Переформованные гибридные детали открывают новые рынки композитов
Сложность и сила. Компоненты, такие как B-кронштейн для контейнеров для хранения самолетов, обладают как высокой сложностью, так и требуют высокой прочности - комбинация, для которой особенно подходит гибридная технология формования. Источник, все изображения | Композиты TxV Aero
Часто на аэрокосмическом рынке OEM-производитель готов платить больше за композитный компонент, зная, что инвестиции принесут дивиденды в виде экономии топлива за счет легкого веса компонента, более длительного срока службы из-за меньшего износа или других сокращений эксплуатационных расходов. и эксплуатационные расходы. Такое представление о «жизненном цикле продукта» открыло для композитов множество рынков и приложений. Более необычным является композитный компонент, стоимость приобретения которого меньше, чем у металлического варианта. Но это меняется. Некоторые новые автоматизированные процессы изготовления композитов начинают склонять чашу весов в пользу композитов, и среди них - гибридный процесс повторного формования, разработанный TxV Aero Composites (Бристоль, Род-Айленд, США).
Совместное предприятие Tri-Mack Plastics Manufacturing (Бристоль, Род-Айленд, США) и Victrex (Thornton Cleveleys, Великобритания), TxV довело свою гибридную технологию формования до состояния коммерческого производства. Компания заключила партнерские отношения с SFS intec Aircraft Components (Althengstett, Германия) с целью модернизации и коммерческого производства кронштейна багажного отсека для самолета, ранее сделанного из алюминия аэрокосмического качества. Сама по себе история успеха, кронштейн также демонстрирует потенциал гибридной формовки и однонаправленной ленты VICTREX AE 250 из углеродного волокна / полиарилэфиркетона (PAEK) для существенной экономии веса и затрат во многих аэрокосмических приложениях - преимущества, достигаемые за счет замены процесса субтрактивной обработки металла на композитный процесс, при котором материал добавляется, а не вычитается.
От вычитания к сложению
Машинисты и механические цеха, производящие металлические компоненты на станках с ЧПУ, прозвали себя «изготовителями стружки» по той очевидной причине, что в их процессах из металлических заготовок вырезается ненужный материал для изготовления компонентов, образуя металлическую стружку. Эти стружки представляют собой дорогостоящий аспект обработки металла, независимо от того, утилизируются ли они, отправляются на переработку или обрабатываются на месте. В случае кронштейна верхнего складского бункера SFS intec от 60 до 70% алюминия становится ломом на нескольких этапах фрезерования, необходимых для его обработки.
Такой высокий процент брака делает стоимость сырья для композитной версии кронштейна нетто-формы или почти чистой формы потенциально ниже, чем стоимость металлического материала. «Мы можем конкурировать с менее дорогим (за фунт) алюминием из-за стружки; если соотношение покупок и продаж составляет 8:1, большая часть закупаемого алюминия переходит в лом », - отмечает Джонатан Суркс, старший менеджер по работе с клиентами TxV. «Еще один фактор - время, затрачиваемое на измельчение каждого компонента. Мы можем изготавливать [составные] детали за минуты, а не часы ».
Помимо затрат на сырье, композитные версии компонентов, таких как кронштейн, обладающие сложной геометрией и требующие высокой несущей способности, были экономически нецелесообразны при использовании традиционно доступных производственных вариантов. С одной стороны, если бы компоненты были изготовлены из недорогого армированного рубленым волокном высокоскоростного процесса с низким уровнем соприкосновения, такого как литье под давлением, компонент не смог бы обеспечить достаточную несущую способность. С другой стороны, если бы он был изготовлен с более несущей, непрерывным армированием волокном с помощью низкоскоростного процесса с высокой степенью касания, обычно включающего некоторую ручную укладку, производство было бы слишком медленным и / или требовало бы производственных затрат, которые привели бы к конечный продукт слишком дорогой.
Из-за этих препятствий на пути к новым применениям композитов этого типа отрасль композитов в целом направила значительные ресурсы на разработку автоматизированных процессов, которые могут производить такие компоненты с достаточно высокой производительностью и с достаточной несущей способностью для удовлетворения потребностей и спецификаций клиентов в аэрокосмической отрасли. . Ориентируясь на коммерческое производство таких композитных компонентов, компания TxV была создана в 2017 году специально для ускорения коммерческого внедрения инновационных производственных процессов для композитных материалов на основе поликетонов в аэрокосмической промышленности.
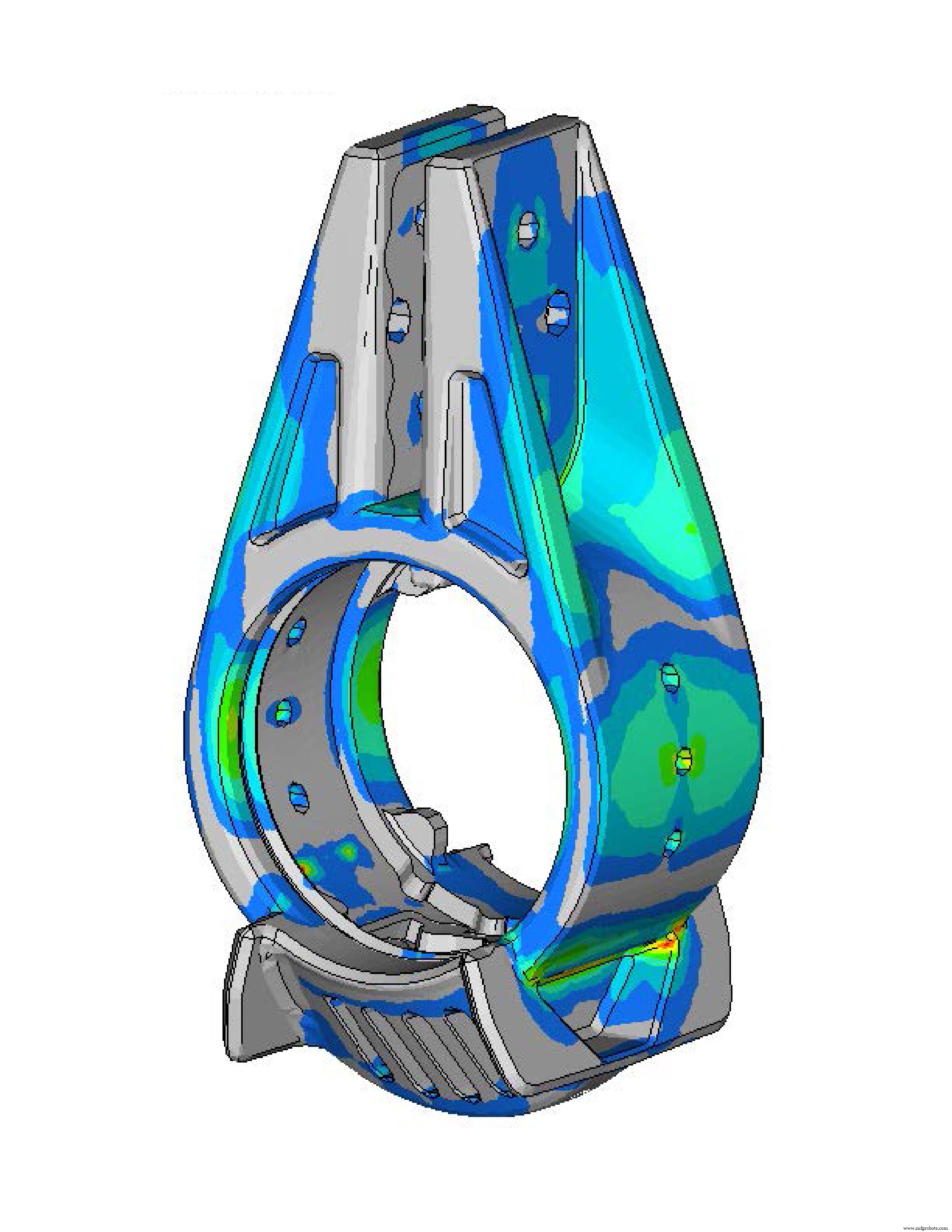
Виртуальное прототипирование. Используя патентованные данные, разработанные для характеристики взаимосвязи между ламинатом и формованием, TxV повторил укладку и ориентацию слоев без необходимости изготовления и тестирования физического прототипа. Итерации продолжаются до тех пор, пока видимые напряжения, показанные здесь, не будут находиться в пределах предоставленного диапазона нагрузок.
Гибридное решение TxV с переформовкой включает в себя два ключевых достижения в области производства композитных компонентов. Во-первых, он автоматизирует производство тех частей компонента, для которых требуется прочность или жесткость непрерывного армирования волокнами. Во-вторых, он увеличивает скорость литья под давлением для получения компонентов сложной геометрии. В частности, он производит специально подобранный ламинат для выдерживания нагрузок, который затем формуют для придания функциональности и создания окончательной геометрии детали. Гибридная технология, по словам Саши Костабеля, руководителя отдела инноваций в SFS intec Aircraft Components, «является хорошим вариантом для компонентов, которые должны выдерживать высокие уровни механических нагрузок и геометрических форм, требующих нескольких этапов обработки при использовании традиционной обработки».
По словам Суркса, сотрудничество с SFS intec было отличным выбором. «Как мировой лидер в области системного навесного оборудования, SFS всегда делает что-то действительно интересное. Они очень изобретательны и готовы инвестировать в новые технологии », - отмечает он. SFS intec также имеет прочные отношения со своими заказчиками самолетов, добавляет он, и они обладают способностью выполнять процессы аттестации, что является ключом к внедрению в аэрокосмической отрасли обновленного компонента.
Кронштейн бункера для хранения самолета, в частности, называемый «B-образным кронштейном», был выбран в качестве первого компонента крепления для модернизации композитных материалов, поскольку он представляет собой компоненты, которые сложно разработать и изготовить. После совместной разработки, концептуализации и проектирования деталей, а также моделирования производительности с помощью инструмента анализа конечных элементов (FEA) Altair (Трой, штат Мичиган, США), команда проекта повторила, начиная с первой статьи, для проверки, тестирования и подтверждения модели. Дизайн для производства был центральным при разработке композитного кронштейна, в котором используются производственные преимущества автоматизированной укладки ленты для элементов, армированных непрерывным волокном, и высокоскоростного литья под давлением для элементов, армированных рубленым волокном.
Строительные скобки
Одним из ключевых аспектов процесса гибридного формования методом перекрытия является использование различных полимеров одного и того же класса. PAEK служит в качестве матричной смолы для частей кронштейна из композиционного материала из непрерывных волокон, в то время как полиэфирэфиркетон (PEEK) используется в областях, отформованных поверх. VICTREX PAEK и PEEK обладают превосходной усталостной, химической и коррозионной стойкостью; отличная стойкость к дыму, пламени и токсичности; быстрая формуемость; и свариваемость. VICTREX AE 250, низкоплавкий ПАЭК (LM PAEK), обеспечивает температуру плавления 40 градусов Цельсия ниже, чем у PEEK. «Когда расплавленный ПЭЭК течет по поверхности композита LM PAEK, более низкая температура плавления обеспечивает прочное прикрепление», - объясняет Суркс.
Конкретным сырьем для кронштейна B является однонаправленная армированная углеродным волокном лента PAEK (58% углеродного волокна) VICTREX AE 250 шириной два дюйма; и короткий VICTREX PEEK 150CA30 с наполнителем из углеродного волокна (30% углеродного волокна). Эти материалы питают производственные ячейки гибридного формования, которые создают кронштейны с помощью следующего многоэтапного процесса.
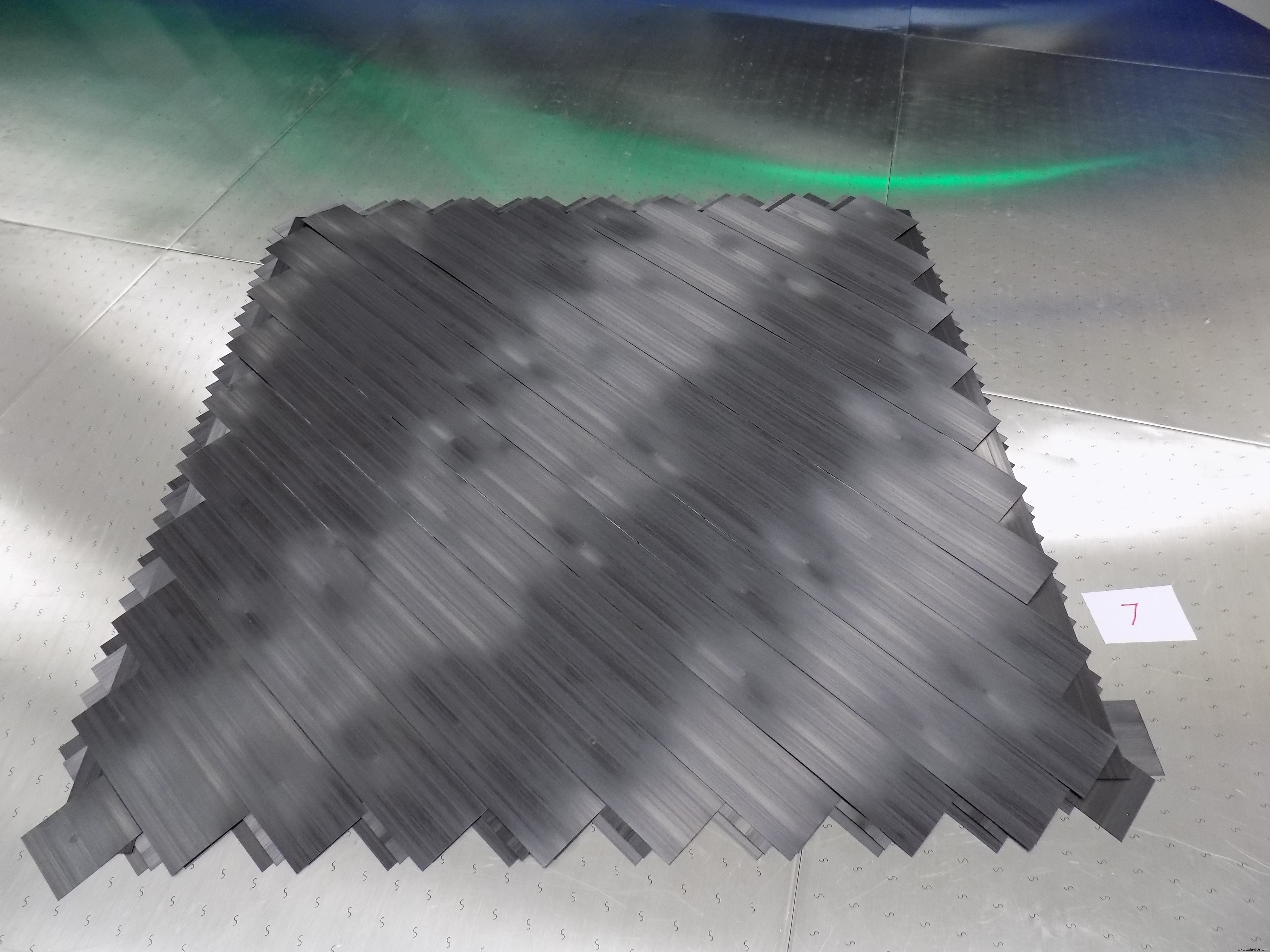
Шаг 1. Автоматическая система укладки ленты Dieffenbacher Fiberforge 2000 производит заготовки из ламината на заказ.
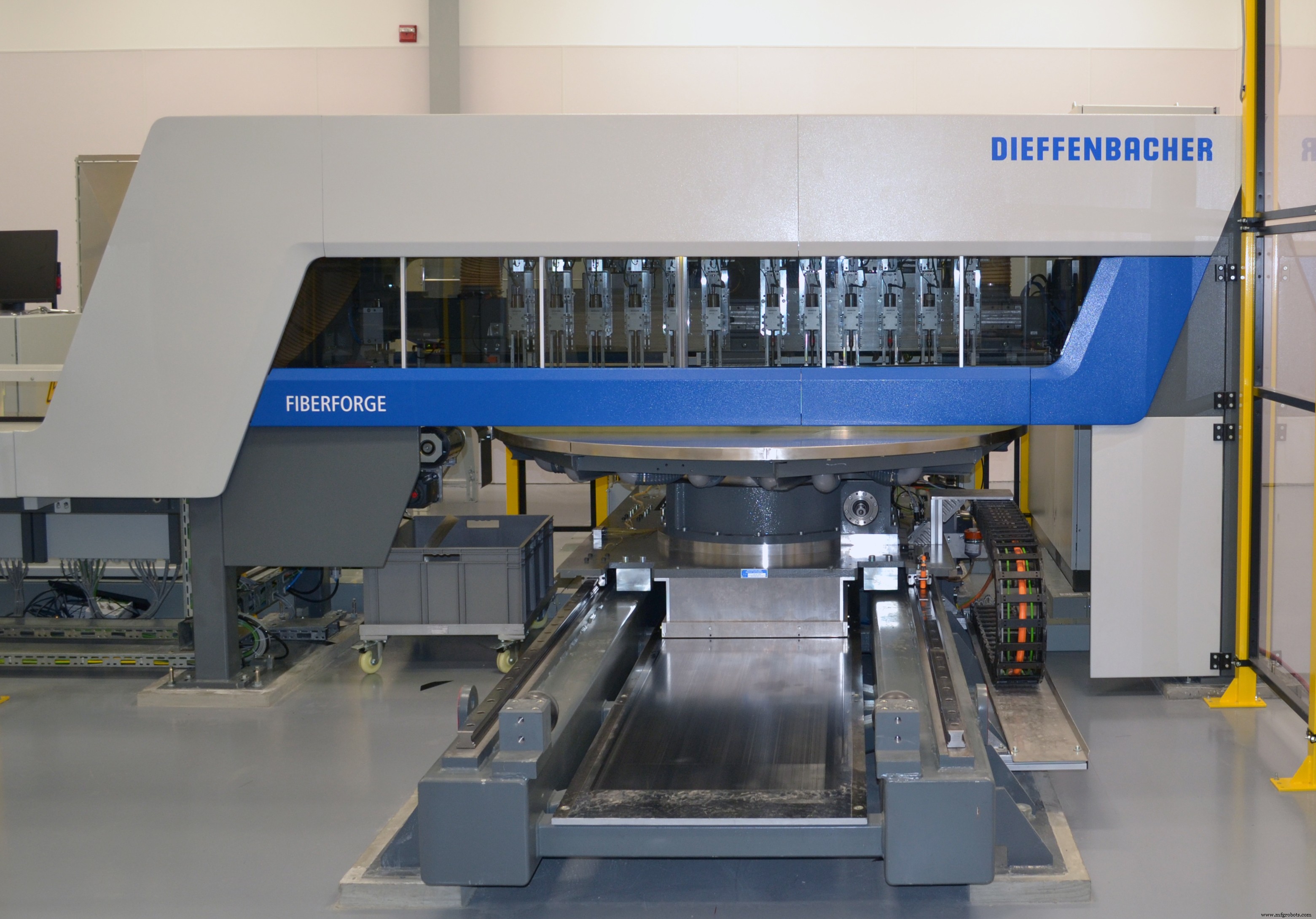
Сначала ленты из углеродного волокна / PAEK укладываются в специально подобранную заготовку с использованием системы укладки ленты Fiberforge 2000 фирмы Dieffenbacher (Эппинген, Германия). «Эта машина в настоящее время является одной из самых быстрых в мире систем для укладки ленты», - утверждает Суркс. Он оснащен роботами для загрузки и перезагрузки катушек с лентой, поэтому он может работать бесперебойно, сводя к минимуму время касания вручную. Layup разработан таким образом, чтобы минимизировать промежутки между лентами. Каждый слой специальной заготовки для кронштейна B проверяется перед укладкой следующего слоя. Процесс выполняется в зоне с контролем окружающей среды, чтобы свести к минимуму возможность попадания посторонних предметов и мусора (FOD).
Затем изготовленные по индивидуальному заказу заготовки объединяются в автоматизированную ячейку, которая требует минимального ручного труда для загрузки и разгрузки ламината. В ячейке согласованные подогреваемые плиты уплотняют панель, устраняя пустоты. Соответствующие холодные плиты затем охладите панель. Два набора плит, поддерживаемых при температуре, намного более эффективны, чем статический пресс с одним набором плит. «В результате резко сокращается время цикла, измеряемое в минутах по сравнению с часами», - говорит Суркс.
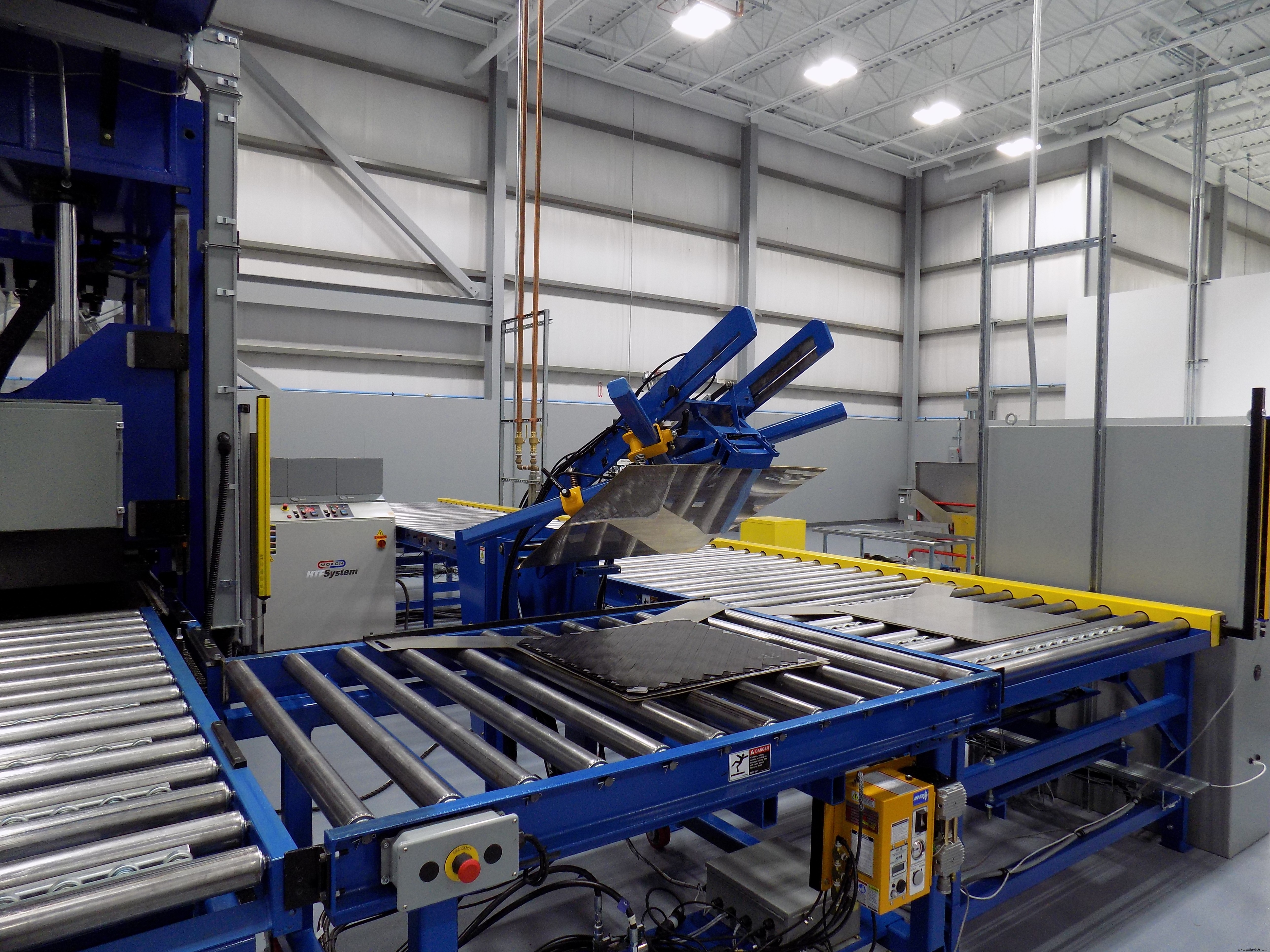
Шаг 2. Изготовленные по индивидуальному заказу заготовки консолидируются в автоматизированной ячейке консолидации, которая включает два набора плит, которые поддерживаются при определенной температуре (одна горячая, одна холодная), чтобы ускорить этот этап.
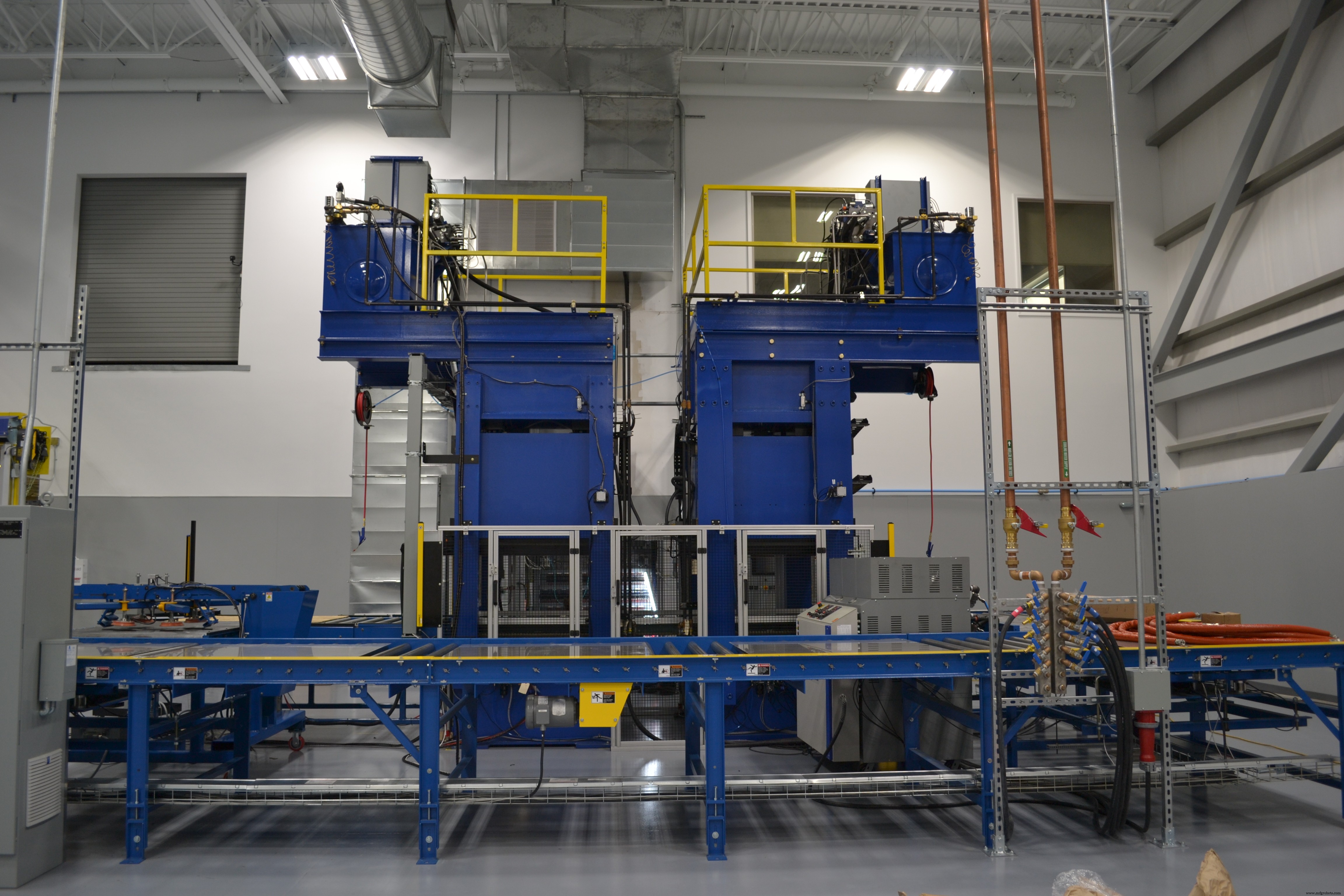
Преформы из консолидированного ламината затем обрабатываются в специальной производственной ячейке, чтобы сформировать основную форму кронштейна (шаг 3). Затем готовые вставки из углеродного волокна / ПАЭК вырезаются из формованных заготовок с помощью гидроабразивной машины Flow International (Кент, Вашингтон, США) (этап 4)
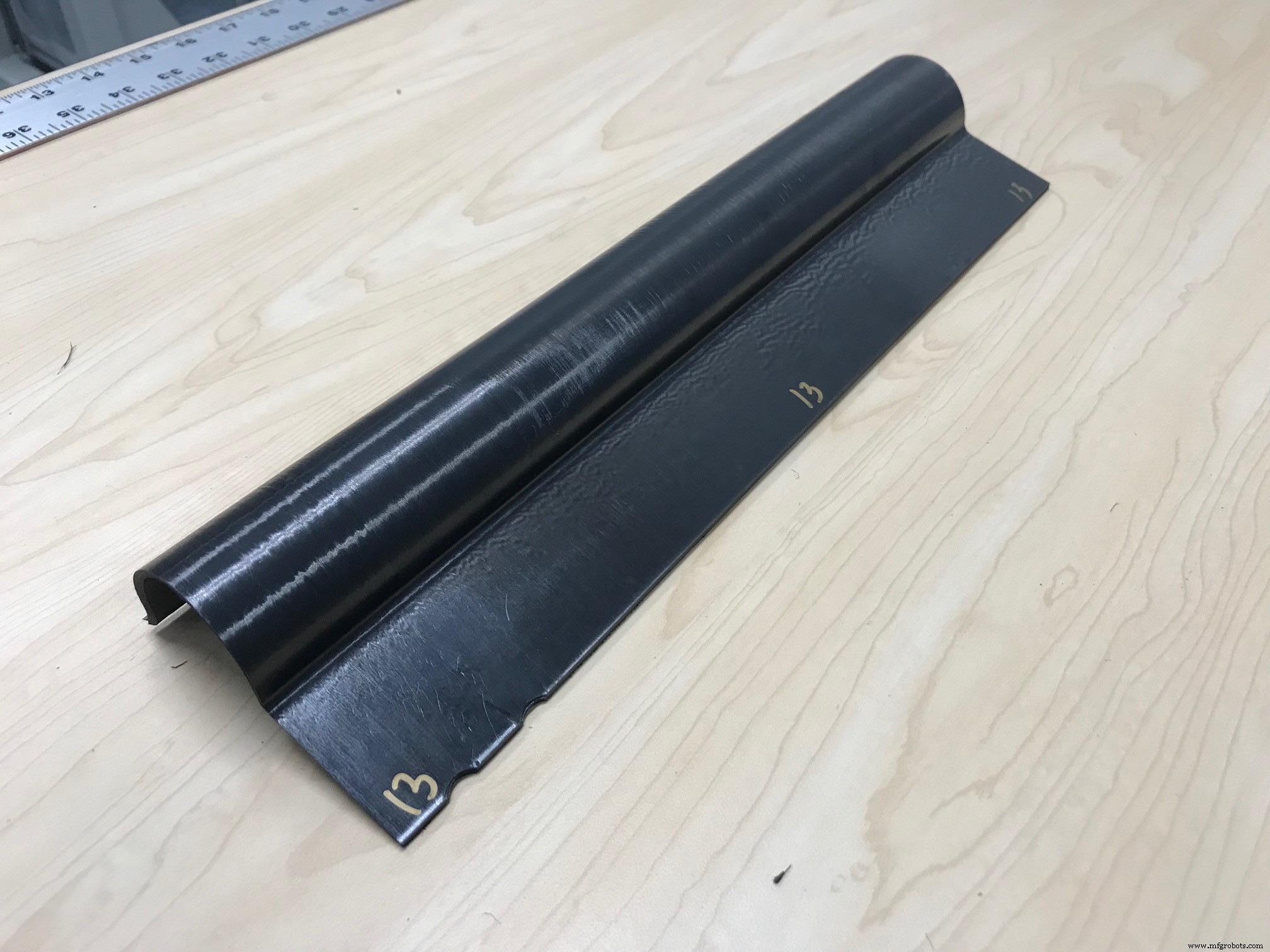
Шаг 3. Фирменная рабочая ячейка формирует основную форму кронштейна.
При определении размера специально подобранной заготовки Суркс отмечает, что для каждого проекта необходимо обдумывать компромисс. «Мы можем задать размер ламината так, чтобы можно было вырезать три или четыре прямоугольника из одной квадратной заготовки. Укладывая заготовку максимально большого размера, а затем разрезая ее на преформы, вы максимально увеличиваете соотношение закупок и продаж; но резка преформ требует больше времени для операций гидроабразивной резки ». В проекте кронштейна B каждый консолидированный ламинат разрезается на несколько преформ
Далее следует этап повторного формования, который выполняется на машине для высокотемпературного литья под давлением Engel (Швертберг, Австрия) (этап 5). Вставки помещаются в полость для литья под давлением, которая затем заполняется расплавленным PEEK. Вставки помещаются в полость для литья под давлением, заполненную расплавленным PEEK, который плавит верхний слой ламината VICTREX AE 250, создавая прочный компонент, связанный расплавом.
При необходимости компонент обрабатывается до окончательной формы. «Хотя наша цель - формование деталей, близких к чистым, - признает Суркс, - часто требуется некоторый минимальный уровень обработки постфактум, чтобы очистить геометрию процесса». Обработка может выполняться гидроабразивной или ЧПУ.
Новаторские результаты
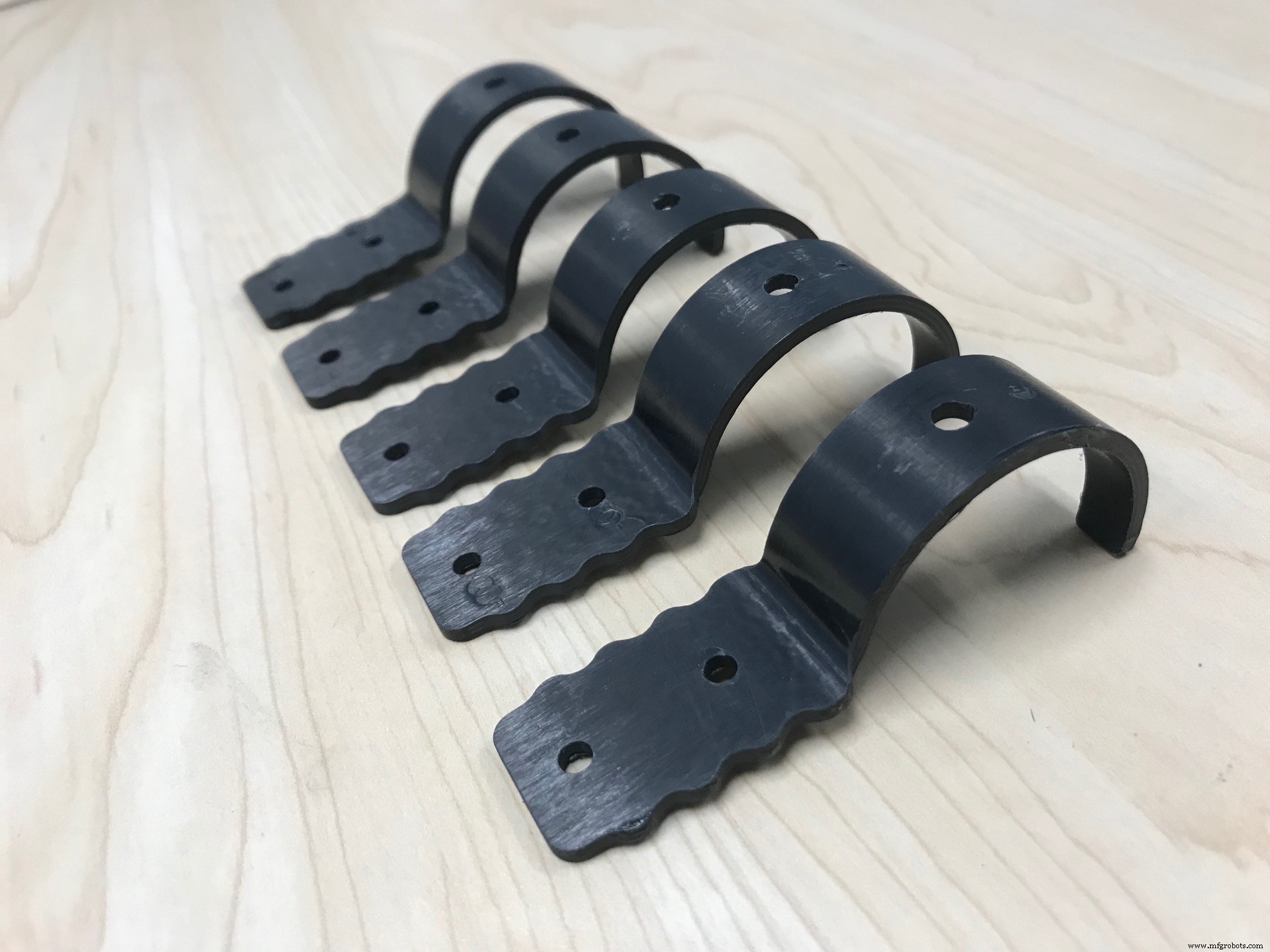
Шаг 4. Станок для гидроабразивной резки Flow International вырезает вставки из углеродного волокна / PAEK из сформированных заготовок. В каждом кронштейне используются две из этих вставок.
При производстве кронштейна SFS intec в процессе гибридного формования TxV время цикла составляет три минуты, а соотношение закупок и продаж составляет 1,06:1. «Это эффективное использование материалов и быстрый производственный процесс, которые позволяют нам производить детали из термопластичных композитов с добавленной стоимостью и позволяют снизить стоимость системы по сравнению с существующими металлическими конструкциями», - подчеркивает Суркс. «Фактически мы заменяем более дешевое сырье с высоким соотношением закупок и доходов и значительным временем обработки на высокотехнологичное решение для материалов». Результатом является снижение веса от 30 до 40% и снижение затрат от 20 до 30% при аналогичной замене, то есть заменяемой детали, которая соответствует тем же геометрическим и эксплуатационным характеристикам, что и существующий компонент. «В частности, снижение веса может достигать 60%, если нам предоставляется возможность полностью изменить конструкцию системы деталей», - отмечает он.
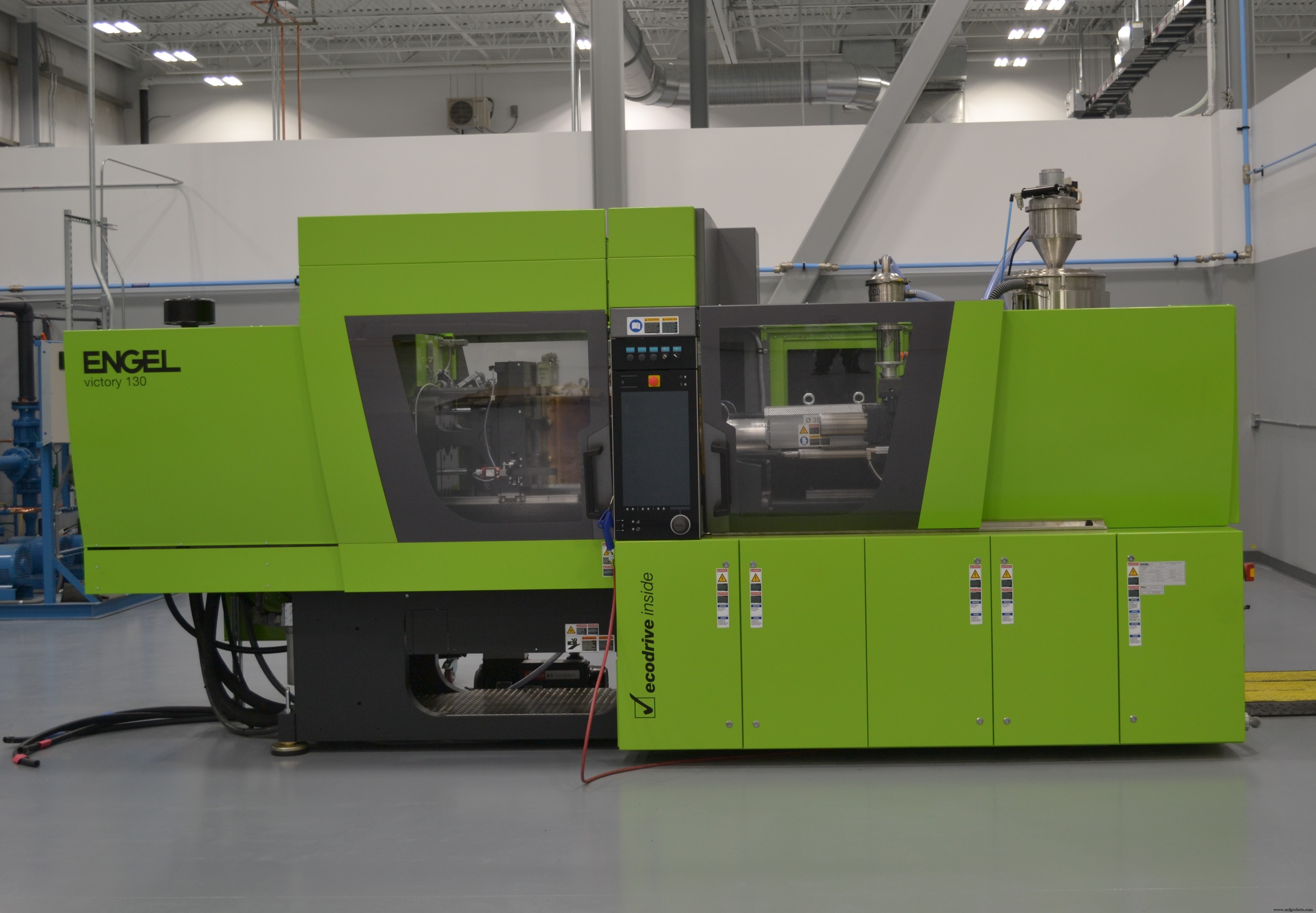
Шаг 5. Термопластавтомат Engel, оптимизированный для гибридного формования PEEK, дополняет композитную деталь путем формования вставок.
Кронштейн из углеродного волокна / PAEK / PEEK также имеет консолидированное количество деталей:TxV и SFS договорились о впрыскивании расширительного наконечника на нижнюю часть детали в той же операции, которая использовалась для функционализации и добавления других функций. Раньше передняя часть расширителя изготавливалась из PEEK и затем удерживалась на месте двумя заклепками. Таким образом, консолидация приводит как к сокращению количества деталей, так и к устранению этапа сборки.
Опыт двух компаний, запустивших TxV, несомненно, позволил добиться успеха в гибридном формовании. Суркс объясняет, что после разработки материалов и технологии обработки PAEK компания Victrex сначала изучила возможности совместно с существующими деловыми партнерами. «Однако компании, обладающие опытом литья под давлением, не имели опыта работы с композитами, армированными непрерывным волокном, и наоборот». Victrex и Tri-Mack сотрудничали в течение нескольких лет, прежде чем в 2017 году сформировали TxV и построили на предприятии специализированный центр передового опыта из поликетоновых композитов, который отличается высокой степенью автоматизации и предназначен для высокопроизводительного серийного производства.
На просьбу сравнить процесс и результаты TxV с традиционным подходом к производству Суркс отмечает, что скоба B не поддается стандартным подходам к производству композитов. «Это было бы очень сложно без механической обработки кронштейна из композитной заготовки, что было бы слишком дорого», - говорит он.
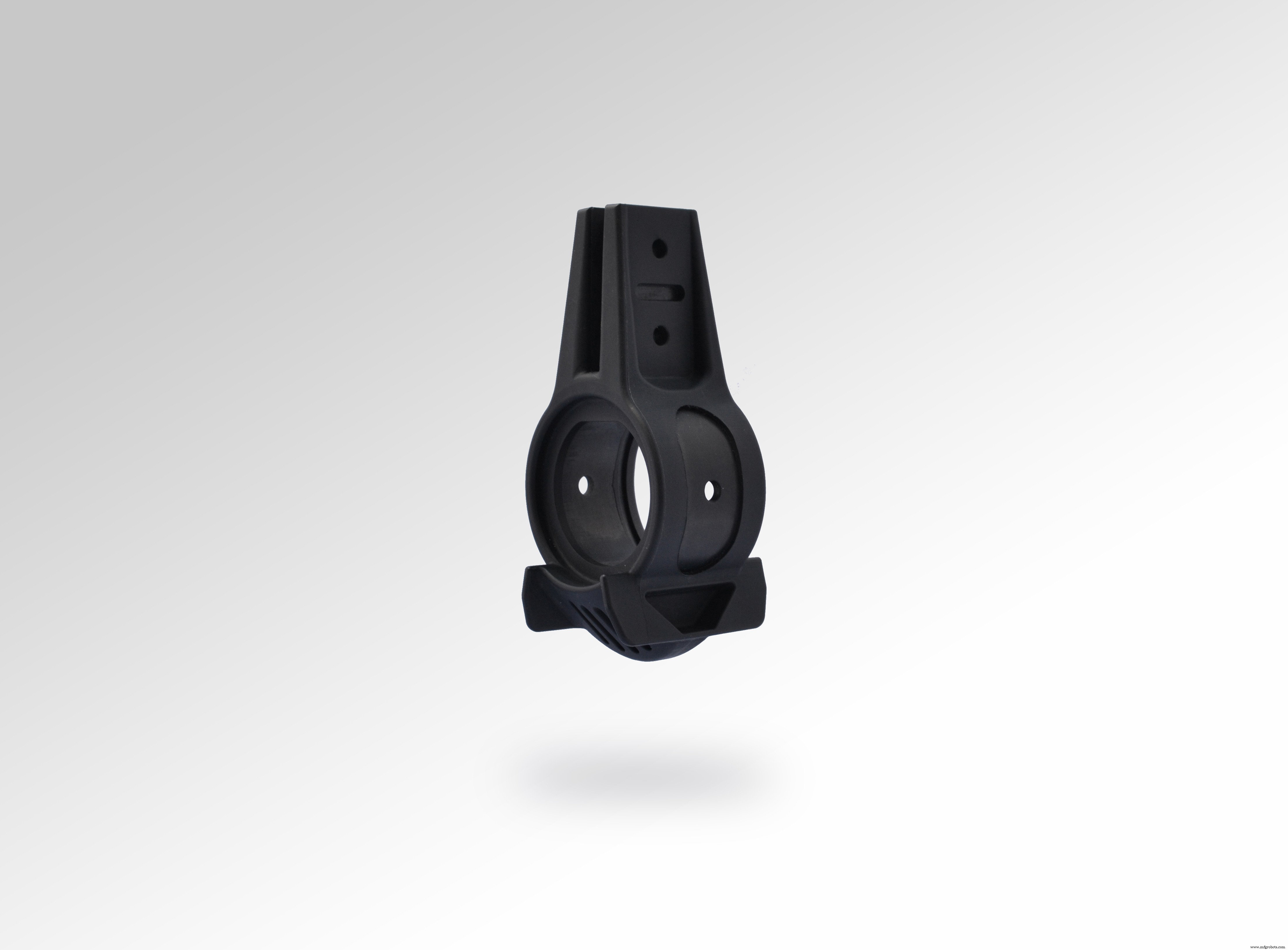
Шаг 6. Последний кронштейн B изготавливается с продолжительностью цикла три минуты, соотношением закупок и вылетов 1,06:1 и экономией веса от 30 до 40%.
Квалифицируйтесь, затем летите
Воспользовавшись возможностью SFS intec провести аттестацию, две компании приступили к сертификации через «точечный дизайн», что означает, что только эта конкретная геометрия детали получает одобрение полета. Детали были изготовлены и прошли испытания, указанные в квалификационном документе. «Учитывая, что эта деталь представляет собой кронштейн верхнего бункера, эксплуатационные нагрузки достигаются довольно легко», - отмечает Суркс. «Однако требования к характеристикам выходят за рамки этих типичных нагрузок и должны охватывать некоторые экстремальные маневры при взлете и посадке». Как CW передается в печать, квалификационный пакет отправлен и ожидает окончательного утверждения хранителем спецификации. TxV и SFS intec ожидают, что эта деталь будет запущена в начале 2020 года.
Как только B-скобка будет квалифицирована, TxV будет масштабироваться до объемов производства. В то время как компания использует существующую линию гибридного формования для производства этих кронштейнов, Суркс подчеркивает, что у компании есть двойной мандат - как производить детали с использованием этой технологии, так и поддерживать промышленных производителей, заинтересованных во внедрении этой технологии. Другими словами, производители композитов могут применять эту технологию производства на своих собственных предприятиях.
Композитные кронштейны, такие как продукт SFS intec, могут занять довольно большой рынок для таких компонентов. В коммерческих самолетах используются тысячи кронштейнов и системных приспособлений, что составляет значительную часть стоимости и веса всего самолета. «Мы убеждены, что компоненты из термопластичного композита будут играть все более важную роль в производстве самолетов», - прогнозирует Костабель.
волокно
- MMF # 5:Руководство по внедрению компонентов в детали, напечатанные на 3D-принтере
- Революционно новый способ производства металлических деталей
- Представляем наш новый кованый материал:оникс
- AT&T и Tech Mahindra совместно работают над новой платформой искусственного интеллекта с открытым исходным кодом
- LANXESS вводит в эксплуатацию две новые производственные линии для термопластичных композитов Tepex
- Ускорение термопластичных композитов в аэрокосмической отрасли
- Nèos International открывает новый штаб-квартиру по производству композитных материалов в Великобритании
- Как производить прецизионные механические компоненты
- Понимание высокоточных компонентов
- Отделка деталей и компонентов