Настройка ультразвуковых датчиков для оптимизации и контроля процесса композитов
Этот блог является продолжением моего отчета о проекте CosiMo («композиты для устойчивой мобильности»). Этот проект был запущен в 2018 году компанией Faurecia Clean Mobility (Нантер, Франция), чтобы продемонстрировать «умное производство» композитной крышки аккумуляторного отсека. Пробная деталь длиной 1100 миллиметров и шириной 530 миллиметров была оснащена нетканым стекловолокном и однонаправленным усилением из углеродного волокна, а также вставками из металла и пенопласта, сложной геометрии, включая различные радиусы и толщину от 2,5 до 10 миллиметров. Деталь была отформована с использованием литьевого формования из термопластической смолы (T-RTM), при котором мономер капролактама был впрыснут, а затем полимеризован на месте во время цикла нагретого прессования с образованием композита полиамида 6 (PA6). Основная цель проекта заключалась в исследовании полностью автоматизированного процесса с использованием замкнутого контура управления процессом на основе датчиков.
В этом блоге более подробно рассматривается сеть из 74 датчиков, используемых в задаче CosiMo, и в частности ультразвуковые датчики, разработанные Аугсбургским университетом (UNA, Аугсбург, Германия), и то, как данные со всех датчиков использовались для построения цифровая модель процесса (цифровой двойник).
Основываясь на успехе CosiMo и необходимости в центре разработки для разработки производства на основе датчиков и искусственного интеллекта, UNA сформировала Аугсбургскую производственную сеть искусственного интеллекта в сотрудничестве с партнером проекта CosiMo, Немецким аэрокосмическим центром (DLR), Центром легких производственных технологий ( ZLP, Аугсбург) и Института литейного производства, композитов и обработки им. Фраунгофера (Fraunhofer IGCV). «Мы создаем новое предприятие площадью 5000 квадратных метров, которым будем совместно управлять», - говорит д-р Маркус Саузе, профессор UNA и директор Аугсбургской производственной сети AI. «У нас будут автоматизированные производственные участки, многие из которых будут сосредоточены на технологиях композитов, что позволит нам продемонстрировать, на что способен ИИ».
Сенсорная сеть CosiMo
Для проекта CosiMo 74 датчика были интегрированы в стальную оснастку RTM, предоставленную Christian Karl Siebenwurst GmbH &Co. KG (Дитфурт, Германия) для формования крышки аккумуляторного отсека T-RTM. Эта сеть, используемая для мониторинга параметров процесса во время закачки смолы, инфильтрации (мониторинг фронта потока) и полимеризации на месте, включала:
- 1 датчик вакуума
- 4 датчика давления / температуры от Kistler (Винтертур, Швейцария)
- 4 датчика температуры от Kistler
- 8 датчиков диэлектрического анализа (DEA) / температуры от Netzsch (Зельб, Германия)
- 57 ультразвуковых датчиков, разработанных Аугсбургским университетом.
В моем первоначальном отчете о CosiMo я обсуждал, как эта сенсорная сеть предназначена для исследований и разработок, а не для стандартного производства:
«Для промышленного серийного производства никто не станет устанавливать такое количество датчиков, и это не то, чего мы ожидаем», - говорит Ян Фабер, руководитель производственного проекта CosiMo в DLR ZLP. «Но для этого исследования эта большая сенсорная сеть была очень точной и помогли нам получить полное представление о процессе и материальное поведение . Мы могли видеть местные эффекты в процессе ответа в зависимости от толщины деталей или используемых материалов, например пенопласта ».
Итак, как была спроектирована эта сеть? «Большинство из них были ультразвуковыми датчиками, потому что у них самая низкая стоимость», - объясняет Фабер. «Мы использовали их в сетке на определенном расстоянии друг от друга. В некоторых местах мы вынули ультразвуковые датчики и вставили датчики температуры / давления Kistler или датчики DEA / температуры Netzsch. И для этих конкретных датчиков, как DEA, так и Kistler, мы просто попытались установить один рядом с литником, куда поступает смола, а затем еще один подальше. Таким образом, мы могли отслеживать места, куда поступает смола, уже некоторое время наблюдая за температурой формы ».
Зачем использовать разные типы датчиков? «Одна из исследовательских задач заключалась в том, чтобы сравнить сигналы и посмотреть, как работают разные датчики», - говорит Фабер. Это важно, потому что разные типы датчиков основаны на разных принципах измерения. Например, датчики DEA измеряют импеданс смолы по переменному току, который можно разделить на разные фракции, которые, в свою очередь, показывают разные эффекты в полимере. Kistler, тем временем, использует пьезорезистивные датчики, которые основаны на кремниевом мосту Уитстона - типе схемы, используемой для измерения динамического электрического сопротивления - подключенной к мембране, которая образует чувствительный конец, установленный в стенке формовочной полости. Мембрана расширяется под давлением, что изменяет электрическое сопротивление кремниевого моста Уитстона, который, в свою очередь, выдает электрический сигнал. «Мы также использовали новый датчик Kistler 4001a, который измеряет давление и температуру», - отмечает Фабер. «Было очень полезно иметь оба значения для выбора локальных точек в инструменте».
Ультразвуковые датчики UNA
Большинство датчиков, используемых в сети компонентов CosiMo, были ультразвуковыми датчиками, разработанными UNA. Саузе отмечает, что им отдали предпочтение не только из-за их низкой стоимости (<10 евро), но и из-за того, что они могут предоставить широкий спектр информации.
Ультразвуковые датчики использовались на протяжении десятилетий для проверки готовых композитных деталей, но также имеют долгую историю литья под давлением. Ультразвуковые датчики отправляют высокочастотную звуковую волну в среду и измеряют ее отражение (эхо-импульс) и / или передачу. В проекте CosiMo номинальная частота составляла 2000 килогерц. Из 57 установленных в пресс-форме ультразвуковых датчиков - на расстоянии 20 миллиметров от поверхности полости - 10 работали в режиме пропускания, остальные - в эхо-импульсном режиме. Ультразвуковые датчики измеряют скорость волны и уменьшение амплитуды (затухание); оба чувствительны к свойствам полимера. Кроме того, скорость волны можно рассчитать как функцию давления и температуры, но ультразвуковые данные должны быть откалиброваны для исследуемого полимера.
«Ультразвуковой датчик, который мы разработали, на самом деле не сильно отличается от того, что имеется в продаже», - говорит Саус. «Он основан на пьезоэлектрическом материале, который довольно чувствителен при преобразовании упругого движения в электрический сигнал. Но там, где типичные датчики могут работать при температурах до 150 ° C, нам приходилось выдерживать высокие температуры термопластического литья, превышающие 200 ° C, что было немного сложно для электроники датчика ».
«Нам также пришлось разработать механическую систему для правильной интеграции датчика в форму, - объясняет он, - для чего требовалась нагрузка пружины с хорошим уплотнением, чтобы обеспечить хорошее соединение. Датчик должен был соответствовать большому количеству требований; так что нам пришлось в значительной степени спроектировать его с нуля. Мы также тщательно продумали акустику всей системы ».
Полимеризация и мониторинг фронта потока
«Акустика сосредоточена на упругих свойствах материалов в форме, - продолжает Саузе. «По сути, жесткость жидкости не такая, как при полной полимеризации. Мы эффективно отслеживаем этот переход. Мы смотрим на акустическую интенсивность отражения волны на границе раздела от формы к полимерному материалу в каждом месте расположения датчика и, таким образом, непрерывно отслеживаем отверждение с течением времени ».
Механизм этого измерения объясняется Sause и Faber et. др., в документе конференции SAMPE Europe 2021 «Сенсорный мониторинг процесса полимеризации in-situ при производстве T-RTM с капролактамом». Отношение амплитуды эхо-сигнала акустического сигнала до и после пропитки преформы зависит от показателя отражения на границе раздела форма-деталь, R. Это приближается к постоянному значению по мере продвижения полимеризации. В идеале, когда полимеризация близится к завершению, изменение R будет нулевым.
Кроме того, по сигналу акустической передачи можно определить время прохождения ультразвуковых волн через пропитанную преформу. Это полезно, поскольку скорость звука через преформу зависит от степени полимеризации. Для экспериментов, завершенных во время публикации доклада SAMPE Europe 2021, время от полного смачивания преформы в месте расположения датчика до завершения полимеризации составляло 240 секунд.
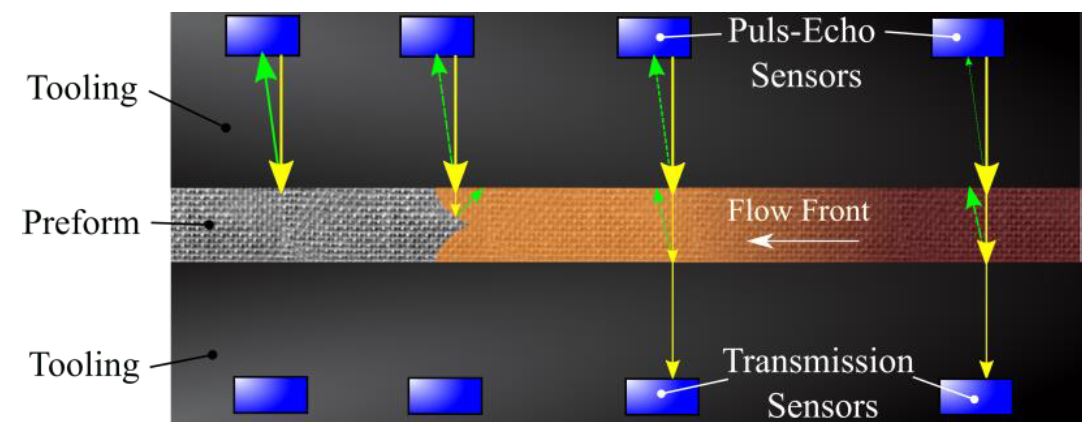
«Мы также можем контролировать поток во время закачки, - объясняет Сауз, - потому что информация об акустическом сигнале изменяется, когда фронт потока полимера проходит через датчик». Также подтверждено в документе SAMPE Europe 2021, акустический сигнал резко упал с исходного нормализованного значения 1 до 0,85-0,9 по прибытии фронта потока капролактама для выбранного датчика через 15 секунд после начала впрыска.
Создание цифрового двойника процесса
Саус говорит, что разработка ультразвукового датчика была на самом деле очень небольшой частью того, что UNA сделала в проекте CosiMo, «и даже не самой захватывающей частью». Он отмечает, что настоящее достижение заключалось в анализе данных и разработке цифровой модели процесса, позволяющей осуществлять управление с обратной связью во время производства деталей.
«Мы пытаемся предоставить информацию о том, что на самом деле происходит в форме», - добавляет он. «У нас есть установленные маршруты, позволяющие более или менее адаптировать процесс к температуре и давлению, но сейчас мы используем информацию об акустическом сигнале, выполняя активную пульсацию в каждом месте расположения датчика. И это позволяет нам определять различные параметры, такие как форма фронта потока, время, за которое он достигает каждой части преформы, и степень полимеризации в каждом месте расположения датчика ».
«В идеале вы можете установить настройки, чтобы включить управление с обратной связью и регулировать во время процесса», - говорит Саус. «Сюда входят такие параметры, как давление впрыска, давление в пресс-форме и температура. Вы также можете использовать эту информацию для оптимизации своих материалов ».
Создание цифрового двойника было многоступенчатым и многосторонним. Все началось с одного из рабочих пакетов, назначенных DLR ZLP. «Мы создали моделирование на основе двухмерной пластины, где мы хотели смоделировать заполнение и полимеризацию с помощью программного обеспечения для моделирования PAM-RTM от ESI Group (Ренжи, Франция)», - говорит Фабер. «Мы получили данные о проницаемости преформ от партнеров проекта ITA (Институт текстильных технологий, RWTH Aachen, Германия) и SGL Carbon (Висбаден, Германия), а также реактивную модель реакции термопластичного полимера из Аугсбургского университета. Затем мы интегрировали все в моделирование и попытались увидеть, насколько близко мы можем реально приблизиться к реальным данным датчика ».
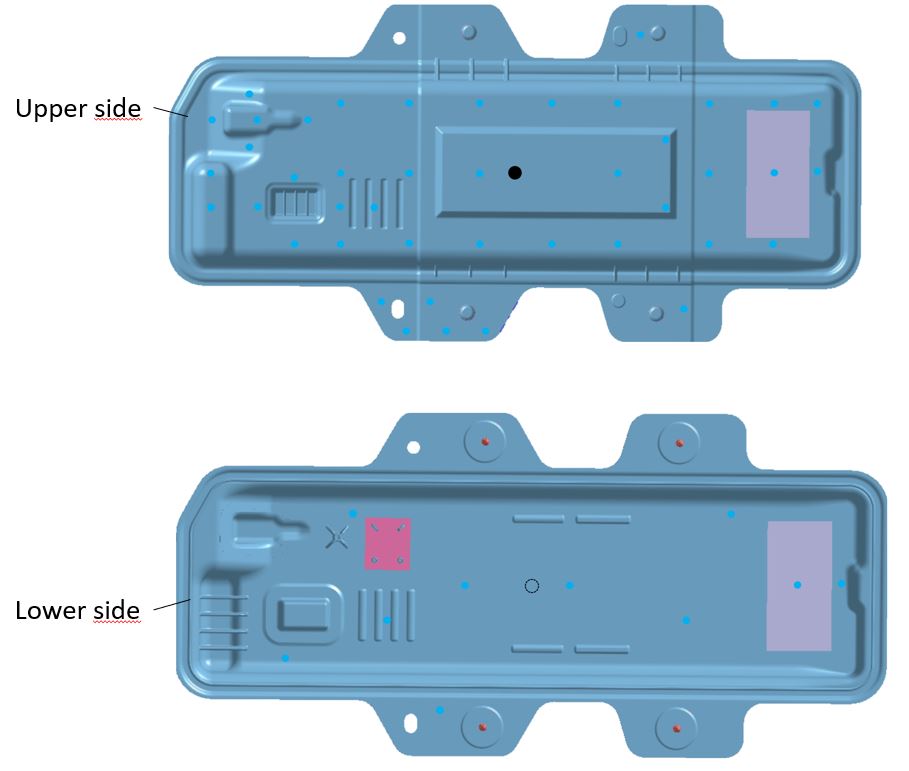
Голубые точки в верхней и нижней формах для демонстрационной части проекта CosiMo предоставили данные в определенных точках на протяжении всего процесса. Затем это было использовано в моделировании цифрового двойника для интерполяции между местоположениями датчиков и моделирования процесса по детали. Фото:проект CosiMo, DLR ZLP в Аугсбурге, Аугсбургский университет
«На основе двухмерной модели пластин мы обнаружили, что на самом деле мы очень близки в отношении наполнения», - продолжает Фабер. «Но у нас были некоторые температурные эффекты во время полимеризации, которые мы не могли описать в моделировании. Например, эта реакция полимеризации является экзотермической, и вы видите небольшое увеличение на датчиках температуры в реальных данных, но увеличение при моделировании было намного выше. Итак, это та область, в которой мы продолжали работать ».
Одна из вещей, которые команда хотела выяснить из моделирования, - это время, необходимое для завершения полимеризации. «Что нам действительно нужно, так это минимальное время, необходимое для формования», - отмечает Фабер. Эта информация была получена из имитационной модели и, как и все симуляции, полагалась на несколько типов датчиков и алгоритмов искусственного интеллекта. Например, Netzsch предоставил диэлектрические датчики, используемые для анализа диэлектрической проницаемости, а также помог с частями цифрового двойника процесса. «Они создали прогностические модели искусственного интеллекта, чтобы исследовать механизмы внутри закачки и предсказать, когда полимеризация должна быть завершена и каково будет состояние полимеризации», - говорит Фабер.
(Обратите внимание, Netzsch объединила свои компетенции в области определения характеристик материалов, кинетического моделирования и сенсорных технологий, чтобы создать новые предложения в области искусственного интеллекта и облачных решений. Этот тип интегрированного решения был успешно продемонстрирован в CosiMo, чтобы обеспечить оценку в реальном времени степени полимеризации и будет продаваться под торговой маркой sensXPERT.)
На основе полной сети датчиков и моделирования было установлено, что 96% было максимальной достигнутой полимеризацией, и для этого потребовалось 4,5 минуты. «Так что это намного быстрее, чем процессы инфузии, но намного медленнее, чем, например, высокоскоростная инъекция с использованием термореактивных материалов».
«Данные датчика соответствуют модели цифрового двойника», - говорит Саус. «Идея заключалась в том, чтобы модель работала одновременно с процессом, который численно стабилизируется данными датчиков. Синие точки представляют собой грубую сетку ультразвуковых датчиков, и затем мы смогли интерполировать между этими точками. Например, мы смогли предоставить видео о том, как фронт потока в детали CosiMo развивается в зависимости от времени, на основе данных измерений с наших датчиков ».
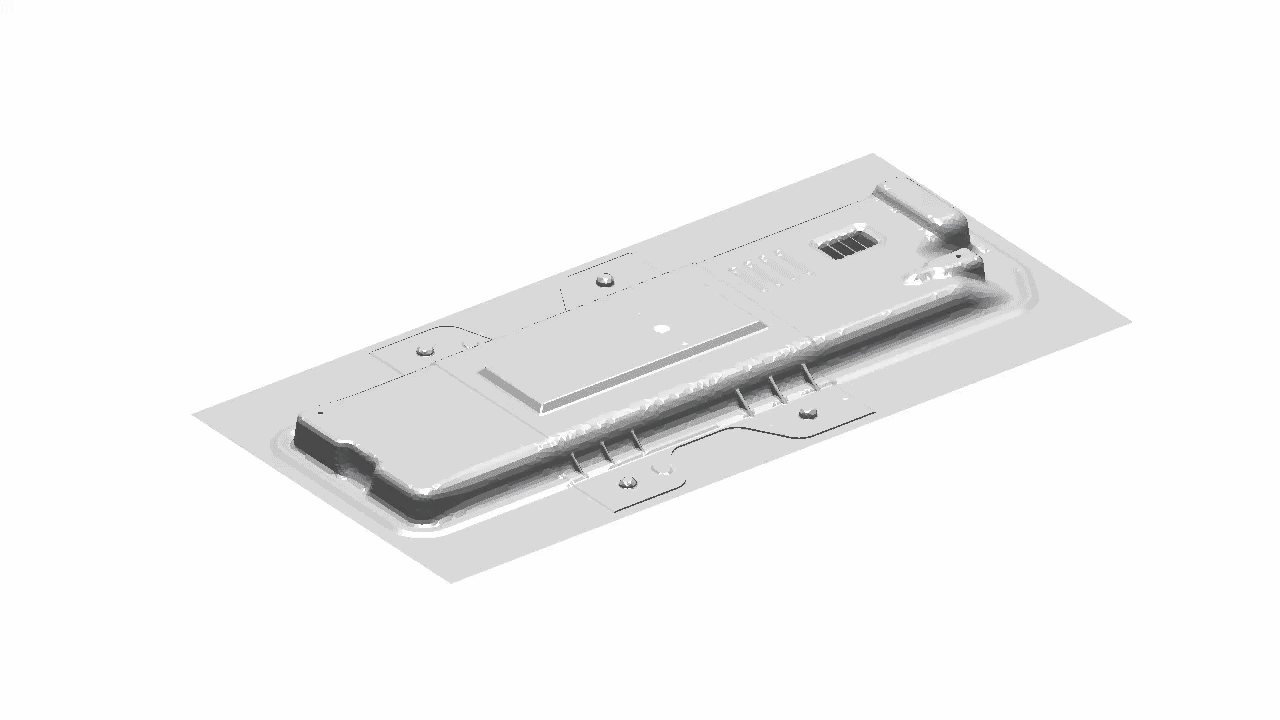
Как были подтверждены прогнозы скорости полимеризации? «У нас было несколько подходов», - говорит Саус. «Во-первых, аспирант здесь, в UNA, выполнял полный набор моделирования кинетики реакции материальной системы капролактам-PA6. Таким образом, он одновременно изучал инфракрасную спектроскопию вместе с реометрическими данными и данными датчиков диэлектрического анализа, чтобы предоставить очень точную модель материала для кинетики отверждения этой системы и подтвердить эту модель. Итак, мы использовали ту же модель для перекрестной проверки наших датчиков ».
Архитектура цифрового двойника
Архитектура работы цифрового двойника описана Stieber et. al. в техническом документе 2020 г. «На пути к мониторингу процессов в реальном времени и машинному обучению для производства композитных конструкций»:
Он состоит из трех частей:оборудования T-RTM, датчиков в пресс-форме и цифрового двойника. Эта структура и цифровой двойник, в частности, были разработаны с учетом следующих целей O1 - O4:
- O1:отслеживайте производственный процесс каждой композитной детали с помощью датчиков инструмента.
- O2:визуализируйте каждый производственный процесс в режиме реального времени, чтобы лучше понять процесс.
- O3. Обучите модели машинного обучения на смоделированных и реальных данных для прогнозирования результатов производственного процесса.
- O4. Используйте обученные модели машинного обучения, чтобы сократить производственный брак.
Затем датчики передают данные в пограничную аналитику цифрового двойника, которая затем может использоваться для прогнозирования будущей динамики фронта потока, определения объемного содержания волокна в каждой текстильной преформе, прогнозирования сухих пятен и обнаружения аномалий, которые могут уменьшить количество бракованных деталей. P>
Оборудование T-RTM состоит из двух стандартных компонентов:горячего пресса Wickert (Ландау-ин-дер-Пфальц, Германия) мощностью 440 килоньютон и узла впрыска T-RTM от KrausMaffei (Мюнхен, Германия). Обе эти машины, а также вся сенсорная сеть подключены к ПЛК (программируемому логическому контроллеру), который отвечает за управление всем производственным процессом.
Поскольку сенсорам требуется предварительная обработка в реальном времени для преобразования необработанных данных в информацию более высокого уровня о фронте потока или отверждении смолы, предварительно обработанные данные записываются непосредственно на краю с помощью устройства сбора данных ibaPDA от iba AG ( Фюрт, Германия). Таким образом, данные датчика записываются и объединяются с согласованной меткой времени, связанной с данными процесса и информацией о части с данными датчика для объективов O1 и O2.
Для автоматической оптимизации производственного процесса сохраненные данные используются для обучения моделей машинного обучения (ML) достижению цели O3. Эти модели отвечают, например, за реконструкцию фронта потока смолы из сенсорной сети, за прогнозирование движения фронта потока и - в идеале - за адаптацию параметров процесса для оптимизации результата либо во время выполнения процесса, либо для последующих прогонов. . Поскольку реальных данных обычно недостаточно для обучения надежных моделей, команда цифровых двойников использовала имитационные прогоны PAM-RTM для дополнения измеренных данных. После предварительного обучения с использованием смоделированных данных цифровой двойник был настроен на реальные данные. Эта стратегия известна как трансферное обучение и успешно применяется в приложениях для компьютерного зрения и обработки естественного языка. Расширенная аналитика, возможная с помощью машинного обучения, обеспечивает расширенные возможности прогнозирования и визуализации процессов, а также управление с обратной связью.
Интеграция датчиков для производства промышленных композитов
Итак, как производители композитных деталей применяют эту технологию для разработки управления с обратной связью в своих производственных процессах? Сауз считает, что имеет смысл использовать несколько типов датчиков для перекрестной проверки потока и мониторинга отверждения / полимеризации и для предоставления дополнительной информации. Затем нужно определить размещение датчика, в том числе, какие типы размещаются в каждом месте. «Например, - отмечает он, - вам нужны датчики давления и температуры не везде, а только там, где вам нужны эти ключевые точки данных, такие как проникновение смолы, точки сложной геометрии и т. Д.»
Сколько датчиков? «Для CosiMo мы использовали 74 датчика, но для полуметровой части вы бы использовали меньше, возможно, 35-40, в зависимости от вашей геометрии и ключевых точек интереса», - говорит Саус. «Это также зависит от производственного процесса. Например, в аэрокосмической отрасли есть процессы, которые используются десятилетиями и хорошо зарекомендовали себя. Для них вам может не понадобиться очень много датчиков, и их можно будет интегрировать без особых усилий в начале. Но другие процессы более неизвестны и потребуют дополнительной работы заранее. Что касается CosiMo, мы рассматривали возможность использования T-RTM с полимеризацией на месте до PA6, и это не было так хорошо задокументировано, как, например, RTM с эпоксидной смолой ».
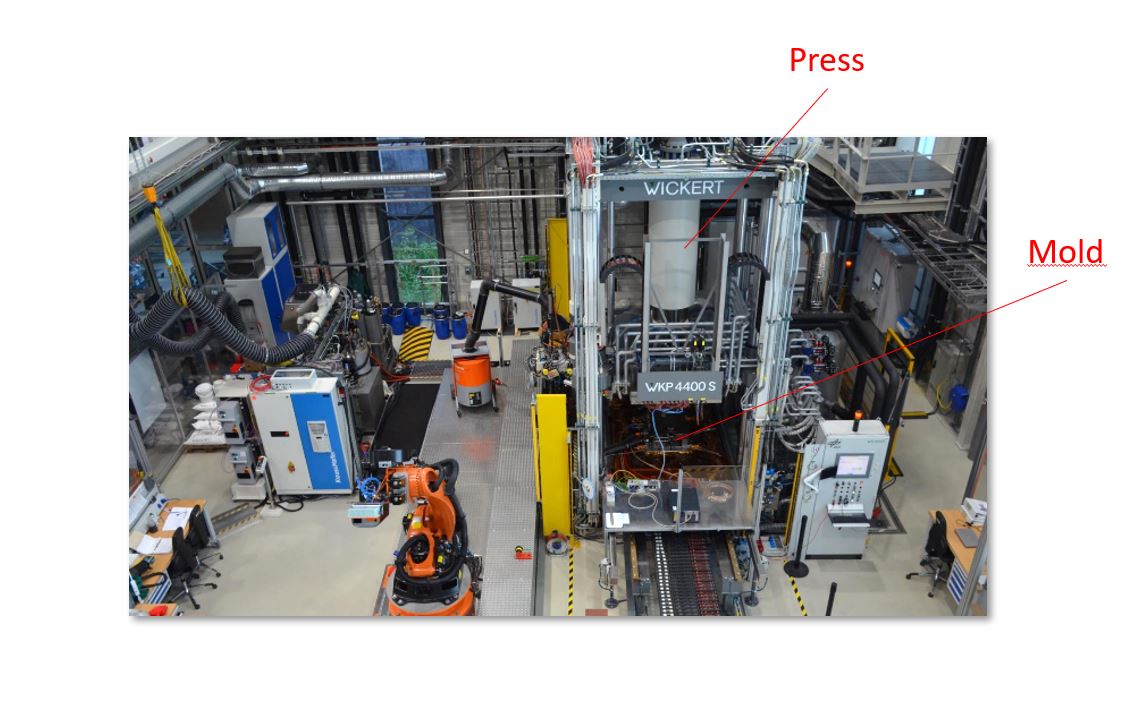
Производственное оборудование в рамках проекта CosiMo включало пресс Wickert 440 кН и литьевую машину KraussMaffei. Фото предоставлено для этой серии:проект CosiMo, DLR ZLP в Аугсбурге, Аугсбургский университет
Насколько затратно по времени создание цифровой модели? И всегда ли это требуется для достижения управления с обратной связью? «Опять же, это зависит от вашего процесса и того, какого уровня вы хотите достичь», - говорит Саус. «Во-первых, наличие интегрированной информации датчика позволяет вам визуализировать, что происходит внутри вашего черного ящика обработки, и какие параметры использовать.
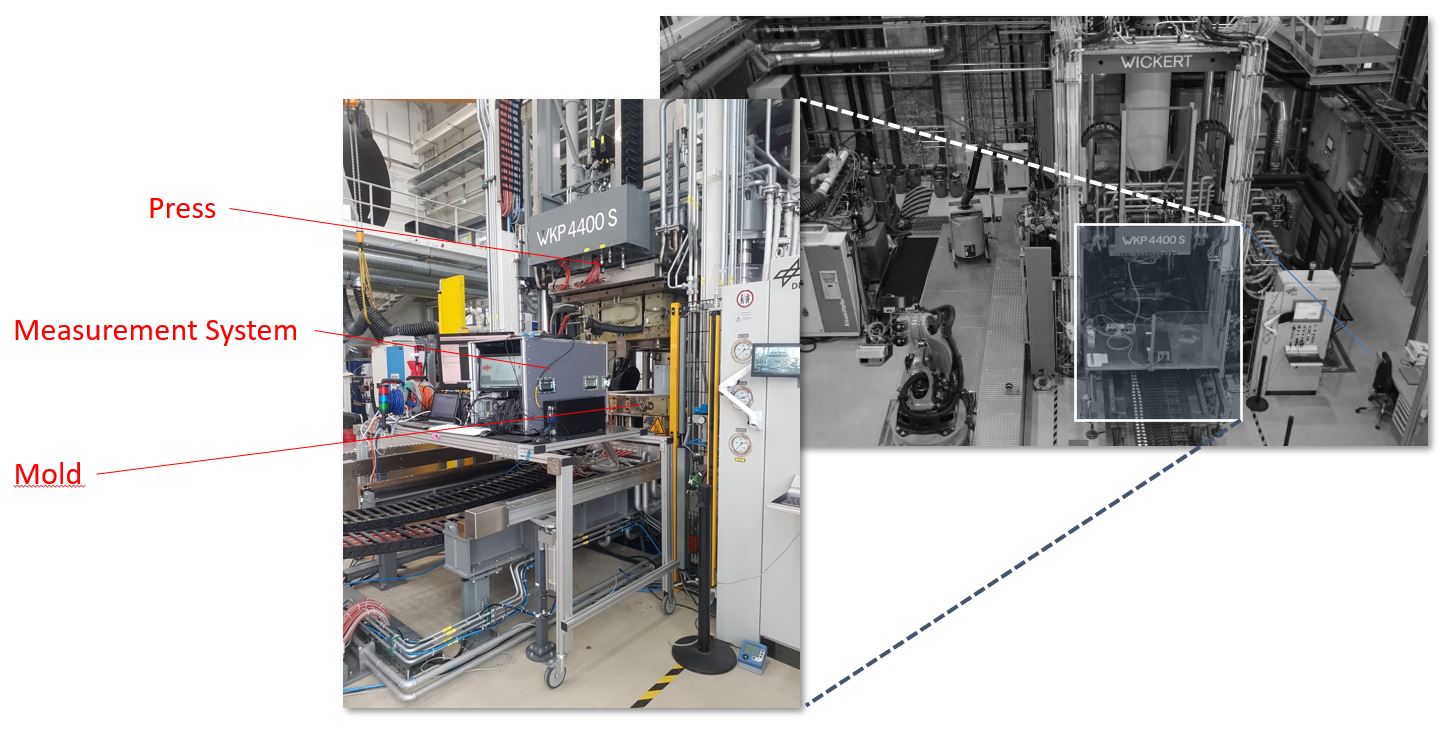
Система управления с обратной связью, разработанная в CosiMo, также включает встроенные датчики и систему сбора данных (система измерения, показанная здесь) от iba AG.
После достижения этой первой цели остается еще несколько шагов для достижения управления процессом с обратной связью. На полпути, возможно, будет визуализация, и вы можете нажать кнопку остановки самостоятельно, чтобы адаптировать процесс и предотвратить брак. Так что это тоже начало. Затем вы можете разработать цифрового двойника, но для этого нужны обучающие данные. Итак, вы должны каким-то образом это предоставить, а это значит, что вы можете создать пару частей для использования в качестве входных данных. Но тогда вам также необходимо производить детали невысокого качества. Итак, это вопрос вашей готовности инвестировать в обучение методам машинного обучения ».
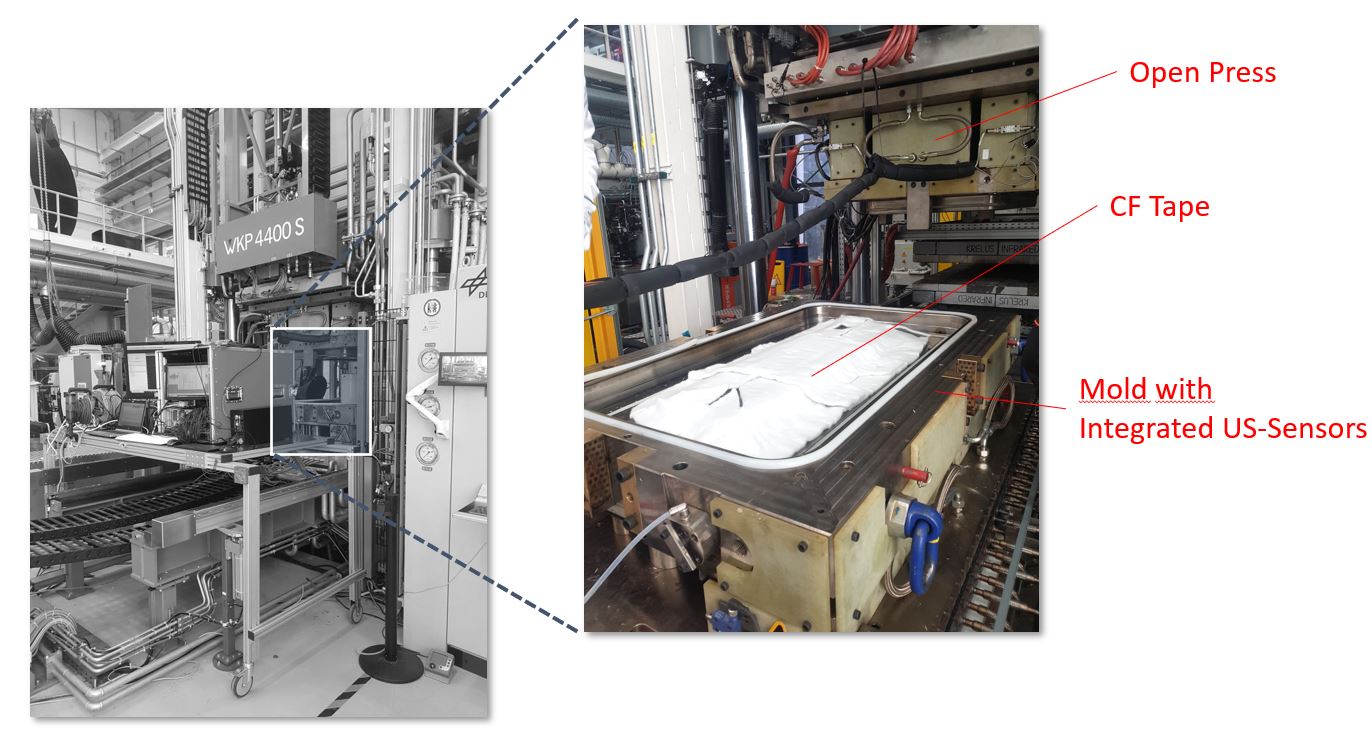
После обучения цифровой двойник может оптимизировать параметры процесса и обеспечивать управление процессом с обратной связью.
Тем не менее, Sause признает, что подход трансфертного обучения, принятый в CosiMo, «можно в определенной степени перенести на аналогичные геометрические формы или системы материалов и другие вариации, которые полностью не меняют ситуацию. Таким образом, вы можете создать свою базу данных с возможностью определения тенденций эффективности, используя уже полученные данные. Затем вы можете использовать это для других вопросов, которые могут у вас возникнуть ».
Итак, начало пути выглядит так:начать использовать датчики и создавать цифровые модели вместе с датчиками, чтобы вы могли понять свой процесс? «Совершенно верно», - говорит Саус. «И я могу заверить вас, что большая часть оборудования, используемого сегодня в производстве, все еще очень глупое. Многие машины не имеют датчиков, которые могут предоставить вам базы данных для обратной связи о том, что происходит. Итак, да, интеграция сенсорных систем была бы самым первым шагом. Но вам нужно делать систематический сбор данных, а также предоставить архитектуру хранения данных, чтобы иметь возможность что-то с данными . На самом деле вы видите много компаний, у которых есть встроенные датчики, но тогда они ничего не делают с данными ».
Производственная сеть AI
Отвечая на вышеперечисленные вопросы, Саус продолжал возвращаться к различным группам в UNA, а также к дочерним компаниям, которые могут обеспечить интеграцию датчиков и услуги цифрового двойника. С этой целью Аугсбургская производственная сеть AI была запущена в январе 2021 года UNA, DLR ZLP и Fraunhofer IGCV. «Структура сотрудничества основана на проектах, которые мы реализовали с DLR и Fraunhofer в прошлом», - говорит Саузе. «Мы берем план развития производства на основе ИИ от CosiMo и теперь расширяем его до очень широкого масштаба. Так, например, бюджет нашей работы в CosiMo составлял 10 миллионов евро, а для AI Production Network - 92 миллиона евро в качестве начального финансирования. Это даст нам возможность начать множество новых исследовательских проектов, таких как CosiMo, по использованию ИИ в производстве. И мы работаем не только с композитами, но мы уделяем им большое внимание ».
Использование ультразвуковых датчиков для улучшения обработки с ЧПУ - это один из проектов, уже начатых в 2021 году. «Вот-вот начнется проект по переработке композитов с керамической матрицей (CMC), - говорит Саус, - и у нас будет несколько проектов, между которыми будет тесная связь. аддитивное производство и повторное использование специально переработанных материалов, армированных волокном ».
Что касается ролей, которые будет играть каждая организация, Саузе поясняет, что здесь нет конкуренции, поскольку у каждого учреждения есть выделенный бюджет. «У всех нас есть своя доля, и поэтому мы можем сотрудничать, как и раньше. Кроме того, мы достаточно хорошо знаем друг друга, а также свои компетенции, сильные и слабые стороны. Работать вместе весело, потому что мы знаем, что можно, а что нельзя. К нам обращались многие компании, желающие работать с нами, и сейчас мы обсуждаем, как найти идеальное соответствие с нашей стороны компетенций ».
Что касается производственного объекта площадью 5 000 квадратных метров, «мы все будем управлять им вместе», - говорит Саус. «Мы планируем открыть к началу 2023 года и начать установку оборудования. И мы предоставим автоматизированные производственные настройки, которые объединяют отдельные ячейки. Многие из них будут сосредоточены на технологиях производства композитов. И мы сделаем это, чтобы продемонстрировать партнерам из отрасли, что ИИ может сделать в такой производственной среде. Мы также хотим, чтобы партнеры из отрасли приходили и размещали машины на нашем предприятии, чтобы мы могли вместе запускать проекты, чтобы увидеть, как связать и интегрировать новые решения для их сайтов ».
Смола
- Клапаны для сложного отключения и управления
- Датчики и системы для CBM
- Разработка процесса нанесения покрытия погружением и оптимизация производительности для электрохромных ус…
- OTOMcomposite разрабатывает программное обеспечение для производства Composites 4.0 с использованием лазерной укладки и…
- Перерабатываемые, ремонтируемые и перерабатываемые эпоксидные смолы для композитов
- TPAC и TPRC разрабатывают процесс переработки термопластичных композитов
- Советы по конфигурации и подключению корпусов панели управления
- Что такое ультразвуковая обработка? - Работа и процесс
- Соединения для управления:коммуникационные интерфейсы для датчиков положения и движения
- Сбор полевых данных для оптимизации процесса