Простые в использовании комплекты позволяют ремонтировать композитные конструкции в полевых условиях
Модульные разводные мосты являются ключевым активом в военных тактических операциях и логистике, а также для восстановления транспортной инфраструктуры во время стихийных бедствий. Композитная конструкция исследуется для уменьшения веса таких мостов, что, в свою очередь, снижает нагрузку на транспортные средства и пуско-подъемные механизмы. Композитные материалы также обладают потенциалом увеличения несущей способности и продления срока службы по сравнению с металлическими мостами.
Усовершенствованный модульный композитный мост (AMCB) является одним из примеров, спроектированных и изготовленных с использованием эпоксидных ламинатов, армированных углеродным волокном (рис. 1), компанией Seemann Composites LLC (Галфпорт, штат Миссисипи, США) и Materials Sciences LLC (Хоршам, Пенсильвания, США). ). Однако возможность ремонта таких конструкций в полевых условиях была проблемой, препятствовавшей внедрению композитов.
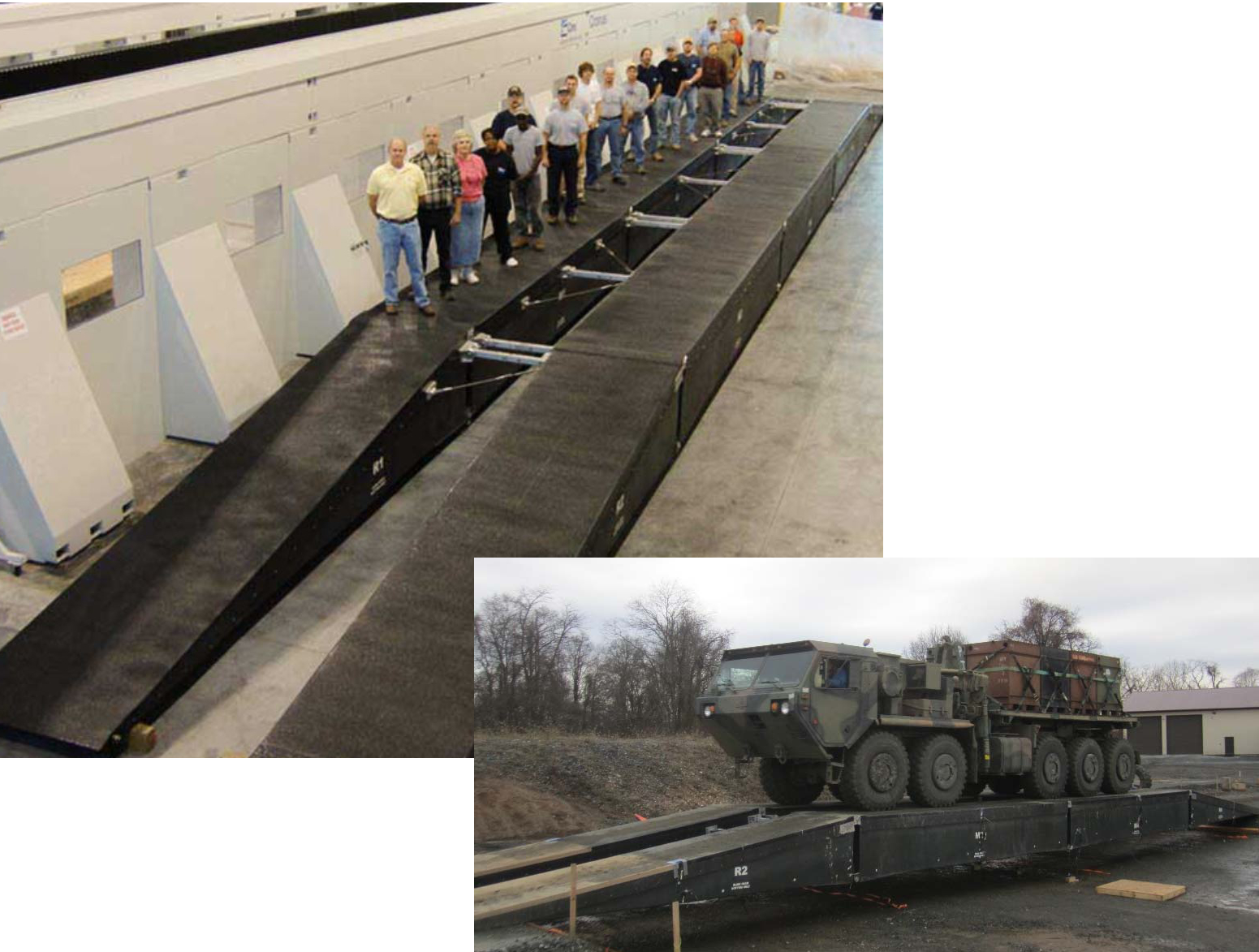
В 2016 году Custom Technologies LLC (Миллерсвилл, штат Мэриленд, США) получила грант фазы I для исследований в области инноваций малого бизнеса (SBIR), финансируемый армией США, на разработку метода ремонта, который может успешно применяться солдатами в полевых условиях. На основе этого метода в 2018 году был присужден грант Фазы II SBIR для демонстрации новых материалов и оборудования с батарейным питанием, которые могут восстановить 90% или более первоначальной прочности конструкции, даже если заплаточный ремонт выполняется новичком без предварительной подготовки. . Осуществимость технологии была подтверждена путем выполнения ряда аналитических задач, выбора материалов, изготовления испытательных образцов и механических испытаний, а также мелкого и полномасштабного ремонта.
От потрескавшейся палубы корабля до палуб моста
Главным исследователем обоих этапов SBIR был Майкл Берген, основатель и президент Custom Technologies LLC. Берген ушел в отставку из Naval Surface Warfare Center (NSWC) Carderock, проработав 27 лет в отделе конструкций и материалов, где он руководил разработкой и применением композитных технологий для флота ВМС США. Доктор Роджер Крейн присоединился к Custom Technologies в 2015 году после ухода из ВМС США в 2011 году, проработав 32 года. Его опыт работы с композитами включает технические публикации и патенты по таким темам, как новые композитные материалы, изготовление прототипов, методы соединения, многофункциональные композиты, мониторинг состояния конструкций и ремонт композитов.
Эти два эксперта уже разработали уникальный процесс с использованием композитных материалов для устранения трещин в 5456 алюминиевых надстройках ракетного крейсера класса CG-47 USS Ticonderoga. «Этот процесс был разработан, чтобы уменьшить рост трещин и служить доступной альтернативой замене плиты настила за 2–4 миллиона долларов», - говорит Берген. «Таким образом, мы продемонстрировали, что умеем делать ремонт вне лаборатории и в реальных условиях эксплуатации. Но проблема заключалась в том, что нынешние методы обращения с военными активами не очень успешны. Возможны следующие варианты:ремонт приклеенного дублера [по сути, приклеивание пластины поверх поврежденного участка] или снятие актива с обслуживания для ремонта на уровне депо (уровень D). Так много активов находится в стороне, потому что требуется ремонт на уровне D ».
Что необходимо, - продолжает он, - это метод, который может быть реализован солдатом, не имеющим опыта работы с композитными материалами, с использованием только комплекта и руководства по ремонту. Наша цель состояла в том, чтобы упростить процесс:прочитать руководство, оценить повреждения и выполнить ремонт. Мы не хотели смешивать жидкие смолы, потому что это требует точного измерения для обеспечения полного отверждения. Нам также нужна была система без отходов HAZMAT, которую нужно было обрабатывать после завершения ремонта. И его нужно было упаковать в виде комплектов, которые можно было бы развернуть в уже существующих сетях ».
Новые склеенные пластыри
Одно из решений, которое Custom Technologies успешно продемонстрировала, - это портативный комплект, который позволяет накладывать композитную заплату, адаптированную к размеру повреждения - до максимум 12 квадратных дюймов - с использованием упрочненного эпоксидного клея. Демонстрации были выполнены на композитных материалах, представляющих колоду AMCB толщиной 3 дюйма, которая имеет сердцевину из бальзы толщиной 3 дюйма (плотность 15 фунтов на кубический фут) с лицевой кожей, состоящей из двух слоев компании Vectorply Corp. (Феникс-Сити, штат Алабама, США). США) Карбоновая ткань C-LT 1100 с двухосным швом 0 ° / 90 °, один слой углеродного волокна C-TLX 1900 с трехосным углом 0 ° / + 45 ° / -45 ° и еще два слоя C-LT 1100, всего пять слоев. «Мы решили, что в наборе будут использоваться готовые заплатки в квазиизотропном наборе подобных мультиаксиальных слоев, чтобы ориентация ткани не была проблемой», - говорит Крейн.
Следующим вопросом была матрица из смолы для ремонта ламината. Чтобы избежать смешивания жидких смол, в пластыре должны использоваться препреги. «Однако проблема заключается в хранении», - объясняет Берген. Чтобы разработать пластырь с возможностью хранения, Custom Technologies совместно с Sunrez Corp. (Эль-Кахон, Калифорния, США) разработали препрег из стекловолокна / сложного винилового эфира, который отверждается за шесть минут с использованием ультрафиолетового (УФ) света. Он также работал с Gougeon Brothers (Бэй-Сити, штат Мичиган, США), которые предложили использовать новую гибкую пленку из эпоксидной смолы.
Ранние исследования уже показали, что эпоксидная смола является наиболее подходящей смолой для препрега из углеродного волокна - виниловый эфир, отверждаемый УФ-излучением, отлично работает с полупрозрачными стекловолокнами, но не отверждается под светонепроницаемыми углеродными волокнами. Основанный на новой пленке Gougeon Brothers, конечный эпоксидный препрег продемонстрировал одночасовое отверждение при 210 ° F / 99 ° C с длительным сроком хранения при комнатной температуре - хранение при низких температурах не требуется. Смола также будет отверждаться при более высоких температурах, говорит Берген, например, при 350 ° F / 177 ° C, если более высокая температура стеклования (T g ) требуется. Оба препрега поставляются в портативном ремонтном комплекте в виде готовых накладок препрегов, запечатанных в конверты из пластиковой пленки.
Поскольку ремонтные комплекты могут находиться на хранении в течение длительного времени, Custom Technologies потребовалось провести исследование срока годности. «Мы купили четыре жестких пластиковых ящика - типичных для того, что военные используют для транспортировки оборудования - и поместили образцы эпоксидного клея и препрега на основе сложного винилового эфира», - говорит Берген. Затем ящики были размещены в четырех разных местах для тестирования:на крыше предприятия Gougeon Brothers в Мичигане, на крыше аэропорта в Мэриленде, на открытом воздухе на объекте в Юкка-Вэлли (пустыня Калифорния) и в лаборатории испытаний коррозии на открытом воздухе. в южной Флориде. Во всех случаях были регистраторы данных, отмечает Берген, «и каждые три месяца мы собирали данные и образцы материалов для оценки. Максимальная температура 140 ° F была зафиксирована в боксах во Флориде и Калифорнии, что является настоящей проблемой для большинства ремонтных смол ». Кроме того, компания Gougeon Brothers провела собственные испытания новой чистой эпоксидной смолы. «Образцы, выдержанные в течение нескольких месяцев в печи при 120 ° F, начали полимеризоваться», - говорит Берген. «Однако для соответствующих образцов, выдержанных при температуре 110 ° F, химический состав смолы улучшился лишь незначительно».
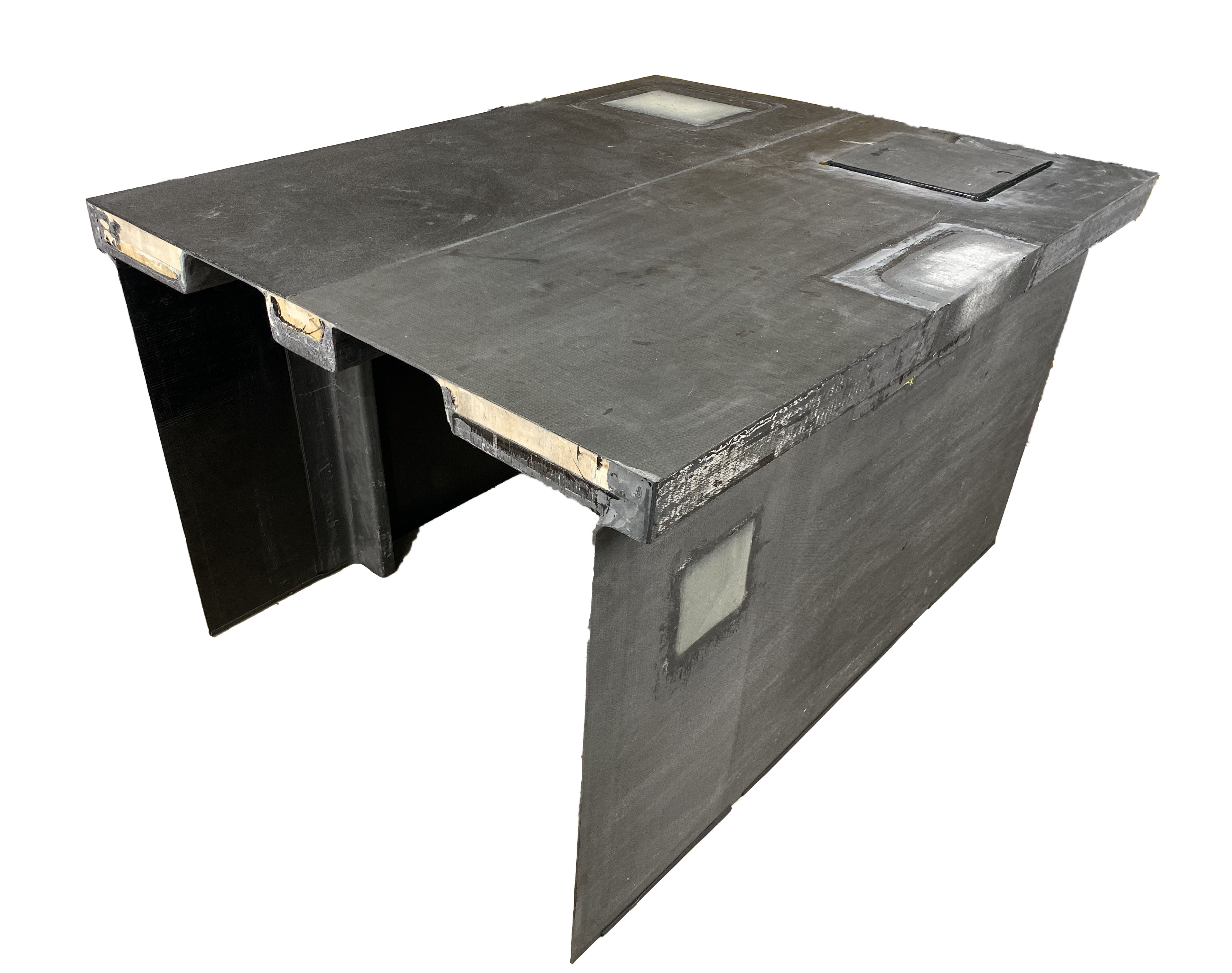
Ремонтное тестирование
Чтобы продемонстрировать технологию ремонта, необходимо было изготовить типичные ламинаты, повредить их и затем отремонтировать. «На этапе I проекта мы сначала работали с мелкомасштабными балками размером 4 x 48 дюймов и испытаниями на четырехточечный изгиб, чтобы оценить жизнеспособность нашего процесса ремонта», - говорит Крейн. «Затем мы перешли на панели 12 x 48 дюймов в проекте Фазы II, приложив нагрузку для создания двухосного напряженного состояния до разрушения, а затем оценили эффективность ремонта. В рамках проекта Фазы II мы также завершили ремонт модели AMCB, которую мы построили ».
По словам Бергена, испытательные панели, использованные для демонстрации ремонтных характеристик, были изготовлены с использованием той же родословной ламината и сердечника, что и AMCB, построенного Seemann Composites, «но мы уменьшили толщину лицевой панели с 0,375 дюйма до 0,175 дюйма на основе параллельных осей. теорема. Этот подход, наряду с дополнительными элементами теории балок и классической теории ламината [CLT], использовался, чтобы связать момент инерции и эффективную жесткость полномасштабного AMCB с более гибкими и экономичными демонстрационными статьями меньшего размера. Затем мы использовали модели анализа методом конечных элементов [FEA], разработанные XCraft Inc. (Бостон, Массачусетс, США), для уточнения конструкции ремонта конструкций ». Ткани из углеродного волокна для тестовых панелей и модели AMCB были закуплены у Vectorply, а сердцевина из бальзы была поставлена Core Composites (Бристоль, Род-Айленд, США).
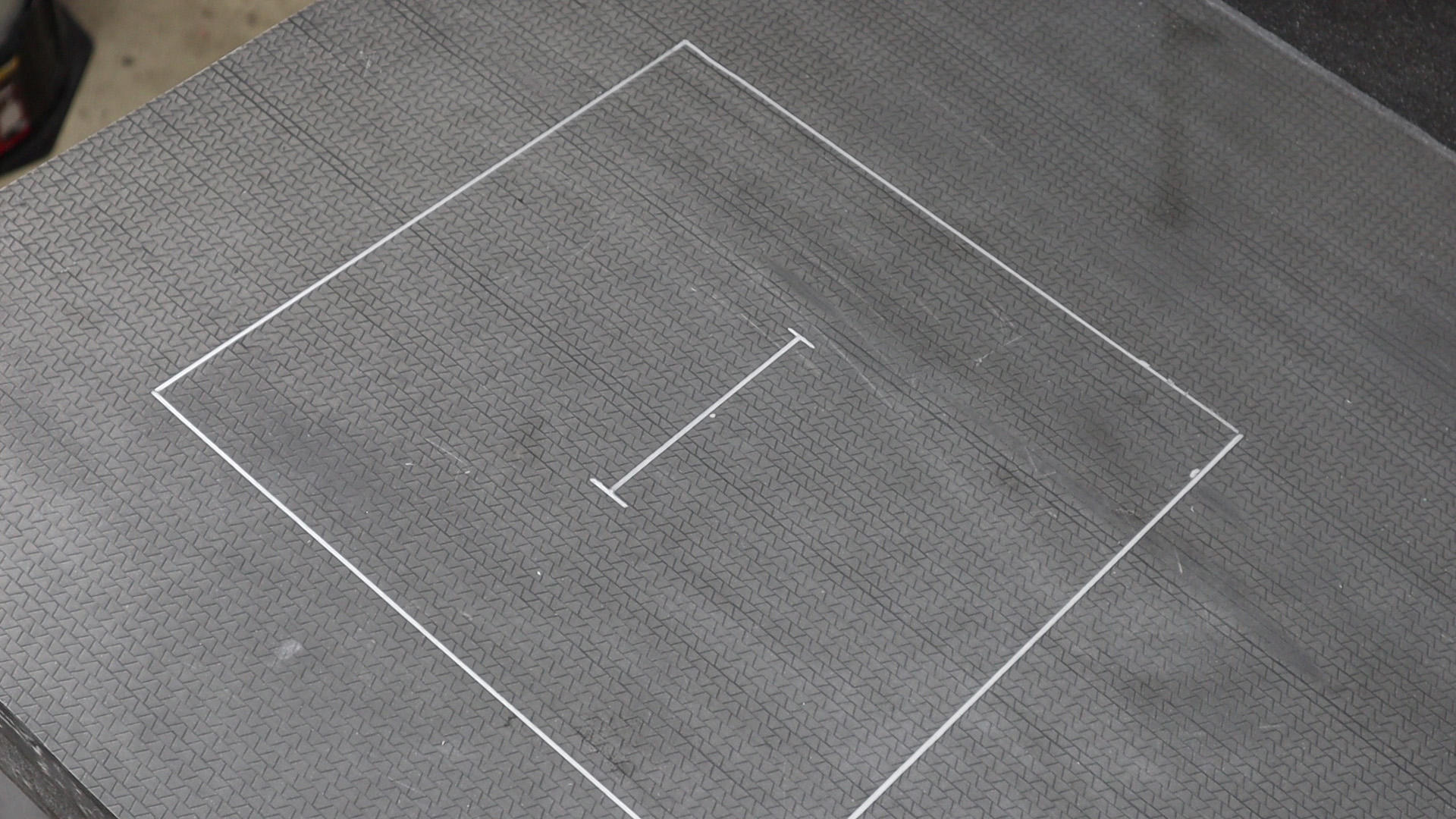
Шаг 1. Эта испытательная панель показывает диаметр отверстия 3 дюйма для имитации повреждений, отмеченных в центре, а также по периметру ремонта. Фото для всех этапов:Custom Technologies LLC.
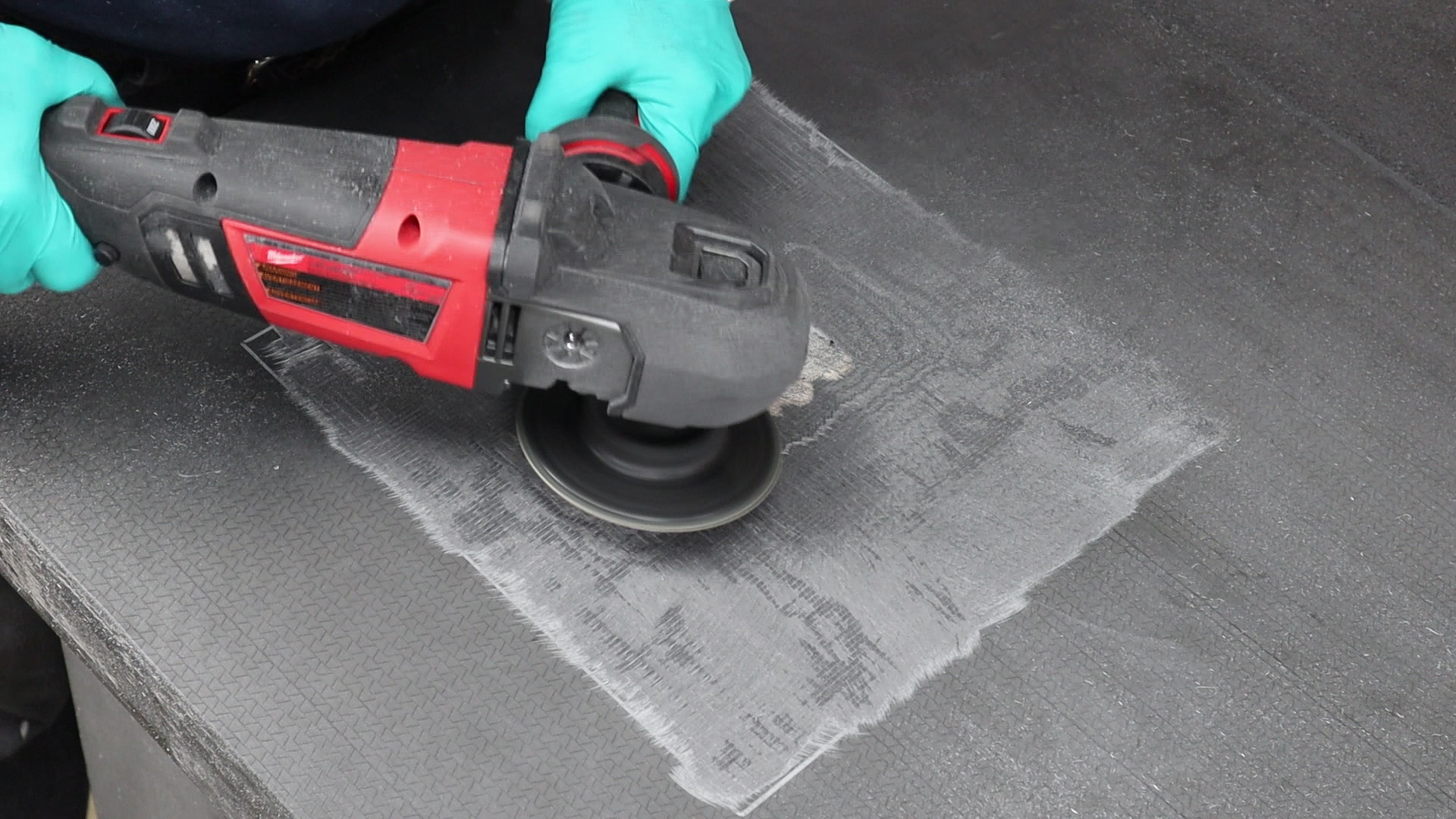
Шаг 2. Ручной шлифовальный станок с батарейным питанием используется для удаления поврежденного материала и скашивания конуса 12:1 для получения ремонтной заплатки.
«Мы хотели смоделировать более высокую степень повреждения испытательных панелей, чем то, что можно увидеть на настилах мостов в полевых условиях», - объясняет Берген. «Итак, наш подход заключался в использовании кольцевой пилы, чтобы проделать отверстие диаметром 3 дюйма. Затем мы вытащили пробку из поврежденного материала и выполнили скашивание 12:1 с помощью ручного пневматического шлифовального станка ».
Для ремонта углеродного волокна / эпоксидной смолы, объясняет Крейн, после того, как «поврежденный» материал облицовки был удален и наложен соответствующий шарф, препрег обрезался по ширине и длине, чтобы соответствовать конусности поврежденного участка. «Для наших испытательных панелей потребовалось четыре слоя препрега, которые позволили выравнивать ремонтный материал с верхней частью оригинального неповрежденного углеродного лицевого листа. После этого три слоя препрега из угля и эпоксидной смолы были центрированы над этим участком ремонта. Каждый последующий слой удлинялся на 1 дюйм со всех сторон от нижнего слоя, что обеспечивало постепенную передачу нагрузки от «хорошего» окружающего материала на ремонтируемую область ». Общее время выполнения этого ремонта, включая подготовку зоны ремонта, разрезание и размещение ремонтного материала, а также применение процедуры отверждения, составило примерно 2,5 часа.
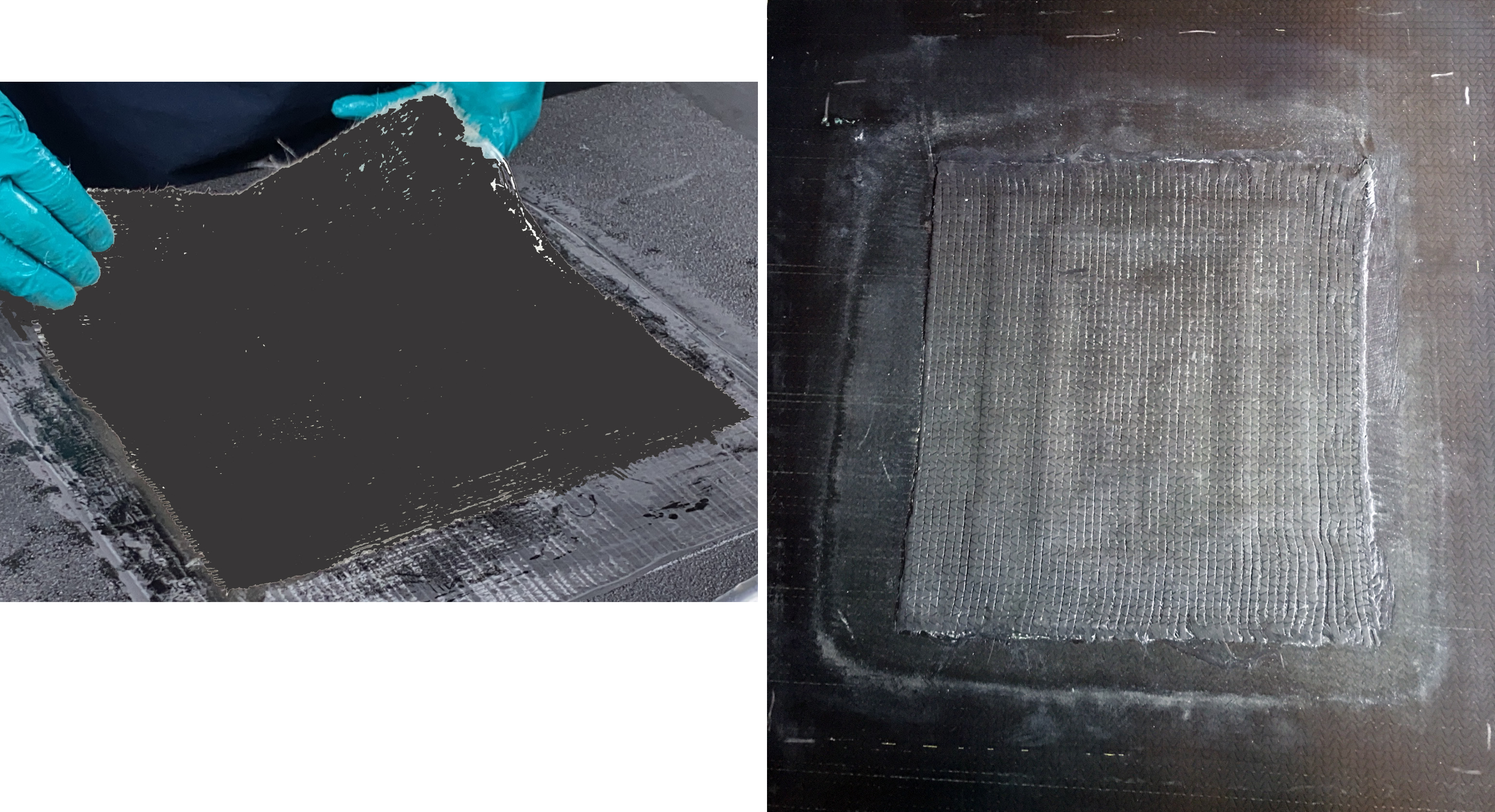
Несмотря на то, что ремонт карбона / эпоксидной смолы выполняется просто и быстро, команда осознала необходимость еще более целесообразного решения, которое могло бы восстановить производительность. Это привело к исследованию препрега, отвержденного ультрафиолетом (УФ). «Интерес к винилэфирной смоле Sunrez был основан на предыдущем опыте ВМС с Марком Ливси, который основал компанию», - объясняет Берген. «Мы начали с предоставления Sunrez квазиизотропной стеклоткани для препрега с их сложным виниловым эфиром и оценили профиль отверждения в различных условиях. Кроме того, зная, что винилэфирная смола не обеспечивает таких подходящих вторичных связывающих свойств, как эпоксидная смола, были предприняты дополнительные усилия по оценке различных связывающих агентов и их квалификации для этого применения ».
Другая проблема заключалась в том, что стекловолокно не обладает такими же механическими свойствами, как углеродное волокно. «Эта проблема была решена путем использования одного дополнительного слоя стекло / винилового эфира по сравнению с углеродно-эпоксидной заплатой», - говорит Крейн. «Причина, по которой требовался только один дополнительный слой, заключалась в том, что стеклянный материал был более тяжелой тканью». В результате получился подходящий пластырь, который можно было наложить, а затем отвердить за шесть минут даже при очень низких / низких температурах внутри помещения без необходимости подачи тепла. Крейн отмечает, что этот ремонт можно завершить за один час.
Обе системы исправлений были продемонстрированы и протестированы. Для каждого ремонта область, которая должна быть повреждена, была помечена (шаг 1), создана с помощью кольцевой пилы и затем удалена с помощью ручной шлифовальной машины с батарейным питанием (шаг 2). Зона ремонта затем была зашита до конуса 12:1. Зачистную поверхность очищали спиртовыми салфетками (шаг 3). Затем пластырь был обрезан по размеру, помещен на очищенную поверхность (шаг 4) и закреплен валиком для удаления пузырьков воздуха. Для препрега из стекловолокна / винилэфирного отверждения, отверждаемого ультрафиолетом, на зону ремонта помещали отрывной слой и пластырь отверждали с использованием беспроводного ультрафиолетового излучения в течение шести минут (этап 5). Для препрега из углеродного волокна / эпоксидной смолы участок ремонта был запакован в вакуумный мешок и отвержден с использованием предварительно запрограммированного однокнопочного устройства для горячей склейки с батарейным питанием в течение одного часа при 210 ° F / 99 ° C.
Действия по исправлению
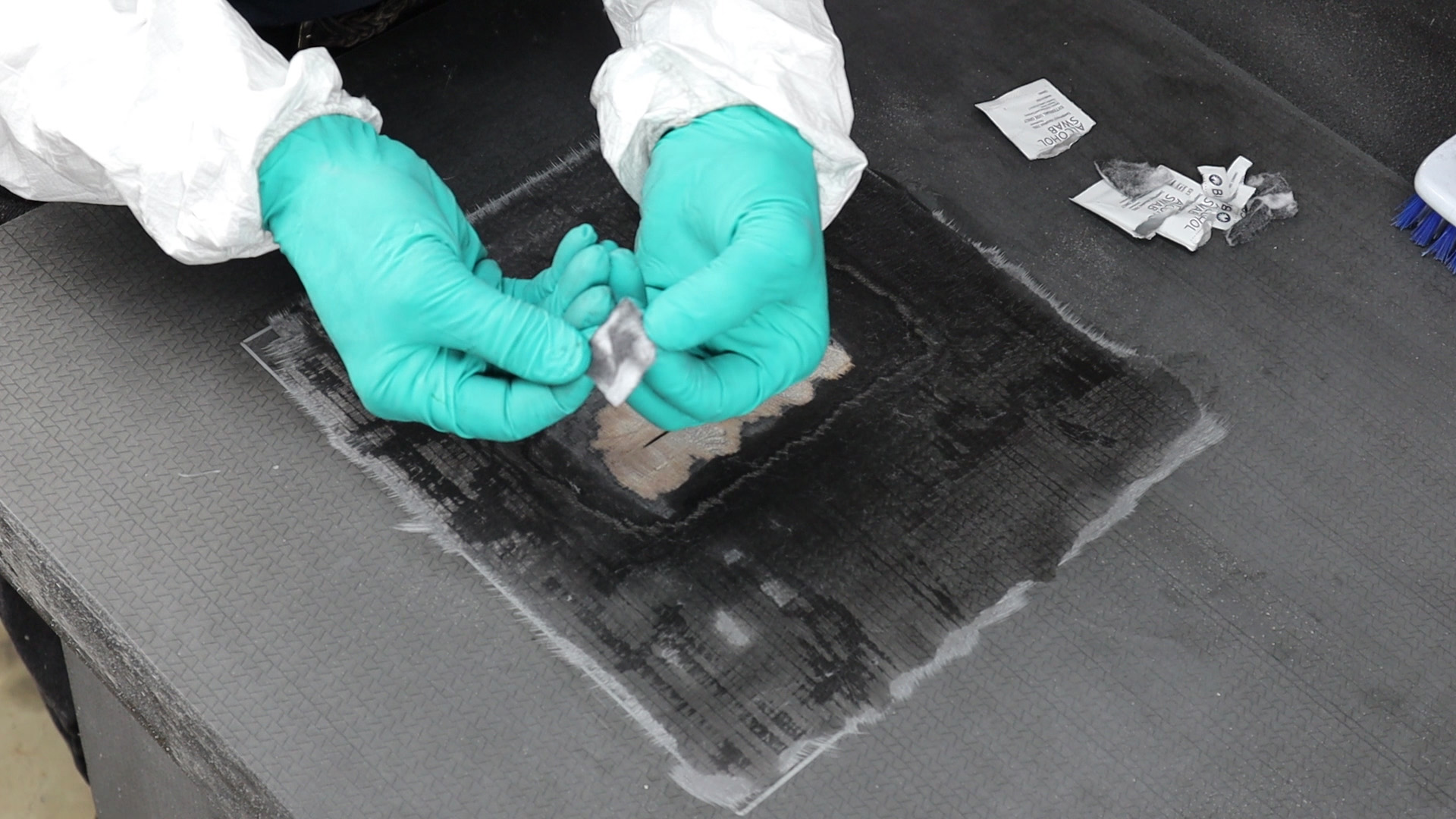
Шаг 3. Подготовленный ремонтный участок протирают растворителем с одноразовыми спиртовыми салфетками.
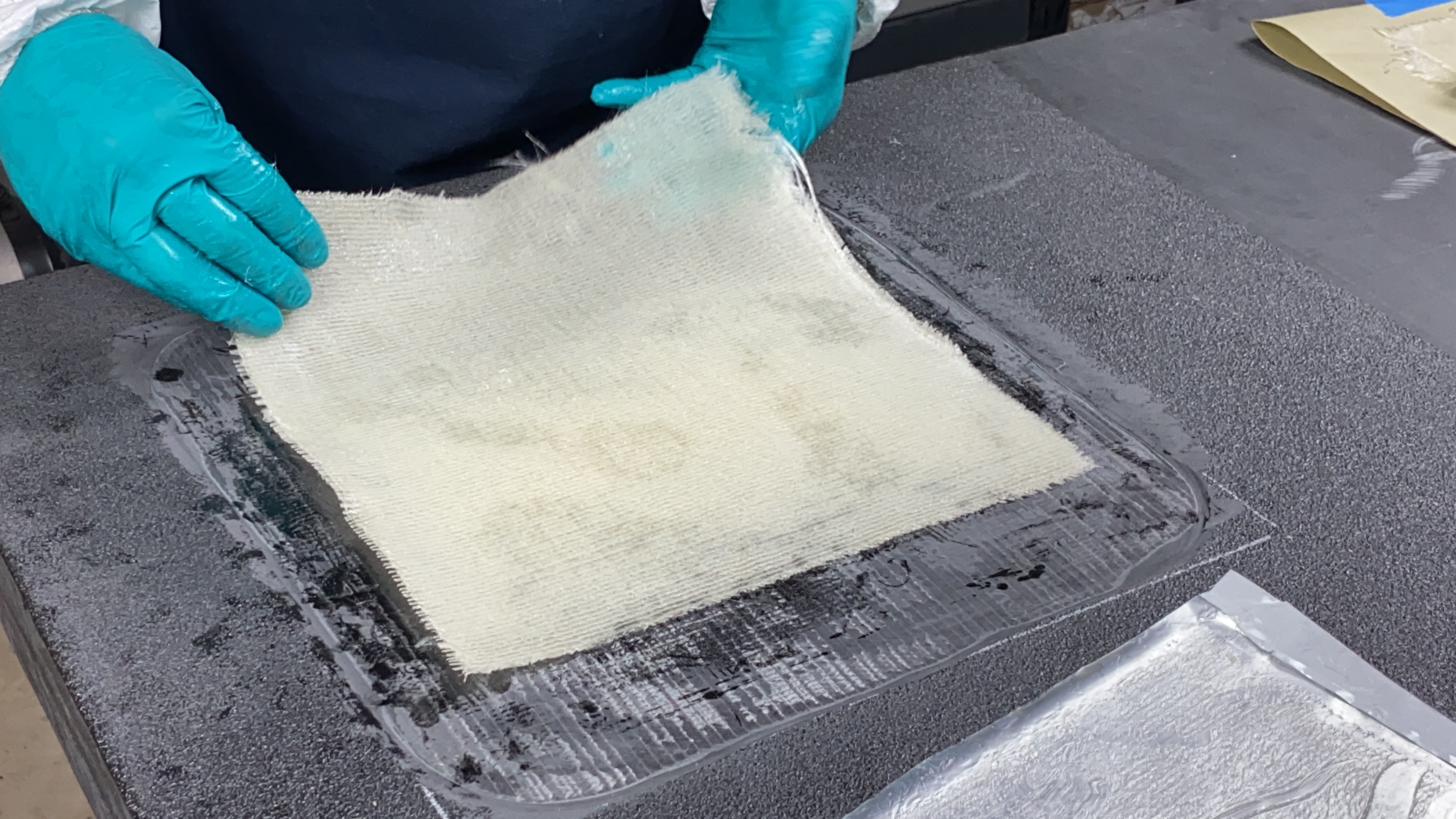
Шаг 4. Ремонтная заплатка из стекловолокна / винилового эфира обрезается по размеру и помещается на ремонтируемую область.
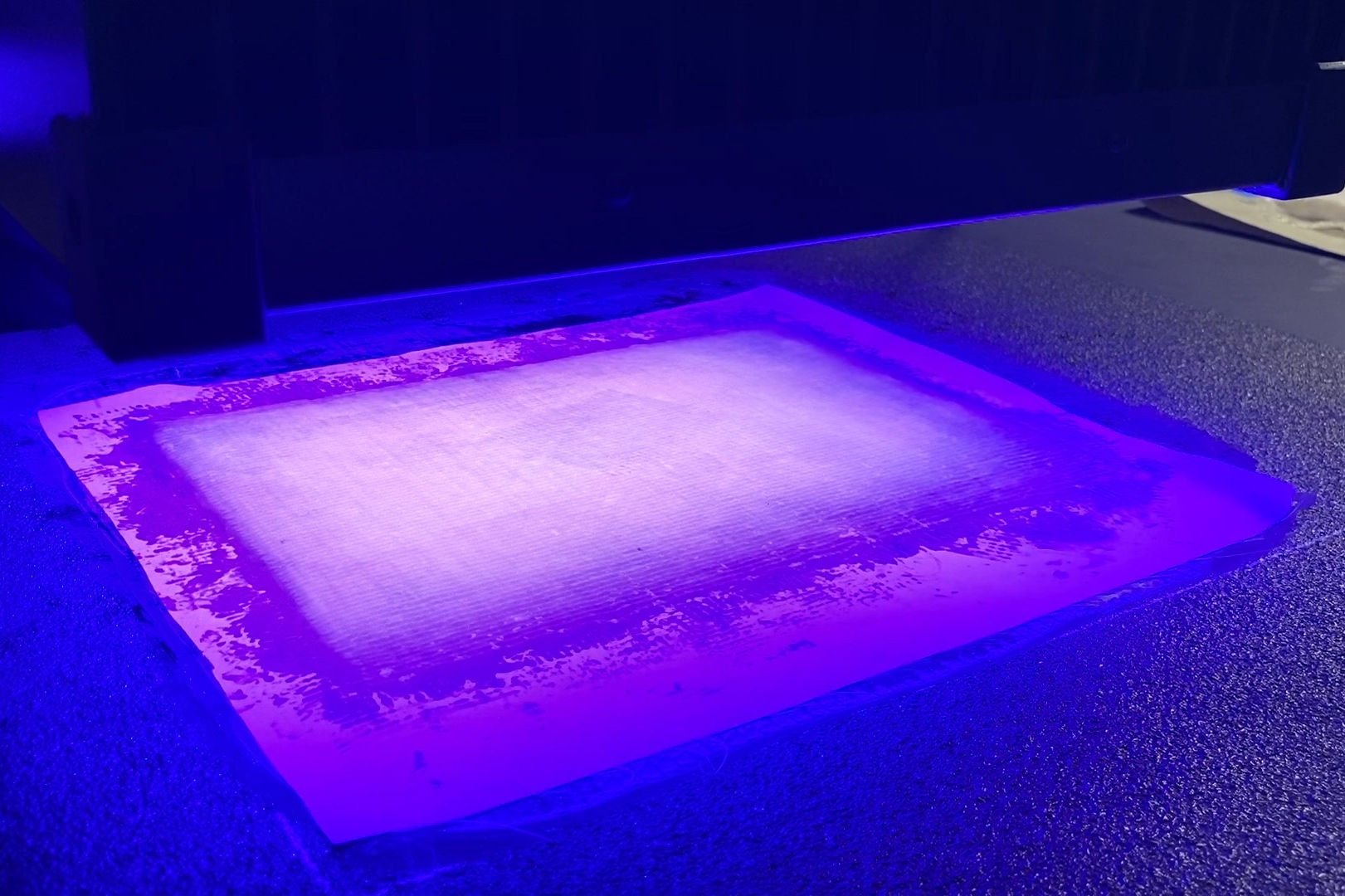
Шаг 5. После того, как на ремонтируемый участок наложен слой отслаивания, пластырь отверждается с использованием беспроводного ультрафиолетового излучения в течение шести минут.
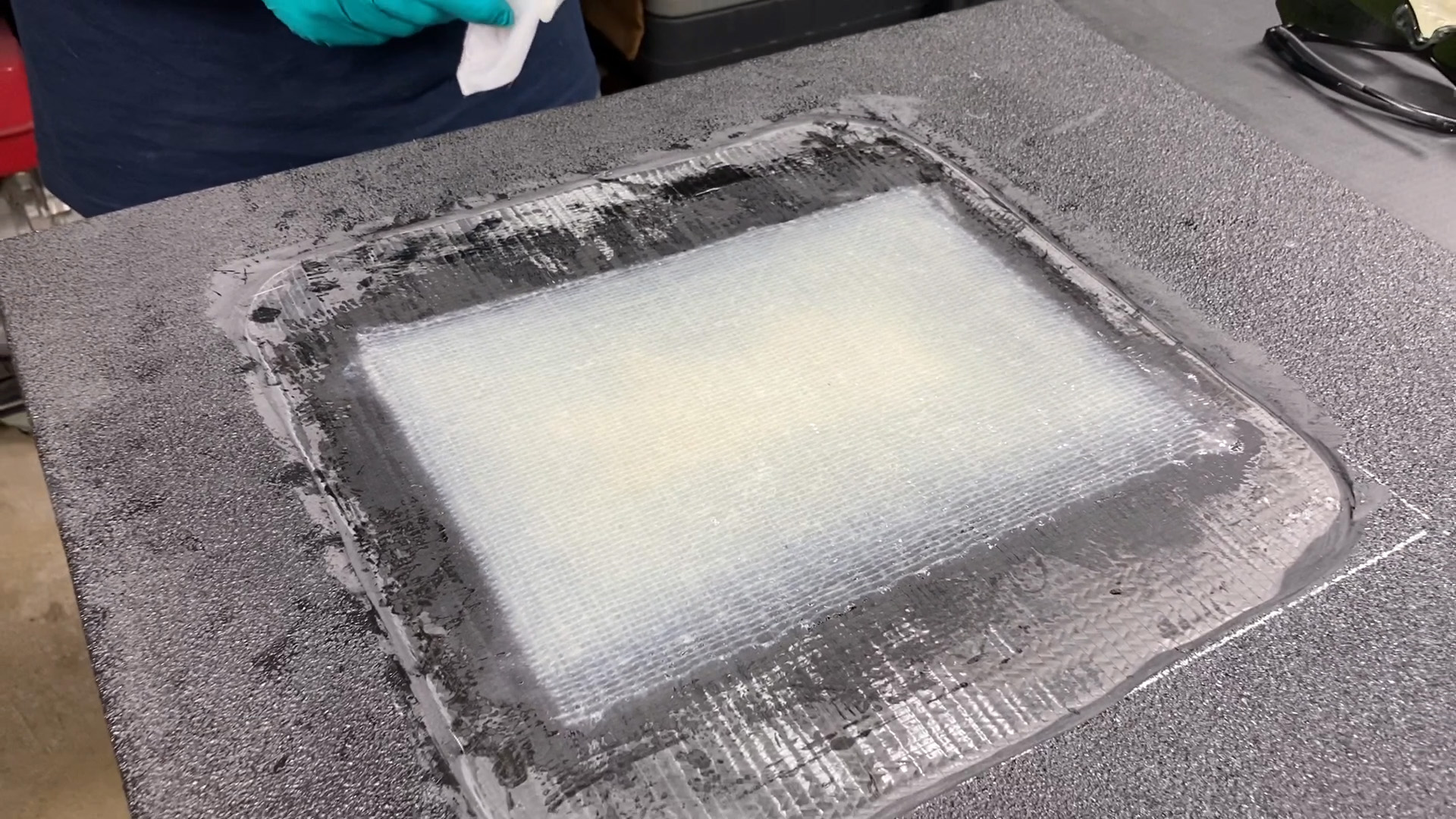
Шаг 6. Завершение ремонта заплаткой из стекловолокна / винилэфирного препрега, отвержденного ультрафиолетом.
Предыдущий Следующий«Затем мы провели испытания, чтобы оценить адгезионную связь заплатки и способность восстанавливать несущую способность конструкции», - говорит Берген. «На этапе 1 от нас требовалось продемонстрировать простоту нанесения и способность восстановить как минимум 75% прочности. Это было достигнуто на 4 x 48-дюймовых балках из углеродного волокна / эпоксидной смолы и балки с сердцевиной из бальзы при четырехточечном изгибе после ремонта смоделированного повреждения. В проекте Фазы 2 использовались панели размером 12 x 48 дюймов, и требовалось обеспечить более 90% прочности при сложных деформационных нагрузках. Мы выполнили все эти требования, а затем засняли методы ремонта на модели AMCB, чтобы дать визуальное представление о том, как использовать методы и оборудование в поле ».
Успех новичков, приложения будущего
Одним из ключевых аспектов проекта было доказать, что новичок может легко завершить ремонт. Для этого у Бергена была идея:«Я пообещал провести демонстрацию двум нашим техническим специалистам в армии:доктору Бернарду Сиа и Эшли Генна. При окончательной проверке проекта Этапа I я попросил Эшли, у которой не было предыдущего опыта ремонта, выполнить ремонт. Используя комплекты и руководство, которые мы предоставили, она применила исправление и без проблем завершила ремонт ».
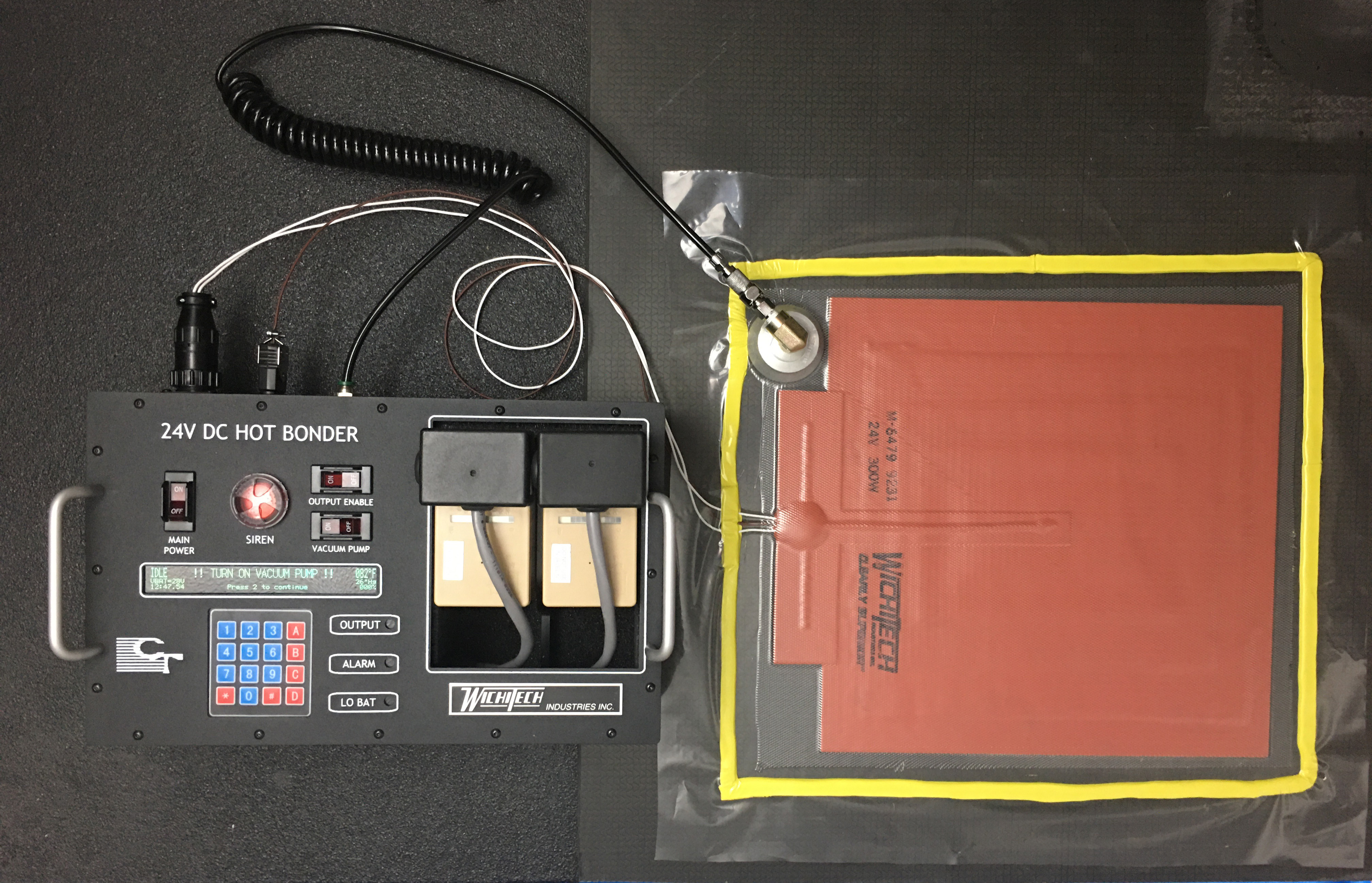
Еще одна важная разработка - система отверждения с батарейным питанием (рис. 2). «С ремонтом в приусадебном участке у вас будет только батарея», - отмечает Берген. «Все технологическое оборудование в нашем разработанном ремонтном комплекте - беспроводное». Сюда входит устройство для горячего склеивания с батарейным питанием, разработанное Custom Technologies совместно с поставщиком оборудования для горячего склеивания WichiTech Industries Inc. (Рэндаллстаун, Мэриленд, США). «Этот термофиксатор с батарейным питанием предварительно запрограммирован на полное отверждение, поэтому новичку не нужно программировать цикл отверждения», - говорит Крейн. «Они просто нажимают кнопку, и это завершает соответствующий наклон и замачивание». Батареи, которые используются в настоящее время, служат год, прежде чем их потребуется перезарядить.
Теперь, когда проект Фазы II завершен, Custom Technologies готовит последующее предложение по усовершенствованию и собирает письма с заинтересованностью и поддержкой. «Наша цель - довести эту технологию до уровня TRL 8 и реализовать ее на практике», - говорит Берген. «Мы также видим потенциал для невоенного применения».
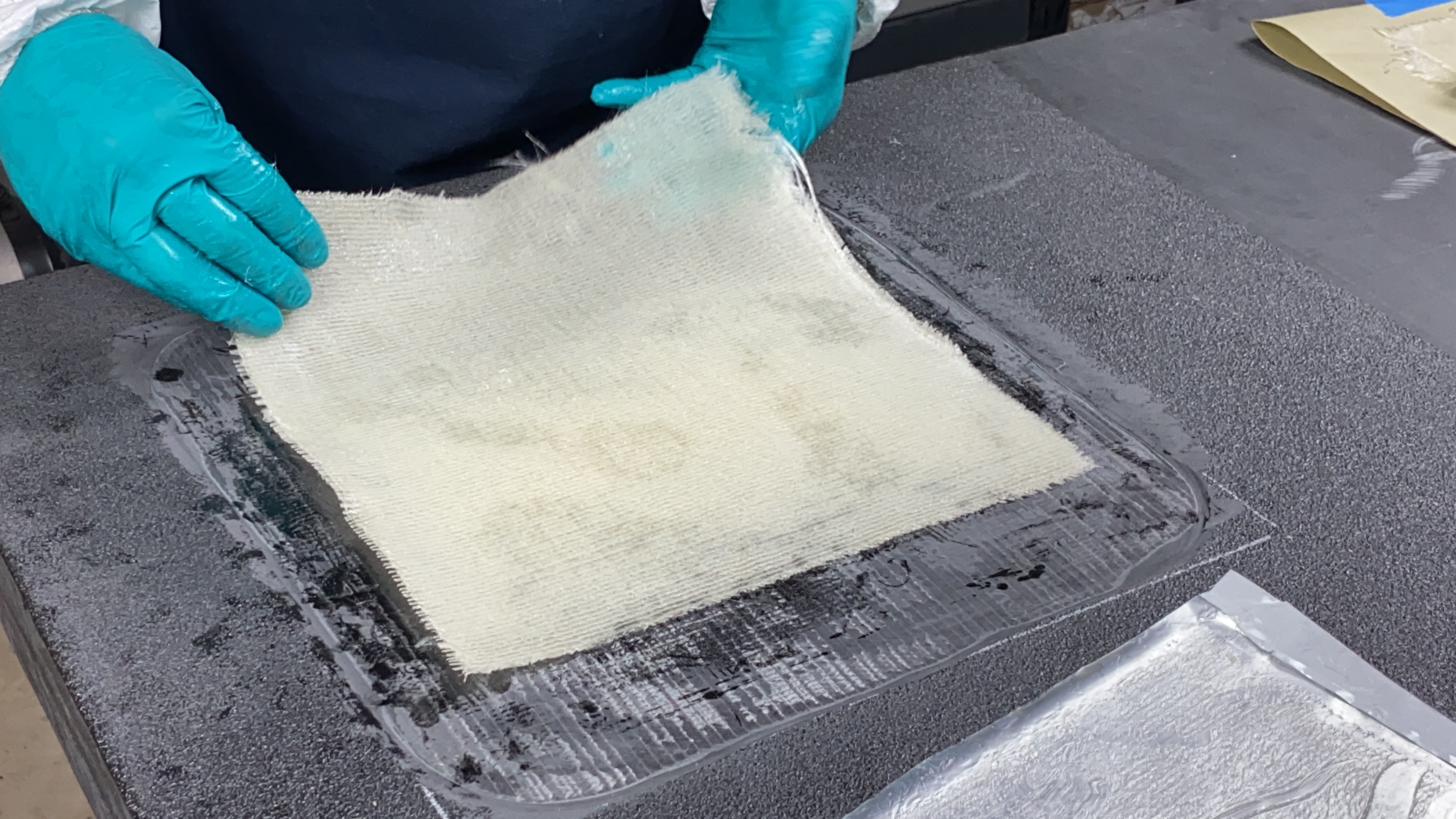
Смола
- 3 самых распространенных инженерных приложения для композитных материалов Thermoset
- Производство композитов:производство композитных материалов
- Структуры термопластов в центре внимания присутствия Engel на выставке China Composites Expo
- Разработка композитных изосеточных структур с использованием инновационной технологии осаждения
- Alveus для коммерциализации услуг Compa Repairs по ремонту композитных судов
- Исследование AFRL продвигает 3D-печать CF / эпоксидных композитов
- Hexcel сотрудничает с Lavoisier Composites, Arkema
- AMRC и Prodrive объединились для улучшения производства перерабатываемых композитных компонентов
- TenCate празднует сборку консорциума термопластичных композитов в Бразилии
- Композитные материалы:где их найти на NPE2018