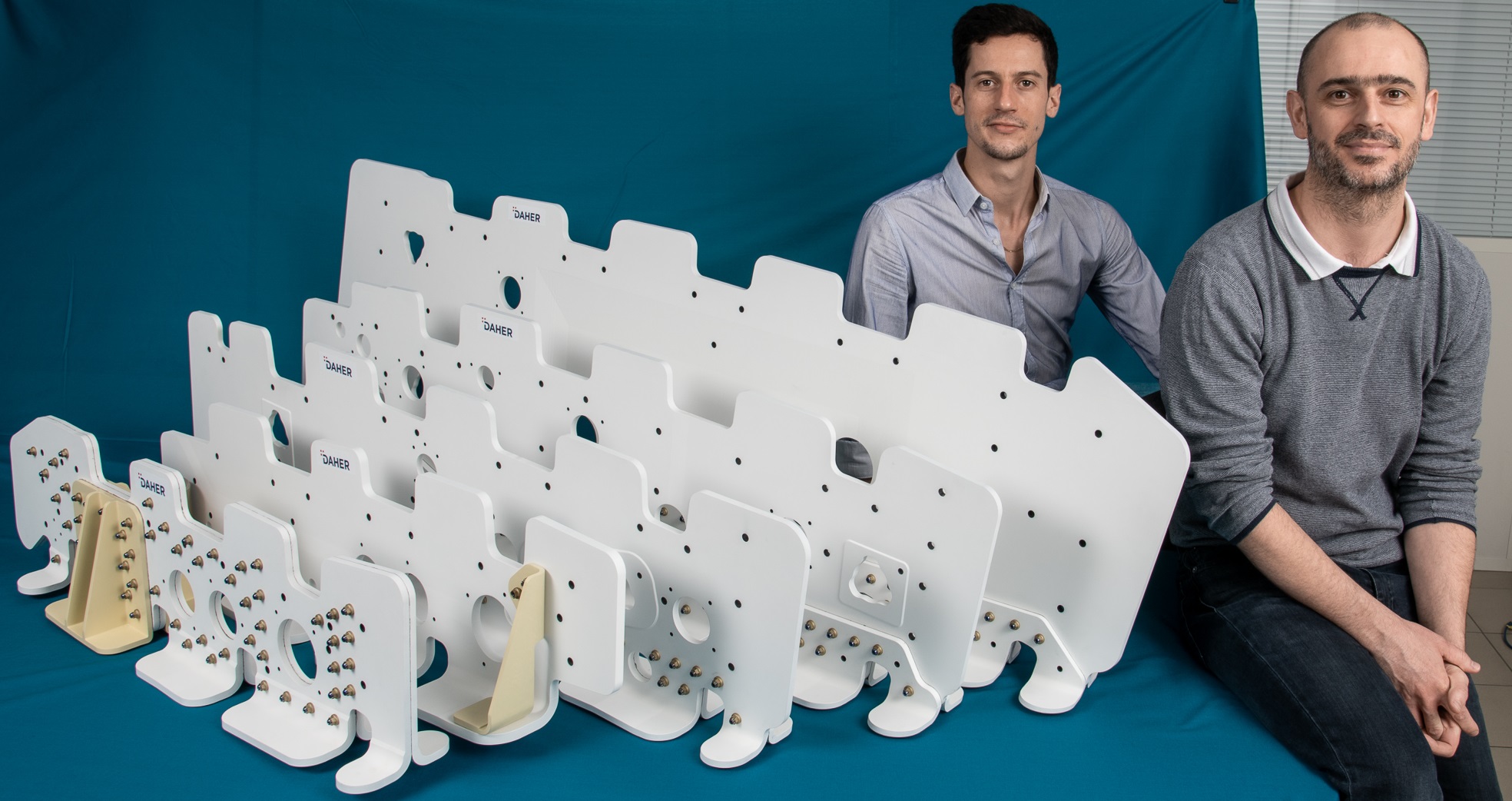
Как и в случае с лонжероном, разработка началась на уровне купонов, элементов и деталей, после чего последовало изготовление субшкальных деталей до того, как были построены окончательные полноразмерные детали. Конде отмечает, что тестирование проводилось на каждом уровне, включая специальные тесты, разработанные Daher для ребер.
Для всех пяти ребер Daher в конечном итоге решила использовать однонаправленные (UD) ленты из углеродного волокна / легкоплавкого полиарилэфиркетона (PAEK), поставляемые Toray Advanced Composites (Морган Хилл, Калифорния, США), с использованием смолы, производимой Victrex (Кливлис, Ланкашир, Великобритания). ). Для изготовления ребер плоские заготовки изготавливаются с использованием AFP с последующим уплотнением в печи - в некоторых случаях материалы предварительно уплотняются перед штамповкой. При необходимости на штампованные детали механически закрепляются дополнительные фланцы или другие компоненты.
Каждая нервюра была спроектирована в соответствии с ее положением вдоль крыла, спецификациями размеров и требованиями к нагрузке (от одной тонны до 50 тонн), поэтому каждое из них уникально в нескольких отношениях. Самое большое ребро имеет длину 2 метра и ширину 1 метр. В любом случае, каждый из них начинается с плоской перемычки, которая представляет собой штамп, имеющий L-образную форму, чтобы создать фланец вдоль нижней части детали, где он соединяется с обшивкой крыла. Для дополнительной устойчивости несколько ребер содержали два L-образных компонента, механически скрепленных друг с другом, чтобы образовать Т-образную форму с двунаправленными фланцами.
К специальным характеристикам относятся кронштейн (изготовленный из термореактивных композитов) для соединения с направляющей закрылка, прикрепленной к нервюру, и ряд отверстий или выступов на определенных выступах для уменьшения веса детали.
«Все время, пока мы проектировали, нам приходилось управлять сложностью в сравнении с затратами», - говорит Байи. «Мы всегда думали о том, чтобы сделать что-то простое, но рентабельное». Конде отмечает, что простота была ключевым моментом и с точки зрения производительности. «Если он будет слишком сложным, он не будет конкурентоспособным с точки зрения потребителя по очень высоким ставкам, которые они хотят иметь».
Одной из проблем, усложняющих конструкцию, была относительная толщина каждого ребра - до 12 миллиметров для самого большого ребра. Более толстые ткани имеют тенденцию к складкам или неправильной форме при штамповке, а более толстым деталям бывает трудно придать готовую форму.
Для механической обработки Daher использовала сочетание гидроабразивной резки и механической обработки в зависимости от потребностей детали, как для смягчения проблем с толщиной детали, так и для регулирования температуры. Кроме того, на ребре толщиной 12 миллиметров команда разработала окно для сброса слоя в середине компонента, чтобы уменьшить общий вес детали. В дополнение к решению этих потенциальных проблем, Конде отмечает, что окно опускания слоя также позволило Daher «опробовать различные виды производственных функций на деталях, чтобы лучше понять поведение деталей».
Процесс формирования штампа оказался еще более сложной задачей. «Мы должны были придумать новый способ штамповки, чтобы снизить риск появления морщин», - говорит Байи. В конечном итоге Дахер разработал собственный метод решения проблемы.
Дальнейшие действия
Помимо WOT, Daher изучает альтернативные методы производства ребер из термопласта, а в будущем планирует разработать полную производственную линию для высокопроизводительного производства.
Например, в то время как демонстраторы WOT используют крепежные детали, Байи отмечает, что благодаря приобретению в 2019 году термопластичных композитов и специалиста по индукционной сварке KVE Composites (Гаага, Нидерланды), Daher обладает возможностями для сварки компонентов в будущем. «Мы работаем над другим, отдельным проектом, чтобы достичь более высокого уровня TRL при сварке деталей с толщиной UD [для использования на узкофюзеляжных самолетах следующего поколения]», - говорит он.
Daher также работает над разработкой полной производственной линии для производства ребер из термопласта в будущем. «Мы действительно улучшаем концепцию и сокращаем количество машин, необходимых для выполнения всех задач, и сокращаем производственные затраты», - говорит Байи, стремясь соответствовать целям массового производства самолетов.
Смола
- Covestro увеличивает инвестиции в термопластические композиты
- Запущены суперконцентраты термопластов, армированных графеном
- Solvay увеличивает емкость термопластичного композитного материала
- Термопластические композиты в Oribi Composites:CW Trending, эпизод 4
- Suprem расширяет возможности термопластов
- Kordsa расширяет линейку термопластичных препрегов
- Термопластические композиты LANXESS, используемые в корпусе заднего сиденья Audi A8
- Технология производства термопластичных сотовых панелей EconCore
- Термопластические композиты:живописный вид
- Сварка термопластичных композитов