Мониторинг состояния машин поддерживает работу завода
В 1901 году Рэнсому Э. Олдсу был выдан патент на идею непрерывно движущейся сборочной линии, которую он использовал для создания первых автомобилей Oldsmobile. В 1913 году Генри Форд усовершенствовал концепцию, добавив движущиеся конвейерные ленты, и благодаря этим двум инновациям время, необходимое для сборки автомобиля, сократилось с полутора дней до полутора часов. Родился современный сборочный завод.
В течение следующих четырех десятилетий идея движущейся производственной линии была принята многими отраслями промышленности, от радио до бритв, от часов до детских кроваток, от гвоздей до газет. Во время Второй мировой войны США построили 300 000 самолетов с использованием движущихся производственных линий. Эта идея стала основой производства по всему миру и остается основным способом выпуска продукции на массовые рынки.
Инструменты и оборудование, используемые для выполнения сборочных работ, являются наиболее важной частью любой линии. В 1950-х годах надежность заводского оборудования становилась важной частью операций. Если одна машина перестанет работать, вся линия остановится до тех пор, пока не будет произведен ремонт. Незадействованные машины и сборщики снизили эффективность и повлияли на затраты. Обслуживание стало важным.
На протяжении второй половины 20-го века техническое обслуживание заводов в основном сводилось к плановому периодическому техническому обслуживанию. Это повысило надежность и срок службы машин, но никак не помогло операторам предсказать и избежать сбоев в работе оборудования или незапланированных простоев. За последние двадцать лет мониторинг состояния машин стал важной частью заводских операций. На фабриках, иногда называемых умными фабриками, промышленным Интернетом вещей (IIoT) или Индустрией 4.0, устанавливаются датчики и аналитические системы, которые следят за состоянием производственного оборудования.
Мониторинг состояния — это процесс оснащения оборудования датчиками, которые могут выявлять существенные изменения параметров, свидетельствующие о неизбежной неисправности или отказе. Эти системы ищут две вещи. Во-первых:машина работает за пределами расчетных параметров, требующих быстрого реагирования? Во-вторых:каковы долгосрочные тенденции критических параметров для прогнозирования того, когда машине потребуется техническое обслуживание, ремонт или замена.
Заводские электродвигатели
Одной из самых распространенных машин на заводах является электродвигатель. По оценкам, сегодня на производственных предприятиях по всему миру работает 300 миллионов двигателей. Они обеспечивают производство, сборку и перемещение продукции на заводе. Выход из строя одного двигателя может привести к полной остановке производственной линии, что обходится в 10 000 долларов в час. Датчики контроля состояния и аналитика заранее предупреждают о проблемах. Быстрое решение этих проблем приводит к снижению затрат на техническое обслуживание, уменьшению количества сбоев в технологическом процессе и повышению безопасности операторов оборудования.
Состояние любого двигателя можно определить, отслеживая три рабочих параметра:
-
Вибрация — измеряется акселерометром.
-
Температура — измеряется датчиком температуры контактного типа.
-
Ток — измеряется индуктивным или шунтирующим датчиком тока.

Акселерометры предоставляют данные о механическом состоянии двигателя. Датчики температуры предоставляют данные как о механическом, так и об электрическом состоянии, а датчики тока следят за электрическим состоянием. Датчики также могут предоставлять данные о состоянии оборудования и инструментов, прикрепленных к двигателю.
Акселерометры
Все вращающиеся двигатели имеют якорь, подвешенный на подшипниках и вращающийся с различной скоростью. Якоря сбалансированы, чтобы не вибрировать при вращении. Однако несбалансированный или поврежденный якорь создает вибрацию, которая может повредить подшипники. Если вибрации находятся на резонансных частотах другого оборудования, присоединенного к двигателю, повреждение может быть серьезным и быстрым. Частота вибрации двигателя совпадает с частотой вращения двигателя и обычно находится в диапазоне от нескольких Гц до 4 кГц. Для измерения этих вибраций подходят акселерометры.
Акселерометры также используются в качестве контактных микрофонов, которые прислушиваются к высокочастотному шуму (визгу) подшипников, в которых закончилась смазка. Эти частоты находятся в диапазоне от 5 кГц до 15 кГц. Пьезоэлектрические акселерометры работают хорошо, потому что они имеют широкую частотную характеристику, которая охватывает оба частотных диапазона с помощью одного устройства.
Обычно для анализа сигнала используется быстрое преобразование Фурье (БПФ). Данные БПФ показывают каждую полосу частот вибрации и ее интенсивность. На рис. 2 показаны собственные частоты и амплитуды вибрации типичного двигателя.
Новые двигатели имеют собственные частоты вибрации, которые записываются и используются в качестве базового уровня для сравнения с данными, полученными позже в течение срока службы двигателя. Если эти измерения остаются в том же диапазоне, что и исходные данные, двигатель находится в хорошем состоянии. Если частоты или интенсивность начинают меняться со временем, это свидетельствует об износе частей двигателя, и отказ может быть неизбежен. Таким образом, ремонт можно планировать до того, как произойдет сбой. Это исключает катастрофические остановки линий и повышает эффективность производства.

На рис. 3 показан датчик вибрации модели 8911 от бизнес-подразделения TE Connectivity Sensors. Он содержит пьезоэлектрический акселерометр и микроконтроллер, выполняющий преобразование БПФ в нужный заказчику формат. Кроме того, этот датчик питается от батареи и передает данные по беспроводной сети на частотах LoRa. Это исключает жесткую проводку. Датчик можно легко установить на двигатель с помощью клея, монтажной шпильки или магнитного основания. Благодаря простому монтажу и отсутствию проводки датчик может перейти от готового к полной эксплуатации за очень короткий период времени и при очень низких затратах.
Датчики температуры
Двумя частями двигателя, наиболее подверженными воздействию высоких температур, являются подшипники и обмотки статора. Чтобы быть эффективными, датчики, которые измеряют эти параметры, должны иметь тесный физический контакт с интересующими частями двигателя, поэтому для двигателей обычно требуются уникальные конструкции.
При эксплуатации подшипники двигателя обычно работают при температуре от 60° до 70°C (140°-160°F). При правильной нагрузке и смазке подшипники могут иметь чрезвычайно длительный срок службы. Наиболее распространенная проблема возникает, когда смазочные материалы исчезают из-за утечек или выходят из строя из-за перегрева окружающей среды. Эти режимы отказа могут возникать в течение довольно длительных периодов работы — 1000 часов. По мере истощения смазочного материала температура подшипника начинает расти, и ее легко отследить с помощью датчика температуры и аналитического программного обеспечения.
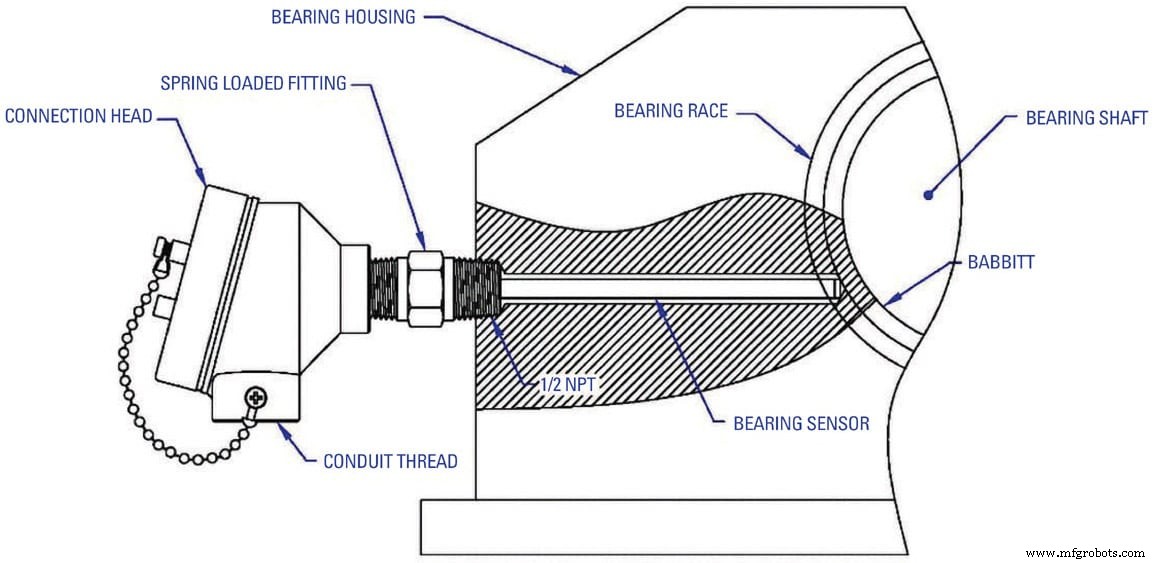
На рис. 4 показан подпружиненный датчик температуры типа NTC или RTD, предназначенный для прямого контакта с внешней обоймой подшипника. Такое крепление обеспечивает наиболее точные измерения температуры. Корпус подшипника должен иметь элементы, предназначенные для размещения датчика температуры и обеспечения близкого доступа к подшипнику.
Датчики температуры также используются для измерения температуры электрических обмоток статора. Это катушки, которые генерируют магнитные поля для вращения якоря. Если эти обмотки повреждены ударом или коррозией, сопротивление провода увеличивается, а их способность проводить ток уменьшается. Это приводит к нагреву затронутых проводов. Их температура может расплавить изоляцию и даже вызвать пожар.

На рисунках 5a и 5b показаны датчики температуры (подразделение TE Connectivity Sensors), встроенные в обмотки статора двигателя. Датчики становятся неотъемлемой частью устройства.
Как и в случае датчиков вибрации, измеряется и записывается начальная рабочая температура. С течением времени температуру периодически измеряют и сравнивают с базовой линией. Если температура начинает отклоняться от нормы, это указывает на механические проблемы с подшипниками или электрические проблемы с обмотками статора. Опять же, техническое обслуживание можно запланировать до того, как произойдет серьезный сбой, что предотвратит неожиданное отключение линии.
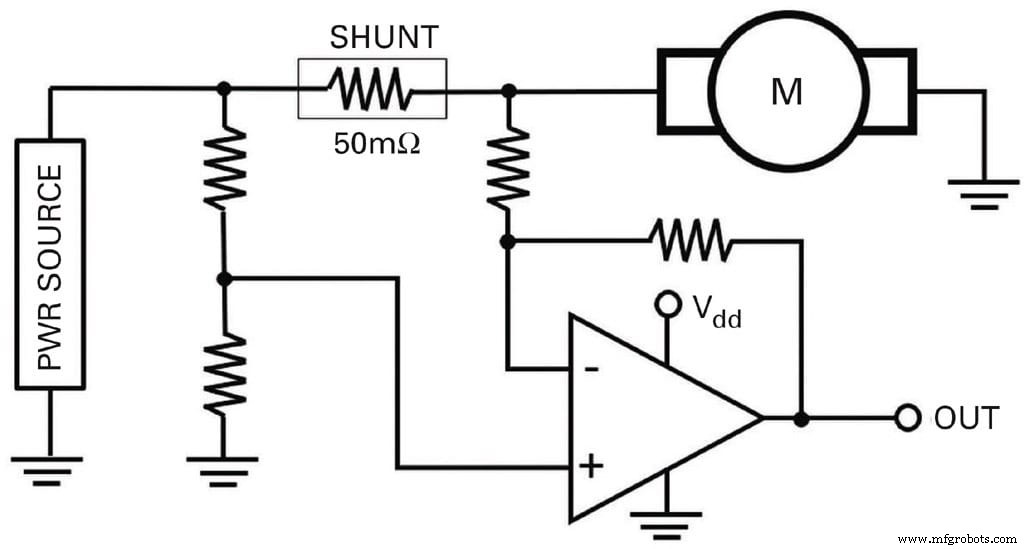
Датчики тока
В то время как датчики вибрации и температуры могут сообщать о физическом состоянии двигателя, датчик тока может проверять его электрическое состояние. Датчики тока бывают двух основных конфигураций:шунтирующие и индуктивные. У каждого есть преимущества и недостатки. На величину потребляемого двигателем тока влияют многие факторы:приложенное напряжение, скорость двигателя, нагрузка на вал двигателя и состояние щеток якоря. Токи вне диапазона могут указывать на проблемы с напряжением питания, короткие замыкания в обмотках статора или якоря, изношенные щетки или проблемы с присоединенными инструментами.

Шунтирующий датчик тока представляет собой резистор очень малой мощности, включенный последовательно с линией электропередачи, ведущей к двигателю. Напряжение, возникающее на резисторе, пропорционально току, протекающему через него. Используя закон Ома (I =E/R) и зная значения напряжения и сопротивления, можно рассчитать ток. Шунты используются там, где требуется очень высокая точность или для высокочастотных бесколлекторных двигателей. На рис. 6 показана схема шунтирующего датчика.
Индуктивные датчики тока используют кольцо с высокой диэлектрической проницаемостью вокруг провода питания. Ток по проводу индуцирует магнитное поле в кольце (Бин). Датчик Холла, встроенный в кольцо, измеряет магнитное поле и через усилитель и катушку, обернутую вокруг кольца, индуцирует обратное магнитное поле (BF) для противодействия Бину. Напряжение, необходимое для создания поля BF, является выходным сигналом. Суммарный эффект двух магнитных полей будет проявляться как нулевое поле на датчике Холла. Чем выше ток в силовом проводе, тем выше должно быть напряжение ЗП. (См. рис. 7)
За мотором

Часто оборудование, прикрепленное к двигателю, также можно контролировать на предмет исправности. На рис. 8 показан пример фрезерного станка, использующего многолезвийную фрезу для обработки плоской поверхности в заготовку. Состояние вращающегося режущего инструмента очень важно для качества операции резки. Чем острее канавки на фрезе, тем точнее рез и тем лучше поверхность готовой работы. По мере того, как каждая канавка делает разрез, ток двигателя увеличивается, чтобы обеспечить необходимую мощность. Острые канавки требуют меньше энергии для резки металла. Тупые флейты требуют большей мощности.

Контролируя ток двигателя для этого фрезерного станка, можно определить, какие канавки на режущем инструменте острые, а какие тупые и нуждаются в заточке.
Вклад мониторинга состояния в IIoT
С момента изобретения производственной линии и вызванной ею промышленной революции появилось множество технических инноваций, которые способствовали прогрессу в производстве. За последние 70 лет заводы демонстрировали средний прирост производительности на 2,8% в год. Внесли свой вклад такие технологии, как электроинструменты, литье под давлением, оборудование для захвата и размещения, автоматические испытания и робототехника. Сегодня к этому добавляется мониторинг состояния машин. Успешный мониторинг состояния начинается с датчиков, расположенных на заводских машинах, которые постоянно сообщают данные об их исправности и работе. Используя аналитику в реальном времени, операторы заводов могут выявлять проблемные места и планировать необходимый ремонт и техническое обслуживание, не дожидаясь катастрофических сбоев. Это обеспечит повышение производительности производства. Однако все начинается с датчиков.
Эта статья была написана Питом Смитом (Pete Smith), старшим менеджером по поддержке продаж и маркетинга, TE Connectivity Sensor Solutions — TES (Шаффхаузен, Швейцария/Бервин, Пенсильвания). Для получения дополнительной информации свяжитесь с г-ном Смитом по адресу Этот адрес электронной почты защищен от спам-ботов. У вас должен быть включен JavaScript для просмотра. или посетите здесь .
Датчик
- Рынок мониторинга состояния достигнет 3,9 млрд долларов к 2025 году
- Как мониторинг состояния улучшает программу PdM
- Продукт SKF Machine Condition Advisor получил награду
- Завод двигателей Honda выигрывает от мониторинга машин
- Устройство SKF позволяет диагностировать состояние машины
- B&R представит решение для мониторинга состояния на выставке Agritechnica
- Мониторинг состояния оборудования завода
- Подводные камни мониторинга состояния и потенциальные возможности заводского обслуживания
- Выполнение мониторинга состояния вашего оборудования
- Мониторинг состояния:5 распространенных типов сбоев и их важность