RTM сжатия для производства будущих аэроструктур
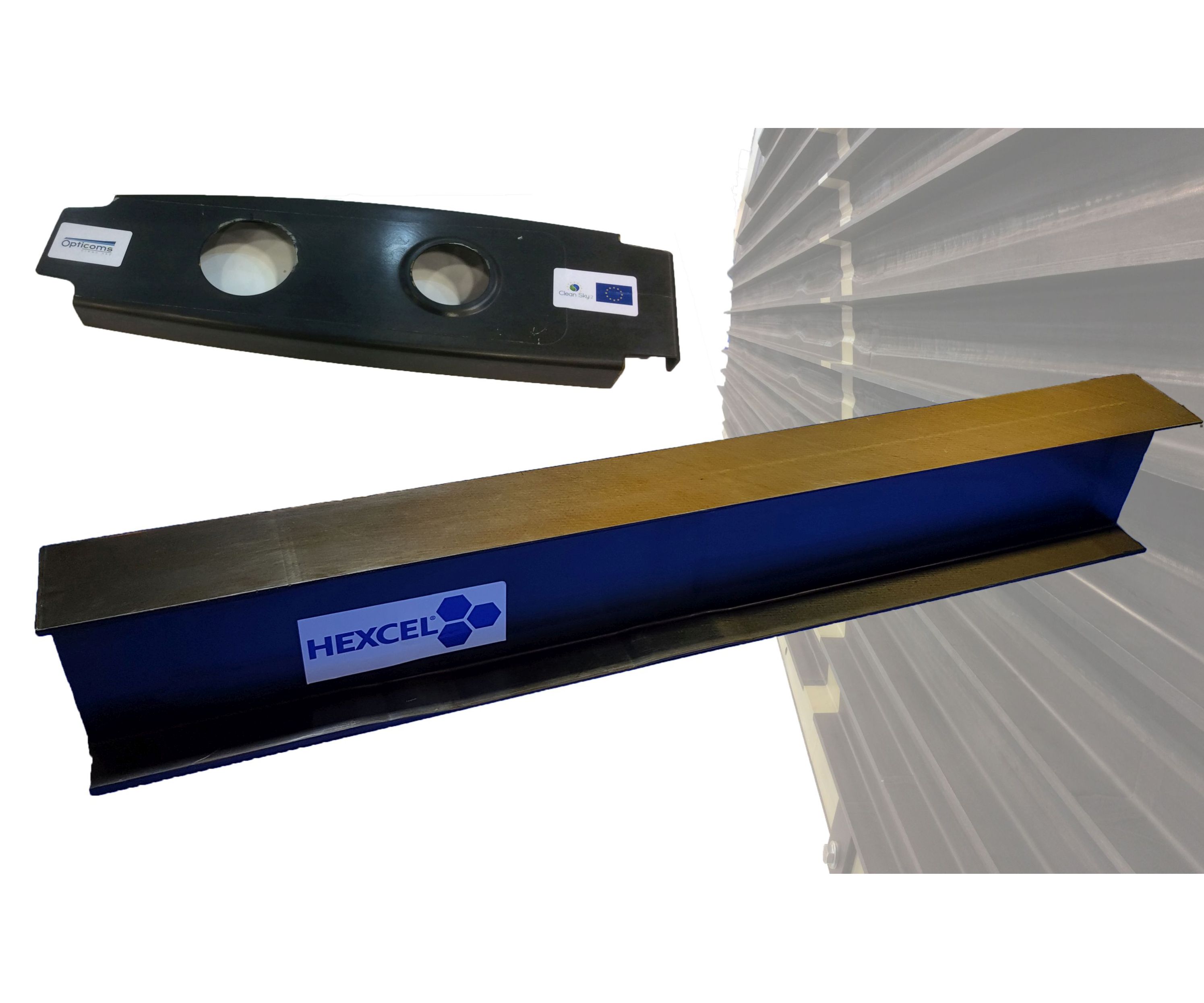
Композиты заняли постоянное место в корпусах коммерческих авиалайнеров, поскольку они позволяют создавать высокопрочные и легкие конструкции, которые обеспечивают более низкие затраты на техническое обслуживание по сравнению с металлом. Текущие прогнозы для следующего поколения как широкофюзеляжных, так и узкофюзеляжных самолетов показывают, что производство композитных планеров будет продолжаться, но только в том случае, если материалы и процессы смогут удовлетворить сложные задачи по низкой стоимости и высокой производительности. Хотя на сегодняшний день эпоксидный препрег, отверждаемый в автоклаве, безраздельно господствует в корпусах самолетов, армированных углеродным волокном (CFRP), разработчики самолетов следующего поколения активно используют технологии вне автоклавов (OOA) с интегрированной автоматизацией и встроенной инспекцией в качестве ключевых факторов для достижения успеха. производство будущего Индустрии 4.0.
Поставщик оборудования и средств автоматизации Techni-Modul Engineering (Coudes, Франция) и его дочерняя компания в США Composite Alliance Corp. (Даллас, Техас, США) установили партнерские отношения с британскими и французскими подразделениями поставщика передовых материалов Hexcel (Стэмфорд, Коннектикут, США). продемонстрировать автоматизированное OOA производство нервюр и стрингеров из углепластика. Детали изготавливаются с помощью автоматизированного предварительного формования сухого армирования из углеродного волокна Hexcel и процесса прессования с переносом смолы (C-RTM), который обеспечивает быстрое проникновение жидкой эпоксидной смолы Hexcel HexFlow RTM6 для производства деталей с объемом волокна 60% и пустотами менее 1%. в 2,5–3,0-часовом цикле, который можно масштабировать для производства нескольких деталей для высокопроизводительного производства.
Разработка сухого армирования
«Мы рассматриваем литье из жидких композитов (LCM) как ответ на трехстороннюю задачу:снизить стоимость, быть готовым к скорости и обеспечить рабочие характеристики первичной структуры», - поясняет Реми Пагьяк, Инженер службы технической поддержки Hexcel по формованию жидких композитов. Компания Hexcel разработала материалы HiMax noncrimp fabric (NCF) и HiTape однонаправленные (UD) из углеродного волокна для удовлетворения требований к характеристикам первичной структуры при использовании процессов LCM. HiMax позволяет быстро укладывать большие плоские конструкции, такие как крылья, в то время как HiTape позволяет настраивать укладку больших и сложных конструкций с минимальными отходами. «Мы можем добиться свойств, аналогичных UD-препрегам последнего поколения», - добавляет Пагьяк.
Hexcel работал над уменьшением пухлости и улучшением драпируемости с помощью HiMax NCF, включая тонкую пряжу стежком 20 dTex. Материалы HiMax производятся на предыдущем предприятии Formax в Лестере, Великобритания, которое Hexcel приобрела в 2016 году. Легкие многоосные буксировщики, производимые на этом предприятии, уже давно предлагают решения для требовательных приложений, таких как гоночные яхты, суперкары и Formula. 1 гоночные автомобили. Теперь материалы NCF используются в проекте демонстрационного крыла, выполненном Airbus Defense and Space (Airbus DS, Кадис, Испания) и Danobat (Эльгойбар, Испания) с использованием последней технологии автоматизированного размещения сухих материалов (ADMP) - типа автоматизированного размещения волокон. (AFP) для NCF (см. «Доказательство жизнеспособности сухой инфузии тканей для больших аэроструктур») - и в проекте ZAero, спонсируемом Airbus, для конструкций из углепластика с нулевым дефектом, таких как крылья крыльев со стрингерами (см. «Производство композитных деталей без дефектов. »).
Как в HiMax, так и в HiTape, Hexcel объединяет слои тонкой, малоплоской термопластичной филаментной вуали, которая действует как связующее, устраняя необходимость в порошковых связующих, которые исторически использовались в сухих материалах для предварительного формования и жидкого формования. Для HiMax эта вуаль прокладывается между слоями NCF; в случае HiTape вуаль наклеивается на обе стороны ленты из углеродного волокна. «При этом вам не нужно использовать порошковое связующее, чтобы удерживать слои UD на месте», - объясняет Паньяк. «HiTape откалиброван и не является лентой с прорезями, поэтому нет« пушинок »и меньше вариаций по ширине для улучшенной обработки AFP. Термопластическая вуаль также добавляет прочности конечному слоистому материалу, и мы продемонстрировали, что можем достичь высоких скоростей наплавки материала с помощью следующего поколения машин AFP ». В статье SAMPE, опубликованной в мае 2015 года, Hexcel описывает преформу одинарной кривизны, изготовленную с использованием ленты HiTape шириной 0,25 дюйма, нанесенной на оборудованном лазером аппарате Coriolis Composites (Quéven, Франция) AFP со скоростью укладки 1 метр / секунду. Он также работал с оборудованием AFP Electroimpact (Мукилтео, Вашингтон, США), чтобы продемонстрировать скорость наплавки до 150 кг / час для полноразмерной лонжеронной конструкции.
Рис. 1 RTM со сжатием
В C-RTM сухая преформа помещается в RTM-форму, но форма только частично закрывается, оставляя зазор между сухой преформой и верхней поверхностью формы. Затем применяется вакуум, впрыскивается смола, и пресс закрывает зазор в форме, проталкивая жидкую смолу в преформу в z-направлении по всей детали. Источник | Hexcel

Адаптация C-RTM для авиакосмической промышленности
C-RTM был впервые представлен с RTM высокого давления (HP-RTM) для автомобильных композитов. Как и в случае с обычным RTM, C-RTM влечет за собой помещение преформы из сухого волокна в соответствующую металлическую форму, впрыскивание жидкой смолы в преформу и затем приложение тепла и давления с помощью приводимого в действие пресса. Однако в C-RTM форма только частично закрывается, оставляя зазор между сухой преформой и верхней поверхностью формы (рис. 1). Затем применяется вакуум, впрыскивается точная доза смешанной смолы, и пресс закрывает зазор в форме, заставляя жидкую смолу опускаться в преформу в z-направлении по всей детали. «Это намного быстрее, чем впрыскивание смолы в плоскость детали», - объясняет инженер-технолог Techni-Modul Engineering Томас Шевалле.
Компания Techni-Modul Engineering увидела возможность адаптировать C-RTM для аэрокосмической промышленности во время своей роли партнера в проекте Clean Sky 2 «Оптимизированные композитные конструкции» (OPTICOMS). Организованная в рамках рабочего пакета B-1.2 («Более доступные композитные конструкции»), OPTICOMS нацелена на снижение производственных затрат на небольшие самолеты (например, региональных реактивных лайнеров) за счет интегрированных структур и автоматизированного производства, исследуя как методы препрега, так и жидкие полимеры. Компания OPTICOMS разработала демонстрационный образец композитного крыла, включающий верхнюю обшивку крыла с тремя лонжеронами, изготовленную в виде единой конструкции за один проход. Полномасштабное крыло (рис. 2) является частью демонстратора инновационных технологий (ITD) AIRFRAME для оценки и доведения технологий до уровня технологической готовности (TRL) 6 для самолетов следующего поколения, которые будут производиться с 2025 года. В июле 2016 года в качестве координатора OPTICOMS была выбрана компания Israel Aerospace Industries (Лод, Израиль). В консорциум также входят производители малых самолетов Piaggio Aerospace (Савона, Италия), Techni-Modul Engineering и поставщики оборудования AFP Coriolis Composites и Danobat.
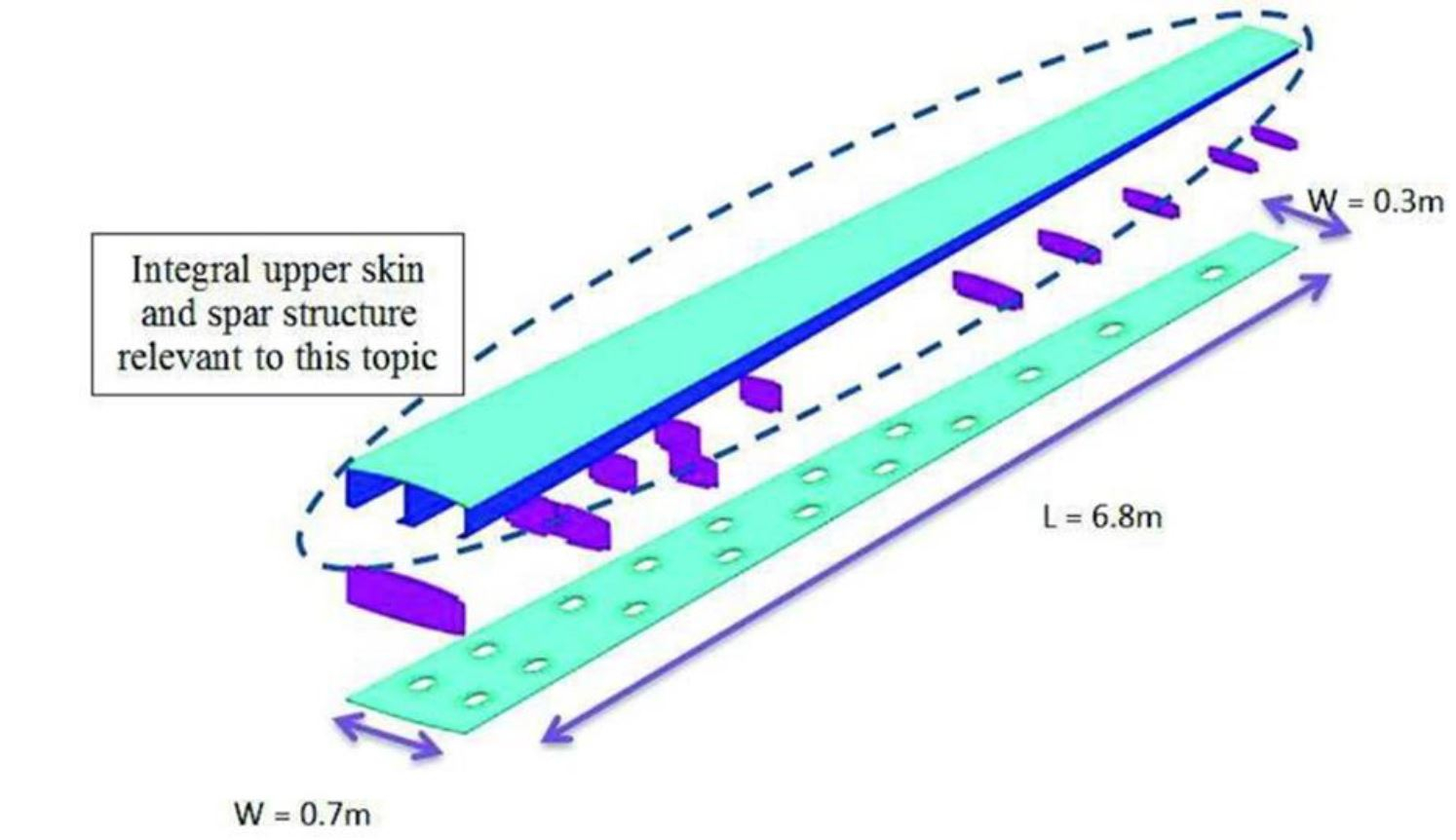
Рис. 2 Ребра Clean Sky 2 OPTICOMS
Techni-Modul является партнером проекта Clean Sky 2 «Оптимизированные композитные конструкции» (OPTICOMS), который разработал демонстрационный образец композитного крыла, включающий нижнюю часть обшивки крыла, несколько нервюр и верхнюю обшивку крыла с тремя лонжеронами. Последний изготавливается как интегрированная конструкция в однократном режиме. Демонстрационный образец будет оцениваться для самолетов следующего поколения, которые будут производиться с 2025 года. Источник | Чистое небо 2
«C-RTM была хорошо известна в отрасли, - объясняет Шевалле, - но с HP-RTM по-прежнему нужен большой печатный станок. Наша разработка заключалась в адаптации C-RTM для быстрого впрыска при более низком давлении, что позволяет производить менее дорогостоящее производство деталей для аэрокосмической отрасли с очень строгими требованиями к большому объему волокна, выравниванию волокон и малым пустотам. Время впрыска нервюры крыла длиной 0,7 метра и шириной 0,2 метра в проекте OPTICOMS было сокращено с 40 до пяти минут. В отдельной программе испытаний стрингера двутавровой балки длиной 900 миллиметров и высотой 150 миллиметров время впрыска было сокращено с одного часа до менее пяти минут.

«Это сокращение времени впрыска, предлагаемое C-RTM, будет еще больше для крупных деталей, таких как цельнокроеные крылья или лопасти винта вертолета», - добавляет Шевалле. Он отмечает, что C-RTM также позволяет впрыскивать высоковязкие смолы, а также использовать системы впрыска при более низком давлении и малотоннажные прессы, что снижает затраты. «Давление в пресс-форме во время C-RTM составляет всего 6 бар, что намного ниже, чем то, что используется в HP-RTM», - объясняет Шевалле. «Этот процесс позволяет получать композиты аэрокосмического качества, но при этом хорошо подходит для больших, тонких деталей и небольших деталей сложной формы».
Автоматическая предварительная формовка
Хотя более быстрое и дешевое впрыскивание смолы и формование OOA являются ключевыми частями этого подхода для более доступного производства аэрокомпозитов, технологическая цепочка по-прежнему требует нескольких этапов для резки и укладки материалов и предварительного формования. «Для нас OPTICOMS также была связана с автоматизацией, - говорит Шевалле. Компания Techni-Modul Engineering поставила не только систему впрыска C-RTM для проекта OPTICOMS, но также робота для захвата и размещения и машину для горячего формования (HDF), которые были интегрированы в полностью автоматизированную производственную ячейку.
Вскоре после открытия OPTICOMS в 2016 году дочерняя компания Techni-Modul Engineering, CAC, получила награду ACE Equipment and Tooling Innovation Award в производственной категории за свою автоматизированную ячейку для 3D-преформования на выставке CAMX 2016 (26-29 сентября, Анахайм, Калифорния, США). В ячейке, способной изготавливать трехмерные преформы из сухого волокна или препрега, использовались вакуумные захваты для захвата, размещения и складывания отрезанных слоев на нагретую форму для преформ. Techni-Modul Engineering и CAC разработали программное обеспечение для подготовки разрезов 2D-материалов для формирования сложных и разворачиваемых поверхностей. Эта ячейка получила дальнейшее развитие в OPTICOMS и проекте испытаний двутавровой балки.
Шаг 1
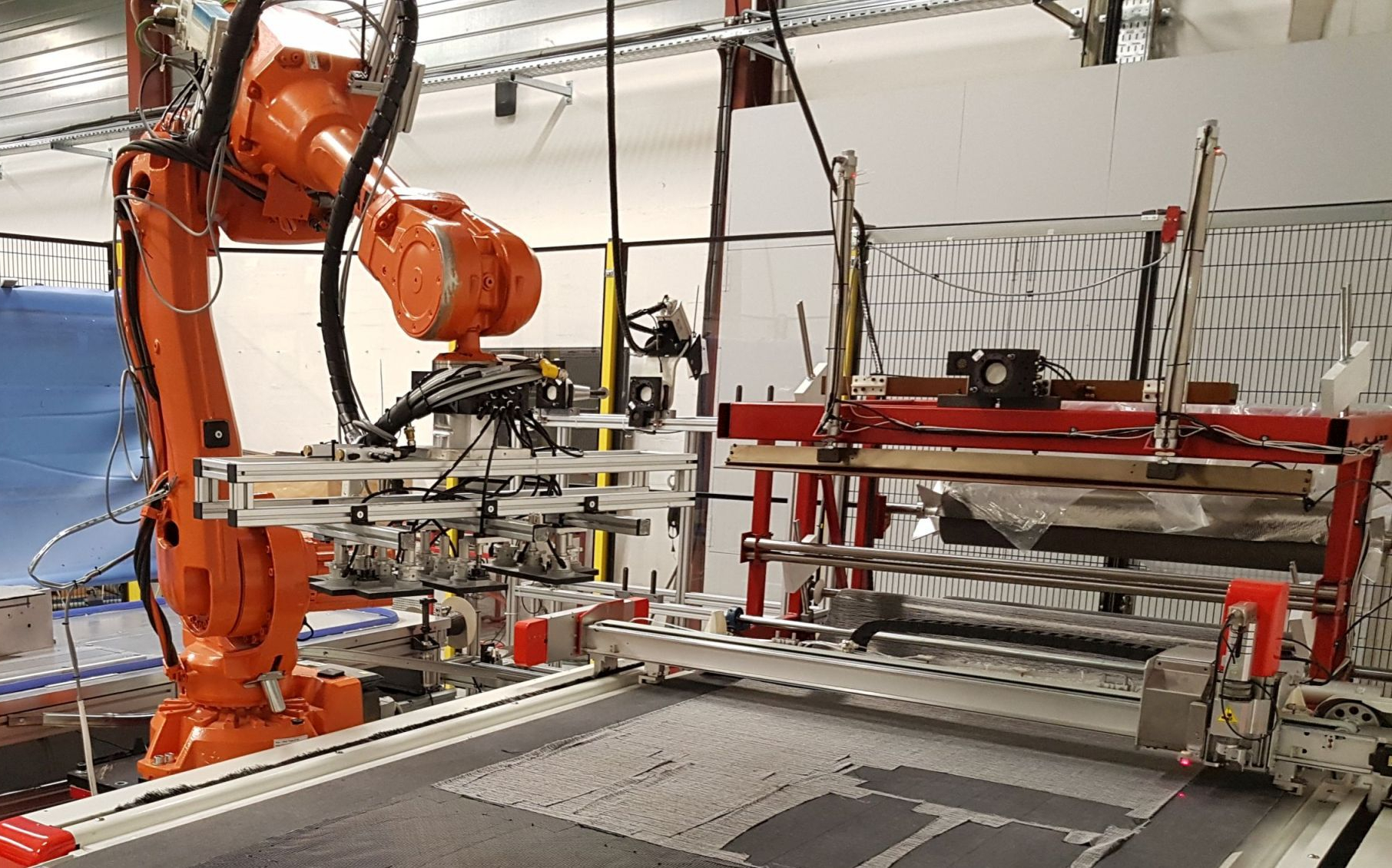
Источник, все изображения шага | Техни-Модуль Инжиниринг
В автоматизированной ячейке Techni-Modul Engineering робот-захватчик снимает слои с автоматического резака и прикладывает их к нагретому инструменту для предварительной формовки.
Шаг 2

Инструменты для предварительного формования располагаются на столе для уплотнения с шарнирной многоразовой вакуумной мембраной (синяя, слева), используемой для выполнения горячего удаления массы через каждые 5-8 слоев во время укладки.
Шаг 3
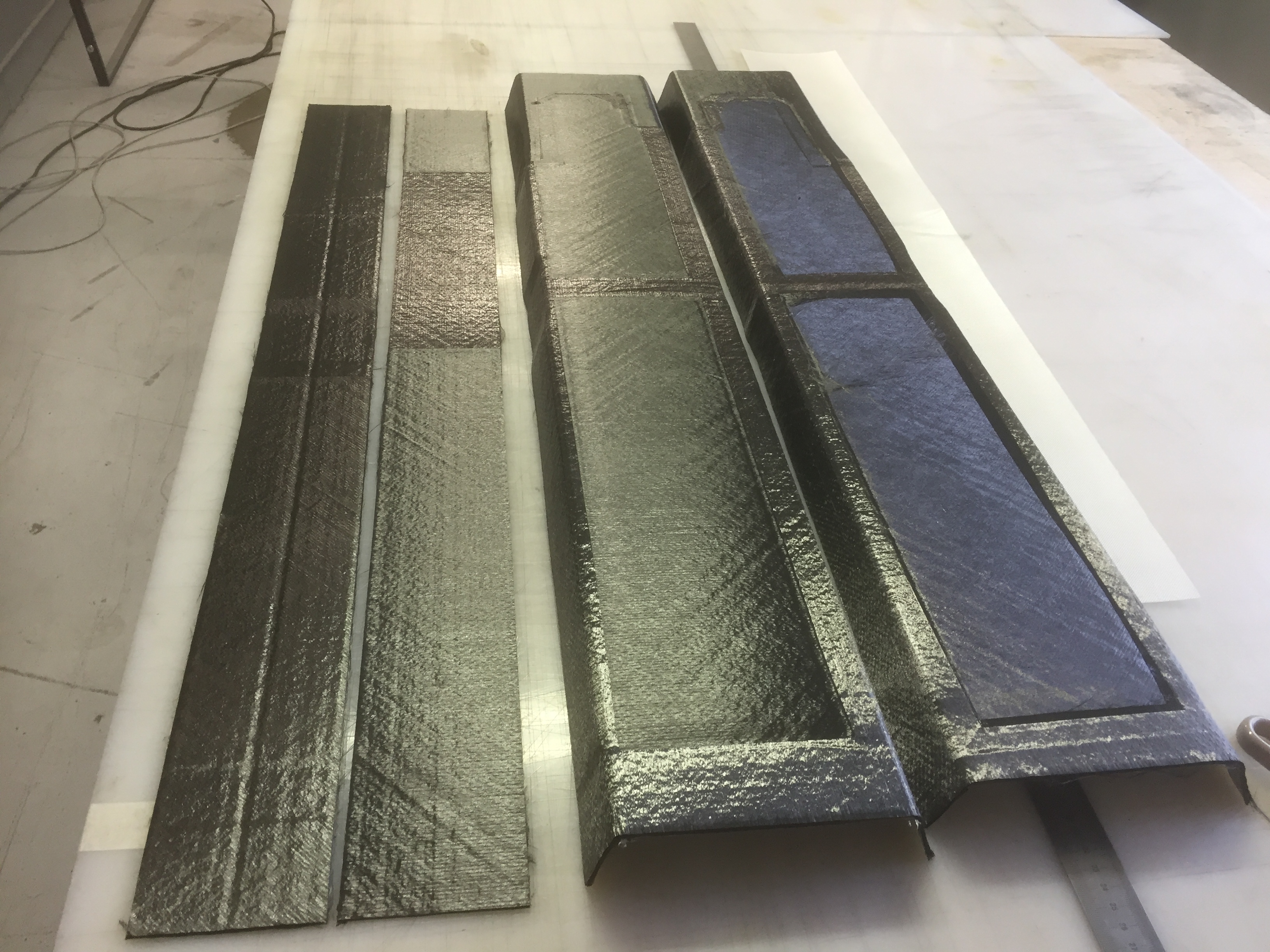
Каждый цикл предварительной формовки стрингера производит одну заготовку C-образной балки (две составляют стенку двутавровой балки) и одну заготовку с плоским фланцем. Здесь показаны два комплекта, необходимые для каждого стрингера двутавровой балки.
Шаг 4
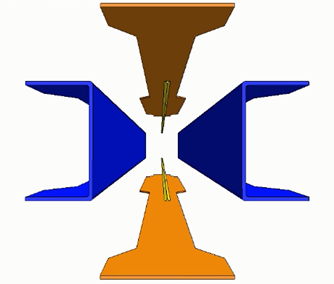
Четыре преформы стрингера двутавровой балки помещаются в пресс-форму RTM, создается вакуум и инжекция смолы завершается за 5 минут.
Шаг 5
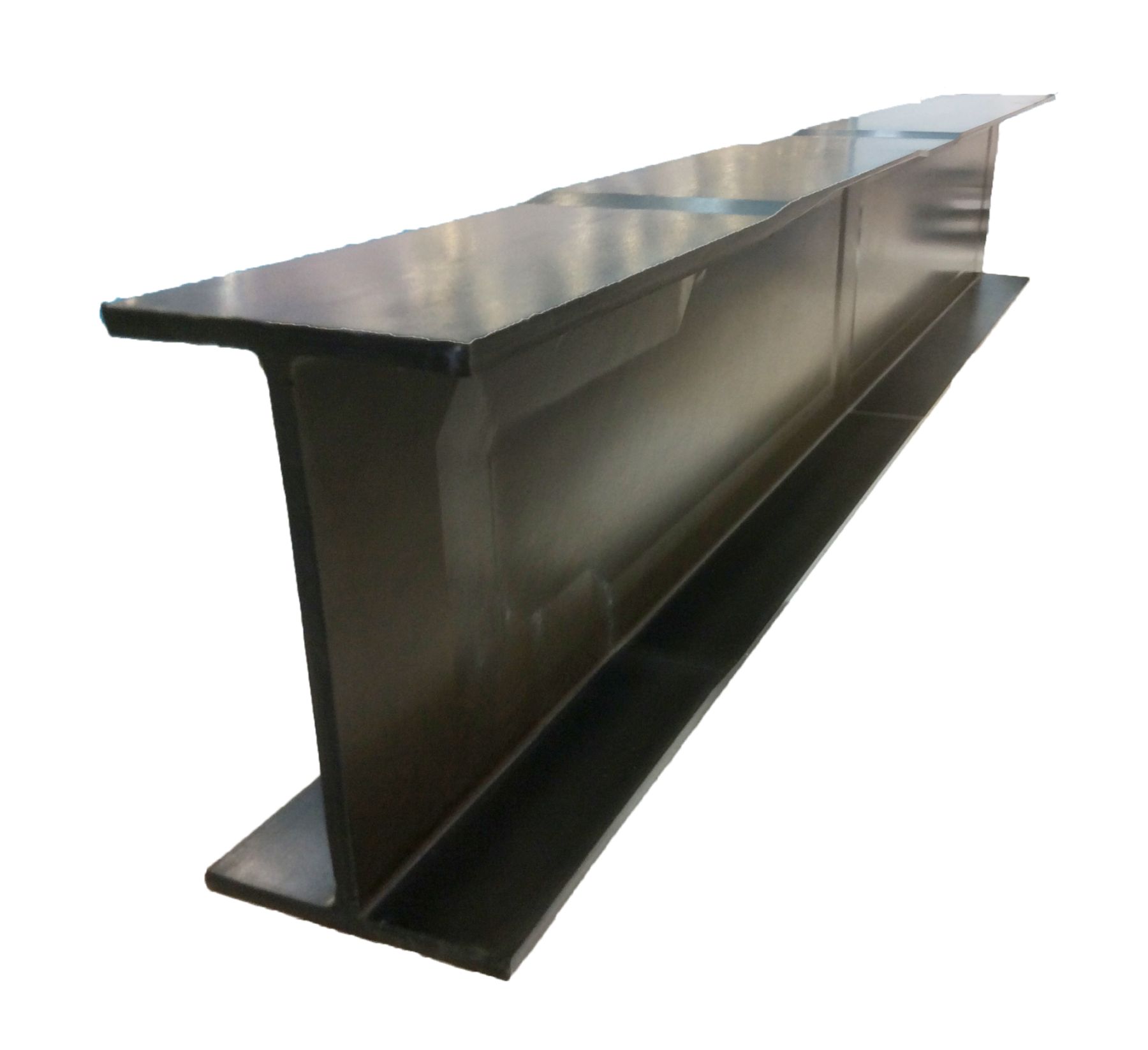
После 90-минутного отверждения стрингер извлекается из формы и обрезается смола для полного цикла обработки детали продолжительностью 4,5 часа.

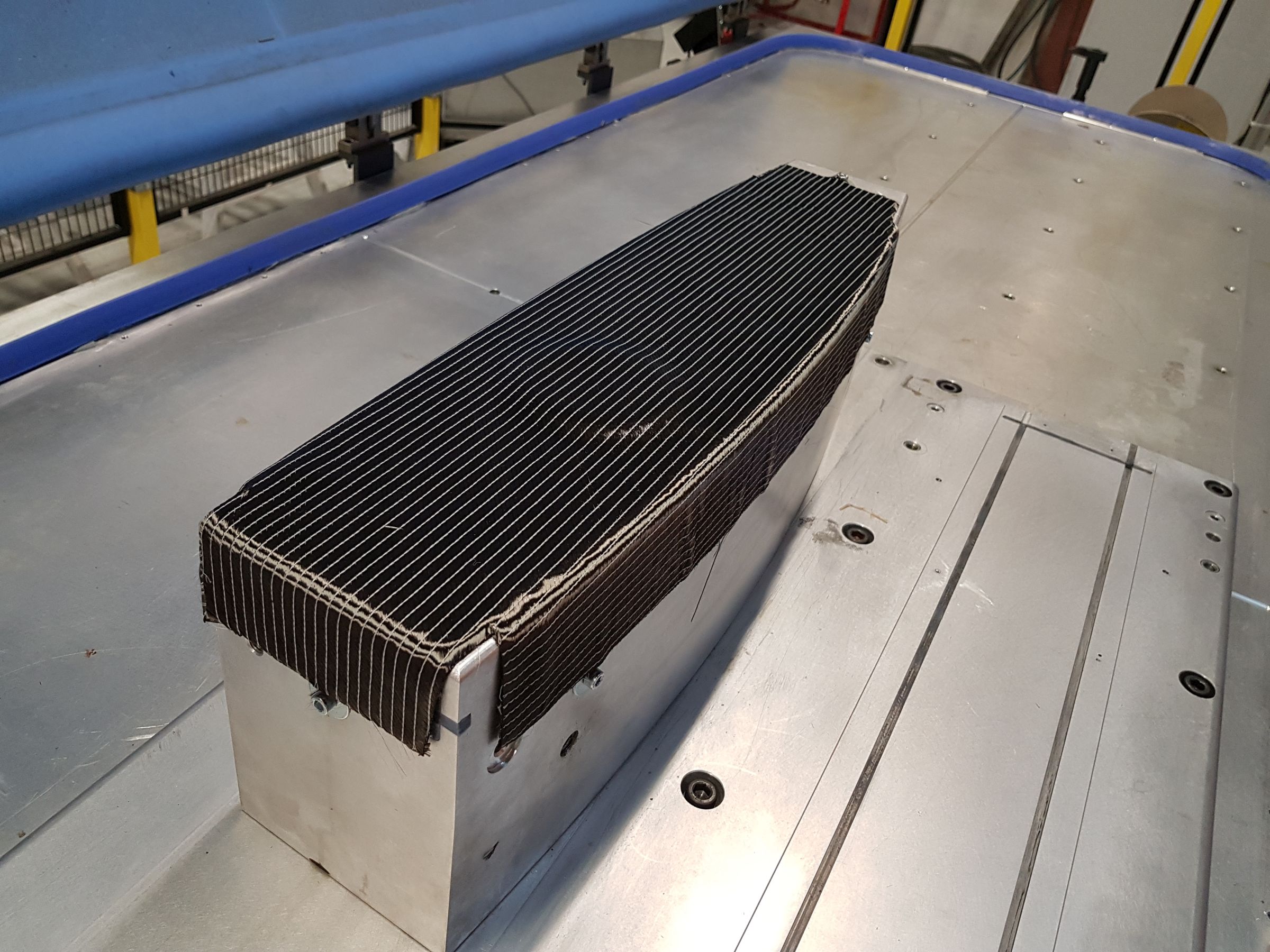
Робот размещает обрезанные слои на нагретом инструменте для изготовления преформ. Каждые 5-8 слоев выполняется отбортовка с подогревом для уплотнения преформы.

Перед удалением массы наносится синяя разделительная пленка.
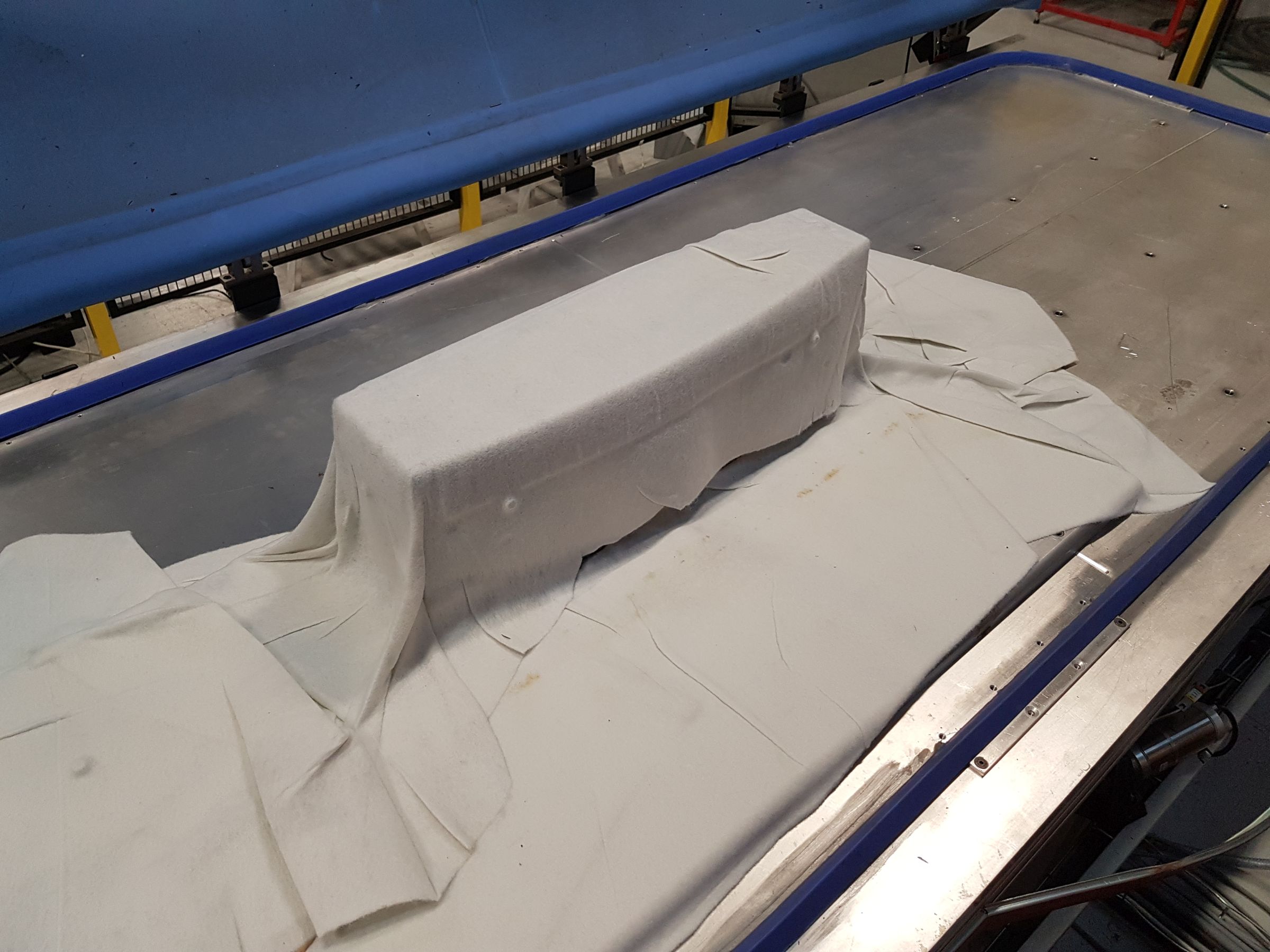
Сапун используется для удаления воздуха через преформу.
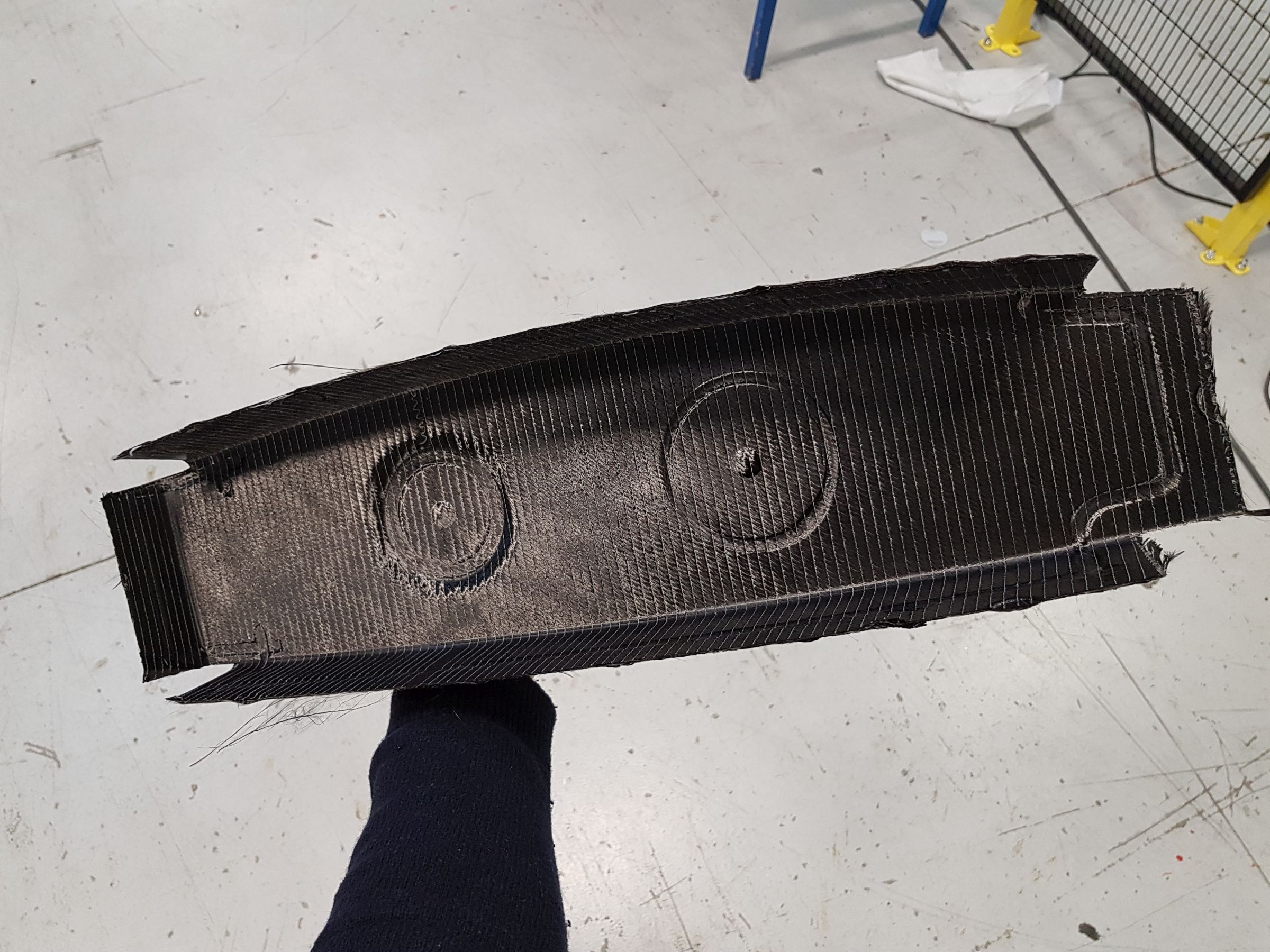
После окончательной обработки заготовка на инструменте охлаждается и вырезы обрезаются (см. Ниже).
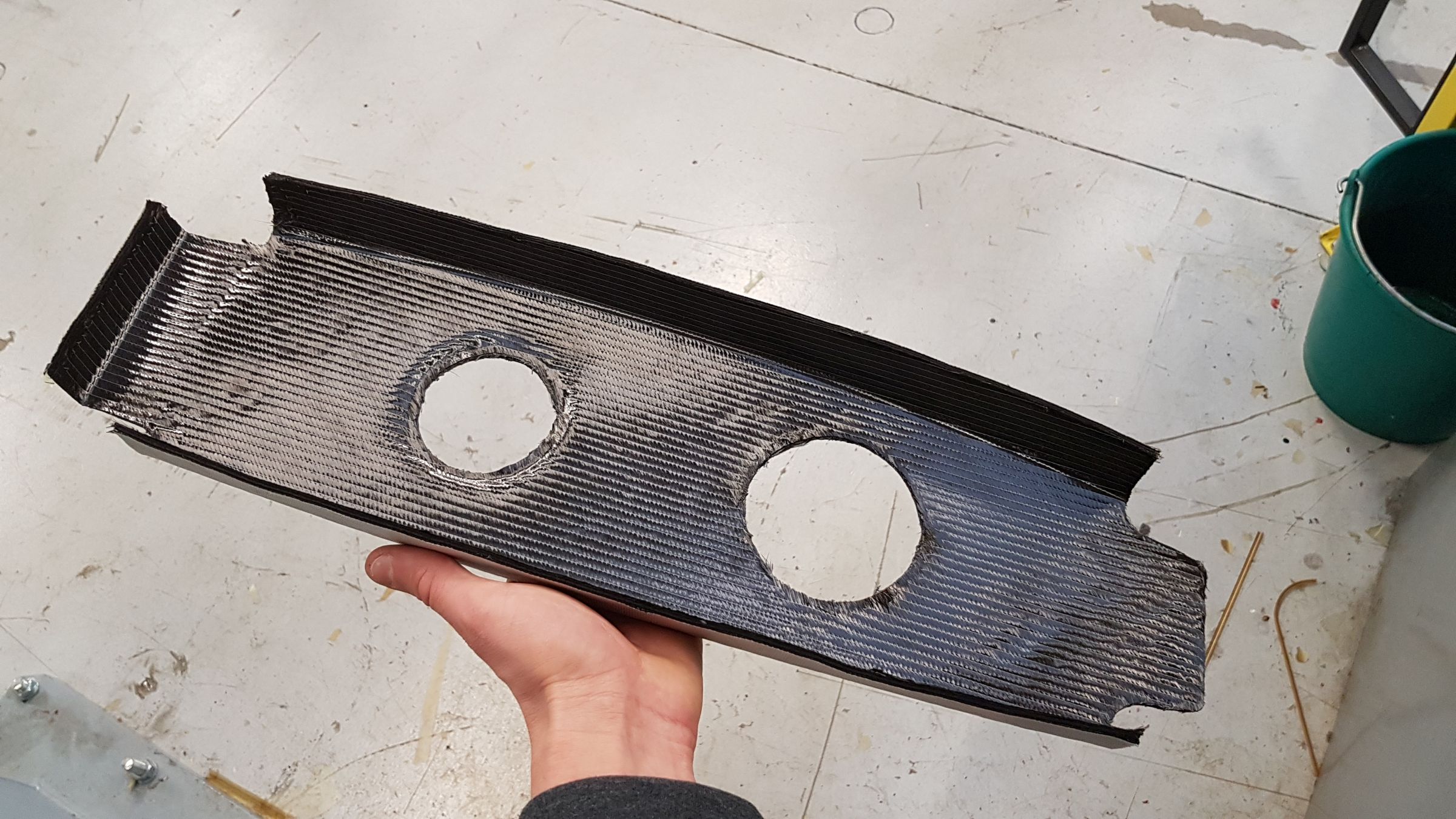
«Мы автоматизировали классическую ручную укладку слоев с помощью роботизированного захвата и складывания», - говорит Шевалле. «Робот захватывает слои из автоматического резака и передает их нагретому инструменту для изготовления преформ, который находится на столе для уплотнения [шаги 1 и 6]». Применяются отслаивающий слой (синяя пленка на шаге 6), сапун (белый материал на шаге 6) и шарнирная многоразовая вакуумная мембрана (светло-голубая слева на шагах 2 и 6), затем вакуум и нагревание для предварительной формы и удаления воздуха из текстильный стек (горячее формование, HDF) при плавлении тонких термопластичных вуалей для создания спрессованной преформы.
«Сколько слоев вы можете уплотнить за один раз, зависит от материалов и формы детали», - объясняет Шевалле. «Для деталей с низкой кривизной, таких как крылья, можно уплотнять каждые 50 слоев. Ребро OPTICOMS, однако, имеет углы 90 градусов, а тестовая двутавровая балка имеет Т-образную форму, поэтому вы должны быть осторожны, чтобы не образовывать складки на слоях во время предварительной формовки ». Он добавляет, что такие сложные формы могут потребовать уплотнения через каждые 5-8 слоев, но все же могут быть частью крупномасштабного промышленного процесса:штабелирование слоев, 2-минутный HDF уплотнение, повторное открытие и снова штабелирование с последующими повторными циклами уплотнения с окончательным охлаждением преформы на инструменте перед перемещением в пресс-форму RTM.
«Наша автоматизированная ячейка может размещать слой за 15 секунд», - отмечает Шевалле. «Укладка нервюры OPTICOMS, состоящая из менее чем 20 слоев, была завершена за 20 минут». Продолжительность простоя стрингера двутавровой балки - 45 минут из-за сложной формы и стека ламината, включая колебания толщины от 1,2 до 6 миллиметров. «Это по-прежнему намного быстрее, чем ручные процессы, и снижает риск ошибок, повышает повторяемость и качество при одновременном снижении затрат», - добавляет он.
Шаг 7
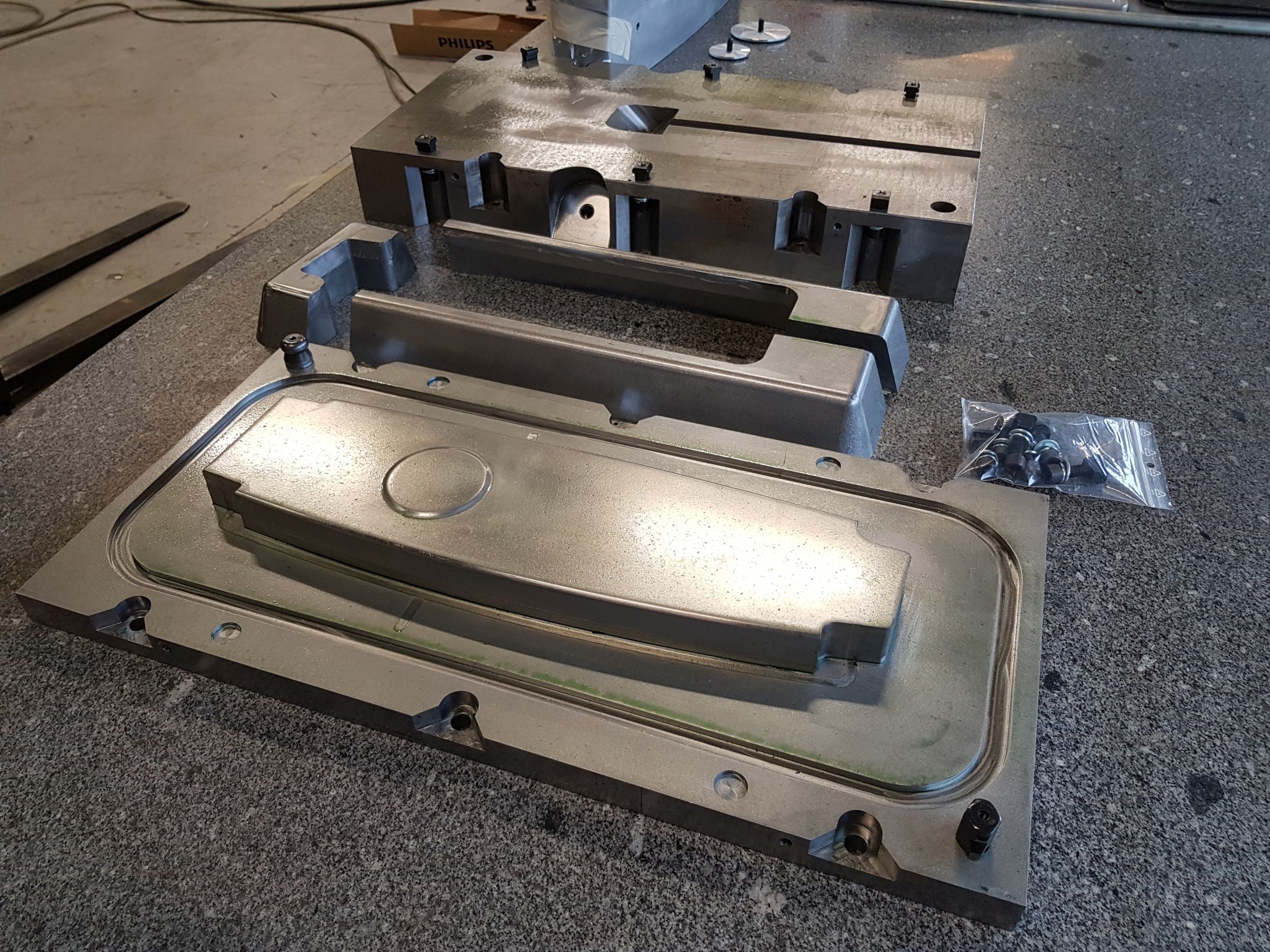
Инструмент RTM для ребра OPTICOMS состоит из нескольких частей.
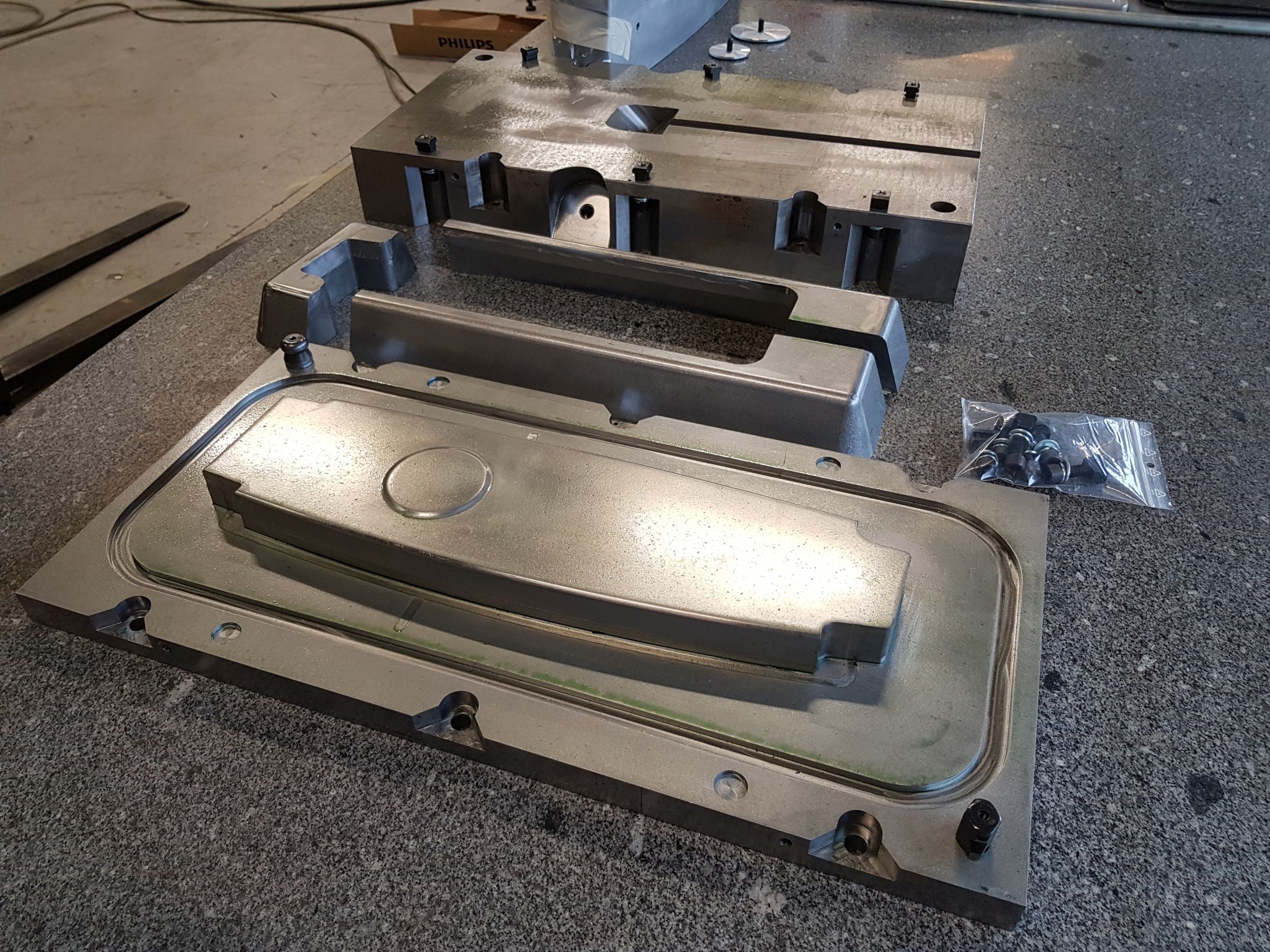
Шаг 8
Заготовка ребра вставляется в инструмент RTM.
Шаг 9
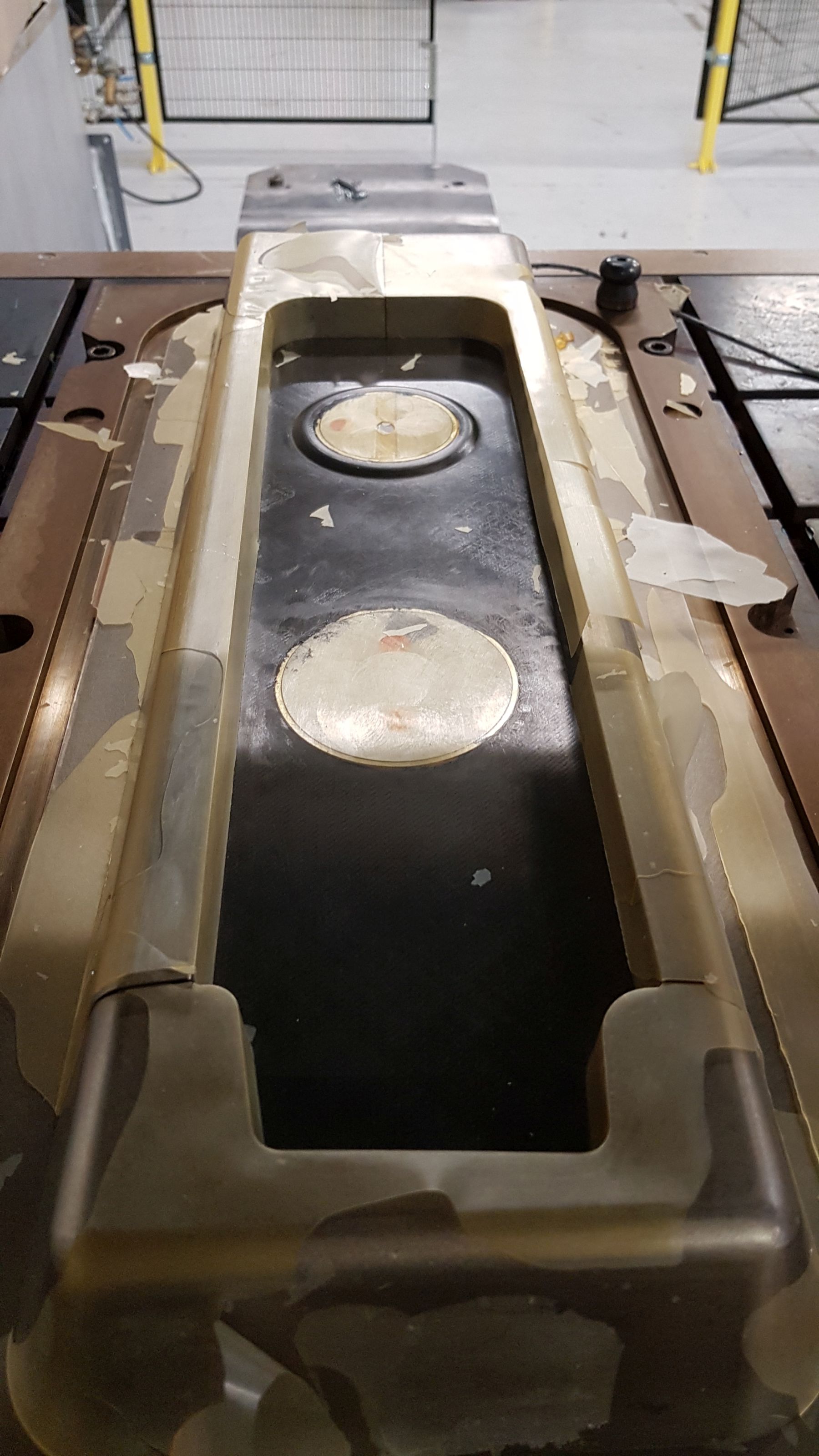
Применяется вакуум, впрыскивается смола, которая проникает в преформу, после чего следует 90-минутное отверждение. Здесь был открыт пресс, чтобы показать вылеченную часть.
Шаг 10
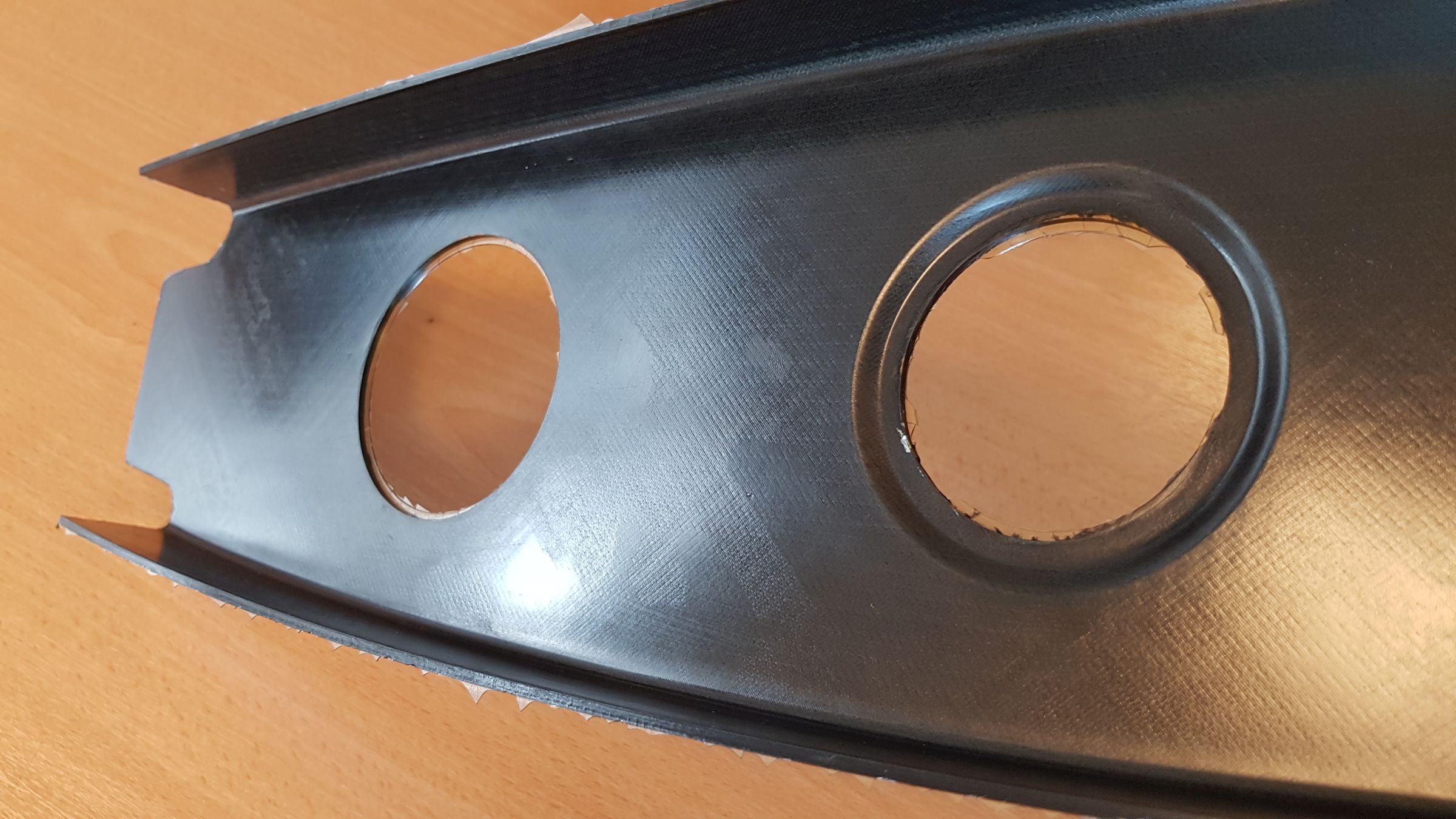
После завершения извлечения из формы всплеск смолы будет удален для полного цикла обработки продолжительностью 4 часа.
Интеллектуальное управление
Еще одна ключевая особенность автоматизированной камеры предварительного формования Techni-Modul Engineering - это интегрированная система управления. Его основу, называемую SMART CONTROL, составляют система камеры и многофункциональное программное обеспечение, которое сравнивает изображения, сделанные во время обработки, с базой данных CAD детали, что позволяет распознавать форму преформы, управлять ориентацией волокон, позиционировать слои и обнаруживать дефекты и посторонние предметы (FOD). ). Обратная связь SMART CONTROL указывает роботу, как подбирать и размещать слои в правильной последовательности и в нужное время, а также предупреждает оператора ячейки при обнаружении ошибок. «Систему можно настроить так, чтобы оператор вручную удалял слой и перезапускал систему, чтобы заменить его, - объясняет Шевалле, - или мы можем работать с заказчиком над созданием автоматизированного решения для удаления дефектных слоев и исправления ошибок».
Те же оптические изображения, которые используются для определения краев и контуров слоев, также используются для управления ориентацией волокон. Шевалле допускает, что если деталь очень большая (например, 2 метра в длину по сравнению с 200 на 200 миллиметров), «вам может понадобиться камера, делающая снимки [из] более высокого вертикального положения, чтобы обнаружить края слоев, а затем переместиться ближе к деталь для проверки ориентации волокон. Вы откалибруете эту последовательность для каждого типа детали. Для обнаружения морщин и FOD существует база данных с различными дефектами, и вы можете добавлять ее, чтобы алгоритм глубокого обучения со временем улучшался. Идея состоит в том, чтобы иметь адаптивную систему ».
Продолжительность цикла и будущее производство
Заготовки для нервюры OPTICOMS были изготовлены с использованием HiMax, а для стрингера двутавровой балки использовалась HiTape. В качестве системы смолы для обоих использовалась однокомпонентная (1K) жидкая эпоксидная смола Hexcel HexFlow RTM6, цикл отверждения которой составляет от 90 до 120 минут при 180 ° C. Это отверждение является самым продолжительным этапом в цикле обработки ребра OPTICOMS и испытательного стрингера двутавровой балки, как показано в Таблице 1.
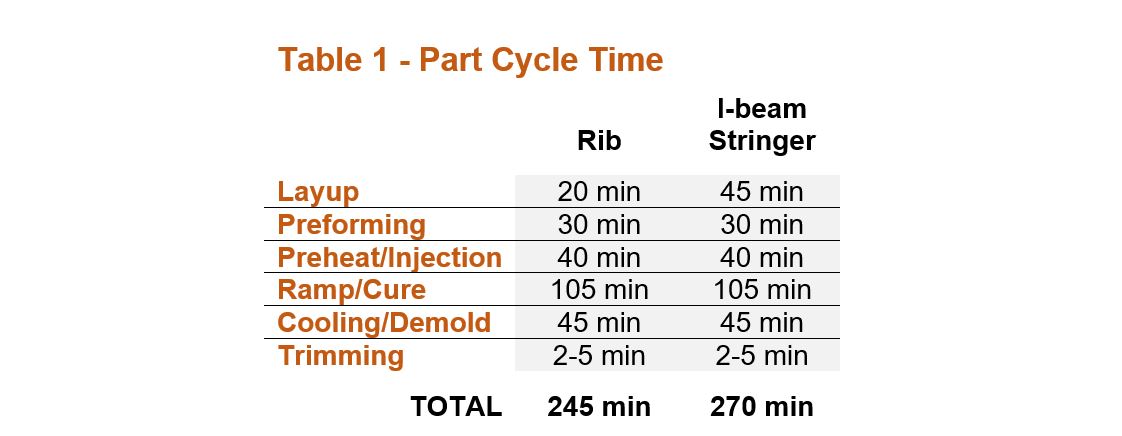
Источник | Техни-Модуль Инжиниринг
На сегодняшний день это единственная эпоксидная смола, подходящая для RTM аэрокосмических конструкций. Однако растет интерес к квалификационным двухкомпонентным системам, которые смешиваются в головке впрыска, что обеспечивает повышенную гибкость цикла отверждения и устраняет необходимость в транспортировке и хранении в холодильнике, необходимых для предотвращения преждевременной реакции предварительно смешанного RTM6.
Airbus Helicopters (Донаууорт, Германия) работал с Alpex Technologies (Милс, Австрия) в проекте SPARTA, чтобы продемонстрировать процесс HP-RTM с использованием двухкомпонентной версии HexFlow RTM6 для достижения 30-минутного отверждения двери A350 при 180 ° C. рама, которая представляет собой первичную конструкцию сложной формы, высотой 2 метра, шириной 200-250 миллиметров и толщиной 8-10 миллиметров (см. «HP-RTM для серийного производства экономичных авиационных конструкций из углепластика»). Airbus также продемонстрировал ребро из углепластика размером 1,5 на 0,5 метра, изготовленное с использованием HP-RTM дочерней компанией Центра композитных технологий (CTC, Штаде, Германия), достигнув 20-минутных циклов формования деталей с объемом волокна 60% и менее 2 % пустот. В прошлом году CTC работала с рядом поставщиков, чтобы перевести детали препрега ручной укладки на HP-RTM для A320. Однако системы 2K на основе смол должны быть аттестованы для производства аэроструктур, и CTC обеспокоена возможностью постоянно обеспечивать качество смеси систем на основе 2K на месте. Alpex использует датчики in-mold от Netzsch (Зельб, Германия) и Kistler (Винтертур, Швейцария), чтобы помочь в достижении этого, а также разрабатываются другие решения (см. «Двухкомпонентная эпоксидная смола для увеличения производства композитных аэроструктур»).>
Даже без систем 2K возможны более высокие объемы производства. Дверные коробки в проекте SPARTA были сняты после первоначального 30-минутного отверждения при 180 ° C и подвергнуты последующему отверждению вне пресса в вакууме для снятия термического напряжения и обеспечения механических свойств. По словам руководителя отдела исследований и разработок Alpex Бернхарда Риттеншобера, для этого требуются дополнительные наборы инструментов, но только один блок пресса и впрыска. Он объясняет, что дополнительные затраты на инструмент компенсируются более низкой стоимостью процесса и пресса и могут быть быстро окупаемы даже при небольшом объеме 500–1000 деталей в год.
«Основным достижением этих демонстраторов является способность изготавливать первичные аэроструктуры с коротким впрыском смолы по сравнению с обычными аэрокосмическими процессами RTM, где было сложно и долго просачивать смолу в такие большие детали с армированием углеродным волокном UD», - говорит Паньяк. . «Мы только находимся в начале того, чего мы можем достичь с помощью этого типа интеллектуального автоматизированного предварительного формования и обработки C-RTM», - добавляет Шевалле. «Он может обеспечить более экономичное и устойчивое производство обшивки с элементами жесткости, предусмотренного для будущих самолетов».
Смола
- Материалы для 3D-печати для космических путешествий?
- Три способа использования композитов в авиакосмической отрасли в будущем
- Henkel предлагает платформу материалов для аддитивного производства
- Материалы:технология производства легких сот на K 2019
- Материалы:огнестойкий высокотемпературный полиамид для 3D-печати
- Подготовка к автономному будущему
- Trelleborg объявляет о новом дистрибьюторе инструментальных материалов
- Arkema Inc. строит завод по производству PEKK в США
- 10 самых прочных материалов для 3D-печати
- Материалы для компонентов Invar 36