11 Глава 6:Нарезание резьбы на токарном станке
ЦЕЛЬ
После завершения этого раздела вы сможете:
• Определите глубину подачи.
• Опишите, как правильно обрезать нить.
• Объясните, как рассчитать шаг, глубину и внутренний диаметр, ширину плоскости.
• Опишите, как установить правильную скорость вращения.
• Опишите, как правильно настроить быстросменный редуктор.
• Опишите, как правильно установить составную паузу.
• Опишите, как установить правильную насадку инструмента.
• Опишите, как установить нулевое значение для компаунда и перекрестной подачи на обоих циферблатах.
• Описать операцию создания потоков.
• Опишите развертывание.
• Опишите, как заточить насадку инструмента.
Нарезание резьбы на токарном станке
Нарезание резьбы на токарном станке — это процесс, при котором на заготовке образуется спиральный гребень одинакового сечения. Это выполняется путем выполнения последовательных надрезов резьбонарезным инструментом той же формы, что и требуемая форма резьбы.
Практическое упражнение:
1. Для этого практического упражнения по нарезанию резьбы вам понадобится кусок круглого материала, повернутый на внешний диаметр протектора.
2. С помощью отрезного или специально заточенного инструмента сделайте надрез для протектора, равный его глубине плюс 0,005 дюйма.
3. Приведенная ниже формула даст вам единую глубину для создания унифицированных потоков:
d =P x 0,750
Где d =одинарная глубина
P =Шаг
n =количество витков на дюйм (TPI)
Глубина подачи =0,75 / n
Расчет потоков
Чтобы нарезать правильную резьбу на токарном станке, необходимо сначала произвести расчеты, чтобы резьба имела правильные размеры. Следующие диаграммы и формулы будут полезны при расчете размеров резьбы.
Пример. Рассчитайте шаг, глубину, внутренний диаметр и ширину лыски для резьбы NC ¾-10.
P = 1 / n = 1 / 10 = 0,100 дюйма.
Глубина = .7500 x Шаг = .7500 x .100 = .0750 дюйма.
Малозначительный диаметр = Большой диаметр – (D + D) = 0,750 – (0,075 + 0,075) = 0,600 дюйма.
Ширина плоскости = P / 8 = (1/8) x (1/10) = 0,0125 дюйма.
Процедура создания потоков:
1. Установите скорость примерно на одну четверть скорости, используемой для поворота.
2. Установите быстросменный редуктор на требуемый шаг резьбы. (количество витков на дюйм)
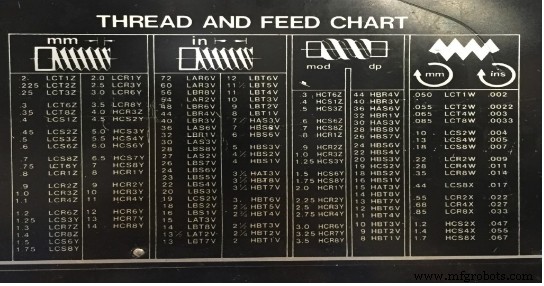
Рис. 1. Диаграмма потока и подачи
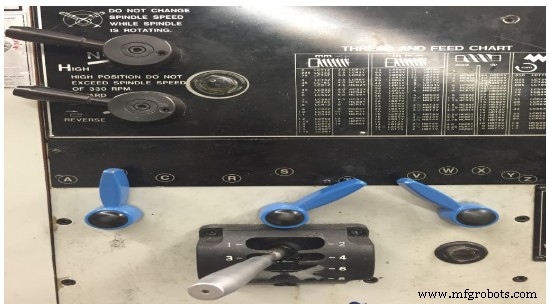
Рисунок 2. Настройка Gearbox
3. Установите составной упор на 29 градусов вправо для правой резьбы.
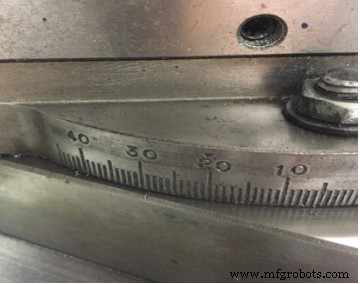
Рис. 3. 29 градусов
4. Установите насадку для нарезания резьбы под углом 60 градусов и установите высоту на центральную точку токарного станка.
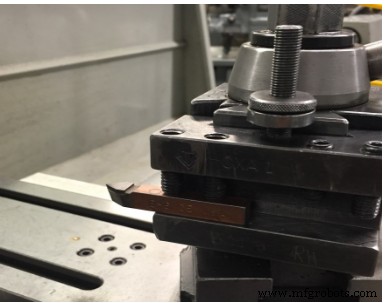
Рис. 4. Инструмент для нарезания резьбы под углом 60 градусов
5. Установите насадку инструмента и прямые углы к работе, используя резьбовой калибр.
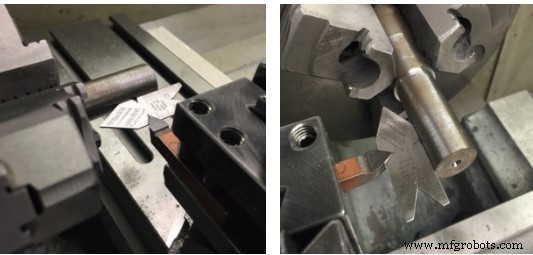
Рис. 5. Использование датчика центра для позиционирования инструмента для обработки резьбы
6. Используя раствор для разметки, покройте область, на которую будет нарезана резьба.
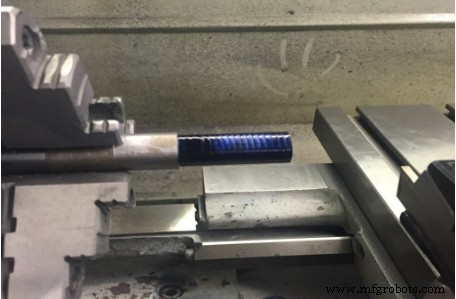
Рис. 6. Макет
7. Переместите инструмент для нарезания резьбы к детали, используя как компаунд, так и поперечную подачу. Установите микрометр на ноль на обоих циферблатах.
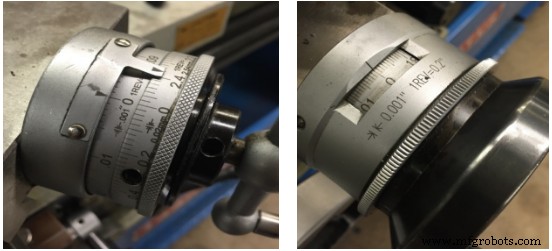
Рис. 7. Составная Рис. 8. Поперечная подачаП>
8. Переместите поперечную подачу на задний инструмент с заготовки, переместите каретку к концу детали и сбросьте поперечную подачу на ноль.
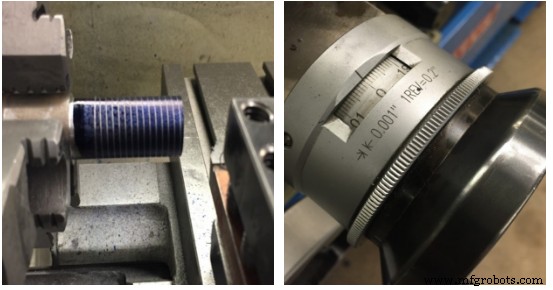
Рис. 9. Конец детали и перекрестная подача Ноль
9. Используя только составной микрометр, подайте от 0,001 до 0,002 дюйма.
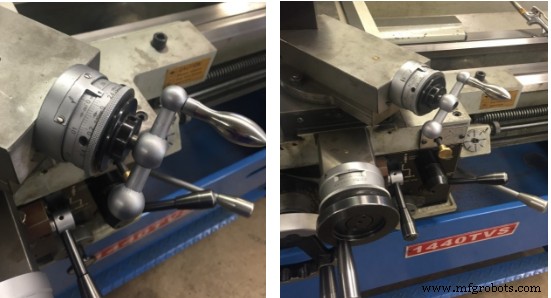
Рис. 10. Комбинированная подача в 0,002 дюймаП>
10. Включите токарный станок и затяните полугайку.
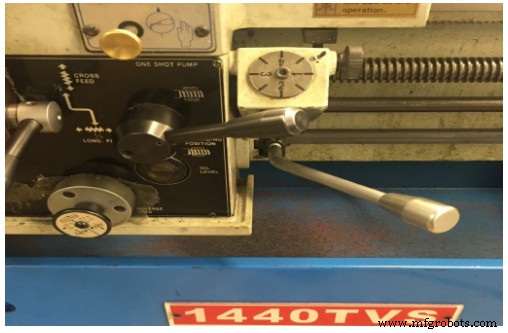
Рис. 11. Рычаг включения/выключения и полугайка Р>
11. Сделайте надрез на детали без смазочно-охлаждающей жидкости. Отсоедините полугайку в конце реза, остановите токарный станок и выдвиньте инструмент, используя поперечную подачу. Верните каретку в исходное положение.
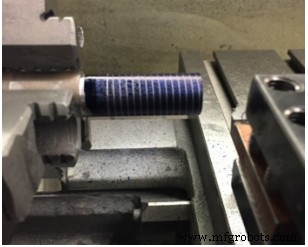
Рис. 12. Начальная позиция
12. С помощью калибра или линейки проверьте шаг резьбы. (количество витков на дюйм)
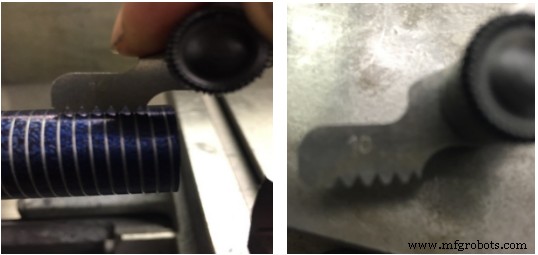
Рис. 13. Измеритель шага винта Рисунок 14. Шаг винта Гейдж(10)
13. Подайте компаунд размером от 0,005 до 0,020 дюйма для первого прохода, используя смазочно-охлаждающую жидкость. Когда вы приблизитесь к окончательному размеру, уменьшите глубину резания до 0,001–0,002 дюйма.
14. Продолжайте этот процесс, пока инструмент не окажется в пределах 0,010 дюйма от глубины чистовой обработки.
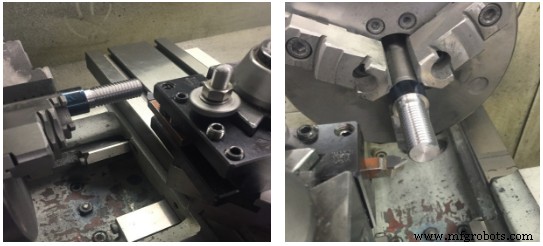
Рис. 15. Работа с потоками
15. Проверьте размер с помощью микрометра резьбы, резьбомера или трехпроводной системы.
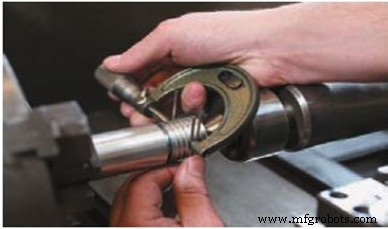
Рис. 16. Измерение по трем проводам
16. Срежьте фаску на конце резьбы, чтобы защитить его от повреждений.
Расширение
Развертки используются для быстрой и точной доводки просверленных отверстий или отверстий до отверстия заданного размера и для получения хорошего качества поверхности. Расширение может быть выполнено после того, как отверстие было просверлено или расточено в пределах от 0,005 до 0,015 дюйма от конечного размера, поскольку расширитель не предназначен для удаления большого количества материала.
Заготовка устанавливается в патрон на шпинделе передней бабки, а развертка поддерживается задней бабкой.
Скорость токарного станка для развёртывания должна быть примерно 1/2 скорости сверления.
Развертка с помощью ручного развертки
Отверстие, которое нужно развернуть вручную, должно быть в пределах 0,005 дюйма от требуемого готового размера.
Заготовка крепится к шпинделю передней бабки в патроне, и шпиндель передней бабки блокируется после точной установки заготовки. Ручная развертка устанавливается в регулируемый ключ для развертки и опирается на центр задней бабки. Поскольку ключ вращается вручную, ручная развертка одновременно подается в отверстие путем поворота маховика задней бабки. Используйте большое количество смазочно-охлаждающей жидкости для развертывания.
Развертка с помощью станочного развертки
Отверстие, которое необходимо расширить с помощью машинной развертки, должно быть просверлено или расточено с точностью до 0,010 дюйма от конечного размера, чтобы машинной развертке оставалось только удалить следы фрезы. Используйте большое количество смазочно-охлаждающей жидкости для развертывания.
Заточите токарную насадку
Процедура:
1. Крепко возьмитесь за насадку, поддерживая рукой набор инструментов для заточки.
2. Держите насадку инструмента под правильным углом, чтобы отшлифовать угол режущей кромки. При этом наклонить нижнюю часть резца к кругу и отшлифовать 10-градусный боковой затыльник или задний угол на режущей кромке. Режущая кромка должна быть около 0,5 дюйма в длину и должна быть примерно на ¼ ширины насадки.
3. Во время заточки насадки перемещайте насадку вперед и назад по поверхности шлифовального круга. Это ускоряет шлифование и предотвращает образование канавок на круге.
4. Наконечник инструмента необходимо часто охлаждать во время операции шлифования, погружая его в воду. Никогда не перегревайте инструментальную насадку.
5. Отшлифуйте торцевой режущий угол так, чтобы он образовывал с боковой режущей кромкой угол чуть меньше 90 градусов. Держите инструмент так, чтобы угол торцевой режущей кромки и задний задний угол в 15 градусов были отшлифованы одновременно.
6. Проверьте величину торцевой разгрузки, когда насадка находится в держателе инструмента.
7. Держите верхнюю часть насадки под углом примерно 45 градусов к оси колеса и отшлифуйте боковую переднюю часть под углом примерно 14 градусов.
8. Отшлифуйте кончик режущего инструмента по небольшому радиусу, сохраняя одинаковый передний и боковой задний угол.
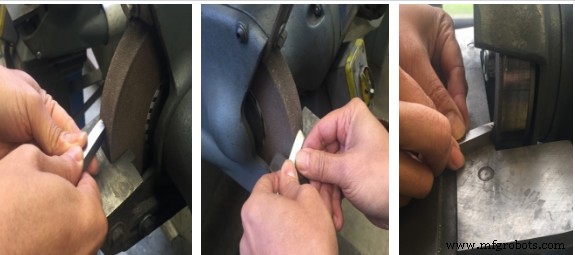
Шлифовка спереди
Материалы режущего инструмента
Насадки для токарных станков обычно изготавливаются из четырех материалов:
1. Быстрорежущая сталь
2. Литейные сплавы
3. Цементированные карбиды
4. Керамика
Свойства, которыми обладает каждый из этих материалов, различны, и применение каждого из них зависит от обрабатываемого материала и состояния станка.
Насадки для токарных станков должны обладать следующими свойствами.
1. Они должны быть жесткими.
2. Они должны быть износостойкими.
3. Они должны выдерживать высокие температуры, возникающие во время операции резки.
4. Они должны выдерживать удары во время резки.
Номенклатура режущего инструмента
Режущие инструменты, используемые на токарных станках, обычно представляют собой однолезвийные режущие инструменты, хотя форма инструмента изменяется для различных применений. Та же номенклатура применяется ко всем режущим инструментам.
Процедура:
1. Основание:нижняя поверхность хвостовика инструмента.
2. Режущая кромка:передняя кромка режущей кромки, которая выполняет резку.
3. Лицо:поверхность, на которую опирается чип, когда он отделяется от изделия.
4. Фланг:поверхность инструмента, прилегающая к режущей кромке и ниже нее.
5. Нос:кончик режущего инструмента, образованный соединением режущей кромки и передней грани.
6. Радиус носа:Радиус, до которого заточен нос. Размер радиуса будет влиять на отделку. Для черновой обработки используется радиус вершины 1/16 дюйма. Для чистовой обработки используется радиус вершины от 1/16 до ⅛ дюйма.
7. Острие:конец инструмента, который был заточен для резки.
8. Хвостовик:корпус насадки или часть, удерживаемая в держателе инструмента.
9. Углы и зазоры токарных резцов
Правильная работа насадки зависит от зазора и переднего угла, которые должны быть заточены на насадке. Хотя эти углы различаются для разных материалов, номенклатура одинакова для всех насадок.
• Угол боковой режущей кромки:угол, который образует режущая кромка со стороной хвостовика инструмента. Этот угол может составлять от 10 до 20 градусов в зависимости от разрезаемого материала. Если угол больше 30 градусов, инструмент будет вибрировать.
• Угол конечной режущей кромки. Угол, образованный концевой режущей кромкой и линией, расположенной под прямым углом к центральной линии насадки инструмента. Этот угол может составлять от 5 до 30 градусов в зависимости от типа огранки и желаемой отделки. Для черновой обработки под углом от 5 до 15 градусов, для токарных инструментов общего назначения используют угол от 15 до 30 градусов. Больший угол позволяет поворачивать режущий инструмент влево при выполнении легких пропилов вблизи упора или патрона или при повороте к плечу.
• Боковой задний угол (зазор):угол заточки на боковой поверхности инструмента ниже режущей кромки. Этот угол может быть от 6 до 10 градусов. Боковой зазор на инструментальной насадке позволяет режущему инструменту продвигаться вдоль вращающейся детали и предотвращает трение боковой поверхности о заготовку.
• Конечный задний угол (зазор):угол отшлифован ниже носовой части насадки, который позволяет подавать режущий инструмент в заготовку. Этот угол может составлять от 10 до 15 градусов для резки общего назначения. Этот угол необходимо измерять, когда насадка удерживается в держателе инструмента. Концевой задний угол зависит от твердости и типа материала, а также типа разреза. Концевой задний угол меньше для более твердых материалов, чтобы обеспечить опору под режущей кромкой.
• Боковой передний угол:угол, под которым грань отшлифована от режущей кромки. Этот угол может составлять 14 градусов для насадок инструментов общего назначения. Боковой передний центрирует более острую режущую кромку и позволяет стружке быстро стекать. Для более мягких материалов боковой передний угол обычно увеличивается.
• Задний (верхний) передний угол:обратный наклон поверхности инструмента от носа. Этот угол может составлять около 20 градусов и предусмотрен в держателе инструмента. Задний передний угол позволяет стружке стекать с острия режущего инструмента.
ЮНИТ-ТЕСТ
1. Что такое шаг для ¼-20 касаний?
2. На какой угол нужно повернуть компаунд для единой резьбы?
3. Объясните, почему вы поворачиваете соединение в вопросе 2.
4. Какая глубина резьбы для винта UNF ½-20?
5. Как сделать левую резьбу? Это не рассматривается в чтении — подумайте об этом?
6. Какой инструмент мы используем для нарезания резьбы?
7. Пожалуйста, опишите Center Gage.
8. Что мы используем для проверки шага резьбы (резьбы на дюйм)?
9. Первый и последний проход, сколько мы подаем смеси?
10. Назовите четыре материала, из которых изготавливаются насадки для инструментов.
Информация об авторстве главы
Эта глава была взята из следующих источников.
- Токарный станок получено из Lathe Массачусетского технологического института, CC:BY-NC-SA 4.0.
- Терминология режущих инструментов получено из Режущих инструментов токарного станка — Формы режущих инструментов Технического колледжа Висконсина, CC:BY-NC 4.0.
- Терминология режущих инструментов получено из типов резцов (токарный станок) Университета Айдахо, CC:BY-SA 3.0.
- Центрирование взято из [документа по токарным станкам с ручным управлением]
Промышленные технологии
- Инструментальный токарный станок
- Токарный станок с ЧПУ
- Токарный станок с ЧПУ(2)
- Токарный станок, предназначенный для точного изготовления крупногабаритных деталей
- Токарный станок оснащен электронным серводвигателем и компьютером для нарезания резьбы
- Комбинированный токарный станок среднего размера
- Что такое шпиндель токарного станка?
- 22 Модуль 5:Работа с ЧПУ
- 24 Модуль 7:Mastercam
- Части токарного станка