Аддитивное производство с промышленной 3D-печатью:стратегии успеха постобработки
Детали, изготовленные методом аддитивного производства (AM), редко бывают готовыми, когда они выходят из печатной платформы или покидают рабочую камеру. Вот пять способов сделать их функциональными, эстетичными и более точными.
Несмотря на все усилия производителей промышленных 3D-принтеров, пластиковые или металлические детали, выходящие из их машин, обычно требуют дополнительной обработки, прежде чем они будут считаться готовыми.
Этот шаг в производстве готовых деталей известен как постобработка, и это неизбежное зло в мире аддитивного производства.
Он включает в себя механическую обработку, термообработку, шлифование и другие абразивные процессы. Это также влечет за собой отделочные операции, такие как покраска и гальваника, а также более экзотические технологии, которые мы обсудим более подробно.
О слоях, опорах и точности
Есть много причин для последующей обработки деталей, напечатанных на 3D-принтере.
Во-первых, большинство этих деталей построены из тонких, как бумага, слоев металла, пластика или композитных материалов. И подобно краям книги в мягкой обложке, поверхности печатной части имеют отчетливо ступенчатый вид, который в зависимости от его применения и косметических требований должен быть сглажен перед использованием.
Удаление шероховатых поверхностей также помогает устранить концентраторы напряжения, которые могут привести к растрескиванию, что является важным фактором для несущих частей.
Большинству напечатанных на 3D-принтере деталей требуются временные опоры в процессе сборки. Эти каркасные структуры помогают предотвратить скручивание слоев и секций вверх или провисание вниз (в зависимости от процесса аддитивного производства), а также сводят к минимуму деформацию, вызванную воздействием тепла. Как только деталь будет готова, эти опорные конструкции должны быть удалены, как правило, механическими или абразивными средствами, хотя, как вы увидите, иногда достаточно теплой ванны.
Последнее, но не менее важное, это частичная точность. Несмотря на огромную свободу проектирования и возможности, которые она предоставляет для изготовления прочных, но легких деталей, 3D-печать пока еще не очень точна, по крайней мере, по обычным стандартам производства. Есть уже описанная шероховатость поверхности, с которой приходится бороться, а также плоскостность, округлость и все остальное. В результате отверстия должны быть рассверлены или расточены, шейки выточены, посадочные поверхности отфрезерованы. Вот почему многие напечатанные на 3D-принтере детали — и, конечно же, сделанные из металла — после печати отправляются в механический цех.
Стратегии успешной постобработки при 3D-печати
К счастью, ряд производителей оборудования, а также сами производители 3D-принтеров предпринимают шаги для устранения этих недостатков АП.
Эта работа станет еще более важной по мере увеличения объемов производства и превращения аддитивных технологий в основной процесс. Хотя вторичные процессы никуда не денутся (о чем знают и субтрактивные производители), эти компании, по крайней мере, облегчат жизнь тем, кто зарабатывает на жизнь печатью деталей.
Берни Кершбаум является генеральным директором одной из таких компаний:Rosler Metal Finishing USA, базирующейся в Батл-Крике, штат Мичиган. Кершбаум считает, что дизайнеры и производители продуктов должны проделать свою домашнюю работу, когда дело доходит до постобработки напечатанных на 3D-принтере деталей, предпочтительно задолго до начала печати.
«Никто не предлагает универсальных технологий финишной обработки, и во многих случаях это также не единый процесс», — говорит Кершбаум.
Он приводит пример напечатанного на 3D-принтере прототипа бутылки для шампуня, который он несколько лет назад помогал крупному покупателю потребительских товаров, для которого потребовалась обширная виброобработка, чтобы добиться того же внешнего вида, что и у пластикового аналога, изготовленного методом литья под давлением. Для других деталей требуется влажная или сухая пескоструйная обработка для выравнивания шероховатых поверхностей, а для некоторых требуется несколько операций финишной обработки для достижения желаемой гладкости. Окраска краской или краской также довольно распространена, как и полировка, шлифовка поверхности и нанесение защитных покрытий.
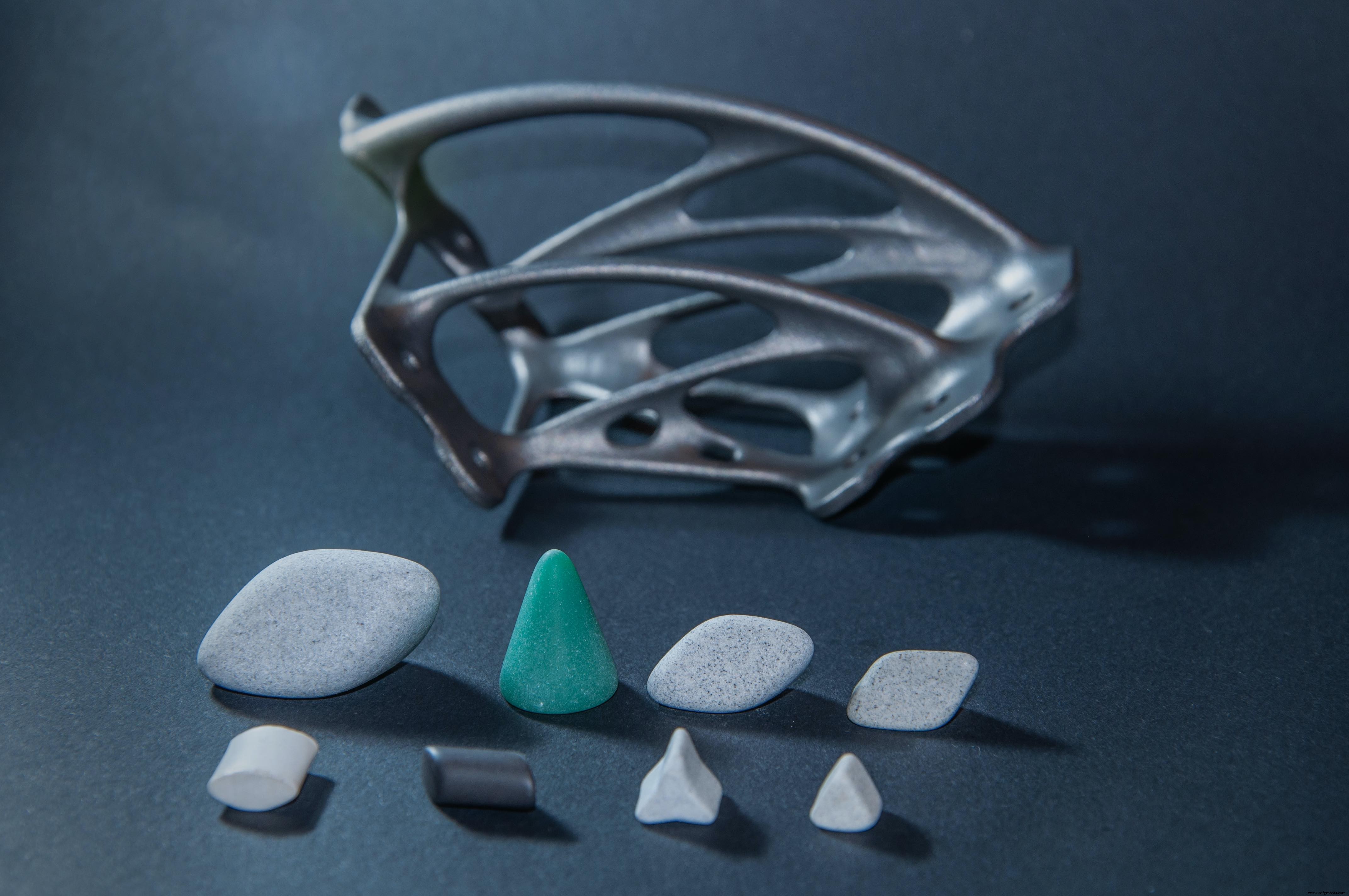
Далее Кершбаум перечисляет различные шаги, необходимые для выполнения этих и других операций постобработки.
К ним относится распаковка заготовок из «торта» в случае струйных и порошковых принтеров. Это удаление поддерживающих структур и сыпучего или спеченного порошка с поверхностей компонентов, а также сглаживание и очистка внутренних проходов. Если объемы позволяют, каждую из этих операций можно выполнять в автоматическом режиме с использованием одной из различных производственных систем марки AM Solutions или выполнять старомодным способом:утомительную шлифовку, сглаживание и полировку вручную.
«Часто вы начинаете с довольно грубой отделки поверхности, но в зависимости от потребностей клиента мы можем без особого труда довести ее до Ra в десятках или даже до однозначных цифр», — говорит Кершбаум. «Дробеструйная обработка и массовая отделка оказались очень эффективными и экономичными процессами для деталей, изготовленных аддитивным способом».
Для постобработки полимерных деталей Луис Фолгар, исполнительный вице-президент компании Additive Manufacturing Technologies (AMT) Inc. из Сидар-Парка, штат Техас, предлагает альтернативу:одну из автоматизированных систем PostPro 3D и PostPro SF50 его компании.
Оба используют запатентованный химический пар, который «безопасен в использовании, относительно недорог и, прежде всего, устойчив» для сглаживания поверхности деталей, напечатанных с помощью технологий порошкового слоя, многоструйного плавления и экструзии.
Полимеры-кандидаты включают нейлон, ABS (акрилонитрилбутадиенстирол), PC (поликарбонат), полипропилен, TPU (термопластичный полиуретан) и TPE (термопластичный эластомер), Ultem и материалы, наполненные стеклом или углеродом, «с PEEK (полиэфирэфиркетон) и PAEK. (полиарилэфиркетон) скоро появится в сети», — говорит Фолгар.
Возможна обработка поверхности детали до 1 мкм Ra (40 µin Ra), добавляет он, с ухудшением размеров не более 0,4 процента, снижением пористости поверхности и растрескивания, а также улучшенными цветовыми характеристиками готовой детали. Как и Rosler и другие поставщики, AMT также предлагает автоматизированные системы обеспыливания и дробеструйной очистки.
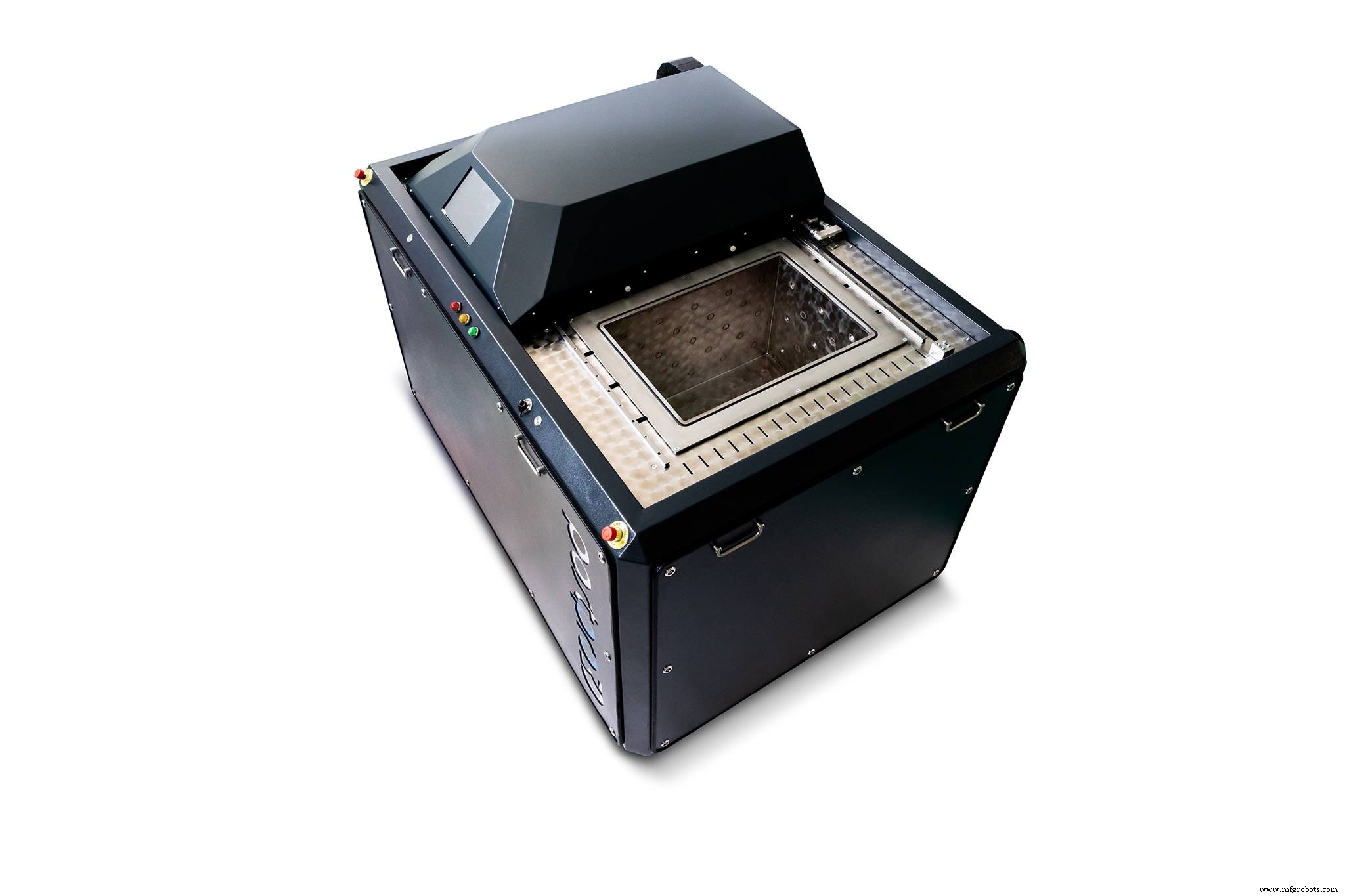
Фелипе Кастанеда — промышленный дизайнер и креативный директор MakerBot в Бруклине, Нью-Йорк, дочерней компании Stratasys. Он отмечает, что для деталей, изготовленных методом FFF (изготовление плавленых нитей), одним из наиболее эффективных способов удаления поддерживающих структур после печати является использование растворимых материалов.
Первым из них является ПВС (поливиниловый спирт), мягкий, биоразлагаемый полимер , который тает под воздействием теплой водопроводной воды. Просто бросьте готовые детали, взболтайте их в течение нескольких минут, и вы получите деталь без опоры. Это хорошо работает для более мягких материалов, таких как PLA (полимолочная кислота) и PETG (полиэтилентерефталатгликоль), но для «более сложных полимеров», таких как ABS, MakerBot поддерживает использование SR-30 от Stratasys.
Как и ПВС, он растворяется в воде, но требует небольшого количества NaOH (едкого натра или щелочи) и немного более высоких температур. Каждый из них применяется во время процесса печати, при этом головка напыления автоматически переключается между заготовкой и вспомогательным материалом по мере необходимости.
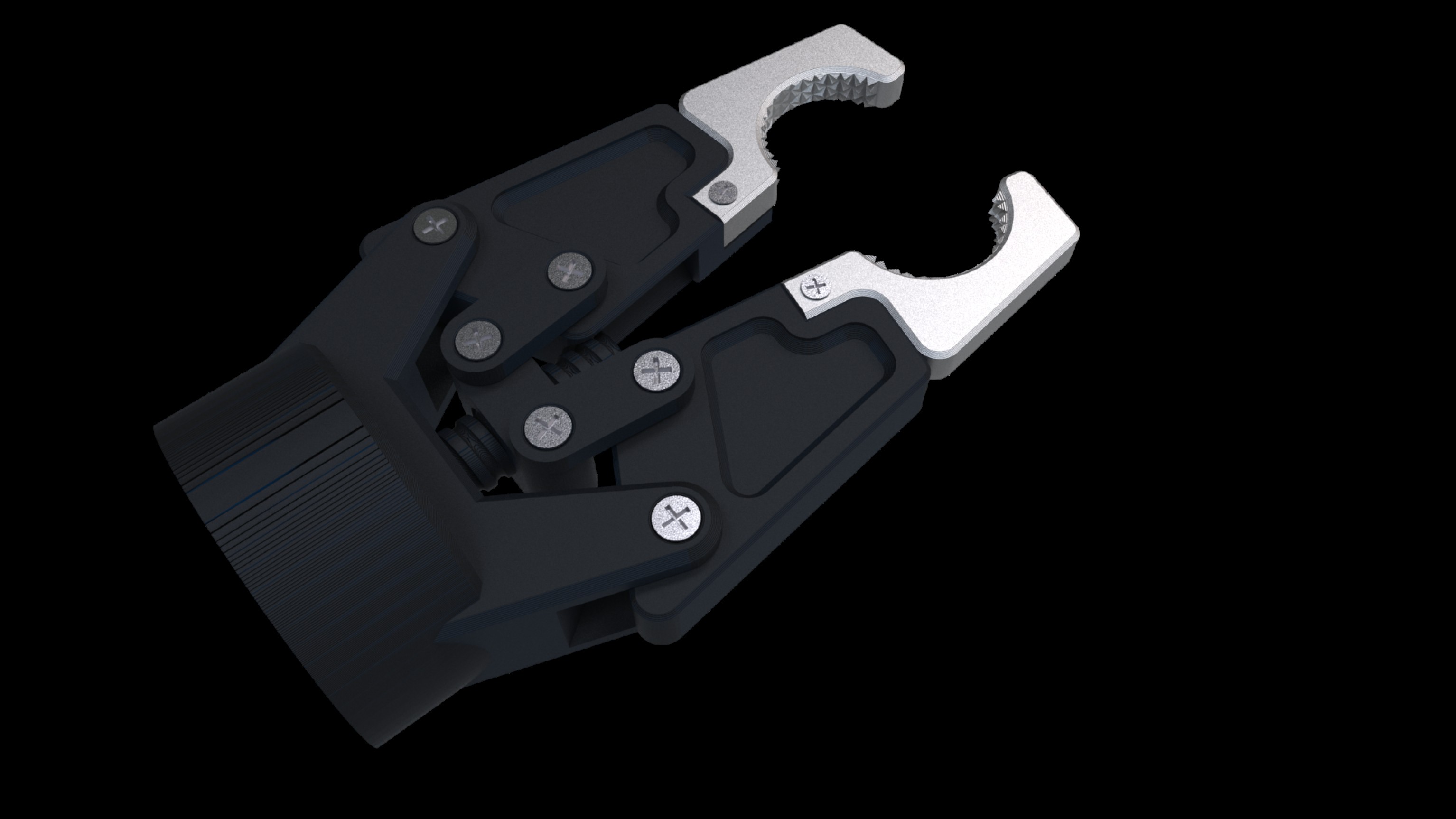
Прелесть этих и других растворимых материалов заключается в возможности создавать опорные конструкции для сложных деталей и особенно внутренней геометрии, которые в противном случае было бы довольно сложно удалить механическими средствами.
Другим вариантом является печать так называемых отрывных поддержек. Здесь львиная доля подложки печатается из того же материала, что и заготовка, а ПВА или СР-30 наносятся только в местах стыка детали и ее подпорок. Процесс удаления такой же, но поскольку печатающей головке не нужно так часто переключаться между материалами, это ускоряет процесс сборки.
«Это также сокращает время, необходимое для роспуска, поэтому во многих случаях он обеспечивает подход, объединяющий лучшее из двух миров», — говорит Кастанеда.
Как упоминалось в начале, существует также механическая обработка, шлифовка и, в случае металлических деталей, термическая обработка, используемая для снятия внутренних напряжений детали и при необходимости упрочнения заготовки.
Поскольку металлы, используемые в большинстве процессов 3D-печати, в значительной степени идентичны их кованым или литым аналогам, здесь нет никакой магии — просто распилите или проволоките электроэрозионной проволокой часть, свободную от рабочей пластины, зажмите ее и приступайте к резке.
Какие методы вы используете для постобработки деталей, изготовленных с помощью аддитивного производства? Поделитесь своими мыслями и идеями в комментариях ниже.
Промышленные технологии
- 8 способов, которыми промышленная 3D-печать меняет производство
- Постобработка для промышленной 3D-печати:путь к автоматизации
- Интервью с экспертом:Джонатан Варбрик из Graphite Additive Manufacturing о достижении успеха с помощью 3D-печати
- Печать предохранителя 1 с предохранителем 1
- Подкаст по аддитивному производству, эпизод 3
- Традиционная металлообработка по-прежнему актуальна в производстве
- Аддитивное производство выходит за рамки настольной 3D-печати
- Пример использования 3D-печати в производстве
- Влияние аддитивного производства на промышленное производство
- Stratasys:повышение экологичности с помощью 3D-печати