Система резки препрега сокращает количество отходов и ускоряет сборку швейцарского бизнес-джета
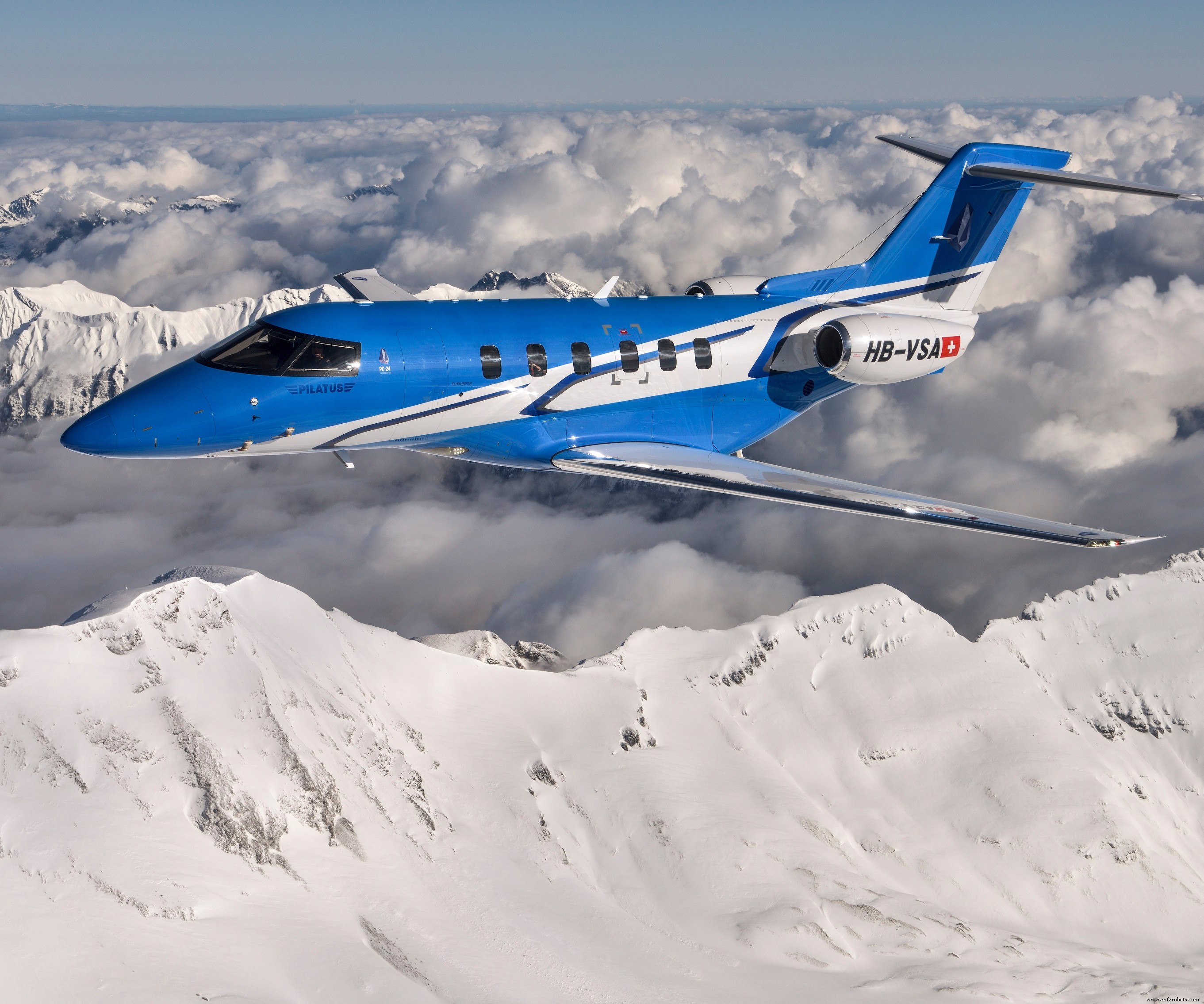
Источник | Цюнд
Благодаря компонентам из углеродного волокна и стекловолокна PC-24 бизнес-джет, производимый компанией Pilatus Aircraft AG (Станс, Швейцария), может похвастаться базовой массой всего 5,3 тонны (менее 12 000 фунтов), что позволяет ему взлетать и приземляться на короткие, грунтовые или гравийные взлетно-посадочные полосы, обычно предназначенные для турбовинтовых самолетов. Фактически, PC-24 способен взлетать на взлетно-посадочной полосе длиной 890 метров (2920 футов), а для посадки требуется всего 720 метров (2362,2 фута).
Компания Pilatus начала использовать детали из углеродного волокна в самом начале своей истории производства самолетов, начав с своих первых компонентов из армированного углеродным волокном пластика (CFRP) и стеклопластика (GFRP) для PC-6 Портер металлический универсальный самолет. Несколько составных компонентов на PC-6 , который впервые взлетел в 1959 году и прошел серийное производство около 500 самолетов, прежде чем был заменен его преемником PC-12 , были заложены вручную. PC-6 сборка, следовательно, потребовала наличия опытной рабочей силы и высоких допусков на детали.
Напротив, последний тип самолета компании, PC-24 , состоит из множества частей, многие из которых фрезерованы с допусками в диапазоне Mμ. PC-24 использует композиты в основном для внутренней и внешней облицовки. Корпуса двигателей и законцовки крыльев также сделаны из углеродного волокна, а также дверцы шасси, воздуховоды, различные патрубки, кожухи и задние кромки крыльев.
Не только PC-24 включает больше составных компонентов, чем PC-6 сделал это в 1959 году, но сейчас сборка стала намного быстрее, что стало возможным, говорит Пилатус, благодаря прогрессу в производственных технологиях. Ключом к этому является постоянное снижение затрат, оптимизация производительности и возможность внедрения современных производственных технологий.
Системы цифровой резки препрега являются частью этой тенденции. Компания Pilatus в течение многих лет полагалась на системы резки Zünd (Альтштеттен, Швейцария), а в 2019 году добавила систему резки препрега Zünd G3 L-2500. Система G3 обеспечивает однослойную резку материалов для соответствующих компонентов в значительной степени автоматизированным процессом, а затем маркирует отрезанные детали с помощью встроенного струйного модуля.
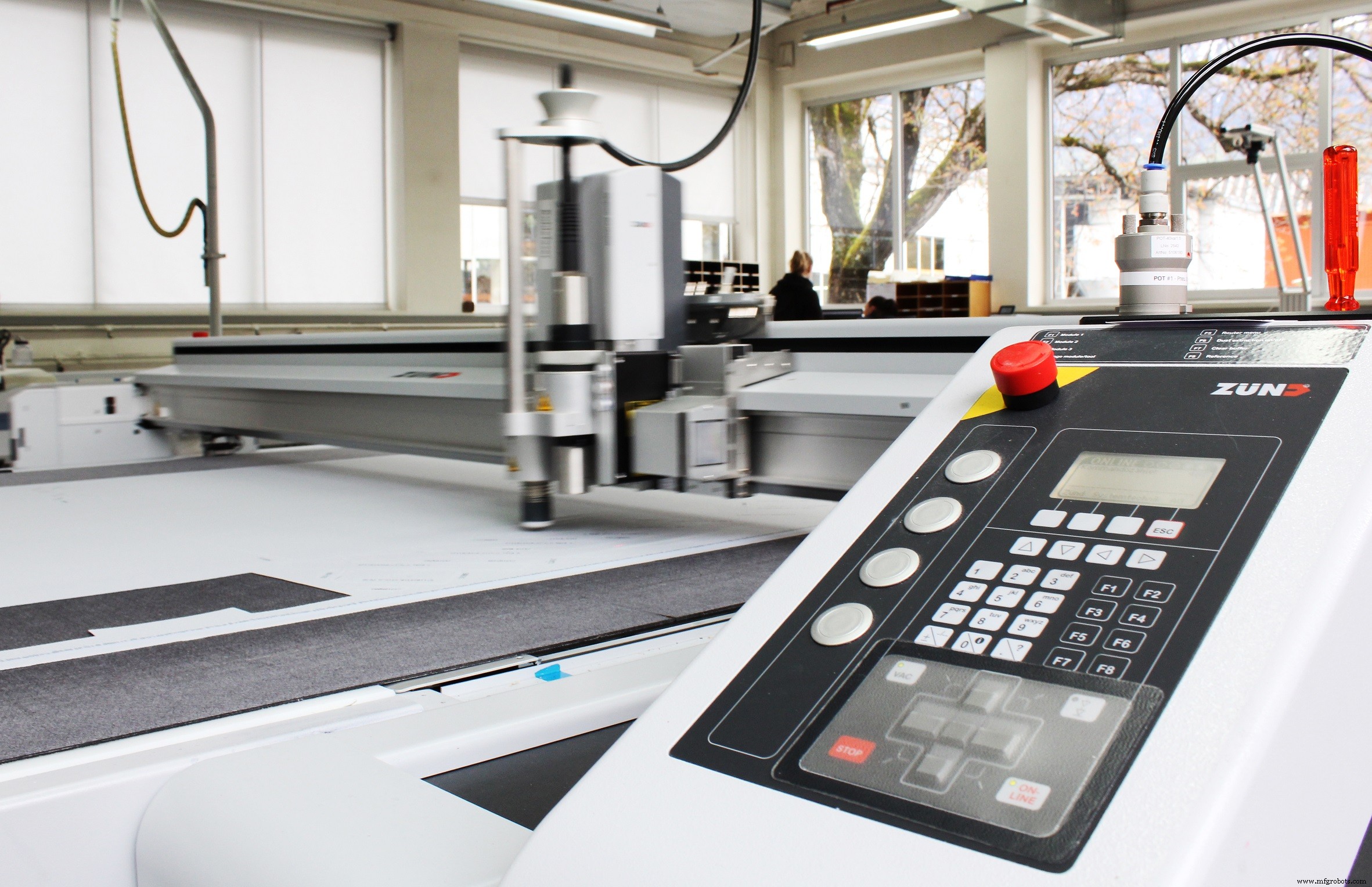
Источник | Цюнд
Pilatus перерабатывает около пяти рулонов препрега в день (примерно 90 квадратных метров), или около 90 000 квадратных метров в год, при этом темпы его потребления неуклонно растут по мере того, как в самолетах компании используется все больше и больше компонентов углепластика и стеклопластика. Pilatus полагается на цифровую резку Zünd более 15 лет, начав с резака серии PN. Повышенный спрос на компоненты из углеродного волокна начал превышать возможности, что привело к добавлению Zünd G3 L-2500 в 2019 году. После завершения резки детали комплектуются и помещаются в холодное хранилище для дальнейшей обработки. Композитные конструкции Pilatus могут состоять из до 350 слоев препрега.
Еще одним фактором успеха Pilatus была ориентация на повышение производительности. По словам Патрика Рорера, менеджера проекта Pilatus по системным закупкам, «при работе с дорогостоящими материалами, такими как углеродное или стекловолокно, всегда важны эффективность и оптимизация материалов. Мы постоянно работаем над повышением утилизации и тем самым сокращением отходов - тем более, что у нас по-прежнему мало возможностей для вторичной переработки ».
Компания заявляет, что сократила объем отходов с 30% до 20%, и в качестве важного фактора в этом успехе она называет эффективные функции раскроя в программном обеспечении Zünd's Cut Center - ZCC. Различные слои детали статически вложены друг в друга, что означает, что отдельные слои детали вложены в запрошенном количестве в соответствии с заказом . Динамическое размещение, то есть когда отдельные слои деталей из нескольких заказов вложены и объединены в один файл разреза, также можно использовать, когда это имеет смысл. По словам Цюнд, это еще больше увеличивает степень использования сырья.
волокно
- Как работает гидроабразивная резка?
- 5 преимуществ гидроабразивной резки
- Водоструйная резка и лазерная резка:в чем разница?
- Как эффективно оптимизировать станок для гидроабразивной резки?
- Что следует учитывать перед покупкой станка для гидроабразивной резки?
- Решение снижает выбросы в систему для Solvay
- Надежность сокращает трату времени, талантов и ресурсов
- Гидроабразивная обработка и резка
- Подходит ли автоматизация вашей системы лазерной резки для вашего приложения?
- ICS представлена в Hartford Business Journal