Индустриализация термопластичной эпоксидной смолы
Cecence (Солсбери, Великобритания) была основана в 2014 году тремя основателями с многолетним опытом работы в области композитных материалов. Директор Майк Оранж имеет долгую историю в производстве армированного углеродным волокном полимера (CFRP) такелажа и мачт для яхт. Глава отдела инноваций Хамфри Буньян ранее возглавлял отдел инноваций Future Fibers (Валенсия, Испания). «Они [Future Fibers] изготавливали цельнокомпозитный такелаж для Кубка Америки и других гоночных судов, а также тросы из углепластика, чтобы удерживать колеса на автомобилях Формулы 1», - говорит Оранж (см. «Композитные материалы для яхтостроения:оснастка для успеха»). «Мы понимали преимущества легкого веса, но взаимодействовали с другими секторами, у которых не было нашего опыта, и они боролись с затратами, расширяя производство и соблюдая правила пожарной безопасности».
Таким образом, компания Cecence (произносится как «вижу смысл», как в обычном смысле слова с композитами из углеродного волокна) была основана, чтобы сосредоточиться на огнестойкости, промышленном производстве и устойчивости. Это привело к таким разработкам, как спинка сиденья из композита из углеродного волокна и биорезины для пассажирских самолетов, которая весила всего 7,5 кг, уменьшила толщину сиденья до менее 20 миллиметров и увеличила пассажирское пространство и комфорт, отвечающий всем требованиям пожарной безопасности, дыма и токсичности (FST).
«В предыдущем проекте Cecence разработала метод производства горячего прессования, который сократил время цикла с 2,5 часов до 7 минут для спинки сиденья эконом-класса с использованием фенольных смол мгновенного отверждения разработан с британским препаратом FTI (Somerset) », - говорит Оранж. Для этой последней описанной выше спинки сиденья, разработанной совместно с Design Q (Реддич, Великобритания), Cecence расширила свой портфель FST, используя препрег на основе смолы на основе полифурилового спирта (PFA), разработанный SHD Composites (Слифорд, Великобритания). PFA - это термореактивный полимер, полученный из биомассы, который действует как фенол с превосходной обработкой поверхности и устойчивостью (см. «Устойчивость к возгоранию без веса»). «Мы работали с SHD Composites и продвигали их химию для более быстрого отверждения», - говорит Оранж. «Это то, что мы делаем:берем материалы, процессы и конструкции и дорабатываем их, чтобы композитные продукты можно было производить в больших масштабах таким образом, чтобы это было коммерчески жизнеспособным, но при этом устойчивым».
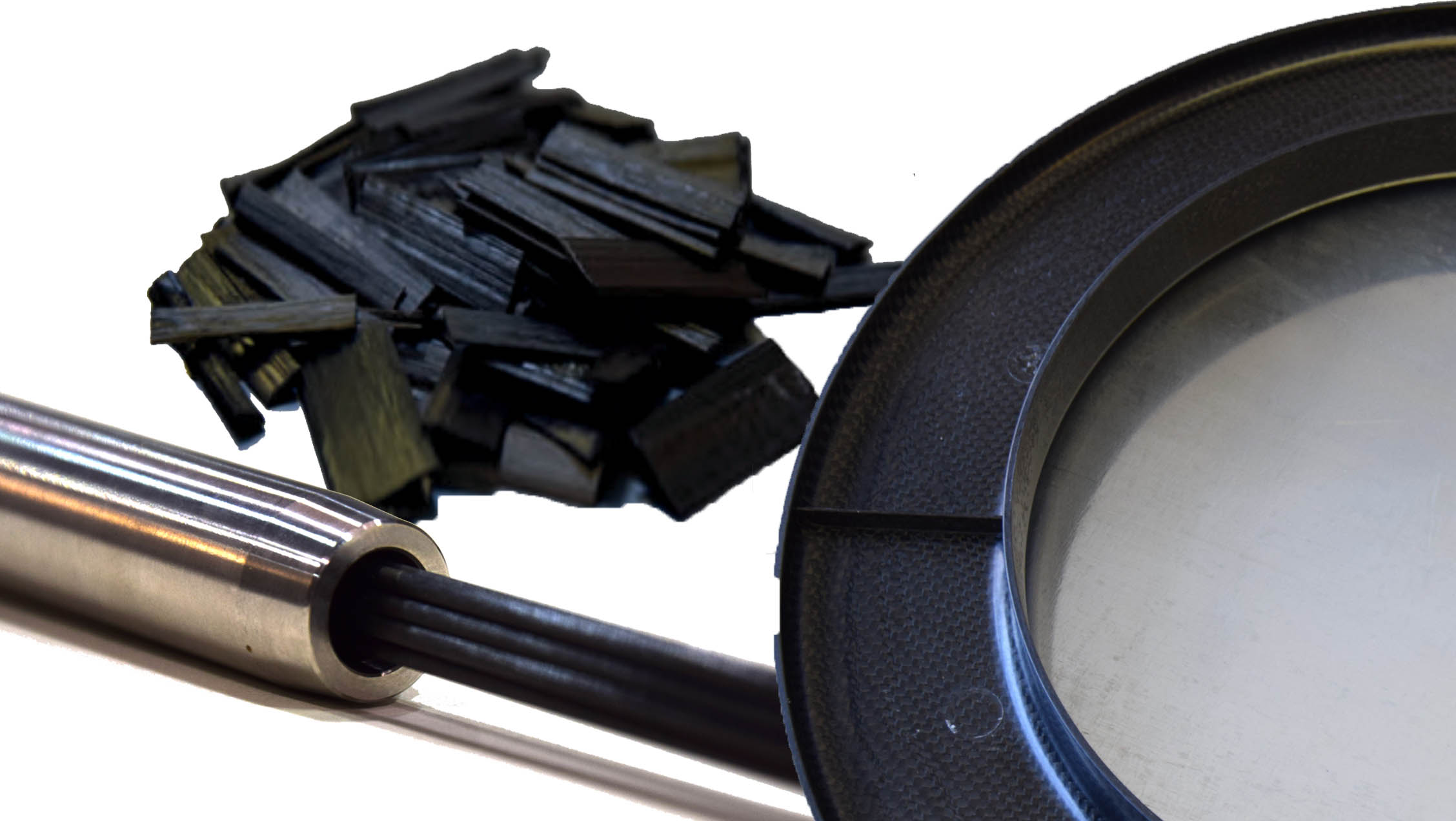
Скорость производства и устойчивость были ключевыми факторами, когда несколько лет назад Cecence столкнулась с системой термопластической эпоксидной смолы. «Этот термопласт с эпоксидными компонентами на конце полимерных цепей использовался тканевой компанией, которая не реализовала свой потенциал в композитах», - объясняет Оранж.
«Мы сразу поняли преимущества термопласта с низкой вязкостью, который может очень хорошо пропитать волокна, обеспечивая при этом термоформованную эпоксидную смолу», - говорит Хамфри Буньян. Компания Cecence разработала препрег на основе этой технологии термопластической эпоксидной смолы, а затем семейство продуктов под торговой маркой K_Series:спиральный K_Rod, полу-прег K_Plate толщиной от 0,25 до 1,98 мм и формовочный компаунд K_Chip (рис.1). «Мы смогли отформовать компоненты менее чем за три минуты, - говорит Оранж, - и продемонстрировали вариант FR, который соответствует требованиям FST для салонов самолетов». Cecence также использовала этот материал для разработки системы композитного оборудования воздушных линий (COHLE) для линий электропередач, которая сокращает количество опорных пилонов / опор вдвое, а общие затраты на установку и эксплуатацию на 100 000 фунтов стерлингов (124 200 долларов США) на километр.
Термоформируемая эпоксидная смола
«В случае типичных термопластов получается матричный полимер с высокой вязкостью, который трудно вдавить в волокна», - объясняет Буньян. «Таким образом, трудно добиться хорошей пропитки жгутов или тканей. Но у термоформованной эпоксидной смолы K_Series очень низкая вязкость - 80 сантипуаз при 100 ° C. Это позволяет нам препрегировать армирующие элементы из стекла, углерода и натурального волокна с превосходным распределением смолы и волокна и, как правило, с содержанием волокна 60% по весу. Мы также можем использовать волокна с проклейкой для эпоксидной смолы, которая обычно несовместима с термопластами ». Тем не менее, эта система является настоящим термопластом, что позволяет производить реформирование готовых деталей при температуре 180-200 ° C без химической реакции или экзотермии.
«Как и эпоксидная смола, она хорошо прилипает к волокну, поэтому волокна не отделяются от матрицы, даже если вы используете более высокое давление во время формования», - отмечает Оранж. Это относится к проблеме, с которой он столкнулся с полиамидом (PA), армированным короткими волокнами, и полипропиленовыми компаундами. «Мы работали со слоем полиамида, расплавленным на ткани горячим прессованием, чтобы получить плоский лист. Матрица не прилипала к волокнам, а только окружала их. Таким образом, когда его вдавливают в деталь, вы получаете выход волокна ».
K_Plate, который обрабатывается при 150–220 ° C, предлагает рабочую температуру 100 ° C для кратковременного воздействия и продолжительного использования при 90 ° C. Измельченный однонаправленный жгут компаундов К_Чип прессуют при 240 ° С. «Т g [температура стеклования] и начало тепловой деформации для K_Series ниже, чем у обычных эпоксидных смол, но это также то, что делает реформирование и переработку возможными », - говорит Оранж. Процессы K_Series также быстрые. «Cecence работал с RocTool [Le Bourget du Lac, Франция] на выставке JEC 2016, чтобы продемонстрировать самый быстро формирующийся термопласт, который они когда-либо видели», - говорит он, отмечая время цикла в 2 минуты 40 секунд для автомобильного капота. «Время выдержки составляло всего 25 секунд до охлаждения при давлении 8-9 бар над вакуумной мембраной. Они также остались довольны отделкой как матовых, так и глянцевых поверхностей [см. Начальное изображение], отметив, что наш материал обеспечивает лучшую отделку из всех протестированных ».
Кроме того, эпоксидные компоненты в продуктах K_Series позволяют легко окрашивать и склеивать композитные детали без специальных грунтовок и подготовки, необходимых для традиционных термопластов. «Вы можете вторично склеить их, используя стандартные клеи», - добавляет Буньян. «Кроме того, благодаря термопласту вы получаете хорошие характеристики межслойного сдвига, и в целом они создают прочные, энергопоглощающие структуры».
Контактная сеть из углепластика для недорогих электрических железных дорог
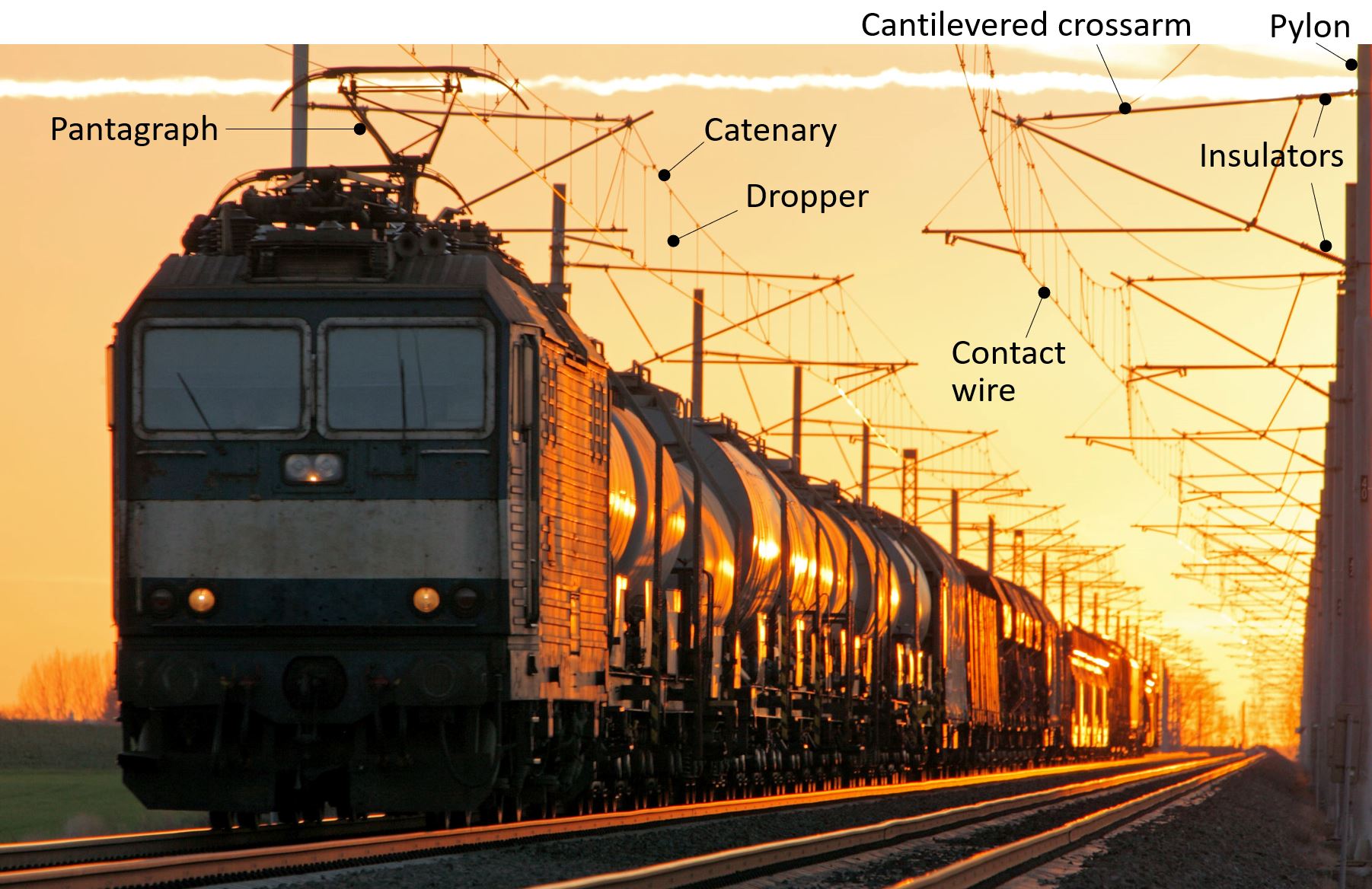
Двойная природа этой термопластичной эпоксидной смолы проиллюстрирована в системе оборудования воздушных линий (OHLE), разработанной Cecence с использованием цепной цепи из углепластика, изготовленной из K_Rod. Контактная сеть и токоведущий контактный провод - это два основных провода в OHLE электрической железной дороги (рис. 2). Электричество доставляется к локомотиву поезда через пантограф, который выходит из верхней части локомотива и прижимается к контактному проводу. «Контактная сеть действует как подвесной мост между пилонами (мачтами, опорами), которые расположены через каждые 25 метров вдоль путей», - поясняет Оранж. Медный контактный провод подвешивается к контактной сети с помощью вертикальных подвесных тросов или капельниц, подобно тому, как проезжая часть поддерживается кабелями в подвесном мосту.
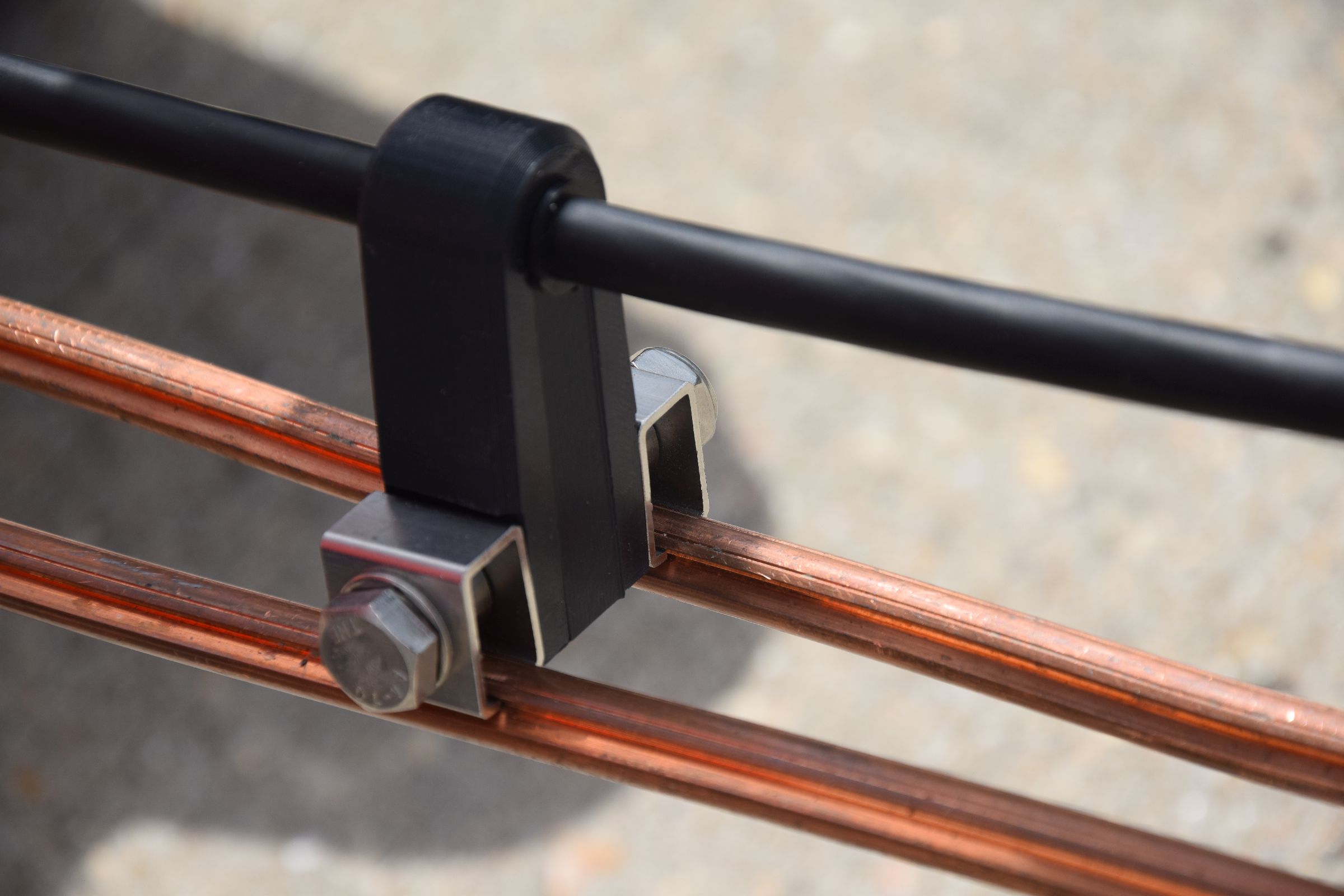
«При использовании натяжного троса K_Rod в качестве контактной сети он может располагаться только на 70 миллиметров над медным контактным проводом», - отмечает Оранжевый (рис. 3). «Вся система более компактна, и визуальное воздействие на окружающую среду значительно меньше». В современных системах OHLE используются стальные контактные кабели, длина которых изменяется при изменении температуры. «Летом они простираются на 400 миллиметров на километр», - отмечает он. Чтобы противодействовать провисанию строп, бетонные противовесы на шкивах устанавливаются в качестве системы автоматического натяжения, но это увеличивает общую стоимость.
«Вес стальной лески и ее профиль провисания также являются причиной того, что необходимо так много опор», - отмечает Оранжевый. «Летом наш кабель из углепластика меняет длину всего на 7 миллиметров на километр, потому что незначительное тепловое расширение углеродного волокна создает термостойкий композит. Кроме того, он на 80 процентов легче стального троса, не прогибается и позволяет размещать пилоны на расстоянии 50 метров друг от друга, что вдвое сокращает количество требуемых пилонов ». Это обеспечивает дополнительную экономию средств, поскольку для каждой опоры имеется консольная траверса, поддерживаемая подпоркой.
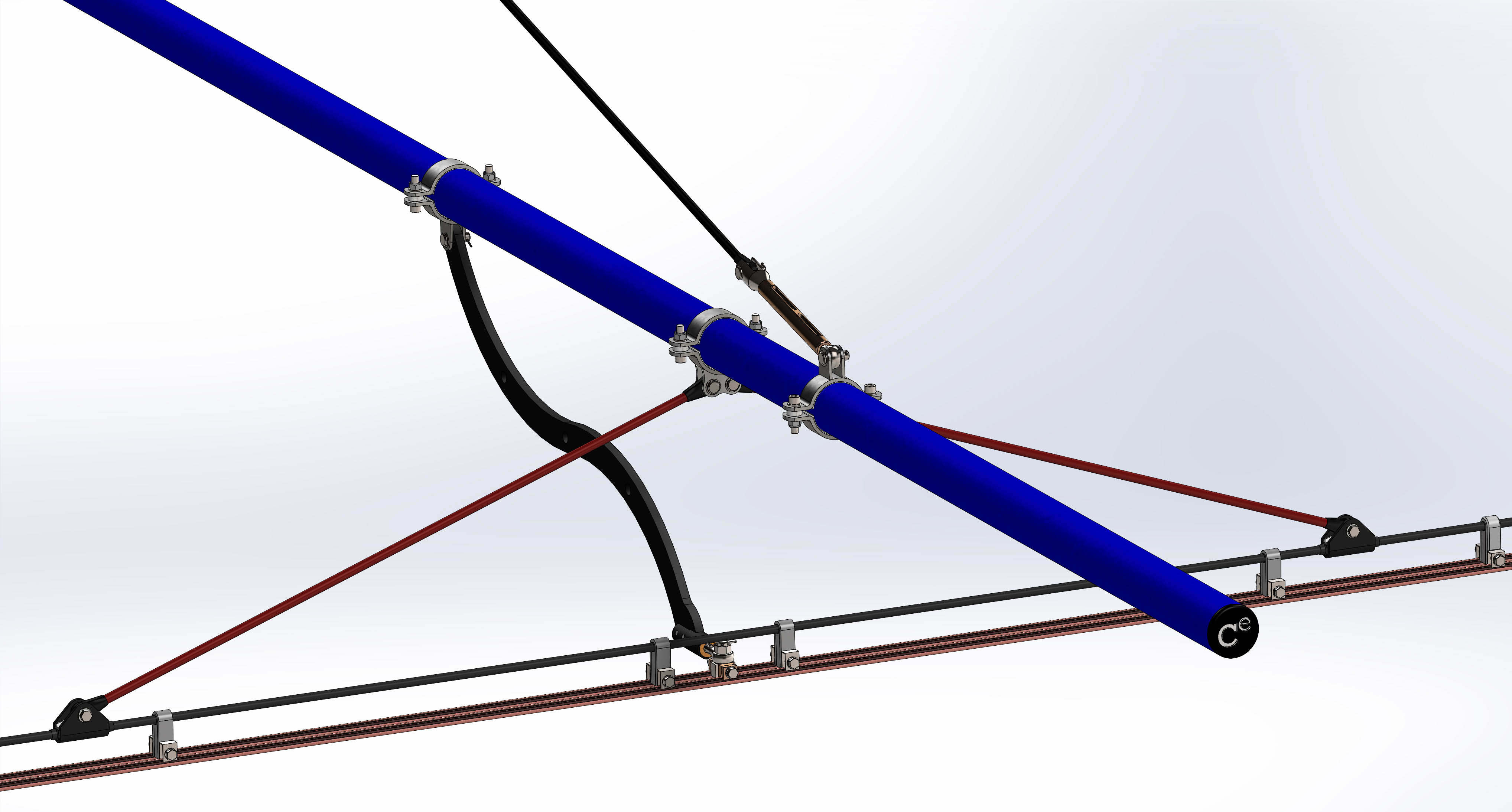
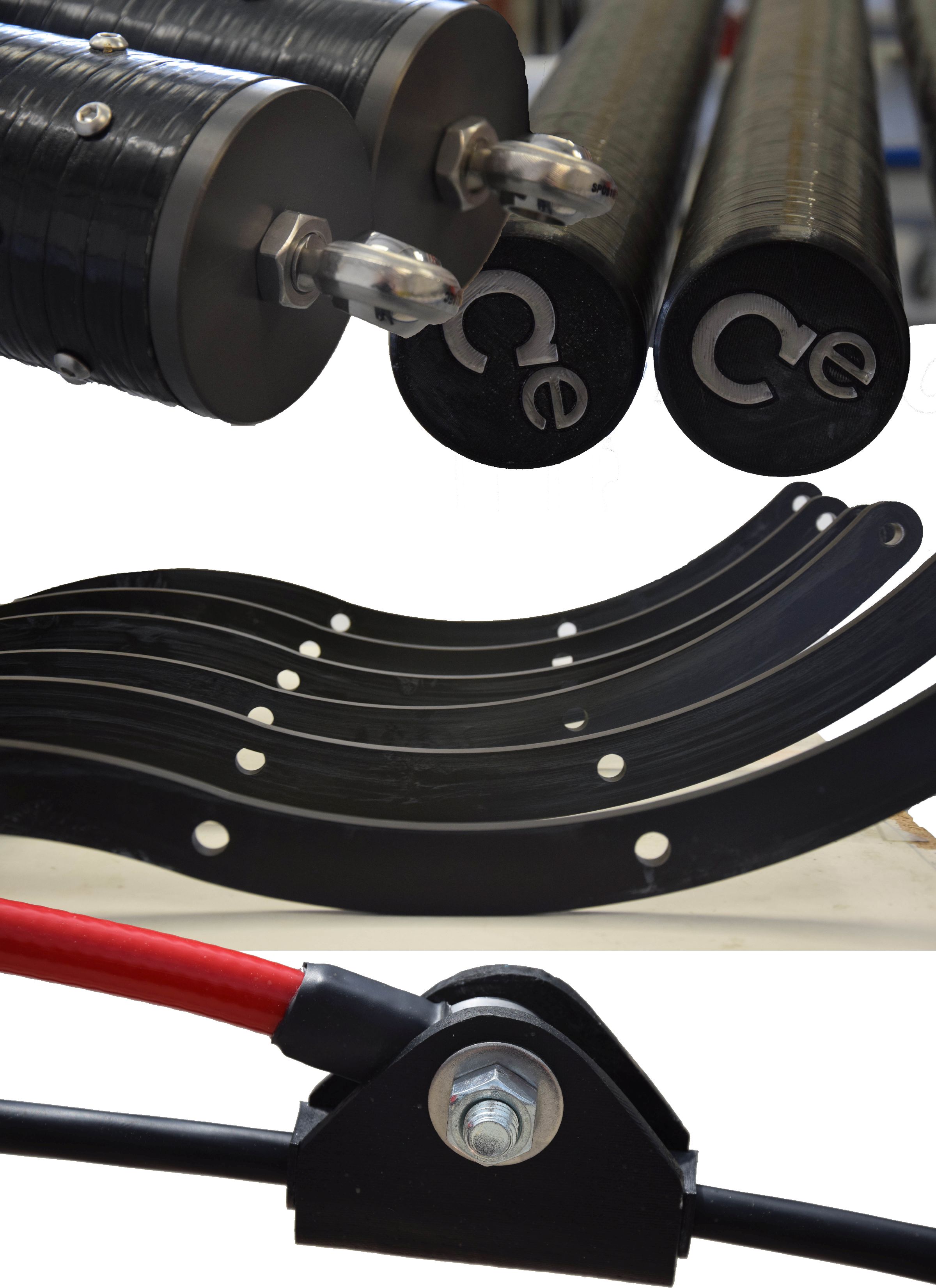
Кроме того, в обычных системах OHLE используются цельнометаллические компоненты, что требует добавления изоляторов для предотвращения нежелательной проводимости электрического тока. «Cecence COHLE не нужны все изоляторы, потому что в нем используются композитные опоры и траверсы из непроводящего стекловолокна (GF) с непроводящими композитными подпорками», - поясняет Оранж. «Мы также используем промежуточные капельницы из полимолочной кислоты (PLA), напечатанной на 3D-принтере. В отличие от металлической системы, опоры не требуют регулярной покраски, а коррозионно-стойкие композиты требуют меньшего обслуживания ».
«Термопластическая эпоксидная смола играет ключевую роль в цепной цепи углепластика», - продолжает он. «Cecence использует его как в сердцевине K_Rod из углеродного волокна, так и в композитной оболочке GF с оплеткой». В результате получается легкий, высокопрочный, изолированный кабель, который можно наматывать и хорошо склеивать при вклеивании в розетку, что решает обычно сложную проблему заделки кабелей из углеродного волокна. Благодаря удивительной передаче нагрузки от сердечника к розетке через оплетку, нам не нужна большая длина розетки, и эта система проста, поэтому ее удобно устанавливать в полевых условиях железнодорожными техниками ».
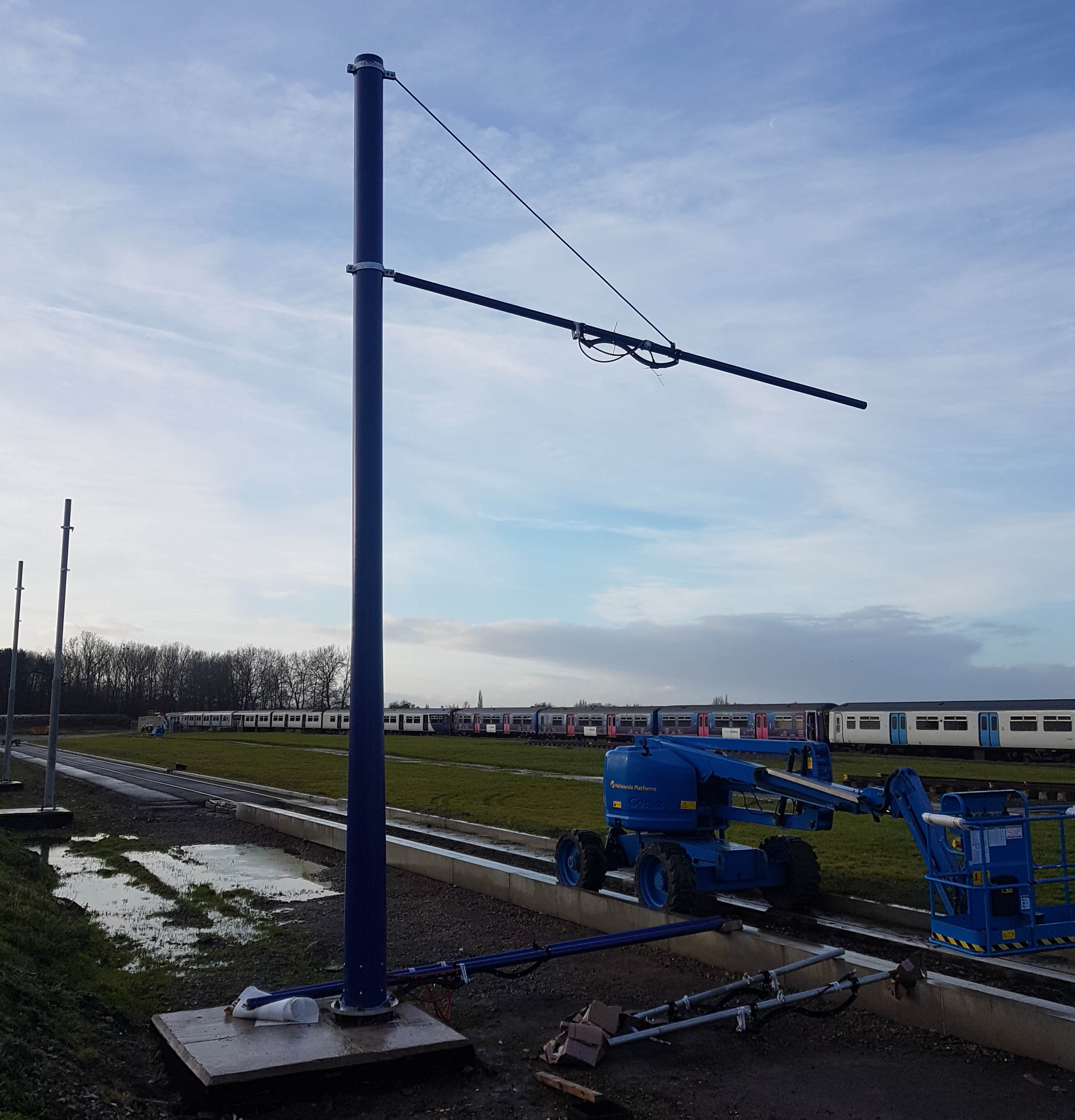
По словам Orange, даже несмотря на то, что кабель из углепластика стоит в три раза дороже стальной контактной сети, общая стоимость системы снижается с 512 000 фунтов стерлингов до 413 000 фунтов стерлингов за километр. Эти затраты, рассчитанные с помощью международной инженерной и инфраструктурной компании Atkins (Лондон, Великобритания), включают экономию на эксплуатации / техническом обслуживании в размере от 400 000 до 3,4 миллионов фунтов стерлингов на километр в течение всего срока службы системы.
«Cecence поставила прототипы компонентов в мае 2019 года, - сообщает Orange, - а наши партнеры по развитию планировали провести электрические линии к февралю 2020 года, но это было отложено из-за COVID-19. Вся система была представлена на выставке Advanced Engineering Show в 2019 году и получила награду Composites UK Innovation Award ».
Дальнейшие разработки и приложения K_Series
Помимо приложения OHLE, Cecence ищет другие возможности для применения своих продуктов K_Series. «Cecence также работала над проектами, в которых кабели K_Rod использовались в качестве анкеров для каменной скалы на строительном проекте в Швейцарии», - говорит Оранж. «Наши партнеры по проекту должны были просверлить в скале отверстия глубиной 80 метров, вставить кабели из углепластика и залить бетоном. Были получены поразительные результаты испытаний, но академический партнер никогда не связывался с промышленностью, чтобы разработать проект, выходящий за рамки лабораторных масштабов . Мы проводим и другие демонстрации, однако эта система устойчива к коррозии и обеспечивает хорошую передачу нагрузки. Его также можно использовать в качестве грунтовых анкеров для различных строительных систем, например, для зданий с защитой от ураганов ».
Видео на YouTube и на веб-сайте Cecence демонстрируют возможность термоформования продуктов K_Plate. «Также обсуждались возможности применения аэрокосмических профилей с изменяемой геометрией / морфингом с британской аэрокосмической компанией», - говорит Оранж. Cecence продемонстрировала рентабельный автомобильный материал, используя K_Chip, изготовленный из рубленых композитных жгутов, в качестве гибридного CF / GF / термопластичного эпоксидного материала, сохраняя соотношение углерода и стекла 2:1, подтвержденное испытаниями. . ”
Компания также разработала высокотемпературную серию K_Series с T g 250-300 ° C, который обрабатывается при 360-400 ° C. «Это было использовано для производителя автомобилей, который хотел, чтобы детали из углепластика выдержали процесс покраски E-Coat при 180 ° C», - говорит Оранж. «У нас также есть материал K-FR, который может соответствовать требованиям FST для вертикального горения самолета, тепловыделению и токсичности дыма, и мы ищем способы помочь с гашением вибрации для снижения шума в салоне самолета. Мы можем настроить термопласт и добавить слои эластомерного материала, чтобы добиться значительного снижения шума ».
Саманта Буньян, третий основатель Cecence и руководитель отдела по взаимодействию с отраслью, отмечает, что возможность вторичной переработки также является ключевой областью развития. Cecence является частью консорциума ReDisCoveR Composites, управляемого Национальным центром композитов (Бристоль, Великобритания). Он был основан в апреле 2019 года и реализует 24 проекта по четырем направлениям:переработка, разборка, круглые материалы и повторное использование. «В рамках этих проектов мы изучаем разборку компонентов и демонстрируем реальную возможность вторичной переработки термопластичных композитов», - говорит Буньян. «Промышленность, наконец, вынуждена доказать пригодность к вторичной переработке, заявленную на протяжении многих лет. Cecence видит преимущества возможности вторичной переработки термопластичных эпоксидных материалов K_Series, но также необходимо продемонстрировать процессы и экономическую целесообразность для этого ».
«Мы считаем, что в общественном транспорте гораздо больше возможностей для экологически чистых композитов, в том числе для салонов самолетов, сидений и рельсов», - говорит Оранж, добавляя, что Cecence является не только партнером в разработке, но и в производстве. «На сегодняшний день мы изготовили 2500 композитных спинок сидений для самолетов типа A320 и были на пути к производству самых легких и тонких спинок сидений в отрасли до вспышки COVID-19. Лом от композитных сидений можно повторно использовать в подлокотниках и подножках. Рециклат также можно использовать в других вспомогательных деталях, в настоящее время использующих первичный пластик. Все это может помочь снизить потребление ископаемого топлива и выбросы, а также облегчить электрификацию и повысить экологичность ».
В композитах, отмечает Саманта Буньян, «устойчивость состоит из трех частей:материалы, обработка (быстрая и низкоэнергетическая) и цепочка поставок. Мы разрушаем все это, работая с новаторами со всего мира, которых не видно, потому что большинство людей смотрят только на крупные компании. Миру нужны новые решения, которые работают на промышленность. Именно этим занимается Cecence ».
Смола
- Производство композитов:производство композитных материалов
- Covestro увеличивает инвестиции в термопластические композиты
- История эпоксидной смолы
- Термопластические композиты в Oribi Composites:CW Trending, эпизод 4
- Устранение проблем термоформования термопластичных композитов
- Развитие аддитивных композитов
- Термопластические композиты:структурный кронштейн бампера
- Mar-Ball, сетчатые композиты объединяются для расширения возможностей эпоксидной смолы
- Термопластические композиты:живописный вид
- Сварка термопластичных композитов