Углеродное волокно позволит использовать eVTOL для воздушного такси
Этот блог является ответом на статью в WIRED , опубликованную в январе 2019 г. журнал, который утверждает, что производство композитов из углеродного волокна сдерживает развитие электромобилей / самолетов с вертикальным взлетом и посадкой (VTOL) для рынка городской мобильности и воздушного такси. Я собираюсь обсудить это, но также предложу несколько потенциально революционных технологий, так что дочитайте до конца.
Хотя я аплодирую автору за освещение этой быстро развивающейся отрасли и за указание на необходимость проектирования с учетом технологичности, временами он вводит в заблуждение, скорее всего, потому, что он не очень хорошо осведомлен в индустрии композитов. Например:
Хотя с технической точки зрения это так, Airbus планирует увеличить количество самолетов А320 до 60 в месяц к середине 2019 года . а Boeing планирует выпустить 57 самолетов в месяц для B737, также в 2019 году. Для A320 это означает производство трех высотой 6,3 м углепластик (углепластик) в сборе с вертикальным оперением в день а также три пролетом 12,45 м Горизонтальное оперение в сборе из углепластика в день .
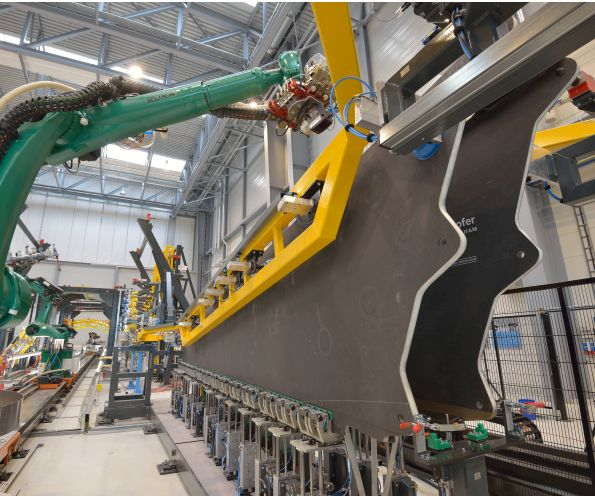
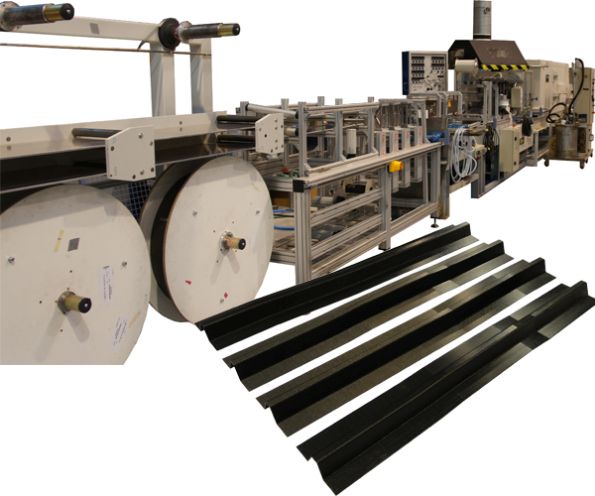
Кроме того, Airbus квалифицирует одну технологию за другой - во многих из них используются композиты, и все они рассчитаны на 60-70 самолетов в месяц - для следующей итерации A320, называемой A320 Neo Plus. Эти технологии композитов охватывают портфель, включая литье полимеров с переносом (RTM), прессование листового формовочного компаунда (SMC) и термопластичные композиты (TPC), время цикла которых легко может достигать 700+ самолетов в год. Некоторые из новейших технологий в разработке сокращают время цикла обработки углепластика с 4 часов до 15 минут или меньше. Большинство новых технологий, одобренных Airbus, в значительной степени автоматизированы, как и новые методы сборки.
Автомобильная промышленность также проложила путь к более высокому массовому производству, чем потребуется для eVTOL ( WIRED привел прогнозируемый спрос на 23000 автомобилей к 2035 году). BMW увеличивает производство своего i3 и i8 модели - обе оснащены пассажирскими ячейками из углепластика - от 130 до 200 единиц в день и поставщик Audi Voith Composites производит заднюю стенку из углепластика для A8 из расчета 150-300 единиц в день . . Обратите внимание, что BMW i3 и i8 модули очень похожи на планер, показанный ниже для Airbus Helicopters EC 135 - оба производителя затем крепят внешние и внутренние компоненты к этой раме.
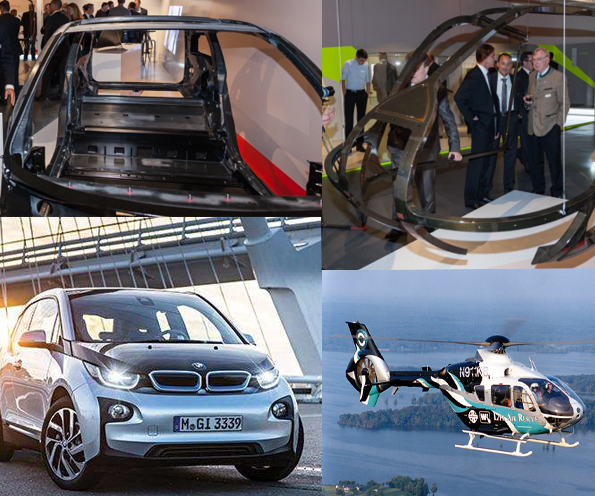
Рамы кузова BMW i3 и i8 очень похож на Airbus Helicopters EC135.
ИСТОЧНИК: Вехи передового кластера - обзор и будущие перспективы, MAI Carbon, стр. 36-7 (вверху), BMW и Airbus Helicopter (внизу).
Между тем Audi A8 Задняя стенка изготавливается с 5-минутным циклом с использованием RTM и автоматизированного размещения сухой ленты из углеродного волокна, адаптированной по длине и ориентации волокон для соответствия конкретным нагрузкам и варьирующейся от основы из 6 слоев (толщиной 1,5 мм) до 19 слоев (толщиной 3,7 мм), в которые добавлена местная арматура для обеспечения высоких точечных нагрузок. Эта единственная деталь обеспечивает 33% жесткости на кручение приводной ячейки при 50% веса по сравнению со сборкой из трех-пяти сварных алюминиевых деталей.
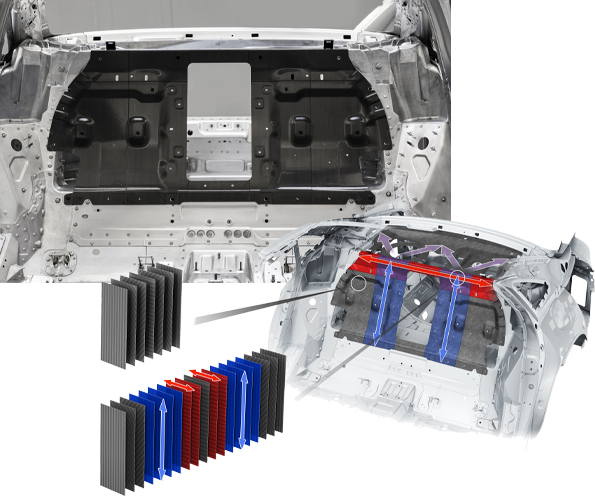
Audi 2019 года A8 имеет заднюю стенку из углепластика, сделанную за 5 минут из ленты из углеродного волокна. ИСТОЧНИК:Audi и Voith Composites.
Термопласты
Но в этих примерах даже не используется термопластическая технология, предпочтительная для нового среднего самолета Boeing (NMA), о котором намечено объявить до 2 квартала 2019 года. Детали из термопласта используются в самолетах с 1990-х годов, а разработка продолжается. с Airbus и европейскими поставщиками Tier 1, которые создают прототипы все больших секций крыла и фюзеляжа (со встроенными ребрами жесткости), которые в этом году будут масштабированы до полноразмерных демонстраторов фюзеляжа. Обратите внимание, что термопластические композиты также позволяют выполнять сварку, что дает дополнительные возможности для устранения крепежа и сборки.
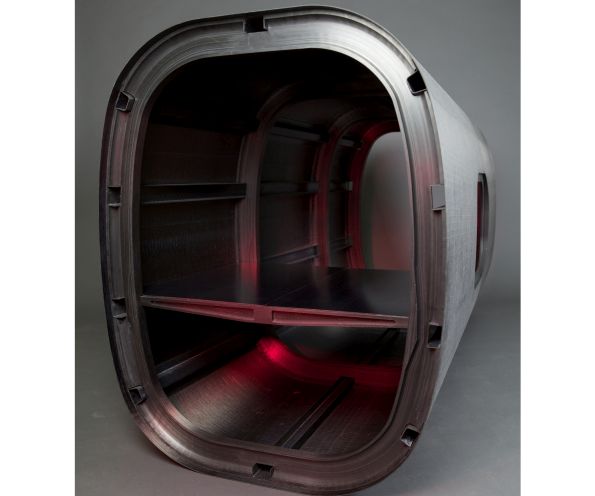
Automated Dynamics, теперь часть Trelleborg Group , произвела эту полноразмерную хвостовую балку вертолета из CF / PEEK с интегральной жесткостью в 2012 году, используя консолидацию на месте во время автоматической укладки волокон, исключив длительные циклы автоклавирования, а также крепежи и клеи.
ИСТОЧНИК:Automated Dynamics, Trelleborg
Цепочка поставок материалов и обработки TPC быстро срослась за последние три года, и теперь все основные поставщики углеродного волокна производят термопластичные ленты и формованные детали с малым временем цикла, продемонстрированные несколькими компаниями как для аэрокосмической, так и для автомобильной промышленности. Сварка термопластов также была продемонстрирована несколькими компаниями.
Выдержка из интервью «Формование поверх композитов, от аэрокосмической до автомобильной», интервью Скотта Кинга из компании CCP Gransden, производящей композиты:
Компания CCP Gransden усовершенствовала свою технологию одноэтапного термоформования и литья под давлением термопластичных композитов для производства легких сложных компонентов с длительностью цикла менее 2 минут с использованием широкого диапазона полимеров и волокон. ИСТОЧНИК:CCP Gransden
Новейшие технологии
Но с 2014 года технология продвинулась вперед и теперь включает несколько интересных разработок:
Термопласты с отформованными поверхностями
В рамках проекта OPTO-Light в AZL Aachen были продемонстрированы ребра и зажимы из термопластичного композита (TPC) на углеродном волокне / эпоксидной смоле . составная часть.
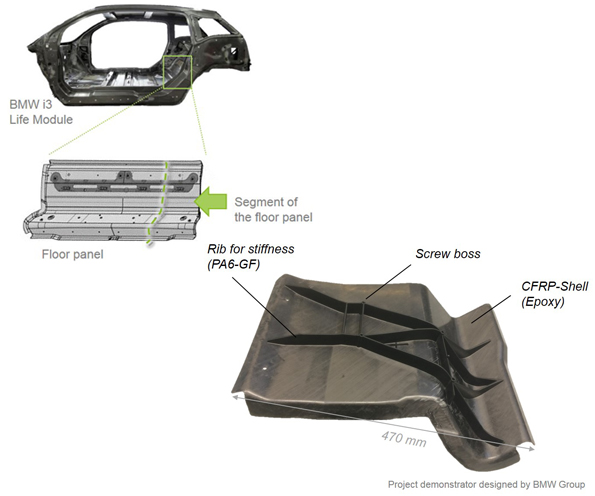
Формование поверх + UD несущие пултрузии
В рамках проекта MAI Skelett были продемонстрированы отформованные пултрузии TPC в двухэтапном 75-секундном процессе для производства конструктивного элемента крыши / рамы лобового стекла, который превосходит все BMW i3 требования к деталям при интеграции насадок и зажимов, а также изменение поведения при столкновении с хрупкого на вязкое разрушение для повышения остаточной прочности BIW.
Партнер проекта SGL Carbon в настоящее время поставляет углеродное волокно с подходящими размерами для решений с одной матрицей с использованием семейства PP или PA6, включая пултрузию, органолист и компаунд для формования, а также опыт проектирования и технологического процесса для разработки деталей, последнее через их Центр легких приложений (LAC, Майтинген, Германия).
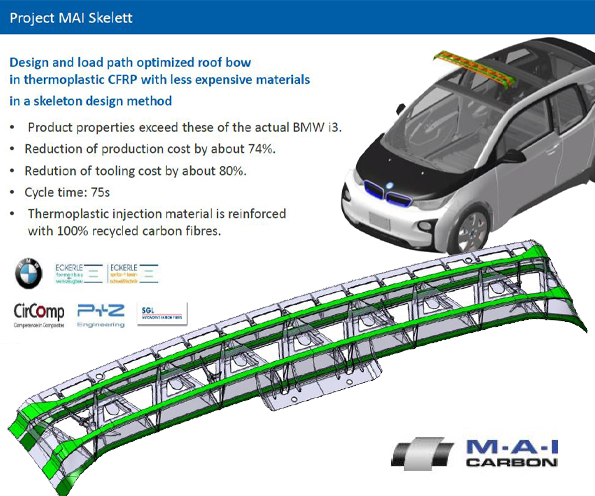
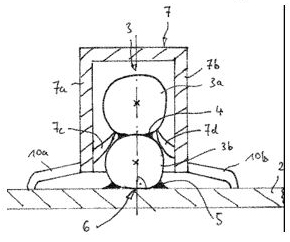
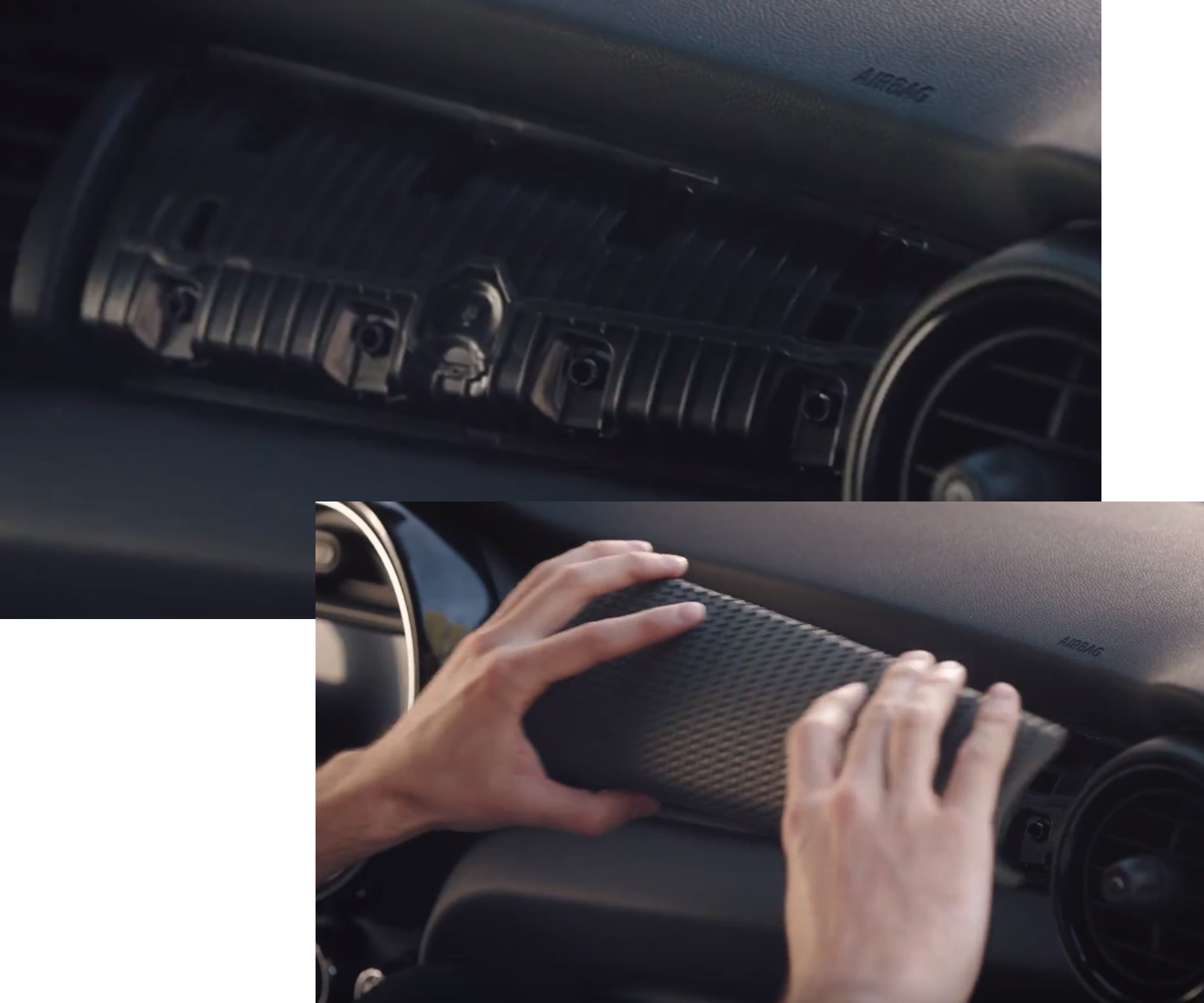
Запатентованный новый BMW , высокоточная система крепления использует литые под давлением зажимы (внизу) и шарики, напечатанные на 3D-принтере (вверху), без застежек, просверленных отверстий или клея. На нижних изображениях показано, как эта система позволяет «прикрепить» изготовленную на 3D-принтере внутреннюю отделку в рамках программы MINI Yours Customized 2019 года.
ИСТОЧНИК:Патент DE 10 2013 г. 214 269 B3 (вверху)
https://www.youtube.com/watch?v=1pyxNKw-nf8 (внизу)
Вернуться к ПРОВОДНОЙ статья и ее необоснованные утверждения:
Это правда, что этот метод производства углепластика использовался в течение многих лет, но также верно и то, что производители самолетов и автомобилей уже перешли на более автоматизированные, практически нулевые отходы материалов и процессов, а также термопласты с доказанными преимуществами в устранение крепежных элементов, возможность вторичной переработки / вторичного использования и ремонтопригодность.
В конце концов, ПРОВОДНОЙ Автор полностью противоречит своему тезису, потому что пионер eVTOL ICON планирует не только продвигать вперед свой планер из углепластика, но и производить детали для более крупных самолетов. Углеродное волокно, очевидно, не будет служить основанием для eVTOLS, но вместо этого уже играет ключевую роль в компаниях, продвигающих интеллектуальные разработки для широкого диапазона транспортных средств будущего, как в воздухе, так и на дороге. Использование новейших технологий имеет смысл, потому что все эти новые автомобили в любом случае должны быть сертифицированы.
Один из ключевых моментов был из статьи генерального директора BetaTechnologies Кайла Кларка:
Генеральный директор Blue Force Technologies Скотт Бледсо также подчеркнул важность наличия аэродинамики, силовой установки, стиля, конструкции и производства . команды, каждая из которых имеет равное место за столом на каждом этапе проектирования и разработки.
Но, пожалуй, самое важное - быть в курсе того, куда движется производство композитов, и связываться со многими поставщиками материалов, оборудования и технологий, которые хотят поделиться своим опытом и помочь в разработке будущих приложений. Свяжитесь с нами на CompositesWorld потому что это то, что мы делаем - обеспечиваем надежные технические связи и информацию.
Смола
- Углеродное волокно
- 3 причины, по которым производители углеродного волокна в ближайшее время будут делать больше
- Что такое углеродное волокно?
- Развитие пластмасс, армированных углеродным волокном
- Пластик, армированный углеродным волокном (CFRP)
- Проводит ли углеродное волокно?
- Fords Last GT будет суперкаром из углеродного волокна ограниченной серии
- Обновленная кабина самолета от Pagani и Airbus с цифровым потолком
- Кроссовки Air Jordan 1 из углеродного волокна - необходимость коллекционера
- Утилизация композитов - больше никаких оправданий