Разработка лицевой маски Fast Radius
Иззи де ла Гуардиа, инженер по приложениям, Fast Radius
Хотя глобальная пандемия выявила множество уязвимых мест в нашей цепочке поставок, она также породила инновации. В частности, 3D-печать позволила профессионалам и любителям воплотить свои страхи в жизнь с беспрецедентной скоростью и доступностью. Мы убедились в этом на собственном опыте при создании нашего респиратора с открытым исходным кодом.
Вот краткое описание процесса и то, как мы смогли создать четыре различных прототипа и провести три сеанса пользовательского тестирования всего за две недели, воспользовавшись преимуществами 3D-печати, многофункциональной команды, а также личных и профессиональных сетей нашей компании.Р>
Быстрое прототипирование и пользовательское тестирование
Поскольку многие американцы начали укрываться на месте в середине марта, Fast Radius получил несколько запросов на респираторы, напечатанные на 3D-принтере, на фоне растущей обеспокоенности по поводу нехватки СИЗ. В пятницу днем ко мне обратился наш генеральный менеджер Джон Нэнри, чтобы возглавить проектные работы, отвечающие этой потребности. Через несколько часов у нас был готовый к печати первый дизайн, вдохновленный проектами с открытым исходным кодом Copper 3D и La Factoría 3D.
Основное внимание при разработке было уделено технологичности всех наших собственных аддитивных машин (Stratasys FDM, Carbon DLS™ и HP Multi Jet Fusion) за счет обеспечения надлежащих углов выступа и вакуумной вентиляции. В ту ночь мы создали наш первый прототип на Carbon DLS.
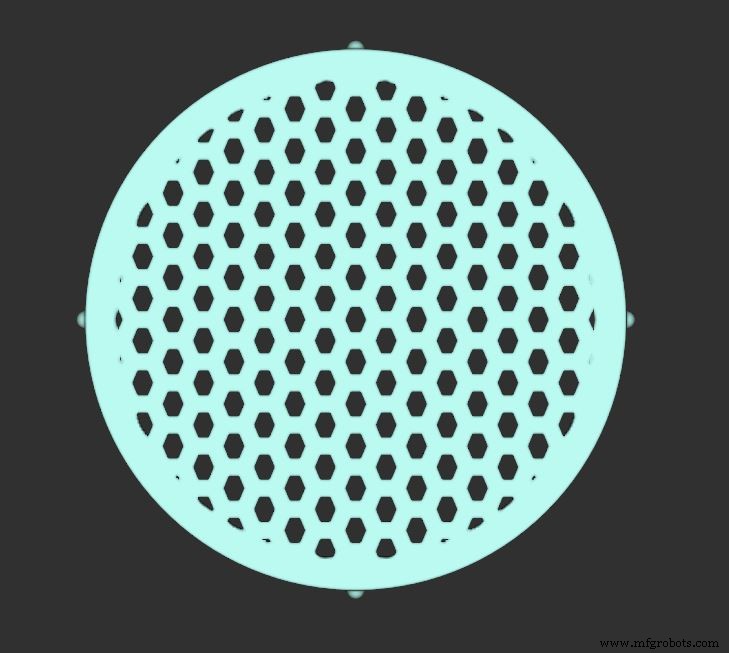
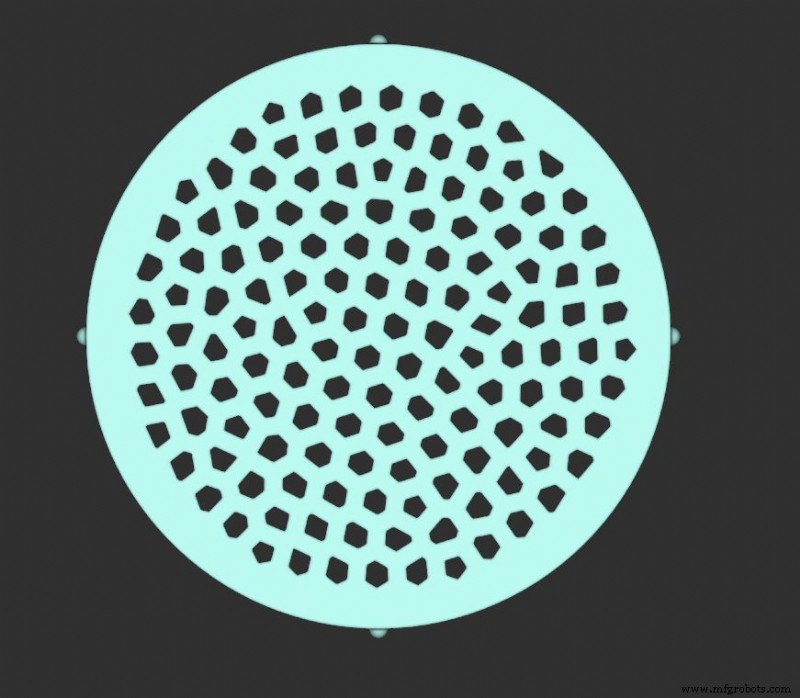
Расширенные инструменты проектирования, такие как nTop Platform, поддерживали быструю итерацию, например переход от шаблона Вороного к более регулярному шестнадцатеричному шаблону, с которым было проще работать любительским FDM-принтерам
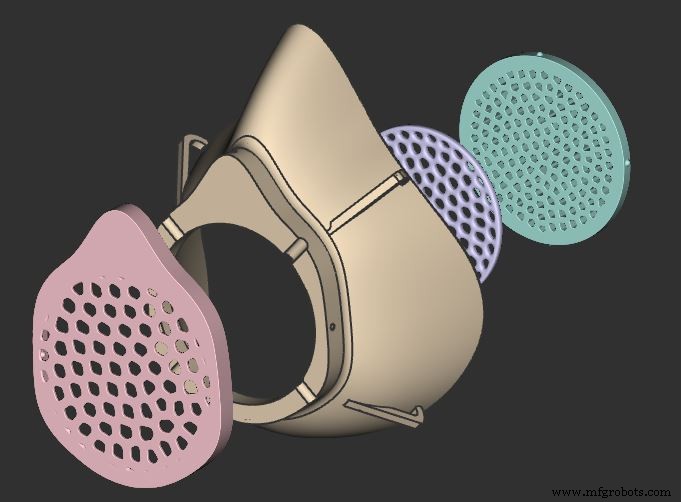
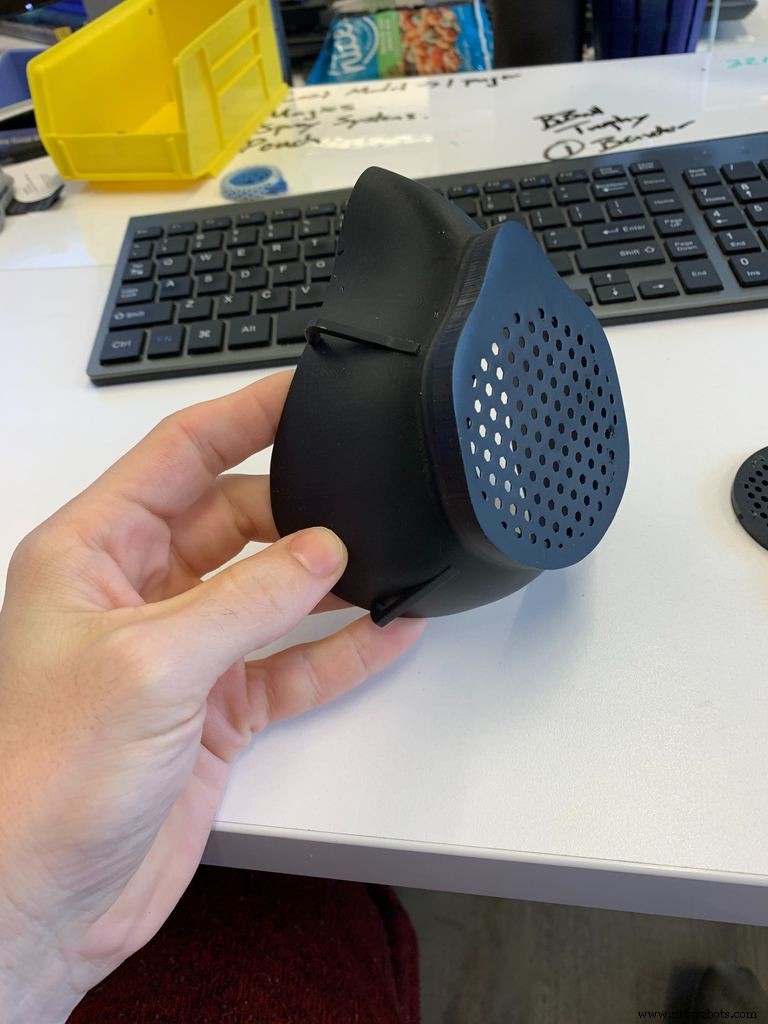
Наш первый печатный прототип включал выступы и каналы, удобные для FDM, для предотвращения образования вакуума на DLS
Эти прототипы повлияли на дальнейшие изменения дизайна:объединение передней крышки с основным корпусом маски для печати как единой детали, утолщение петель ремешка для долговечности, а также уменьшение плотности рисунка сетки и создание его круглой формы для облегчения печати на FDM. Мы смогли начать печатать наши вторые прототипы к вечеру субботы, всего через 24 часа после начала проекта.
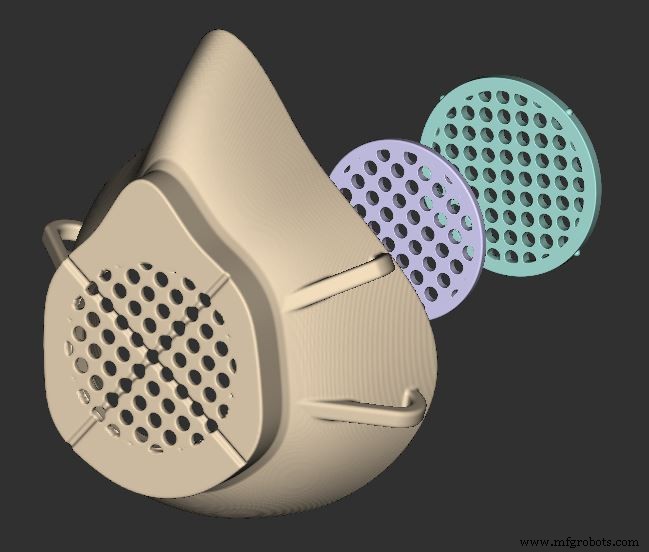
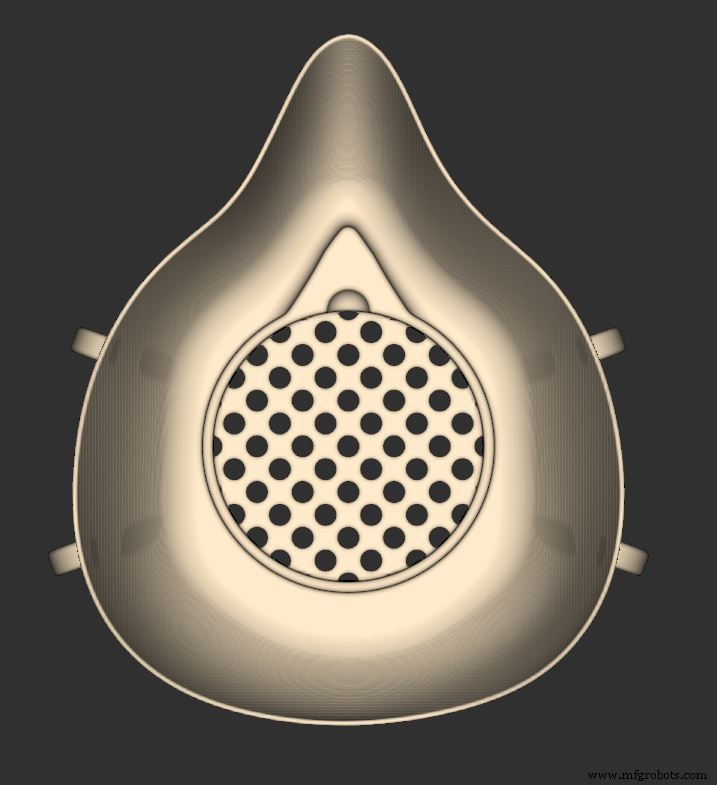
Наш второй печатный прототип с объединенными частями (слева). Внутри маски с углублением, чтобы вставить палец и выдвинуть защелкивающуюся крышку фильтра (справа).
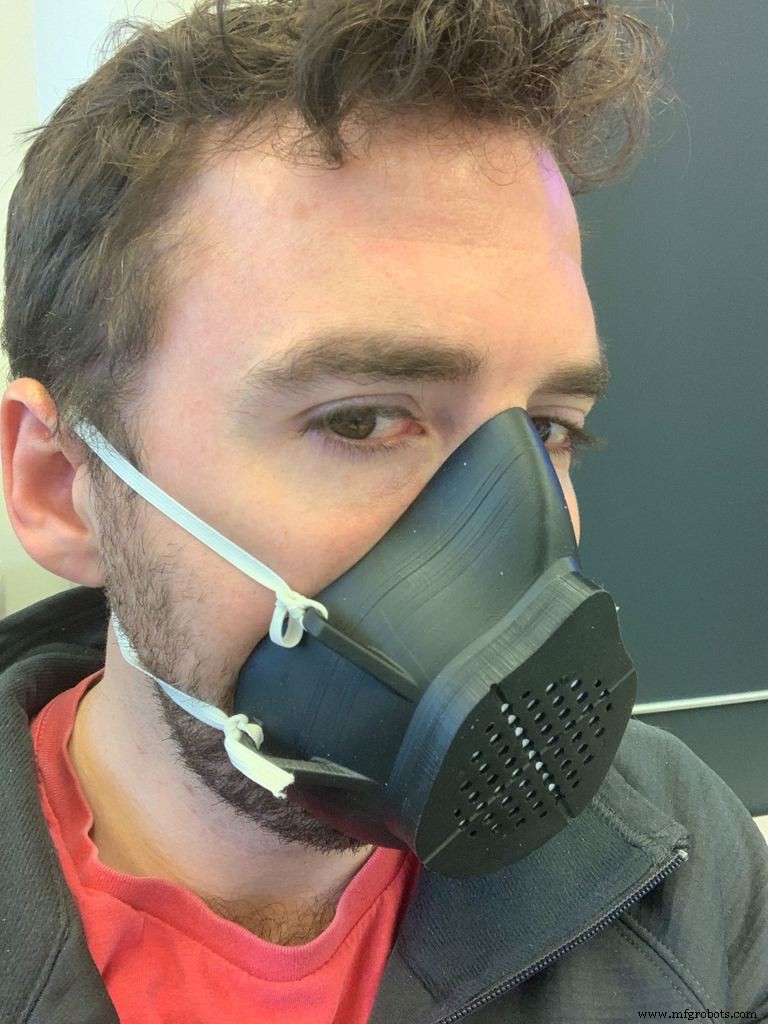
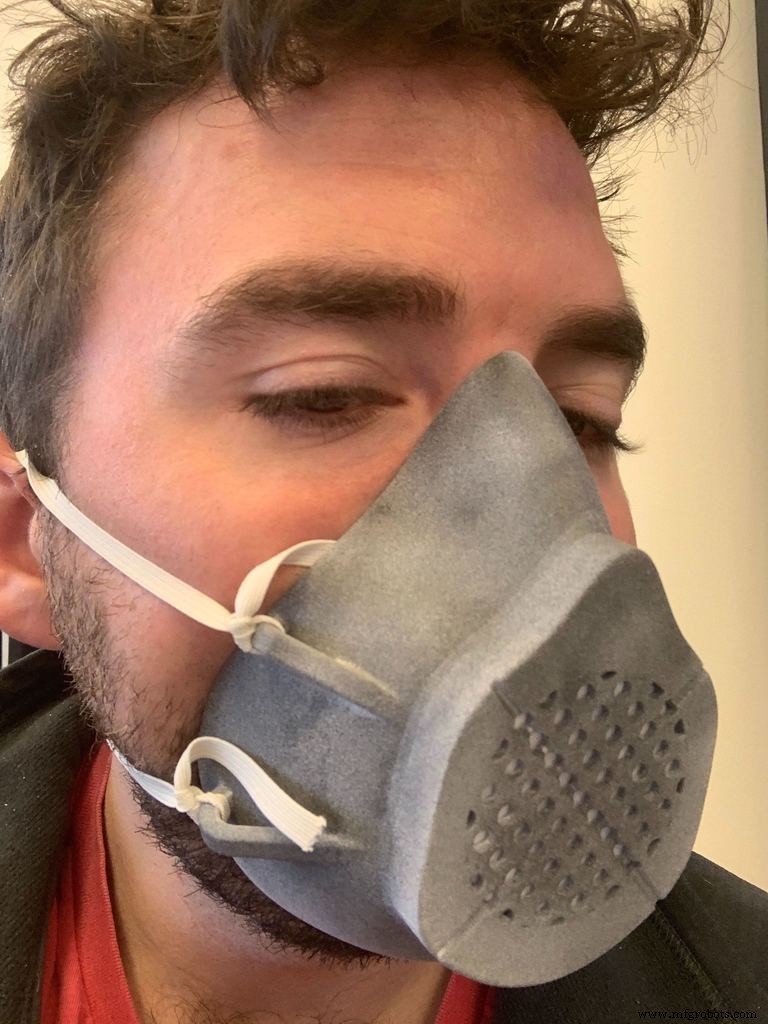
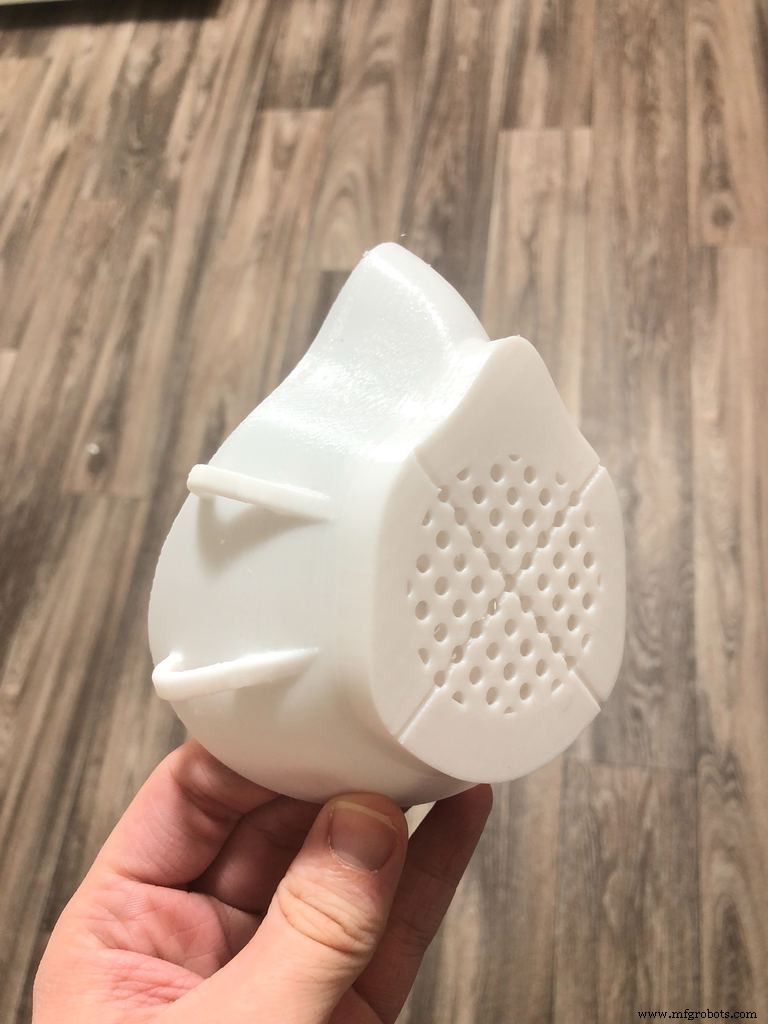
Второй напечатанный прототип из Carbon RPU70 (слева), HP PA12 (в центре) и PLA с FDM-печатью (справа)
Параллельно с процессом проектирования мы подключились к нашей сети, чтобы лучше понять потребность и определить людей для пользовательского тестирования. Менее чем за 24 часа наши друзья из P33 связали нас с дюжиной врачей и сотрудников фонда медицинских исследований, чтобы лучше узнать о масках N95. Наши сотрудники также связались со знакомыми медицинскими работниками. К воскресенью, всего через два дня после запуска проекта, мы провели тестирование нашего второго прототипа на 10 человек в четырех местах.
Следующие две недели продолжались по этой схеме — дизайн, печать, тестирование, повторение. В нашем третьем печатном прототипе был изменен механизм удержания фильтра. Смещенная полукруглая геометрия периметра функционирует как кулачок, который фиксирует деталь на месте при скручивании за счет трения (см. ниже). Есть два выступа, которые прижимают крышку вниз в повернутом или заблокированном положении, чтобы обеспечить хорошее уплотнение вокруг фильтра. Мы создали версию с перфорированной областью в форме сердца, чтобы сделать маску менее устрашающей. Начиная с этой серии прототипов, мы разработали и протестировали маски двух разных размеров.
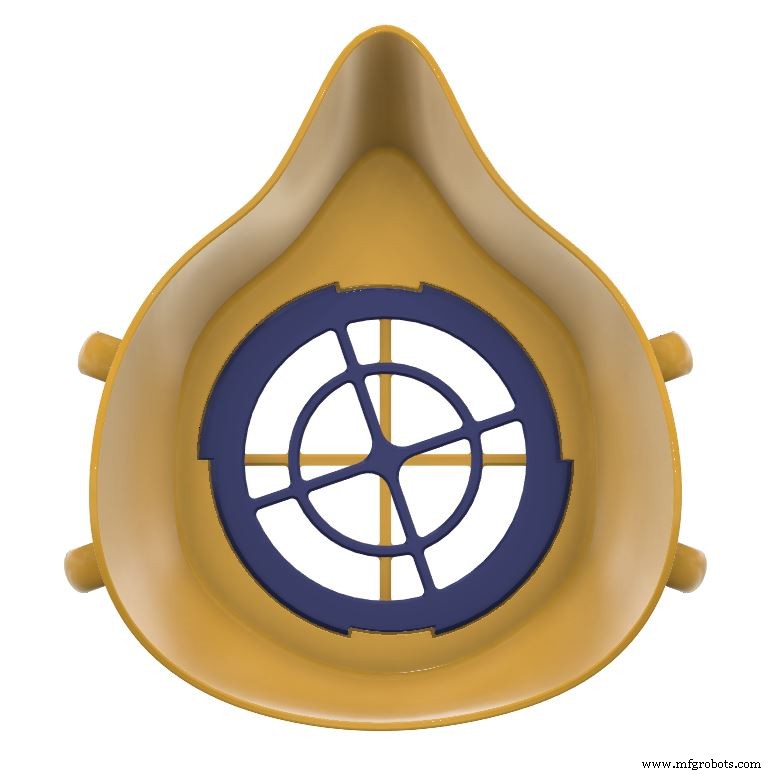
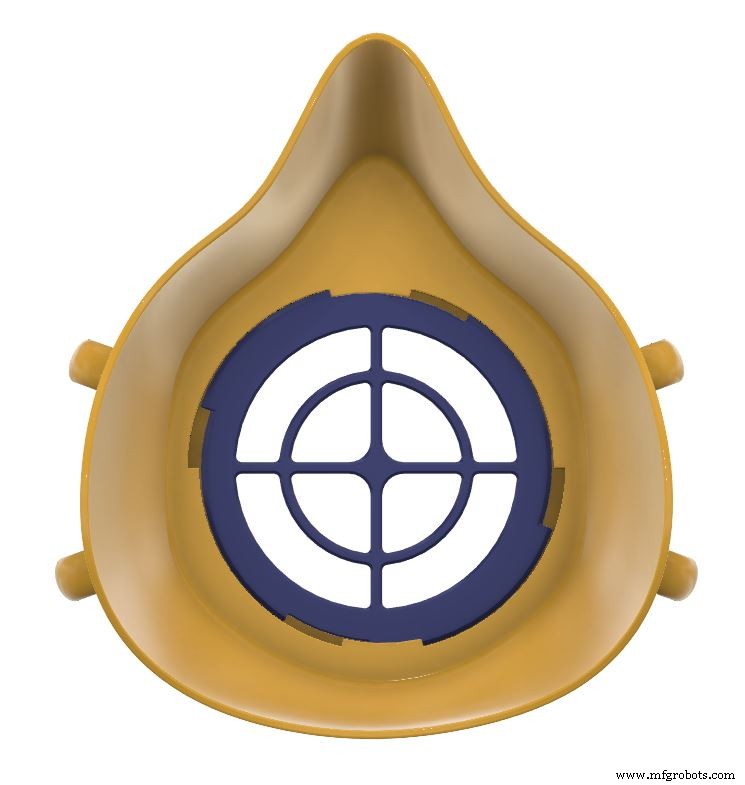
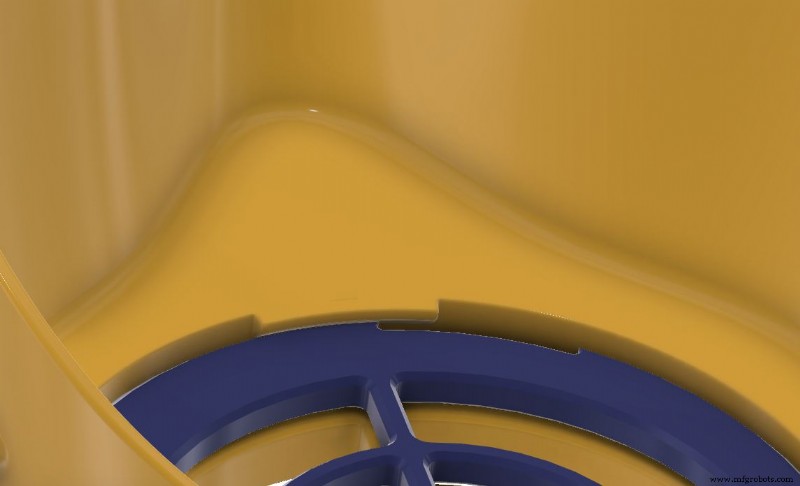
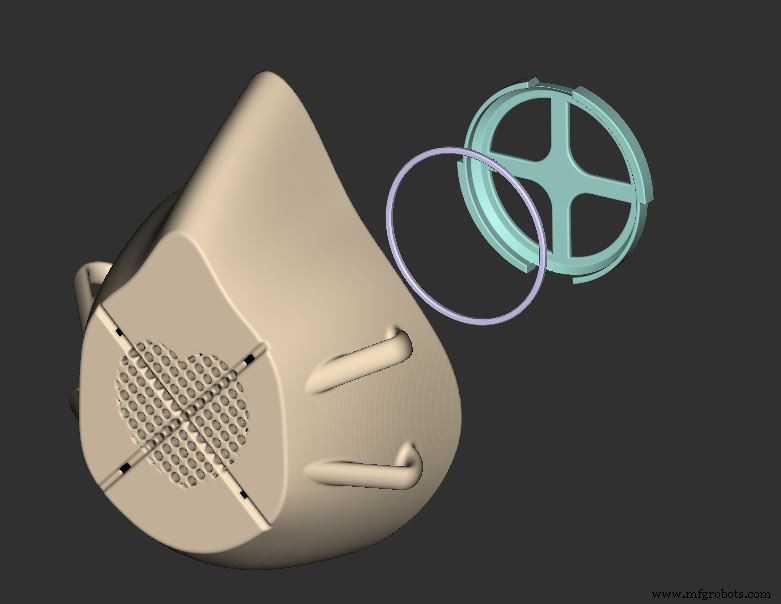
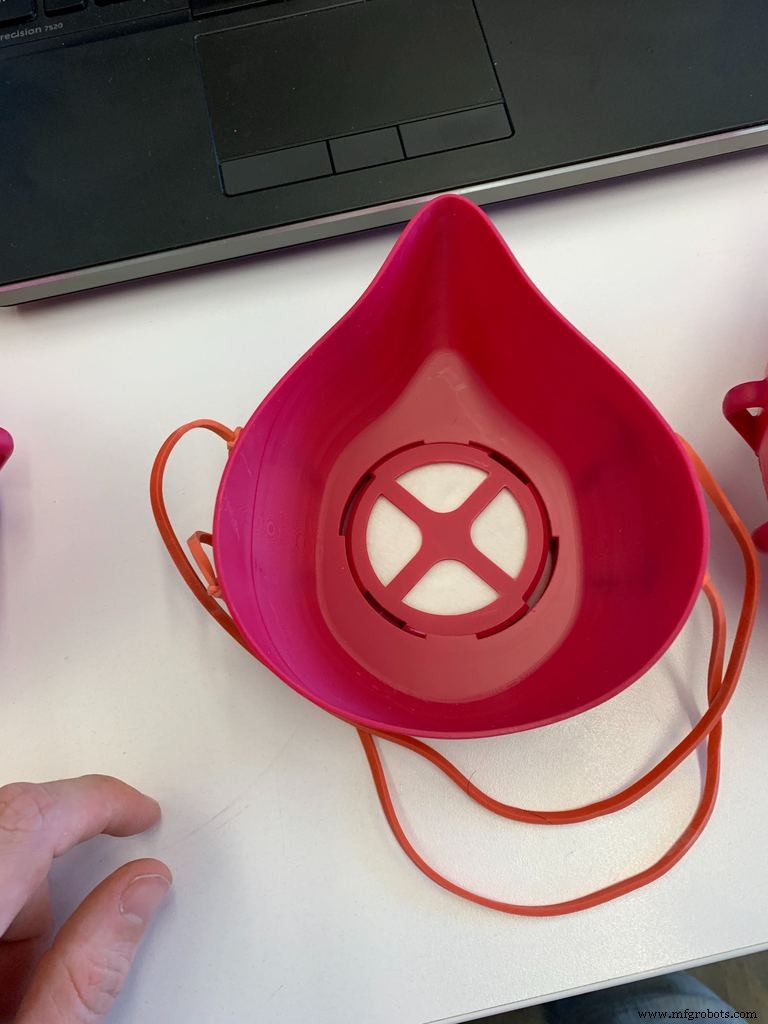
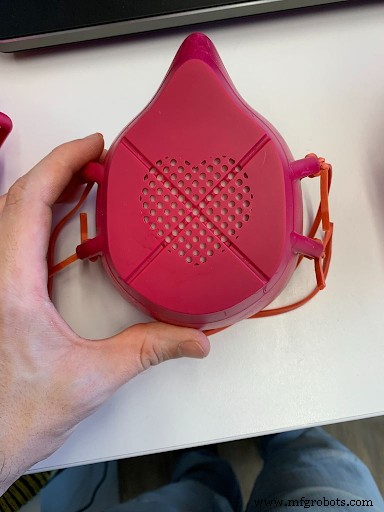
Третий печатный прототип с поворотной крышкой.
К четвертому прототипу нас в первую очередь интересовала легкость дыхания и правильная посадка. Чтобы решить эту проблему, мы попытались максимально увеличить перфорированную область и свести к минимуму ее плотность (к сожалению, потеряв сердце), чтобы уменьшить сопротивление воздушному потоку. Мы также изменили измерения для двух размеров на основе отзывов пользователей. На данный момент мы были достаточно уверены в функциях и размерах маски, чтобы выпустить первую версию с открытым исходным кодом.
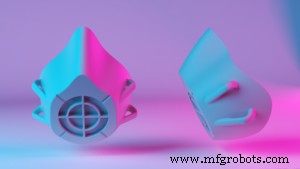
Дизайн для специальных возможностей
Чтобы сделать маску доступной как можно большему количеству людей, мы создали дизайн с открытым исходным кодом, который можно было бы изготовить на бытовых 3D-принтерах. Это решение добавило ограничений по дизайну и материалам. Жесткая маска не может соответствовать широкому спектру форм лица, поэтому мы решили добавить гибкий материал к внутреннему краю маски, чтобы улучшить ее прилегание к лицу.
Мы создали прототип первой концепции, используя SIL 30 на Carbon DLS. Далее мы протестировали множество методов создания эффективной герметизации лица (описанных ниже), в том числе разрезанную перчатку, печатный и формованный силикон, формуемый материал для лицевого протеза костюма, уплотнители из ТПУ и ПЛА, напечатанные методом FDM, и герметизирующие прокладки. В конечном итоге мы остановились на уплотнителе, который является биосовместимым, легко очищаемым и легкодоступным.
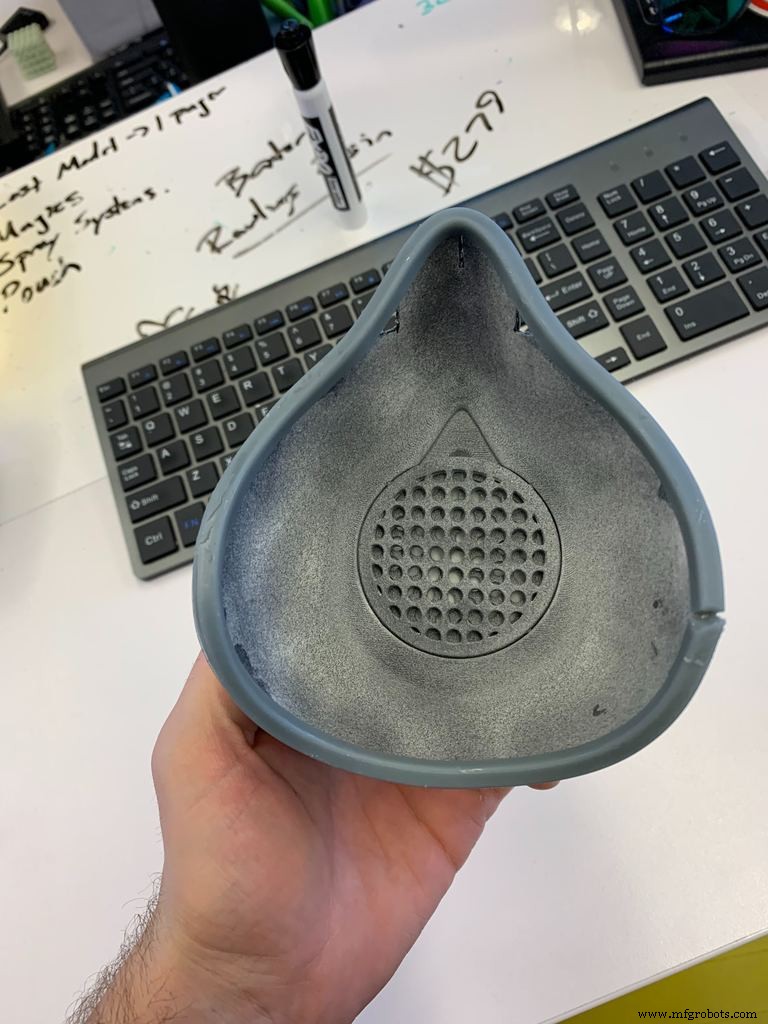
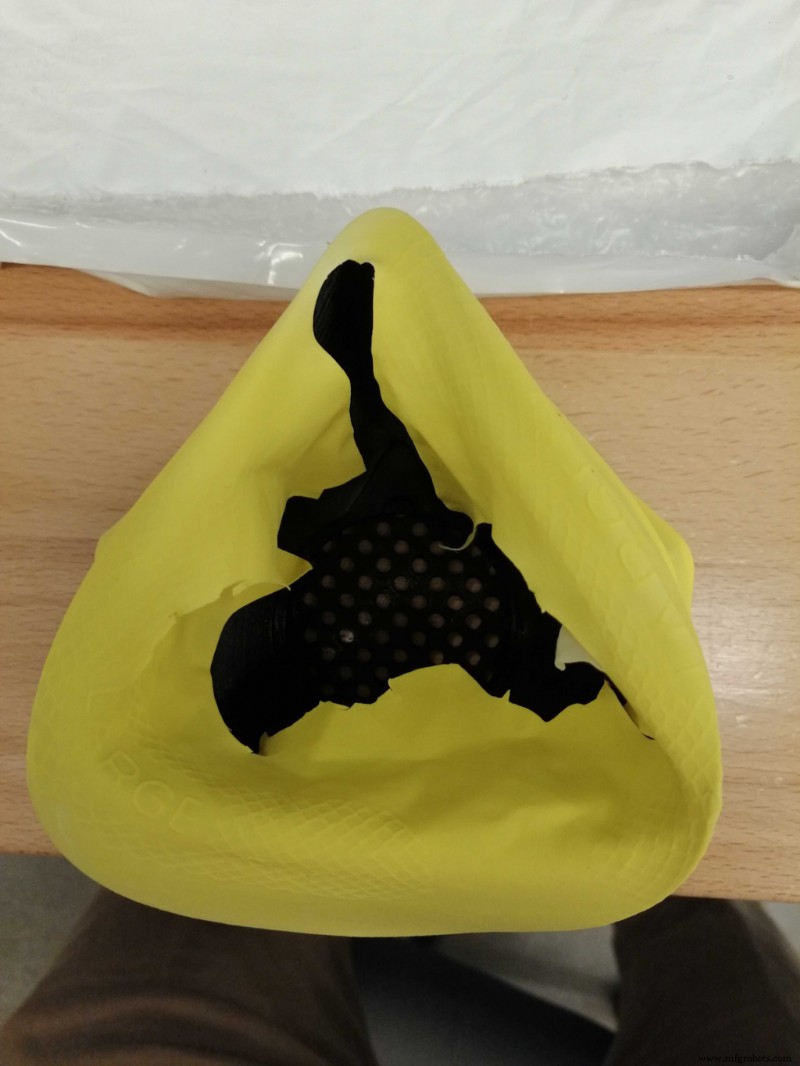
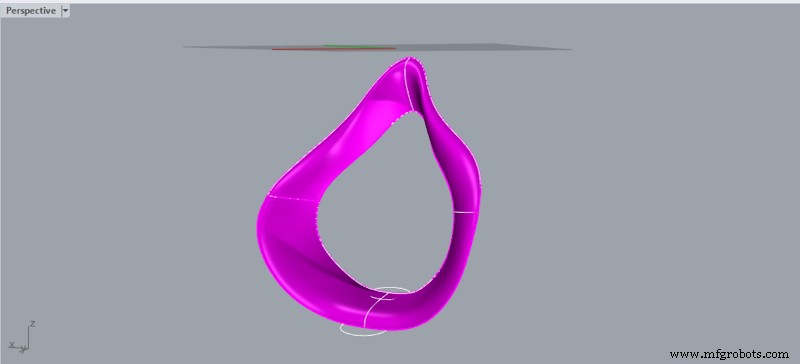
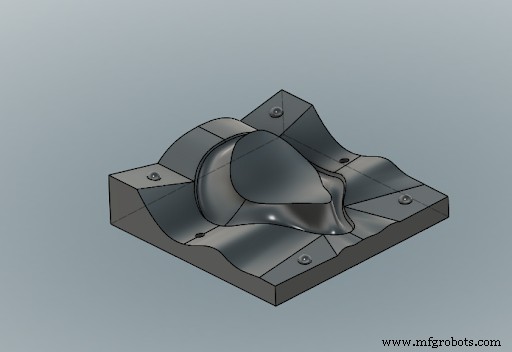
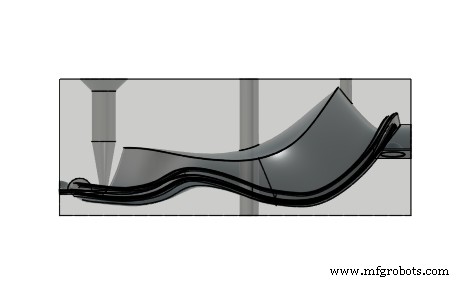
Мокап формы для формовочного силикона
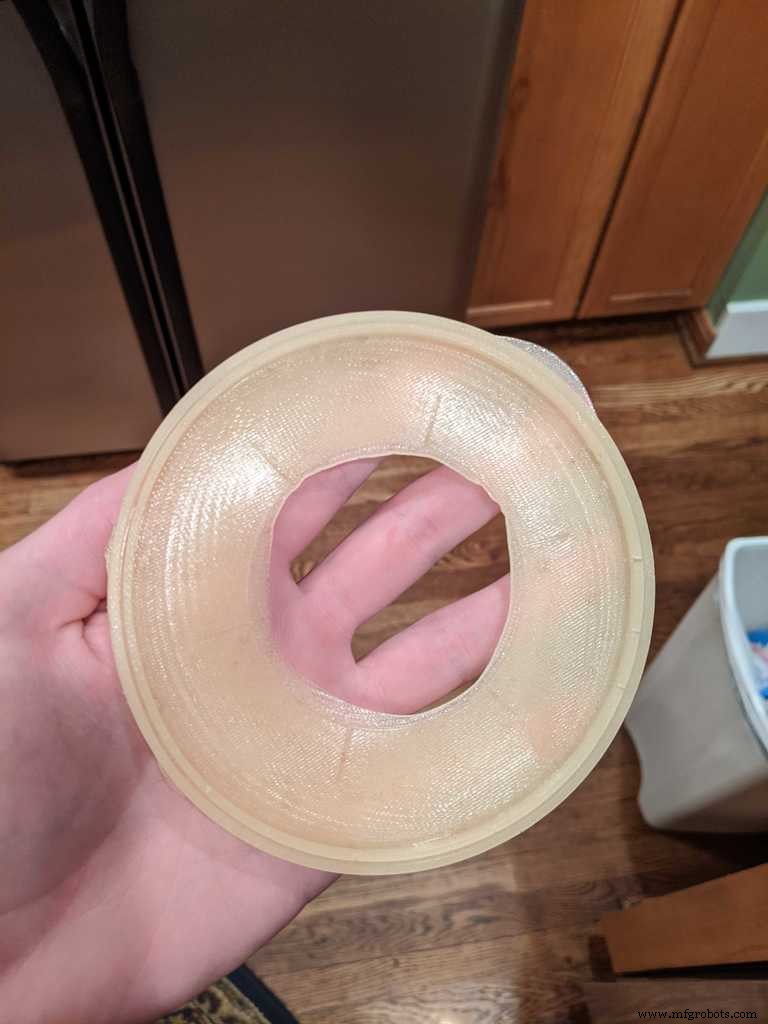
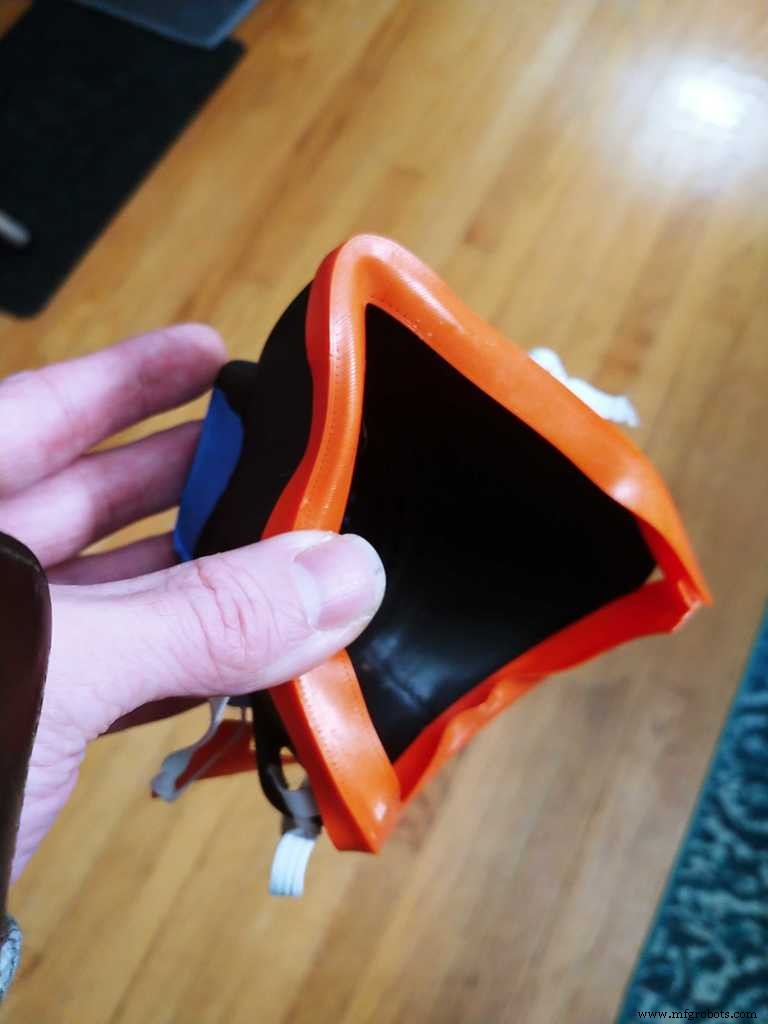
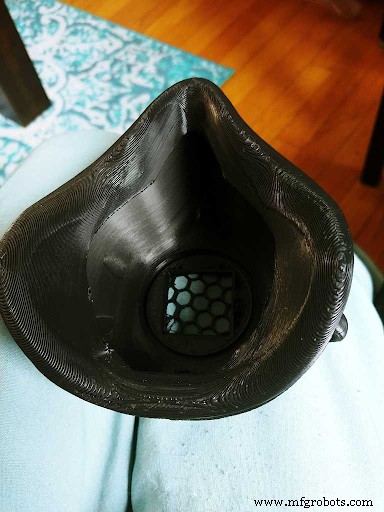
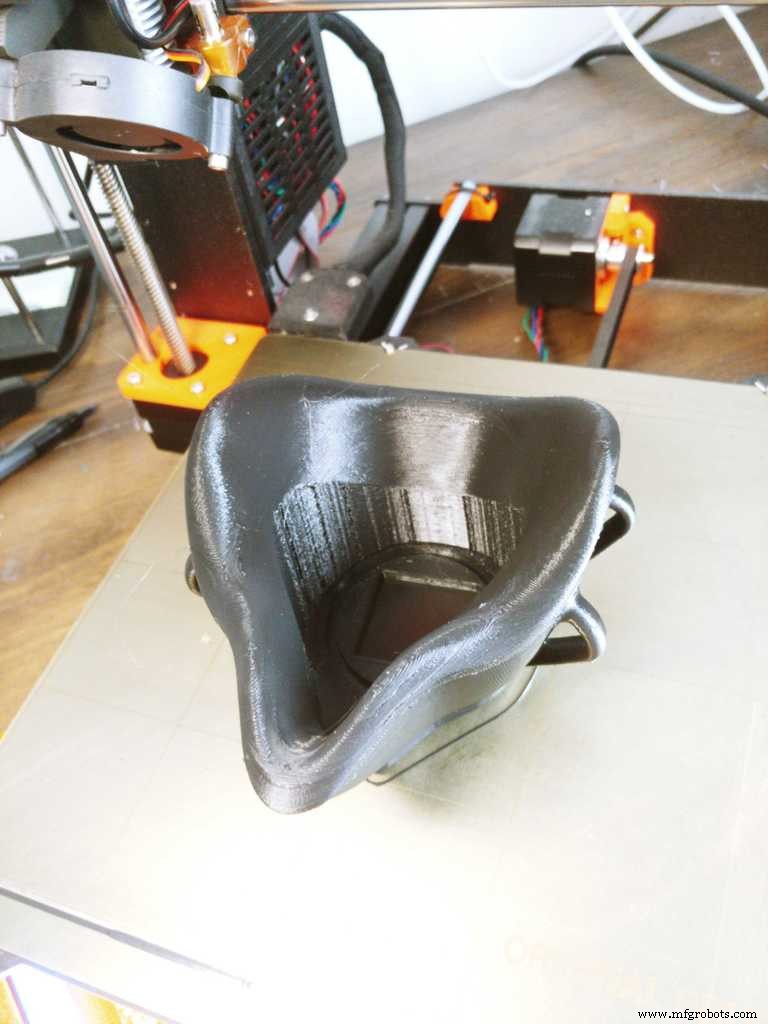
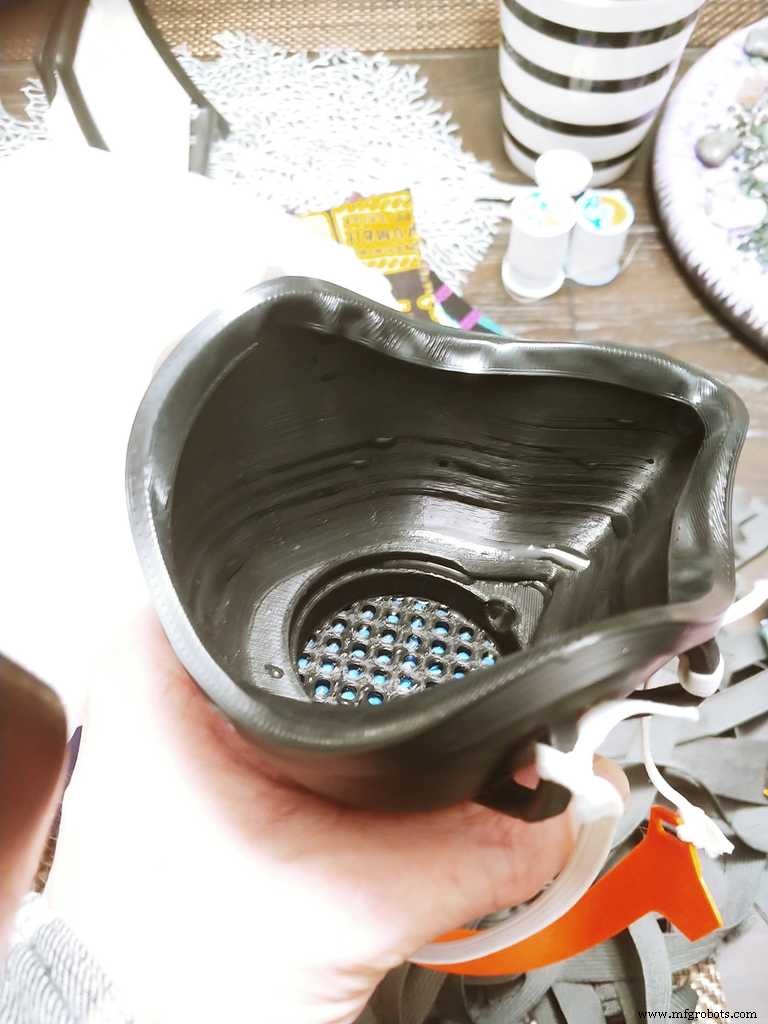
Встроенное тонкое уплотнение PLA
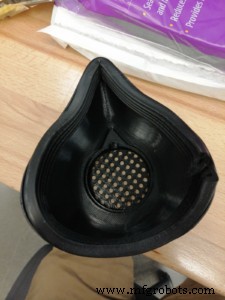
Быстрое формирование команды
Я приписываю успешную и быструю итерацию этого проекта не только силе инструментов цифрового проектирования и технологии аддитивного производства, но и самоотверженности и разнообразию команды, которую мы собрали из разных подразделений компании. Дэниел Бейкер (руководитель производственно-технического отдела) предоставил отзыв о DFM и провел всю ночь на печати и постобработке прототипов. Тим Урадник (инженер по применению) достал материал для уплотнений, собрал прототипы и проехал по всему Чикаго, чтобы провести социально дистанцированное тестирование пользователей. Юрайа Фоули и Элдон Уитис (лаборанты) тестировали прототипы и исследовали встроенные уплотнения на своих личных 3D-принтерах дома в нерабочее время.
Ник Тонини (менеджер программы) предлагал бесконечно изобретательные решения и отзывы о дизайне. Джерри О'Лири (главный дизайнер) улучшил наши проекты и создал концептуальные визуализации. Чарли Вуд (менеджер отдела вычислительной техники) руководил проектированием уплотнений. Холли Дойчман (директор по материалам и технологиям производства) связалась с нашими партнерами и командой юристов, прежде чем опубликовать дизайн. Шейла Селеш (старший контент-менеджер) и Остин Белисл (специалист по контенту) упаковывали, публиковали и продвигали наш дизайн.
Приведенный выше список благодарностей предназначен не только для того, чтобы воздать должное тем, кто внес свой вклад в этот процесс, но и для того, чтобы продемонстрировать силу корпоративной культуры в создании новых возможностей. Мы работали над этим проектом вне наших обычных обязанностей и командных структур, потому что мы хотели создать продукт, который мог бы оказать влияние на мир за пределами Fast Radius. Этот дух также пересек границы компании; мы благодарны P33 и всем врачам, которые поделились своим временем и опытом. Если мы больше ничему не научимся из этой пандемии, я надеюсь, что мы продолжим целенаправленно воспитывать культуру разнообразия, смирения и сотрудничества, работая над реагированием на насущные глобальные вызовы.
Наш дизайн доступен и готов к печати. Файлы САПР и инструкции можно найти на нашем веб-сайте.
Готовы создавать детали с помощью Fast Radius?
Начать цитатуПромышленные технологии
- Будущее за… Сотрудничество
- Функция в журнале MRO
- Метка два
- За кулисами нашего блога
- Воздействие COVID-19 на производство
- Ощутимые преимущества VR в инженерной сфере
- Таблица, данные, лежащие в основе информации
- История нашего самого популярного видео
- Значение обнаружения частичного разряда
- Будущее технического обслуживания