Ускорение RTM с датчиками теплового потока
Шасси шасси, составляющее 3-5% веса самолета, долгое время использовалось для снижения веса с целью повышения его эффективности. Это стало еще более важным в связи с неизбежным переходом на электрические двигательные установки, снижающие потребление энергии и вредные выбросы.
Например, Safran Landing Systems (Велизи, Франция) обеспечит отключение двигателей, электрическое руление с помощью электродвигателей, встроенных в колеса шасси самолета, снижая выбросы NOx, CO 2 , Выбросы CO и несгоревших углеводородов на 51%, 61%, 73% и 62% соответственно. Это огромная победа для более экологичной авиации, но электродвигатели требуют энергии, а батареи, необходимые для обеспечения этой энергии, тяжелые.
Таким образом, потребность в легких конструкциях шасси кажется идеальным решением для применения композитов, за исключением одной проблемы. «Поскольку шасси представляет собой конструкцию с одинарной нагрузкой, отказ конструктивного элемента может привести к серьезным аварийным условиям посадки», - говорит Пит Вергоувен, технолог GKN Fokker Landing Gear (Хелмонд, Нидерланды). Компания GKN Fokker Landing Gear более десяти лет работала над демонстрацией технической осуществимости конструкций шасси из композитных материалов, включая разработку армированных углеродным волокном полимера (CFRP) тормозных скоб для F-35 Lightning II . «Из-за своей критичности конструкции шасси являются одними из самых консервативных в коммерческих самолетах». Следовательно, они в основном изготавливаются из высокопрочных металлов.
Однако эта тенденция начинает меняться. Clean Sky 2 стремится к снижению веса на 30%, но с помощью компонентов из углепластика в проекте HECOLAG (High Efficiency Composites LAnding Gear) для двух применений. В первом приложении была разработана альтернатива углепластика для существующей алюминиевой верхней опоры сопротивления . для носовой стойки шасси A350-1000, первоначально разработанной и изготовленной компанией Liebherr-Aerospace (Линденберг, Германия). Партнеры HECOLAG - Королевский аэрокосмический центр Нидерландов (NLR, Marknesse) и GKN Fokker Landing Gear разработали этот перетягивающий шарнир из углепластика в соответствии с требованиями Liebherr. Используя разработанную собственными силами технологию автоматизированного формования, NLR построила функциональные прототипы перетяжки из углепластика, которые были протестированы GKN Fokker Landing Gear.
Во втором заявлении, оцениваемом HECOLAG, NLR и GKN Fokker Landing Gear также разработали нижнюю стойку опоры из углепластика. совместно с Safran Landing Systems для электрифицированных основных стоек шасси. CW представит конкретный отчет об общих результатах проекта HECOLAG позже в 2021 году, но здесь основное внимание уделяется подпроекту INNOTOOL 4.0 под руководством руководителя темы GKN Fokker Landing Gear для продвижения высокоавтоматизированного производства конструкций шасси из углепластика с использованием литья под давлением (RTM). . В частности, INNOTOOL 4.0 стремится продемонстрировать инструменты, интегрированные с датчиками, которые приведут к созданию инструментов меньшего размера с меньшей массой для более быстрых производственных циклов, упрощения обработки и снижения энергопотребления, а также повышенной автоматизации для снижения затрат и интеллектуального управления процессами композитов 4.0. Проект INNOTOOL 4.0 финансируется совместным предприятием Clean Sky 2 в рамках исследовательской и инновационной программы ЕС Horizon под GAP № 821261.
Цели INNOTOOL 4.0
Демонстрационный образец для этой второй части HECOLAG (см. Начальное изображение) является скорее общей частью, объясняет Вергоувен. «Он предназначен для демонстрации методологий проектирования, моделирования и производства деталей, которые обеспечат характеристики, производительность и стоимость, необходимые для узкофюзеляжных самолетов». К концу 2017 года консорциум HECOLAG определил первоначальную часть демонстратора углепластика и производственный инструмент, проанализировал термическое поведение инструмента и провел испытания производительности. Этот большой и сложный продукт прошел предварительную проверку проекта и в том же году достиг уровня технологической готовности (TRL) 4. «Основываясь на проблемах и уроках, извлеченных из этого первого демонстратора, мы искали партнеров для разработки технологии инструментов RTM для оптимизации и сокращения цикла отверждения», - говорит Вергувен. Конкурс на участие в программе Clean Sky 2 для партнеров был объявлен в 2018 году и был присужден консорциуму INNOTOOL 4.0, в который входят поставщик оборудования и средств автоматизации Techni-Modul Engineering (TME, Coudes, Франция) и компания Isojet Equipements, специализирующаяся на впрыске смол (Corbas, Франция). Они начали работу в апреле 2019 года и завершили начальные этапы в марте 2021 года.
«Композитная деталь должна быть конкурентоспособной по стоимости с кованной сталью и алюминием», - отмечает Вергувен из GKN Fokker Landing Gear. «Это возможно только с помощью автоматизации, позволяющей сократить количество рабочих часов и использовать более доступные материалы, чем нынешний углепластик аэрокосмического качества, отверждаемый в автоклаве».
Таким образом, INNOTOOL 4.0 стремился интегрировать датчики в инструментарий RTM, который будет контролировать и управлять процессами впрыска и отверждения, включая обнаружение фронта потока смолы. «Наша цель - полностью автоматизировать процесс - загрузить преформу, нажать кнопку, и формовочное оборудование будет управлять температурой, давлением, вакуумом и отверждением», - говорит Стефан Бессон, коммерческий директор TME. Тем не менее, это первый случай, когда GKN Fokker Landing Gear и TME работают с мониторингом отверждения. «Раньше мы работали с датчиками температуры и давления, - говорит Бессон, - но не с датчиками текучести и полимеризации смолы».
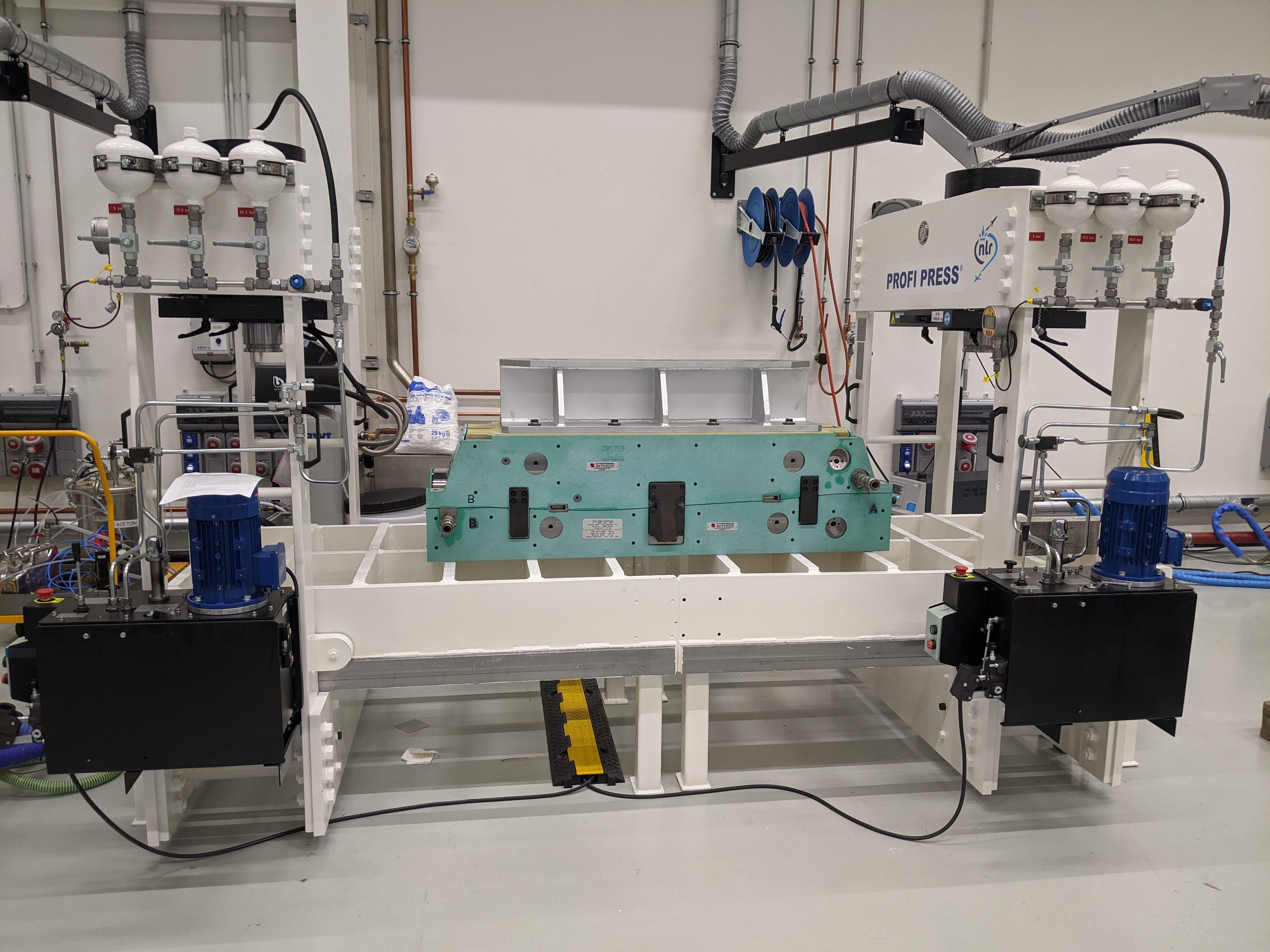
Первоначальные вехи проекта INNOTOOL 4.0 требовали от TME и Isojet поставки в NLR формовочного инструмента с датчиками и системы впрыска, которые будут использоваться для производства демонстрационных деталей в марте и апреле 2021 года. Параллельно TME будет использовать существующий инструмент для производства Плиты из углепластика - размером 600 x 600 миллиметров и толщиной 1-8 миллиметров - модифицированы теми же датчиками для испытаний контроля процесса на своем предприятии. «Это то, что вы предпочли бы делать в небольшом масштабе в первый раз, чем непосредственно на большом инструменте с дорогостоящей деталью», - говорит Вергоувен. Таким образом, TME использовала другой инструмент, но те же датчики, чтобы показать их возможности и глубину. После завершения этого тестирования NLR затем повторно использовала бы основной инструмент HECOLAG для создания нового раунда демонстраторов углепластика для дальнейшей оптимизации управления процессом на реальных деталях.
Разработка производственных инструментов RTM
TME начала производство инструментов для проектирования RTM с использованием программного обеспечения CATIA V5 от Dassault Systèmes (Велизи-Виллакублей, Франция) для механического и электрического проектирования и ANSYS (Канонсбург, Пенсильвания, США) для теплового и механического моделирования. Этот инструмент будет работать в паре с поршневой системой Isojet 1K-2K (для одно- и двухкомпонентных смол) для нагнетания Hexcel (Стэмфорд, Коннектикут, США) HexFlow 2K RTM 6 и Solvay (Alpharetta, Ga., США) 1K Однокомпонентные эпоксидные смолы PRISM EP 2400 для аэрокосмической промышленности при давлении впрыска до 20 бар.
«Форма этого формовочного инструмента очень сложна», - отмечает Бессон, «сочетая разную толщину в трехмерной сухой преформе с замкнутой трубчатой формой. Это создает сложные переходы толщины с проблемами, связанными с сборкой преформы, точностью конца слоя, внутренними температурными градиентами и усадкой смолы, а также с тем, как оптимизировать метод нагрева и нагревательную способность внутренней оправки, чтобы обеспечить короткое время цикла. Чтобы обеспечить короткое время цикла, все элементы инструмента должны быть простыми в использовании, прочными и допускать быстрое нагревание и охлаждение ». Несмотря на то, что в рамках проекта INNOTOOL 4.0 вкратце требовались решения для неметаллических форм, был разработан типичный согласованный набор верхней и нижней стальных форм из-за давления, необходимого для минимизации складок и обеспечения выравнивания волокон во время формования.
Соответствующие верхняя и нижняя формы и оправка нагреваются и охлаждаются. «В согласованных формах используется интегрированный водяной контур, а оправка имеет электрический нагрев», - поясняет Бессон. «Циркуляция воды обеспечивает быстрый нагрев и охлаждение, чтобы сократить время неполного цикла, а электрический нагрев обеспечивает то же самое в оправке, где пространство ограничено».
«Другой проблемой было количество деталей в оправке», - говорит Бессон. «Из-за сложной формы и необходимости снятия оправки после формования она состояла из шести самонагревающихся компонентов и двух опорных элементов, через которые проходят датчики для контроля внутренней температуры деталей оправки. При использовании эти элементы собираются вручную с помощью базовой опоры, которая направляет оператора ». Работа с надувной оправкой в качестве решения будет завершена в рамках более крупного проекта HECOLAG, но это не было включено в подпроект INNOTOOL 4.0.
Датчики теплового потока
Первоначально TME планировала использовать диэлектрические датчики для контроля текучести и отверждения смолы (см. «Объединение диэлектрических измерений переменного и постоянного тока для контроля отверждения композитов»), но перешла на датчики теплового потока от TFX (Boncourt, Швейцария). «По мере продвижения в разработке нам нужны были датчики, которые позволяли бы контролировать измерения без прямого контакта с полимерами и композитными материалами», - объясняет Хорхе Лопес Торрес, менеджер проектов TME. «Датчики TFX позволили это сделать, потому что они измеряют тепловой поток, который распространяется через материалы». Он указывает, что это в основном то же измерение, которое используется в дифференциальной сканирующей калориметрии (ДСК), лабораторном методе, который анализирует состояние отверждения полимера или композита. Примечательно, что как датчики TFX, так и тестирование DSC измеряют тепло, выделяемое во время полимеризации / отверждения, и выдают кривую теплового потока в зависимости от температуры и времени.
Для датчиков TFX данные о температуре поступают от внутреннего датчика температуры в датчиках теплового потока. Хотя диэлектрические датчики аналогичным образом оснащены внутренним датчиком температуры, эти два датчика сильно различаются. «Диэлектрические датчики напрямую измеряют свойства полимера во время отверждения», - объясняет менеджер TFX д-р Фабьен Кара. «Датчики теплового потока не показывают состояние материала в данный момент. Однако измерение тепла, выделяемого во время течения смолы и полимеризации, дает хорошее представление о том, как протекает процесс и насколько повторяем цикл отверждения для каждой произведенной детали. И, как и DSC, нам нужно видеть всю кривую процесса отверждения, но наша способность отслеживать отверждение очень надежна ».
Многолетний опыт
Основанная в 2000 году как Thermoflux, датчики TFX использовались в испытаниях в научно-исследовательских центрах и в промышленных приложениях более чем 100 клиентами по всему миру. «Мы начали работать с RTM более 15 лет назад, - говорит Кара, - сначала с BMW в области автомобильных запчастей, а также с техническим центром, ныне известным как Institute de Soudure [(Сен-Авольд, Франция)]. В 2006 и 2012 годах мы начали два крупных проекта по мониторингу отверждения лопаток вентиляторов авиационных двигателей, изготовленных с использованием RTM и 3D-тканых преформ. У Safran есть система сбора данных, которую мы разработали для них в их лаборатории композитов недалеко от Парижа. Они могут одновременно записывать до 100 сигналов [(тепловой поток, температура и давление]) и анализировать их для отверждения и контроля технологических циклов ». TFX также работал с Hexcel в своей лаборатории в Les Avenières, Франция, чтобы контролировать качество и циклы обработки термореактивных смол, вводимых в сухие преформы. Датчики TFX также использовались в проекте с IRT-M2P (Порселетт, Франция) для демонстрации Compression RTM (Подробнее). «Наши датчики очень эффективны для быстрых процессов, таких как прессование, в том числе с формовочными смесями SMC и BMC», - отмечает Кара. «Мы также выиграли награду JEC Innovation в 2016 году вместе с компанией Huntsman Advanced Materials [(Базель, Швейцария)] за разработку под названием« Конструкционные эпоксидные детали с автоклавным качеством менее чем за 1 минуту ».
В TFX есть датчики для каждого типа процесса формования композитов, в зависимости от метода передачи тепла к датчику:теплопроводности (RTM, прессование и литье под давлением), конвекции (автоклав, печь) и излучения (намотка нити, AFP). Датчики, использованные в проекте INNOTOOL 4.0, были токопроводящими, предназначенными для встраивания в металлические формы RTM. «Они обеспечивают исключительно воспроизводимый сигнал на расстоянии до 1 миллиметра от поверхности инструмента и композитного материала», - отмечает Кара.
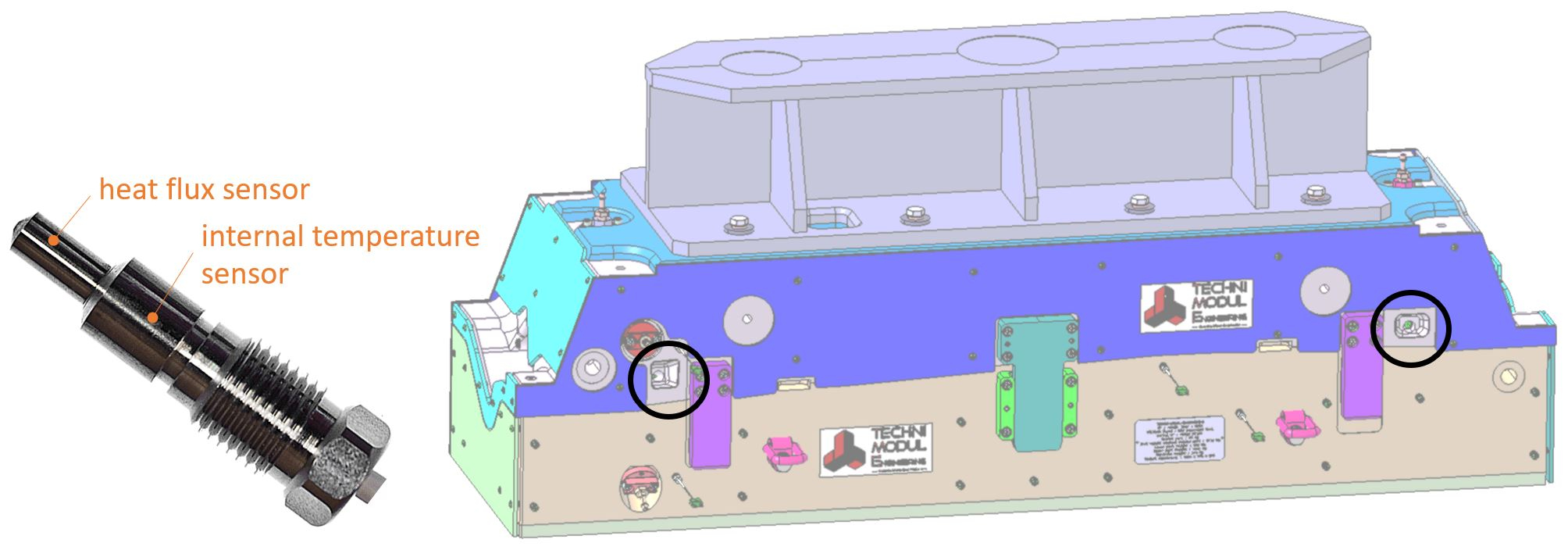
TME установила два датчика TFX-191 - один на входе смолы и один на выходе смолы - в верхнюю форму согласованного производственного набора инструментов, который затем отправил в NLR (рис. 1, 2). NLR использовала этот производственный инструмент для изготовления деталей демонстратора HECOLAG в марте и апреле 2021 года. Датчики TFX-191 предназначены для толстых металлических инструментов.
Параллельно TME взяла собственный инструмент меньшего размера, который использовался для изготовления образцов пластин из углепластика, и модифицировала его двумя датчиками TFX-224, которые короче, для более тонких инструментов (рис. 3). Этот набор инструментов для пластин RTM был затем использован для проведения демонстрационных испытаний датчиков в соответствии с описанными выше целями INNOTOOL 4.0. «Эти датчики аналогичны тем, что мы использовали для Safran, - говорит Кара, - но теперь они улучшены, чтобы стать более компактными и чувствительными». Датчики были размещены около центра детали и выхода смолы. В дополнение к датчикам теплового потока компания TFX разработала и поставила две системы сбора данных:одну поставила в Isojet, а другую использовала TME для испытаний пластин из углепластика.
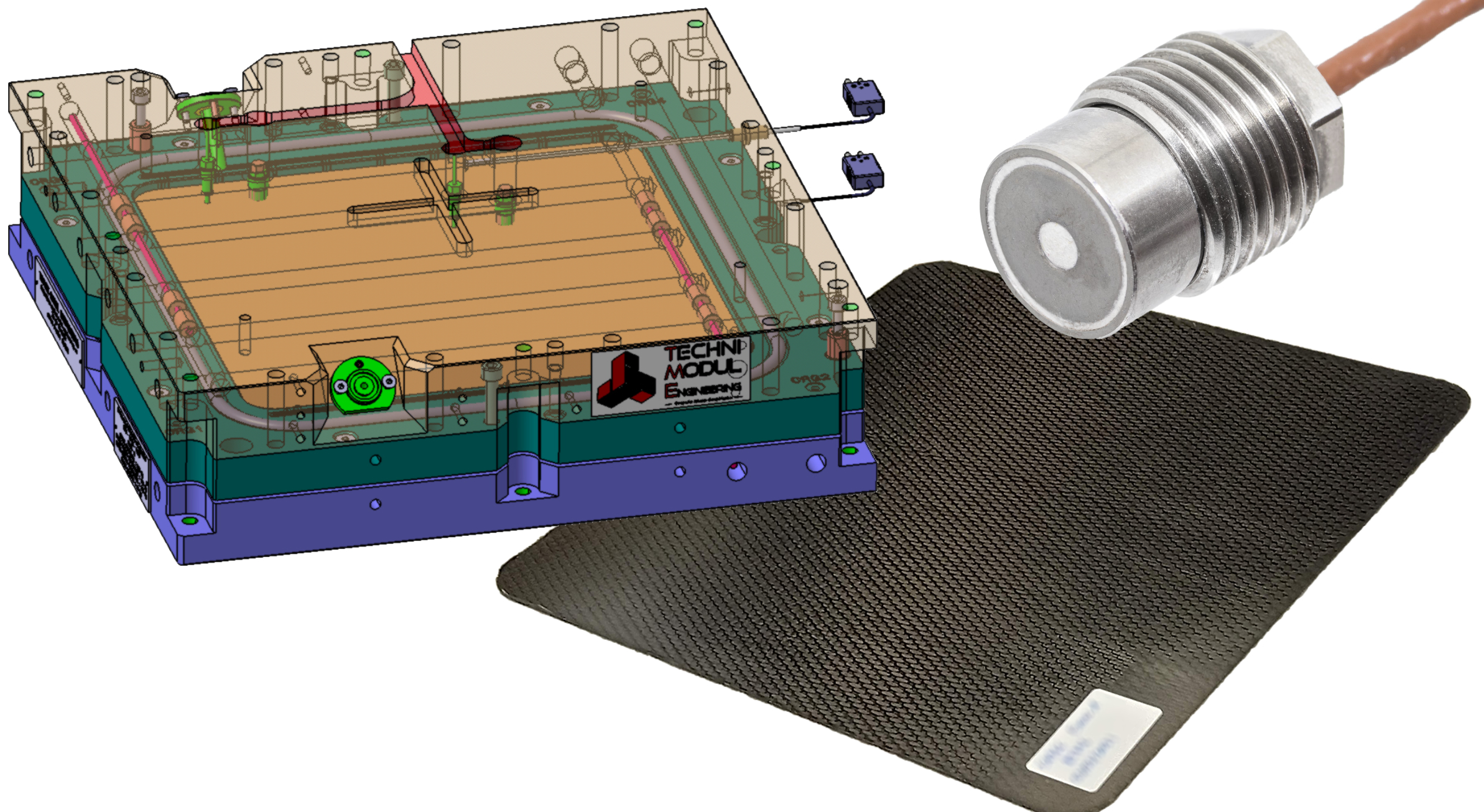
Результаты тестирования INNOTOOL 4.0
В ходе испытаний, проведенных TME с использованием пластинчатого инструмента, модифицированного датчиками TFX, были протестированы две разные смолы - HexFlow RTM 6 и PRISM EP 2400, а также влияние толщины детали и общего времени отверждения. «Датчики давали хорошие сигналы для отслеживания цикла отверждения», - говорит Кара. «Затем команда проанализировала кривые отверждения и показала, что время отверждения RTM 6 может быть сокращено как минимум на 30 минут по сравнению с предписанным двухчасовым лечением».
Это можно увидеть на приведенной ниже кривой, где t =0 часов - начало закачки. Обратите внимание:время отверждения начинается, когда температура достигает 180 ° C, а конец отверждения соответствует 99% относительного уровня отверждения (см. Вертикальную ось справа). Конец отверждения также совпадает со стабилизацией сырого теплового потока.
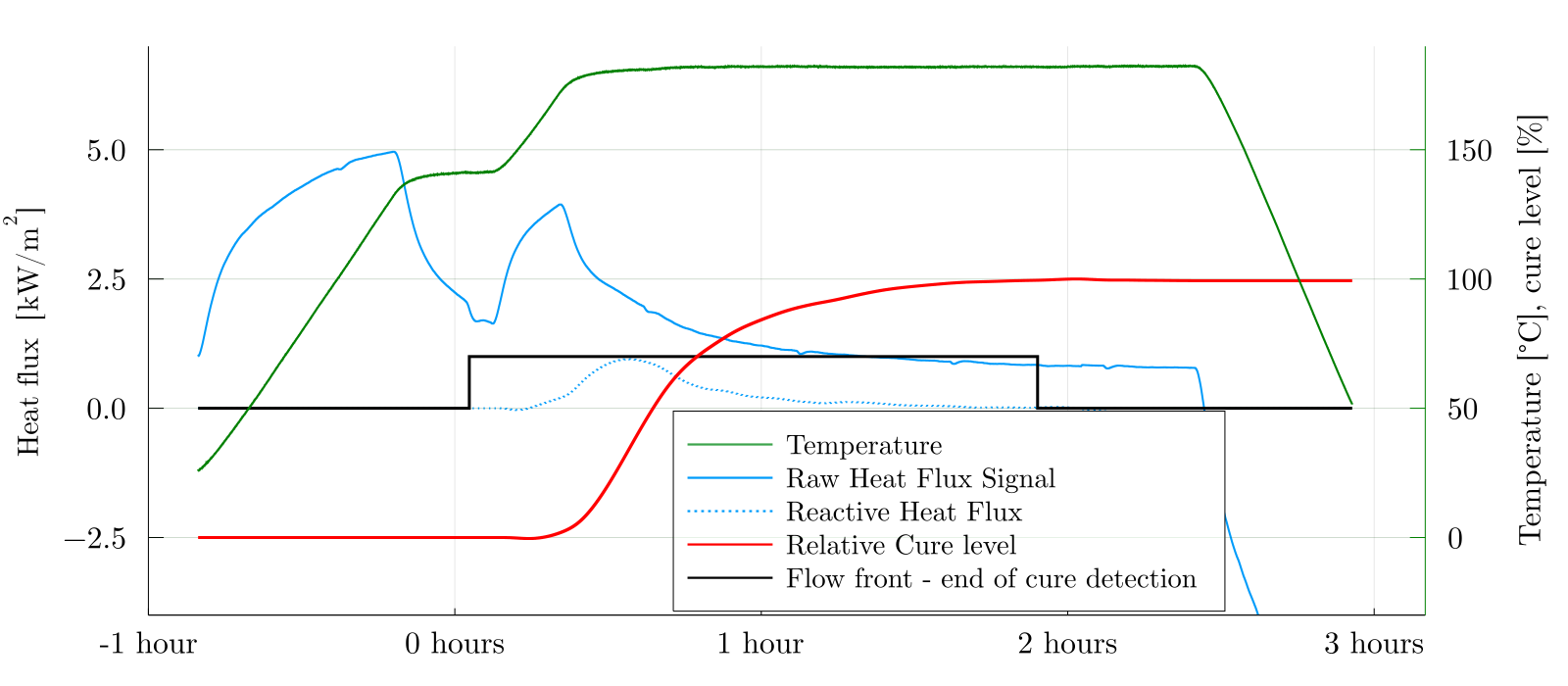
Это было подтверждено измерениями состояния отверждения демонтированных деталей с использованием динамического механического анализа (DMA), лабораторного метода, альтернативного DSC, который измеряет температуру стеклования (T g ) для композитов. «Результаты прямого доступа к памяти подтвердили, что для смолы RTM 6 T g остается неизменным после 90 минут отверждения при 180 ° C », - добавляет он.
Также было исследовано влияние толщины. «Первые плиты из углепластика, испытанные TME в ходе демонстрационных испытаний сенсоров, имели толщину менее 2 миллиметров», - отмечает Кара. «Эти пластины также имели большой объем волокна (50-60%) и медленный цикл отверждения, чтобы предотвратить экзотермический эффект и возможные проблемы с термическим напряжением и качеством деталей. Все это вполне нормально для деталей авиакосмической отрасли, но это означает, что смолы очень мало, и, следовательно, количество теплового потока, выделяемого при реакции смолы, было небольшим. Таким образом, мы, по сути, искали иглу теплового потока из-за отверждения смолы в океане нагрева инструмента и детали ».
Другими словами, как объясняет Кара:«Большинство циклов отверждения RTM в аэрокосмической отрасли включают нагнетание смолы при одной температуре и затем постепенное отверждение при второй, более высокой температуре. Таким образом, когда вы заканчиваете впрыск, вы нагреваете инструмент до температуры отверждения, что создает большой тепловой поток во всей системе ». Однако, как и при испытании DSC, ключом к мониторингу отверждения с помощью датчиков теплового потока является измерение тепла, выделяемого во время полимеризации / отверждения, и отображение этих измерений в виде кривой зависимости теплового потока от температуры в системе формования и времени. «Итак, мы изобрели метод, который помогает нам вычесть базовую линию нагрева формы и передачу этого тепла к детали, чтобы можно было определить тепловой поток реакции смолы».
Таким образом, по словам Кара, даже несмотря на то, что условия обработки исходных тонких пластин были очень сложными, «мы все еще могли видеть тепловой поток от реакции смолы. Однако, производя также более толстые детали, мы смогли точно увидеть разницу в уровнях теплового потока в зависимости от толщины детали, и это подтвердило наш мониторинг отверждения в тонких деталях ». Обратите внимание, что приведенная выше кривая (также показанная на начальной фотографии) была получена с использованием смолы RTM 6 на пластине толщиной 3,2 мм.
Однако результаты определения фронта потока смолы были более проблематичными. «Для датчика около выхода мы могли очень хорошо видеть поток, но не для датчика около центра, где смола прибыла очень поздно», - говорит Кара. «Для обнаружения фронта потока с помощью датчиков теплового потока требуется, чтобы поток смолы произвел изменение местного теплового поля. Это происходит, когда температура смолы отличается от температуры преформы ». Он отмечает, что ΔT более 0,1 ° C достаточно для обнаружения. «Однако при испытаниях тонких пластин из углепластика температура в форме была очень равномерной, и смола поступала очень медленно. Таким образом, теплового контраста было недостаточно для обнаружения поступления смолы по сравнению с тепловым шумом в системе в целом. Однако поступление смолы на выходе происходило быстрее из-за бегунов [зазоров между преформой и краем формы, см. «Изготовление деталей сложной геометрии RAPM»], что помогает создать больший тепловой контраст, который было легче обнаружить и контролировать. ”
Кара предполагает, что этот мониторинг фронта потока смолы можно улучшить с помощью новых активных датчиков, разработанных TFX, которые используют встроенную в датчик возможность нагрева. «Это позволяет датчикам обеспечивать тепловой контраст, необходимый в деталях и процессах, где это по своей природе сложно», - поясняет он.
Расширение возможностей комплексного управления процессами
«Мы довольны проделанной работой, - говорит Торрес, - но это только первый шаг. Цель состоит в том, чтобы использовать эти датчики теплового потока для управления обработкой композитов в производственных условиях ». Это возможно, говорит Кара, путем автоматической отправки сигнала от сенсорной системы к инжекционному оборудованию в зависимости от поступления смолы и в пресс на основе нулевого наклона кривой отверждения. Торрес добавляет, что TME имеет системы управления технологическим процессом для литьевой машины и пресса RTM, которые регулируют температуру и давление. «Следующим шагом, - говорит он, - будет интеграция датчиков TFX в эти системы управления и управление всем процессом с портативного компьютера». Кара отмечает, что датчики TFX и сбор данных также работают с датчиками давления (например, Kistler, Winterthur, Швейцария), чтобы помочь в этом общем управлении процессом, и его компания разрабатывает датчик, который будет измерять тепловой поток, температуру и давление в одном интегрированном устройстве.
Но насколько доступен этот контроль процесса? Кара говорит, что первоначальные инвестиции в систему мониторинга в размере 10–30 000 долларов, как правило, окупаются на этапе разработки, сокращая количество проб и ошибок за счет улучшения понимания процессов и деталей. «Затем система продолжает обеспечивать экономию во время производства, сокращая время цикла, обеспечивая повторяемость и обеспечивая раннее обнаружение отклонений или несоответствий».
В GKN Fokker Вергувен считает, что после того, как будет доказана способность сократить время цикла и снизить стоимость, «тогда можно будет представить композиты не только в типах компонентов шасси, продемонстрированных в проектах INNOTOOL 4.0 и HECOLAG, но и во всех типах компонентов. части. Это откроет нам пространство для дизайна и позволит нам еще больше расширить границы легких шасси ». Бессон видит еще более широкое применение:«Этот тип управления процессом можно разработать для всех видов пресс-форм и композитных деталей».
Смола
- Типы датчиков и их принципиальные схемы
- AMS, чтобы осветить Sensors Expo 2019 инновационными демонстрациями
- Отображение расхода температуры в доме с помощью дешевых датчиков
- Измерение температуры с помощью однопроводного датчика DS18B20 и Raspberry Pi
- Управление эффектом с помощью реальных датчиков
- Считывание аналоговых датчиков с одним контактом GPIO
- Считывание аналоговых датчиков с помощью Raspberry Pi и Zabbix Supervisor
- Контроллер полива Win10 IOT с датчиками влажности
- Улучшение мониторинга загрязнения воздуха с помощью датчиков Интернета вещей
- Упрощение изготовления датчиков с помощью клеевых составов